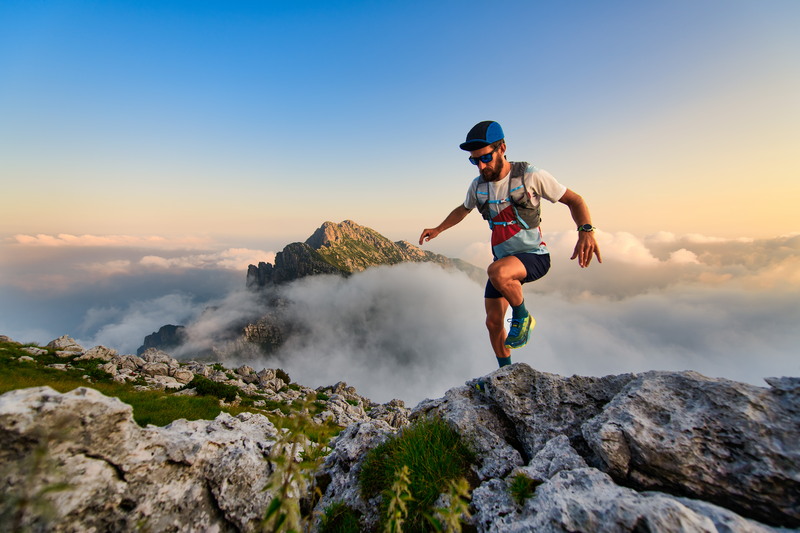
95% of researchers rate our articles as excellent or good
Learn more about the work of our research integrity team to safeguard the quality of each article we publish.
Find out more
MINI REVIEW article
Front. Mater. , 26 January 2023
Sec. Polymeric and Composite Materials
Volume 10 - 2023 | https://doi.org/10.3389/fmats.2023.1129676
This article is part of the Research Topic Additive Manufacturing for Polymers View all 10 articles
With the development of modern industry, the requirements for mechanical equipment are increasingly stringent, and increasing attention has been paid to reducing wear or lubrication in the movement of mechanical structural parts. Polymers are widely used in the field of mechanical structural parts due to their high processing performance and comprehensive performance. However, the relatively weak mechanical and tribological properties of polymers limit their further application in mechanical equipment lubrication. Incorporation of fillers is a common method to improve the friction properties of polymers. Among various fillers, carbon nanotubes (CNTs) are considered the ideal fillers to significantly improve the tribological properties of polymers. Therefore, this paper reviews the tribological properties of carbon nanotube modified polymer materials. The tribological wear mechanism of polymers and the influence of friction-reducing fillers on the tribological properties of polymers and the related lubrication mechanism explanation are outlined, and the factors influencing the tribological properties of composites by carbon nanotubes and the related lubrication mechanism explanation are analyzed. The presented review will be beneficial for the production of high-performance polymer nanocomposites.
In recent years, due to the development of society and the growing depletion of the traditional fossil energy, the requirements for energy saving and environmental protection of machinery and equipment have increase. Reducing wear loss and strengthen the lubricating between the mechanical moving parts are the important ways to achieve the energy saving and material loss, and therefore wear-resistant materials, as an essential component in the operation of equipment, have increasingly high requirements for their frictional properties (Lin et al., 2011; Kuang et al., 2022). The use of lubricating oil or the self-lubricating structural parts is a common method to reduce friction and anti-wear (Maruyama et al., 2017; John and Menezes, 2021). However, liquid lubricating materials are susceptible to environmental factors and lose their lubricating effects in the harsh scenarios such as high vacuum, high load and extreme high or low temperature environments (Kian et al., 2019). Therefore, the role of lubricated, wear-resistant solid materials in machinery and equipment is becoming increasingly important.
Polymers are compounds with relative molecular masses of several thousand to several million, with the excellent processing properties and comprehensive performance, widely used in people’s clothing, food, housing, transportation, various sectors of the national economy and cutting-edge technology (Moreno-Navarro et al., 2017; Grancarić et al., 2018; Afolabi et al., 2019; Wang et al., 2022b). Polymers have important applications in wear resistant parts such as bearings. For example, epoxy resins are used in machinery and equipment as bearing materials and friction members due to their high corrosion resistance, low coefficient of friction (COF) and high dimensional stability (Bashandeh et al., 2021), polytetrafluoroethylene (PTFE) is used as oil-free lubricated mechanical parts due to high chemical resistance and low COF (Jang et al., 2007), etc. However, pure polymers are often difficult to use directly as wear-resistant materials (Unal et al., 2010; Kaybal et al., 2021). For the one hand, the intrinsic low thermal conductivity and heat resistance of polymers may lead to the significant changes in their mechanical properties under high temperature conditions, thus reducing their wear resistance and service life. For the other hand, different polymers have different properties and also exhibit different frictional behaviors. For example, PTFE, ultra-high molecular weight polyethylene (UHMWPE) and polyurethane (PU) have excellent self-lubricating properties, but their mechanical properties and heat resistance are relatively poor. Polyimide (PI), poly (ether-ether-ketone) (PEEK) and epoxy resin (EP) have better mechanical and thermal properties, but their COF are relatively high (Maksimkin et al., 2017; Lim et al., 2018; Arif et al., 2020; Cui et al., 2022; Ding et al., 2022). Therefore, these problems limit the universality of polymer applications in the actual mechanical equipment.
Compounding fillers or blending other polymers is the most common and effective way to improve the tribological properties of polymers. PTFE, UHMWPE, Molybdenum disulfide (MoS2), SiC, carbon fiber, etc. Are used as lubricant materials or reinforcing fillers to improve the friction properties of polymers (Li et al., 2007; Chanda et al., 2019; Salem et al., 2019; Cao et al., 2020). Among them, CNTs are the ideal modifiers for the fabrication of polymer composites with high tribological properties due to their unique structures and excellent properties.
This paper reviews the tribological properties of carbon nanotube modified polymer materials. Firstly, the tribological wear mechanism of polymers, the friction-reducing fillers on the tribological properties of polymers and the related lubrication mechanism explanation are outlined. Then, the factors influencing the tribological properties of carbon nanotube/polymer composites and the related lubrication mechanism explanation are analyzed. Finally, the challenges and prospects of carbon nanotube/polymer composites with high tribological properties are summarized.
The wide range of variations in the mechanical properties of polymers and their strong dependence on temperature, deformation rate and the sensitivity of their failure process to environmental conditions make the polymer wear process much more complex compared to metals. Most scholars now classify this complex process into four types: adhesive wear, corrosive wear, abrasive wear and fatigue wear, and the various types of wear can undergo transformation (Lancaster, 1978).
In the relative motion of the friction vice, the surface of the friction couples, although the surface appears flat, the micro-surface is still uneven, which only shows the local contact. At this point, even if a smaller load is applied, the local stress on the actual contact surface is sufficient to cause plastic deformation, so that the oxide film on this part of the surface, etc. is squeezed, and the atoms of the two contact surfaces will be bonded due to bonding interaction. In the subsequent continuation of sliding, the adhesion point is sheared off and transferred to the counterpart surface, which comes off to form abrasive chips, resulting in the loss of material on the surface of the part (Archard, 1953; Belyi et al., 1977; Bijwe et al., 2001; Fukuda and Morita, 2017; Paul and Bhowmik, 2022). Abrasive wear is also caused when hard particles are present within the contact surface. The polymer undergoes a cutting process like planing under the action of abrasive particles, and this process can directly cause material removal and form a chip, which is micro cutting. In contrast, plowing is the extrusion of the polymer by abrasion to the sides, which does not directly cause material removal, but after several deformations can produce shedding and secondary chip formation. The rougher the counterpart surface, the greater the wear rate (WR) of the polymer (Dmitriyeva and Grayevskaya, 1983; Njoku et al., 2021). There may also be fatigue wear on the rough pair surface, when the friction pair slides against each other, the rough peaks of the soft surface are easily deformed, while the soft rough peaks break first under cyclic loading, resulting in a smoother surface. In this way, the contact state is no longer rough peak to rough peak, but the hard surface of the rough peak on the relatively smooth soft surface sliding. When the hard surface rough peak slides on the soft surface, the points on the soft surface are subjected to a cyclic load, which produces shear plastic deformation in the surface layer and accumulates, causing dislocation buildup at a certain depth under the surface, which leads to the formation of cracks or pores. When the crack is formed at a certain depth, according to the stress field analysis, the positive stress on the parallel surface prevents the crack from expanding in the depth direction, so the crack extends in the direction of the parallel surface at a certain depth. When the crack extends to a critical length, the material between the crack and the surface will flake off in the form of flakes of abrasive chips (Atkins et al., 1984; Bogdanovich, 2013; Hussain and Khan, 2022; Zhou et al., 2023). While the corrosive wear of polymers mainly takes place in the form of chemical degradation and oxidation, the high temperature generated at the sliding interface can cause severe degradation or softening of some polymers. In addition to temperature, many factors influence the chemical degradation of polymers, such as the catalytic effect of some oxygen species, the activation energy of polymer degradation and interfacial contact stress (Chen et al., 2014).
