- 1Department of Mathematics, College of Science, King Saud University, Riyadh, Saudi Arabia
- 2DBS and H, CEME, National University of Sciences and Technology, Islamabad, Pakistan
- 3Department of Mathematics, College of Science, King Khalid University, Abha, Saudi Arabia
This article examines the impact of buoyancy on the magnetic Eyring-Powell nanofluid flow toward a stretching surface. Coupled similarity equations are created from the governing flow equations. For the particular instance of pure fluid flow, the numerically computed self-similar results are matched with the available literature and found to be in acceptable harmony. The shooting approach was used to arrive at numerical computations to the constitutive ordinary differential equations. The impacts of different fluid flow parameters, nano concentration parameters and heat transfer, are shown graphically for both aiding and opposing flows. It has been discovered that for both aiding and opposing problems, the skin friction is less affected by the buoyant force brought on by temperature differences. Under buoyancy, the rate of heat transfer increments for aiding flow problem while it declines for opposing flow.
1 Introduction
Water, oil, and other common fluids have relatively low thermal conductivities. As a result, heat transport analysis via these common fluids has been difficult for many years. The concept of raising the solid volume percentage in a fluid-solid mixture to increase thermal conductivity was initially proposed by Maxwell (Maxwell, 1873). These combinations contained particles of dimensions of millimeters and micrometers. Even though these fluids have improved thermal performance, they are nevertheless prone to a number of difficulties such abrasion, clogging, and pressure loss. According to Choi (Choi et al., 1995), a nanofluid is a type of fluid that has a tiny concentration of nanoparticles (about 100 nm) dispersed in the base fluid. Such nanoparticles’ thermal performance is dramatically altered by dispersion in common fluids. The study of magneto-hydrodynamic flow is crucial since it is used in various technical phenomena, such as the production of electrical energy and geo-physics. The MHD impact on a free convection heat transport was modeled by Sparrow et al. (Sparrow and Cess, 1961). They discovered that the presence of a magnetic field has a major impact on free convection. In a stretched surface with fixed given velocity and temperature, Chen and Strobel (Chen and Strobel, 1980) investigated the buoyancy effect in a laminar boundary layer. The magnetic field impact flow model of a Newtonian fluid for stretching wall due to unvarying temperature was taken into consideration by Chakrabarti and Gupta (Chakrabarti and Gupta, 1979). The unsteady flow case of a non-Newtonian fluid above a revolving disc was investigated by Attia (Attia, 2014). View more recent literature by visiting Refs. (Xu et al., 2007; Buongiorno, 2010; Vajravelu et al., 2011; Ibrahim and Shanker, 2012; Aly and Vajravelu, 2014; Akbar et al., 2015; Khan et al., 2021; Khan et al., 2022; Waini et al., 2022).
When performing a heat transfer analysis on a steady MHD boundary layer extent, Mukhopadhyay (Mukhopadhyay, 2013) noticed that the expanse of the skin friction parameter rises in the extant of a magnetic impact, which results in a decrease in velocity. Stretching surfaces have recently come under the attention of many researchers due to their widespread use in engineering processes. Nadeem et al. (Nadeem et al., 2014) used numerical evaluation to interpret the MHD boundary layer extent of a nanoparticle-saturated Maxwell non-Newtonian fluid past a stretched surface. The heat transfer with radiation impacts, chemical reactions of nth order and viscous effects, Makinde (Makinde, 2011) looked into the modeling of heat and mass flux for a non-Newtonian Boussinesq fluid over a vertically held porous sheet. Ibrahim and Makinde (Ibrahim and Makinde, 2013) had investigated the issue of boundary layer extent and heat transmission caused by a nano-fluids across a vertical surface with double stratification. When analyzing the transport equations, Brownian movement, thermo-phoresis, solutal layer and thermal layer characteristics were all taken into account. Akbar et al. (Akbar et al., 2014) had used a homogeneous model to discuss the stagnation-point flow problem for carbon nanotubes flow over a stretching surface using base flow as water with slip and convective constraints. The constitutive boundary layer modeling of nanofluid is streamlined via similarity transformations. Through Refs. (Ebaid et al., 2013; Ellahi et al., 2015; Ibrahim and Makinde, 2015; Sheikholeslami et al., 2015; Anuar et al., 2020; Turkyilmazoglu, 2020; Wahid et al., 2020; Rostami et al., 2021; Turkyilmazoglu, 2021), more recent research material can be reviewed.
