- China Harbour Engineering Company Limited (CHEC), Beijing, China
Cement deep mixing piles, as representatives of deep mixing technology, are mature and widely applied. However, effective application cases of cement deep mixing piles are relatively scarce in countries like Malaysia in Southeast Asia. In this paper, the application of cement deep mixing pile reinforcement in Malaysia is presented. Solidifying material was selected for deep mixing piles based on the soil conditions using unconfined compressive strength (UCS) tests. The relationship between the strength of deep mixing piles on-site and soil properties (type, organic matter content, and ion content) was analyzed. And a quality evaluation of the deep mixing piles in the project is conducted based on Kolmogorov-Smirnov (K-S) tests and relevant standards. Results show that fly ash cement is suitable as a solidifying agent for acidic soil layers containing organic matter in the local area. The strength of piles is significantly related to the soil condition. The UCS of cement mixing piles in silty clay and peat soils is smaller than clay. The overall correlation between organic matter content in the soil and UCS is negative, particularly when the organic matter content ranges from 10% to 14%, resulting in a significant drop in UCS. The bilateral significance probability is greater than 0.05 in K-S test, indicating that the UCS results in the projectconform to a normal distribution. Additionally, the evaluation of the overall quality of the mixing piles aligns with the requirements in the Japanese standard “Manual of Deep Mixing Construction Technology for Harbors and Airports” and the Chinese standard “Technical Code for Building Foundation Detection”.
1 Introduction
The widespread use of cement deep mixing piles in soft foundation reinforcement is attributed to its cost-effectiveness and ease of operation (Xue et al., 2024; Sukkarak et al., 2021). By using deep mixing machinery to simultaneously drill and inject cement or cement slurry into the soft soil, the soft soil at the foundation depth is solidified into cement-treated soil with sufficient strength and stability after a certain curing period (Phutthananon et al., 2023; Zhu et al., 2022). This technique aims to reinforce the foundation and is a widely utilized method for strengthening soft soil foundations.
Since cement, geopolymer and other cementitious materials have good structural strength and engineering performance (Lyu et al., 2020; Lyu et al., 2019; Lyu et al., 2021; Li et al., 2024a; Wang et al., 2024; Li et al., 2024b; Li et al., 2024c; Li et al., 2024d), numerous scholars have conducted studies focusing on the impact of cement on the solidification of soft soil (Liu and Starcher, 2013; Eissa et al., 2022; Wu et al., 2024). Truong (Truong et al., 2020) investigated the performance of silicate cement stabilized soils treated with ground granulated blast furnace slag (GGBFS), finding that the unconfined compressive strength increases with higher binder content, lower natural moisture content of soft soil. The UCS of soils treated with cement-GGBFS is higher than that of soils treated with silicate cement. Xu et al. (2009) conducted unconfined compressive strength tests and demonstrated significant differences in the effectiveness of slag silicate cement and ordinary silicate cement in strengthening coastal soft soils. Chen and Wang (2007) conducted direct shear tests and unconfined compression tests on soft soils stabilized with cement in different regions, finding that the particle size composition and organic matter content of specimens have a significant impact on the stabilisation effect. Xing et al. (2017) explored the influence of high montmorillonite content and different ions on the mechanical properties of saline-alkali soil cement. Montmorillonite accelerates the water-cement reaction, exhibits filling effects, volcanic ash effects, and can reduce the negative impact of corrosive ions on the strength of saline-lkali soil cement. Haji and Mir (2023) studied the effect of nano gypsum (NG) on the mechanical properties of cement stabilized silt-clay soil (CSS). The UCS increased by 9.11 times, and the cohesion increased by 4.44 times. However, there was almost no change in the internal friction angle. Liu et al. (2024) proposed stabilizing farmland road soft soil with cement and confirmed the effectiveness of cement stabilization through direct shear tests. Compared to untreated soil samples, the friction angle and cohesion of cement-stabilized soft soil were improved.
Nevertheless, the quality of cement deep mixing piles is a crucial in meeting specific engineering requirements (Shen et al., 2023; Pongsivasathit et al., 2021; Bergado et al., 1999). In response, researchers have conducted studies based on engineering case studies. Xu et al. (2006) analyzed the field situation of cement-soil mixing pile reinforcement in marine soft soil foundation in Lianyungang, China. The results indicate that the slag cement can be used as a solidifying agent, with content of 21%. Jia et al. (2004) employed cement and fly ash for the reinforcement of soft clay in the Minjiang River estuary area in China. The maximum strength of the reinforced soil was achieved when the mass ratio of cement was 16% and the fly ash content was 40% of the cement mass. Lu et al. (2018) studied the variation of cement-soil mixing piles in Weicheng Road soft soil in Wuxi, China. It was found that under the condition of fixed cement content, the addition of fly ash, lime, triethanolamine, sodium chloride, and sand has different enhancing effects on the solidificationof the silty soil. Quang et al. (2019) conducted unconfined compression tests and direct shear tests on cement-stabilized soft soil in Vung Long City, Vietnam. The results show that the shear strength increases with the cement content, and there is a significant difference between the shear strength of unsaturated/saturated samples and the Young’s modulus. Xu et al. (2012) researched the strength characteristics of cement-soil mixing piles in coastal soft soil in Jiangsu. The results reveal that due to the high moisture and salt content in the lower soil layer, the strength of the cement-soil in the pile body exhibits a characteristic of higher strength at the top and lower strength at the bottom.
In conclusion, the above engineering cases study analyzed the material mix design and strength of cement deep mixing piles under specific geological conditions but lacked a study on the strength change and overall quality evaluation of cement deep mixing piles on-site. Therefore, the cement deep mixing pile reinforcement applied in Malaysia was used as a case study in this research, whereby deep mixing pile solidifying materials suitable for the local conditions were selected, the relationship between deep mixing pile strength and soil properties, organic matter, and ion content was analyzed, and the overall quality of deep mixing piles was evaluated. The results can provide references for improving the quality of cement deep mixing piles in soft soil in similar engineering projects in the future.
