- 1School of Traffic and Transportation Engineering, Changsha University of Science and Technology, Changsha, China
- 2School of Civil Engineering, Hubei Engineering University, Xiaogan, China
- 3Hunan Hengyong Expressway Construction and Development Co., Ltd, Changsha, China
- 4China Construction Seventh Engineering Division Corp., Ltd, Zhengzhou, China
Fog seal technology is widely used in airport asphalt pavement. The research on the performance and application of fog seal material is basically at the level of modified emulsified asphalt. The fog seal test method in the existing specification has defects. Three kinds of fog seal materials with different substrates were selected in this paper. Based on the characteristics of fog seal treatment and the relevant specifications of fog seal and airport pavement. Wet Track Abrasion Test (WTAT), Cantabro test, Water seepage test, and Pendulum instrument tester pavement friction coefficient test were improved. Test the pavement performance of different types of fog seals. The results show that the mass loss of material C was less than 10% after 200 and 400 cycles of wear. The improvement effect of material C on raveling resistance and impermeability was far better than that of materials A and B. The improvement of material C on the raveling resistance of the mixture could reach 50%. The immediate improvement effect on the impermeability was nearly 100%. The skid resistance performance of the three fog seal materials decreased after treatment. The decrease in material C was more significant than in materials A and B. In constructing material C, the dose of emery should be appropriately increased. It was advisable to not be less than 0.35 kg/m2. The fog seal layer improves pavement performance. It has reference significance for using fog seal technology to treat early airport pavement diseases.
1 Introduction
Airport pavement is one of the significant infrastructures in various countries that require different investments to ensure the safety of aircraft transportation (Xiao et al., 2019). However, the airport pavement is exposed to a particular service environment. These factors can cause more damage to the pavement surface materials than ordinary flexible pavement due to the frequent effects of temperature stress, dynamic stress, and tire wear (Peng et al., 2023; Zhang et al., 2023). Preventive maintenance is an effective strategy to extend the service life of airport pavements and mitigate the risk of pavement deterioration (Feng X. et al., 2019; You et al., 2020). The fog seal technology has been applied to airport pavement maintenance and has received wide recognition (Xu et al., 2021). Fog seals can increase the adhesion of pavement asphalt, reduce the destructive rate of the pavement, extend the service life of the road, and defer the need for expensive repair and reconstruction work (Jia et al., 2021; Xu et al., 2021). The fog seal material has high fluidity and can penetrate the gaps and microcracks in the road surface structure after spraying, improving the impermeability of the pavement (Xv et al., 2022). Aggregates can be effectively stabilized by fog seal technology (Guo et al., 2017). Prevent traffic accidents caused by aggregate spatter on the road surface. Traffic can usually resume in about 3 h, which meets the high road traffic supply demand at the airport (Minaka et al., 2021). The performance of conventional emulsified asphalt fog seals is often unsatisfactory regarding mechanical strength, cohesion, water resistance, and durability (Rahman et al., 2020). The performance test method of the fog seal layer differs from the actual pavement condition (Im and Kim, 2013).
Many researchers have attempted to improve its effectiveness through modification. For example, Feng (Feng P. et al., 2019) prepared a bio-oil-modified emulsified asphalt fog seal and tested its permeability and indoor skid resistance, finding that it had a good treatment effect on the pavement. Jiang (Jiang et al., 2021) prepared an epoxy-emulsified asphalt fog seal with emery sand. The skid resistance fog seal specimen met the technical requirements of ordinary asphalt pavement, with only a 27.4% reduction in British Pendulum Number (BPN) after 100,000 times of wear. Hu et al. (Hu et al., 2020) used waterborne epoxy-modified asphalt emulsion as a fog seal. They conducted laboratory and field tests, showing that the pavement texture and skid resistance was significantly improved after sand fog sealing. Liu (Liu et al., 2021) prepared a waterborne epoxy resin SBR composite modified emulsified asphalt fog sealing layer. He tested its pavement performance and durability, concluding it had good durability and could extend its service life. Cui et al. (Cui et al., 2019) prepared a silicone resin polymer-based fog seal and tested its ability to isolate water, improving the moisture resistance of asphalt mixtures. They also determined the optimal ratio of this kind of fog seal by impermeability test, Marshall test, and rutting test. Xu (Xu et al., 2022) modified emulsified asphalt by adding two thermosetting materials. The materials were waterborne cationic acrylate (WCA) and waterborne epoxy resin, and their potential in airport pavement fog sealing technology was tested and analyzed. It can be seen from recent studies that although modified emulsified asphalt fog seal has been extensively researched, there are few studies on non-emulsified asphalt fog seal.