The influence of buoyancy on the MHD flow problem of Eyring Prandtl nanofluid toward a stretching wall has been investigated in this work. Coupled similarity equations are created from the governing flow equations. For the particular instance of pure fluid flow, the numerically evaluated self-similar results are matched with the accessible literature and established to be in good harmony. The impacts of different fluid flow, heat flux, and nano particles concentration parameters are shown graphically for each aiding and adhesive flows. It has been discovered that for each aiding and opposite flow problems, the skin friction is less affected by the buoyant force brought on by temperature differences. Under buoyancy, the rate of heat flux rises for aiding flow and decreases for opposite flow. The results from the base fluid’s limiting case comparison are in good accord with those from the literature. Although the aforementioned studies point to the fact that the Eyring–Powell model has been extensively studied in different flow configurations with the consideration of a number of different geometries. The prime motivation here is to discuss the non-Newtonian Eyring–Powell fluid model with buoyancy and nanofluid effects. Therefore, the objective is to solve the momentum, thermal and concentration equations and attempt to find numerical solutions representing the flow, temperature and concentration fields. The rheology of the Eyring–Powell fluid as associated to the Newtonian fluid is mined from the exact average velocity expression.
2 Mathematical model
According to (Akbar et al., 2015), the constitutive modelling for the Eyring-Powell fluid non-Newtonian model is provided as.
3 Mathematical formulation
We talk about a constant, two-dimensional flow over a wall that coincides with the flow’s confinement plane of an incompressible, non-Newtonian, Eyring-Powell fluid. The linear stretching is what causes the flow (see Figure 1).
Following the application of boundary layer approximations, the constitutive equations for the Eyring-Powell nanofluid model with buoyancy effects can be defined as follows.
