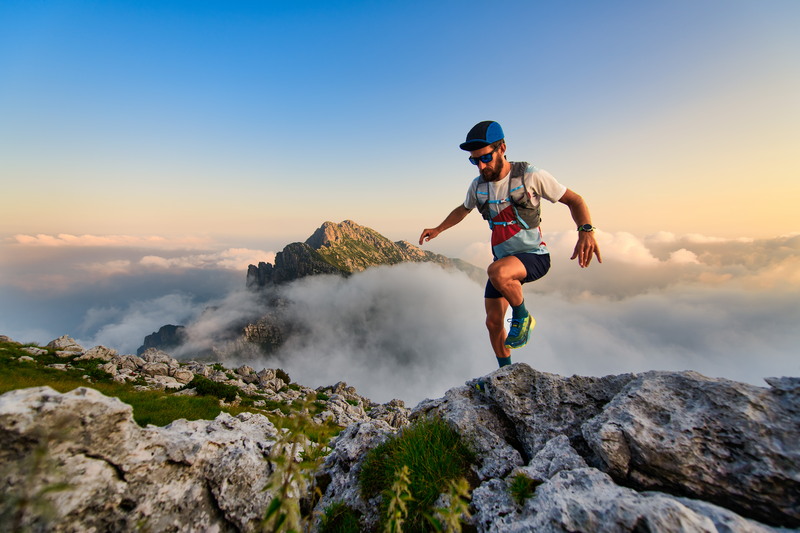
95% of researchers rate our articles as excellent or good
Learn more about the work of our research integrity team to safeguard the quality of each article we publish.
Find out more
EDITORIAL article
Front. Mater. , 27 September 2023
Sec. Polymeric and Composite Materials
Volume 10 - 2023 | https://doi.org/10.3389/fmats.2023.1296247
This article is part of the Research Topic ECCM Research Topic on Advanced Manufacturing of Composites View all 14 articles
Editorial on the Research Topic
ECCM Research Topic on advanced manufacturing of composites
The 20th European Conference on Composite Materials (ECCM20) took place in Lausanne, Switzerland, June 26-30, 2022, organized by the Composite Construction Laboratory (CCLab) and the Laboratory for Processing of Advanced Composites (LPAC) of the Ecole Polytechnique Fédérale de Lausanne (EPFL). The Conference theme was “Composites meet Sustainability”. As a result, even if all fields of research related to composite processing, properties and applications were covered, sustainability aspects were highlighted with specific lectures, roundtables, and sessions on a range of topics, from bio-based composites to energy efficiency in materials production and use phases, as well as end-of-life scenarios and recycling.
Following the conference, we invited participants who focused on the field of advanced manufacturing methods and automation for composite materials, with a particular emphasis on sustainability aspects, to contribute a full paper to form a Research Topic, in the Polymer Composite section of Frontiers in Materials.
The resulting collection of articles in Frontiers in Materials highlights the diversity in approaches and methods used to address this Research Topic through composites manufacturing. We identified three main pathways of sustainable development: i) research related to the adaptation of more sustainable material classes, ii) research towards the improved modelling of manufacturing processes limiting materials waste, iii) research towards novel manufacturing and tooling methods reducing energy demand.
A first strategy explored the use of recycled or natural materials. Borges et al. approached the Research Topic by exploring second life of carbon fiber reinforced polymer (CFRP) scraps into PEEK carbon composites, using a twin-screw extruder. They found that this type of composite can lead to parts of industrial relevance, if the CF is sufficiently long, even at low fiber content. Guerfala et al. produced hybrid composites combining long flax and basalt fibers with a biosourced PA11 matrix, for semi-structural automotive applications, highlighting the potential of hybridization to enhance the composite properties with respect to pure flax fiber composites, while keeping all constituents naturally sourced. Bodaghi et al. also evaluated long flax fiber composites, with PP matrices, and proposed to analyze their thermal conductivity as a method to evaluate the consolidation quality of the obtained parts. Biswas et al. evaluated the use of nanofillers to further enhance the mechanical properties of carbon fiber laminates, in addition to their physical properties such as electrical conductivity. Although these fillers may affect the manufacturing route, they can help in the quest to limit material resources.
