- Zhengzhou Shengda University, Zhengzhou, China
With the rapid development of science and technology, compared with traditional textiles, which provide basic functions such as shelter from the body and cold, intelligent textiles can create a more comfortable and safe environment for people, improve work efficiency and meet people’s demand for diversified functions. At present, polypropylene material has the characteristics of temperature sensitivity, washing resistance, friction resistance, good whiteness and softness, and is widely used in textile, clothing and other industries. In this paper, The temperature sensitivity of cross-linked cotton fabric was characterized by measuring and analyzing the equilibrium swelling ratio, wetting time and surface contact angle. The temperature at which polymer properties suddenly change is 35°C, and the initial wetting time of cross-linked cotton fabric is longer than that of original cotton fabric. When the temperature exceeds 150°C, it loses its temperature sensitivity, resulting in the cross-linked cotton fabric being insensitive to temperature. The most suitable polymer concentration is 1%–8%. According to the DSC curve of P(MEO2MA-co-EGMA360) in the range of 60°C–20°C, the glass transition temperature (Tg) was determined. There is an obvious endothermic peak on the DSC curve near −26°C, which indicates that the glass transition temperature of P(MEO2MA-co-EGMA360) is −26°C, and P (MEO2MA-EGMA360). It is in a viscous state at room temperature. The air permeability and moisture permeability of cross-linked cotton fabric can be adjusted by changing the temperature, and the wearing comfort of the fabric can be improved. The test results of fabric wearability show that after crosslinking reaction, the washing fastness and rubbing fastness of fabric are within acceptable range, while whiteness, softness and mechanical properties are not affected. Considering comprehensively, when the polymer concentration is 8%, the drying temperature is 130°C and the drying time is 2 min, the finished fabric has the best indexes. This is mainly due to the spontaneous “self-adjustment” of aggregation morphology between the hydrogen bonding between polymer and water molecules and the hydrophobic interaction between molecules themselves in order to maintain a delicate dynamic balance, thus reaching a new thermodynamic equilibrium state. When the temperature exceeds the transition temperature, the surface of P(MEO2MA-co-EGMA360) film changes from a dense film structure to a porous structure, so that the air and moisture permeability can be adjusted and the wearing comfort of the fabric can be improved.
1 Introduction
At present, polyacrylate polymers are mostly applied to textiles by grafting. This method is tedious and time-consuming in the process of preparing textile composites, and there are a lot of residual solvents, metal ion catalysts, etc. which are not easy to clean, so it is impossible to characterize the physical and chemical properties of polymers. In view of this, the cross-linking method used in this paper to prepare responsive textile materials is more convenient, faster, green and environmentally friendly than grafting, and is conducive to industrial production.
Intelligent textiles refer to textiles that can perceive or respond to the stimulation of the external environment, while retaining the original style of the fabric (Chen, 2010; Wang et al., 2012). Intelligent textiles originate from intelligent materials, and Takagi Junyi put forward the concept of intelligent materials according to the idea of combining materials with information science (Shi, 1994). Intelligent textile is a kind of silk with shape memory function based on intelligent polymer hydrogel, which is considered as the earliest intelligent textile (Hongu and Phillips, 1997). Intelligent textiles based on these materials include shape memory, intelligent waterproof and moisture permeable, intelligent temperature control and color-changing camouflage textiles (Crespy and Rossi, 2007; Liu and Hu, 2005). Intelligent textiles can create a more comfortable and safe environment for people, and meet people’s diversified needs (Gu and Cao, 2006).
As a typical LCST temperature-sensitive polymer, polypropylene (N- isopropylacrylamide) has been widely studied by scholars (Heskins and Guillet, 1968a; Laschewsky et al., 2013). Temperature-responsive polymer is one of the most important stimulus-responsive polymers. The aqueous solution of this kind of polymer has a very important parameter, that is, the lower critical solution temperature. When the temperature rises above LCST, the polymer chains contract and aggregate, and precipitate is precipitated from water, which shows the phenomenon of phase separation (Fujishige et al., 2004; Xue et al., 2016). The main chain of the polymer contains nitrogen elements, such as poly N- isopropylacrylamide (PNIPAM), poly N, N- diethylacrylamide (PDEAAM), poly 2- carboxyisopropylacrylamide (PCIPAAM), etc. André et al. (2005) prepared a temperature-sensitive block copolymer poly block copolymer with butyl acrylate and diethyl acrylamide as monomers. Gottmanis (Gotzamanis et al., 2006) and others successfully prepared the block copolymer of poly (2- ethyl methacrylate) and poly (ethyl methacrylate) by group transfer polymerization. Scarpa et al. (1967) first discovered that PNIPAm aqueous solution has a reversible change from homogeneous phase to solid-liquid separation phase at about 32°C. Heskins et al. (Heskins and Guillet, 1968b) found an obvious endothermic peak at about 40°C, which they attributed to the change of enthalpy of polymer during phase transition. Zhong et al. (2011a) studied the shrinkage behavior of polyethylene glycol methacrylate (PMDEGA), and