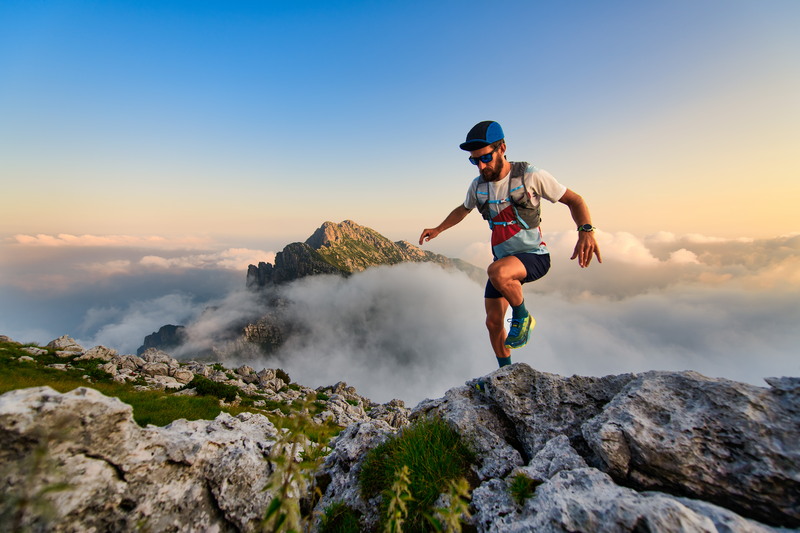
94% of researchers rate our articles as excellent or good
Learn more about the work of our research integrity team to safeguard the quality of each article we publish.
Find out more
REVIEW article
Front. Mater. , 27 January 2025
Sec. Structural Materials
Volume 11 - 2024 | https://doi.org/10.3389/fmats.2024.1458752
This article is part of the Research Topic Advancing Low-Carbon Solutions in Materials and Technologies for 3D Construction Printing View all articles
The construction industry has recently increased the adoption of additive manufacturing (AM, also known as 3D-printing) technologies. This review paper presents the state of the art of ground-based AM systems in construction, focusing comprehensively on developments in the material aspect towards using unmanned aerial vehicles (UAV), commonly referred to as “drones”. AM itself is introduced, and an overview of the history of AM is provided. Key projects developing both ground-based cementitious and polymeric AM applications for construction purposes are reviewed along with material constituents, AM deposition methods and reinforcement techniques to mitigate against crack propagation. The review details a cutting-edge Aerial Additive Manufacturing (AAM) system developed to utilise untethered, self-powered UAV platforms extruding material during autonomous flight, which is designed to bring multi-agent aerial mobility to AM in the construction industry. An overview of the history of UAV development is presented, as well as the current use of UAV platforms combined with material deposition devices for construction and considerations for developing suitable materials and future research.
Additive manufacturing (AM) has experienced growth in multiple industrial sectors (Mandolini et al., 2022), including the enormous and high economic and environmental-impact construction industry (Khajavi et al., 2021). AM has been defined by the ASTM International Committee F42 on AM Technologies as the “process of joining materials to make objects from three-dimensional (3D) model data, usually layer by layer, as opposed to subtractive manufacturing methodologies” (ASTM, 2012). Modern AM technology can be traced back to the patented invention of stereolithography by Charles Hull in 1986 (Wohlers et al., 2016). Stereolithography involves realising objects one discreet layer at a time by using computer-controlled Ultraviolet (UV) rays to solidify a UV-sensitive liquid polymer. The first commercial AM machine appeared in 1987 (Wohlers et al., 2016). Epoxy resins were also developed for use with the new technology (Wohlers et al., 2016).
In the 1990s, three commercial methods of AM were established (Wohlers et al., 2016):
• Fused deposition modelling (FDM) - involving the extrusion of thermo-plastic filaments from a nozzle to create an object one layer at a time from a digital, horizontally sliced software model. FDM progressed to accounting for most AM technological applications by 2019 (Kaščak et al., 2021).
•Solid ground curing - using a UV-sensitive liquid polymer, solidifying full layers in one pass by flooding UV light through glass-plate masks.
•Laminated object manufacturing - this method cuts from a volume of sheet material using a digitally guided laser, and the layers are stacked.
FDM emerged as the prominent and most influential AM technology. During the 21st century, rapid development in the commercialisation of AM occurred with an ongoing increase in the number of industrial applications, most notably in the manufacture of components for the medical and aerospace sectors (Wohlers et al., 2016). The FDM printing process normally utilized a nozzle extrusion temperature ranging from 230°C to 250°C, with a layer height set between 0.1 mm and 0.3 mm depending on the desired resolution. The print speed was maintained at approximately 50 mm/s, ensuring precise filament deposition and consistent layer bonding. These parameters were optimized to maintain the integrity of the thermoplastic material while minimizing warping and ensuring repeatability. In addition to polymers, AM processes use materials such as metals, ceramics, composites and biological materials. Technologies developed to the extent that the materials used within AM processes could be liquid, filament, paste, powder, or solid sheets of material (Wohlers et al., 2016).
Compared to other industrial sectors, the development of AM in construction has been relatively slow and is still essentially in a state of relative infancy (Buswell et al., 2007; Bos et al., 2016; Paolini et al., 2019; Tay et al., 2017; Camacho et al., 2018). The past decade has seen an increase in the number of AM projects in the construction industry and construction-related research, creating larger-scale objects using 3D-printable concrete, mortar or cementitious paste, in addition to research involving polymers such as insulating polyurethane foams (Tay et al., 2017; Camacho et al., 2018). Fresh cementitious material rheological properties, choice of aggregate and speed of curing are key to such studies (Song and Li, 2021; Mechtcherine et al., 2020a). Until now, ordinary Portland cement (OPC) still dominates in most 3D printable cementitious materials proposed, but other alternative cement systems such as sustainable geopolymers (Ur Rehman and Sglavo, 2020; Voney et al., 2021; Archez et al., 2021; Muthukrishnan et al., 2021; Bong et al., 2021; Panda and Tan, 2018; Munir et al., 2021; Panda et al., 2017), reactive magnesium oxide cement (RMC) (Khalil et al., 2020), magnesium potassium phosphate cement (MKPC) (Weng et al., 2019) and calcium sulphoaluminate (CSA) cement (Ma et al., 2020; Chen et al., 2020a,b,c) have drawn attention, to reduce the carbon print of OPC. The aggregate to binder ratio for the printable mixtures has been studied (Chen Y. et al., 2020; Le et al., 2012a; Rahul et al., 2019; Paul et al., 2018; Tay et al., 2019; Rahul et al., 2020; Panda et al., 2019b,a). Supplementary cementitious materials (SCM) such as pulverised fuel ash (PFA, fly ash), silica fume, calcined clay and limestone have also been used in many printable cementitious materials (Mohan et al., 2021b; Figueiredo et al., 2019; Panda and Tan, 2019; Mohan et al., 2021a; Scrivener et al., 2018b,a; Zunino and Scrivener, 2021; Chen et al., 2021). The mix proportions for the 3D printing of cementitious materials by using eco-friendly binders (Panda and Tan, 2019; Kazemian et al., 2017; Chen et al., 2019; Alghamdi et al., 2019; Muthukrishnan et al., 2020), waste aggregates (Xiao et al., 2020; Ding et al., 2020a; Cuevas et al., 2021; Ting et al., 2021; Ding et al., 2021; Li et al., 2021), chemical admixtures (Chen et al., 2020c; Chen et al., 2018; Qian et al., 2018) and nano-additives (Chu et al., 2021; Sikora et al., 2021; Moeini et al., 2020; Chougan et al., 2020) are reviewed in the literature (Sikora et al., 2021; Rehman and Kim, 2021).
AM in the construction industry generally uses large, ground-based processes that rely on favourable topography, soil and weather conditions (Kreiger et al., 2015; Lim et al., 2012). The size of a ground-based additive-manufactured building is limited by the size of the 3D printing machinery, while the manoeuvrability of the 3D printing system could limit the architectural design. In contrast, aerial additive manufacturing (AAM), also referred to as aerial additive building manufacturing, can release building projects from creative, dimensional and logistical ground-based constraints (as shown in Figure 1) (Economist, 2017). An aerial approach could effectively reduce safety risks and costs when facing elevated, hostile, or inaccessible environments (Dams et al., 2017; Furkan Kaya et al., 2024).
This review first presents an overview of representative ground-based AM projects for both cementitious and polymeric materials. The paper then discusses the knowledge transfer for materials from AM towards AAM. A systematised overview of AAM to date, including unmanned aerial vehicles (UAV), materials development trajectory design and printing, is then presented in detail. Finally, this paper proposes areas for continuing research, aiming to provide guidance to both AM and construction material research communities with a particular emphasis upon the use of multiple printing agents.
The past decade has seen the rapid development of AM research in the construction industry, where the applications of ground-based AM have been increasingly studied in recent years (Paolini et al., 2019). Both gantry-based and robotic-arm-based systems have been created to print building parts using cementitious and polymeric materials. In this session, key ground-based AM processes and their applications in research and construction projects are reviewed.
Cementitious materials are typically printed using a method of layered filament extrusion. Selected salient investigations are depicted in the timeline illustrated in Figure 2. It should be noted that not all 3D-printed concrete AM studies utilise the method of extruding one layer at a time based on the FDM principle. For example, an alternative particle bed fusion method involves depositing a binding solution into a powder bed of material to fuse particles together, solidifying the powder where required, leaving unused material to be later removed (Lim et al., 2009; Lowke et al., 2018; 2015; Morgante et al., 2017; Fratello, 2021; Teizer et al., 2016; House, 2021; Aghaei-Meibodi et al., 2017). However, this approach does not lend itself readily to in-situ construction due to being highly vulnerable to inclement weather (Tay et al., 2017). Other studies have investigated the spraying of cementitious material, such as the Knit Candela project developed at ETH, Zurich, Switzerland (Architects, 2021).
Figure 2. Examples of cementitious material AM studies, with the year of publication commencement indicated.
All cementitious studies feature ground-based mixers, pumps and deposition components. Extrusion-based cementitious studies generally use either an XYZ coordinate gantry frame or robotic arms with multiple (typically four or six) degrees of freedom (DOF). Robotic arms can be static or mobile. The anisotropic properties found in the layers of extruded material are the subject of ongoing research (Ducoulombier et al., 2020; Ding et al., 2020b; Murcia et al., 2020; Van Der Putten et al., 2020). Reinforcement and cracking considerations are first discussed before the introduction of each research and construction project since it is important for practical applications.
It is inevitable that concrete will feature some degree of cracking, as the deposited material is typically restrained and will be subject to tensile forces (Passuello et al., 2009). Examples of the different types of cracking which can occur are:
•Shrinkage cracking will occur due to fresh concrete mixes containing liquid water;
•Structural cracking, which occurs as a result of loading over long periods of time or can occur in phased construction, for example, bridges (Issa, 1999);
•Thermal cracking of concrete can occur with the heat of the hydration reaction, causing a rise or descend in temperature and a corresponding expansion of the material (Šavija and Schlangen, 2016);
•Cracking can also occur due to water expansion attributed to freezing or cyclic freeze-thaw conditions (Yang et al., 2006).
Reinforcement phases in cementitious materials can provide resistance to crack propagation in addition to providing a degree of ductility and taking tensile forces, and reducing the risk of sudden, brittle failure. There have been several approaches to reinforcing extruded cementitious material. Traditional steel reinforcement used in concrete is not naturally compatible with an AM approach, but it has been possible to autonomously deposit fresh concrete around pre-positioned steel reinforcing bars (Lloret-Fritschi, 2016). However, with the absence of traditional steel reinforcement, there have been several approaches to addressing and improving the tensile strength, ductility and resistance to crack propagation in fresh cementitious material. Alternative reinforcement approaches undertaken in cementitious material include:
•Short, chopped fibres, typically ranging from 5 mm to 20 mm long, extruded within the filament as part of the fresh mix. Fibrous materials include polymers such as polyethylene (PE) (Ding et al., 2021), polypropylene (PP) (Le et al., 2012a; Li et al., 2018) and polyvinyl alcohol (PVA) (Lloret-Fritschi, 2016; Hossain et al., 2013) and other fibres such as carbon, glass and steel (Li et al., 2021; Chu et al., 2021; Bos et al., 2019; Arunothayan et al., 2020; Pham et al., 2020);
•Continuous lengths of reinforcing material extruded either in tandem with the cementitious material, with the reinforcement becoming entrained in the extruded material (Ducoulombier et al., 2020; Bos et al., 2017; Mechtcherine et al., 2020b), or placed on top of a recently extruded layer before the extrusion of the following layer (Wangler and Flatt, 2018);
•Application of nanotechnology, where incorporating nanomaterials can effectively reduce the defects or porosity of cementitious matrices at the nanoscale (Metaxa et al., 2021). Nanomaterials including nanosilica (Sonebi et al., 2015; Kruger et al., 2019; Reales et al., 2019), nanoclay (Panda et al., 2019b; Quanji et al., 2014; Qian et al., 2019) and carbon-based materials (Goldmann et al., 2021; Qureshi and Panesar, 2020; Sun et al., 2017; Madbouly et al., 2020; Meng and Khayat, 2018; Konsta-Gdoutos et al., 2010; Horszczaruk et al., 2015) such as carbon nanotubes (CNTs), graphene nanoplatelets (GNPs), nano-graphite platelets (NGPs), graphene oxide (GO), reduced graphene oxide (rGO) can improve the resistance of cementitious materials to crack propagation (Sikora et al., 2021);
•The use of a mesh-mould technique, which involves printing a 3D mesh with a material such as a rapidly cooling thermoplastic. Cementitious material is then applied around the cooled, printed mesh, with the mesh ultimately serving as reinforcement (Tay et al., 2017; Marchment and Sanjayan, 2020). The concept of formwork, also serving as reinforcement, has also been introduced by projects developed at ETH Zurich (Hack et al., 2017).
Hossain et al. reported that the addition of polyvinyl alcohol (PVA) and metallic fibres to cementitious mixes (to a maximum of 0.3% by volume) were effective in substantially increasing fracture energy, particularly the steel fibres (Hossain et al., 2013). This would reduce the quantity of tensile reinforcement required (and increase energy-absorbing capacity), but not act as a complete substitute for tensile reinforcement. Therefore, it can be surmised that the primary function of the addition of fibres to cementitious mixes is to resist crack propagation and provide a measure of ductility rather than to significantly increase flexural or tensile strengths and remove the need for steel rebar entirely.
Figure 3 shows images of different extrusion-based cementitious systems for 3D-printing structures, and the underlying AM cementitious studies are presented in the following sections.
Figure 3. AM in construction studies using a layered extrusion method with cementitious materials: (A) Contour crafting, Southern California (Zareiyan and Khoshnevis, 2017), (B) Concrete printing, Loughborough (Le et al., 2012a), (C) Smart dynamic casting, ETH Zurich (Wangler et al., 2017), (D) 3DCP, TU Eindhoven (Bos et al., 2018), (E) Multiple mobile robots, Nangyang (Zhang et al., 2018).
