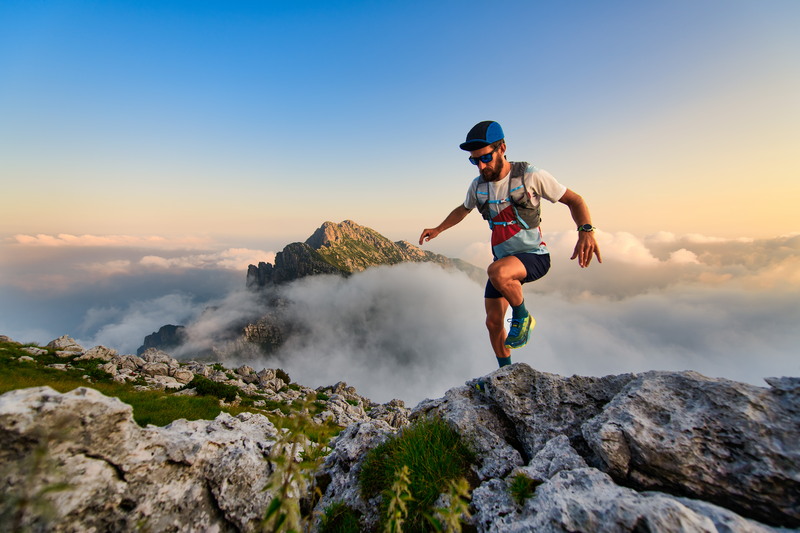
95% of researchers rate our articles as excellent or good
Learn more about the work of our research integrity team to safeguard the quality of each article we publish.
Find out more
ORIGINAL RESEARCH article
Front. Mater. , 14 March 2024
Sec. Polymeric and Composite Materials
Volume 11 - 2024 | https://doi.org/10.3389/fmats.2024.1267197
This article is part of the Research Topic 2022 Retrospective: Polymeric and Composite Materials View all 7 articles
The hydration reaction of mass concrete seriously endangers the structural safety. At present, the concrete production relies excessively on fly ash due to hydration reaction. In view of the problem that the demand of fly ash exceeds the supply, this paper proposes to use dacite powder to partially replace fly ash as the raw material for preparing cementitious materials. Through comprehensive tests and microstructure tests, various properties of dacite powder and fly ash composite cementitious materials are studied. The results show that: 1. The dacite powder with a specific surface area of 650 m2/kg, a fineness of 15% under laser particle size and a ball-milling time of 1.0 h has the best performance. 2. It is advisable to mix dacite powder and fly ash. The total amount of dacite powder should not exceed 30% of the cementitious material. It has the best performance when the amount of dacite powder and fly ash is the same. 3. The alkali activity of aggregate can hardly be inhibited by mixing dacite powder alone. The recommended measures to inhibit the alkali activity of aggregate are: i) mixing more than 20% fly ash alone. ii) mixed with 25% dacite powder and more than 15% fly ash.
During the hardening process of concrete, hydration heat reactions occur and a large amount of heat is released (Lv et al., 2022). For mass concrete, the internal and external heat dissipation conditions are different. The speed of surface temperature reduction is fast while the speed of internal is slow, resulting in temperature gradients in the concrete and the formation of temperature stress which lead to temperature cracks (Zhang et al., 2018; Su, 2020). It seriously endangers structural safety especially in concrete dams in water conservancy and hydropower projects in that these cracks will directly affect the anti-seepage performance, thus bringing huge risks. As long as it is a concrete component, cracking cannot be avoided. Therefore, the hydration reaction solution of mass concrete is one of the key issues in studying concrete materials. Many methods have been explored in engineering, such as installing cooling water pipes inside the concrete, controlling the temperature during concrete pouring and strengthening construction management (Deng, 2019; Wang, 2020).
These measures are all external measures rather than improvements aimed at the concrete material itself. This paper believes that the relationship between hydration heat and cement is the closest. Therefore, as long as the cement dosage or proportion can be reduced, the problem of temperature cracks in concrete caused by hydration reaction can be fundamentally solved. Researchers are searching for various materials to reduce cement consumption. Currently, the most mature alternative is fly ash, such as the three Gorge Hydropower Station on the Yangtze River in China, which has successfully reduced the phenomenon of dam cracking by the application of fly ash. Fly ash, together with other famous Volcanic ash additives, has been widely used in concrete to replace ordinary Portland cement (Hemalatha and Ramaswamy, 2017).
Fly ash is a solid waste generated by thermal power plants, which is recovered from the flue gas from coal combustion and has a low production rate. After adding fly ash particles to concrete to replace some cement, due to its chemical composition (Sun et al., 2022), not only can the strength of the concrete remain unchanged, but also many characteristics of the concrete can be improved, such as reducing concrete cracking (Hallal et al., 2010; Herath et al., 2020; Jiang et al., 2020). The most crucial thing is that the addition of fly ash reduces the amount of cement used, and the heat release of concrete is also reduced and delayed. Specifically, it delays the reaction of cement hydration heat, reduces the heat release in the early stage of cement and the total heat release throughout the entire life cycle, providing sufficient time for the formation of concrete strength (Zeng and Li, 2014; Zhao et al., 2015). Through extensive practice and exploration, people have gradually mastered the correct use of fly ash, making it an indispensable material in engineering construction (Feng et al., 2022). However, the project relies heavily on fly ash and is affected by low-carbon policies, resulting in a shortage of fly ash supply. Therefore, it is urgent to find alternative materials or materials that can partially replace fly ash.
(Al-Hashem et al., 2022) proposed using metakaolin as a substitute material for cement and conducted research on its mechanics and durability, suggesting that metakaolin may be a potential substitute material for concrete (Qureshi et al., 2022). proposed using red mud as a substitute for cement and conducted research on the mechanical properties, durability, microstructure and environmental impact, proving that it helps improve the mechanical properties and durability of concrete but reduces its fluidity (Zaid et al., 2021). proposed to add rice husk ash into cementitious materials as an admixture, studied the compressive strength, splitting tensile strength and flexural strength of the materials and made a microstructure evaluation, and proposed that this material has the potential to prepare high-performance concrete. Santana et al. (Santana et al., 2022) proposed to add natural Volcanic ash to modify concrete and studied the activity, durability, compressive strength and other aspects of Volcanic ash. They found that natural Volcanic ash materials have a negative impact on the life of concrete (Sun et al., 2022). added materials such as solid waste materials and found that they would reduce the compressive strength of concrete (Ruidong et al., 2021). proposed adding iron tailings powder to modify concrete is beneficial to the working performance of concrete and found that adding these materials would weaken the compressive strength of cementitious materials. It can be seen that various powder and construction waste materials have gradually become the mainstream of our research. For example, using porous ceramic waste as concrete aggregate to partially replace coarse aggregate (Amin et al., 2021). Using fiber-reinforced concrete produced with waste lathe fibers to assess the performance (Çelik et al., 2022). Using reinforced concrete beams produced with waste lathe scraps to improve bending performance (Karalar et al., 2022). Unfortunately, these studies either objectively described the phenomenon but did not prove that the material could replace fly ash, or some studies found that adding a certain material did not receive positive feedback. Some research areas are limited and only focus on the mechanical properties of materials, but many aspects have not been studied, which may have hidden shortcomings. Therefore, it is necessary to conduct comprehensive research (Li, 2020).
