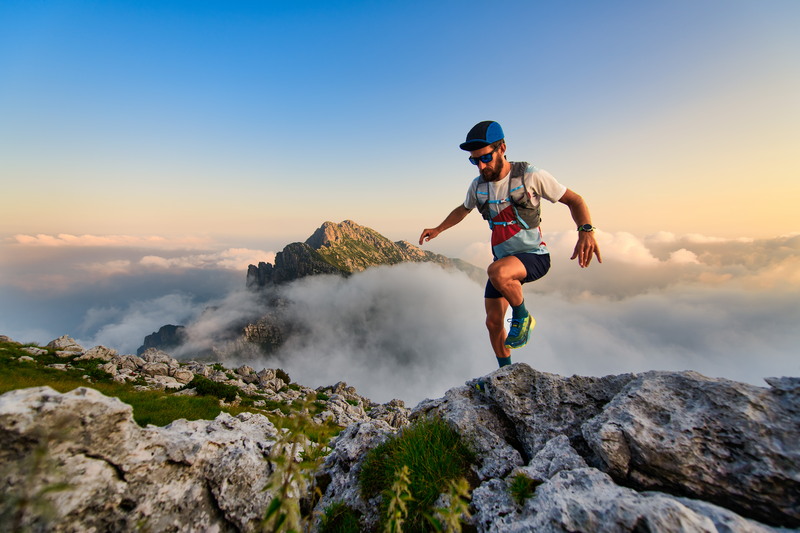
95% of researchers rate our articles as excellent or good
Learn more about the work of our research integrity team to safeguard the quality of each article we publish.
Find out more
REVIEW article
Front. Mater. , 30 August 2022
Sec. Polymeric and Composite Materials
Volume 9 - 2022 | https://doi.org/10.3389/fmats.2022.995516
This article is part of the Research Topic Fabrication, Characterization, and Deterioration Mechanism of Advanced Polymeric, Ceramic and Metallic Composite Materials in Electrical and Electronic Engineering View all 7 articles
In recent years, solid organic materials such as silicone rubber and epoxy resin have been widely used in electrical equipment due to their excellent insulation properties. However, as a result of manufacturing and design flaws as well as aging issues during operation, the insulating materials in the linked state no longer fit tightly and tiny structural defects (defect size less than 10 mm) develop, such as debonding at the composite interface, pores or cracks within the insulating material, etc. Tiny defects are prone to partial discharges and breakdowns, compromising the safety of high-voltage power equipment, particularly when subjected to strong electric fields. Therefore, it is necessary to carry out non-destructive testing (NDT) for such tiny defects. Such defects are small in size, easily buried in the material, and even some are wrapped in metal, which in turn requires very high detection accuracy, but traditional methods are difficult to achieve, so NDT technologies for tiny defects within insulating materials have become a research hotspot in the field of electric power in recent years. This paper firstly introduces the sources of tiny defects in solid organic insulating materials for electrical equipment. Secondly, the harm caused by structural defects is elaborated. Finally, emerging NDT methods and their advantages and limitations in defect detection are described in detail. The review aims to provide the reader with a comprehensive overview of most of the NDT techniques used in the detection of tiny defects within solid organic insulating materials for electrical equipment and their most salient features.
With the continuous development of extra high voltage and ultra-high voltage, higher requirements are placed on the insulation system of power equipment. Silicone rubber, epoxy resin, cross-linked polyethylene (XLPE), insulating paper, and other solid organic materials are widely used in high-voltage electrical equipment, due to their excellent electrical properties, high and low temperature resistance, hydrophobic properties, etc. (Hackam, 1999; Wu and Cheng, 2017). However, imperfect processes in the production of organic materials lead to residues of reactants (de Tourreil et al., 2000; Montesinos et al., 2002), high voltage electrical equipment is not designed and erected properly, resulting in long-term mechanical loads (Kumosa et al., 2005; Kone et al., 2017; Yuan et al., 2022), complicated operating environment leads to material aging problems (Yuan and Wang, 2020), tiny defects within the insulation materials can be caused by these problems. Tiny defects in the high electric field region are prone to partial discharges (Xing et al., 2021; Meng et al., 2022), causing permanent damage to insulating materials. The air in the defects can accelerate the aging of the material, which will further reduce the mechanical properties and insulation properties of the material, forming a vicious cycle and leading to the collapse of the insulation system. Eventually, the equipment will breakdown. Not only does it cause damage to high-voltage power equipment, but it also seriously affects the normal operation of the grid system. Therefore, it is necessary to carry out NDT of tiny defects inside the insulating material (Liu et al., 2022a).
Based on the magnitude of the defect, there are three categories for tiny defects. Firstly, millimeter defects range in size from 1 to 10 mm. Secondly, sub-millimeter defects range in size from 0.1 to 1 mm. Lastly, micron defects range in size from 1 to 100 μm.
This paper begins by summarizing the causes of tiny defects from three perspectives: the manufacture of insulating materials, the design and manufacture of equipment, and the operational environment, including internal ones like the synthesis of solid organic materials and imperfect design of high voltage power equipment, as well as external ones like temperature, humidity, mechanical stress, and radiation, can cause tiny defects. These factors will result in millimeter-and micron-scale structural defects in insulating materials, and these defects will cause serious harm to the power grid system, including the failure of composite insulators, transformers, cables, and other components. The novel NDT techniques were then grouped and summarized according to the magnitude of the defect. Microwave technology and infrared thermography are two technologies for finding millimeter-sized defects. Currently, the most popular methods for finding sub-millimeter-level defects are terahertz (THz) technology and ultrasonic technology. Non-linear ultrasound technology and X-ray computed tomography are both capable of detecting micron-scale defects. Also presented are their advantages and detecting principles. Finally, the emerging NDT technology’s drawbacks are outlined, along with potential future routes for advancement.
Tiny defects are one of the main reasons for the insulating materials' failure. Such defects can occur for a variety of reasons, including internal ones like the synthesis of solid organic materials and inadequate high-voltage power equipment design, as well as external ones like temperature, humidity, mechanical stress, and radiation (Spellman et al., 1999; Saleem and Akbar, 2022). External factors are the main cause of tiny defects. Composite insulators, XLPE cables, and oil-immersed transformers play an important role in grid systems, but are also prone to failure (Jin et al., 2022), caused by tiny defects. Therefore, many scholars have done a lot of research on the mechanism of tiny defects.
The following research has been done recently on the internal mechanism of tiny defects. Yuan et al. (2015) analyzed two shattered mandrels and concluded that the interface defects in the composite insulator were primarily caused by the outflow of the release agent. Interfacial gaps cause internal electric field distortions and partial discharges, accelerating the hydrolysis of the mandrel, which in turn leads to continued defect enlargement. The core rod of the composite insulator is made of epoxy resin glued to a stretched glass fiber, and needs to add a release agent when drawing glass fiber in order to reduce friction (Liang et al., 2021). During the pressing process of the sheath and the mandrel, the release agent precipitates under the influence of temperature and pressure. This degrades the bonding strength between the sheath and the mandrel and causes defects. Qi et al. (2019) reported that incomplete reaction of additives, improper material handling, and metal inclusions can result in the formation of tiny defects during the synthesis of cross-linked polyethylene. These tiny defects will continue to grow under the influence of various factors and will eventually lead to the failure of the cable material. Production process defects are inevitable (Zhang et al., 2021), power equipment’s service life is influenced by production quality, which requires tight management.
The following study has been conducted on the external mechanism for the generation of tiny defects. In general, interface defects are caused by a variety of external factors and are a complex, long-term process. Bastidas and Rowland (2017) reported that composite insulators are subject to various dynamic mechanical loads during design, production, and installation (de Tourreil, 1990). Long-term physical aging will cause the bonding performance between the mandrel and the sheath to deteriorate, resulting in minute air defects. In regions of high electric fields, minute defects can trigger partial discharges, resulting in permanent interface damage and, ultimately, interface decomposition. Wang et al., 2020a placed the composite glass fiber reinforced epoxy resin in hot air at 130 °C for thermal aging. With aging time, the surface of the resin began to become wrinkled and pores appeared, and the pores would further develop into micro cracks, resulting in When air enters the resin, thermal aging is aggravated, forming a vicious circle. Cracks will develop into the resin, and after developing to the interface, the fiber and the resin matrix will be debonded. In addition to this, the curing agent used in the FRP manufacturing process generates nitric acid under the action of water and electricity (Tourreil et al., 2005). Nitric acid will corrode the epoxy resin, causing the epoxy-silicon rubber interface to separate, and the air gap will distort the electric field and cause partial discharge. Under the dual action of an electric field and air, it will accelerate the decomposition of epoxy resin, eventually resulting in the failure of composite insulators (Gao et al., 2018; Liang et al., 2018; Nandi and Reddy, 2020; Xu et al., 2021).
