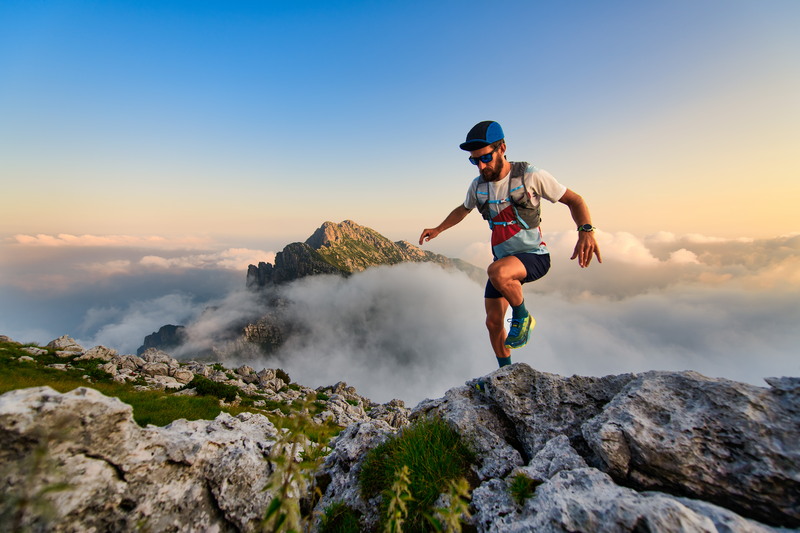
95% of researchers rate our articles as excellent or good
Learn more about the work of our research integrity team to safeguard the quality of each article we publish.
Find out more
ORIGINAL RESEARCH article
Front. Mater. , 24 November 2023
Sec. Polymeric and Composite Materials
Volume 10 - 2023 | https://doi.org/10.3389/fmats.2023.1267514
This article is part of the Research Topic Development of Novel Biodegradable Materials under Cryogenic Environment View all 6 articles
This research aims to investigate the mechanical performance of the different weight proportions of nano-TiO2 combined with Kevlar fiber-based hybrid composites under cryogenic conditions. The following parameters were thus considered: (i) Kevlar fiber mat type (100 and 200 gsm); (ii) weight proportions of TiO2 nanofiller (2 and 6 wt%); and (iii) cryogenic processing time (10–30 min at −196°C). The composites were fabricated through compression molding techniques. After fabrication, the mechanical characteristics of the prepared nanocomposites—such as tensile, bending, and impact properties—were evaluated. The optimal mechanical strength of nanofiller-based composites was analyzed using response surface methodology (RSM) and artificial neural networks (ANNs). Compositions, such as four weight percentages of nano-TiO2 filler, 200 gsm of the Kevlar fiber mat, and 20 min of cryogenic treatment, were shown to produce the maximum mechanical strength (65.47 MPa of tensile, 97.34 MPa of flexural, and 52.82 J/m2 of impact). This is because residual strains are produced at low temperatures (cryogenic treatment) due to unstable matrices and fiber contraction. This interfacial stress helps maintain a relationship between the reinforcement and resin and improves adhesion, leading to improved results. Based on statistical evaluation, the ratio of correlation (R2), mean square deviation, and average error function of the experimental and validation data sets of the experimental models were analyzed. The ANN displays 0.9864 values for impact, 0.9842 for flexural, and 0.9764 for tensile. ANN and RSM models were used to forecast the mechanical efficiency of the suggested nanocomposites with up to 95% reliability.
Research interest in the use of natural fiber as reinforcement in composites has grown over the past 15 years to create environmentally friendly, renewable sources. The recyclability, availability, and excellent mechanical properties of natural fabrics are the main reasons for accelerating their use as reinforcement to replace conventional fibers (Luzi et al., 2019; Behnam Hosseini, 2020). Organic fiber-based composite materials have aroused interest because they can replace artificial fiber-based composites. Biosourced fibers can meet industry needs for reinforced composites by 31% (Li et al., 2006; Su et al., 2008). Bast fiber-based (kenaf, hemp, ramie, and jute) composites have brought to attention some natural materials accessible in various industries, including maritime, automobile, and architecture. However, the watery character of organic fiber composites, which affects the interface qualities between reinforcement and resin and reduces the composite’s mechanical capabilities, is a major problem (Rana et al., 1998; Li et al., 2000). Textile composites are commonly utilized; these incorporate reinforcement of either natural or synthetic fibers or textiles within the matrix. Composite materials, which are characterized by considerably reduced weight, exhibit enhanced mechanical, thermal, electrical, and ballistic properties. Depending on the application’s specific requirements, these attributes can be further fine-tuned with diverse surface treatments (Velmurugan and Babu, 2020). Synthetic fibers constitute the primary constituents; these encompass a range of materials including glass, carbon, boron, polyethylene, and aramid fibers. Among these, para-aramid Kevlar fibers have stood out, featuring 1,4-para-substituted aromatic rings. These monomeric chains form unidirectional hydrogen bonds that combine to generate sheets and are subsequently rolled into microfibrils with diameters of 12–60 nm. When these microfibrils aggregate, they form Kevlar fibers known for their rigidity and nonlinear behavior under crosswise compression and longitudinal elasticity when subjected to longitudinal strain (Thakur et al., 2014). Highly crystalline poly-aramid Kevlar fibers exhibit densities of 1.44–1.47 g per cm3. Kevlar fibers come in various grades, including K-29 (maximal hardness), K-49 (greater elasticity), K-100, K-119 (enhanced ductility), K-129 (superior shock resistance), K-149, and KM2 (notable rigidity and toughness). Kevlar fibers are favored as textiles due to their ability to reinforce the polymeric matrix, yielding Kevlar fiber-reinforced polymer (KFRP) textile composites. These composites are renowned for their exceptional durability, elasticity, impact resistance, shock-absorbing capabilities, heat resistance, thermal insulation, low density, minimal thermal conductivity, and heightened multidimensional consistency (Prasob and Sasikumar, 2018; Ganesan et al., 2020). The matrix material in these composites can be thermoset polymers such as epoxy, phenolic, or bismaleimide, known for their exceptional toughness, high heat resistance, and favorable electrical properties. Alternatively, a thermoplastic polymer may be employed, such as low- or high-density polyethylene, polyester, acrylics, or polypropylene (PP). KFRPs find widespread application in creating thermal insulators with stress-bearing rigidity across industries like cryogenics, aerospace, military, and law enforcement protection against high-velocity projectiles and containment systems for propulsion engines (Uma Devi et al., 1997; Prasob and Sasikumar, 2019). Due to their anisotropic behavior and composition, Kevlar fibers exhibit lower compressive, shear, and torsional strength and elastic modulus. To add specific strength and rigidity to fiber-based composites, Kevlar fibers are incorporated into a variety of topologies, including woven patterns (such as plain, twill, or satin weaves), braided yarn in bi- or tri-dimensional configurations, and unidirectional long or chopped fibers. The composite’s matrix component imparts stiffness and stability (Praveenkumara et al., 2022).