2 Project overview
The East Coast Rail Link (ECRL) is a railway that Malaysia intends to construct on the Malay Peninsula. The project is located on the east coast of Malaysia and has been divided into several sections. The case study is sourced from the sixth section project. The sixth section project has a starting and ending mileage from CH313 + 900 to CH458 + 000, with a total length of 144.1km, including 108.3 km of subgrade, which accounts for 75% of the entire line. The line is located in the central part of the Malaysian peninsula, passing through Kuantan, Gambang, Maran, Temerloh from east to west, as shown in Figure 1.
The soft soil in the sixth section project is mainly distributed in low-lying areas such as inter hill valleys, river terraces, and floodplains. The main types are soft soil in valley and river phases. The soft soil has uneven thickness distribution, large undulations in the base, poor engineering mechanical properties, and significant impact of rainfall on the stability and settlement of embankments. In addition, the project area has a high organic matter content in the soil due to natural evolution and long-term immersion and sedimentation corrosion of trees, resulting in humus soil on the surface and insufficient foundation bearing capacity. The length of soft soil distribution is 30.057 km, accounting for 38.9% of the total length of the base, and the thickness of soft soil varies from 3 m to 15 m.
Soil sampling analysis was conducted on some organic matter soft soil sections. According to the test data, samples had an organic content of 14.4% ∼ 16.9%. Due to\constantly subjected to a chemically corrosive environment of marshy waterlogging, the surface organic soil exhibits acidity, a strong odor, and still retains some plant roots that have not completely decomposed. The moisture content range is 52.4% ∼ 60.4%, the bulk density range is 1.66 ∼ 2.01 g/cm3, the compression modulus range is 2.19 ∼ 5.91 MPa, the undrained strength range is 7 ∼ 20kPa, the consolidated quick shear strength cohesion range is 4 ∼ 6 kPa, and the internal friction angle is 1.8 ∼ 3.5°.
Since cement deep mixing piles have advantages of wide applicability to soil types, short construction period, low cost, high degree of construction mechanization, and some soft base have problems with deep soft soil (8–15 m deep) and high organic matter content, cement deep mixing piles are used for treatment. The design consists of 31 sections, totaling 9.5km, accounting for 12.5% of the total length of the roadbed. The total pile length is 3.616 million linear meters, with a designed pile diameter of 0.5 m. There are two pile arrangements: square and equilateral triangle, with pile spacing of 0.8 ∼ 1.2 m and pile length of 4 ∼ 14 m. A deep mixing pile machine (SP-05A18) is applied from Wuhan Tianbao Construction Machinery Co., Ltd. China as shown in Figure 2. The construction technology is dual injection and quadruple mixing. The construction process is as follows: drilling rig in place → slurry preparation → drilling rig start → drilling, advancing, and spraying → lifting drill bit and mixing at the same time → drilling and spraying again → lifting and mixing again → cleaning and shifting. The drilling mixing speed is 0.8 ∼ 1.0 m/min with a rotation speed of 30r/min, and then the mixing speed increased to 1.0 ∼ 1.2 m/min with a rotation speed of 40r/min.
3 Materials and methods
3.1 Soft soil solidifying materials
The basic properties of solidifying materials, gypsum, lime, sulphate-resistant cement, slag cement, and fly ash cement, are shown in the Table 1. Solidifying materials account for a certain weight percentage of the soft soil when adding them into the soil.
3.2 Unconfined compressive Strength (UCS) test
The unconfined compressive strength is tested in accordance with Standard Test Method for Unconfined Compressive Strength of Cohesive Soil (ASTM, 2024). The cemented soil specimens, kept until curing age, are placed at the center of the base plate of the testing machine as shown in Figure 3. Upon starting the testing machine, the specimens are uniformly loaded at a rate of (0.03–0.15) kN/s until failure, and the failure load is recorded. The strength is calculated as the maximum force at specimen failure divided by the cross-sectional area of the specimen before testing. Each set of parallel specimens consists of six samples (at least).
3.3 Soil organic matter and ion test
Soil organic matter content is determined using the alkali digestion method. Strong alkalis (such as sodium hydroxide) are used to digest the organic matter in the soil, and the organic carbon content in the solution is measured. Soil ion content is measured using ion chromatography. Soil samples are extracted to obtain soil solutions, and then ion chromatography is used to quantitatively analyze the ions in the soil solution. The number of repetitions is three.
3.4 Quality evaluation of deep mixing pile
The Kolmogorov-Smirnov (K-S) test is based on the cumulative distribution function and is used to examine whether an empirical distribution conforms to a theoretical distribution or to compare the significance difference between two empirical distributions (Lanzante, 2021). The basic idea is to compare the cumulative frequency F(x) of sample observations with the probability distribution Fx(x) of different hypothesized theories, in order to determine the type of probability distribution of the cumulative frequency.
The Harbor and Airport Construction Deep Mixing Treatment Technology Manual (Coastal Technology Research Center, 2018) requires that the design UCS value meets the requirements of Equation 1:
Where,
The determination of representative values for UCS in accordance with Technical Code for Testing of Building Foundation Soils (Ministry of Housing and Urban Rural Development of the PRC, 2015) is determined through Equations 2, 3.
Where, Φk represents the standard value of in-situ test data, γs is the statistical correction factor, Φm represents the mean value of in-situ test data, n is the number of samples, δ is the coefficient of variation of the in-situ test data.
