- School of Civil Engineering and Architecture, Nanchang Hangkong University, Nanchang, China
A large amount of waste concrete is produced during old city reconstruction. In order to realize the lightweight reuse of recycled concrete aggregate, a new preparation scheme of foamed concrete is proposed. Through single-factor tests, the effects of recycled coarse aggregate (RCA) gradation, RCA volume ratio, water-cement ratio and foam content on the preparation process and performance of RCA foamed concrete (RCAFC) were explored. The results showed that RCA grade has significant influence on the performance of RCAFC. Grading level Ⅲ (i.e., the mass ratio of five-type aggregates sized, respectively, 9.5–16 mm, 16–19 mm, 19–26.5 mm, 26.5–31.5 mm and 31.5–37.5 mm is 2:4:8:3:3) can reduce the water absorption by 4.6%, increase the compressive strength by 6.0%, and decrease the difficulty of sample preparation compared with the natural grading. The increase of RCA volume fraction is directly proportional to the compressive strength and inversely proportional to the water absorption. With the raising of water-cement ratio, the fluidity of foamed concrete paste increases linearly, the dry density decreases, the water absorption decreases first and then increases, and the compressive strength increases first and then decreases. The increase of foam content is inversely proportional to fluidity, dry density and compressive strength, and it is directly proportional to water absorption. Among the above four factors, the grade of RCA has the greatest impact on the early strength of the sample, whilst the content of foam is the smallest.
Highlights
• A new preparation scheme for lightweight foam concrete with recycled coarse aggregate (RCA) from waste concrete is proposed.
• The dumping and filling process can realize both direct utilization and control of the RCA amount.
• The influence of RCA gradation, volume fraction, water-cement ratio and foam content on the performance of RCA foam concrete was systematically analyzed.
1 Introduction
In the process of urbanization, due to the old city reconstruction, engineering construction and other reasons, a large number of construction waste will be generated, such as waste concrete, waste bricks, etc. Among them, China produces 1.55 billion to 2.4 billion tons of construction waste every year (Yuan et al., 2020). However, the traditional construction waste treatment method will not only cause certain harm to the environment, but also waste construction waste to a certain extent. Foamed concrete has the advantages of light weight and controllable compressive strength (Ma et al., 2018; Wang et al., 2020). Since the appearance in 1923, it has been widely used in the fields of foundation treatment (Liu et al., 2020), road widening (Shi et al., 2020), etc. Ordinary foamed concrete is mainly made of cement, foam and water, and its weight is generally 400–1850 kg/m3 (Raj et al., 2019). Portland cement is an important adhesive in foamed concrete materials. However, relevant research shows that the production of 1 ton of cement will produce about 800 kg of CO2, and the amount of CO2 produced by cement accounts for 8% of the total man-made amount (Damtoft et al., 2008). Therefore, it is necessary to prepare construction waste as recycled aggregate and replace it with cement to reduce cement consumption (Oikonomou, 2004).
In order to reveal the influence of added aggregate on the performance of foamed concrete, scholars have carried out a lot of work. Yang et al. (2022) prepared foamed concrete by replacing a certain proportion of cement with recycled concrete powder. It is found that the addition of recycled concrete micro powder has little effect on the dry density of the specimen, but it reduces the compressive strength. Yang et al. (2020) also found that when the replacement rate of recycled brick micro powder was lower than 15%, the 28 day compressive strength of foamed concrete slightly increased, and when the replacement rate was 30%, the associated compressive strength was far lower than the control group. Xiao et al. (2022a) studied the feasibility of using recycled waste concrete fine aggregate to prepare recycled foamed concrete, and analyzed the fluidity, compressive strength, energy absorption and water softening properties of recycled foamed concrete. The above methods can improve the performance of foamed concrete to a certain extent, but there are also some shortcomings. For example, although recycled micro powder and fine aggregate can meet the light characteristics of foamed concrete and better match the characteristics of foamed concrete materials, its cost is high.
Coarse aggregate is the strength skeleton of plain concrete. It is the structural unit with the highest strength, the smallest volume shrinkage, the lowest cost and the best durability in concrete (Beshr et al., 2003). As a composite material, the compressive strength, elastic modulus and crack resistance of concrete will increase with the increase of coarse aggregate content (Stock et al., 1979). Verian et al. (2018) summarized the potential and challenges in the process of replacing natural aggregates with recycled concrete aggregates. Some researchers found that recycled concrete aggregates can reduce the performance of concrete, while some researchers found that recycled concrete aggregates can improve the performance of concrete. Yan et al. (2022) found that when calcined nano-attapulgite content is 6 wt% and recycled coarse aggregate (RCA) replacement rate is 30 wt% and 50 wt%, and the strength increases by 13.2% and 16.1% compared with that without calcined nano-attapulgite. Moreover, recycled coarse aggregate accounts for 60% of all crushed concrete (Ulsen et al., 2019). Therefore, it is necessary to improve the preparation process of foamed concrete by adding coarse aggregate. On the one hand, the application of coarse aggregate in foamed concrete is to add lightweight coarse aggregate. For example, Wang et al., (2021a), Wang et al. (2021b) found that with the increase of foamed concrete density, the compressive strength and energy absorption capacity of ceramsite foamed concrete are significantly improved. Ibrahim et al. (2020) prepared a new type of lightweight coarse aggregate with a particle size of 10–20 mm. They found that when 25% lightweight coarse aggregate is added, the strength of foamed concrete can be improved more effectively. Due to the high density of RCA, it will sink during mixing with foamed concrete slurry, which greatly increases the difficulty of sample preparation (Osman et al., 2022). Therefore, conventional coarse aggregate can also be added by changing the preparation process, such as two-stage pouring method. Wu et al. (2015) used RCA in the preparation of foamed concrete through the two-stage pouring method and produced recycled brick aggregate foamed concrete block with dry density of 1637 kg/m3. The above methods can improve the performance of foamed concrete to a certain extent, but there are also some shortcomings. For example, although lightweight coarse aggregate can improve the performance of foamed concrete, it does not touch the demand of recycling construction waste; while the two-stage pouring method often encounters problems such as heavy weight and difficulty in pouring quality control. In view of this, in order to realize the resource utilization of recycled aggregate from construction waste and meet the requirements for the preparation of foamed concrete, in this paper, a new preparation scheme for foamed concrete is proposed based on the technology of throwing and filling aggregate concrete (Shen et al., 2010). Some scholars have carried out some research on riprap aggregate concrete. For example, Shen et al. (2014) found that the use of riprap aggregate concrete technology can improve the compressive strength of test pieces and reduce the cement content by 20% for C30∼C80 concrete. Xu et al. (2020) found that when the distribution-filling rate was 15%, the compressive strength of distributing-filling coarse aggregate concrete was increased by 11.6%–27.0% compared with ordinary concrete. Therefore, the method of dumping and filling coarse aggregate is beneficial to the improvement of concrete performance.
As for the influence of different factors on the performance of foamed concrete, scholars have also carried out some research. For example, Xiao et al. (2022b) found that with the increase of the replacement rate of recycled concrete, the compressive strength of foamed concrete gradually decreased, and the decreasing trend became larger. Zhang S et al. (2022) found that with the increase of foam content, the water absorption of foamed concrete materials increased linearly and the compressive strength decreased linearly. Oren et al. (2020) found that with the increase of water-binder ratio, the porosity of foamed concrete increased, which led to the reduction of compressive strength of foamed concrete and the increase of water absorption. Favaretto et al. (2017) found that when construction waste was used as fine aggregate, the compressive strength of foamed concrete with particle size of 1.18–4.75 mm was higher than that of 0.6–1.18 mm, but smaller than that of 0.6 mm. Through the above analysis, it can be found that water binder ratio, foam content, recycled aggregate gradation and foam content will have a certain degree of impact on the performance of foamed concrete materials. Therefore, it is necessary to study the performance of recycled aggregate foamed concrete when different factors change.
