- 1Department of Technology and Cybernetics, Faculty of Agriculture and Technology, University of South Bohemia in České Budějovice, České Budějovice, Czechia
- 2Faculty of Mechanical Engineering, Institute of Technology and Materials, Jan Evangelista Purkyně University in Ústí nad Labem, Ústí and Labem, Czechia
Introduction: The marking of interchangeable cutting inserts according to ISO 6987 does not include the know-how of cutting tool manufacturers in the design of chip-breakers or the application of coatings. These small differences have a key effect on the efficiency and service life of cutting tools and result in qualitative and quantitative differences in production, which is related to the reduction or increase in costs associated with the appropriate choice of cutting tool. The design of the inserts also affects the shape and size of the chips produced, which is important to monitor for a safe machining process and subsequent waste management. This research deals with the effect of selected factors on the tool life and the form of the chips produced.
Methods: Indexable cutting inserts of the type CNMG 120408 from three different manufacturers were tested for their lifetime under identical cutting conditions (vc = 80 m s−1, ap = 1.5 mm, f = 0.3 mm·ot−1) on steel 1.6582 hardened to 40–44 HRC. These inserts are made of sintered tungsten carbide in a cobalt binder, coated with Al2O3 and TiCN layers. During machining, the wear of the main flank was continuously measured until the critical wear rate VBmax = 0.3 mm was reached. At the same time, the produced chips were continuously collected and analyzed in terms of their shape and size. The number of chips produced per 100 g of chips was calculated to obtain an analogous value indicating the total chip collection in terms of waste management. The SEM was used to identify both the types of coating layers present on the investigated inserts and the types of wear observed after reaching critical wear.
Results: The longest lifetime was achieved by the PM 4325 insert coated by 11.5 ± 1.2 µm TiCN layer and 5.3 ± 0.3 µm Al2O3 layer with a time T = 19.5 min. The chips produced were in the forms of arch connected and arch loose and the average chip length was 27.9 ± 7.6 mm. The number of chips per 100 g produced by the PM 4325 was 1,494 ± 401 pieces, which was the lowest count of chips within the experiment (which is not optimal). The MP3 -WPP20S insert coated by 17.8 ± 0.4 µm TiCN layer and 15.1 ± 0.3 µm Al2O3 layer achieved lifetime T = 17.4 min even though it has twice the thickness of the coating compared to PM 4325. Produced chips in the forms of arch connected, arch loose and tubular short shape and the average chip length was 34.1 ± 5.5 mm, which was the worst chip length result within the experiment in terms of chip evaluation. The number of chips per 100 g produced by MP3 -WPP20S was 1,520 ± 401 pieces. The E-M GRADE T9325 insert coated by 7.2 ± 0.5 µm TiCN layer and 5.1 ± 0.2 µm Al2O3 layer achieved the shortest lifetime with a time T = 10.8 min. The chips produced were arch loose in shape, with an average chip length of 8.2 ± 0.7 mm. The number of chips per 100 g produced by the E-M GRADE T9325 was 2,392 ± 259 pieces, achieving the best result in the experiment in terms of chips produced. The achieved results are correlated with different combinations of thicknesses of Al2O3 and TiCN protective coatings revealed by SEM analysis.
Discussion/Conclusion: Together with the geometrical nuances of the design of the different manufacturers, factor of combinations of coatings thicknesses has an influence on the variation of the wear progress and the achievement of a specific lifetime value of the cutting inserts. The experiment concludes that the thickness of the coating layers alone does not have a direct effect on the overall lifetime of the tool, and the approximate lifetime of the cutting edge cannot be predicted based on the parameters of the coating layers. When choosing a cutting tool, the manufacturer should carry out a test series for the specific material to be machined, despite the declaration of the composition and thickness of the coating layers. The analysis of the produced chips led to the conclusion that the wafers with a thinner coating layer, especially the Al2O3 layer, formed better chips in terms of their shape and size due to the different heat distribution during machining.
1 Introduction
Compared to solid conventional tools, manufacturing companies nowadays use an exchangeable cutting tool system in the form of standardized indexable cutting inserts quite commonly. However, it is still true that the correct choice of a cutting tool depends on its geometrical, physical and chemical properties (Denkena et al., 2020). These properties determine the behavior of the cutting tool in interaction with the workpiece and the cutting environment, which have a natural tendency to change its geometry and the efficiency of removing the processed material (Marko et al., 2014). A non-optimal tool choice for a given manufacturing situation may reduce the quality of the machined surface and reduce the tool life, thereby causing unwanted losses to the company in the form of increased tool costs, incidental costs associated with tool costs such as increased consumption of process fluids, increased waste management costs and possible increase in product scrap (Suresh et al., 2012). Ideally, before starting a particular type of production, a company should conduct a test series to observe the behavior of different cutting tool variants in terms of their tool life and effect on the desired workpiece. During the development of cutting inserts, the portfolio of their geometric variations has been greatly expanded, and the classification system according to ISO 3687 is continuously being expanded. With the development of computer programs and applications, the algorithms for assigning a specific type of cutting tool to a certain machined material and cutting conditions are being improved. However, since chip machining is a complex system in which every parameter plays a role, it is still an approximate recommendation within the application, rather than a strict assignment of a tool with maximum optimization (Sohal and Eyada, 1989; Isakov, 2014).
Tooling costs are approximately 3% of total machining costs. The direct impact of cost reduction within the optimization of the cutting tool is relatively negligible (around 1% cost reduction with a 50% increase in tool efficiency). However, the indirect impact is significant in the form of a reduction in the cost of machines, additional tools or production time. If the optimization of tool selection could increase the cutting speed by 20%, it would reduce the production cost of the machined part by up to 15%. The saving of cooling lubricants is also related to the saving of machine time, or rather to the use of more efficient cutting tools (Bobzin, 2017). In practice, however, this is neglected, primarily to reduce the cost of researching and purchasing cutting tools, as well as for time reasons (Astakhov, 2004). Also, the work capacity of employees who would otherwise be engaged in regular manufacturing activities needs to be considered (Krar and Gill, 2003). Paradoxically, the cost of selecting the ideal cutting tool is represented in a very small amount in the sum of the costs associated with an inappropriate tool for a particular situation (Wu et al., 2017). Manufacturing companies, with the effort to reduce unwanted losses, are increasingly trying to consider the mentioned phenomenon of selecting the appropriate cutting tool. However, beyond financial and personnel constraints, they are also forced to spend money on specific measuring devices that have very limited use beyond the initial (testing) phase of production, which is related to the efficiency of the workload of specially trained operators of these devices (Janásek et al., 2012; Wijanarka et al., 2018). Also, for these reasons, there is a greater integration between manufacturing companies and commercially oriented testing laboratories or universities with well-equipped laboratories and trained researchers (Bi and Wang, 2012).
As mentioned above, when choosing a cutting tool for a specific machined material and cutting conditions, for time reasons, manufacturers orient themselves mainly according to the information that producers of cutting tools publish for their products. Data on the ideal range of cutting parameters, the category of machined material, the recommended character of machining (heavy roughing to fine finishing) or only the names of the coating layers used are often available. Less often, there is a graph available for ideal chip formation or comparison with a competitive, unnamed insert. However, these are always data related to the model machined material and model cutting conditions. Due to the nature of the multi-criteria machining process, there is a risk of a situation where, despite the available information about a specific cutting tool, it turns out in practice that the cutting process does not proceed ideally, the tool wears quickly, the machined surface does not meet the required parameters or a chip is formed, which can make the process itself difficult or even to stop. The data obtained from this research show, on selected inserts of the same type according to ISO 6987, how their wear takes place in different ways, taking into account the findings from a detailed analysis of their functional components, especially the composition of the coating layers. At the same time, this research deals with the correlation between the achieved service life of the inserts under the given cutting conditions and the form of the formed chip, which in terms of shape and length may or may not meet the safety and environmental requirements for a specific machining process, see below.
1.1 Coated carbide-based tools
Since the invention of the electric arc furnace, the development of cutting materials has advanced significantly. One of the main benefits of the arc furnace has been the ability to melt hard materials in the form of carbides. Sintered carbides have the highest flexural strength, Young’s modulus and fracture toughness of the cutting materials used and can therefore be used for high feed rate machining and heavy-duty interrupted cutting (Prengel et al., 2001). The disadvantage is the lower thermomechanical stability, which limits the use at higher cutting speeds (Reis et al., 2019).
