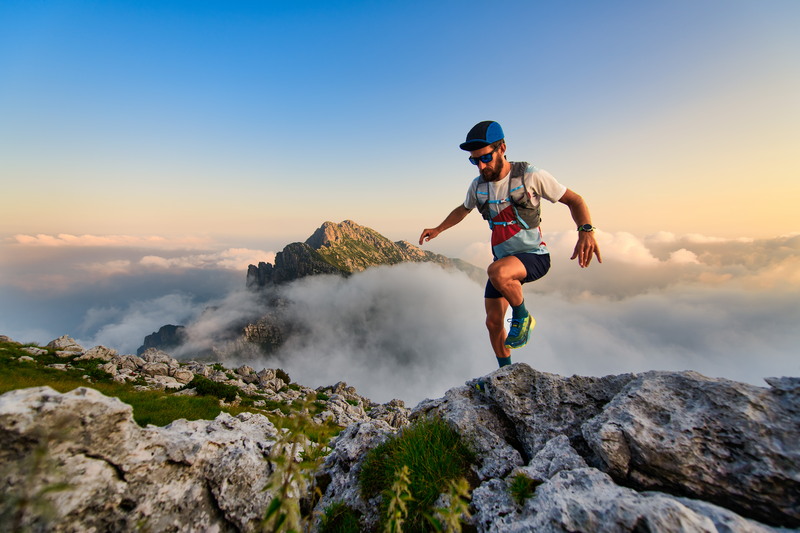
94% of researchers rate our articles as excellent or good
Learn more about the work of our research integrity team to safeguard the quality of each article we publish.
Find out more
ORIGINAL RESEARCH article
Front. Mater. , 05 October 2022
Sec. Polymeric and Composite Materials
Volume 9 - 2022 | https://doi.org/10.3389/fmats.2022.973660
This article is part of the Research Topic Editors’ Showcase: Polymeric and Composite Materials View all 7 articles
Particulate matter (PM) pollution has become a serious threat to human health. Accordingly, an air filtration media that can efficiently remove particulate matter should be developed immediately. Nanofibrous membrane filter prepared by electrospinning technology has nanoscale diameter, high specific surface area, and relatively high porosity, which are suitable for dust removal. This paper explored the effects of electrospinning parameters on the microscopic morphology, fiber diameter, and pore size of polyacrylonitrile (PAN) nanofibrous membranes, including polymer solution concentration, applied voltage, and tip-to-collector distance. Thereafter, filtration efficiencies of electrospun PAN fibrous membrane and Polytetrafluoroethylene (PTFE), Cellulose acetate (CA), Nylon commercial filter were compared by removing smoke PMs. Results showed that fiber diameter and pore size increase with increasing concentration but decrease with increasing distance. With an increase in applied voltage, fiber diameter and pore size first decreased and increased thereafter. Lastly, filtration experimental results showed that filtration efficiency of electrospun PAN nanofibrous membranes was higher than that of those commercial filter membranes for ultra fine dust (0.3–0.5 μm).
Particulate matter (PM) pollution in the atmosphere has become a serious threat to human health (Xiao et al., 2018). Air pollution is attributable to harmful particles and gases emitted into the air. Air pollution includes carbon monoxide (CO), sulfur dioxide (SO2), nitrogen oxides (NOx), volatile organic compounds (VOC), heavy metals, and inhalable particulate matter (Kampa and Castanas, 2008; AYDIN and İLKILIÇ, 2017).
Severe PM pollution can particularly cause abominable effects on the human respiratory tract, cardiovascular system, nervous system, and other organs and systems, thereby substantially increasing the risk of diseases, such as heart disease, stroke, cancer, and acute respiratory infections (Kampa and Castanas, 2008). According to World Health Organization (WHO) statistics, environmental (outdoor) air pollution in urban and rural areas was estimated to cause the premature death of 4.2 million people worldwide due to exposure to PM2.5 in 2016 (Croitoru and Sarraf, 2017; Su et al., 2019; Nazarenko et al., 2021). Therefore, air filtration media that can efficiently remove particulate matter should be developed (Wang et al., 2019).
To alleviate the serious negative effects caused by ultra-fine PM, researchers have conducted numerous studies. Researchers found that air filtration is currently one of the most effective and direct methods. Existing air filtration technologies typically use high-efficiency particulate air (HEPA) filters made of tiny fiberglass to remove tiny particles from the atmosphere. However, current nonwoven filter media cannot remove the most penetrating particle sizes (i.e., between 0.1 μm and 0.5 μm) because pores formed by micron-sized fibers are considerably large (Wang et al., 2016). However, the fibrous membrane prepared by electrospinning technology can markedly overcome the shortcomings of traditional filter media (Zhu et al., 2017). Electrospinning can produce nanoscaled (i.e., 40–1,000 nm) fibers, and nanofibrous membrane composed of electrospun fibers also has the advantages of high specific surface area, small aperture, high porosity, and good pore uniformity (Gopal et al., 2006; Wang et al., 2016; Li et al., 2021). Moreover, electrospinning can produce fibers with controllable morphology and connectivity by precisely controlling the process conditions (Nam et al., 2019). Therefore, electrospun nanofibrous filters have a higher potential than traditional filters for air filtration applications (Wang et al., 2007; Deng et al., 2021).