obtained the variation curves of rotation radius Rg of heterogeneous phase at different temperatures. Heskins et al. (Zhong et al., 2011b) found that with the increase of molecular weight, the viscosity of PNIPAM aqueous solution decreased under the same conditions. Kim et al. (2006) tested the rheological properties of block copolymer P aqueous solution of polyethylene glycol methacrylate and polycaprolactone at 6°C–70°C. Chen et al. (2010) prepared nanofibers with core-sheath structure by electrospinning technology. PVC-like coated fabrics are widely used in the development of life jackets, cold-proof and immersion-resistant clothing as immersion-resistant clothing fabrics (Gu, 2000), but once they meet with water, they can prevent water from invading the human body, resist immersion and moisture, and fully realize the protective effect on the human body (Zhang and Song, 2019). Liu Shufang et al. (Liu et al., 2019) cross-linked N- tert-butyl acrylamide-co-acrylamide and P(NIBA-co-AAM) on cotton fabric by coating method, and found that the cross-linked cotton fabric with weight gain rate of 8%–14% has the function of water resistance and immersion resistance. Ma Xiaoguang et al. (Ma, 2019) The fabric grafted by PAMPS/NIPAM still has good temperature-sensitive property and soaking resistance. Liu et al. (2014) found that the surface of raw cotton and fiber treated by initiator had typical gully structure. Wang et al. (Wang and Yu, 2015) tested that the air permeability of BTCA cross-linked cotton fabric was lower than that of the original cotton fabric as expected, and it was possible that BTCA formed a continuous film on the fiber surface, which blocked the channel for the fabric to transport moisture to the outside world; Wu et al. (2016) initiated grafting of dimethylaminoethyl methacrylate onto cotton fabric by surface ATRP, and obtained grafted cotton fabric with high pH and temperature response. Ye et al. (2015) found that the copolymer P(NIPAM-EGMA) with 5 mol% has good surface hydrophilicity at the transition temperature. Hu et al. (Hou et al., 2019; Cheng Hanlie et al., 2022; Cheng H. et al., 2022) combined polyurethane with PNIPAM grafted nonwoven fabric to obtain nonwoven fabric composite with a layer of poly (N-isopropylacrylamide)/polyurethane thermosensitive gel on the surface. Mylsamy, Bhuvaneshwaran, etc. combine fibers/fillers as reinforcing materials for different polymer composites, which provides potential for developing multi-functional structures and materials for leading applications. Because biological materials and synthetic materials have their own advantages and disadvantages, different materials are used in combination or in composite form to improve physical, chemical, mechanical and biological quality (1Mylsamy et al., 2023). Aru Chamy K, Myl Samy B, Palaniappansk, etc. prepared textile composites with different fabric weight ratios by molding process, and tested the interlaminar shear, bending, compression, tensile and impact strength of the composites according to ASTM standards. The prepared natural fiber composite material (cotton/bamboo) can be used as an environment-friendly substitute for man-made materials conducive to pollution management (Aruchamy et al., 2023). Kumar, Karavalasu Velusamy Mahesh and others regard graphene oxide (GO) as a carbon-based filler, which has excellent properties for preparing polypropylene (PP) nanocomposites (Kumar et al., 2019). Aruchamy, K., Subramani, S.P. and others think that the decrease of yarn spacing and the increase of yarn hairiness lead to the decrease of air permeability and water permeability. With the increase of bamboo fiber content, the water permeability and air permeability of fabrics increase (Aruchamy et al., 2020). Viet, C.X., Ismail, H., Masa, A., Hayeemasae, N, etc. prepared carboxyl functionalized graphene-based polypropylene nanocomposites by melt blending method (Viet et al., 2021).
In this paper, the cross-linked temperature-sensitive polypropylene polymer P(MEO2MA-co-EGMA360) was used to prepare textile composites, which solved various problems existing in the previous temperature-sensitive polymers, and the permeability/humidity, cleaning performance and wearability (whiteness, washing fastness, strength and softness) of the composite fabrics were measured. Finally, the intelligent textiles with intelligent cleaning and comfort control were prepared, which laid a theoretical foundation for the preparation of intelligent textiles based on polyacrylate temperature-sensitive polymers. The novelty of this paper mainly lies in that the types of copolymers are different from previous literature, and polypropylene copolymers are used this time. The results of this paper focus on the application, without in-depth analysis of the polymer structure, and analyze the changes of the main properties of the fabric before and after treatment.
2 Materials and methods
2.1 Experimental materials
Fabric specification of raw materials and reagents: 40D×40D plain cotton fabric, 180 g/cm2, provided by Procter & Gamble Company of America, 95% of 2- methyl -2-acrylic acid -2-(2- methoxyethoxy) ethyl ester (MEO2MA); Poly (ethylene glycol) methacrylate (EGMA 360), Mn = 360 g/mol, 95%; Polyethylene glycol methyl ether methacrylate (OEGMA300), Mn = 300 g/mol, 95%, provided by Sigma-Aldrich Reagents Co., Ltd. (N- pentamethyl divinyl triamine) (PMDETA), 99%; 2- bromoethyl isobutyrate (EBiB), 98%; Cuprous bromide (Cubr); Anisole (AR), the above reagents are provided by Shanghai Alddin Reagents Co., Ltd. Tetrahydrofuran (THF), n-hexane, 1,4- dioxane, ammonia water, dichloromethane. The above reagents are provided by Hangzhou Gaojing Fine Chemical Co., Ltd. Hydrogen peroxide (AR) is provided by Wuxi Zhanwang Chemical Reagent Co., Ltd.