This paper proposes to use dacite powder instead of fly ash to modify concrete. At present, there is little research on dacite. studied the mechanical properties of dacite and carried out triaxial unloading tests. It is pointed out that the confining pressure difference and elastic modulus of the dacite decrease with the increase of the unloading rate (Wang et al., 2020). studied the damage of dacite under freeze-thaw cycle through numerical simulation and found that dacite presents brittle failure. These articles study the mechanical properties of dacite in its original rock state. However, the research on the micro level of the dacite is blank at present so it is urgent to carry out research to obtain the research data of dacite powder.
Dacite is a kind of volcanic ash rock. It has been proved that volcanic ash rock can improve durability. For instance, the effect of adding natural volcanic ash minerals on durability (Hunyak et al., 2019a)and the effect of blast furnace slag on durability (Markiv et al., 2016). It has also been proved that volcanic ash rock can reduce hydration heat (Najimi et al., 2008) after being added, but these data do not include dacite. Grinding process is an important processing step in studying stone powder, Krishnaraj L has studied the Impact of Chloride Grinding Aid with Modified Fly Ash using Topdown Nanotechnology on Grinding Performance (Krishnaraj and Ravichandran, 2019a). He also studied grinding impact of fly ash particles and its characterization analysis in cement mortar composites. (Krishnaraj and Ravichandran, 2019b). This paper conducts different ratio tests on dacite after ball-milling. The material after ball-milling has filling and water reducing effects, which can improve the mechanical and durability properties of the material (Supit et al., 2014).
This paper has carried out a lot of experimental studies on the physical and mechanical properties of cementitious materials mixed with dacite powder. The results show that 30% dacite can improve the workability of concrete. It has no effect on the setting time and mortar strength. It can improve impermeability and crack resistance. The most important thing is to reduce the adiabatic temperature rise of cement hydration heat. Therefore, dacite powder can be used as part of the alternative raw materials for fly ash. This solves the problem of temperature cracks caused by hydration reactions in mass concrete and the excessive reliance on fly ash in engineering construction. This study can provide reference for related research.
The dacite samples used in this research were mined from Tibet, China. Dacite naturally appears in large white blocks. As is shown in Figure 1.
The chemical composition of dacite is shown in Table 1.
The fly ash used in this experiment is Class F Grade II fly ash produced by Guizhou Panjiang Power Investment and Generation Company. Fly ash appears as a fine gray powder.
The performance test results of fly ash are shown in Table 2.
The cement used is ordinary Portland 42.5 cement produced by Tibet Kaitou Haitong Cement Company. The chemical composition analysis results of the cement are shown in Table 3 and the physical performance testing results are shown in Table 4.
The water for mixing and curing in this indoor mix proportion test is tap water of Guiyang City.
In this test, aggregates from dacite quarry are mainly used. The raw materials are taken from the site and transported back to Guiyang for processing artificial aggregates. The fine aggregate is artificial sand and the coarse aggregate is classified as small stone (5mm–20 mm), medium stone (20mm–40 mm), and large stone (40mm–80 mm). The test results of artificial sand are shown in Table 5. The test results of coarse aggregate are shown in Table 6.
The water reducer used in this experiment is GK-3000 polycarboxylic acid series high-performance water reducer produced by Shijiazhuang Chang’an Yucai Building Materials Company.
The performance testing results of GK-3000 polycarboxylic acid based high-performance water reducer are shown in Table 7.
The air entraining admixture used for normal concrete is GK-9A produced by Shijiazhuang Chang’an Yucai Building Materials Company. The performance test results of the air entraining admixture are shown in Table 8.
In this study, advanced XRD, SEM and other equipment are used to test and analyze the performance of cementitious materials. Through data analysis and research, the recommended amount of dacite powder is obtained when preparing cementitious materials.
The aggregate used in this test is dacite aggregate. According to the chemical composition results of Dacite in Table 1, the content of SiO2 in dacite is high and the aggregate has potentially harmful alkali reactivity.
Alkali aggregate reaction is known as the chronic cancer of concrete. It poses great harm to concrete. Its harm not only lies in greatly reducing the strength of concrete structures, but also leading to cracks, exacerbating corrosion and freeze-thaw damage, thereby greatly shortening the service life of concrete components. Therefore, it is essential to study the alkali activity of aggregates.
For the dacite aggregate in this project, the aggregate alkali activity test shall be carried out first to see whether there is alkali activity. If there is alkaline activity, separate tests should be conducted to suppress the alkaline activity of aggregates with different amounts of fly ash. The alkaline activity of aggregates is determined by using the mortar rod rapid method.
Dacite is grinded into artificial sand and then the artificial sand is ball milled at different time to obtain fine powders of different fineness. The activity of dacite powders at different ball milling time is studied. The proposed ball milling time of dacite fine powder is 0.5 h, 1.0h, 1.5 h and 2 h respectively.
In order to determine which milling time gets the best performance of dacite powder, the tests of dacite powder under different milling time were carried out. Therefore, the fineness control index of dacite powder is obtained.
Fluidity tests were carried out on cementitious materials prepared from dacite powders at different ball milling time to evaluate the effect of ball milling time on flow performance.
The activity of dacite powder at different grinding time was detected. The evaluation of activity is a curve chart with the Hydroxide ion concentration as the abscissa and the Calcium oxide concentration as the ordinate. The test results are plotted on the coordinate axis. If the test point falls below the curve, the activity test is considered as qualified.
In order to explore the influence of different proportions of fly ash and dacite powder on the heat release of cement hydration reaction, hydration heat tests of different proportions of cement were carried out.