Based on the friction and wear behavior of polymers, incorporation of functional fillers to affect the friction process, leading to the improvement of tribological properties of polymer is an effective and viable way. In filler modified polymer composites, the fillers can be classified into reinforcing fillers and lubricating fillers according to their functions.
The lubricant fillers include the familiar PTFE, graphite, MoS2, etc (Lu and Friedrich, 1995; Qiao et al., 2007; Khare et al., 2015; Zalaznik et al., 2016; Chen et al., 2020; Li et al., 2022b). Gu et al. found that the wear surface of polymethyl methacrylate (PMMA) was uneven with many torn flakes and surface bumps, and the COF curve fluctuated in a wide range, while the wear surface of PTFE/PMMA composites filled with PTFE was relatively smooth with only slight scratches and a smoother COF curve, indicating that the friction process of PMMA-based composites is more stable by filling with PTFE. This is because the PTFE carbon chain backbone can only accommodate the bulk F atoms in a helical conformation, and the whole macromolecular chain presents a stiff rod-like structure. Due to the strong electrostatic repulsive force of F atoms around the carbon chain and the bulk effect of fluorine atoms, the smooth linear chains without branching side chains are connected by weak van der Waals forces, and the PTFE macromolecule chains are very easy to unwind and slip, and form transfer film and reduce the COF, but the filling of PTFE will make the hardness of the composite material decrease and cause the increase of WR (Gu et al., 2018). Because of the weak van der Waals force between the layers and interlaminar sliding occurs easily, graphite was considered as a typical lubricant filler. Zhang et al. found that the COF of graphite/PTFE composites decreased gradually with the increase of graphite content. During the sliding process, the graphite flakes become thinner and fall off, exposing the surface of the friction substrate, while the peeled graphite micro flakes form a hard transfer film on the surface of the friction substrate, which can effectively reduce the COF (Zhang et al., 2008). The other lubricant fillers such as MoS2 (Yang et al., 2020), Hexagonal boron nitride (h-BN) (Rao et al., 2021), Zirconium phosphate (ZrP) (Cai et al., 2023), etc. were also reported to improve the tribological properties of polymers by forming the complete transfer film on the surface of the friction substrate, thus reducing the COF of the composite. However, the addition of lubricant fillers adversely affects the WR. The increase of WR can be attributed to the decrease in the hardness of the resultant composite caused by the addition of the lubricant fillers. The wear resistance of the composites depends to some extent on the hardness of the composites, so the decrease in hardness will cause a decrease in the wear resistance of the composites.
Unlike abrasion-reducing fillers, the addition of reinforcing fillers aims to improve the mechanical properties of the composite material such as hardness, strength, impact resistance, creep resistance, etc. (Lustiger et al., 1990; Friedrich et al., 1993; Friedrich et al., 1995). The elastic modulus and tensile strength of the reinforced filler are generally higher than those of the polymer, which in turn leads to filler composite reinforcement (Papon et al., 2012). When the complex is subjected to external stress, the stress is transferred to the filler particles through the resin-filler phase interface, making the filler particles the main stressed phase. The stress transfer mechanism is applicable to both zero-dimensional, one-dimensional and two-dimensional nano-reinforced fillers (Papageorgiou et al., 2020). The improved mechanical properties of polymeric materials increase the load-bearing capacity of polymeric materials, meaning that the material is less prone to plastic deformation and spalling during friction. At the same time, it can maintain the structural integrity of the composite material under high loads (Su et al., 2016). In addition, the excellent mechanical properties significantly inhibit the creation and spread of cracks on the wear surface, thus improving wear resistance (Huang et al., 2013). He et al. found that Perfluoroalkoxy filled with Al2O3 particles exhibited ultra-high load-bearing capacity and low COF under sliding conditions (He et al., 2017). Li et al. demonstrated that glass fiber incorporation can substantially improve the mechanical properties of the composites such as tensile strength, tensile modulus, flexural strength, and flexural modulus, and at the same time, the composites exhibit excellent wear resistance (Li et al., 2013). This is due to the strong interfacial bonding between glass fibers and polyether ether ketone, which leads to the interruption of the fiber removal process and causes the accumulation of abrasive particles near the glass fibers, thus avoiding the abrasion of the matrix resin. Nemati et al. studied the effect of graphene on the wear resistance of PTFE was investigated, and the results showed that the addition of graphene effectively improved the wear resistance of the PTFE coating. When graphene was added up to 15 vol%, the friction factor and WR were significantly reduced to 0.1 and 0.65 × 10−9mm3/(N-m), respectively (Nemati et al., 2016).
Although remarkable achievements have been made in the researches of the friction properties of polymer composites, there are still some technical problems. The addition of the solid lubricating fillers can significantly reduce the friction coefficient of polymer composites, but the friction loss effect is not obvious due to the adverse effects on the hardness, modulus and other properties of polymer composites. With regards to the reinforced fillers, they can significantly improve the mechanical properties of polymer composites, but the large amounts of loadings are often needed to achieve the required friction properties, which may affect other properties of the polymer. Therefore, it is still important to research the new wear-resistant fillers.
CNTs are an ideal one-dimensional nanomaterial currently prepared artificially as hollow cylinders enclosed by concentric graphitic surfaces, which exhibit many unique physical properties due to the uniqueness of their own compositional structure (Jun and Gaind, 2015; Zang et al., 2015). CNTs have strong wear resistance and self-lubricating properties, with a wear resistance 100 times higher than that of bearing steel and a COF of 0.06–0.1. CNTs also have excellent Thermal stability and electrical conductivity (He et al., 2018; Cui et al., 2021). CNTs have received a great deal of attention from researchers since their introduction in 1991.
Due to the unique structure and excellent properties, CNTs were introduced to modify polymer for improving the properties of polymer such as mechanical properties, electrical properties, and thermal stability, which have been confirmed by the previous reports (Kotop et al., 2021; Parnian and D’Amore, 2021). Kang et al. prepared CNT/PP composites by melt injection molding method. It was found that the thermal degradation temperature of PP increased by 50°C after filling with CNT, and the thermal conductivity and tensile strength increased with the increase of CNT content (Kang et al., 2010). Liang et al. showed that the flexural modulus of PP increased with increasing CNTs content when filled with CNTs, indicating that CNTs can effectively improve the flexural stiffness of the polymer (Liang et al., 2018). Also, the fracture impact strength of CNT/PP with 4% wt. was increased by 40% compared to pure PP. In addition to this, the addition of CNTs to rubber materials can also reduce the adhesion strength of ice to rubber materials, allowing rubber-based components to work in extreme weather (Valentini et al., 2018). Therefore, the addition of CNTs is an effective method for developing high-performance polymer nanocomposites.