2.2 Preparation method of polyacrylate temperature-sensitive polymer
Table 1 atom transfer radical polymerization (ATRP) was used. In a 100 m L reaction flask, monomers MEO2MA (3.14 m L, 17 mmol), OEGMA300 (0.86 m L, 3 mmol) or EGMA360 (0.98 m L, 3 mmol) were added, and then 10 mL anisole was added to dissolve them. Then, the catalyst CuBr (20 mg, 0.14 mmol) and ligand PMDETA (45 mL, 0.21 mmol) were added, stirred and dissolved, and then the initiator EBiB (21 mL, 0.14 mmol) was added to seal the reaction bottle. As ATRP is sensitive to oxygen, all the above operations are carried out in glove box (Labstar, M.Braun Company, Germany). Take the above reaction bottle out of the glove box, and stir in oil bath at 90°C for 3 h. Open the reaction bottle, place the reaction solution in an ice-water bath, stir and quench, and terminate the reaction. After 20 min, the mixture was dissolved in tetrahydrofuran, and then the catalyst was removed by neutral alumina to obtain viscous liquid. Finally, precipitate with n-hexane, shake and stand, remove the upper layer, clear the night, dissolve and precipitate for three times, and then dry to constant weight, so as to obtain a colorless and transparent colloidal final product with a yield of 70%–80%.
2.3 Preparation method of intelligent textiles
Textiles are washed with acetone and ethanol to remove impurities, then boiled in 10% Na2CO3 solution for 3h, finally washed with clean water, and dried at 60°C for later use. Firstly, the temperature-sensitive polymer P(MEO2MA-co-EGMA360) is mixed with cross-linking agent, initiator and solvent to prepare cross-linking finishing liquid. Then, the finishing liquid is used to pad the textile, and after pre-drying and baking, the temperature-sensitive polymer and the fabric have a cross-linking reaction to prepare the intelligent textile with temperature response. Preparation process: preparation of padding finishing liquid → second dipping and second rolling (rolling rate 70–80%) → pre-drying (60°C, 5 min)→ baking (110–150°C, 1–5 min) → water washing → drying.
3 Results and discussion
3.1 Analysis of temperature-sensitive properties of intelligent textiles made of polypropylene
The temperature response of cross-linked cotton fabric is the key to its application. The temperature sensitivity of cross-linked cotton fabric was characterized by measuring and analyzing the equilibrium swelling ratio, wetting time and surface contact angle of cross-linked cotton fabric. Before the experimental test, five pieces of fabric treated under different conditions were selected to ensure the accuracy of the experimental results.
3.1.1 Effect of polymer concentration on swelling ratio
Figures 1, 2 shows the curve of equilibrium swelling ratio (ESR) of raw cotton fabric and cross-linked cotton fabric with different P(MEO2MA-co-EGMA360) concentrations at 25°C–50°C. Because the raw cotton fabric is not temperature-sensitive, its equilibrium swelling rate does not change within the tested temperature range. The initial ESR of cross-linked cotton fabric with 8% concentration reached 133%, and then changed little at 25°C–35°C. However, when the temperature exceeds 35°C, the ESR decreases obviously, and finally the ESR is close to that of the original cotton fabric. This is because the cross-linked cotton fabric has a layer of temperature-sensitive copolymer P(MEO2MA-co-EGMA360) on its surface. At 35°C (below TT), P(MEO2MA-co-EGMA360) absorbs water and expands, forming hydrogen bonds with surrounding water molecules, so the weight of cross-linked cotton fabric increases, which shows the increase of ESR. When the temperature exceeds 35°C, the hydrogen bond breaks, the molecular chain of P(MEO2MA-co-EGMA360) shrinks, and the water molecules are released, and the volume shrinks obviously, and the phase transition behavior occurs, which shows that the ESR decreases significantly. The ESR of cross-linked cotton fabrics with 2% and 4% P(MEO2MA-co-EGMA360) concentration also decreased at 25°C–35°C, but compared with 8% cross-linked cotton fabrics, the ESR shrinkage of the former decreased less and the phase transition behavior was not obvious.
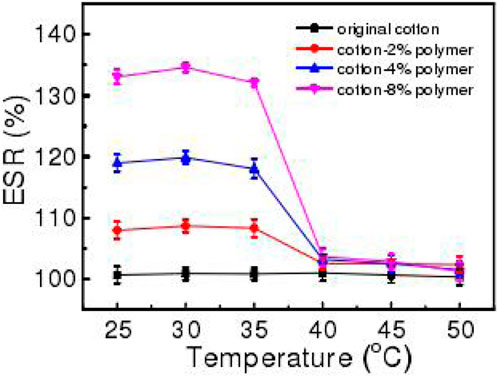
FIGURE 2. Curve of equilibrium swelling ratio of raw cotton fabric and cross-linked cotton fabric with different concentrations with temperature.
3.1.2 Effect of polymer concentration on wetting time
Wettability is an important index of fabric surface properties. The change process of wetting time between 30°C and 50°C of raw cotton fabric and cross-linked cotton fabric with different P(MEO2MA-co-EGMA360) concentration was measured, as shown in Figure 3. Due to the high water absorption of cotton fabric, the water droplets on the original cotton fabric spread quickly in about 5 s, so the wetting time is about 5 s. When the initial wetting time of 8% cross-linked cotton fabric is 19 s, the spreading speed of water droplets is much slower than that of the original cotton fabric. It may be that pure cotton fabric has good hygroscopicity, and after water drops drop onto the fabric, they quickly spread around through the fibers. Although the surface of crosslinked cotton fabric is hydrophilic P(MEO2MA-co-EGMA360) layer, the diffusion speed of water drops in the polymer is much slower, so the initial wetting time of crosslinked cotton fabric is longer than that of the original cotton fabric. With the increase of temperature, the wetting time of cross-linked cotton fabric suddenly changed from 35°C to 45°C, and increased from 18 s to 33 s.
