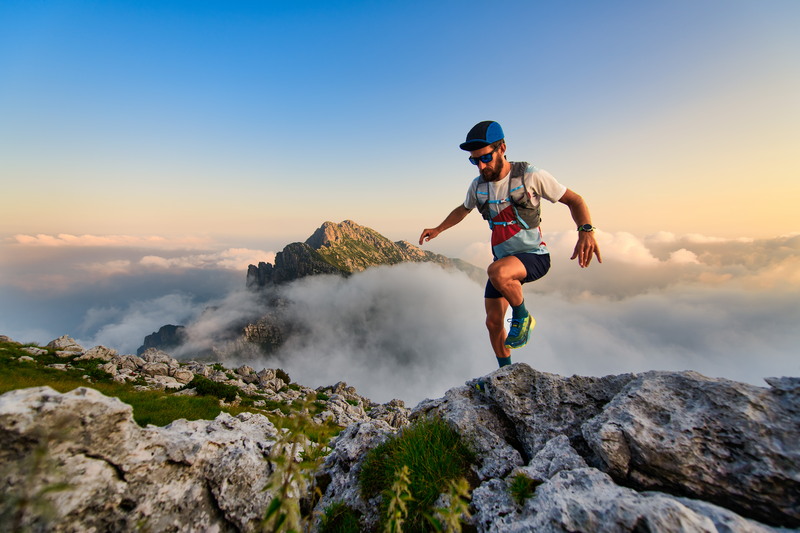
95% of researchers rate our articles as excellent or good
Learn more about the work of our research integrity team to safeguard the quality of each article we publish.
Find out more
ORIGINAL RESEARCH article
Front. Mater. , 13 January 2023
Sec. Structural Materials
Volume 10 - 2023 | https://doi.org/10.3389/fmats.2023.1101146
This article is part of the Research Topic Sustainable Fiber Reinforced Cementitious Composites for Construction and Building Materials View all 14 articles
In this study, PET plastic waste, which is a type of polymer commonly used in the manufacture of plastic bottles, has been incorporated into concrete by partially replacing the natural fine aggregate. An experimental study was conducted by casting and testing 90 concrete cylinders and 54 concrete cubes. A concrete mixture was designed in which the natural fine aggregate was substituted partially with PET plastic waste (PW) at a ratio of 0%, 25%, and 50%, with various w/c ratios of .40, .45, and .55. Physical, mechanical, and durability properties were assessed. The downside of the test results show degradation in each of the following characteristics: slump, compressive strength, splitting tensile strength, ultrasonic pulse velocity, water absorption, and porosity. The degradation of these characteristics increased with the increase in the volume of plastic aggregate (PA) and the w/c ratio. While the positive side of the results showed that with the increase of the PA volume and the w/c ratio, the fresh and dry densities decreased further, and by using 50% PET, the dry density became below 2000 kg/m3. Therefore, it is classified as lightweight concrete. Moreover, the fracture of concrete changed from brittle to more ductile compared to control concrete. Also, the thermal conductivity decreased significantly (11%–47%), and by using 50% of PET, the thermal conductivity became less than .71 W/mK, and accordingly, classified as a bearing insulator.
Concrete is one of the most popular and used building materials in the world (Kılıç et al., 2003; Topçu and Uygunoğlu, 2007; Akçaözoğlu et al., 2010; Khan et al., 2021b; Kumar et al., 2021; Khan et al., 2022d). Per year, “around 12 billion tonnes of concrete are produced worldwide, which is approximately 10 billion tonnes of rock (Shah and Wang, 2004). Besides, the concrete demand is estimated to grow to 18 billion tonnes by 2050 (Khoshkenari et al., 2014). The concrete industry has a significant environmental impact. Virtually, the use of concrete cannot be restricted, but there are different approaches to reduce its environmental impact. On the other hand, the human lifestyle and the new technology have led to the development of PW products, for which the enquiry of disposal perseveres (Khan et al., 2022a; Khan et al., 2022b). The majority of this solid PW is deposited in waste dump sites. This management of waste is unfavorable because most wastes are non-biodegradable and stay in the natural environment for hundreds and thousands of centuries (Rahmani et al., 2013; Barreto et al., 2021; de Azevedo et al., 2021; Room et al., 2021; Fediuk and Ali, 2022; Lesovik et al., 2022). Accordingly, the environmental friendliness of this process decreases” (Qaidi et al., 2022a).
However, “since earthquake forces are directly proportional to building mass, lightweight aggregate is a critical component in reducing the unit weight of concrete to make earthquake-resistant structures” (Kılıç et al., 2003; Qaidi et al., 2022b). Lightweight aggregates are often used in place of traditional aggregates to reduce the unit weight of concrete. There are various lightweight concrete applications that use natural or manufactured lightweight aggregates in the literature today. The cost of making artificial lightweight aggregate, on the other hand, is considerable due to the requirement of a high incineration temperature or heat treatment. As a result, unlike other materials, scientists are interested in using waste plastic granules as lightweight aggregate in the creation of lightweight concrete. This method enables the low-cost recycling of plastic trash as well as the manufacturing of lightweight concrete (Qaidi et al., 2022c; Tayeh et al., 2022a; Tayeh et al., 2022b).
According to Plastic-Europe (2019), plastics can usually be classified into two groups: thermoplastic and thermosetting. Thermoplastics, for example, PET, polyethylene (PE), polystyrene (PS), polypropylene (PP), and high-density polyethylene (HDPE), can be frequently reheated, reshaped, and frozen. In contrast, thermosets cannot be reformed after heated and formed, such as epoxy, silicone, melamine, phenolic, and polyurethane (PU). PET is the most common plastic around the world as it is frequently utilized for containers and bottles for various purposes. Bottles are discarded at a rate of almost half a billion each year; a million bottles are discarded every minute worldwide, and this rate is predicted to rise by 23% by 2025 (Qaidi and Al-Kamaki, 2021). Figure 1 shows the chemical compositions of the major types of polymers, as well as the global market share for each type, with C-O polymers (PET, PU, etc.) covering more than 18% of the worldwide market share (Ali et al., 2021; Khan, 2023).
FIGURE 1. Forms of synthetic plastics and percentage distribution of their market share (Ali et al., 2021).
