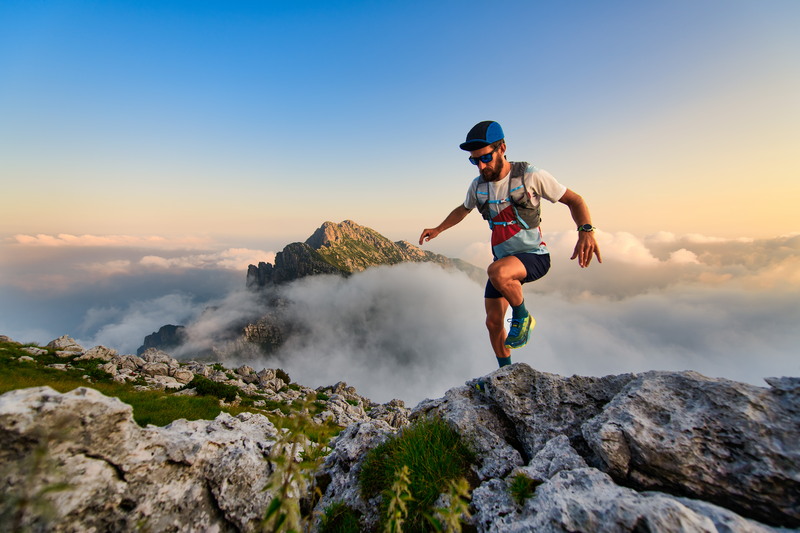
94% of researchers rate our articles as excellent or good
Learn more about the work of our research integrity team to safeguard the quality of each article we publish.
Find out more
ORIGINAL RESEARCH article
Front. Mater. , 27 June 2022
Sec. Environmental Degradation of Materials
Volume 9 - 2022 | https://doi.org/10.3389/fmats.2022.934215
This article is part of the Research Topic Materials Corrosion in High Temperature Molten Salt Environments View all 6 articles
In this article, the nickel aluminide coating prepared by the chemical vapor deposition method has adhered deliberately with nano-alumina film on the surface by the electrophoresis method. The analysis results of oxidation behavior in the air at 1,000°C reported that the nano-alumina particles adhering to the nickel aluminide coating surface appear to be effective in facilitating the θ-Al2O3 to α-Al2O3 phase transformation. The fast θ to α phase transformation helps reduce the oxidation rate of the nickel–aluminum coating and prevents the cracking and peeling in the oxide scale. The research addressed a novel method to improve the high-temperature oxidation resistance of nickel aluminide coatings.
Nickel aluminide coatings, such as NiAl and Ni2Al3, are generally applied to the surfaces of engine turbine components to lengthen their service life (Goward, 1970; Goward and Boone, 1971; Leng et al., 2020). The common preparation methods of nickel aluminide coatings include slurry, powder embedding, physical vapor deposition, and chemical vapor deposition (CVD) (Nicholls, 2003; Bouchaud et al., 2013; Mollard et al., 2013; Montero et al., 2013). Compared with the other methods, the coating prepared by the CVD method has a stronger bonding force with the substrate and is denser, so its high-temperature oxidation resistance is better (Warnes and Punola, 1997; Yavorska et al., 2011; Goral et al., 2020).
The surface of the nickel aluminide coating will form protective thermally grown oxide (TGO)-Al2O3 at high temperatures (Swadba et al., 2011). Several types of Al2O3 have been found on alloys forming aluminides, such as γ-Al2O3, δ-Al2O3, θ-Al2O3, and α-Al2O3. α-Al2O3 is a good protective oxide scale because of its thermodynamic stability and slow growth rate (An et al., 2000). During the oxidation at a temperature above 1,100°C, the nickel aluminide coating quickly forms the thermodynamically stable α-Al2O3 scale, while the metastable alumina variants scales (normally γ and θ) are formed after a oxidation for a long time (Khana et al., 2019) at a temperature below 1,100°C, during which they always experience the phase transformation of metastable-to-stable alumina (Peng et al., 2003; Huang and Peng, 2016), such as θ-to-α. This phase transformation accompanies a volume shrinkage of about 10%, sometimes resulting in the generation of micro-cracks in the alumina scale (Peng et al., 2003; Veal et al., 2006; Wang and Zhou, 2012; Huang and Peng, 2016).