4 Results and discussion
4.1 Effect of solidifying materials on UCS of deep mixing piles
4.1.1 Effect of gypsum and lime
According to the soil test results, the pH value of the soil is 3.9, indicating that it is acidic soil. Therefore, lime and gypsum are added to ordinary Portland cement to adjust the soil pH. The change in UCS is shown in Figure 4. The water-cement ratio is 0.5, and the sampling depth of the soil is within 2 m. With an increase in the cement content and curing days, the UCS of the cement mixed piles shows an increasing trend. However, this strength increase is very limited. For example, when the cement content is 35% and cured for 28 days, the UCS reaches only 0.48 MPa, which does not meet the strength standard. This may be due to the insufficient hydration reaction between the cement and the soil. Since gypsum and lime are alkaline materials, when added to acidic soil, they will balance the soil’s acidity. However, the cement did not undergo sufficient hydration reaction when reacting with the soil, resulting in insufficient strength of the cement mixed piles.
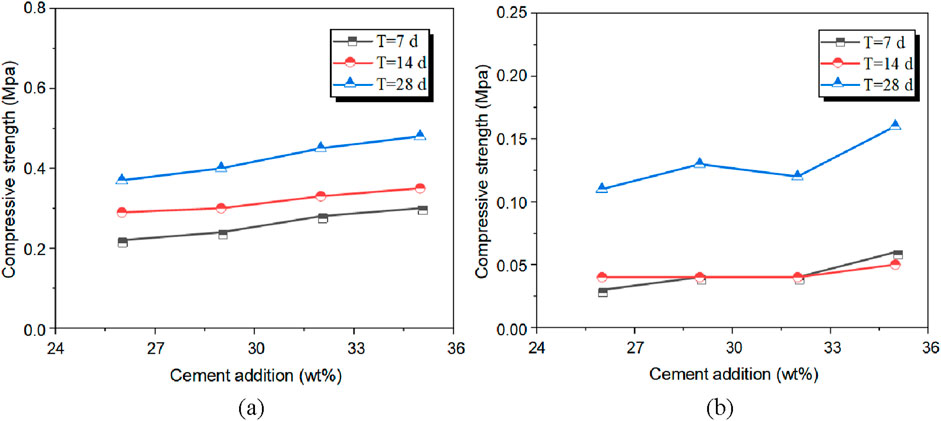
Figure 4. Indoor UCS of deep mixing piles: (A) adding 30wt% gypsum in cement; (B) adding 10wt% lime in cement.
4.1.2 Effect of sulfate-resistant cement
According to the soil test results, the SO42- content is 0.105%, indicating a sulfate soil environment. Sulfate environments can lead to sulfate attack on concrete. Therefore, a 52.5 sulfate-resistant cement was used, and the indoor UCS variation is shown in Figure 5. Under the same water-cement ratio and soil sampling depth, with a cement content of 26% and cured for 7 days, the UCS of the mixed piles is 0.04 MPa. Even after 7 days, there is no significant increase. When the cement content is increased to 35% and cured for 28 days, the compressive strength of the cement mixed piles is only 0.3 MPa, far below the requirement of 1 ∼ 1.5 MPa at 28 days. This is because although 52.5 sulfate-resistant cement can resist sulfate erosion, the high organic matter content in acidic soils will balance the acidity and alkali with sulfate-resistant cement, resulting in insufficient hydration between the cement and the soil, leading to poorer strength.
4.1.3 Effect of slag cement
Due to the inability to achieve the expected goals by adding lime, gypsum, and using sulfate-resistant cement in cement mixed piles, it was decided to replace ordinary Portland cement with slag cement, which has better reactivity. A water-cement ratio of 0.5 was designed. The indoor UCS is shown in Figure 6. When the slag cement content is 20%, the 28-day strength is 0.81 MPa, which does not meet the requirement. However, when the slag cement content is increased to 26%, the strength significantly increases. After 14 days of curing, the UCS reaches 1.12 MPa, meeting the design requirement. This indicates that slag cement can substantially improve the UCS of cement mixed piles.
However, it is important to note that application of slag cement content may lead to some issues. Firstly, the higher price of slag cement compared to other types may increase project costs. Secondly, in actual construction, excessive slag content may increase the difficulty and complexity of construction. Additionally, as Malaysia does not locally produce slag cement, it may be challenging to obtain an adequate supply of slag cement.
4.1.4 Effect of fly ash cement
Due to the inability to achieve the target strength in cement mixed piles, it was decided to replace ordinary 52.5 Portland cement with fly ash cement. A water-cement ratio of 0.8 was used, and the indoor UCS is shown in Figure 7. With an increase in the fly ash cement content and curing days, the UCS of the mixed piles significantly increases. When the cement content is 12%, the 28-day UCS is 0.61 MPa. With a cement content of 28% and 28 days of curing, the UCS of the fly ash cement mixed piles reaches 1.32 MPa. This indicates that fly ash cement with better reactivity effectively improves the strength quality of cement mixed piles.
Based on the above results, in areas with organic-rich acidic soil, it is suggested that fly ash cement was chosen as the solidifying agent with a cement content of 18%. This approach can achieve the required UCS in a relatively short period, while considering construction quality, project economics, and other factors such as soil characteristics, construction conditions, and material availability.
4.2 Mechanical properties of cement deep mixing piles on site
4.2.1 UCS of deep mixing piles at different depths
In order to control the construction quality of cement deep piles, field test piles will be conducted before. Two typical sites were chosen based on the actual site conditions and geological data. The first field test site, CH373 + 380, is located in a low-lying soft foundation catching water area with severe waterlogging during the rainy season. The characteristics of the soft soil at this site include soft soil with N values ranging from 2 to 6, silty clay. Observing soil samples from different depths, it was found that from 0 to 15 m, the soil samples were mainly silty clay. At depths of 10–15 m, the soil samples contained coarse sand and strong weathered sandstone, as shown in Figure 8. There are 3 groups of test piles, with 6 piles in each group, a pile diameter of 0.5 m, and a pile length of approximately 9.5 m.