The fundamental flaw of the epoxy matrix, which limits its usage, is lower tensile strength, which is caused by excessive cross-linking concentration and the stress distribution created during curing. Numerous secondary nanofillers have augmented it to address the problem of poor yield stress, including nanosilica, carbon nanofibers, graphene, fumed silica, and rubber nanoparticles (Hemanth et al., 2017; Mannan et al., 2022). Epoxy nanocomposite is a secondary phase strengthened by nanofillers. The term “fiber-reinforced epoxy nanocomposite” refers to an epoxy nanocomposite that contains fiber as a reinforcement. Selecting the proper nanosized additives for sophisticated polymeric composites improves the effectiveness of organic composites (Chowdhury et al., 2021; Jawaid et al., 2022). As a result, adding nanofiller to existing fillers creates cutting-edge composites with numerous benefits. A much larger surface region between fillers and the polymer matrices is created per unit of volume due to the increased incidence angle of nanosized additives (Nayak et al., 2022). Consequently, this type of nanocomposite has excellent versatility, high strength, stiffness, lightweight, and corrosion-resistant qualities. The addition of nanofiller has improved tensile, thermostability, electromagnetic, and anaerobic decomposition qualities (Ramesh et al., 2022). Regarding metallic and metal oxide nanomaterials as reinforcement agents in fiber-reinforced composites, TiO2 nanoparticles are thought to be the most popular nanofiller now available. Amazing specificity, excellent dispersion, high adhesion, superior thermal resilience, and strong chemical cleanliness are some of titanium oxide’s appealing characteristics (Alsaadi et al., 2017; Maharana et al., 2021). However, the expense of such nanoparticles is by far their biggest drawback, although this is offset by employing a modest quantity of nanofiller. Optimum mechanical qualities are often only possible with minimal filler loading (Santhosh et al., 2018).
The hybridization of lightweight materials with more than one reinforcement component, such as fibrous materials, has been extensively studied. Investigators have attached great importance to hybrid reinforced composites because of their special ability to customize mechanical properties (Friedrich, 2018). Fiberglass, carbon, Kevlar, and basalt are frequently used as reinforcing materials in hybrid composites and a few nanoscale nanoparticles. Since it has the greatest mechanical properties and dimensional stability of any reinforcement, Kevlar fiber is one of the most commonly used hybrids in natural fiber composites (Matykiewicz, 2020; Hussian Siyal et al., 2021). Due to its high cost and lack of recyclability, this fiber is regarded as ineffective, despite its excellent strength and rigidity. There are several important benefits to adding titanium dioxide (TiO2) filler to Kevlar composite materials. It improves the material’s mechanical qualities, such as impact resistance and tensile strength, making it more resilient and appropriate for structural uses. TiO2 offers superior UV protection for outdoor and aerospace applications, reducing material deterioration from prolonged sun exposure. Additionally, it lessens water absorption and increases thermal stability, which is critical for applications requiring moisture and heat resistance. Additionally, TiO2 can affect electrical and dielectric characteristics for applications such as electronics, and it enhances flame resistance, making it important in fire safety applications. Overall, Kevlar composites perform better, are more durable, and are more appropriate for various applications when TiO2 filler is added. The increasing use of Kevlar materials in cryogenic environments is a new field. Artificial materials composed of fibers can have better mechanical qualities owing to their cold features (Yogesh et al., 2022; Velmurugan and Natrayan, 2023). For example, materials used to build airplanes should be able to withstand extreme heat or cooling rates of up to 200 °C (Xu et al., 2017; Kara et al., 2018). Cryogenically processed lightweight materials and their matrix have greater strength, are often more durable, and have better durability and abrasion resistance. Consequently, liquid N2 processing of materials may become a crucial feature of innovative products to enhance the characteristics of composites made from organic resources (Zhang et al., 2009; Sethi et al., 2015).
Investigating how well these hybrid materials work in a cryogenic setting is novel. Due to thermal expansion and embrittlement, freezing temperatures can substantially affect the mechanical properties of a substance. An exciting research component examines how hybrid materials maintain or improve their mechanical features under difficult circumstances. The current project is unique as it is one of the first to analyze nanocomposite with interlaced Kevlar as reinforcement, and nano-TiO2 as filler in the epoxy matrix in cryogenic temperatures. The findings of this study might pave the way for novel applications of natural fiber-based composite in severe cold conditions.
The fundamental goal of the current research is to build, evaluate, and improve the material features of hybrid composite materials using the following conditions: weight proportions of nano-TiO2, thickness of Kevlar fiber in gsm, and duration of cryogenic processing. To complete these objectives, the composites were fabricated hybrid nanocomposites which had been compression-molded. The nanocomposites were fabricated using the following parameters: weight ratio of TiO2 filler, type of Kevlar mat, and cryogenic treatment duration. After fabrication, the composites were tested, and their impact on process parameters was optimized using RSM and ANN networks. This study offers a unique combination of materials, investigates how they behave in a difficult setting, employs cutting-edge statistical and machine learning approaches for optimization, and discusses the significance of the results for real-world applications. These add to the topic’s originality.