The hydration heat and heat release rate of some representative samples (JZ, F50WF0, F25WF1.0h25, F0WF1.0h50) were measured using a TAM constant temperature microcalorimeter from the United States for 1 day, 2 days, and 3 days.
In order to explore the rule of the influence of different admixtures on the compressive strength of mortar, the mortar contrast test was adopted. The mortar mix ratio was designed as water binder ratio 0.5, mortar ratio 3:1 and the cement was low heat 42.5 cement. The gravel were taken from dacite in the project area.
In order to study the influence of dacite powder grinding time and content on the crack resistance of composite cementitious materials, the cement paste samples were prepared and the ring method crack resistance test was carried out. According to the combination design of parameter changes, the water binder ratio was 0.26. The dimensions of the test piece are: inner diameter 41.3 mm, outer diameter 66.7 mm and height 25.4 mm. Crack resistance tests were conducted to determine the time at which cracking occurs during the shrinkage process.
During the experiment, the appearance and development of shrinkage cracks were observed using the MG10085-1 reading microscope, and the width and length of the cracks were measured. The cracks are measured at positions 6 mm, 12 mm, and 18 mm away from the top surface of the sample, denoted as b1, b2, and b3. The average width of the cracks at each position is taken as the width of the crack.
Take the mortar sample after the mortar strength test and use absolute ethanol to stop the hydration. Break the sample and take a small section with the side length less than 8 mm at the center. Dry it in a vacuum drying box at 50°C to constant weight and spray gold on the sample surface. Use JSM-7610FPlus Scanning electron microscope to observe the microscopic morphology of cement hydration products.
The point scanning of pure cement mortar (JZ group), cement mortar mixed with fly ash alone (F50WF0 group) and cement mortar mixed with fly ash dacite powder (F30WF1.0h20 group) was carried out by using ULTIM MAX40 energy spectrum analyzer to observe the micro morphology and elemental distribution of the samples.
Take the mortar samples after the mortar strength test and use absolute alcohol to terminate hydration. Dry them in a vacuum drying oven for 24 h (drying temperature of 50 °C), then grind them to a particle size of less than 75 microns (200 mesh). Use a Japanese physics Rigaku/Smart Lab SE type XRD instrument for phase analysis.
The hydration reaction process of cement involves multiple minerals, generating complex hydration substances that have a significant impact on macroscopic properties. The hydration reaction equations of cement at each stage are shown in Equations 1–4 below.
In order to explore whether dacite powder can inhibit aggregate alkali activity, dacite powder with grinding fineness of 15% was used and mortar bar rapid method was selected to test the effect of dacite powder with different content on inhibiting aggregate alkali activity.
Scanning electron microscope was used to observe the microscopic morphology of each group of samples to evaluate the effect of dacite powder on the inhibition of alkali aggregate activity.
When detecting the alkali activity of aggregates, if the expansion rate of the samples is less than 0.1% after 14 days, the aggregates do not have activity. If the expansion rate of the samples is greater than 0.2% after 14 days, then the aggregate is a potentially harmful alkali active aggregate. If the expansion rate of the specimen is between 0.1% and 0.2% after 14 days, a comprehensive evaluation of this type of aggregate should be conducted in conjunction with on-site usage history, petrographic analysis and test results after the sample observation time has been extended to 28 days.
The alkali activity test results of dacite aggregates are shown in Figure 2.
The experimental results in Figure 2 indicate that the 14 days expansion rate results of all four groups of samples exceed 0.2%. Therefore, dacite aggregate is potentially harmful alkali activated aggregate.
When evaluating whether admixtures can effectively suppress harmful alkali aggregate reactions, if the expansion rate of the 28 days comparison samples is less than 0.1%, then the inhibitory effect of admixtures on the harm of alkali aggregate reactions is effective.
The calculation and analysis results of inhibition rate of aggregate alkali activity by fly ash alone are shown in Figure 3.
With a single addition of 15% or more fly ash, the expansion rate of the 28 days samples is less than 0.10%. Under this dosage, the suppression effect of fly ash on the alkali aggregate reaction harm of the aggregate is evaluated as effective. As the amount of fly ash increases, the inhibitory effect becomes better.
The principle of adding fly ash to suppress potential alkaline activity hazards is that the insoluble substance formed by the active silica in fly ash and the hydrated Ca (OH)2 in cement can further prevent the dissolution of SiO2. Therefore, the addition of fly ash reduces the effective alkali content in the concrete, and adsorbs the limited alkali to the particle surface of fly ash, so that its surface captures K+, Na+ and generates R-CSH gel, thus reducing or avoiding the probability of alkali participating in the alkali aggregate reaction. At the same time, the addition of fly ash reduces the content of Ca (0H)2, weakens the promoting effect of Ca (OH)2 on the alkali aggregate reaction, alleviates the formation of ettringite expansion phase, improves the compactness of the interface, and thus also plays a role in inhibiting the expansion of alkali aggregate reaction. And the higher the content of fly ash, the lower the expansion rate of mortar, the better its inhibitory effect on the alkaline activity of aggregates.
Due to the slightly higher 28 days expansion rate when the fly ash content is 15%, from a safety perspective, it is recommended to add 20% or more fly ash to make.
The test results of fineness, specific surface area, water demand ratio and strength activity index of dacite powder under different ball milling times are shown in Table 9.
TABLE 9. Test results of fineness, water demand ratio and strength activity index of dacite powder under different ball-milling time.
With the increase of ball-milling time, dacite powder becomes more broken.
Adding dacite powder is beneficial to the strength growth of cement-based cementitious materials. The strength activity index of dacite powder under different ball-milling time is more than 60%, which meets the requirements of Volcanic ash activity.
Laser Particle size analysis was carried out on dacite powder at different ball-milling time to study the effect of ball-milling time on particle distribution characteristics. The particle size analysis of dacite powder was analyzed by MASTERSIZER2000 laser particle size analyzer. The results of powder size distribution curve under different ball-milling time are shown in Figure 4.
When the ball-milling time is 0.5 h, the particle size shows a significant concentration and there are more large particle sizes with larger fineness.
When the ball-milling time is 1 h, the phenomenon of particle size concentration weakens, large particles decrease and the change in particle content is the largest.
Compared with 1 h, the ball-milling time of 1.5 h presents multimodal distribution but the particle size distribution has no obvious change.