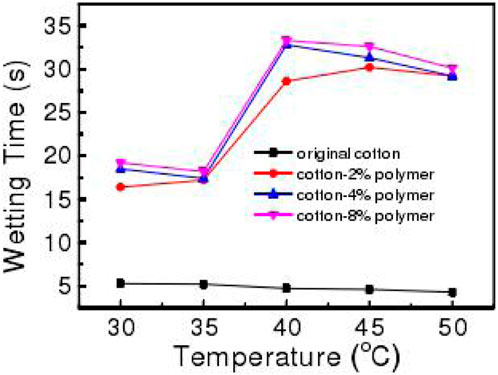
FIGURE 3. Contact angle curves of raw cotton and cross-linked cotton fabric with different polymer concentrations with temperature.
3.1.3 Effect of baking temperature on hydrophilicity and hydrophobicity
By measuring the change of contact angle of cross-linked cotton fabric prepared at baking temperature of 110°C, 120°C, 130°C, 140°C, 150°C for 5 min, the influence of baking temperature on hydrophilicity and hydrophobicity of cross-linked cotton fabric was characterized. The cross-linked cotton fabric prepared at 130°C and 140°C baking temperature has obvious temperature-sensitive property, which indicates that the polymer and fabric cross-link under this condition. Figure 4 the change of contact angle is similar to the change of wetting time of cross-linked cotton fabric. That is, in the transition temperature range, the surface of crosslinked fabric changes from hydrophilic to hydrophobic, the water contact angle increases, and the wetting time decreases. However, the contact angle of the cross-linked cotton fabric did not change as expected when the baking temperature was increased to 150°C. The reason for this phenomenon was that the side chain of P(MEO2MA-co-EGMA360) was decomposed at a higher temperature, and the temperature-sensitive property was lost, which led to the cross-linked cotton fabric not being temperature-responsive.
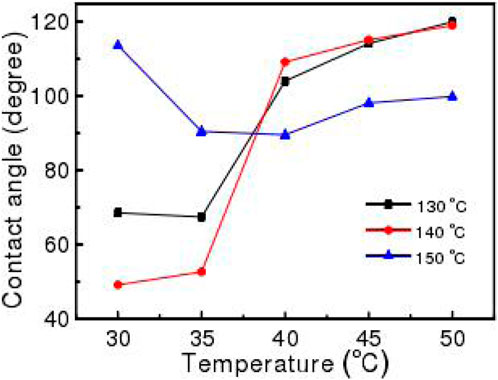
FIGURE 4. Contact angle curve of P(MEO2MA-co-EGMA360) crosslinked cotton fabric baked at different temperatures for 2 min with temperature.
To sum up, only when the baking temperature is controlled between 130°C and 140°C can the cross-linked cotton fabric have good temperature sensitivity. The curing time should be controlled for more than 2 min, which can ensure the complete crosslinking reaction. Considering the energy saving, the baking temperature is 130°C and the baking time is 2 min. The cross-linked cotton fabric has good temperature-sensitive performance.
3.2 Intelligent comfort control analysis of intelligent textiles prepared from polypropylene
The comfort of textiles is the most direct feeling of human body to clothes during wearing. There are many factors that cause the discomfort of textiles, including the air permeability, moisture permeability and heat insulation of fabrics.
By measuring the air permeability and moisture permeability of cross-linked cotton fabric, and comparing with the original cotton fabric, it is characterized that the cross-linked fabric has intelligent and comfortable control performance. The air permeability test results are shown in Figure 5A. For convenience of comparison, the difference between air permeability of fabric at 45°C and 25°C is calculated, and the difference is used as the dependent variable, and the cross-linked cotton fabrics with different polymer concentrations are plotted as independent variables (Figure 5B). It can be seen from the figure that the air permeability of raw cotton fabric has increased by 2 mm/s in the process of increasing from 25°C (198 mm/s) to 45°C (200 mm/s). It may be due to the slight thermal expansion of the fabric during the heating process, the corresponding increase of pores and the easy penetration of gas, so the air permeability slightly increased. In contrast, the air permeability of 2% cross-linked cotton fabric at 25°C is 192 mm/s, which is somewhat lower than that of the original cotton fabric. This is because the polymer is cross-linked on the cotton fabric to form a polymer film, which blocks the pores between the cotton fabric fibers, and the air flow is blocked, resulting in the decrease of air permeability. However, when the temperature was raised to 45°C, the air permeability of P(MEO2MA-co-EGMA360) cross-linked cotton fabric increased to 198 mm/s, and the air permeability increased. The reason is that at room temperature (below TT), the temperature-sensitive polymer on cross-linked cotton fabric keeps gel state by absorbing the moisture in the air, and forms a dense polymer film on the fabric, with low air permeability; When the temperature rises above TT, the polymer film shrinks and collapses, resulting in a large number of tiny holes and gaps, which promotes the increase of air permeability. With increasing the concentration of P(MEO2MA-co-EGMA36o), the thickness of polymer layer on the surface of cross-linked cotton fabric increases. As expected, the air permeability of cross-linked cotton fabric decreases obviously at 250C°C, but at 45°C, it decreases much more gently. As can be seen from Figure 5, with the increase of polymer concentration, the enhancement effect of air permeability shows an upward trend. The above analysis shows that the comfort control function of cross-linked cotton fabric is more obvious at high concentration.