Huntsman epoxy resin (AW 106) with a 1.52 g/cm3 density and hardener HV 953 U were used as matrix materials in the current research. The resin and matrix were procured from Deesh Chemical Industries, Chennai, Tamil Nadu, India. The Kevlar fiber mat (K-129 type with 200 gsm) used as the current study’s reinforcement was purchased from Rithu Recourses, Salam, India. The filaments were splashed in clean water before use and dehydrated in an oven at 75 °C. The highest purity and quality titanium oxide (TiO2) was purchased from Naga Chemical Industry in Chennai, Tamil Nadu, India. Table 1 shows some typical properties of the reinforcement and fillers.
For composite preparations, 200 gsm (grams per square meter) of Kevlar fiber was preferred since it improves mechanical qualities and structural integrity and meets application-specific criteria. Improved strength, better load-bearing ability, and improved durability against delamination are all made possible by Kevlar fiber’s higher gsm, resulting in a composite product with superior hardness and impact resistance. In order to ensure that the composite satisfied the required performance objectives and was well-suited for its intended use—whether in aviation, the military, automobiles, or other sectors—the decision was frequently dictated by the particular demands of the application.
The composite was fabricated using compression molding. In the first step, we mixed the different weight proportions of nano-TiO2 particles (2, 4, and 6 wt%) with epoxy resin through an ultrasonicator. This process took approximately 10 min, using ultrasonic waves to help mix them evenly. After mixing, TiO2 and epoxy were mixed in a special tube, and high-frequency sound waves were used to further mix them for 30 min. After that, the hardener was added to an epoxy–nanofiller mixer in a suitable weight proportion (10:1). Then the prepared mixer was poured into the Kevlar fiber mat, which was placed into a 300 × 300 × 3 mm metallic mold. Finally, the prepared mold was placed into the compression molding machine. The temperature and pressure of the compression molding process were maintained at approximately 170 °C and 15 bar, respectively. The same process was repeated up to 17 times to produce 17 different composite plates. Once the compression molding process was completed, the fabricated hybrid laminates were placed under ambient conditions for 24 h. Finally, the fabricated laminates were cut into different sizes (based on the ASTM standard) to examine their mechanical properties. Table 2 displays the composite’s features and respective concentrations.
A regulated high-temperature liquid chamber with preprogrammed controllers was utilized for the cryogenic rehabilitation process. The temperature was cooled to 196 °C using a measured preservation rate (3 °C/min). According to the concept designs, the created samples were submerged in N2 fluid at 77 K for 10, 20, and 30 min of cold working. After preparation, the composite was periodically warmed to an ambient temperature of 40°C/h.
Response surface methodology (RSM) is a combination of quantitative methodologies that can be utilized to examine data and their interaction effects through analytical trials to simultaneously build and resolve multidimensional problems. RSM is a geometrically based method used to estimate and describe the experimentally ideal conditions and a polynomial equation to construct a relationship between direct and indirect parts. A well-known RSM concept for enhancing strength properties is the Box–Behnken design (BBD). All longitudinal, nonlinear, and two different relationships were estimated using the spinning lesser designs that constitute the Box–Behnken model. Design decrease is not permitted: there are no corners in the design process. The axis endpoints are outside the rotating full factorial entity’s created visual studio container. The direction from the center of the design enabled the anticipated response to be calculated with the same variation. As shown in Table 1, extraction experiments utilizing BBD were conducted on three factors: Kevlar fiber mat (A), weight ratio of Kevlar (B), and cryogenic treatment durations (C). Results were calculated using a least-squares method for multi-regression evaluation (Sethi et al., 2015).
where i stands for a coding number of a self-determining component, yi for its actual value, yo for its real value depending on the middle, and y for its modifying requirements. In the BBD, a cluster of spots only exists at the halfway point of an edge piece and the simulated center of the multidimensional blocks. The average results from a set of process conditions were utilized after three test iterations. The quadratic polynomial equation may be employed to prompt the quantitative response surface on such variables in a configuration with the three primary self-determining elements, Y1, Y2, and Y3 (2):
where X is the expected response, α0 is the perfect quantities, Z1, Z2, and Z3 are momentous influences,
The tensile characteristics of both primary and hybridized materials were tested according to the ASTM D3039-76 standard. The sample measured 250 × 25 × 3 mm. According to the ASTM D3039-76 regulation, the gauge length throughout the experiment was 150 mm, and the crosshead speeds were 2 mm/min. Measurements were made of the tensile characteristics, strain, and modulus of dry and saltwater-aged materials. The test was conducted using Instron-3389 Universal Testing Equipment. Three specimens of each type were used to examine them, and the average information was then published. This bending test was carried out according to ASTM D7264 specifications. The sample measured 70 × 12.7 × 3. The depth ratio for most of the experiment’s span length of 60 mm was 20:1. Utilizing the ASTM D256 criteria, the impact strength of both the original and hybridized composites was assessed. A 65 × 12.7 × 3 mm specimen was employed for the evaluation. Every specimen was examined three times, with the average result being noted. The fracture surface of the fabricated composites was examined through a scanning electron microscope (SEM). This mechanical and morphological analysis was conducted at SRM University, Chennai, Tamil Nadu, India.
The RSM method for the mechanical features of hybridized fiber composites of Kevlar and nano-TiO2 is as follows: this study discovered that the tension, bending, and shock resistance values of the connection factor (R2) were, respectively, 0.9846, 0.9836, and 0.9850, proving the method’s suitability and the generated parameter’s precision. It is obvious that the relationships between tensile properties and respective components effectively compensate for information errancy. In Eqs 3–5, the symbols A, B, and C represent the Kevlar fiber types, TiO2 filler weight proportions, and cryogenic treatment durations, respectively.