A sintered carbide is a heterogeneous material consisting of hard carbide particles in a metallic binder, which is prepared by powder metallurgy technology. For practical purposes, mainly hexagonal tungsten carbide (WC) and cubic carbides of titanium (TiC), tantalum (TaC) and niobium (NbC) are used in the manufacturing of cutting tools (Nordin et al., 1998). Carbide particles increase strength, hardness and chemical stability and their size is usually between 0.1 and 14 μm. Carbide particles are fixed in a metallic, most commonly cobalt (Co.) binder, with the volume of the binder tending to be around 5%–40% of the total volume (Aneiro et al., 2008). To increase the cutting performance of this group of tools, the application of coatings on their surface, either in the total area or on its functional part, is used. Coatings are usually made in multiple layers with different properties, mainly to increase resistance to mechanical wear, to protect the tool against high cutting temperatures or to increase the chemical stability of the functional parts of the cutting tool (Prengel et al., 1998). The combinations of the selected coatings are applied by Chemical Vapor Deposition (CVD) or Physical Vapor Deposition (PVD) methods and beyond the actual design of the layers, the application of the coatings must be technologically precise, as otherwise there is a risk of a reduction in the useful properties of the coating layer, either due to imperfect adhesion to the substrate, a reduction in the required hardness or toughness of the individual layers or a lack of a smooth surface without the presence of inequalities (Schintlmeister et al., 1984; Ducros et al., 2003; Bobzin, 2017). Problems with cracked layers have been virtually solved thanks to the trend of lowering application temperatures, and innovations in the development of PVD coatings for precision applications. CVD coatings for roughing applications are also supported by the recently developed High Power Impulse Magnetron Sputtering (HIPIMS) coating deposition method (Hsu et al., 2005; Martan and Beneš, 2012; Bradley et al., 2015).
1.2 The environmental consequences
The advantage of sintered carbide cutting tools is their established recycling process. After the tool has worn out or reached the end of its useful life, it tends to be recycled, which involves dissolution into atomic particles, cleaning, separation and subsequent crystallization into primary powder products (Mitchel, 2013). However, this process requires some energy consumption and by optimizing for maximum tool durability of functional parts, the recycling portion of the cutting material life cycle can be reduced (Dahmus and Gutowski, 2004).
In addition to worn cutting tools, the natural waste product of chip machining is the removed workpiece material in the form of chips. The issue of chips lies in their shape and size (length), and these parameters are addressed at several levels (Sai et al., 2005). The first concerns the product manufacturing process itself, where due to the requirement for continuous tool change on automated machines and systems, waste material in the form of chips must not interfere with the tool change path (Bhuiyan et al., 2014). In this case, there is a risk of chips becoming entangled on the tool or tool holder, making it impossible to change the machining operation. For this reason, chips may also be judged by the direction of departure from the cutting point (Barry and Gerald, 2002). In extreme cases, the machining process may be interrupted due to chip ingress between the tool cutting edge and the machined layer, which may cause tool destruction (Yılmaz et al., 2020).
The qualitative plane of optimal chip shape is mainly concerned with the workpiece surface parameters (Su et al., 2015). The chip, as such, generally has a higher hardness than the original (machined) material. In addition, its edges are very sharp and thus risk disturbing the structure of the machined surface, characteristically with long continuous chips. A similar case also occurs on the tool side, where the outgoing chip (in this case, too small) disturbs the tool surface layers and can initiate microcracks on the tool edge, which would lead to premature breakage of the cutting edge (Woody et al., 2008).
The quantitative level refers to the management of the generated chips in the context of waste management. In the case of the formation of long continuous chips (arch connected chips), the machine workspace fills up quickly and needs to be emptied continuously. The large volume of waste in the form of long and continuous chips excessively occupies the storage space and makes subsequent handling difficult (Viharos et al., 2003). In the case of the formation of elementary or small cell chips (loose connected chips), the storage layout is used more efficiently, the frequency of removal of waste products from the production area is reduced and the recycling process is made more efficient. These factors have a significant impact on reducing the financial costs associated with waste management (Kuntoğlu and Sağlam, 2019).
The shape and length of the chip produced is dependent on the properties of the work material, the set cutting conditions, the application of process fluids in the cutting environment, the tool geometry, the properties of the cutting material and also the type of cutting tool coating (Barry and Gerald, 2002). The description and classification of the shape, size and direction of the chip leaving the cutting point is addressed in ISO 3685 (Viharos et al., 2003). In many studies, optimization of the cutting process by the Taguchi method or by ANOVA (analysis of variance) can be encountered. In the evaluation of cutting tool wear, the chip formation factor is also important in terms of monitoring the wear process and the machining process as such (Leksycki et al., 2020). However, the evaluation of waste material in the form of chips is time-consuming and despite the obvious importance of the shape and length of the produced chips, this part of the qualitative and quantitative evaluation of the cutting process is often neglected (Janeková et al., 2018).
2 Experimental methodology
This article presents data and conclusions that are part of the research on the wear of cutting tools carried out in cooperation between the Faculty of Mechanical Engineering of the Jan Evangelista Purkyně University in Ústí nad Labem and the Faculty of Agriculture and Technology of the University of South Bohemia in České Budějovice. The following subsections describe the experimental part of the work in terms of the components and materials that served the research purposes described in this article.
The essence of this experiment is to compare the service life and wear of indexable cutting inserts of the same type from different manufacturers. It follows from the above facts that the choice of a specific cutting tool has a complex effect on the machining process. Each parameter involved affects the course of machining, and this is also the case with the geometric and utility properties of a specific type of insert from a specific manufacturer. Assuming that inserts of the same type according to ISO 6987 will be compared with each other, among the main difference parameters that individual manufacturers implement in their cutting tools, one can count in particular the different chamfering structure of the edge, the different design of the chip breaker and the differences in the composition and thickness of the coating layers that protect the surface of the cutting tool especially against the effects of high cutting temperatures and abrasive wear due to the interaction with the hard parts of the machined material. The differences in the designs of the selected inserted inserts are described in the subsection, see below.
2.1 Workpiece material and tool material
As part of the experiment, steel 1.6582 according to EN 10027–2 was used. The supplied material was hardened to 40–44 HRC for the purpose of the experiment. The chemical composition of the supplied experimental material was subjected to chemical analysis with a Bruker Q4 Tasman spark emission spectrometer, which confirmed that the supplied material complies with the chemical composition tolerance of the standard, see Table 1 (EN 10027-2:2015, 2015).
In general, the Cr-Ni-Mo steels have good ductility, high strength and very good corrosion resistance after quenching and tempering (Maropoulos et al., 2004). The selected steel is commonly used for manufacturing high-stress components used in general engineering, especially in the automotive industry (e.g., gears, shafts, pins, eccentrics, etc.) and aircraft industry (include propeller shafts, rotors, discs, connecting rods, gear shafts, and heavy forgings). Outside of machining operations, this material can be used for drawn, extruded or cold-formed products (Branco et al., 2012). It is suitable for heat treatment and steel 1.6582 has a partial vibration damping capability and is therefore also used for the manufacturing of cutting tool shanks. Due to the high variability of use and a relatively lower purchase price, the tested material has potential from both the utility and cost perspectives (Nagode et al., 2016). In terms of the above information, this material presents challenges for the machining process and the optimization of machining techniques through a significant potential for industrial applications, especially in industries that require durable and robust components such as aerospace and automotive. A great advantage for the experiment is the high suitability for hardening to required level. Thanks to this, it is possible to ensure the repeatability of experimental conditions in the case of research on indexable cutting inserts from other manufacturers or under different cutting conditions.
The subjects of testing were the replaceable inserts of the type CNMG 120408 according to ISO 6987 from three different manufacturers. The substrate of the cutting inserts consists of sintered carbide type WC and Co. binder with the addition of other carbides (Ta, Nb). This is an ISO group of inserts composed of HC carbides (coated hardmetals) with coating layers to reduce wear due to the mechanisms accompanying the machining process. Before machining, the tested inserts were subjected to energy dispersive X-ray (EDX)/scanning electron microscope (SEM) analysis using a Tescan Vega 3 scanning electron microscope, supplemented by a Bruker X-Flash analyzer to describe the composition of the coated layers in the unworn condition, see below. Namely, these are the cutting inserts.
2.1.1 CNMG 120408E-M GRADE T9325
Substrate - HC with CVD coated by titanium carbo-nitride (TiCN) + Al2O3 (Figure 1B). Primary use is for P - steel group, alternative use is for stainless steels - M and cast iron K. EDX analysis confirmed the presence of a TiCN layer with a thickness of 7.2 ± 0.5 µm and an Al2O3 layer with a thickness of 5.1 ± 0.2 µm, see Figure 1. The substrate material is composed of W carbide and Co. binder.
