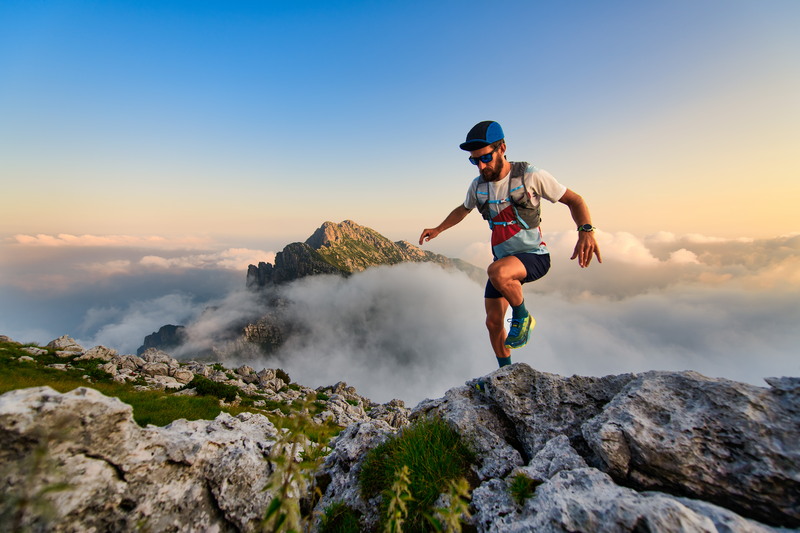
95% of researchers rate our articles as excellent or good
Learn more about the work of our research integrity team to safeguard the quality of each article we publish.
Find out more
EDITORIAL article
Front. Mater. , 24 January 2023
Sec. Structural Materials
Volume 10 - 2023 | https://doi.org/10.3389/fmats.2023.1145618
This article is part of the Research Topic Fluxes and Steel Quality View all 5 articles
Editorial on the Research Topic
Fluxes and steel quality
Control of steel quality is one of the most important topics for steelmakers. Fluxes plays critical roles in the production of high-quality steels and therefore has received increasing research interests in recent years. One of the aspects of steel quality is cleanliness of steel, which is reflected by the composition, size distribution, morphology of non-metallic inclusions in steels. The non-metallic inclusions can be controlled by optimizing operations from steel refining to continuous casting. The recent studies (You et al., 2021; Scheller and Shu, 2014) have revealed the impact of reaction between slag/flux and steel on the inclusion evolutions during steel refining. Among these, the optimization of ladle slag/flux is one of the crucial steps for achieving better steel cleanliness. The surface quality of steel cast products is another important issue since the surface defects will lead to the post-processing of steel and even downgrading or rejecting the products. The formation of surface defects, e.g., longitudinal cracks, is closely related to the performance of mold fluxes. It is well accepted that the longitudinal crack in steel mainly stems from the large shrinkage induced by peritectic reaction from δ-Fe to γ-Fe. Mild cooling provide by high crystallinity mold fluxes is the most efficient way to reduce the occurrence of longitudinal cracks (Hanao et al., 2012).
The aims of Research Topic: Fluxes and steel quality are to collect the state-of-the-art research work in fluxes/slag for improving steel quality. To this end, four articles including three original and one review work have been published in this Research Topic, covering the topics of the modelling thickness of mold fluxes film, melting of mold powder, reaction between slag and titanium steel and deoxidation of high-silicon austenitic stainless steel.
The first two articles are dealing with the behavior of mold powder in continuous casting of steel. Xu et al. established three-dimensional fluid flow, heat transfer and solidification model, interfacial heat transfer model and two-dimensional stress-strain model to calculate the thickness distributions of liquid slag, solid slag and air gap in the ultra-high speed billet continuous casting mold, and analyzed the effects of melting temperature of mold flux and mold taper. Kölbl assessed the melting rate determination methods with respect to their ability to determine melting rates under service-related conditions and developed criteria for this purpose. Fifteen methods have been classified into two groups and the second group allow for the melting determination of mold powders in service. The restrictions for heating rate are determined from the conditions for Fourier and Biot numbers of varying test setups.
The last two articles are mainly related to the reaction between slag and steel for achieving better steel cleanliness and yield of valued elements. Dou et al. developed a thermodynamic model of the slag-steel reaction of austenitic stainless steel containing 5.0 wt% Si with CaF2-CaO-Al2O3-MgO-SiO2 slag based on the ion-molecular coexistence theory (IMCT) to investigate the deoxidation reaction and the oxygen control mechanism of the steel. The model was validated by the experimental data in laboratory. Optimized Al2O3 and basicity have been proposed to achieve low oxygen content in steel. Zhao et al. established a thermodynamic model for seven CaO-MgO-BaO-CaF2-SiO2-Al2O3-TiO2 ladle slags based on the Ion and Molecule Coexistence theory (IMCT) and validated the model using experimental data at 1873K for reducing the reaction between Ti in steel and slag to obtain better yields. The influences of CaO/SiO2, CaO/Al2O3, TiO2, BaO on slag thermodynamics and reaction between Ti steel and slag were investigated.
The four articles published in this Research Topic give us the glimpse of recent development in fluxes and slags for steel quality. We hope that these articles will be interesting and useful to the researchers in both academic unit and steel plants. We believe the research interests for fluxes and slags in process metallurgy will be continued and hope these articles in the Research Topic will stimulate some interests in this area.
All authors listed have made a substantial, direct, and intellectual contribution to the work and approved it for publication.
The authors declare that the research was conducted in the absence of any commercial or financial relationships that could be construed as a potential conflict of interest.
All claims expressed in this article are solely those of the authors and do not necessarily represent those of their affiliated organizations, or those of the publisher, the editors and the reviewers. Any product that may be evaluated in this article, or claim that may be made by its manufacturer, is not guaranteed or endorsed by the publisher.
Hanao, M., Kawamoto, M., and Yamanaka, A. (2012). Influence of mold flux on initial solidification of hypo-peritectic steel in a continuous casting mold. ISIJ Int. 52 (7), 1310–1319. doi:10.2355/isijinternational.52.1310
Scheller, P. R., and Shu, Q. (2014). Inclusion development in steel during ladle metallurgical treatment-A process simulation model–part: Industrial validation. steel Res. Int. 85 (8), 1310–1316. doi:10.1002/srin.201300375
Keywords: fluxes, steel quality, slag, slag metal reaction, mold powder
Citation: Shu Q, Li J and Yan B (2023) Editorial: Fluxes and steel quality. Front. Mater. 10:1145618. doi: 10.3389/fmats.2023.1145618
Received: 16 January 2023; Accepted: 18 January 2023;
Published: 24 January 2023.
Edited and reviewed by:
John L. Provis, The University of Sheffield, United KingdomCopyright © 2023 Shu, Li and Yan. This is an open-access article distributed under the terms of the Creative Commons Attribution License (CC BY). The use, distribution or reproduction in other forums is permitted, provided the original author(s) and the copyright owner(s) are credited and that the original publication in this journal is cited, in accordance with accepted academic practice. No use, distribution or reproduction is permitted which does not comply with these terms.
*Correspondence: Qifeng Shu, cWlmZW5nLnNodUBvdWx1LmZp
Disclaimer: All claims expressed in this article are solely those of the authors and do not necessarily represent those of their affiliated organizations, or those of the publisher, the editors and the reviewers. Any product that may be evaluated in this article or claim that may be made by its manufacturer is not guaranteed or endorsed by the publisher.
Research integrity at Frontiers
Learn more about the work of our research integrity team to safeguard the quality of each article we publish.