High-voltage power equipment is the heart of the power transmission system, and its operational dependability is crucial for the power system’s proper operation. Insulation deterioration is one of the leading causes of high-voltage power equipment failure (Wang et al., 2022). Tiny defects can destroy the integrity of the structure (White et al., 2001), affect the local voltage distribution, generate partial discharges (Mauoux and Laurent, 1995), damage the interface material, and the presence of oxygen and water in the tiny defects can accelerate the material aging, which will result in the collapse of the insulation system, the failure of the equipment, unplanned power outages, severe economic loss, and even cause disasters such as electric shock and fire (Nazmul Huda et al., 2012). Important components of the power system, such as composite insulators, XLPE cables, and transformers, are susceptible to failure due to modest insulation system flaws. Numerous researchers have discovered that minute flaws at the silicone rubber-mandrel contact can cause the insulator to fail (Armentrout et al., 2003; Wang et al., 2014; Zheng and Gao, 2019). Tiny defects in a cable might lead it to crack and eventually fail (Zhang et al., 2018; Batalović et al., 2019). Tiny defects in insulating cardboard will cause the risk of overheating and local breakdown of the transformer (Zhang et al., 2014; Hou et al., 2021). These faults will cause damage to high-voltage power equipment, affect the normal transmission of electricity, and cause power outages, followed by the failure of the factory to operate normally, resulting in a lot of economic losses.
Infrared thermography testing is a non-contact, non-destructive transient detection technology that uses an infrared thermal imager to acquire surface temperature data from the object being studied (Meola et al., 2004). The infrared thermal imaging system comprises an external heater source, an infrared camera, a control system, and an image processing system. When infrared thermal imaging technology detects defects in composite materials, a heat source is positioned above the organic material to be tested to heat its surface, and heat flow is conveyed within the material. Due to the considerable difference in thermal properties such as thermal conductivity between air and the tested organic material, the temperature distribution on the surface of the material is changed when there are faults inside the organic material. The change in the surface temperature of the material is captured by the infrared camera positioned above the sample, and the collected surface temperature information is processed by the image processing unit to obtain a temperature field heat map. Based on the temperature change in the temperature field heat map, information such as defect scale and defect depth is obtained (Qu et al., 2020). Figure 1 shows the principle of infrared thermography testing.
FIGURE 1. Principle of infrared thermal wave imaging detection (Qu et al., 2020).
Infrared thermography non-destructive testing technology has the advantages of quick and intuitive detection, no harm to the human body, and no physical contact, thus it is widely utilized in aviation, industry, medicine, and other fields. The method has been widely utilized in the United States, France, and Russia to detect internal faults in aviation composite materials, and the American Society for Testing Materials (ASTM) has established an inspection standard to correspond. Recently, infrared thermography has been extensively utilized in the electrical power industry to detect intrinsic faults in organic materials (Cao et al., 2008; Chou and Yao, 2009; Huda et al., 2012). However, infrared thermography has numerous drawbacks. For example, infrared thermography equipment is costly (Usamentiaga et al., 2014) and its results are vulnerable to ambient factors (Ibarra-Castanedo and Maldague, 2013).
Infrared thermography is a quick and effective technique for identifying delamination, debonding, and foreign substances within organic composites (Inagaki et al., 1999; Wu et al., 2011). Huda and Taib (2013) used infrared thermal imaging technology to find the defect of peeling off epoxy resin insulation coating on a dry-type transformer core. Liu et al. (2017) suggested a method for detecting internal faults in composite insulators by pulse thermal imaging. This approach uses a flashlight as a pulse heat source to heat a silicone rubber sheath with internal flaws and captures surface temperature data using a thermal imager, with an acquisition time of 60 s and an acquisition frequency of 25 Hz. The enormous quantity of acquired data reveals the internal faults of the silicone rubber, demonstrating the viability of the pulse thermal imaging approach for detecting the internal defects of the composite insulator. Wei et al., 2021a proposed an improved peak slope time method based on pulsed thermal imaging technology, which improved the accuracy of defect depth estimation. Figure 2 shows the imaging effect of pulsed thermal imaging to detect internal defects in the composite insulator.
FIGURE 2. Raw thermal images of silicon rubber plate specimen (A) The 100th frame of raw thermal images sequence, (B) The 275th frame of raw thermal images sequence (Liu et al., 2017).
There are two ways of microwave detection: reflection and transmission. The detection method is to inject electromagnetic waves with a frequency of 300 MHz to 300 GHz into the organic material through the probe. The incident microwave interacts with the internal structure of the organic material and the reflection or transmission at the interface of different media, using a probe to receive reflected or transmitted waves and judge the information of internal defects in materials based on the characteristics of the received reflected or transmitted waves (Lutz et al., 2012). Figure 3 shows the working principle of the microwave detection system.
Microwave testing is a real-time, nondestructive testing technology that offers the benefits of easy operation, robust penetrability, high detection accuracy, and low cost (Pastorino, 2004). Typically, the microwave signal power is only a few milliwatts, so there are no safety issues. There are numerous uses for microwave inspection in the aerospace field, the food industry, and the construction industries. Examples include the detection of internal faults in fiber-reinforced composites in aviation (Li et al., 2021a), foreign body contamination in food (Ricci et al., 2020; Tobon Vasquez et al., 2020), and pipe weld inspection (Stakenborghs and Little, 2010), etc. However, the skin effect occurs when microwaves enter metals and high-conductivity composites, so microwave inspection cannot be used to detect internal defects within these materials.
Based on the above advantages, microwave non-destructive testing technology can be used to detect millimeter-scale pores inside insulating materials of high-voltage power equipment (Li et al., 2019), delamination (Bakhtiari et al., 1994; Qaddoumi et al., 1996; Shrifan et al., 2021), foreign bodies (Umeda et al., 1980), fractures (Brown et al., 1999) and other defects. Wang et al. (2015) discovered the internal flaws of composite insulators using 24 GHz microwaves and evaluated the effect of detection distance on the detection outcomes. The study of experimental findings revealed that the microwave inspection process is sensitive to inspection distance and that there is an optimal detection distance. Mei et al. (2021) developed a full-scale composite insulator detection system based on microwave detection technology. Wang et al., 2021a used a vector network analyzer and a waveguide to build a microwave inspection system, using microwaves with a frequency of 2–24 GHz, and measured significant differences in the waveforms of composite insulators with different defect characteristics, proving that the microwave reflection technology detects composite insulator feasibility defects. Figure 4 shows the results of different defect characteristics detected by microwave technology.
Digital shearography is a non-contact, highly accurate, and rapid non-destructive testing technology (Zhu et al., 2011; Liu et al., 2022b). Its inspection system includes a laser emitter, a shearing device, an imaging system, and an image processing system. The sample is deformed by heating or applying force, then the laser transmitter emits a beam to illuminate the surface of the object to be measured. The reflected light produces two mutually misaligned images on the CCD camera through the shearing device, and the two mutually misaligned images form a stripe map through the image processing system. The map can reflect the internal defects of the sample (Huang, 2021). Figure 5 shows the working principle of the digital shearography technique.
FIGURE 5. The working principle of digital shearography technique (Kumpati et al., 2021).
Digital shearography does not require a reference beam, so its optical detection system is reasonably simple, and the technology can directly measure displacement changes on the measuring object’s surface (Hung et al., 2013). Digital shearography technologies are widely used in the automotive and aerospace industries (Hung and Ho, 2005; Kumpati et al., 2021) because of their significant advantages. For example, they are used to check the quality of car tires and detect defects in aircraft composites. The technology has become increasingly popular for detecting defects inside insulating materials in recent years. Gu et al. (2018) discovered artificial defects within aluminum plates using phase-shifting dual-observation digital shearography. The defects were 30 mm wide and 2 mm deep, with a depth measurement error of less than 5%. Liu et al. (2019) successfully found artificial defects inside composite insulators based on digital shearography, validating the feasibility of the technology for the detection of defects inside composite insulators. Wei et al., 2021b used a new method combining infrared thermography with digital shearography to detect different sizes of debonding defects between silicone rubber and steel plates.
Liang et al., 2020a first presented a new approach for detecting air gap flaws within insulators using induced charge tomography (ICT). The principle of ICT is to reconstruct the dielectric constant and electric field division inside gas-insulated transmission lines (GIL) using induced charges on the conductor and pipe wall surface, and the rebuilt result reflects a good indication of internal defects (Liang et al., 2020b; Li et al., 2021b).