As a result, prompting the conversion of metastable-to-stable alumina is advantageous for improving the oxidation resistance of nickel aluminide coatings at high temperatures (Khana et al., 2019). Moreover there is a well-known fact that a rising temperature causes a faster phase transformation of the metastable-to-stable alumina, dopants or template effects have been found to change this process (Tolpygo and Clarke, 2000; Huang et al., 2019). For instance, Pint and his co-workers (Pint et al., 1997; Huang et al., 2019) found that Y2O3, La2O3, ZrO2, and HfO2 dispersions in β-NiAl tend to retard the θ-to-α phase transformation, whereas TiO2 dispersion appears to promote this process. Lately, Peng and his co-workers (Xu et al., 2010; Huang and Peng, 2016; Wang et al., 2016; Khana et al., 2019) reported the promoted formation of an α-Al2O3 scale on nickel aluminide with surface Cr2O3 particles. On these bases, we have a concept that spreading oxide particles (e.g., Cr2O3) with the same crystallographic structure as α-Al2O3 to aluminide can promote the growth of an α-Al2O3 scale at a high temperature (Yin and Zhen, 2015). Valet et al. (Liu et al., 2007; Huang and Peng, 2016; Khana et al., 2019) found that the remaining fine α-Al2O3 grits, used for the polishing surface of the intermetallic sample, appeared to promote the nucleation of α-Al2O3.
In this article, nano-alumina particles were deposited on the surface of aluminide coatings by electrophoresis, and their effects on the phase transition and oxidation kinetics of the nickel aluminide coatings were investigated. It is aimed to better understand the phase transitions of the oxidative properties of nickel aluminides, and find a more effective way to improve the oxidation resistance of these nickel aluminide oxides by promoting the growth of α-Al2O3.
The pure nickel samples with dimensions of 10 mm × 10 mm × 2 mm were cut from an electrolyte pure nickel plate. After being abraded to a final 2,000 grit SiC paper, they were ultrasonically cleaned in acetone. By using the CVD method, the Ni2Al3 coating was developed on the pure nickel surface after aluminizing at 750°C × 200 torr for 3 h. The preparation process is as follows: high-purity Cl2 was injected into the reaction chamber containing high-purity aluminum particles (purity: 99.99%, size: 3 mm) to generate gas-phase halide AlClx. AlClx was carried into the deposition chamber by Ar, and then was reduced to activity [Al] by H2. The [Al] deposited on the pure nickel, and reacted with nickel to form a nickel aluminum coating. After aluminizing for 3 h, the samples were cooled to room temperature with the furnace. The main equations involved in the reaction are as follows:
The nano-Al2O3 film was made to adhere to the nickel aluminum coating surface by electrophoresis technology. High temperature oxidation experiments were performed using the SETSYS evolution thermo-gravimetric analyzer (for in situ recording oxidation curves) in the air at 1,000°C for 50 h. A nickel layer was coated on the oxide scale surface using electroplating in the acidic electroless nickel plating mixed solution (containing 25 g/L C3H6O3, 6.25 g/L Na2CO3, 43 g/L NiSO4·6H2O, and 25 g/L NaH2PO2·H2O) at 98°C for 5 h. Scanning electron microscope (SEM), energy dispersive spectroscopy (EDS), and X-ray diffraction (XRD) were used to investigate the surface and cross-section morphologies, structure, and the phases of various nickel aluminide coatings.
