- 1School of Safety Science and Emergency Management, Wuhan University of Technology, Wuhan, China
- 2School of Materials Science and Engineering, Wuhan University of Technology, Wuhan, China
- 3Center for Scientific and Technological Cooperation and Achievement Transformation, Wuhan University of Technology, Wuhan, China
- 4School of Science, Wuhan University of Technology, Wuhan, China
Heat-resistant magnetic microwave absorption coatings are vital important for the stealth safety of apparatus working at elevated temperature or electromagnetic compatibility of high density/power electronic devices. In this work, we proposed a heat-resistant coating with nanocrystalline FeCoCr micropowders as the absorbents and silicone resin as the matrix. The evolution of microstructure, absorption and adhesion of FeCoCr/silicone resin coatings were investigated after heat treatment at 400°C. The results show that the roughness of FeCoCr powders slightly increased due to the formation of nanoparticles, while their crystalline phase maintained body-centered cubic structure with grain size increasing from 10.8 nm to 18.1 nm after heat treatment. The saturated magnetization and coercivity of FeCoCr powders also increased after heat treatment. The adhesion of FeCoCr/silicone resin coatings exhibited sharp increase with the extension of heat treatment time, i.e., from 7.59 MPa at room temperature to 11.78 MPa after heat treatment at 400°C for 10 h; this phenomenon occurred due to the condense of FeCoCr-resin interfaces. The complex permittivity of the coating was reduced after heat treatment, while the complex permeability increased; this gave rise to enhancement of microwave absorption and showed the working potential of the FeCoCr/silicone resin coatings at elevated temperature.
1 Introduction
Microwave absorption materials have attracted tremendous attention in recent years either for stealth of military objects or for reduction of electromagnetic in civilian devices (Xu et al., 2021), by applying of novel materials with various compositions (Xu et al., 2020) and microstructures (Quan et al., 2019). Heat-resistant high performance microwave absorbing materials are crucial for improving the stealth ability of aircraft against radar detection and suppressing electromagnetic interference of high-precision and high-power electronic equipments which radiate heat at working (Qin and Brosseau, 2012; Peng et al., 2014). They can maintain stable structure, mechanical and electromagnetic properties at high temperature without cracking or falling off, which is vital important to ensure the thermal service safety of equipments (Jia et al., 2018).
At present, heat-resistant microwave absorbing materials mainly involve ceramics, carbon materials, magnetic metallic materials. Ceramic materials have attracted wide attention due to their excellent chemical and thermal stability. A variety of ceramic microwave absorbing materials including SiO2 (Ma et al., 2019), Al2O3 (Wang et al., 2015), BaTiO3 (Qing et al., 2014), SiC (Yang et al., 2013) and Si3N4 (Li et al., 2015) have been developed. Those materials showed low density, high hardness, high strength, good oxidation resistance, high thermal stability. However, improving their dielectric properties and wide-band absorption remains a great challenge. Carbon materials have the advantages of light weight, good corrosion resistance and high electrical conductivity. They have attracted much attention in the field of heat-resistant absorbing materials in recent years, such as carbon nanotubes (Song et al., 2009), graphene (Cao et al., 2015) and carbon black (Xu et al., 2018). However, carbon materials generally can work at temperature lower than 400°C, and the regulation of their permittivity is complex, leading to large thickness and narrow absorption bandwidth. Magnetic metallic absorbents have great potential in preparation of thin-layer, lightweight, wide-band and strong absorbing microwave materials since they possess both dielectric and magnetic loss mechanisms (Magisetty et al., 2018; Fu et al., 2022). However, when they are used at elevated temperature, many challenges appear, such as growth of grain, oxidation and mechanical deterioration when combining with polymeric matrix. Therefore, new heat-resistant materials based on magnetic metallic absorbents are ought to be developed, and the evolution of their properties are to be investigated.
In terms of heat-resistant matrix, silicone resin has organic-inorganic skeleton with Si-O-Si main chain structure and shows excellent heat resistance and processability (Robeyns et al., 2018). The structure and molecular weight of silicone resin are closely related to its properties. Some researchers have shown that silicone resin with higher crosslinking degree and molecular weight and better heat resistance can be obtained by silane addition reaction (Pagliaro et al., 2013), which is an important matrix for the preparation of magnetic microwave absorption materials in low and medium temperature regions. Heat-resistant microwave absorption materials based on silicone resin and carbonyl iron powders have been studied (Zhou et al., 2015; Zhang et al., 2018). However, Fe/silicone resin coating can be used at low temperature, due to the easy oxidation of Fe. Moreover, the adhesion of the coating, one of the most important property for practical applications, are rarely concerned. Therefore, developing novel magnetic metallic absorbents with thermal stability and their robust composite coatings with silicone resin is vital important.