Liang et al., 2020c reconstructed the dielectric constant distribution of a GIL with two crack defects using ICT techniques. The reconstructed dielectric constant distribution map not only reveals the profile of the insulator but also identifies defects within the insulator. Therefore, the technology can be utilized for online monitoring and diagnostics of electrical equipment, and it enables visual detection of defects, which has promising future applications.
With the continuous development of non-destructive testing technology, the detection accuracy has also improved. Therefore, ultrasonic testing methods and terahertz testing methods are proposed for sub-millimeter defects.
Ultrasonic testing employs a single probe that emits sound waves with a frequency greater than 20 kHz. Ultrasonic waves are transmitted into the tested sample via a coupling agent (Deng et al., 2017). If the sample being tested contains flaws such as porosity, delamination, debonding, cracks, etc., the ultrasonic wave will be completely reflected at the fault. The echoes are reflected back along the same path and received by the probe, while the signal acquisition unit converts the obtained acoustic impulses into electrical signals that are displayed on the screen. By measuring the position and amplitude of the reflected waves, the location and size of the detected defects can be determined (Tiwari et al., 2017; Zhao et al., 2020). Figure 6 depicts the ultrasonic testing principle.
Ultrasonic testing is a conventional NDT technique (Arias and Achenbach, 2004), but it offers the benefits of strong penetrability, high sensitivity, quick detection speed, and low cost. Ultrasonic inspection is widely used in the pipeline industry, aerospace, and electrical power fields, including the detection of defects such as cracks, cavities, and pores in pipelines (Alobaidi et al., 2015), fatigue and fracture detection of composite materials for aircraft (Yawn et al., 1999), and detecting submillimeter defects in organic insulating materials (Merten, 2010). However, high-frequency ultrasonic waves are severely attenuated in air, and the attenuation increases with frequency when travelling through organic materials (Thomas et al., 2014). Consequently, pulse waves with a lower frequency are typically utilized for defect detection.
Complex composite insulator shapes make it difficult to detect tiny defects using conventional ultrasonic testing methods. Therefore, numerous researchers have undertaken exhaustive studies on ultrasonic testing technologies. Varlow et al. (1994) detected air gap defects inside 20 mm thick XLPE samples using an ultrasonic pulse echo technique. Yuan et al. (2016) tested composite insulator samples with artificial defects using a phased array ultrasonic testing technique and effectively discovered the air gap defect between the glass-fiber reinforced plastic mandrel and the silicone rubber and the pore defect under the insulator shed. Huang et al. (2018) employed pulsed ultrasound as the excitation signal, assessed the amplitude, phase, and spectrum of the echo, devised an imaging method suited for air gaps and internal impurities, and successfully discovered flaws with a depth of 55 mm and a size of 1 mm in silicone rubber. Additionally, ultrasound can also detect air gap flaws in organic insulating materials such as XLPE and epoxy resin. Tian et al. (2019) successfully detected faults of various sizes in epoxy resin inside gas-insulated switchgear (GIS) by using ultrasonic pulse echo. Zhou et al. (2020) utilized the ultrasonic pulse echo method to detect air gap flaws in 15 mm thick epoxy resin samples with a 2 mm fault size. Figure 7 demonstrates the findings of ultrasonic pulse echo inspection technology used to detect faults of various sizes within epoxy resin.
FIGURE 7. Reflected ultrasonic waveforms at voids with different depths d in the specimen (A) No defects, (B) Void with depth d = 15 mm, (C) Void with depth d = 20 mm (Tian et al., 2019).
Despite the fact that ultrasonic testing technology has effectively detected micron-scale defects in insulating materials, a coupling agent is required for sample testing, and the tedious operation is not favorable to practical applications. Researchers presented THz nondestructive testing technology to address this issue.
The principle of terahertz detection is similar to other electromagnetic wave detections. The optical parameters of the tested sample are extracted by using the characteristics of the frequency band (0.1–10 THz) (Fukunaga et al., 2011), and then the defect information inside the detection object is obtained by analysis. Terahertz waves mainly have the following four advantages: 1. low energy, which will not have adverse effects on human health during testing; 2. coherence, which can simultaneously measure parameters such as phase and amplitude during testing; 3. selective penetration, good penetration for non-polar substances, polar substances and metals have high absorption of terahertz waves; 4. transient, the transmission or reflection behavior of terahertz waves in the detection sample is completed in a short time, saving a lot of testing time.
According to the various propagation pathways, terahertz time-domain spectroscopy (THz-TDS) systems can be split into two modes: transmission and reflection (Tao et al., 2020). Terahertz waves have good penetrability to non-polar insulating materials. According to the different characteristics of hydrogen bond oscillations, the substances containing hydrogen bond structures can be finely analyzed. Therefore, the transmission mode is often used to detect the micro-water content in objects (Yin et al., 2020). The terahertz time-domain spectroscopy system uses a femtosecond laser as a terahertz radiation source to scan the sample point by point or side, and uses a terahertz detector to record the terahertz wave time-domain signal or frequency-domain signal and process the collected signal to generate For two-dimensional images, information such as defect depth and size can be obtained by calculating parameters such as the time domain waveform of the sample and the peak delay time of the blank sample reference waveform. The principle of the THz detection system is shown in Figure 8.
Terahertz waves have excellent penetration into non-polar materials and are widely utilized in cultural heritage protection, food and aerospace, such as the hollowing deterioration of stone (Meng et al., 2021), testing the internal moisture content of fruits (Gong et al., 2022), microstructure optimization of thermal barrier coatings for aircraft engines (Ye et al., 2020), and defect detection in rocket fuels (Hlosta et al., 2022). Terahertz time-domain spectroscopy is also used to detect submillimeter-scale defects in insulating materials in high-voltage equipment (Cheng et al., 2021). Cheng et al. (2016) performed NDT on silicone rubber-epoxy boards with artificial defects using a pulse wave of 0.one to two THz. By examining the delay time between the peak of the sample’s time-domain waveform and the peak of the reference waveform, the precise location of faults with a depth of 0.4 mm and a minimum size of 1.5 mm was determined with an error of less than 3%. Xie et al. (2020) used a transmissive terahertz time-domain spectroscopy system for NDT of cross-linked polyethylene samples with artificial defects. By combining the refractive index and dielectric properties of XLPE by collecting the amplitude and phase information of the time-domain signal and other parameters, the calculated defect size of XLPE is 1.04mm, while the actual defect size is 1.01mm, and the calculation error is only 2.9%. Consequently, terahertz time-domain spectroscopy can find the XLPE air gap defects. Li et al., 2021c successfully discovered interfacial flaws and metal foreign bodies in insulating paperboard. Zhang et al. (2022) utilized a terahertz frequency-modulated continuous wave nondestructive inspection imaging system to linearly scan the XLPE cable with prefabricated defects, reconstruct a three-dimensional perspective image, and intuitively observe the prefabricated air and water hole defects in the insulating layer. Figure 9 shows the results of the THz method used to detect debonding and metallic foreign objects in insulating paperboard.
FIGURE 9. THz time domain waveforms in the debonding and metal foreign matter regions (Li et al.,2021).
X-ray Digital Radiography (X-DR) is a quick, intuitive, and effective nondestructive testing technology (Wang H. et al., 2019; Zhang et al., 2020). Its detection system consists of four parts: digital imaging, image processing, protection modules, and auxiliary facilities (Yan, 2013). The X-DR inspection principle is that the radiation source emits X-rays that pass through the sample. The attenuated transmitted rays are converted into analogue and digital signals by the radiation receiving and converting device, and the findings are visually displayed on the display via an image processing system, allowing for the viewing of the sample’s interior defects. Figure 10 shows the X-DR detection system.
FIGURE 10. X-DR detection system (Zhang et al., 2020).
X-DR is one of the most common techniques used in modern industrial detection. For instance, it is extensively used to detect welds and internal faults in castings in the field of mechanical engineering (Zhao, 2014), as well as to expose poor restoration work and forgeries of old buildings in the field of cultural heritage (Casali, 2006). Recently, X-ray digital imaging technology has been extensively utilized for the detection of interior faults in insulation materials (Yu et al., 2012; Tan et al., 2019). Zhang et al. (2017) employed X-DR technology to detect air hole defects within the quad bundle spacer damper and to conduct quality checks on the T-joints of the copper strip of the earthing network at the construction site, where they discovered air hole problems. Yin et al. (2018) found internal air hole defects in basin-type insulators utilizing an industrial CT/DR inspection system, and the minimum defect diameter was 0.5 mm. Test results confirmed the viability of this technology for detecting internal defects in basin-type insulators. Jiang et al. (2020) conducted DR non-destructive testing on epoxy resin supported insulating rods and detected defects in cavity defects and delamination defects. This provided a theoretical reference for defect detection in epoxy resin supported insulating rods, which has significant engineering application value.