As the road surface is treated by fog seal technology, its skid resistance performance cannot be guaranteed (Islam et al., 2017; Zhang et al., 2019). To test its improvement effect, researchers mostly use the pendulum value method to test the skid resistance performance of the road (Qureshi et al., 2013; Ministry of Transport of the People’s Republic of China, 2019). Still, the test is directly measured after the fog seal material is dried and the pendulum value method is tested. The swing direction is consistent with the driving law, and the vehicle will also have a sideslip on the road surface (Wu et al., 2021). There is a big gap between the test and the actual driving condition of the road surface. The basic principle of fog seal to improve the pavement is that the emulsion penetrates the interconnected voids and small cracks to prevent water from eroding the pavement (Cui et al., 2019). Therefore, the fog seal is significant for improving the impermeability of the pavement. Currently, researchers mostly use the test method of seepage coefficient to test. Still, because of the connected voids on the top and side of the rutting plate, the seepage coefficient is larger than the actual result. In addition, when the airport pavement is subjected to aircraft landing, the pavement aggregate is prone to scattering, and the aggregate can be protected after fog seal treatment (Praticò et al., 2015). Currently, the researchers mostly use the asphalt mixture Cantabro Test (T 0733–2011) to test its performance. The Cantabro Test measures the degree of aggregate loss on the pavement surface under traffic load. This loss is caused by the lack of asphalt content or cohesiveness, which differs from the principle of fog seal treatment of pavement dispersion. At the same time, the application of fog seal technology in airport pavement is more and more extensive. There are few studies on airport pavement, and the test methods of such studies have not changed accordingly due to airport pavement (Xu et al., 2022).
In this paper, three kinds of fog seal materials are selected. The material properties are emulsified asphalt, modified emulsified asphalt and special material properties. The Cantabro test, water seepage test and pavement friction coefficient test were improved. Verify the rationality of the test improvement. The performance of fog seal was tested by improved test and wet track abrasion test (WTAT). The improvement effect of non-emulsified asphalt fog seal on the performance of the mixture is analyzed, which provides a theoretical reference for the application of fog seal technology in airport asphalt pavement.
2 Materials and methods
2.1 Materials
Three kinds of fog seal materials were selected. Material A is a fog seal with emulsified asphalt as a matrix additive, and materials B and C were non-emulsified asphalt fog seals.
Material A consisted of emulsified asphalt as the base, blended with clay, modifier, additive, tackifier, and fine sand. The additive was a polymer-based viscosity modifier that enhanced the elasticity and oil resistance of the cover materials. It also formed a black and dry film on the asphalt pavement surface.
Material B comprised modified asphalt, fine aggregate, polymer modifier, and catalyst. The modified asphalt did not contain harmful substances such as coal tar, which was less harmful to environmental pollution and the human body.
Material C consisted of natural rock asphalt as the main ingredient and petroleum, petroleum asphalt, heavy in solvent naphtha, solvent, additives, and emery. The medium molecular-weight additive improved the solubility of each component and ensured the material’s stability.
The recommended dose of various fog seal materials is shown in Table 1.
2.2 Mixture design
SBS-modified asphalt is selected. The gradation of the asphalt mixture is shown in Figure 1. The optimum oil-stone ratio is 4.0%. AC-13 gradation is adopted. Marshall and rutting plate pieces are made according to JTG E20-2011 (Ministry of Transport of the People’s Republic of China, 2011). The Marshall specimen was used to test the raveling resistance performance, and the rutting plate specimen was used to test the impermeability and skid resistance performance.
2.3 Test method
Fog seal is a common technique for pavement maintenance, but it may not meet the practical engineering requirements of skid resistance performance, wear resistance, and impermeability (Islam et al., 2017; Zhang et al., 2019). In addition, the current specification imposes higher standards for pavement quality after fog seal treatment (Airport Department of China Civil Aviation Administration, 2010; Civil Aviation Administration of China, 2017; Civil AviationAdministration of China, 2019). This paper tests and analyzes the performance of wear resistance, loose resistance, impermeability, and skid resistance to verify the rationality of the new test method.
Currently, only the wear resistance of the fog seal has a direct measurement method, and the other three properties need to be completed using an asphalt mixture performance test. The raveling resistance and impermeability tests are based on standard JTG E20-2011 (Ministry of Transport of the People’s Republic of China, 2011) ‘Cantabro test of asphalt mixture (T 0733–2011)' and ‘Water seepage test of asphalt mixture (T0730-2011)'. The skid resistance test is based on standard JTG 3450–2019 (Ministry of Transport of the People’s Republic of China, 2019) ‘Pendulum instrument tester pavement friction coefficient test (T 0964–2008)'. However, these three methods are designed for asphalt mixture performance, so it is necessary to modify the principle of fog seal treatment to obtain optimal test results. The overall test scheme is shown in Figure 2.