For the moment, the role of CNTs in wear reduction and wear resistance is also very impressive, mainly as the reinforcement of complexes and additives to lubricating fluids, and the like (Wang et al., 2020; Li et al., 2022a; Wang et al., 2022a). Chen et al. prepared CNTs-reinforced EP composites using oligoaniline assisted dispersion method and investigated their tribological properties (Chen et al., 2017). It was found that the CNTs of the composites had good dispersion, based on which the crystallinity and tribological wear properties of the composites were improved, and the composites had lower WR and COF. Gao et al. showed that significantly lower COF for CNT bio-lubricants compared to dry conditions, showing optimal and durable antifriction characteristics (Gao et al., 2021). It was beneficial to suppressing the removal of multifiber block debris, tensile fracture, and tensile-shear fracture, with the advantages of tribological properties and material removal behavior. CNT improves the wear resistance of polymers more than some other fillers. Remanan et al. added CNT and B4C to Poly Aryl Ether Ketone. Comparing B4C, the WR of the composites was reduced by 34% with the addition of CNT (Remanan et al., 2017). Ren et al. added CNT and Mo2S to EP. at the same 4% content, the WR of the CNT/EP composite was 50% less than that of the Mo2S/EP composite (Ren et al., 2019). Surya et al. used fibers to reinforce natural rubber materials. CNT and graphite nanofibers reinforced compounds improved the wear resistance simultaneously by 43% and 33% respectively, while SiC and aramid nanofibers improved it by 10% and 8% respectively (Surya et al., 2022). Recent researches on the tribological performance of CNT/polymer nanocomposites were summarized in Table 1.
The reason why CNT improves the frictional properties of polymers is not just a single effect like other conventional fillers, but the result of a synergistic effect of several factors (Figure 1). First of all, due to the special characteristics of the CNT structure, a carbon film is formed regardless of whether the CNT is attached to the polymer matrix or when it falls into the gap of the friction substrate due to wear. This hard and self-lubricating carbon film effectively avoids direct scraping of the friction substrate and reduces the COF and WR (Zhang et al., 2020; Dwivedi et al., 2022). In the next place, when the CNT/polymer composite is subjected to stress, it is transferred to the CNT through the bonding interface, making the CNT the main stressor. Due to the ultra-high aspect ratio and strength of CNT, the strength of the composite is also enhanced, which is less prone to plastic deformation and improves the wear resistance of the polymer (Zare and Rhee, 2020; Duan et al., 2021). Meanwhile, when the composite material produces microcracks due to friction, CNT can effectively inhibit the growth of microcracks, reduce grinding chips, and improve the wear resistance of the material (Bahramnia et al., 2021). The CNT incorporation also improves the thermal conductivity and thermal stability of the composite material, preventing it from softening under the high temperature conditions of frictional heating and failure, which affects wear resistance and service life (Shimizu et al., 2020; Yan et al., 2020).
FIGURE 1. Friction reduction models of HDPE (a-1, a-2, a-3), HDPE with moderate 5p [6-xujyhof MWCNTs (b-1, b-2, b-3), and excess MWCNTs (c-1, c-2, c-3) (Wu et al., 2021).
The improvements of the tribological properties of polymer composites by incorporation of CNTs had been confirmed by the previous researches, but in fact, some important factors in CNTs/polymer composites needed to be clarified.
CNTs are classified as multi-walled carbon nanotube (MWCNT) and single walled carbon nanotube (SWCNT). Meanwhile, the same type of CNTs have different lengths and diameters. Adrian Cotet et al. compared the effect of SWCNT and MWCNT on the tribological properties of vinyl ester nanocomposites (Cotet et al., 2019). MWCNT decreased the COF of nanocomposites, but the addition of SWCNT increased the COF at high sliding velocities. It was shown that the presence of MWCNT in the fragments contributed to the lubrication effect due to the strong interaction of MWCNT with the polymer matrix, while SWCNT in the fragments played the role of a third body in the sliding motion. Liu et al. introduced two different diameters of MWCNTs to bismaleimide resin, and the significant difference on WR and COF between the resultant MWCNT/bismaleimide composites was observed. Li et al. added CNT to grease to prepare lithium-based grease and investigated the effect of tube diameter and tube length on its frictional properties (Li et al., 2019). The results show that the tube diameter of CNTs has little effect on the friction reduction performance of CNTs, and the COF becomes slightly larger when the tube diameter is larger, and the COF curves all fluctuate not much. However, the length of CNTs has some influence on the friction performance of grease, and the WR is lower when the tube is longer. Due to the strong interaction between CNTs, they are very agglomerated when added to the matrix of polymers, leading to the degradation of composite properties. Therefore, achieving uniform dispersion of CNTs in the matrix resin is the key to prepare high-performance composites. Simultaneously, there are large differences in the properties of the polymer matrix and CNTs, and the regions connecting the transition interact chemically or physically to form interfaces with different properties, and the interface state of CNTs and the matrix has a correlation with the friction properties.
As described above, the interaction between CNTs and polymer matrix is an important factor in the tribological properties of CNTs/polymer composites. Therefore, it can be seen that the modification of CNT has a great influence on the friction properties of the composites. Nowadays, the commonly used modification methods of CNT are covalent bond modification and non-covalent bond modification (Bhattacharyya et al., 2004; Lou et al., 2004; Bahun et al., 2006; Xu et al., 2007; Yan et al., 2011; Zhang et al., 2012; Amirkhani et al., 2020; Atif et al., 2020; Kim et al., 2021). Bhanu et al. explored the changes in the frictional properties of MWCNTs by different functionalizations of MWCNTs, which were prepared into composites with polyformaldehyde (POM), respectively, and found that the WR and COF of 0.5% wt. silylated MWCNTs/POM composites were reduced the most, compared with pure POM, followed by aminated, carbonylated, acid-treated and finally pure MWCNT, which can be attributed to the better dispersion of silylated MWCNTs and stronger interfacial bonding between silylated MWCNTs and POM matrix. However, the excessive modification can greatly destroy the graphite structure of CNTs, leading to the significantly decrease of the intrinsic mechanical properties of CNTs. Therefore, the modified method and the degree of modification needed to be optimized (Goriparthi et al., 2019).
In addition to the type and modification of CNT, the CNT content in the composites also affects the frictional properties of the polymers. Chopra et al. prepared MWCNT/butylene polyterephthalate (PBT) composites with low filler content and investigated their frictional properties using melt compounding method (Chopra et al., 2017). The results showed that the COF of the composites decreased with the increase of carbon nanotube content and the effect of load was not significant. As the carbon nanotube content increased, the wear of the composites was the first to decrease and then to increase. As a matter of fact, the loading of CNTs often relates the dispersion of CNTs in polymer matrix. Severe agglomerates usually observed in the high loading of CNTs/polymer composites fabricated by traditional dispersion technologies, which cause the inefficient improvement of CNTs in the tribological properties of polymer composites. However, Han et al. made a buckypaper (BP) of MWCNT, into EP to improve the frictional properties of BP/EP composites, while solving the dispersion problem of MWCNT with high loading (about 40% wt.). Under the given experimental conditions, BP/EP composites have a lower COF and wear than pure EP. In the case of ozone-modified BP/EP, it has better frictional properties up to four times that of pure EP (Han et al., 2015). Therefore, the method such as pre-building buckypaper may provide a viable way to fabricate the high loading of CNTs/polymer composites with the homogeneous dispersion, which may have unexpected tribological properties.