When foamed concrete material is used in the widening project of old roads, due to its light self-weight, it often has problems such as easy to float, generation of interior cavities and serious performance degradation 3 after immersion in water. In view of this, in order to realize the resource utilization of recycled aggregate from construction waste and meet the requirements for the preparation of foamed concrete, in this paper, a new preparation scheme for foamed concrete is proposed based on the technology of throwing and filling aggregate concrete. The dumping and filling process can not only realize the direct utilization of RCA, but also control the amount of RCA added, which can prevent the excessive weight of foamed concrete due to excessive RCA, and also improve the above problems. Therefore, the present RCAFC can improve the utilization rate of waste materials, reduce the amount of cement material, improve the economy and the construction quality. On this basis, the influence of RCA gradation, RCA volume fraction, water-cement ratio and foam content on the performance of RCAfoamed concrete (RCAFC) was systematically analyzed by single-factor research method.
2 Preparation scheme of RCAFC samples
2.1 Materials
The RCA, with the particle size range 4.75–37.5 mm, was collected from C30 waste concrete test block broken by manual hammering. Besides, the ordinary Portland cement PO 42.5 is used and the basic indexes are listed in Table 1. Further, the compound foaming agent is adopted, with the foaming multiple 32, the 1 h (h) bleeding rate 74 mL, and the dilution ratio with tap water 1:50.
2.2 RCA grading design and specimen preparation process
Based on natural grading (grading level Ⅰ with particle size from 4.75 to 37.5 mm), grading level Ⅱ was formed by increasing the content of smaller particle aggregates and reducing the larger ones, and the particle size range is 4.75–31.5 mm. Further, both large and small-size particles were reduced to form grading level Ⅲ, with the particle size varying from 9.5 mm to 37.5 mm. Grading level Ⅳ is achieved by increasing larger particles and reducing smaller ones, and the particle size range is 16.0–37.5 mm. Accordingly, the grading curves of grading schemes Ⅰ, Ⅱ, Ⅲ, and Ⅳ are plotted in Figure 1, and the related physical properties are shown in Table 2.
The sample preparation includes three stages: pretreatment of RCA → preparation of foamed concrete slurry → preparation of RCAFC test block. The size of all test blocks is 150 mm×150 mm × 150 mm. The flow chart of preparation of RCAFC is shown in Figure 2 and the corresponding pouring diagrams are shown in Figure 3. After filming, each block shall be cured indoor at 20°C ± 1°C for 24 h, and then demolded. Thereafter, we put it into the thermostatic water bath for further curing to specified age (7 days (7 days) or 28 days). Finally, it shall be dried until there is no mass change.

FIGURE 3. Three stages of on-site test block pouring: (A) Laboratory waste concrete; (B) Artificial crushing; (C) Soaking treatment of RCA; (D) Cement paste after mixing; (E) Add foam; (F) Foam concrete paste after mixing; (G) Grout pouring; (H) First dumping and filling of RCA; (I) Continue to pour grout; (J) Second dumping and filling of RCA; (K) Completion of pouring; (L) Film.
2.3 Test plan
In this paper, the influence of RCA gradation, RCA volume fraction, water-cement ratio and foamcontent on the physical and mechanical properties of RCAFC are studied by single-factor tests. The test fit is shown in Table 3. Among them, the RCA gradations are grading level I (natural gradation), grading level II, grading level III, grading level Ⅳ. The volume fraction of RCA is 25%, 30% and 35% respectively. The water-cement ratio is 0.45, 0.5, 0.55 and 0.6, respectively. The content of foam is 4%, 5%, 6% and 7% respectively (accounting for the cement mass ratio). In the table, W/B represents water-cement ratio, RCA represents recycled coarse aggregate, F represents foam content, and AG represents recycled coarse aggregate gradation. For example, W/B-0.5 means that the water-cement ratio is 0.5, RCA-25% means that the RCA volume ratio is 25%, F-5% means that the foam content is 5%, AG-III means that the RCA gradation is selected as grading III. Moreover when RCA-25% and AG-III are selected, the RCA volume fraction is converted to mass = 25% × 2620 (apparent density) = 655 kg/m3.
2.4 Test methods
In these experiments, three samples were prepared for each group. Water absorption and dry density of each block were tested in accordance with “Foamed Concrete (JG/T266-2011)” (Ministry of Housing and Urban Rural Development, 2011). The compressive strength and fluidity tests were performed closely following the “Technical Specification for Filling Engineering of Bubble Mixed Lightweight Soil (CJJ/T177-2012)” (Ministry of Housing and Urban Rural Development, 2012).
Dry density test: the 3 test blocks were placed in a drying oven with a temperature of (60 ± 5)°C to dry, and then weighed. Finally, the average weight of the three test blocks is taken.
Water absorption test: firstly, put the dried test block into a constant temperature tank at 25°C with a depth of 1/3 of the height of the test block for 24 h. Then put the test block into a constant temperature tank with a depth of 2/3 of the height of the test block and keep it for 24 h. Then the test block was placed in a constant temperature water bath 30 mm above the surface of the test block for 24 h. Finally, weigh the test block.
Compressive strength test: the dried sample is placed on the pressure test machine, and the speed of 1.5 kN/s continuous uniform loading until the test block is destroyed, and the failure load is recorded finally.
Fluidity test: pour evenly mixed foamed concrete slurry slowly into a hollow cylinder of 80 mm × 80 mm. Then scrape the surface with a flat knife, and slowly lift the hollow cylinder. After standing for 1 min, use a ruler to measure the maximum horizontal diameter. The maximum horizontal diameter is the fluidity of the sample.
3 Results and analysis
3.1 Failure form
For comparison, two samples, respectively, composed of the ordinary foamed concrete (without aggregate) and RCAFC with 30% (volume rate) RCA were tested where the water-cement ratio is 0.5 and the foam content (foam-cement mass ratio) is 5%.
For ordinary foamed concrete, there was no obvious crack at the initial stage, and small cracks began to appear at the middle stage. When close to the peak stress, obvious cracks first appeared in the middle of the block. Immediately after that, the crack expanded rapidly and finally caused the damage of the sample. See Figure 4A for the failure morphology.