2.3.1 Wet track abrasion test
WTAT method from standard JT/T 1330–2020 (Airport Department of China Civil Aviation Administration, 2020) was used to evaluate the wear resistance of the fog seal material by studying the difference in wear resistance under the dose and wear revolution conditions. A circular WTAT oil-felt substrate with a diameter of 286 mm was made and floated up and down according to the recommended dose range in Table 1. Four different test doses were determined for each fog seal material. According to the dose, the fog seal material was evenly applied to the oil felt, and the wet wheel abrasion tester was used to carry out the abrasion test in two 200 revolutions each. The mass loss after two wear times was measured, m0 and m1, respectively. The wear resistance of the fog seal was evaluated by comparing the residual mass fraction of the two times. The residual mass fraction of the first and second wear was calculated as T1 and T2, respectively.
Calculation formula of residual mass fraction:
Where T is wear abrasion mass fraction, m0 is test dose, and m1 is wear mass loss.
2.3.2 Improve cantabro test
To determine the optimal asphalt-aggregate ratio, the standard test method of JTG E20-2011 (Ministry of Transport of the People’s Republic of China, 2011) Cantabro test of asphalt mixture (T 0733–2011) was adopted. The fog seal material was applied on both surfaces of the Marshall specimens, and the mass loss before and after the application was measured and compared. The test results are presented in Schedule 2.
As shown in Figure 3, the mass loss of the specimens after the fog seal material treatment was not significantly reduced, and the error due to the specimen preparation was too large. Therefore, several groups of immersion standard Cantabro tests were conducted using material A to increase the mass loss rate and make it more observable. The test results are presented in Schedule 3.
From the test data of the immersion mentioned above Cantabro test, it can be found that the improvement effect of fog seal treatment on the raveling resistance performance of Marshall specimens cannot be highlighted. The optimum oil-stone ratio of AC-13 was reduced to 3.4% and 3.6%, respectively. This increased the area of the coating material, and the outer surface of the specimen was completely coated with the material. As a result, the mass loss rate of the specimen increased. The dose value of the material was based on the recommended dose range in Table 1 to obtain the median dose. In addition, an upper limit dose and a lower limit dose outside the recommended range were selected for the test, and the specific dose is shown in Schedule 4.
Testing procedures are below. Marshall specimens with 3.4% and 3.6% oil-stone ratios were made, respectively. The identical samples were divided into groups I and II (three in each). The specimens were immersed in water at room temperature for 3 days. The 9 min Cantabro test was performed directly in group I, and the mass loss was ΔS1. According to Schedule 5, the amount of fog seal material required on the surface of the specimen was calculated. All kinds of fog seal materials were evenly applied on the surface of group II models, then placed in an oven at 50°C for 3 h to completely dry the surface fog seal material. The group II specimens were subjected to the 9 min Kentucky Flying Test, and the mass loss was ΔS2. Two mass losses obtained from the same oil-stone ratio were taken, and the mass loss ratio was S.
Calculation formula of mass loss ratio:
Where S is the mass loss ratio, ΔS1 is the group I quality loss, and ΔS2 is group Ⅱ quality loss.
2.3.3 Improve water seepage test
The impermeability test was based on the Water seepage test of asphalt mixture (T 0730–2011) in standard JTG E20-2011 (Ministry of Transport of the People’s Republic of China, 2011). The trial compared the impermeability of the mixture before and after applying the fog seal material under different doses and void content conditions to evaluate the ability of the fog seal material to fill the cracks and voids of the pavement. To enhance the testing effect, simulate various road conditions, and improve the accuracy and efficiency of the test, a new water seepage test method was developed in this paper.
1) Simulate different pavement conditions
In order to simulate the seepage rate of the pavement with different degrees of slight cracks on the pavement, the parameters of the specimens were adjusted, and the void content of the models was controlled by the number of rolling times and the oil-stone ratio. Finally, the rutting plate specimens with 5%, 8%, and 11% void content were prepared according to the parameters in Schedule 5.
2) Improve the test method
To avoid the influence of plugging material on the subsequent application of fog sealing material, the plugging material was changed to light clay in the test, which had low cost, no residue, and could be recycled. The comparison data of the same specimen was fundamental, so considered increasing the number of single plate tests. To ensure that the surface of the model was dry, a test was first carried out in the center of the specimen. The light clay was taken down, the water in the sample was dried, and the position was adjusted upward, lower left, and lower right. Four comparative tests were carried out (see Figure 4 in the test area), and the average value of the four data was taken as the specimen’s original seepage rate.