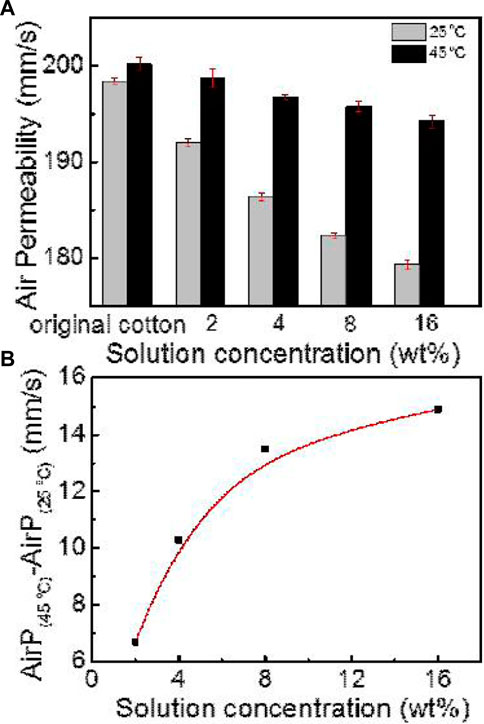
FIGURE 5. (A) Column chart of the change of air permeability of raw cotton and P(MEO2MA-co-EGMA360) cross-linked cotton fabric with polymer concentration at 45°C and 25°C; (B) Variation curve of air permeability difference between raw cotton and cross-linked cotton fabric with polymer concentration at 45°C and 25°C.
The moisture permeability of fabric is also one of the important factors affecting the wearing comfort of fabric. Figure 6 shows the change curve of moisture permeability ratio of raw cotton and cross-linked cotton fabrics with different concentrations at 45°C and 25°C. The air permeability ratio of raw cotton fabric is 3, while that of crosslinked cotton fabric with 2% polymer concentration is 3.5. The principle of this phenomenon is the same as that of air permeability. The moisture permeability of cross-linked cotton fabric is enhanced when the concentration of the cross-linked cotton fabric is between 2% and 8%. When the concentration reaches 16%, it is now decreasing. This may be due to the fact that under the condition of 16% concentration, the polymer is enough to cover the fabric. The curve shows that in the process of phase transition, the hydrophobic chain segments of polymer molecules move and approach, but due to the large thickness, the channel through which water vapor can pass cannot be formed. Therefore, when the concentration is too high, the adjustment effect of cross-linked cotton fabric on moisture permeability is not obvious enough.
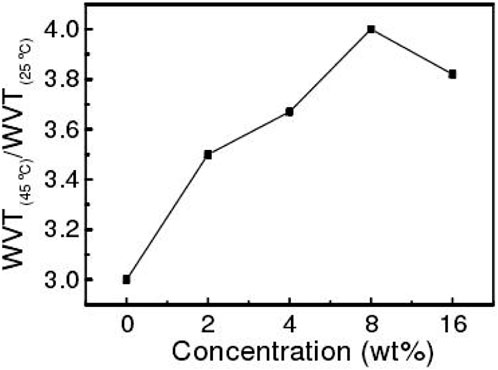
FIGURE 6. Curve of the ratio of moisture permeability of raw cotton and P(MEO2MA-co-EGMA360) cross-linked cotton fabric with polymer concentration at 45°C and 25°C.
To sum up, compared with the original cotton fabric, the crosslinked cotton fabric with polymer concentration of 1%–8% can adjust the air permeability and moisture permeability by changing the temperature, thus improving the wearing comfort of the fabric, and it has the function of intelligent comfort control.
3.3 Wearability analysis of intelligent textiles made of polypropylene
Good wearability is a necessary condition for textile application. The cross-linking combination of P(MEO2MA-co-EGMA360) and cotton fabric has been studied on its washing fastness, rubbing fastness, whiteness and softness, in order to obtain cross-linked cotton fabric with good wearability.
3.3.1 Fastness to washing
The daily cleaning of textiles is an essential part of our daily life. The flexible intelligent textiles based on polyacrylic acid cool temperature-sensitive polymer proposed in this paper have intelligent cleaning performance, but its application is limited to less washing and higher cleaning efficiency compared with ordinary textiles. Therefore, washing fastness is still an important indicator of its application.
Figure 7 shows the curve of the weight loss rate of polymer on the surface of cross-linked cotton fabric with washing times. It can be seen from the figure that when the concentration of P(MEO2MA-co-EGMA360) is 2%, the weight loss rate of polymer reaches 5% in the first two washing processes. This may be due to the fact that during the crosslinking reaction, some temperature-sensitive polymers did not react chemically with the crosslinking agent, resulting in covalent bonding, but were entangled or adsorbed on the surrounding polymers by physical bonding. In the process of stirring and cleaning in aqueous solution, they separated from the crosslinked cotton fabric, resulting in the weight reduction. The weight loss rate of cross-linked cotton fabric continued to decrease with the increase of washing times. When it reached the fourth time, the weight loss rate was 6%, and the weight of cross-linked cotton fabric remained unchanged after continuous washing. The concentration of P(MEO2MA-co-EGMA360) increased to 4%, 8% and 16%, and the amount of polymer on the cross-linked cotton fabric increased, so the weight loss rate was higher in the previous cleaning processes. The same point is that the weight of cross-linked cotton fabric with different polymer concentrations is balanced after 4 times of cleaning. It is worth mentioning that even though the cross-linked cotton fabric with polymer concentration of 16% has been washed five times, the weight loss rate is 16%, indicating that 84% of the polymer still remains on the fabric. Therefore, it can be concluded that the prepared cross-linked cotton fabric has good washing fastness.
3.3.2 Friction fastness
In the process of wearing textiles, it is inevitable to encounter various kinds of friction, which will not only cause the loss of fabric fibers and yarns, but also affect the aesthetic appearance of clothes, and affect the various properties of fabrics.