After the ball-milling time reaches 2 h, the change in particle size content is relatively small. With only a small portion of the particle size content changing significantly, its rate of change is still smaller compared with the rate after 1 h ball-milling.
According to the above analysis and the actual situation of the project, it can be seen that the 1 h dacite powder curve basically presents normal distribution.
The flow test results of dacite powder cementitious materials under different ball-milling times are shown in Figure 5.
FIGURE 5. Experimental results of fluidity of dacite powder cementitious material system at different ball milling time: (A) Initial fluidity; (B) Fluidity after standing for 0.5 h.
Proper amount of dacite powder can improve the fluidity of cement paste and play a certain role in lubrication. However, with the increase of dacite powder content, the fluidity of cement paste decreases continuously and the fluidity of cement paste decreases approximately linearly with the increase of dacite powder content. After the cement slurry is left standing for 0.5 h, the fluidity loss rate of cement slurry mixed with dacite powder is less than that of pure cement slurry, which indicates that adding a certain amount of dacite powder is conducive to maintaining the fluidity of cement slurry.
With the increase of grinding time of dacite powder, the specific surface area of dacite powder increases and the fluidity of single dacite powder cement slurry decreases. Considering the working performance, dacite powder admixture with a particle size that is too small should not be used.
In order to verify the influence of dacite powder on the fluidity of cement-based materials, concrete tests were used to compare the influence of dacite powder admixtures on concrete slump under different ball-milling time. The test results are shown in Table 10.
TABLE 10. Effect of stone powder admixture on slump and compressive strength of concrete under different ball-milling time.
The test results indicate that:
Because the particles of fly ash are spherical and smooth under the microscope, its rolling lubrication effect is conducive to the slump of concrete. The lubrication effect is better than that of dacite powder.
The slump of concrete can be improved by adding appropriate amount and fineness of dacite powder. When 30% of dacite powder is added, the powder with ball-milling time of 0.5 h (fineness 39%) and 1.0 h (fineness 15%) lubricates the concrete. The powder with ball-milling time of 1.5 h (fineness 11.1%) and 2.0 h (fineness 5.7%) (i.e., finer dacite powder) slightly reduces the slump of concrete and blocks the concrete.
From the perspective of concrete compressive strength, the finer the fineness of dacite powder and the longer the grinding time, the higher the compressive strength of concrete. However, the proportion is not considerable, with an increase of 4.9% (2h/0.5 h), 3.0% (2h/1 h) and 2.2% (2h/1 h), respectively.
The activity test results of dacite powder with different grinding time and fineness are plotted as shown in Figure 6.
From Figure 6, it can be seen that:
The test result point A of dacite fine powder with grinding time of 0.5 h (i.e., fineness of 39%) falls above the curve which means that it is unqualified.
When the grinding time is 1.0 h (i.e., fineness 15%) and 1.5 h (i.e., fineness 11.1%), the test result points B and C of dacite powder fall below the curve which means it is qualified.
The activity of dacite powder has little change with the increase of grinding time.
The activity test results of dacite powder show that dacite powder has certain Volcanic ash activity characteristics after being ball-milled to a certain fineness. The fineness of qualified dacite fine powder in this test is 15%, which can be used as the fineness control index of dacite powder.
Dacite powder can be used as cementitious material together with cement and fly ash.
The 1-day, 2-day, and 3-dimensional hydration reaction heat release of some representative samples (JZ, F50WF0, F25WF1.0h25, F0WF1.0h50) was measured using the American TAM constant temperature microcalorimeter to obtain the heat release rate and cumulative heat release. The heat release rate and cumulative heat release curve is shown in Figure 7.
FIGURE 7. Hydration heat release curve: (A) Hydration heat release rate curve; (B) Accumulated heat release curve of hydration reaction.
From Figure 7, it can be seen that:
The peak time of hydration heat release of pure cement (JZ group), fly ash mixed alone (F50WF0 group), fly ash mixed with dacite powder (F25WF1.0h25 group) and dacite powder mixed alone (F0WF1.0h50 group) were 9.3 h, 13.5 h, 11.2 h and 9.8 h, respectively, indicating that the peak time of hydration heat release of cement was significantly delayed by the addition of dacite powder and fly ash.
The peak values of hydration heat release of the four groups are 2.45 mw/g, 1.35 mw/g, 1.42 mw/g and 1.47 mw/g, respectively, which indicates that adding dacite powder and fly ash can reduce the peak values of hydration heat release of cement.
The total amount of hydration heat release for the four groups at 72 h was 228.76 J/g, 131.42 J/g, 133.83 J/g and 143.12 J/g, respectively. It shows that the hydration heat release of cement is significantly reduced by adding dacite powder and fly ash. With the increase of dacite powder content (0%, 25%, 50% of the total cementitious material), the total heat release gradually increases, reaching the maximum at 50%, which is 37.44% lower than the control group.
The 72 h exothermic rates of the four groups were 0.19 mw/g, 0.11 mw/g, 0.14 mw/g and 0.12 mw/g, respectively, indicating that the hydration exothermic rate of cement was significantly reduced by adding dacite powder and fly ash. With the increase of dacite powder content (accounting for 0%, 25%, 50% of the total cementitious material), the exothermic rate first increased and then decreased, reaching the maximum when the dacite powder content was 25%, which was 26.32% lower than the control group.
This can be explained by the fact that the addition of dacite powder and fly ash reduces the cement content in the cementitious material, thus reducing the total heat release of cement hydration. Active substances in fly ash and dacite powder (such as silicic acid, aluminic acid, etc.) can react with Ca (OH)2 in cement to generate new hydration products and form new cementitious systems. These cementitious systems need to consume a certain amount of cement hydration heat, thus delaying the exothermic process of cement hydration reaction.
To investigate the variation of the influence of different admixtures on the compressive strength of mortar, a mortar comparison test was conducted. The mortar mix design was based on a water cement ratio of 0.5, a cement sand ratio of 3:1 and a low heat 42.5 cement. Sand is taken from the dacite quarry where the project is located. The compressive strength test results of mortar with different admixtures are shown in Figure 8.
The results of the mortar strength test in Figure 8 indicate that:
When adding fly ash alone, with the continuous increase of fly ash content at the same age, the compressive strength of mortar at each age decreases continuously.
The 7 days early strength of Dacite powder alone is higher than that of fly ash alone at the same dosage.
When dacite powder is added alone, the compressive strength of mortar at each age decreases with the increase of dacite powder content at the same age.
