- 1Center of Hypergravity Experimental and Interdisciplinary Research, Zhejiang University, Hangzhou, Zhejiang, China
- 2Center of Electron Microscopy and State Key Laboratory of Silicon Materials, School of Materials Science and Engineering, Zhejiang University, Hangzhou, Zhejiang, China
- 3College of Civil Engineering and Architecture, Zhejiang University, Hangzhou, China
The turbine blades were directionally solidified by a high-rate solidification process by the Bridgman technique using directional solidified Ni-based master superalloy DZ125 and operated on the engine bench with a high-temperature gas environment of more than 1500 °C from combustor and high-speed rotation of more than 13500 rpm for 400 h. A service-environment-based model was put forward to simulate the distribution of temperature and stress on the DZ125 blade in service. It was found that the distribution of temperature and stress on the serviced DZ125 blade was closely related to its geometric structure. The microstructural evolution of the serviced DZ125 blade was analyzed and the variations of microstructures with temperature and stress were investigated by using a scanning electron microscope. The results revealed that the evolution process of microstructures on the serviced DZ125 blade was different from that of the standard sample tested at constant temperature and uniaxial tensile stress. The reason for this discrepancy was explored using a combination of finite-element calculation and diffusion coefficient calculation.
1 Introduction
Gas turbine is one of the most efficient heat-to-power conversion machinery and widely used in aero-engines. In the service of gas turbines, the integrity of turbine blades as a core component of aero-engines is of great importance to the service safety (Rogge et al., 2018). In addition, temperature and centrifugal stress on turbine blades change sharply during take-off, cruise, and landing of aircrafts. Because of these, as the key aerodynamic part responsible for the energy transformation in gas turbines, turbine blades are always manufactured by advanced superalloys. It should be known that turbine blades work at various speeds and temperatures, and it leads to turbine blades subjected to a wide range of temperature and stress produced by high-temperature gas from the combustion chamber and high-speed rotation in service (Zadvorniy et al., 2015).
The directional solidified (DS) superalloy DZ125 exhibits columnar crystalline morphology with the <001> orientation, which is parallel to the centrifugal stress of blades (Chen et al., 2020). Compared with polycrystalline and wrought superalloys, the DZ125 superalloy can render superior microstructural stability and mechanical properties at elevated temperatures due to the elimination of undesirable transverse grain boundaries (Fu et al., 2020). The DZ125 superalloy also possesses exceptional elevated temperature strength, high resistance to creep, no obvious thin-wall effect, good oxidation and corrosion resistance, as well as good fracture toughness and is widely employed in manufacturing high-pressure turbine blades (Pollock and Argon, 1994;Duscher et al., 2004; Chellali et al., 2016). A large amount of experimental and theoretical studies regarding the DZ125 superalloy were conducted to explore the relationship between mechanical properties and the γ–γ′ microstructural degradation (Cottura et al., 2012; Fedelich et al., 2012; Sadowski and Golewski, 2012; Cottura et al., 2016; Barba et al., 2018). Understanding the failure mechanism and predicting creep lifetime have been a long-term requirement in order to ensure the flight safety of engines. In this respect, macroscopic methods, e.g., macroscopic constitutive modeling, are insufficient mainly because the plastic deformation takes place at external stress far below macroscopic yield stress according to the classic strength theory, but the microstructural degradation of the DZ125 superalloy under high-temperature and low-stress conditions is observed experimentally. The DZ125 superalloy mainly consists of channel-like γ phase and cuboid γ′ phase surrounded by the matrix γ phase. Operating at a high-temperature and high-speed rotating state, the DZ125 superalloy strengthened by γ′ precipitates inevitably experiences the microstructural degradation, mainly including coarsening, connection, dissolution, and rafting of γ′ precipitates (Fu et al., 2019; Fu et al., 2020), and finally results in blade failure.
In recent years, investigations on γ′ precipitates degradation were extensively carried out and many models for coarsening and rafting of γ′ precipitates were proposed and well applied for DS superalloys (Ichitsubo et al., 2003; Dye et al., 2008; Takahashi et al., 2008). Recent decades have seen an increasing interest in estimating the remaining creep lifetimes of turbine blades as a means of ensuring the safety of engines. Gan et al. (2020) introduced the initial damage terms that are related with the topologically close-packed (TCP) phase and the coarsen γ′ precipitates when predicting the remaining lifetime. Tian et al. (2011) considered the micropores in the lifetime prediction model. These reported results can predict the residual lifetime well when applied to standard samples; Huang et al. (2022) used smooth and three types of U-shape single-edge notched plate specimens to investigate stress rupture behavior of the DZ125 superalloy. A combined creep-viscoplasticity constitutive model was employed to analyze the distribution of stress and strain near the notch root. The results indicated that the different stress distribution and creep restraint between asymmetric notched plate specimens and symmetric notched round bars are the main reasons for the corresponding failure mechanism; Wang et al. (2021) used a combination of hot isostatic pressing (HIP) and rejuvenation heat treatment (RHT) technology to restore creep-damaged DZ125 superalloy and then studied the influence of microstructural restoration on the high-temperature fatigue property of the DZ125 superalloy. The results showed that the HIP + RHT process could effectively heal internal cavities and recover the degraded γ′ phase in creep-damaged DZ125 superalloy to the initial cubic-like particles. However, due to the complex geometrical structure and service conditions of turbine blades, it is questionable that the lifetime evaluation method by the microstructure of the standard samples in the lab can be directly used for the service-exposed turbine blades. Holländer et al. (2016) studied the effect of service-induced microstructural degradation on the tensile and fatigue properties of two service-exposed industrial gas turbine blades using small-scale samples, revealing that the microstructural degradation in the air foil section has a detrimental effect on the fatigue resistance. It should be noted that investigations of the turbine blade material for actual service mostly focus on the establishment of the damage evaluation criteria for blades (Holländer et al., 2016; Tong et al., 2016; Wang et al., 2021). In their work, the microstructure of the material under different conditions, for which the stress applied is surface force (e.g. uniaxial tensile stress), was obtained and then quantitatively characterized as the characteristic parameters of the material under the specific temperature and stress (Guo et al., 2019a). In this way, the service condition of the blade was obtained by comparing the characteristic parameters of the microstructure on blades with the standard sample. It is clear that the diversity of the degradation mechanism of the microstructures between blades and the standard samples was ignored, and thus, the rationality of comparing the blades and the standard samples was rarely discussed. Nevertheless, the difference must exist because of the uncertainty of service history and the complexity of temperature and stress distribution for turbine blades exposed to a combined environment of high-temperature gas and high-speed rotation.