Composite insulators have the advantages of light weight, excellent mechanical qualities, excellent insulating capabilities, and anti-pollution flashover performance over traditional ceramic insulators, and are widely used in transmission lines (Ghosh and Khastgir, 2018). The sheath made of silicone rubber is joined to the core rod made of glass fiber-reinforced plastic through the action of a couplant to create contact-type bonding and a composite insulator (Jeenjitkaew and Guild, 2017). Interfacial defects are one of the most prevalent failure forms of composite insulators, accelerating the aging of organic materials, reducing mechanical qualities and even causing insulator strings to fail, which poses a significant threat to the regular operation of the power grid (Rouhanizadeh and Kermanshachi, 2020).
Interface defects not only include macroscopically visible air gap defects but also include macroscopically difficult-to-find kissing defects formed by the breakage of chemical bonds between the interfaces, and the size of such defects is less than 100 microns. Emerging NDT technologies such as infrared thermal imaging, microwaves, THz, and ultrasonic are difficult to detect kissing defects (Wang Y. et al., 2020). For this type of interface defect, scholars from Chongqing University proposed a new non-destructive testing method based on non-linear ultrasonic. The principle of the nonlinear ultrasonic testing system is shown in Figure 11. Zhang et al. (2019) proposed that the interface failure of the insulator was caused by the low surface roughness of the core rod and the failure of the coupling agent. They also introduced the hydrogen bond spring model and the friction hysteresis model into the mechanical wave conduction process for simulation calculation, and discovered that the contact interface failure will result in a decrease in mechanical wave conduction. This caused the peak value of the second harmonic to grow. The samples with flaws measuring 50 microns in size were subsequently examined using an ultrasonic examination device. It was determined that there was no significant difference between the well-bonded sample and the defective sample in terms of the fundamental wave, but that there was a substantial difference in terms of the second harmonic. To verify the correctness of the theory, the normalized nonlinear parameters are finally constructed to analyze the interface state of the composite insulator. Wang et al., 2020a created nonlinear parameters by mathematical modeling and numerical calculation and inspected contact insulator samples using high-power ultrasonic testing equipment. The comparison of harmonics reveals that the amplitude of the second harmonic of insulators with kissing defects is much greater than that of samples without faults. According to the experimental results, the developed nonlinear parameters may successfully diagnose the close-contact defects that form during the initial phase of interface debonding. Figure 12 depicts the outcomes of nonlinear ultrasonic techniques used to detect minute defects in composite insulators.
FIGURE 12. Experimental results of the plate samples with 1–20 μm defect (A) Time domain signal, (B) Spectrogram (Wang et al.,2019).
The X-ray computed tomography (XCT) detection system uses a computer-controlled ray source to emit X-rays of different wavelengths, scans the sample through penetration, and uses a detector to collect transmission signals in different directions. The collected signals are processed by an image reconstruction algorithm to obtain multiple two-dimensional tomographic images. A three-dimensional three-dimensional view of the tested sample is reconstructed from the two-dimensional image, which can intuitively display the defect information inside the sample (Brisard et al., 2020). Figure 13 illustrates the principle of computed tomography detection. According to the aforementioned principles, it is necessary to use a high-precision motion control system to continuously adjust the sample’s position during the inspection process, so that the sample is in the optimal position, and to create high-quality two-dimensional tomograms and three-dimensional three-dimensional images to facilitate subsequent defect analysis of the inspected samples.
FIGURE 13. Principles of tomographic imaging (A) Parallel-beam, (B) Cone-beam (Brisard et al.,2020).
X-ray computed tomography detection is a nondestructive testing technique with the benefits of short wavelength, strong penetrability, intuitive imaging, and the identification of micron-scale defects (Wang X. et al., 2021). XCT is used in a wide range of applications in aerospace, food, and construction, such as assessing the porosity of composite materials for airplanes (Dilonardo et al., 2020), inspecting the quality of agricultural products (Du et al., 2019), and measuring the density and moisture content of wood (Wang et al., 2019c; Wang J. et al., 2019). In recent years, XCT detection technology has been extensively utilized for the detection of defects in insulating materials (Hao et al., 2019). Li et al. (2017) created an industrial computed tomography non-destructive testing system for power equipment and carried out non-destructive testing of basin-type insulators in GIS. Using the three-dimensional image generated by the scanning process, the position and magnitude of faults in epoxy resin were intuitively and clearly identified. Liu and Tan (2020) utilized a standing wave electron linear accelerator as a ray source, a line array detector composed of multiple detector units as a detection system, and an image reconstruction processing system composed of multiple processing units to create an industrial computed tomography nondestructive testing system. This system was applied to nondestructive testing and quality evaluation of power equipment materials. Huang et al. (2021) used X-ray micro-computed tomography to scan and image composite insulators with abnormal heating and discovered that there were defects within them that led to abnormal fever, with a defect detection precision of 2 μm. Zhang and Luo (2022) utilized X-ray computed tomography for non-destructive testing of insulating tie rods in GIS circuit breakers and discovered air gap defects between epoxy resin and aluminum alloy inserts. Figure 14 depicts the results of the X-ray micro-computed tomography technique used to discover the composite insulator’s interior flaws. Presently, there are few applications for defect detection within insulating materials, but it has been utilized extensively in the medical, aerospace, national defense, and military industries, and has collected a great deal of expertise. Consequently, X-ray computed tomography technology has a great deal of room for improvement in the detection of power equipment, and it will be utilized extensively in the future for the identification of internal defects in organic insulating materials.
FIGURE 14. 3D images of the air gap and the through channels in the rods, obtained by the X-ray micro-CT method (Huang et al.,2021).
The advantages and disadvantages of the previously discussed NDT methods are compared in Table 1.
The existing non-destructive testing method can only be used to detect material defects in the laboratory and cannot be utilized to detect the real operating state of electrical equipment. The primary causes are as follows:
Firstly, there are insufficient techniques for remote detection. Continuously operating high-voltage equipment is surrounded by a strong electric field. To ensure personal safety, detecting equipment must be kept at a distance of more than 2 m from personnel.
Secondly, the miniaturization of detection equipment. High-voltage equipment cannot be detected online due to the system’s overall complexity. Structural miniaturization is an unavoidable requirement to achieve on-line detection of nondestructive testing technologies.
Lastly, environmental adaptability. Temperature, electromagnetic radiation, etc. interfere with the detection accuracy. Near high-voltage equipment, there is a strong electromagnetic field that interferes with the detection of electromagnetic radiation such as microwaves, terahertz waves, and X-rays. The thermal conductivity of insulating materials is less than that of metals, and the propagation speed of heat waves in insulating materials is slower. As a result, the infrared thermal imaging detection technology is greatly influenced by the ambient temperature, and the greater the detection depth, the greater the error.
There is still a long way to go for NDT technology to achieve online detection, and a great deal of research is required to address the obstacles along the way.
XZ: Writing—original draft, Conceptualization, Methodology. LC: Resources, Supervision, Writing—review and editing. YL: Supervision, Editing. BT: Writing, Investigation. JW: Supervision, Investigation. RL: Supervision, Funding acquisition.
This work was supported by the National Natural Science Foundation of China [Grant No. 52077013].
Thanks for the strong guidance given by LC in the writing of the paper, the help of BT, YL and JW, and the financial support of RL.
The authors declare that the research was conducted in the absence of any commercial or financial relationships that could be construed as a potential conflict of interest.
All claims expressed in this article are solely those of the authors and do not necessarily represent those of their affiliated organizations, or those of the publisher, the editors and the reviewers. Any product that may be evaluated in this article, or claim that may be made by its manufacturer, is not guaranteed or endorsed by the publisher.