With the rapid development of electrospinning technology, coaxial (García-Mateos et al., 2019; Liu et al., 2021; Gao et al., 2022), tri-axial (Wang et al., 2020; Zhao et al., 2021), modified coaxial/tri-axial (Ning et al., 2021; Yu and Lv, 2022), side-by-side (Qi et al., 2020; Xu et al., 2022a; Yu et al., 2022), other complicated processes (Hu et al., 2012) has begun to appear, but so far these techniques still have some drawbacks. For example, in the structural design of the coaxial needle in the coaxial electrospinning technology, the flow rate matching is a relatively complicated matter. In addition, in the multi-needle electrospinning technology, the arrangement of the needles and the electric field interference between the needles are also the main problems that need to be solved. Therefore, the mainstream is still the single-fluid electrospinning process (Zhang et al., 2021; Ling et al., 2022), which hold the greatest promise for producing commercial fibrous products. According to the principle of the electrospinning technique, high voltage (i.e., 0–30 kV) is applied between the blunt needle and metal collecting plate to form a stable high-voltage electric field. A polymer solution is pulled by an electric field to form a stable continuous jet, which is deposited and solidified on the metal collecting plate after flying for some distance, eventually forming the fiber felt (Subbiah et al., 2005; Bhardwaj and Kundu, 2010; Xue et al., 2019). Therefore, the species and concentration of the polymer solution, applied voltage, and distance between the tip and metal collecting plate are closely related to the morphology and structure of the nanofibrous membrane. Beyond this aspect, spinning time, flow rate, type of collecting plate, and ambient parameters, such as temperature and humidity, also relatively affect the electrospinning process (De Vrieze et al., 2009; Li and Wang, 2013; Aliabadi, 2017). As shown Figure 1, according to the air filtration mechanism, air filters block the spread of particulate matter in the air through interception, inertia, Brownian diffusion, and electrostatic attraction (Zhu et al., 2017). Hence, filtration performance is often inseparable from the fiber diameter, pore size, and distribution structure of the filter membrane (Zhu et al., 2017; Nam et al., 2019).
The preparation technology of electrospun nanofiber membranes for air filtration has been substantially developed (Liu et al., 2020). Park and Park (2005) prepared electrospun PA-6 nano-mesh fiber under different conditions, studied the effect of applied voltage and rotational speed of drum collector on the nanofiber morphology and filtration performance, and found that electrospun fibers were better than glass commercial high-efficiency air filter media made of fibers with higher filtration performance. Qin and Wang (2006) successfully prepared polyvinyl alcohol (PVA) nanofibrous membrane by electrospinning technology and measured its fiber diameter, aperture, filtration efficiency, and pressure drop. The results showed that the smaller fiber diameter and pore diameter are more conducive to improving filtration efficiency but not conducive to air circulation. Srikrishnarka et al. (2020) made electrospun fibers out of polyacrylonitrile (PAN), polystyrene (PS), polyvinyl pyrrolidone (PVP), and PVA, thereby showing high efficiency (i.e., 95%–100%) in filtering PM2.5.
Polyacrylonitrile (PAN) membrane material has the advantages of diverse structure, high stability and easy functionalization, which is an ideal and widely used separation membrane material. It has been widely used in ion adsorption, water treatment and other fields, and plays an important role (Xu et al., 2022b). In this study, PAN nanofibrous membranes were prepared by single-fluid electrospinning technology and investigated the effects of electrospinning parameters (e.g., solution concentration, applied voltage, and distance from tip to collector) on morphological characteristics, such as fibrous diameter and pore size. In addition, the filtration efficiency of the electrospun fibrous membranes was compared with that of the commercial filter membranes by removing smoke PM2.5.
Polyacrylonitrile powder (PAN, average Mw = 150,000), N, N-Dimethylformamide (DMF, purity = 99%) were purchased from Sigma Aldrich and used as received without further purification. PP non-woven fabric substrate (filtration efficiency was negligible) and Polytetrafluoroethylene (PTFE), Cellulose acetate (CA), Nylon commercial filter membranes were purchased from online stores.