In fact, the actual service conditions of turbine blades is a coupling environment of non-isothermal and high-speed rotation. It is quite different from the isothermal and uniaxial stress of the standard sample in the laboratory, and airworthiness authorities (e.g., FAA in the United States and EASA in Europe) require turbine blades to undergo the special experiments to simulate the actual service conditions. Rowe and Freeman (1961) investigated the overheating service degradation of the M252 superalloy to explore the effect of the higher abnormal operational temperature, which is referred to as overheating service (Dye et al., 2008), on creep property. Zhao et al. (2022) investigated the role of oxidation and recrystallization on very-high-cycle fatigue of the DZ125 superalloy at a temperature from 850 to 1000 °C because very-high-cycle fatigue is the most important failure mode of turbine blades in modern engines. Therefore, it is of critical importance to directly study the failure mechanism of turbine blades under the simulated engine operating conditions to the greatest extent.
It is well known that temperature and stress are two crucial factors that influence the microstructural degradation of Ni-based superalloys (Kakehi, 1999; Maldini et al., 2007; Yue et al., 2019). To be more specific, temperature is a scalar while stress is a vector. When testing the creep property of the materials at constant temperature in the laboratory, the applied axial stress is the surface force. The stress that turbine blades bear when rotating at high speed is the inertial force or body force, which is a function of the material density and the distance to the rotation center. It can be predicted that different stress loading methods of the surface force and the body force may affect the microstructure and mechanical properties of the materials in different ways when testing the mechanical properties of the same materials at the same temperature.
In our work, a turbine blade with the film cooling holes was manufactured by the DZ125 superalloy and in service on the engine bench with a high-temperature gas environment of more than 1500 °C from combustor and high-speed rotation of more than 13500 rpm for 400 h. A service-environment-based model was put forward to simulate distribution of temperature and stress on blades in service. The service-induced microstructural degradation of the DZ125 blade was analyzed and the variations of microstructures with temperature and stress were investigated by a scanning electron microscope. The service-induced microstructural degradation of the DZ125 blade is in the way different from that of the standard sample tested at constant temperature and uniaxial tensile stress. The reason for this discrepancy was explored using a combination of finite-element calculation and diffusion coefficient calculation.
2 Experimental and methods
2.1 Experimental
The DZ125 turbine blades were directionally solidified by a high-rate solidification (HRS) process with a 3.5 mm/min withdrawal rate by the Bridgman technique at the AECC Beijing Institute of Aeronautical Materials. The DZ125 blades were subsequently subjected to the standard heat treatment: 1180 °C/2 h + 1230 °C/3 h with air cooling (AC) + 1100 °C/4 h (AC) + 870 °C/20 h (AC). The chemical composition of the DZ125 superalloy is Ni-8.9% Cr-10% Co-7% W-2% Mo-5.2% Al-0.9% Ti-0.8% Ta-1.5% Hf (wt%). In order to simulate the geometric structure of the turbine blade body as much as possible, the film cooling holes (FCHs) of the heat-treated DZ125 blades were perforated by using an electrical discharge machine (EDM, Rotary Electro-Discharge Grinder, ZGD703C) and then drilled by the high-speed electric spark machining method in strict accordance with the processing technology of FCHs at AVIC Manufacturing Technology Institute. The surface quality of the FCHs is fine. The inner wall roughness of the FCHs drilled is uniform. The DZ125 blades with the film cooling holes operate on the engine bench with the high-temperature gas environment of more than 1500 °C from combustor and high-speed rotation of more than 13500 rpm for 400 h. In order to compare with the service-induced microstructure at the typical locations on the DZ125 blade, the specimen cut from the blade rabbet is considered to be the original microstructure.