Herein, we proposed a heat-resistant coating with nanocrystalline FeCoCr micropowders as the absorbents and silicone resin as the matrix. The evolution of microstructure, absorption and adhesion of FeCoCr/silicone resin coatings were investigated after heat treatment at 400°C for different time. The FeCoCr/silicone resin coatings showed efficient microwave absorption and robust adhesion after working at elevated temperature.
2 Materials and methods
Spherical Fe42.5Co42.5Cr15 alloy powders were prepared by melt-spray method. Flaky FeCoCr powders were produced by milling of the raw powders with ball milling machine. The morphology of spherical and flaky FeCoCr powders can be seen in Supplementary Figure S1, while the elemental composition of the powder can be seen in Supplementary Figure S2. During the milling process, ethanol was used as the process-control agent. The milling rate and time were 200 r/min and 60 min, respectively. The milled powders were separated from ethanol by magnets, followed by drying at 60°C for 3 h.
During the preparation of FeCoCr/silicone resin composite coatings, weight ratio of 4:1 between FeCoCr powder and silicone resin was used. Firstly, silicone resin was added to a beaker, followed by the adding of xylene. After stirring at rate of 500 r/min for 20 min, the silicone resin was considered to be uniformly dispersed in xylene. Secondly, flaky FeCoCr powders were added to the dispersion, followed by mechanical stirring at 1,000 r/min for 60 min. After that, FeCoCr/silicone resin coatings were prepared by spray coating. Titanium cylinders of Φ25 mm were used to support the coatings for adhesion test. After spray coating, the FeCoCr/silicone resin coatings were cured at 80°C for 1 h and subsequent at 180°C for 3 h.
Heat treatment of FeCoCr powders and FeCoCr/silicone resin coatings in air was performed in a tubular furnace. Microstructures of FeCoCr absorbent powders and coatings were characterized by scanning electron microscope (SEM S-4800), while their crystalline structures were analyzed by X-ray diffraction (XRD, D8 Advance diffractometer). Adhesion of coatings was measured by a universal mechanical testing machine (CMT5105, SANS, China) using pull-off method. Test standard is in accordance with ISO 4624:2016. At least five samples were tested to obtain average value of adhesion. Complex permittivity and permeability of coatings were measured according to coaxial line method by a vector network analyzer (N5230, Agilent, United States). Coatings were sculptured into toroidal shape with outer diameter of 7.0 mm and inner diameter of 3.0 mm to measure complex permittivity and permeability.
3 Results and discussions
3.1 Microstructure, crystalline and magnetic properties of FeCoCr powders
Figure 1 shows SEM images of FeCoCr absorbent powders at room temperature and after heat treatment at 400°C for 1 h, 5 h and 10 h. From Figure 1, the surface of FeCoCr powders was neither flat nor smooth, which was caused during the ball milling process. After heat treatment for 1 h (Figure 1B), nano-sized particles were observed on the surface; those nanoparticles may be formed by slightly oxidation. From Figures 1C, D, with the extension of heat treatment time, the nanoparticles on the surface were getting more and more obvious, leading to slight increase in roughness of the surface. However, the nanoparticles densely distributed on the surface, and thus the formation of nanoparticles did not change the overall morphology of the powder. Therefore, FeCoCr powders can maintain its morphology stability at temperature as high as 400°C.
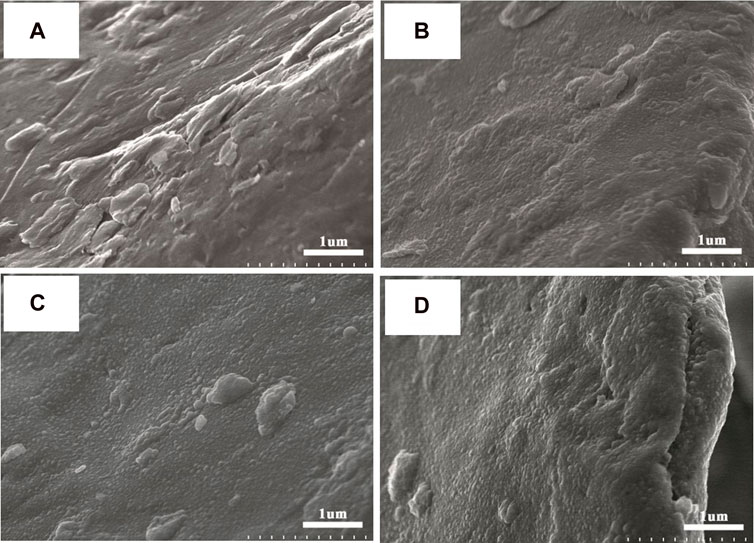
FIGURE 1. SEM images of FeCoCr powders after heat treatment at 400°C for different time: (A) raw, (B) 1 h, (C) 5 h, (D) 10 h.