Various PAN solutions were prepared. As shown in Figure 2, PAN powders were dissolved into DMF solvent and placed on a magnetic stirrer. After stirring at 60°C for 12 h, it was allowed to stand at room temperature until the bubbles disappeared. According to the preceding method, PAN solutions with mass fractions of 7 wt%, and 10 wt% were prepared.
All prepared solutions were used for further electrospinning process.
All nanofibrous membranes were fabricated by using electrospinning equipment, as shown in Figure 3. The electrospinning system was mainly composed of a high-voltage power supply (AU-30P1-L (220 V), Korea), micro-syringe pump (PC570-3,311), blunt needle, and plate collector (aluminum foil). A 20 ml plastic syringe was used to draw 10 ml of polymer solution, and the syringe was fixed on a micro-syringe pump by a clamp bar. Thereafter, a polymer solution was injected into a 21G (inner diameter = 0.51 mm) blunt needle with a high voltage of 10–15 kV applied to the tip. Flow rate was set to 1 ml/h, and the distance from tip to plate collector was set to 10–15 cm. Lastly, collected nanofibrous membranes were dried in a drying oven at 60°C for 1 h to remove the residual solvent. Ambient temperature and humidity were 20 ± 5°C and 30 ± 5%, respectively.
To investigate the influence of concentration, voltage, and distance on the microstructure of the PAN nanofibrous membrane, the surface microscopic morphology of the nanofibrous membrane was observed by field emission scanning electron microscope (FE-SEM, S-4800, Japan). The single fiber diameter was measured by image analysis software (ImageJ) and the average diameter was calculated. Thereafter, fiber diameter distribution was estimated by using graphic software (Origin 2018).
The unique pore structure and pore connectivity of the electrospinning nanofibrous membrane enable the effective interception of particles in the air during the filtration process, showing considerable application value. Therefore, the influence of the pore structure of nanofibrous membranes on its filtration effect should be explored. This study calculated the pore size and distribution of nanofibrous membranes using ImageJ (analysis particle) software to analyze the FE-SEM image.
As shown in Figure 4, a two-bottle filtration unit was designed and fabricated for smoke filtration experiments. In the filtration experiment, PMs were generated by burning incense in a glass bottle. Moreover, smoke PMs had a wide size distribution, ranging from 0.3 μm to 2.5 μm, with the majority of the particles being below 1 μm. The initial concentration of smoke was controlled by burning the incense for 30 s. A small air compressor was used to provide an airflow rate of 32 L/min. To ensure that incense completely passes through the fiber membrane, air circulation time was set to 30 s. PAN nanofibrous membranes and PTFE commercial filters were attracted between two pieces of PP non-woven fabric substrate to ensure that the membrane samples were not damaged by squeezing. Before and after filtration, a particle counter (TSI 6306-V2) was used to count the total number of particles contained in the two glass bottles. Filtration efficiency (η) is defined as follows:
where Cleft and Cright are the number of particles before and after filtration, respectively.
Each filtration experiment was repeated thrice, and the average and standard deviation of the experimental results were calculated.
Concentration of polymer solution is one of the most important parameters in the electrospinning process (Deitzel et al., 2001; Aliabadi, 2017). The reason is that a change in concentration substantially affects the viscosity and surface tension of the solution and affects the morphology of the fibrous membrane thereafter (Fong et al., 1999; Deitzel et al., 2001).
Therefore, the effect of different concentrations of PAN solution on the microstructure of fibrous membranes under the same electrospinning condition was studied. To directly observe the surface morphology of the PAN fibrous membrane, two types of fibrous membranes with different PAN contents were prepared under the same electrospinning condition, 7 wt% and 10 wt%, respectively. The reason is that when the concentration was decreased from 7 wt% to 4 wt%, due to the too low concentration of the solution, electrospinning would be converted into electrospray, a wet membrane would be formed in the collectors (Lv et al., 2021), and filamentous fibers could not be formed. When the solution concentration was increased from 10 wt% to 13 wt%, a smooth electrospinning process was not allowed despite attempts to apply the maximum experimental condition voltage (15 kV). This is because the high molecular weight and high concentration of the solution will increase the viscosity of the solution to a higher range, and the fluidity of the solution will be greatly reduced, resulting in the inability to form an effective jet, or even the formation of electrospray particles (Lv et al., 2021). The FE-SEM images of electrospun PAN fibrous membranes with concentrations of 7 wt% and 10 wt% are shown in Figure 5.
FIGURE 5. FE-SEM image, diameter, and aperture distribution of PAN nanofibrous membrane under different concentrations. (A,B,C) 7 wt%; (D,E,F) 10 wt%.