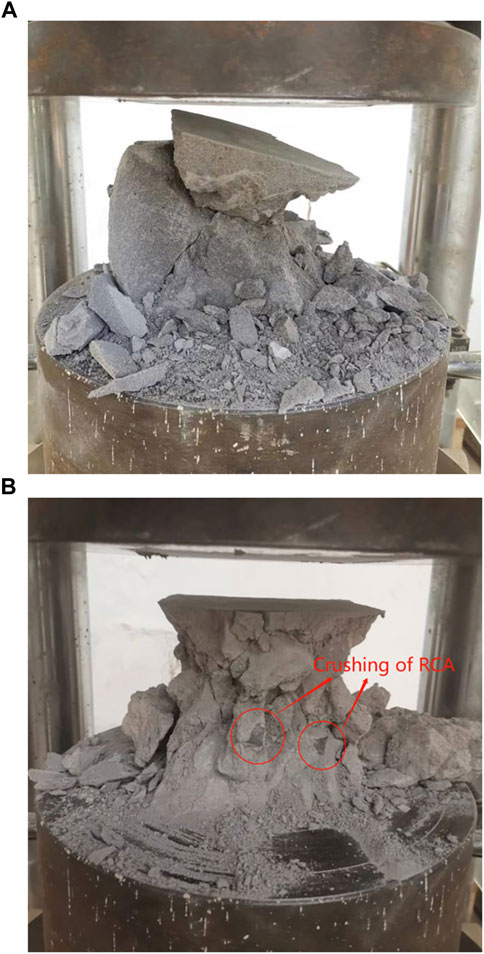
FIGURE 4. Failure morphology of test blocks: (A) Ordinary foam concrete (without aggregate); (B) RCAFC.
As for the RCAFC, its failure mode was obviously different. At the initial stage, there was no crack. When the stress was close to the peak stress, the crack first appeared on both sides of the test block. Then, with the continuous increase of the compressive force, cracks occurred in the middle of the specimen. At the same time, the axial deformation of the sample increased, and the outer surface began to crack, similar to the failure process of traditional concrete. Finally, a pair of “cores” were formed from top to bottom (see Figure 4B). The failure surface seems to be the external surface area of a pair of cones approximately symmetrical from top to bottom (Kang et al., 2018). The difference in failure morphology between RCAFC and traditional concrete is that RCAFC displays “flattening” phenomenon due to the poresinner the test block being crushed. Moreover, it is found that part of RCA was broken during compression, and RCA played a certain role in bearing pressure, as shown in Figure 4B. Accordingly, to fully utilize the bearing capacity of RCA, the strength of foamed concrete matrix itself should also be increased.
3.2 Influence of RCA gradation on specimen properties
In this testing group, it is assumed that the volume fraction of RCA is 25%, the water-cement ratio is 0.5, and the foam content is 5% with the RCA grading level varies from grading Ⅰ to Ⅳ according to Section 2.2. The coordination is as shown in No. ⅰ in Table 3. The corresponding results and discussion include.
(1) The variation of the dry density of the sample with the RCA gradation is shown in Figure 5A. It can be seen that when natural grading (grading Ⅰ) is adopted, the dry density of RCAFC reaches the minimum value of 1270 kg/m3. When grading Ⅳ is adopted, the dry density achieves the maximum value, which is 1337 kg/m3. This may be due to the minimum apparent density of grading Ⅰ, which results in the minimum amount of RCA per cubic meter at grading Ⅰ when the same RCA volume fraction is used. Moreover, there are many small and medium-size particles in the natural grading. When the dumping method is used for filling, due to the low weight of a single particle, the extrusion to the foamed concrete matrix is small, resulting in less foam breakage. The proportion of large-size particles in gradation Ⅳ is the biggest, and the squeezing force of large-size particles on foamed concrete matrix is stronger than that of small-size particles in the process of dumping and filling. The apparent density of grading Ⅳ is the largest among four gradations.
(2) The variation of water absorption with the grading of RCA is shown in Figure 5B. It can be found that the water absorption decreases with the increase of large particle size proportion in RCA. The water absorption of RCAFC increases with the increase of the proportion of small and medium-size RCA. When grading Ⅱ is adopted, the water absorption of RCAFC reaches the maximum value, i.e., 9.3%. When grading Ⅳ is adopted, the water absorption reaches the minimum, which is 7.9%. The related reasons may be: the proportion of small and medium size particles is the largest in grading Ⅱ; RCAFC with small-size RCA is mostly composed of cement mortar, and the large porosity of cement mortar itself may eventually lead to the large overall water absorption rate of aggregate; in addition, when the proportion of small and medium size particles in RCA is large, the extrusion pressure of RCA on the foamed concrete matrix is small during the filling process, which leads to the large porosity and finally large water absorption of the specimen. As for grading Ⅳ, its content of large size aggregate is the largest; most of the large size aggregate is wrapped with a layer of cement mortar on the surface of natural aggregate, and the water absorption of natural aggregate is significantly lower than that of cement mortar; the above results in the low water absorption of the recycled aggregate itself; furthermore, the large particle size aggregate has a large squeezing force on the matrix of foamed concrete, which increases the amount of foam breakage and reduces the porosity, and ultimately leads to the lowest water absorption of the specimen.
(3) The varied compressive strength of RCAFC with the grading of RCA is shown in Figure 5C. It can be viewed that when grading Ⅱ is adopted, the 7 days and 28 days compressive strengths reach the maximum, while those of grading Ⅰ are the minimum. In addition, when grading Ⅰ∼Ⅳ are adopted, respectively, the 7 days compressive strength of the sample reaches, respectively, 76.9%, 70.4%, 76.2% and 68.0% of the 28 days. It can also be seen that the early strength formation speed of grading Ⅱ and Ⅳ is slower. These results may attribute to: gradation Ⅱ has a larger proportion of small-size particles and higher bonding density of the test block; when the load is applied, micro-cracks will occur simultaneously between the small-size particles and the foamed concrete matrix; RCA plays a certain energy absorption role in the failure of the test piece, resulting in a strong energy absorption capacity, which is similar to ceramsite foamed concrete (Wang et al., 2021a); on the other hand, the RCA with small particle size has a large water absorption, which will absorb more water during the pre-soaking process of the aggregate. As a result, the water-cement ratio is slightly increased, thereby increasing the compressive strength. In grading Ⅲ and Ⅳ with a large proportion of large-size aggregate, RCA is prone to non-uniform during the filling process, which may lower the compressive strength to a certain extent, compared with grading Ⅱ.
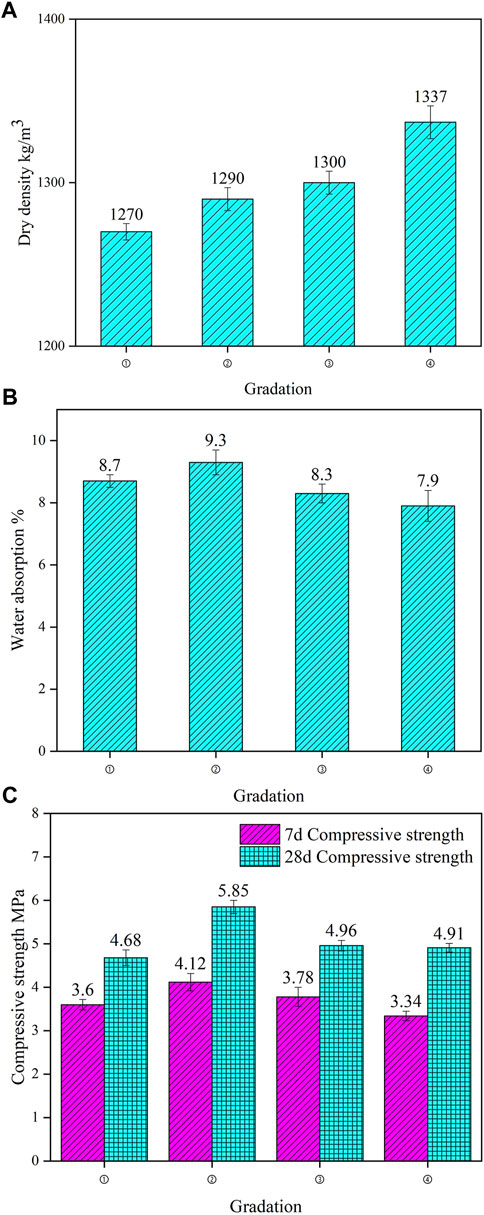
FIGURE 5. The influence of RCA gradation on sample performances: (A) dry density; (B) water absorption; (C) compressive strength.