Evolution in crystalline structure of FeCoCr absorbent powders after heat treatment was studied by XRD. Figure 2 shows the XRD spectra of FeCoCr absorbent powders at room temperature and after heat treatment at 400°C for 1 h, 5 h, and 10 h. It can be seen that under each heat treatment condition, there were three obvious diffraction peaks locating at 44.54°, 64.88° and 82.20°, corresponding to (110) (200) and (211) crystal planes of bcc phase, respectively. However, compared to the bcc structure of CoFe (PDF#44-1433) and Cr (PDF#85-1335), the position between CoFe and Cr indicates the presence of bcc-FeCoCr alloy (Kumar et al., 2020). After heat treatment at 400°C, the shape of diffraction peak did not change significantly, whereas the diffraction peaks became sharper with the increase of heat treatment time, giving rise to narrower half-peak width. The reason may be that the grain size increased while the internal strain decreased after heat treatment; reduction of internal defects promoted better arrangement of atoms in the lattice. Table 1 shows the grain size and internal strain of FeCoCr absorbent powders calculated according to Hall-Williamson formula (Takaki et al., 2018). The relationship between average grain size (D) and internal strain (ε) can be expressed by
where β is width of half maximum of diffraction peaks, k is Scherer constant of 0.89, λ is X-ray wavelength of 0.154 nm and θ is diffraction angle. The XRD spectra of FeCoCr powders at room temperature and after heat treatment at 400°C for 1 h, 5 h and 10 h indicate that heat treatment has little effect on the composition, but the grain size increased gradually with the increase of heat treatment time. From Table 1, the grain size increased relatively slowly at 1 h and 5 h, but it accelerated after 5 h. The grain size increased from 10.8 nm at room temperature to 18.1 nm at 400°C for 10 h, i.e., increased by 67.59%.
The static magnetic properties of FeCoCr powders after heat treatment were also investigated. Figure 3 shows the hysteresis loop, saturation magnetization and coercivity of FeCoCr absorbent powders after heat treatment at room temperature and 400°C for 1 h, 5 h and 10 h. It can be seen from Figure 3A that FeCoCr powders showed good soft magnetic properties before and after heat treatment. The hysteresis loop is smooth without obvious hysteresis phenomenon. Figure 3B shows the enlarged hysteresis loop near the magnetic field intensity close to 0. It can be seen that the slope gradually increases with the extension of heat treatment time, indicating the increase of initial magnetic susceptibility. It can be seen from Figures 3C, D that with the extension of heat treatment time, the saturated magnetization (Ms) of FeCoCr powders gradually increased. Compared with Ms of 65.12 emu/g at room temperature, the Ms after 10 h heat treatment at 400°C increased to 78.64 emu/g and increased by 20.76%. The increase of Ms is closely related to the release of internal stress in nanocrystalline grains. It has been reported that (He et al., 2012) when the internal structure of the grain is improved with the reduction of the defects such as dislocations or impurities, the specific surface area of the grain length decreases. Hence, the internal strain preventing the rotation of the magnetic domains in the material would be significantly reduced, thus leading to increase of Ms. However, it can be seen from Figure 3C that Ms increased relatively large after 1 h and 5 h of heat treatment, but relatively small after 10 h of heat treatment. Contrary to the variation trend of internal strain, internal strain decreased relatively small after 1 h and 5 h of heat treatment, but decreased largely after 10 h of heat treatment. The phenomenon of Ms variation may be the result of the internal strain reduction and the slow oxidation of a small amount of absorbent powder during heat treatment. As is seen in Figure 3D, the coercivity (Hc) increased initially but decreased subsequently with the extension of heat treatment time. Hc increased from 204.02 Oe at room temperature to 227.34 Oe after 1 h treatment at 400°C, and then it decreased to 219.4 Oe and 205.96 Oe after 5 h and 10 h treatment at 400°C. The change of Hc may be the balance results among Cr oxidation, segregation of Cr elements, increase of internal strain and increase of grain size, etc. During heat treatment, irreversible slow oxidation occurred, the composition and structure of the powder changed slightly, causing slight deterioration of the static magnetic properties. In addition, Cr atoms tended to segregate from internal of grains to grain boundaries, resulting in pining effect of grain boundaries and reduction of antiferromagnetic elements in the crystal. Moreover, with the decrease of internal strain, the magnetic domain is easier to rotate, caused the increase of Hc. Therefore, the variation of Hc did not follow single trend under the contradictory effect of slight oxidation of powder and interference of Cr element.