Figure 8 shows the change curve of weight loss rate of polymer P(MEO2MA-co-EGMA360) on cross-linked cotton fabric after 50 rubs. Obviously, after 10 times of rubbing, the amount of polymer on the fabric obviously decreased by 17%. Then, in the process of 15–20 times of rubbing, the weight decreases less until it reaches equilibrium after 50 times. The reason for this phenomenon is similar to the washability of cross-linked cotton fabric.
The polymer layer on the surface of cross-linked cotton fabric is worn out during friction, which may affect the temperature-sensitive performance of cross-linked fabric. Therefore, the temperature-sensitive property stability of crosslinked cotton fabric was characterized by measuring the change of equilibrium swelling rate of crosslinked fabric at 25°C and 45°C after rubbing. As shown in Figure 9, before the friction test, the ESR of P(MEO2MA-co-EGMA360) cross-linked cotton fabric at 25°C and 45°C was 105% and 136% respectively, that is, the difference between ESR at the transition temperature and ESR at the transition temperature was 31%, and the ESR of cross-linked cotton fabric suddenly changed near the transition temperature. With the increase of rubbing times, the difference between them gradually decreases, which is because part of P(MEO2MA-co-EGMA360) is consumed in the rubbing process, resulting in the decrease of the temperature-sensitive property of the fabric. After 25 to 50 times of rubbing, the difference of ESR kept at about 23%, reaching a relatively balanced state, which indicated that P(MEO2MA-co-EGMA360) cross-linked cotton fabric had good friction resistance and durability in daily life applications.
3.3.3 Whiteness
The choice of clothes color is an important way for people to enhance their overall aesthetic feeling and show their individuality. The dyeing of yarn or fabric is a complicated process, and pure white original fabric is often favored because it will not affect other dyed colors.
It can be seen from Figure 10 that the whiteness of the original cotton fabric is 78.3%, and the whiteness of the crosslinked cotton fabric with 2% P(MEO2MA-co-EGMA360) concentration is still 78.3% after cross-linking. With the increase of P(MEO2MA-co-EGMA360) concentration, the whiteness of cross-linked cotton fabric decreased slightly, from 78.2% to 77.9%. It can be seen that the whiteness of cross-linked cotton fabric with 16% polymer concentration decreases by less than 1% compared with the original cotton fabric. Under the preparation conditions adopted in this experiment, the whiteness of cross-linked cotton fabric has no obvious change compared with the original cotton fabric. This phenomenon should be attributed to mild reaction conditions, and the baking temperature of 130°C was finally selected in the experiment to avoid fabric yellowing.
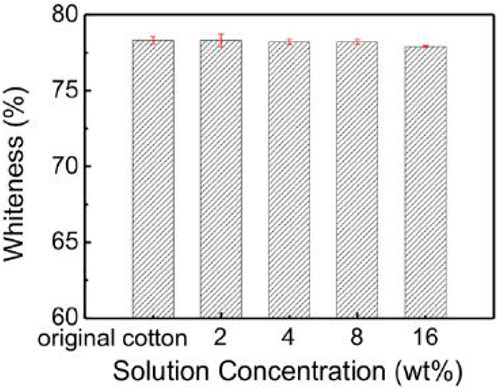
FIGURE 10. Column chart of whiteness change of raw cotton fabric and cross-linked cotton fabric with different polymer concentrations.
3.3.4 Softness
Softness is an important index to evaluate the wearability of fabric. For cross-linked cotton fabric, the polymer layer on the surface directly affects the handle of the fabric. Therefore, the state of polymer at room temperature is bound to play a decisive role in the softness of cross-linked cotton fabric. In view of this, the DSC curve of P(MEO2MA-co-EGMA360) in the range of 60°C–20°C was measured, and its glass transition temperature (Tg) was determined. It can be seen from Figure 11 that an obvious endothermic peak appears on the DSC curve around −26°C, indicating that the glass transition temperature of P(MEO2MA-co-EGMA360) is −26°C. Therefore, it can be inferred that P(MEO2MA-co-EGMA360) is in a viscous state at room temperature, which can also be known from the fact that “the synthesized product is a colloidal substance” in the process of polymer preparation.
4 Conclusion
In this paper, P(MEO2MA-co-EGMA360) was synthesized, and the intelligent textiles with temperature-sensitive properties were prepared by padding, drying and baking. Through the fabric washing experiment and the measurement of air permeability and moisture permeability, it is proved that the cross-linked fabric has the functions of intelligent cleaning and comfort control. The specific results are as follows:
(1) By measuring and analyzing the equilibrium swelling ratio, wetting time and surface contact angle of the crosslinked cotton fabric, the temperature sensitivity of the crosslinked cotton fabric was characterized. The temperature of polymer property mutation was 35°C, the initial wetting time of the crosslinked cotton fabric was longer than that of the original cotton fabric, and it lost its temperature sensitivity when the temperature exceeded 150°C, which led to the non-temperature sensitivity of the crosslinked cotton fabric. The most suitable concentration of polymer is 1%–8%. At this time, the air permeability and moisture permeability of crosslinked cotton fabric can be adjusted by changing the temperature, and improve the wearing comfort of the fabric. At the same time, the washability and rubbing fastness of the fabric are within an acceptable range, and the whiteness, softness and mechanical properties are not affected, thus meeting the requirements of functional stability of intelligent textiles in daily life.
(2) The test results of fabric wearability show that after cross-linking reaction, the washability and rubbing fastness of the fabric are within an acceptable range, and the whiteness, softness and mechanical properties are not affected. Considering comprehensively, when the polymer concentration is 8%, the baking temperature is 130°C and the baking time is 2 min, the treated fabric has the best indexes.
