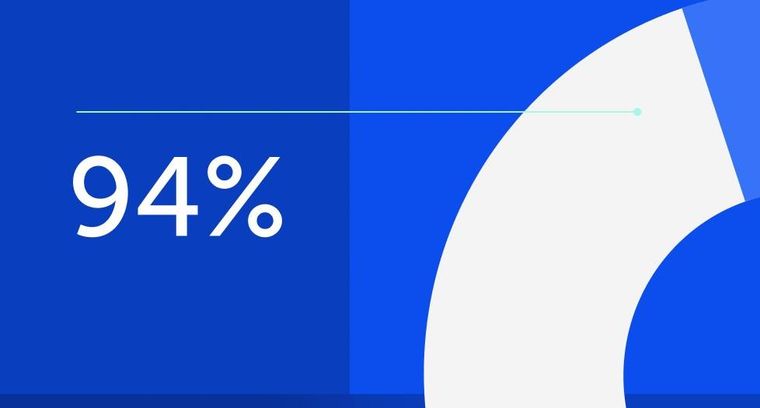
94% of researchers rate our articles as excellent or good
Learn more about the work of our research integrity team to safeguard the quality of each article we publish.
Find out more
ORIGINAL RESEARCH article
Front. Mater., 03 July 2023
Sec. Polymeric and Composite Materials
Volume 10 - 2023 | https://doi.org/10.3389/fmats.2023.1185215
This investigation is primarily concerned with the effect of fly ash, basalt powder, and tungsten carbide (WC) on the mechanical, microstructural, and tribological behaviour of areca fiber-reinforced composites. The fillers (5–10 wt. %) were included with the areca fiber epoxy reinforced composites. In comparison to areca fiber composites without fillers, the inclusion of fly ash, basalt powder, and WC increased the tensile strength by 33–48.2 MPa. The tensile strength of an A2 composite containing areca fiber (20 wt. %), epoxy (70 wt. %) and basalt powder (10 wt. %) was measured to be 48.2 MPa. Similarly, filler incorporation enhanced flexural, impact, and Shore D hardness properties by up to 21.25%, 13.18%, and 15.66%, respectively. Furthermore, the hybridization of fillers enhanced the mechanical properties and abrasion resistance of areca fiber reinforced composites. The inclusion of filler increases the load-carrying capability and adhesion, as determined by SEM. The river-like pattern demonstrates that ductile failure was dominated in the A5 [areca fiber (20 wt. %), epoxy (70 wt. %), fly ash (5 wt. %) and basalt powder (5 wt. %)] composites. A4 [areca fiber (20 wt. %), epoxy (70 wt. %), fly ash (5 wt. %) and tungsten carbide (5 wt. %)] composite has a lower wear resistance than all other composites. The hybrid filler-reinforced composite exhibits increased wear resistance as a result of the absence of wear detritus and textured surfaces.
Composites of synthetic fiber-reinforced polymer were used in aerospace and vehicle applications. Although possessing strong mechanical qualities and a higher resilience to environmental ageing, these fiber composites are both environmentally and socially dangerous. Researchers are currently using natural fibers as reinforcement for polymer-based composites. Natural fibers are preferable to synthetic fibers because they are durable, biodegradable, inexpensive, and lightweight (Ganapathy et al., 2021). These fibers are excellent for use as reinforcement materials in the production of polymer composites that are suited for a variety of lightweight applications, including structural and automobile (Sanjay et al., 2016; Sanjay et al., 2018). The limitations of natural fiber-reinforced composites are fiber delamination, low modulus, water absorption, and inadequate application to low load-bearing materials (Ahmad et al., 2020). Using various polymer resin matrixes, natural fibers such ramie, cotton, sisal, kenaf, banana, and pineapple have been employed (Mittal et al., 2016; Nguyen et al., 2019; Sumesh et al., 2022). It is confirmed that hemp, ramie, flax, and cotton have higher costs than any other fibers, yet they do not offer significant mechanical benefits (Ashok et al., 2020). In the majority of works on natural fiber composites, numerous researchers have examined the various plant fiber components. Several researchers have made studies on various components (stem fibers, sheath fiber, fruit husk, and root) of various palms such as date palm, coconut palm, and areca palm (Ashok et al., 2020). Areca appears to be one of the most promising natural fiber-reinforcing materials due to the fact that it is affordable, widely available, and a perennial crop with a high yield potential (Srinivasa and Bharath, 2011). The type of the fiber-matrix bond is mainly responsible for determining the qualities of areca fibers. The effect of alkali treated on the mechanical behavior of areca fiber-reinforced composites was investigated by (Shanmugasundaram et al., 2018). (Muralidhar et al., 2019) studied the tensile properties of coarse areca fiber, fine areca fiber sandwiched with glass fiber. The tensile strength of coarse fiber was less than the fine fiber. Subhakanta Nayak et al. (Nayak and Mohanty, 2019) found that mechanical properties of the polyvinyl alcohol thermoplastic matrix short areca sheath fiber. The highest mechanical properties were found in the 27 wt% of areca fiber polynvinyl alcohol reinforced composites. (Pavankalyan et al., 2018) studied the mechanical and thermal properties of areca fiber reinforced polypropylene polymer