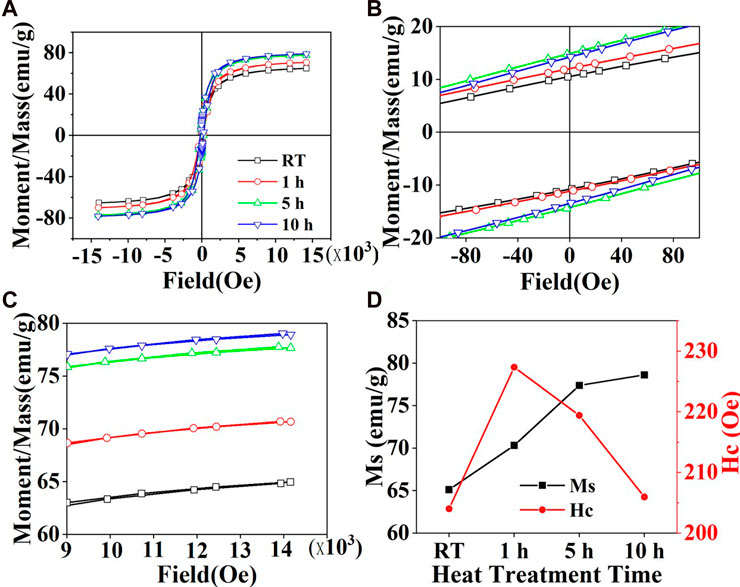
FIGURE 3. Static magnetic properties of FeCoCr powders after heat treatment at 400°C: (A) hysteresis loop, (B) enlargement of magnetization at low magnetic field, (C) enlargement of magnetization at high magnetic field, (D) changes in saturation magnetization and coercivity with heat treatment time.
3.2 Microstructure and adhesion of FeCoCr/silicone resin coating
The long-term application of heat-resistant microwave absorbing materials cannot be achieved without excellent mechanical properties. When the microwave absorbing composite material is used as a coating, it needs to have good adhesion with the substrate. Therefore, the adhesion of FeCoCr/silicone resin coatings at room temperature and after heat treatment at 400°C were tested. From Figure 4A, it can be seen that after heat treatment at 400°C, adhesion of the coating increased. Before heat treatment, the adhesion was 7.59 MPa, whereas the adhesion increased to 11.78 MPa after 10 h heat treatment, giving an increase of 55.20% and indicating the excellent heat resistance of FeCoCr/silicone resin coating. Figures 4B, C are the photos of adhesion test samples using the pulling method before and after heat treatment for 10 h. It can be seen that before heat treatment, the coating fractured at the weak layer on the surface of the coating. After heat treatment, the coating exhibited none uniform fracture surface in the middle of the testing cylinders. The crystal phase of FeCoCr/silicone resin coating was also revealed by XRD (see Supplementary Figure S3), showing stable crystalline structure after heat treatment. Therefore, it can be concluded that heat treatment can be helpful to enhance the interface adhesion between the absorbent powders and silicone resin.
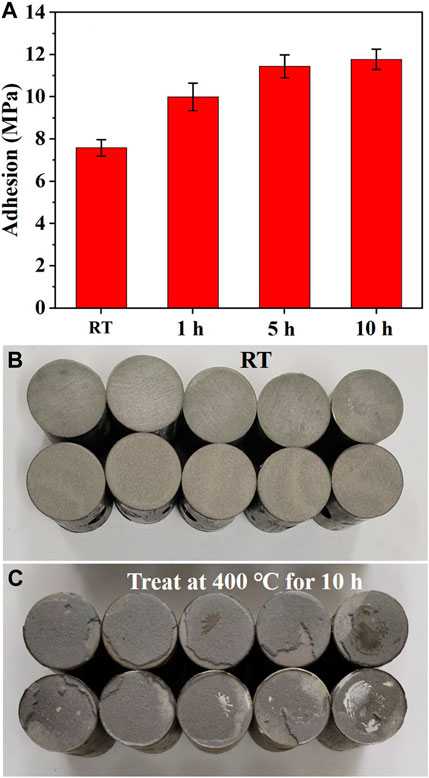
FIGURE 4. (A) Adhesion and (B,C) photos for adhesion test samples of FeCoCr/silicone resin coatings before and after heat treatment at 400°C.
The change of mechanical properties is closely related to the internal interfaces of composite materials. Figure 5 shows SEM images of the fracture coating after pulling test. In Figure 5, flaky powders evenly dispersed in silicone resin and mainly arranged in parallel. Figure 5A shows the microstructure of fracture surface of FeCoCr/silicone resin coating without heat treatment. Flaky FeCoCr powders densely embedded in the coating, but showed obvious microscale gaps away from the matrix. Therefore, it is reasonable to conclude that the powder-resin interfaces were weak and generated cracks upon the applying of external pulling force. Figures 5B–D show the microstructure of fracture surface of the FeCoCr/silicone coatings after heat treatment at 400°C for 1 h, 5 h and 10 h, respectively. To clearly show the distribution of FeCoCr particles in silicon resin, element mapping of the coating was carried out and included in Supplementary Figure S4. Compared with the coating without heat treatment, the coating after heat treatment for 1 h was much dense with few microscale gaps at powder-resin interfaces. After heat treatment for 5 and 10 h, the fracture mechanism had changed, i.e., the powder-resin interfaces were tight and the cracks generated in the matrix rather than at the interfaces. The deep holes or inwards propagating of large cracks were observed in the samples after heat treatment for 5 h and 10 h. Therefore, after heat treatment, the powder-resin interfaces were tight and robust, leading to the change of crack location from the interfaces to the matrix upon external pulling force during adhesion tests.
