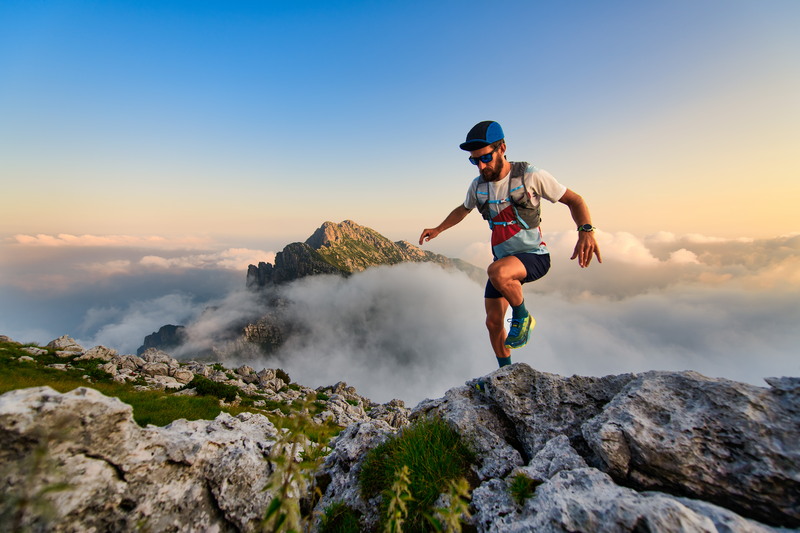
95% of researchers rate our articles as excellent or good
Learn more about the work of our research integrity team to safeguard the quality of each article we publish.
Find out more
EDITORIAL article
Front. Mater. , 01 July 2022
Sec. Smart Materials
Volume 9 - 2022 | https://doi.org/10.3389/fmats.2022.943315
This article is part of the Research Topic Preparation, Properties and Applications of Electro-Responsive Smart Materials View all 6 articles
Editorial on the Research Topic
Preparation, Properties and Applications of Electro-Responsive Smart Materials
Electro-responsive materials are a kind of smart material with the ability to alter their mechanical or physical properties in response to an external electric field. Due to their unique properties, electro-responsive materials can be implemented in smart structures, such as soft actuators, deformable wings, artificial muscles, flexible cells, smart fluids dampers, stiffness tunable isolators, sensing concretes, and so on. The preparation, testing, mechanisms, theories, and applications of electro-responsive materials are of interest to scholars in smart materials and structures. In the preparation of these materials, one key task is to find optimal compositions to achieve stability yet maximize their physical response to the external electric field. Another priority is to develop electro-responsive materials with various physical responses. In properties testing, the key task is to develop methodology to measure the response more accurately. In engineering applications, the focus is on exploring the application of electro-responsive materials in such fields as materials, mechanical engineering, civil engineering, biomedical devices, space exploration, and stretchable electronics.
As a result of the growing attention on the sensing techniques in soft electro-mechanical systems, such as wearable electronic equipment and artificially intelligent devices, soft-strain sensors have been explored extensively. Their inherent advantages include biocompatibility, high flexibility, and sensitivity, as well as a broad sensing range. Chang et al. investigated a biological template method to fabricate an ionic polymer-metal composite (IPMC) strain sensor with bionic hierarchical structures. The multi-level structure of the reed leaf surface, which can improve the contact area between the substrate and the electrode layers, was utilized as the natural template. Hierarchical structures were observed on the IPMC samples, including pyramid strips with a width in the range of 60 μm–80 μm as well as synaptic scatters with a diameter of around 10 μm. In addition, five kinds of sensors with different interface structures were obtained by combining the traditional microneedle-roller-roughening and chemical-plating processes. It was found that the IPMC sensor with a reed-leaf and microneedle structure on each side demonstrated the best performance, along with high linearity, a sensitivity of 62.5 mV/1%, and a large generated voltage peak under given mechanical stimuli, which was 3.7 times of that in the sample fabricated without roughening. This work presented a feasible strategy for future interface design and performance optimization of ionic soft sensors.
Electrorheological (ER) fluids are considered a type of smart fluid because their rheological characteristics can be altered through an electric field. Cheng et al reported a novel TiO2-based giant ER fluid that exhibits ultra ER effects at low electric fields. When the external field strength was 2 kV/mm, the static yield stress of the TiO2-based giant ER fluid reached 122 kPa, which was several orders of magnitude higher than other giant ER fluids published so far. This character gives the advantage of low power consumption, sufficient shear stress, low leaking current, and security. It was found that this low-field high-performance characteristic was mainly derived from the interface polarization of TiO2 dielectric particles and the–OH group. The work serves as a promising indication of how to achieve highly active ER materials and understand the detailed mechanism.
