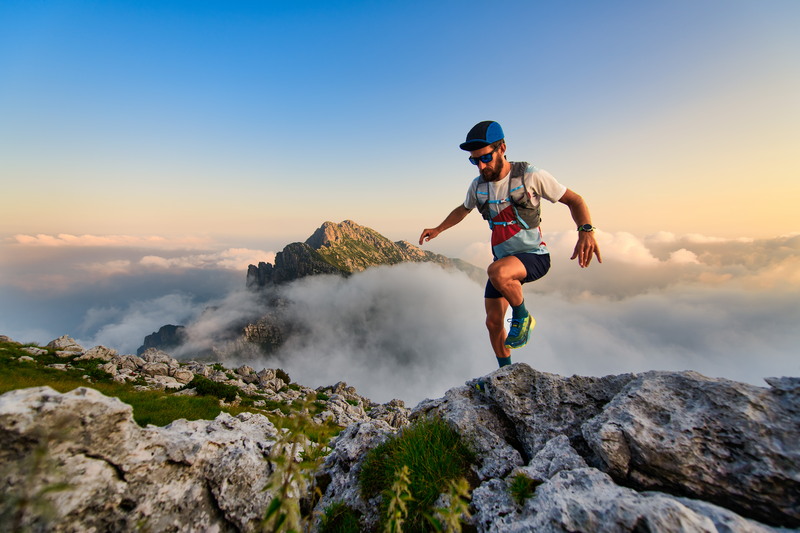
95% of researchers rate our articles as excellent or good
Learn more about the work of our research integrity team to safeguard the quality of each article we publish.
Find out more
EDITORIAL article
Front. Mater. , 13 June 2023
Sec. Polymeric and Composite Materials
Volume 10 - 2023 | https://doi.org/10.3389/fmats.2023.1230323
This article is part of the Research Topic Additive Manufacturing for Polymers View all 10 articles
Editorial on the Research Topic
Additive manufacturing for polymers
Additive manufacturing (AM), also known as 3D printing, is a kind of technology that manufactures solid parts based on a 3D model (CAD model) with a layer-by-layer accumulation of materials; this allows AM to make flexible and customized designs of product structures and to quickly and accurately transform design ideas into prototypes or even parts to shorten the time-to-market and reduce costs, with irreplaceable advantages in the manufacturing of complex structural characteristics and the delicate design of component structures. However, there are still many limitations in the development of polymer 3D printing, such as the restricted available materials, and the mechanical strength of the products still needs to be higher than those produced by traditional methods. Hence, to further expand the application area of AM and break the development bottleneck, developing new high-performance AM materials and optimizing the AM printing process (including improving resolution, precision, scale, and speed) are highly required.
This Research Topic aimed to capture the recent developments of advancing new technologies, processes, methods, materials, systems, and applications in AM of polymers, expecting to widen the knowledge in this area and promote research and application. The Research Topic has currently collected nine papers, including six original research articles and three reviews.
The six original research papers mainly focus on the development of new materials. Liang et al. successfully prepared Sn-doped β-tricalcium phosphate (Sn@TCP) scaffolds by direct inject writing 3D printing and high-temperature sintering. The osteogenesis of the prepared Sn@TCP was correlated with the concentration of doped Sn. Moreover, the Sn@TCP scaffolds exhibited satisfactory biocompatibility and demonstrated better compressive and osteogenic abilities than pure TCP scaffolds, showing the potential of 3D-printed tin-doped β-TCP scaffolds for tissue engineering.
Li et al. grew microporous Mo2N single crystals and polycrystalline Mo2N from nonporous MoO3 single crystals. Mo2N had a much higher N2 reduction reaction rate than MoO3 single crystals. In addition, the porous Mo2N single crystals exhibited better catalytic efficiency and long-term stability than polycrystalline Mo2N. This investigation suggested a new approach for developing and designing molybdenum-based porous single crystals as electrocatalysts for ammonia synthesis.
Li et al. prepared poly (N-isopropyl acrylamide) gels by 3D printing and in situ polymerized polyaniline on poly (N-isopropyl acrylamide) substrate using phytic acid to constitute an interpenetrating network. The composite hydrogels had excellent tensile properties, high electrical conductivity, and sensitive thermal response sensitivity, which could be used in stimulus-response electronics, flexible electronics, and artificial intelligence wearable devices.