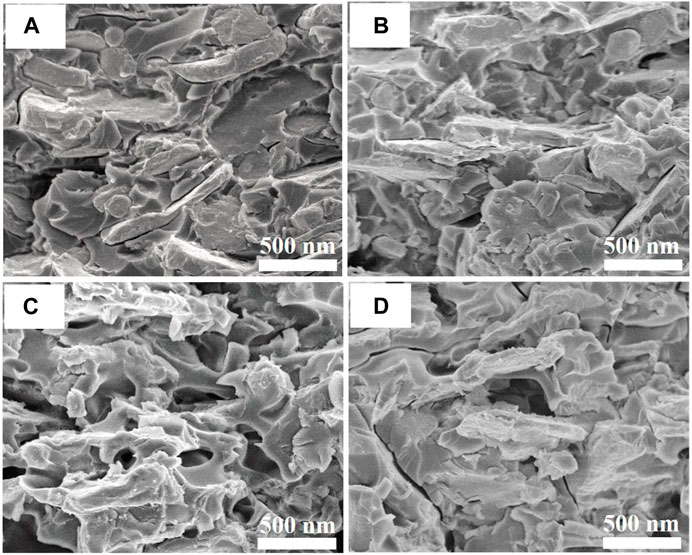
FIGURE 5. SEM images for fracture surface of FeCoCr/silicone resin coatings after adhesion test for samples heat treated at 400°C for different time: (A) 0 h, (B) 1 h, (C) 5 h and (D) 10 h.
3.3 Electromagnetic properties of FeCoCr/silicone resin coatings
The variation in electromagnetic properties of FeCoCr/silicone resin microwave absorbing coating at different heat treatment time were further investigated. Figure 6 shows electromagnetic parameters of FeCoCr/silicone resin coating before and after heat treatment at 400°C for 1 h, 5 h and 10 h. It can be seen from Figures 6A, B that at room temperature, the complex permittivity of FeCoCr/silicone resin coating showed strong dispersion over different frequency (Moon et al., 2000; Qing et al., 2010); and the complex permittivity of the composite coating decreased after heat treatment. The reasons leading to the reduction of permittivity are as follows. Firstly, a small amount of insulating oxide layer generated on the surface of the absorbent powders during heat treatment, which increased the resistivity of the coating. According to the free electron theory and the interface/electron polarization, the insulating oxides will lead to the reduction of complex permittivity (Song et al., 2014; Lv et al., 2017). Secondly, during heat treatment, impurities or part of silicone resin molecules may undergo thermal degradation and leave pores. According to the equivalent medium theory (Wang et al., 2013), introduction of pores will lead to the reduction of complex permittivity. It can be seen from Figures 6C, D that the complex permeability of FeCoCr/silicone resin coating increased with the increase of heat treatment time. This is due to the substantial release of internal stress in the absorbent powder, which intensifies the domain wall motion, thus elevating the domain wall vibration to increase the imaginary part of permeability. After heat treatment for 1 h, the imaginary part of permeability of the coating roughly kept stable, indicating that further heat treatment cannot cause continuous oxidation in FeCoCr powders. The stability of permeability shows that FeCoCr/silicone resin coatings are promising for working at elevated temperature.
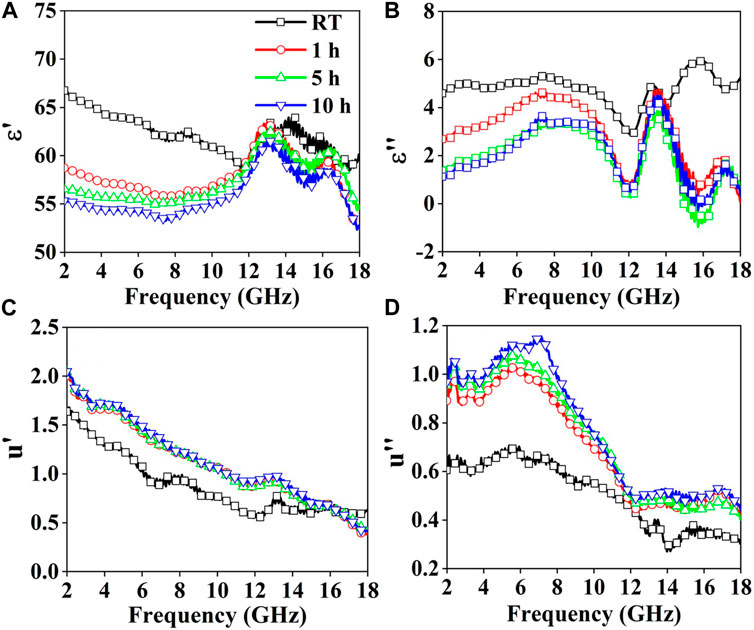
FIGURE 6. Electromagnetic properties of FeCoCr/silicone resin coatings after heat treatment at 400°C for different time: (A) real part of permittivity, (B) imaginary part of permittivity, (C) real part of permeability, (D) imaginary part of permeability.
