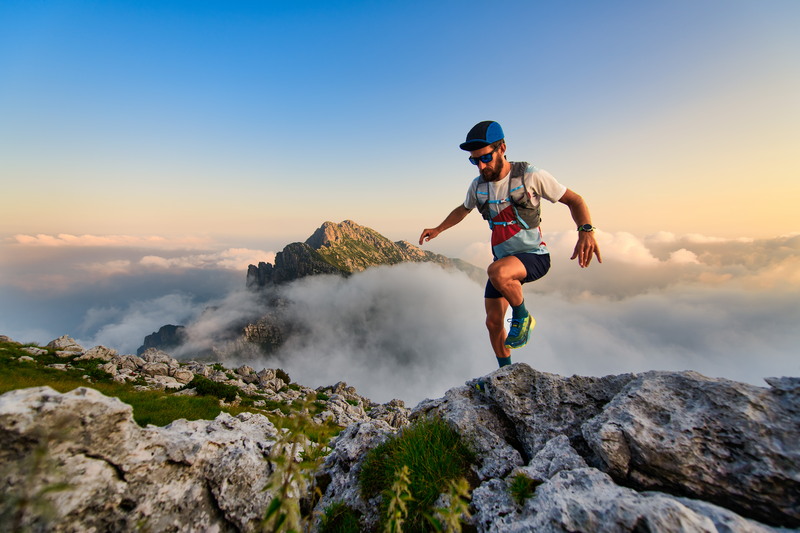
95% of researchers rate our articles as excellent or good
Learn more about the work of our research integrity team to safeguard the quality of each article we publish.
Find out more
EDITORIAL article
Front. Mater. , 08 November 2023
Sec. Environmental Degradation of Materials
Volume 10 - 2023 | https://doi.org/10.3389/fmats.2023.1288636
This article is part of the Research Topic Protective Coatings in Harsh Environments View all 5 articles
Editorial on the Research Topic
Protective coatings in harsh environments
Expanding human activity space and better utilizing natural resources are always the continuous driving forces for the development of human society. With the significant development of engineering technologies over the last two centuries, we humans can set foot on the moon and reach areas (deep space, deep sea, polar region, etc.) that intelligence life might not have touched. Such areas generally have extremely harsh service conditions for components (high service temperature, high stress level, extremely corrosive environments, high radiation level, etc.) which keep challenging the engineering technologies. Usually, a single material cannot meet all the service requirements. Therefore, a reasonable and practical solution is to apply a protective coating on the surface of mechanical components to increase the performance (the corrosion/erosion resistance, tribology performance, and thermal isolation). Coating technologies play a more and more critical role in meeting the service requirements in harsh environments.
In harsh service environments, the surface of material significant degradation in performing its task in service as a result of exposure. Failures often happen in the form of corrosion, oxidation, erosion, wear, and mechanical fracture. Though coating technology has proved to be an effective method of inhibiting surface failure in different environments and is also successfully applied in many equipment, the performance of protecting coatings would definitely change when the service environments go to the harsh, which might possess a higher temperature, higher pressure, more complex chemical combinations, and so on. Therefore, the primary purpose of this Research Topic is to explore coating materials with excellent protective function under harsh environments, providing technical support for the development of high-end equipment in more extreme conditions.
The scope of this Research Topic is specifically focused on the coating technologies which are developed to improve the performance of mechanical components serving in harsh environments. Harsh environments mean environments with different and more extreme characteristics in comparison with normal environments, such as high temperature, high pressure, high speed, complex chemical combinations, etc. The performance and mechanism of protective coatings, the design and fabrication of advanced coatings, and the application and effect of new coatings in different harsh environments are welcome. Subtopics of coating technologies include, but are not limited to, the following.
• Electrochemical deposition
• Chemical vapor deposition
• Physical vapor deposition
• Ion Implantation
• Thermal spraying
• Heat treatment
Consequently, this Research Topic has collected four significant contributions. The corresponding concise abstracts are briefly summarized below, respectively.
Wu et al. directed their study on “Combining the good tribological properties with the high adhesion strength of the amorphous carbon films in-situ grown on PI”. While polyimide (PI) finds widespread use in modern industries due to its exceptional heat resistance, dielectric qualities, radiation resistance, and chemical stability, its diminished hardness and subpar wear resistance curtail its operational lifespan. This experimentation involved the carbon plasma treatment of polyimide surfaces to facilitate the creation of amorphous carbon films, aided by in-situ transition layers. The microstructure, mechanical attributes, and tribological characteristics of the amorphous carbon films were meticulously investigated. Findings revealed a substantial enhancement in the hardness and wear resistance of the PI surface through the integration of an amorphous carbon film featuring an in-situ transition layer. Significantly, the in-situ transition endowed the film high adhesion strength on the PI substrate. The roles of carbon plasma in the deposition process of the amorphous carbon, specifically the deposition effect and the induction effect, which pertains to the impact on the top layer of the PI substrate, underwent thorough systematic analysis. This study effectively achieves the goal of safeguarding the PI surface with a high-adhesion-strength amorphous carbon film, additionally proposing a novel avenue for enhancing adhesion between hard coatings and flexible substrates.