Figures 5A,D show that the PAN nanofibers are randomly arranged and distributed, forming a complex pore structure. At a concentration of 7 wt%, many fusiform or bead-like fibers were formed. The possible reason is that although the 7 wt% solution can be drawn into filamentous fibers, the degree of entanglement between molecular chains when the solution is stretched in an electric field due to the insufficient viscosity of the solution to resist the solution shrinkage caused by surface tension low, leading to the scission and agglomeration of molecular chains, thereby forming fusiform or bead-like fibers (Fong et al., 1999; Gao et al., 2017). When the solution concentration was increased to 10 wt%, it was found that the fusiform or beaded fibers disappeared completely, instead smooth fibers were formed. This result implies that at higher solution concentrations, the solution viscosity also increases, which is more favorable for the formation of smooth fibers.
As shown in the distribution diagram, when the concentration of PAN solution was 7 wt%, the diameter of PAN fibers prepared under the condition of 11 kV and 11 cm was concentrated in the range of 150–250 nm, with an average diameter of 228 nm (Figure 5B) and average pore size of 0.96 μm (Figure 5C). However, when the concentration of PAN solution was increased to 10 wt%, the diameter of PAN fibers was concentrated between 400 nm and 500 nm, with an average diameter of 452 nm (Figure 5E) and average pore size of 1.44 μm (Figure 5F). The possible main reason is that when concentration increases from 7 wt% to 10 wt%, the viscosity of PAN solution would substantially increase, and the entanglement between PAN molecular chains would become considerably close. Under the same conditions, the tensile refinement of the 10 wt% solution jet in the electric field was more difficult than that of the 7 wt% solution. Thus, the diameter of PAN fiber would increase with an increase in solution concentration. The results indicated that when the concentration of the solution increases, fiber diameter and pore size would increase. The possible reason is that the coarse fibers can deposit only a few fibers per unit area, reducing the probability for fibers to cross each other, resulting in a sharp decrease in the number of pores and an increase in pore size.
Voltage applied to the needle is also one of the most important parameters in the electrospinning process (Jacobs et al., 2010). Voltage applied determines the intensity of the electric field. If voltage is considerably small to overcome the surface tension of the solution, the Taylor cone and jet cannot be formed, or the jet cannot be fully stretched owing to the weak electric field strength, thereby forming thick fibers. If voltage is high, then charge in the droplet will be excessively accelerated, resulting in the jet injection rate being greater than the solution feeding rate and unable to form a Taylor cone, or the jet does not have enough time to be fully stretched to form coarser fibers under the same distance. To investigate the influence of applied voltage on the morphology of the membrane, PAN nanofibrous membranes with 10 wt% concentration were prepared at 11, 13, and 15 kV under the condition that other parameters were unchanged. Microscopic morphologies of fiber membranes are shown (Figures 6A,D,G).
FIGURE 6. FE-SEM image, diameter, and aperture distribution of PAN nanofibrous membrane under different voltage. (A,B,C) 11 kV; (D,E,F) 13 kV; (G,H,I) 15 kV.
As shown in Figure 6, when applied voltage was 11 kV, the average diameter of the fibers was 452 nm (Figure 6B), and the fiber diameters were concentrated between 400 nm and 500 nm, with an average pore size of 1.44 μm (Figure 6C). When voltage was increased to 13 kV, fiber diameter decreased slightly to 395 nm (Figure 6E), pore size also decreased to 1.29 μm (Figure 6F), and fiber diameter was mainly distributed between 350 nm and 450 nm. The possible reason is that when voltage increases, electric field strength also increases. Hence, the electric field pulling force on the jet also increases, resulting in the formation of considerably fine fibers. When applied voltage was increased to 15 kV, fiber diameter increased to 730 nm (Figure 6H), pore size also increased to 1.77 μm (Figure 6I), and diameter was concentrated between 650 nm and 750 nm. The possible reason is that voltage was considerably high, and the electric field strength increases accordingly, increasing the amount of jets injection, or the injection rate was significantly fast, which substantially reduced stretching time and degree of refinement of the jets in the electric field. Eventually, fiber with markedly thick diameter was formed. Therefore, pore size is positively correlated to fiber diameter.
Distance between the tip and collector is also one of the important parameters in electrospinning (Hekmati et al., 2013). Distance determines the strength of the electric field, and the flight distance of jets (Levitt et al., 2018). Relatively weak electric field strength and force will be generated at a long distance, resulting in insufficient tensile force to refine the jet, thereby leading to thick fibers. By contrast, a markedly strong electric field will be formed at a short distance, and the jet is accelerated at a short distance so that it is not fully stretched. To more intuitively explore the effect of spinning distance on the morphology of PAN fiber membranes, PAN fibrous membranes with a concentration of 10 wt% were prepared at distances of 11, 13, and 15 cm with other parameters unchanged. Microscopic morphologies of the fiber membrane at different distances are shown (Figures 7A,D,G).