The specimens were cut from the interested locations of the blade for the observation of
2.2 Temperature field model of the blade
In order to simulate temperature distribution of the cross sections on the DZ125 blade in service, the temperature field model was put forward on the basis of the overall energy continuity across the blade with the consideration of heat transfer between hot gas traversing the blade and cooling air passing through a cooling channel inside the blade from blade root to blade tip. The cooling air usually comes from the exit of the upstream compressor. According to the study of Saturday et al. (2017), a radial temperature distribution along the blade height is given in Figure 1. It can be seen that temperature along the blade height continuously increases from the root, reaches the maximum at the middle of the blade, and then decreases gradually. Clearly, the maximum temperature occurs at the middle of the blade (B point) while the minimum temperature occurs at the root (A point) and the tip (C point) of the blade. To simplify the model, temperature from B point to A point and C point of the blade, separately, can be approximately linear with the blade height (Shi et al., 2013). To decrease the working temperature of the turbine blade surface, several rows of film cooling holes are machined on the blade body. During the operation, the cooling gas flowing from the holes can form a thin layer of air-cooled film on the blade surface so as to avoid the heat transfer between the high-temperature gas and the blade directly. Under the ideal conditions, the blade surface is adiabatic without heat exchange with the air-cooled film. The cooling efficiency of the air-cooled film,
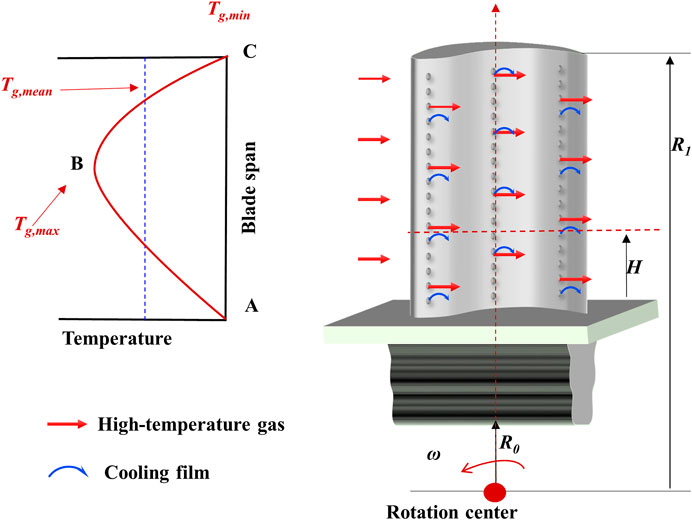
FIGURE 1. Schematic of the model assisted in calculating the temperature and stress distribution of the DZ125 blade in service.
Here, we assume that gas temperature
where
2.3 Stress distribution model of the blade
In order to simulate stress distribution of the cross sections on the DZ125 blade in service, the stress distribution model was built considering the centrifugal force derived from the blade rotation. The centrifugal force
where
3 Results
3.1 Temperature and stress distribution on the blade
The temperature distribution of the blade wall, especially along the radial and longitudinal direction of the blade in service, is mainly decided by gas temperature and distribution of film cooling holes in the blade body. The temperature field model and the stress field model are used to calculate temperature and stress distribution of the blade wall in service. Table 1 gives the parameters used in the models. The calculated results by Eqs. 2, 3 are shown in Figure 2 and Table 2. Figure 2A indicates that the temperature distribution of the blade wall is abruptly inhomogeneous along the radial direction on a longitudinal section. On any longitudinal section, the temperature at the leading edge (LE) and the trailing edge (TE) of the blade is the highest while the temperature at the pressure side (PS) and the suction side (SS) is relatively low and about lower than 850 °C. Temperature near the blade tip is approximately comparable to that near the blade root. The typical characteristic of stress distribution in Figure 2B is linearly gradient along the longitudinal direction and the centrifugal stress level is equivalent on any radial section. The centrifugal stress gradient along the longitudinal direction is about 11 MPa/mm, and the temperature gradient from the blade root to the upper middle part of the blade is about 3–5 °C/mm.
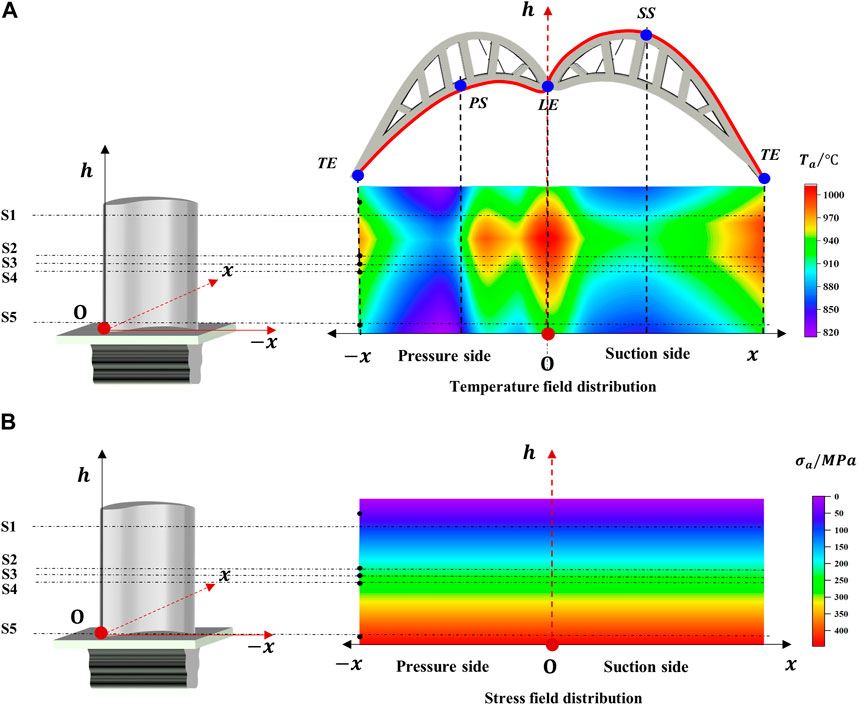
FIGURE 2. Temperature and centrifugal stress profiles of the DZ125 blade in service. (A) Temperature distribution of the DZ125 blade wall with film cooling holes and (B) centrifugal tensile stress distribution along the blade height.
It was found in Figure 2 that the temperature and stress distribution on the DZ125 blade exposed to a combined environment of high-temperature gas and high-speed rotation were closely related to the geometric structure. The coupling of temperature and stress has a significant influence on the morphological evolution of γ′ precipitates and γ matrix of the DZ125 blade. In order to examine the microstructural degradation of the blade after service, the typical locations of the blade are selected to assess the microstructural degradation degree of the blade based on the calculated temperature and stress field distribution. Because there is a big difference in temperature and stress between the radial and longitudinal section, as shown in Figure 3, the five representative cross sections and the four typical locations at each cross section are chosen for assessment of the microstructural degradation of the DZ125 blade. Among the selected cross sections as shown in Figure 3, section 1 (S1) is close to the blade tip and corresponds to medium temperature and low stress, section 5 (S5) is near the blade root, corresponding to low temperature and high stress, and section 2, section 3, and section 4 (S2, S3, and S4) are taken at the middle height of the blade and the distance between each section is 3 mm. S2, S3, and S4 are the typical representative of high temperature and medium stress. The three sections are predicted to have a serious microstructural degradation. The direction of microstructural observation is perpendicular to the direction of centrifugal tensile stress.