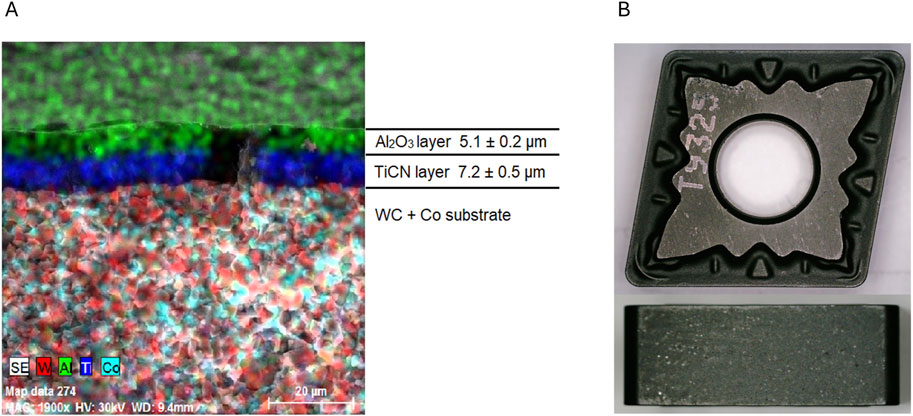
Figure 1. (A) SEM analysis of unworn coated layers. (B) Macroscopic composition of CNMG 120408E-FM T9325 cutting insert.
2.1.2 CNMG 120408-PM 4325
Substrate - HC with CVD coating Ti (C, N) + Al2O3 + TiN (Figure 1A). The primary use is for group P - steel, the alternative use is for cast iron - group K. EDX analysis confirmed the presence of a TiCN layer with a thickness of 11.5 ± 1.2 µm and an Al2O3 layer with a thickness of 5.3 ± 0.3 µm, see Figure 2. Furthermore, the substrate material composed of carbide W and Co. binder is also visible. The Chemical bonding of the applied coating layers was confirmed, and on the contrary, diffusion of elements from the carrier substrate into the coating was not observed.
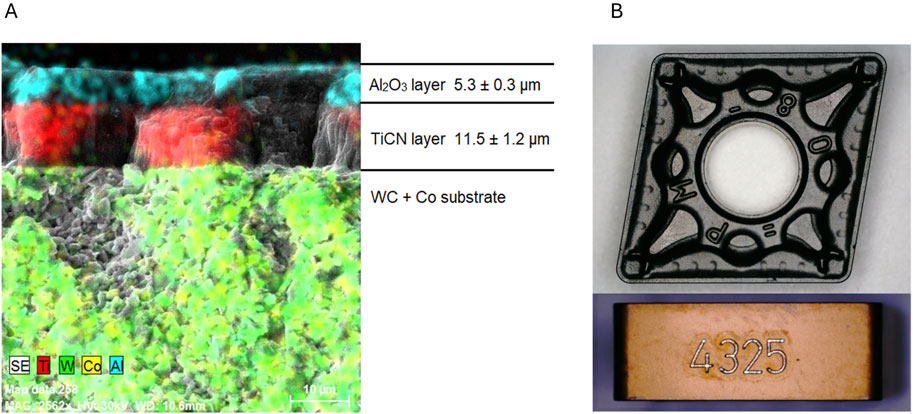
Figure 2. (A) SEM analysis of unworn coated layers. (B) Macroscopic composition CNMG 120408-PM 4325 cutting insert.
2.1.3 CNMG 120408-MP3 WPP20S
Substrate - HC with CVD coating TiCN + Al2O3 (Figure 1A). The Primary use is for P-group steels, alternative use is for cast iron - K-group. EDX analysis confirmed the presence of a TiCN layer with a thickness of 17.8 ± 0.4 µm and an Al2O3 layer with a thickness of 15.1 ± 0.3 µm, see Figure 3. The substrate material is composed of carbide W and Co. binders.
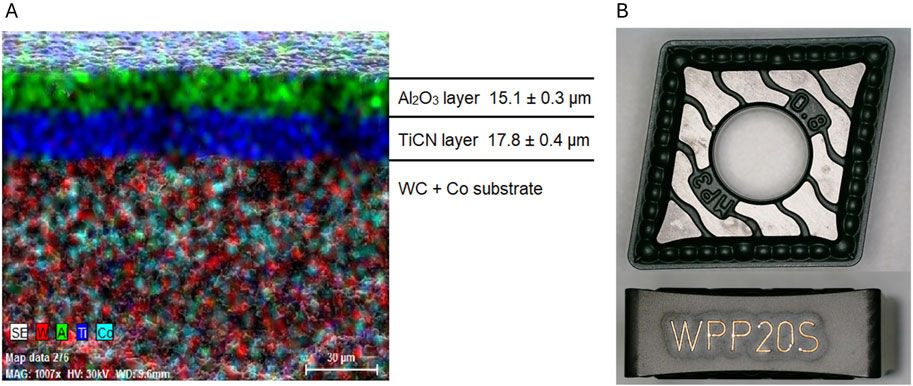
Figure 3. (A) SEM analysis of unworn coated layers. (B) Macroscopic composition of CNMG 120408E-MP3 WPP20S cutting insert.
It is clear from Figures 1–3 that despite the properties corresponding to the marking of the CNMG 120408 inserts, the processing of the individual inserts differs in the design of functional elements such as the chip sealer. The primary designation of the selected inserts corresponds to the material used as test material in the experiment, see Table 2. For clarity, the abbreviated marking of the selected inserts is used in Table 2 and the following subsections, except for the conclusion. Effective applications for machined materials are classified by ISO 513:2012. The selected inserts are recommended by the manufacturers for machining low, medium and high alloy steels, ferritic and martensitic steels - group P, gray, ductile and tempered cast iron - K and stainless, austenitic-ferritic steels - group M.
The differences in the dimensions of the edges of the examined cutting inserts are summarized in Table 3. These are chamfering structure parameters, where the value a [°] expresses the rake angle, the value b [°] expresses the bevel of chamfering land and the value c [mm] expresses the land width.
2.2 Experimental setup
The experiment was carried out on a Doosan Lynx 220 LM CNC lathe, controlled by a Fanuc i-series system. The machined blank was in the form of a cylindrical bar with an initial diameter of 50 mm and a length of 330 mm, with a hardened depth of 15 mm from the surface of the part. Due to the insert holder used, a minimum machinable diameter of 23 mm was specified.
The machining parameters were identical for all the inserts tested. After an initial series of test cuts, a range of cutting parameters was determined that ensured a stable cutting process without undesirable system chatter. The cutting speed (vc) was chosen to be 80 m s-1, the depth of cut (ap) was set to 1.5 mm and the feed rate (f) was set to 0.3 mm·ot-1. The aim was to approximate the cutting conditions used in practice during conventional machining at lower cutting speeds due to the combined effect of the process fluid (cutting fluid) and the lower cutting temperature. Depth of cut and feed rate values are based on the recommendations of the insert manufacturers. Higher cutting speeds have been shown to reduce the effect of cutting force, especially when machining steel workpieces. In practice, there is thus a balance between the advantage of reduced cutting forces and higher production efficiency resulting from the use of higher cutting speeds, and the undesirable higher thermal stress on the cutting tool caused by higher cutting temperatures (Xu et al., 2021).
2.3 Experimental design
The data acquisition procedure was based on design of experiment (DOE) policy. The main flank wear as a function of time of tool engagement on workpiece material was evaluated. Under the specified cutting conditions, workpiece material was removed to maintain the stability of the cutting process. After removing a material layer with ap = 1.5 mm and a length of cut (lc) - 0.5 mm (to prevent engagement with the adjacent cutting edge), the machining was stopped. The insert under examination was removed from the holder and wear was measured using an Olympus SZX10 stereomicroscope equipped with a Bresser MicroCam-II camera to take a record of the actual condition, see Figure 4A. Using the measurement software, the VBmax value was measured by micrometrical method, see Figure 4B. After measurement, the indexable insert was returned to the standard PCLNR 2020 K12 holder, ensuring repeatability of the measurement in terms of tool position.
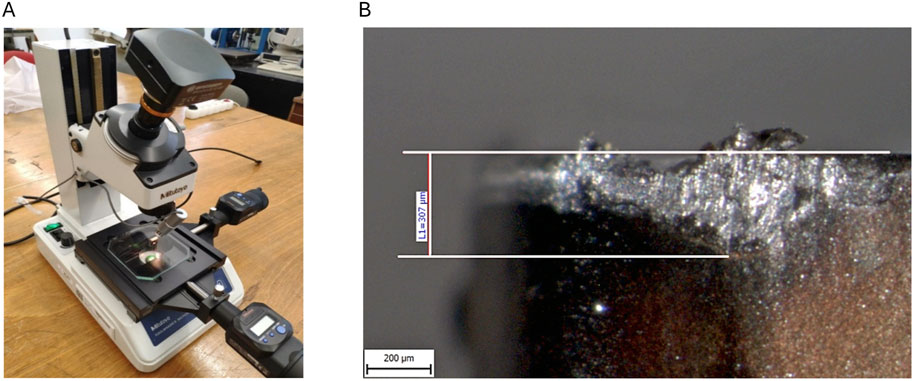
Figure 4. (A) Flank wear measuring microscope setup. (B) Example of micrometric measurement of flank wear.
