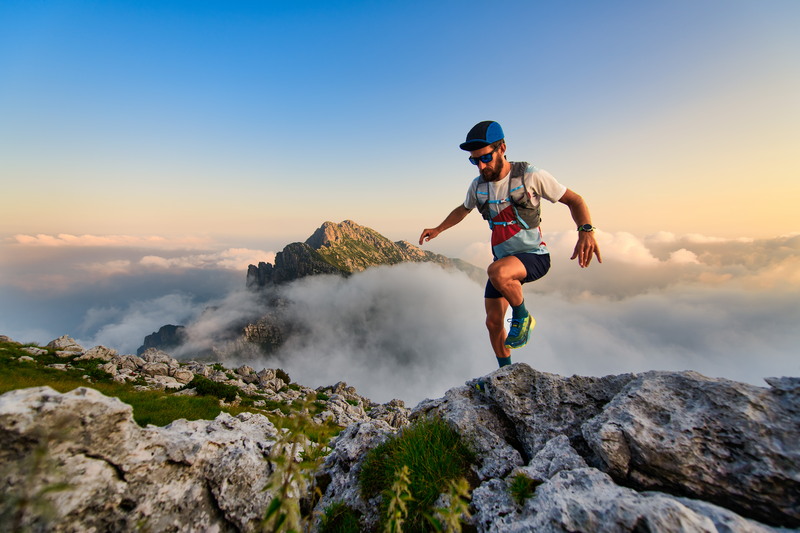
94% of researchers rate our articles as excellent or good
Learn more about the work of our research integrity team to safeguard the quality of each article we publish.
Find out more
ORIGINAL RESEARCH article
Front. Mater. , 22 June 2023
Sec. Mechanics of Materials
Volume 10 - 2023 | https://doi.org/10.3389/fmats.2023.1178518
This article is part of the Research Topic Innovators in Mechanics of Materials View all 7 articles
Introduction: This investigation explores the heat and mass transfer properties of a non-Newtonian nanofluid containing graphene nano-powder and ethylene glycol during peristalsis. The rheological characteristics of the nanofluid are determined using the Carreau-Yasuda model, and various factors such as viscous dissipation, Lorentz force, Ohmic heating, and Hall effects are taken into account. Mixed convection and thermal radiation effects are also considered in the analysis, and the problem is mathematically described using the long wavelength and low Reynolds number approximations.
Methods: The resulting nonlinear system is solved using numerical methods to obtain the solutions. The dominant effects of mixed convection and thermal radiation are given particular attention, while the influences of other parameters are discussed in relation to these dominant effects.
Results and Discussion: The results demonstrate that increasing the Brinkman number, heat source, and thermal slip parameter leads to higher nanofluid temperatures. However, the heat transfer rate decreases with a higher Hall parameter. The velocity near the center of the channel increases for higher values of the concentration Grashof and Hall parameters. Furthermore, an increase in the Hall and Brownian motion parameters results in a higher concentration of nanoparticles. These findings have practical implications in various fields, including materials science, chemical engineering, and biomedical engineering.
Peristaltic flows are a special type of flow generated by continuous waves of area contraction/expansion traveling on the walls of hollow tube-like structures of many living beings. The propagation of such waves propels the fluid confined inside the tube in the direction parallel to the propagation. In fact, peristaltic mechanisms are noted to be one of the very familiar fluid transport structures in the individual body as well as by way of which various fluids are moved over a short distance. In physiology, such flows find their applications in the transport of urine through the urinary tract, of food through the digestive tract, of bile through the bile duct, and in the transport of reproductive cells, etc. The utility of the peristaltic mechanism persuaded engineers to adopt such a mechanism in devising several engineering devices as well, particularly in processes where the constituents to be transported are sensitive/corrosive and are meant to be insulated from direct contact with the external environment. Latham, (1966) provided a pioneering study for the analysis of peristaltic phenomena, followed by Shapiro et al. (1969) who utilized the “long wavelength and low Reynolds number approach” to investigate such flows. Based on the utility of peristaltic flows, literature on the topic grew with time, incorporating analysis of such flows in different flow settings, some of which can be found in (Dobrolyubov and Douchy, 2002; Reddy et al., 2005; Abbasi et al., 2015). It is well established that many of the naturally occurring fluids (e.g., blood, semi-digested food, lava, etc.) are non-Newtonian. This fact makes the flow analysis of such fluids additionally important. Keeping this in mind, the peristaltic movement of non-Newtonian fluids is analyzed via studies (Abbasi et al., 2014; Babu and Narayana, 2016; Abbasi and Shehzad, 2017).