FIGURE 7. FE-SEM image, diameter, and aperture distribution of PAN nanofibrous membrane under different distances. (A,B,C) 11 cm; (D,E,F) 13 cm; (G,H,I) 15 cm.
Figure 7 shows that when spinning distance was 11 cm, average diameter of the fibers was 395 nm (Figure 7B), average pore size was 1.29 μm (Figure 7C), and fiber diameters were concentrated between 350 nm and 450 nm. When distance increased to 13 cm, fiber diameter decreased slightly to 374 nm (Figure 7E), pore size also decreased to 1.14 μm (Figure 7F), and fiber diameter was mainly distributed between 350 nm and 400 nm. When distance increased to 15 cm, fibers with diameter of 335 nm (Figure 7H) and pore diameter of 1.09 μm (Figure 7I) were obtained, and diameters were concentrated between 300 nm and 350 nm. The results indicated that when the spinning distance was short, a relatively strong electric field would be formed under the condition of constant voltage. Moreover, the jets would be accelerated to the collector at a short distance and strong electric field. Consequently, the jets cannot be sufficiently stretched. However, when spinning distance increased, the jets can fly farther in the electric field, thereby intensifying the degree of fiber refinement and resulting in finer fibers. Lastly, pore size has been demonstrated to be positively related to fiber diameter.
To compare the difference in filtration efficiency between electrospun PAN nanofibrous membranes and commercial filtration membranes, three commercial filtration membranes (PTFE, Cellulose acetate and Nylon) which are widely used in dust removal and water treatment fields, were selected for comparison.
Figure 8 shows the FE-SEM images of the four membranes used in the air filtration experiments, respectively. Figure 8A shows an electrospun PAN fibrous membrane, Figure 8B shows a PTFE filter membrane, Figure 8C shows a Cellulose acetate filter membrane, and Figure 8D shows a Nylon filter membrane.
FIGURE 8. FE-SEM images of four membranes used in air filtration experiments. (A) Electrospun PAN membrane; (B) PEFE filter membrane (C) Cellulose acetate filter membrane; (D) Nylon filter membrane.
Under the same conditions, the PM2.5 filtration experiment was carried out using the smoke filter equipment built in the laboratory. The experimental results are shown in Figure 9. The filtration efficiency of PTFE and Nylon filter membrane for PM0.3 is only 89.43% and 91.30%, respectively, but the filtration efficiency of electrospun PAN fibrous membrane and CA filter membrane for PM0.3 is as high as 95.85% and 96.83%, higher than PTFE and Nylon filter membrane. In addition, the filtration efficiencies of the four filtration membranes for PM0.5 were 99.66%, 98.78%, 96.83%, and 97.89%, respectively, among which the PAN fibrous membrane had the highest filtration efficiency. And in the filtration efficiency of PM0.5 or more, PAN fibrous membrane also ranks first. Therefore, on the whole, the filtration efficiency of the electrospun PAN fibrous membrane for ultrafiltration particles is much higher than that of several commercial filtration membranes. This result may be attributed to the electrospun PAN fibrous membranes with nanoscale fibrous diameter and three-dimensionally distributed pore structures. The nanoscale fiber diameter increases the specific surface area of the PAN fibrous membrane and the contact area between PMs and fibers, thereby improving the PMs retention capacity of the fibers. Moreover, the three-dimensionally distributed pores can form interconnected channels in the membrane, which is beneficial to prolong the air circulation in the membrane, thereby improving the filtration efficiency.
FIGURE 9. Comparison of filtration efficiencies of electrospun PAN nanofibrous membranes and commercial filter membranes for smoke PMs.
To explore the effects of electrospinning parameters on the morphology of fibrous membranes, three important parameters were selected: solution concentration, applied voltage, and distance from tip to collector. PAN nanofibrous membranes were fabricated with finer and uniformly distributed diameters and interconnected pores by electrospinning. Filtration efficiency of the electrospun PAN fibrous membranes was compared with that of PTFE, Cellulose acetate, and Nylon commercial filter membranes through a smoke filtration experiment. The results show that electrospinning parameters have an important effect on fibrous membrane, and fiber diameter and pore size increase with solution concentration and decrease with distance from tip to collector. Note that fiber diameter initially decreases and increases thereafter as applied voltage increases. Compared with the commercial filter membrane, the electrospun fibrous membrane has a nanoscale diameter, and pore channel that can prolong airflow. These aspects are of immense significance for the improvement of filtration efficiency.
The original contributions presented in the study are included in the article/supplementary material, further inquiries can be directed to the corresponding author.
