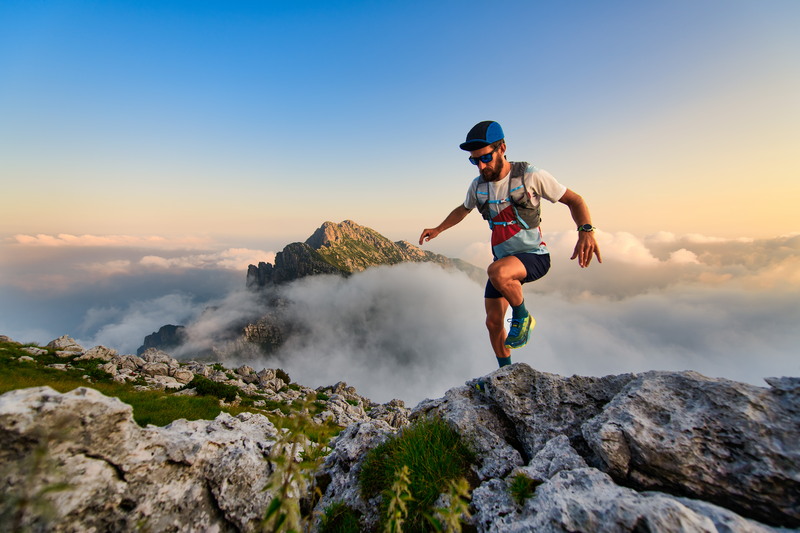
95% of researchers rate our articles as excellent or good
Learn more about the work of our research integrity team to safeguard the quality of each article we publish.
Find out more
ORIGINAL RESEARCH article
Front. Mater. , 10 May 2022
Sec. Environmental Degradation of Materials
Volume 9 - 2022 | https://doi.org/10.3389/fmats.2022.896341
This article is part of the Research Topic Machining Technology and Environmental Degradation Mechanism of Surface Microstructure of Special Materials View all 10 articles
The nanoindentation test is extensively used to obtain the mechanics performance of different kinds of materials. In this study, the general process in the lapping and polishing of Q235 steel samples for nanoindentation has been analyzed by considering the pressure (P), rotation speed of the lapping and polishing plate (rp), flow rate of abrasive slurry (Qa), and the processing time (t). It is found from the lapping experiments with a full factorial design that the optimized processing parameters are rp of 200 r/min, P of 30 N, and t of 4 min considered in this study by considering the material removal rate and subsurface damage. The central composite design method has been used to design the polishing experiments, and the support vector machine (SVM) method has been used to deal with these experimental results, and it is found that the developed SVM model can accurately predict the surface roughness under different processing parameters. Then, based on the SVM model, the genetic algorithm (GA) method is used to obtain the optimized processing parameters in the polishing process, and it is found from the SVM-GA study that the optimized processing parameters in the lapping process are rp of 108 r/min, P of 33 N, Qa of 20 ml/min, and t of 3 min. Finally, a set of nanoindentation tests have been conducted to evaluate the lapping and polishing performance, and it is found that the surface integrity has been significantly improved after the optimization of the lapping and polishing parameters by using the SVM-GA method considered in this study.
With the fast development in the fabrication of structures on the functional materials used in aerospace engineering, renewable energy engineering, and microelectronics engineering, the characterization of material properties at the microscale and nanoscale levels must be accurately obtained (Reggente et al., 2020; Hossain et al., 2022). Currently, nanoindentation is considered a powerful technique used to quantitatively characterize the mechanical properties of different kinds of materials (Das et al., 2022), and by fitting the appropriate models to the curve of force with respect to displacement obtained from the test, the major material properties, such as the elastic modulus, hardness, and fracture toughness can be measured at the microscale and nanoscale (Isik et al., 2022; Song et al., 2022). Since the indentation depths are in the order of nanometers, the surface quality of the sample has an essential effect on the nanoindentation test (Chen et al., 2014). Therefore, it is necessary to investigate the preparation of samples with good surface integrity.