3.2 The typical microstructures on the blade
The morphology of the DZ125 blade rabbet is regarded as the original microstructure in this work. Figure 4A gives the typical morphology of the blade rabbet. The
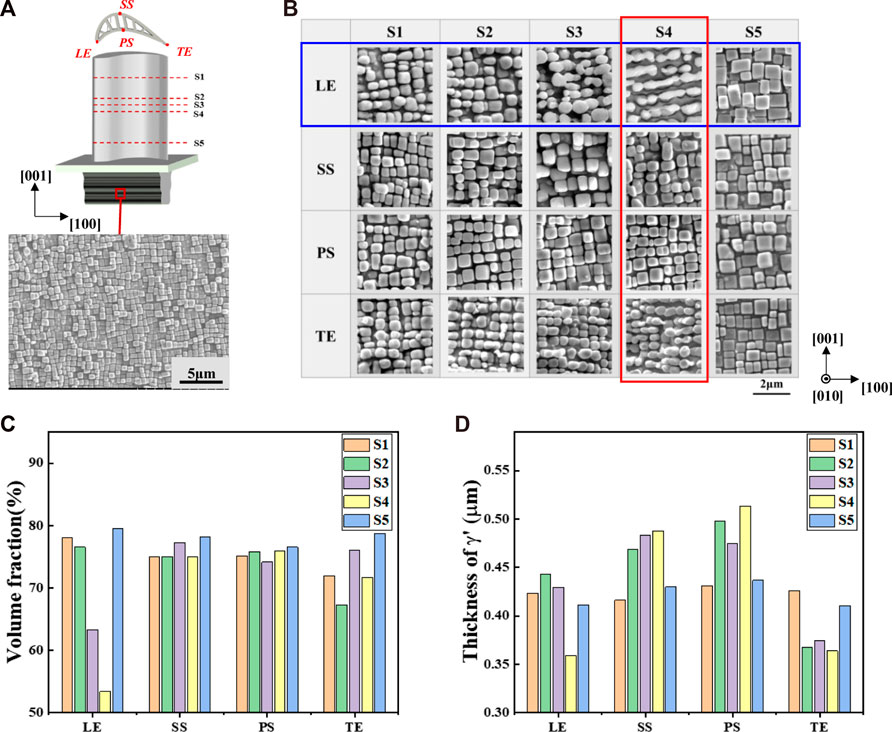
FIGURE 4. (A) Morphology of the DZ125 blade rabbet, (B) microstructural evolution of the selected locations on the serviced DZ125 blade, and (C, D) volume fraction and thickness of
The representative sections are examined to show microstructural degradation in different ways mainly resulted from the gradient change in temperature and stress closely related to the geometric structure of the blade. The γ–γ′ morphology of the LEs on the five cross sections is shown in the blue box of Figure 4B. As expected, there is an obvious difference in morphologies and sizes of the γ′ precipitates, comparing with that of the DZ125 blade rabbet. S3 and S4, however, show the most obvious rafting and serious coarsening of the γ′ precipitates because of high temperature and larger stress, while S1 and S2 as well as the area in between show slight coarsening but no obvious rafting due to low stress. It should be noted that the cubic-like shapes of the γ′ precipitates at S5 seem to still keep possibly due to low temperature even though centrifugal stress at S5 is relatively high among the five examined cross sections. Temperature and stress of S4 are high among the five chosen cross sections as shown in the red box of Figure 4A. The figures in the red box of Figure 4B show that the γ′ precipitates at the LE and TE are of the most obvious degradation. According to the geometric structure of the blade, it is known that the LE is directly impacted by high-temperature gas in service, resulting in the significant increase in temperature at the LE as shown in Figure 2A. Comparing the morphologies of γ′ precipitates at the LE and TE, it can be seen that there is a slight difference in the sizes of the γ′ precipitates. The stress of the LE is comparable to that of the TE, while the temperature of the TE is lower than that of the LE. The temperature at the SS and PS is low due to film cooling compared with that at the LE and TE so that the γ′ precipitates basically maintain the cubic shape.
Along the circumferential direction of the blade, the degradation of γ′ precipitates at the LE and TE is usually severe, especially at the LE of S3 and S4. The γ′ precipitates of the SS and PS can roughly maintain the cubic-like shape on each cross section. Relatively, there is no significant difference in the morphologies of γ′ precipitates among observation points of S5. The γ′ precipitates at S1 and S2 have a certain degree of distortion on each cross section. The γ′ precipitates of the LE and TE of S3 and S4 have obviously rafting, especially at S4, where the γ′ precipitates even have a certain degree of dissolution.
Figure 4C shows the volume fraction of γ′ precipitates on the selected cross sections. It can be seen from Figure 4C that the volume fraction of γ′ precipitates at the LE varies greatly. The volume fractions of γ′ precipitates of S3 and S4 are lower than 65% while the volume fractions of γ′ precipitates of S1, S2, and S5 are close to 75%, and the volume fraction of the γ′ precipitates at the TE is also quite different. The volume fractions of the γ′ precipitates at the SS and PS are closer, about 75%. The volume fraction of the γ′ precipitates at S5 is totally higher than that of other sections. Figure 4D shows the thickness of γ′ precipitates on the selected points. It can be seen that the γ′ precipitates at the SS and PS are significantly higher than the LE and TE and this phenomenon is the most evident in S4. The thickness of γ′ precipitates at the different positions of S4 has a great change, which means that the morphology of γ′ precipitates is more sensitive to temperature than stress.