In applications where composite materials are subjected to cyclic loading, such as bridge construction or elevated structures, the long-term durability and fatigue properties become critical factors for evaluation. Research has shown that incorporating fibers, such as steel, polypropylene, or polyvinyl alcohol (PVA), can significantly enhance the fatigue life of cementitious composites. For instance, studies have demonstrated that carbon and glass fibers improve the resistance to crack propagation under cyclic loading by distributing stresses and enhancing the material’s tensile strength. Furthermore, nanomaterials like graphene and carbon nanotubes (CNTs) have been proven to reduce micro-cracking and improve the long-term integrity of the matrix by increasing both toughness and stiffness. These enhancements are essential for maintaining structural integrity and minimizing maintenance in cyclically loaded applications.
Microscopy can be useful for examining how microstructural properties relate to the mechanical performance of materials for AM.
Papadakis et al. (1999) showed used Scanning Electron Microscopy (SEM) and Atomic force microscopy (AFM) to examine the microstructure of fly ash and silica fume with cement paste, with SEM providing a good overview of the surface textures and AFM revealing that silica fume particles were spheroid and also cylindrical in shape, and further information concerning pore microstructure. Additives reacting with calcium hydroxide in the cement paste resulted in small spheroid bulges, giving surfaces an additional roughness. Pore and grain refinements identified by AFM can be responsible for enhancing strength and durability.
Fibres are a popular reinforcement option to add to AM materials and Masoud et al. (2024) used SEM to examine the microstructural properties of polypropylene fibres within a geopolymer concrete matrix, revealing distribution, alignment and interlocking properties. Fibres were revealed to provide a bridging effect connecting elements of the matrix, which enhances stress distribution, improves load-bearing capacity and with greater distribution of localised stresses mitigating the risk of crack propagation in that locality. SEM can also reveal signs of incomplete hydration within the matrix, identified by a lack of uniformity in texture across the geopolymer concrete matrix surface, with some areas appearing to be less consolidated, or appearing as a powdery residue. Non-uniform hydration and geopolymerisation reactions can result in a reduction of strength development and increased porosity, although the presence of the fibres can still result in improved ductility and durability. Incomplete hydration at sites of fibre-matrix interface can be a hindrance to the effective transfer of loads between the matrix and fibres, reducing the effectiveness of the fibrous reinforcement. Incomplete hydration may also be identified by dehydration cracks being observed, initiating from the edges of an aggregate particle being partially enveloped by the geopolymerisation gel phase; this can result in the bond between the fibres and matrix being reduced, promoting the likelihood of fibre pull-out under applied load.
The alignment of fibres, and the observed phenomenon of fibres bridging voids within a matrix, can be beneficial in creating load-bearing pathways that can distribute applied loads, therefore contributing to an improvement in the resistance to crack propagation and the toughness of the material. A lack of uniformity in the alignment of fibres can result in uneven stress distributions or stress concentrations within the material, promoting crack propagation and leading to a reduction in mechanical strength. Tensile fibres offer potential benefits in resisting crack propagation, but a non-uniform distribution, possibly with clusters of fibres together, may reduce the capacity of the material to fully use the tensile properties and reinforcement potential of added fibres Masoud et al. (2024).
Polypropylene are an example of hydrophobic fibres. A drawback of using fibres with water-repellent properties is they may influence moisture interaction by the surrounding cementitious matrix curing process Rostami et al. (2020) Hydrophobic fibres can promote incomplete hydration and a site where fibres are located risks being a site of incomplete dehydration, which can be identified as voids, cracks, and grainy particulates in the microstructure. Fibres may act as local barriers, restricting adjacent matrix region to the access of water. Incomplete hydration can result in the bonding between fibres and matrix being compromised, reducing strength and robustness Rostami et al. (2020) and promoting crack propagation.
The addition of fibres to additive manufacturing material can improve fracture toughness post-fracture but also cracking due to shrinkage or drying. Fibres can consist of fiberglass, carbon, polypropylene (PP), polyvinyl alcohol (PVA), or steel Zaid and El Ouni (2024).
The alignment of the fibres, and the observed phenomenon of them bridging voids in the matrix, can be beneficial in creating load-bearing pathways that can distribute applied loads, therefore contributing to an improvement in the resistance to crack propagation and the toughness of the material. A lack of uniformity in the alignment of fibres can result in uneven stress distributions or stress concentrations within the material, promoting crack propagation and reducing mechanical strength. Tensile fibres offer potential benefits in resisting crack propagation, but a non-uniform distribution, possibly with clusters of fibres together, may reduce the capacity of the material to fully use the tensile properties and reinforcement potential of added fibres Masoud et al. (2024).
The use of unidirectional carbon fibre bundles to improve fracture toughness in a polymer composite was explored by Akasheh and Aglan, 2019. It was found that wrapping carbon fibre around the notch in tests blunted the notch and redirected crack propagation away from the notch tip, promoting fracture resistance. However, too many added fibres can create a saturation level, beyond which any gains can be reversed as a result of notch-targeted reinforcement Akasheh and Aglan (2019).
Another approach in improving toughness in addition to reinforcing fibres is to use architectural design. An example is using sinusoidal design in additive manufacturing in three orientations. The sinusoidal design in the ‘y’ orientation demonstrated fracture toughness equivalent to a cast volume of cementitious materials with an improvement in flexural strength and an improvement in fracture toughness in relation to a perpendicular lamellar by utilizing the sinusoidal design Prihar et al. (2024). The use of bio-inspired designs, informed by the structures of living organisms is another area of developing research to utilise the properties of designs such as a Bouligand structure, which resembles plywood and has aligned fibres which can help to mitigate crack propagation and improve toughness Aghaee et al. (2024).
The following sections present a review of existing AM applications and cementitious materials used.
Contour Crafting was a pioneering study into cementitious construction using AM, conceived in 1998 and under continuous development ever since (Figure 3A). Using an XYZ gantry frame, it possessed top and side trowels adjacent to a six-axis nozzle, which smoothed extruded filaments as printing occurred, resulting in a characteristic smooth finish to the concrete (Khoshnevis, 2004).
In its early stages, the project experimented with clay and used form ties to connect adjacent layers together (Khoshnevis, 2004). As of 2017, the material water/cement ratio is 0.5, natural river sand (maximum particle size of 4 mm) is used at a sand:binder ratio of greater than 2:1, mix densities are 2,200 kg/m3 and 28-day compressive strengths are 26 MPa (ASTM C 39) (Zareiyan and Khoshnevis, 2017). A nozzle diameter of 15 mm has been used (Khoshnevis, 2004). Polypropylene fibres, superplasticiser and silica fume, have also been added to the mixes (Zareiyan and Khoshnevis, 2018).
The Concrete Printing study based at Loughborough University, United Kingdom, began in the early 2010s, also using a gantry frame during the first phase (Figure 3B), and experimented with 12 mm long chopped polypropylene fibres into the fresh concrete mix. The size of the nozzle and, therefore, extruded filament diameter was 9 mm (Le et al., 2012a). In contrast with Contour Crafting, the extruded objects exhibit a characteristic ribbed, layered effect because of its extrusion resolution.
Shear strengths of concrete material at rest were recorded as approximately 0.5 kPa–2.5 kPa with the concrete printing method (Le et al., 2012a), differing considerably with variation in superplasticiser and accelerator added. The mixes typically possessed a water/cement mass ratio in the region of 0.25–0.4 and added 0.5% by mass of superplasticiser. High 28-day compressive strengths greater than 75 MPa were recorded with mix densities of approximately 2,300 kg/m3. Cementitious binders were based upon CEM I with added pulverised fuel ash, sand and silica fume (Le et al., 2012a).
The 2012 phase of study on fresh mixes considered the optimum fresh mix to have a 3:2 sand/binder ratio, with the binder consisting of 70% cement, 20% pulverised fuel ash and 10% silica fume plus 1.2 kg/m3 of 12 mm long, 0.18 mm diameter polypropylene fibres added to minimise crack propagation. The water/binder ratio was 0.26, which is low and associated with high-performance strength of concrete, with a superplasticiser and retarder added at 1% and 0.5%, respectively, by weight of the binder. This mix provided good buildability, and the open-time of the fresh mix was considered to be 100 min (Le et al., 2012a).
Investigations have evolved over the years, and recent 3DCP experiments based at Loughborough University have featured a large robotic arm that is also capable of milling extruded material. A large ABB IRB 6640 6-axis robotic arm with a 2.4 by 1.5
Milling extruded material can be performed by the ABB IRB 6640 robotic arm with a spindle motor affixed to the end of the arm and the milling end tool used was a 16 mm diameter non-coated ball nose flute cutter. Dobrzanski et al. (2022) demonstrated the milling of material consisting of Cement (42.5 kg), fly ash/PFA (3.32 kg), Silica fume (3.64 kg), river sand (49.7 kg), BASF Master Glenium 51 superplasticiser (0.607 kg) and water (15.5 kg) by the robotic arm set-up.
Smart Dynamic Casting (SDC) (Figure 3C), developed at ETH Zurich from 2012 onwards, applies the construction technique of vertical slip forming to produce non-standard concrete elements using a robotic arm (Wangler et al., 2017). Rather than extruding horizontal layers, or depositing adhesive into a bed of powdered material, the method places fresh, wet concrete using an adjustable formwork casing, which rises vertically to form column elements of variable dimensions significantly larger than the formwork element itself.
The method requires powerful accelerating admixtures and precision timing so that the fresh concrete leaves the formwork in a solid enough state to resist deformation due to loading caused by subsequently deposited material in the upper portions of the column. However, the material must not become rigid too quickly to avoid cracking caused by friction against the vertically moving formwork.
A disadvantage of this approach is the geometrical and architectural constraints resulting from formwork design and motion capability. However, a notable advantage of removing layers is avoiding “cold joints” and concern over whether there is appropriate inter-layer bonding and cohesion.
The accelerators are reported as enabling a vertical building rate in the region of 1 m per hour. An accelerator used in the project development was BASF X-seed 100. Water/binder ratios were typically 0.25–0.30, and the superplasticiser was Glenium ACE 30 at 1.5% by weight of cement. Polyvinyl alcohol fibres were added at 1% volume of cement, and sand with particle sizes of less than 4 mm was added as 37% of the dry material constituents. Yield stresses begin at around 1 kPa at 45 min following mixing (Lloret-Fritschi, 2016).
The XtreeE team formed from researchers originally working on the DEMOCRITE project, a collaboration between the Paris-Malaquais School of Architecture, the Arts et Métiers ParisTech engineering school, the Conservatoire National des Arts et Métiers, INRIA Sophia Antipolis and the École Nationale Supérieure de Création Industrielle-Les Ateliers (XtreeE, 2021). The team developed an FDM-like technique, using a 6-axis industrial robot controlled by HAL Robotics software, enabling a geometrical complexity of printed structures for 3D printing (Schwartz, 2013). For example, the team printed a complex-shaped wall-element of dimensions 1.36 m
The premix for 3D printing consists of 30%–40% by weight (wt%) ordinary Portland cement CEM I, 40–50 wt% crystalline silica, 10 wt% silica fume and 10 wt% limestone filler. The water/(cement and sand) mass ratio is very small, only 0.1. Gripping polymer-based resin was added to improve the interface bonding between printed layers. An accelerating and thresholding agent was also added to achieve suitable rheology and a setting time for 3D printing (Gosselin et al., 2016). This 3D printing process had two steps; a mortar premix was first prepared and remained in a shearing mixer in order to avoid setting; the premix was then transferred using a peristaltic pump to a mixing screw located within the print head for printing.
ETH Zurich have also developed the mesh mould system and, subsequently, the Knit Candela project in collaboration with Zaha Hadid Architects. Mesh Mould was developed with a vision to unify formwork and reinforcement in a digital process. A mobile robotic arm bends, welds, and cuts steel reinforcement to additively manufacture a digitally designed mesh. This can take place either on-site or in a prefabricated/factory environment. The printed mesh is subsequently both in-filled with concrete and covered with concrete layers as an external finish, resulting in a structural element (Hack et al., 2017).
Mesh mould mixes featured high quantities of sand (particle sizes up to a maximum of 2 mm) in relation to other AM cementitious studies, with a sand/binder ratio of approximately 2.5:1 and a water/binder (CEM I) ratio of 0.6. Polymer fibres (RMH 182-4) were added to the mixes. The density of the mortars was approximately 2,100 kg/m3. Yield stresses of the fresh mixes from the spread flow tests were approximately 0.73 kPa with polymer fibres and 0.290 kPa without polymer fibres (Hack et al., 2017).
The Knit Candela system has created a five-tonne concrete “waffle” shell with a falsework-less formwork method, using a digitally designed and prefabricated knitted textile as a structural shuttering layer and a form-found cable net tensile structure which acts as the primary load-bearing formwork. On-site, the formwork was tensioned onto a timber and steel rig and coated with a cement paste consisting of a fast-acting accelerating admixture. The first coat of cement paste was 1 mm thick and was sprayed to stiffen the textile formwork and minimise deformation due to the deposition of subsequent layers of paste. Glass fibre-reinforced concrete was then applied manually in several layers to a thickness of 30 to - 40 mm (Popescu et al., 2021).
The cement paste used for the coating was a binary blend of calcium aluminate cement and hemihydrate, designed to harden rapidly once sprayed. The paste’s open time was 90 min at ambient temperature, after which rapid hardening took place. A progressive cavity mortar pump and an air compressor delivered the paste.
The project highlights the importance of limiting tensile forces within autonomously deposited cementitious material in AM applications. The digital design was based on low-strength concrete with a compressive strength of 20 MPa (ASTM C 39). The presence of glass-fibre reinforcement allowed a tensile strength of 4 MPa–6 MPa. No traditional steel bar reinforcement was used; therefore, the fibres were the sole reinforcing material present (Popescu et al., 2021).
The gantry frame approach was also adopted by the TU Eindhoven study (Figure 3D), with mix densities in the region of 2000 kg/m3 (Wolfs et al., 2018). Methods of reinforcing extruded concrete filaments were explored as a significant feature of this project. The entraining of a continuous steel cable within the extruded mortar was investigated as a reinforcing method, along with the use of short steel fibres. The nozzle of the printing device was expanded to incorporate a rotating spool feeding the reinforcement into the printing head, ensuring the reinforcing cable was fully integrated into the extruded concrete filament (Bos et al., 2018).
Materials initially trialled with this approach were 0.35 mm diameter nylon fishing line and 0.4 mm diameter steel wire. These were rejected as unsuitably thin and lacking in flexibility as the wires pulled out of the concrete material. More effective was the commercially available high-strength steel cable provided by Bekaert NV with reported tensile strengths of 500–2000 N. Mechanisms of failure under tensile loading of the material with entrained steel cable included cable breakage and pull-out from the material. Ductile failure of the cable is preferable to a sudden failure caused by pull-out attributed to debonding at the cable-cement interface (Bos et al., 2016; Bos et al., 2019).
The cementitious material was based upon CEM I with fine aggregate added as sand particles with a maximum particle size of 1 mm. Rheology-modifying admixtures were added as part of the fresh mix. 28-day compressive strengths achieved by the mixes were 30 MPa and 28-day tensile strengths were approximately 5 MPa. The nozzle was relatively large, measuring 40 mm × 10 mm. The exothermic hydration reaction between the cementitious binding materials and water was allowed to take place without the need to add chemical admixtures for retarding the reaction (Bos et al., 2016).
