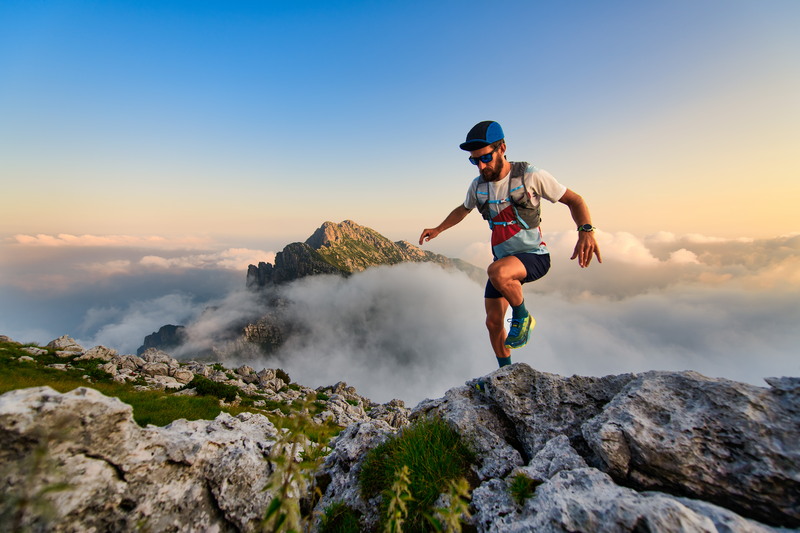
95% of researchers rate our articles as excellent or good
Learn more about the work of our research integrity team to safeguard the quality of each article we publish.
Find out more
ORIGINAL RESEARCH article
Front. Mater. , 24 April 2023
Sec. Structural Materials
Volume 10 - 2023 | https://doi.org/10.3389/fmats.2023.1195428
This article is part of the Research Topic Recent Advances in Testing and Modeling of Performance-related Mechanical Properties of Asphalt Mixtures View all 6 articles
The study investigated the modification mechanism of modified ground calcium carbonate (GCC) mineral powder using in asphalt concrete. Two types of Titanate coupling agents, namely, K38S (TCA-K38S) and 201 (TCA-201), as well as sodium stearate coupling agent, were adopted to prepare modified GCC. The optimized preparation process was obtained through the orthogonal test. Two kinds of modified GCC were preferably selected to prepare asphalt concrete according to modification mechanism characterization, their performance was analyzed and evaluated at macro and micro levels. The study results show that, the optimal scheme of sodium stearate modified GCC is modification temperature of 80°C, modification time of 50 min, modifying agent dosage of 2.0%. The crystal structure of GCC remains unchanged after modification, with the original lattice structure being maintained. TCA-201 and sodium stearate exhibit better coating properties than that of TCA-K38S. The contact angles of TCA-201 and sodium stearate modified GCC are larger than that of TCA-K38S modified GCC. The in-service performance of AC-13C asphalt concrete modified with sodium stearate is found to be superior to that of TCA-201 modified AC-13C asphalt concrete. Compared with the unmodified AC-13C asphalt concrete, the Marshall modulus, residual stability, freeze-thaw splitting strength ratio, and maximum flexural tensile strain of sodium stearate modified AC-13C asphalt concrete are increased by 54.55%, 2.73%, 10.47%, and 26.41% respectively. This paper provides theoretical guidance for the application of GCC mineral powder in asphalt concrete.
Mineral powder, an inorganic filler with particle size smaller than 0.15 mm, is obtained by grinding natural rocks or other mineral materials. It is categorized into alkaline mineral powder and acid mineral powder. The main component of alkaline mineral powder is ground calcium carbonate (GCC) from sources like limestone, magmatic rock. The main component of acid mineral powder is silica from materials like granite (Awed et al., 2022; Chen et al., 2022; Xing et al., 2022). Limestone with uniform lithology is widely distributed, easy to mining and processing, it is preferred over basalt in terms of cost and availability, making limestone mineral powder a common choice for asphalt concrete (Lesueur et al., 2013; Diab and Enieb, 2018). Antunes et al. (2016) studied the effect of chemical composition and particle geometry of six different mineral fillers on the consistency and stripping resistance of filler–asphalt mixture. Although mineral powder typically constitutes only 6%–8% of the total mineral aggregate in asphalt concrete, its surface area accounts for 70%–90% of the overall surface area of mineral aggregate. The adequate usage of mineral powder can improve the high-temperature stability of asphalt concrete, enhance the ability of asphalt pavement to resist external damage, and extend the in-service life of highway (Alvarez et al., 2012; Tarbay et al., 2019; Guo and Tan, 2021).