composites. Due to poor fiber-matrix adhesion, increased fiber content lowered mechanical characteristics. (ChikkolVenkateshappa et al., 2010) found that the flexural strength of potassium hydroxide-treated areca fiber-reinforced composites increased with different fiber weight percentages. (Srinivasa et al., 2011) found that the flexural and impact strength of the areca fiber-reinforced epoxy composites increased with an increase in the fiber loading percentage. (Srinivasa and Bharath, 2011) pure polynvinyl alcohol exhibits the maximum erosion rate at 30° impact angle, while polynvinyl alcohol/areca composites have the maximum erosion rate at 45° impact angle, regardless of fiber loading, indicating semi-ductile behaviour. Most of the researchers studied the effect of fiber treatment on mechanical and wear properties of areca fiber polymer composites.
The majority of research works on natural fiber composites have focused on the effect of fiber treatment (ChikkolVenkateshappa et al., 2010; Pavankalyan et al., 2018; Shanmugasundaram et al., 2018; Muralidhar et al., 2019; Nayak and Mohanty, 2019), fiber arrangement (Nayak and Mohanty, 2019), and varying fiber loading percentages (Srinivasa et al., 2011). However, there are very few investigations that have been conducted on the use of fillers to reinforce natural fiber composites. Although there is an extensive literature on the use of organic and inorganic fillers in composite materials, the effect of hybridization of fillers on areca fiber composites has not been reported. This study aimed to investigate the influence of organic fillers (fly ash and basalt powder) and inorganic fillers (WC) on the tensile, flexural, impact, and hardness properties of areca fiber-epoxy reinforced composites. The objective of this research is to promote the potential use of areca fiber as a material for various non-structural applications.
Areca fiber was procured from Vruksha Composites in Chennai, India and used as reinforcement. Prior to processing, these fibers were soaked for 24 h at room temperature in a 6% NaOH solution to strengthen the interfacial adhesion between the fiber and matrix, which enhanced the mechanical properties (Dhanalakshmi et al., 2017). These fibers were then cleaned with distilled water and dried in a warm oven set at 70°C. The dried fibers were cut into lengths of 150–200 mm and utilized to create composite materials. Both the hardener (HY951) and epoxy resin (LY556) were bought from Covai Seenu & Company in Coimbatore, India. The fly ash was collected from the power plant and it was ground using ball milling machine. The WC and basalt powder was purchased from Ultrananotech Private Limited and pramod marbles and stone industries, India. Figure 1 depicts the procedures used for filler dispersion and composite fabrication. The filler and acetone were combined for 15 min with a magnetic stirrer and 15 min with a probe sonicator. This mixing technique was carried out extensively after adding enough epoxy resin. Epoxy and filler were blended with the hardener at the end. To prevent the mixture from sticking to the mould, non-silicone white wax was put within the mould. The fiber was placed in the mould of the compression moulding machine after the wax had been applied. The mould was filled with a mixture of epoxy, filler, and hardener. Pressure (12 MPa) and temperature (120°C) were the operational parameters employed in this investigation to manufacture all composite materials.
All six samples were prepared using the same method, and the specifics of each sample are provided in Table 1. The composite plates were sliced for mechanical testing once the composites were dried.
All mechanical testing samples were cut using a water jet cutting machine in adherence to the ASTM standard. UsingAimil universal testing equipment, the tensile and flexural strengths of each sample were tested in accordance with ASTM D-3039 and ASTM D790-07, respectively. The impact resistance of the samples was determined using a digital Izod impact tester in accordance with ASTM D-256. Shore D hardness testing was conducted in accordance with ASTM D2240 using a Shore D hardness tester. The dry wear test was conducted using pin-on-disc equipment (DUCOM machine) in accordance with ASTM G99 specifications. The samples measured 15 mm, 5 mm, 5 mm, and were placed perpendicular into an EN-32 steel disc with a 50 mm track diameter. Using scanning electron microscopy, the tensile fracture and worn surfaces were studied (SEM).