The cross-sectional morphology (Figure 1A) shows that a single layer of nickel aluminide coating (∼30 µm thickness) was deposited on pure nickel after aluminizing. The coating was dense and well adherent to the pure Ni substrate. The Ni content and Al content of the coating were 39.3 at.% and 58.9 at.%, respectively. The XRD result (Figure 1C) characterized them as deposited coating as a δ-Ni2Al3 phase. Backscattered SEM images of the polished cross-section of a nano-Al2O3 film sample are shown in Figure 1B. The as-electrophoresis Al2O3 film was continuous with a thickness of around 3 µm. However, the Al2O3 film was partially detached from the coating due to grinding and polishing during the preparation process.
FIGURE 1. Cross-sectional morphologies of Ni2Al3 coatings (A) naked, (B) with an Al2O3 film on the surface, and (C) XRD pattern of the naked Ni2Al3 coating.
Figure 2 shows the dependence on the time of mass grain and the square of mass grain of naked and Al2O3 film-covered Ni2Al3 coatings oxidated at 1,000°C for 50 h. The mass grain of Al2O3 film-covered Ni2Al3 coating is less than that of the naked one as shown in Figure 2A. In the early stages of oxidation , the surface of the two types of coatings quickly formed an aluminum oxide scale, and the oxidation weight gain rate was high. Due to the presence of alumina, the contact surface between oxygen and the coating gradually decreased, and the alumina scale gradually stabilized, so the oxidation weight gain curve tended to be flat. As shown in Figure 2B, during the 50-h oxidation, the oxidation processes of both coatings can be divided into two stages: In the initial stage (<3 h), the parabolic oxidation rate constant (KpI) of the Al2O3 film–covered Ni2Al3 coating is 3.2 × 10–13 g2/cm4s lower than that of the naked coating with parabolic oxidation rate constant KpI of ∼4.4 × 10–13 g2/cm4s. In the steady stage (>3 h), the parabolic oxidation rate constant (KpⅡ) of the Al2O3 film–covered Ni2Al3 coating is 1.2 × 10–13 g2/cm4s, also lower than that of the naked coating with parabolic oxidation rate constant KpⅡ of ∼2.4 × 10–13 g2/cm4 s.
FIGURE 2. (A) Oxidation kinetics curves and (B) corresponding parabolic plots of naked and Al2O3 film–covered Ni2Al3 coatings oxidated in air at 1,000 °C.
The Al2O3 film-covered coating macroscopic surface after oxidation is shown in Figure 3A, and then the electrophoretic alumina film was removed using alcohol, as shown in Figure 3B. The surface characteristics of the naked Ni2Al3 coating changes with the increasing oxidation duration , as illustrated in Figures 4A,C,E,G. Fine alumina crystals developed on the surface at the early stage of high-temperature oxidation (30 min), and the color depth difference was caused by the distinct growth directions. The size of thin needle-like alumina crystals grew bigger after 2 h oxidation, and the oxide scale got thicker and denser. After being oxidized for 5 h, some acicular alumina became stagnant, cracks appeared on the surface, and the acicular alumina crystals were rapidly regenerated in the spalling area. After 50 h of oxidation, the oxide scale is mostly composed of acicular alumina and round alumina. According to the above morphologies and the characteristics of the alumina phase structure (Swadba et al., 2011), it can be judged that θ-Al2O3 is rapidly formed in the early stage of oxidation, and then the θ phase is partially converted into the α phase. The growth of α-Al2O3 will inhibit the growth of the θ phase. The lateral growth direction of α-Al2O3 resulted in surface unevenness. The conversion of θ phase to α phase will cause the microcracks or even local spalling because of volume shrinkage (the transformation from metastable alumina to α-Al2O3 is a reconstructive phase transition, which is a first-order phase transition and the process is irreversible). The spalling area will quickly generate θ-Al2O3, so both θ-Al2O3 and α-Al2O3 phases can be seen on the surface after high-temperature oxidation for 50 h. For the Al2O3 film–covered Ni2Al3 coating, an α-Al2O3 scale was formed rapidly in the early stage of oxidation. With the prolongation of oxidation time, the oxide scale gradually thickens and becomes flat (Figures 4B,D,F,H). After 5 h of oxidation, the