During the grinding process of GCC, unsaturated Ca2+and CO32- ions form on the particle surface. As Ca2+and CO32- ions are highly reactive and readily hydrate with moisture in the air, leading to the formation of polar hydroxyl groups on the surface of GCC powder. Consequently, it becomes challenging to achieve uniform dispersion of GCC powder in the non-polar polymer matrices. Additionally, the alkaline hydroxyl groups exhibit strong hydrophilic and oleophobic properties, which weakens the affinity of GCC and organic system, resulting in poor interface bonding between the two materials. Curtis et al. (1993) indicated that the presence of water weakened the adsorption capacity of the two most polar components of asphalt to the aggregate. In addition, to achieve the toughening and reinforcing effect of GCC, it is necessary to minimize the particle size. However, smaller GCC particles have a larger specific surface area and higher surface energy, making them more prone to agglomeration (Upadhyaya et al., 2013), which can affect the performance of the final product.
Therefore, the surface modification of industrial GCC is necessary to change the physical and chemical properties, improve its compatibility and dispersion with the asphalt matrix, and enhance its interface bonding force with the organic matrix, thereby enhancing the comprehensive performance of asphalt concrete. Coupling agents, such as stearic acid or stearate, are widely used for the modification of GCC (Liang et al., 2018; Yu et al., 2020; Han et al., 2022), they can change the solution system, and then modify the surface of mineral filler. The hydrophile-lipophile balance value of stearic acid/stearate is typically between 6 and 8, which means a strong wetting ability for the mineral filler. One end of stearic acid/stearate is a lipophilic long-chain alkane, which enhances its compatibility with the polymer matrix, while the other end is a hydrophilic carboxyl group that can bind to GCC (Rudawska et al., 2017; Seeharaj et al., 2019). An alkaline environment is more conducive to reduce the consumption of stearic acid/stearate, improve the activation degree of GCC (Li et al., 2020). Researches has shown that GCC mineral powder modified with coupling agents significantly improves high-temperature performance of modified asphalt (Li et al., 2019). Hao et al. (2012) prepared the nano CC composite modified asphalt and found that dynamic stability of nano CC composite modified asphalt concrete AC-13 was enhanced from 991 times/mm to 1,269 times/mm, and the residual stability was improved from 0.87 to 0.94.
Currently, there is limited research on the impact of surface modification of mineral powder on their macro and micro properties, and the evaluation of mineral powder performance in the current specification is mainly based on physical indexes. It cannot fully reflect its comprehensive properties and interaction modification mechanism. In this study, two kinds of titanate coupling agent and sodium stearate coupling agent were employed to modify the surface of GCC powder using a mechanochemical method. The optimum preparation process of modified GCC powder was determined by the assessment of the activation degree and oil absorption value and whiteness, then, the modification mechanism was analyzed at both macro and micro levels.
The chemical component of GCC powder (2000 mesh) are shown in Table 1, other addition agent like Titanate coupling agent K38S (TCA- K38S), Titanate coupling agent 201(TCA- 201), Sodium stearate (analytically pure), Anhydrous ethanol (analytically pure), Isopropyl alcohol (analytically pure) are employed in this study, the main technical parameters of them are listed in Table 2.
70# Class A road Petroleum Asphalt is adopted in this study, according to the Standard Test Methods of Bitumen and Bituminous Mixtures for Highway Engineering (2011), The technical indexes of 70# Class A road Petroleum Asphalt are shown in Table 3.
The aggregate used in this study is limestone, and the mineral filler is homemade modified GCC powder. The aggregate is divided into four grades, namely, S10 aggregate: 10–15 mm, S12 aggregate: 5–10mm, S15 aggregate: 0∼5mm, and mineral filler. Bulk density of aggregates is determined in accordance with the requirements of Test Methods of Aggregate for Highway Engineering (2005), the values are 2.673 g/cm3, 2.625 g/cm3, 2.595 g/cm3, 2.671 g/cm3.
In recent years, there are many researches on the surface modification of GCC powder, and the evaluation criteria on chemical indexes of GCC powder are relatively mature. In this study, activation degree, oil absorption value and whiteness are selected as the preferably chemical evaluation indexes, and the optimal modification process parameters of modified GCC powder are evaluated by orthogonal test. The activation, oil absorption and whiteness are determined according to the Analytic method for calcium carbonate (GB/T 19281-2014).
To determine the content of calcium carbonate in the obtained sample and verify the modifying agent coatings, in the air atmosphere and the range of 10°C–900°C, the fully dried samples are subjected to TG-DTA at the temperature increment of 10°C/min.
The D8ADVANCE X-ray diffractometer produced by BRUKER AXS GMBH in Germany is used to observe and characterize the crystal structure and cell type of calcium carbonate particles before and after modification, as shown in Figure 1A.
Signa 500 electron microscope (SEM) produced by Carl Zeiss Microscopy GmbH in Germany, as shown in Figure 1B, is employed to observe and characterize the morphology of GCC powder.
The TENSOR 27 Fourier transform infrared spectrometer (FT-IR) produced by BRUKER AXS GMBH in Germany (Figure 1C), is adopted to analyze the characteristic groups on the sample surface before and after modification and to infer the chemical reaction mechanism and the strength of chemical bond.
The interface contact angle between GCC powder sample and water is measured by JJC-2 contact angle meter.