Because of the benefits of plastics, such as their versatility and low cost, there is an increasing need for plastics all over the world. As a consequence, the world generated 368 million tonnes (Mt) of plastics in 2019, out of which 57.9 Mt were generated in Europe (Zulkernain et al., 2021). In the European Union, according to Plastic-Europe (2019) for post-consumer PW, as shown in Figure 2, about 39.5% of post-consumer plastic was recycled, and 43% of this waste was recovered for fuel and the rest of it is deposited in the landfill. While globally, only about 25% of PW is recycled and it is estimated that more than 33% of the PW produced will be recycled by 2050 (Babafemi et al., 2018; Almeshal et al., 2022; Emad et al., 2022; Faraj et al., 2022; He et al., 2022). Even if this estimate is correct, the volume of non-recycled waste remains highly undesirable and inefficient. As a result, millions of tonnes of plastic end up every year in oceans and landfills (Khan et al., 2019; Khan, 2022).
FIGURE 2. Recycling, energy recovery, and landfill percentages for plastic post-consumer waste in the EU in 2018 (Plastic-Europe, 2019).
The common techniques for treating PWs are varied, like burial, incinerate, and recycling. An undesirable effect of the burial method is the fact that plastic products slowly dissolve, and it takes hundreds of years to come back to the natural cycle. While the heat generated during the incinerate can be beneficial in the incinerate method. However, the burning of other forms of waste such as PET will release toxic gases. So, recycling appears to be the safest path for compliance with the ecosystem and economic gains (Albano et al., 2009). As a result, the recycling rate will be improving, and demand for natural raw material production will decrease. Thus, the environmental pressure on the concrete sector is reduced and eliminates the demand for capital assets, and as a result, contributes to sustainable production (Khan et al., 2021a; Khan, 2021). For these reasons, several papers have been conducted to use this waste in concrete and it is still ongoing. However, studies clearly indicated that not all of them are acceptable as concrete aggregates, as the types of PW that rely on resin and PET had been stated to have the greatest utilization rate for concrete production (Kore, 2018; Akeed et al., 2022; Al-Tayeb et al., 2022). Recycling PET into concrete, on the other hand, reduces quarrying operations and is a big step toward sustainability due to its economic and environmental benefits, therefore substituting PET for aggregates is a mutualistic solution to both concerns. Thus, the goal of the study is to investigate the behavior of concrete that contains a considerable amount of recycled PW of type PET as a fine aggregate.
Building materials such as cement and aggregate are in high demand as the construction sector increases. “As is well known, concrete mixes comprise 60 to 80 percent aggregate by volume, despite the fact that aggregate is a non-renewable resource. Continuous quarrying has a negative environmental impact as well as a scarcity of aggregate. As a result, aggregate replacement is preferred to reduce demand for quarries. PET, on the other hand, is a type of PW derived from human waste. As a result, there will be fewer landfills in the coming years. However, because recycling PET into concrete reduces quarrying operations and is a big step toward sustainability due to its economic and environmental benefits, replacing PET for aggregates is a mutualistic solution to both concerns”. Thus, the goal of the study is to understand the performance of concrete that contains a considerable amount of recycled PW of type PET as a fine aggregate.
Ordinary Portland cement (OPC) Type I which conformed with the Iraqi standard specification (I.O.S.) (No. 5/1984) (COSQC, 1984a) was used as the only binder in this study. The chemical properties and physical and mechanical properties of the OPC are presented in Table 1 and Table 2, respectively.
TABLE 2. The physical and mechanical characteristics of OPC Qaidi et al. (2022a).
The primary fine aggregate used in this study is natural sand which was sourced from the Khabor region of Dahok city in Iraq. The natural sand was sieved to ensure the natural sand used to have a maximum particle size of 4.75 mm. The natural fine sand possesses a fineness modulus of 2.81, specific gravity of 2.7, absorption of 1.14%, and bulk density of 1,634 kg/m3. The sieve analysis evaluation of the fine aggregates indicates they conform to the I.Q.S. No. 45/1984 Zone 2 (COSQC, 1984b).
Natural crushed aggregate from the Sejia district of Dahok city in Iraq was used as the coarse aggregate to produce the concrete mixtures. The crushed aggregates were sieved to ensure the maximum aggregate size is 19 mm. The aggregates were then washed to remove impurities and dried in the open air before use in the production of the concrete mixtures. The analysis of the properties of the aggregates showed that it conforms with the I.O.S. No. 45/1984 (COSQC, 1984b). The specific gravity, absorption, and bulk density of the coarse aggregate used are 2.67, .68%, and 1,540 kg/m3, respectively.
PET waste bottles (type BC210) were “processed and reused as partial replacement of the fine aggregate in this study. These PET bottles were supplied by the Light Plastic Factory. The properties of the PET waste bottles are presented in Table 3. After receiving the PET waste bottles, they were processed as follows: (i) removal of bottle caps followed by the washing and drying of the bottles, (ii) shredding and grinding of the PET waste bottles using a plastic granulator machine, and (iii) sieving the grinded PET waste bottles to obtain PET aggregate with a maximum aggregate size of 4.75 mm” (Qaidi et al., 2022a). Figure 3 shows the processed PET used as aggregates. It can be observed from Figure 3 that the PET aggregates possess flaky and angular morphology. The sieve analysis of all the aggregate used in this study is presented in Figure 4.
TABLE 3. “Physical and mechanical characteristics of used PET” Qaidi et al. (2022a).
For all concrete mixtures, potable water free of impurities was utilized as the mixing solution.
Superplasticizer (SP) with trading name “Sika ViscoCrete Hi-Tech 1,316 conforming to ASTM C494 (ASTM-International, 2015) type D and G was added into the concrete mixtures to improve the workability. Furthermore, several testing were carried out in order to determine the optimal dosage of SP, which impacts the fresh and mechanical properties of concrete mixes” (Qaidi et al., 2022a). The properties of the SP are presented in Table 4.
TABLE 4. Specification of superplasticizer Qaidi et al. (2022a).
The concrete mixtures made in this study were designed by ACI 211.1-91-R-02 (Aci-211-1-91, 2002) with w/c of .40, .45, and .55. The PET aggregates were used to replace the natural fine sand up to 50% at an increment of 25% (i.e., 0%, 25%, and 50%). Table 5 presents a detailed composition of the nine concrete mixtures made and evaluated. The mixture ID in Table 5 represents the content of PET aggregate used as a replacement of the fine aggregate and the w/c used.