Multi-axis robotic arms are the main alternative to gantry frames in extrusion-based cementitious printing. Apis Cor, a company based in Boston, USA, has 3D printed a house in situ on location in Russia. The company is a strong advocate of in-situ printing over pre-fabrication, favouring the transport of an on-site printer compared to pre-fabricated components, which require assembling. The speed of construction was notable, with the 38 m2 of printed building area reported to have been completed in a 24-h period (Ghaffar et al., 2018). The company is a commercial operation, and precise cementitious mix details are not readily available in published literature.
A multiple-agent approach has been developed by Nanyang Technological University, with two robotic arms working simultaneously to print a single structure (Figure 3E). The robot arms each have six degrees of freedom and a reach of 1.74 m, and the object printed is longer than the reach of an individual robot arm. The robotic arms are on mobile bases, which allows them to be manoeuvred into position. However, while the robotic arms are extruding material, the bases must remain in position; therefore, each arm prints the area within its locality and the limit of its reach (Zhang et al., 2018).
Water/binder ratios are around 0.4, and sand/binder ratios are below 1.0. Silica fume was added along with pulverised fuel ash, sand and superplasticiser to the OPC binder. The material was extruded through a 10 mm diameter nozzle (Zhang et al., 2018).
The Chinese company WinSun Decoration Design Engineering have 3D-printed several high-profile projects, including single-story houses in high volumes, progressing to a five-story high building, reputed to be the tallest 3D-printed building in the world at the time of 2015 (Stampler, 2015).
This is not an in-situ approach - the company prints pre-fabricated components, which are then taken to the site and erected. Details of the deposition equipment and materials used are commercially sensitive and are not readily available in published literature. However, it has been reported that cementitious mixes contain glass reinforcing fibres (Ghaffar et al., 2018). When considering the size and height of the fabricated components, which have ranged up to 6 m high, 10 m wide and 40 m long, a large gantry-based method with an integrated robotic arm would be capable of delivering such a structure. Of note is the speed at which the buildings can be printed; for example, a 250 m2 3D printed office building was reportedly completed in only 17 days (Ghaffar et al., 2018; Hager et al., 2016).
Bio-inspired architectural design and geometric features, for example, examining the load-bearing structures to be found in living organisms, are an emerging area of development within additive manufacturing Aghaee et al. (2024). The 2K (Two-component) project, a collaboration between TU Wien, Austria, the Austrian Marshall Plan Foundation and Princeton University, US, examines bio-inspired cementitious additive manufacturing utilising interlocking mechanisms enabling modular designs of structures for which digital fabrication is suitable for the geometrically complex toolpaths, involving both rectilinear and curvilinear trajectories. Research to date introduces a “2-K″ robotic system that investigates the fabrication of interlocking suture and dovetail mechanism designs. Bio-inspired architectural design will inform continuing research, including the use of a Bouligand structure, which is a multi-layered and rotated microstructure featuring aligned fibers often found in natural materials and can promote the resistance of the material to crack propagation Daneshvar (2024).
Polymeric material investigations can involve layered extrusion or spraying. The use of polyurethane foam can serve in several ways, firstly as proof of concept, secondly as a demonstration of the deposition of material intended as insulation layers, and thirdly with the polymeric material acting in a structural capacity.
Selected polymeric investigations are summarised in Table 1 with Figure 4 showing different polymer-based systems for 3D-printing structures.
Figure 4. Salient AM in construction studies using polymeric materials. (A) 3D-printed Canal House project, the Netherlands, (B) Cable-suspended 3D-printing system, University of Laval, Quebec (Barnett and Gosselin, 2015), (C) Digital Construction platform, Steven Keating, Mediated Matter Group, MIT Media Lab, 2016, (D) Foam additive manufacturing, University of Nantes, France (ⓒ 2018 International Federation of Automatic Control. Reproduced with the permission of IFAC from Kévin Subrin, Thomas Bressac, Sébastien Garnier, Alexandre Ambiehl, Elodie Paquet, Benoit Furet, “Improvement of the mobile robot location dedicated for habitable house construction by 3D printing”. IFAC-PapersOnLine, 51/11, pp. 716-721.) (Subrin et al., 2018).
The 3D-printed Canal House project designed by DUS architects in Amsterdam (Figure 4A), the Netherlands, uses a biodegradable thermoplastic polypropylene (Hager et al., 2016) and the building was created by a 6 m high gantry frame 3D-printer known as the Kamermaker. The printer can produce polypropylene blocks measuring 2.2 m × 2.2 m x 3.5 m, which weigh 180 kg each (Buchanan and Gardner, 2019).
The created object was influenced by traditional Dutch canal houses and has been designed to be disassembled and reassembled in another location (Buchanan and Gardner, 2019). There is a concern, however, that the material used is too brittle as a structural material for horizontal spans in a larger building (Ghaffar et al., 2018).
A cable-suspended 3D-printing system developed by the University of Laval, Quebec, uses a single-component polyurethane foam with a density of 25 kg/m3 as a proof of concept material, with shaving foam serving as support material, each extruded from an adapted foam dispensing gun (Figure 4B). The shaving foam does not permanently bond with the polyurethane foam and can be easily removed with water once its purpose has been served. The cable-suspended robot has six degrees of freedom (Barnett and Gosselin, 2015).
The project team elected to use a light foam material, as concrete was deemed to be too heavy for a system where the robot is suspended in the air on cables working in tension. Additionally, fresh concrete presents the challenge of changing properties as the material hydrates. The foam was deposited in layers, and sufficient time had to pass for a layer to solidify before the subsequent layer was deposited. The method printed a 2.16 m tall statue (Barnett and Gosselin, 2015). However, a light foam with a density of only 25 kg/m3 cannot be considered a structural material; therefore, in a construction scenario, this method could only serve as a foam insulation deposition method.
A 3D-printing technique with similarities to FDM, named Big Area Additive Manufacturing (BAAM), was developed by Oak Ridge National Laboratory (Biswas et al., 2017; Duty et al., 2017; Compton et al., 2017). The ability to print a polymer component up to 6 m
Acrylonitrile butadiene styrene (ABS) and carbon fiber-reinforced ABS (CF-ABS) materials were used for BAAM. ABS printed components exhibited almost isotropic material properties, similar to injection moulded ABS, while for CF-ABS printed components, a high degree of anisotropy was observed, where the tensile strength (
As part of the research project known as Additive Manufacturing Integrated Energy (AMIE), the BAAM system was applied to print CF-ABS segments of a cylindrical building with a footprint of 19.5 m2 and a height of 2.8 m. The shape of all printed segments was half-rings. The half-ring segments were then combined into full rings to form the tension rod in the building. Overall, about 6,136 kg of CF-ABS material was used for printing over a time period of approximately 225 h (Biswas et al., 2017).
The Digital Construction platform developed by the Massachusetts Institute of Technology (MIT) features a compound robotic arm on a tracked mobile system. It consisted of a large hydraulic robotic arm with four degrees of freedom and a smaller electric robotic arm with six degrees of freedom, controlled using real-time environmental data (Figure 4C). The concept of the compound robotic system was that of a shoulder and hand, with the shoulder (hydraulic arm) for global positioning and the hand (electric arm) for fine-tuning and adjustments (Keating et al., 2017).
The study used a quick-setting, two-component, closed-cell polyurethane foam with a density of 28 kg/m3 and compressive strength of 0.16 MPa. The project fabricated a 14.6 m diameter, 3.7 m tall hemispherical dome. The purpose of the structure and the use of foam was to demonstrate the creation of formwork suitable for a proposed cast concrete structure rather than using the foam as a structural material in its own right (Keating et al., 2017). It is interesting to note that the project team considered aerial drones, but ultimately chose the robotic arm approach due to the higher payload possibilities. The investigation also preferred the greater flexibility of robotic arms rather than a gantry frame approach (Keating et al., 2017).
A method of 3D printing foam developed by the University of Nantes deposits two layers of foam material intended as external and internal insulation layers (Figure 4D). Wet structural concrete is then proceeded into the void between the two layers of foam; hence, the solidified foam insulation layers also serve as permanent formwork for the concrete (Subrin et al., 2018).
The foam, when deposited and exposed to the environment, expanded between 30–45 times its liquid volume, which clearly presents a challenge regarding the consistency of deposition and the height of the layers. With the light, high-expanding foam, printing speed is fast - a foam element measuring 1.75 m × 1.75 m x 2.5 m could be printed in 30 minutes (Subrin et al., 2018).
It is acknowledged, though, that the curing of the concrete between the foam layers would lead to potential issues with thermal cracking as the restrained fresh concrete, subjected to elevated temperatures, tends to expand. This may lead to challenges with the concrete pushing against the foam layers, potentially causing failure of the foam material. Equally, if the foam layer is strong and inflexible, without expansion joints, the concrete may crack.
Ground-based AM investigations can use a single deposition agent or multiple agents. It is the latter option of utilising multiple agents working in a coordinated manner, to which AAM can further contribute. When compared to conventional ground-based robots and manufacturing machines, UAVs have the advantage of being unrestricted in 3D space and being more capable of reaching remote locations, thus releasing each deposition agent from a ground-based envelope and design constraints.
Polyurethane foam is a thermosetting polymer consisting of two liquid components: a di-alcohol (e.g., polyol) resin and a di-isocyanate hardening agent featuring two isocyanate N=C=O-R groups. Initial design development for a miniature deposition device for AAM was considered, using high-expanding, low-density polyurethane foam liquid components. Ground-based polymeric material extrusion typically involves a commercially available foam material, which is extruded in a mixed-liquid component form before curing post-deposition. It was anticipated that with the mixed-liquid components, commercially available foam products would be suitable for AAM applications to both demonstrate proof of concept and serve as an option for insulation material using low-density foam and the scope to investigate high-density polyurethane foam as a potential structural material.
A wide range of bespoke, specially developed cementitious material mixes are employed for ground-based or tethered AM applications. It was envisaged that AM construction project material mixes published in literature might form the basis of AAM investigations, but AAM material mix development would ultimately have to deviate significantly.
Portland cement is one of the most manufactured materials in the world and is considered the premier inorganic binder for concrete in the construction industry. It is manufactured by firing limestone and clay at temperatures of approximately 1,450°C prior to grinding the resulting cooled clinker with gypsum to control setting. The clinker reacts with added water forming a paste that gradually stiffens as it hydrates, typically developing rigidity in a couple of hours (Banfill, 2006). Adding sand or other forms of fine aggregate to cement pastes creates mortar, and the addition of coarse aggregate or gravel makes concrete. Prior to achieving rigidity, in the first couple of hours following the addition of water, the cementitious material can be classified as being “fresh” (Banfill, 2006). The nature of the setting process is critical for AM.
AM techniques are capable of reducing the amounts of cementitious material required per project through innovative and efficient structural design and reduction in material wastage (Dams, 2020). The significant carbon footprint of concrete can be reduced further by using industrial by-products such as pulverised fuel ash and ground granulated blast-furnace slag to augment the use of Ordinary Portland Cement (OPC) in binder systems (Jiao et al., 2017).
Four main factors proposed by the authors including “workability”, “buildability”, and “open-time” along with “carryability” (Dams et al., 2023) will affect the performance of AAM and the quality of the printed products (shown in Figure 5). Carryability is dominated by the specification of the UAV, including its ability to deliver the power required to operate an onboard extrusion device and the payload capacity, which must include both the extrusion device and the material to be deposited. A greater capacity, in terms of power and payload, equates to more material deposited per flight. In addition, the ability to control the UAV’s trajectory and manipulation of the deposition nozzle will determine the accuracy and complexity of the printed structure. Workability describes the ability of the material to flow (liquid-like behaviour) through the deposition device, which is defined by the rheology. Buildability describes the ability of wet material (solid-like behaviour) to resist deformation under load or the extent to which layers can retain structure and support subsequent layers. Open-time can be defined as the period of time following mixing in which fresh properties remain consistent and the mix workable. This is especially important for thermosetting polymers and cementitious materials. Open-time is a key factor for AAM, since the mix must remain fresh for a sufficient time to allow for UAV loading, flight and deposition, with rapid hardening of material following extrusion being desired to mitigate deformation.
Figure 5. Four main factors - “carryability”, “workability”, “buildability” and “open-time” proposed by the authors that must be optimized to enable AAM.
With fresh cementitious mixes, there is a trade-off between workability and buildability for practical applications. Buildability is governed primarily by stiffness rather than strength (Bos et al., 2016). Both higher-slump, fast-curing concrete mixes and lower-slump, slower-curing mixes have been investigated previously. The latter approach has lower stiffness and lower initial strength, therefore reducing buildability, but with respect to layer adhesion, it can accommodate greater lateral deviation of nozzle extrusion. By maintaining workability and keeping the surface chemically active, it reduces sensitivity to time between layer depositions (Bos et al., 2016). The use of a superplasticiser in cementitious mixes can be desirable to reduce water/cement ratios, increase early age strength and maintain workability (Natanzi and McNally, 2020).
There are a range of additives used to enhance the mechanical properties and behaviour of additive manufacturing materials. The intention is to modify the material and increase or promote desired mechanical properties, whether improving strength or toughness, or enhancing workability or buildability. These can include metakaolin, micro-silica, granulated blast furnace slag and fly ash to supplement cementitious material, plus retarders, reinforcing fibres, aggregate and plasticisers. Some additives such as silica fume and silica flour can be added to improve strength, density which are important for the extruded material to retain shape following deposition, and workability, and other constituents such as viscosity modifying admixtures and plasticisers are added to improve the workability of the material, which is important while the fresh material is moving through the deposition system Dams et al. (2024). Nanoclay and viscosity modifying admixtures have emerged as important constituents to modify the rheological properties of materials. Nanoclay has been shown to improve significantly improve strength, stiffness, yield strength, and plastic viscosity. Alkali-activated cements are another option Zaid and El Ouni (2024). Calcium aluminate cements in conjunction with calcium sulphate can improve mechanical properties and induce a flash setting if a fast curing time following material deposition is required; however, care must be taken with the timing of the accelerated setting, so material does not cure while still within a deposition system, and curing is affected by environmental conditions and water temperatures Dams et al. (2023).
Figure 6 illustrates a diagram proposed by the authors to inform AAM cementitious material development. The diagram depicts constituents in accordance with the workability-buildability trade-off while also recognising that strength must also be considered, as an AAM cementitious material must remain structurally viable with a compressive strength suitable for construction. It was envisaged that adding rheologically-modifying admixtures with shear-thinning properties such as gums (for example, cellulose gum) would be a notable feature to both improve workability and promote buildability in the mix once deposited, thus minimising potential lateral deformation of an extruded filament due to the deposition of the subsequent layers.
Figure 6. A diagram showing the trade-off between workability and buildability, the constituents used in AM applications and additional constituents proposed for AAM structurally viable cementitious material, with a focus upon workability being of primary importance for a miniaturised deposition process.
Ground-based AM applications typically involve large construction-scale deposition equipment with metal parts. AAM would necessarily facilitate the miniaturisation of the deposition process, as each UAV would have to be able to power both itself in flight and carry the deposition device. Therefore, a prime approach for AAM would be that cementitious material must be more lightweight than that used for ground-based applications, with a higher water/binder ratio and the use of additives with more rounded particles such as PFA to aid workability. Mixes would need to be deposited using less energy than ground-based applications.