Abrasive machining technology, as one of the non-traditional machining technologies, has been extensively used to produce complicated structures and smooth surfaces with high efficiency and accuracy (Ge J. et al., 2021; Cheng et al., 2022; Zhang et al., 2022), by which the material removal is made by the successive impacts of abrasive particles on the target surface (Hu et al., 2022; Qi et al., 2022). The abrasive lapping and polishing techniques are often used to realize the high surface finish of the flat target surface (Ge J. Q. et al., 2021; Ji et al., 2022). Li et al. conducted the investigation on the fixed-abrasive planetary lapping technology according to a generic model, and the lapping uniformity has been improved due to the uniform distribution of the particle trajectories moving on the target surface (Li et al., 2019). By analyzing the kinematics and trajectory in the fixed-abrasive planetary lapping process, Wen et al. explored the effect of the rotation speed ratio of the work piece to the lapping plate on the distribution of the particle trajectories in the machining of interdigitated micro-channels on bipolar plates, and it is found that the surface integrity has been enhanced (Wen et al., 2016). Chen et al. designed a novel driving system which was fixed on the single-side planetary abrasive lapping machine to realize the irrational rotation speed ratio of the work piece to the lapping plate which can improve the surface quality in terms of the surface form uniformity (Chen et al., 2021). In addition, in the abrasive polishing process, the abrasive slurry is usually used to conduct the precision and ultra-precision polishing of the target surface with free abrasive particles. Strey and Scandian studied the effect of the abrasive polishing load on the surface roughness and material removal rate of hard-brittle materials, and it is found that the related processing parameters have significant effects on the surface finish (Strey and Scandian, 2021). By designing the ice-bonded abrasive polishing tool, Nayak and Ramesh Babu investigated the influence of the tool and work piece interface temperature rise on the life of the polishing process, and this type of polishing plate could be used to improve the polishing life and the surface quality (Nayak and Ramesh Babu, 2020).
According to the aforementioned analysis, to improve the surface integrity in the lapping and polishing process, the novel designs of the lapping or polishing plate with different driving systems are generally used; however, limited research has been contributed to the optimization of the processing parameters involved in the lapping and polishing process for the improvement of the surface quality, which is the most convenient and effective way with the lowest cost as well. Thus, in this study, the optimization in the lapping and polishing of steel samples for nanoindentation will be investigated by using the support vector machine and genetic algorithm methods.
As shown in Figure 1, in the experiment, a GP-1000 A automatic lapping and polishing machine is used, including the abrasive slurry feeding system, rotation speed control system, lapping and polishing plate, work piece fixture, and pressure loading system, in which the range of the pressure (P) is from 5 to 60 N, and the range of the rotation speed of the lapping and polishing plate (rp) is from 0 to 1,000 r/min. In general, both the lapping and polishing processes are necessary for the preparation of samples for the nanoindentation tests with high surface integrity, and the lapping and polishing processes considered in this study are shown in Figure 2. In the lapping process, the sandpapers with relatively large sizes of abrasive particles are fixed on the lapping and polishing plates to achieve a high material removal rate from the target within a given processing time (t). In the polishing process, free abrasive particles with relatively small sizes are formed between the work piece and the lapping and polishing plates by using the abrasive slurry feeding system with a given flow rate (Qa) to realize the high surface integrity on the target.
FIGURE 2. Schematic representation of the lapping and polishing of steel samples for nanoindentation.
In this study, the Q235 steel is selected as the work piece, with dimensions of 15 mm × 15 mm×5 mm, whose density is 7.85 g/cm3, elastic modulus is 210 GPa, and its original Ra and SSD are about 300–500 nm and 9–12 μm, respectively. Moreover, the PSA Silicon Carbide sandpapers with different sizes of P800 (average diameter of 22 µm), P1200 (average diameter of 15 µm), P2400 (average diameter of 10 µm), and P4000 (average diameter of 5 µm) are employed in the lapping process, while in the polishing process, the diamond and silicon dioxide abrasives with different sizes (see Figure 2) are used from the rough polishing process to the final polishing process. Since P, rp, Qa, and t are the major processing parameters that could affect the performance of the lapping and polishing processes, it is required to explore the optimized design of these processing parameters.
In the lapping process, according to the previous studies, P and rp are the essential factors that would affect the lapping performance in terms of the material removal rate (MRR) and subsurface damage (SSD), and it is found that when the processing time for each lapping process shown in Figure 2 is more than 3 min, both of the MRR and SSD seems to be stable. Thus, in the lapping process, three levels of P at 20, 30, and 40 N and three levels of rp at 100, 150, and 200 r/min are considered with a full factorial design under t = 4 min, which results in a total of nine tests (Xie et al., 2021).