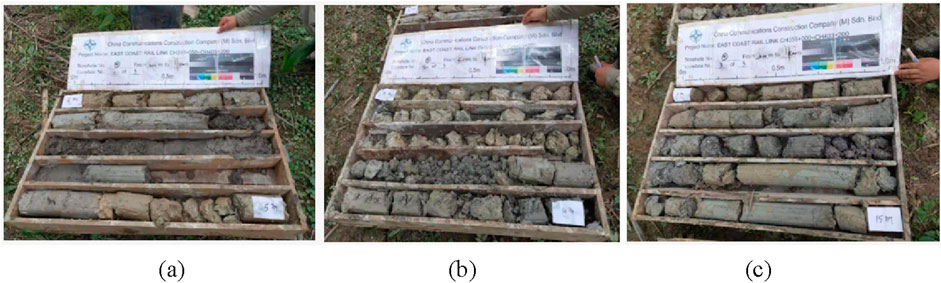
Figure 8. Soil condition at CH373 + 380: (A) 0–5 m silty clay; (B) 5–10 m silty clay with coarse sand; (C) 10–15 m containing coarse sand and strongly weathered sandstone.
Figure 9A shows the variation of pile UCS with depth of soil layers (UCS of the mixing piles is conducted every meter). It can be observed that under different cement addition, the UCS of the pile changes consistently, gradually increasing with depth. At depths of 0–3 m, the UCS of the mixed piles is less than 3 MPa. This is because the shallow layers consist of silt and clay, resulting in a weaker and uneven pile. In the depth range of 3.0–9.0 m, the pile strength increases rapidly, with mostly long piles and high strength. In addition, it can be clearly seen from the three-dimensional graph Figure 9B that when the cement addition is at 18wt%, the UCS value of the cement deep mixing pile is the highest (approximately at each 1 m depth).The average value of pile UCS increases with the cement dosage, and the coefficient of variation shows a similar trend of variation.
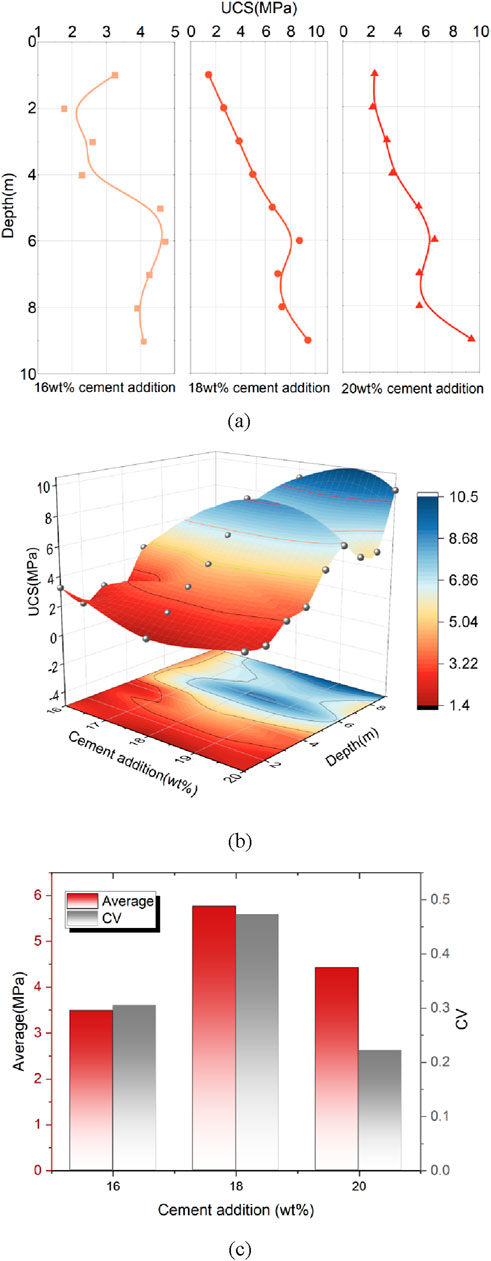
Figure 9. UCS change of deep mixing piles at CH373 + 380: (A) UCS change with depth and deep mixing pile core; (B) 3 d version of UCS change; (C) average and coefficient of variation.
Therefore, the 28-day UCS at test pile location CH373 + 380 is generally high. For soil conditions of this type, the laboratory is suggested to conduct multiple on-site soil sampling events to reduce the cement content and select a more economical and reasonable cement content as construction mix design.
The second test pile location (CH323 + 440) has a surface layer of approximately 3 m peat soil, with flat and open surroundings, belonging to perennially low-lying waterlogged marshland. The soft soil at this site has N values ranging from 1 to 8. Observing soil samples from different depths, it was found that from 0 to 2.9m, the soil samples were mainly humus soil. At depths of 2.9–12m, the soil samples were mainly silty clay containing loose coarse sand at the last 1 m depth, as shown in Figure 10. There are 3 groups of test piles, with 5 piles in each group, a pile diameter of 0.5m, and a pile length of 13 m.