Take a certain amount of GCC powder, add about 400 mL water, then add 1.5–2 mL sodium hexametaphosphate solution (200 g/L). Disperse with ultrasonic 3–15 min. The particle size of the sample was determined by laser particle size analyzer according to the A. method for calcium carbonate (GB/T 19281-2014).
High-temperature resistance, low-temperature resistance and water stability are important indexes of asphalt concrete. Marshall test, wheel tracking test, immersion Marshall test, freeze-thaw splitting test, low-temperature bending test are conducted according to Standard Test Methods of Bitumen and Bituminous Mixtures for Highway Engineering (2011), the Marshall stability, dynamic stability, residual stability, and freeze-thaw splitting strength ratio are determined for in-service performance assessment of asphalt concrete, as shown in Figure 2.
FIGURE 2. In-service performance assessment test, (A) Marshall test, (B) freeze-thaw splitting test, (C) low-temperature bending test.
Titanate coupling agent is quantitatively weighed and added into anhydrous ethanol to make a mass fraction of 60% modifying agent solution. By the same method, sodium stearate modifying agent is quantitatively weighed and added into isopropyl alcohol to prepare a mass fraction of 60% modifying agent solution. The GCC mineral filler of 2 kg is dried to a constant weight and heated to the specified temperature, then put it into modifying machine with specified amount of modifying agent. The temperature is controlled within the optimal modification temperature range of ±5°C. After modification, the modified GCC powder can be obtained by drying and grinding.
In order to obtain the optimized preparation process of modified GCC, L9 (34) orthogonal test is designed with oil absorption value, activation degree and whiteness as evaluation indexes. Three factors including modification time, modifying agent dosage and modification temperature are selected, each factor is equipped with 3 levels, specific orthogonal test design and specific level can be seen from Table 4.
AC-13C dense gradation asphalt concrete is prepared for the study on the influence of modified GCC. Asphalt concrete proportion is designed with Marshall test. The 70# Class A road Petroleum Asphalt and four grades of aggregate are employed according to the suspension dense design principle of continuous dense gradation. m (S10 aggregate): m (S12 aggregate): m (S15 aggregate): m (mineral filler) = 29: 30: 35: 6, the optimum asphalt-aggregate ratio of AC-13C asphalt concrete is 4.6%, the asphalt concrete gradation is shown in Figure 3.
The activation degree is a measure of the hydrophobicity after GCC surface treatment, which indicates the degree of coating on the surface of calcium carbonate. A higher activation degree reflects a better modification effect. The oil absorption value is determined by measuring the volume of dioctyl phthalate absorbed by the powder pores. The smaller the oil absorption value, the higher the dispersion, the better the modification effect. Higher whiteness indicates higher purity and a more stable and uniform nature. According to the ranking of factor significance, the influence of modification time, modifying agent dosage, and modification temperature on the above indexes can be determined. The optimized preparation process can be obtained through the range analysis of orthogonal test results, as shown in Table 5.
Range analysis results of orthogonal tests are presented in Appendix Table A1, the scheme satisfies most factors is chosen as a superior scheme. The superior scheme of TCA-K38S modified GCC is modification temperature of 80°C, modification time of 50 min, modifying agent dosage of 2.0%. The superior scheme of TCA-201 modified GCC is modification temperature of 80°C, modification time of 70 min, modifying agent dosage of 2.0%. The superior scheme of sodium stearate modified GCC is modification temperature of 80°C, modification time of 50 min, modifying agent dosage of 2.0%. The indexes are detected under the superior scheme of each modified GCC, then, compared with the 9 groups of test results in Table 5, the optimal modification scheme is obtained, as shown in Table 6.
The contact angle reflects the wettability of calcium carbonate (Valencia and Pileggi, 2018). It can be seen from Table 7 that the average measured contact angle of GCC without modification is 72.3± 3°. It indicates the GCC powder is hydrophilic, but not completely hydrophilic. However, the contact angles of modified GCC are increased compared to unmodified GCC, indicating that the surface becomes more hydrophobic and lipophilic due to the modification. The surface energy of modified GCC is significantly reduced, which makes the modified GCC has good dispersion in asphalt concrete. Table 7 also shows that the contact angle of TCA-201 modified GCC increases most significantly, indicating that TCA-201 has the best modification effect. Sodium stearate also shows good modification effect, with a contact angle reaching 102.7° ± 3°. On the other hand, TCA-K38S shows the least improvement in contact angle, with a contact angle of 87.5° ± 3°, indicating the least effective modification. Therefore, in practical application, regardless of the spalling condition of modifier, TCA-201 modified GCC and sodium stearate modified GCC are preferred due to their better practical effect.
Calcite is a crystalline form of GCC, it is diffraction angles of the standard spectra are 23.08°, 29.46°, 35.96°, 39.42°, 43.16°, 47.64°, 48.58° and 57.40° respectively. Figure 3 shows a comparison of the diffraction peaks of GCC before and after modification, and it can be observed that the peaks are corresponding and the peak shape is similar, indicating that the crystal shape of the mineral powder remains unchanged after modification, and it is still of the calcite type (Bahranowski et al., 2021). The crystal structure of GCC is not altered by the modification process, and the original lattice structure is still maintained.