In the life-cycle analysis of materials for additive manufactured construction, both cementitious and polymeric options offer distinct advantages and challenges, especially regarding sustainability and recyclability. Cementitious materials, such as concrete and geopolymer cements, are known for their durability and excellent compressive strength, which contribute to a long service life with minimal maintenance. However, traditional cement production is highly energy-intensive and responsible for substantial CO2 emissions, especially from Portland cement Thiel et al. (2024). To address this, low-carbon alternatives like geopolymer cements and blended cements incorporating fly ash or slag have been developed, lowering embodied carbon and reducing the overall environmental footprint over the structure’s lifecycle Luhar et al. (2020) Despite these advances, end-of-life processing for cementitious materials typically involves downcycling, where demolished concrete is crushed and reused as aggregate. This approach, while beneficial for reducing waste, often results in lower-quality material compared to virgin aggregates, which limits its application in high-strength construction projects. Some research is now focusing on chemical recycling methods that could potentially recover cementitious binders for reuse, although this technology is still emerging.
Polymeric materials, often used in 3D-printed construction for non-structural components, have the advantage of lower initial production emissions, particularly when bio-based or recycled polymers are used. Bio-based polymers, such as PLA derived from corn starch, offer lower carbon footprints than traditional petrochemical-based polymers and can sometimes achieve similar performance. Recycled polymers also contribute to reduced embodied carbon but may degrade in quality with each recycling cycle, limiting their reuse potential Bedarf et al. (2021). Polymers generally lack the long-term durability and resilience of cementitious materials, especially in outdoor or structural applications, due to susceptibility to UV degradation, chemical exposure, and mechanical wear. Emerging solutions, such as UV-stabilized polymers and protective coatings, are being developed to improve polymer durability. Additionally, while thermoplastics like ABS are recyclable, their material properties can weaken over time, and thermosetting polymers, which provide added strength, are chemically fixed and thus challenging to recycle. Innovations in chemical recycling—breaking down polymers into their original monomers—show promise but are currently energy-intensive and not widely implemented.
Beyond individual material properties, both cementitious and polymeric materials are evolving through hybrid and bio-based innovations. Bio-concretes that incorporate bacteria for self-healing, or waste-derived additives like biochar, are advancing sustainable cementitious options that prioritize longevity and minimize waste. Hybrid bio-polymer composites that integrate natural fibers, such as hemp or flax, also show potential for creating durable, partially biodegradable materials, aligning with circular economy goals.
Building construction using additive manufacturing (AM) technology faces several significant limitations that currently restrict its broader application. One primary challenge is material limitations, as many 3D-printable materials, especially polymers and certain cementitious compounds, lack the structural strength and durability of traditional materials like reinforced concrete or steel, limiting their use in large-scale, load-bearing (Buswell et al., 2018). Issues like UV degradation and limited resilience to extreme weather can affect the longevity of printed structures. Additionally, size constraints and equipment limitations mean that many 3D printers are restricted to producing small or modular components, which then require assembly, increasing labor and potentially compromising structural integrity. Quality control is also a challenge, as maintaining consistent layer adhesion and precise material curing is difficult, which can lead to weaknesses or defects not as easily detectable as in traditional construction (Asprone et al., 2018).
Beyond materials and equipment, regulatory barriers also play a role, as design and structural codes have yet to adapt to AM’s unique properties and capabilities, limiting certification for safety and compliance and restricting certain architectural designs (Bos et al., 2016). Lastly, economic factors like high initial costs for equipment and specialized materials, along with supply chain challenges, contribute to scalability issues, while environmental concerns around the energy consumption of 3D printing processes and difficulties in recycling specialized materials further complicate AM’s eco-friendly potential. Despite these barriers, ongoing advancements in materials, printing technologies, and regulatory frameworks are steadily improving the feasibility and sustainability of 3D printing in construction.
Aerial Additive Manufacturing (AAM) is able to bring multi-agent aerial mobility to additive manufacturing in the construction industry, aiming to create or repair structures in challenging environments, such as working at height and post-disaster reconstruction. AAM involves coordinated unmanned aerial vehicles (UAVs, also known as “drones”) carrying lightweight deposition devices, extruding material through a nozzle while in-flight (Dams et al., 2020; Dams et al., 2023). An aerial deposition approach ultimately significantly differs from ground-based AM applications since it requires lower-density mixes and miniaturised, lighter deposition devices for UAV carriage.
This section introduces a brief history of UAV use and design and discusses their current development within the construction industry. It also reviews the recent development of UAV-compatible deposition devices that can successfully deposition polymeric or cementitious materials during flight.
UAVs, often referred to as “drones” or “aerial robots”, can be defined as aircraft flown with no pilot present on board (Chen et al., 2016). UAV development has existed since the 1950s, initially developing unmanned aerial torpedoes for military purposes, with the second definition above differentiating UAVs from non-reusable cruise missiles, which were developed in tandem. There are three UAV use classifications:
•(1) Pilot-less target craft used for training purposes;
•(2) Combat air vehicles designed for lethal military strikes.
•(3) Reconnaissance aircraft designed to gather data for surveillance and inspection purposes (Keane and Carr, 2013). The third category, which can apply to non-military use, is relevant to this review.
Commercially, four categories of UAV hardware design are available:
•Fixed wing.
•Fixed wing hybrid.
•Single rotor.
•Multiple rotor.
The most common multiple rotor design is the four-rotor-blade quadcopter, although designs can feature six or eight rotary blades (Babel, 2015), which increase lift capacity. Fixed-wing aircraft can carry larger payloads and can fly at higher altitudes, but multi-rotor designs possess greater agility and greater fault tolerance (Chen et al., 2016). Figure 7 shows images of fixed wing and rotary wing UAVs.
Civilian UAV use has become established in a variety of sectors, including agriculture, mining (for post-blast surveying), aerial photography and filming, journalistic data gathering and cartography (Babel, 2015), in addition to personal leisure use. Multiple applications can be categorised under the heading of “payload delivery”, which involves the use of UAVs delivering materials in solid, liquid or gaseous form in manners and locations which can be difficult for humans to operate in a safe or competitive manner, for example, chemical crop-spraying in the agricultural sector (Feron and Johnson, 2008). The utilisation of UAVs in the construction sector has also recently increased; however, this primarily concerns surveillance, safety inspection work and data gathering for 3D modelling (Ghaffar et al., 2018). It is worth mentioning that several material-spraying UAVs for construction were reported and demonstrated (Murison, 2023; Block, 2023; Choi, 2017), despite not being directly relevant to AAM for construction.
In order to meet the requirement of AAM, Kovač’s group introduced a custom-developed manipulator for tool-tip stabilisation, with the capability of extruding polyurethane foam in-situ (Hunt et al., 2014; Sareh et al., 2017; Chermprayong et al., 2019). Since AAM requires a high degree of agility, coupled with tight tolerances for lateral position, a quadcopter multi-rotor was identified as the most suitable solution. This design was large enough to carry the envisaged payloads (shown in Figure 8A). In addition, the new aerial robot system integrated a lightweight Delta manipulator in order to improve accuracy when interacting with the infrastructure (Chermprayong et al., 2019). A DJI Matrice 100 (M100), with a maximum takeoff weight of 3.6 kg, was used as the quadrotor platform. The Delta manipulator, which has three identical limbs and uses only revolute joints, is capable of 3 degrees of freedom in pure translational motion. The system also integrated onboard visual-inertial odometry-aided navigation, enabling the UAV to perform under various operational conditions, such as hovering in windy conditions. Recently, Kovač’s group has developed BuilDrones for depositing materials during flight (Zhang et al., 2022) (shown in Figures 8B, C). The BuilDrones were equipped with a dynamically self-aligning delta manipulator, which could improve the manufacturing accuracy by up to 5 mm so as to print complex geometry with precise trajectory requirements (Zhang et al., 2022). The same group has done further developments on a high-payload compact co-axial hexacopter Orr et al. (2021) to increase the payload capacity and flight endurance even more, and the first offshore inspection is demonstrated (Kocer et al., 2022).
Figure 8. (A) Aerial 3D printer, quadcopter with integrated foam printing module in an orientation ready for printing developed by Kovač’s group (Hunt et al., 2014) (B, C) BuilDrones (Zhang et al., 2022) equipped with an error-compensating delta manipulator which provides stabilisation to the nozzle, developed by Kovač’s group and printing a peano curve trajectory, (D) 3D printing hexacopter (Nettekoven and Topcu, 2021), (E) 3D printing asphalt UAV (Eskandari Torbaghan et al., 2020).
As another example first shown in TCT Asia 2018, a Chinese 3D printer manufacturer, DediBot, developed a UAV called Fly Elephant, being equipped with a Delta-like printer on the bottom (Co, 2021; Koslow, 2018). Details about Fly Elephant are limited due to commercial confidentiality. An important difference between the Fly Elephant and Kovač’s is that the Fly Elephant has an umbilical cord attached to the top of the drone, which supplies power and material to be printed. Although this negates the need for batteries to reduce payload weight and the need to re-load material, it restricts the freedom of movement by being tethered to the ground. Furthermore, restrictions of tethered flight can be identified and are summarised below:
•Strictly restricts the task parallelisation by causing trajectory problems.
•Significant reduction of the building envelope since the longer the tether is, the heavier it becomes, and the UAVs’ ability to carry it is compromised.
•Tethers affect the flight dynamics of the UAV due to changing the centre of gravity of the platform.
Recently, Nettekoven et al. developed a 3D printing hexacopter for AM (illustrated in Figure 8D), which consists of a DJI F550 ready-to-fly UAV, FDM 3D printing equipment, flight electronics and batteries (Efraim et al., 2015). The customized motors were mounted on 3D printed mounts with a dihedral angle of 8%. This angle is helpful to increase the UAV’s stability and to reduce vibrations caused by the complex airflow between the propellers and ground (Nettekoven and Topcu, 2021).
Aiming to fill in cracks and potholes on roads autonomously, the infrastructure robotics project “Self-Repairing Cities” has contributed to the development of a hybrid aerial–ground Asphalt 3D Printing UAV (Smith, 2018; Eskandari Torbaghan et al., 2020; Doychinov et al., 2019). The UAV used was a modified DJI M600 Pro hexrotor, which consists of six motors, six batteries (6 × 3.7 V 100 mAh lithium polymer), three inertial measurement units and three global positioning systems (GPS) (Figure 8E). It has a payload capacity of 6.5 kg and approximately 20 min of flight time with a full payload. An asphalt extruder was integrated with the UAV. It is noteworthy that the 3D printing process was initiated once the UAV had landed, which negates the need to hover during printing; this removes the possibility of propeller downwash affecting extruded fresh material, but the landing process results in the following points:
•The print canvas is the envelope of the printer which is carried.
•Printing occurs once landing has taken place, with vulnerability to potentially difficult terrain conditions.
Fused Deposition Modelling (FDM) is a suitable principle for AAM. The feasibility of UAV 3D extrusion-printing polyurethane foam during controlled flight has been demonstrated (Hunt et al., 2014). In order to investigate liquid-like polymer and cementitious mortars and pastes suitable for AAM, a deposition device was designed by Kovač’s group. A 60 mL cartridge design accommodating two cartridges was developed specifically for systems requiring two liquid-based components such as polyurethane (Dams et al., 2020). However, this system could also function using one cartridge for the extrusion of cementitious materials (Dams et al., 2018b). The deposition device used a powered descending plunger to push the material out of the cartridge (Dams, 2020). Considering the payload of a typical flying UAV, the total mass of the device, when full of material, was within the 1 kg payload limit. 60 mL cartridges were considered to have a practical capacity of 50 mL due to modifications of the cartridge side to allow re-filling by injection of material through a hole. In the recent research paper published in Nature, a cartridge was used to have a theoretical maximum volume of 310 mL with a practical volume of 202 mL to allow for the insertion of a tapered component at the base of the cartridge and the plunger (Zhang et al., 2022). A smart servo motor actuated the extrusion, while the worm drive was adopted for power transmission and converting the rotary to linear motion so that the plunger could push the material out of the material cartridge (Zhang et al., 2022).
Hunt et al. covered an initial, preliminary phase of material experimentation and demonstrated the feasibility of low-density polyurethane foam for AAM by spraying mixed foam material from a UAV during a flight onto a spherical inflatable formwork (Hunt et al., 2014).
Dams et al. investigated the structural potential of three commercially available expanding polyurethane foams of varying density (i.e., LD40, Reprocell 300 and Reprocell 500) and their feasibility for deposition using an autonomous flying dual-syringe device (Dams et al., 2020). All three foams were successfully drawn up, mixed and deposited by a single-motor dual-syringe deposition device. They found that Reprocell 500 high-density foams showed compressive strengths exceeding 30 MPa, comparable to those of concrete, and flexural strengths similar to the lower range of timber, which demonstrated its potential to be used as a structural material. By applying approximately twice as much power and energy, the syringe device was capable of depositing material with a density over ten times higher. Properties of polyurethane foam, such as low weight and high volume due to expansion, further suggest its suitability for AAM.
In order to tackle the lateral deformation challenge, Dams et al. further investigated the ability of micro-particles to increase the viscosity of fresh polyurethane foam while still in a liquid state (Dams et al., 2018b). The addition of glasscell (rounded particles), silicell (sub-angular to angular particles) and treecell (elongated fibres) to Reprocell 500 foam was investigated. When the liquid components of Reprocell 500, combined with the micro-particles, were deposited on to a free surface using the dual-syringe deposition device, an unexpected expansion was observed. The micro-particles exhibited accelerating properties, which resulted in a subsequent reduction in foam density. The exothermic reaction even took longer to occur compared to hand-mixing in a container. The AAM project carried out the printing of a metre-high polyurethane foam cylindrical structure using an untethered, self-powered flying UAV, as shown in Figure 9C (Zhang et al., 2022).
Figure 9. (A,B): A 6-m-tall block tower assembled by two UAVs (Augugliaro et al., 2014) (C) The cylindrical foam structure printed by the “Buildrone” of the Aerial Additive Manufacturing project (Zhang et al., 2022). (D) Three trajectory designs for a cementitious wall, left to right: a rounded “peano curve” design, adjacent parallel printed filaments and a hybrid design featuring alternate layers or the peano curve design and parallel filaments.
Based on the above results, it is reasoned that future investigations concerning high-density polyurethane foams could center upon either foaming retardation or the temporary 3D-printed supporting material. The addition of chemical catalytic agents to increase the mix liquid temperature and accelerate the exothermic reaction could lead to earlier solidification and foaming retardation.
Dams et al. first investigated a workable cement paste mix suitable for a miniature autonomous deposition device, combining the variables of water/cement (w/c) ratio and superplasticiser % by weight (wt.) of cement (Dams et al., 2017; Dams et al., 2018b). CEM I Portland cement with a particle size of 5–30
Preliminary trial mixes highlighted an issue with constituent segregation in mixes designed with buildability considerations as a priority. Mixes with levels of fine aggregate >1:1 were prone to segregation whilst inside the cartridge, resulting in zones of compacted fine aggregate around the cartridge base. This resulted in the material possessing a disproportionately high water content when passing through the nozzle, leading to a detrimental effect on buildability. Cementitious mixes using constituents such as angular-particle sand, silica fume and LimeX were trialled to assess the buildability of the material and the ability to be printed in multiple layers from a miniature deposition device (Dams et al., 2023).