In the polishing process, P, rp, Qa, and t are found to be the important factors affecting the polishing performance in terms of surface roughness (Ra) so that three levels of P at 20, 30, and 40 N, three levels of rp at 100, 150, and 200 r/min, three levels of Qa at 10, 15, and 20 ml/min, and three levels of t at 1.5, 2, and 2.5 min are used in this study. Because of the many processing parameters considered previously, the traditional full factorial design would result in a large number of tests which is not suitable for this study. The central composite design (CCD) has been extensively used to optimize the experimental design with the least number of tests (Imanian and Biglari, 2022), which can not only evaluate the linear and interaction terms but can also estimate the high-order effects. Thus, the experimental design in the polishing process is determined by the CCD method which results in a total of 31 tests.
The MRR, SSD, and Ra are the three essential factors that can be used to evaluate the lapping and polishing performance. The MRR can be calculated by measuring the mass of the work piece with an accuracy of 0.01 mg before and after the lapping process within the given processing time, whereas it is hard to obtain the MRR by measuring the mass loss before and after the polishing process because of the little material removal in this process. The SSD can be measured after the lapping process by using the Nano Indenter G200 with an accuracy of 0.01 nm and maximum depth of 500 μm, and again, this is hard to be obtained after the polishing process because the limited SSD can be observed. Ra can be measured after both the lapping and polishing processes with the assistance of the SuperView White Light Interferometer with an accuracy of 0.002 nm. Thus, these three significant factors are considered in this study to quantitatively evaluate the lapping and polishing performance.
The experimental results in the lapping process are shown in Table 1. When P is 30 N, the depth of the SSD is the smallest under the same rp, and the depth of the SSD increases sharply from 30 to 40 N, which agrees well with the existing research results. It is attributed to the reason that the variation of pressure in this range results in an increase in the thermal effect, thus causing large damage to the target. It is also found from Table 1 that rp is positively correlated with the depth of the SSD, which indicates that within the range of 100–200 r/min, the lower the rotation speed, the better the depth of the SSD will be. In addition, rp and P are found to be positively correlated with the MRR, and the MRR is maximum when P is 40 N and rp is 200 r/min. Since the results of the full factorial experiment can be directly compared from Table 1, the combination of the optimal levels of each factor is the optimized combination of processing parameters without considering the interactions. From the perspective of the SSD and MRR, the optimized processing parameters in the lapping process are found to be rp of 200 r/min, P of 30 N, and t of 4 min considered in this study.
According to the optimized processing parameters in the lapping process, the original samples of the Q235 steel have been first lapped with these optimized processing parameters, and then, they are polished under different conditions, as shown in Table 2, where the experimental results in the polishing process are given. Since many combinations of the processing parameters are considered by using the CCD method, in this study, a support vector machine (SVM) is proposed to deal with these experimental results. The SVM is a supervised machine learning model that uses classification algorithms for two-group classification problems. After giving an SVM model sets of labeled training data for each category, it can categorize new data (Fayed and Atiya, 2021; Liang et al., 2022). Thus, by using MATLAB software, 31 experimental data in terms of Ra are trained with the SVM method to obtain the fitness function, which can be used to predict the Ra under different processing parameters. To evaluate the predicting capacity of the SVM method, additional five tests have been conducted, and the results are shown in Table 3.
Figure 3A shows the evaluation of the predicting accuracy of the SVM, where the red dots represent the training data based on the 31 experimental results, and the blue dots represent the predicting data according to the processing parameters given in Table 3, and it can be seen from this figure that the value of R2 is 0.99415 which indicates that by using the developed SVM model, it can accurately predict Ra under different processing parameters considered in this study. It can be also seen from Figure 3B that the quantitative comparison between the SVM predicting results and experimental results show a good agreement.
FIGURE 3. (A) Evaluation of the predicting accuracy of the SVM and (B) quantitative comparison between the SVM predicting results and experimental results.
Furthermore, according to the SVM fitness function, the genetic algorithm (GA) is used in this study to obtain the optimized processing parameters in the polishing process (Jeyaranjani and Devaraj, 2022), and it is found from the SVM-GA study that the optimized processing parameters in the lapping process are rp of 108 r/min, P of 33 N, Qa of 20 ml/min, and t of 3 min considered in this study, and the predicting value of Ra is 1.07 nm under this condition. The corresponding experiments have also been carried out to verify the accuracy of the SVM-GA method, and the surface morphology of the Q235 steel sample is shown in Figure 4, where the Ra is about 1 nm, so that it may be deduced that the SVM-GA method has been correctly developed for use to predict and optimize the polishing process.