With the same amount of dacite powder, the mortar strength increases with the increase of ball-milling time of dacite powder, which indicates that the activity of dacite powder is related to its fineness. When the ball-milling time of dacite powder is more than 1.0 h, the compressive strength of mortar increases by about 0.5 MPa every 0.5 h increase in the ball-milling time of dacite powder. It indicates that when the fineness of dacite powder changes from finer to finer, although the activity increases slightly, however, the mortar strength increases slightly. Therefore, considering the use of cement-based materials mixed with dacite powder, the ball-milling time of dacite powder is suggested to be 1.0 h (that is, the fineness is controlled to be 15%).
Analysis of action mechanism of dacite powder in mortar cementation system: dacite powder plays a filling and nucleation role in cement mortar. On the one hand, dacite powder optimizes the gradation of mortar system, making the pore structure of cement mortar more compact. On the other hand, dacite powder has nucleation effect in cement-based materials. dacite powder, as a core, promotes the generation of cement hydration products and optimizes the pore structure of cement mortar. However, too much dacite powder will lead to poor workability of mortar, increased porosity of mortar, decreased compactness and decreased strength. When the content of dacite powder exceeds 30%, the compressive strength of mortar will decrease more compared with the benchmark mortar. Therefore, considering the strength development of cement-based materials mixed with dacite powder, the upper limit of the content of dacite powder alone is 30%.
It is advisable to mix dacite powder and fly ash. The high strength growth rate of fly ash in the later period can be used to make up for the defect of slightly low strength growth rate of dacite powder in the later period. The total content of dacite powder does not exceed 30% of the cementitious material and the best performance is achieved when the content of dacite powder is the same as that of fly ash.
The relationship between dacite powder grinding time and cracking performance evaluation index and the relationship between dacite powder content and cracking performance evaluation indexes are shown in Figure 9.
FIGURE 9. Relationship between dacite powder and evaluation index of cracking performance: (A) grinding time; (B) amount.
From the results in Figure 9, it can be seen that:
The grinding time of dacite powder (that is, different fineness) has obvious influence on the crack resistance of mortar. With the increase of dacite powder grinding time (that is, the fineness becomes finer), the crack occurrence time first increases and then decreases, and the total fracture area first decreases and then increases. When the grinding time is 1.0 h (the fineness is 15%), the crack resistance performance is the best. At this time, the degree of delaying the occurrence of cracks is the most significant. The total fracture area decreases by 40%.
The content of dacite powder has obvious influence on the crack resistance of mortar. With the increase of dacite powder content (accounting for 20%, 25%, 30% and 50% of the total amount of cementitious materials), the time of crack occurrence is gradually delayed and the total area of the crack is gradually reduced as well. When the dacite powder content is 50%, the crack resistance performance is the best. At this time, the degree of delayed crack occurrence is the most significant. The total area of the crack is reduced by 70% compared with the control group.
For the test piece with fly ash alone (F50WF0 group), compared with the test piece with fly ash and dacite powder, its strength changes slowly and its elastic modulus rises slowly. The tensile strain borne by the test piece has never reached the ultimate tensile strain which means it has not cracked in this test cycle showing good crack resistance.
The addition of dacite powder reduces the cracking sensitivity of the samples. Combining its hydration characteristics and microscopic topography, the main reason is that dacite powder can fill the voids in cement paste, improve the microstructure and fracture mechanism of cement-based materials, increase the toughness of materials. At the same time, dacite powder slows down the drying shrinkage rate of cement paste through water absorption reaction, thereby reducing the risk of cracking.
The micro morphology images of each group of samples are shown in Figure 10.
FIGURE 10. Scanning electron microscopy (SEM) photos of each group of samples after 28 days: (A) JZ (control group mortar); (B) F50WF0(fly ash50%,dacite0%); (C) F25WF0.525 (fly ash25%,0.5 h dacite25%.
The results of Figure 10 indicate that:
For the variable group of dacite powder grinding time (Figures 10C–E), it can be seen from the observation of Figure 15D that the mortar with grinding time of 1.0 h (fineness of 15%) has fewer pores between the hydration and cementitious products and the microstructure is more dense. It can be clearly observed that the flocculent calcium silicate hydrate (C-S-H) is filled in the crystal structure of Calcium hydroxide (CH) with smooth surface. However, by observing the images in Figures 15C, E, which show the grinding time of 0.5 h (fineness 39%) and 1.5 h (fineness 11.1%) mortar, it is evident that some microcracks and pores, hydration products are dispersed and the overall continuity of the microstructure is poor.
For the dacite powder mixing variable group (Figure 10 (b), (d), (f), (g)), observation of SEM images shows that when the dacite powder content is 20%, the C-S-H gel is interlaced in clusters. The morphology of C-S-H gel has developed from poorly crystallized fibrous to multi-layer reticular and the slurry is relatively dense, indicating that dacite powder has fully played its filling role and nucleation role at this time. On the one hand, the filling role of dacite powder has optimized the grading of the mortar system and improved the compactness. On the other hand, dacite powder, as the core point of cement hydration product crystallization, promotes the generation of cement hydration products. When optimizing the pore structure of mortar, it also improves the interface bonding performance, making its flexural and compressive strength significantly improved.
When the content of dacite powder reaches 30%, the filling effect of dacite powder in mortar system has become saturated. Excess dacite powder exists in the middle of cement or interface in the form of free, which plays a dilution role, leading to the reduction of mechanical properties of mortar.
The microstructure and elemental distribution energy spectrum of the sample are shown in Figure 11.
FIGURE 11. Energy dispersive spectroscopy (EDS) results of each group of samples: (A) JZ; (B) F50WF0; (C) F30WF1.0h20.
It can be seen from Figure 11 that the element composition of the hydrated cement mortar mixed with fly ash alone share the similar results with that mixed with fly ash and dacite powder, which mainly contains C, O, Si, Ca, Al, Mg, S, Na and other elements.
Phase analysis was carried out using a Japanese physics Rigaku/Smart Lab SE type XRD instrument and the XRD spectra of each group of samples were obtained, as shown in Figure 12.
FIGURE 12. XRD spectrum of cement mortar: (A) Cement mortar with dacite powder at different grinding times; (B) Cement mortar with different content of dacite powder.
From Figure 12, it can be seen that:
The addition of fly ash and dacite powder does not change the type of hydration products of mortar. Compared with the XRD pattern of pure cement mortar benchmark group, the hydration products of mortar mixed with fly ash and dacite powder have no new diffraction peaks, but the diffraction peak strength of each crystal has changed.
