- 1College of Mechanical and Electrical Engineering, Zhengzhou Railway Vocational and Technical College, Zhengzhou, China
- 2Zhengzhou Key Laboratory of Advanced Functional Materials, Zhengzhou, China
- 3College of Mechanical and Electrical Engineering, Zhengzhou Tourism Vocational College, Zhengzhou, China
This paper briefly analyzes the current development of lightweight design and applications for hydraulic support in the coal mines. Specifically, the comparative investigations of lightweight design demonstrate the potential application for carbon fiber reinforced composites (CFRP) in the production and manufacturing process of hydraulic support. After analyzing the major industrial applications of CFRP in the three main parts, hydraulic structure, cylinder and special frames, it demonstrated the feasibility of the potential CFRP exploitations in the future research of hydraulic support for coal mining sites.
1 Introduction
Hydraulic support is the key structure of fully mechanized coal mining equipment. Its function is to support the roof of the mine, ensure the safety of the working space, and move the scraper conveyor and shearer in the working face (Buyalich et al., 2019; Gou, 2014). Therefore, the lightweight of coal mine hydraulic support inevitably requires the modifications of hydraulic supports design, with changing structures or replacing materials, so as to lower down the cost and improve the product competitiveness. There are two ways to facilitate the lightweight design (Yan, 2017): to change the structures or to replace the materials. Researches on structural modification focus on the optimization of structure by using simulation technology (Cheng et al., 2021; Chen and Liang, 2010; Cui and Zhang, 2012; Shao et al., 2012; Zhu et al., 2012; Han, 2020), Although these studies have made considerable progress, there is still lack of lightweight optimization through reducing the material mass. Carbon fiber composites have high strength, high Young’s modulus, high temperature resistance and corrosion resistance. With gradual cost drop, carbon fiber composites possess a wide range of applications in the design and manufacture of hydraulic supports. Although the lightweight research on new materials replacement is still in the preliminary stage, the application of carbon composite has made a new guidance. Owing to the advantages of high fatigue tolerance and impact resistance, carbon fiber reinforced composites (CFRP) can be exploited for structural parts applied with variable loads, which have been widely used in aerospace, national defense, wind power equipment, automobile manufacturing and rail transportations (Li et al., 2017; Duan et al., 2019). For instance, Wang (Wang, 2016) applied the CFRP on top beam of the hydraulic support, and used the 3D finite element model to simulate the roof beams. Results demonstrated optimization of the beam structure and reduction of the volume and weight provided a solid theoretical ground for the feasible CFRP applications. Moreover, the specific strength and modulus of carbon fiber composites can be improved by orders of magnitude, compared with high strength steel (Deng and Hao, 2019).
2 CFRP applications on hydraulic structure
The main loaded parts of hydraulic support are commonly welded, such as the top beam and the base. In mining sites, structural design for the top beam, such as the strength requirement and parameters optimization, is critical because the external load contacts the top beam to transfer force, aiming at achieving the significant technical and economic benefits by proper weight reduction (Xue, 2018). The carbon fiber honeycomb structure, including upper and lower panels, can improve the plate stiffness and stability, consolidate the internal I-shaped structure, and further reduce the surface density of the panels, as shown in Figure 1A. Carbon fiber structure reinforces the panel, to bear the load and improve the flexural performance. Due to the incombustibity, the panel can be exploited to manufacture some high-temperature resistant facilities, specifically suitable for the mining environment. Moreover, carbon fiber honeycomb panel can be resized under various requirements, in terms of its extraordinary plasticity. Therefore, the honeycomb structure possesses the feasibility to replace the box structure of top beam, shield beam, base, links and other major loaded parts in hydraulic support.