The ANOVA approach often controls the RSM design and its variables’ adequacy and relevancy. The F-value is used to determine the suitability of the model. The ANOVA outcomes for the material characteristics of mixed lightweight materials are displayed in Tables 3–5. Using a prototypical F-value of 49.47, Table 3 demonstrates that the cubic model is adequate for forecasting ductility. Table 2 shows that the F rate of a quadratic equation prototype is below 0.0001, demonstrating that the prototypical is substantial. Furthermore, this study explores the diverse impacts of different Kevlar fiber types (labeled as A) and nano-TiO2 (designated as B) on crucial models (Sabarinathan et al., 2022).
Using a prototypical F rate of 46.74, Table 4 demonstrates that the cubic prototypical is suitable for forecasting bending behavior. The “Prob > F” rate of a quadratic equation prototypical is below 0.0001, indicating that the prototypical is substantial. Similarly, the impact behavior results were achieved with an F-value of 50.93. The weight ratio of the nano-TiO2 models in the Kevlar fiber type (A) and (B) models is also important. In addition to the previously listed models, some others are less evident. Moreover, the weight proportion of the nano-TiO2 models in Kevlar fiber type (A) is important. A couple more are not immediately apparent in addition to previously described models. Figure 1 shows the stress–strain relationship of tensile and flexural behavior.
The influence of fiber thickness (gsm) on the mechanical behaviors of Kevlar–nano-TiO2-mixed epoxy composite, such as tension, bending, and impact strength, is depicted in Figures 2A–C. The finest mechanical properties of Kevlar fiber are 200 gsm, which is superior to 100 gsm and 150 gsm. Poor levels at 100 gsm composite are due to inadequate load transmission caused by uneven fiber dispersion throughout matrices. Consequently, the composites industrialized a lattice district through a feeble fiber-to-fiber interface. The composite material was ripped out of the matrix when added in this condition. This illustrates that the 100 gsm contributing positively to the Kevlar fiber composite is inadequate for maintaining the mechanical stress. The composite’s mechanical properties improve when the mixture’s fiber is raised from 100 gsm to 200 gsm. This is primarily attributable to the fibers and matrix forming a strong link that prevented gaps in the composites by accepting additional fibers and maintaining proper load distribution. The collaboration between the reinforcement and the resin improved the fiber quantity. Consequently, more power is necessary to disrupt the link between the interlaced cellulose fibers (Mannan et al., 2022; Mohit et al., 2023).
FIGURE 2. Tensile behavior of TiO2/Kevlar-based nanocomposites, (A) Kevlar Mat type vs. Weight ratio of TiO2 vs. Tensile strength: (B) Kevlar Mat type vs. Cryogenic treatment vs. Tensile strength; (C) Weight ratio of TiO2 vs. Cryogenic treatment vs. Tensile strength.
The efficacy of the bending characteristics of the nano-TiO2 filler additives is shown in Figures 3A–C. Four weight percentages (4 wt%) of nano-TiO2 showed greater mechanical strength than 2 wt% and 6 wt%. A 4 wt% content of nano-TiO2 in resin may have better stress distribution and transmission, explaining its improved mechanical properties. The number and size of holes in the polymeric matrix improved with the addition of more loaded TiO2, which impacted the decohesion binding between the matrix and the reinforcement (Alsaadi et al., 2017; Hussian Siyal et al., 2021). Incorporating much more filled TiO2 into the polymeric matrix enhanced the permeability and diameter of the pores, which influenced the decohesion binding between fibers and matrix. Consequently, the adhesion, interwoven Kevlar, and combined nanoscale padding formulations produced adequate adhesives between surface nerve entrapment at a concentration of 4 wt%. Furthermore, the inclusion of 2 wt% and 6 wt% TiO2 resulted in a poor outcome, showing decreased strength properties. Moreover, 2 wt% and 6 wt% concentrations exhibited poor boundary adhesive of composites in woven Kevlar and polymeric, resulting in agglomerate due to poor adhering and poor hybrid functional capabilities.
FIGURE 3. Bending behavior of TiO2/Kevlar-based nanocomposites, (A) Kevlar Mat type vs. Weight ratio of TiO2 vs. Flexural strength; (B) Kevlar Mat type vs. Cryogenic treatment vs. Flexural strength; (C) Weight ratio of TiO2 vs. Cryogenic treatment vs. Flexural strength.
During cryogenic treatment, the nanocomposite surface experienced heat fluctuation and was visible in fluid N2 at −196 °C. Cryo-ablation is an exclusive approach to progressing thermoplastic nanocomposites’ material properties. Figures 4A–C shows how polymer-based hybrid composites’ mechanical properties are affected by cryogenic handling, which may be caused by the residual pressure formed through the firmness interface due to the compound substance’s freezing effort. Residual strains are produced at low temperatures due to the shifting matrices and fiber contraction. This interfacial stress helps maintain a relationship between the reinforcement and resin and improves adhesion, leading to improved results, although this is only feasible for the first 20 min. Thereafter, the composites’ mechanical characteristics decreased. This could occur due to layer-specific microcracking, potholing, or excessive stress (Sethi et al., 2015; Ganesan et al., 2020; Velmurugan and Babu, 2020). Figures 5A–C demonstrates the RSM values of actual and predicted values of TiO2-based hybrid composites.
FIGURE 4. Impact behavior of TiO2/Kevlar-based nanocomposites, (A) Kevlar Mat type vs. Weight ratio of TiO2 vs. Impact strength; (B) Kevlar Mat type vs. Cryogenic treatment vs. Impact strength; (C) Weight ratio of TiO2 vs. Cryogenic treatment vs. Impact strength.