As per Figure 4, it can be observed that the reaction temperature for several modified GCC falls within the range of 200°C–300°C, as reported in studies by Yuan et al. (2019) and Nakarai et al. (2021). Upon comparing the curve of unmodified GCC with the curves of modified GCC, it is evident that unmodified GCC shows minimal mass loss and remains relatively stable as the temperature increases in the temperature range of 200°C–600°C, while modified GCC exhibits varying degrees of mass loss with the increase of temperature, and the extent of mass loss roughly corresponds to the amount of modifying agent added. This shows that, in the process of temperature rise, the modifying agent molecules adsorbed on the surface of GCC are detached, resulting in the mass loss of modified GCC. Note that the TCA-201 modified GCC and sodium stearate modified GCC show larger mass loss in the same temperature range, which indicates that the nature of TCA-201 and sodium stearate modified GCC is more active. Moreover, it can be observed from Figure 4 that, the mass of GCC decreases significantly beyond 600°C, indicating the decomposition of GCC.
FIGURE 4. Modified GCC (A) XRD spectrum and (B) TG-DTA, a: Unmodified GCC, b: TCA-201 modified GCC, c: TCA-K38S modified GCC, d: sodium stearate modified GCC.
Figure 5 shows the FT-IR spectrum of unmodified GCC and modified GCC. In curve a, typical absorption peaks of calcium carbonate can be observed at 1,430 cm-1, 1,085 cm-1, 870 cm-1, and 710 cm-1, corresponding to antisymmetric stretching vibration peak, symmetric stretching vibration peak, out-of-plane bending vibration peak and in-plane bending vibration peak of CO32-, respectively (Feng et al., 2021; Águila-Almanza et al., 2022). The peak at 3,440 cm-1 corresponds to the stretching vibration absorption peak of -OH on the surface of GCC. Additionally, peaks at 2,855 cm-1 and 2,952 cm-1, indicate the presence of -CH2- symmetric and antisymmetric stretching vibration peaks respectively, which are attributed to long-chain alkyl groups in the titanate structure. It indicates that a titanate coupling agent has been grafted onto the surface of GCC. The titanate coupling agent forms a bond between the inorganic end RO- of the molecule and the -OH on the surface of calcium carbonate, resulting in adsorption of the coupling agent as a single molecule on the surface of calcium carbonate, forming a layer of molecular film and altering the surface properties of GCC.
FIGURE 5. Infrared spectrogram, (A) Unmodified GCC, (B) TCA-201 modified GCC, (C) TCA-K38S modified GCC, (D) sodium stearate modified GCC.
After the modification of GCC with sodium stearate, the intensity of the stretching vibration absorption peak at 3,440 cm-1 significantly decreases, indicating a reduction in hydrophilicity and an increase in oil repellency of the modified GCC. Additionally, new peaks at 2,850 cm-1 and 2,920 cm-1 corresponding to -CH2- symmetric stretching vibration and antisymmetric stretching vibration are observed, suggesting the presence of sodium stearate on the surface of GCC. By comparing the infrared spectra before and after sodium stearate modification, it is found that the characteristic peak of CO32- at 1,430 cm-1 is stronger than that before modification. The results show that the carboxyl group in sodium stearate and calcium ion on the surface of GCC form a calcium carboxylate. The organic modifying agent sodium stearate has a long-chain alkyl end, resulting in a fur-like two-dimensional curved structure on the surface of the modified GCC particles. When the coating amount reaches a single layer, GCC is completely modified by sodium stearate.
During the production of GCC, superfine GCC particles tend to agglomerate after grinding, which will affect the performance of asphalt mixtures. Therefore, the particle size and distribution of GCC after surface modification, TCA-201, TCA-K38S and sodium stearate modified GCC were analyzed using a laser particle size analyzer, and the results are shown in Figure 6.
As can be seen from Figure 6, the fineness of the GCC modified by mechanochemical method meets higher standards, with particle sizes all below 60 μm. Compared with the particle size of the unmodified GCC, the median particle size (D50) of GCC increases, and the coarse-grained particle size (D90) of modified GCC also increases under the same sieve residual conditions. This is because during surface mechanical modification, the modifying agent binds the small particle size GCC to the original GCC particles, blunting the sharp edges and angles on the surface of GCC to some extent. The flat crystal cleavage plane of the particle surface coated with the modifying agent further increases the particle size. The larger the particle size, the smaller the angle of repose between the free surface of GCC and the horizontal plane. Moreover, the friction force of spherical particles of modified GCC powder is reduced during rolling, resulting in improved fluidity of the GCC powder.