To evaluate the absorption performance of FeCoCr/silicone resin coatings, the reflection loss of the coating was simulated with the complex permittivity and permeability according to the theory of transmission line. Figure 7A shows the simulated reflection loss of FeCoCr/silicone coating with thickness of 1 mm before and after heat treatment. It can be seen that the minimum reflection loss of the composite coating without heat treatment was only −4.75 dB, and the band width with reflection loss less than −4 dB was only 2.95 GHz (i.e., 7.35–10.30 GHz). After heat treatment, the minimum reflection loss of the coating decreased, indicating the increase of absorption. Moreover, the band width also increased. Especially, after heat treatment at 400°C for 10 h, the minimum reflection loss reached −6.18 dB, and the band width with reflection loss less than −4 dB increased to 5.90 GHz (i.e., 4.98–10.88 GHz). According to the analysis of the electromagnetic parameters, the improvement of absorption was mainly due to the increase of magnetic loss with the increase of permeability and due to the improvement of air-coating impedance matching with the reduction of permittivity. The simulated reflection loss FeCoCr/silicone resin coatings with different thickness is presented in Figure 7B. It can be seen that the coating are promising for working at low frequency bands.
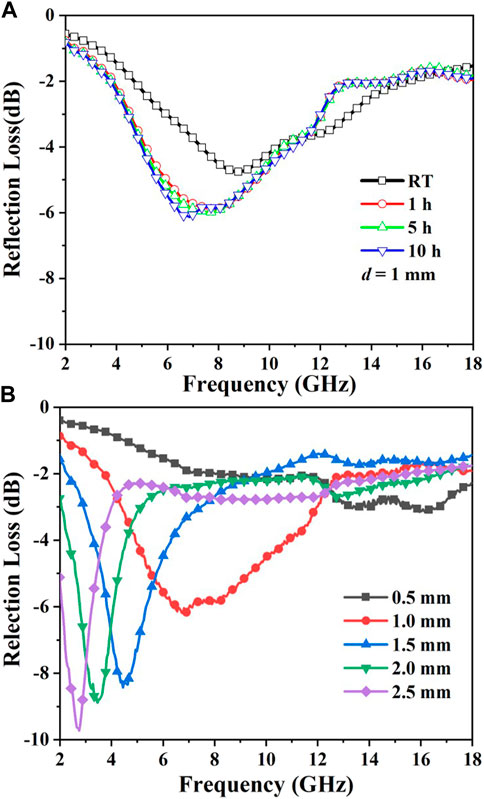
FIGURE 7. Simulated reflection loss of FeCoCr/silicone resin coating (A) after heat treatment at 400°C for different time and (B) with different thickness after heat treatment at 400°C for 10 h.
4 Conclusion
In this work, thermal stability for microstructure, crystal structure and static magnetic properties of nanocrystalline FeCoCr powders were studied, followed by investigation in the evolution of microstructure, adhesion and microwave absorption of FeCoCr/silicone resin composite coatings at elevated temperature. Surface roughness of FeCoCr powders slightly increased due to the formation of oxidation nanoparticles after heat treatment at 400°C. The crystalline phase of FeCoCr powders maintained the same after heat treatment, whereas their grain size increased from 10.8 nm to 18.1 nm. The saturated magnetization of FeCoCr powders was found to increase from 65.12 emu/g to 78.64 emu/g after heat treatment, which was due to the reduction of internal strain. The proposed FeCoCr/silicone resin composite coatings showed robust mechanical properties after working at 400°C for 10 h, exhibiting an adhesion of 11.78 MPa after heat treatment. The increase of adhesion was closely related to the interfaces between FeCoCr powders and silicon resin, i.e., weak interfaces at room temperature was significantly enhanced and condensed after working at elevated temperature. After heat treatment, the complex permittivity of the coating decreased whereas the complex permeability increased. The peak value of reflection loss of a 1-mm-thick coating decreases from −4.75 dB at room temperature to 6.18 dB after 10 h of heat treatment, indicating that the absorption performance of the coating was significantly enhanced and can remain stable at high temperature.
Data availability statement
The original contributions presented in the study are included in the article/Supplementary Material, further inquiries can be directed to the corresponding authors.
Author contributions
Conceptualization, ZhC and ZyC; Data curation, ZhC and DY; Formal analysis, ZhC and ZyC; Funding acquisition, ZhC; Methodology, ZyC and BY; Supervision, ZhC and CC; Validation, ZyC and DY; Writing—original draft, DY and CC; Writing—review and editing, ZhC, CC, and YW. All authors have read and agreed to the published version of the manuscript.
Funding
This research was funded by the National Natural Science Foundation of China (No. 52071239), Aeronautical Science Foundation of China (2018ZF65002), National Innovation and Entrepreneurship Training Program for College Student (202210497012).