To enhance cohesion and stability within the open-time of cementitious-based fresh mixes, an approach of developing a pseudoplastic composite material with the addition of polymeric rheology modifying admixtures (RMA) is under investigation by Dams et al. (2020), Dams et al. (2018a), Dams et al. (2021). To modify the rheology of the mix, foaming agents, silicone oil and hydrocolloids are all under investigation as RMAs, both in isolation and combination, to assess potential synergistic effects. For example, hydroxyethyl methyl cellulose (HEMC), a synthetic hygroscopic compound chemically derived from cellulose, along with hydroxypropyl methyl cellulose (HPMC) can be used as RMA to slow the nucleation of calcium silicates and further retard hydration (Zhang et al., 2022). Xanthan gum, a hydrophilic native bio-polysaccharide, can also be used as RMA. It affects the viscosity by adsorbing onto cement particles, therefore increasing the inter-particle attraction. Moreover, the rigid molecules of xanthan gum can provide sufficient buildability in mortars without the requirement for fine aggregate (Zhang et al., 2022). As shown in Figure 9D.
Dams et al. investigated the addition of fibres as a reinforcement to the cement-based matrix, aiming to increase the ductility of the material, reduce crack propagation and improve tensile capacity (Dams, 2020; Dams et al., 2018a; Dams et al., 2019). Synthetic polyvinyl alcohol (PVA), polypropylene (PP), alkali-resistant glass (ARG), Aramid and Kevlar fibres, along with natural banana fibres, were investigated to evaluate contributions to the workability, buildability, mechanical strength and failure mechanisms of the cementitious composite material (Figures 10A, B). In the first attempt, mortar with a 0.08% PVA fibre volume content was found to be the most suitable mix for the AAM deposition system (Dams et al., 2018a). It possessed an appropriate balance between workability and buildability, with a competitive flexural strength of 7 MPa and compressive strength above 40 MPa.
Figure 10. (A, B) Buildability tests with four fresh circular layers extruded by the powered deposition device for each mix shown (Dams et al., 2018a; Dams et al., 2019). (C) Macro (left) and SEM (center, right) micro images of cement-fibre composites containing PVA, aramid, Kevlar and banana fibres (Dams et al., 2019).
Following the above study, pastes containing 0.75% volume PVA and Kevlar fibres were also shown to possess a suitable balance between workability and buildability, being competitive in mechanical tests and possessing sufficient workability for the deposition device (Dams et al., 2019) [152]. However, banana fibres at 0.35% volume showed greater layer deformation. Mixes with 0.35% or 0.75% volume Aramid fibres became stiff; thus, they possessed poor workability. This is also true for the 0.75% volume banana fibres, as Aramid and Banana fibre mixes could not be processed at 0.75% volume due to the limitation of the deposition device. Thus, it could be concluded that Aramid and banana fibres were unsuitable for miniaturised AAM, despite the fact that they provided the highest flexural strengths and most ductile failures in the 7-day and 28-day compressive and flexural tests. In addition, as shown in Figure 10C, rupture can be seen with Aramid and banana fibres. PVA fibres were observed to fail by pull-out, which is characterized by a smooth, unbroken fibre-end. This may be due to the high tensile capacity rather than the inadequacy of molecular bonding or mechanical anchorage.
Apart from workability and buildability, open time is also a key parameter for AAM, as the mix must remain in the fresh liquid state for a period of time to allow for UAV loading, flight and deposition. Once deposited, however, rapid hardening of material is desirable to mitigate against deformation. Rheological properties and hydration times are key parameters which enable successful printing. Calcium aluminate cement (CAC) and calcium sulphate (CS) are an option as additives for AAM due to their ability to increase early strength and promote hydration (Dams, 2020).
Cementitious mixes featuring nano-particles have also been investigated for AAM. Chen et al. examined the addition of inorganic fullerene tungsten disulfide IF-
Microscopy revealed that a cured matrix with IF-
In summary, OPC-based cementitious pastes and mortars are an option for AAM. Additive and admixture options, along with the justification for inclusion and the characteristics they introduce to the mix (buildability or workability), are summarized in Table 2. OPC forms the basis of the binder and is augmented by PFA to aid workability and minimise carbon footprint. Fibres are suitable for AAM, improving buildability while not prohibitively impeding workability and promoting flexural ductility. The introduction of an accelerating agent would reduce the mix’s open time.
Table 2. List of constituents in addition to CEM I for consideration in AAM cementitious materials, with the material characteristics and purposes concerning properties [Kaščak et al., 2021].
UAVs can operate dynamically in space, so their use opens up entirely new possibilities for AM in architecture. As an early investigation, two research groups from ETH Zurich collaborated to create the first experimental architecture in 2012, called Flight Assembled Architecture, resulting in a 6 m tall, 1500-module tower (shown in Figures 9A, B) (Willmann et al., 2012). A fleet of UAVs dynamically assembled the tower. This research “makes empty airspace tangible to the designer” (Willmann et al., 2012; Augugliaro et al., 2014), especially in the field of UAV trajectory design. A cylindrical tower was built using polyurethane foam sprayed from untethered UAVs in self-powered flight as shown in Figure 9C (Zhang et al., 2022).
Which trajectory design is favourable for AAM? Designs for AAM need to be informed by the following considerations (Dams, 2020):
•The lateral precision of the UAV during flight.
•The desire to create a lightweight, efficient and aesthetic design.
•The extent to which an extruded bead of material would deflect while spanning voids in the previously deposited layer.
•The extent to which an extruded bead of material might settle when under compressive loading from subsequently deposited layers.
•Geometric properties of the nozzle - dimensions and shape - circular or rectangular.
•The effect of layer design and orientation on the potential for anisotropy in printed materials
Zhang et al. (2022), explored differing trajectory designs and nozzle shapes. A crucial consideration for nozzle shape is the ability, or precision, of a flying UAV to be able to rotate about its own axis. Extrusion thus far with flying UAVs has used a circular nozzle, although lateral stability of untethered UAV deposition is an area of ongoing activity, and there are advantages of using a rectangular nozzle over a circular one, most notably the deposition of filaments with a greater width in respect to height, allowing for greater contact area between layers and promoting layer adhesion while minimising effects of lateral instability or imprecision. Using a circular nozzle, three trajectory designs for printing a wall with cementitious material were explored as shown in Figure 9D (Zhang et al., 2022):
•A rounded “peano curve” design.
•Multiple adjacent parallel filaments.
•A hybrid design featuring alternate layers or the peano curve design and parallel filaments.
Parameters to be further examined are both the compressive strength of extruded designs and the quantity of material used in the extrusion. It was found that the hybrid design possessed a good combination of material use, with less material extruded than for a parallel filament wall, but also has the advantage of alternating layers of allowing for lateral imprecision of trajectory deposition (Zhang et al., 2022). As the lateral and rotational stability of flying untethered UAVs improves further, future research may focus on upscaling with deposition using a rectangular nozzle to further improve layer adhesion and strength and increase wall width with each UAV extrusion.
Anisotropy is an important issue in additive manufacturing materials. Anisotropic properties may be influenced by the orientation of layers, printing process, curing conditions and porosity. A layered additive manufacturing method may result in anisotropic properties in the deposited material, with printed material exhibiting differing strengths and stiffnesses based on the orientation of the load relative to the print layers. Layer orientation affects material properties, with the deposited material being stronger in the direction parallel to the layers but weaker perpendicular to the layer direction. Potentially weaker locations at interface boundaries where extruded layers meet can promote failure caused by internal stresses Zaid and El Ouni (2024).
A developing field of research regarding anisotropic properties is microlattices, looking at customising and optimising the dimensions of a lattice structure to create lightweight material with optimised mechanical properties for additive manufacturing Li et al. (2024).
A further developing field of research is using modelling to understand and predict the anisotropic properties of additive manufacturing materials. Baktheer and Classens conducted a review of numerical modelling regarding anisotropic properties in cured 3D printed concrete. Modelling methods have three main categories - macro-scale phenomenological continuum models which uses an anisotropic damage smeared method, macro-scale interface-based models, which explicitly account for the behaviour of the interfacial between printed layers and detailed meso-scale discrete models, which look at the inherent heterogeneity of concrete. The developing techniques consider pore structure and orientation, interlayer bond strength, moisture distribution and drying effects with the associated stresses, cyclic loading and fatigue behaviour and fluid transportation Baktheer and Classen (2024).
The current state of AM in construction from ground-based to aerial processes has been reviewed, including representative ground-based AM research projects for cementitious and polymeric materials. These projects mainly involve large ground-based, fixed-position approaches, such as frames, rotating compound arm systems, robotic frames moving upon dual rails, or the use of autonomous mobile coordinated, grounded robots using simultaneous localization and mapping algorithms.
When considering AAM, the four main factors—“carryability”, “workability”, “buildability”, and “open-time”—were introduced as key material properties that must be carefully controlled to enable effective printing. Exploring natural fillers like hemp, flax, and industrial byproducts such as fly ash, slag, and rice husk ash offers a way to substitute traditional materials, thereby lowering carbon emissions while improving strength and flexibility. Hybrid material compositions, where bio-based fillers are combined with conventional cementitious or polymeric matrices, can create materials that balance durability, flexibility, and biodegradability, opening possibilities for novel 3D-printed structures that are lighter and stronger.
An overview of UAVs and recent developments in aerial 3D printer materials and trajectories was reviewed, with a focus on material development. High-density polyurethane foam has significant structural potential for AAM if temporary supporting material is used to act as containing formwork. Foam can also serve as an insulating element in a composite system or as temporary support for fresh extruded cement layers. In terms of cementitious materials, cement mixes exhibit greater suitability in the fresh state for AAM compared to thermoset polymer resin. These mixes need to be combined with appropriate additives and admixtures and suitable water/cement ratios to achieve a suitable balance between workability and buildability.
Further development of deposition devices would support AAM materials research to enable stiffer, denser mixes to be extruded and the upscaling of deposited filaments. Developments such as increasing the size of the cartridge and the ability to generate greater plunger forces by changing to an auger design would enable larger quantities of stiffer materials to be deposited. As the rotational stability of deposition agents improves, nozzle dimensions and the use of rectangular nozzles can be further developed.
Investigation of interfacial layer-to-layer adhesion of 3D-printed material could lead to improved mechanical properties. Characterization using techniques such as micro-computed tomography (Micro-CT), and flexural, tensile, and pull-off strength tests are common approaches. The shrinkage, including both plastic and drying of cured layered specimens and crack propagation, should also be investigated using fracture mechanics theory, such as Griffith’s criterion and fracture energy tests. Environmental testing under simulated conditions—such as extreme temperatures, UV radiation, humidity, and chemical pollutants—is crucial to understand the long-term durability and resilience of AM materials, particularly polymers that may degrade under harsh weather conditions.
Reinforcement in AM construction is also important. Incorporating nanoparticles like nano-clay, nano-silica, graphene, and carbon nanotubes can significantly enhance tensile strength and reduce shrinkage in both polymeric and cementitious materials, contributing to improved mechanical performance of printed structures. Fibrous content, as a substitute for traditional steel rebar and as a method of addressing shrinkage and cracking, is a subject of ongoing work throughout all AM cementitious research projects. Fibers such as carbon should also be trialed in fresh mixes. The incorporation of conductive nanoparticles opens the possibility of creating ‘smart’ construction materials that can monitor structural health or adapt to environmental changes, leading to more resilient and adaptive AM structures.
Investigation of other potential additives or admixtures, such as nano-clay for AAM, has been shown to reduce open-time and improve cohesion, stability, and increase viscosity Rubio et al. (2017). Other additives, such as graphene and carbon nanotubes, may also be considered to expand the functionality of 3D-printed components.
Life-cycle assessments or the application of multi-criteria analysis methods should be applied to these novel cementitious pastes to assess the long-term environmental impacts of AAM materials (Maskell et al., 2018). Exploring natural fillers and hybrid materials contributes to sustainability goals, ensuring that advancements in AM support environmentally friendly construction practices.
Future research in additive manufacturing materials for construction offers numerous exciting avenues that could reshape the industry’s sustainability and performance. Ongoing research into innovative materials and technologies is vital to push the boundaries of additive manufacturing in construction, enabling the creation of sustainable, resilient, and high-performance structures.
BD: Conceptualization, methodology, software, validation, formal analysis, investigation, resources, data curation, writing–original draft, writing–review and editing, visualization, project administration. BC: Conceptualization, methodology, software, validation, formal analysis, investigation, resources, data curation, writing–original draftt, writing–review and editing, visualization. YK: Conceptualization, methodology, software, validation, formal analysis, investigation, resources, data curation, writing–original draft, writing–review and editing, visualization. PS: Conceptualization, methodology, software, validation, resources, writing–review and editing, supervision, project administration, funding acquisition. MK: Conceptualization, methodology, software, validation, resources, writing–review and editing, supervision, project administration, funding acquisition. RJB: Conceptualization, methodology, software, validation, resources, writing–review and editing, supervision, project administration, funding acquisition.
The author(s) declare that financial support was received for the research, authorship, and/or publication of this article. The Aerial Additive Manufacturing project is funded by the Engineering and Physical Sciences Research Council (EPSRC) (grant number EP/N018494/1). The project was supported by the Royal Woolfson Society (fellowship grant number RSWF/R1/18003). Further support was provided by the EPSRC Centre for Decarbonisation of the Built Environment (dCarb) (grant number EP/L016869/1).
The authors express thanks to the Aerial Robotics Laboratory at Imperial College, London, United Kingdom the laboratory of Sustainability Robotics at Empa, Switzerland and the technical support of the Department of Architecture and Civil Engineering laboratories, University of Bath, United Kingdom.
The authors declare that the research was conducted in the absence of any commercial or financial relationships that could be construed as a potential conflict of interest.
The author(s) declared that they were an editorial board member of Frontiers, at the time of submission. This had no impact on the peer review process and the final decision.
All claims expressed in this article are solely those of the authors and do not necessarily represent those of their affiliated organizations, or those of the publisher, the editors and the reviewers. Any product that may be evaluated in this article, or claim that may be made by its manufacturer, is not guaranteed or endorsed by the publisher.
AAM, Aerial Additive Manufacturing; AM, Additive Manufacturing; CAC, Calcium Aluminate Cement; CS, Calcium Sulphate; CNT, Carbon nanotubes; CSA, Calcium Sulphoaluminate; DOF, Degrees of Freedom; FDM, Fused Deposition Modelling; GNP, Graphene nanoplates; GO, Graphene Oxide; HEMC, Hydroxyethyl methyl cellulose; HPMC, Hydroxypropyl methyl cellulose; MKPC, Magnesium Potassium Phosphate Cement; NGP, Nano-graphite Platelets; OPC, Ordinary Portland Cement; PFA, Pulverised Fuel Ash (fly ash); PP, Polypropylene; PVA, Polyvinyl Alcohol; RMA, Rheological Modifying Admixture; SCM, Supplementary Cementitious Materials; SDC, Smart Dynamic Casting; RMC, Reactive Magnesium oxide Cement; UAV, Unmanned Aerial Vehicle.