The concrete mixtures were prepared as per ASTM-C192/C192M (2009) by using an electrical rotary tilting drum mixer with a capacity of .1 m3. The concrete mixtures were prepared by mixing the aggregates and OPC for 3 minutes followed by the addition of potable water premixed with the SP. After the mixing process was completed, the slump of the concrete mixtures was evaluated followed by casting of the samples for the properties to be evaluated. After casting the samples, the surfaces of the moulds were covered with a plastic sheet to avoid the loss of water from the samples. At approximately 24 h after casting the concrete samples, the samples were removed from the moulds and cured in water until the testing age. Furthermore, Superplasticizer (Polycarboxylic acid water-reducing agent) complying to ASTM C494 type D and G was added to the concrete mixtures to increase workability and eliminate the problem of PET floating in the mix.
The details of the tests carried out are outlined in Table 6.
Sandpaper was used to “smooth the surface of the cylinders and then cleaned with isopropyl alcohol. Then, two strain gauges (Model PL-60-11-3LJC-F) were installed, one horizontally and one vertically as T-shaped and equally spaced in the mid-height of all samples. The strain gauges were connected to the digital collector (data logger) for data collection during the compression test” (Qaidi et al., 2022a) as shown in Figure 5.
The workability of the mixture was evaluated in terms of the slump. Figure 6 shows the effect of PET content and w/c on the resulting workability of the concrete mixtures. “It can be noted that the slump reduced with higher content of PET regardless of the w/c ratio used. For example, compared to the control mix, at the 25% replacement, the reduction rate is 33.33% (w/c of .40), 38.1% (w/c of .45), and 41.28% (w/c of .55). While, at 50% replacement, the reduction rate is 79.9% (w/c of .40), 82.86% (w/c of .45), and 90.83% (w/c of .55). Nevertheless, all mixtures evaluated were still workable to some extent. The reduction in the workability of the concrete with the incorporation of PET can be attributed to the flat and irregular shape of PET particles which embodied them with a larger surface area compared to that of the natural sand. As a result, there would be further friction among the particles resulting in less workability of the concrete mixtures” (Qaidi et al., 2022a).
FIGURE 6. Slump test results for different ratios of PET and w/c: (A) slump value; and (B) reduction ratio.
The detrimental impact of the PET aggregate on the workability of the concrete mixture is more significant in mixtures made with higher w/c. This significant impact of the PET aggregate at higher w/c can be linked to bleeding as the interface between PET particles and the hydrated Portland cement becomes more porous at higher w/c. This behavior occurred as a result of the inability to water absorption and the flat form of the PET particles (Xie et al., 2021; Khan et al., 2022c). Thus, lowering the workability of the mixture. Similar observations have been reported by other studies where PET aggregates were used (Albano et al., 2009; Rahmani et al., 2013).
Figures 7, 8 present the fresh and dry densities results with different proportions of PET particles and w/c ratios. The results showed that the fresh and dry densities of all mixtures decreased with higher PET content. For fresh density, a maximum reduction of 17.75% was observed for concrete made with w/c of .55 and PET aggregate as a 50% replacement of the natural sand. For the dry density, the maximum reduction was 21.63% when the concrete was made with a w/c of .55 and PET as a 50% replacement of the natural sand. The reduction in the density of the concrete when PET aggregates were incorporated can be ascribed to the lower density of PET aggregates compared to that of natural sand.
FIGURE 7. Fresh density test results for different ratios of PET and w/c: (A) fresh density value; and (B) reduction ratio.
FIGURE 8. Dry density test results for different ratios of PET and w/c: (A) dry density value; and (B) reduction ratio.
The decline in concrete density is “more pronounced when higher w/c especially for the dry density, as shown in Figures 7, 8. This has been related to the excess water in the concrete samples that does not take part in the water and cement reactions. Thus, so small canals are formed that can create pores after drying. Therefore, lower unit weights are achieved for higher w/c ratios, as confirmed by Choi et al. (2005). Moreover, values of dry density for mixtures including 0% of PET PAs decreased from 2,388 kg/m3 (w/c of .40), 2,376 kg/m3 (w/c of .45), and 2,347 kg/m3 (w/c of .55) to 1993 kg/m3, 1964 kg/m3, and 1839 kg/m3, respectively, for mixtures including 50% of PET PAs. Thus, all dry density values, at the replacement ratio of 50%, were below 2000 kg/m3 [minimum dry density needed for lightweight concrete as per the classification of RILEM-LC2 (1978)]. Accordingly, these concretes are classified as lightweight concretes” (Qaidi et al., 2022a). This result is also within the scope of the results obtained by Azhdarpour et al. (2016).
Water absorption refers to the gradation of material porosity by measuring the ratios of water absorbed under a particular state (Farhana et al., 2015; Babafemi et al., 2018). Figures 9, 10 show the influence of w/c and PET aggregate content on the water absorption and the porosity of concrete mixtures evaluated. The values presented for each mixture represent the average value. From the data presented, the water absorption and porosity of concrete, irrespective of the w/c ratio, increased significantly with higher PET aggregate content. For example, compared to the reference mixture, at the 50% replacement, the increased rate of water absorption and porosity was, respectively, 101.25% and 69.32% (w/c of .40), 143.6% and 89.96% (w/c of .45), and 181% and 95.85% (w/c of .55). This behavior occurred because of the fact that natural aggregates and plastic are not sufficiently combined in the concrete matrix, leading to a porous matrix. This could be attributed to two factors: (i) the smooth surface and irregular shape of most PAs weakens the bond between the aggregates and the matrix of cement; and (ii) PAs almost have no absorption capacity for water, this will cause water to accumulate in the ITZ. Consequently, after these samples have dried, they create blank cavities. Accordingly, allowing the water absorption to increase when the specimens are exposed to water (Ahmed et al., 2021; Cao and Khan, 2021; Maglad et al., 2022).
FIGURE 9. Water absorption test results for various ratios of PET and w/c: (A) water absorption value; and (B) increase the percentage.
FIGURE 10. Porosity test results for different ratios of PET and w/c: (A) porosity value; and (B) increase percentage.
From the data presented in Figures 9, 10, “it can be observed that the water absorption and porosity increased with higher w/c. This is because the coated surface of the aggregate (surface-coating pozzalanics materials around aggregate) is smaller in case of a higher w/c ratio. So, as the volume of paste is decreased, the pores in the concrete increase, and the water absorption increases. Moreover, as this study mentioned before, the extra water in the concrete samples that has not reacted with the cement and has not been absorbed by the waste PET particles creates cavities after drying” (Qaidi et al., 2022a). Therefore, higher water absorption and porosity are achieved for higher w/c ratios, as confirmed by Albano et al. (2009); Heredia (2018).