The final term in Eq. 2’s right-hand side denotes the effect of the thermal buoyancy effect on the flow profile, having "+" and "-" notations denotes, respectively, the buoyancy-assist and the opposing flow areas.
By using cross-differentiation, we can take p out of Eqs 4, 5. For this issue, the similarity transformations can be expressed as
The following ordinary (similarity) differential equations are produced using the similarity transformation 7).
depending on the boundary constraints
primes indicate differentiation with relation to
Expressions for the Sherwood Number, Nusselt Number, and the Skin friction are considered by:
4 Numerical method
The shooting approach was used to arrive at numerical computations to the constitutive Ordinary Differential Eqs 8–10 with the boundary constraints in Eq (11). The (BVP) Boundary value Problem was first converted into an initial value problem (IVP), and the far field boundary condition was given an appropriate finite value, such as, say i.e.,
5 Results and discussion
The Eyring-Powell nanofluid numerical solutions for stretching sheets are shown here with graphs that show the buoyancy effects. Figs
In Figures 3A–C, the influence of the flow parameters on the dimensionless heat flux is explored. Both helpful and opposing flows are covered by Figures 3A–C. The thermal boundary layer thickness is generally increased by Prandtl number, the ratio of buoyancy forces on the rescaled nano-particles volume fraction, and the thermophoresis parameter, whereas temperature profile increases with an increase in the ratio of buoyancy forces on the rescaled nanoparticle concentration and the thermophoresis parameter and decreases with an uplift in
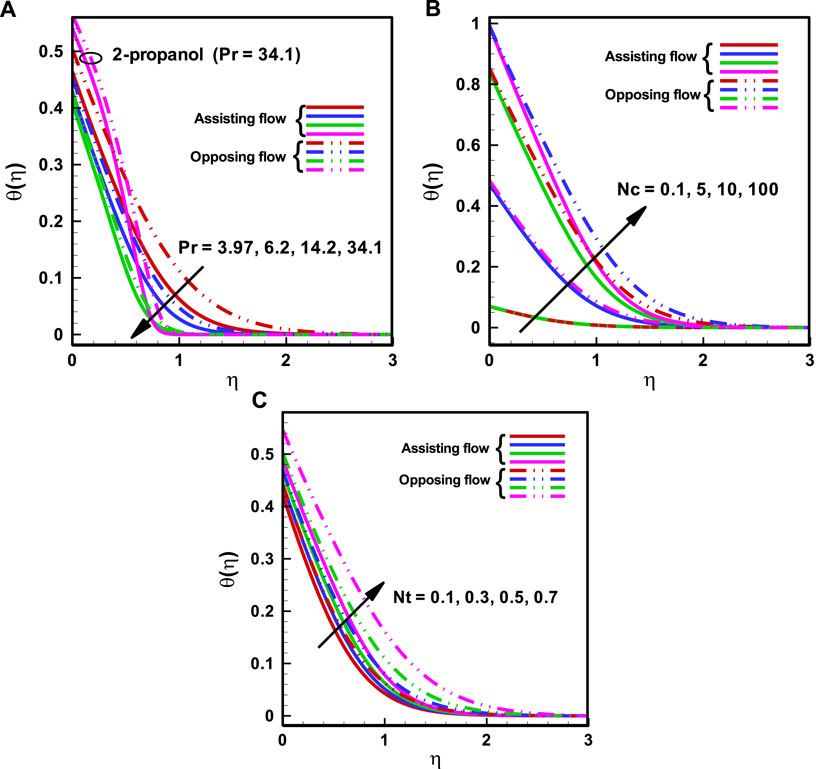
FIGURE 3. Variation of Temperature Profile for (A)
Figures 4A, and Figure 5B) illustrate how the
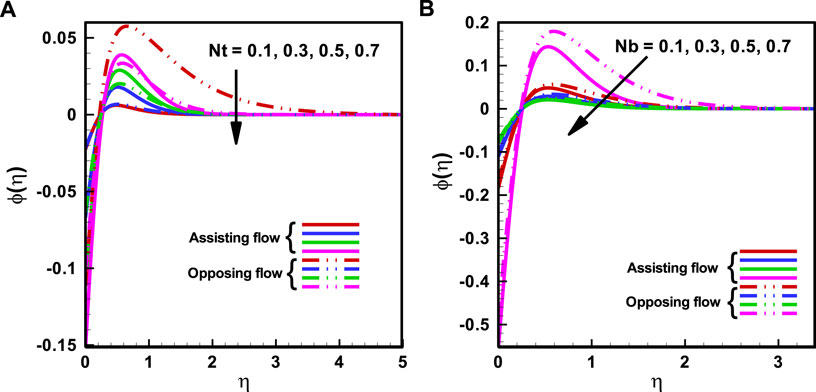
FIGURE 4. Variation of nanoparticles fraction profile (A). The Thermo-Phoresis Parameter
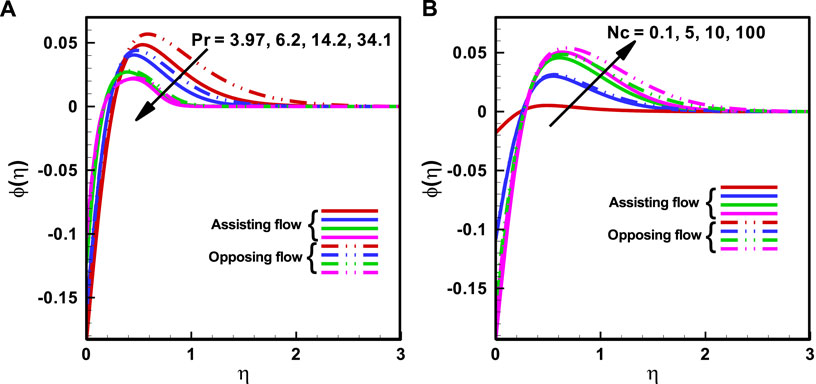
FIGURE 5. Variation of nanoparticles fraction profile for (A) Prandtl number Pr (B) The ratio of buoyancy forces on the rescaled nanoparticle volume fraction Nc.