Aghaee, K., Li, L., Roshan, A., and Namakiaraghi, P. (2024). Additive manufacturing evolution in construction: from individual terrestrial to collective, aerial, and extraterrestrial applications. J. Build. Eng. 110389. doi:10.1016/j.jobe.2024.110389
Aghaei-Meibodi, M., Bernhard, M., Jipa, A., and Dillenburger, B. (2017). The smart takes from the strong. Fabr. Rethink. Des. Constr. 3, 210–217. doi:10.2307/j.ctt1n7qkg7.33
Akasheh, F., and Aglan, H. (2019). Fracture toughness enhancement of carbon fiber–reinforced polymer composites utilizing additive manufacturing fabrication. J. Elastomers and Plastics 51, 698–711. doi:10.1177/0095244318817867
Alghamdi, H., Nair, S. A., and Neithalath, N. (2019). Insights into material design, extrusion rheology, and properties of 3d-printable alkali-activated fly ash-based binders. Mater. Des. 167, 107634. doi:10.1016/j.matdes.2019.107634
Archez, J., Texier-Mandoki, N., Bourbon, X., Caron, J., and Rossignol, S. (2021). Shaping of geopolymer composites by 3d printing. J. Build. Eng. 34, 101894. doi:10.1016/j.jobe.2020.101894
Arunothayan, A. R., Nematollahi, B., Ranade, R., Bong, S. H., and Sanjayan, J. (2020). Development of 3d-printable ultra-high performance fiber-reinforced concrete for digital construction. Constr. Build. Mater. 257, 119546. doi:10.1016/j.conbuildmat.2020.119546
Asprone, D., Auricchio, F., Menna, C., and Mercuri, V. (2018). 3D printing of reinforced concrete elements: Technology and design approach. Constr. Build. Mater. 165, 218–231.
ASTM (2012). Standard terminology for additive manufacturing technologies, F2792-12a. Pennsylvania: ASTM International, 1–9.
Augugliaro, F., Lupashin, S., Hamer, M., Male, C., Hehn, M., Mueller, M. W., et al. (2014). The flight assembled architecture installation: cooperative construction with flying machines. IEEE Control Syst. 34, 46–64. doi:10.1109/MCS.2014.2320359
Babel, J. (2015). Up in the air: the emerging issue of drones in the construction industry. XL Catlin Constr. Insid. 5, 2015.
Baktheer, A., and Classen, M. (2024). A review of recent trends and challenges in numerical modeling of the anisotropic behavior of hardened 3d printed concrete. Addit. Manuf. 89, 104309. doi:10.1016/j.addma.2024.104309
Banfill, P. (2006). The rheology of fresh cement and concrete-rheology review. Bull. - Br. Soc. Rheol. 61, 130.
Barnett, E., and Gosselin, C. (2015). Weak support material techniques for alternative additive manufacturing materials. Addit. Manuf. 8, 95–104. doi:10.1016/j.addma.2015.06.002
Bedarf, P., Dutto, A., Zanini, M., and Dillenburger, B. (2021). Foam 3d printing for construction: a review of applications, materials, and processes. Automation Constr. 130, 103861. doi:10.1016/j.autcon.2021.103861
Biswas, K., Rose, J., Eikevik, L., Guerguis, M., Enquist, P., Lee, B., et al. (2017). Additive manufacturing integrated energy—enabling innovative solutions for buildings of the future. J. Sol. Energy Eng. 139, 015001. doi:10.1115/1.4034980
Bong, S. H., Xia, M., Nematollahi, B., and Shi, C. (2021). Ambient temperature cured ‘just-add-water’geopolymer for 3d concrete printing applications. Cem. Concr. Compos. 121, 104060. doi:10.1016/j.cemconcomp.2021.104060
Bos, F., Wolfs, R., Ahmed, Z., and Salet, T. (2016). Additive manufacturing of concrete in construction: potentials and challenges of 3d concrete printing. Virtual Phys. Prototyp. 11, 209–225. doi:10.1080/17452759.2016.1209867
Bos, F., Bosco, E., and Salet, T. (2019). Ductility of 3d printed concrete reinforced with short straight steel fibers. Virtual Phys. Prototyp. 14, 160–174. doi:10.1080/17452759.2018.1548069
Bos, F., Wolfs, R., Ahmed, Z., and Salet, T. (2016). Additive manufacturing of concrete in construction: potentials and challenges of 3d concrete printing. Virtual Phys. Prototyp. 11, 209–225. doi:10.1080/17452759.2016.1209867
Bos, F. P., Ahmed, Z. Y., Jutinov, E. R., and Salet, T. A. (2017). Experimental exploration of metal cable as reinforcement in 3d printed concrete. Materials 10, 1314. doi:10.3390/ma10111314
Bos, F. P., Ahmed, Z. Y., Wolfs, R. J., and Salet, T. A. (2018). “3d printing concrete with reinforcement,” in High tech concrete: where technology and engineering meet: proceedings of the 2017 fib symposium, held in maastricht, The Netherlands, june 12-14, 2017 (Springer), 2484–2493.
Buchanan, C., and Gardner, L. (2019). Metal 3d printing in construction: a review of methods, research, applications, opportunities and challenges. Eng. Struct. 180, 332–348. doi:10.1016/j.engstruct.2018.11.045
Buswell, R. A., Leal De Silva, W. R., Jones, S. Z., and Dirrenberger, J. (2018). 3D printing using concrete extrusion: A roadmap for research. Cem. Concr. Res. 112, 37–49.
Buswell, R., Xu, J., De Becker, D., Dobrzanski, J., Provis, J., Kolawole, J. T., et al. (2022). Geometric quality assurance for 3d concrete printing and hybrid construction manufacturing using a standardised test part for benchmarking capability. Cem. Concr. Res. 156, 106773. doi:10.1016/j.cemconres.2022.106773
Buswell, R. A., Soar, R., Gibb, A. G., and Thorpe, A. (2007). Freeform construction: mega-scale rapid manufacturing for construction. Autom. Constr. 16, 224–231. doi:10.1016/j.autcon.2006.05.002
Camacho, D. D., Clayton, P., O’Brien, W. J., Seepersad, C., Juenger, M., Ferron, R., et al. (2018). Applications of additive manufacturing in the construction industry–a forward-looking review. Autom. Constr. 89, 110–119. doi:10.1016/j.autcon.2017.12.031
Chen, B., Tsui, H., Dams, B., Taha, H. M., Zhu, Y., and Ball, R. J. (2023). High performance inorganic fullerene cage ws2 enhanced cement. Constr. Build. Mater. 404, 133305. doi:10.1016/j.conbuildmat.2023.133305
Chen, M., Guo, X., Zheng, Y., Li, L., Yan, Z., Zhao, P., et al. (2018). Effect of tartaric acid on the printable, rheological and mechanical properties of 3d printing sulphoaluminate cement paste. Materials 11, 2417. doi:10.3390/ma11122417
Chen, M., Li, L., Wang, J., Huang, Y., Wang, S., Zhao, P., et al. (2020a). Rheological parameters and building time of 3d printing sulphoaluminate cement paste modified by retarder and diatomite. Constr. Build. Mater. 234, 117391. doi:10.1016/j.conbuildmat.2019.117391
Chen, M., Liu, B., Li, L., Cao, L., Huang, Y., Wang, S., et al. (2020b). Rheological parameters, thixotropy and creep of 3d-printed calcium sulfoaluminate cement composites modified by bentonite. Compos. B. Eng. 186, 107821. doi:10.1016/j.compositesb.2020.107821
Chen, M., Yang, L., Zheng, Y., Huang, Y., Li, L., Zhao, P., et al. (2020c). Yield stress and thixotropy control of 3d-printed calcium sulfoaluminate cement composites with metakaolin related to structural build-up. Constr. Build. Mater. 252, 119090. doi:10.1016/j.conbuildmat.2020.119090
Chen, S., F Laefer, D., and Mangina, E. (2016). State of technology review of civilian uavs. Recent Pat. Eng. 10, 160–174. doi:10.2174/1872212110666160712230039
Chen, Y., Figueiredo, S. C., Li, Z., Chang, Z., Jansen, K., Çopuroğlu, O., et al. (2020d). Improving printability of limestone-calcined clay-based cementitious materials by using viscosity-modifying admixture. Cem. Concr. Res. 132, 106040. doi:10.1016/j.cemconres.2020.106040
Chen, Y., He, S., Zhang, Y., Wan, Z., Çopuroğlu, O., and Schlangen, E. (2021). 3d printing of calcined clay-limestone-based cementitious materials. Cem. Concr. Res. 149, 106553. doi:10.1016/j.cemconres.2021.106553
Chen, Y., Li, Z., Chaves Figueiredo, S., Çopuroğlu, O., Veer, F., and Schlangen, E. (2019). Limestone and calcined clay-based sustainable cementitious materials for 3d concrete printing: a fundamental study of extrudability and early-age strength development. Appl. Sci. 9, 1809. doi:10.3390/app9091809
Chermprayong, P., Zhang, K., Xiao, F., and Kovac, M. (2019). An integrated delta manipulator for aerial repair: a new aerial robotic system. IEEE Robot. Autom. Mag. 26, 54–66. doi:10.1109/mra.2018.2888911
Chougan, M., Ghaffar, S. H., Jahanzat, M., Albar, A., Mujaddedi, N., and Swash, R. (2020). The influence of nano-additives in strengthening mechanical performance of 3d printed multi-binder geopolymer composites. Constr. Build. Mater. 250, 118928. doi:10.1016/j.conbuildmat.2020.118928
Chu, S., Li, L., and Kwan, A. (2021). Development of extrudable high strength fiber reinforced concrete incorporating nano calcium carbonate. Addit. Manuf. 37, 101617. doi:10.1016/j.addma.2020.101617
Compton, B. G., Post, B. K., Duty, C. E., Love, L., and Kunc, V. (2017). Thermal analysis of additive manufacturing of large-scale thermoplastic polymer composites. Addit. Manuf. 17, 77–86. doi:10.1016/j.addma.2017.07.006
Cuevas, K., Chougan, M., Martin, F., Ghaffar, S. H., Stephan, D., and Sikora, P. (2021). 3d printable lightweight cementitious composites with incorporated waste glass aggregates and expanded microspheres–rheological, thermal and mechanical properties. J. Build. Eng. 44, 102718. doi:10.1016/j.jobe.2021.102718
Dams, B. (2020). Cementitious and polymeric materials for aerial additive manufacturing. Bath, United Kingdom: University of Bath. Ph.D. thesis. doi:10.1680/jcoma.17.00013
Dams, B., Amornrattanasereegul, N., Shepherd, P., and Ball, R. (2019). “Cement-fibre composites for additive building manufacturing,” in Proceedings of the IOMMM 38th cement and concrete science conference, 14. London, United Kingdom: University of Bath.
Dams, B., Chen, B., Kaya, Y. F., Orr, L., Kocer, B. B., Shepherd, P., et al. (2024). Fresh properties and autonomous deposition of pseudoplastic cementitious mortars for aerial additive manufacturing. IEEE Access 12, 34606–34631. doi:10.1109/access.2024.3373188
Dams, B., Chen, B., Shepherd, P., and Ball, R. J. (2023). Development of cementitious mortars for aerial additive manufacturing. Appl. Sci. 13, 641. doi:10.3390/app13010641
Dams, B., Hei, Y., Shepherd, P., and Ball, R. (2021). “Novel cementitious materials for extrusion-based 3d printing,” in 2nd international conference on construction materials for sustainable future, CoMS 2020.
Dams, B., Lumlerdwit, K., Shepherd, P., and Ball, R. (2018a). “Fibrous cementitious material development for additive building manufacturing,” in Proceedings of the IOMMM 38th cement and concrete science conference (London, United Kingdom: University of Coventry).
Dams, B., Peng, J., Shepherd, P., and Ball, R. (2018b). Cementitious mortars and polyurethane foams for additive building manufacturing, 103–107.
Dams, B., Sareh, S., Zhang, K., Shepherd, P., Kovac, M., and Ball, R. J. (2020). Aerial additive building manufacturing: three-dimensional printing of polymer structures using drones. Proc. Inst. Civ. Eng. Constr. Mater. 173, 3–14.
Dams, B., Wu, Y., Shepherd, P., and Ball, R. (2017). “Aerial additive building manufacturing of 3d printed cementitious structures,” in 37th cement and concrete science conference.
Daneshvar, D. (2024). 3d printing of architected cementitious composites: a study on engineering the interface and mechanical properties of bio-inspired architectures. Vienna, Austria: Austrian Marshall Plan Foundation.
Ding, T., Xiao, J., Zou, S., and Wang, Y. (2020a). Hardened properties of layered 3d printed concrete with recycled sand. Cem. Concr. Compos. 113, 103724. doi:10.1016/j.cemconcomp.2020.103724
Ding, T., Xiao, J., Zou, S., and Yu, J. (2021). Flexural properties of 3d printed fibre-reinforced concrete with recycled sand. Constr. Build. Mater. 288, 123077. doi:10.1016/j.conbuildmat.2021.123077
Ding, T., Xiao, J., Zou, S., and Zhou, X. (2020b). Anisotropic behavior in bending of 3d printed concrete reinforced with fibers. Compos. Struct. 254, 112808. doi:10.1016/j.compstruct.2020.112808
Dobrzanski, J., Buswell, R., Cavalaro, S., Kinnell, P., Wang, W., Xu, J., et al. (2022). Milling a cement-based 3d printable mortar in its green state using a ball-nosed cutter. Cem. Concr. Compos. 125, 104266. doi:10.1016/j.cemconcomp.2021.104266
Doychinov, V., Abdellatif, M., Kaddouh, B., Malik, B., Jackson-Mills, G., Fuentes, R., et al. (2019). “Infrastructure robotics research at the university of leeds,” in Robotics research (IEEE: University of Leeds).
Ducoulombier, N., Demont, L., Chateau, C., Bornert, M., and Caron, J.-F. (2020). Additive manufacturing of anisotropic concrete: a flow-based pultrusion of continuous fibers in a cementitious matrix. Procedia Manuf. 47, 1070–1077. doi:10.1016/j.promfg.2020.04.117
Duty, C. E., Kunc, V., Compton, B., Post, B., Erdman, D., Smith, R., et al. (2017). Structure and mechanical behavior of big area additive manufacturing (baa) materials. Rapid Prototyp. J. 23, 181–189. doi:10.1108/rpj-12-2015-0183
Efraim, H., Shapiro, A., and Weiss, G. (2015). Quadrotor with a dihedral angle: on the effects of tilting the rotors inwards. J. Robot. Syst. 80, 313–324. doi:10.1007/s10846-015-0176-4
Eskandari Torbaghan, M., Kaddouh, B., Abdellatif, M., Metje, N., Liu, J., Jackson, R., et al. (2020). Robotic and autonomous systems for road asset management: a position paper. Proc. Inst. Civ. Eng. Smart Infrastruct. Constr. 172, 83–93. doi:10.1680/jsmic.19.00008
Feron, E., and Johnson, E. N. (2008) Aerial robotics. Springer Handbook of Robotics F/44, 1009–1029.
Figueiredo, S. C., Rodríguez, C. R., Ahmed, Z. Y., Bos, D. H., Xu, Y., Salet, T. M., et al. (2019). An approach to develop printable strain hardening cementitious composites. Mater. Des. 169, 107651. doi:10.1016/j.matdes.2019.107651
Fratello, R. S. (2021). Rael san fratello. Available at: http://www.rael-sanfratello.com/,urldate=2021-09-30.