As evident from Figure 7, the surface of unmodified GCC has crystal cleavage planes with different widths, it presents irregular open layered structure with a large specific surface area and stable skeleton structure. However, after modification by the modifying agent, the angular surface and crystal cleavage surface of the GCC powder basically disappear, and the unfavorable morphological characteristics are improved (Habte et al., 2019; Shan et al., 2022; Zhao et al., 2022). As can be seen in Figures 7B,C,D, the surface of the modified GCC is coated with a layer of oily bright substance, which indicates that the modifying agent is bonded with the matrix particles. The surface of the particles becomes more rounded, and the particles adhere to each other less, resulting in a looser GCC powder. This is mainly because the molecular structure of organic matter is relatively slender, the separation distance between the GCC powder particles coated with the modifying agent is relatively large, making it difficult for them to aggregate. It is observed that TCA-201 forms a dense layer of organic matter on the surface of GCC, and sodium stearate also forms a layer of organic matter, although the surface of sodium stearate modified GCC is rough. TCA-K38S has the worst coating property, with some parts of GCC remaining incompletely coated. This can also explain why the oil absorption value and activation degree of modified GCC by sodium stearate and TCA-K38S are weaker than that of TCA-201. Based on the combined analysis of contact angle, TG-DTA and SEM, sodium stearate and TCA-201 are preferred modifying agents for preparing modified GCC asphalt mixtures, and the in-services performance of their asphalt mixtures are remained to be evaluated.
FIGURE 7. SEM picture, (A) Unmodified GCC, (B) TCA-201 modified GCC, (C) TCA-K38S modified GCC, (D) sodium stearate modified GCC.
According to the Test Methods of Aggregate for Highway Engineering (2005), the apparent density, water content, gradation, hydrophilicity coefficient, plasticity index and heating stability of ordinary mineral powder, TCA-201 modified GCC and sodium stearate modified GCC were tested and compared, and the results are presented in Table 8.
It can be seen from Table 8 that the measured physical values of GCC meet the specification requirements. The hydrophilic coefficient of TCA-201 and sodium stearate modified GCC is 0 after modification, indicating that they are hydrophobic. Therefore, when anhydrous ethanol with added water is used, the liquid limit and plastic limit of the two modified GCC powders can be detected, and the measured values are slightly larger. After adjusting the testing scheme, the plasticity index of the modified GCC powder is higher than that of the original GCC powder, but it meets the specification requirements.
Marshall stability refers to the maximum load that a specimen can withstand before failure under a load at a temperature of 60°C, and flow value refers to the deformation when the maximum load is reached. Marshall modulus can indirectly reflect the rutting resistance of asphalt concrete, where a larger Marshall modulus indicates smaller deformation, stronger resistance to external forces, higher strength of asphalt concrete, and better deformation resistance at high temperatures (Feng et al., 2019; Jahanbakhsh et al., 2020). The rutting test is commonly used to determine the high-temperature rutting resistance of asphalt concrete. The results of Marshall modulus and dynamic stability are shown in Figure 8.
As shown in Figure 8, compared with the unmodified AC-13C asphalt concrete, the Marshall modulus of TCA-201 modified AC-13C asphalt concrete and sodium stearate modified AC-13C asphalt concrete increases by 40.91% and 54.55% respectively. The dynamic stability of TCA-201 modified AC-13C asphalt concrete and sodium stearate modified AC-13C asphalt concrete is improved by 3.14 times and 2.12 times, respectively. The modified GCC has a significant positive effect on improving the high-temperature resistance of AC-13C asphalt concrete.
The high-temperature resistance of TCA-201 and sodium stearate modified AC-13C asphalt concrete has been improved to different degrees, and the modification effect of TCA-201 modified GCC is more significant than that of sodium stearate modified GCC. Analysis indicates that the activity of the two kinds of modified GCC powder has been significantly improved. Both modifying agents form a uniform and dense film that covers the surface of GCC powder. The inner side of the film reacts with various functional groups on the surface of GCC and forms a strong chemical bond, and the lipophilic outer side of the film reacts or physically entangles with the organic polymer asphalt. This results in a firm bond between the inorganic GCC powder and the organic asphalt, forming an asphalt slurry that enhances the adhesion of aggregate in asphalt concrete. The oil absorption value of the modified GCC powder is greatly reduced, leading to increased dispersion of the modified GCC powder in the asphalt mixture. This results in more evenly distributed voids in the asphalt mix and increased compactness, ultimately improving the high-temperature resistance of the asphalt concrete.
The water stability of asphalt concrete is an important performance index that affects the stability and service life of pavement structure. Immersion Marshall test and freeze-thaw splitting test were conducted to study the water stability of modified GCC asphalt concrete (Liu et al., 2019; Álvarez et al., 2020). The test results are shown in Figure 9.
It can be seen from Figure 9 that the residual stability of TCA-201 modified asphalt concrete and sodium stearate modified asphalt concrete is both increased by 2.73%, compared with the unmodified asphalt concrete. And the freeze-thaw splitting strength ratio is increased by 6.61% and 10.47%, respectively. The modified GCC powder has a significant improvement effect on the water stability of AC-13C asphalt concrete.