In summary, grading Ⅲ has the advantages of rapid sample preparation, low water absorption, high compressive strength, and materials closer to natural grading. Accordingly, grading Ⅲ is finally chosen as the optimal grading, and constantly taken in the subsequent tests.
3.3 Influence of RCA volume fraction specimen properties
In this group, we mainly examine the effect of RCA volume fraction on the sample properties. To this end, the RCA gradation, water-cement ratio and foam content are, respectively, grading Ⅲ, 0.5, and 5%, while the volume fraction of RCA takes 25%, 30% and 35% in turn. The coordination is as shown in No. ⅱ in Table 3. The major experimental results and findings are.
(1) The relationship curve between the dry density of the test block and the volume fraction of RCA is shown in Figure 6A. Obviously, the dry density of the RCAFC approximately linearly increases with the RCA volume fraction, which was also revealed in Amran et al. (2015). This is mainly because the density of RCA is higher than that of foamed concrete matrix. Moreover, with the increase of the volume fraction, the squeezing effect of RCA on the foamed concrete matrix becomes stronger during the dumping and filling process so that more foam will break and overflow the slurry. In addition, when the volume fraction increases by 5% from 25%, the dry density of the sample increases by 6.2% and 7.2%, respectively, which suggests the increasing of the dry density with the increased RCA volume fraction.
(2) The relationship curve between the water absorption of the test piece and the volume fraction of RCA is illustrated in Figure 6B. The water absorption property of the aggregate used in foamed concrete will directly affect the water absorption property of the matrix. With the increase of water absorption of aggregate, the water absorption of the specimen increases (Pasupathy et al., 2021). It can be observed that the water absorption of RCAFC decreases linearly with the volume fraction of RCA. This is mainly because the water absorption of RCA is lower than that of foamed concrete matrix. Moreover, with the increase of RCA volume fraction, the squeezing effect among aggregates increases, further resulting in the increase of the squeezing effect on foamed concrete matrix, which leads to an increase in the amount of foam broken, and finally accelerates the rate of porosity reduction of RCAFC. In addition, when the volume fraction of RCA increased by 5% from 25%, the water absorption decreased by 8.4% and 11.8%, respectively, which infers heavier impact of the volume fraction of RCA on the water absorption. Therefore, it can be conclude that the water absorption of aggregates will directly affect the water absorption performance of the form concrete.
(3) The relationship curve between the compressive strength and the volume fraction of RCA is plotted in Figure 6C. It is found that the 7 days and 28 days cube compressive strength of the sample increases linearly with the RCA volume fraction. Moreover, the increasing trend of 7 days cube compressive strength is stronger than that of 28 days. The main reason is that with the increase of volume fraction, the skeleton effect between aggregates becomes more obvious. When the volume fraction of RCA increases by 5% from 25%, the 7 days compressive strength increases by 2.45% and 9.3%, respectively, and the 28 days compressive strength increases by 6.0% and 4.0%, respectively. In addition, when the volume fraction is, respectively, 25%, 30%, and 35%, the 7 days compressive strength reaches 76.2%, 73.6%, and 77.3% of the 28 days. Furthermore, when the volume fraction is 35%, the early strength of the sample is formed fastest.
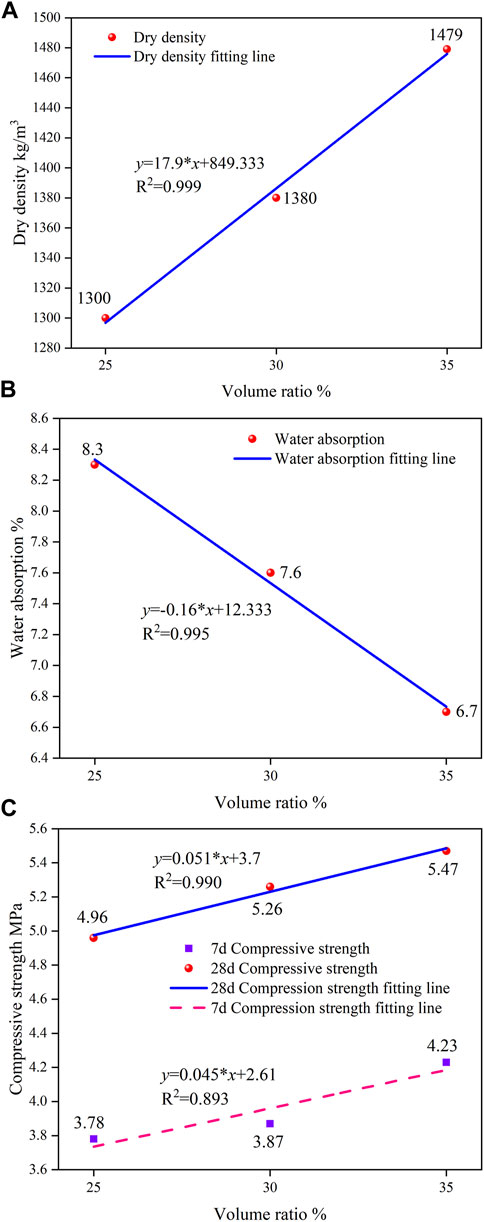
FIGURE 6. The influence of RCA volume fraction on sample performances: (A) dry density; (B) water absorption; (C) compressive strength.
However, when the volume fraction of RCA is 35%, the stacking space of RCA is limited. Therefore, it is necessary to carefully arrange the RCA through external force to help the aggregate sink, which is complex and inevitably causes difficulty to on-site construction. When 25% and 30% volume fraction are adopted, the RCA can sink naturally and meet the requirements of sample preparation. Further seeing that the compressive strength of 30% volume fraction sample is 6.05% higher than that of 25% volume fraction sample, the RCA volume fraction is finally selected as 30% in all the following tests.
3.4 Influence of water-cement ratio on specimen properties
In this series, we further investigate the effect of water-cement ratio on the sample performances. For this purpose, the RCA gradation level is Ⅲ, the RCA volume fraction is 30%, and the foam content is 5%. Four water-cement ratios, i.e., 0.45, 0.50, 0.55, and 0.60 are successively considered. The coordination is as shown in No. ⅲ in Table 3. The associated experimental results are listed as follows.
(1) The change of fluidity of foamed concrete paste with the water-cement ratio is illustrated in Figure 7A, which shows that the fluidity increases with the increased water-cement ratio. When the water-cement ratio increased by 0.05 from 0.45, the fluidity increased by 17.1%, 19.8%, and 4.3%, respectively, suggesting that when the water-cement ratio changes between 0.55 and 0.6, its influence on the mobility is not significant. When the ratio is 0.45, it is found that the matrix has great resistance to the settlement of RCA during the dumping process, which causes incompletely sinking of aggregates and requires external force to assist their further settlement. When the water-cement ratio increases to 0.5, 0.55 and 0.6, the RCA can freely sink. Besides, it is found that when RCA with gradation level Ⅲ and 30% volume fraction is used, the fluidity of foamed concrete slurry needs to be more than 190 mm, so that the RCA can completely sink through its own weight. However, excessive water will cause segregation of foamed concrete matrix (Raj et al., 2019) and affect other properties of the sample, so it is necessary to control the water-cement ratio within a certain range.