FIGURE 5. Actual vs. predicted values of TiO2/Kevlar-based hybrid nanocomposites, (A) tensile; (B) flexural; and (C) impact behaviors.
It is widely known that modeling and analysis of the extraction procedure may anticipate the extraction method and complex linkages. A useful tool for interpreting the link between inputs and enhanced experiments is artificial neural networks (ANNs). The ANN model can generalize recently acquired knowledge and learn the structure of the iterative mechanism from historical data. The input, hidden, and output neurons of the ANN model are three separate layers that could be used to estimate the association between the source and destination nodes. Learning (70%), evaluation (15%), and verification (15%) are the three categories into which all the information is arbitrarily split (Ismail et al., 2022; Pragadish et al., 2022).
The output of the ANN model is assessed using the performance indicators of mean square and regression coefficients. The toolkit of MATLAB Version R2015 was used to run the ANN calculations for this investigation. We used a three-layer ANN with a Levenberg–Marquardt back-propagation algorithm of 1,000 steps, a tangential sigmoidal function at the hidden state, and a linear activation functional at the output nodes. After constructing the system, the given statistical models are incorporated into the 4–4–3 ANN design (Figure 6). A correlation matrix and a proportional confidence level were used to evaluate the strategy. The entire flowchart for the ANN predictions is shown in Figure 7. The existing ANN system uses Formula 4 to compute the anticipated average inaccuracy.
Table 6 displays the learning, verification, and assessment measurement categories and the estimated error percentage. Figures 8A–C show how well the neurological theory predicts the future. “Tensile” had a reliability of all parameters of 0.9764. The average number of predicted errors fell below 3%, with values of 0.9842 for bending and 0.9864 for impact; Figure 9 demonstrates this. Figures 10A–C illustrate the study results and the relationship between network flexibility. Observed variables were within the desired limits, and the investigation was applied to assess the accuracy of experimental data (Hemanth et al., 2017; Santhosh et al., 2018; Devarajan et al., 2021). The reliability of the investigation, prognosis, and ANN models is summarized in Figure 9. The study of experimental data revealed that both the RSM and ANN procedures provide trustworthy outcomes.
FIGURE 8. Performance features of the ANN model: (A) tensile; (B) flexural; and (C) impact behaviors.
FIGURE 10. Comparison of experimental/ANN outcomes of (A) tensile; (B) flexural; and (C) impact behaviors of TiO2-based nanocomposites.
Compared to RSM-computed observations, the ANN method produced good outcomes and more reliable forecasts with an accuracy rating of 95%. The ANN optimum model facilitates the integration of the variability contributing to a given cast composition. Since it lowers costs, this is ideal for the parts of the automotive sector that employ natural fibers. Table 7 displays the mechanical property performance that performs best based on observable, analytical, and ANN results.
The SEM photographs of Kevlar and Kevlar/TiO2 hybrid composites are shown in Figures 11A, B. Figure 11A shows the Kevlar fiber strengthened with epoxy. It was discovered that the strands had been pulled out of the polymer and that they developed a crack throughout the fiber. The intricate fiber pattern was a barrier against polymeric distortion and fracture development. Most of the TiO2 nanoparticles remained well coupled with the polymers for the 4 wt% of TiO2-reinforced Kevlar fiber epoxy laminated materials, as shown in Figure 11B. This indicates that the TiO2 nanoparticles were present in the polymer. However, a fracture might form through the pores on the TiO2 in well-combined TiO2 nanoparticles, as shown by a thin epoxy polymer film attached to the TiO2 nanoparticles. The surface of the fracture also appeared to be rough and to include branching, bending cracks, and crack pinning. Spherical silica-reinforced epoxy polymer was also studied for these features (Deka et al., 2005; Yıldırım et al., 2021) The outermost layer of fracturing for the 6 wt% TiO2 and Kevlar fiber-reinforced epoxy polymer was rough, and the spaces surrounding the fillers suggest that the TiO2 particles may have de-bonded from the polymer. Additionally, Figure 11C shows that fillers tended to collect. TiO2 nanoparticle buildup served as a carrier of failure that might further weaken the mechanical properties. After 20 and 30 min of cryogenic treatment, hybrid composites fail, as shown in Figures 11D, E. TiO2 filler is well bonded to fiber and matrix in Figure 11D. This may have occurred due to compressive stress in the laminate’s topmost layer. The matrix’s fracture propagation is shown in Figure 11E, which may be due to excessive tension building up in the composite.
FIGURE 11. Microstructural images of hybrid composites after tensile (MPa) failures of (A) pure Kevlar; (B) Kevlar/4 wt% of TiO2; (C) Kevlar/6 wt% of TiO2; (D) cryogenic at 20 min treatment, and (E) cryogenic at 30 min treatment.
An important development in composite substances and their efficacy in harsh environments may be seen in statistical optimization research employing RSM and ANN approaches. This discovery has revealed new ways of combining Kevlar fibers, epoxy matrix, and TiO2 filler to obtain improved mechanical qualities, which exceed what these materials are capable of on their own.
• Under this investigation, the lightweight material’s performance of TiO2-based interlaced Kevlar/epoxy-based hybridization was created and improved using RSM. The process parameter factors for TiO2- and Kevlar-influenced lightweight materials were set at 4% TiO2, 200 gsm of Kevlar, and 20 min durations of cryogenic processing following the multi-response surface approach. Correspondingly, the correlation coefficients for tension, bending, and impact strength (R2) are 0.9846, 0.9836, and 0.9850.
• The weight proportion of the inclusion of TiO2 additives is one of the greatest crucial elements, according to the RSM conclusion. Hybrid composites with improved mechanical properties result from the fusion of several elements. Since regulated fillers reinforce stability, the 4 wt% of TiO2 demonstrated increased mechanical strength compared to 2 wt% and 6 wt%. ANN verifies this because 6 wt% filler creates accumulation, which reduces the mechanical properties of the composites.