scale appeared to slightly peel. After 50 h of oxidation, a dense and stable alumina scale has been formed. Therefore, there is no phase change in the oxide scale of the Al2O3 film–covered coating during the whole oxidation process. It can be seen in Figure 5A that the coating degradation completely conforms to the mechanism of the nickel–aluminum coating: δ-Ni2Al3→β-NiAl→γ′-Ni3Al. At the beginning of oxidation, the generated alumina is too thin and its X-ray diffraction peak intensity is weak, so the original diffraction peak pattern is partially enlarged as shown in Figures 5B′,C′, from which it is known that the α phase is formed on the surface of the electrophoretic alumina film sample from the beginning of oxidation. Based on the XRD, SEM, and TGA analysis, the early oxidation progress of aluminide in the absence and presence of the surface Al2O3 film is shown in Figure 6. At the beginning of oxidation (Stage Ⅰ), θ-Al2O3 is rapidly formed on the naked aluminide surface, while α-Al2O3 is formed on the surface of the aluminide coating with electrophoretic Al2O3 particles (An et al., 2000). Then both increase to form an alumina scale (Stage Ⅱ); the alumina is much denser as shown in Figures 4C,D. In stage Ⅲ, generated α-Al2O3 grows inward and outward at the same time, during which the most electrophoresed Al2O3 film on the surface is pushed outward, and a small part is wrapped by the outwardly growing α-Al2O3 (Huang and Peng, 2016). At this time, the exposed θ-Al2O3 of the naked sample transforms into α-Al2O3 (Figure 4E). With α-Al2O3 gradually increasing, an α-Al2O3 scale was formed at the interface between NiAl coating and θ-Al2O3 (Stage Ⅳ). During this phase transition, volume shrinkage will occur, resulting in cracks or even peeling of the scale (Tolpygo and Clarke, 2000), which are visible on the surface topography (Figure 4).
FIGURE 3. Surface with (A) alumina particles after oxidation and (B) removal of alumina particles after oxidation.
FIGURE 4. Surface morphologies of the alumina scale formed on the δ-Ni2Al3 coating at 1,000°C for different oxidation times. (A), (C), (E), and (G): Ni2Al3; (B), (D), (F), and (H): Al2O3 film–covered Ni2Al3.
FIGURE 5. XRD patterns of (A) Ni2Al3 coating at different times and (B) and (C) 30 min and 50 h naked and the Al2O3 film–covered Ni2Al3 coating after oxidation in the air at 1,000°C and (B′) (C′) locally magnified.
FIGURE 6. Schematic transient oxidation progress of the Ni2Al3 coatings (A) without and (B) with the surface Al2O3 particles.
The nickel aluminide thermally grows θ-Al2O3 before α-Al2O3 because the former has lower surface energies and thus a much lower nucleation barrier ΔG*. This is the direct origin of why the metastable alumina phases rather than the most stable ones usually form during the initial oxidation of β-NiAl (Huang et al., 2019). Therefore, during the subsequent oxidation, the undesirable metastable-to-stable phase transformation of alumina becomes unavoidable. The direct α-Al2O3 formation without metastable-to-stable alumina phase transformation on typical oxide particles (e.g., α-Al2O3, Cr2O3, and Fe2O3) means that the template effect of the oxides isostructural to α-Al2O3 intrinsically reduces ΔG* of α-Al2O3 down to such a level in favor of its thermal nucleation (Pint et al., 1997; Wang and Zhou, 2012; Yin and Zhen, 2015; Huang et al., 2019). The template effect has been widely studied by revealing some oxides (e.g., Cr2O3 and Fe2O3), which are isostructural to α-Al2O3, and may serve as the nucleation sites facilitating the growth of the α-Al2O3 (Pint et al., 1997; Wang and Zhou, 2012; Yin and Zhen, 2015; Huang et al., 2019). This interpretation coincides well with a promoted θ-to-α alumina phase transformation on β-NiAl when it has been embedded with the fine particles of α-Al2O3 (Veal et al., 2006). The electrophoretic α-Al2O3 particles have the same HCP crystal structure as the α-Al2O3 grown from the coating and can act as an epitaxial growth platform for α-Al2O3 during oxidation, reducing the nucleation energy of the latter. Therefore, when the surface is completely covered with alumina nanoparticles, the θ-to-α phase transition can be skipped when the coating is oxidized at 1,000°C, and α-Al2O3 is directly generated.