The composite samples following the tensile and flexural test are shown in Figure 2. Figure 3 shows the stress vs. strain curve of all six areca fiber composites.
Figure 4 depicts the results of the evaluation of the tensile and flexural strengths of several areca fiber polymer composites. Without the addition of filler materials, the tensile strength of the areca fiber epoxy reinforced composites was 32 MPa (Ashok et al., 2018).
However, the inclusion of fly ash, basalt powder, and WC fillers to the areca fiber epoxy-reinforced composites improved their tensile strength in comparison to those without fillers. The highest tensile strength of 48.2 MPa was observed for A5 composites having 5 wt% fly ash and 5 wt% basalt powders, which increased nearly 33.60% compared to those without filler areca fiber polymer composites. Least tensile strength was noticed in the A1 and A3 composites compared to the other composites. The A3 exhibited the lowest tensile strength among all other materials. Due to insufficient wetting of WC during tensile loading, the interfacial adhesion between areca fibers and matrix was weakened, resulting in a lower tensile strength. Similar effects were observed in sisal-reinforced epoxy composites (Singh et al., 2021). Inadequate mixing of fly ash and WC may cause for the reduced strength in comparison to basalt powder. A2 (10 wt% basalt powder) had a tensile strength that was 25.49% and 30.01% higher than the A1 and A3 composites, respectively. The combined effect of two fillers in reinforced composites (A4, A5, and A6) increased tensile strength in comparison to single filler reinforced composites (A1 and A3). However, it was less than the A2-composites. Despite the presence of two fillers in areca fiber reinforced composites, basalt powder predominated, followed by fly ash and WC. The fly ash with WC (A4) composites showed the second highest tensile strength. The addition of fly ash filler to the basal (A4) shows a significant improvement in the tensile strength as compared to composites (WC + basalt powder). During composite tensile testing, it was observed that the WC filler does not maintain effective load transfer (Singh et al., 2021). In this investigation, basalt powder was the most efficient filler compared to the other fillers used in this study. As the proportion of cationic surfactant increases, the possibility of fly ash and WC fillers agglomerating reduces due to repulsion. Inorganic also fills the matrix’s meso and microvoids, enhancing the composites’ superior packing.
The tensile modulus of each composite are calculated from the stress-strain curve of each composites. Tensile modulus of the areca fiber composites are shown in Table 2. The tensile modulus of the A5 composite was high compare to all other composites.
The flexural strength of different areca fiber-reinforced composites are illustrates in Figure 4. The flexural strength of areca fiber-reinforced composites without any filler was 60 MPa (Ashok et al., 2018). The results demonstrate conclusively that fly ash, basalt powder, and WC increased the flexural strength of areca fiber composites. A5 composite was shown to have a superior flexural strength of 76.2 MPa, which is approximately 21.25% higher than composites without filler material. Composites A2 and A6 exhibited the second-highest flexural strength. The composites reinforced with fly ash (A1) and WC (A3) had the lowest flexural strength. The improved load transfer and elastic deformation of the composite was attributed to the increased interfacial stiffness and better adherence of fly ash powder at smaller particle sizes (Senthilkumar et al., 2018). Hence; it was the major reason for the lower flexural strength of the fly filler reinforced composites. In addition to this, the WC with fly ash and basalt powder in the composites also reduced the flexural strength. The accumulation of WC makes the composite more brittle, and it reduces the stiffness of the areca fiber. (Srinivasa et al., 2011) found that the flexural strength of the areca fiber composites is enhanced by increasing the weight fraction of areca fiber. The basalt powder filler enhanced the composite’s flexural strength in comparison to other fillers. In addition to other fillers, the filler increased the composite’s flexural strength. Basalt powder effectively bonds areca fiber with epoxy resin at their interfaces. (Vivek and &Kanthavel, 2019) observed a similar effect, in which the flexural strength of basalt powder-reinforced natural fiber composites was totally dependent on the filler’s adhesion to the fiber and matrix. Good interfacial bonding between the filler, areca fiber, and epoxy resin was primarily responsible for the composite’s retained rigidity.