XZ conducted literature survey, experimental operation, data collection, theoretical analysis, manuscript writing, etc. KK was responsible for funding acquisition, resource provision, supervision, project management, manuscript revision and editing.
This work was supported by the National Research Foundation of Korea (NRF) grant funded by the Korea government (MSIT) (No. NRF-2022R1F1A1059592).
The authors would like to particularly thank KK for his generous constructive criticism, commentary and editorial assistance in preparing this manuscript.
The authors declare that the research was conducted in the absence of any commercial or financial relationships that could be construed as a potential conflict of interest.
All claims expressed in this article are solely those of the authors and do not necessarily represent those of their affiliated organizations, or those of the publisher, the editors and the reviewers. Any product that may be evaluated in this article, or claim that may be made by its manufacturer, is not guaranteed or endorsed by the publisher.
Aliabadi, M. (2017). Effect of electrospinning parameters on the air filtration performance using electrospun polyamide-6 nanofibers. CI&CEQ. 23 (4), 441–446. doi:10.2298/CICEQ160509059A
Aydin, H., and İlkiliç, C. (2017). Air pollution, pollutant emissions and harmfull effects. J. Eng. Technol. Manage. 1 (1), 8–15.
Bhardwaj, N., and Kundu, S. C. (2010). Electrospinning: A fascinating fiber fabrication technique. Biotechnol. Adv. 28 (3), 325–347. doi:10.1016/j.biotechadv.2010.01.004
Croitoru, L., and Sarraf, M. (2017). Estimating the health cost of air pollution: The case of Morocco. J. Environ. Prot. (Irvine, Calif. 8 (10), 1087–1099. doi:10.4236/jep.2017.810069
De Vrieze, S., Van Camp, T., Nelvig, A., Hagström, B., Westbroek, P., and De Clerck, K. (2009). The effect of temperature and humidity on electrospinning. J. Mat. Sci. 44 (5), 1357–1362. doi:10.1007/s10853-008-3010-6
Deitzel, J. M., Kleinmeyer, J., Harris, D., and Tan, N. B. (2001). The effect of processing variables on the morphology of electrospun nanofibers and textiles. Polymer 42 (1), 261–272. doi:10.1016/S0032-3861(00)00250-0
Deng, Y., Lu, T., Cui, J., Samal, S. K., Xiong, R., and Huang, C. (2021). Bio-based electrospun nanofiber as building blocks for a novel eco-friendly air filtration membrane: A review. Sep. Purif. Technol. 277, 119623. doi:10.1016/j.seppur.2021.119623
Fong, H., Chun, I., and Reneker, D. H. (1999). Beaded nanofibers formed during electrospinning. Polymer 40 (16), 4585–4592. doi:10.1016/S0032-3861(99)00068-3
Gao, C., Zhang, L., Wang, J., Cheng, Y., Chen, Z., Yang, R., et al. (2022). Coaxial structured drug loaded dressing combined with induced stem cell differentiation for enhanced wound healing. Biomater. Adv. 134, 112542. doi:10.1016/j.msec.2021.112542
Gao, J., Huang, X., Wang, L., Zheng, N., Li, W., Xue, H., et al. (2017). Super-hydrophobic coatings based on non-solvent induced phase separation during electro-spraying. J. Colloid Interface Sci. 506, 603–612. doi:10.1016/j.jcis.2017.07.089
García-Mateos, F. J., Ruiz-Rosas, R., Rosas, J. M., Rodríguez-Mirasol, J., and Cordero, T. (2019). Controlling the composition, morphology, porosity, and surface chemistry of lignin-based electrospun carbon materials. Front. Mat. 6, 114. doi:10.3389/fmats.2019.00114
Gopal, R., Kaur, S., Ma, Z., Chan, C., Ramakrishna, S., and Matsuura, T. (2006). Electrospun nanofibrous filtration membrane. J. Memb. Sci. 281 (1-2), 581–586. doi:10.1016/j.memsci.2006.04.026
Hekmati, A. H., Rashidi, A., Ghazisaeidi, R., and Drean, J.-Y. (2013). Effect of needle length, electrospinning distance, and solution concentration on morphological properties of polyamide-6 electrospun nanowebs. Text. Res. J. 83 (14), 1452–1466. doi:10.1177/0040517512471746
Hu, S., Xie, Z., Qian, J., Blackshaw, S., and Zhu, H. (2012). Wiley interdiscip. Rev. Comput. Mol. Sci. 2 (1), 167–185. doi:10.1002/wnan.1772
Jacobs, V., Anandjiwala, R. D., and Maaza, M. (2010). The influence of electrospinning parameters on the structural morphology and diameter of electrospun nanofibers. J. Appl. Polym. Sci. 115 (5), 3130–3136. doi:10.1002/app.31396
Kampa, M., and Castanas, E. (2008). Human health effects of air pollution. Environ. Pollut. 151 (2), 362–367. doi:10.1016/j.envpol.2007.06.012
Levitt, A. S., Vallett, R., Dion, G., and Schauer, C. L. (2018). Effect of electrospinning processing variables on polyacrylonitrile nanoyarns. J. Appl. Polym. Sci. 135 (25), 46404. doi:10.1002/app.46404
Li, Y., Wang, D., Xu, G., Qiao, L., Li, Y., Gong, H., et al. (2021). ZIF-8/PI nanofibrous membranes with high-temperature resistance for highly efficient PM0. 3 air filtration and oil-water separation. Front. Chem. 1116, 810861. doi:10.3389/fchem.2021.810861
Li, Z., and Wang, C. (2013). “Effects of working parameters on electrospinning,” in One-dimensional nanostructures (Germany: Springer), 15–28.