Poly (ionic liquid) (PIL), as a new type of polyelectrolyte, has great potential applications in various fields, one of which is ER fluids. Because of the plasticizing effect of counterions in PIL, the glass transition temperature of PIL is relatively low, which limits the operating temperature range of PIL-based ER fluids. Making composite particles by introducing inorganics into PIL is an effective way to improve the thermal stability of PIL; however, the fabrication processes are always complex. Zhang et al proposed a facile one-pot method to prepare PIL/TiO2 composite particles. In this method, both the polymerization of ionic liquid monomer and the hydrolysis of titanate occurred in one system where PIL/TiO2 composite particles were easily obtained. The PIL/TiO2 particles not only showed a broader working temperature range (∼100°C) but also exhibited a higher ER effect than pure PIL particles. This method is suitable for fabricating a large number of ER materials with a stable and excellent ER effect.
Improving the transmission torque is meaningful for the application of electrorheological fluids. Li et al proposed a corrugated disc that improves transmission torque by putting the device in a shear-squeeze mode. They compared and analyzed the shear-motion characteristics of ER fluids between the flat disk and the corrugated disk, and between the double-flat disks. Their experimental results showed that the new design can enhance the transmission torque more than twice as much as the conventional design. The enhancement mainly depends on the structural parameters of the device and the performance of the ER fluids.
As a new type of magnetic sensitivity smart material, magnetorheological elastomers have been broadly applied in the field of intelligent structures and devices. Wang et al proposed a new mechanical model named the modified Bouc-Wen model, which appropriately combines the traditional Bouc-Wen model and the fractional derivative model. The simulation model was established using the Simulink software, and the fractional derivative part of the modified model was approximately calculated using the Oustaloup filter algorithm. The fitness values of simulation and experimental data under different loading conditions are higher than 98%. The modified model is accurate and effective in a wide range of strain amplitudes, frequencies, and magnetic fields. This work provides a theoretical basis for the engineering application of magnetorheological elastomers.
XD, BL, QP and TT were all guest associate editors of this editorial. XD drafted this editorial, which was further edited by BL, QP and TT. All the authors agreed to publication.
We thank the support from the National Natural Science Foundation of China (Nos. 52178459 and 52075411).
The authors declare that the research was conducted in the absence of any commercial or financial relationships that could be construed as a potential conflict of interest.
All claims expressed in this article are solely those of the authors and do not necessarily represent those of their affiliated organizations, or those of the publisher, the editors and the reviewers. Any product that may be evaluated in this article, or claim that may be made by its manufacturer, is not guaranteed or endorsed by the publisher.
We thank all authors and all reviewers for their valuable contributions.
Keywords: electro-responsive, ionic polymer-metal composite, electrorheological fluids, magnetorheological elastomers, smart materials (A)
Citation: Dong X, Li B, Peng Q and Tian T (2022) Editorial: Preparation, Properties and Applications of Electro-Responsive Smart Materials. Front. Mater. 9:943315. doi: 10.3389/fmats.2022.943315
Received: 13 May 2022; Accepted: 19 May 2022;
Published: 01 July 2022.
Edited and reviewed by:
Weihua Li, University of Wollongong, AustraliaCopyright © 2022 Dong, Li, Peng and Tian. This is an open-access article distributed under the terms of the Creative Commons Attribution License (CC BY). The use, distribution or reproduction in other forums is permitted, provided the original author(s) and the copyright owner(s) are credited and that the original publication in this journal is cited, in accordance with accepted academic practice. No use, distribution or reproduction is permitted which does not comply with these terms.
*Correspondence: Xufeng Dong, ZG9uZ3hmQGRsdXQuZWR1LmNu
Disclaimer: All claims expressed in this article are solely those of the authors and do not necessarily represent those of their affiliated organizations, or those of the publisher, the editors and the reviewers. Any product that may be evaluated in this article or claim that may be made by its manufacturer is not guaranteed or endorsed by the publisher.
Research integrity at Frontiers
Learn more about the work of our research integrity team to safeguard the quality of each article we publish.