Comparing with the other fillers, such as PTFE, graphite, UHMWPE, carbon fiber etc., CNTs exhibit some unique features, i) CNTs not only show the self-lubricating effect (low COF), but also strengthen the polymer, indicating the CNTs/polymer composites have low COF and mass loss, and these excellent overall performances make CNTs/polymer composites are more adaptable for mechanical parts (Golchin et al., 2016; Sakka et al., 2017; Chen et al., 2018). ii) CNTs also are other fillers for fabricating functional polymer conposites, for example, the network of CNTs can act as the electrical conductive paths and mass transfer barrier for improving the electrical conductivity, electromagnetic shielding, fire retardance and water-resistance of polymer composites (Kashiwagi et al., 2005; Spitalsky et al., 2010; Xia et al., 2022).
According to literature, the incorporation of CNTs can significantly improve the tribological properties of polymer, and the improvement mechanism was researched systematically. However, some problems of the application of CNTs in polymer are still needed to be further clarified. 1) The improvement mechanism of CNTs in the tribological properties of polymer is still not entirely clear, especially in the more complex scenario in terms of wear mechanism and wear-debris formation. The tribological behavior of CNTs/polymer composites is influenced by many factors, and it is difficult to evaluate these factors. Therefore, how to quantity analysis the influences of the factor may help to comprehend the improvement mechanism. 2) The dispersion, appropriate modification and high loading of CNTs are often difficult to achieve. Because of the strong interaction between the nanotubes, CNTs are difficult to achieve the prospective dispersion and the high loadings, leading to the low efficiency of improvements of CNTs in polymer.
Overall, the field of high wear resistant CNTs/polymer composites is still in its infancy. The future development trend of high wear resistant CNTs/polymer composites should focus on refining the theory, optimizing the preparation process (the dispersion and modification of CNTs methods) and achieving the higher loading. Furthermore, the high wear resistant CNTs/polymer composites are rarely in practical applications at present, which means and they have great practical value and broad development prospects.
In order to meet the current manufacturing, the requirements for wear resistance of polymers are increasing, and the design of composite materials with low COF and low WR is of practical importance for energy saving and safety. Filler modification has been the mainstream method to improve the wear resistance of polymers. Since the introduction of CNT, it has been widely used in the research of improving the wear resistance of polymers because of its unique physical properties and advantages. Nowadays, people have gradually overcome the difficulties in the application of CNT and understand its wear resistance mechanism. In the future, starting from the physical and chemical structure of the polymer itself, it will be an important research direction for polymer-based composites to establish the linkage and mechanism between the maintenance of mechanical strength and tribological applications during the service of CNT/polymer, and to provide scientific data and theoretical guidance for the long-term application of polymer lubricant materials.
All authors listed have made a substantial, direct, and intellectual contribution to the work and approved it for publication.
This research was financially supported by the Open Project Program of Fujian Key Laboratory of Novel Functional Textile Fibers and Materials, Minjiang University, China (No. FKL7FM 2010), National Natural Science Foundation of China (52103356), Fujian Provincial Department of Science and Technology (2020H0045, 2020J01770) and the Bureau of Science and Technology of Quanzhou (2021C009R, 2020C060).
The authors declare that the research was conducted in the absence of any commercial or financial relationships that could be construed as a potential conflict of interest.
All claims expressed in this article are solely those of the authors and do not necessarily represent those of their affiliated organizations, or those of the publisher, the editors and the reviewers. Any product that may be evaluated in this article, or claim that may be made by its manufacturer, is not guaranteed or endorsed by the publisher.
Adarmanabadi, S. R., Jafari, M., Farrash, S. M. H., Heidari, M., and Zheng, J. (2021). Effect of nano clay, nano-graphene oxide and carbon nanotubes on the mechanical and tribological properties of crosslinked epoxy nanocomposite. Plos One 16, e0259401. doi:10.1371/journal.pone.0259401
Afolabi, L. O., Ariff, Z. M., Megat-Yusoff, P. S. M., Al-Kayiem, H. H., Arogundade, A. I., and Afolabi-Owolabi, O. T. (2019). Red-mud geopolymer composite encapsulated phase change material for thermal comfort in built-sector. Sol. Energy 181, 464–474. doi:10.1016/j.solener.2019.02.029
Agrawal, S., Singh, N. K., Upadhyay, R. K., Singh, G., Singh, Y., Singh, S., et al. (2021). Effect of different lubricating environment on the tribological performance of cnt filled glass reinforced polymer composite. Materials 14, 2965. doi:10.3390/ma14112965
Ahmed Baduruthamal, Z., Mohammed, A. S., Kumar, A. M., Hussein, M. A., and Al-Aqeeli, N. (2019). Tribological and electrochemical characterization of uhmwpe hybrid nanocomposite coating for biomedical applications. Materials 12, 3665. doi:10.3390/ma12223665
Ali, A. B., Abdul Samad, M., and Merah, N. (2017). Uhmwpe hybrid nanocomposites for improved tribological performance under dry and water-lubricated sliding conditions. Tribol. Lett. 65, 102–110. doi:10.1007/s11249-017-0884-y
Ali, S. D., Ferda, M., and Harun, M. (2014). Mechanical and tribological performances of polypropylene composites containing multi-walled carbon nanotubes. Int. J. Surf. Sci. Eng. 8, 292. doi:10.1504/ijsurfse.2014.065831
Amirkhani, F., Mosadegh, M., Asghari, M., and Parnian, M. J. (2020). The beneficial impacts of functional groups of cnt on structure and gas separation properties of peba mixed matrix membranes. Polym. Test. 82, 106285. doi:10.1016/j.polymertesting.2019.106285
Archard, J. F. (1953). Contact and rubbing of flat surfaces. J. Appl. Phys. 24, 981–988. doi:10.1063/1.1721448
Arif, M. F., Alhashmi, H., Varadarajan, K. M., Koo, J. H., Hart, A. J., and Kumar, S. (2020). Multifunctional performance of carbon nanotubes and graphene nanoplatelets reinforced peek composites enabled via fff additive manufacturing. Compos. Part B, Eng. 184, 107625. doi:10.1016/j.compositesb.2019.107625
Ashok Gandhi, R., Palanikumar, K., Ragunath, B. K., and Paulo Davim, J. (2013). Role of carbon nanotubes (cnts) in improving wear properties of polypropylene (pp) in dry sliding condition. Mater. Eng. 48, 52–57. doi:10.1016/j.matdes.2012.08.081