• 200 gsm of Kevlar fiber provides maximum mechanical strength compared to 100 gsm. This is because a mat made of 200-gsm fiber requires greater force to separate the fiber bundles. Cryogenic therapy lasting 20 min rather than 10 and 30 min shows the greatest strength. The fiber and matrix have higher compatibility after 20 min of cryogenic treatment.
• The ANN also displays values of 0.9864 for impact strength, 0.9842 for flexural, and 0.9764 for tensile. ANN and RSM models were used to predict the mechanical efficiency of the suggested nanocomposites with up to 95% reliability. Depending on the results of mechanical qualities as opposed to the real, RSM and ANN are anticipated to be more dependable.
The study of cryogenic settings is particularly interesting because it provides insights into how hybrid composites behave when exposed to extreme temperature variations. The difficulties presented by cold temperatures highlight the significance of creating materials capable of preserving their firmness in these circumstances.
The study’s conclusions about the statistical techniques used to optimize TiO2-based interlaced Kevlar/epoxy hybrid composites have important ramifications for various applications. These improved lightweight materials exhibit superior mechanical qualities over and beyond those of their constituent parts. Advanced aircraft materials that can tolerate large temperature swings and provide hardness and endurance in challenging circumstances are examples of potential uses. These composite materials may also be used to create components with high strength and resistance appropriate for the automotive and military sectors. With precise weight ratios of TiO2 and Kevlar fiber, the improved composite formula guarantees better performance and dependability, making it a potential option for applications where structural integrity is crucial. The study also points to possible applications in industries such as construction, where stronger mechanical properties are crucial. These results open the door to creating composite substances with various uses in challenging situations, including aircraft and automobiles.
• Advanced material development: The results offer a solid basis for further research into composite materials. Future studies might concentrate on customizing these materials for particular uses, such as lightweight and durable parts for the aerospace, automobile, and defense sectors. This may result in novel materials with even more remarkable qualities.
• Environmental considerations: Developing environmentally friendly composites has potential as people’s awareness of ecological issues grows. Research into environmentally friendly matrices, fillers, and manufacturing methods may create green hybrids that satisfy performance and sustainability standards.
• Smart composite materials: The creation of smart materials may be made possible by incorporating sensors and monitoring features into such composites. In particular, these substances are important for monitoring structural health in civil and aeronautical engineering applications because they can give immediate information on their strength and damage.
• Automation and industrial adoption: Another interesting area is the industrial use of these sophisticated composites. It is possible to expedite the manufacturing process and increase its cost-effectiveness and accessibility for various applications using automation and optimization.
• Cryogenic applications: Additional investigation into the behavior of these hybrid composites in cryogenic environments can yield important information for space exploration, medical technology, and other sectors that deal with extremely low temperatures.
• Predictive modeling: The precision of forecasting mechanical characteristics can be improved by creating more complex forecasting algorithms, perhaps with the help of artificial intelligence and machine learning. This would simplify the creation of materials with particular characteristics for various purposes.
• Cross-disciplinary collaborations: Creative solutions can be discovered through collaboration involving researchers from other domains, engineers, and materials scientists. For instance, the medical sector may profit from these materials’ strength, biocompatibility, and low weight to create implants and prosthetics.
The potential for innovation in a variety of sectors as well as the need for superior materials in various industries presents a large and attractive scope for advanced research in the field of hybrid materials.
The original contributions presented in the study are included in the article/Supplementary Material; further inquiries can be directed to the corresponding author.
LN: conceptualization, methodology, resources, validation, and writing–original draft. GJ: data curation, formal analysis, methodology, and writing–review and editing. PP: supervision, visualization, and writing–review and editing. SD: project administration, resources, supervision, and writing–review and editing.
The author(s) declare that no financial support was received for the research, authorship, and/or publication of this article.
The authors declare that the research was conducted in the absence of any commercial or financial relationships that could be construed as a potential conflict of interest.
All claims expressed in this article are solely those of the authors and do not necessarily represent those of their affiliated organizations, or those of the publisher, the editors, and the reviewers. Any product that may be evaluated in this article, or claim that may be made by its manufacturer, is not guaranteed or endorsed by the publisher.