The Al2O3 particle pretreatment significantly decreases the oxidation rate, leading to a slower degradation rate of the nickel aluminide. As seen in the cross-sectional characteristics in Figure 7, after 50 h of oxidation, the phase structures of both types of coatings are NiAl + Ni3Al phases, indicating that the unstable δ-Ni2Al3 phase degenerates into the NiAl phase at a high temperature of 1,000 °C, and then unceasingly degenerates into the Ni3Al phase with oxidation time prolongation. In Figure 7, the thickness of the naked coating and the Al2O3 film–covered coating after oxidation is thicker than that before oxidation, indicating that both coatings have a certain degree of Al elements internal-diffusion during the high-temperature oxidation process. It can be seen from Figures 7A,B that the alumina scale thickness of the naked coating is about 7.9 µm, which is twice that of the Al2O3-scale–covered coating (∼3.5 µm). This is consistent with the analysis result of the oxidation growth curve. During the oxidation process, aluminum ions moving from the inside of the coating to the coating surface meet with oxygen atoms to form an aluminum oxide scale, so there will be a γ-Ni3Al phase formed due to the Al rapid consumption between the aluminum oxide film and the nickel–aluminum coating. Since the naked coating needs to consume more Al elements to form the aluminum oxide scale, the thickness of the γ-Ni3Al phase coating is significantly thicker than that of the Al2O3 film–covered coating, which is near the aluminum oxide scale. The reason for the difference in the thickness of the two coatings is that electrophoretic alumina can promote the formation of α-Al2O3 on the coating surface, which can effectively prevent the oxygen element from entering the coating, reducing the consumption of the Ni2Al3 coating. Therefore, promoting the formation of stable-phase α-Al2O3 is an effective way to improve the high-temperature oxidation resistance and prolong the life of the coating. The large difference in coating consumption in the same sample is due to the consumption of aluminum elements again to form an aluminum oxide scale after the local scale peels off. With the prolongation of oxidation time, the cracks increase and cause local peeling of the aluminum oxide scale. The spalled area will quickly deplete the nickel–aluminum coating to form a new aluminum oxide scale.
FIGURE 7. Cross-sectional morphologies of the Al2O3 scales on the (A) and (B) naked Ni2Al3 coating, and (C) and (D) the Al2O3 film–covered Ni2Al3 after 50 h of oxidation in the air at 1,000°C.
The Ni2Al3 coating with a thickness of 35 μm was prepared on the pure Ni matrix using a chemical vapor deposition method at 750°C × 200 T for 3 h, and then the Al2O3 film was made to adhere to the Ni2Al3 coating surface by electrophoresis technology. Because of the lower power required to form the critical nuclei, the θ-Al2O3 formed earlier on the naked Ni2Al3 coating and then undergo a θ-to-α Al2O3 transition process during the oxidation process at 1,000 °C. The electrophoretic Al2O3 film adhering to Ni2Al3 coating can skip this phase transition because the Al2O3 film on the coating surface can provide a crystal template to promote the nucleation of α-Al2O3 at the beginning of oxidation. The rapid nucleation of α-Al2O3 significantly reduces the oxidation rate of NiAl coating and prevents microcracks and voids caused by phase transformation.
The original contributions presented in the study are included in the article/supplementary material; further inquiries can be directed to the corresponding author.
YF carried out experiments; XS directed the experiment and analyzed experimental results; SD analyzed experimental results.
The work is supported by the Graduate Innovation Special Fund Project of Nanchang Hangkong University (project Grant No. YC2021-S660).
The authors declare that the research was conducted in the absence of any commercial or financial relationships that could be construed as a potential conflict of interest.