The Izod impact test specimens and results of areca fiber-reinforced composites with various fillers are shown in Figures 5A, B. The results clearly demonstrate that, in comparison to composites without the inclusion of filler, the presence of fillers improved the impact strength of the composites. (Ashok et al., 2018) found that the impact strength of areca fiber-reinforced composites without fillers was 11J. A4 and A5 composites demonstrated maximum impact strengths of 16.11J–15.34J, which is 31.719%–28.29% higher than the composites without filler. Composites with single filler (A1, A2, and A3) possessed lower impact strength than composites with two fillers (A4 and A5). A1 and A2 composites showed the inferior impact strength compared to other composites. A1, A2, A3, A4, A5, A6 improved their impact strengths by 9.3%, 23.29%, 20.058%, 31.71%, 28.29%, and 22.37%, respectively. Generally, voids occur during the production of composites reinforced with natural fibers (Singh et al., 2021). These voids can increase stress and accelerate up the growth and development of cracks. Fillers effectively inhibit crack formation and propagation in areca fiber-reinforced composites by effectively filling these voids.
Fillers can serve as a good bond between the fiber and the matrix, which increases interfacial bonding and contributes to the enhancement of impact strength. The inclusion of fillers helps to fill the composite’s voids. However, this helps to delay the formation and development of micro cracks. The increase in impact resistance may be attributable to the fact that fillers absorb energy due to their higher surface-to-volume ratio (Singh et al., 2021). The decrease in impact strength in A1 was due to inadequate agglomeration and wetting.
Figure 6 depicts the influence of fillers on the Shore D hardness of areca fiber-reinforced composites. The Shore D hardness of the areca fiber-reinforced composite was 70 (Rajakumar et al., 2022). The inclusion of filler materials such as fly ash, basalt powder, and WC to the composite strengthened its hardness properties as compared with areca fiber composites without filler. With the inclusion of fillers, the polymer and fiber links are kept in position, hence increasing the stiffness and hardness of the composite. It was noticed that, over composites without filler, the average Shore D hardness was increased by 12.5 % (A1), 19.54 % (A2), 10.2 % (A3), 18.6% (A4), 15.6% (A5), and 13.5% (A6) for composites with filler added composites. Comparing basalt-reinforced composite to fly ash and WC, a considerable improvement was seen. Improper dispersion of WC fillers at low loading led to an increase in inter-particle distance, which was the major cause of the A3 lower hardness.
The slight decrease in hardness was noticed in the A4, A5, and A6 composites compare to the A2 composites. It was due to filler heterogeneities and void content. (Jothibasu et al., 2018; Padmaraj et al., 2018) showed comparable increases in hardness values for areca fiber reinforced composites.
In this work, pin-on disc equipment was used to conduct the dry wear test. Figure 7 shows that when normal load and sliding velocity increase, the wear rate dramatically rises for all areca fiber composites. By subjecting the specimens to the corresponding normal load and sliding velocity of 15, 25, and 35 N and 120, 240, and 360 rpm, the wear test was carried out, respectively.
The major operational parameters for the wear of polymer composites were the applied load and sliding speed. In order to vary it, a set sliding distance of 500 m was used. For each combination, about three specimens were evaluated, and the average value was noted. At all combinations of normal loads and sliding velocity, the wear rate for A1 composites continues to be the highest, whereas the wear rate for A4 composites continues to be the lowest. At 35 N load and 360 rpm speed, the A1 composite had the maximum wear rate (1,495 µm). A4 composite showed the least wear rate (132 µm) at 15 N load at 120 rpm. According to the normal load, the wear rate of A4 remains between 132 mm and 318 mm at lower sliding velocity (120 rpm), and between 408 μm and 965 μm at higher sliding velocity (360 rpm) (15 N–35 N). The WC with fly ash fillers strongly incorporated the areca fiber epoxy matrix interphase, resulting in transfer layers on the material surface that decreased wear resistance under all loading conditions. Govindan et al. (Govindan et al., 2022) reported similar kinds of findings. Next to A4, the least wear rate was noticed in the A5 composites at lower sliding velocity (120 rpm) irrespective normal load. However, at greater sliding velocity and normal loads, A2 had a lower wear rate compared to A5. It was shown that at increasing loading conditions, the A2 composite’s wear behaviour gradually decreased. The increase in contact area and decreased abrasion resistance of fly ash were the main causes of the A5 composite’s decreased wear resistance under higher loading conditions (Renukappa et al., 2011).
The wear rate of composites A2, A5, and A6 ranges from 1,002 m to 1,092 m. The basalt powder was added to composites A2, A5, and A6. However, the composite material A2 had a superior wear rate to A5 and A6. The minor increase in wear resistance of A5 and A6 was due to the hybridization of the filler material. A1 composites had the highest wear rate regardless of the loading circumstances. The use of fly ash filler in A1 composites decreases their abrasion resistance. This may be the result of an increase in the actual contact area of the resin and an appropriate filler concentration in the frictional composition. Fly ash has a lower abrasion resistance than WC and basalt powder. From the wear data, it was determined that filler materials can reduce the stress on sisal fibers and avoid thermal and mechanical breakdown of the matrix in the contact region.