FIGURE 4. Surface morphology of the Q235 steel sample after the lapping and polishing processes at rp = 108 r/min, P = 33 N, Qa = 20 ml/min, and t = 3 min.
To evaluate the lapping and polishing performance after the optimization of the processing parameters considered in this study, a set of nanoindentation tests have been conducted to measure the elastic modulus and hardness of the Q235 steel samples. The elastic modulus test results are shown in Figure 5. Indentation points 1 and 2 are taken from the Q235 steel sample without the optimization of the lapping and polishing parameters, and the remaining points are taken from the same work piece after the optimization of processing parameters. It can be seen from Figure 5 that with the increase of depth from the target surface, the elastic modulus gradually reduces to be stable. To be specific, the decreasing trend of the elastic modulus from points 1 and 2 is lower than other test points, and the overall values of the elastic modulus from points 1 and 2 are larger than other test points. It indicates that although the surface hardening phenomenon of the work piece could not be eliminated by the lapping and polishing processes, this surface hardening phenomenon could be improved by the optimization of the processing parameters to control the surface integrity (Qi et al., 2018).
In addition, Figure 6 shows the comparison of the hardness test results before and after the optimization of the lapping and polishing parameters. Nine different points are selected for each sample, and it can be seen from Figure 6A that the curves of hardness are relatively scattered without the optimization of the lapping and polishing parameters, which indicates that the differences in the nine curves of hardness are mainly caused by the non-uniform surface integrity. It is noticed from Figure 6B that the nine curves of hardness are similar after the optimization of the processing parameters, and the errors between each curve are small which demonstrates that the surface integrity has been significantly improved after the optimization of the lapping and polishing parameters by using the SVM-GA method considered in this study.
FIGURE 6. (A) Hardness test results without optimization and (B) hardness test results after optimization.
The nanoindentation test is extensively used to obtain the mechanics performance of different kinds of materials, and to accurately measure these values of mechanics, the sample is required to have good surface integrity in terms of surface roughness and subsurface damage. The abrasive lapping and polishing processes are often used to prepare the sample for nanoindentation with a good surface finish; however, many processing parameters are related to the lapping and polishing processes. It is necessary to optimize these parameters to perform good machining ability with high efficiency and accuracy. In this study, the general process in lapping and polishing of steel samples for nanoindentation has been analyzed, and an in-house developed automatic lapping and polishing machine has been used to conduct the lapping and polishing tests on Q235 steel samples by considering the major processing parameters, including the pressure, rotation speed of the lapping and polishing plate, flow rate of abrasive slurry, and processing time. It is found from the lapping experiments with a full factorial design that the optimized processing parameters are rp of 200 r/min, P of 30 N, and t of 4 min considered in this study by considering the MRR and SSD. The CCD method has been used to design the polishing experiments, and the SVM method has been used to deal with these experimental results, and it is found that the developed SVM model can accurately predict Ra under the different processing parameters considered in this study. Then, based on the SVM model, the GA method is used to obtain the optimized processing parameters in the polishing process, and it is found from the SVM-GA study that the optimized processing parameters in the lapping process are rp of 108 r/min, P of 33 N, Qa of 20 ml/min, and t of 3 min. Finally, a set of nanoindentation tests have been conducted to evaluate the lapping and polishing performance, and it is found that the surface integrity has been significantly improved after the optimization of the lapping and polishing parameters by using the SVM-GA method considered in this study.
The raw data supporting the conclusion of this article will be made available by the authors, without undue reservation.
Conceptualization, DW; data curation, QW; formal analysis, ZC; investigation, ZC; software, QW; supervision, DW; writing—original draft, ZC; writing—reviewing and editing, DW.
This research was funded by the National Natural Science Foundation of China (Grant number 51775509) and the Zhejiang Provincial Natural Science Foundation (Grant number LZ17E050003).
The authors declare that the research was conducted in the absence of any commercial or financial relationships that could be construed as a potential conflict of interest.