The influence of the PET aggregate content and w/c on the compressive strength of concrete is presented in Table 7. “The presented results are the average of three specimens whose individual values are (±2.0 MPa) relevant to the average mentioned in Table 7. Generally, and at all test ages, while the substitution rate of PET particles increases, the trend of compressive strength is further reduced. For example, compared to the control mix, at the 25% replacement at 90-day, the reduction rate in strength was 43.46% (w/c of .40), 40.96% (w/c of .45) and 25.2% (w/c of .55). While, at the 50% replacement, the reduction rate was 76.12% (w/c of .40), 76.82% (w/c of .45), and 74.41% (w/c of .55). This strength lessening can be labelled by the following reasons: The bonding strength between cement paste and PW surfaces is diminished as a consequence of the smooth surface and flat shape of the plastic particles acting as a barrier and preventing cement paste from adhering to the natural aggregate. As a consequence, the ITZ in concrete containing PET particles is weaker than in control concrete, lowering the resulting compressive strength. Also, the water that did not get absorbed by the PET and did not take part in the reaction between water and cement surrounded these aggregates. This made the bonding weaker and led to the formation of tiny channels that, when dry, could turn into pores” (Qaidi et al., 2022a).
On the other hand, “it is noticed that when increasing the ratio of w/c, the compressive strength decreases, similar to the conventional concrete mixtures. Because, in the case of higher ratios of w/c, the coated surface of the aggregates (surface-coating pozzalanics materials around aggregate) is smaller, and as a result of lower paste volume, higher bleeding water quantity occurs (Xie et al., 2021; Khan et al., 2022b). The latter (excess water), which is mainly located around PET particles, does not participate in the reaction with the cement, generates a weaker connection between the cement paste and the PET particles, also, generates some small channels which can form pores after drying, causing a decrease in strength” (Ahmad et al., 2022; Al-Tayeb et al., 2022; Tayeh et al., 2022c).
To understand the impact of replacing a natural aggregate with a PA with various w/c ratios on the behavior of splitting tensile strength of concrete at 90 days, the experimental results are shown in Table 7. Generally, the results show performance reductions of tensile strength for any pattern of substitution, like compressive strength but with less severe due to the flexible nature of plastic. Accordingly, decreases in split tensile strength can be related to the same reasons as decreases in compressive strength.
From the failure patterns for both PET-containing and non-containing concrete, the splitting failures of PA concrete specimens did not show the typical brittle failure that was noted in the control concrete case. In other words, the inclusion of PW aggregates in concrete changed the concrete specimen fracture mode from brittle to more ductile failure. It was also noted that the concrete control specimens had a sudden breakage accompanied by sound. In contrast, the failure occurred smoothly without sound during breaking for specimens with PAs. This behavior is possible because of (i) according to Azhdarpour et al., 2016, the existence of flexible plastic particles at failure starting points. In this location (at the surfaces of failure), a part of the shear stress is transformed into tensile stress to beat the tensile strength of the PW. Also, plastic particles withstand part of the stress applied before being isolated from other materials. In other words, the plastic aggregates having angular and flat form can serve as a bridge between the two split parts. In contrast, fine aggregates are semi-spherical and brittle, causing them to separate from the surrounding cement before failure; and (ii) in specimens without PW, a failure occurs in the matrix around the aggregates and through coarse aggregate in the ITZ. Whereas in PET-concrete, failure mainly occurs around PET particles because of the elastic modulus mismatch and, also, the poor bond strength between cement paste and PET PW aggregate. This remark is compatible with the observation of Kou et al. (2009). Besides, the pores and cavities have appeared on the specimen external surface in honeycomb form. These observations are in line with those of Albano et al. (2009).
The stress-strain curves governed from compression tests, with different percentages of PET quantity and w/c, are plotted in Figure 11. From the data presented, “for a constant w/c ratio, it can be noticed that: (i) PET-concrete achieved the highest strain increase; and (ii) the peak compressive stress is less at a high PA level, but the corresponding strains are higher. In other words, due to the high flexibility of plastic, the ductility behavior will be enhanced at high PA substitutions. But, compared to the control concrete, the peak compressive stress was lower. Consequently, these reductions impact the stress-strain graph and lead to a decrease in the gradient of the graph during its linear elastic phase” (Qaidi et al., 2022a).
FIGURE 11. Stress-strain curve for cylinders with different ratio of PET and: (A) .40 w/c; (B) .45 w/c; and (C) .55 w/c.
UPV is a non-destructive test to verify concrete uniformity and quality. Durability and concrete strength are evaluated via the concrete specimen by determining the speed of an ultrasonic pulse through the concrete. Mostly, pulse velocity is influenced by the moisture quantity, density, and elasticity of the material (Akçaözoğlu et al., 2013). Figure 12 presents the UPV performance at different curing ages (7, 28, 90 days) for concrete specimens with different PET quantity and w/c ratios. Each value shown is an average of three cubes. Results indicate that UPV decreases by increasing the PET quantity in the mix. Such behavior can be attributed to: (i) the incorporation of PET directly affects the porosity of the concrete (cavities are formed), which in turn attenuates the velocity of the ultrasonic waves: and (ii) plastic particles have a plate structure (flat and angular shape), which has a role in becoming the refractive limit of ultrasonic waves. In contrast, as shown in Figure 12, it can be gotten that the UPV raised with curing age due to improving the chemical and physical characteristics of concrete as a result of continuing the hydration reactions. On the other hand, one can recognize from Figure 12, that the UPV declines as the w/c ratio increases. This is attributable to extra water stored in the pores which leave empty holes in the concrete upon hardening. Such outcomes have already been confirmed by Albano et al. (2009); Rahmani et al. (2013).