(2) The variation of dry density with water-cement ratio is graphically shown in Figure 7B. It demonstrates that with the increase of water-cement ratio, the dry density of RCAFC shows a downward trend, which is just consistent with the intention of lightweight. When the water-cement ratio is 0.45, the water-content in the foamed concrete matrix is low, and the cement will absorb water from the foam, leading to foam degradation. With the increase of the water-cement ratio, the water demand during slurry mixing meets the requirements of foam, the foam breakage rate is low. Besides, with the increased water-cement ratio, the fluidity of foamed concrete paste increases, which reduces the resistance of RCA and the damage to the foamed concrete matrix in the process of dumping and filling, and therefore improves the stability of foam and decreases the dry density. When the water-cement ratio increased by 0.05 from 0.45, the dry density decreased by 1.6%, 1.0%, and 0.3%, respectively, meaning that the dry density decreases slowly with the increased water-cement ratio, and when the water-cement ratio changes between 0.55 and 0.6, its effect on the dry density is not obvious.
(3) The water absorption at different water-cement ratio is displayed in Figure 7C. It can be seen that the water absorption decreases first and then increases with the water-cement ratio. When the water-cement ratio is 0.55 and 0.60, respectively, the water absorption reaches its minimum and maximum. When the water-cement ratio increases from 0.45 to 0.55, more complete cement hydration reaction and more hydration products are generated, which well fills the gap of the pore wall, making the thickness of the pore wall increase and more resistant to water entering. When the water-cement ratio reaches 0.6, free water in the test piece increases, thus raising the number of pores (Oren et al., 2020). Moreover, in the subsequent hardening evaporation process, a connected pore structure may be formed, which may lead to the increase of water absorption. This phenomenon conforms to the work of Nambiar and Ramamurthy, (2007).
(4) The tested compressive strength at various water-cement ratio is collected in Figure 7D. Obviously, the compressive strength first increases and then decreases with the increased water-cement ratio. The main reason is that when the water-cement ratio is 0.45, the amount of water in the foamed concrete matrix is less, and the RCA absorbs part of the water after being dumped and filled, which makes the water content in the sample cannot meet the requirements of cement hydration, and lowers the cube compressive strength. When the water-cement ratio increases to 0.5 and 0.55, the water content in RCAFC is more appropriate. When it further increases to 0.6, there is too much water in the foamed concrete paste. Bubbles increase the number of pores under the continuous impact of water, and the excess water evaporation process also causes the increase of pores, eventually leading to the increase of porosity. The irregular pore structure makes the specimen vulnerable to stress concentration (Liu et al., 2016).
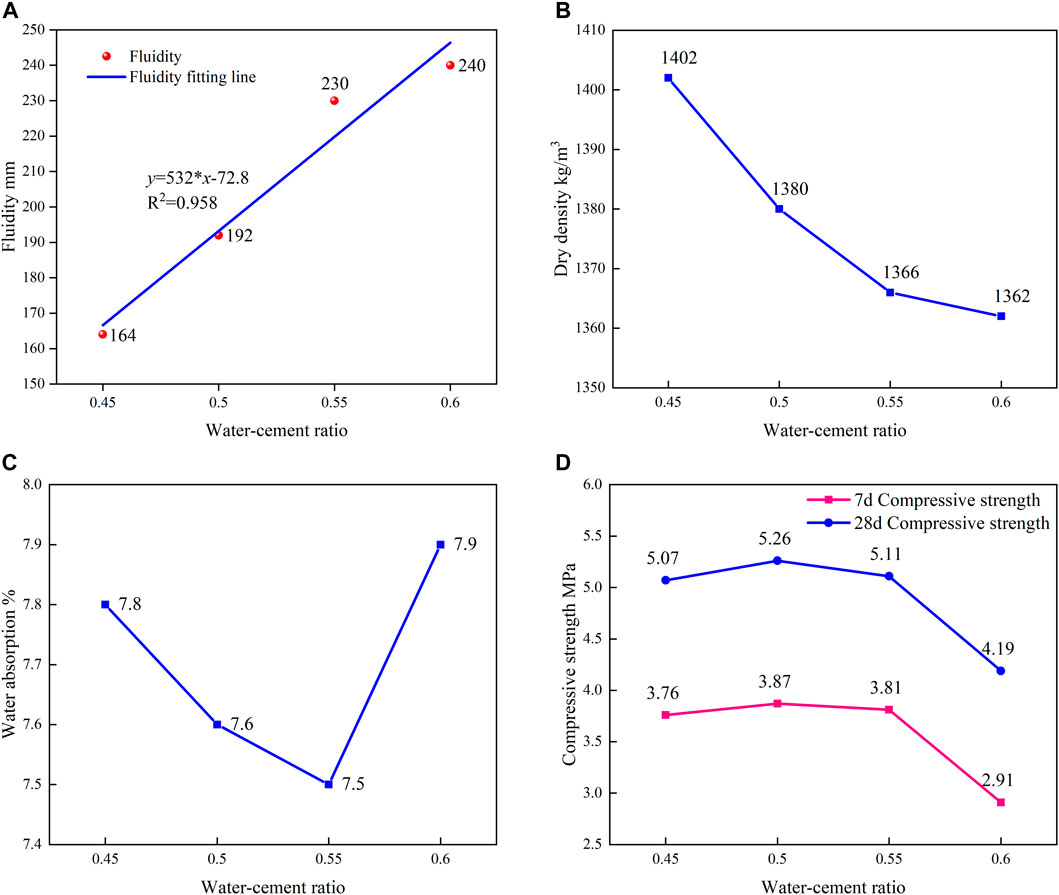
FIGURE 7. The influence of water-cement ratio on sample performances: (A) fluidity; (B) dry density; (C) water absorption; (D) compressive strength.
When the water-cement ratio increases by 0.05 from 0.45, the 7 days compressive strength differs by 2.9%, 1.6% and 30.9%, respectively, and the 28 days compressive strength differs, respectively, by 3.7%, 2.9% and 22.0%. These results show that when the water-cement ratio changes between 0.45 and 0.55, it has little effect on the early and late compressive strength. When increased from 0.55 to 0.6, the early and late strength significantly decreases. In addition, when the water-cement ratio is, respectively 0.45, 0.5, 0.55 and 0.6, the 7 days compressive strength of the sample is, respectively, 74.2%, 73.6%, 74.6% and 69.5% of the 28 days, inferring that the early strength formation of the sample is the slowest when water-cement ratio is 0.6.
Generally, the dry density and water absorption of the sample is within the scope of the specification requirements at prescribed water-cement ratio. Therefore, we mainly focus on the cube compressive strength and preparation difficulty (fluidity). From the strength point of view, when the water-cement ratio is 0.5 and 0.55, the cube compressive strength is larger, reaching 5.26 MPa and 5.11 MPa, respectively, and the difference between the two is only 2.85%. When the water-cement ratio is 0.55, the fluidity of foamed concrete matrix reaches 230 mm; besides, the process of RCA dumping and filling is more convenient and the sample preparation speed is faster. After comprehensive consideration, the optimal water-cement ratio is 0.55.
3.5 Influence of foam content on specimen properties
With the RCA gradation level Ⅲ, the RCA volume fraction 30%, and the water-cement ratio 0.55, we finally inspect the properties of RCAFC under different foam content, i.e., 4%, 5%, 6% and 7%. The coordination is as shown in No. ⅳ in Table 3. The key results and findings include.