To minimize the effect of the interconnected voids on the surface of the rutting plate on the test accuracy, applying the fog seal material was divided into two steps. The fog seal material was used outside the water seepage area after measuring the water seepage rate of the original specimen. After sealing the interconnected voids outside the water seepage area (radius of 75 mm) (as shown in Figure 4A, denoted as A1, with an area of 0.072 m2) to eliminate interference, the water seepage rate at this stage was measured. Then, the water seepage area (as shown in Figure 4B, the shaded part is denoted as A2, with an area of 0.018 m2) was sealed with the fog seal material, and then the water seepage rate at this stage was measured.
The influence of connected voids was eliminated. The number of tests on the same specimen was increased as much as possible. The final test method made the data more accurate. The specific test methods were as follows.
The rutting plate was made according to the intermediate gradation of Figure 1. The models were coated with hot asphalt and wrapped with paper to avoid too high temperatures. This prevented the surrounding asphalt from flowing closed and causing pollution. The first measuring point was taken in the center of the specimen. The water permeability coefficient of the point was measured. Then, the sample was placed in a dry, ventilated place to dry. Three to four measuring points were selected near the center point, and the above steps were repeated. The water permeability coefficient was measured, and the average value was the water permeability coefficient of the original specimen. According to Schedule 4, the shadow part in Figure 5A was smeared with the corresponding quality of fog seal material. After it reaches complete drying, the point seepage coefficient was measured as S1. The corresponding dose in Schedule 5 shows that the shadow part in Figure 5B was smeared with the corresponding fog seal material. After it was completely dried, the water permeability coefficient was measured, which was the water permeability coefficient of the specimen after the fog seal material was sealed, which is counted as S2.
Calculation formula of seepage coefficient:
Where S is the water permeability coefficient, v0 is the first timing of the water (mL), usually 100 mL, v1 is the second timing of the water (mL), usually 500 mL, t0 is the time of the first time (s), and t1 is the time of the second timing (s).
2.3.4 Improve pendulum instrument tester pavement friction coefficient test
The Method of testing pavement friction coefficient with pendulum instrument (T 0964–2008) in standard JTG 3450–2019 (Ministry of Transport of the People’s Republic of China, 2019) was adopted. This method evaluated the effect of fog seal material on pavement skid resistance by comparing the changes in pavement friction coefficient under different materials and doses. The rutting plate wear test was used to simulate the condition of the asphalt pavement after a period of use, and the fog seal material (as shown in Schedule 6) with the typical dose and the increased dose (about 30% higher than the standard dose) was applied for testing.
1) Rutting plate specimens were prepared according to the method in water seepage test. The friction coefficient of the original specimen was tested, which was counted as B;
2) The surface of the specimen was treated with a wet wheel abrasion tester (the wear range is the circular area in Figure 6). The surface of the specimen was ground to a friction coefficient of about 75 BPN. The friction coefficient was calculated to be B1;
3) The prescribed dose of fog seal material was applied on the surface of the specimen according to the rectangular range shown in Figure 6;
4) After it reached complete drying, the four friction coefficients at this time were tested according to the arrow direction in Figure 6. The average value was taken, which was the friction coefficient on the surface of the specimen after applying the fog seal, which was counted as B2.
Friction coefficient calculation formula:
Where BPN20 is converted to the BPN at a standard temperature of 20 °C; BPNT is BPN measured at road surface temperature T; ΔBPN is temperature correction.
3 Results and discussion
3.1 Wear resistance performance analysis
Quality change of fog seal is shown in Figure 7, specimen after test is shown in Figure 8. The wear loss of the fog seal layer increased linearly with the increase of wear cycles. The wear loss of the three fog seal materials was significantly different, and material C had much better wear resistance than the other two materials. After 400 cycles of wear, the remaining mass of material C was consistently above 90%, while the remaining group of the other two materials was only about 70%. This was due to the different adhesion of the interface between the three materials and the mixture in the water environment. The adhesion of materials A and B decreased after soaking in water, which made them more prone to wear. On the other hand, material C was water-insoluble, and the additive was a medium molecular weight substance, which gave it excellent overall stability, showing the best durability among the three materials (Huang et al., 2020). This indicated that under the combined conditions of rainwater weather and tire wear, the performance of the fog seal would gradually deteriorate.