Figures 8A–D depicts the SEM fracture surfaces of the tensile samples A1, A3, A4, and A5 of areca fiber reinforced composites. Fiber tear and breakage are observed in the A1 and A3fracture surface (Figures 8A, B). Even though there was no crack, the decrease in tensile strength was caused predominantly by the presence of voids and fiber tear on the fracture surfaces. The river like pattern was noticed A1 confirms the failure is mixed mode failure (ductile and brittle). The adhesion between fiber and matrix was good in the A4 sample, which was confirmed by the fiber breakage on the fracture surface. A4 composites have a higher load carrying capacity than A1 and A3 composites, as evidenced by the absence of fiber tear and voids. The fracture surfaces of the A4 samples have the pattern that likes a river (Figure 8C). The presence of a river-like pattern indicates that the failure was dominated by the ductile. Similar failure was seen in composites containing graphene-filled banyan aerial root fibers (Ganapathy et al., 2021). The existence of a river pattern on the fracture surface demonstrates that the matrix cohesion of the A4 specimens was superior. Hence, it was the reason for higher tensile strength as compare to A1, A3 and A4 composites.
The A1 composite exhibits cracks, grooved surfaces, and wear debris (Figure 9A). It shows that a larger surface was worn as a result of a greater wear rate. It indicates that a larger surface was worn because the rate of wear was greater. The wear debris and cracks are seen in the A2 composites (Figure 9B). There is cracks on the worn surfaces, which increases the wear rate of the A2 sample. (Sumesh et al., 2022) observed a similar kind of crack formation in oil cake filler-added natural fiber epoxy composites. The crack formation in A2 was less compare to A1. It is likely that a protective layer is formed as a result of the layer’s ability to give a more uniform distribution of contact stresses with a lower magnitude, resulting in less wear as compared to A1. The worn surface of A3 composite (Figure 9C) was similar surfaces of A1 and A2 composites. However, wear debris and cracks are seen large in portion as compared to A2. This clearly demonstrated that WC filler’s binding to the epoxy resin was superior to that of the other two fillers. The addition of WC filler to the areca fiber epoxy composite performed better under the higher operating wear conditions as compared to fly ash and basalt powder. (Singh et al., 2021) reported that as the normal load and sliding speed increased, surface distortion of sisal fiber composites increased during dry wear.
Figure 9D shows the worn surface of A4 composites. In comparison to fly ash, the influence of WC on the A4 composite during high loading circumstances was greater. The growth of scaling layers and the absence of cracks and wear debris confirmed this conclusion. The combination of fly ash with WC enhanced the wear resistance of the areca fiber composites, especially in higher loading conditions. From the worn surface, it was confirmed that during wear, both fillers prevented the matrix contact area from thermal and mechanical failures. The worn surface of A5 composites (Figure 9E) exhibits surface cracks and wear debris. During high loading conditions, the influence of basalt powder in the A5 composite was high compared to fly ash. As illustrated in Figure 9F, the worn surface pattern of the A6 is comparable to that of the A4. Wear debris and cracks was not seen in the A6 specimens. However, grooved surfaces were not noticed in the SEM images of A6 specimens. Chang and Friedrich (Chang et al., 2014) observed a similar type of worn surface in titanium oxide filler reinforced composites. It was confirmed that both fillers prevented thermal and mechanical failures in the matrix contact area during wear. Consequently, the wear rate of A6 composites was lower than other A1, A2, A3, and A5 composites. The wear rate was slightly higher than the A4 composites.
All in all, “Areca-fiber epoxy composites reinforced with fillers” have a wide range of applications due to their excellent mechanical, morphological, and tribological properties. The addition of fillers enhances the properties of the composites, making them suitable for a variety of industrial applications. This article explores the applications of areca fiber epoxy composites reinforced with various fillers, based on recent research studies.
i. Automotive Industry: areca fiber epoxy composites reinforced with various fillers can be used in the automotive industry for the manufacturing of lightweight components. These composites have remarkable mechanical characteristics like,” higher tensile strength,” “higher modulus of elasticity,” and “lower density,” making them an ideal choice for the manufacturing of automotive parts such as bumpers, spoilers, and dashboard components. The use of these composites can significantly reduce the weight of the vehicle, resulting in improved fuel efficiency.