4 Discussion
During the operation, the DZ125 blade is exposed to the complicated environment of high-temperature gas and high-speed rotation. It can be predicted that the microstructural degradation mechanism of the DZ125 blade may be different from that of the standard samples under the same condition (Serin et al., 2004). The change in the volume fraction and the thickness of γ′ precipitates with temperature and stress is shown in Figure 5. It can be seen that the volume fraction of γ′ precipitates is more sensitive to temperature because it decreases significantly with the increase in temperature. In general, the influence of pressure on the equilibrium of the system can be reasonably neglected for the condensed system. For the DZ125 superalloys, temperature affects the proportion of precipitates at equilibrium, and stress, while not affecting the proportion of precipitates at equilibrium, can accelerate this process. When stress is lower than about 220 MPa, the rafting process of γ′ precipitates is very hard to achieve the thermodynamic equilibrium even if the operation lasts more than 400 h according to the study of Chen et al. (2016). It is why the change of the volume fraction of γ′ precipitates with the rising temperature is unapparent under low stress, but the volume fraction of γ′ precipitates noticeably declines once stress is higher than the critical value. At the same time, the thicknesses of γ′ precipitates would significantly change with stress. It should be accepted that the coarsening and rafting processes of γ′ precipitates are a diffusion-control one. The coupling effect of temperature and stress affects the chemical potential gradient of elements and then influences the diffusion direction of elements, finally resulting in the change in the morphology of
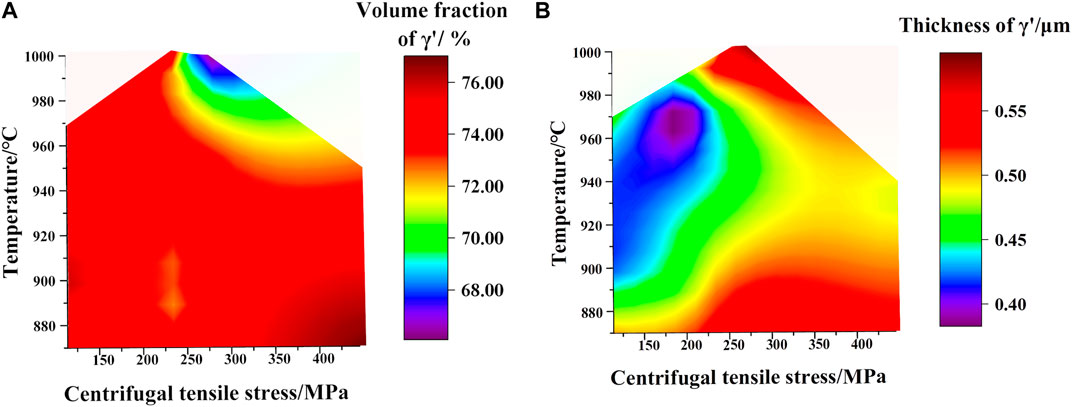
FIGURE 5. Coupling effects of stress and temperature on the configuration of
Figure 2 shows the temperature and stress distribution of the DZ125 blade in service are significantly geometry dependent, resulting in the fact that, as shown in Figure 4, the morphologies of the DZ125 blade after service may be quite diverse (Knowles et al., 2019). It should be noted that he evolution of γ′ precipitates is essentially the result of element diffusion which is related to temperature and stress. Thus, considering the diffusion process is of great importance. According to Fick’s first law and the related thermodynamic theory (the details of the theoretical derivation are given in Supplementary Material), the effects of stress and temperature on the diffusion coefficient can be obtained, as shown in Figure 6, in which the ranges of temperature and centrifugal stress are selected based on Figure 5. The curve of parameter (
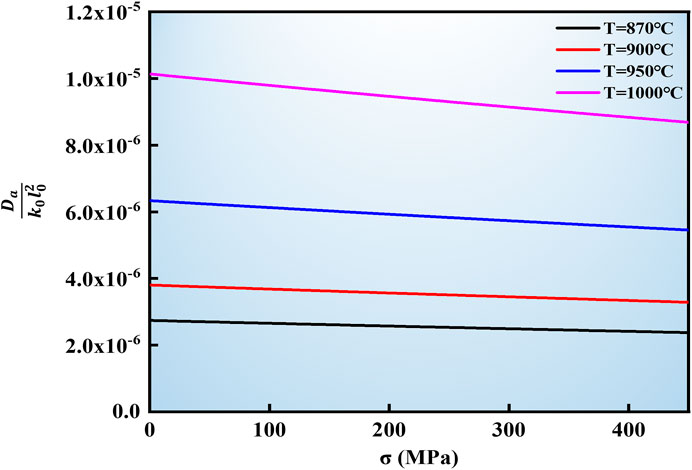
FIGURE 6. Curve of