The importance of nanofluids and their utility cannot be overstated by any means. Since the proposal of the novel idea of nanofluids by Choi and Eastman, (1995), scientists and engineers have found numerous ways in which nanofluids enhance the performance of many scientific and engineering processes. Unique and modifiable thermals, as well as chemical properties of nanofluids, make them an ideal substance to achieve high performance in engineering processes such as in modern drug delivery systems, diagnostics and treatments of tumors/cancerous cells, and domestic/industrial heating/cooling systems. IT and automobile industries are some of the areas witnessing considerable advancements due to the use of nanofluids. Buongiorno, (2006) proposed that incorporating the Brownian motion and thermophoresis properties is essential in the flow study of nanofluids. Tiwari and Das, (2007) used effective thermophysical quantities for the analysis of nanofluid transport making use of the two-phase approach. Keeping the two-phase approach in view, several experimental investigations were carried out to propose different empirical relations predicting effective thermophysical quantities that are in close ties with that of experimental results. Some of these relations were specific for specific nanofluids whereas some models were proposed to predict the general behavior of nanofluids (Xue, 2005; Rudyak and Krasnolutskii, 2014; Shehzad et al., 2015).
Hybrid nanofluids are further modifications of nanofluids obtained by mixing more than one different nanosized particle in a base fluid. Mixtures thus obtained possess enhanced and precise thermophysical and chemical properties required for several processes. Recently, the flow analysis of nanofluids under different flow conditions has been reported in a number of studies, some of which are given through references (Izadi et al., 2019; Abbasi et al., 2022; Haq et al., 2022; Kumar and Sharma, 2022; Rehman et al., 2022; Yasmin et al., 2023). Investigations revealed that the addition of nanoparticles beyond a certain fraction of the total volume can perturb the rheological characteristics as well. Mixtures thus obtained act as non-Newtonian fluids of different types. Hence, the flow analysis of non-Newtonian nanofluids becomes important and has been attended in some of the studies given through references (Akbar et al., 2015; Rasheed et al., 2015; Eldabe et al., 2020; Gul et al., 2020; Sharma et al., 2023).
The present study delves into the peristalsis of non-Newtonian nanofluid, taking into account several factors to highlight its novelty. The study incorporates the rheologic properties of the fluid, applying the Carreau-Yasuda model, as well as viscous dissipation. Additionally, it considers the Lorentz force rendered by a uniform magnetic field, Ohmic heating, and Hall effects. The analysis also incorporates the effects of mixed convection, thermal radiation, and porous medium, making it more comprehensive. The mathematical description is obtained using the “long wavelength and low Reynolds number approximations,” and the boundaries adopt the slip condition of velocity and jump condition of temperature. Due to the resulting nonlinear system’s complexity, numerical solutions employing the inherent command in Mathematica are found. The study’s key findings are then briefly outlined at the end, emphasizing its novelty and significance.
An electrically conducting 2D incompressible peristalsis of Carreau-Yasuda (C-Y) nanofluid is contemplated in a symmetric channel of width
here
Thus, the study assumes that the flow is occurring in a symmetric channel of width with sinusoidal waves propagating at a constant wave speed at its walls. The flow is electrically conducting, 2D, and incompressible. The nanofluid being studied follows the Carreau-Yasuda model. Additionally, the channel walls are maintained at a constant mass concentration and temperature, and the flow is affected by an external magnetic field and various assumptions including mixed convection, heat absorption/generation, modified Darcy’s law, thermophoresis diffusion, Ohmic heating, Brownian diffusion, magnetic field/flux, viscous dissipation, and thermal radiation. Therefore, the leading equations for the underlying flow with these assumptions are given as (Shehzad et al., 2015; Gul et al., 2020):
In the above equations,
where
where,
For Carreau-Yasuda (C-Y) nanofluid, the extra stress tensor is presented as (Abbasi and Shehzad, 2017; Gul et al., 2020):
here
in which
Here, the shear rate
Furthermore,
The relationship between fixed frame
Utilizing the above-stated transformation to Eqs 2–6, we obtain.