Atif, M., Afzaal, I., Naseer, H., Abrar, M., and Bongiovanni, R. (2020). Review-surface modification of carbon nanotubes: A tool to control electrochemical performance. Ecs J. Solid State S. C. 9, 041009. doi:10.1149/2162-8777/ab8929
Atkins, A. G., Omar, M. K., and Lancaster, J. K. (1984). Wear of polymers. J. Mater. Sci. Lett. 3, 779–782. doi:10.1007/BF00727971
Bahramnia, H., Semnani, H. M., Habibolahzadeh, A., and Abdoos, H. (2021). Epoxy/polyurethane hybrid nanocomposite coatings reinforced with mwcnts and sio2 nanoparticles: Processing, mechanical properties and wear behavior. Surf. Coat. Tech. 415, 127121. doi:10.1016/j.surfcoat.2021.127121
Bahun, G. J., Wang, C., and Adronov, A. (2006). Solubilizing single-walled carbon nanotubes with pyrene-functionalized block copolymers. J. Polym. Sci. Part A, Polym. Chem. 44, 1941–1951. doi:10.1002/pola.21308
Bashandeh, K., Tsigkis, V., Lan, P., and Polycarpou, A. A. (2021). Extreme environment tribological study of advanced bearing polymers for space applications. Tribol. Int. 153, 106634. doi:10.1016/j.triboint.2020.106634
Belyi, V. A., Sviridyonok, A. I., Smurugov, V. A., and Nevzorov, V. V. (1977). Adhesive wear of polymers. J. Lubr. Technol. 99, 396–400. doi:10.1115/1.3453232
Bhattacharyya, S., Kymakis, E., and Amaratunga, G. A. J. (2004). Photovoltaic properties of dye functionalized single-wall carbon nanotube/conjugated polymer devices. Chem. Mater 16, 4819–4823. doi:10.1021/cm0496063
Bijwe, J., Indumathi, J., John Rajesh, J., and Fahim, M. (2001). Friction and wear behavior of polyetherimide composites in various wear modes. Wear 249, 715–726. doi:10.1016/S0043-1648(01)00696-2
Bogdanovich, P. N. (2013). Fatigue wear of materials under dynamic contact loading. J. Frict. Wear+ 34, 349–357. doi:10.3103/S1068366613050036
Cai, T., Zhan, S. P., Yang, T., Jia, D., Cheng, B. X., Tu, J. S., et al. (2023). Molecular dynamics simulation of α-ZrP/uhmwpe blend composites containing compatibilizer and its tribological behavior under seawater lubrication. J. Appl. Polym. Sci. 140, e53321. doi:10.1002/app.53321
Cao, X. W., Li, Y. P., and He, G. J. (2020). Fabrication of self-lubricating porous uhmwpe with excellent mechanical properties and friction performance via rotary sintering. Polymers-Basel 12, 1335. doi:10.3390/polym12061335
Chanda, A., Sinha, S. K., and Datla, N. V. (2019). Tribological studies of epoxy-carbon nanofiber composites-effect of nanofiber alignment using ac electric field. Tribol. Int. 138, 450–462. doi:10.1016/j.triboint.2019.06.014
Chang, Q. X., Wang, K. S., and Zhao, H. J. (2013). The friction and wear properties of short carbon/cnt/pa6 hybrid composites under dry sliding conditions. Int. J. Polym. Mater. 62, 540–543. doi:10.1080/00914037.2011.641629
Chen, B. B., Li, X., Jia, Y. H., Xu, L., Liang, H. Y., Li, X. F., et al. (2018). Fabrication of ternary hybrid of carbon nanotubes/graphene oxide/mos2 and its enhancement on the tribological properties of epoxy composite coatings. Compos. Part A, Appl. Sci. Manuf. 115, 157–165. doi:10.1016/j.compositesa.2018.09.021
Chen, B., Chen, J., Li, J. Y., Tong, X., Zhao, H. C., and Wang, L. P. (2017). Oligoaniline assisted dispersion of carbon nanotubes in epoxy matrix for achieving the nanocomposites with enhanced mechanical, thermal and tribological properties. Chin. J. Polym. Sci. 35, 446–454. doi:10.1007/s10118-017-1911-z
Chen, J. H., Trevarthen, J. A., Deng, T., Bradley, M. S. A., Rahatekar, S. S., and Koziol, K. K. K. (2014). Aligned carbon nanotube reinforced high performance polymer composites with low erosive wear. Compos. Part A, Appl. Sci. Manuf. 67, 86–95. doi:10.1016/j.compositesa.2014.08.009
Chen, W., Wang, Z. X., Liu, X., Jia, J. H., and Hua, Y. (2020). Effect of load on the friction and wear characteristics of si3n4-hbn ceramic composites sliding against peek in artificial seawater. Tribol. Int. 141, 105902. doi:10.1016/j.triboint.2019.105902
Chopra, S., Batthula, S., Deshmukh, K., and Peshwe, D. (2017). Tribological behaviour of multi-walled carbon nanotubes (mwcnt) filled polybutylene terephthalate (pbt) nanocomposites. T Indian I Met. 70, 801–807. doi:10.1007/s12666-017-1055-4
Chopra, S., Deshmukh, K. A., Deshmukh, A. D., and Peshwe, D. R. (2018). Functionalization and melt-compounding of mwcnts in pa-6 for tribological applications. IOP Conf. Ser. Mater. Sci. Eng. 346, 012005. doi:10.1088/1757-899X/346/1/012005
Cotet, A., Bastiurea, M., Andrei, G., Cantaragiu, A., and Hadar, A. (2019). Dry sliding friction analysis and wear behavior of carbon nanotubes/vinylester nanocomposites, using pin-on-disc test. Rev. Chim-Bucharest 70, 3592–3596. doi:10.37358/RC.19.10.7603
Cui, J., Zhao, J., Wang, S., Wang, Y., and Li, Y. (2021). Effects of carbon nanotubes functionalization on mechanical and tribological properties of nitrile rubber nanocomposites: Molecular dynamics simulations. Comp. Mater Sci. 196, 110556. doi:10.1016/j.commatsci.2021.110556
Cui, Y., Li, C., Li, Z. L., Yao, X. J., Hao, W., Xing, S. L., et al. (2022). Deformation-driven processing of cnts/peek composites towards wear and tribology applications. Coatings (Basel) 12, 983. doi:10.3390/coatings12070983
Deenoi, S., and Dechjarern, S. (2019). Effect of cryogenic and coating treatments on wear and friction between titanium alloy and uhmwpe for knee implants. Mater. today Proc. 17, 1939–1948. doi:10.1016/j.matpr.2019.06.237
Ding, C. J., Xing, Z. Y., Wang, Z. H., Qin, Z. Z., Wang, J., Zhao, X. L., et al. (2022). The comprehensive effect of tensile strength and modulus on abrasive wear performance for polyurethanes. Tribol. Int. 169, 107459. doi:10.1016/j.triboint.2022.107459
Dmitriyeva, T. V., and Grayevskaya, L. M. (1983). The processes accompanying metal wear in polymer-containing abrasive media. Wear 84, 353–359. doi:10.1016/0043-1648(83)90275-2
Duan, K., Li, L., Wang, F., Liu, S., Hu, Y., and Wang, X. (2021). New insights into interface interactions of cnt-reinforced epoxy nanocomposites. Compos Sci. Technol. 204, 108638. doi:10.1016/j.compscitech.2020.108638
Dwivedi, U. K., Singh, S., Shukla, S. C., and Hashmi, S. A. R. (2022). Investigation on tribo-characteristics of calotropis gigantea fiber-reinforced-cnt modified polymer composites. Polym. Bull. Berl. Ger. 79, 697–707. doi:10.1007/s00289-020-03532-6
Friedrich, K., Lu, Z., and Häger, A. M. (1993). Overview on polymer composites for friction and wear application. Theor. Appl. Fract. Mec. 19, 1–11. doi:10.1016/0167-8442(93)90029-b
Friedrich, K., Lu, Z., and Hager, A. M. (1995). Recent advances in polymer composites' tribology. Wear 190, 139–144. doi:10.1016/0043-1648(96)80012-3
Fukuda, K., and Morita, T. (2017). Physical model of adhesive wear in early stage of sliding. Wear 376-377, 1528–1533. doi:10.1016/j.wear.2017.01.078
