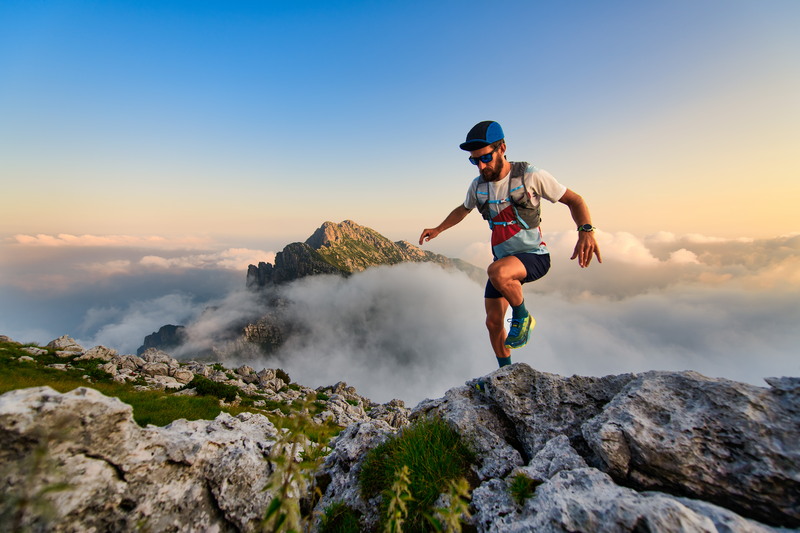
95% of researchers rate our articles as excellent or good
Learn more about the work of our research integrity team to safeguard the quality of each article we publish.
Find out more
ORIGINAL RESEARCH article
Front. Mater. , 23 November 2023
Sec. Polymeric and Composite Materials
Volume 10 - 2023 | https://doi.org/10.3389/fmats.2023.1298241
This article is part of the Research Topic Recent Advances in Functional Materials: Polymers and Composite Materials View all 6 articles
Asphalt mixture is a temperature sensitive material. With the change of external environment temperature, asphalt pavement is prone to temperature-related diseases. Adding phase change material (PCM) to asphalt pavement to adjust pavement temperature is one of the effective methods at present. At present, there are many types of research on PCMs, but the research on PCMs added to the pavement structure is very scarce. In this paper, through the temperature test of rutting plate specimens with different layer combinations, the cooling effect of pavement structure combinations with PCMs added to different layers (upper layer, middle layer, and bottom layer) in pavement structure under different illumination times are discussed. Through the self-designed environmental simulation box, the real-time monitoring of the temperature of different layers in the pavement structure is realized. The cooling effect between different layers in different phase change pavement structure combinations is analyzed, and compared with each layer of ordinary pavement structure, and the best addition method is obtained for phase change materials, which provides a certain reference for the construction and specific application of PCM asphalt pavement, and made important contributions to the development of asphalt cooling pavement. The results show that the PCM can effectively reduce the temperature of each layer of the pavement structure. Under different illumination durations, the cooling effect of the samples with PCM in the upper layer was the worst. The samples with phase change material in the middle layer had the best cooling effect in the upper and middle layers of the pavement. The addition of phase change material to both the upper and middle layers had the most obvious cooling effect on the lower layer of the pavement. Therefore, combined with the comprehensive consideration of economy and cooling effect, the comprehensive cooling effect of adding PCMs to the middle surface layer is the best. It is recommended to add phase change materials to the middle surface layer during asphalt cooling pavement construction.
Road performance has always been a concern (Wang et al., 2022; Wang et al., 2023), and asphalt roads are an important part of it. Asphalt mixture is a kind of black material which is highly absorbing solar radiation (Cheng et al., 2023). The temperature of asphalt pavement is higher than the atmospheric temperature, which leads to the occurrence of high temperature deformation. In addition, the heat absorption of asphalt pavement not only leads to the increase of pavement temperature but also releases a lot of heat to the surrounding environment, resulting in pavement diseases and ' urban heat island effect (Wen-Juan et al., 2008; FENG et al., 2011; Takebayashi and Moriyama, 2012). Asphalt is a temperature-sensitive material. Therefore, its mechanical behavior and performance are significantly affected by the ambient temperature as it is directly exposed to the external environment. This may lead to high temperature distress, such as rutting, bleeding, and slipping, as well as low temperature cracking after continuous high temperature or low temperature and rapid cooling (Mallick et al., 2015; Behnia et al., 2017; Alimohammadi et al., 2020). Therefore, some scholars began to study the use of cooling pavement to reduce the heat island effect brought by asphalt pavement in summer and increase the durability of pavement in high temperature environments (Chen et al., 2009; Li, 2012; Qin and Hiller, 2014).