As diffusion depends on stress at high temperature, it is necessary to obtain the stress distribution at the
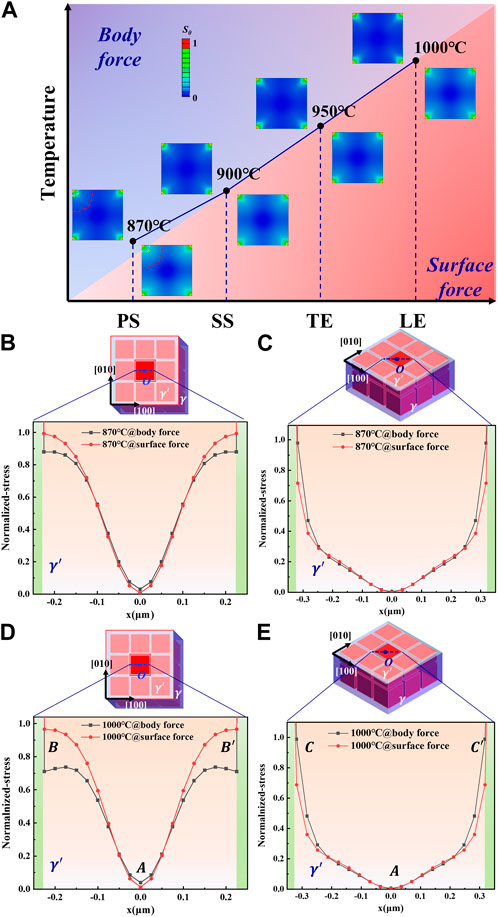
FIGURE 7. Microscopic stress distribution at the
It has been known that rafting of
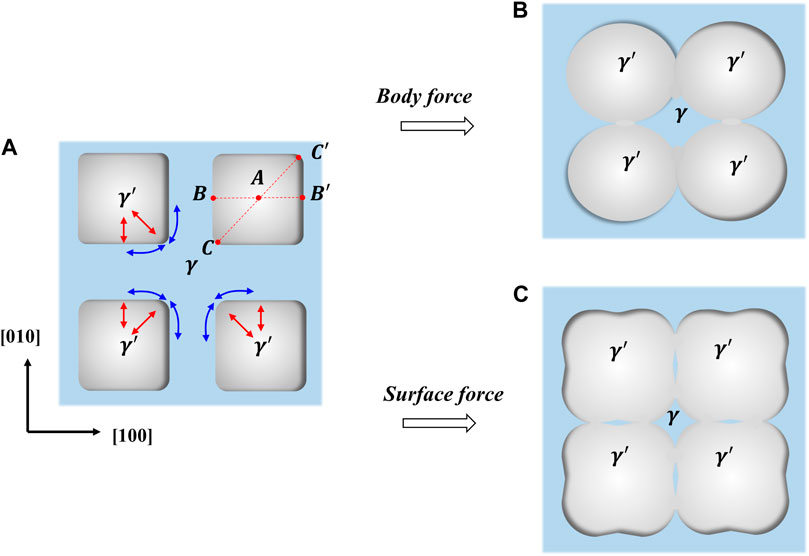
FIGURE 8. (A) Migration diagram of the
Based on Figure 6 and the diffusion model, the model regarding the migration of the
Figure 9 gives the microstructures of each point on S4 of the DZ125 blade after service. As temperature increases, the
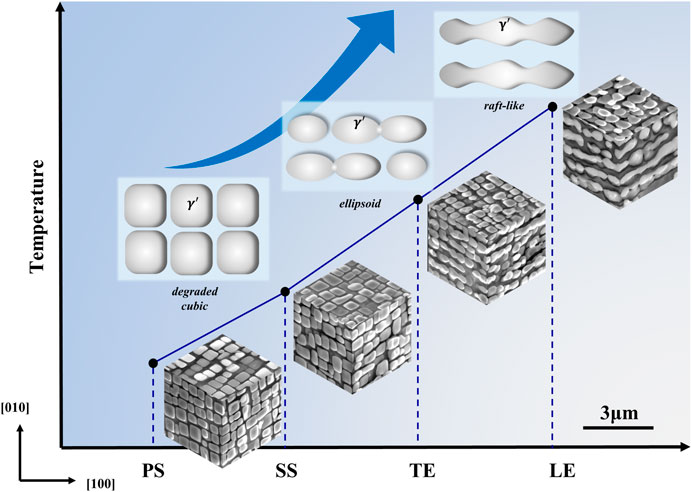
FIGURE 9. Evolution of the microstructure of the serviced DZ125 blade with temperature at S4 and the schematic of the evolution process of
5 Conclusion
The directional solidified Ni-based master superalloy DZ125 was used to directionally solidify turbine blades by the Bridgman technique. The DZ125 turbine blades with the film cooling holes were operated on the engine bench with the high-temperature gas environment of more than 1500 °C from combustor and high-speed rotation of more than 13500 rpm. The microstructural evolution of the served DZ125 blades was analyzed, and the variations of microstructures with temperature and stress were investigated. The following conclusions are drawn.
A service-environment-based model was put forward to simulate the distribution of temperature and stress on the DZ125 blade in service. It was found that the distribution of temperature and stress on the serviced DZ125 blade were closely related to its geometric structure. Based on the calculated results, the LE, PS, SS, and TE locations on five sections were selected to analyze the change in the volume fraction and the size of
Data availability statement
The original contributions presented in the study are included in the article/Supplementary Material; further inquiries can be directed to the corresponding author.
Author contributions
HW designed the experiments and supervised the project. JZ and YX performed the experiments and analyzed the data. YX and HF performed the computational simulations. YX wrote the paper. HW and HF revised the paper.
Funding
This work was supported by the Basic Science Center Program for Multiphase Evolution in Hypergravity of the National Natural Science Foundation of China (grant number 51988101) and the National Natural Science Foundation of China (grant number 52173302).
Conflict of interest
The authors declare that the research was conducted in the absence of any commercial or financial relationships that could be construed as a potential conflict of interest.
Publisher’s note
All claims expressed in this article are solely those of the authors and do not necessarily represent those of their affiliated organizations, or those of the publisher, the editors, and the reviewers. Any product that may be evaluated in this article, or claim that may be made by its manufacturer, is not guaranteed or endorsed by the publisher.