Conflict of interest
The authors declare that the research was conducted in the absence of any commercial or financial relationships that could be construed as a potential conflict of interest.
The handling editor BM declared a shared affiliation with the authors at the time of the review.
Publisher’s note
All claims expressed in this article are solely those of the authors and do not necessarily represent those of their affiliated organizations, or those of the publisher, the editors and the reviewers. Any product that may be evaluated in this article, or claim that may be made by its manufacturer, is not guaranteed or endorsed by the publisher.
Supplementary material
The Supplementary Material for this article can be found online at: https://www.frontiersin.org/articles/10.3389/fmats.2023.1168418/full#supplementary-material
References
Cao, W. Q., Wang, X. X., Yuan, J., Wang, W. Z., and Cao, M. S. (2015). Temperature dependent microwave absorption of ultrathin graphene composites. J. Mater. Chem. C 3, 10017–10022. doi:10.1039/c5tc02185e
Fu, Z., Chen, Z., Wang, R., Xiao, H., Wang, J., Yang, H., et al. (2022). Deformation-thermal Co-induced ferromagnetism of austenite nanocrystalline FeCoCr powders for strong microwave absorption. Nanomaterials 12, 2263. doi:10.3390/nano12132263
He, J., Wang, W., and Guan, J. (2012). Internal strain dependence of complex permeability of ball milled carbonyl iron powders in 2-18 GHz. J. Appl. Phys. 111, 093924. doi:10.1063/1.4716028
Jia, Z., Lin, K., Wu, G., Xing, H., and Wu, H. (2018). Recent progresses of high-temperature microwave-absorbing materials. Nano 13, 1830005. doi:10.1142/s1793292018300050
Kumar, R., Kumar, A., Verma, N., Philip, R., and Sahoo, B. (2020). FeCoCr alloy-nanoparticle embedded bamboo-type carbon nanotubes for non-linear optical limiting application. J. Alloys Compd. 849, 156665. doi:10.1016/j.jallcom.2020.156665
Li, M., Yin, X., Zheng, G., Chen, M., Tao, M., Cheng, L., et al. (2015). High-temperature dielectric and microwave absorption properties of Si3N4–SiC/SiO2 composite ceramics. J. Mater. Sci. 50, 1478–1487. doi:10.1007/s10853-014-8709-y
Lv, H. L., Guo, Y. H., Wu, G. L., Ji, G. B., Zhao, Y., and Xu, Z. J. C. (2017). Interface polarization strategy to solve electromagnetic wave interference issue. Acs Appl. Mater. Interfaces 9, 5660–5668. doi:10.1021/acsami.6b16223
Ma, J. R., Shu, J. C., Cao, W. Q., Zhang, M., Wang, X. X., Yuan, J., et al. (2019). A green fabrication and variable temperature electromagnetic properties for thermal stable microwave absorption towards flower-like Co3O4@rGO/SiO2 composites. Compos. Part B-Engineering 166, 187–195. doi:10.1016/j.compositesb.2018.11.119
Magisetty, R., Shukla, A., and Kandasubramanian, B. (2018). Magnetodielectric microwave radiation absorbent materials and their polymer composites. J. Electron. Mater. 47, 6335–6365. doi:10.1007/s11664-018-6580-3
Moon, K. S., Choi, H. D., Lee, A. K., Cho, K. Y., Yoon, H. G., and Suh, K. S. (2000). Dielectric properties of epoxy-dielectrics-carbon black composite for phantom materials at radio frequencies. J. Appl. Polym. Sci. 77, 1294–1302. doi:10.1002/1097-4628(20000808)77:6<1294:aid-app14>3.0.co;2-e
Pagliaro, M., Ciriminna, R., Pandarus, V., and Beland, F. (2013). Platinum-based heterogeneously catalyzed hydrosilylation. Eur. J. Org. Chem. 2013, 6227–6235. doi:10.1002/ejoc.201300290
Peng, C. H., Chen, P. S., and Chang, C. C. (2014). High-temperature microwave bilayer absorber based on lithium aluminum silicate/lithium aluminum silicate-SiC composite. Ceram. Int. 40, 47–55. doi:10.1016/j.ceramint.2013.05.101
Qin, F., and Brosseau, C. (2012). A review and analysis of microwave absorption in polymer composites filled with carbonaceous particles. J. Appl. Phys. 111, 061301. doi:10.1063/1.3688435
Qing, Y. C., Mu, Y., Zhou, Y. Y., Luo, F., Zhu, D. M., and Zhou, W. C. (2014). Multiwalled carbon nanotubes BaTiO3/silica composites with high complex permittivity and improved electromagnetic interference shielding at elevated temperature. J. Eur. Ceram. Soc. 34, 2229–2237. doi:10.1016/j.jeurceramsoc.2014.02.007