Some scholars have studied the thermal reflective layer and thermal resistance technology to reduce the pavement temperature (Doulos et al., 2004). The thermal reflective layer improves the reflectivity and radiation efficiency of the pavement surface and then reduces the pavement temperature by preventing external heat transfer to the pavement structure (Sujith Kumar et al., 2014; Zheng et al., 2015). However, the use of thermal reflective technology is too costly, the durability is flawed, and the application of coatings is limited because it may affect the skid resistance of the pavement and cause safety hazards. The thermal resistance technology to reduce the pavement temperature is to add thermal resistance materials, which can effectively reduce the pavement temperature. Heat-resistant materials include ceramics, ceramic sand, diatomite, bauxite, and refractory (Huang et al., 2009; González-Corrochano et al., 2011; Ren et al., 2014; Pancar, 2016). Phase change materials (PCM) are functional materials that absorb or release heat energy (phase change enthalpy) by undergoing phase change. The stored energy can be used to adjust the ambient temperature. This temperature regulation function of PCM has been widely used in the construction, electronics, and textile industries (Oró et al., 2012). The research on the application of PCMs in asphalt pavement began in 2010, and then the related research increased year by year. The active temperature regulation of asphalt pavement can be achieved by PCM doping, thereby slowing down the temperature change rate and maintaining the ideal working temperature more continuously (Manning et al., 2015).
Initial research was based on fatty acids, paraffin, and their composite PCMs, which are used to regulate the temperature of asphalt pavements to prevent cracking, freezing, and frosting at low temperatures (Chao et al., 2010; Ma et al., 2011a; Ma et al., 2011b; Chen et al., 2011; Ma et al., 2011c; Bian et al., 2012; Ma et al., 2014). Subsequently, it was found that the heat absorption of PCMs under higher temperature conditions can be used to reduce the rutting and urban heat island effect of asphalt pavement. Among them, PCMs based on polyols such as PEG show good functionality and applicability (He et al., 2013; Jin et al., 2017; Liu et al., 2021). At present, many PCMs are suitable for temperature regulation of asphalt pavement, but unencapsulated solid-liquid PCMs are prone to volatilize, leak, and damage the performance of asphalt and asphalt mixture when directly used in asphalt or asphalt mixture (Dai et al., 2021; Kakar et al., 2020). Therefore, a lot of research has been carried out on the preparation method of CPCM. Ahmed (Sari, 2004) prepared two kinds of paraffin high density polyethylene composites by melt blending. Chen et al. (2010) A novel shape-stabilized phase change material (SSPCM) was prepared by melt intercalation (Sarier and Onder, 2007). Four different microcapsules were prepared with urea and formaldehyde as shell materials and n-octadecane, n-octadecane-PEG600, n-eicosane -n-hexadecane, PEG1000-Na as capsule materials. Ma et al. (2013) by using a thin film layer to encapsulate PCM, a composite shape-stable phase change material is prepared to ensure stability. Liu et al. (Xing et al., 2006) Paraffin and high density polyethylene (HDPE) were used as core materials, and sodium silicate monohydrate (Na2SiO3.9H2O) and hydrochloric acid (HCl) were used as coating materials to prepare microcapsules.
So far, there are many studies on cooling materials, but research on which pavement structure to add cooling materials is very scarce. In this paper, the temperature test is carried out on the rut plate specimens of different layers, and the use method of cooling materials is optimized, which is of great significance to the construction and application of phase change asphalt pavement.
In this paper, the gradation of each layer of the experimental asphalt pavement is shown in Figure 1. The asphalt used is SBS (I-D) modified asphalt produced by Dongguan Taihe Asphalt Products Co., Ltd. The basic performance indicators are shown in Table 1. The technical indicators of aggregate and filler are shown in Table 2. The phase change material is DTC phase change material produced by Beijing Qintian Technology Group, as shown in Figure 2 and the relevant technical parameters are shown in Table 3. The type and additional amount of each structural layer of asphalt pavement in the experiment are shown in Figure 3.
In this paper, different combination design schemes are tested by using the self-developed pavement environment simulation box. The road environment simulation box can achieve continuous heating at a maximum temperature of 80°C, and simulate the relevant air humidity, and realize the automatic adjustment of the set temperature through the relevant temperature sensing device, as shown in Figure 4.