Gao, T., Zhang, Y. B., Li, C. H., Wang, Y., An, Q. L., Liu, B., et al. (2021). Grindability of carbon fiber reinforced polymer using cnt biological lubricant. Sci. Rep-Uk 11, 22535. doi:10.1038/s41598-021-02071-y
Golchin, A., Wikner, A., and Emami, N. (2016). An investigation into tribological behaviour of multi-walled carbon nanotube/graphene oxide reinforced uhmwpe in water lubricated contacts. Tribol. Int. 95, 156–161. doi:10.1016/j.triboint.2015.11.023
Goriparthi, B. K., Naveen, P. N. E., Ravi Sankar, H., and Ghosh, S. (2019). Effect of functionalization and concentration of carbon nanotubes on mechanical, wear and fatigue behaviours of polyoxymethylene/carbon nanotube nanocomposites. B Mater Sci. 42, 98–12. doi:10.1007/s12034-019-1746-z
Grancarić, A. M., Jerković, I., Koncar, V., Cochrane, C., Kelly, F. M., Soulat, D., et al. (2018). Conductive polymers for smart textile applications. J. Industrial Text. 48, 612–642. doi:10.1177/1528083717699368
Gu, D. P., Zhang, L. X., Chen, S. W., Song, K. F., and Liu, S. Y. (2018). Significant reduction of the friction and wear of pmma based composite by filling with ptfe. Polymers-Basel 10, 966. doi:10.3390/polym10090966
Han, J. H., Zhang, H., Chu, P. F., Imani, A., and Zhang, Z. (2015). Friction and wear of high electrical conductive carbon nanotube buckypaper/epoxy composites. Compos Sci. Technol. 114, 1–10. doi:10.1016/j.compscitech.2015.03.012
He, Y., Farokhzadeh, K., and Edrisy, A. (2017). Characterization of thermal, mechanical and tribological properties of fluoropolymer composite coatings. J. Mater Eng. Perform. 26, 2520–2534. doi:10.1007/s11665-017-2690-y
He, Y., Luo, H. X., Jin, H. H., Qiu, S., and Li, Q. W. (2018). Thiophene-containing polymer on sorting semiconducting single-walled carbon nanotubes. Polym. (Guilford) 159, 59–63. doi:10.1016/j.polymer.2018.11.011
Huang, T., Li, T. S., Xin, Y. S., Liu, P., and Su, C. (2013). Mechanical and tribological properties of hybrid fabric–modified polyetherimide composites. Wear 306, 64–72. doi:10.1016/j.wear.2013.06.010
Hussain, M. Z., and Khan, S. (2022). Fabrication and tribological behavior of mno2/epoxy nanocomposites. High. Perform. Polym. 34, 742–758. doi:10.1177/09540083221079510
Jang, I., Burris, D. L., Dickrell, P. L., Barry, P. R., Santos, C., Perry, S. S., et al. (2007). Sliding orientation effects on the tribological properties of polytetrafluoroethylene. J. Appl. Phys. 102, 123509. doi:10.1063/1.2821743
John, M., and Menezes, P. L. (2021). Self-lubricating materials for extreme condition applications. Materials 14, 5588. doi:10.3390/ma14195588
Jun, L., and Gaind, P. P. (2015). Advanced physical chemistry of carbon nanotubes. Annu. Rev. Phys. Chem. 66, 331–356. doi:10.1146/annurev-physchem-040214-121535
Kang, C. H., Yoon, K. H., Park, Y., Lee, D., and Jeong, S. (2010). Properties of polypropylene composites containing aluminum/multi-walled carbon nanotubes. Compos. Part A, Appl. Sci. Manuf. 41, 919–926. doi:10.1016/j.compositesa.2010.03.011
Kashiwagi, T., Douglas, J. F., Du, F., Winey, K. I., Harris, R. H., and Shields, J. R. (2005). Nanoparticle networks reduce the flammability of polymer nanocomposites. Nat. Mater 4, 928–933. doi:10.1038/nmat1502
Kaybal, H. B., Ulus, H., and Avcı, A. (2021). Seawater aged basalt/epoxy composites: Improved bearing performance with halloysite nanotube reinforcement. Fiber Polym. 22, 1643–1652. doi:10.1007/s12221-021-0671-0
Khare, N., Limaye, P. K., Soni, N. L., and Patel, R. J. (2015). Friction and wear characteristics of peek and peek composites in water lubricated slow speed sliding. Tribol. online 10, 84–90. doi:10.2474/trol.10.84
Kian, B., Pixiang, L., Jacob, L. M., and Andreas, A. P. (2019). Tribological performance of graphene and ptfe solid lubricants for polymer coatings at elevated temperatures. Tribol. Lett. 67, 99. doi:10.1007/s11249-019-1212-5
Kim, Y., Kim, Y., Park, J., Han, S. W., and Kim, S. M. (2021). Purification effect of carbon nanotube fibers on their surface modification to develop a high-performance and multifunctional nanocomposite fiber. Carbon (New York) 173, 376–383. doi:10.1016/j.carbon.2020.11.026
Kotop, M. A., El-Feky, M. S., Alharbi, Y. R., Abadel, A. A., and Binyahya, A. S. (2021). Engineering properties of geopolymer concrete incorporating hybrid nano-materials. Ain Shams Eng. J. 12, 3641–3647. doi:10.1016/j.asej.2021.04.022
Kuang, W. J., Miao, Q., Ding, W. F., and Li, H. N. (2022). A short review on the influence of mechanical machining on tribological and wear behavior of components. Int. J. Adv. Manuf. Tech. 120, 1401–1413. doi:10.1007/s00170-022-08895-w
Lancaster, J. K. (1978). Wear mechanisms of metals and polymers. Trans. IMF 56, 145–153. doi:10.1080/00202967.1978.11870471
Li, E. Z., Guo, W. L., Wang, H. D., Xu, B. S., and Liu, X. T. (2013). Research on tribological behavior of peek and glass fiber reinforced peek composite. Phys. Procedia 50, 453–460. doi:10.1016/j.phpro.2013.11.071
Li, H., Ma, Y., Li, Z., Cui, Y., and Wang, H. (2018). Synthesis of novel multilayer composite microcapsules and their application in self-lubricating polymer composites. Compos Sci. Technol. 164, 120–128. doi:10.1016/j.compscitech.2018.05.042
Li, M., Jiang, J., Lu, X., Gao, J., Jiang, D., and Gao, L. (2022a). Natural rubber reinforced with super-hydrophobic multiwalled carbon nanotubes: Obvious improved abrasive resistance and enhanced thermal conductivity. J. Polym. Eng. 42, 688–694. doi:10.1515/polyeng-2021-0233
Li, M. X., Deng, X. Q., Guo, P. K., Xu, P., and Tian, H. Y. (2019). Tribological properties and mechanism of carbon nanotubes in grease. Lubr. Eng. 44, 120–126. doi:10.3969/j.issn.0254-0150.2019.04.020
Li, W. J., Cui, S. H., and Han, J. M. (2007). Sliding wear resistance of metal-ptfe self-lubricant material. Hang kong cai liao xue bao 27, 75–78. doi:10.1016/S1001-6058(07)60030-4
Li, Y., Chen, Y., Guo, Y., Bian, D., and Zhao, Y. (2022b). Tribological behavior of peek/ptfe composites reinforced with carbon fibers and graphite. Materials 15, 7078. doi:10.3390/ma15207078
Liang, J. Z., Zou, S. Y., and Du, Q. (2018). Impact and flexural properties of polypropylene composites reinforced with multi-walled carbon nanotubes. Polym. Test. 70, 434–440. doi:10.1016/j.polymertesting.2018.07.029
Lim, W. S., Khadem, M., Anle, Y., and Kim, D. E. (2018). Fabrication of polytetrafluoroethylene–carbon nanotube composite coatings for friction and wear reduction. Polym. Compos. 39, E710–E722. doi:10.1002/pc.24135
Lin, L., Kim, D., Kim, W., and Jun, S. (2011). Friction and wear characteristics of multi-layer graphene films investigated by atomic force microscopy. Surf. Coat. Tech. 205, 4864–4869. doi:10.1016/j.surfcoat.2011.04.092
Lou, X. D., Daussin, R., Cuenot, S., Duwez, A. S., Pagnoulle, C., Detrembleur, C., et al. (2004). Synthesis of pyrene-containing polymers and noncovalent sidewall functionalization of multiwalled carbon nanotubes. Chem. Mater 16, 4005–4011. doi:10.1021/cm0492585