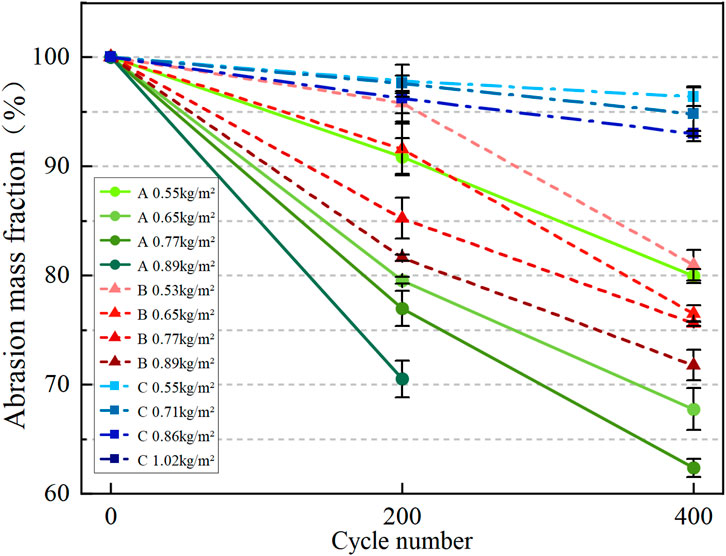
FIGURE 7. Quality change of fog seal. Note: Among them, the third group of specimens of material A ended the test process in advance because of the wear of the models without completing the specified times. The fourth concentration of material C was too large for the oil-felt specimen, and it was not easy to smear evenly.
The mass loss of the three fog seals increased with the increase of the dose of the material, and the wear resistance of cloth C was the least sensitive to the change of the dose. The proliferation of the dose did not enhance the adhesion between the material and the mixture interface. On the contrary, the humidity sensitivity of the fog seal material continued to rise, and it was easier to fall off underwear and water. Under different doses, the residual mass of material C changed within 7%. The primary material of material C was rock asphalt. This material had higher strength and peel resistance, forming a dense, bright protective film on the free surface (Li et al., 2020). This film could effectively prevent the wet wear of wheels.
3.2 Raveling resistance performance analysis
Figure 9 showed mass loss rate under different oil-stone ratios. The fog seal treatment significantly reduced the mass loss rate of the specimens, and material C had a much better treatment effect than materials A and B. The three kinds of fog seal materials could fill the voids and microcracks on the road surface after coating and wrapping the exposed aggregates of the road surface. This reduced the possibility of raveling and improved the overall performance of the road surface (Guo et al., 2017; Sahebzamani et al., 2018). After applying material C, its raveling resistance performance was significantly improved. The mass loss of the specimens was reduced by up to 50%, and the improvement range was 2–3 times that of materials A and B. The primary raw material of material C was natural rock asphalt. This material had a molecular weight of up to 9,000, a high temperature viscosity, and excellent adhesion with alkaline aggregates. Hence, the specimens showed excellent raveling resistance properties.
The raveling resistance performance of the mixture increased with the increase of the material dose. Still, the change in the material dose had little effect on the raveling resistance performance, and the change range was within 3%. This indicated that increasing the dose did not significantly improve the adhesion of the fog seal material. The improvement effect depended more on the primary adhesion of each material. The slight performance improvement caused by the increase in dose was assumed to be due to the slight increase in viscosity. However, from the practical application perspective, considering the wear resistance test results, increasing the dose of materials was not recommended to obtain better raveling resistance.
The smaller the oil-stone ratio was, the more significant the improvement effect of the fog seal material was on the raveling resistance performance. The impermeability after material C treatment was the least sensitive to the change in the oil-stone ratio. As the oil-stone ratio decreased, under the same gradation condition, the surface voids of the mixture became larger, and the fog seal material penetrated the surface voids more easily. This material acted as a binder, enhancing the cohesion from the inside, and protected the aggregate during the impact and rolling process. The sensitivity of the raveling resistance performance of the three materials to the change in oil-stone ratio was different. From high to low was A > B > C. Figure 10 showed that material C had a stable and superior performance in raveling resistance for different oil-stone ratio specimens, as long as the dose of the fog seal met or exceeded the recommended level. Materials A and B were inferior to material C in this aspect. It could be seen that material C was a better choice under different degrees of pavement damage.
3.3 Impermeability performance analysis
Results of the water seepage test is shown in Figure 11. With the expansion of the fog seal material’s coating area, the water permeability coefficient of the asphalt mixture decreased, and material C had the best improvement effect. This shown that the fog seal material could seal the pavement gap and fill the micro-cracks, thereby preventing the pavement from water seepage. The seepage coefficient of pavement was less than 10 mL/min when the void content was 5%, and the dose of material C was either 0.71 kg/m2 and 0.86 kg/m2. This value met the technical requirements of airport pavement after spraying the fog seal (Airport Department of China Civil Aviation Administration, 2010).
The fog seal material enhanced the mixture’s impermeability more effectively when the void content was more less. For instance, material C improved impermeability by 100% when the void content was 5% but only by 61% when the void content was 11%. This phenomenon could be attributed to the fact that the surface voids of the dense graded low void content mixture were fewer, and thus the fog seal material could exert its full treatment effect. However, when the road surface void content increased, the fog seal material could not fill these voids adequately, leading to poor improvement of fog seal material. Hence, the fog seal method was not recommended for treating pavement with severe damage.