ii. Aerospace Industry: areca fiber epoxy composites reinforced with various fillers can also be used in the aerospace industry. The composites’ lightweight nature and excellent mechanical properties make them suitable for manufacturing aircraft components such as wings, fuselage, and tail sections. The use of these composites in the aerospace industry can result in improved fuel efficiency and reduced carbon emissions.
iii. Construction Industry: areca fiber epoxy composites reinforced with various fillers can also be used in the construction industry. These composites have superior mechanical characteristics like “higher tensile strength,” and “lower thermal expansion,” making them ideal for construction applications such as roofing, flooring, and wall panels. The use of these composites in the construction industry can result in reduced construction time and improved durability.
iv. Packaging Industry: the fabricated polymeric composites can also be used in the packaging industry for the manufacturing of packaging materials. These composites have superior mechanical characteristics like, “higher tensile strength,” and “lower water absorption,” making them an ideal choice for manufacturing packaging materials such as boxes, trays, and containers.
v. Sporting Goods Industry: Areca fiber epoxy composites reinforced with various fillers can also be used in the sporting goods industry. These composites have splendid “physicomechanical characteristics” like, “higher tensile strength,” and “lower density,” making them an ideal choice for manufacturing sporting-goods including,“golf clubs,” “tennis rackets,” and “bicycle frames.”
Hence, the fabricated composites have a broader-spectrum of applications in various industries owing to their excellent physicomechanical, morphological, and tribological characteristics. The addition of fillers enhances the characteristics of the composites, making them suitable for a variety of industrial applications. The continued development and research of developed composites will likely result in the discovery of new applications and further expand their industrial use.
The areca fiber composites were included with fly ash, basalt powder, and WC using the compression moulding process, following mechanical and wear results. The mechanical and wear properties of fly ash, basalt, and WC filler powders combined with areca fiber were superior.
i. The highest tensile strength of 48.2 MPa was noticed in the hybrid filler reinforced areca fiber composite and the lowest tensile strength of 33 MPa was observed in the fly ash filler reinforced composites. The tensile strength of the hybrid filler added composite was higher than that of the single filler added composite.
ii. Similarly, flexural strength increased by 5.06%, 20.21%, 6.54%, 19.13%, 21.25%, and 6.25% with fly ash, basalt powder, WC, fly ash + WC, fly ash + basalt, and WC + basalt, respectively. The hybrid filler-substituted (fly ash + basalt) sisal fiber composite was shown to have improved flexural strength.
iii. With the addition of fly ash and WC, the maximum impact resistance reached 16.11 J. Composite with fly ash as filler exhibited the lowest impact strength.
iv. The Shore D hardness of composites with filler was increased by 12.5% (fly ash), 19.544% (basalt), 10.25% (WC), 18.6% (fly ash + WC), 19.544% (fly ash + basalt), and 13.58% (WC + basalt).
v. The A4 (fly ash + WC) composite has a lower wear resistance than all other composites.
vi. SEM fractography of tensile samples exhibited the river pattern, fiber breakage, fiber tear, and pull out, indicating that the addition of filler improved bonding and that ductile failure dominated the tensile failure.
vii. Composites with a lower wear resistance exhibited more cracks and wear debris surfaces (A1).
The original contributions presented in the study are included in the article/supplementary material, further inquiries can be directed to the corresponding authors.
Conceptualization, PM, SM, SD, and SS; methodology, PM, SM, SD, and SS; formal analysis, PM, SM, SD, and SS; investigation, PM, SM, SD, and SS; writing—original draft preparation, PM, SM, SD, and SS; writing—review and editing, SS, AK, BS, and SU; supervision, SS, AK, BS, and SU; project administration, SS, BS, and SU; funding acquisition, SS, BS, and SU. All authors contributed to the article and approved the submitted version.
This study received funding from King Saud University, Saudi Arabia through researchers supporting project number (RSP2023R145). Additionally, the APCs were funded by the King Saud University, Saudi Arabia through researchers supporting project number (RSP2023R145).
The authors would like to thank King Saud University, Riyadh, Saudi Arabia, with researchers supporting project number RSP2023R145.
The authors declare that the research was conducted in the absence of any commercial or financial relationships that could be construed as a potential conflict of interest.
All claims expressed in this article are solely those of the authors and do not necessarily represent those of their affiliated organizations, or those of the publisher, the editors and the reviewers. Any product that may be evaluated in this article, or claim that may be made by its manufacturer, is not guaranteed or endorsed by the publisher.