In this paper, the temperature data of each layer are recorded by sensors and temperature recorders. The model OHR-H700 of the recorder can record the temperature in real time after connecting the sensors, and store and export the temperature data, as shown in Figure 5.
In this paper, the phase change material (A) is added to the upper layer, the phase change material (B) is added to the middle layer, and the phase change material (C) is added to the upper layer and the middle layer. The three combined design schemes are tested separately, and the blank control (D) of the ordinary pavement is set, as shown in Figure 6.
In order to realize the detection of the temperature between the various layers of the composite pavement, the sensors are buried according to the characteristics of different layers in this paper. The design of test points in different layers is shown in Figure 7.
In this paper, the road surface temperature is collected by sensors attached to the road surface and monitored in real time. The temperature inside each layer is monitored by drilling the rut plate inside and embedding the sensor into the layer, as shown in Figure 8. According to the layer combination design scheme, the rut board is put into the pavement environment simulation box, and each layer of the pavement is connected by the sensor, and each layer of the composite pavement is monitored in real time by the temperature recorder, as shown in Figure 9. The experimental test time is 4 h, 6 h, 8 h and 10 h respectively, and then the cooling performance of different layer combination design schemes under different illumination time is obtained.
It can be seen from Figure 10 that after 4 h, the temperature difference between group A and group D is not large, which indicates that the phase change material of the upper layer has failed after 4 h. The temperature difference of test point 8 is the largest, which indicates that the phase change material has an effect in the early stage, and the heating rate of the lower layer has also slowed down. Figure 11 shows that there is a temperature difference between group B and group D after 4 h, and the overall temperature difference is above 5°C. It shows that the addition of phase change materials in the middle layer has a great effect. Figure 12 shows the temperature difference between group C and group D after 4 h. The temperature difference of the test point 2 is 2.2°C, the temperature difference of the test point 4 and 5 is above 4°C, and the temperature difference of the test point 7 and 8 is above 5°C. The comparison of the cooling effect of different phase change layers after 4 h of illumination shows that the temperature of phase change materials added to different pavement structures after 4 h of illumination is lower than that of ordinary pavement structures, and the comprehensive cooling effect of group B is the best. The cooling effect of group B on the upper layer is greater than that of group C, which may be due to the fact that the PCM of group C is close to the failure temperature. The comprehensive comparison of cooling effect: group B > group C > group A > group D.
It can be seen from Figure 13, at 6 h, there was no difference in the temperature of the middle layer between group A and group D, and the temperature difference between test points 7 and 8 becomes smaller. Figure 14 shows that there is a temperature difference between group B and group D after 6 h, and the overall temperature difference is above 4°C. It can be seen in Figure 15 that although the temperature difference between group C and group D became smaller after 6 h, the change was not significant. It shows that the addition of phase change materials in the middle layer also has a great effect in 6 h. And the comprehensive cooling effect of group B is still the best. The cooling rate of group A was further reduced, and the temperature between the test points 4,5,7 and 8 was almost the same as that of the ordinary structure. The comprehensive comparison of cooling effect: group B > group C > group A > group D.
It can be seen from Figure 16, at 8 h, there was almost no difference in the temperature of the test points 1 to 5 between group A and group D, but there was a temperature difference in the test points 6 to 8. It can be seen from Figure 17 that after 8 h, there was a temperature difference of more than 3°C between group B and group D. It can be seen from Figure 18 that the temperature difference between group C and group D became smaller after 8 h, but the change range was not large.
The comparison of the cooling effect of different phase change layers after 8 h of illumination shows that the cooling effect of group C is still significantly better than that of group B, but the cooling effect of group B was still obvious. Combined with the cooling effect of the bottom surface layer, the structure of Group C still performs best.
It can be seen from Figure 19 that the temperature difference between group A and group D and the 8-h comparison are basically unchanged. Figure 20 shows that there is a temperature difference between group B and group D after 10 h, and the overall temperature difference is above 3°C. It can be seen from Figure 21 that the temperature difference between group C and group D became larger after 10 h, but the change range was not large. Comprehensive analysis shows that after 10 h of long-term illumination, the temperature of the final layers of the phase change material pavement structure is lower than that of the ordinary pavement structure. After 10 h of illumination, the cooling effect of group A remained basically unchanged. The cooling effect of group B and group C was obviously effective, but the cooling performance of group C was slightly stronger than that of group B.