Furthermore, the addition of TCA-201 and sodium stearate modified GCC powder can improve the water stability as well as the physical and mechanical properties of AC-13C asphalt concrete, and the modification effect of sodium stearate is more significant than that of TCA-201. Analysis indicates that the activation degree of modified GCC powder is improved, and the immersion wetting between asphalt slurry and modified GCC powder enhances the interfacial adsorption strength. The improvement of asphalt slurry viscosity increases the thickness of structural asphalt film, effectively prevents water from entering the interface between asphalt and aggregate, thereby enhancing the anti-spalling property. In addition, the increased compactness reduces the internal gaps, the number of connected pores is reduced, resulting in improved water stability and low permeability of the asphalt concrete.
Asphalt pavement shrinkage cracks, which occur under low temperature conditions, are one of the main types of damage to asphalt pavement. The existence of shrinkage cracks not only affects the appearance of the pavement, but also may cause other the pavement issues. To study the low-temperature performance of the asphalt concrete, a low-temperature bending test was conducted (Iwanski et al., 2020; Alattieh et al., 2021). The measurement results of low-temperature bending and tensile strain are shown in Figure 10.
Figure 10 reveals that the maximum flexural tensile strain of asphalt concrete under different types of mineral powder. It can be seen that the maximum flexural tensile strain of TCA-201 modified asphalt concrete and sodium stearate modified asphalt concrete is increased by 19.18% and 26.41%, respectively, compared with the unmodified AC-13C asphalt concrete.
The cracking of asphalt pavement is primarily caused by the fracture of the contact surface between aggregates, and the strength of this contact surface between aggregates is mainly affected by the properties of asphalt slurry. Modified GCC powder with high activation degree can improve the dispersion in the asphalt slurry, and enhance the viscosity and toughness of asphalt slurry. In addition, the hydrophobic and lipophilic properties of the modified GCC powder, along with its low oil absorption value, facilitate close bonding between the asphalt and aggregate, and dispersion and transfer of stress caused by external loads. This helps to prevent cracking due to stress concentration and minimize crack expansion, resulting in improved low-temperature performance and reduced shrinkage cracks in the asphalt concrete pavement.
TCA-K38S, TCA-201 and sodium stearate were employed to prepare modified GCC, two kinds of modified GCC were preferably selected to prepare asphalt concrete and their performance were evaluated at macro and micro levels. The main results are as follows:
(1) The optimal modification scheme for TCA-201 modified GCC is a modification temperature of 80°C, modification time of 70 min, and modifying agent dosage of 2.0%. The optimal scheme for sodium stearate modified GCC is a modification temperature of 80°C, modification time of 50 min, modifying agent dosage of 2.0%. The contact Angles of TCA-201 and sodium stearate modified GCC are larger, indicating that their nature is more active.
(2) After surface modification, the median particle size (D50) of GCC and the coarse-grained particle size (D90) of GCC are increased. However, the crystal structure of GCC is not changed after modification, and the original lattice structure is still maintained. The surface of GCC has an irregular open layered structure, with a large specific surface area and stable skeleton structure. TCA-201 and sodium stearate show better coating properties than that of TCA-K38S.
(3) Compared with the unmodified AC-13C asphalt concrete, sodium stearate modified AC-13C asphalt concrete exhibits improved performance, with an increase in Marshall modulus, residual stability, freeze-thaw splitting strength ratio, and maximum flexural tensile strain by 54.55%, 2.73%, 10.47%, and 26.41% respectively. The Pavement in-service performance of sodium stearate modified AC-13C asphalt concrete is superior to that of TCA-201 modified AC-13C asphalt concrete.
The original contributions presented in the study are included in the article/supplementary material, further inquiries can be directed to the corresponding author.
ZZ: methodology, conceptualization, writing—original draft, validation. WY: supervision, project administration, validation, writing—review and editing. All authors have read and agreed to the published version of the manuscript.
The authors wish to express their sincere gratitude for the support of the Shandong Hi-Speed Group Co., Ltd.
Author ZZ was empolyed by Shandong Hi-Speed Construction Management Group Co, Ltd.
The remaining author declares that the research was conducted in the absence of any commercial or financial relationships that could be construed as a potential conflict of interest.
All claims expressed in this article are solely those of the authors and do not necessarily represent those of their affiliated organizations, or those of the publisher, the editors and the reviewers. Any product that may be evaluated in this article, or claim that may be made by its manufacturer, is not guaranteed or endorsed by the publisher.