Furkan Kaya, Y., Orr, L., Bahadir Kocer, B., and Kovac, M. (2024) “Aerial repair and aerial additive manufacturing,” in Infrastructure robotics: methodologies, robotic systems and applications, 367–384.
Ghaffar, S. H., Corker, J., and Fan, M. (2018). Additive manufacturing technology and its implementation in construction as an eco-innovative solution. Autom. Constr. 93, 1–11. doi:10.1016/j.autcon.2018.05.005
Goldmann, E., Górski, M., and Klemczak, B. (2021). Recent advancements in carbon nano-infused cementitious composites. Materials 14, 5176. doi:10.3390/ma14185176
Gosselin, C., Duballet, R., Roux, P., Gaudillière, N., Dirrenberger, J., and Morel, P. (2016). Large-scale 3d printing of ultra-high performance concrete–a new processing route for architects and builders. Mater. Des. 100, 102–109. doi:10.1016/j.matdes.2016.03.097
Hack, N., Wangler, T., Mata-Falcón, J., Dörfler, K., Kumar, N., Walzer, A. N., et al. (2017). Mesh mould: an on site, robotically fabricated, functional formwork. Second Concr. Innov. Conf. (2nd CIC) 19, 1–10.
Hager, I., Golonka, A., and Putanowicz, R. (2016). 3d printing of buildings and building components as the future of sustainable construction? Procedia Eng. 151, 292–299. doi:10.1016/j.proeng.2016.07.357
Horszczaruk, E., Mijowska, E., Kalenczuk, R. J., Aleksandrzak, M., and Mijowska, S. (2015). Nanocomposite of cement/graphene oxide–impact on hydration kinetics and young’s modulus. Constr. Build. Mater. 78, 234–242. doi:10.1016/j.conbuildmat.2014.12.009
Hossain, K., Lachemi, M., Sammour, M., and Sonebi, M. (2013). Strength and fracture energy characteristics of self-consolidating concrete incorporating polyvinyl alcohol, steel and hybrid fibres. Constr. Build. Mater. 45, 20–29. doi:10.1016/j.conbuildmat.2013.03.054
House, D. (2021). Smart slab. Available at: http://dfabhouse.ch/smart-slab/,,urldate=2021-09-30.
Hunt, G., Mitzalis, F., Alhinai, T., Hooper, P. A., and Kovac, M. (2014). 3D printing with flying robots, 4493–4499.
Issa, M. A. (1999). Investigation of cracking in concrete bridge decks at early ages. J. Bridge Eng. 4, 116–124. doi:10.1061/(asce)1084-0702(1999)4:2(116)
Jiao, D., Shi, C., Yuan, Q., An, X., Liu, Y., and Li, H. (2017). Effect of constituents on rheological properties of fresh concrete-a review. Cem. Concr. Compos 83, 146–159. doi:10.1016/j.cemconcomp.2017.07.016
Kaščak, J., Gašpár, Š., Paško, J., Knapčíková, L., Husár, J., Baron, P., et al. (2021). Design of an atypical construction of equipment for additive manufacturing with a conceptual solution of a printhead intended for the use of recycled plastic materials. Appl. Sci. 11, 2928. doi:10.3390/app11072928
Kazemian, A., Yuan, X., Cochran, E., and Khoshnevis, B. (2017). Cementitious materials for construction-scale 3d printing: laboratory testing of fresh printing mixture. Constr. Build. Mater. 145, 639–647. doi:10.1016/j.conbuildmat.2017.04.015
Keane, J. F., and Carr, S. S. (2013). A brief history of early unmanned aircraft. Johns Hopkins Apl. Tech. Dig. 32, 558–571.
Keating, S. J., Leland, J. C., Cai, L., and Oxman, N. (2017). Toward site-specific and self-sufficient robotic fabrication on architectural scales. Sci. Robot. 2, eaam8986. doi:10.1126/scirobotics.aam8986
Khajavi, S. H., Tetik, M., Mohite, A., Peltokorpi, A., Li, M., Weng, Y., et al. (2021). Additive manufacturing in the construction industry: the comparative competitiveness of 3d concrete printing. Appl. Sci. 11, 3865. doi:10.3390/app11093865
Khalil, A., Wang, X., and Celik, K. (2020). 3d printable magnesium oxide concrete: towards sustainable modern architecture. Addit. Manuf. 33, 101145. doi:10.1016/j.addma.2020.101145
Khoshnevis, B. (2004). Automated construction by contour crafting—related robotics and information technologies. Autom. Constr. 13, 5–19. doi:10.1016/j.autcon.2003.08.012
Kocer, B. B., Orr, L., Stephens, B., Kaya, Y. F., Buzykina, T., Khan, A., et al. (2022). “An intelligent aerial manipulator for wind turbine inspection and repair,” in 2022 UKACC 13th international conference on control (CONTROL), 226–227. doi:10.1109/Control55989.2022.9781451
Konsta-Gdoutos, M. S., Metaxa, Z. S., and Shah, S. P. (2010). Multi-scale mechanical and fracture characteristics and early-age strain capacity of high performance carbon nanotube/cement nanocomposites. Cem. Concr. Compos. 32, 110–115. doi:10.1016/j.cemconcomp.2009.10.007
Kreiger, M. A., MacAllister, B. A., Wilhoit, J. M., and Case, M. P. (2015). “The current state of 3d printing for use in construction,” in The proceedings of the 2015 conference on autonomous and robotic construction of infrastructure. Ames (Ames, IA: Iowa), 149–158.
Kruger, J., Zeranka, S., and van Zijl, G. (2019). An ab initio approach for thixotropy characterisation of (nanoparticle-infused) 3d printable concrete. Constr. Build. Mater. 224, 372–386. doi:10.1016/j.conbuildmat.2019.07.078
Le, T. T., Austin, S. A., Lim, S., Buswell, R. A., Gibb, A., and Thorpe, T. (2012a). Mix design and fresh properties for high-performance printing concrete. Mater. Struct. 45, 1221–1232. doi:10.1617/s11527-012-9828-z
Li, L., Xiao, B., Fang, Z., Xiong, Z., Chu, S., and Kwan, A. (2021). Feasibility of glass/basalt fiber reinforced seawater coral sand mortar for 3d printing. Addit. Manuf. 37, 101684. doi:10.1016/j.addma.2020.101684
Li, X., Wang, P., Zhao, M., Su, X., Tan, Y. H., and Ding, J. (2024). Customizable anisotropic microlattices for additive manufacturing: machine learning accelerated design, mechanical properties and structural-property relationships. Addit. Manuf. 104248. doi:10.1016/j.addma.2024.104248
Li, Z., Wang, L., and Ma, G. (2018). Method for the enhancement of buildability and bending resistance of 3d printable tailing mortar. IJCSM 12, 37–12. doi:10.1186/s40069-018-0269-0
Lim, S., Buswell, R. A., Le, T. T., Austin, S. A., Gibb, A. G. F., and Thorpe, T. (2012). Developments in construction-scale additive manufacturing processes. Autom. Constr. 21, 262–268. doi:10.1016/j.autcon.2011.06.010
Lim, S., Le, T., Webster, J., Buswell, R., Austin, A., Gibb, A., et al. (2009). “Fabricating construction components using layered manufacturing technology,” in Global innovation in construction conference (UK: Loughborough University Leicestershire), 512–520.
Lloret-Fritschi, E. (2016). Smart Dynamic Casting-A digital fabrication method for non-standard concrete structures. ETH Zurich. Ph.D. thesis.
Lowke, D., Dini, E., Perrot, A., Weger, D., Gehlen, C., and Dillenburger, B. (2018). Particle-bed 3d printing in concrete construction–possibilities and challenges. Cem. Concr. Res. 112, 50–65. doi:10.1016/j.cemconres.2018.05.018
Lowke, D., Weger, D., Henke, K., Talke, D., Winter, S., and Gehlen, C. (2015) “3d-drucken von betonbauteilen durch selektives binden mit calciumsilikatbasierten zementen–erste ergebnisse zu beton-technologischen und verfahrenstechnischen einflüssen,” in Proceedings of the tagungsbericht, 19.
Luhar, S., Suntharalingam, T., Navaratnam, S., Luhar, I., Thamboo, J., Poologanathan, K., et al. (2020). Sustainable and renewable bio-based natural fibres and its application for 3d printed concrete: a review. Sustainability 12, 10485. doi:10.3390/su122410485
Ma, G., Salman, N. M., Wang, L., and Wang, F. (2020). A novel additive mortar leveraging internal curing for enhancing interlayer bonding of cementitious composite for 3d printing. Constr. Build. Mater. 244, 118305. doi:10.1016/j.conbuildmat.2020.118305
Madbouly, A. I., Mokhtar, M., and Morsy, M. (2020). Evaluating the performance of rgo/cement composites for shm applications. Constr. Build. Mater. 250, 118841. doi:10.1016/j.conbuildmat.2020.118841
Mandolini, M., Pradel, P., and Cicconi, P. (2022). Design for additive manufacturing: methods and tools. Appl. Sci. 12, 6548. doi:10.3390/app12136548
Marchment, T., and Sanjayan, J. (2020). Mesh reinforcing method for 3d concrete printing. Automation Constr. 109, 102992. doi:10.1016/j.autcon.2019.102992
Maskell, D., Thomson, A., and Walker, P. (2018). Multi-criteria selection of building materials. Proc. Inst. Civ. Eng. Constr. Mater. 171, 49–58. doi:10.1680/jcoma.16.00064
Masoud, L., Hammoud, A., Mortada, Y., and Masad, E. (2024). Rheological, mechanical, and microscopic properties of polypropylene fiber reinforced-geopolymer concrete for additive manufacturing. Constr. Build. Mater. 438, 137069. doi:10.1016/j.conbuildmat.2024.137069
Mechtcherine, V., Bos, F. P., Perrot, A., Da Silva, W. L., Nerella, V., Fataei, S., et al. (2020a). Extrusion-based additive manufacturing with cement-based materials–production steps, processes, and their underlying physics: a review. Cem. Concr. Res. 132, 106037. doi:10.1016/j.cemconres.2020.106037
Mechtcherine, V., Michel, A., Liebscher, M., and Schmeier, T. (2020b). Extrusion-based additive manufacturing with carbon reinforced concrete: concept and feasibility study. Materials 13, 2568. doi:10.3390/ma13112568
Meng, W., and Khayat, K. H. (2018). Effect of graphite nanoplatelets and carbon nanofibers on rheology, hydration, shrinkage, mechanical properties, and microstructure of uhpc. Cem. Concr. Res. 105, 64–71. doi:10.1016/j.cemconres.2018.01.001
Metaxa, Z. S., Tolkou, A. K., Efstathiou, S., Rahdar, A., Favvas, E. P., Mitropoulos, A. C., et al. (2021). Nanomaterials in cementitious composites: an update. Molecules 26, 1430. doi:10.3390/molecules26051430
Moeini, M. A., Hosseinpoor, M., and Yahia, A. (2020). Effectiveness of the rheometric methods to evaluate the build-up of cementitious mortars used for 3d printing. Constr. Build. Mater. 257, 119551. doi:10.1016/j.conbuildmat.2020.119551
Mohan, M. K., Rahul, A., De Schutter, G., and Van Tittelboom, K. (2021a). Early age hydration, rheology and pumping characteristics of csa cement-based 3d printable concrete. Constr. Build. Mater. 275, 122136. doi:10.1016/j.conbuildmat.2020.122136
Mohan, M. K., Rahul, A., Van Tittelboom, K., and De Schutter, G. (2021b). Rheological and pumping behaviour of 3d printable cementitious materials with varying aggregate content. Cem. Concr. Res. 139, 106258. doi:10.1016/j.cemconres.2020.106258
Munir, Q., Peltonen, R., and Kärki, T. (2021). Printing parameter requirements for 3d printable geopolymer materials prepared from industrial side streams. Materials 14, 4758. doi:10.3390/ma14164758
Murcia, D. H., Genedy, M., and Taha, M. R. (2020). Examining the significance of infill printing pattern on the anisotropy of 3d printed concrete. Constr. Build. Mater. 262, 120559. doi:10.1016/j.conbuildmat.2020.120559
Muthukrishnan, S., Kua, H. W., Yu, L. N., and Chung, J. K. (2020). Fresh properties of cementitious materials containing rice husk ash for construction 3d printing. J. Mater. Civ. Eng. 32, 04020195. doi:10.1061/(asce)mt.1943-5533.0003230
Muthukrishnan, S., Ramakrishnan, S., and Sanjayan, J. (2021). Effect of alkali reactions on the rheology of one-part 3d printable geopolymer concrete. Cem. Concr. Compos. 116, 103899. doi:10.1016/j.cemconcomp.2020.103899
Natanzi, A. S., and McNally, C. (2020). “Characterising concrete mixes for 3d printing,” in Second RILEM international conference on concrete and digital fabrication: digital concrete 2020 (Springer), 2, 83–92. doi:10.1007/978-3-030-49916-7_9
Nettekoven, A., and Topcu, U. (2021). “A 3d printing hexacopter: design and demonstration,” in 2021 international conference on unmanned aircraft systems (ICUAS) (IEEE), 1472–1477.