As seen in the Figures 6A–C), the
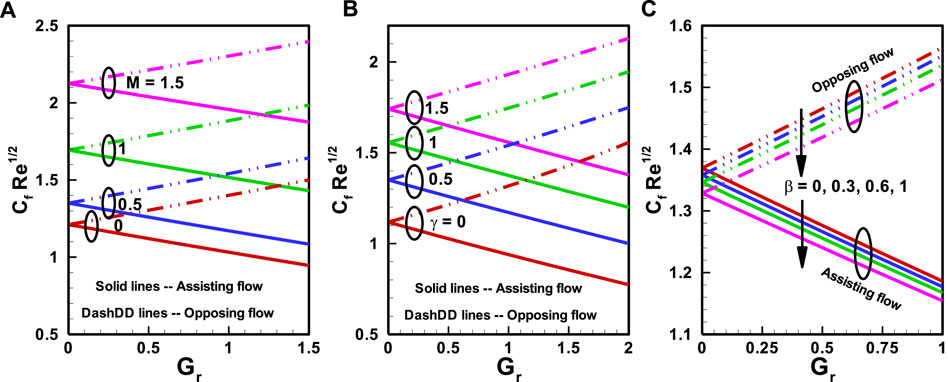
FIGURE 6. Variation of Coefficient for Skin friction (A) Hartmann number
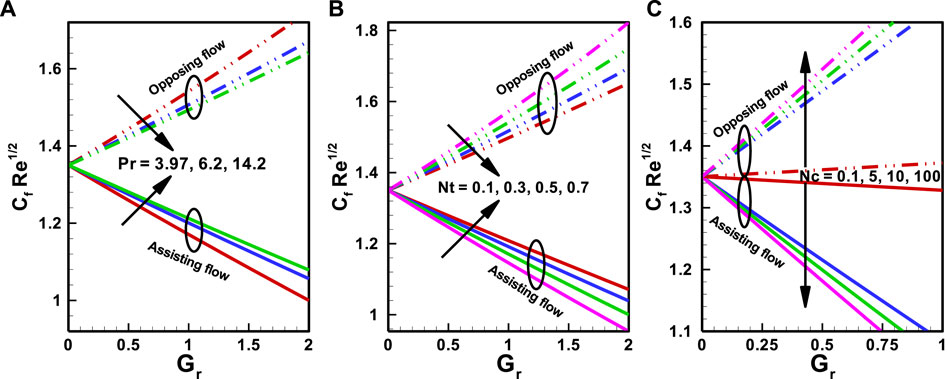
FIGURE 7. Variation of Coefficient for Skin friction (A) Prandtl number
In Figures 8A, and Figure 9B), both for aiding and opposing flows, the influences of various factors on
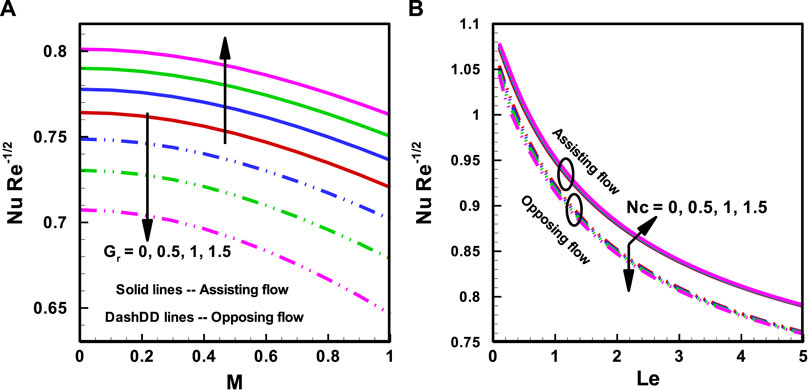
FIGURE 9. Nusselt number for (A) buoyancy influence via Temperature Difference
Streamlines and isotherms have been displayed in the Figure 10, and Figure 12) to aid in understanding the fluid flow behaviour. The streamlines will be close to the sheet’s axis when we increase the Eyring-Powell fluid parameter, as shown in Figure 10. In contrast to the aiding flow, opposing flow streams are being confined and moving toward the sheet’s axis. When compared to streamlines, isotherm outcomes are, however, the opposite. In contrast to the opposing flow, isotherms lines for aiding flows are contained and moving in the direction of the sheet’s axis, as seen in the Figure 11, and Figure 12. Table 1 compares the results of the current study to the body of prior research. The skin friction coefficient’s numerical values are provided in Table 2.