The area of characteristic peaks of SiO2, CH and C-S-H is obviously changed by adding fly ash and dacite powder. The largest change in peak area is the characteristic peak of SiO2. With the increase of dacite powder grinding time, its peak strength first increases and then decreases, reaching the maximum when the grinding time is 1.0 h (fineness 15%). With the increase of dacite powder content, its peak strength does not change significantly because in cement mortar, the total content of fly ash and dacite powder remains unchanged and also some of the powders do not participate in hydration reaction filling in the mortar pores in the original form. At the same time, dacite powder provides nucleation sites for the crystallization of cement hydration products promoting the generation of cement hydration products, making the content of C-S-H in cement mortar increase.
The addition of dacite powder and fly ash reduces the CH content in cement mortar, increases the C-S-H content and improves the strength of cement mortar, which is the same as the results of SEM and EDS analysis. It fully explains the change rule of mortar strength.
The relationship between mortar samples prepared with dacite powder at different dosage and age is shown in Figure 13.
FIGURE 13. Test results of inhibiting aggregate alkali activity by adding dacite powder: (A) Sample expansion rate; (B) Admixture inhibition rate.
The test results of inhibiting aggregate alkali activity by adding dacite powder alone show that:
After adding 15%–50% of dacite powder alone, the 28 days expansion rate of mortar samples is still greater than 0.10%. When 55% dacite powder is added, the expansion rate of 28 days specimen is less than 0.10%. It shows that the alkali activity of aggregate can not be effectively inhibited by adding dacite powder (15%–50%) alone. Only by adding more than 55% of dacite powder alone can the alkali activity of aggregate be inhibited.
When the content of dacite powder is low (30% and below), the expansion rate of 1day and 7 days mortar samples is higher than the reference aggregate, but after 14days, the expansion rate of mortar specimens is lower than the reference aggregate. It shows that dacite powder at early age promotes the alkali activity of aggregate but it has a certain inhibitory effect at later stage.
As the single addition of dacite powder can hardly effectively inhibit the alkali activity of the encouraged aggregate, it is necessary to mix dacite powder and fly ash. The result curve is shown in Figure 14.
FIGURE 14. Test results of inhibiting aggregate alkali activity by adding fly ash and dacite powder: (A) Sample expansion rate; (B) Admixture inhibition rate.
The results of aggregate alkali activity inhibition show that when dacite powder and fly ash are mixed. The expansion rate of 28 days mortar samples is less than 0.10% when the content of dacite powder is fixed at 25%, and the content of fly ash is 10% or more, indicating that dacite powder must be mixed with fly ash to effectively inhibit the alkali activity of aggregate.
Based on the above conclusions, the recommended test plan for suppressing the alkali activity of aggregates is: (i) Add only 20% or more fly ash. (ii) Mixed with 25% dacite powder and more than 15% fly ash.
Scanning electron microscope is used to observe the micro morphology of each group of test pieces. As is shown in Figure 15.
FIGURE 15. Microtopography of dacite powder inhibiting alkali aggregate activity after 28 days: (a1) JZ; (a2) JZ; (B) F10S0 (C); F10S0; (D) F20S30; (E) F25S25.
From Figure 15, it can be seen that:
The interface transition area of the reference sample has a loose structure and there are obvious cracks at the edge of the aggregate.
Compared with the reference sample, the sample mixed with fly ash and dacite powder has a closer connection between the aggregate and the cement paste and the sample holes are significantly reduced, indicating that the alkali aggregate reaction is significantly inhibited. In addition, no obvious alkali silicate gel is found in the figure. There is no crack in the transition area between dacite aggregate and cement paste, which indicates that no expansion damage has occurred to the test piece.
We investigates whether dacite can partially replace fly ash to prepare large volume concrete that meets the requirements for construction and ultimately be applied in water conservancy and hydropower projects such as hydraulic structures consisting of large volume concrete components. The value of such application lies in: First and foremost, if the project area contains a large amount of Dacite, We can mine and process nearby as raw materials for mortar preparation, which can greatly save costs and have high economic efficiency. Moreover, in the face of a shortage of fly ash, it is possible to reduce dependence on fly ash. As the production process of fly ash can have a negative impact on the environment, the substitution of fly ash is also a form of environmental protection. Last but not least, in the current research, no one has studied dacite. It is unknown whether it can be used as a material for mortar preparation like other volcanic ash. Therefore, the research has strong research reference value.
The four most important physical properties of cementitious materials are fineness, fluidity, strength and durability. The corresponding macroscopic experimental analyses are: dacite powder fineness test, cementitious material flowability test, cementitious material strength test and cementitious material crack resistance performance test. Fineness is one of the important factors in the grading of cementitious materials. Fineness tests provide quantitative grinding indicators corresponding to the performance of dacite powder. The dacite powder produced with this grinding indicator is used to prepare cementitious materials. Flowability is one of the important indicators for the formation and compaction of concrete. Flowability tests have shown that the addition of dacite powder has a positive effect on improving the flowability of cementitious materials, but it is necessary to control the dosage and fineness so that provide quantitative indicators. Strength is one of the most important indicators of structural components. The mortar strength test quantitatively demonstrates the performance of the content of dacite powder on the strength of cementitious materials and provides ratio recommendations. The crack resistance performance directly affects the durability of concrete materials and cannot be ignored. The crack resistance test research establishes a functional relationship between the dosage of dacite powder and the development of cracks, and quantitatively provides evaluation indicators.
The chemical properties of cementitious materials mainly include two aspects: hydration heat characteristics and alkaline activity characteristics. The corresponding macroscopic experimental studies are hydration heat test and aggregate alkali activity test. Reducing the heat of hydration is crucial for large volume concrete as it can reduce or even avoid the harm caused by concrete cracking. We establishes a functional relationship between the addition of fly ash and dacite powder and the heat of hydration release. Alkali activity is known as the ‘cancer’ of concrete, therefore, controlling it within a reasonable range is an important research topic. Alkaline activity testing is mainly used to determine whether dacite has alkaline activity, and if so, how to suppress alkaline activity by adding fly ash.
In order to provide a more objective explanation, research was conducted at the micro scale and four aspects were carried out: Scanning Electron Microscopy (SEM) Analysis, Energy Dispersive Spectroscopy (EDS) Analysis, Phase Content Test (XRD) Analysis and Microscopic Experiment on the Inhibition of Alkali Aggregate Activity by Dacite Powder.