Alsaadi, M., Ugla, A. A., and Erklig, A. (2017). A comparative study on the interlaminar shear strength of carbon, glass, and Kevlar fabric/epoxy laminates filled with SiC particles. J. Compos. Mater. 51 (20), 2835–2844. doi:10.1177/0021998317701559
Behnam Hosseini, S. (2020). Natural fiber polymer nanocomposites. Fiber-Reinforced Nanocomposites Fundam. Appl., 279–299. doi:10.1016/B978-0-12-819904-6.00013-X
Chowdhury, M. A., Hossain, N., Shuvho, M. B. A., Kowser, M. A., Islam, M. A., Ali, M. R., et al. (2021). Improvement of interfacial adhesion performance of the kevlar fiber mat by depositing SiC/TiO2/Al2O3/graphene nanoparticles. Arabian J. Chem. 14 (11), 103406. doi:10.1016/j.arabjc.2021.103406
Deka, D. J., Sandeep, G., Chakraborty, D., and Dutta, A. (2005). Multiobjective optimization of laminated composites using finite element method and genetic algorithm. J. Reinf. Plastics Compos. 24 (3), 273–285. doi:10.1177/0731684405043555
Devarajan, Y., Nagappan, B., Choubey, G., Vellaiyan, S., and Mehar, K. (2021). Renewable pathway and twin fueling approach on ignition analysis of a dual-fuelled compression ignition engine. Energy and Fuels 35 (12), 9930–9936. doi:10.1021/acs.energyfuels.0c04237
Friedrich, K. (2018). Polymer composites for tribological applications. Adv. Industrial Eng. Polym. Res. 1 (1), 3–39. doi:10.1016/j.aiepr.2018.05.001
Ganesan, V., and Kaliyamoorthy, B. (2020). Utilization of taguchi technique to enhance the interlaminar shear strength of wood dust filled woven jute fiber reinforced polyester composites in cryogenic environment. J. Nat. Fibers 19, 1990–2001. doi:10.1080/15440478.2020.1789021
Hemanth, R. D., Kumar, M. S., Gopinath, A., and Natrayan, L. (2017). Evaluation of mechanical properties of E-Glass and coconut fiber reinforced with polyester and epoxy resin matrices. Int. J. Mech. Prod. Eng. Res. Dev. 7 (5), 13–20. doi:10.24247/ijmperdoct20172
Hussian Siyal, S., Ali Jogi, S., Muhammadi, S., Ahmed Laghari, Z., Ali Khichi, S., Naseem, K., et al. (2021). Mechanical characteristics and adhesion of glass-Kevlar hybrid composites by applying different ratios of epoxy in lamination. Coatings 11 (1), 94. doi:10.3390/coatings11010094
Ismail, S. O., Akpan, E., and Dhakal, H. N. (2022). Review on natural plant fibres and their hybrid composites for structural applications: recent trends and future perspectives. Compos. Part C. Open Access 9, 100322. doi:10.1016/j.jcomc.2022.100322
Jawaid, M., Chee, S. S., Asim, M., Saba, N., and Kalia, S. (2022). Sustainable kenaf/bamboo fibers/clay hybrid nanocomposites: properties, environmental aspects and applications. J. Clean. Prod. 330, 129938. doi:10.1016/j.jclepro.2021.129938
Kara, M., Kırıcı, M., Tatar, A. C., and Avcı, A. (2018). Impact behavior of carbon fiber/epoxy composite tubes reinforced with multi-walled carbon nanotubes at cryogenic environment. Compos. Part B Eng. 145, 145–154. doi:10.1016/j.compositesb.2018.03.027
Li, Y., Mai, Y. W., and Ye, L. (2000). Sisal fibre and its composites: a review of recent developments. Compos. Sci. Technol. 60, 2037–2055. doi:10.1016/S0266-3538(00)00101-9
Li, Z., Wang, X., and Wang, L. (2006). Properties of hemp fibre reinforced concrete composites. Compos. Part A Appl. Sci. Manuf. 37, 497–505. doi:10.1016/j.compositesa.2005.01.032
Luzi, F., Puglia, D., and Torre, L. (2019). 10 - natural fiber biodegradable composites and nanocomposites: a biomedical application. Biomass, Biopolymer-Based Mater. Bioenergy Constr. Biomed. Other Industrial Appl., 179–201. doi:10.1016/B978-0-08-102426-3.00010-2
Maharana, S. M., Pandit, M. K., and Pradhan, A. K. (2021). Influence of fumed silica nanofiller and stacking sequence on interlaminar fracture behaviour of bidirectional jute-kevlar hybrid nanocomposite. Polym. Test. 93, 106898. doi:10.1016/j.polymertesting.2020.106898
Mannan, K. T., Sivaprakash, V., Raja, S., Patil, P. P., Kaliappan, S., and Socrates, S. (2022). Effect of Roselle and biochar reinforced natural fiber composites for construction applications in cryogenic environment. Mater. Today Proc. 69, 1361–1368. doi:10.1016/j.matpr.2022.09.003
Matykiewicz, D. (2020). Hybrid epoxy composites with both powder and fiber filler: a review of mechanical and thermomechanical properties. Materials 13 (8), 1802. doi:10.3390/ma13081802
Mohit, H., Rangappa, S. M., Gapsari, F., Siengchin, S., Marwani, H. M., Khan, A., et al. (2023). Effect of bio-fibers and inorganic fillers reinforcement on mechanical and thermal characteristics on carbon-kevlar-basalt-innegra fiber bio/synthetic epoxy hybrid composites. J. Mater. Res. Technol. 23, 5440–5458. doi:10.1016/j.jmrt.2023.02.162
Nayak, S., Nayak, R. K., and Panigrahi, I. (2022). Effect of nano-fillers on low-velocity impact properties of synthetic and natural fibre reinforced polymer composites-a review. Adv. Mater. Process. Technol. 8 (3), 2963–2986. doi:10.1080/2374068x.2021.1945293
Pragadish, N., Kaliappan, S., Subramanian, M., Natrayan, L., Satish Prakash, K., Subbiah, R., et al. (2022). Optimization of cardanol oil dielectric-activated EDM process parameters in machining of silicon steel. Biomass Convers. Biorefinery 14, 121–135. doi:10.1007/s13399-021-02268-1
Prasob, P. A., and Sasikumar, M. (2018). Static and dynamic behavior of jute/epoxy composites with ZnO and TiO2 fillers at different temperature conditions. Polym. Test. 69, 52–62. doi:10.1016/j.polymertesting.2018.04.040
Prasob, P. A., and Sasikumar, M. (2019). Viscoelastic and mechanical behaviour of reduced graphene oxide and zirconium dioxide filled jute/epoxy composites at different temperature conditions. Mater. Today Commun. 19, 252–261. doi:10.1016/j.mtcomm.2019.02.005