To increase understanding of the impact of the substitute of normal fine aggregate with a PA with various w/c ratios on the thermal conductivity (kc) behavior of concrete, the theoretical results obtained by the exponential equation provided by ACI-122R (2002) are presented in Table 8. Moreover, as this study mentioned earlier, the coefficient of Kc of this equation depends on the form of aggregate utilized in the mixtures of concrete. From the data presented, it can be found that with an increase in the quantity of PET aggregates, at a constant ratio of w/c, a significant decrease in Kc occurs. The reason for this decrease is attributed to (i) the PET aggregate had lower Kc (.15–.24 W/mK), compared with natural aggregate (2 W/mK), as stated by Hannawi et al. (2010). “Therefore, the PET aggregates act to slow thermal heat spread, causing a decline in Kc; and (ii) the presence of a large number of pores in the structure of PET-concrete, which reduces the Kc as a result of the low Kc of the air in these voids” (Akçaözoğlu et al., 2013).
On the other hand, from the data presented in Table 8, one can notice that the maximum reduction in Kc value is 46.99% (kc = .71 W/mK) for 50% replacement of PET (w/c ratio of .55), in comparison with control concrete (kc = 1.35 W/mK). Consequently, these composites (50% PET with .55 w/c) could be utilized as a bearing insulator according to RILEM-LC2 (1978) (kc sample <.75 W/mK,;
Figure 13 presents the relationship between the concrete compressive strength and split tensile strength at 90 days for several PET proportions and w/c ratios. Besides, the presented figure compares the relationship with that of other studies by Neville and Brooks (2010); ACI-318-19 (2019). Based on Figure 13, correlation follows a direct relationship. The related experimental expression derived from this analysis is:
FIGURE 13. The relationship between the concrete compressive strength and split tensile strength at 90 days.
The empirical relations of Neville and Brooks (2010); ACI-318-19 (2019), respectively, are expressed as:
As shown in Figure 13, it was observed that the ACI Building Code Eq. 3 ACI-318-19 (2019) gives a ratio closer to Eq. 1, as it appears to have reduced the tensile strength of the split. While Eq. 2 that proposed by Neville and Brooks (2010) underestimates considerably the split tensile strength of the respective PET substitution.
Figure 14 presents the relationship between the concrete compressive strength and UPV at 7, 28, and 90 days, for several PET proportions and w/c ratios. It can be remarked that the compression strength increases with an increase in ultrasonic speed for all w/c ratios. The experimental data are correlated to Eq. 4 where (V) is the UPV, and (fc´) is the compressive strength. Moreover, the coefficient of determination (R2) equals .95, thereby indicating a strong correlation.
FIGURE 14. The relationship between the properties of concrete for its compressive strength and UPV at 7, 28, and 90 days.
Figure 15 presents the relationship between compressive strengths and thermal conductivity at 28 days, for several PET proportions and w/c ratios. It remarks a direct relationship between them since R2 is .955.
Figure 16 presents the relationship between compressive strength and curing time at 7, 28, and 90 days, for several PET proportions and w/c ratios. Generally, the rate of strength, for the concrete-PET and the control concrete, has a similar pattern. The majority of mixes of PET-concrete were able to produce about 75%–90% of their corresponding 28-day strength at 7 days. Accordingly, it is close to controlling concrete.
Even so, it was found that the early development of the PET-concrete strength was somewhat changed from that of the control concrete. In Figure 16, the strength comparison showed that the PET-concrete mixtures developed within (75%–90%) of their 28 days strength in 7 days. In contrast, control concrete developed within (70%–80%). This behavior has also been studied by Tang et al. (2008), who mentioned that the probable cause could be because of the introduction of a PS aggregate, which would reduce the capacity of the specific thermal concrete causing a decreased heat loss to the environmental surroundings through the hydration process. Tang et al. (2008) based his conclusion on the investigation of Wang et al. (2007) who carried out a calorimetric test to calculate the temperature history of freshly concrete made from PS aggregate for 72 h. Overall, it can be an inference that concrete with a PET aggregate can have a superior accelerated early age because of the greater and faster heat produced during hydration.
This study investigated the influence of PET aggregate and w/c on the properties of concrete. Based on the results obtained from this experimental study, the following conclusions can be drawn.
1 Increasing the amount of PA as a partial replacement for sand, regardless of the w/c ratio, affects the workability of fresh concrete relative to the control mixture.
2 There is a decrease in the fresh density and dry density of PET-containing concrete with increasing replacement ratio and w/c ratios.
3 Concrete with 50% PA at .40-.55 w/c, had a dry density below 2000 kg/m3. Thus, this concrete can be categorized as lightweight concrete.
4 The percentages of water absorption and porosity in concrete using PET aggregate rise as the replacement ratios and w/c increase.
5 As the PET substitution ratio and w/c ratio increased, the compressive strength of all PET-concrete mixes decreased compared to the control concrete for all curing ages. Therefore, PET-concrete is recommended for non-structural applications (such as pavements and sports stadiums, wall panels, and channel liners), with a replacement ratio of no more than 25%.
6 The reason for the decline of the compressive strength is the reduction of cement hydration due to the following factors: (i) the weakness of the ITZ as a result of the smooth surface and flat shape of the plastic particles; and ii) the hydrophobic nature of the PET particles that has limited the entry of water into the concrete microstructure during the curing process.
7 It can be concluded from the stress-strain curves that with the increase of the PET quantity, the maximum stress increases significantly, and the plasticity behavior is improved due to the high elasticity of the plastic particles, but compared to the conventional concrete, the peak compressive stress was lower.
8 Because of the high porosity of PET-concrete and the lamination structure (angularity) of plastic particles, the UPV decreased at all curing ages as the proportion of PET particles and w/c ratios increased.
The following points suggest potential future research on this topic:
1. Studying the relationship between plastic concrete and steel reinforcement.
2. Studying the characteristics of PET and how the source influences concrete behavior.
3. Evaluating and comparing the entire construction monetary cost of making concrete with plastic versus traditional conventional concrete.
4. Studying the impact of combining plastic aggregate and fibers on the characteristics of concrete.
5. Studying the long-term durability of concrete with PET flakes.
The original contributions presented in the study are included in the article/Supplementary Material, further inquiries can be directed to the corresponding authors.
Conception and design of study: YA-K, SQ, and IH; Acquisition of data: YÖ, AFD, MS, and VS; Analysis and/or interpretation of data: SQ. Drafting the manuscript: YA-K, SQ, IH, YÖ, AFD, MS, and VS; Revising the manuscript critically for important intellectual content: AFD, MS, AND VS. Approval of the version of the manuscript to be published: YA-K, SQ, IH, YÖ, AFD, MS, and VS.