Ling, J., Karuppiah, C., Das, S., Misnon, I. I., Yang, C.-C., Jose, R., et al. (2022). Electrospun ternary composite metal oxide fibers as an anode for lithium-ion batteries. Front. Mat. 9, 88. doi:10.3389/fmats.2022.815204
Liu, H., Zhang, S., Liu, L., Yu, J., and Ding, B. (2020). High‐performance PM0. 3 air filters using self‐polarized electret nanofiber/nets. Adv. Funct. Mat. 30 (13), 1909554. doi:10.1002/adfm.201909554
Liu, Y., Chen, X., Yu, D.-G., Liu, H., Liu, Y., and Liu, P. (2021). Electrospun PVP-core/PHBV-shell fibers to eliminate tailing off for an improved sustained release of curcumin. Mol. Pharm. 18 (11), 4170–4178. doi:10.1021/acs.molpharmaceut.1c00559
Lv, H., Guo, S., Zhang, G., He, W., Wu, Y., and Yu, D.-G. (2021). Electrospun structural hybrids of acyclovir-polyacrylonitrile at acyclovir for modifying drug release. Polymers 13 (24), 4286. doi:10.3390/polym13244286
Nam, C., Lee, S., Ryu, M., Lee, J., and Lee, H. (2019). Electrospun nanofiber filters for highly efficient PM2. 5 capture. Korean J. Chem. Eng. 36 (10), 1565–1574. doi:10.1007/s11814-019-0370-3
Nazarenko, Y., Pal, D., and Ariya, P. A. (2021). Air quality standards for the concentration of particulate matter 2.5, global descriptive analysis. Bull. World Health Organ. 99 (2), 125–137D. doi:10.2471/BLT.19.245704
Ning, T., Zhou, Y., Xu, H., Guo, S., Wang, K., and Yu, D.-G. (2021). Orodispersible membranes from a modified coaxial electrospinning for fast dissolution of diclofenac sodium. Membranes 11 (11), 802. doi:10.3390/membranes11110802
Park, H.-S., and Park, Y. O. (2005). Filtration properties of electrospun ultrafine fiber webs. Korean J. Chem. Eng. 22 (1), 165–172. doi:10.1007/BF02701480
Qi, H., Ma, Q., Xie, Y., Song, Y., Tian, J., Yu, W., et al. (2020). Electrospun polyfunctional conductive anisotropic Janus-shaped film, derivative 3D Janus tube and 3D plus 2D complete flag-shaped structures. J. Mat. Chem. C Mat. 8 (19), 6565–6576. doi:10.1039/D0TC00366B
Qin, X. H., and Wang, S. Y. (2006). Filtration properties of electrospinning nanofibers. J. Appl. Polym. Sci. 102 (2), 1285–1290. doi:10.1002/app.24361
Srikrishnarka, P., Kumar, V., Ahuja, T., Subramanian, V., Selvam, A. K., Bose, P., et al. (2020). Enhanced capture of particulate matter by molecularly charged electrospun nanofibers. ACS Sustain. Chem. Eng. 8 (21), 7762–7773. doi:10.1021/acssuschemeng.9b06853
Su, S.-Y., Liaw, Y.-P., Jhuang, J.-R., Hsu, S.-Y., Chiang, C.-J., Yang, Y.-W., et al. (2019). Associations between ambient air pollution and cancer incidence in taiwan: An ecological study of geographical variations. BMC Public Health 19 (1), 1496–1498. doi:10.1186/s12889-019-7849-z
Subbiah, T., Bhat, G. S., Tock, R. W., Parameswaran, S., and Ramkumar, S. S. (2005). Electrospinning of nanofibers. J. Appl. Polym. Sci. 96 (2), 557–569. doi:10.1002/app.21481
Wang, B., Wang, Q., Wang, Y., Di, J., Miao, S., and Yu, J. (2019). Flexible multifunctional porous nanofibrous membranes for high-efficiency air filtration. ACS Appl. Mat. Interfaces 11 (46), 43409–43415. doi:10.1021/acsami.9b17205
Wang, H., Zheng, G., and Sun, D. (2007). "Electrospun nanofibrous membrane for air filtration", in: 2007 7th IEEE conference on nanotechnology. 02-05 August 2007, Hong Kong, China. (IEEE NANO): IEEE), 1244-1247.