At the same time, a sample of the produced chips was taken from a special container placed under the workpiece in the working area of the CNC lathe. The chips were then evaluated for their size and shape in the same way as the wear on the cutting tool. The chip recovery vessel was cleaned after each tool run into the workpiece to avoid mixing up chips from different machining stages. The visual assessment of chips was performed with an Olympus SZX10 stereomicroscope equipped with a Bresser MicroCam-II digital camera equipped with measurement software. The result is a chronological documentation of the chip shape and length, see selected macro images in Figures 5A–D. The digitally assessed chips were selected in numbers of 4–6 pieces so that their composition was representative of the chips produced within the sample.
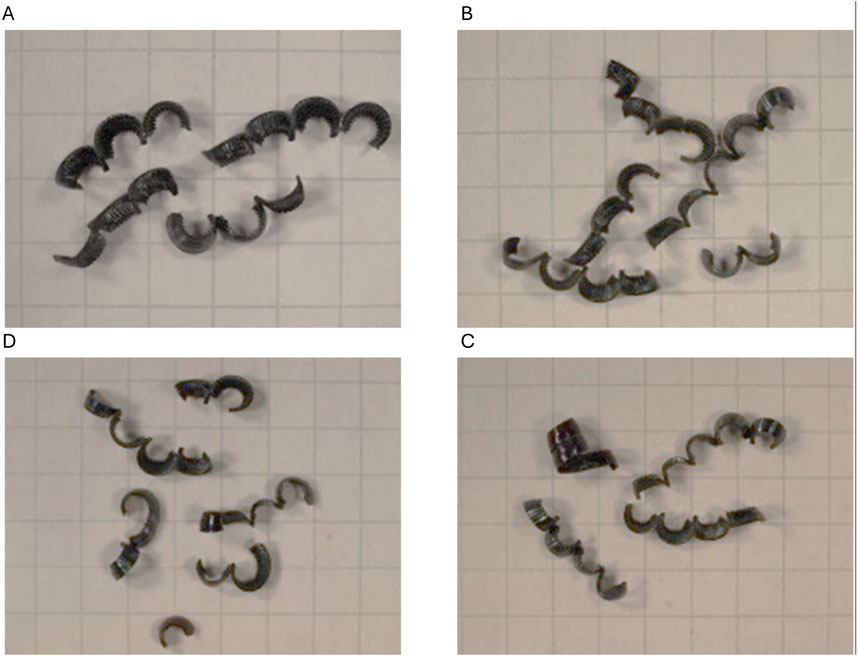
Figure 5. (A) Macroscopic chip evaluation at T = 2 [min]. (B) Macroscopic chip evaluation at T = 7.5 [min]. (C) Macroscopic chip evaluation at T = 12 [min]. (D) Macroscopic chip evaluation at T = 21 [min].
At the same time, the chips were evaluated in terms of the number of chips per 100 g of chips collected, for which precise laboratory scales A&D GF-200P were used. This is a value that corresponds analogously to their shape and size and can be used to quantify the quantity produced, which is practical information for waste management planning. This procedure was repeated until the specified critical flank wear of the cutting tool VBmax = 0.3 mm was reached. This value is based on the recommendations used in manufacturing practice for a flank wear limit of 0.3–0.5 mm for coated carbide cutting tools (Sheikh-Ahmad and Davim, 2012).
After the completion of the experimental part, the individual inserts were subjected to SEM analysis including elemental analysis of the worn surface. A Tescan Vega 3 electron microscope with a Bruker elemental analyzer was used for the evaluation.
3 Results and discussion
The measured wear values of the tool’s main flank were analyzed and plotted on a timeline relative to the time the tool was engaged. At the same time, the collected samples of produced chips were examined in terms of their shape, length and number of chips per 100 g of chips collected. The examined inserts that had reached critical wear were evaluated using SEM and EDX analyzer, focusing on the type and extent of wear of the main tool flank surface area.
3.1 Investigated tool flank wear
Figure 6 shows graphically the wear history over time of all the examined indexable inserts. The PM 4325 insert with a time of 19.5 min achieved the best result, respectively the longest cutting edge life. This was followed by the MP3 WPP20S insert with a cutting edge life of 17.4 min and the lowest cutting edge life was achieved by the E-M GRADE T9325 insert with a time of 10.8 min.
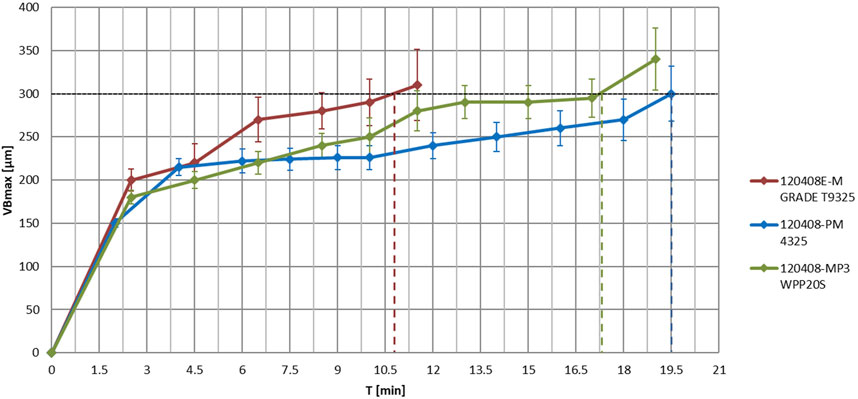
Figure 6. Progression of VBmax parameter of investigated cutting inserts for 1.6582 steel, vc = 80 m min−1.
Several types of cutting edge wear were identified by SEM, which are, however, characteristic of carbide cutting tools. Main flank wear, crater wear on rake face, local chipping and workpiece material in the form of built-up edge (BUE) were the most represented.
The E-M GRADE T9325 insert has been worn down to the TiCN coating level below the cutting edge line to the area where the interface between the tool cutting edge and the workpiece is located. In this area, notch wear is observed due to the aforementioned spinning as well as the chip mass leaving the cutting plane, as indicated by the underlying abrasive wear area on the main spine created by the departing chip, see Figure 7A. The wear was identified in the form of a worn area along the cutting edge line which transitioned to a crater wear on the tool rake face, see Figure 7B. Elemental analysis allowed the level of wear observed to be determined. The cutting edge line was worn down to the level of the TiCN layer with a gradual transition to the underlying support substrate consisting of WC, see Figures 7C, D. The greatest material loss on the tool occurred at the interface between the tool cutting edge and the workpiece.

Figure 7. (A) SEM analysis of worn main flank. (B) SEM analysis of worn rake face. (C) EDX analysis of worn main flank. (D) EDX analysis of worn rake face.
The wear of the main spine on the PM 4325 insert followed the cutting edge line evenly. There is partial chipping in the area where the tool is in point contact with the workpiece material, but this is replaced by BUE material on the tool rake face, see Figure 8A. A clearer identification of the chipping of small particles of the cutting edge can be seen in Figure 8B, looking at the tool rake face. Also, wear in the form of notch wear is more easily identified. The cutting edge line wear visible on the tool rake face gradually transitions to notch wear, similar to the PM 4325 insert.
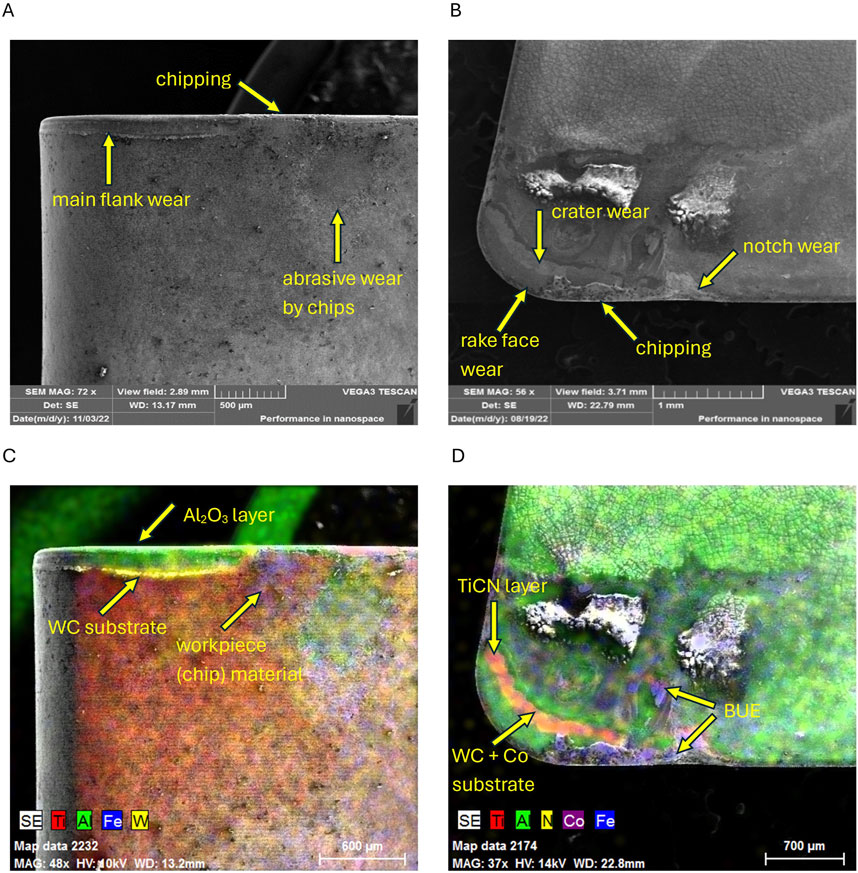
Figure 8. (A) SEM analysis of worn main flank. (B) SEM analysis of worn rake face. (C) EDX analysis of worn main flank. (D) EDX analysis of worn rake face.