6 Conclusion
The influence of buoyancy forces on a magnetic Eyring-Powell nano-fluid flow over a vertical stretching wall is numerically analysed. The linear stretching case is considered for this incompressible non-Newtonian Eyring-Powell fluid flow problem. The major outcomes of this work are presented as follows.
• The extent of the boundary layer and the velocity profile each rise with an uplift in the Eyring-Powell fluid parameter. The boundary layer becomes thicker as the value of
• The Eyring-Powell flow characteristics and velocity profile behavior is the same for both favorable and adverse flows.
• The
• It is clear that for all flow values, opposing flow has a higher skin friction coefficient than helping flow.
• When we increase the Eyring-Powell fluid parameter, the streamlines will be near to the axis of the sheet. Opposing flow streams are constrained and travelling in the direction of the sheet’s axis in contrast to the assisting flow. However, the results of isotherms are the opposite of streamlines. Isotherms lines for assisting flows are contained and travelling in the direction of the sheet’s axis, in contrast to the opposing flow.
Data availability statement
The original contributions presented in the study are included in the article/supplementary material, further inquiries can be directed to the corresponding author.
Author contributions
FD model the problem NS Done the writeup of the manuscript and done solution methodology SS Write introduction and prepared graphs All three authors done the proof reading.
Conflict of interest
The authors declare that the research was conducted in the absence of any commercial or financial relationships that could be construed as a potential conflict of interest.
Publisher’s note
All claims expressed in this article are solely those of the authors and do not necessarily represent those of their affiliated organizations, or those of the publisher, the editors and the reviewers. Any product that may be evaluated in this article, or claim that may be made by its manufacturer, is not guaranteed or endorsed by the publisher.
References
Akbar, N. S., Ebaid, A., and Khan, Z. H. (2015). Numerical analysis of magnetic field effects on Eyring-Powell fluid flow towards a stretching sheet. J. Magnetism Magnetic Mater. 382, 355–358. doi:10.1016/j.jmmm.2015.01.088
Akbar, N. S., Nadeem, S., and Hayat Khan, Z. (2014). The combined effects of slip and convective boundary conditions on stagnation-point flow of CNT suspended nanofluid over a stretching sheet. J. Mol. Liq. 196, 21–25. doi:10.1016/j.molliq.2014.03.006
Aly, E. H., and Vajravelu, K. (2014). Exact and numerical solutions of MHD nano boundary-layer flows over stretching surfaces in a porous medium. Appl. Math. Comput. 232, 191–204. doi:10.1016/j.amc.2013.12.147
Anuar, N. S., Bachok, N., Turkyilmazoglu, M., MdArifina, N., and Rosali, H. (2020). Analytical and stability analysis of MHD flow past a nonlinearly deforming vertical surface in Carbon Nanotubes. Alexandria Eng. J. 59, 497–507. doi:10.1016/j.aej.2020.01.024
Attia, H. A. (2014). Unsteady flow of a non-Newtonian fluid above a rotating disk with heat transfer. Int. J. Heat Mass Transf. 46 (14), 2695–2700. doi:10.1016/s0017-9310(03)00029-2
Buongiorno, J. (2010). Convective transport in nanofluids. J. Heat Transf. Am. Soc. Mech. Eng. 128 (3), 240–250. doi:10.1115/1.2150834
Chakrabarti, A., and Gupta, A. S. (1979). Hydromagnetic flow and heat transfer over a stretching sheet. Quart. Appl. Math. 37, 73–78. doi:10.1090/qam/99636
Chen, T. S., and Strobel, F. A. (1980). Buoyancy effects in boundary layer adjacent to a continuous, moving horizontal flat plate. Trans. ASME J. Heat. Transf. 102, 170–172. doi:10.1115/1.3244232
Choi, S. U. S. (1995). “Enhancing thermal conductivity of fluids with nanoparticles,” in Developments and applications of non-Newtonian flows. Editors D. A. Siginer, and H. P. Wang (New York: ASME), 66, 99–105.