Lu, Z. P., and Friedrich, K. (1995). On sliding friction and wear of peek and its composites. Wear 181, 624–631. doi:10.1016/0043-1648(95)90178-7
Lustiger, A., Uralil, F. S., and Newaz, G. M. (1990). Processing and structural optimization of peek composites. Polym. Compos. 11, 65–75. doi:10.1002/pc.750110109
Maksimkin, A. V., Nematulloev, S. G., Chukov, D. I., Danilov, V. D., and Senatov, F. S. (2017). Bulk oriented uhmwpe/fmwcnt films for tribological applications. Polymers-Basel 9, 629. doi:10.3390/polym9110629
Manoj Kumar, R., Rajesh, K., Haldar, S., Gupta, P., Murali, K., Roy, P., et al. (2019). Surface modification of cnt reinforced uhmwpe composite for sustained drug delivery. J. Drug Deliv. Sci. Tec. 52, 748–759. doi:10.1016/j.jddst.2019.05.044
Maruyama, T., Saitoh, T., and Yokouchi, A. (2017). Differences in mechanisms for fretting wear reduction between oil and grease lubrication. Tribol. T 60, 497–505. doi:10.1080/10402004.2016.1180469
Meng, H., Sui, G. X., Xie, G. Y., and Yang, R. (2009). Friction and wear behavior of carbon nanotubes reinforced polyamide 6 composites under dry sliding and water lubricated condition. Compos Sci. Technol. 69, 606–611. doi:10.1016/j.compscitech.2008.12.004
Mertens, A. J., and Senthilvelan, S. (2018). Mechanical and tribological properties of carbon nanotube reinforced polypropylene composites. Proc. Institution Mech. Eng. Part L, J. Mater. Des. Appl. 232, 669–680. doi:10.1177/1464420716642620
Moreno-Navarro, F., Sol-Sánchez, M., and Rubio-Gámez, M. C. (2017). Structural analysis of polymer modified bituminous materials in the rehabilitation of light-medium traffic volume roads. Constr. Build. Mater. 156, 621–631. doi:10.1016/j.conbuildmat.2017.09.006
Naresh Kumar, N., Yap, S. L., Bt Samsudin, F. N. D., Khan, M. Z., and Pattela Srinivasa, R. S. (2016). Effect of argon plasma treatment on tribological properties of uhmwpe/mwcnt nanocomposites. Polymers-Basel 8, 295. doi:10.3390/polym8080295
Nemati, N., Emamy, M., Yau, S., Kim, J. K., and Kim, D. E. (2016). High temperature friction and wear properties of graphene oxide/polytetrafluoroethylene composite coatings deposited on stainless steel. Rsc Adv. 6, 5977–5987. doi:10.1039/c5ra23509j
Njoku, C. E., Omotoyinbo, J. A., Alaneme, K. K., and Daramola, M. O. (2021). Physical and abrasive wear behaviour of urena lobata fiber-reinforced polymer composites. J. Reinf. Plast. Comp. 40, 341–351. doi:10.1177/0731684420960210
Ogawa, D., Morimune-Moriya, S., and Nakamura, K. (2022). Effective polymerization technique for plasma-treated multiwalled carbon nanotubes to maximize wear resistance of composite polyurethane. J. Vac. Sci. Technol. B, Nanotechnol. Microelectron. 40, 022803. doi:10.1116/6.0001390
Papageorgiou, D. G., Li, Z., Liu, M., Kinloch, I. A., and Young, R. J. (2020). Mechanisms of mechanical reinforcement by graphene and carbon nanotubes in polymer nanocomposites. Nanoscale 12, 2228–2267. doi:10.1039/c9nr06952f
Papon, A., Montes, H., Lequeux, F., Oberdisse, J., Saalwchter, K., and Guy, L. (2012). Solid particles in an elastomer matrix: Impact of colloid dispersion and polymer mobility modification on the mechanical properties. Soft Matter 8, 4090–4496. doi:10.1039/c2sm06885k
Parnian, P., and D’Amore, A. (2021). Fabrication of high-performance cnt reinforced polymer composite for additive manufacturing by phase inversion technique. Polymers-Basel 13, 4007. doi:10.3390/polym13224007
Paul, R., and Bhowmik, S. (2022). Adhesive wear behaviour of surface modified bamboo filler reinforced polymer composite under different contact condition. J. Nat. Fibers 19, 12208–12223. doi:10.1080/15440478.2022.2054893
Qiao, H., Guo, Q., Tian, A., Pan, G., and Xu, L. (2007). A study on friction and wear characteristics of nanometer al2o3/peek composites under the dry sliding condition. Tribol. Int. 40, 105–110. doi:10.1016/j.triboint.2006.02.069
Rao, Y. S., Mohan, N. S., Shetty, N., and Shivamurthy, B. (2021). Effects of solid lubricant fillers on the flexural and shear strength response of carbon fabric-epoxy composites. Polym. Test. 96, 107085. doi:10.1016/j.polymertesting.2021.107085
Remanan, M., Kannan, M., Rao, R. S., Bhowmik, S., Varshney, L., Abraham, M., et al. (2017). Microstructure development, wear characteristics and kinetics of thermal decomposition of hybrid nanocomposites based on poly aryl ether ketone, boron carbide and multi walled carbon nanotubes. J. Inorg. Organomet. P 27, 1649–1663. doi:10.1007/s10904-017-0626-5
Ren, Z., Yang, Y., Lin, Y., and Guo, Z. (2019). Tribological properties of molybdenum disulfide and helical carbon nanotube modified epoxy resin. Materials 12, 903. doi:10.3390/ma12060903
Sakka, M. M., Antar, Z., Elleuch, K., and Feller, J. F. (2017). Tribological response of an epoxy matrix filled with graphite and/or carbon nanotubes. Friction 5, 171–182. doi:10.1007/s40544-017-0144-z
Salem, A., Guezmil, M., Bensalah, W., and Mezlini, S. (2019). Tribological behavior of molybdenum disulphide particles-high density polyethylene composite. Mater Res. Express 6, 075402. doi:10.1088/2053-1591/ab10d1
Sapiai, N., Jumahat, A., Jawaid, M., and Santulli, C. (2021). Abrasive wear behavior of cnt-filled unidirectional kenaf–epoxy composites. Processes 9, 128. doi:10.3390/pr9010128
Saravanan, D., Palanisamy, C., and Raajeshkrishna, C. R. (2019). Tribological performance of multi walled carbon nanotubes-alumina hybrid/epoxy nanocomposites under dry sliding condition. Mater Res. Express 6, 105067. doi:10.1088/2053-1591/ab3ada
Shimizu, T., Kishi, R., Kobashi, K., Morimoto, T., Okazaki, T., Yamada, T., et al. (2020). Improved thermal stability of silicone rubber nanocomposites with low filler content, achieved by well-dispersed carbon nanotubes. Compos. Commun. 22, 100482. doi:10.1016/j.coco.2020.100482
Song, H., Qi, H., Li, N., and Zhang, X. (2011). Tribological behaviour of carbon nanotubes/polyurethane nanocomposite coatings. Micro Nano Lett. 6, 48. doi:10.1049/mnl.2010.0167
Song, J. F., Lei, H., and Zhao, G. (2019). Improved mechanical and tribological properties of polytetrafluoroethylene reinforced by carbon nanotubes: A molecular dynamics study. Comp. Mater Sci. 168, 131–136. doi:10.1016/j.commatsci.2019.05.058
Spitalsky, Z., Tasis, D., Papagelis, K., and Galiotis, C. (2010). Carbon nanotube–polymer composites: Chemistry, processing, mechanical and electrical properties. Prog. Polym. Sci. 35, 357–401. doi:10.1016/j.progpolymsci.2009.09.003
Su, C., Xue, F., Li, T. S., Xin, Y. S., and Wang, M. M. (2016). Study on the tribological properties of carbon fabric/polyimide composites filled with sic nanoparticles. J. Macromol. Sci. Phys. 55, 627–641. doi:10.1080/00222348.2016.1179248
Surya, K. P., Mukhopadhyay, R., Naskar, K., and Bhowmick, A. K. (2022). A comparative study on the effect of different fibrous nanofillers on the properties of natural rubber nanocomposites. Polym. Compos. doi:10.1002/pc.27169