The improvement of different doses is shown in Figure 12. With the increase in the dose of fog seal material, the impermeability of the mixture was improved, and the sensitivity of material C to the change of dose was the highest. The increased material dose increases viscosity, which could block more water seepage. The sensitivity of impermeability to the dose change of the three materials was different. From high to low is material C > material B > material A. The reason was that material A is based on emulsified asphalt. If there was uneven mixing, insufficient moisture, or insufficient dose, cracking might occur during drying, and its impermeability was significantly reduced. The fluidity of material B was better than that of material A, and it was easier to close the gap evenly, so the improvement effect of material B was slightly better than that of material A; material C had less fluidity and greater viscosity. The surface voids could be tightly sealed by uniform application, and it had certain toughness in the dry state, so it was not easy to crack. At the same time, when the void content was significant and the fog seal dose was small, the improvement effect of impermeability was also poor. It can be seen that when pavement damage was severe if the fog seal was used for treatment, the fog seal material could not be used in small doses.
3.4 Skid resistance performance analysis
The fog seal material reduced the pavement friction coefficient. The skid raveling resistance performance of material C-coated specimens decreased most significantly. The friction coefficient of the samples coated with material A and material C ranged from 55BPN to 60BPN, indicating a specific attenuation and meeting open traffic conditions. The main reason for attenuating the friction coefficient was that the fog seal material was directly applied to the surface of the specimen, wrapping the surface aggregate and making the surface smoother.
Friction coefficient at different doses is shown in Figure 13. The friction coefficients of materials A and B increased slightly with the dose increase, while the friction coefficient of material C decreased further. Materials A and B contained more sand when the dose increased. The sand floated on the specimen surface when the emulsion penetrated the gap. After drying, the friction coefficient increased to some extent. Material C was based on rock asphalt, which could form a thick and glossy protective film on the free surface. The sand floating on the surface was coated by material C, severely attenuating the friction coefficient. In addition, when the dose increased, although the amount of sand also increased, the sand could no longer weaken the smoothness of the surface, so when the overall dose of the material increased, the friction coefficient decreased.
4 Conclusion
This paper evaluates the improvement effect of fog seal material on the performance of asphalt mixture from four aspects.
1) Material C has the best durability. Its wear resistance and anti-stripping performance are the best. After the use of material C, the anti-stripping performance of the specimen was increased by 50%. The test results are significantly affected by the oil-stone ratio. When the void content is large, the fog seal material is easier to penetrate the gap. It can be used as a part of the binder, play a role in consolidation.
2) The influence of pore content dominates the impermeability of the material. When the gap of the mixture is too large, the fog seal material cannot be evenly covered on the road surface. The use of fog seal has little effect.
3) The influence of void content dominates the impermeability of materials. The medium dose selected in the test is recommended for construction. The fog seal material cannot be evenly covered on the surface of the road when the gap of the road surface is too large. Therefore, if the fog seal is used when the road surface damage is severe, the fog seal material cannot be used in small doses.
4) The complete research results show that material C has achieved good treatment effect on the pavement with loose pavement and serious water seepage, and the wear resistance is stable. In the construction process, the amount of emery should be appropriately increased to not less than 0.35 kg/m2. The improvement of material A and material B on pavement performance is limited. When it acts on looser and more serious roads, the dose can be appropriately increased to 0.9 kg/m2. At the same time, the amount of water should be appropriately increased to increase its flow capacity. But construction should be scheduled for the summer. In this paper, according to the characteristics of fog seal treatment, the existing standard experiments are improved. But there are still some shortcomings. This paper does not consider biological modification and other types of fog seals. The applicability of airport pavement is studied without combining the performance of fog seal material, which is also the follow-up research direction.
Data availability statement
The original contributions presented in the study are included in the article/Supplementary Material, further inquiries can be directed to the corresponding authors.
Author contributions
PL contributed to the conception and design of the study. WP participated in the writing of the first draft of the article and conducted data analysis. JM compiled the experimental data and some manuscripts. XY and ZL provided help in data analysis. LK participated in the test of experimental samples. All authors contributed to the article and approved the submitted version.
Funding
This work was supported by the National Key Research and Development Program of China (2021YFB2601000), Guangxi Key Research and Development Program (AB17292035), the National Natural Science Foundation of China (51878075), Hunan Provincial Natural Science Foundation of China (2022JJ30594), and Postgraduate Scientific Research Innovation Project of Hunan Province (QL20220189).
Conflict of interest
Author XY is employed by Hunan Hengyong Expressway Construction and Development Co., Ltd; Author LK is employed by China Construction Seventh Engineering Division Corp., Ltd.
The remaining authors declare that the research was conducted in the absence of any commercial or financial relationships that could be construed as a potential conflict of interest.
