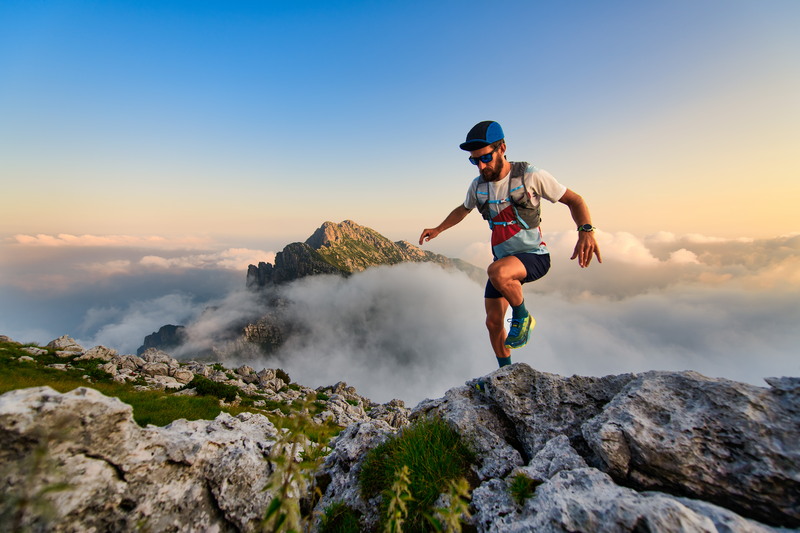
95% of researchers rate our articles as excellent or good
Learn more about the work of our research integrity team to safeguard the quality of each article we publish.
Find out more
EDITORIAL article
Front. Mater. , 15 May 2023
Sec. Smart Materials
Volume 10 - 2023 | https://doi.org/10.3389/fmats.2023.1210416
This article is part of the Research Topic Characterization and Application of Magneto-sensitive Soft Materials View all 20 articles
Editorial on the Research Topic
Characterization and application of magneto-sensitive soft materials
Magneto-sensitive soft materials are new synthetic functional materials that is normally composed of ferromagnetic or ferrimagnetic particles (size in a range from several nanometers to hundreds of micrometers), carriers (including water, organic solvent, liquids, gels, polymer and foams), surfactants and necessary additives. Being different from “hard” solid materials, “soft” means magneto-sensitive materials exist in the form of colloidal liquids, gels, and elastomers, such as magnetic fluids (MF), also called ferrofluids or magnetic liquids, magnetorheological fluids (MRF), magnetorheological gels (MRG), magnetorheological elastomers (MRE) and magnetorheological foams (MRFoam), so as to possess fluidity and magnetism simultaneously and can be easily deformed by applying external magnetic field force. Differences in the size of the magnetic particles and different carriers bring to magneto-sensitive soft materials distinct characteristics and behavior and provide many new perspectives and ideas for engineering application. This Research Topic covers innovations and applications in the field of different magneto-sensitive soft materials. We are proud to present 10 peer-reviewed contributions offering the latest insights on magnetic fluids and magnetorheological fluids.
Magnetic fluids are nanocolloids made up of nanometer-sized ferromagnetic particles dispersing in a carrier liquid (typically comprises three parts: base carrier liquid, surfactant, and ferromagnetic particles). Since the particles are easier to agglomerate, ferromagnetic particles are typically coated with surfactants to prevent agglomeration. Magnetic nanoparticles are uniformly disseminated in the carrier liquid with the assistance of surfactants, which play a crucial role in the magnetic fluid composition. Li et al. systematically studied the coating state and colloidal stability of oleic acid (OA) and 3-(N,N-Dimethylmyristylammonio) propanesulfonate (DP) coated magnetite nanoparticles in the polar and apolar carrier liquid. The total Gibbs interfacial energy was analyzed based on Van Oss-Chaudhry-Good and DLVO theory to describe the behaviors of coated particles in solvents. Zang et al. studied the effect of different fatty acids as surfactants on the rheological properties of magnetic fluids. The results showed that the mixed fatty acids showed greater viscosity growth and a greater slope of the viscosity growth curve than the magnetic fluids dispersed with a single acid. This indicates that the mixed fatty acids have more stable rheological properties. The viscousity-temperature performance of kerosene-base magnetic fluids at low temperatures can be improved by adjusting the ratio of mixed fatty acids. The most typical application of magnetic liquids is sealing, which has the outstanding advantages of zero leakage, long life and low resistance. Magnetic fluid seals as a class of non-contact sealing technology have been a research focus. In order to solve the problem of the pole shoes in the ferrofluid seal being easily damaged under the situation of the large radial beating of the main shaft, Liu et al. proposed a new structure of the ferrofluid seal that use a radial-charged ring magnet as the magnetic source. Considering that the ring magnets have problems of uneven magnetization and installation difficulties, use split magnets to take the place of ring magnets. Experiments and simulations were conducted on the above new structures, and all structures have a certain sealing pressure, which presents a reference example for the innovative design of magnetic fluid sealing structures. For the requirement of high vacuum and leakage rate of some small diameter low speed devices, Liu et al. designed a dual magnetic multi-stage magnetic fluid seal device by analyzing the advantages and disadvantages of four different vacuum magnetic fluid seal devices. The magnetic field strength and distribution of this seal device were analyzed using Ansys simulation software, and the proposed device was optimized by the calculation results. Compared with the traditional seal form, the multi-magnetic multi-stage magnetic fluid seal device has low processing difficulty, high reliability, and good pressure resistance performance. Although magnetic liquid sealing is widely used, but once magnetic liquid is injected into the structure of seal, it is difficult to estimate the working status of the magnetic fluid in the gap and then predict the failure. This hinders the further application of magnetic fluid seals in some important application, such as nuclear reaction. Therefore, it is imperative to find a non-destructive testing method to estimate the sealing status of the magnetic fluid seal. Chen et al. found that the state of the seal could be estimated by analyzing the acoustic emission (AE) signals generated during different magnetic fluid seals. By conducting the pressure test, analyzing the characteristic value of the acoustic emission signal, this is the first experiment of verifying the acoustic emission technique of magnetic fluid sealing. Dai et al. further proposed to perform higher-order cumulative image processing on sound signals and train convolutional neural network models for autonomous learning of image features, and experiments showed that the accuracy of the trained models for image recognition was much higher than other methods.