Unal, H., Kurtulus, E., Mimaroglu, A., and Aydin, M. (2010). Tribological performance of ptfe bronze filled composites under wide range of application conditions. J. Reinf. Plast. Comp. 29, 2184–2191. doi:10.1177/0731684409345617
Upadhyay, R. K., and Kumar, A. (2018). A novel approach to minimize dry sliding friction and wear behavior of epoxy by infusing fullerene c70 and multiwalled carbon nanotubes. Tribol. Int. 120, 455–464. doi:10.1016/j.triboint.2018.01.028
Valentini, L., Bittolo Bon, S., Hernández, M., Lopez-Manchado, M. A., and Pugno, N. M. (2018). Nitrile butadiene rubber composites reinforced with reduced graphene oxide and carbon nanotubes show superior mechanical, electrical and icephobic properties. Compos Sci. Technol. 166, 109–114. doi:10.1016/j.compscitech.2018.01.050
Venkatesan, M., Palanikumar, K., and Boopathy, S. R. (2018). Experimental investigation and analysis on the wear properties of glass fiber and cnt reinforced hybrid polymer composites. Sci. Eng. Compos. Mater. 25, 963–974. doi:10.1515/secm-2017-0068
Wang, H. Y., Zhu, M. L., Chang, L., and Ye, L. (2020). Mechanical reinforcement and wear resistance of aligned carbon nanotube/epoxy nanocomposites from nanoscale investigation. J. Appl. Polym. Sci. 137, 49182. doi:10.1002/app.49182
Wang, J. H., Zhuang, W. P., Liang, W. F., Yan, T. T., Li, T., Zhang, L. X., et al. (2022a). Inorganic nanomaterial lubricant additives for base fluids, to improve tribological performance: Recent developments. Friction 10, 645–676. doi:10.1007/s40544-021-0511-7
Wang, Y., Borgatta, J., and White, J. C. (2022b). Protecting foods with biopolymer fibres. Nat. food 3, 402–403. doi:10.1038/s43016-022-00519-6
Wu, Y., Dong, C., Yuan, C., Bai, X., Zhang, L., and Tian, Y. (2021). Mwcnts filled high-density polyethylene composites to improve tribological performance. Wear 477, 203776. doi:10.1016/j.wear.2021.203776
Xia, Z., Wang, R., Qu, B., Wu, Q., Zhuo, D., and Zheng, Y. (2022). Microwave absorbing properties of polyaniline coated buckypaper reinforced epoxy resin composites. J. Appl. Polym. Sci. 139, e53154. doi:10.1002/app.53154
Xin, Y. S., Xu, F. L., Wang, M. M., and Li, T. S. (2018). Synergistic effects of carbon nanotube/nano-MoS2 hybrid on tribological performance of polyimide nanocomposite films. Tribol. Lett. 66, 25. doi:10.1007/s11249-017-0977-7
Xu, G. D., Zhu, B., Han, Y., and Bo, Z. S. (2007). Covalent functionalization of multi-walled carbon nanotube surfaces by conjugated polyfluorenes. Polymer 48, 7510–7515. doi:10.1016/j.polymer.2007.11.012
Yan, Y. F., Meng, Z. J., Xin, X. C., Liu, H., and Yan, F. Y. (2020). Tribological behavior and thermal stability of thermoplastic polyimide/poly (ether ether ketone) blends at elevated temperature. J. Macromol. Sci. Phys. 60, 175–189. doi:10.1080/00222348.2020.1841952
Yan, Y. H., Yang, S. B., Cui, J., Jakisch, L., Pötschke, P., and Voit, B. (2011). Synthesis of pyrene-capped polystyrene for dispersion of pristine single-walled carbon nanotubes. Polym. Int. 60, 1425–1433. doi:10.1002/pi.3096
Yang, M., Zhang, C. H., Su, G. D., Dong, Y. J., Mekuria, T. D., and Lv, Q. T. (2020). Preparation and wear resistance properties of thermosetting polyimide composites containing solid lubricant fillers. Mater Chem. Phys. 241, 122034. doi:10.1016/j.matchemphys.2019.122034
Yousef, S., Visco, A. M., Galtieri, G., and Njuguna, J. (2016). Wear characterizations of polyoxymethylene (pom) reinforced with carbon nanotubes (pom/cnts) using the paraffin oil dispersion technique. JOM 68, 288–299. doi:10.1007/s11837-015-1674-3
Zalaznik, M., Novak, S., Huskić, M., and Kalin, M. (2016). Tribological behaviour of a peek polymer containing solid mos 2 lubricants: Tribological behaviour of a peek/mos 2 polymer composite. Lubr. Sci. 28, 27–42. doi:10.1002/ls.1299
Zang, X. N., Zhou, Q., Chang, J. Y., Liu, Y. M., and Lin, L. W. (2015). Graphene and carbon nanotube (cnt) in mems/nems applications. Microelectron. Eng. 132, 192–206. doi:10.1016/j.mee.2014.10.023
Zare, Y., and Rhee, K. Y. (2020). Analysis of the connecting effectiveness of the interphase zone on the tensile properties of carbon nanotubes (cnt) reinforced nanocomposite. Polymers-Basel 12, 896. doi:10.3390/polym12040896
Zhang, A. B., Tang, M., Luan, J. F., and Li, J. Y. (2012). Noncovalent functionalization of multi-walled carbon nanotubes with amphiphilic polymers containing pyrene pendants. Mater Lett. 67, 283–285. doi:10.1016/j.matlet.2011.09.103
Zhang, J. G., and Deng, J. (2011). The effect of maleic anhydride grafted styrene-ethylene-butylene-styrene on the friction and wear properties of polyamide6/carbon nanotube composites. Polym-Plast Technol. 50, 1533–1536. doi:10.1080/03602559.2011.603778
Zhang, M. J., Chen, B. B., Dong, Z., Wang, S., Li, X., Jia, Y. H., et al. (2020). Enhancement on the tribological properties of poly(phthalazinone ether sulfone ketone) by carbon nanotube-supported graphitic carbon nitride hybrid. Polym. Compos. 41, 3768–3777. doi:10.1002/pc.25674
Zhang, X. T., Liao, G. X., Jin, Q., Feng, X. B., and Jian, X. G. (2008). On dry sliding friction and wear behavior of ppesk filled with ptfe and graphite. Tribol. Int. 41, 195–201. doi:10.1016/j.triboint.2007.08.003
Keywords: carbon nanotube, polymer, composite, tribologcial properties, mechanical properties
Citation: Miao Y, Chen Q, Li Y, Zhuo D and Wang R (2023) Tribological properties of carbon nanotube/polymer composites:A mini-review. Front. Mater. 10:1129676. doi: 10.3389/fmats.2023.1129676
Received: 22 December 2022; Accepted: 17 January 2023;
Published: 26 January 2023.
Edited by:
Jianlei Wang, Chinese Academy of Sciences (CAS), ChinaReviewed by:
Zhaoqi Niu, Northwestern Polytechnical University, ChinaCopyright © 2023 Miao, Chen, Li, Zhuo and Wang. This is an open-access article distributed under the terms of the Creative Commons Attribution License (CC BY). The use, distribution or reproduction in other forums is permitted, provided the original author(s) and the copyright owner(s) are credited and that the original publication in this journal is cited, in accordance with accepted academic practice. No use, distribution or reproduction is permitted which does not comply with these terms.
*Correspondence: Qinghui Chen, Y2hlbnFoQGZqbnUuZWR1LmNu; Yonggui Li, bHlnd3hqZEBzaW5hLmNvbQ==; Rui Wang, d2FuZ3J1aUBmamlyc20uYWMuY24=
Disclaimer: All claims expressed in this article are solely those of the authors and do not necessarily represent those of their affiliated organizations, or those of the publisher, the editors and the reviewers. Any product that may be evaluated in this article or claim that may be made by its manufacturer is not guaranteed or endorsed by the publisher.
Research integrity at Frontiers
Learn more about the work of our research integrity team to safeguard the quality of each article we publish.