Supplementary material
The Supplementary Material for this article can be found online at: https://www.frontiersin.org/articles/10.3389/fmats.2023.1165971/full#supplementary-material
References
Barba, D., Alabort, E., Garcia-Gonzalez, D., Moverare, J. J., Reed, R. C., and Jerusalem, A. (2018). A thermodynamically consistent constitutive model for diffusion-assisted plasticity in Ni-based superalloys. Int. J. Plasticity 105, 74–98. doi:10.1016/j.ijplas.2017.12.007
Chellali, M. R., Zheng, L., Schlesiger, R., Bakhti, B., Hamou, A., Janovec, J., et al. (2016). Grain boundary segregation in binary nickel–bismuth alloy. Acta Mater. 103, 754–760. doi:10.1016/j.actamat.2015.11.003
Chen, B., Zhao, Z., Dong, C., and Yang, X. (2020). Initiation and early-stage growth of internal fatigue cracking under very-high-cycle fatigue regime at high temperature. Metallurgical Mater. Trans. A 51 (4), 1575–1592. doi:10.1007/s11661-020-05633-3
Chen, Y., Zheng, Y., and Feng, Q. C. (2016). Evaluating service temperature field of high-pressure turbine blades made of directionally solidified dz125 superalloy based on micro-structural evolution. Acta Metall. Sin. 52, 1545–1556. doi:10.11900/0412.1961.2016.00170
Cottura, M., Appolaire, B., Finel, A., and Le Bouar, Y. (2016). Coupling the Phase Field Method for diffusive transformations with dislocation density-based crystal plasticity: Application to Ni-based superalloys. J. Mech. Phys. Solids 94, 473–489. doi:10.1016/j.jmps.2016.05.016
Cottura, M., Bouar, Y. L., Finel, A., Appolaire, B., Ammar, K., and Forest, S. (2012). A phase field model incorporating strain gradient viscoplasticity: Application to rafting in Ni-base superalloys. J. Mech. Phys. Solids 60 (7), 1243–1256. doi:10.1016/j.jmps.2012.04.003
Duscher, G., Chisholm, M. F., Alber, U., and Ruhle, M. (2004). Bismuth-induced embrittlement of copper grain boundaries. Nat. Mater 3 (9), 621–626. doi:10.1038/nmat1191
Dye, D., Ma, A., and Reed, R. C. (2008). “Numerical modelling of creep deformation in a CMSX-4 single crystal superalloy turbine blade,” in Proceedings of the International Symposium on Superalloys, 01 January 2008 (United Kingdom: Oxford University Press), 911–919.
Eshati, S., Abu, A., Laskaridis, P., and Khan, F. (2013). Influence of water–air ratio on the heat transfer and creep life of a high pressure gas turbine blade. Appl. Therm. Eng. 60 (1-2), 335–347. doi:10.1016/j.applthermaleng.2013.06.061
Fedelich, B., Epishin, A., Link, T., Klingelhoffer, H., Kunecke, G., Portella, P. D., et al. (2012). Rafting during high temperature deformation in a single crystal superalloy: Experiments and modeling. United States: Wiley, 490–500.
Fu, C., Chen, Y., He, S., Antonov, S., Li, L., Zheng, W., et al. (2019). ICME framework for damage assessment and remaining creep life prediction of in-service turbine blades manufactured with Ni-based superalloys. Integrating Mater. Manuf. Innovation 8 (4), 509–520. doi:10.1007/s40192-019-00161-4
Fu, C., Chen, Y., Li, L., Antonov, S., and Feng, Q. (2020). Evaluation of service conditions of high pressure turbine blades made of DS Ni-base superalloy by artificial neural networks. Mater. Today Commun. 22, 100838. doi:10.1016/j.mtcomm.2019.100838
Gan, W., Gao, H., Zhao, Y., Wen, Z., Lu, G., Jiang, B., et al. (2020). Influence of microstructure degradation induced by pretreatment on the creep behavior in Ni-based single-crystal superalloy with different orientations. J. Mater. Res. 35 (6), 610–622. doi:10.1557/jmr.2020.35
Guo, X., Qin, X. Y., Huang, D. W., and Yan, X. J. (2019b). Morphology evolution and probability characteristic of γ' phase in single crystal superalloy during creep rafting. Key Eng. Mater. 827, 373–378. doi:10.4028/www.scientific.net/kem.827.373
Guo, X., Zheng, W., Xiao, C., Li, L., Antonov, S., Zheng, Y., et al. (2019a). Evaluation of microstructural degradation in a failed gas turbine blade due to overheating. Eng. Fail. Anal. 103, 308–318. doi:10.1016/j.engfailanal.2019.04.021
Holländer, D., Kulawinski, D., Weidner, A., Thiele, M., Biermann, H., and Gampe, U. (2016). Small-scale specimen testing for fatigue life assessment of service-exposed industrial gas turbine blades. Int. J. Fatigue 92, 262–271. doi:10.1016/j.ijfatigue.2016.07.014
Huang, J., He, Z., Lyu, S., Yang, X., Shi, D., Sun, Y., et al. (2022). A physically-based representative stress methodology for predicting stress rupture life of Ni-based DS superalloy. Chin. J. Aeronautics 2022, 1–6. doi:10.1016/j.cja.2022.07.006
Ichitsubo, T., Koumoto, D., Hirao, M., Tanaka, K., Osawa, M., Yokokawa, T., et al. (2003). Rafting mechanism for Ni-base superalloy under external stress: Elastic or elastic–plastic phenomena? Acta Mater. 51 (14), 4033–4044. doi:10.1016/s1359-6454(03)00224-6
Kakehi, K. (1999). Tension/compression asymmetry in creep behavior of a Ni-based superalloy. Scr. Mater. 41 (5), 461–465. doi:10.1016/s1359-6462(99)00191-8
Knowles, A., Reynolds, L., A Vorontsov, V., and Dye, D. (2019). A nickel based superalloy reinforced by both Ni3Al and Ni3V ordered-fcc precipitates. Scr. Mater. 162, 472–476. doi:10.1016/j.scriptamat.2018.12.013
Liu, C., Zhu, H., Bai, J., and Xu, D. (2010). Film cooling performance of converging slot-hole rows on a gas turbine blade. Int. J. Heat Mass Transf. 53 (23-24), 5232–5241. doi:10.1016/j.ijheatmasstransfer.2010.07.036
Maldini, M., Angella, G., and Lupinc, V. (2007). Analysis of creep curves of a nickel base superalloy in a wide stress/temperature range. Mater. Sci. Eng. A 462 (1-2), 436–440. doi:10.1016/j.msea.2005.11.084
Pollock, T. M., and Argon, A. S. (1994). Directional coarsening in nickel-base single crystals with high volume fractions of coherent precipitates. Acta Metallurgica Materialia 42 (6), 1859–1874. doi:10.1016/0956-7151(94)90011-6
Rogge, T., Berger, R., Pohle, L., Rolfes, R., and Wallaschek, J. (2018). Efficient structural analysis of gas turbine blades. Aircr. Eng. Aerosp. Technol. 90 (9), 1305–1316. doi:10.1108/aeat-05-2016-0085
Rowe, J. P., and Freeman, J. W. (1961). Final report to National Aeronautics and Space Administration: Relations between microstructure and creep-rupture properties of Nickel-base alloys as revealed by overtemperature exposures. United States: University of Michigan, 149.