(3) According to the DSC curve of P(MEO2MA-co-EGMA360) in the range of 60°C–20°C, and its glass transition temperature (Tg) was determined. There is an obvious endothermic peak on the DSC curve around −26°C, which indicates that the glass transition temperature of P(MEO2MA-co-EGMA360) is −26°C, and P (MEO2MA-EGMA360). Therefore, it can be inferred that P(MEO2MA-co-EGMA360) is in a viscous state at room temperature.
Data availability statement
The original contributions presented in the study are included in the article/Supplementary Material, further inquiries can be directed to the corresponding author.
Author contributions
ZW contributed to conception and design of the study, organized the database, performed the statistical analysis, wrote the first draft of the manuscript, wrote sections of the manuscript. I contributed to manuscript revision, read, and approved the submitted version.
Acknowledgments
The authors would like to show sincere thanks to those techniques who have contributed to this research.
Conflict of interest
The author declares that the research was conducted in the absence of any commercial or financial relationships that could be construed as a potential conflict of interest.
Publisher’s note
All claims expressed in this article are solely those of the authors and do not necessarily represent those of their affiliated organizations, or those of the publisher, the editors and the reviewers. Any product that may be evaluated in this article, or claim that may be made by its manufacturer, is not guaranteed or endorsed by the publisher.
References
André, X., Zhang, M., and Müller, H. E. (2005). Thermo-and p H-Responsive Micelles of Poly (acrylic acid)-block-Poly (N, N-diethylacrylamide). Macromol. Rapid Commun. 26 (7), 558–563. doi:10.1002/marc.200400510
Aruchamy, K., Mylsamy, B., Palaniappan, S. K., Subramani, S. P., Velayutham, T., Rangappa, S. M., et al. (2023). Influence of weave arrangements on mechanical characteristics of cotton and bamboo woven fabric reinforced composite laminates. J. Reinf. Plastics Compos. 0 (0), 776–789. doi:10.1177/07316844221140350
Aruchamy, K., Subramani, S. P., Palaniappan, S. K., Pal, S. K., Mylsamy, B., and Chinnasamy, V. (2020). Effect of blend ratio on the thermal comfort characteristics of cotton/bamboo blended fabrics. J. Nat. Fibers 19, 105–114. doi:10.1080/15440478.2020.1731903
Chen, M., Dong, M., Havelund, R., Regina, V. R., Meyer, R. L., Besenbacher, F., et al. (2010). Thermo-responsive core-sheath electrospun nanofibers from poly (N-isopropylacrylamide)/polycaprolactone blends. Chem. Mater. 22 (14), 4214–4221. doi:10.1021/cm100753r
Chen, Z. L. (2010). Progress in textile science and technology. Adv. Text. Sci. Technol. 71 (2), 88–934. doi:10.1177/004051750107100216
Cheng, H., Dong, Y., Lu, C., Qin, Q., and Cadasse, D. (2022a). Intelligent oil production stratified water injection technology. Wirel. Commun. Mob. Comput. 2022, 7. 3954446. doi:10.1155/2022/3954446
Cheng, H., Wei, J., and Cheng, Z. (2022b). Study on sedimentary facies and reservoir characteristics of Paleogene sandstone in Yingmaili block, Tarim basin. Geofluids 2022, 1–14. doi:10.1155/2022/1445395
Crespy, D., and Rossi, R. M. (2007). Temperature-responsive polymers with LCST in the physiological range and their applications in textiles. Polym. Int. 56 (12), 1461–1468. doi:10.1002/pi.2277
Fujishige, S., Kubota, K., and Ando, I. (2004). Phase transition of aqueous solutions of poly (N-isopropylacrylamide) and poly (N-isopropylmethacrylamide). J. Phys. Chem., 88–98.
Gotzamanis, G. T., Tsitsilianis, C., Hadjiyannakou, S. C., Patrickios, C. S., Lupitskyy, R., and Minko, S. (2006). Cationic telechelic polyelectrolytes: Synthesis by group transfer polymerization and self- organization in aqueous media. Macromolecules 39 (2), 678–683. doi:10.1021/ma051592e
Gu, Z. Y., and Cao, L. (2006). Intelligent textile design and application. Beijing: Chemical Industry Press, 100–101.
Gu, Z. Y. (2000). Development trend of high-tech protective fabrics. Chin. labor Prot. Artic., 24–29.
Heskins, M., and Guillet, J. E. (1968b). Solution properties of poly (N- isopropylacrylamide). J. Macromol. Science-Chemistry 2 (8), 1441–1455. doi:10.1080/10601326808051910
Heskins, M., and Guillet, J. E. (1968a). Solution properties of poly (N-isopropylacrylamide). J. Macromol. Science-Chemistry 2 (8), 1441–1455. doi:10.1080/10601326808051910
Hongu, T., and Phillips, G. O. (1997). New fibers. 2. New York: Woodhead Publishing Series in Textiles, 239–247.
Hou, Z. K., Cheng, H. L., Sun, S. W., Chen, J., Qi, D. Q., and Liu, Z. B. (2019). Crack propagation and hydraulic fracturing in different lithologies. Appl. Geophys. 16 (2), 243–251. doi:10.1007/s11770-019-0764-3
Kim, M. S., Hyun, H., Seo, K. Sl., Cho, Y. H., Won Lee, J., Rae Lee, C., et al. (2006). Preparation and characterization of MPEG–PCL diblock copolymers with thermo-responsive sol-gel-sol phase transition. J. Polym. Sci. Part A Polym. Chem. 44 (18), 5413–5423. doi:10.1002/pola.21659
Kumar, K. V. M., Krishnamurthy, K., Rathanasamy, R., Sathish Kumar, P., Pal, K., and Nayak, G. C. (2019). Influence of graphene oxide on the static and dynamic mechanical behavior of compatibilized polypropylene nanocomposites. Mater. Test. 61 (10), 986–990. doi:10.3139/120.111411
Laschewsky, A., Müller-Buschbaum, P., and Papadakis, C. M. (2013). Thermo-responsive amphiphilic di-and triblock copolymers based on poly and poly: Aggregation and hydrogel formation in bulk solution and in thin films. Heidelbeg: Springer International Publishing, 15–34.