Orr, L., Stephens, B., Kocer, B. B., and Kovac, M. (2021). “A high payload aerial platform for infrastructure repair and manufacturing,” in 2021 aerial robotic systems physically interacting with the environment (AIRPHARO), 1–6. doi:10.1109/AIRPHARO52252.2021.9571052
Panda, B., Lim, J. H., and Tan, M. J. (2019a). Mechanical properties and deformation behaviour of early age concrete in the context of digital construction. Compos. B. Eng. 165, 563–571. doi:10.1016/j.compositesb.2019.02.040
Panda, B., Paul, S. C., Hui, L. J., Tay, Y. W. D., and Tan, M. J. (2017). Additive manufacturing of geopolymer for sustainable built environment. J. Clean. Prod. 167, 281–288. doi:10.1016/j.jclepro.2017.08.165
Panda, B., Ruan, S., Unluer, C., and Tan, M. J. (2019b). Improving the 3d printability of high volume fly ash mixtures via the use of nano attapulgite clay. Compos. B. Eng. 165, 75–83. doi:10.1016/j.compositesb.2018.11.109
Panda, B., and Tan, M. J. (2018). Experimental study on mix proportion and fresh properties of fly ash based geopolymer for 3d concrete printing. Ceram. Int. 44, 10258–10265. doi:10.1016/j.ceramint.2018.03.031
Panda, B., and Tan, M. J. (2019). Rheological behavior of high volume fly ash mixtures containing micro silica for digital construction application. Mater. Lett. 237, 348–351. doi:10.1016/j.matlet.2018.11.131
Paolini, A., Kollmannsberger, S., and Rank, E. (2019). Additive manufacturing in construction: a review on processes, applications, and digital planning methods. Addit. Manuf. 30, 100894. doi:10.1016/j.addma.2019.100894
Papadakis, V., Pedersen, E., and Lindgreen, H. (1999). An afm-sem investigation of the effect of silica fume and fly ash on cement paste microstructure. J. Mater. Sci. 34, 683–690. doi:10.1023/a:1004500324744
Passuello, A., Moriconi, G., and Shah, S. P. (2009). Cracking behavior of concrete with shrinkage reducing admixtures and pva fibers. Cem. Concr. Compos. 31, 699–704. doi:10.1016/j.cemconcomp.2009.08.004
Paul, S. C., Tay, Y. W. D., Panda, B., and Tan, M. J. (2018). Fresh and hardened properties of 3d printable cementitious materials for building and construction. Arch. Civ. Mech. Eng. 18, 311–319. doi:10.1016/j.acme.2017.02.008
Pham, L., Tran, P., and Sanjayan, J. (2020). Steel fibres reinforced 3d printed concrete: influence of fibre sizes on mechanical performance. Constr. Build. Mater. 250, 118785. doi:10.1016/j.conbuildmat.2020.118785
Popescu, M., Rippmann, M., Liew, A., Reiter, L., Flatt, R. J., Van Mele, T., et al. (2021). Structural design, digital fabrication and construction of the cable-net and knitted formwork of the knitcandela concrete shell. Struct. (Elsevier) 31, 1287–1299. doi:10.1016/j.istruc.2020.02.013
Prihar, A., Garlock, M. E., Najmeddine, A., and Moini, R. (2024). Mechanical performance of sinusoidally architected concrete enabled by robotic additive manufacturing. Mater. and Des. 238, 112671. doi:10.1016/j.matdes.2024.112671
Qian, Y., Lesage, K., El Cheikh, K., and De Schutter, G. (2018). Effect of polycarboxylate ether superplasticizer (pce) on dynamic yield stress, thixotropy and flocculation state of fresh cement pastes in consideration of the critical micelle concentration (cmc). Cem. Concr. Res. 107, 75–84. doi:10.1016/j.cemconres.2018.02.019
Qian, Y., Ma, S., Kawashima, S., and De Schutter, G. (2019). Rheological characterization of the viscoelastic solid-like properties of fresh cement pastes with nanoclay addition. Theor. Appl. Fract. Mech. 103, 102262. doi:10.1016/j.tafmec.2019.102262
Quanji, Z., Lomboy, G. R., and Wang, K. (2014). Influence of nano-sized highly purified magnesium alumino silicate clay on thixotropic behavior of fresh cement pastes. Constr. Build. Mater. 69, 295–300. doi:10.1016/j.conbuildmat.2014.07.050
Qureshi, T. S., and Panesar, D. K. (2020). Nano reinforced cement paste composite with functionalized graphene and pristine graphene nanoplatelets. Compos. B. Eng. 197, 108063. doi:10.1016/j.compositesb.2020.108063
Rahul, A., Santhanam, M., Meena, H., and Ghani, Z. (2019). 3d printable concrete: mixture design and test methods. Cem. Concr. Compos. 97, 13–23. doi:10.1016/j.cemconcomp.2018.12.014
Rahul, A., Sharma, A., and Santhanam, M. (2020). A desorptivity-based approach for the assessment of phase separation during extrusion of cementitious materials. Cem. Concr. Compos. 108, 103546. doi:10.1016/j.cemconcomp.2020.103546
Reales, O. A. M., Duda, P., Silva, E. C., Paiva, M. D., and Toledo Filho, R. D. (2019). Nanosilica particles as structural buildup agents for 3d printing with portland cement pastes. Constr. Build. Mater. 219, 91–100. doi:10.1016/j.conbuildmat.2019.05.174
Rehman, A. U., and Kim, J.-H. (2021). 3d concrete printing: a systematic review of rheology, mix designs, mechanical, microstructural, and durability characteristics. Materials 14, 3800. doi:10.3390/ma14143800
Rostami, R., Zarrebini, M., Sanginabadi, K., Mostofinejad, D., Mahdi Abtahi, S., and Fashandi, H. (2020). An investigation into influence of physical and chemical surface modification of macro-polypropylene fibers on properties of cementitious composites. Constr. Build. Mater. 244, 118340. doi:10.1016/j.conbuildmat.2020.118340
Rubio, M., Sonebi, M., and Amziane, S. (2017). 3d printing of fibre cement-based materials: fresh and rheological performances. Acad. J. Civ. Eng. 35, 480–488. doi:10.26168/icbbm2017.74
Sareh, S., Siddall, R., Alhinai, T., and Kovac, M. (2017). “Bio-inspired soft aerial robots: adaptive morphology for high-performance flight,” in Soft robotics: trends, applications and challenges: proceedings of the soft robotics week, april 25-30, 2016, livorno, Italy (Springer), 65–74.
Šavija, B., and Schlangen, E. (2016). Use of phase change materials (pcms) to mitigate early age thermal cracking in concrete: theoretical considerations. Constr. Build. Mater. 126, 332–344. doi:10.1016/j.conbuildmat.2016.09.046
Schwartz, T. (2013). “Hal: extension of a visual programming language to support teaching and research on robotics applied to construction,” in Rob— arch 2012: robotic fabrication in architecture, art, and design (Springer), 92–101.
Scrivener, K., Avet, F., Maraghechi, H., Zunino, F., Ston, J., Hanpongpun, W., et al. (2018a). Impacting factors and properties of limestone calcined clay cements (lc3). Green Mater 7, 3–14. doi:10.1680/jgrma.18.00029
Scrivener, K., Martirena, F., Bishnoi, S., and Maity, S. (2018b). Calcined clay limestone cements (lc3). Cem. Concr. Res. 114, 49–56. doi:10.1016/j.cemconres.2017.08.017
Sikora, P., Chougan, M., Cuevas, K., Liebscher, M., Mechtcherine, V., Ghaffar, S. H., et al. (2021). The effects of nano-and micro-sized additives on 3d printable cementitious and alkali-activated composites: a review. Appl. Nanosci. 12, 805–823. doi:10.1007/s13204-021-01738-2
Smith, K. (2018). Self-repairing cities: leeds’ quest for an autonomous-robot maintenance army. Constr. Res. Innov. 9, 91–94. doi:10.1080/20450249.2018.1556500
Sonebi, M., García-Taengua, E., Hossain, K., Khatib, J., and Lachemi, M. (2015). Effect of nanosilica addition on the fresh properties and shrinkage of mortars with fly ash and superplasticizer. Constr. Build. Mater. 84, 269–276. doi:10.1016/j.conbuildmat.2015.02.064
Song, H., and Li, X. (2021). An overview on the rheology, mechanical properties, durability, 3d printing, and microstructural performance of nanomaterials in cementitious composites. Materials 14, 2950. doi:10.3390/ma14112950
Stampler, L. (2015). A Chinese company 3d-printed this five story apartment building. New York, NY: Time Magazine.
Subrin, K., Bressac, T., Garnier, S., Ambiehl, A., Paquet, E., and Furet, B. (2018). Improvement of the mobile robot location dedicated for habitable house construction by 3d printing. IFAC-PapersOnLine 51, 716–721. doi:10.1016/j.ifacol.2018.08.403
Sun, S., Ding, S., Han, B., Dong, S., Yu, X., Zhou, D., et al. (2017). Multi-layer graphene-engineered cementitious composites with multifunctionality/intelligence. Compos. B. Eng. 129, 221–232. doi:10.1016/j.compositesb.2017.07.063
Tay, Y. W. D., Panda, B., Paul, S. C., Noor Mohamed, N. A., Tan, M. J., and Leong, K. F. (2017). 3d printing trends in building and construction industry: a review. Virtual Phys. Prototyp. 12, 261–276. doi:10.1080/17452759.2017.1326724
Tay, Y. W. D., Ting, G. H. A., Qian, Y., Panda, B., He, L., and Tan, M. J. (2019). Time gap effect on bond strength of 3d-printed concrete. Virtual Phys. Prototyp. 14, 104–113. doi:10.1080/17452759.2018.1500420
Teizer, J., Blickle, A., King, T., Leitzbach, O., and Guenther, D. (2016). “Large scale 3d printing of complex geometric shapes in construction,” in Isarc. Proceedings of the international symposium on automation and robotics in construction (Auburn: IAARC Publications), 33.1
Thiel, C., Hechtl, C. M., Gehlen, C., and Kränkel, T. (2024). “Sustainability potential of additive manufactured concrete structures–studies on the life cycle assessment and circularity of an extruded exterior wall,” in RILEM international conference on concrete and digital fabrication (Springer), 13–21.
Ting, G. H. A., Tay, Y. W. D., and Tan, M. J. (2021). Experimental measurement on the effects of recycled glass cullets as aggregates for construction 3d printing. J. Clean. Prod. 300, 126919. doi:10.1016/j.jclepro.2021.126919
Ur Rehman, A., and Sglavo, V. M. (2020). 3d printing of geopolymer-based concrete for building applications. Rapid Prototyp. J. 26, 1783–1788. doi:10.1108/rpj-09-2019-0244
Van Der Putten, J., Azima, M., Van den Heede, P., Van Mullem, T., Snoeck, D., Carminati, C., et al. (2020). Neutron radiography to study the water ingress via the interlayer of 3d printed cementitious materials for continuous layering. Constr. Build. Mater. 258, 119587. doi:10.1016/j.conbuildmat.2020.119587
Vaziri, H. S., Shokuhfar, A., and Afghahi, S. S. S. (2019). Investigation of mechanical and tribological properties of aluminum reinforced with tungsten disulfide (ws2) nanoparticles. Mater. Res. Express 6, 045018. doi:10.1088/2053-1591/aafa00
Voney, V., Odaglia, P., Brumaud, C., Dillenburger, B., and Habert, G. (2021). From casting to 3d printing geopolymers: a proof of concept. Cem. Concr. Res. 143, 106374. doi:10.1016/j.cemconres.2021.106374
Wangler, T., and Flatt, R. J. (2018) First RILEM international conference on concrete and digital fabrication–digital concrete 2018, 19. Springer.
Wangler, T., Lloret, E., Reiter, L., Hack, N., Gramazio, F., Kohler, M., et al. (2017). Digital concrete: opportunities and challenges. RILEM Tech. Lett. 1, 67–75. doi:10.21809/rilemtechlett.2016.16
Weng, Y., Ruan, S., Li, M., Mo, L., Unluer, C., Tan, M. J., et al. (2019). Feasibility study on sustainable magnesium potassium phosphate cement paste for 3d printing. Constr. Build. Mater. 221, 595–603. doi:10.1016/j.conbuildmat.2019.05.053
Willmann, J., Augugliaro, F., Cadalbert, T., D’Andrea, R., Gramazio, F., and Kohler, M. (2012). Aerial robotic construction towards a new field of architectural research. Int. J. Archit. Comput. 10, 439–459. doi:10.1260/1478-0771.10.3.439
Wohlers, T., Gornet, T., Mostow, N., Campbell, I., Diegel, O., Kowen, J., et al. (2016). History of additive manufacturing. Wohler’s Report 2016-2022
Wolfs, R., Bos, F., and Salet, T. (2018). Early age mechanical behaviour of 3d printed concrete: numerical modelling and experimental testing. Cem. Concr. Res. 106, 103–116. doi:10.1016/j.cemconres.2018.02.001
Xiao, J., Zou, S., Yu, Y., Wang, Y., Ding, T., Zhu, Y., et al. (2020). 3d recycled mortar printing: system development, process design, material properties and on-site printing. J. Build. Eng. 32, 101779. doi:10.1016/j.jobe.2020.101779
Xu, F., Yan, C., Shyng, Y.-T., Chang, H., Xia, Y., and Zhu, Y. (2014). Ultra-toughened nylon 12 nanocomposites reinforced with if-ws2. Nanotechnology 25, 325701. doi:10.1088/0957-4484/25/32/325701
Yang, Z., Weiss, W. J., and Olek, J. (2006). Water transport in concrete damaged by tensile loading and freeze–thaw cycling. J. Mater. Civ. Eng. 18, 424–434. doi:10.1061/(asce)0899-1561(2006)18:3(424)
Zaid, O., and El Ouni, M. H. (2024). Advancements in 3d printing of cementitious materials: a review of mineral additives, properties, and systematic developments. Constr. Build. Mater. 427, 136254. doi:10.1016/j.conbuildmat.2024.136254
Zareiyan, B., and Khoshnevis, B. (2017). Interlayer adhesion and strength of structures in contour crafting-effects of aggregate size, extrusion rate, and layer thickness. Autom. Constr. 81, 112–121. doi:10.1016/j.autcon.2017.06.013
Zareiyan, B., and Khoshnevis, B. (2018). Effects of mixture ingredients on interlayer adhesion of concrete in contour crafting. Rapid Prototyp. J. 24, 584–592. doi:10.1108/rpj-02-2017-0029
Zhang, K., Chermprayong, P., Xiao, F., Tzoumanikas, D., Dams, B., Kay, S., et al. (2022). Aerial additive manufacturing with multiple autonomous robots. Nature 609, 709–717. doi:10.1038/s41586-022-04988-4
Zhang, X., Li, M., Lim, J. H., Weng, Y., Tay, Y. W. D., Pham, H., et al. (2018). Large-scale 3d printing by a team of mobile robots. Autom. Constr. 95, 98–106. doi:10.1016/j.autcon.2018.08.004
Zhu, Y. Q., Sekine, T., Li, Y. H., Wang, W. X., Fay, M. W., Edwards, H., et al. (2005). Ws2 and mos2 inorganic fullerenes-super shock absorbers at very high pressures. Adv. Mater. 17, 1500–1503. doi:10.1002/adma.200401962
Keywords: aerial additive manufacturing, construction industry, unmanned aerial vehicles, material properties, cementitious material, polymers, rheology
Citation: Dams B, Chen B, Kaya YF, Shepherd P, Kovac M and Ball RJ (2025) The rise of aerial additive manufacturing in construction: a review of material advancements. Front. Mater. 11:1458752. doi: 10.3389/fmats.2024.1458752
Received: 03 July 2024; Accepted: 18 November 2024;
Published: 27 January 2025.
Edited by:
Seyed Hamidreza Ghaffar, University of Birmingham, United KingdomReviewed by:
Lucio Nobile, University of Bologna, ItalyCopyright © 2025 Dams, Chen, Kaya, Shepherd, Kovac and Ball. This is an open-access article distributed under the terms of the Creative Commons Attribution License (CC BY). The use, distribution or reproduction in other forums is permitted, provided the original author(s) and the copyright owner(s) are credited and that the original publication in this journal is cited, in accordance with accepted academic practice. No use, distribution or reproduction is permitted which does not comply with these terms.
*Correspondence: Binling Chen, YmM5MzBAYmF0aC5hYy51aw==, Y2hlbmJsQGJpdC5lZHUuY24=
†ORCID: Barrie Dams, orcid.org/0000-0001-7081-5457; Binling Chen, orcid.org/0000-0003-0719-7398; Yusuf Furkan Kaya, orcid.org/0000-0003-2963-1896; Paul Shepherd, orcid.org/0000-0001-7078-4232; Mirko Kovac, orcid.org/0000-0002-9720-2463; Richard J. Ball, orcid.org/0000-0002-7413-3944
Disclaimer: All claims expressed in this article are solely those of the authors and do not necessarily represent those of their affiliated organizations, or those of the publisher, the editors and the reviewers. Any product that may be evaluated in this article or claim that may be made by its manufacturer is not guaranteed or endorsed by the publisher.
Research integrity at Frontiers
Learn more about the work of our research integrity team to safeguard the quality of each article we publish.