Ahmad, F., Yuvaraj, N., and Bajpai, P. K. (2020). Effect of reinforcement architecture on the macroscopic mechanical properties of fiberous polymer composites: A review. Polym. Compos. 41 (6), 2518–2534. doi:10.1002/pc.25666
Ashok, R. B., Srinivasa, C. V., and Basavaraju, B. (2020). Study on morphology and mechanical behavior of areca leaf sheath reinforced epoxy composites. Adv. Compos. Hybrid Mater. 3, 365–374. doi:10.1007/s42114-020-00169-x
Ashok, R. B., Srinivasa, C. V., and Basavaraju, B. (2018). A review on the mechanical properties of areca fiber reinforced composites. Sci. Technol. Mater. 30 (2), 120–130. doi:10.1016/j.stmat.2018.05.004
Chang, L., Friedrich, K., and Ye, L. (2014). Study on the transfer film layer in sliding contact between polymer composites and steel disks using nanoindentation. J. Tribol. 136 (2). doi:10.1115/1.4026174
ChikkolVenkateshappa, S., Bennehalli, B., Kenchappa, M. G., and Ranganagowda, R. P. G. (2010). Flexural behaviour of areca fibers composites. BioRes 5 (3), 1846–1858.
Dhanalakshmi, S., Ramadevi, P., and Basavaraju, B. (2017). A study of the effect of chemical treatments on areca fiber reinforced polypropylene composite properties. Sci. Eng. Compos. Mater. 24 (4), 501–520. doi:10.1515/secm-2015-0292
Ganapathy, T., Sathiskumar, R., Sanjay, M. R., Senthamaraikannan, P., Saravanakumar, S. S., Parameswaranpillai, J., et al. (2021). Effect of graphene powder on banyan aerial root fibers reinforced epoxy composites. J. Nat. Fibers 18 (7), 1029–1036. doi:10.1080/15440478.2019.1675219
Govindan, P., Arul Jeya Kumar, A., and Lakshmankumar, A. (2022). Wear and morphological analysis on basalt/sisal hybrid fiber reinforced poly lactic acid composites. J. Mater. 236 (5), 1053–1066. doi:10.1177/14644207211067657
Jothibasu, S., Mohanamurugan, S., and Vinod, A. (2018). Influence of chemical treatments on the mechanical characteristics of areca sheath-flax fibres based epoxy composites. Rasayan J. Chem. 11 (3), 1255–1262. doi:10.31788/rjc.2018.1133096
Mittal, V., Saini, R., and Sinha, S. (2016). Natural fiber-mediated epoxy composites–a review. Compos. Part B Eng. 99, 425–435. doi:10.1016/j.compositesb.2016.06.051
Muralidhar, N., Kaliveeran, V., Arumugam, V., and Srinivasula Reddy, I. (2019). A study on areca nut husk fibre extraction, composite panel preparation and mechanical characteristics of the composites. J. Institution Eng. (India) Ser. D 100, 135–145. doi:10.1007/s40033-019-00186-1
Nayak, S., and Mohanty, J. R. (2019). Study of mechanical, thermal, and rheological properties of areca fiber-reinforced polyvinyl alcohol composite. J. Nat. Fibers 16 (5), 688–701. doi:10.1080/15440478.2018.1432000
Nguyen, H., Jamali Moghadam, M., and &Moayedi, H. (2019). Agricultural wastes preparation, management, and applications in civil engineering: A review. J. Material Cycles Waste Manag. 21 (5), 1039–1051. doi:10.1007/s10163-019-00872-y
Padmaraj, N. H., Keni, L. G., Chetan, K. N., and Shetty, M. (2018). Mechanical characterization of areca husk-coir fiber reinforced hybrid composites. Mater. Today Proc. 5 (1), 1292–1297. doi:10.1016/j.matpr.2017.11.214
Pavankalyan, S., Christu Paul, R., and Kamalakannan, K. (2018). Experimental Investigation of areca fiber reinforced polypropylene polymer composite for automotive components. Int. J. Pure Appl. Math. 118 (24).