Elemental analysis confirmed the extent of wear on the main tool flank down to the level of the supporting substrate and the relatively minor abrasive wear on the flank surface by the departing chips, which left traces of adhered machining material and exposed the protective layer of Al2O3, see Figure 8C. Wear to the level of the support material also occurred on the tool rake face, in the groove-shaped wear area. There was also a well identifiable BUE in the areas of the hollowed out cutting edge and also in the area of notch wear occurring, see Figure 8D.
The wear on the main flank of the MP3 WPP20S insert followed the line of the cutting edge with a gradual transition to the interface between the tool edge and the workpiece. From this point onwards, massive abrasive wear occurred on the tool’s main spine area from the exiting chip, see Figure 9A. Edge wear is evident on the tool rake face with a transition to slight groove-shaped wear. Slight notch wear is also evident on the rake face, see Figure 9B. Workpiece material adherence to the main tool flank in the form of BUE is visible in the area below the cutting edge and partially on the abrasive worn surface in Figure 9C. More significant is the level of wear caused by the exiting chip, which has exposed a larger area of the TiCN layer on the spine surface. Elemental analysis of the tool rake face allows to define the boundaries of the groove-shaped wear on the rake face exposed by the TiCN coating and its connection to the notch wear area, where wear occurred down to the level of the supporting substrate. At the same time, the areas where BUE formed on the rake face are visible, see Figure 9D.
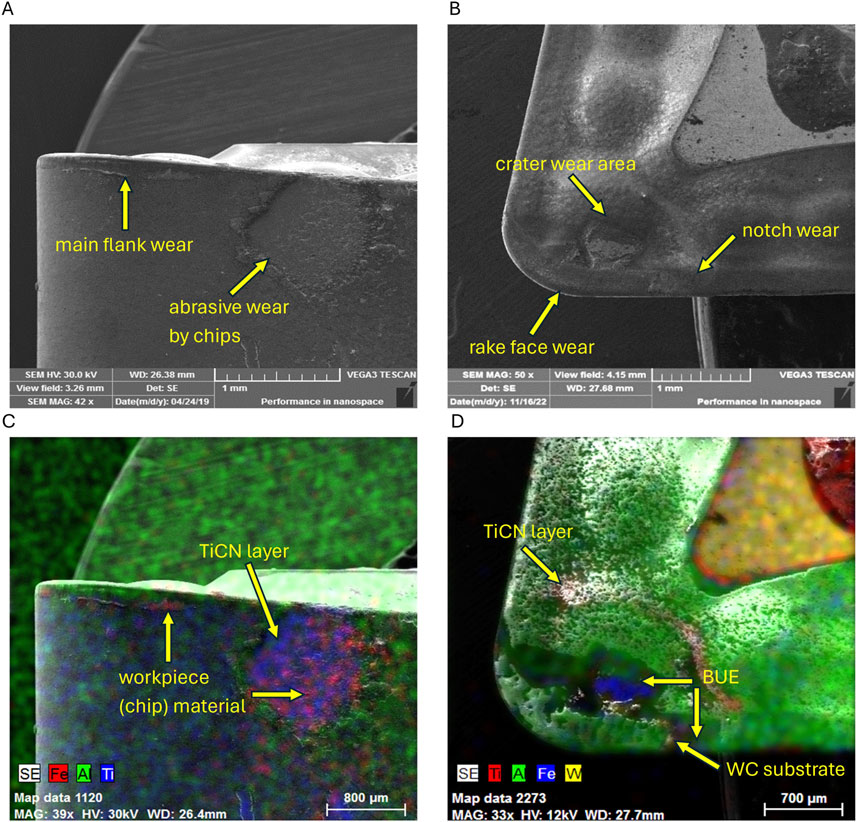
Figure 9. (A) SEM analysis of worn main flank. (B) SEM analysis of worn rake face. (C) EDX analysis of worn main flank. (D) EDX analysis of worn rake face.
3.2 Produced chips
Simultaneously with the detection of the degree of wear of the examined inserts as a function of the tool time in the shot, the produced chips were collected according to the same methodology described in subsection 3.1.
The data presented in Table 4 show the differences in the shape and length of the chips produced for the complete experimental section. Since the cutting tool-material contact interface is continuously changing due to cutting edge wear and cyclic adhesion of workpiece material, the evolution of chip size relative to a given indexable insert was also placed in the context of the time the cutting tool spent in engagement. The progression of changes in the average chip lengths produced for a given insert is visualized in Figure 10.
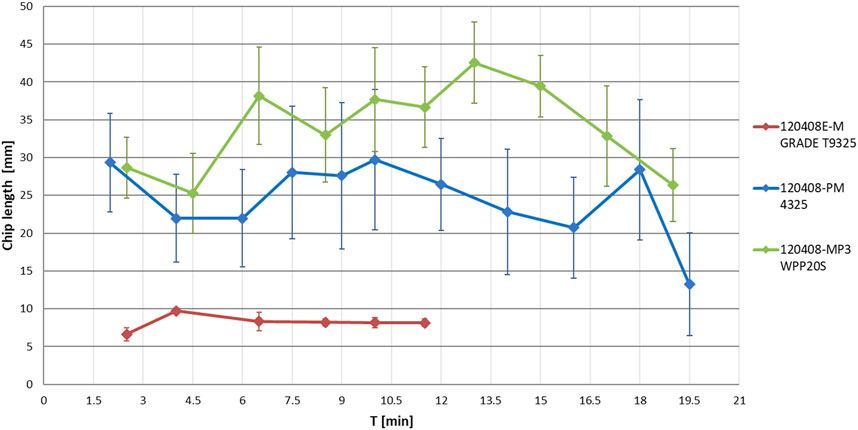
Figure 10. Chip length progression according to machining time of investigated cutting inserts for 1.6582 steel, vc 80 m min−1.
3.3 Discussion of the data obtained
The following obvious results emerge from the data obtained. In terms of the cutting edge life of the examined indexable inserts, or the time to reach the specified critical wear, the PM 4325 insert performs best with a time of 19.5 min, see Figure 6. The wear identified on the insert surface is consistent with carbide sintered tools, except for the local chipping of the cutting edge. This has multiple causes, most commonly high tensile stresses on the cutting edge caused by high cutting parameters, cyclic stresses from chip formation, and the presence of inclusions or BUE. Due to the EDX analysis using SEM, a correlation between chipping and BUE is observed just near the cutting edge on the tool rake face, see Figure 8D. In contrast to the other inserts examined, PM 4325 has an applied Al2O3 layer to protect against thermal stress approximately half the size of the TiCN layer, which protects the surface against mechanical abrasion. This may be related to the nature of the types of wear observed, due to the distribution of heat at the cutting point to the surrounding area, specifically part of it to the cutting tool mass. The thickness of the coating layers is known to influence the wear pattern of the cutting tool, however, an increase in thickness does not necessarily mean an increase in wear resistance (Vereschaka et al., 2021). Within the parameters of the experiment, the disposition of the coated layers of the PM 4325 insert appears to have proven to be effective.
The MP3 WPP20S insert is in second place in terms of edge life evaluation with a time of 17.4 min, see Figure 5. The difference in reaching the specified critical value of the main flank wear VBmax = 0.3 mm is therefore not significant. The observed wear patterns on the tool’s main flank and rake face again correspond to those of sintered carbide tools. Compared to the PM 4325 insert, a lower amount of BUE and less exposure of the substrate underneath the coating layers can be observed, see Figure 9. This is probably due to the relatively thick protective layers of Al2O3 and TiCN compared to the other investigated inserts, see Figure 3A. It is possible to account for the factor of changes in the internal structure of the coatings during their growth as part of the wear rate (Ophus et al., 2010; Dulmaa et al., 2021). Differences in the cutting geometry of the tool can also be added to the observed wear rates - for example, the apparent difference in cutting edge angle, see Figure 3B, despite the generally identical markings with the other CNMG 120408 inserts according to ISO 6987.