Águila-Almanza, E., Hernández-Cocoletzi, H., Rubio-Rosas, E., Calleja-González, M., Lim, H. R., Khoo, K. S., et al. (2022). Recuperation and characterization of calcium carbonate from residual oyster and clamshells and their incorporation into a residential finish. Chemosphere 288, 132550. doi:10.1016/j.chemosphere.2021.132550
Alattieh, S. A., Al-Khateeb, G. G., and Zeiada, W. (2021). Evaluation of low-and intermediate-temperature performance of bio oil-modified asphalt binders. Sustain 13, 4039. doi:10.3390/su13074039
Alvarez, A. E., Ovalles, E., and Caro, S. (2012). Assessment of the effect of mineral filler on asphalt-aggregate interfaces based on thermodynamic properties. Constr. Build. Mat. 28, 599–606. doi:10.1016/j.conbuildmat.2011.08.089
Álvarez, D. A., Aenlle, A. A., Tenza-Abril, A. J., and Ivorra, S. (2020). Influence of partial coarse fraction substitution of natural aggregate by recycled concrete aggregate in hot asphalt mixtures. Sustain. doi:10.3390/SU12010250
Antunes, V., Freire, A. C., Quaresma, L., and Micaelo, R. (2016). Effect of the chemical composition of fillers in the filler-bitumen interaction. Constr. Build. Mat. 104, 85–91. doi:10.1016/j.conbuildmat.2015.12.042
Awed, A. M., Tarbay, E. W., El-Badawy, S. M., and Azam, A. M. (2022). Performance characteristics of asphalt mixtures with industrial waste/by-product materials as mineral fillers under static and cyclic loading. Road. Mat. Pavement Des. 23, 335–357. doi:10.1080/14680629.2020.1826347
Bahranowski, K., Klimek, A., Gaweł, A., and Serwicka, E. M. (2021). Rehydration driven na-activation of bentonite—Evolution of the clay structure and composition. Mater. (Basel) 14, 7622. doi:10.3390/ma14247622
Chen, Y., Xu, S., Tebaldi, G., and Romeo, E. (2022). Role of mineral filler in asphalt mixture. Road. Mat. Pavement Des. 23, 247–286. doi:10.1080/14680629.2020.1826351
Code of China (2011). JTG E20-2011, standard test methods of bitumen and bituminous mixtures for highway engineering. Beijing: JT Professional Standard - Transport.
Code of China (2005). JTG E42-2005, test methods of aggregate for highway engineering. China: Test Methods of Aggregate for Highway Engineering.
Curtis, C. W., Ensley, K., and Epps, J. (1993). Fundamental properties of asphalt-aggregate interactions including adhesion and absorption SHRP-A-341. Strateg. Washingt: Hiughw. Res. Progream.
Diab, A., and Enieb, M. (2018). Investigating influence of mineral filler at asphalt mixture and mastic scales. Int. J. Pavement Res. Technol. 11, 213–224. doi:10.1016/j.ijprt.2017.10.008
Feng, C., Zhang, H., li, C., Jia, W., and Lai, F. (2019). The effects of hollow glass microsphere modification on the road performances and thermal performance of asphalt binder and mixture. Constr. Build. Mat. 220, 64–75. doi:10.1016/j.conbuildmat.2019.05.183
Feng, J., Yang, F., and Qian, S. (2021). Improving the bond between polypropylene fiber and cement matrix by nano calcium carbonate modification. Constr. Build. Mat. 269, 121249. doi:10.1016/j.conbuildmat.2020.121249
Guo, M., and Tan, Y. (2021). Interaction between asphalt and mineral fillers and its correlation to mastics’ viscoelasticity. Int. J. Pavement Eng. 22, 1–10. doi:10.1080/10298436.2019.1575379
Habte, L., Shiferaw, N., Mulatu, D., Thenepalli, T., Chilakala, R., and Ahn, J. W. (2019). Synthesis of nano-calcium oxide fromwaste eggshell by sol-gel method. Sustain 11, 3196. doi:10.3390/su11113196
Han, X., Lao, Y. H., Lan, J., Tan, S. Q., Song, J. H., Cen, R. J., et al. (2022). “Preparation and characterization of starch active interface calcium carbonate for biodegration,” in Key engineering materials. doi:10.4028/www.scientific.net/KEM.905.238
Hao, X., Zhang, A., and Yang, W. (2012). “Study on the performance of nano calcium carbonate modified asphalt concrete AC-13,” in Advanced materials research. doi:10.4028/www.scientific.net/AMR.450-451.503
Iwanski, M. M., Chomicz-Kowalska, A., and Maciejewski, K. (2020). Resistance to moisture-induced damage of half-warm-mix asphalt concrete with foamed bitumen. Mater. (Basel) 13, 654. doi:10.3390/ma13030654
Jahanbakhsh, H., Karimi, M. M., Naseri, H., and Nejad, F. M. (2020). Sustainable asphalt concrete containing high reclaimed asphalt pavements and recycling agents: Performance assessment, cost analysis, and environmental impact. J. Clean. Prod. 244, 118837. doi:10.1016/j.jclepro.2019.118837
Lesueur, D., Petit, J., and Ritter, H. J. (2013). The mechanisms of hydrated lime modification of asphalt mixtures: A state-of-the-art review. Road. Mat. Pavement Des. 14, 1–16. doi:10.1080/14680629.2012.743669