A second strategy relied on improving the modelling methods to limit waste or poor-quality parts or improving part production. As an example, Mulye et al. developed a unified modelling approach to simulate the forming and consolidation of thermoplastic composites made from prepreg patches (Quilted Stratum Process). Through-thickness stress, final deformed shape of the plies including the squeeze flow effect and the changes in the orientation of fibers within the plies during and after the process were thus predicted. Manufacturers can thus design better tooling based on the outcomes of the numerical process simulation to achieve the desired product quality and final fiber orientation which results from the initial position of the patch, its forming and squeeze flow. Jan de Wit et al. proposed a numerical simulation of inductive heating for UD thermoplastic composites, combining electromagnetic and thermal effects. This led to improved design of UD laminates for easier induction welding during the assembly phase. Döbrich and Brauner developed a digital twin model, using a machine vision system based on a simple Microsoft Kinect camera to evaluate local fiber orientations after preform draping. This data can be compared to numerical simulations, enabling detection of deviations or unwanted defects. Similarly, Osterberger et al. evaluated experimental visual methods to analyze fiber orientations after part draping, as well as wrinkles or other potential defects, for comparison with numerical predictions. Results were more satisfactory for UD laminates than for cross-ply laminates which are more difficult to visually analyze. Jimenez Martin et al. analyzed wrinkling patterns in large draped NCF fabrics using 3D scans, highlighting the complexity of scaling-up the processes to large scale. Maidl et al. also made use of optical inspection to detect defects during the braiding of preforms. A single camera can track yarn curvature and angular spacing in real time using image analysis, to propose corrective actions as soon as these parameters deviate, thus enabling reduced scrap rates and improved preform reproducibility.
A third strategy investigated novel manufacturing and tooling concepts to lower energy demand and improve part processing kinetics and quality. Naseri et al. proposed an elegant way to produce nanocomposite film heaters for out-of-oven energy-efficient curing of thermoset composites. With these heating films, a composite based on a commercial prepreg was cured using 400 times less energy than in a conventional convection oven. Maes et al. introduced zonal heating of molds, to tailor the temperature profile to adapt it to part thickness variations. They showed that this approach can save up to 45% in energy consumption as compared to convection heating. Finally, Zhilyaev et al. proposed to further improve the additive manufacturing of continuous fiber reinforced thermoplastics through a post-consolidation process to lower voids. An advanced finite element model allowed to evaluate potential process-induced deformations and simulate porosity reduction; this model was validated against experimental data from the manufacturing of an aerospace part.
In summary, the need to develop sustainable solutions in composites is driving innovation in many areas. Contributions focus on the bio-sourcing of materials, the reduction of waste and energy consumption in production, the optimal design of parts and production tools, and better control of manufacturing processes to reduce defects and production waste. The use of digital process twins and advanced monitoring techniques contributes to this overall objective. Undoubtedly, the sustainability of composites solutions will remain the focus of future research.
CB: Writing–review and editing. BC: Writing–review and editing. LD: Writing–review and editing. CD: Writing–review and editing. VM: Writing–original draft, Writing–review and editing.
We would like to thank all the contributors of this Research Topic, as well as the reviewers, for their valuable contributions to the ECCM 20 legacy.
The authors declare that the research was conducted in the absence of any commercial or financial relationships that could be construed as a potential conflict of interest.
The author(s) declared that they were an editorial board member of Frontiers, at the time of submission. This had no impact on the peer review process and the final decision.
All claims expressed in this article are solely those of the authors and do not necessarily represent those of their affiliated organizations, or those of the publisher, the editors and the reviewers. Any product that may be evaluated in this article, or claim that may be made by its manufacturer, is not guaranteed or endorsed by the publisher.
Keywords: composite manufacturing, sustainability, energy efficiency, automation, digital twin
Citation: Binetruy C, Caglar B, Daelemans L, Dransfeld C and Michaud V (2023) Editorial: ECCM Research Topic on advanced manufacturing of composites. Front. Mater. 10:1296247. doi: 10.3389/fmats.2023.1296247
Received: 18 September 2023; Accepted: 19 September 2023;
Published: 27 September 2023.
Edited and reviewed by:
Robert Li, City University of Hong Kong, Hong Kong SAR, ChinaCopyright © 2023 Binetruy, Caglar, Daelemans, Dransfeld and Michaud. This is an open-access article distributed under the terms of the Creative Commons Attribution License (CC BY). The use, distribution or reproduction in other forums is permitted, provided the original author(s) and the copyright owner(s) are credited and that the original publication in this journal is cited, in accordance with accepted academic practice. No use, distribution or reproduction is permitted which does not comply with these terms.
*Correspondence: Véronique Michaud, dmVyb25pcXVlLm1pY2hhdWRAZXBmbC5jaA==
Disclaimer: All claims expressed in this article are solely those of the authors and do not necessarily represent those of their affiliated organizations, or those of the publisher, the editors and the reviewers. Any product that may be evaluated in this article or claim that may be made by its manufacturer is not guaranteed or endorsed by the publisher.
Research integrity at Frontiers
Learn more about the work of our research integrity team to safeguard the quality of each article we publish.