Liu, B., and Hu, Y. (2005). The application of temperature-sensitive hydrogels to textiles: A review of Chinese and Japanese investigations. Fibres Text. East. Eur. 13 (6), 45–49. doi:10.33263/BRIACI122.22162228
Liu, S. F., Gu, Z. Y., and Niu, J. R. (2019). Preparation of intelligent anti-leaching fabrics based on coating method. Text. journals 30 (08), 101–106. doi:10.1016/j.indcrop.2021.113646
Liu, X., Li, Y., Hu, J., Jiao, J., and Li, J. (2014). Smart moisture management and thermoregulation properties of stimuli-responsive cotton modified with polymer brushes. RSC Adv. 4 (109), 63691–63695. doi:10.1039/c4ra11080c
Ma, X. G. (2019). Polymerized P(AMPS/NIPA) gel and its intelligent spinning initiated by microwave low temperature plasma. Tianjin, China: Tianjin Polytechnic University, 99–112.
Mylsamy, B., Aruchamy, K., Subramani, S. P., Palaniappan, S. K., Rangappa, S. M., and Siengchin, S. (2023). “Chapter 14 state of the art of advanced fiber materials: Future directions, opportunities, and challenges,” in Fiber materials: Design, fabrication and applications. Editors Aslam Jeenat, and Verma Chandrabhan (Berlin, Boston: De Gruyter), 357–372.
Scarpa, J. S., Mueller, D. D., and Klotz, I. M. (1967). Slow hydrogen-deuterium exchange in a non-.alpha.-helical polyamide. J. Am. Chem. Soc. 89 (24), 6024–6030. doi:10.1021/ja01000a006
Viet, C. X., Ismail, H., Masa, A., and Hayeemasae, N. (2021). Silane-coupled kenaf fiber filled thermoplastic elastomer based on recycled high density polyethylene/natural rubber blends. Polímeros 2 (31). doi:10.1590/0104-1428.20210039
Wang, W., and Yu, W. (2015). Preparation and characterization of CS-g-PNIPAAm microgels and application in a water vapour-permeable fabric. Carbohydr. Polym. 127, 11–18. doi:10.1016/j.carbpol.2015.03.040
Wang, X. Q., Xin, B. J., and Xu, J. (2012). Research progress and development trend of intelligent textile. Int. Text. Rev. 40 (10), 38–41. doi:10.1049/cim2.12024
Wu, J. D., Zhang, C., Jiang, D. J., Zhao, S. F., Jiang, Y. L., Cai, G. Q., et al. (2016). Self-cleaning p H/thermo-responsive cotton fabric with smart-control and reusable functions for oil/water separation. RSC Adv. 6 (29), 24076–24082. doi:10.1039/c6ra02252a
Xue, N., Qiu, X. P., Chen, Y., Satoh, T., Kakuchi, T., and Winnik, F. M. (2016). Effect of chain architecture on the phase transition of star and cyclic poly (N-isopropylacrylamide) in water. J. Polym. Sci. Part B Polym. Phys. 54 (20), 2059–2068. doi:10.1002/polb.24114
Ye, Y., Huang, J., and Wang, X. (2015). Fabrication of a self-cleaning surface via the thermosensitive copolymer brush of p (nipaam-pegma). ACS Appl. Mater. Interfaces 7 (40), 22128–22136. doi:10.1021/acsami.5b07336
Zhang, C. H., and Song, C. Y. (2019). The application of high performance protective clothing in europe. Chin. Personal. Prot. Equip. (4), 53–54.
Zhong, Q., Wang, W., Adelsberger, J., Golosova, A., Bivigou Koumba, A. M., Laschewsky, A., et al. (2011a). Collapse transition in thin films of poly(methoxydiethylenglycol acrylate). Colloid Polym. Sci. 289 (5-6), 569–581. doi:10.1007/s00396-011-2384-1
Keywords: intelligent textiles, low carbon, temperature-sensitive polypropylene, cross-linked cotton fabric, intelligent cleaning
Citation: Wu Z (2023) Design of a new clean and comfortable temperature-sensitive polyethylene-based copolymer textile. Front. Mater. 10:1225412. doi: 10.3389/fmats.2023.1225412
Received: 19 May 2023; Accepted: 26 July 2023;
Published: 04 August 2023.
Edited by:
Yingjie Cai, Wuhan Textile University, ChinaReviewed by:
Agus Arsad, University of Technology Malaysia, MalaysiaSathish Kumar Palaniappan, King Mongkut’s University of Technology North Bangkok, Thailand
Copyright © 2023 Wu. This is an open-access article distributed under the terms of the Creative Commons Attribution License (CC BY). The use, distribution or reproduction in other forums is permitted, provided the original author(s) and the copyright owner(s) are credited and that the original publication in this journal is cited, in accordance with accepted academic practice. No use, distribution or reproduction is permitted which does not comply with these terms.
*Correspondence: Zebin Wu, 160407124@stu.cuz.edu.cn