Qing, Y., Zhou, W., Luo, F., and Zhu, D. (2010). Epoxy-silicone filled with multi-walled carbon nanotubes and carbonyl iron particles as a microwave absorber. Carbon 48, 4074–4080. doi:10.1016/j.carbon.2010.07.014
Quan, B., Shi, W., Ong, S. J. H., Lu, X., Wang, P. L., Ji, G., et al. (2019). Defect engineering in two common types of dielectric materials for electromagnetic absorption applications. Adv. Funct. Mater. 29, 1901236. doi:10.1002/adfm.201901236
Robeyns, C., Picard, L., and Ganachaud, F. (2018). Synthesis, characterization and modification of silicone resins: An “Augmented Review”. Prog. Org. Coatings 125, 287–315. doi:10.1016/j.porgcoat.2018.03.025
Song, W., Cao, M., Hou, Z., Yuan, J., and Fang, X. (2009). High-temperature microwave absorption and evolutionary behavior of multiwalled carbon nanotube nanocomposite. Scr. Mater. 61, 201–204. doi:10.1016/j.scriptamat.2009.03.048
Song, Z., Deng, L., Xie, J., Zhou, P., Lu, H., and Wang, X. (2014). Synthesis, dielectric, and microwave absorption properties of flake carbonyl iron particles coated with nanostructure polymer. Surf. Interface Analysis 46, 77–82. doi:10.1002/sia.5351
Takaki, S., Masumura, T., and Tsuchiyama, T. (2018). Proposal of simplified modified williamson-Hall equation. Isij Int. 58, 2354–2356. doi:10.2355/isijinternational.isijint-2018-517
Wang, Y., Luo, F., Wei, P., Zhou, W. C., and Zhu, D. M. (2015). Enhanced dielectric properties and high-temperature microwave absorption performance of Zn-doped Al2O3 ceramic. J. Electron. Mater. 44, 2353–2358. doi:10.1007/s11664-015-3787-4
Wang, Z., Nelson, J. K., Hillborg, H., Zhao, S., and Schadler, L. S. (2013). Dielectric constant and breakdown strength of polymer composites with high aspect ratio fillers studied by finite element models. Compos. Sci. Technol. 76, 29–36. doi:10.1016/j.compscitech.2012.12.014
Xu, H., Yin, X., Li, M., Ye, F., Han, M., Hou, Z., et al. (2018). Mesoporous carbon hollow microspheres with red blood cell like morphology for efficient microwave absorption at elevated temperature. Carbon 132, 343–351. doi:10.1016/j.carbon.2018.02.040
Xu, X., Shi, S., Tang, Y., Wang, G., Zhou, M., Zhao, G., et al. (2021). Growth of NiAl-layered double hydroxide on graphene toward excellent anticorrosive microwave absorption application. Adv. Sci. 8, 2002658. doi:10.1002/advs.202002658
Xu, X., Wang, G., Wan, G., Shi, S., Hao, C., Tang, Y., et al. (2020). Magnetic Ni/graphene connected with conductive carbon nano-onions or nanotubes by atomic layer deposition for lightweight and low-frequency microwave absorption. Chem. Eng. J. 382, 122980. doi:10.1016/j.cej.2019.122980
Yang, H. J., Yuan, J., Li, Y., Hou, Z. L., Jin, H. B., Fang, X. Y., et al. (2013). Silicon carbide powders: Temperature-dependent dielectric properties and enhanced microwave absorption at gigahertz range. Solid State Commun. 163, 1–6. doi:10.1016/j.ssc.2013.03.004
Zhang, Y., Xu, J., Feng, Y., and Qiu, T. (2018). Hot-air aging failure mechanisms of carbonyl iron powder/methyl vinyl silicone rubber microwave-absorbing materials. Adv. Polym. Technol. 37, 3262–3275. doi:10.1002/adv.22095
Keywords: thermal stability, microwave absorption, absorbent, silicone resin, magnetic loss
Citation: Yuan D, Chen Z, Cai C, Yang B, Wang Y and Chen Z (2023) Microstructures, absorption and adhesion evolution of FeCoCr/silicone resin coatings at elevated temperature. Front. Mater. 10:1168418. doi: 10.3389/fmats.2023.1168418
Received: 17 February 2023; Accepted: 14 March 2023;
Published: 24 March 2023.
Edited by:
Binbin Mao, Wuhan University of Technology, ChinaCopyright © 2023 Yuan, Chen, Cai, Yang, Wang and Chen. This is an open-access article distributed under the terms of the Creative Commons Attribution License (CC BY). The use, distribution or reproduction in other forums is permitted, provided the original author(s) and the copyright owner(s) are credited and that the original publication in this journal is cited, in accordance with accepted academic practice. No use, distribution or reproduction is permitted which does not comply with these terms.
*Correspondence: Changwei Cai, Y2hhbmd3ZWlAd2h1dC5lZHUuY24=; Zhihong Chen, el9jaGVuQHdodXQuZWR1LmNu