Using the following dimensionless quantities (Abbasi and Shehzad, 2017; Gul et al., 2020):
In the above non-dimensional quantities,
Thus, the dimensionless quantities stated in Eq. 19 yield the satisfaction of the continuity equation, whereas Reynolds number and long wavelength are approximated to be small and long, correspondingly, which results in the following set of equations:
where
Applying cross-differentiating and substituting the values of
The flow rates in non-dimensional settings in the fixed
where
The slip boundary conditions are vital in many practical situations, especially in scenarios where the contact surfaces are lubed. Hence, the considerations of slip for velocity, temperature, and concentration are accounted for here. The dimensionless form of boundary conditions making use of the stresses defined via Eq. 24 for wall slip is stated as (Abbasi and Shehzad, 2017):
The non-dimensionless form of a peristaltic wall is described as:
where
This section aims to provide graphical results explaining the effects of various flow parameters involved in this study. In this study, we looked at how different parameters affect the distribution of fluid velocity, temperature, concentration, and heat and mass transfer rates in a channel under mixed convection and thermal radiation along with other flow parameters. The relationship among different flow parameters is provided by Eq. 19. We specifically considered the velocity slip parameter, concentration Grashof number, thermal Grashof number, Hartmann number, and Hall parameter, which are commonly used in similar studies. Below, we provide a brief description of these parameters and their typical range for a better understanding for readers:
• The velocity slip parameter measures the difference in velocity between the fluid and the solid surface and characterizes the effect of slip velocity on fluid motion. It ranges from zero to one, where zero represents no-slip and one represents free-slip.
• The concentration Grashof number is a dimensionless parameter that describes buoyancy-driven flow caused by concentration gradients in a fluid. Its typical range is between
• The thermal Grashof number is a dimensionless parameter that describes buoyancy-driven flow caused by temperature gradients in a fluid. Similar to the concentration Grashof number, the typical range for thermal Grashof number is between
• The Hartmann number is a dimensionless parameter that characterizes the effect of a magnetic field on the motion of an electrically conducting fluid. Its typical range is between 0 and 100.
• The Hall parameter is a dimensionless parameter that describes the influence of the magnetic field on the motion of a conducting fluid and considers the Hall effect. Its typical range is between zero and one.
• For mixed convection, typical parameter ranges are Reynolds number of 10–1,000 and Grashof number of
In the subsequent subsections, the velocity profile, temperature distribution, concentration profile, and heat and mass transfer rates at the boundary are presented and explained.
Figures 2A–E interact with the influence of velocity slip parameter
Figures 3, 4 relate to the impact of “Brinkman number
Graphical influences of the concentration slip parameter
Figures 7–11 have been developed to examine the phenomena of heat “absorption/generation parameter
This research investigated the properties of heat and mass transfer in the case of a non-Newtonian nanofluid under peristaltic motion, with a focus on the influence of mixed convection and thermal radiation effects. Key findings are as follows:
• Both mixed convection and thermal radiation had significant impacts on the behavior of the nanofluid.
• A rise in the Brinkman number led to a rise in temperature distribution, highlighting the significance of mixed convection effects.
• The heat transfer rate decreased with a higher Hall parameter, indicating the importance of mixed convection effects.
• An enhancement in the thermal radiation parameter led to a reduction in temperature profiles, while the concentration profile decreased with an increase in the concentration slip parameter and Hartmann number, highlighting the importance of thermal radiation effects.
• A rise in the Hall parameter and Brownian motion parameter resulted in an increase in the concentration of nanoparticles.
• Intensification in the Hartmann number and thermal radiation parameter led to an increase in the mass transfer rates.
• Overall, the study provided insights into the mixed effects of mixed convection and thermal radiation on the heat and mass transfer characteristics of non-Newtonian nanofluids and can have practical implications in a choice of engineering applications.
The findings of this study can have practical implications in several areas. One such area is the field of biomedical engineering, where the understanding of heat and mass transfer during peristalsis is crucial in the design of drug delivery systems. The use of non-Newtonian nanofluids in drug delivery can have significant benefits, such as improved drug solubility, increased drug loading capacity, and controlled release of drugs. However, the thermal and mechanical stresses experienced by the nanofluid during peristalsis can affect the efficiency and safety of the drug delivery system. The outcomes of these findings can specify insights into the heat and mass transfer characteristics of non-Newtonian nanofluids during peristalsis, which can aid in the design of more efficient and safe drug delivery systems.