The research is partially funded by the Ministry of Science and Higher Education of the Russian Federation under the strategic academic leadership program “Priority 2030” (Agreement 075-15-2021-1333 dated 30.09.2021).
The authors declare that the research was conducted in the absence of any commercial or financial relationships that could be construed as a potential conflict of interest.
All claims expressed in this article are solely those of the authors and do not necessarily represent those of their affiliated organizations, or those of the publisher, the editors and the reviewers. Any product that may be evaluated in this article, or claim that may be made by its manufacturer, is not guaranteed or endorsed by the publisher.
Aci-122r (2002). Guide to thermal properties of concrete and masonry systems. Michigan, PA: ACI- Institute.
Aci-211-1-91 (2002). Standard practice for selecting proportions for normal, heavyweight, and mass concrete (Reapproved 2002). ACI- Institute.
Aci-318-19 (2019). Building Code requirements for structural concrete (ACI 318-19) and commentary (ACI 318r-19). ACI Committee 318.
Ahmed, H. U., Mohammed, A. A., Rafiq, S., Mohammed, A. S., Mosavi, A., Sor, N. H., et al. (2021). Compressive strength of sustainable geopolymer concrete composites: A state-of-the-art review. Sustainability 13, 13502. doi:10.3390/su132413502
Ahmad, J., Majdi, A., Babeker Elhag, A., Deifalla, A. F., Soomro, M., Isleem, H. F., et al. (2022). A step towards sustainable concrete with substitution of plastic waste in concrete: Overview on mechanical, durability and microstructure analysis. Crystals 12, 944. doi:10.3390/cryst12070944
Akçaözoğlu, S., Atiş, C. D., and Akçaözoğlu, K. (2010). An investigation on the use of shredded waste PET bottles as aggregate in lightweight concrete. Waste Manag. 30, 285–290. doi:10.1016/j.wasman.2009.09.033
Akçaözoğlu, S., Akçaözoğlu, K., and Atiş, C. D. (2013). Thermal conductivity, compressive strength and ultrasonic wave velocity of cementitious composite containing waste PET lightweight aggregate (WPLA). Compos. Part B Eng. 45, 721–726. doi:10.1016/j.compositesb.2012.09.012
Akeed, M. H., Qaidi, S., Ahmed, H. U., Faraj, R. H., Mohammed, A. S., Emad, W., et al. (2022). Ultra-high-performance fiber-reinforced concrete. Part IV: Durability properties, cost assessment, applications, and challenges. Case Stud. Constr. Mater. 17, e01271. doi:10.1016/j.cscm.2022.e01271
Al-Tayeb, M. M., Aisheh, Y. I. A., Qaidi, S. M. A., and Tayeh, B. A. (2022). Experimental and simulation study on the impact resistance of concrete to replace high amounts of fine aggregate with plastic waste. Case Stud. Constr. Mater. 17, e01324. doi:10.1016/j.cscm.2022.e01324
Albano, C., Camacho, N., Hernández, M., Matheus, A., and Gutierrez, A. (2009). Influence of content and particle size of waste pet bottles on concrete behavior at different w/c ratios. Waste Manag. 29, 2707–2716. doi:10.1016/j.wasman.2009.05.007
Ali, S. S., Elsamahy, T., Al-Tohamy, R., Zhu, D., Mahmoud, Y. a.-G., Koutra, E., et al. (2021). Plastic wastes biodegradation: Mechanisms, challenges and future prospects. Sci. Total Environ. 780, 146590. doi:10.1016/j.scitotenv.2021.146590
Almeshal, I., Al-Tayeb, M. M., Qaidi, S. M. A., Abu Bakar, B. H., and Tayeh, B. A. (2022). Mechanical properties of eco-friendly cements-based glass powder in aggressive medium. Mater. Today Proc. 58, 1582–1587. doi:10.1016/j.matpr.2022.03.613
Astm-C138 (2015). Unit weight, yield, and gravimetric air content of concrete. West Conshohocken, PA: ASTM International.
Astm-C192/C192m (2009). Standard practice for making and curing concrete test specimens in the laboratory. West Conshohocken, PA: ASTM International.
Astm-C39 (2012). Standard test method for compressive strength of cylindrical concrete specimens. Chủ biên.
Astm-C496 (2008). ASTM C496/C496M-04e1 standard test method for splitting tensile strength of cylindrical concrete specimens. Annu B ASTM Stand.
Astm-C597 (2009). 597, Standard test method for pulse velocity through concrete. West Conshohocken, PA: ASTM International.
Astm-C642 (2015). Standard test method for density, absorption, and voids in hardened concrete. West Conshohocken, PA: ASTM International.
Astm-International (2015). ASTM-C494: Standard specification for chemical admixtures for concrete. West Conshohocken, PA): Astm-International.
Azhdarpour, A. M., Nikoudel, M. R., and Taheri, M. (2016). The effect of using polyethylene terephthalate particles on physical and strength-related properties of concrete; a laboratory evaluation. Constr. Build. Mater. 109, 55–62. doi:10.1016/j.conbuildmat.2016.01.056
Babafemi, A. J., Šavija, B., Paul, S. C., and Anggraini, V. (2018). Engineering properties of concrete with waste recycled plastic: A review. Sustainability 10, 3875. doi:10.3390/su10113875
Barreto, E. D. S., Stafanato, K. V., Marvila, M. T., De Azevedo, A. R. G., Ali, M., Pereira, R. M. L., et al. (2021). Clay ceramic waste as pozzolan constituent in cement for structural concrete. Materials 14, 2917. doi:10.3390/ma14112917
Cao, M., and Khan, M. (2021). Effectiveness of multiscale hybrid fiber reinforced cementitious composites under single degree of freedom hydraulic shaking table. Struct. Concr. 22, 535–549. doi:10.1002/suco.201900228
Choi, Y.-W., Moon, D.-J., Chung, J.-S., and Cho, S.-K. (2005). Effects of waste PET bottles aggregate on the properties of concrete. Cem. Concr. Res. 35, 776–781. doi:10.1016/j.cemconres.2004.05.014
Cosqc (1984a). IQS No. 5: Portland cement. Baghdad, Iraq: Central Organization for Standardization and Quality Control.
Cosqc (1984b). IQS No. 45: Aggregate form natural sources for concrete and building construction. Baghdad, Iraq: Central Organization for Standardization and Quality Control.