Liu et al. developed two different lattice-oriented porous single crystalline-like TiO2 by a lattice reconstruction strategy of solid-solid phase transformation. Next, Ti3⁺ was introduced into the lattice to obtain a series of TinO2n−1 monomers with a Magneli phase. Porous single crystalline-like TinO2n−1 had an enhanced exciton lifetime, exhibited significant visible light absorption, and could be used as an electrode to provide strong photocurrents, opening up new avenues for the design of novel photovoltaic materials and the tuning of surface photoreactivity.
Lee et al. evaluated the mechanical strength of 3D-printed agate-based composites. They demonstrated that the arrangement and thickness of the reinforcement layers were vital factors affecting the physical properties of 3D-printed composites.
Belei et al. analyzed the effect of printed Laser-Powder Bed Fusion surface roughness and Fused Filament Fabrication parameters on the strength of Ti-6Al-4V/PA-CF joints produced by this process combination using a three-point bending test method. The data analysis indicated that the printing speed was the main parameter affecting the joint strength, followed by the inclination angle, with the coating height exhibiting only a minor effect.
The three reviews primarily summarized the AM of functional polymer composites with enhanced mechanical, electrical, biological, optical, and other properties. Sun et al. reviewed the respective manufacturing mechanisms and applications of AM and foaming. They summarized several methods for generating cellular structures through AM: 1) cellular scaffolds; 2) composite printing foam; 3) post-foaming of printed solid scaffolds; and 4) in situ foam 3D printing. Finally, the Research Topic and development trends of the 3D printing foams were analyzed.
Li et al. described the principle of vat polymerization technology and reviewed the current development of vat polymerization technology for manufacturing nanocomposites. Next, they analyzed the challenges faced by the 3D printing of nanocomposites based on vat polymerization and pointed out that the development bottleneck should be broken by further reducing the production cost of nanofillers and improving the compatibility of nanofillers with the resin matrix.
Miao et al. reviewed the tribological properties of carbon nanotubes (CNTs)-modified polymer composites. They analyzed the lubrication mechanism of polymers and the factors that influence the tribological properties of CNTs/polymer composites. In addition, the limitations of CNTs in improving the tribological properties of polymers were summarized, providing a reference for the preparation of high-performance polymers.
In conclusion, this Research Topic presented insightful and innovative reports focusing on the polymer AM technique, promoting the development of this field. We sincerely thank all authors and reviewers for contributing to this Research Topic.
XZ: writing—original draft preparation. JW: writing—review and editing. All authors contributed to the article and approved the submitted version.
This work is supported by Ningbo Public Welfare Science and Technology Planning Project (Grant No. 2022S099), the Regional Development Project of Fujian (Grant No. 2022H4020), the STS Project of Putian-CAS (Grant No. 2020HJST009), the Major Project of Science and Technology in Fuzhou (Grant No. 2021-ZD-281), and the Fuzhou Foreign Scientific and Technological Cooperation Projects (Grant No. 2022-Y-008).
We thank the authors participating in this Research Topic for their excellent articles and reviewers for their valuable comments.
The authors declare that the research was conducted in the absence of any commercial or financial relationships that could be construed as a potential conflict of interest.
All claims expressed in this article are solely those of the authors and do not necessarily represent those of their affiliated organizations, or those of the publisher, the editors and the reviewers. Any product that may be evaluated in this article, or claim that may be made by its manufacturer, is not guaranteed or endorsed by the publisher.
Keywords: 3D printing, additive manufacturing, polymers, process, applications, modelling
Citation: Zhou X and Wang J (2023) Editorial: Additive manufacturing for polymers. Front. Mater. 10:1230323. doi: 10.3389/fmats.2023.1230323
Received: 28 May 2023; Accepted: 01 June 2023;
Published: 13 June 2023.
Edited and reviewed by:
Robert Li, City University of Hong Kong, Hong Kong SAR, ChinaCopyright © 2023 Zhou and Wang. This is an open-access article distributed under the terms of the Creative Commons Attribution License (CC BY). The use, distribution or reproduction in other forums is permitted, provided the original author(s) and the copyright owner(s) are credited and that the original publication in this journal is cited, in accordance with accepted academic practice. No use, distribution or reproduction is permitted which does not comply with these terms.
*Correspondence: Jianlei Wang, amx3YW5nQGZqaXJzbS5hYy5jbg==
Disclaimer: All claims expressed in this article are solely those of the authors and do not necessarily represent those of their affiliated organizations, or those of the publisher, the editors and the reviewers. Any product that may be evaluated in this article or claim that may be made by its manufacturer is not guaranteed or endorsed by the publisher.
Research integrity at Frontiers
Learn more about the work of our research integrity team to safeguard the quality of each article we publish.