In this paper, the self-made environmental simulation box is used to study the cooling effect of asphalt pavement combinations with phase change materials added to different layers. The cooling effect of each layer of different phase change material asphalt pavement combinations under different light durations is analyzed. Compared with the traditional ordinary pavement, the main research conclusions are as follows:
(1) By comparing the pavement structure of adding phase change materials in different layers with the ordinary pavement structure, it can be seen that the phase change materials used can effectively reduce the pavement temperature.
(2) The combination of adding phase change materials to the upper and middle layers has the best cooling effect on the bottom layer. The pavement structure of adding phase change materials to the upper layer is not ideal for the cooling effect of the upper layer after 6 h of illumination.
(3) Under different illumination times, comparing the temperature of each layer of the phase change material pavement structure with the temperature of the ordinary pavement structure, it can be seen that the comprehensive cooling effect of adding phase change material to the middle layer is the best.
(4) The cooling effect of the pavement with phase change materials reaches saturation after 10 h, and the cooling rate is almost unchanged.
The datasets presented in this article are not readily available because No. Requests to access the datasets should be directed to amlhbmd5dUBzdHUuY3N1c3QuZWR1LmNu.
PH: Conceptualization, Funding acquisition, Writing–review and editing. DF: Investigation, Writing–review and editing. DL: Writing–review and editing. XG: Writing–review and editing. YJ: Writing–original draft. ZL: Visualization, Writing–original draft. XH: Data curation, Validation, Writing–review and editing.
The authors declare financial support was received for the research, authorship, and/or publication of this article. The study was supported by the National Natural Science Foundation of China (Grant No. 51778071).
Authors PH, DF, and DL were employed by Guangzhou Congpu Expressway Company.
The remaining authors declare that the research was conducted in the absence of any commercial or financial relationships that could be construed as a potential conflict of interest.
All claims expressed in this article are solely those of the authors and do not necessarily represent those of their affiliated organizations, or those of the publisher, the editors and the reviewers. Any product that may be evaluated in this article, or claim that may be made by its manufacturer, is not guaranteed or endorsed by the publisher.
Alimohammadi, H., Zheng, J., Buss, A., Schaefer, V. R., Williams, C., and Zheng, G. (2020). Field and simulated rutting behavior of hot mix and warm mix asphalt overlays. Constr. Build. Mater. 265, 120366. doi:10.1016/j.conbuildmat.2020.120366
Behnia, B., Buttlar, W. G., and Reis, H. (2017). Spiral cracking pattern in asphalt materials. Mater. Des. 116, 609–615. doi:10.1016/j.matdes.2016.11.077
Bian, X., Tan, Y., Lv, J., and Shan, L. Y. (2012). Preparation of latent heat materials used in asphalt pavement and theirs’ controlling temperature performance. Adv. Eng. Forum 5, 322–327. doi:10.4028/www.scientific.net/aef.5.322
Chao, L., Biao, M., Xiao-Man, W., et al. Experimental study on self-adjustable temperature asphalt mixture. International Workshop on Energy and Environment in the Development of Sustainable Asphalt Pavements, Xi'an, 2010 .
Chen, M. Z., Wei, W., and Wu, S. P. (2009). On cold materials of pavement and high-temperature performance of asphalt concrete. Mater. Sci. Forum 620-622, 379–382. doi:10.4028/www.scientific.net/msf.620-622.379
Cheng, C., Liu, J., Gong, F., Fu, Y., Cheng, X., and Qiao, J. (2023). Performance and evaluation models for different structural types of asphalt mixture using shape-stabilized phase change material. Constr. Build. Mater. 383, 131411. doi:10.1016/j.conbuildmat.2023.131411
Chen, M., Hong, J., Wu, S., Lu, W., and Xu, G. J. (2011). Optimization of phase change materials used in asphalt pavement to prevent rutting. Adv. Mater. Res. 219-220, 1375–1378. doi:10.4028/www.scientific.net/amr.219-220.1375