Liu et al. centered their investigation on “Tuning microstructure and mechanical and wear resistance of ZrNbTiMo refractory high-entropy alloy films via sputtering power”. The remarkable properties of high-entropy alloy (HEA) films have garnered significant attention. This study involved the synthesis of a series of ZrNbTiMo refractory high-entropy alloy (RHEA) films through magnetron sputtering, employing sputtering power ranging from 90 to 210 W. The influence of sputtering power on the microstructure, mechanical characteristics, and tribological behavior of these innovative ZrNbTiMo RHEA films was systematically explored. These films exhibit a nanocomposite structure, comprising a combination of nanocrystalline and amorphous phases. With an increment in sputtering power, the film’s crystallinity initially rises from 13.03% to 20.07% and subsequently declines to 2.40%. ZrNbTiMo films deposited at 150 W manifest a high hardness of 7.5 GPa, a toughness of 0.437 MPa × m1/2, and superior wear resistance (wear rate: 5.223 × 10−7 mm3/N∙m) compared to other films. The mechanism governing nanocrystalline growth was elucidated by the interplay between diffusion capacity and the available atom deposition time. Extensive examination was conducted on the toughening and wear resistance mechanisms inherent to the ZrNbTiMo film.
Yu et al. directed their attention to “NaCl-induced hot corrosion behaviors of NiSiAlY coatings”. Within marine settings, NiCrAlY coatings containing elevated Cr content are susceptible to pronounced corrosion due to NaCl influence. Consequently, NiSiAlY coatings, varying in Si content, were introduced and applied to Ni-based superalloy via multi-arc ion plating. The resultant coatings predominantly comprised a γ’-Ni3Al phase alongside a minor β-NiAl phase. Subsequent NaCl-induced hot corrosion assessments were carried out at temperatures of 500, 600, and 700°C. Relative to Ni-based alloy substrates, NiSiAlY coatings displayed robust corrosion resistance to NaCl at elevated temperatures. However, an excessive Si quantity induced degradation in the coating’s hot corrosion resistance. In this work, the corrosion mechanisms of the tested coatings were discussed. Moreover, the role of Si was also investigated.
Pang et al., conducted a study on the “Effects of ambient humidity and sintering temperature on the tribological and antistatic properties of PEEK and CF/PEEK”. Polyether ether ketone (PEEK) is represents a notable example of the specialized engineering plastics. Owning to its high molding temperature, conventional plastic molding method and cavity abrasives often fall short of meeting requisite standards. To address this, pure PEEK samples were fabricated using vacuum hot pressing sintering technology across varying sintering temperatures. Mechanical property assessments and microstructural characterizations revealed that the pure PEEK sintered at 350°C exhibited exceptional friction and wear properties. Subsequently, PEEK and CF/PEEK composites were prepared at the optimal sintering temperature. Friction experiments for the prepared materials were conducted using UMT-2 apparatus. The impact of ambient humidity on the tribological, wear and antistatic properties of the materials was comprehensively investigated. The surface analysis and properties of the materials were measured by 3D profiler, scanning electron microscope, friction electrostatic tester. The findings indicated alteration in the friction coefficient of PEEK and CF/PEEK composite with rising ambient humidity. The wear rate of PEEK initially decreased and then increased, reaching its lowest of 3.09 × 10−5 mm3/Nm at an ambient humidity of 40%. The wear rate of CF/PEEK composite exhibited slight variations, significantly lower than that of PEEK, with adhesive wear being the primary mechanism. Surface frictional static electricity of both PEEK and CF/PEEK composites diminished as humidity levels increased.
YW: Writing–original draft, Writing–review and editing. GZ: Writing–review and editing. KZ: Writing–review and editing. XZ: Writing–review and editing. DZ: Writing–review and editing.
Author DZ was employed by Forschungszentrum Jülich GmbH.
The remaining authors declare that the research was conducted in the absence of any commercial or financial relationships that could be construed as a potential conflict of interest.
All claims expressed in this article are solely those of the authors and do not necessarily represent those of their affiliated organizations, or those of the publisher, the editors and the reviewers. Any product that may be evaluated in this article, or claim that may be made by its manufacturer, is not guaranteed or endorsed by the publisher.
Keywords: harsh environments, protective coatings, degradation, corrosion, wear
Citation: Wang Y, Zhang G, Zhang K, Zhang X and Zhou D (2023) Editorial: Protective coatings in harsh environments. Front. Mater. 10:1288636. doi: 10.3389/fmats.2023.1288636
Received: 04 September 2023; Accepted: 06 October 2023;
Published: 08 November 2023.
Edited and reviewed by:
Changdong Gu, Zhejiang University, ChinaCopyright © 2023 Wang, Zhang, Zhang, Zhang and Zhou. This is an open-access article distributed under the terms of the Creative Commons Attribution License (CC BY). The use, distribution or reproduction in other forums is permitted, provided the original author(s) and the copyright owner(s) are credited and that the original publication in this journal is cited, in accordance with accepted academic practice. No use, distribution or reproduction is permitted which does not comply with these terms.
*Correspondence: Yongxin Wang, eXh3YW5nQG5pbXRlLmFjLmNu
Disclaimer: All claims expressed in this article are solely those of the authors and do not necessarily represent those of their affiliated organizations, or those of the publisher, the editors and the reviewers. Any product that may be evaluated in this article or claim that may be made by its manufacturer is not guaranteed or endorsed by the publisher.
Research integrity at Frontiers
Learn more about the work of our research integrity team to safeguard the quality of each article we publish.