Alobaidi, W. M., Alkuam, E. A., Al-Rizzo, H. M., and Sandgren, E. (2015). Applications of ultrasonic techniques in oil and gas pipeline industries: A review. Am. J. Operations Res. 05, 274–287. doi:10.4236/ajor.2015.54021
Arias, I., and Achenbach, J. D. (2004). A model for the ultrasonic detection of surface-breaking cracks by the scanning laser source technique. Wave Motion 39, 61–75. doi:10.1016/j.wavemoti.2003.06.001
Armentrout, D. L., Kumosa, M., and McQuarrie, T. S. (2003). Boron-free fibers for prevention of acid induced brittle fracture of composite insulator GRP rods. IEEE Trans. Power Deliv. 18, 684–693. doi:10.1109/TPWRD.2003.813599
Bakhtiari, S., Qaddoumi, N., Ganchev, S. I., and Zoughi, R. (1994). Microwave noncontact examination of disbond and thickness variation in stratified composite media. IEEE Trans. Microw. Theory Tech. 42, 389–395. doi:10.1109/22.277431
Bastidas, P. D., and Rowland, S. M. (2017). “Interfacial aging in composite insulators as a result of partial discharge activity,” in 2017 IEEE Electrical Insulation Conference (EIC), 13–16. doi:10.1109/EIC.2017.8004690
Batalović, M., Zildžo, H., Matoruga, H., Matoruga, M., and Berberović, S. (2019). “Detection of defect presence inside the insulation of cable accessories through changes in cable capacitance,” in 2019 XXVII International Conference on Information, Communication and Automation Technologies (ICAT), 1–4. doi:10.1109/ICAT47117.2019.8938874
Brisard, S., Serdar, M., and Monteiro, P. J. M. (2020). Multiscale X-ray tomography of cementitious materials: A review. Cem. Concr. Res. 128, 105824. doi:10.1016/j.cemconres.2019.105824
Brown, L. M., Novack, M. R., Qaddoumi, N., and Bigelow, T. (1999). “Application of NDE technologies to support in-service health monitoring of flexible composite components,” in Nondestructive evaluation of aging materials and composites III (Newport Beach, CA, United States: SPIE), 226–235. doi:10.1117/12.339852
Cao, Y., Gu, X., and Jin, Q. (2008). “Infrared technology in the fault diagnosis of substation equipment,” in 2008 China International Conference on Electricity Distribution, 1–6. doi:10.1109/CICED.2008.5211792
Casali, F. (2006). “X-ray and neutron digital radiography and computed tomography for cultural heritage,” in Physical techniques in the study of art, archaeology and cultural heritage. Editors D. Bradley, and D. Creagh (Elsevier), 41–123. doi:10.1016/S1871-1731(06)80003-5
Cheng, L., Wang, L., Mei, H., Guan, Z., and Zhang, F. (2016). Research of nondestructive methods to test defects hidden within composite insulators based on THz time-domain spectroscopy technology. IEEE Trans. Dielectr. Electr. Insul. 23, 2126–2133. doi:10.1109/TDEI.2016.7556487
Cheng, Z., Yang, L., Cheng, L., and He, Y. (2021). “Application of terahertz spectroscopy in defect detection of power cable terminal insulation material,” in 2021 46th International Conference on Infrared, Millimeter and Terahertz Waves (IRMMW-THz), 1–2. doi:10.1109/IRMMW-THz50926.2021.9567419
Chou, Y.-C., and Yao, L. (2009). “Automatic diagnostic system of electrical equipment using infrared thermography,” in 2009 International Conference of Soft Computing and Pattern Recognition, 155–160. doi:10.1109/SoCPaR.2009.41
de Tourreil, C. H. (1990). Response of composite insulators to dynamic mechanical loads. IEEE Trans. Power Deliv. 5, 379–383. doi:10.1109/61.107301
de Tourreil, C., Pargamin, L., Thevenet, G., and Prat, S. (2000). “Brittle fracture” of composite insulators: why and how they occur,” in 2000 power engineering society summer meeting (cat. No.00CH37134), 4, 2569–2574. doi:10.1109/PESS.2000.867394
Deng, H., He, Z., and Chen, L. (2017). Ultrasonic guided wave-based detection of composite insulator debonding. IEEE Trans. Dielectr. Electr. Insul. 24, 3586–3593. doi:10.1109/TDEI.2017.006665
Dilonardo, E., Nacucchi, M., De Pascalis, F., Zarrelli, M., and Giannini, C. (2020). High resolution X-ray computed tomography: A versatile non-destructive tool to characterize CFRP-based aircraft composite elements. Compos. Sci. Technol. 192, 108093. doi:10.1016/j.compscitech.2020.108093
Du, Z., Hu, Y., Ali Buttar, N., and Mahmood, A. (2019). X-ray computed tomography for quality inspection of agricultural products: A review. Food Sci. Nutr. 7, 3146–3160. doi:10.1002/fsn3.1179
Fukunaga, K., Mizuno, M., Destic, F., Massenot, S., and Mollier, J.-C. (2011). “Non destructive observation of defects in composite materials using time domain THz imaging,” in 2011 Annual Report Conference on Electrical Insulation and Dielectric Phenomena, 239–242. doi:10.1109/CEIDP.2011.6232641
Gao, Y., Liang, X., Bao, W., Li, S., and Wu, C. (2018). Failure analysis of a field brittle fracture composite insulator: Characterization by FTIR analysis and fractography. IEEE Trans. Dielectr. Electr. Insul. 25, 919–927. doi:10.1109/TDEI.2018.006928
Ghosh, D., and Khastgir, D. (2018). Degradation and stability of polymeric high-voltage insulators and prediction of their service life through environmental and accelerated aging processes. ACS Omega 3, 11317–11330. doi:10.1021/acsomega.8b01560
Gong, Z., Deng, D., Sun, X., Liu, J., and Ouyang, Y. (2022). Non-destructive detection of moisture content for ginkgo biloba fruit with terahertz spectrum and image: A preliminary study. Infrared Phys. Technol. 120, 103997. doi:10.1016/j.infrared.2021.103997
Gu, G., Xu, X., Qiu, C., Zhang, F., and Xu, G. (2018). “Quantitative measurement of embedding depth of internal defect using phase-shifting dual-observation digital shearography,” in Optical metrology and inspection for industrial applications V (SPIE), 211–216. doi:10.1117/12.2326956
Hackam, R. (1999). Outdoor HV composite polymeric insulators. IEEE Trans. Dielectr. Electr. Insul. 6, 557–585. doi:10.1109/TDEI.1999.9286745
Hao, G., Liu, R., Wan, S., Guo, X., Yang, Y., and Zheng, X. (2019). “The interface effect in X-ray testing of concentric multi-layer materials,” in 2019 IEEE 3rd Conference on Energy Internet and Energy System Integration (EI2), 2827–2831. doi:10.1109/EI247390.2019.9061743
Hlosta, P., Nita, M., Powala, D., and Świderski, W. (2022). Terahertz radiation in non-destructive testing of composite pyrotechnic materials. Compos. Struct. 279, 114770. doi:10.1016/j.compstruct.2021.114770
Hou, Z., Minhong, L., Jiandian, C., Guanxin, Q., and Yong, Z. (2021). “Research on electromagnetic characteristics of power transformer in distribution network,” in 2021 IEEE International Conference on Advances in Electrical Engineering and Computer Applications (AEECA), 1011–1016. doi:10.1109/AEECA52519.2021.9574400
Huang, H., Wang, T., Lv, Q., Ma, X., Zhang, F., Zeng, H., et al. (2021). Failure analysis of “lantern-like” composite insulator heating defects and the improved dye penetration test method. IEEE Access 9, 50646–50651. doi:10.1109/ACCESS.2021.3068464
Huang, X. (2021). Design of dynamic defect detection system for laser shearing speckle interferometry. doi:10.27470/d.cnki.ghbgc.2021.000534
Huang, Z., Zeng, Y., Wang, R., Ma, J., Nie, Z., and Jin, H. (2018). “Study on ultrasonic detection system for defects inside silicone rubber insulation material,” in 2018 International Conference on Power System Technology (POWERCON), 3651–3658. doi:10.1109/POWERCON.2018.8601738
Huda, A. S. N., and Taib, S. (2013). Application of infrared thermography for predictive/preventive maintenance of thermal defect in electrical equipment. Appl. Therm. Eng. 61, 220–227. doi:10.1016/j.applthermaleng.2013.07.028
Huda, A. S. N., Taib, S., Jadin, M. S., and Ishak, D. (2012). A semi-automatic approach for thermographic inspection of electrical installations within buildings. Energy Build. 55, 585–591. doi:10.1016/j.enbuild.2012.09.014
Hung, Y. Y., and Ho, H. P. (2005). Shearography: An optical measurement technique and applications. Mater. Sci. Eng. R Rep. 49, 61–87. doi:10.1016/j.mser.2005.04.001