All claims expressed in this article are solely those of the authors and do not necessarily represent those of their affiliated organizations, or those of the publisher, the editors, and the reviewers. Any product that may be evaluated in this article, or claim that may be made by its manufacturer, is not guaranteed or endorsed by the publisher.
Chen, Z., Wang, X., Giuliani, F., and Atkinson, A. (2014). Surface Quality Improvement of Porous Thin Films Suitable for Nanoindentation. Ceramics Int. 40, 3913–3923. doi:10.1016/j.ceramint.2013.08.035
Chen, Z., Wen, D., Lu, J., Yang, J., Hong, T., and Qi, H. (2021). Surface Quality Improvement by Using a Novel Driving System Design in Single-Side Planetary Abrasive Lapping. Materials 14, 1691. doi:10.3390/ma14071691
Cheng, Z., Qin, S., and Fang, Z. (2022). Numerical Modeling and Experimental Study on the Material Removal Process Using Ultrasonic Vibration-Assisted Abrasive Water Jet. Front. Mater. Accepted Publ. 9, 895271. doi:10.3389/fmats.2022.895271
Das, A., Altstadt, E., Kaden, C., Kapoor, G., Akhmadaliev, S., and Bergner, F. (2022). Nanoindentation Response of Ion-Irradiated Fe, Fe-Cr Alloys and Ferritic-Martensitic Steel Eurofer 97: The Effect of Ion Energy. Front. Mater. 8, 811851. doi:10.3389/fmats.2021.811851
Fayed, H. A., and Atiya, A. F. (2021). Decision Boundary Clustering for Efficient Local SVM. Appl. Soft Comput. 110, 107628. doi:10.1016/j.asoc.2021.107628
Ge, J. Q., Ren, Y. L., Xu, X. S., Li, C., Li, Z. A., and Xiang, W. F. (2021b). Numerical and Experimental Study on the Ultrasonic-Assisted Soft Abrasive Flow Polishing Characteristics. Int. J. Adv. Manuf Technol. 112, 3215–3233. doi:10.1007/s00170-021-06598-2
Ge, J., Hu, W., Xi, Y., Ren, Y., Xu, X., and Zhang, C. (2021a). Gas-liquid-solid Swirling Flow Polishing and Bubble Collapse Impact Characteristics. Powder Tech. 390, 315–329. doi:10.1016/j.powtec.2021.05.087
Hossain, M., Qin, B., Li, B., and Duan, X. (2022). Synthesis, Characterization, Properties and Applications of Two-Dimensional Magnetic Materials. Nano Today 42, 101338. doi:10.1016/j.nantod.2021.101338
Hu, W., Teng, Q., Hong, T., Saetang, V., and Qi, H. (2022). Stress Field Modeling of Single-Abrasive Scratching of BK7 Glass for Surface Integrity Evaluation. Ceramics Int. 48, 12819–12828. doi:10.1016/j.ceramint.2022.01.153
Imanian, M. E., and Biglari, F. R. (2022). Modeling and Prediction of Surface Roughness and Dimensional Accuracy in SLS 3D Printing of PVA/CB Composite Using the central Composite Design. J. Manufacturing Process. 75, 154–169. doi:10.1016/j.jmapro.2021.12.065
Isik, M., Gasanly, N. M., and Rustamov, F. A. (2022). Determination of Mechanical Properties of Bi12TiO20 Crystals by Nanoindentation. Mater. Sci. Semiconductor Process. 140, 106389. doi:10.1016/j.mssp.2021.106389
Jeyaranjani, J., and Devaraj, D. (2022). Improved Genetic Algorithm for Optimal Demand Response in Smart Grid. Sust. Comput. Inform. Syst. 35, 100710. doi:10.1016/j.suscom.2022.100710
Ji, R., Zhang, L., Zhang, L., Li, Y., Lu, S., and Fu, Y. (2022). Processing Method for Metallic Substrate Using the Liquid Metal Lapping-Polishing Plate. Front. Mater. Submitted for publication 9, 896346. doi:10.3389/fmats.2022.896346
Li, H. N., Yang, Y., Zhao, Y. J., Zhang, Z., Zhu, W., Wang, W., et al. (2019). On the Periodicity of Fixed-Abrasive Planetary Lapping Based on a Generic Model. J. Manufacturing Process. 44, 271–287. doi:10.1016/j.jmapro.2019.05.036
Liang, Y., Hu, S., Guo, W., and Tang, H. (2022). Abrasive Tool Wear Prediction Based on an Improved Hybrid Difference Grey Wolf Algorithm for Optimizing SVM. Measurement 187, 110247. doi:10.1016/j.measurement.2021.110247