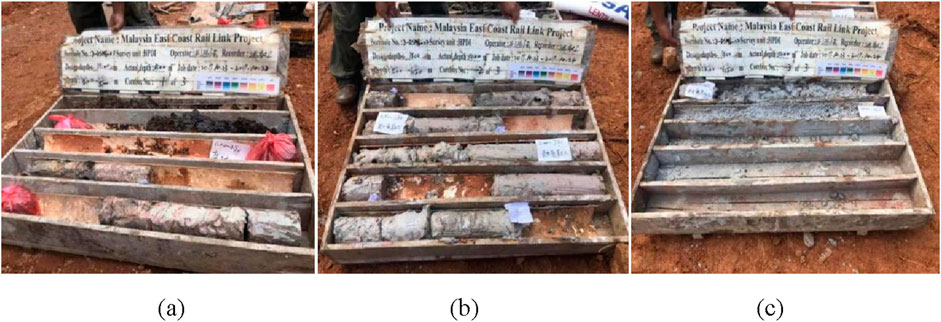
Figure 10. Soil condition at CH323 + 440: (A) 0–2.9 m humus soil; (B) 2.9–11 m silty clay, soft plastic; (C) 11–12 m loose coarse sand.
It can be observed in Figure 11A that the unconfined compressive strength variation of the pile is closely related to the geological conditions of the pile soil layers. Due to the presence of peat soil (0–3 m) with significant differences in organic matter content, the overall pile is discontinuous, with some test blocks failing to achieve a strength of 1 MPa. For soil samples deeper than 3 m, the 28-day UCS meets the design requirements. At depths of 7–9 m, there is a layer of red clay interbed, with UCS ranging from 1.19 to 2.23 MPa, lower than the strengths at other depths. In addition, it can be clearly seen from the depth-cement-UCS 3D graph that when the cement addition is 18 wt%, the UCS values change relatively uniformly with depth, and exhibit the maximum values at depths of 2 m and 12 m.The average UCS of the clay layer cores reaches 3.42 MPa, while the value of cores in the silt and clay layer is only 1.47 MPa, representing a decrease of 57.02%. This demonstrates a detrimental impact of the silt and clay layers on the quality of cement mixed piles. The average pile strength is maximum when the cement content is at 22%, which also corresponds to the maximum coefficient of variation.
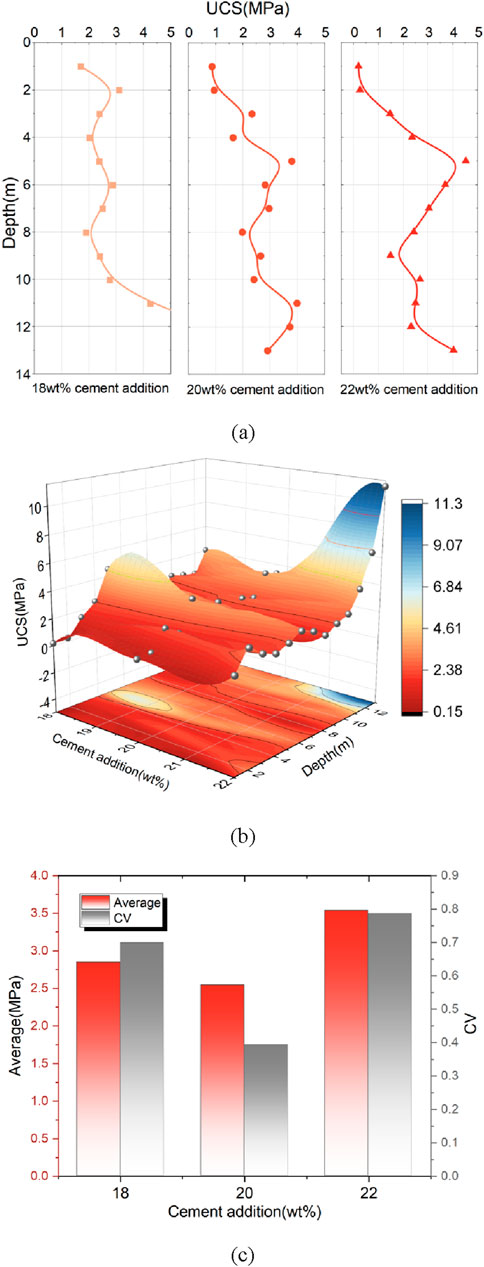
Figure 11. UCS change of deep mixing piles at CH323 + 440: (A) UCS change with depth and deep mixing pile core; (B)3 d version of UCS change; (C) average and coefficient of variation.
Therefore regarding CH323 + 440, when the plasticity index of the soil in this area exceeds 30, the drilling and grouting are not affected, indicating that the cement deep mixing process is suitable for certain soils with a high plasticity index. Due to the perennial accumulation of water at this test pile site, the moisture content of the underlying soil layer reaches 120%. The core sampling results show that the strength at 28 days is greater than 1 MPa, proving that the cement deep mixing process is applicable to some soil layers with high moisture content. Moreover, for the organic and peat soil in the surface layer, it is recommended to remove the roots in the surface layer and use new types of mud solidification materials or excavate the organic soil from the surface layer to ensure the quality of pile strength.
4.2.2 UCS of deep mixing piles under different organic matter contents
The chart in Figure 12 shows the change of the cement mixed pile UCS with organic matter content. It can be observed that the organic matter content in the soil is generally negatively correlated with UCS, indicating that higher organic matter leads to lower mechanical strength of cement mixed piles. Particularly, when the organic matter content is between 10% and 14%, there is a significant decrease in UCS. Taking the example of a cement content of 18%, the UCS decreases from 1.30 MPa to 0.71 MPa, representing a decrease of 45.38%.
This is mainly due to the interaction between the decomposed substance (humic acid and fulvic acid), the main components of organic matter, and the hydration products of cement. In peat soil, humic acid tends to combine with calcium ions in the hydration products of cement, hindering the formation of calcium crystallization and strength. When cement contact with fulvic acid, the fulvic acid acts as an adsorbent layer, delaying the hydration process of cement. Furthermore, fulvic acid easily combines with mineral particles containing aluminum elements, causing the disintegration of hydration products such as hydrated calcium aluminate, hydrated calcium sulfoaluminate, and hydrated iron aluminate, thereby disrupting the formation of structural strength (Kang et al., 2017).