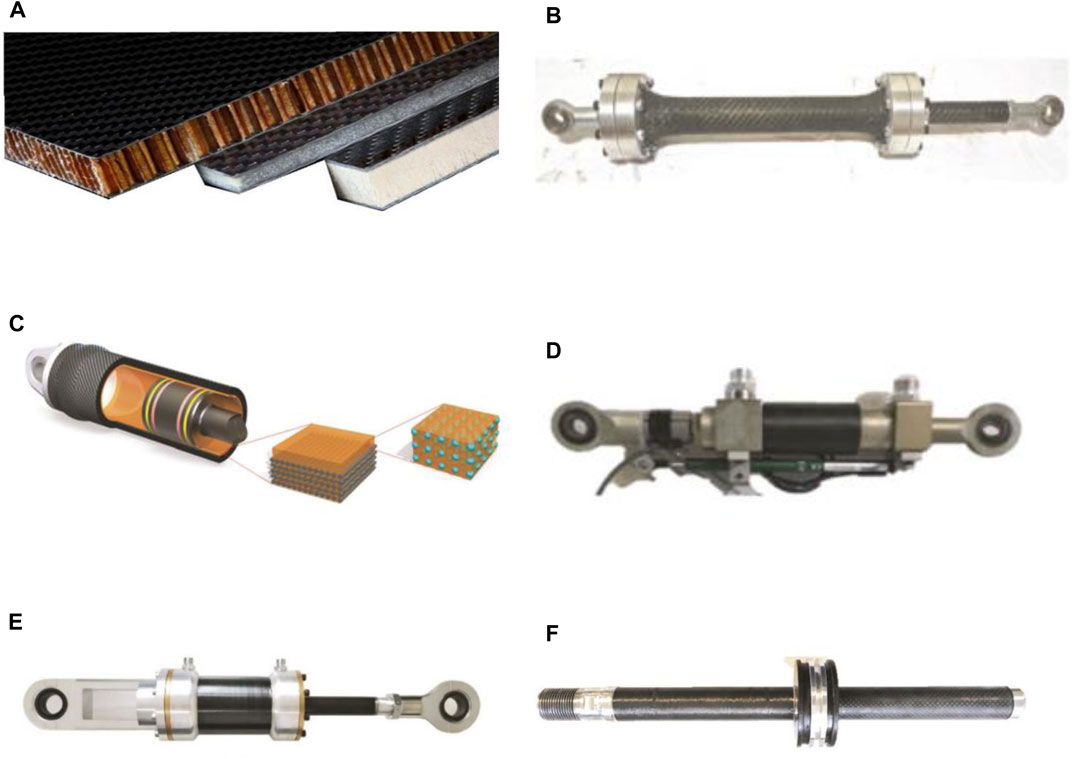
FIGURE 1. (A) Carbon fiber honeycomb panel; (B) Carbon fiber hydraulic cylinder; (C) Schematic diagram of nano coating; (D) Carbon fiber hydraulic cylinder made by Zhejiang University; (E) Carbon fiber cylinder; (F) Piston rod.
3 CFRP applications of on hydraulic cylinder
Hydraulic cylinder is another important part of hydraulic support. However, due to the heavy weight, low strength, weak stiffness and fatigability, the traditional steel hydraulic cylinder cannot adapt to the requirement of the modern design. Using CFRP to fabricate hydraulic cylinder, can achieve high stiffness, high strength, lateral force bending stiffness, and seal improvement for in and out of the oil channel, such as friction pair. Solazzi (Solazzi, 2019) designed a connection structure between CFRP and aluminum alloy piston, as shown in Figure 1B. Compared with the traditional steel hydraulic cylinder, the weight of the CFRP cylinder can be dramatically reduced to 88%, with no leakage. But the starting pressure, running friction and other test data, remained undiscussed. ELASSWAD (Elasswad et al., 2018) proposed a CFRP hydraulic cylinder, using a robot knee joint for the piston rod. The cylinder was dynamically tested, but the design pressure was merely 1.5 MPa, whose efficiency needs to be further improved. The CFRP hydraulic cylinder manufactured by the Lightweight Centre of Saxony (LZS) was tested with a 30% weight reduction to replace the retractable and retractable actuators for the nose landing gear of passenger aircraft (Modler et al., 2016). Scholz (Scholz and Kroll, 2014) designed a nano Al2O3 reinforced epoxy coating to replace the metal lining, in terms of the failure of FRP lamination structure and various mechanical properties, as shown in Figure 1C. After 50,000 piston stroke tests under typical working conditions of 0.4Hz and 35Mpa, it was found that the coating was not cracked and the interface was not stratified. It is further proved that the nano-structured coating possesses stiff toughness, high wear resistance and strong adhesion. Ritchie (Li et al., 2022) manufactured a CFRP piston and an end cover for the underground mining equipment. Although their weights are lighter than the steel piston and end cover, carbon fiber surface finish is not consistent, which causes the material fragments off and damage the hydraulic system. This problem hinders the CFRP applications on the hydraulic cylinder. Zhang (Zhang et al., 2016) developed a lightweight coated CFRP hydraulic cylinder (0.89 kg), as shown in Figure 1D, with working pressure of 21 MPa, cylinder diameter of 25 mm, rod diameter of 15 mm and stroke of 57 mm. Shang et al. (2021) designed a 75 mm diameter CFRP cylinder to adapt to the characteristics of winding forming process, and a prototype of CFRP cylinder with aluminum alloy, as shown in Figure 1E-(f), which met requirements for the hydraulic cylinder under the Chinese GB/T 15,622–2005 standard, with 31.5 MPa pressure, no leakage, and 0.05 MPa starting pressure. Results demonstrated efficient lightweight facilitation. The CFRP hydraulic cylinder developed by Harbin FRP Research Institute (Elasswad et al., 2018) adopted the CFRP reinforced metal lining. The knurled and sandblasted interface is exploited to prevent the bonding between CFRP and metal. Under special groove design, the cylinder and the end cover are connected on the inner surface of the end cover. The piston rod uses CFRP reinforced metal lining, whose weight is 45% lighter than the prototype. Consequently, the commercialization of the CFRP based product can be potentially applied for lightweight purposes, although the researches of CFRP on the hydraulic cylinder and other important components are still in shortage.