Hung, Y. Y., Yang, L. X., and Huang, Y. H. (2013). “Non-destructive evaluation (NDE) of composites: digital shearography,” in Non-destructive evaluation (NDE) of polymer matrix composites woodhead publishing series in composites science and engineering. Editor V. M. Karbhari (Cambridge, United Kingdom: Woodhead Publishing), 84–115. doi:10.1533/9780857093554.1.84
Ibarra-Castanedo, C., and Maldague, X. P. V. (2013). “Infrared thermography,” in Handbook of technical diagnostics: Fundamentals and application to structures and systems. Editor H. Czichos (Berlin, Heidelberg: Springer), 175–220. doi:10.1007/978-3-642-25850-3_10
Inagaki, T., Ishii, T., and Iwamoto, T. (1999). On the NDT and E for the diagnosis of defects using infrared thermography. NDT E Int. 32, 247–257. doi:10.1016/S0963-8695(98)00059-0
Jeenjitkaew, C., and Guild, F. J. (2017). The analysis of kissing bonds in adhesive joints. Int. J. Adhesion Adhesives 75, 101–107. doi:10.1016/j.ijadhadh.2017.02.019
Jiang, W., Liu, R., Yang, Y., and Wan, S. (2020). Defect analysis of 110 kV GIS ZF4-126 epoxy resin support insulation rod based on finite element analysis and DR testing. Insulators Surge Arresters, 228–233. doi:10.16188/j.isa.1003-8337.2020.01.038
Jin, L., Zhou, G., Yuan, Z., Jin, H., and Man, X. (2022). Study on initial discharge process of insulator pollution flashover considering quantum. IEEE Trans. Dielectr. Electr. Insul. 1, 1. doi:10.1109/TDEI.2022.3190346
Kone, G., Volat, C., and Ezzaidi, H. (2017). Numerical investigation of electric field distortion induced by internal defects in composite insulators. High. Volt. 2, 253–260. doi:10.1049/hve.2016.0096
Kumosa, M., Kumosa, L., and Armentrout, D. (2005). Failure analyses of nonceramic insulators. Part 1: Brittle fracture characteristics. IEEE Electr. Insul. Mag. 21, 14–27. doi:10.1109/MEI.2005.1437604
Kumpati, R., Skarka, W., and Ontipuli, S. K. (2021). Current trends in integration of nondestructive testing methods for engineered materials testing. Sensors 21, 6175. doi:10.3390/s21186175
Li, J., Yang, L., He, Y., Li, W., and Wu, C. (2021a). Terahertz nondestructive testing method of oil-paper insulation debonding and foreign matter defects. IEEE Trans. Dielectr. Electr. Insul. 28, 1901–1908. doi:10.1109/TDEI.2021.009655
Li, J., Zhao, R., Du, B., Hao, L., and Bian, K. (2021b). Research progress of nondestructive detection methods for defects of electrical epoxy insulators. Trans. China Electrotech. Soc. 36, 4598–4607. doi:10.19595/j.cnki.1000-6753.tces.201033
Li, Z., Feng, Y., Liu, W., Chen, C., and Yin, K. (2017). Research on nondestructive testing system of industrial CT in power equipment material. SHANDONG Electr. POWER 44, 39–42. doi:10.3969/j.issn.1007-9904.2017.07.009
Li, Z., Haigh, A., Soutis, C., Gibson, A., and Wang, P. (2019). A review of microwave testing of glass fibre-reinforced polymer composites. Nondestruct. Test. Eval. 34, 429–458. doi:10.1080/10589759.2019.1605603
Li, Z., Wang, P., Haigh, A., Soutis, C., and Gibson, A. (2021c). Review of microwave techniques used in the manufacture and fault detection of aircraft composites. Aeronaut. J. 125, 151–179. doi:10.1017/aer.2020.91
Liang, B., Zhang, Z., Yin, T., Yang, S., Shao, J., and Manchester, W. (2021). Research status of semi-permanent release agent. MATEC Web Conf. 353, 01004. doi:10.1051/matecconf/202135301004
Liang, H., Du, B., and Li, J. (2020a). “3D electric field reconstruction inside GIL by induced charge tomography,” in 2020 IEEE Conference on Electrical Insulation and Dielectric Phenomena (CEIDP), 435–438. doi:10.1109/CEIDP49254.2020.9437447
Liang, H., Du, B., and Li, J. (2020b). “Defect recognition inside superconducting gas insulated line by induced charge tomography,” in 2020 IEEE International Conference on Applied Superconductivity and Electromagnetic Devices (ASEMD), 1–2. doi:10.1109/ASEMD49065.2020.9276105
Liang, H., Du, B., and Li, J. (2020c). Electric field reconstruction inside gas insulated transmission line by induced charge tomography. IEEE Trans. Dielectr. Electr. Insul. 27, 1372–1375. doi:10.1109/TDEI.2020.008887
Liang, X., Bao, W., and Gao, Y. (2018). Decay-like fracture mechanism of silicone rubber composite insulator. IEEE Trans. Dielectr. Electr. Insul. 25, 110–119. doi:10.1109/TDEI.2018.006773
Liu, L., Guo, C., Xiang, Y., Tu, Y., Wang, L., and Xuan, F.-Z. (2022a). A semisupervised learning framework for recognition and classification of defects in transient thermography detection. IEEE Trans. Ind. Inf. 18, 2632–2640. doi:10.1109/TII.2021.3101309
Liu, L., Guo, C., Xiang, Y., Tu, Y., Wang, L., and Xuan, F.-Z. (2022b). Photothermal radar shearography: A novel transient-based speckle pattern interferometry for depth-tomographic inspection. IEEE Trans. Ind. Inf. 18, 4352–4360. doi:10.1109/TII.2021.3124576
Liu, L., Mei, H., Wang, L., Zhao, C., and Guan, Z. (2017). “Pulsed infrared thermography to inspect the internal defects of composite insulators,” in 2017 IEEE Electrical Insulation Conference (EIC), 467–470. doi:10.1109/EIC.2017.8004665
Liu, L., Wang, L., Mei, H., and Guo, C. (2019). Defects detection methods for composite insulators based on shearing speckle interferometry. Proc. CSEE 39, 4599–4606. doi:10.13334/j.0258-8013.pcsee.181228
Liu, W., and Tan, H. (2020). Development and application of CT nondestructive testing system for power equipment materials industry. J. Henan Sci. Technol., 70–72. doi:10.3969/j.issn.1003-5168.2020.05.026
Lutz, B., Cheng, L., Guan, Z., and Wang, L. (2012). “Microwave-based detection of internal defects in composite insulators for outdoor application,” in 2012 IEEE International Conference on Condition Monitoring and Diagnosis, 1175–1178. doi:10.1109/CMD.2012.6416370
Mauoux, C., and Laurent, C. (1995). Contribution of partial discharges to electrical breakdown of solid insulating materials. IEEE Trans. Dielectr. Electr. Insul. 2, 641–652. doi:10.1109/94.407028
Mei, H., Jiang, H., Chen, J., Yin, F., Wang, L., and Farzaneh, M. (2021). Detection of internal defects of full-size composite insulators based on microwave technique. IEEE Trans. Instrum. Meas. 70, 1–10. doi:10.1109/TIM.2021.3085111
Meng, T., Huang, R., Lu, Y., Liu, H., Ren, J., Zhao, G., et al. (2021). Highly sensitive terahertz non-destructive testing technology for stone relics deterioration prediction using SVM-based machine learning models. Herit. Sci. 9, 24. doi:10.1186/s40494-021-00502-7
Meng, X., Mei, H., Zhu, B., Yin, F., and Wang, L. (2022). Influence of pollution on surface streamer discharge. Electr. Power Syst. Res. 212, 108638. doi:10.1016/j.epsr.2022.108638
Meola, C., Carlomagno, G. M., and Giorleo, L. (2004). Geometrical limitations to detection of defects in composites by means of infrared thermography. J. Nondestr. Eval. 23, 125–132. doi:10.1007/s10921-004-0819-z
Merten, A. (2010). “Non-destructive test methods for hollow-core composite insulators,” in 2010 International Conference on High Voltage Engineering and Application, 536–539. doi:10.1109/ICHVE.2010.5640709
Montesinos, J., Gorur, R. S., Mobasher, B., and Kingsbury, D. (2002). Mechanism of brittle fracture in nonceramic insulators. IEEE Trans. Dielectr. Electr. Insul. 9, 236–243. doi:10.1109/94.993741
Nandi, S., and Reddy, B. S. (2020). Understanding field failures of composite insulators. Eng. Fail. Anal. 116, 104758. doi:10.1016/j.engfailanal.2020.104758
Nazmul Huda, A. S., Taib, S., Jadin, M. S., and Ishak, D. (2012). A semi-automatic approach for thermographic inspection of electrical installations within buildings. Energy Build. 55, 585–591. doi:10.1016/j.enbuild.2012.09.014
Pastorino, M. (2004). Recent inversion procedures for microwave imaging in biomedical, subsurface detection and nondestructive evaluation applications. Measurement 36, 257–269. doi:10.1016/j.measurement.2004.09.006