(1) Figure 8A plots the fluidity of foamed concrete matrix at different foam content. It can be seen that with the increase of foam content, the fluidity of foamed concrete matrix approximately shows a linear downward trend. When the content of foam increased by 1% from 4%, the fluidity of adjacent proportion decreased by 4.6%, 8.3% and 2.8%, respectively. Moreover, when the foam content changes from 5% to 6%, the influence on mobility is the largest. In addition, when the content of foam is 7%, the fluidity still meets the requirement of more than 190 mm. The reason is mainly due to the lower self-weight and higher air content, which provides greater cohesion to the foamed concrete matrix (Krishna et al., 2021).
(2) The relationship curve between the dry density and the content of foam is shown in Figure 8B, from which we can observe that the dry density of RCAFC decreases linearly with the foam content. Increasing foam content introduces more air into the foamed concrete matrix during mixing, resulting in a large increase in porosity and a decrease in dry density. During the mixing process of foamed concrete slurry, the blades of the mixer will squeeze the foam. With the increase of foam content, the proportion of extruded foam also increases, which eventually leads to a significant increase in the number of foam defoaming in foamed concrete (Zhang L et al., 2022). When the content of foam increased by 1% from 4%, the dry density decreased by 3.8%, 3.7%, and 3.5%, respectively, which suggests the slowing down of the decreasing trend of dry density due to the increased breaking amount of foam.
(3) The variations of the water absorption with the foam content is plotted in Figure 8C. As we can see, the water absorption increases linearly with the foam content. The main reason is that with the increase of foam content, the number of pores increases, and the pores merge. As a result, the number of connecting holes also increases, which raises the speed of water entering the pores and therefore increases the water absorption (Ibrahim et al., 2020). When the content of foam increased by 1% from 4%, the water absorption increased by5.6%, 13.3%, and 4.7%, respectively. Besides, when the content of foam is 5–6%, the change of water absorption is the largest.
(4) The compressive strength at various content of foam is illustrated in Figure 8D, which shows that with the increase of foam content, the cube compressive strength of RCAFC at 7 days and 28 days age presents a linear downward trend. On the one hand, with the increase of foam content, bubbles are generated and merged, which may form larger pores, and the number of communicating pores also increases significantly (Ma and Chen, 2015). On the other hand, the strength of foamed concrete matrix decreases with the increased foam content, which drives the change of destroying process from the concurrent failure of foamed concrete matrix and a small part of RCA to the failure of only foamed concrete matrix, since the wrapped RCA has no bearing effect. When the content of foam increased by 1% from 4%, the 7 days compressive strength of the sample decreased by 14.6%, 32.8% and 30.1%, respectively, and the 28 days compressive strength of the sample decreased, respectively, by 16.4%, 34.4% and 28.4%. Further, when the content of foam is changed from 4% to 5%, the reduction rate of 7 days and 28 days compressive strength of the sample is the minimum. In addition, when the content of foam varies from 4% to 7%, the 7 days compressive strength of the sample reaches 73.0%, 74.6%, 76.4% and 74.6% of the 28 days, respectively, showing that the early strength is formed fastest when the content of foam is 6%.
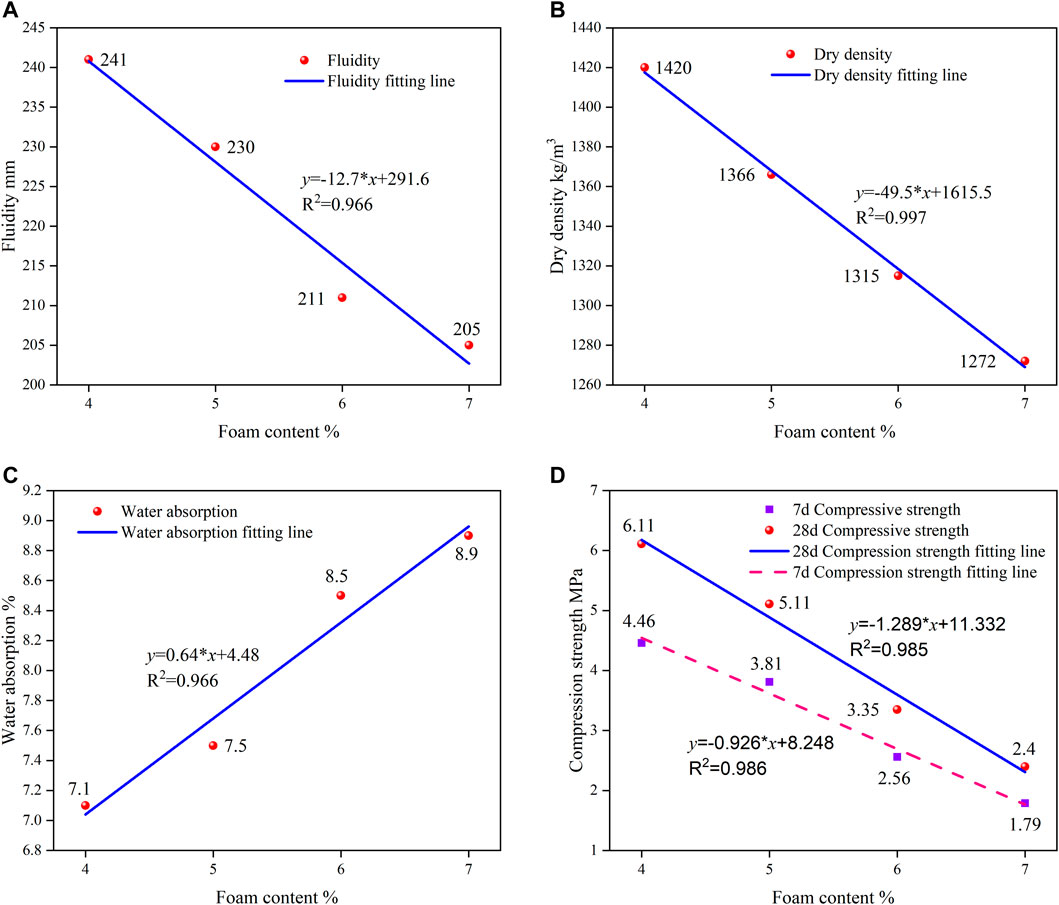
FIGURE 8. The influence of foam content on sample performances: (A) fluidity; (B) dry density; (C) water absorption; (D) compressive strength.
On the whole, when the content of foam changes to 6% and 7%, the compressive strength of the sample decreases significantly, which cannot meet the requirements of the specification (Ministry of Housing and Urban Rural Development, 2011). When the content of foam is 4% (5%), the dry density is 1420 kg/m3 (1366 kg/m3), the water absorption is 7.1% (7.5%), the 28 days cube compressive strength is 6.11 (5.11) MPa, which shall meet the requirements for compressive strength of dry density grade A14 and A12 in the specification (Ministry of Housing and Urban Rural Development, 2011).
4 Conclusion and perspectives
In this paper, a new preparation scheme for lightweight foamed concrete with recycled coarse aggregate from waste concrete is proposed. Our dumping and filling process can realize both direct utilization and control of the RCA amount. Through single-factor tests, the paper systematically analyzed the influence of recycled concrete aggregate gradation, recycled concrete aggregate volume ratio, water-cement ratio and foam content on the preparation process and performance of recycled concrete aggregate foamed concrete, in close accordance with JG/T 266-2011 (Ministry of Housing and Urban Rural Development, 2011) and CJJ/T177-2012 (Ministry of Housing and Urban Rural Development, 2012). The main conclusions are as follows.