De Azevedo, A. R., Marvila, M. T., Ali, M., Khan, M. I., Masood, F., and Vieira, C. M. F. (2021). Effect of the addition and processing of glass polishing waste on the durability of geopolymeric mortars. Case Stud. Constr. Mater. 15, e00662. doi:10.1016/j.cscm.2021.e00662
Emad, W., Mohammed, A. S., Bras, A., Asteris, P. G., Kurda, R., Muhammed, Z., et al. (2022). Metamodel techniques to estimate the compressive strength of UHPFRC using various mix proportions and a high range of curing temperatures. Constr. Build. Mater. 349, 128737. doi:10.1016/j.conbuildmat.2022.128737
Faraj, R. H., Ahmed, H. U., Rafiq, S., Sor, N. H., Ibrahim, D. F., and Qaidi, S. M. A. (2022). Performance of self-compacting mortars modified with nanoparticles: A systematic review and modeling. Clean. Mater. 4, 100086. doi:10.1016/j.clema.2022.100086
Farhana, Z., Kamarudin, H., Rahmat, A., and Al Bakri, A. (2015). “The relationship between water absorption and porosity for geopolymer paste,” in Materials science forum: Trans tech publ, 166–172.
Fediuk, R., and Ali, M. (2022). Recyclable materials for ecofriendly technology. Materials 15, 7133. doi:10.3390/ma15207133
Hannawi, K., Prince, W., and Kamali-Bernard, S. (2010). Effect of thermoplastic aggregates incorporation on physical, mechanical and transfer behaviour of cementitious materials. Waste Biomass Valorization 1, 251–259. doi:10.1007/s12649-010-9021-y
He, X., Yuhua, Z., Qaidi, S., Isleem, H. F., Zaid, O., Althoey, F., et al. (2022). Mine tailings-based geopolymers: A comprehensive review. Ceram. Int. 48, 24192–24212. doi:10.1016/j.ceramint.2022.05.345
Heredia, N. V. (2018). Incorporation of waste polyethylene terephthalate (PET) into concrete using statistical mixture design. Newfoundland: Masters, Memorial University of Newfoundland.
Khan, M. A. (2021). Towards progressive debonding in composite RC beams subjected to thermo-mechanical bending with boundary constraints–A new analytical solution. Compos. Struct. 274, 114334. doi:10.1016/j.compstruct.2021.114334
Khan, M. A. (2022). Bond parameters for peeling and debonding in thin plated RC beams subjected to mixed mode loading–Framework. Adv. Struct. Eng. 25, 662–682. doi:10.1177/13694332211065184
Khan, M. A. (2023). “Integrating BIM with ERP systems towards an integrated multi-user interactive database: Reverse-bim approach,” in Recent trends in construction technology and management (Springer), 209–220.
Khan, M. A., Irfan, S., Rizvi, Z., and Ahmad, J. (2019). A numerical study on the validation of thermal formulations towards the behaviour of RC beams. Mater. Today Proc. 17, 227–234. doi:10.1016/j.matpr.2019.06.423
Khan, M., Imam, M. K., Irshad, K., Ali, H. M., Hasan, M. A., and Islam, S. (2021a). Comparative overview of the performance of cementitious and non-cementitious nanomaterials in mortar at normal and elevated temperatures. Nanomaterials 11, 911. doi:10.3390/nano11040911
Khan, M., Sutanto, M. H., Napiah, M. B., Zoorob, S. E., Al-Sabaeei, A. M., Rafiq, W., et al. (2021b). Investigating the mechanical properties and fuel spillage resistance of semi-flexible pavement surfacing containing irradiated waste PET based grouts. Constr. Build. Mater. 304, 124641. doi:10.1016/j.conbuildmat.2021.124641
Khan, M., Cao, M., Chu, S., and Ali, M. (2022a). Properties of hybrid steel-basalt fiber reinforced concrete exposed to different surrounding conditions. Constr. Build. Mater. 322, 126340. doi:10.1016/j.conbuildmat.2022.126340
Khan, M., Cao, M., Xie, C., and Ali, M. (2022b). Effectiveness of hybrid steel-basalt fiber reinforced concrete under compression. Case Stud. Constr. Mater. 16, e00941. doi:10.1016/j.cscm.2022.e00941
Khan, M., Lao, J., and Dai, J.-G.The Hong Kong Polytechnic University, Hong Kong, China (2022c). Comparative study of advanced computational techniques for estimating the compressive strength of UHPC. J. Asian Concr. Fed. 8, 51–68. doi:10.18702/acf.2022.6.8.1.51
Khan, M. I., Sutanto, M. H., Yusoff, N. I. M., Zoorob, S. E., Rafiq, W., Ali, M., et al. (2022d). Cementitious grouts for semi-flexible pavement surfaces—a review. Materials 15, 5466. doi:10.3390/ma15155466
Khoshkenari, A. G., Shafigh, P., Moghimi, M., and Mahmud, H. B. (2014). The role of 0–2 mm fine recycled concrete aggregate on the compressive and splitting tensile strengths of recycled concrete aggregate concrete. Mater. Des. 64, 345–354. doi:10.1016/j.matdes.2014.07.048
Kılıç, A., Atiş, C. D., Yaşar, E., and Özcan, F. (2003). High-strength lightweight concrete made with scoria aggregate containing mineral admixtures. Cem. Concr. Res. 33, 1595–1599. doi:10.1016/s0008-8846(03)00131-5
Kore, S. D. (2018). Sustainable utilization of plastic waste in concrete mixes-a review. J. Build. Mater. Struct. 5, 212–217. doi:10.34118/jbms.v5i2.59
Kou, S., Lee, G., Poon, C., and Lai, W. (2009). Properties of lightweight aggregate concrete prepared with PVC granules derived from scraped PVC pipes. Waste Manag. 29, 621–628. doi:10.1016/j.wasman.2008.06.014
Kumar, S., Singh, E., Mishra, R., Kumar, A., and Caucci, S. (2021). Utilization of plastic wastes for sustainable environmental management: A review. ChemSusChem 14, 3985–4006. doi:10.1002/cssc.202101631
Lesovik, V., Tolstoy, A., Fediuk, R., Amran, M., Ali, M., and De Azevedo, A. R. (2022). Improving the performances of a mortar for 3D printing by mineral modifiers. Buildings 12, 1181. doi:10.3390/buildings12081181
Maglad, A. M., Zaid, O., Arbili, M. M., Ascensão, G., Șerbănoiu, A. A., Grădinaru, C. M., et al. (2022). A study on the properties of geopolymer concrete modified with nano graphene oxide. Buildings 12, 1066. doi:10.3390/buildings12081066
Plastic-Europe (2019). An analysis of European plastics production, demand and waste data, 147. Plastics–the facts.