Li, J., Yang, S., Liu, Y., Muhammad, Y., Su, Z., and Yang, J. (2019). Studies on the properties of modified heavy calcium carbonate and SBS composite modified asphalt. Constr. Build. Mat. 218, 413–423. doi:10.1016/j.conbuildmat.2019.05.139
Li, S., Ren, H., Wu, Q., and Ye, Y. (2020). Preparation and mechanical properties of modified magnesium oxysulfate cement incorporating alkali conditioner. Sci. Adv. Mat. 12, 1558–1567. doi:10.1166/sam.2020.3853
Liang, Y., Yu, K., Zheng, Q., Xie, J., and Wang, T. J. (2018). Thermal treatment to improve the hydrophobicity of ground CaCO 3 particles modified with sodium stearate. Appl. Surf. Sci. 436, 832–838. doi:10.1016/j.apsusc.2017.12.023
Liu, W., Li, H., Zhu, H., and Xu, P. (2019). Properties of a steel slag-permeable asphalt mixture and the reaction of the steel slag-asphalt interface. Mater. (Basel) 12, 3603. doi:10.3390/ma12213603
Nakarai, K., Shibata, M., Sakamoto, H., Owada, H., and Kosakowski, G. (2021). Calcite precipitation at cement–bentonite interface. Part 1: Effect of carbonate admixture in bentonite. J. Adv. Concr. Technol. 19, 433–446. doi:10.3151/jact.19.433
Rudawska, A., Jakubowska, P., and Kloziński, A. (2017). Surface free energy of composite materials with high calcium carbonate filler content. Polimery/Polymers 62, 434–440. doi:10.14314/polimery.2017.434
Seeharaj, P., Sripako, K., Promta, P., Detsri, E., and Vittayakorn, N. (2019). Facile and eco-friendly fabrication of hierarchical superhydrophobic coating from eggshell biowaste. Int. J. Appl. Ceram. Technol. 16, 1895–1903. doi:10.1111/ijac.13235
Shan, Z., Zhang, P., and Kou, H. (2022). Mechanical and engineering behavior of MICP-treated coarse siliceous sands. KSCE J. Civ. Eng. 26, 79–87. doi:10.1007/s12205-021-0054-5
Tarbay, E. W., Azam, A. M., and El-Badawy, S. M. (2019). Waste materials and by-products as mineral fillers in asphalt mixtures. Innov. Infrastruct. Solut. 4, 5. doi:10.1007/s41062-018-0190-z
Upadhyaya, P., Nema, A. K., Sharma, C., Kumar, V., and Agrawal, D. D. (2013). Physicomechanical study of random polypropylene filled with treated and untreated nano-calcium carbonate: Effect of different coupling agents and compatibilizer. J. Thermoplast. Compos. Mat. 26, 988–1004. doi:10.1177/0892705711433349
Valencia, G. A., and Pileggi, R. G. (2018). Aplicabilidade do método modificado de Washburn para medidas de ângulo de contato de carbonato de cálcio. Ceramica 64, 197–206. doi:10.1590/0366-69132018643702232
Xing, B., Du, Y., Fang, C., Sun, H., Lyu, Y., and Fan, W. (2022). Particle morphology of mineral filler and its effects on the asphalt binder-filler interfacial interaction. Constr. Build. Mat. 321, 126292. doi:10.1016/j.conbuildmat.2021.126292
Yu, L., Sun, S., Hao, D., and Hou, X. (2020). PREPARATION And CHARACTERIZATION Of ORGANIC MODIFIED CALCIUM CARBONATE By SODIUM STEARATE (OR SODIUM OLEATE) USING WET METHOD. Surf. Rev. Lett. 27, 1950224. doi:10.1142/S0218625X1950224X
Yuan, Z. c., wu, Z., and Chen, Q. (2019). Permeability modeling of self-healing due to calcium carbonate precipitation in cement-based materials with mineral additives. J. Cent. South Univ. 26, 567–576. doi:10.1007/s11771-019-4028-4
Keywords: modified ground calcium carbonate, modification mechanism, microscopic characterization, performance evaluation, asphalt concrete
Citation: Zhang Z and Yan W (2023) Modified ground calcium carbonate mineral powder using in asphalt concrete: modification mechanism characterization at macro and micro levels. Front. Mater. 10:1195428. doi: 10.3389/fmats.2023.1195428
Received: 28 March 2023; Accepted: 12 April 2023;
Published: 24 April 2023.
Edited by:
Derun Zhang, Huazhong University of Science and Technology, ChinaReviewed by:
Yuanyuan Li, Wuhan Institute of Technology, ChinaCopyright © 2023 Zhang and Yan. This is an open-access article distributed under the terms of the Creative Commons Attribution License (CC BY). The use, distribution or reproduction in other forums is permitted, provided the original author(s) and the copyright owner(s) are credited and that the original publication in this journal is cited, in accordance with accepted academic practice. No use, distribution or reproduction is permitted which does not comply with these terms.
*Correspondence: Wenda Yan, MTUyODg4NzQ0ODdAMTI2LmNvbQ==
Disclaimer: All claims expressed in this article are solely those of the authors and do not necessarily represent those of their affiliated organizations, or those of the publisher, the editors and the reviewers. Any product that may be evaluated in this article or claim that may be made by its manufacturer is not guaranteed or endorsed by the publisher.
Research integrity at Frontiers
Learn more about the work of our research integrity team to safeguard the quality of each article we publish.