Chen, M., Zheng, S., Wu, S., and Xu, G. (2010). Melting intercalation method to prepare lauric acid/organophilic montmorillonite shape-stabilized phase change material. J. Wuhan Univ. Technology-Mater Sci Ed 25 (4), 674–677. doi:10.1007/s11595-010-0068-1
Dai, J., Ma, F., Fu, Z., Jia, M., Shi, K., et al. (2021). Applicability assessment of stearic acid/palmitic acid binary eutectic phase change material in cooling pavement. Renew. Energy 175, 748–759. doi:10.1016/j.renene.2021.05.063
Doulos, L., Santamouris, M., and Livada, I. (2004). Passive cooling of outdoor urban spaces. The role of materials. Sol. Energy 77 (2), 231–249. doi:10.1016/j.solener.2004.04.005
Feng, X., Zha, X., and Jun, W. (2011). Study on new mix design method for balancing anti-rutting and anti-cracking. J. Wuhan Univ. Technol. 33 (5), 86–89. doi:10.3963/j.issn.1671-4431.2011.05.019
GonzáLEZ-Corrochano, B., Alonso-AzcáRATE, J., Rodas, M., Barrenechea, J., and Luque, F. (2011). Microstructure and mineralogy of lightweight aggregates manufactured from mining and industrial wastes. Constr. Build. Mater. 25 (8), 3591–3602. doi:10.1016/j.conbuildmat.2011.03.053
He, L. H., Li, J. R., and Zhu, H. Z. (2013). Analysis on application prospect of shape-stabilized phase change materials in asphalt pavement. Appl. Mech. Mater. 357-360, 1277–1281. doi:10.4028/www.scientific.net/amm.357-360.1277
Huang, B., Dong, Q., and Burdette, E. G. (2009). Laboratory evaluation of incorporating waste ceramic materials into Portland cement and asphaltic concrete. Constr. Build. Mater. 23 (12), 3451–3456. doi:10.1016/j.conbuildmat.2009.08.024
Jin, J., Lin, F., Liu, R., Xiao, T., Zheng, J., Qian, G., et al. (2017). Preparation and thermal properties of mineral-supported polyethylene glycol as form-stable composite phase change materials (CPCMs) used in asphalt pavements. Rep 7 (1), 16998. doi:10.1038/s41598-017-17224-1
Kakar, M. R., Refaa, Z., Bueno, M., Worlitschek, J., Stamatiou, A., and Partl, M. N. (2020). Investigating bitumen’s direct interaction with Tetradecane as potential phase change material for low temperature applications. Road Mater. Pavement Des. 21 (8), 2356–2363. doi:10.1080/14680629.2019.1601127
Li, H. (2012). Evaluation of Cool pavement strategies for heat island mitigation. Dissertations and Theses - Gradworks.
Liu, Z., Wei, K., Wang, S., Ma, B., Wang, X., Shi, W., et al. (2021). Effect of high-temperature-resistant epoxy resin/polyethylene glycol 2000 composite stereotyped phase change material particles on asphalt properties. Constr. Build. Mater. 300, 124007. doi:10.1016/j.conbuildmat.2021.124007
Ma, B., Adhikari, S., Chang, Y., Ren, J., Liu, J., and You, Z. (2013). Preparation of composite shape-stabilized phase change materials for highway pavements. Constr. Build. Mater. 42, 114–121. doi:10.1016/j.conbuildmat.2012.12.027
Ma, B., Li, J., Wang, X. M., and Xiao, N. (2011b). Effect of composite shape-stabilized phase change material on asphalt mixture temperature. Adv. Mater. Res. 311-313, 2151–2154. doi:10.4028/www.scientific.net/amr.311-313.2151
Ma, B., Ma, J., Wang, D. L., and Peng, S. G. (2011c). Preparation and properties of composite shape-stabilized phase change material for asphalt mixture. Appl. Mech. Mater. 71-78, 118–121. doi:10.4028/www.scientific.net/amm.71-78.118
Ma, B., Si, W., Ren, J., Wang, H. n., Liu, F. w., and Li, J. (2014). Exploration of road temperature-adjustment material in asphalt mixture. Road Mater. Pavement Des. 15 (3), 659–673. doi:10.1080/14680629.2014.885462
Ma, B., Wang, S. S., and Li, J. (2011a). Study on application of PCM in asphalt mixture. Adv. Mater. Res. 168-170, 2625–2630. doi:10.4028/www.scientific.net/amr.168-170.2625
Mallick, R. B., Li, H., Harvey, J., Myers, R., Veeraragavan, A., and Reck, N. (2015). Pavement life–extending potential of geosynthetic-reinforced chip seal with high-reflectivity aggregates. Transp. Res. Rec. 2474 (1), 19–29. doi:10.3141/2474-03
Manning, B. J., Bender, P. R., Cote, S. A., Lewis, R. A., Sakulich, A. R., and Mallick, R. B. (2015). Assessing the feasibility of incorporating phase change material in hot mix asphalt. Sustain. Cities Soc. 19, 11–16. doi:10.1016/j.scs.2015.06.005