SEM analysis is aimed at studying the continuity of cementitious materials with different components at the microscale, in order to determine the optimal density and strength performance of the cementitious material at what dosage. EDS analysis is aimed at studying the relationship between the ratio of dacite powder and fly ash and the cementitious content of cementitious materials, which can inhibit the hydration heat reaction. XRD analysis, like SEM analysis, both indicate that the addition of fly ash and dacite powder reduces the C-H content in cement mortar and increases the C-S-H content, thereby improving the strength of cement mortar. Microscopic experiments and mechanism analysis of the inhibition of alkaline aggregate activity, through microscopic electron microscopy photography, has proven that the specimens mixed with fly ash and dacite powder have a tighter connection between the aggregate and cement slurry. The sample pores are significantly reduced, indicating that the alkaline aggregate reaction is significantly inhibited. The above micro experiments are powerful supplements to the results of macro tests.
Through physical and chemical properties, as well as macroscopic experimental analysis and microscopic scale research, evidence has been provided that dacite powder can be used as a cement-based material. Dosage indicators have been proposed to meet the requirements of fineness, strength, flowability, durability and controllable hydration heat reaction together with alkali activity hazards. The above research results indicate that partial replacement of fly ash with dacite is feasible, thereby exerting economic benefits and filling the research gap for the absence of dacite in the volcanic ash family.
In this paper, the comprehensive properties and microstructure of cementitious material prepared by partially replacing fly ash with dacite powder are studied. Suggestions are made on the control of particle fineness and dosage. The conclusions are as follows:
1. The paper reveals that dacite powder can partly replace fly ash as cementitious material. It enriches the research system of concrete materials and perfects the lack of data in the field of dacite as raw material for concrete preparation.
2. Four specifications of dacite powder with ball-milling time of 0.5 h (fineness 39%), 1.0 h (fineness 15%), 1.5 h (fineness 11%) and 2.0 h (fineness 5.7%) were obtained by ball milling. Combined with the test results and engineering practice, it is recommended that the dacite powder with ball-milling time of 1.0 h be selected. The performance of dacite powder is the best when the fineness is 15%.
3. Proper amount of dacite powder can improve the fluidity of cement paste and cement slurry. However, with the increase of dacite powder content, the fluidity of cement paste and cement slurry decreases.
4. It is advisable to mix dacite powder and fly ash. The total amount of dacite powder should not exceed 30% of the cementitious material. It has the best performance when the amount of dacite powder and fly ash is the same.
5. The alkali activity of aggregate can hardly be inhibited by mixing dacite powder alone. The recommended measures to inhibit the alkali activity of aggregate are: (i) mixing more than 20% fly ash alone. (ii) Mixed with 25% dacite powder and more than 15% fly ash.
The raw data supporting the conclusion of this article will be made available by the authors, without undue reservation.
LL: Conceptualization, Data curation, Investigation, Methodology, Software, Writing–original draft, Writing–review and editing. JT: Data curation, Investigation, Writing–review and editing. HQ: Funding acquisition, Investigation, Methodology, Writing–review and editing. JZ: Data curation, Investigation, Writing–review and editing. YG: Investigation, Writing–review and editing.
The author(s) declare financial support was received for the research, authorship, and/or publication of this article. This work was supported by Guizhou Province Science and Technology Plan Project (Grant No [2016]1154, Grant No [2018]2809, Grant No [2019]2869).
Authors LL, JT, HQ, JZ, and YG were employed by Power China Guiyang Engineering Corporation Limited.
All claims expressed in this article are solely those of the authors and do not necessarily represent those of their affiliated organizations, or those of the publisher, the editors and the reviewers. Any product that may be evaluated in this article, or claim that may be made by its manufacturer, is not guaranteed or endorsed by the publisher.
Al-Hashem, M. N., Amin, M. N., Ajwad, A., Afzal, M., Khan, K., Faraz, M. I., et al. (2022). Mechanical and durability evaluation of Metakaolin as cement replacement material in concrete. Materials 15 (22), 7868. doi:10.3390/ma15227868
Amin, M., Zeyad, A. M., Tayeh, B. A., and Saad Agwa, I. (2021). Engineering properties of self-cured normal and high strength concrete produced using polyethylene glycol and porous ceramic waste as coarse aggregate. Constr. Build. Mater. 299, 124243. doi:10.1016/j.conbuildmat.2021.124243
Çelik, A. İ., Özkılıç, Y. O., Zeybek, Ö., Özdöner, N., and Tayeh, B. A. (2022). Performance assessment of fiber-reinforced concrete produced with waste lathe fibers. Sustainability 14 (19), 11817. doi:10.3390/su141911817
Deng, S. (2019). Temporal-spatial optimization of temperature control measures for dam concrete construction. Yellow River 41 (08), 124–128.
Feng, H., Nie, S., Guo, A., Lv, L., Chu, L., and Yu, J. (2022). Fresh properties and compressive strength of MPC-based materials with blended mineral admixtures. Case Stud. Constr. Mater. 17, e01201. doi:10.1016/j.cscm.2022.e01201
Hallal, A., Kadri, E., Ezziane, K., Kadri, A., and Khelafi, H. (2010). Combined effect of mineral admixtures with superplasticizers on the fluidity of the blended cement paste. Constr. Build. Mater. 24 (8), 1418–1423. doi:10.1016/j.conbuildmat.2010.01.015
Hemalatha, T., and Ramaswamy, A. (2017). A review on fly ash characteristics – towards promoting high volume utilization in developing sustainable concrete. J. Clean. Prod. 147, 546–559. doi:10.1016/j.jclepro.2017.01.114
Herath, C., Gunasekara, C., Law, D. W., and Setunge, S. (2020). Performance of high volume fly ash concrete incorporating additives: a systematic literature review. Constr. Build. Mater. 258, 120606. doi:10.1016/j.conbuildmat.2020.120606
Hunyak, O., Sobol, K., Markiv, T., and Bidos, V. (2019a). The effect of natural pozzolans on properties of vibropressed interlocking concrete blocks in different curing conditions. Prod. Eng. Arch. 22 (22), 3–6. doi:10.30657/pea.2019.22.01
Jiang, H., Fall, M., Yilmaz, E., Li, Y., and Yang, L. (2020). Effect of mineral admixtures on flow properties of fresh cemented paste backfill: assessment of Time Dependency and thixotropy. Powder Technol. 372, 258–266. doi:10.1016/j.powtec.2020.06.009
Karalar, M., Özkılıç, Y. O., Deifalla, A. F., Aksoylu, C., Arslan, M. H., Ahmad, M., et al. (2022). Improvement in bending performance of reinforced concrete beams produced with waste lathe scraps. Sustainability 14 (19), 12660. doi:10.3390/su141912660
Krishnaraj, L., and Ravichandran, P. T. (2019a). Impact of Chloride grinding Aid with modified fly ash using Topdown Nanotechnology on grinding performance. Constr. Build. Mater. 199, 225–233. doi:10.1016/j.conbuildmat.2018.12.019
Krishnaraj, L., and Ravichandran, P. T. (2019b). Investigation on grinding impact of fly ash particles and its characterization analysis in cement mortar composites. Ain Shams Eng. J. 10, 267–274. doi:10.1016/j.asej.2019.02.001
Li, W. (2020). Experimental study on mechanical properties of dacite under the unloading condition of a hydropower station. Pearl River 41 (01), 13–17+68.