Nayak, B., and Ramesh Babu, N. (2020). Influence of Tool and Workpiece Interface Temperature Rise on the Life of Ice Bonded Abrasive Polishing Tool. Wear 462-463, 203511. doi:10.1016/j.wear.2020.203511
Qi, H., Cheng, Z., Cai, D., Yin, L., Wang, Z., and Wen, D. (2018). Experimental Study on the Improvement of Surface Integrity of Tungsten Steel Using Acoustic Levitation Polishing. J. Mater. Process. Tech. 259, 361–367. doi:10.1016/j.jmatprotec.2018.04.043
Qi, H., Shi, L., Teng, Q., Hong, T., Tangwarodomnukun, V., Liu, G., et al. (2022). Subsurface Damage Evaluation in the Single Abrasive Scratching of BK7 Glass by Considering Coupling Effect of Strain Rate and Temperature. Ceramics Int. 48, 8661–8670. doi:10.1016/j.ceramint.2021.12.077
Reggente, M., Angeloni, L., Passeri, D., Chevallier, P., Turgeon, S., Mantovani, D., et al. (2020). Mechanical Characterization of Methanol Plasma Treated Fluorocarbon Ultrathin Films through Atomic Force Microscopy. Front. Mater. 6, 338. doi:10.3389/fmats.2019.00338
Song, Y., Pan, Z., Li, Y., Jin, W., Gao, Z., Wu, Z., et al. (2022). Nanoindentation Characterization on the Temperature-dependent Fracture Mechanism of Chinese 316H Austenitic Stainless Steel under Creep-Fatigue Interaction. Mater. Characterization 186, 111806. doi:10.1016/j.matchar.2022.111806
Strey, N. F., and Scandian, C. (2021). Abrasive Polishing Load Effect on Surface Roughness and Material Removal Rate of Al2O3, ZTA and SiC. Wear 477, 203787. doi:10.1016/j.wear.2021.203787
Wen, D., Qi, H., Ma, L., Lu, C., and Li, G. (2016). Kinematics and Trajectory Analysis of the Fixed Abrasive Lapping Process in Machining of Interdigitated Micro-channels on Bipolar Plates. Precision Eng. 44, 192–202. doi:10.1016/j.precisioneng.2015.12.005
Xie, Y., Gui, F. X., Wang, W. J., and Chien, C. F. (2021). A Two-Stage Multi-Population Genetic Algorithm with Heuristics for Workflow Scheduling in Heterogeneous Distributed Computing Environments. IEEE Trans. Cloud Comput., Accepted for publication. doi:10.1109/TCC.2021.3137881
Keywords: lapping and polishing process, processing parameter optimization, nanoindentation, SVM-GA, Q235 steel
Citation: Cheng Z, Wei Q and Wen D (2022) Optimization of Lapping and Polishing of Steel Samples for Nanoindentation Based on SVM-GA. Front. Mater. 9:896341. doi: 10.3389/fmats.2022.896341
Received: 14 March 2022; Accepted: 04 April 2022;
Published: 10 May 2022.
Edited by:
Guijian Xiao, Chongqing University, ChinaReviewed by:
Jimmy Yao, KGW Prestress Co. Ltd., AustraliaCopyright © 2022 Cheng, Wei and Wen. This is an open-access article distributed under the terms of the Creative Commons Attribution License (CC BY). The use, distribution or reproduction in other forums is permitted, provided the original author(s) and the copyright owner(s) are credited and that the original publication in this journal is cited, in accordance with accepted academic practice. No use, distribution or reproduction is permitted which does not comply with these terms.
*Correspondence: Donghui Wen, d2VuZG9uZ2h1aTAzQHRzaW5naHVhLm9yZy5jbg==
Disclaimer: All claims expressed in this article are solely those of the authors and do not necessarily represent those of their affiliated organizations, or those of the publisher, the editors and the reviewers. Any product that may be evaluated in this article or claim that may be made by its manufacturer is not guaranteed or endorsed by the publisher.
Research integrity at Frontiers
Learn more about the work of our research integrity team to safeguard the quality of each article we publish.