Oró, E., De Gracia, A., Castell, A., Farid, M., and Cabeza, L. (2012). Review on phase change materials (PCMs) for cold thermal energy storage applications. Appl. Energy 99, 513–533. doi:10.1016/j.apenergy.2012.03.058
Pancar, E. (2016). Using recycled glass and zeolite in concrete pavement to mitigate heat island and reduce thermal cracks. Adv. Mater. Sci. Eng. 2016, 1–8. doi:10.1155/2016/8526354
Qin, Y., and Hiller, J. E. (2014). Understanding pavement-surface energy balance and its implications on cool pavement development. Energy and Build. 85, 389–399. doi:10.1016/j.enbuild.2014.09.076
Ren, J., Ma, B., Si, W., Zhou, X., and Li, C. (2014). Preparation and analysis of composite phase change material used in asphalt mixture by sol–gel method. Constr. Build. Mater. 71, 53–62. doi:10.1016/j.conbuildmat.2014.07.100
Sarı, A. (2004). Form-stable paraffin/high density polyethylene composites as solid–liquid phase change material for thermal energy storage: preparation and thermal properties. Energy Convers. Manag. 45 (13), 2033–2042. doi:10.1016/j.enconman.2003.10.022
Sarier, N., and Onder, E. (2007). The manufacture of microencapsulated phase change materials suitable for the design of thermally enhanced fabrics. Thermochim. Acta 452 (2), 149–160. doi:10.1016/j.tca.2006.08.002
Sujith Kumar, C. S., Suresh, S., Yang, L., Yang, Q., and Aravind, S. (2014). Flow boiling heat transfer enhancement using carbon nanotube coatings. Appl. Therm. Eng. 65 (1), 166–175. doi:10.1016/j.applthermaleng.2013.12.053
Takebayashi, H., and Moriyama, M. (2012). Study on surface heat budget of various pavements for urban heat island mitigation. Adv. Mater. Sci. Eng. 2012, 1–11. doi:10.1155/2012/523051
Wang, J., Luo, X., Huang, X., Ye, Y., and Ruan, S. (2022). Analysis on effects of joint spacing on the performance of jointed plain concrete pavements based on long-term pavement performance database. Materials 15 (22), 8132. doi:10.3390/ma15228132
Wang, J., Xiong, Y., Li, Q., Jin, D., Hu, Y., and Che, T. (2023). Experimental investigation on the preparation and surface treatment of biomass fibers for stone mastic asphalt mixtures modification. Constr. Build. Mater. 408, 133667. doi:10.1016/j.conbuildmat.2023.133667
Wen-Juan, Y., Hai-Rong, G. U., and Yong-Ti, S. (2008). Influence of pavement temperature on urban heat island. J. Highw. Transp. Res. Dev. 3, 25.
Xing, L., Hongyan, L., Shujun, W., et al. (2006). Preparation and thermal properties of form-stable paraffin phase change material encapsulation. Sol. Energy (12), 80. doi:10.1016/j.enconman.2005.10.031
Keywords: cool pavement, thermal energy storage, phase change materials, asphalt pavement, urban heat island (UHI)
Citation: Huang P, Fan D, Li D, Gong X, Jiang Y, Liu Z and Huang X (2023) Layer combination design and effect evaluation of phase change cooling asphalt pavement. Front. Mater. 10:1298241. doi: 10.3389/fmats.2023.1298241
Received: 21 September 2023; Accepted: 13 November 2023;
Published: 23 November 2023.
Edited by:
Chuanbao Cao, Beijing Institute of Technology, ChinaCopyright © 2023 Huang, Fan, Li, Gong, Jiang, Liu and Huang. This is an open-access article distributed under the terms of the Creative Commons Attribution License (CC BY). The use, distribution or reproduction in other forums is permitted, provided the original author(s) and the copyright owner(s) are credited and that the original publication in this journal is cited, in accordance with accepted academic practice. No use, distribution or reproduction is permitted which does not comply with these terms.
*Correspondence: Xiangbing Gong, eGJnb25nQGNzdXN0LmVkdS5jbg==
Disclaimer: All claims expressed in this article are solely those of the authors and do not necessarily represent those of their affiliated organizations, or those of the publisher, the editors and the reviewers. Any product that may be evaluated in this article or claim that may be made by its manufacturer is not guaranteed or endorsed by the publisher.
Research integrity at Frontiers
Learn more about the work of our research integrity team to safeguard the quality of each article we publish.