4.2.3 Changes in UCS under different ion contents
The on-site soil ion detection results are shown in the Table 2. It can be observed that the soil from 0 to 3 m depth consists of peat soil, while the soil from 3 to 9 m depth is made up of silty clay with soft plasticity. Compared to the silty clay layer, the magnesium ion content in the peat soil has increased by 9.76%, while the aluminum and silicon content have decreased by 15.02% and 1.46% respectively. Furthermore, when comparing the UCS of cement-mixed piles in peat soil to those in silty clay, it is noted that the average UCS of cement-mixed piles in peat soil is lower than that in silty clay.
This is because, on one hand, the presence of a higher amount of magnesium ion in peat soil reacts with hydrated calcium silicate and hydrated calcium aluminate, which decreases the strength of the mixed piles. On the other hand, the decrease in aluminum and silicon content in peat soil reduces the formation of hydration products, affecting the strength of the mixed piles, ultimately resulting in weak strength of cement-mixed piles in peat soil layers. (Xiong et al., 2019).
4.3 Quality evaluation of on-site deep mixing piles based on k-s test
Based on the K-S test (Kolmogorov-Smirnov test) combined with the domestic standard Technical code for testing of building foundation soils (Ministry of Housing and Urban Rural Development of the PRC, 2015) and the Japanese Technical Manual for Deep Mixing Treatment in Harbor and Airport Construction (Coastal Technology Research Center, 2018), the overall quality of the testing can be evaluated. In statistics, commonly utilized non-parametric tests include the chi-square test and the K-S (Kolmogorov-Smirnov) test. The K-S test does not require data to be divided into intervals and is used to verify whether a single research subject follows a normal distribution. It is suitable for this project.
Firstly, it is known that in the deep mixing plies sections, the random sampling results meet the project standard requirements where 90% of the individual piles exceed the specified strength (i.e., the uniaxial compressive strength should be no less than 1.0 MPa at 28 days). Secondly, according to the coring time and project mileage, the on-site cement mixing pile core data can be divided into regions A, B, and C. The core sampling time for region A is in 2021, with a mileage of CH324-CH392, pile length range of 6 ∼ 12m, and a diameter of 0.5 m. The core sampling time for region B is in 2022, with a mileage of CH392 to CH419, pile length range of 6 ∼ 11m, and a diameter of 0.5 m. The core sampling time for region C is 2023–2024, with a mileage of CH419 ∼ CH450, piles length range of 6–14m, and diameter of 0.5 m. K-S tests are conducted on each region, and the results are shown in Table 3. Upon the results, the two-tailed significance probability is greater than 0.05, so the unconfined compressivestrength (UCS) values for each region conform to a normal distribution, as illustrated by the distribution in Figure 13.
Using the comprehensive evaluation method outlined in the Japanese manual (Coastal Technology Research Center, 2018), the project’s testing results are assessed. The results for Regions A, B, and C are presented in Table 4. According to the provisions of the Japanese technical manual, when the confidence level exceeds 84.1% (K = 1.0), the construction quality in each region meet the requirement of 1.0 MPa. However, when meeting K = 2.0 (a confidence level greater than 97.7%), no region’s strength value surpasses the design value. Therefore, based on the criterion of K = 1, the construction quality in all regions is deemed satisfactory.
Using the provisions of the Chinese code (Ministry of Housing and Urban Rural Development of the PRC, 2015), the results for each region are presented in Table 5. The standard value Φk of the in-situ tests conducted in the three project regions A, B, and C greatly exceeds the design strength value of 1.0 MPa, meeting the design requirements. Therefore, the construction quality in all regions is considered satisfactory.
Simultaneously, the project has carried out 1,130 tests on the bearing capacity of cement deep mixing composite base as shown in Figure 14. Results showed that over 99% of cement deep mixing composite base met the requirement of a settlement less than 40 mm. This further verifies that the cement deep mixing piles conform to the designed requirement.
5 Conclusion
Fly ash cement was chosen as the solidifying agent with a cement addition of 18wt%. This approach can achieve the required UCS in a relatively short period, while considering construction quality, project economics, and other factors such as soil characteristics, construction conditions, and material availability.
During the on-site pile testing, the strength of the piles is significantly correlated with the soil layers in which they are located. Compared to piles in clay layers, the strength of cement deep mixing piles in silty clay and peat soil decreases. The cement deep mixing process is suitable for certain soils with a high plasticity index and some soil layers with high moisture content. For the organic and peat soil in the surface layer, it is recommended to remove the roots in the surface layer and use new types of solidification materials or excavate the organic soil from the surface layer to ensure the quality of pile strength.
The organic matter content in the soil is generally negatively correlated with strength, especially when the organic content is between 10% and 14%, leading to a substantial decrease in the unconfined compressive strength (UCS). The presence of aluminum and silicon elements enhances the strength of cement soil and the effectiveness of cement deep mixing pile formation, while magnesium ions decrease the strength of cement soil, which adversely affects the performance of deep mixing piles.
Based on the results of the Kolmogorov-Smirnov (K-S) test, if the two-tailed significance probability is greater than 0.05, then the unconfined compressive strength (UCS) values in each region conform to a normal distribution. Simultaneously, they meet the overall quality assessment requirements for deep mixing piles as stipulated in the Japanese “Technological Manual for Deep Mixing Treatment in Harbor and Airport Construction” and the Chinese “Technical Code for Building Foundation Testing”.
In subsequent research, try as many locally suitable soft soil solidification materials as possible, and adjust the construction process by adding test pile points according to different soft soil areas, in order to obtain deep mixing piles with moderate strength as much as possible.
Data availability statement
The raw data supporting the conclusion of this article will be made available by the authors, without undue reservation.