Ebaid, A., El-arabawy, H. A., and Nader, Y. (2013). New exact solutions for boundary-layer flow of a nanofluid past a stretching sheet. Int. J. Diff. Eq. 10 (11), 2591–2594. doi:10.1166/jctn.2013.3253
Ellahi, R., Hassan, M., and Zeeshan, A. (2015). Shape effects of nanosize particles in Cu–H2O nanofluid on entropy generation. Int. J. Heat Mass Transf. 81, 449–456. doi:10.1016/j.ijheatmasstransfer.2014.10.041
Ibrahim, W., and Makinde, O. D. (2015). Double-diffusive in mixed convection and MHD stagnation point flow of nanofluid over a stretching sheet. J. Nanofluids 4, 28–37. doi:10.1166/jon.2015.1129
Ibrahim, W., and Makinde, O. D. (2013). The effect of double stratification on boundary-layer flow and heat transfer of nanofluid over a vertical plate. Comput. Fluids 86, 433–441. doi:10.1016/j.compfluid.2013.07.029
Ibrahim, W., and Shanker, B. (2012). Unsteady MHD boundary-layer flow and heat transfer due to stretching sheet in the presence of heat source or sink. Comput. Fluids 70, 21–28. doi:10.1016/j.compfluid.2012.08.019
Khan, U., Zaib, A., Ishak, A., Bakar, S. A., Animasaun, I. L., Yook, S. J., et al. (2022). Insights into the dynamics of blood conveying gold nanoparticles on a curved surface when suction, thermal radiation, and Lorentz force are significant: The case of Non-Newtonian Williamson fluid. case Newt. Williamson fluid Math. Comput. Simul. 193, 250–268. doi:10.1016/j.matcom.2021.10.014
Khan, U., Ishak, A., and Zaib, A. (2021). Simulation of MHD CuO–water nanofluid flow and convective heat transfer considering Lorentz forces. Chin. J. Phys. 74, 350–364.