4 CFRP applications of special frames
With the environmental protection purposes, researchers innovatively developed two new kinds of hydraulic supports, the solid filling support (Cui et al., 2011) and the paste filling support (Zhang et al., 2010), as shown in Figure 2A,B. With the assistance of the filling conveyors, such supports have been widely applied in the coal mining sites. Furthermore, the applications of CFRP on bottom panel of the solid filling support and clapboard of the paste filling support achieved the extraordinary lightweight effects, due to the high strength and toughness of CFRP. Therefore, such applications also demonstrate high-cost CFRP can be exploited in some certain circumstances, where economic benefits could cover the cost of CFRP.
5 Discussions
The application of CFRP can reduce the weight of the support, enhance the lifting and extending performances and prolong the service life of the hydraulic support. Follow the cost reduction the application of carbon fiber reinforced composites in the manufacturing process of hydraulic support is expected to achieve large-scale industrial practices in the future.
1) Carbon fiber honeycomb panel could replace the top beam, shield beam, base, links and other main loaded parts of the hydraulic support with box structure at the technical level. However, there is still a lack of investigations on the related optimization design and experimental verification.
2) Carbon fiber composites research of hydraulic cylinder has a certain amount of progress on commercial use, but the high cost restricts its applications in hydraulic support columns and jack. Furthermore, the universal testing standards for CFRP cylinder has not yet been set up, which cannot assist to achieve complete characterized performances for the products, such as high pressure resistance, low leakage, low friction (Li et al., 2022).
3) Weight reduction for the equipment parts is the goal of high efficiency in the coal mine industry. With the development and application of special support, it is expected to apply carbon fiber composites for the hydraulic support to drive the lightweight development in the coal mines, and achieve promising effects of energy conservation and emission reduction.
Author contributions
HG and MZ carried out the structure of the article and wrote the paper, PL and ML figured out the literature review on CFRP applications, YZ finished drafting and analysis and the final version of the manuscript.
Funding
This research is funded by the Key Research Project of Zhengzhou Railway Vocational and Technical College in 2022 (2104220001).
Conflict of interest
The authors declare that the research was conducted in the absence of any commercial or financial relationships that could be construed as a potential conflict of interest.
Publisher’s note
All claims expressed in this article are solely those of the authors and do not necessarily represent those of their affiliated organizations, or those of the publisher, the editors and the reviewers. Any product that may be evaluated in this article, or claim that may be made by its manufacturer, is not guaranteed or endorsed by the publisher.
References
Buyalich, G., Byakov, M., Buyalich, K., and Shtenin, E. (2019). Development of powered support hydraulic legs with improved performance. E3S Web Conf. 105, 03025. doi:10.1051/e3sconf/201910503025
Chen, L., and Liang, J. (2010). Application of ANSYS in optimal design of hydraulic support. Mach. Des. Manuf. 3, 82–84. doi:10.19356/j.cnki.1001-3997.2010.03.036
Cheng, Y., Liu, Z., and Zhang, N. (2021). “Structure Design of Hydraulic Cylinder Support Based on Finite Element Analysis,” in Paper presented at 2021 12th International Conference on Civil Engineering, Materials and Machinery Changchun, China. doi:10.25236/ICCEMM.2021.033
Cui, Y., Guo, H., and Jin, T. (2011). Design of the six-column solid filling hydraulic support. Min. Mach. 39, 21–24. doi:10.16816/j.cnki.ksjx.2011.07.006
Cui, S. W., and Zhang, L. Y. (2012). Strength Analysis of High Strength Steel Hydraulic Support. Appl. Mech. Mater. 1867 (184–185), 676–679. doi:10.4028/www.scientific.net/AMM.184-185.676
Deng, K., and Hao, S. (2019). Discussion on lightweight design of hydraulic support for coal mine. Shandong Ind. Technol. 16, 16. doi:10.16640/j.cnki.37-1222/t.2019.06.012
Duan, Q., Han, Z., and Sun, M. (2019). Research on application of new Q890 high strength steel in hydraulic support. Coal Mine Mach. 40, 119–121. doi:10.13436/j.mkjx.201904042
Elasswad, M., Tayba, A., Abdellatifalfayad, S., and Khalil, K. (2018). Development of lightweight hydraulic cylinder for humanoid robots applications. Proc. Institution Mech. Eng. Part C J. Mech. Eng. Sci. 232 (18), 3351–3364. doi:10.1177/0954406217731794
Gou, X. (2014). Lightweight design and research of hydraulic support for coal mine. Chongqing, China: Chongqing University of Technology. Master Thesis.