Qaidi, S., Al-Kamaki, Y. S. S., Al-Mahaidi, R., Mohammed, A. S., Ahmed, H. U., Zaid, O., et al. (2022a). Investigation of the effectiveness of CFRP strengthening of concrete made with recycled waste PET fine plastic aggregate. PLOS ONE 17, e0269664. doi:10.1371/journal.pone.0269664
Qaidi, S., Najm, H. M., Abed, S. M., Özkılıç, Y. O., Al Dughaishi, H., Alosta, M., et al. (2022b). Concrete containing waste glass as an environmentally friendly aggregate: A review on fresh and mechanical characteristics. Materials 15, 6222. doi:10.3390/ma15186222
Qaidi, S. M. A., Tayeh, B. A., Isleem, H. F., De Azevedo, A. R. G., Ahmed, H. U., and Emad, W. (2022c). Sustainable utilization of red mud waste (bauxite residue) and slag for the production of geopolymer composites: A review. Case Stud. Constr. Mater. 16, e00994. doi:10.1016/j.cscm.2022.e00994
Qaidi, S. M. A., and Al-Kamaki, Y. S. S.University of Duhok (2021). State-of-the-Art review: Concrete made of recycled waste PET as fine aggregate. J. Duhok Univ. 23, 412–429. doi:10.26682/csjuod.2020.23.2.34
Rahmani, E., Dehestani, M., Beygi, M., Allahyari, H., and Nikbin, I. (2013). On the mechanical properties of concrete containing waste PET particles. Constr. Build. Mater. 47, 1302–1308. doi:10.1016/j.conbuildmat.2013.06.041
Rilem-Lc2 (1978). Recommendation: Functional classification of lightweight concrete. Mater. Struct. 5, 173–175.
Room, S., Ali, M., Alam, M. A., Khan, U., Ammad, S., and Saad, S. (2021). “Assessment of lightweight Aggregate concrete using textile washing stone,” in Proceeding of the 2021 Third International Sustainability and Resilience Conference: Climate Change, Sakheer, Bahrain, November 2021 (IEEE), 327–333.
Shah, S. P., and Wang, K. (2004). “Development of ‘green’cement for sustainable concrete using cement kiln dust and fly ash,” in Proceedings of the International Workshop on Sustainable Development and Concrete Technology, Beijing, China, May 2004 (Beijing, China: Iowa State University, Ames), 15–23.
Tang, W. C., Lo, Y., and Nadeem, A. (2008). Mechanical and drying shrinkage properties of structural-graded polystyrene aggregate concrete. Cem. Concr. Compos. 30, 403–409. doi:10.1016/j.cemconcomp.2008.01.002
Tayeh, B. A., Akeed, M. H., Qaidi, S., and Bakar, B. H. A. (2022a). Influence of microsilica and polypropylene fibers on the fresh and mechanical properties of ultra-high performance geopolymer concrete (UHP-GPC). Case Stud. Constr. Mater. 17, e01367. doi:10.1016/j.cscm.2022.e01367
Tayeh, B. A., Akeed, M. H., Qaidi, S., and Bakar, B. H. A. (2022b). Influence of sand grain size distribution and supplementary cementitious materials on the compressive strength of ultrahigh-performance concrete. Case Stud. Constr. Mater. 17, e01495. doi:10.1016/j.cscm.2022.e01495
Tayeh, B. A., Akeed, M. H., Qaidi, S., and Bakar, B. H. A. (2022c). Influence of the proportion of materials on the rheology and mechanical strength of ultrahigh-performance concrete. Case Stud. Constr. Mater. 17, e01433. doi:10.1016/j.cscm.2022.e01433
Topçu, İ. B., and Uygunoğlu, T. (2007). Properties of autoclaved lightweight aggregate concrete. Build. Environ. 42, 4108–4116. doi:10.1016/j.buildenv.2006.11.024
Wang, K., Ge, Z., Grove, J., Ruiz, J. M., Rasmussen, R., and Ferragut, T. (2007). Developing a simple and rapid test for monitoring the heat evolution of concrete mixtures for both laboratory and field applications.
Xie, C., Cao, M., Guan, J., Liu, Z., and Khan, M. (2021). Improvement of boundary effect model in multi-scale hybrid fibers reinforced cementitious composite and prediction of its structural failure behavior. Compos. Part B Eng. 224, 109219. doi:10.1016/j.compositesb.2021.109219
Keywords: plastic waste, polyethylene terephthalate, mechanical properties, durability properties, functional properties
Citation: Qaidi S, Al-Kamaki Y, Hakeem I, Dulaimi AF, Özkılıç Y, Sabri M and Sergeev V (2023) Investigation of the physical-mechanical properties and durability of high-strength concrete with recycled PET as a partial replacement for fine aggregates. Front. Mater. 10:1101146. doi: 10.3389/fmats.2023.1101146
Received: 17 November 2022; Accepted: 02 January 2023;
Published: 13 January 2023.
Edited by:
Li Li, Northwest A and F University, ChinaReviewed by:
Ayaz Ahmad, University of Galway, IrelandCopyright © 2023 Qaidi, Al-Kamaki, Hakeem, Dulaimi, Özkılıç, Sabri and Sergeev. This is an open-access article distributed under the terms of the Creative Commons Attribution License (CC BY). The use, distribution or reproduction in other forums is permitted, provided the original author(s) and the copyright owner(s) are credited and that the original publication in this journal is cited, in accordance with accepted academic practice. No use, distribution or reproduction is permitted which does not comply with these terms.
*Correspondence: Shaker Qaidi, c2hha2VyLmFiZGFsQHVvZC5hYw==; Ibrahim Hakeem, aXloYWtlZW1AbnUuZWR1LnNh
Disclaimer: All claims expressed in this article are solely those of the authors and do not necessarily represent those of their affiliated organizations, or those of the publisher, the editors and the reviewers. Any product that may be evaluated in this article or claim that may be made by its manufacturer is not guaranteed or endorsed by the publisher.
Research integrity at Frontiers
Learn more about the work of our research integrity team to safeguard the quality of each article we publish.