Makinde, O. D. (2011). Mhd mixed-convection interaction with thermal radiation and nth order chemical reaction past A vertical porous plate embedded in A porous medium. Chem. Eng. Commun. 198 (4), 590–608. doi:10.1080/00986445.2010.500151
Mukhopadhyay, S. (2013). MHD boundary layer flow and heat transfer over an exponentially stretching sheet embedded in a thermally stratified medium. Alexandiria Eng. J. 52, 259–265. doi:10.1016/j.aej.2013.02.003
Nadeem, S., Ul Haq, R., and Khan, Z. H. (2014). Numerical study of MHD boundary layer flow of a Maxwell fluid past a stretching sheet in the presence of nanoparticles. J. Taiwan Inst. Chem. Eng. 45 (1), 121–126. doi:10.1016/j.jtice.2013.04.006
Rostami, S., Ellahi, R., Oztop, H. F., and Goldanlou, A. S. (2021). A study on the effect of magnetic field and the sinusoidal boundary condition on free convective heat transfer of non-Newtonian power-law fluid in a square enclosure with two constant-temperature obstacles using lattice Boltzmann method. J. Therm. Analysis Calorim. 144 (6), 2557–2573. doi:10.1007/s10973-020-10202-2
Sheikholeslami, M., Ganji, D. D., Younus Javed, M., and Ellahi, R. (2015). Effect of thermal radiation on magnetohydrodynamics nanofluid flow and heat transfer by means of two phase model. J. Magnetism Magnetic Mater. 374, 36–43. doi:10.1016/j.jmmm.2014.08.021
Sparrow, E. M., and Cess, R. D. (1961). The effect of a magnetic field on free convection heat transfer. Int. J. Heat. Mass Tran. 3 (4), 267–274. doi:10.1016/0017-9310(61)90042-4
Turkyilmazoglu, M. (2020). Eyring-Powell fluid flow through a circular pipe and heat transfer: Full solutions. Int. J. Numer. Methods Heat Fluid Flow 30, 4765–4774. doi:10.1108/hff-12-2019-0925
Turkyilmazoglu, M. (2021). Stagnation-point flow and heat transfer over stretchable plates and cylinders with an oncoming flow: Exact solutions. Chem. Eng. Sci. 238, 116596. doi:10.1016/j.ces.2021.116596
Vajravelu, K., Prasad, K. V., Lee, J., Lee, C., Pop, I., and Gorder, R. A. V. (2011). Convective heat transfer in the flow of viscous Ag-water and Cu-water nanofluids over a stretching surface. Int. J. Therm. Sci. 50, 843–851. doi:10.1016/j.ijthermalsci.2011.01.008
Wahid, N. S., Turkyilmazoglu, M., Hafidzuddin, M. E. H., Abd Rahmin, N. A., Wahid, N. S., Arifin, N. M., et al. (2020). MHD hybrid Cu-Al<sub>2</sub>O<sub>3</sub>/water nanofluid flow with thermal radiation and partial slip past a permeable stretching surface: Analytical solution. J. Nano Res. 64, 75–91. doi:10.4028/www.scientific.net/jnanor.64.75
Waini, I., Khan, U., Zaib, A., Ishak, A., and Pop, I. (2022). Inspection of TiO2-CoFe2O4 nanoparticles on MHD flow toward a shrinking cylinder with radiative heat transfer. J. Mol. Liq. 361, 119615. doi:10.1016/j.molliq.2022.119615
Xu, H., Liao, S. J., and Pop, I. (2007). Series solutions of unsteady three-dimensional MHD flow and heat transfer in the boundary layer over an impulsively stretching plate. Eur. J. Mech. - B/Fluids 26, 15–27. doi:10.1016/j.euromechflu.2005.12.003
Nomenclature
(
(
Keywords: double diffusion, magnetic field, natural convection, eyring-powell model, nanofluids, stretching sheet
Citation: Duraihem FZ, Sher Akbar N and Saleem S (2023) Mixed convective eyring-powell ferro magnetic nanofluid flow suspension towards a stretching surface with buoyancy effects through numerical analysis. Front. Mater. 10:1109755. doi: 10.3389/fmats.2023.1109755
Received: 28 November 2022; Accepted: 05 January 2023;
Published: 23 January 2023.
Edited by:
Ali Saleh Alshomrani, King Abdulaziz University, Saudi ArabiaReviewed by:
Aurang Zaib, Sciences and Technology Islamabad, PakistanMustafa Turkyilmazoglu, Hacettepe University, Türkiye
Copyright © 2023 Duraihem, Sher Akbar and Saleem. This is an open-access article distributed under the terms of the Creative Commons Attribution License (CC BY). The use, distribution or reproduction in other forums is permitted, provided the original author(s) and the copyright owner(s) are credited and that the original publication in this journal is cited, in accordance with accepted academic practice. No use, distribution or reproduction is permitted which does not comply with these terms.
*Correspondence: Noreen Sher Akbar, bm9yZWVuLnNoZXJAY2VtZS5udXN0LmVkdS5waw==