The worst result in the experiment was achieved by the indexable cutting insert E-M T9325 with a cutting edge life of 10.8 min. Flank wear and rake face wear are characteristics of sintered carbide cutting tools, in this case with higher rake face wear to the level of the substrate, see Figure 6. Notch wear identified at the tool/workpiece interface was more significant in contrast to the other inserts investigated. The observed wear rate, as well as the relative shortness of the time to reach the specified critical wear rate of the main spine (almost half that of the other inserts tested), is most likely due to the weaker protection provided by the coating layers. These were applied in the same order, i.e., Al2O3 against thermal stress and TiCN to increase wear resistance, but with a significantly lower thickness of TiCN compared to PM 4325 and E-MP3 WPP20S, see Figure 1A. Lower coating thicknesses of Al2O3 were also measured compared to PM 4325 and E-MP3 WPP20S. The applied thicknesses of the individual coatings below 10 µm of the E-M T9325 insert, apparently influenced the shortest cutting edge life within the experiment, which has also been observed in other experiments (Vereschaka et al., 2021).
In addition to the course of wear, the formation of chips in terms of their shape and size was monitored in relation to the development of wear of the observed inserts. The suitability of the formed chips is classified according to ISO 3685. In terms of chip suitability for handling and waste material management, the best results were achieved by the E-M T9325 insert. During its application, an arch loose chip was formed with a constant average length of 8.2 ± 0.7 mm throughout the monitored working section, see Figure 10. In contrast, the PM 4325 and E-MP3 WPP20S inserts showed more than twice worse results in terms of average chip length. Even though the type of chips formed by the E-M T9325 insert falls into the group of ideal cases, abrasive wear was identified by the chip leaving the cutting point. However, it should be noted that the shaped chip generally has a higher hardness than the original unmachined material and specifically the E-M T9325 insert has the weakest coating on the supporting WC-Co substrate of all the inserts examined. This implies that the heat produced during the machining process cannot be dissipated in a certain amount by the tool material (which is primarily undesirable) and in the case of stronger tool protection by the Al2O3 coating, it must be dissipated more by other participants in the cutting process, including the chip, which may affect its plasticity during forming and may initiate the formation of longer chips.
The PM 4325 insert formed an arch loose and arch connected chip 24.6 ± 4.8 mm long on average during the cutting process, however, during the machining process the chip length overwhelmingly oscillated between 20 and 30 mm. These types of chips are not ideal in contrast to the chips formed by the E-M T9325 insert, and even in this case, wear of the main spine surface caused by abrasion of the chip as it left the forming site was documented.
In terms of chip formation, the E-MP3 WPP20S insert produced the worst results, producing chips of the arch loose, arch connected and tubular short types with an average length of 34.1 ± 5.5 mm with a length oscillation between 25 and 45 mm. Arch connected and tubular short chips of greater length are not desirable, especially in the latter case where there is a risk of the twisted chip returning to the point of origin under the cutting edge, which could cause destruction of the cutting edge. A possible reason for this result could be that abrasive wear of the main tool flank below the chip exit point from the workpiece/tool interface area showed the highest intensity.
During machining, the component of energy required to overcome friction in the system of tool-chip-workpiece surfaces is almost completely transformed into heat and increases the temperature of the tool surface, which is one of the basic principles of machining. The connection between the thickness and composition of the coating and the temperature at the cutting point confirms the hypothesis about the influence of the thickness of the coating on the formation of the chip in terms of the distribution of thermal energy, and thus its resulting shape and size (Bobzin et al., 2021). The strength of the coating is also related to the distribution of the cutting force and with the sequence of the coating-thickness dependent resultant compressive residual stress, which increases with greater thickness of coating layer. Therefore, a thick coating thickness does not always have to be advantageous for a given machining process (Zhao et al., 2022). The number of chips per 100 g of chips collected was calculated analogously to the average length of chips collected. This value gives a more realistic view of the set of waste produced within the whole. For the E-M T9325 insert, which formed the most user-optimal type and length of chips, a value of 2,392 ± 259 chips per 100 g of chips was obtained. The PM 4325 insert with 1,494 ± 401 chips per 100 g of chips and the MP3 WPP20S with 1,520 ± 350 chips per 100 g of chips were significantly lower. From this and the above, the average chip length is important information in terms of the machining process, its manufacturability and safety. However, from the point of view of the further management of the waste material in the form of chips, the average length of the chips produced is not so important, since as an average value it may lead to misleading conclusions about the real composition of the chips produced, which is important information for the waste management sector.
Since the primary factor for the user of the insert is the possibility of using it for the longest possible time in terms of the quality properties of the workpiece, the life of the insert, or its cutting edge, is often prioritized over the optimal shape and length of the chip produced, unless these are a safety risk for the machining process itself. Similarly, the demands or costs of processing waste in the form of chips are neglected. However, in view of the constant optimization of engineering production and its outputs, it is good to look for options that are as close as possible to the positive extremes in several chip machining criteria. We can definitely recommend the continuation of a closer study of the properties of the coatings applied to the investigated inserts, such as the Vickers microhardness of the individual layers, as well as heat distribution using a thermal camera or thermocouple method. The hardness value of the layer (e.g., TiCN) is key to determining the ability to resist mechanical wear. For this, it would be possible to use the methods of nanoindentation or nanoscratch (Fischer-Cripps et al., 2006). In this way, it would be possible to partially test the adhesion between the individual components of the coating protection, the consistency of which also has an effect on wear resistance (Chen et al., 2010). At the same time, the ability to withstand heat and eventually dissipate it into the environment plays a role, which is significantly related to friction (Chamani and Majid, 2018).
It would also be useful to supplement the study with monitoring of cutting forces using a dynamometer. Data obtained using a dynamometer due to the consideration of the variability of the genesis of coatings can enable the use of the tool load measurement method and the analysis of the machining process using mathematical-physical models, providing a whole range of other useful parameters (Píška and Humár, 2001). However, it is evident that the parameters monitored as part of the experiment indicate that, based on the proportional nuances of the cutting edge geometry and the applied coatings, significantly different wear courses of indexable cutting inserts can be expected despite the unified marking using ISO 3687.
Due to the information obtained regarding the different parameters of the coatings, it is recommended to monitor the surface roughness of the functional surfaces of the cutting tool. The roughness of the surface also increases with a greater thickness of the coating, therefore there is a greater occurrence of unevenness, which under certain cutting conditions initiates the formation of point adhesion joints. They can be cyclically broken off and created again. The increased roughness of the functional surface due to the thick of the coating layer could be one of the factors that influenced the worse results of MP3 WPP20S compared to PM 4325. Fine wear debris can cause plastic deformation that gradually increases the actual contact area between the workpiece and tool surface (coating), resulting in the continuous formation and growth of additional adhesive points. These adhesive points prevent the ingress of the process fluid and the mutual sliding of the contact surfaces, which can cause fluctuations in the friction curve (Zhao et al., 2022; Bai et al., 2024).
4 Conclusion
A study was carried out on the wear of CNMG 120408-type indexable inserts from three different manufacturers. The continuously monitored parameter was the wear of the main flank of the tool VBmax, whose critical limit was set at 0.3 mm. Simultaneously with the wear history, a sample of the produced chips was taken and evaluated for shape and size according to ISO 3685 in relation to tool wear during machining. Steel 1.6582 according to EN 10027–2, hardened to 40–44 HRC, was chosen as the test material. The expansion of the subject area compared to other published materials of a similar focus is, in addition to the mutual comparison of the life of the cutting edge depending on construction differences undefined by the ISO 6987 standard, and the relationship between the deposited coating layers, as well as the correlation of the utility properties of the selected inserts, such as their tool life and the form of the produced chip, which it is precisely related to the realization of coatings on functional surfaces examined by SEM. The following conclusions can be drawn from the results obtained in the experiment.
i: Based on the continuous wear monitoring, it can be concluded that the longest life of cutting edge was achieved by the PM 4325 insert with a time T = 19.5 min. This was followed by the MP3 WPP20S insert with T = 17.4 min. In the experiment, the E-M T9325 indexable insert achieved the shortest life of cutting edge with time T = 10.8 min.
ii: Elemental analysis using SEM was used to identify differences in the coating layers applied to the tool substrate. The design and distribution of these layers, together with the geometric differences of the functional surfaces and chip breaker, have a direct impact on the wear process, the lifetime of the cutting edge, and the occurrence and severity of the different types of wear characteristic of cutting tools made of sintered carbide. However, the lifetime of the cutting edge cannot be predicted based on the thickness of the individual layers. The largest thickness of coatings of the MP3 WPP20S insert did not ensure the longest tool life under the given cutting conditions, and at the same time, a rapid difference in the life of PM 4325 and E-M T9325 was observed with relatively small differences in coating thicknesses.
iii: Based on continuous monitoring of the produced chips shape and size, individual chip types were identified that were suitable for machining only by testing of E-M T9325 insert. The PM 4325 and MP3 WPP20S inserts did not produce ideal chips either in terms of shape or length, and there were significant variations in the dimensional continuity of the produced chips.