Author contributions
ZX: Conceptualization, Writing–original draft. WZ: Investigation, Writing–review and editing. XZ: Data curation, Writing–review and editing. FM: Methodology, Writing–review and editing. FQ: Supervision, Writing–original draft. GX: Project administration, Writing–review and editing. ZN: Formal Analysis, Writing–review and editing. JC: Resources, Writing–review and editing.
Funding
The author(s) declare that financial support was received for the research, authorship, and/or publication of this article. The research is supported by key research and development projects of China Communications Construction Group Company Limited in 2021 (2021-ZJKJ-18). Authors appreciate its financial support gratefully.
Conflict of interest
Author(s) ZX, WZ, XZ, FM, FQ, GX, ZN and JC were employed by China Harbour Engineering Company Limited (CHEC).
The authors declare that this study received funding from China Communications Construction Group Company Limited. the funder had the following involvement: study design, collection, analysis of data.
Publisher’s note
All claims expressed in this article are solely those of the authors and do not necessarily represent those of their affiliated organizations, or those of the publisher, the editors and the reviewers. Any product that may be evaluated in this article, or claim that may be made by its manufacturer, is not guaranteed or endorsed by the publisher.
References
Bergado, D. T., Balasubramaniam, A. S., Soralump, S., and Lin, D. G. (1999). Mix design of soil-cement deep mixing method (DMM) for rehabilitation of bangna-bangpakong highway, bangkok, Thailand. Meeting11th asian regional conference on soil mechanics and geotechnical engineering, SEOUL, South Korea, AUG 16-20. Int Soc Soil Mech and Geotech Engn.
Chen, H., and Wang, Q. (2007). Laboratory study on consolidation effect of different area soft soils stabilized with cement. Rock Soil Mech. 28 (2), 423–426.
Coastal Technology Research Center (2018). Technical manual for deep mixing treatment in harbor and Airport construction No. 48. Tokyo: Daiko Printing Co., Ltd.
Eissa, A., Bassuoni, M., Ghazy, A., and Alfaro, M. (2022). Improving the properties of soft clay using cement, slag, and nanosilica: experimental and statistical modeling. J. Mater. Civ. Eng. 34 (4), 04022031. doi:10.1061/(asce)mt.1943-5533.0004172
Haji, T. R., and Mir, B. A. (2023). Effect of nano-gypsum on mechanical properties cement admixed marginal silty soil. Constr. Build. Mater. 408, 133639. doi:10.1016/j.conbuildmat.2023.133639
Jia, C., Huang, M., and Yao, H. (2004). Experimental research on stabilization of soft soil with cement and fly-ash in the Minjiang estuary. J. Tongji Univ. Nat. Sci. 32 (7), 884–888.
Kang, G., Tsuchida, T., Kim, Y. S., and Baek, W. J. (2017). Influence of humic acid on the strength behavior of cement-treated clay during various curing stages. J. Mater. Civ. Eng. 29 (8). doi:10.1061/(asce)mt.1943-5533.0001919
Lanzante, J. R. (2021). Testing for differences between two distributions in the presence of serial correlation using the Kolmogorov-Smirnov and Kuiper's tests. Int. J. Climatol. 41, 6314–6323. doi:10.1002/joc.7196
Li, H., Jin, P., Yan, C., Zhang, N., and Li, L. (2024c). Impact of polyethylene fiber and microsilica on fracture properties of high strength high toughness geopolymer concrete (HSHTGC). Dev. Built Environ. 18, 100399. doi:10.1016/j.dibe.2024.100399
Li, H., Li, L., Zhang, N., and Feng, Q. (2024a). Hybrid effect of polyethylene fibre and nano-calcium carbonate on the flowability and strength of a geopolymer composite. Mag. Concr. Res. 76 (4), 188–200. doi:10.1680/jmacr.23.00090
Li, L., Ma, Z., Gao, C., Sun, A., Liu, B., and Pu, B. (2024d). Hybrid effect of nano-CaCO3 and polypropylene fiber on fresh and hardened properties of alkali-activated material. J. Mater. Civ. Eng. 6 (36), 4024143. doi:10.1061/jmcee7.mteng-16701
Li, L., Sun, H., Zhang, Y., and Li, Z. (2024b). Dynamic evolution of crack fractal of polypropylene fiber reinforced geopolymer during flexural process. Eng. Fract. Mech. 300 (16), 109992. doi:10.1016/j.engfracmech.2024.109992
Liu, A. J. C., Abu, T. Z., Bong, J. Y., Ling, F. N. L., and Yunusa, G. H. (2024). Effect of cement stabilization on shear strength parameters of soft soils on agricultural road. Int. J. Sustain. Constr. Eng. Technol. 15 (1), 15–24. doi:10.30880/ijscet.2024.15.01.002
Liu, C., and Starcher, R. D. (2013). Effects of curing conditions on unconfined compressive strength of cement- and cement-fiber-improved soft soils. J. Mater. Civ. Eng. 25 (8), 1134–1141. doi:10.1061/(asce)mt.1943-5533.0000575
Lu, X. H., Cui, M. X., Wang, P. F., and Li, B. (2018). Application in cement soil of stabilizer in silt soft soil of Wuxi in China. J. Coast. Res. 83 (83), 316–323. doi:10.2112/si83-052.1
Lyu, Z., Guo, Y., Chen, Z., Shen, A., Qin, X., Yang, J., et al. (2019). Research on shrinkage development and fracture properties of internal curing pavement concrete based on humidity compensation. Constr. Build. Mater. 203, 417–431. doi:10.1016/j.conbuildmat.2019.01.115
Lyu, Z., Shen, A., and Meng, W. (2021). Properties, mechanism, and optimization of superabsorbent polymers and basalt fibers modified cementitious composite. Constr. Build. Mater. 276 (5), 122212. doi:10.1016/j.conbuildmat.2020.122212
Lyu, Z., Shen, A., Mo, S., Chen, Z., He, Z., Li, D., et al. (2020). Life-cycle crack resistance and micro characteristics of internally cured concrete with superabsorbent polymers. Constr. Build. Mater. 259 (3), 119794. doi:10.1016/j.conbuildmat.2020.119794
Ministry of Housing and Urban Rural Development of the PRC (2015). JGJ340-2015. Technical code for testing of building foundation. China: Soils China Architecture and Building Press.