Praveenkumara, J., Madhu, P., Yashas Gowda, T. G., Sanjay, M. R., and Siengchin, S. (2022). A comprehensive review on the effect of synthetic filler materials on fiber-reinforced hybrid polymer composites. J. Text. Inst. 113 (7), 1231–1239. doi:10.1080/00405000.2021.1920151
Ramesh, C., Vijayakumar, M., Alshahrani, S., Navaneethakrishnan, G., Palanisamy, R., Natrayan, L., et al. (2022). Performance enhancement of selective layer coated on solar absorber panel with reflector for water heater by response surface method: a case study. Case Stud. Therm. Eng. 36, 102093. doi:10.1016/j.csite.2022.102093
Rana, A. K., Mandal, A., Mitra, B. C., Jacobson, R., Rowell, R., and Banerjee, A. N. (1998). Short jute fiber-reinforced polypropylene composites: effect of compatibilizer. J. Appl. Polym. Sci. 69, 329–338. doi:10.1002/(sici)1097-4628(19980711)69:2<329::aid-app14>3.0.co;2-r
Sabarinathan, P., Annamalai, V. E., Vishal, K., Nitin, M., Natrayan, L., Veeeman, D., et al. (2022). Experimental study on removal of phenol formaldehyde resin coating from the abrasive disc and preparation of abrasive disc for polishing application. Adv. Mater. Sci. Eng. 2022, 1–8. doi:10.1155/2022/6123160
Santhosh, M. S., Sasikumar, R., Natrayan, L., Kumar, M. S., Elango, V., and Vanmathi, M. (2018). Investigation of mechanical and electrical properties of Kevlar/E-glass and Basalt/E-glass reinforced hybrid composites. Int. J. Mech. Prod. Eng. Res. Dev. 8 (3), 591–598. doi:10.24247/ijmperdjun201863
Sethi, S., Rathore, D. K., and Ray, B. C. (2015). Effects of temperature and loading speed on interface-dominated strength in fibre/polymer composites: an evaluation for in-situ environment. Mater. Des. (1980-2015) 65, 617–626. doi:10.1016/j.matdes.2014.09.053
Su, F. H., Zhang, Z. Z., and Liu, W. M. (2008). Tribological behavior of hybrid glass/PTFE fabric composites with phenolic resin binder and nano-TiO2 filler. Wear 264, 562–570. doi:10.1016/j.wear.2007.04.007
Thakur, V. K., Thakur, M. K., and Gupta, R. K. (2014). Review: raw natural fiber-based polymer composites. Int. J. Polym. Analysis Charact. 19, 256–271. doi:10.1080/1023666X.2014.880016
Uma Devi, L., Bhagawan, S. S., and Thomas, S. (1997). Mechanical properties of pineapple leaf fiber-reinforced polyester composites. J. Appl. Polym. Sci. 64, 1739–1748. doi:10.1002/(sici)1097-4628(19970531)64:9<1739::aid-app10>3.0.co;2-t
Velmurugan, G., and Babu, K. (2020). Statistical analysis of mechanical properties of wood dust filled Jute fiber based hybrid composites under cryogenic atmosphere using Grey-Taguchi method. Mater. Res. Express 7, 065310. doi:10.1088/2053-1591/ab9ce9
Velmurugan, G., and Natrayan, L. (2023). Experimental investigations of moisture diffusion and mechanical properties of interply rearrangement of glass/Kevlar-based hybrid composites under cryogenic environment. J. Mater. Res. Technol. 23, 4513–4526. doi:10.1016/j.jmrt.2023.02.089
Velmurugan, G., Natrayan, L., Chohan, J. S., Vasanthi, P., Angalaeswari, S., Pravin, P., et al. (2023). Investigation of mechanical and dynamic mechanical analysis of bamboo/olive tree leaves powder-based hybrid composites under cryogenic conditions. Biomass Convers. Biorefinery 14, 1–13. doi:10.1007/s13399-023-04591-1
Xu, F., Fan, W., Zhang, Y., Gao, Y., Jia, Z., Qiu, Y., et al. (2017). Modification of tensile, wear and interfacial properties of Kevlar fibers under cryogenic treatment. Compos. Part B Eng. 116, 398–405. doi:10.1016/j.compositesb.2016.10.082
Yıldırım, F., Tatar, A. C., Eskizeybek, V., Avcı, A., and Aydın, M. (2021). Impact response of nanoparticle reinforced 3D woven spacer/epoxy composites at cryogenic temperatures. J. Compos. Mater. 55 (28), 4231–4244. doi:10.1177/00219983211037052
Yogesh, P., Singarayar, S. P., Rajkamal, M. D., Venkatesh, T., kumar Gupta, R., and Yatika, G. (2022). Mechanical performance of aloe vera/dharbai-based hybrid epoxy composites with enhanced NaHCO3 treatment. Mater. Today Proc. 69, 1394–1401. doi:10.1016/j.matpr.2022.09.204
Keywords: nanocomposites, Kevlar mat, response surface methodology, optimization, mechanical properties, sustainability, cryogenic environment
Citation: Natrayan L, Janardhan G, Paramasivam P and Dhanasekaran S (2023) Enhancing mechanical performance of TiO2 filler with Kevlar/epoxy-based hybrid composites in a cryogenic environment: a statistical optimization study using RSM and ANN methods. Front. Mater. 10:1267514. doi: 10.3389/fmats.2023.1267514
Received: 26 July 2023; Accepted: 30 October 2023;
Published: 24 November 2023.
Edited by:
Sanjay M. R., King Mongkut’s University of Technology North Bangkok, ThailandReviewed by:
Vishwas Mahesh, Siddaganga Institute of Technology, Tumakuru, IndiaCopyright © 2023 Natrayan, Janardhan, Paramasivam and Dhanasekaran. This is an open-access article distributed under the terms of the Creative Commons Attribution License (CC BY). The use, distribution or reproduction in other forums is permitted, provided the original author(s) and the copyright owner(s) are credited and that the original publication in this journal is cited, in accordance with accepted academic practice. No use, distribution or reproduction is permitted which does not comply with these terms.
*Correspondence: Seshathiri Dhanasekaran, c2VzaGF0aGlyaS5kaGFuYXNla2FyYW5AdWl0Lm5v
Disclaimer: All claims expressed in this article are solely those of the authors and do not necessarily represent those of their affiliated organizations, or those of the publisher, the editors and the reviewers. Any product that may be evaluated in this article or claim that may be made by its manufacturer is not guaranteed or endorsed by the publisher.
Research integrity at Frontiers
Learn more about the work of our research integrity team to safeguard the quality of each article we publish.