Publisher’s note
All claims expressed in this article are solely those of the authors and do not necessarily represent those of their affiliated organizations, or those of the publisher, the editors and the reviewers. Any product that may be evaluated in this article, or claim that may be made by its manufacturer, is not guaranteed or endorsed by the publisher.
Supplementary material
The Supplementary Material for this article can be found online at: https://www.frontiersin.org/articles/10.3389/fmats.2023.1231461/full#supplementary-material
References
Airport Department of China Civil Aviation Administration (2010). Technical guide for site maintenance of civil airport flight area AC-140-CA-2010-3.
Airport Department of China Civil Aviation Administration (2020). Fog seal material with emulsion mastic for asphalt pavement JT/T 1330—2020.
Civil Aviation Administration of China (2017). Specifications for asphalt pavement design of civil airports MH/T 5010-2017. Beijing: China Civil Aviation Press.
Civil Aviation Administration of China (2019). Specifications for asphalt pavement construction of civil airports MH/T 5011-2019. Beijing: China Civil Aviation Press.
Cui, P., Wu, S., Xu, H., and Lv, Y. (2019). Silicone resin polymer used in preventive maintenance of asphalt mixture based on fog seal. Polymers 11, 1814. doi:10.3390/polym11111814
Feng, X., Guo, L., Ren, G., and Liu, S. (2019a). Research on the causes and prevention of airport pavement diseases. Iop Conf. Ser. Earth Environ. Sci. 330, 022042. doi:10.1088/1755-1315/330/2/022042
Feng, P., Wang, H., Zhang, X., Mohd Hasan, M. R., You, Z., and Gao, J. (2019b). Study on workability and skid resistance of bio-oil–modified fog seal with sand. J. Test. Eval. 48, 20190224. doi:10.1520/jte20190224
Guo, T., Wang, C., Yang, X., and Sun, X. (2017). Development and performance of sand fog seal with cooling and air purification effects. Constr. Build. Mater. 141, 608–618. doi:10.1016/j.conbuildmat.2017.03.003
Hu, C. C., Li, R., Zhao, J. Y., Leng, Z., and Lin, W. W. (2020). Performance of waterborne epoxy emulsion sand fog seal as a preventive pavement maintenance method: From laboratory to field. Adv. Mater. Sci. Eng. 2020, 1–9. doi:10.1155/2020/6425817
Huang, M., Huang, Z., and Zhu, H. (2020). Excellent stability of molecular catalyst/bivo4 photoanode in borate buffer solution. Nano Energy 70, 104487. doi:10.1016/j.nanoen.2020.104487
Im, J. H., and Kim, Y. R. (2013). Methods for fog seal field test with polymer-modified emulsions. Transp. Res. Rec. J. Transp. Res. Board 2361, 88–97. doi:10.3141/2361-11
Islam, R. M., Arafat, S., and Wasiuddin, N. M. (2017). Quantification of reduction in hydraulic conductivity and skid resistance caused by fog seal in low-volume roads. Transp. Res. Rec. 2657, 99–100. doi:10.3141/2657-11
Jia, Y., Wang, S., Huang, A., Gao, Y., Wang, J., and Zhou, W. (2021). A comparative long-term effectiveness assessment of preventive maintenance treatments under various environmental conditions. Constr. Build. Mater. 273, 121717. doi:10.1016/j.conbuildmat.2020.121717
Jiang, Y., Fan, J., Lv, P., Yuan, K., Yi, Y., Tian, T., et al. (2021). Development of the fog seal layer characterized by durability in terms of skid resistance. Adv. Mater. Sci. Eng. 2021, 1–18. doi:10.1155/2021/6210875
Li, R., Karki, P., and Hao, P. (2020). Fatigue and self-healing characterization of asphalt composites containing rock asphalts. Constr. Build. Mater. 230, 116835. doi:10.1016/j.conbuildmat.2019.116835
Liu, F., Zheng, M., Liu, X., Ding, X., Wang, F., and Wang, Q. (2021). Performance evaluation of waterborne epoxy resin-sr composite modified emulsified asphalt fog seal. Constr. Build. Mater. 301, 124106. doi:10.1016/j.conbuildmat.2021.124106
Minaka, U. S., Okamura, M., and Ono, K. (2021). Verification of effectiveness and design procedure of gravel drains for liquefaction remediation. Soils Found. 61, 1191–1206. doi:10.1016/j.sandf.2021.06.002
Ministry of Transport of the People's Republic of China (2011). Standard test methods of bitumen and bituminous mixtures for highway engineering JTG E20-2011. Beijing: China Communications Press.
Ministry of Transport of the People's Republic of China (2019). Field test methods of highway subgrade and pavement JTG 3450-2019.