(1) By redesigning the preparation scheme for foamed concrete, the whole sample was poured in three layers. The pouring height is, respectively, 2/5, 2/5 and 1/5 of the mold height. This method realizes the preparation of lightweight concrete by directly applying the coarse aggregate of waste concrete.
(2) Adjusting the gradation can improve the performance of RCAFC and the construction convenience. Comprehensively considering the dry density, water absorption, cube compressive strength and preparation difficulty of the sample, RCA gradation level Ⅲ (i.e., the mass ratio of five-type aggregates sized, respectively, 9.5–16 mm, 16–19 mm, 19–26.5 mm, 26.5–31.5 mm and 31.5–37.5 mm is 2:4:8:3:3) is the most reasonable grading.
(3) Based on grading Ⅲ, with the increase of RCA volume fraction, the dry density and compressive strength of RCAFC increase linearly, while the water absorption decreases linearly. When the volume fraction of RCA is 30%, not only can the normal pouring of samples be achieved, but also the compressive strength of RACFC can be improved. Therefore, in order to achieve the optimum strength, the volume fraction of RCA is finally selected as 30%. When gradation Ⅲ is adopted and the volume fraction of RCA is 30%, it is recommended that the fluidity of foamed concrete paste should be greater than 190 mm.
(4) With the increase of water-cement ratio, the fluidity of foamed concrete paste increases linearly. At the same time, the dry density decreases, the water absorption decreases first and then increases, while the compressive strength increases first and then decreases. In addition, the difficulty of specimen preparation can be reduced with the increase of water-cement ratio. The water-cement ratio of the value 0.55 is the most reasonable ratio.
(5) With the increase of foam content, the fluidity, dry density and compressive strength show a linear decline trend, while the water absorption gives a linear increase trend. When the foam content is 4% or 5%, the dry density and compressive strength can meet the requirements for compressive strength of Foamed concrete (JG/T266-2011) with dry density grade of A14 and A12.
(6) According to all the compressive strength data of our tests, the 7 days compressive strength of the sample can reach 74% of the 28 days. Among all the four influencing factors (i.e., RCA gradation, RCA volume ratio, water-cement ratio and foam content), the RCA gradation has the largest effect on the early strength of the sample, while thefoam content has the smallest.
Based on the present work and in view of that previous studies have shown the drying shrinkage of foamed concrete is 4–10 times larger than that of ordinary concrete due to the absence of coarse aggregate (Amran et al., 2015), the difference between RCAFC and ordinary foamed concrete in drying shrinkage shall be further studied. In addition, seeing that this paper mainly analyzes the macro performance of RCAFC materials, further work may also focus on the impact of dumped RCA on the interface transition zone and pore structure of RCAFC from micro perspectives. When foamed concrete material is used in the widening project of old roads, due to its light self weight, it often has problems such as easy to float in the presence of groundwater, cavities in the interior, and serious performance degradation after immersion in water. When RCAFC material is used in the widening project of old roads, we should take the dry density of the material as the control quantity, and select the dry density of RCAFC to be slightly greater than that of water. It can prevent subgrade from floating when encountering groundwater or precipitation, and improve the quality of subgrade. The application of RCAFC materials in road widening can be further studied later.
Data availability statement
The original contributions presented in the study are included in the article/Supplementary Material, further inquiries can be directed to the corresponding author.
Author contributions
All authors listed have made a substantial, direct, and intellectual contribution to the work and approved it for publication. SH: Conceptualization, methodology, supervision. PZ: Methodology, investigation, original draft, editing. HZ: Conceptualization, review and editing. DK: Investigation. XW: Conceptualization.
Funding
This work was supported by the National Natural Science Foundation of China (Grant No. 52068054 and 12062015) and the Postgraduate Innovation Special Fund of Nanchang Hangkong University (Grant No. YC2021-S700).
Conflict of interest
The authors declare that the research was conducted in the absence of any commercial or financial relationships that could be construed as a potential conflict of interest.
Publisher’s note
All claims expressed in this article are solely those of the authors and do not necessarily represent those of their affiliated organizations, or those of the publisher, the editors and the reviewers. Any product that may be evaluated in this article, or claim that may be made by its manufacturer, is not guaranteed or endorsed by the publisher.
References
Amran, Y., Farzadnia, N., and Ali, A. (2015). Properties and applications of foamed concrete; a review. Constr. Build. Mater. 101, 990–1005. doi:10.1016/j.conbuildmat.2015.10.112
Beshr, h., Almusallam, A., and Maslehuddin, M. (2003). Effect of coarse aggregate quality on the mechanical properties of high strength concrete. Constr. Build. Mater. 17 (2), 97–103. doi:10.1016/s0950-0618(02)00097-1
Damtoft, J. S., Lukasik, J., Herfort, D., Sorrentino, D., and Gartner, E. (2008). Sustainable development and climate change initiatives. Cement.Concr. Res. 38 (2), 115–127. doi:10.1016/j.cemconres.2007.09.008
Favaretto, P., Hidalgo, G., Sampaio, C., Silva, R., and Lermen, R. (2017). Characterization and use of construction and demolition waste from south of Brazil in the production of foamed concrete blocks. Appl. Sci. 7 (10), 1090. doi:10.3390/app7101090
Ibrahim, N., Ismail, K., Amat, R., Rahim, N., and Nazmi, N. (2020). Potential use of foam in the production of lightweight aggregate (LWA) and its performance in foamed concrete. IOP E. E. S. 476 (1), 012037. doi:10.1088/1755-1315/476/1/012037
Kang, Y., Jia, Y., and Luo, Y. (2018). Fracture morphology and mechanism of concrete cube test blocks subjected to compression failure. J. Xi'an Univ. Archit. Technol. 50 (02), 202–208.
Krishna, A., Siempu, R., and Kumar, G. (2021). Study on the fresh and hardened properties of foam concrete incorporating fly ash. Mater. Today Proc. 46, 8639–8644. doi:10.1016/j.matpr.2021.03.599
Liu, K., Yue, F., S, Q., Zhou, C., Xiong, Z., and He, Y. (2020). Assessment of the use of fiberglass-reinforced foam concrete in high-speed railway bridge approach involving foundation cost comparison. Adv. Struct. Eng. 23 (2), 388–396. doi:10.1177/1369433219867622
Liu, Z., Zhao, K., Hu, C., and Tang, Y. (2016). Effect of water-cement ratio on pore structure and strength of foam concrete. Adv. Mater. Sci. Eng. 2016, 1–9. doi:10.1155/2016/9520294
Ma, C., and Chen, B. (2015). Properties of a foamed concrete with soil as filler. Constr. Build. Mater. 76, 61–69. doi:10.1016/j.conbuildmat.2014.11.066
Ma, S., Chen, W., and Zhao, W. (2018). Mechanical properties and associated seismic isolation effects of foamed concrete layer in rock tunnel. J. Rock. Mech.Geotech. Eng. 11 (1), 159–171. doi:10.1016/j.jrmge.2018.06.006
Ministry of Housing and Urban Rural Development (2012). CJJ/T177-2012, Technical specification for foamed mixture lightweight soil filling engineering. Beijing, China: Ministry of Housing and Urban Rural Development.
Ministry of Housing and Urban Rural Development (2011). JG/T 266-2011, Foamed concrete. Beijing, China: Ministry of Housing and Urban Rural Development.