Rajakumar, I., Raguraman, D., Isaac, J. S., Suthan, R., Bhattacharya, S., Seikh, A. H., et al. (2022). Mechanical properties of polymer composites reinforced with alkaline-treated natural fibre. Adv. Polym. Technol. 2022, 1–7. doi:10.1155/2022/1458547
Renukappa, N. M., Suresha, B., Devarajaiah, R. M., and Shivakumar, K. N. (2011). Dry sliding wear behaviour of organo-modified montmorillonite filled epoxy nanocomposites using Taguchi’s techniques. Mater. Des. 32 (8-9), 4528–4536. doi:10.1016/j.matdes.2011.03.028
Sanjay, M. R., Arpitha, G. R., Naik, L. L., Gopalakrishna, K., and Yogesha, B. (2016). Applications of natural fibers and its composites: An overview. Nat. Resour. 7 (3), 108–114. doi:10.4236/nr.2016.73011
Sanjay, M. R., Madhu, P., Jawaid, M., Senthamaraikannan, P., Senthil, S., and Pradeep, S. (2018). Characterization and properties of natural fiber polymer composites: A comprehensive review. J. Clean. Prod. 172, 566–581. doi:10.1016/j.jclepro.2017.10.101
Senthilkumar, K., Saba, N., Rajini, N., Chandrasekar, M., Jawaid, M., Siengchin, S., et al. (2018). Mechanical properties evaluation of sisal fibre reinforced polymer composites: A review. Constr. Build. Mater. 174, 713–729. doi:10.1016/j.conbuildmat.2018.04.143
Shanmugasundaram, N., Rajendran, I., and Ramkumar, T. (2018). Characterization of untreated and alkali treated new cellulosic fiber from an Areca palm leaf stalk as potential reinforcement in polymer composites. Carbohydr. Polym. 195, 566–575. doi:10.1016/j.carbpol.2018.04.127
Singh, T., Gangil, B., Ranakoti, L., and Joshi, A. (2021). Effect of silica nanoparticles on physical, mechanical, and wear properties of natural fiber reinforced polymer composites. Polym. Compos. 42 (5), 2396–2407. doi:10.1002/pc.25986
Srinivasa, C. V., Arifulla, A., Goutham, N., Santhosh, T., Jaeethendra, H. J., Ravikumar, R. B., et al. (2011). Static bending and impact behaviour of areca fibers composites. Mater. Des. 32 (4), 2469–2475. doi:10.1016/j.matdes.2010.11.020
Srinivasa, C. V., and Bharath, K. N. (2011). Impact and hardness properties of areca fiber-epoxy reinforced composites. J. Mater. Environ. Sci. 2 (4), 351–356.
Sumesh, K. R., Kavimani, V., Rajeshkumar, G., Ravikumar, P., and Indran, S. (2022). An investigation into the mechanical and wear characteristics of hybrid composites: Influence of different types and content of biodegradable reinforcements. J. Nat. Fibers 19 (8), 2823–2835. doi:10.1080/15440478.2020.1821297
Keywords: areca fibers, epoxy resin, mechanical properties, wear, fracture
Citation: Miniappan PK, Marimuthu S, Dharani Kumar S, Sharma S, Kumar A, Salah B and Ullah SS (2023) Exploring the mechanical, tribological, and morphological characteristics of areca fiber epoxy composites reinforced with various fillers for multifaceted applications. Front. Mater. 10:1185215. doi: 10.3389/fmats.2023.1185215
Received: 13 March 2023; Accepted: 20 June 2023;
Published: 03 July 2023.
Edited by:
Brahim Aissa, MPB Technologies and Communications, CanadaReviewed by:
Senthilkumar Krishnasamy, King Mongkut’s University of Technology North Bangkok, ThailandCopyright © 2023 Miniappan, Marimuthu, Dharani Kumar, Sharma, Kumar, Salah and Ullah. This is an open-access article distributed under the terms of the Creative Commons Attribution License (CC BY). The use, distribution or reproduction in other forums is permitted, provided the original author(s) and the copyright owner(s) are credited and that the original publication in this journal is cited, in accordance with accepted academic practice. No use, distribution or reproduction is permitted which does not comply with these terms.
*Correspondence: S. Marimuthu, ZHJzbWFyaW11dGh1QGdtYWlsLmNvbQ==; S. Dharani Kumar, c2RoYXJhbmlrdW1hcm1lY2hAZ21haWwuY29t; Shubham Sharma, c2h1YmhhbTU0M3NoYXJtYUBnbWFpbC5jb20=, c2h1YmhhbXNoYXJtYWNzaXJjbHJpQGdtYWlsLmNvbQ==; Syed Sajid Ullah, c3llZC5zLnVsbGFoQHVpYS5ubw==
Disclaimer: All claims expressed in this article are solely those of the authors and do not necessarily represent those of their affiliated organizations, or those of the publisher, the editors and the reviewers. Any product that may be evaluated in this article or claim that may be made by its manufacturer is not guaranteed or endorsed by the publisher.
Research integrity at Frontiers
Learn more about the work of our research integrity team to safeguard the quality of each article we publish.