In addition to magnetic fluids, magnetorheological fluids (MRF) is another magneto-sensitive soft materials which been studied extensively. MRF are promising in controllable damping based on regulated apparent viscosity under magnetic field control and have been employed in various damping devices. He et al. designed a new type of variable damping MR torsional damper (MRTD) and proposed a semi-active control method to effectively control the torsional vibration of the crankshaft under multiple harmonic resonances, and a joint control simulation analysis was performed using Amesim and Matlab software. The simulation results indicated that the skyhook damping control significantly reduced the torsional vibration amplitude under both acceleration and uniform speed conditions, verifying the effectiveness of the skyhook-based control strategy for MRTD. Zou et al. signed and fabricated a magnetorheological energy absorber (MREA) with disc springs as recoiling parts, modeled the MR fluid flow based on the Bingham constitutive model, and then carried out unsteady extension based on the quasi-steady model. The experimental tests of the MREA show that the unsteady extension of the quasi-steady model can designate the behaviors of the MREA in different impact speeds better than the original; thus, the controllability of the MREA is verified. MR foam is a newly developed porous intelligent material, which can change its characteristics continuously, actively and reversibly under controllable external magnetic action, but its stiffness and storage modulus of foam are still very low and insufficient, thus limiting its application potential. Thus, Khaidir et al. improved the structure and storage modulus of MR foam by adding silica nanoparticles as an additive. By examining its rheological properties, it is known that the storage modulus of MR foam was increased by 260% with the addition of silica nanoparticles, especially at 4 wt%, due to the highest stiffness between 45 and 162 kPa. The results show that silica nanoparticles have good dispersion in the foam matrix, improve and strengthen the microstructure of MR foam, thus increasing the stiffness and storage modulus of MR foam. To reveal the transient temperature distribution pattern inside the MR grease torsional vibration damper and explore the relationship between the current and internal temperature of the device. Xiao et al. performed transient temperature simulation for MR grease devices, the results of the analysis reveal the internal temperature distribution and temperature rise characteristics of the torsional vibration damper, which provide a theoretical basis for the structural optimization and control strategy design of the MRG torsional vibration damper considering temperature as a factor.
These Research Topic contributions provide information about the latest developments in magneto-sensitive soft materials in relation to various aspects, such as material development and characterization, modelling, new structural design of the equipment, numerical calculation, simulation. The editors hope that you find these articles useful and are inspired by them.
ZZ prepared the draft. DL, MY, XN, and WL edited the draft. All authors listed have made a substantial, direct, and intellectual contribution to the work and approved it for publication. All authors contributed to the article and approved the submitted version.
The authors declare that the research was conducted in the absence of any commercial or financial relationships that could be construed as a potential conflict of interest.
All claims expressed in this article are solely those of the authors and do not necessarily represent those of their affiliated organizations, or those of the publisher, the editors and the reviewers. Any product that may be evaluated in this article, or claim that may be made by its manufacturer, is not guaranteed or endorsed by the publisher.
Keywords: magnetic fluids (MF), magnetorheological fluids (MRF), magneto-sensitive soft materials, non-contact sealing, torsional vibration damper, intelligent material, energy absorber
Citation: Zhang Z, Li D, Yu M, Niu X and Li W (2023) Editorial: Characterization and application of magneto-sensitive soft materials. Front. Mater. 10:1210416. doi: 10.3389/fmats.2023.1210416
Received: 22 April 2023; Accepted: 08 May 2023;
Published: 15 May 2023.
Edited and reviewed by:
Yancheng Li, Nanjing Tech University, ChinaCopyright © 2023 Zhang, Li, Yu, Niu and Li. This is an open-access article distributed under the terms of the Creative Commons Attribution License (CC BY). The use, distribution or reproduction in other forums is permitted, provided the original author(s) and the copyright owner(s) are credited and that the original publication in this journal is cited, in accordance with accepted academic practice. No use, distribution or reproduction is permitted which does not comply with these terms.
*Correspondence: Zhili Zhang, emx6aGFuZ0BianR1LmVkdS5jbg==
Disclaimer: All claims expressed in this article are solely those of the authors and do not necessarily represent those of their affiliated organizations, or those of the publisher, the editors and the reviewers. Any product that may be evaluated in this article or claim that may be made by its manufacturer is not guaranteed or endorsed by the publisher.
Research integrity at Frontiers
Learn more about the work of our research integrity team to safeguard the quality of each article we publish.