In addition, the study can also have implications in the fields of materials science and chemical engineering, where the use of non-Newtonian nanofluids is becoming increasingly prevalent in various industrial applications, such as heat exchangers and cooling systems. The understanding of the effects of viscous dissipation, Lorentz force, Ohmic heating, and Hall effects on the heat and mass transfer characteristics of these nanofluids can aid in the design and optimization of these systems for improved efficiency and reduced energy consumption. Generally, the findings of this study can have positive impacts on the development of drug delivery systems, as well as various industrial applications, leading to improved efficiency, reduced energy consumption, and, potentially, lower costs.
The original contributions presented in the study are included in the article/Supplementary Material, further inquiries can be directed to the corresponding author.
The author confirms being the sole contributor of this work and has approved it for publication.
The author declares that the research was conducted in the absence of any commercial or financial relationships that could be construed as a potential conflict of interest.
All claims expressed in this article are solely those of the authors and do not necessarily represent those of their affiliated organizations, or those of the publisher, the editors and the reviewers. Any product that may be evaluated in this article, or claim that may be made by its manufacturer, is not guaranteed or endorsed by the publisher.
Abbasi, F. M., Alsaedi, A., and Hayat, T. (2014). Peristaltic transport of Eyring-Powell fluid in a curved channel. J. Aerosp. Eng. 27 (6), 04014037. doi:10.1061/(asce)as.1943-5525.0000354
Abbasi, F. M., Hayat, T., Ahmad, B., and Chen, B. (2015). Peristaltic flow with convective mass condition and thermal radiation. J. Cent. South Univ. 22, 2369–2375. doi:10.1007/s11771-015-2762-9
Abbasi, F. M., and Shehzad, S. A. (2017). Heat transfer analysis for peristaltic flow of Carreau-Yasuda fluid through a curved channel with radial magnetic field. Int. J. Heat Mass Transf. 115, 777–783. doi:10.1016/j.ijheatmasstransfer.2017.08.048
Abbasi, F. M., Zahid, U. M., Akbar, Y., and Hamida, M. B. B. (2022). Thermodynamic analysis of electroosmosis regulated peristaltic motion of Fe3O4–Cu/H2O hybrid nanofluid. Int. J. Mod. Phys. B 36, 2250060. doi:10.1142/s0217979222500606
Akbar, T., Nawaz, R., Kamran, M., and Rasheed, A. (2015). Magnetohydrodynamic (MHD) flow analysis of second grade fluids in a porous medium with prescribed vorticity. AIP Adv. 5, 117133. doi:10.1063/1.4936184
Babu, D. H., and Narayana, P. V. S. (2016). Joule heating effects on mhd mixed convection of a jeffrey fluid over a stretching sheet with power law heat flux: A numerical study. J. Magnetism Magnetic Mater. 412, 185–193. doi:10.1016/j.jmmm.2016.04.011
Buongiorno, J. (2006). Convective transport in nanofluids. J. Heat Transf. 128, 240–250. doi:10.1115/1.2150834
Choi, S. U. S., and Eastman, J. A. (1995). Enhancing thermal conductivity of fluids with nanoparticles ASME. Int. Mech. Eng. Congr. Expo., 12–17.
Dobrolyubov, A. I., and Douchy, G. (2002). Peristaltic transport as the travelling deformation waves. J. Theor. Biol. 219, 55–61. doi:10.1016/s0022-5193(02)93107-3
Eldabe, N. T., Moatimid, G. M., Abouzeid, M. Y., ElShekhipy, A. A., and Abdallah, N. F. (2020). A semianalytical technique for MHD peristalsis of pseudo plastic nanofluid with temperature-dependent viscosity: Application in drug delivery system. Heat Transfer-Asian Res. 49, 424–440. doi:10.1002/htj.21619
Gul, M., Abbasi, F., Shehzad, S. A., and Shafee, A. (2020). Entropy generation for peristaltic motion of Carreau’s fluid with mixture of ethylene glycol and boron-nitride nanoparticles. Phys. Scr. 95, 035212. doi:10.1088/1402-4896/ab49f8
Haq, I., Bilal, M., Ameer Ahammad, N., Ghoneim, M. E., Ali, A., and Weera, W. (2022). Mixed convection nanofluid flow with heat source and chemical reaction over an inclined irregular surface. ACS Omega 7 (34), 30477–30485. doi:10.1021/acsomega.2c03919