iv: While the greater thickness and distribution of deposited layers may have a positive effect of protecting the tool cutting edge from thermal stress and abrasion from the workpiece material, for the purpose of optimally shaped chips under given cutting conditions, it could on the contrary have a negative impact in terms of their size and shape due to less distribution of heat generated during machining into the tool mass. In the case of stronger tool protection by Al2O3 coating, a larger proportion of the heat must be dissipated by the chip, which may affect its plasticity and solidification in longer lengths.
v: In addition to the setting up of the machining process itself, the information on the size and shape of the chip is important for the further management of the waste generated by the machining technology. However, a more precise figure is the amount of chips per 100 g of chips formed, which is not linked to the average length of the chips formed but defines the average number of chips formed for better planning in terms of waste product management capacity. The smaller this parameter is, the larger, respectively longer chips have to be transported from the production site and processed, thus reducing the efficiency of waste material management, as the use of transport and processing space is reduced by less densification of the chip material.
vi: As part of the experiment, data on the wear process of selected CNMG 102408 type inserts were obtained and the chips produced by these inserts were evaluated simultaneously. However, the results of these data show conflicting trends in terms of the achieved cutting edge life and optimally formed chips. If the given conditions were to occur in real production, the manufacturer would have to give priority to one of the priorities. Either use a cutting insert with a longer service life and take measures for the safe removal of chips from the machining area or use a cutting insert with better chip formation but with a lower service life.
vii: Based on the observed differences in performance between the indexable cutting inserts, further research into the properties of individual coating layers can be recommended, as these will probably have a significant effect on the course of wear and, at the same time, a non-negligible effect on the formation of chips.
Data availability statement
The original contributions presented in the study are included in the article/Supplementary Material, further inquiries can be directed to the corresponding author.
Author contributions
KŠ: Conceptualization, Data curation, Formal Analysis, Funding acquisition, Investigation, Methodology, Project administration, Resources, Supervision, Visualization, Writing–original draft, Writing–review and editing. PKa: Conceptualization, Data curation, Formal Analysis, Funding acquisition, Investigation, Methodology, Visualization, Writing–original draft, Writing–review and editing. PČ: Conceptualization, Data curation, Formal Analysis, Investigation, Visualization, Writing–original draft, Methodology, Resources, Supervision, Writing–review and editing. PKí: Conceptualization, Data curation, Methodology, Supervision, Visualization, Writing–original draft, Writing–review and editing. FŠ: Conceptualization, Investigation, Methodology, Resources, Supervision, Visualization, Writing–original draft, Writing–review and editing. RH: Conceptualization, Visualization, Writing–review and editing, Data curation, Investigation. TZ: Conceptualization, Data curation, Formal Analysis, Methodology, Project administration, Resources, Writing–review and editing. VV: Conceptualization, Formal Analysis, Methodology, Project administration, Resources, Supervision, Visualization, Writing–review and editing.
Funding
The author(s) declare that financial support was received for the research, authorship, and/or publication of this article. This research was funded by Supported by the OP VVV Project Development of new nano and micro coatings on the surface of selected metallic materials-NANOTECH ITI II., Reg. No. CZ.02.1.01/0.0/0.0/18_069/0010045.
Conflict of interest
The authors declare that the research was conducted in the absence of any commercial or financial relationships that could be construed as a potential conflict of interest.
Publisher’s note
All claims expressed in this article are solely those of the authors and do not necessarily represent those of their affiliated organizations, or those of the publisher, the editors and the reviewers. Any product that may be evaluated in this article, or claim that may be made by its manufacturer, is not guaranteed or endorsed by the publisher.
Supplementary material
The Supplementary Material for this article can be found online at: https://www.frontiersin.org/articles/10.3389/fmats.2024.1432039/full#supplementary-material
References
Aneiro, F. M., Coelho, R. T., and Brandão, L. C. (2008). Turning hardened steel using coated carbide at high cutting speeds. J. Braz. Soc. Mech. Sci. Eng. 30 (2). doi:10.1590/s1678-58782008000200002
Astakhov, V. P. (2004). The assessment of cutting tool wear. Int. J. Mach. Tools Manuf. 44 (6), 637–647. doi:10.1016/j.ijmachtools.2003.11.006
Bai, C., Liu, T., Shi, L., Song, L., Li, Y., Su, R., et al. (2024). Effect of different Mg2Si concentrations on the wear properties and microstructure of Mg2Si/al–5 Wt. % Cu composites. Int. J. Metalcasting. doi:10.1007/s40962-024-01321-9
Barry, J., and Gerald, B. (2002). The mechanisms of chip formation in machining hardened steels. J. Manuf. Sci. Eng. 124 (3), 528–535. doi:10.1115/1.1455643
Bhuiyan, M. S. H., Choudhury, I. A., and Dahari, M. (2014). Monitoring the tool wear, surface roughness and chip formation occurrences using multiple sensors in turning. J. Manuf. Syst. 33 (4), 476–487. doi:10.1016/j.jmsy.2014.04.005
Bi, Z. M., and Wang, L. (2012). Optimization of machining processes from the perspective of energy consumption: a case study. J. Manuf. Syst. 31 (4), 420–428. doi:10.1016/j.jmsy.2012.07.002
Bobzin, K. (2017). High-performance coatings for cutting tools. CIRP J. Manuf. Sci. Technol. 18, 1–9. doi:10.1016/j.cirpj.2016.11.004
Bobzin, K., Brögelmann, T., Kruppe, N. C., Carlet, M., Hoffmann, D. C., Breidenstein, B., et al. (2021). HPPMS tool coatings: chip Formation and friction. Vakuum Forschung und Praxis 33 (4), 26–33. doi:10.1002/vipr.202100765
Bradley, J. W., Mishra, A., and Kelly, P. J. (2015). The effect of changing the magnetic field strength on HIPIMS deposition rates. J. Phys. D Appl. Phys. 48 (21), 215202. doi:10.1088/0022-3727/48/21/215202
Branco, R., Costa, J. D., and Antunes, F. V. (2012). Low-cycle fatigue behaviour of 34CrNiMo6 high strength steel. Theor. Appl. Fract. Mech. 58 (1), 28–34. doi:10.1016/j.tafmec.2012.02.004
Canadian Metalworking (2013). Downsize your turning inserts. Canadian Metalworking. Available at: https://www.canadianmetalworking.com/canadianmetalworking/blog/cuttingtools/downsize-your-turning-inserts.
Chamani, H. R., and Majid, R. A. (2018). Prediction of friction coefficients in nanoscratch testing of metals based on material flow lines. Theor. Appl. Fract. Mech. 94, 186–196. doi:10.1016/j.tafmec.2018.02.004
Chen, Y., Bakshi, S. R., and Agarwal, A. (2010). Correlation between nanoindentation and nanoscratch properties of carbon nanotube reinforced aluminum composite coatings. Surf. Coatings Technol. 204 (16–17), 2709–2715. doi:10.1016/j.surfcoat.2010.02.024
Dahmus, J. B., and Gutowski, T. G. (2004). “An environmental analysis of machining,” in Manufacturing engineering and materials handling engineering. doi:10.1115/imece2004-62600
Denkena, B., Michaelis, A., Herrmann, M., Pötschke, J., Krödel, A., Vornberger, A., et al. (2020). Influence of tool material properties on the wear behavior of cemented carbide tools with rounded cutting edges. Wear 456-457, 203395. doi:10.1016/j.wear.2020.203395
Ducros, C., Benevent, V., and Sanchette, F. (2003). Deposition, characterization and machining performance of multilayer PVD coatings on cemented carbide cutting tools. Surf. Coatings Technol. 163-164, 681–688. doi:10.1016/s0257-8972(02)00656-4
Dulmaa, A., Cougnon, F. G., Dedoncker, R., and Depla, D. (2021). On the grain size-thickness correlation for thin films. Acta Mater. 212, 116896. doi:10.1016/j.actamat.2021.116896
EN 10027-2: 2015 (2015). Designation systems for steels-Part 2: numerical system. Brussels, Belgium: CEN.
Fischer-Cripps, A. C., Karvánková, P., and Vepřek, S. (2006). On the measurement of hardness of super-hard coatings. Surf. Coatings Technol. 200 (18–19), 5645–5654. doi:10.1016/j.surfcoat.2005.07.096
Hsu, C.-H., Lu, J.-K., and Tsai, R.-J. (2005). Effects of low-temperature coating process on mechanical behaviors of adi. Mater. Sci. Eng. A 398 (1-2), 282–290. doi:10.1016/j.msea.2005.03.092
Isakov, E. (2014). ANSI B212.4-2002: Indexable Inserts Identification Guide with Shapes, Tolerances, and Kennametal Systems. Cut. Tool. Eng. Available at: https://www.ctemag.com/articles/ansi-b2124-2002-indexable-inserts-identification-guide-shapes-tolerances-and-kennametal (Accessed November 27, 2024).