Qaddoumi, N., Zoughi, R., and Carriveau, G. W. (1996). Microwave detection and depth determination of disbonds in low-permittivity and low-loss thick sandwich composites. Res. Nondestruct. Eval. 8, 51–63. doi:10.1080/09349849609409587
Qi, F., Wan, D., OuYang, X., Jiang, Q., Zhao, M., and Zhou, H. (2019). Influence of different XLPE cable defects on the initiation of electric trees. J. Electr. Eng. Technol. 14, 2625–2632. doi:10.1007/s42835-019-00296-6
Qu, Z., Jiang, P., and Zhang, W. (2020). Development and application of infrared thermography non-destructive testing techniques. Sensors 20, 3851. doi:10.3390/s20143851
Ricci, M., Crocco, L., and Vipiana, F. (2020). “Microwave imaging device for in-line food inspection,” in 2020 14th European Conference on Antennas and Propagation (EuCAP), 1–4. doi:10.23919/EuCAP48036.2020.9135775
Rouhanizadeh, B., and Kermanshachi, S. (2020). Third-rail insulator failure causes and mitigating practices: A comparative study of multiple case studies in the U.S. Urban Rail Transit 6, 205–217. doi:10.1007/s40864-020-00134-3
Saleem, M. Z., and Akbar, M. (2022). Review of the performance of high-voltage composite insulators. Polymers 14, 431. doi:10.3390/polym14030431
Shrifan, N. H. M. M., Jawad, G. N., Isa, N. A. M., and Akbar, M. F. (2021). Microwave nondestructive testing for defect detection in composites based on K-means clustering algorithm. IEEE Access 9, 4820–4828. doi:10.1109/ACCESS.2020.3048147
Spellman, C. A., Young, H. M., Haddad, A., Rowlands, A. R., and Waters, R. T. (1999). Survey of polymeric insulator ageing factors. Eleventh Int. Symposium High Volt. Eng. 4, 160–163. doi:10.1049/cp:19990817
Stakenborghs, R., and Little, J. (2010). Microwave based NDE inspection of HDPE pipe welds. American Society of Mechanical Engineers Digital Collection, 185–193. doi:10.1115/ICONE17-75742
Tan, H. Y., Li, L., Wu, G. L., and Wang, Q. (2019). Digital imaging detection and image analysis of internal structural defects in GIS. Optoelectron. Instrum. Proc. 55, 592–596. doi:10.3103/S8756699019060098
Tao, Y. H., Fitzgerald, A. J., and Wallace, V. P. (2020). Non-contact, non-destructive testing in various industrial sectors with terahertz technology. Sensors 20, 712. doi:10.3390/s20030712
Thomas, G., Emadi, A., Mijares-Chan, J., and Buchanan, D. A. (2014). “Low frequency ultrasound NDT of power cable insulation,” in 2014 IEEE International Instrumentation and Measurement Technology Conference (I2MTC) Proceedings, 1126–1129. doi:10.1109/I2MTC.2014.6860918
Tian, F., Hao, Y., Zou, Z., Zheng, Y., He, W., Yang, L., et al. (2019). An ultrasonic pulse-echo method to detect internal defects in epoxy composite insulation. Energies 12, 4804. doi:10.3390/en12244804
Tiwari, K. A., Raisutis, R., and Samaitis, V. (2017). Hybrid signal processing technique to improve the defect estimation in ultrasonic non-destructive testing of composite structures. Sensors 17, 2858. doi:10.3390/s17122858
Tobon Vasquez, J. A., Scapaticci, R., Turvani, G., Ricci, M., Farina, L., Litman, A., et al. (2020). Noninvasive inline food inspection via microwave imaging technology: An application example in the food industry. IEEE Antennas Propag. Mag. 62, 18–32. doi:10.1109/MAP.2020.3012898
Tourreil, C. D., Thévenet, G., and Brocard, E. (2005). Determination of the brittle fracture process of field failed HV insulators.
Umeda, T., Miyashita, T., and Kako, Y. (1980). New evaluation method of dielectric materials using a microwave technique. IEEE Trans. Elect. Insul. 15, 340–349. doi:10.1109/TEI.1980.298261
Usamentiaga, R., Venegas, P., Guerediaga, J., Vega, L., Molleda, J., and Bulnes, F. G. (2014). Infrared thermography for temperature measurement and non-destructive testing. Sensors 14, 12305–12348. doi:10.3390/s140712305
Varlow, B. R., Auckland, D. W., and Smith, C. D. (1994). Application of ultrasound to the NDT of solid insulation. IEE Proc. - Sci. Meas. Technol. 141, 20–24. doi:10.1049/ip-smt:19949588
Wang, H., Cheng, L., Liao, R., Zhang, S., and Yang, L. (2019a). Non-destructive testing method of micro-debonding defects in composite insulation based on high power ultrasonic. Available at: https://ietresearch.onlinelibrary.wiley.com/doi/full/10.1049/hve.2019.0044 (Accessed July 15, 2022).
Wang, H., Cheng, L., Liao, R., Zhang, S., and Yang, L. (2020a). Nonlinear ultrasonic nondestructive detection and modelling of kissing defects in high voltage composite insulators. IEEE Trans. Dielectr. Electr. Insul. 27, 924–931. doi:10.1109/TDEI.2019.008523
Wang, J., Ding, W., Liu, Y., Zheng, Z., and Ge, C. (2019b). Application of X-ray inspection for ultra high voltage gas-insulated switchgear. IEEE Trans. Power Deliv. 34, 1412–1422. doi:10.1109/TPWRD.2019.2903531
Wang, J., Liang, X., and Gao, Y. (2014). Failure analysis of decay-like fracture of composite insulator. IEEE Trans. Dielectr. Electr. Insul. 21, 2503–2511. doi:10.1109/TDEI.2014.004485
Wang, L., Du, J., and Zhang, N. (2021a). “Key technology of nondestructive testing of solid insulating materials in power equipment,” in 2021 International Conference on Advanced Electrical Equipment and Reliable Operation (AEERO), 1–5. doi:10.1109/AEERO52475.2021.9708120
Wang, L., Li, A., Cheng, L., Hu, X., Yang, J., and Chen, W. (2015). Microwave-based non-destructive testing method on composite insulators. Available at: https://www.cnki.com.cn/Article/CJFDTotal-GDYJ201502035.htm (Accessed July 14, 2022).
Wang, Q., Liu, X., Yang, S., Jiang, M., and Cao, J. (2019c). Non-destructive detection of density and moisture content of heartwood and sapwood based on X-ray computed tomography (X-CT) technology. Eur. J. Wood Prod. 77, 1053–1062. doi:10.1007/s00107-019-01459-y
Wang, X., Cheng, Z., Cheng, L., Yang, L., Liao, R., Zhang, S., et al. (2021b). “Non-destructive testing of internal defects in composite post insulators using microwave technique,” in 2021 International Conference on Sensing, Measurement & Data Analytics in the era of Artificial Intelligence (ICSMD), 1–5. doi:10.1109/ICSMD53520.2021.9670835
Wang, Y., Feng, C., Fei, R., and Luo, Y. (2020b). Thermal-ageing characteristics of dry-type transformer epoxy composite insulation. High. Perform. Polym. 32, 741–752. doi:10.1177/0954008320906439
Wang, Y., Webb, D., and Yang, H. (2022). POFBG-based humidity detection method for insulating gas in electrical equipment. IEEE Trans. Instrum. Meas. 71, 1–6. doi:10.1109/TIM.2022.3172428
Wei, Y., Ding, L., Han, Y., Luo, Y., Su, Z., and Zhang, D. (2021a). Characterizing defects in materials with fusion of thermography and shearography. Measurement 182, 109736. doi:10.1016/j.measurement.2021.109736
Wei, Y., Zhang, S., Luo, Y., Ding, L., and Zhang, D. (2021b). Accurate depth determination of defects in composite materials using pulsed thermography. Compos. Struct. 267, 113846. doi:10.1016/j.compstruct.2021.113846
White, S. R., Sottos, N. R., Geubelle, P. H., Moore, J. S., Kessler, M. R., Sriram, S. R., et al. (2001). Autonomic healing of polymer composites. Nature 409, 794–797. doi:10.1038/35057232
Wu, C. Q., Wang, W. P., Yuan, Q. G., Li, Y. J., Zhang, W., and Zhang, X. D. (2011). Infrared thermography non-destructive testing of composite materials. Adv. Mat. Res. 294, 1307–1310. doi:10.4028/www.scientific.net/amr.291-294.1307
Wu, K., and Cheng, C. (2017). Interface charges between insulating materials. IEEE Trans. Dielectr. Electr. Insul. 24, 2633–2642. doi:10.1109/TDEI.2017.006442
Xie, S., Yang, F., Huang, X., Yu, X., and Gao, B. (2020). Air gap detection and analysis of XLPE cable insulation based on terahertz time domain spectroscopy. Trans. China Electrotech. Soc. 35, 2698–2707. doi:10.19595/j.cnki.1000-6753.tces.190662
Xing, Z., Wang, , and Xu, Y. (2021). Defects and failure types of solid insulation in gas-insulated switchgear: In situ study and case analysis. Available at: https://ietresearch.onlinelibrary.wiley.com/doi/full/10.1049/hve2.12127 (Accessed July 13, 2022).