Wang, M., Hou, J., Yu, D.-G., Li, S., Zhu, J., and Chen, Z. (2020). Electrospun tri-layer nanodepots for sustained release of acyclovir. J. Alloys Compd. 846–156471. doi:10.1016/j.jallcom.2020.156471
Wang, S.-X., Yap, C. C., He, J., Chen, C., Wong, S. Y., and Li, X. (2016). Electrospinning: A facile technique for fabricating functional nanofibers for environmental applications. Nanotechnol. Rev. 5 (1), 51–73. doi:10.1515/ntrev-2015-0065
Xiao, J., Liang, J., Zhang, C., Tao, Y., Ling, G.-W., and Yang, Q.-H. (2018). Advanced materials for capturing particulate matter: Progress and perspectives. Small Methods 2 (7), 1800012. doi:10.1002/smtd.201800012
Xu, H., Zhang, F., Wang, M., Lv, H., Yu, D.-G., Liu, X., et al. (2022a). Electrospun hierarchical structural films for effective wound healing. Biomater. Adv. 136, 212795. doi:10.1016/j.bioadv.2022.212795
Xu, X., Zhang, M., Lv, H., Zhou, Y., Yang, Y., and Yu, D.-G. (2022b). Electrospun polyacrylonitrile-based lace nanostructures and their Cu (Ⅱ) adsorption. Sep. Purif. Technol. 288, 120643. doi:10.1016/j.seppur.2022.120643
Xue, J., Wu, T., Dai, Y., and Xia, Y. (2019). Electrospinning and electrospun nanofibers: Methods, materials, and applications. Chem. Rev. 119 (8), 5298–5415. doi:10.1021/acs.chemrev.8b00593
Yu, D. G., Wang, M., and Ge, R. (2022). Strategies for sustained drug release from electrospun multi‐layer nanostructures. Wiley Interdiscip. Rev. Nanomed. Nanobiotechnol. 14 (3), e1772. doi:10.1002/wnan.1772
Yu, D., and Lv, H. (2022). Preface. Curr. Drug Deliv. 19 (1), 1–3. doi:10.2174/156720181901220120094538
Zhang, X., Guo, S., Qin, Y., and Li, C. (2021). Functional electrospun nanocomposites for efficient oxygen reduction reaction. Chem. Res. Chin. Univ. 37 (3), 379–393. doi:10.1007/s40242-021-1123-5
Zhao, K., Lu, Z.-H., Zhao, P., Kang, S.-X., Yang, Y.-Y., and Yu, D.-G. (2021). Modified tri–axial electrospun functional core–shell nanofibrous membranes for natural photodegradation of antibiotics. Chem. Eng. J. 425, 131455. doi:10.1016/j.cej.2021.131455
Keywords: electrospinning, PAN nanofiber, fiber diameter, pore size, smoke filtration efficiency, commercial filter membrane
Citation: Zhu X and Kim K (2022) Electrospun polyacrylonitrile fibrous membrane for dust removal. Front. Mater. 9:973660. doi: 10.3389/fmats.2022.973660
Received: 20 June 2022; Accepted: 20 September 2022;
Published: 05 October 2022.
Edited by:
Vijayanandh Raja, Kumaraguru College of Technology, IndiaReviewed by:
Jiefeng Gao, Yangzhou University, ChinaCopyright © 2022 Zhu and Kim. This is an open-access article distributed under the terms of the Creative Commons Attribution License (CC BY). The use, distribution or reproduction in other forums is permitted, provided the original author(s) and the copyright owner(s) are credited and that the original publication in this journal is cited, in accordance with accepted academic practice. No use, distribution or reproduction is permitted which does not comply with these terms.
*Correspondence: Kiwoong Kim, a3draW1AaG51Lmty
Disclaimer: All claims expressed in this article are solely those of the authors and do not necessarily represent those of their affiliated organizations, or those of the publisher, the editors and the reviewers. Any product that may be evaluated in this article or claim that may be made by its manufacturer is not guaranteed or endorsed by the publisher.
Research integrity at Frontiers
Learn more about the work of our research integrity team to safeguard the quality of each article we publish.