Izadi, M., Oztop, H. F., Sheremet, M. A., Mehryan, S. A. M., and Abu-Hamdeh, N. (2019). Coupled FHD–MHD free convection of a hybrid nanoliquid in an inversed T-shaped enclosure occupied by partitioned porous media. Part A Appl. 76, 479–498. doi:10.1080/10407782.2019.1637626
Kumar, S., and Sharma, K. (2022). Entropy optimized radiative heat transfer of hybrid nanofluid over vertical moving rotating disk with partial slip. Chin. J. Phys. 77, 861–873. doi:10.1016/j.cjph.2022.03.006
Rasheed, A., Nawaz, R., Khan, S. A., Hanif, H., and Wahab, A. (2015). Numerical study of a thin film flow of fourth grade fluid. Int. J. Numer. Methods Heat Fluid Flow 25 (4), 929–940. doi:10.1108/hff-06-2014-0188
Reddy, M. V. S., Mishra, M., Sreenadh, S., and Rao, A. R. (2005). Influence of lateral walls on peristaltic flow in a rectangular duct. J. fluids Eng. 127, 824–827. doi:10.1115/1.1994876
Rehman, A., Khan, W., Abdelrahman, A., Jan, R., Khan, M. S., and Galal, A. M. (2022). Influence of Marangoni convection, solar radiation, and viscous dissipation on the bioconvection couple stress flow of the hybrid nanofluid over a shrinking surface. Front. Mater. 9, 964543. doi:10.3389/fmats.2022.964543
Rudyak, Y., and Krasnolutskii, S. L. (2014). Dependence of the viscosity of nanofluids on nanoparticle size and material. Phys. Lett. A 378, 1845–1849. doi:10.1016/j.physleta.2014.04.060
Shapiro, A. H., Jaffrin, M. Y., and Weinberg, S. L. (1969). Peristaltic pumping with long wavelengths at low Reynolds number. J. Fluid Mech. 37, 799–825. doi:10.1017/s0022112069000899
Sharma, B. K., Kumar, A., Gandhi, R., Bhatti, M. M., and Mishra, N. K. (2023). Entropy generation and thermal radiation analysis of EMHD jeffrey nanofluid flow: Applications in solar energy. Nanomaterials 13, 544. doi:10.3390/nano13030544
Shehzad, S. A., Abbasi, F. M., Hayat, T., and Alsaadi, F. (2015). Model and comparative study for peristaltic transport of water based nanofluids. J. Mol. Liq. 209, 723–728. doi:10.1016/j.molliq.2015.05.058
Tiwari, R. K., and Das, M. K. (2007). Heat transfer augmentation in a two-sided lid-driven differentially heated square cavity utilizing nanofluids. Int. J. Heat Mass Transf. 50, 2002–2018. doi:10.1016/j.ijheatmasstransfer.2006.09.034
Xue, Q. Z. (2005). Model for thermal conductivity of carbon nanotube-based composites. Phys. B Condens. Matter. 368, 302–307. doi:10.1016/j.physb.2005.07.024
Keywords: peristalsis, non-Newtonian nanofluid, mixed convection, slip conditions, Hall effects, low Reynolds number
Citation: Alrashdi AMA (2023) Mixed convection and thermal radiation effects on non-Newtonian nanofluid flow with peristalsis and Ohmic heating. Front. Mater. 10:1178518. doi: 10.3389/fmats.2023.1178518
Received: 02 March 2023; Accepted: 07 June 2023;
Published: 22 June 2023.
Edited by:
Erkan Oterkus, University of Strathclyde, United KingdomReviewed by:
Mas Irfan Purbawanto Hidayat, Sepuluh Nopember Institute of Technology, IndonesiaCopyright © 2023 Alrashdi. This is an open-access article distributed under the terms of the Creative Commons Attribution License (CC BY). The use, distribution or reproduction in other forums is permitted, provided the original author(s) and the copyright owner(s) are credited and that the original publication in this journal is cited, in accordance with accepted academic practice. No use, distribution or reproduction is permitted which does not comply with these terms.
*Correspondence: Abdulwahed Muaybid A. Alrashdi, YW1hYTIwQGxlaWNlc3Rlci5hYy51aw==
Disclaimer: All claims expressed in this article are solely those of the authors and do not necessarily represent those of their affiliated organizations, or those of the publisher, the editors and the reviewers. Any product that may be evaluated in this article or claim that may be made by its manufacturer is not guaranteed or endorsed by the publisher.
Research integrity at Frontiers
Learn more about the work of our research integrity team to safeguard the quality of each article we publish.