All claims expressed in this article are solely those of the authors and do not necessarily represent those of their affiliated organizations, or those of the publisher, the editors, and the reviewers. Any product that may be evaluated in this article, or claim that may be made by its manufacturer, is not guaranteed or endorsed by the publisher.
An, T. F., Guan, H. R., Sun, X. F., and Hu, Z. Q. (2000). Effect of the θ–α-Al2O3 Transformation in Scales on the Oxidation Behavior of a Nickel-Base Superalloy with an Aluminide Diffusion Coating. Oxid. Mater. 54, 301–316.
Bouchaud, B., Rannou, B., and Pedraza, F. (2013). Slurry Aluminizing Mechanisms of Ni-Based Superalloys Incorporating an Electrosynthesized Ceria Diffusion Barrier. Mater. Chem. Phys. 143, 416–424. doi:10.1016/j.matchemphys.2013.09.022
Goral, M., Ochal, K., Kubaszek, T., and Drajewicz, M. (2020). The Influence of Deposition Technique of Aluminide Coatings on Oxidation Resistance of Different Nickel Superalloys. Mater. Today Proc. 33, 1746–1751. doi:10.1016/j.matpr.2020.04.863
Goward, G. W., and Boone, D. H. (1971). Mechanisms of Formation of Diffusion Aluminide Coatings on Nickel-Base Superalloys. Oxid. Mater. 3, 475–495. doi:10.1007/bf00604047
Goward, G. W. (1970). Current Research on the Surface Protection of Superalloys for Gas Turbine Engines. JOM 22, 31–39. doi:10.1007/bf03355665
Huang, Y., Peng, X., and Chen, Q. (2019). TiO2 Nanoparticles-Assisted α-Al2O3 Direct Thermal Growth on Nickel Aluminide Intermetallics: Template Effect of the Oxide with the Hexagonal Oxygen Sublattice. Corros. Sci. 153, 109–117. doi:10.1016/j.corsci.2019.03.025
Huang, Y., and Peng, X. (2016). The Promoted Formation of an α-Al 2 O 3 Scale on a Nickel Aluminide with Surface Cr 2 O 3 Particles. Corros. Sci. 112, 226–232. doi:10.1016/j.corsci.2016.07.029
Khana, A., Huang, Y., Dong, Z., and Peng, X. (2019). Effect of Cr2O3 Nanoparticle Dispersions on Oxidation Kinetics and Phase Transformation of Thermally Grown Alumina on a Nickel Aluminide Coating – ScienceDirect. Corros. Sci. 150, 91–99.
Leng, W., Pillai, R., Naumenko, D., Galiullin, T., and Quadakkers, W. J. (2020). Effect of Substrate Alloy Composition on the Oxidation Behaviour and Degradation of Aluminide Coatings on Two Ni Base Superalloys. Corros. Sci. 167, 81–99. doi:10.1016/j.corsci.2020.108494
Liu, G., Li, M., Zhu, M., and Zhou, Y. (2007). Transient of Alumina Oxide Scale on β-NiAl Coated on M38G Alloy at 950°C. Intermetallics 15, 1285–1290. doi:10.1016/j.intermet.2007.03.010
Mollard, M., Rannou, B., Bouchaud, B., Balmain, J., Bonnet, G., and Pedraza, F. (2013). Comparative Degradation of Nickel Aluminized by Slurry and by Pack Cementation under Isothermal Conditions. Corros. Sci. 66, 118–124. doi:10.1016/j.corsci.2012.09.009
Montero, X., Galetz, M. C., and Schütze, M. (2013). Low-activity Aluminide Coatings for Superalloys Using a Slurry Process Free of Halide Activators and Chromates. Surf. Coatings Technol. 222, 9–14. doi:10.1016/j.surfcoat.2013.01.033
Nicholls, J. R. (2003). Advances in Coating Design for High-Performance Gas Turbines. MRS Bull. 28 (9), 659–670. doi:10.1557/mrs2003.194
Peng, X., Clarke, D. R., and Wang, F. (2003). Transient-alumina Transformations during the Oxidation of Magnetron-Sputtered CoCrAl Nanocrystalline Coatings. Oxid. Metals 60, 225–240. doi:10.1023/a:1026015101783
Pint, B. A., Treska, M., and Hobbs, L. W. (1997). The Effect of Various Oxide Dispersions on the Phase Composition and Morphology of Al2O3 Scales Grown on β-NiAl. Oxid. Met. 47, 1–20. doi:10.1007/bf01682369
Swadba, L., Nawrat, G., Mendala, B., and Goral, M. (2011). The Influence of Deposition Process on Structure of Platinum-Modified Aluminide Coatings O Ni-Base Superalloy. Key Eng. Mat. 465, 247–250.