Xu, H., Xie, C., Gou, B., Wang, R., Li, Y., Yang, H., et al. (2021). Reappearance of typical characteristics of FRP core rods in the decay-like fracture insulator. IEEE Trans. Dielectr. Electr. Insul. 28, 1449–1456. doi:10.1109/TDEI.2021.009632
Yan, W. (2013). Research of X-DR technology in power equipment structural defects diagnosis. Available at: https://kns.cnki.net/kcms/detail/detail.aspx?dbcode=CMFD&dbname=CMFD201402&filename=1013314928.nh&uniplatform=NZKPT&v=GZewnGofWXnkSL3EyYxe53DQzgHJ0sn-53Z0V1h-q0Mq-lt2tXQr2Iok2coXBznM (Accessed August 4, 2022).
Yawn, K. R., Drake, T. E., Osterkamp, M. A., Chuang, S. Y., Acres, P., Thomas, M., et al. (1999). “Large-scale laser ultrasonic facility for aerospace applications,” in Review of Progress in quantitative nondestructive evaluation: Volume 18a–18B review of progress in quantitative nondestructive evaluation. Editors D. O. Thompson, and D. E. Chimenti (Boston, MA: Springer US), 387–393. doi:10.1007/978-1-4615-4791-4_48
Ye, D., Wang, W., Zhou, H., Fang, H., Huang, J., Li, Y., et al. (2020). Characterization of thermal barrier coatings microstructural features using terahertz spectroscopy. Surf. Coatings Technol. 394, 125836. doi:10.1016/j.surfcoat.2020.125836
Yin, J., Cheng, L., Wang, H., Liao, R., and Cheng, Z. (2020). Study on polarization characteristics and rapid detection method of micro water content in the terahertz band containing micro-water oil-immersed insulating paperboard. Trans. China Electrotech. Soc. 35, 2940–2949. doi:10.19595/j.cnki.1000-6753.tces.190824
Yin, K., Chen, C., Sun, X., Li, Z., and Feng, Y. (2018). Research on the application of industrial CT/DR detection system in the detection of basin-type insulator. Shandong Electr. Power 45, 33–36. doi:10.3969/j.issn.1007-9904.2018.08.008
Yu, H., Wei, J., Zhao, X., Ma, Y., and Chen, L. (2012). “The perspective detection of the X-ray digital radiography for the electrical equipment,” in 2012 International Conference on High Voltage Engineering and Application, 591–599. doi:10.1109/ICHVE.2012.6357096
Yuan, C., Xie, C., Li, L., Zhang, F., and Gubanski, S. M. (2016). Ultrasonic phased array detection of internal defects in composite insulators. IEEE Trans. Dielectr. Electr. Insul. 23, 525–531. doi:10.1109/TDEI.2015.005225
Yuan, Tu Youping, and Wang, Cheng (2020). Heating source of glass fibre reinforced polymer under AC and DC electric fields after hygrothermal ageing - Yuan - 2020 - IET Science. Measurement & Technology - Wiley Online Library. Available at: https://ietresearch.onlinelibrary.wiley.com/doi/full/10.1049/iet-smt.2019 (Accessed July 13, 2022).
Yuan, T., Zhang, R., Zhang, Q., Wu, W., and Cai, Y. (2015). Discussion of the erosion on the interface between housing and core of composite insulators. Available at: https://www.cnki.com.cn/Article/CJFDTotal-DCPQ201504005.htm (Accessed July 11, 2022).
Yuan, Z., Tu, Y., Li, R., Zhang, F., Gong, B., and Wang, C. (2022). Review on the characteristics, heating sources and evolutionary processes of the operating composite insulators with abnormal temperature rise. CSEE J. Power Energy Syst. 8, 910–921. doi:10.17775/CSEEJPES.2019.02790
Zhang, Q., Gao, B., Ma, R., Yan, Z., and Li, X. (2020). Application of Xray detection technology in power equipment fault diagnosis. Ningxia Electr. Power, 40–44. doi:10.3969/j.issn.1672-3643.2020.04.008
Zhang, S., Cheng, L., Liu, Y., Liao, R., Wang, T., and Huang, H. (2021). Study on the detection method of holes in composite insulator rods. High. Volt. 6, 873–880. doi:10.1049/hve2.12083
Zhang, S., Guo, C., Cheng, L., Wang, H., and Liao, R. (2019). Testing method for composite insulators interface based on nonlinear ultrasonic. IEEE Access 7, 83111–83119. doi:10.1109/ACCESS.2019.2924050
Zhang, T., Xie, L., Zhang, X., Lv, L., and Li, T. (2017). Defect inspection technology application of power transmission and transformation equipments based on DR. Inn. Mong. Electr. Power 35, 89–92. doi:10.3969/j.issn.1008-6218.2017.06.011
Zhang, W. D., Liu, Q., He, N., and Wang, J. W. (2014). Typical PD type of GIS, transformer, switchgear and other substation equipment. Adv. Mat. Res. 1045, 893–897. doi:10.4028/www.scientific.net/AMR.1044-1045.893
Zhang, X., and Luo, G. (2022). Defect detection method of GIS insulation pull rod based on industrial CT. Nondestructive Testing 44, 17–21. doi:10.11973/wsjc202202004
Zhang, Z., Assala, P. D. S., and Wu, L. (2018). Residual life assessment of 110kV XLPE cable. Electr. Power Syst. Res. 163, 572–580. doi:10.1016/j.epsr.2017.12.027
Zhang, Z., Xu, J., Jia, R., Wu, Y., Guan, , Han, S., et al. (2022). Terahertz non-destructive testing and imaging of high-voltage cables. Front. Phys. 10. doi:10.3389/fphy.2022.893145
Zhao, R. Y., Li, J., Chen, Y., Liang, H. C., Yao, H., Du, B. X., et al. (2020). “Defects detection of high voltage insulation pull rod based on ultrasonic wave method,” in 2020 IEEE International Conference on High Voltage Engineering and Application (ICHVE), 1–4. doi:10.1109/ICHVE49031.2020.9279505
Zhao, Z. (2014). Study on rapid identification of defects in X-ray digital imaging detection. Available at: https://kns.cnki.net/kcms/detail/detail.aspx?dbcode=CMFD&dbname=CMFD201402&filename=1014262525.nh&uniplatform=NZKPT&v=LMiI4zIVrM7KMG0TdXSyBi7lqmWGUdBYEpvyy2Y2TdFxmPRUxhVnVsqnoq1qHZs2 (Accessed August 5, 2022).
Zheng, Wei, and Gao, (2019). Discussions on fracture mechanisms of composite insulator. Available at: https://iopscience.iop.org/article/10.1088/1757-899X/740/1/012049/meta (Accessed July 14, 2022).
Zhou, F., Wang, D., Gao, C., Huang, R., Tian, F., Yang, X., et al. (2020). “Study on the ultrasonic method to detect large size insulated equipment for GIS,” in 2020 12th IEEE PES Asia-Pacific Power and Energy Engineering Conference (APPEEC), 1–4. doi:10.1109/APPEEC48164.2020.9220615
Keywords: organic insulating materials, tiny defects, high voltage power equipment, aging, non-destructive testing5
Citation: Zhang X, Cheng L, Liu Y, Tao B, Wang J and Liao R (2022) A review of non-destructive methods for the detection tiny defects within organic insulating materials. Front. Mater. 9:995516. doi: 10.3389/fmats.2022.995516
Received: 16 July 2022; Accepted: 11 August 2022;
Published: 30 August 2022.
Edited by:
He Li, Berkeley Lab (DOE), United StatesReviewed by:
Xilin Wang, Tsinghua University, ChinaCopyright © 2022 Zhang, Cheng, Liu, Tao, Wang and Liao. This is an open-access article distributed under the terms of the Creative Commons Attribution License (CC BY). The use, distribution or reproduction in other forums is permitted, provided the original author(s) and the copyright owner(s) are credited and that the original publication in this journal is cited, in accordance with accepted academic practice. No use, distribution or reproduction is permitted which does not comply with these terms.
*Correspondence: Li Cheng, Y2hlbmdsMTZAY3F1LmVkdS5jbg==
Disclaimer: All claims expressed in this article are solely those of the authors and do not necessarily represent those of their affiliated organizations, or those of the publisher, the editors and the reviewers. Any product that may be evaluated in this article or claim that may be made by its manufacturer is not guaranteed or endorsed by the publisher.
Research integrity at Frontiers
Learn more about the work of our research integrity team to safeguard the quality of each article we publish.