Sadowski, T., and Golewski, P. (2012). Detection and numerical analysis of the most efforted places in turbine blades under real working conditions. Comput. Mater. Sci. 64, 285–288. doi:10.1016/j.commatsci.2012.02.048
Saturday, E. G., Li, Y. G., Ogiriki, E. A., and Newby, M. A. (2017). Creep-life usage analysis and tracking for industrial gas turbines. J. Propuls. power 33 (5), 1305–1314. doi:10.2514/1.b35912
Sen, B., Schmidt, D. L., and Bogard, D. G. (1996). Film cooling with compound angle holes: Heat transfer. J. Turbomach. 118 (4), 800–806. doi:10.1115/1.2840937
Serin, K., Gobenli, G., and Eggeler, G. (2004). On the influence of stress state, stress level and temperature on γ-channel widening in the single crystal superalloy CMSX-4. Mater. Sci. Eng. A 387, 133–137. doi:10.1016/j.msea.2004.01.114
Shi, D., Dong, C., and Yang, X. (2013). Constitutive modeling and failure mechanisms of anisotropic tensile and creep behaviors of nickel-base directionally solidified superalloy. Mater. Des. 45, 663–673. doi:10.1016/j.matdes.2012.09.031
Sinha, A. K., Bogard, D. G., and Crawford, M. E. (1991). Film-cooling effectiveness downstream of a single row of holes with variable density ratio. J. Turbomach. 113 (3), 442–449. doi:10.1115/1.2927894
Takahashi, A., Kobayashi, Y., and Kikuchi, M. (2008). Phase field simulation of rafting behavior of γ`Phase in nickel base superalloy. Adv. Mater. Res. 33-37, 471–476. doi:10.4028/www.scientific.net/amr.33-37.471
Tian, S., Zhang, S., Fushun, L., Anan, L., and Jingjing, L. (2011). Microstructure evolution and analysis of a single crystal nickel-based superalloy during compressive creep. Mater. Sci. Eng. A 528 (15), 4988–4993. doi:10.1016/j.msea.2011.03.035
Tong, J., Ding, X., Wang, M., Yagi, K., Zheng, Y., and Feng, Q. (2016). Assessment of service induced degradation of microstructure and properties in turbine blades made of GH4037 alloy. J. Alloys Compd. 657, 777–786. doi:10.1016/j.jallcom.2015.10.071
Wang, S., Ditta, A., Xu, Y., and Zhang, Z. (2021). Effect of microstructures restoration on high temperature fatigue behavior of DZ125 superalloy. Prog. Nat. Sci. Mater. Int. 31 (4), 633–640. doi:10.1016/j.pnsc.2021.07.005
Yue, Q., Liu, L., Yang, W., Sun, D., and Huang, T. (2019). Stress dependence of the creep behaviors and mechanisms of a third-generation Ni-based single crystal superalloy. J. Mater. Sci. Technol. 35 (5), 752–763. doi:10.1016/j.jmst.2018.11.015
Zadvorniy, E. A., Kravchuk, L. V., Buiskikh, K. P., Kiselevskaya, S. G., Feofentov, N. N., and Lebedin, A. Y. (2015). Analysis of the material damage influence on the stress-strain state of gas-turbine engine blades. Strength Mater. 47 (6), 797–803. doi:10.1007/s11223-015-9716-1
Keywords: turbine blade, microstructural evolution, high-speed rotation, high temperature, diffusion
Citation: Xie Y, Zhao J, Fu H and Wei H (2023) Dependence of microstructural evolution on the geometric structure for serviced DZ125 turbine blades. Front. Mater. 10:1165971. doi: 10.3389/fmats.2023.1165971
Received: 14 February 2023; Accepted: 24 March 2023;
Published: 10 April 2023.
Edited by:
Sheng Guo, Chalmers University of Technology, SwedenReviewed by:
Liuliu Han, Max-Planck-Institut für Eisenforschung, GermanyJunyang He, Central South University, China
Copyright © 2023 Xie, Zhao, Fu and Wei. This is an open-access article distributed under the terms of the Creative Commons Attribution License (CC BY). The use, distribution or reproduction in other forums is permitted, provided the original author(s) and the copyright owner(s) are credited and that the original publication in this journal is cited, in accordance with accepted academic practice. No use, distribution or reproduction is permitted which does not comply with these terms.
*Correspondence: Haoran Fu, RnVockB6anUuZWR1LmNu; Hua Wei, aHVhd2VpQHpqdS5lZHUuY24=