Tolpygo, V. K., and Clarke, D. R. (2000). Microstructural Study of the Theta-Alpha Transformation in Alumina Scales Formed on Nickel-Aluminides. Mater. A. T. High. Temp. 17, 59–70. doi:10.1179/mht.2000.011
Veal, B. W., Paulikas, A. P., and Birtcher, R. C. (2006). Mechanisms and Control of Phase Transition in Thermally Grown Aluminas. Appl. Phys. Lett. 89, 505. doi:10.1063/1.2364124
Wang, X., Peng, X., Tan, X., and Wang, F. (2016). The Reactive Element Effect of Ceria Particle Dispersion on Alumina Growth: A Model Based on Microstructural Observations. Sci. Rep. 6, 29593, 1–10. doi:10.1038/srep29593
Wang, Y. D., and Zhou, Y. B. (2012). Cyclic-Oxidation of RexOy-Modified Aluminide Coating. Amr 557-559, 1721–1726. doi:10.4028/www.scientific.net/amr.557-559.1721
Warnes, B. M., and Punola, D. C. (1997). Clean Diffusion Coatings by Chemical Vapor Deposition. Surf. Coatings Technol. 94-95, 1–6. doi:10.1016/s0257-8972(97)00467-2
Xu, C., Peng, X., and Wang, F. (2010). Cyclic Oxidation of an Ultrafine-Grained and CeO2-Dispersed δ-Ni2Al3 Coating. Corros. Sci. 52, 740–747. doi:10.1016/j.corsci.2009.10.034
Yavorska, M., Sieniawski, J., Filip, R., and Gancarczyk, T. (2011). Microstructure Investigation of Aluminide Coatings after Platinum Modification Deposited by CVD Method on Inconel 713 LC Ni-Base Superalloy. Amr 409, 883–888. doi:10.4028/www.scientific.net/amr.409.883
Keywords: Nickel aluminide coating, alumina modified, high temperature, oxidation, phase transition
Citation: Fang Y, Shu X and Dong S (2022) High Temperature Oxidation Behavior of Nano-Alumina–Modified NiAl Coating. Front. Mater. 9:934215. doi: 10.3389/fmats.2022.934215
Received: 02 May 2022; Accepted: 16 May 2022;
Published: 27 June 2022.
Edited by:
Yi Xu, Nanchang University, ChinaReviewed by:
Zenghua Gao, Aerospace Special Materials and Processing Technology Institute Beijing, ChinaCopyright © 2022 Fang, Shu and Dong. This is an open-access article distributed under the terms of the Creative Commons Attribution License (CC BY). The use, distribution or reproduction in other forums is permitted, provided the original author(s) and the copyright owner(s) are credited and that the original publication in this journal is cited, in accordance with accepted academic practice. No use, distribution or reproduction is permitted which does not comply with these terms.
*Correspondence: Xiaoyong Shu, eGlhb3lvbmcyMDJAMTI2LmNvbQ==
Disclaimer: All claims expressed in this article are solely those of the authors and do not necessarily represent those of their affiliated organizations, or those of the publisher, the editors and the reviewers. Any product that may be evaluated in this article or claim that may be made by its manufacturer is not guaranteed or endorsed by the publisher.
Research integrity at Frontiers
Learn more about the work of our research integrity team to safeguard the quality of each article we publish.