Lv, J., Tian, B., Li, L., and Quan, L. (2022). Mechanisms of hydration heat inhibitors on the early heat release process of cement. Front. Mater. 9, 1049202. doi:10.3389/fmats.2022.1049202
Markiv, T., Sobol, K., Franus, M., and Franus, W. (2016). Mechanical and durability properties of concretes incorporating natural zeolite. Archives Civ. Mech. Eng. 16 (4), 554–562. doi:10.1016/j.acme.2016.03.013
Najimi, M., Jamshidi, M., and Pourkhorshidi, A. (2008). Durability of concretes containing natural pozzolan. Proc. Institution Civ. Eng. - Constr. Mater. 161 (3), 113–118. doi:10.1680/coma.2008.161.3.113
Qureshi, H. J., Ahmad, J., Majdi, A., Saleem, M. U., Al Fuhaid, A. F., and Arifuzzaman, M. (2022). A study on sustainable concrete with partial substitution of cement with Red Mud: a Review. Materials 15 (21), 7761. doi:10.3390/ma15217761
Ruidong, W., Yu, S., Juanhong, L., Linian, C., Guangtian, Z., and Yueyue, Z. (2021). Effect of iron tailings and slag powders on workability and mechanical properties of concrete. Front. Mater. 8. doi:10.3389/fmats.2021.723119
Santana, J. J., Rodríguez-Brito, N., Blanco-Peñalver, C., Mena, V. F., and Souto, R. M. (2022). Durability of reinforced concrete with additions of natural pozzolans of volcanic origin. Materials 15 (23), 8352. doi:10.3390/ma15238352
Su, P. (2020). Influencing factors and temperature control measures of RCC dam construction in high altitude and cold area of Tibet. Hongs. River 39 (02), 15–19.
Sun, M., Hu, K., Zhang, Y., Wei, G., and Rong, H. (2022b). Molecular simulation and experimental investigation on enhancement of microbe cement in municipal solid waste incineration fly ash. Front. Mater. 9, 1013580. doi:10.3389/fmats.2022.1013580
Sun, Y., Wang, Z., Park, D., Kim, W., Kim, H., Yan, S., et al. (2022a). Analysis of the isothermal hydration heat of cement paste containing mechanically activated Fly Ash. Thermochim. Acta 715, 179273. doi:10.1016/j.tca.2022.179273
Supit, S. W. M., Shaikh, F. U. A., and Sarker, P. K. (2014). Effect of ultrafine fly ash on mechanical properties of high volume fly ash mortar. Constr. Build. Mater. 51, 278–286. doi:10.1016/j.conbuildmat.2013.11.002
Wang, D. (2020). Simulation study of temperature control in sanhekou RCC srch dam. Acta. Mech. Sin. 37 (01), 463–468+500.
Wang, J., Liang, X. L., and Wen, L. (2020). Experimental study on physical and mechanical properties of rock under the condition of freeze-thaw cycle. Sci. Technol. Eng. 21 (24), 10421–10429. doi:10.1155/2021/9980549
Zaid, O., Ahmad, J., Siddique, M. S., and Aslam, F. (2021). Effect of incorporation of rice husk ash instead of cement on the performance of steel fibers reinforced concrete. Front. Mater. 8. doi:10.3389/fmats.2021.665625
Zeng, Q., and Li, K. (2014). Reaction and microstructure of cement–fly-ash system. Mater. Struct. 48 (6), 1703–1716. doi:10.1617/s11527-014-0266-y
Zhang, G., Liu, Y., and Liu, Y. (2018). Reviews on temperature control and crack prevention of high concrete dam. J. Hydraul. Eng. 49 (09), 1068–1078.
Zhao, J., Wang, D., Wang, X., Liao, S., and Lin, H. (2015). Ultrafine grinding of fly ash with grinding aids: impact on particle characteristics of ultrafine fly ash and properties of blended cement containing ultrafine fly ash. Constr. Build. Mater. 78, 250–259. doi:10.1016/j.conbuildmat.2015.01.025
Keywords: dacite powder, fly ash, hydration reaction, cementitious materials, microstructure
Citation: Liu L, Tan J, Qiu H, Zhang J and Guo Y (2024) Study on microstructural and mechanical properties of cementitious materials composed of fly ash and dacite powder. Front. Mater. 11:1267197. doi: 10.3389/fmats.2024.1267197
Received: 26 July 2023; Accepted: 19 February 2024;
Published: 14 March 2024.
Edited by:
Pradeep R. Varadwaj, The University of Tokyo, JapanReviewed by:
Yashas Gowda T. G, Malnad College of Engineering, IndiaCopyright © 2024 Liu, Tan, Qiu, Zhang and Guo. This is an open-access article distributed under the terms of the Creative Commons Attribution License (CC BY). The use, distribution or reproduction in other forums is permitted, provided the original author(s) and the copyright owner(s) are credited and that the original publication in this journal is cited, in accordance with accepted academic practice. No use, distribution or reproduction is permitted which does not comply with these terms.
*Correspondence: Huanfeng Qiu, cWl1aHVhbmZlbmcxOTgzQDE2My5jb20=
Disclaimer: All claims expressed in this article are solely those of the authors and do not necessarily represent those of their affiliated organizations, or those of the publisher, the editors and the reviewers. Any product that may be evaluated in this article or claim that may be made by its manufacturer is not guaranteed or endorsed by the publisher.
Research integrity at Frontiers
Learn more about the work of our research integrity team to safeguard the quality of each article we publish.