Han, L. (2020). Application of Q690 steel plate in hydraulic support structure. Tong Coal Sci. Technol., 18–21. doi:10.19413/j.cnki.14-1117.2020.06.006
Li, X., Xu, K., Zhao, G., Zhao, X., and Yao, L. (2017). Development of low carbon bainite steel with yield strength of 890MPa. Coal Mine Mach. 38, 127–129. doi:10.19413/j.cnki.14-1117.2020.06.006
Li, Y., Shang, Y., Wan, X., Jiao, Z., and Yu, T. (2022). Design and experiment on light weight hydraulic cylinder made of carbon fiber reinforced polymer. Compos. Struct. 291, 115564. doi:10.1016/j.compstruct.2022.115564
Modler, N., Hufenbach, W., Cherif, C., Ulbricht, V., Gude, M., Maron, B., et al. (2016). Novel Hybrid Yarn Textile Thermoplastic Composites for Function Integrating Multi Material Lightweight Design. Adv. Eng. Mater. 18 (3), 361–368. doi:10.1002/adem.201600028
Scholz, S., and Kroll, L. (2014). Nanocomposite glide surfaces for FRP hydraulic cylinders – evaluation and test. Compos. Part B Eng. 61, 207–213. doi:10.1016/j.compositesb.2014.01.044
Shang, Y., Wang, X., Yu, T., Li, Y., and Jiao, Z. (2021). Lightweight integrated piston rod structure. Chinese Patent, CN113027853A[P].
Shao, Y., Zeng, Q., Xian, G., Liu, X., and Wang, C. (2012). Product information modeling of hydraulic support based on ontology. Min. Mach. 40, 17–20. doi:10.16816/j.cnki.ksjx.2012.09.005
Solazzi, L. (2019). Feasibility study of hydraulic cylinder subject to high pressure made of aluminum alloy and composite material. Compos. Struct. 209, 739–746. doi:10.1016/j.compstruct.2018.11.021
Wang, F. (2016). Optimization design and analysis of top beam of composite plate hydraulic support. Hebei, China: Hebei University of Engineering.
Xue, C. (2018). Lightweight design of hydraulic support for coal mine. Mach. Manag. Dev. 33, 38–39. doi:10.16525/j.cnki.cn14-1134/th.2018.11.017
Yan, X. (2017). Lightweight design and research of hydraulic support for coal mine. Mod. Industrial Econ. Inf. Technol. 7, 79–80+96. doi:10.16525/j.cnki.14-1362/n.2017.11.35
Zhang, J., Bao, J., Zhang, D., Bing, X., and Chao, Q. Inlaid connection of carbon fibre reinforced plastic cylinder, IEEE International Conference on Aircraft Utility Systems, 10-12 Oct. 2016. Beijing, China, 1024–1029.
Zhang, W., Yang, M., Guo, H., and Liang, Y. (2010). Design of the paste filling hydraulic supports. Coal Mine Mach. 31, 125–126. doi:10.13436/j.mkjx.2010.12.046
Keywords: carbon fiber, reinforced plastics, hydraulic support, lightweight, equipment
Citation: Guo H, Zhou M, Li P, Lv M and Zhang Y (2022) Prospects of carbon fiber composites applications in hydraulic supports. Front. Mater. 9:997258. doi: 10.3389/fmats.2022.997258
Received: 18 July 2022; Accepted: 03 August 2022;
Published: 30 August 2022.
Edited by:
Huan Qi, Zhejiang University of Technology, ChinaReviewed by:
Sida Liu, Jiangxi University of Science and Technology, ChinaShi Wentian, Beijing Technology and Business University, China
Wang Zhankui, Henan Institute of Science and Technology, China
Copyright © 2022 Guo, Zhou, Li, Lv and Zhang. This is an open-access article distributed under the terms of the Creative Commons Attribution License (CC BY). The use, distribution or reproduction in other forums is permitted, provided the original author(s) and the copyright owner(s) are credited and that the original publication in this journal is cited, in accordance with accepted academic practice. No use, distribution or reproduction is permitted which does not comply with these terms.
*Correspondence: Miaomiao Zhou, bW16aG91MjAyMkBvdXRsb29rLmNvbQ==