Janásek, A., Čep, R., Čepová, L., Kratochvíl, J., Vrba, V., and Petřkovská, L. (2012). Tool life reliability of indexable cutting inserts. Technol. Eng. 9 (2), 30–34. doi:10.2478/teen-2012-0008
Janeková, M., Koštialiková, D., Dubec, A., Burget, M., and Pešlová, F. (2018). The heat treatment impact on material properties of 34CRNIMO6 steel. Manuf. Technol. 18 (6), 912–916. doi:10.21062/ujep/200.2018/a/1213-2489/mt/18/6/912
Krar, S. F., and Gill, A. (2003). Exploring advanced manufacturing technologies. New York: Industrial Press.
Kuntoğlu, M., and Sağlam, H. (2019). Investigation of progressive tool wear for determining of optimized machining parameters in turning. Measurement 140, 427–436. doi:10.1016/j.measurement.2019.04.022
Leksycki, K., Feldshtein, E., Królczyk, G. M., and Legutko, S. (2020). On the chip shaping and surface topography when finish cutting 17-4 Ph precipitation-hardening stainless steel under near-dry cutting conditions. Materials 13 (9), 2188. doi:10.3390/ma13092188
Marko, H., Simon, K., Tomaz, I., Matej, P., Joze, B., and Miran, B. (2014). Turning parameters optimization using particle swarm optimization. Procedia Eng. 69, 670–677. doi:10.1016/j.proeng.2014.03.041
Maropoulos, S., Ridley, N., and Karagiannis, S. (2004). Structural variations in heat treated low alloy steel forgings. Mater. Sci. Eng. A 380 (1–2), 79–92. doi:10.1016/j.msea.2004.03.053
Martan, J., and Beneš, P. (2012). Thermal properties of cutting tool coatings at high temperatures. Thermochim. Acta 539, 51–55. doi:10.1016/j.tca.2012.03.029
Mitchell, J. (2013). “Downsize Your Turning Inserts,” in Canadian Metalworkings. Elgin, IL, USA: Tungaloy Canada. Available at: https://www.canadianmetalworking.com/canadianmetalworking/blog/cuttingtools/downsize-your-turning-inserts.
Nagode, A., Resnik, A., Bizjak, M., Kosec, G., Karpe, B., Budak, I., et al. (2016). Development of banded microstructure in 34CrNiMo6 steel. Metallurgy 55 (3), 329–332. https://hrcak.srce.hr/153612.
Nordin, M., Larsson, M., and Hogmark, S. (1998). Mechanical and tribological properties of multilayered PVD tin/CRN, tin/Mon, tin/NBN and tin/tan coatings on cemented carbide. Surf. Coatings Technol. 106 (2-3), 234–241. doi:10.1016/s0257-8972(98)00544-1
Ophus, C., Luber, E. J., and Mitlin., D. (2010). Analytic description of competitive grain growth. Phys. Rev. E 81 (1), 011601. doi:10.1103/physreve.81.011601
Píška, M., and Humár, A. (2001). Testování PVD povlaků na rychlořezných vrtácích (1. část). MM Průmyslové spektrum 10, 58–61. Available at: https://www.mmspektrum.com/clanek/testovani-pvd-povlaku-na-rychloreznych-vrtacich.
Prengel, H. G., Jindal, P. C., Wendt, K. H., Santhanam, A. T., Hegde, P. L., and Penich, R. M. (2001). A new class of high performance PVD coatings for carbide cutting tools. Surf. Coatings Technol. 139 (1), 25–34. doi:10.1016/s0257-8972(00)01080-x
Prengel, H. G., Pfouts, W. R., and Santhanam, A. T. (1998). State of the art in hard coatings for carbide cutting tools. Surf. Coatings Technol. 102 (3), 183–190. doi:10.1016/s0257-8972(96)03061-7
Reis, B. C., Júnior dos Santos, A., Fernanda dos Santos, N., Araújo Câmara, M., Faria, P. E. de, and Mendes Abrão, A. (2019). Cutting performance and wear behavior of coated cermet and coated carbide tools when turning AISI 4340 steel. Int. J. Adv. Manuf. Technol. 105 (1-4), 1655–1663. doi:10.1007/s00170-019-04392-9
Sai, W. B., Zghal, A., and Ben Ayed, K. (2005). Carbide and ceramic tool life in high speed turning. Int. J. Veh. Des. 39 (1/2), 140. doi:10.1504/ijvd.2005.007225
Schintlmeister, W., Wallgram, W., Kanz, J., and Gigl, K. (1984). Cutting tool materials coated by chemical vapour deposition. Wear 100 (1-3), 153–169. doi:10.1016/0043-1648(84)90011-5
Sheikh-Ahmad, J., and Davim, J. P. (2012). “Tool wear in machining processes for composites,” in Machining technology for composite materials, 116–153. doi:10.1533/9780857095145.1.116
Sohal, G. S., and Eyada, O. K. (1989). “An expert system for the selection of indexable inserts and tool holders,” in Proceedings of the 2nd international conference on Industrial and engineering applications of artificial intelligence and expert systems, 1, 417–421. doi:10.1145/66617.66668
Su, G., Liu, Z., Li, L., and Wang, B. (2015). Influences of chip serration on micro-topography of machined surface in high-speed cutting. Int. J. Mach. Tools Manuf. 89, 202–207. doi:10.1016/j.ijmachtools.2014.10.012
Suresh, R., Basavarajappa, S., Gaitonde, V. N., and Samuel, G. L. (2012). Machinability investigations on hardened AISI 4340 steel using coated carbide insert. Int. J. Refract. Metals Hard Mater. 33, 75–86. doi:10.1016/j.ijrmhm.2012.02.019
Vereschaka, A., Volosova, M., Sitnikov, N., Milovich, F., Andreev, N., Bublikov, J., et al. (2021). Influence of the thickness of nanolayers in wear-resistant layer of Ti-tin-(Ti, Cr, al)n coating on the tool life and wear pattern of the carbide cutting tools in steel turning. Procedia CIRP 101, 262–265. doi:10.1016/j.procir.2021.02.027
Viharos, Z. J., Markos, S., and Szekeres, C. (2003). “ANN-based chip-form classification in turning,” in Metrology in the 3rd millennium: XVII IMEKO world congress, 1469–1473.
Wijanarka, B. S., Nuchron, N., Rahdiyanta, D., and Habanabakize, T. (2018). The task of machine tool operators in small and medium enterprises in Indonesia. J. Pendidik. Teknol. Dan. Kejuru. 24 (1), 39–45. doi:10.21831/jptk.v24i1.18004
Woody, B. A., Scott Smith, K., Adams, D. J., and Barkman, W. E. (2008). “Assessment of the process parameters and their effect on the chip length when using CNC toolpaths to provide chip breaking in turning operations,” in ASME 2008 international manufacturing science and engineering conference, 1, 533–540. doi:10.1115/msec_icmp2008-72468
Wu, D., Jennings, C., Terpenny, J., Gao, R. X., and Kumara, S. (2017). A comparative study on machine learning algorithms for smart manufacturing: tool wear prediction using random forests. J. Manuf. Sci. Eng. 139 (7). doi:10.1115/1.4036350
Xu, Q., Liu, J., Cai, G., Jiang, D., and Zhou, J. (2021). A fuzzy evaluation of tool materials in the turning of marine steels. Metals 11 (11), 1710. doi:10.3390/met11111710
Yılmaz, B., Karabulut, Ş., and Güllü, A. (2020). A review of the chip breaking methods for continuous chips in turning. J. Manuf. Process. 49, 50–69. doi:10.1016/j.jmapro.2019.10.026
Keywords: tool wear, coated carbide layers, indexable inserts, hardened steel, chip evaluation, SEM, turning
Citation: Šramhauser K, Kraus P, Černý P, Kříž P, Špalek F, Horký R, Zoubek T and Vochozka V (2024) Comparative flank wear and produced chips types analysis of CNMG 120408 indexable cutting inserts after machining hardened 1.6582 steel. Front. Mater. 11:1432039. doi: 10.3389/fmats.2024.1432039
Received: 13 May 2024; Accepted: 11 November 2024;
Published: 05 December 2024.
Edited by:
Nicola Maria Pugno, University of Trento, ItalyReviewed by:
Mahmoud Ebrahimi, University of Maragheh, IranShuiquan Huang, Yanshan University, China
Copyright © 2024 Šramhauser, Kraus, Černý, Kříž, Špalek, Horký, Zoubek and Vochozka. This is an open-access article distributed under the terms of the Creative Commons Attribution License (CC BY). The use, distribution or reproduction in other forums is permitted, provided the original author(s) and the copyright owner(s) are credited and that the original publication in this journal is cited, in accordance with accepted academic practice. No use, distribution or reproduction is permitted which does not comply with these terms.
*Correspondence: Karel Šramhauser, c3JhbWhhdXNlckBmenQuamN1LmN6