Peng, W., Li, P., Gong, W., Tian, S., Wang, Z., Liu, S., et al. (2023). Preparation and mechanism of rubber-plastic alloy crumb rubber modified asphalt with low viscosity and stabilized performance. Constr. Build. Mater. 388, 131687. doi:10.1016/j.conbuildmat.2023.131687
Praticò, F. G., Vaiana, R., and Iuele, T. (2015). Macrotexture modeling and experimental validation for pavement surface treatments. Constr. Build. Mater. 95, 658–666. doi:10.1016/j.conbuildmat.2015.07.061
Qureshi, N. A., Tran, N. H., Watson, D., and Jamil, S. M. (2013). Effects of rejuvenator seal and fog seal on performance of open-graded friction course pavement. Maejo Int. J. Sci. Technol. 7, 189.
Rahman, M. N., Sarkar, M. T. A., Elseifi, M. A., Mayeux, C., and Cooper, S. B. (2020). Effects of emulsion types, application rates, and crumb rubber on the laboratory performance of chip seal. Constr. Build. Mater. 260, 119787. doi:10.1016/j.conbuildmat.2020.119787
Sahebzamani, H., Alavi, M. Z., and Farzaneh, O. (2018). Evaluating effectiveness of polymerized pellets mix additives on improving asphalt mix properties. Constr. Build. Mater. 187, 160–167. doi:10.1016/j.conbuildmat.2018.07.143
Wu, T., Qiu, W., Kim, C., Chang, K., and Lu, X. (2021). Study of metabolomics in selenium deprived Przewalski's Gazelle (Procapra przewalskii). Struct. Infrastructure Eng., 1–12. ahead-of-print. doi:10.1017/S000711452100355X
Xiao, F., Ma, D., Wang, J., Cai, D., Lou, L., and Yuan, J. (2019). Impacts of high modulus agent and anti-rutting agent on performances of airfield asphalt pavement. Constr. Build. Mater. 204, 1–9. doi:10.1016/j.conbuildmat.2019.01.138
Xu, L., Zhao, Z., Li, X., Yuan, J., Zhou, Q., and Xiao, F. (2021). Cracking investigation on fog seal technology with waterborne acrylate and polyurethane as a clean modification approach. J. Clean. Prod. 329, 129751. doi:10.1016/j.jclepro.2021.129751
Xu, L., Jiang, C., and Xiao, F. (2022). Application of fog-seal technology with waterborne thermosetting additive in asphalt pavement. J. Mater. Civ. Eng. 34. doi:10.1061/(asce)mt.1943-5533.0004288
Xv, L., Wang, X., Li, X., Guan, X., and Xiao, P. (2022). Effect of waterborne EmulsiononPerformance of polymer-modified FogSeal materials. J. Tongji Univ. Nat. Sci. 50, 1471–1481. doi:10.11908/j.issn.0253-374x.21465
You, L., Dai, Q., You, Z., Zhou, X., and Washko, S. (2020). Stability and rheology of asphalt-emulsion under varying acidic and alkaline levels. J. Clean. Prod. 256, 120417. doi:10.1016/j.jclepro.2020.120417
Yu, B., Gu, X., Ni, F., and Guo, R. (2015). Multi-objective optimization for asphalt pavement maintenance plans at project level: Integrating performance, cost and environment. Transp. Res. Part D Transp. Environ. 41, 64–74. doi:10.1016/j.trd.2015.09.016
Zhang, X., Wang, H., Hasan, M. R. M., Gao, J., and Irfan, M. (2019). Traffic open time prediction of fog seal with sand using image processing technology. Constr. Build. Mater. 209, 9–19. doi:10.1016/j.conbuildmat.2019.03.070
Keywords: fog seal, airport pavement, non-emulsified asphalt fog seal, pavement performance, testing technologies
Citation: Li P, Peng W, Mao J, Yan X, Liu Z and Kong L (2023) Airport pavement performance evaluation of pavement fog seal based on optimized test technology. Front. Mater. 10:1231461. doi: 10.3389/fmats.2023.1231461
Received: 30 May 2023; Accepted: 14 July 2023;
Published: 03 August 2023.
Edited by:
Dawei Wang, RWTH Aachen University, GermanyReviewed by:
Peiwen Hao, Chang’an University, ChinaXinxing Zhou, Shanxi Transportation Technology Research and Development Co., Ltd., China
Copyright © 2023 Li, Peng, Mao, Yan, Liu and Kong. This is an open-access article distributed under the terms of the Creative Commons Attribution License (CC BY). The use, distribution or reproduction in other forums is permitted, provided the original author(s) and the copyright owner(s) are credited and that the original publication in this journal is cited, in accordance with accepted academic practice. No use, distribution or reproduction is permitted which does not comply with these terms.
*Correspondence: Wenju Peng, cHdqMTExMkBmb3htYWlsLmNvbQ==; Jing Mao, bWF5X21hby5ubkBmb3htYWlsLmNvbQ==