Nambiar, E., and Ramamurthy, K. (2007). Sorption characteristics of foam concrete. Cement.Concrete. Res. 37 (9), 1341–1347. doi:10.1016/j.cemconres.2007.05.010
Oikonomou, N. (2004). Recycled concrete aggregates. Cement.Concrete. Comp. 27 (2), 315–318. doi:10.1016/j.cemconcomp.2004.02.020
Oren, O., Gholampour, G., Gencel, O., and Ozbakkaloglu, T. (2020). Physical and mechanical properties of foam concretes containing granulated blast furnace slag as fine aggregate. Constr. Build. Mater. 238, 117774. doi:10.1016/j.conbuildmat.2019.117774
Osman, G., Turhan, B., Zeynep, B., and Togay, O. (2022). A detailed review on foam concrete composites: Ingredients, properties, and microstructure. Appl. Sci. 12 (11), 5752. doi:10.3390/app12115752
Pasupathy, K., Ramakrishnan, S., and Sanjayan, J. (2021). Influence of recycled concrete aggregate on the foam stability of aerated geopolymer concrete. Constr. Build. Mater. 271, 121850. doi:10.1016/j.conbuildmat.2020.121850
Raj, A., Sathyan, D., and Mini, K. (2019). Physical and functional characteristics of foam concrete: A review. Constr. Build. Mater. 221, 787–799. doi:10.1016/j.conbuildmat.2019.06.052
Shen, W., Dong, R., Li, J., Zhou, M., Ma, W., and Zha, J. (2010). Experimental investigation on aggregate interlocking concrete prepared with scattering–filling coarse aggregate process. Constr. Build. Mater. 24 (11), 2312–2316. doi:10.1016/j.conbuildmat.2010.04.023
Shen, W., Zhang, C., Li, X., Shi, H., Wang, G., and Tian, X. (2014). Low carbon concrete prepared with scattering-filling coarse aggregate process. Int. J.Concr.Struct. M. 8 (4), 309–313. doi:10.1007/s40069-014-0080-5
Shi, X., Huang, J., and Su, Q. (2020). Experimental and numerical analyses of lightweight foamed concrete as filler for widening embankment. Constr. Build. Mater. 250, 118897. doi:10.1016/j.conbuildmat.2020.118897
Stock, A., Hannantt, D., and Williams, R. (1979). The effect of aggregate concentration upon the strength and modulus of elasticity of concrete. Mag. Concr. Res. 31 (109), 225–234. doi:10.1680/macr.1979.31.109.225
Ulsen, C., Tseng, E., Angulo, S., Landmann, M., Contessotto, R., Balbo, J., et al. (2019). Concrete aggregates properties crushed by jaw and impact secondary crushing. J. Mater. Res. Technol. 8 (1), 494–502. doi:10.1016/j.jmrt.2018.04.008
Verian, K., Ashraf, W., and Cao, Y. (2018). Properties of recycled concrete aggregate and their influence in new concrete production. Resour. Conserv. Recy. 133, 30–49. doi:10.1016/j.resconrec.2018.02.005
Wang, X., Huang, J., Dai, S., Ma, B., and Jiang, Q. (2020). Investigation of silica fume as foam cell stabilizer for foamed concrete. Constr. Build. Mater. 237 (C), 117514. doi:10.1016/j.conbuildmat.2019.117514
Wang, X., Liu, L., Jia, K., and Zhou, H. (2021). Mechanical properties and energy absorption characteristics of ceramsite foam concrete. J. Build. Mater. 24 (01), 207–215.
Wang, X., Liu, L., Zhou, H., Song, T., Qiao, Q., and Zhang, H. (2021). Improving the compressive performance of foam concrete with ceramsite: Experimental and meso-scale numerical investigation. Mater. Des. 208, 109938. doi:10.1016/j.matdes.2021.109938
Wu, L., Yao, J., Gao, S., Zhu, X., Zhou, B., and Xu, X. (2015). Research on factors affecting physical and mechanical properties of pre -placed concrete slabs with recycled brick aggregate manufactured by grouting. J. Water Resour. Archit. Eng. 13 (06), 214–220.
Xiao, J., Hao, L., Cao, W., and Ye, T. (2022). Influence of recycled powder derived from waste concrete on mechanical and thermal properties of foam concrete. J. Build.Eng. 61, 105203. doi:10.1016/j.jobe.2022.105203
Xiao, J., Zhang, H., Zou, S., Duan, Z., and Ma, Y. (2022). Developing recycled foamed concrete for engineered material arresting system. J. Build. Eng. 53, 104555. doi:10.1016/j.jobe.2022.104555
Xu, G., Shen, W., Fang, D., Zhou, M., Zhang, B., Du, X., et al. (2020). Influence of size and surface condition of distributing-filling coarse aggregate on the properties of aggregate-interlocking concrete. Constr. Build. Mater. 261, 120002. doi:10.1016/j.conbuildmat.2020.120002
Yan, J., Liu, X., Wang, X., Wang, L., Weng, W., Yu, X., et al. (2022). Influence of nano-attapulgite on compressive strength and microstructure of recycled aggregate concrete. Cem. Concr. Comp. 134, 104788. doi:10.1016/j.cemconcomp.2022.104788
Yang, D., Liu, M., and Ma, Z. (2020). Properties of the foam concrete containing waste brick powder derived from construction and demolition waste. J. Build. Eng. 32, 101509. doi:10.1016/j.jobe.2020.101509
Yang, D., Liu, M., Zhang, Z., Yao, P., and Ma, Z. (2022). Properties and modification of sustainable foam concrete including eco-friendly recycled powder from concrete waste. Case. Stud. Constr. Mat. 16, e00826. doi:10.1016/j.cscm.2021.e00826
Yuan, J., Zeng, X., and Chen, M. (2020). Estimating the construction waste generation in Jinan using the grey system theory. China. e. Sci. 40 (09), 3894–3902.
Zhang, L., Zhao, Z., Zhang, N., Rong, H., and Yue, C. (2022). Preparation and performance of raw soil foam concrete. J. Build. Mater. 25 (02), 199–205.
Keywords: recycled waste concrete, grading of recycled coarse aggregate, volume fraction of recycled coarse aggregate, water-cement ratio, foam content, indoor test
Citation: Han S, Zhang P, Zhang H, Kang D and Wang X (2023) Physical and mechanical properties of foamed concrete with recycled concrete aggregates. Front. Mater. 10:1106243. doi: 10.3389/fmats.2023.1106243
Received: 23 November 2022; Accepted: 02 February 2023;
Published: 14 February 2023.
Edited by:
Shih-Chen Shi, National Cheng Kung University, TaiwanReviewed by:
Ping Duan, China University of Geosciences Wuhan, ChinaSudharshan N. Raman, Monash University Malaysia, Malaysia
Sigit Tri Wicaksono, Sepuluh Nopember Institute of Technology, Indonesia
Copyright © 2023 Han, Zhang, Zhang, Kang and Wang. This is an open-access article distributed under the terms of the Creative Commons Attribution License (CC BY). The use, distribution or reproduction in other forums is permitted, provided the original author(s) and the copyright owner(s) are credited and that the original publication in this journal is cited, in accordance with accepted academic practice. No use, distribution or reproduction is permitted which does not comply with these terms.
*Correspondence: Peiheng Zhang, MTE3OTY4NjQ1N0BxcS5jb20=