Phutthananon, C., Jongpradist, P., Kandavorawong, K., Dias, D., Guo, X., and Jamsawang, P. (2023). Reliability assessment for serviceability limit states of stiffened deep cement mixing column-supported embankments. J. Rock Mech. Geotechnical Eng. 15 (9), 2402–2422. doi:10.1016/j.jrmge.2023.05.008
Pongsivasathit, S., Petchgate, W., Horpibulsuk, S., and Piyaphipat, S. (2021). Corrigendum to “Composite contiguous pile wall and deep mixing column wall as a dam – design, construction and performance” [Case Stud. Construct. Mater. 15 (2021) 1–16]. Case Stud. Constr. Mater. 16, e00904. doi:10.1016/j.cscm.2022.e00904
Quang, V. P., Nhat, T. P., Ba, V.Le., and Dinh, U. V. (2019). “Experimental studies on the improvement of soft soils by cement in vinh long city,” in Proceedings of the International Conference on Sustainable Civil Engineering and Architecture. Lecture Notes in Civil Engineering, China, October 2022.
Shen, H., Li, X., Duan, R., Zhao, Y., Zhao, J., Che, H., et al. (2023). Quality evaluation of ground improvement by deep cement mixing piles via ground-penetrating radar. Nat. Commun. 14 (1), 3448. doi:10.1038/s41467-023-39236-4
Sukkarak, R., Jongpradist, P., Kongkitkul, W., Jamsawang, P., and Likitlersuang, S. (2021). Investigation on load-carrying capacity of geogrid-encased deep cement mixing piles. Geosynth. Int. 28 (5), 450–463. doi:10.1680/jgein.21.00026
Truong, S. B., Thi, N. N., and Thanh, D. N. (2020). An experimental study on unconfined compressive strength of soft soil-cement mixtures with or without GGBFS in the coastal area of vietnam. Adv. Civ. Eng. 2020 (1), 1–12. doi:10.1155/2020/7243704
Wang, K., Li, J., Li, L., Deng, E., Zhang, Y., and Li, Z. (2024). Machine learning to estimate the bond strength of the corroded steel bar-concrete. Struct. Concr. 25: 696–715. doi:10.1002/suco.202300401
Wu, Y., Liu, X., Yang, J., and Liu, Q. (2024). Influence of the wide range cement content on the properties of cement–treated marine soft soil and bound method of semi–solidified soil. Case Stud. Constr. Mater. 20, e03180. doi:10.1016/j.cscm.2024.e03180
Xing, H., Xiong, F., and Zhou, F. (2017). Improvement for the strength of salt-rich soft soil reinforced by cement. Mar. Georesources and Geotechnol. 1-5. doi:10.1080/1064119X.2016.1278064
Xiong, F., Xing, H., and Li, H. (2019). Experimental study on the effects of multiple corrosive ion coexistence on soil-cement characteristics. Soils Found. 59 (2), 398–406. doi:10.1016/j.sandf.2018.12.001
Xu, C., Dong, T., and Ye, G. (2006). Application of cement deep mixing method in Lianyungang marine soft soil foundation. Rock and Soil Mech. 27 (3), 495–498.
Xu, C., Guo, H. F., and Yang, X. M. (2009). Comparation analyses of the effects of marine soft soil improved by portland cement and slag cement. Rock and Soil Mech. 30 (9), 2737–2740.
Xu, S., Yan, C., and Xu, B. (2012). Strength characteristics of the mixed cement pile in marine soft soil. Coal Geol. and Explor. 40 (1), 34–37.
Xue, Z. J., Zhu, W. F., Li, L. C., Chao, J., Yan, C. G., Wang, Y. X., et al. (2024). Carbon emissions assessment of cement mixing piles for soft loess improvement and carbon emission reduction using white mud-cement composite material. Case Stud. Constr. Mater. 21, e03397. doi:10.1016/j.cscm.2024.e03397
Keywords: cement deep mixing pile, unconfined compressive strength, case study, evaluation, fly ash cement
Citation: Xue Z, Zhang W, Zhao X, Meng F, Qin F, Xiao G, Nie Z and Chen J (2024) Utilization of cement deep mixing pile for soft soil foundation: a malaysian case study. Front. Mater. 11:1484228. doi: 10.3389/fmats.2024.1484228
Received: 21 August 2024; Accepted: 31 October 2024;
Published: 15 November 2024.
Edited by:
Pawel Polaczyk, Texas Tech University, United StatesReviewed by:
Li Li, Northwest A and F University, ChinaMounir Bouassida, Tunis El Manar University, Tunisia
Guoqiang Sun, Beijing University of Technology, China
Zhenghua Lyu, Guangdong Ocean University, China
Copyright © 2024 Xue, Zhang, Zhao, Meng, Qin, Xiao, Nie and Chen. This is an open-access article distributed under the terms of the Creative Commons Attribution License (CC BY). The use, distribution or reproduction in other forums is permitted, provided the original author(s) and the copyright owner(s) are credited and that the original publication in this journal is cited, in accordance with accepted academic practice. No use, distribution or reproduction is permitted which does not comply with these terms.
*Correspondence: Guliang Xiao, Z2x4aWFvMzBAMTYzLmNvbQ==