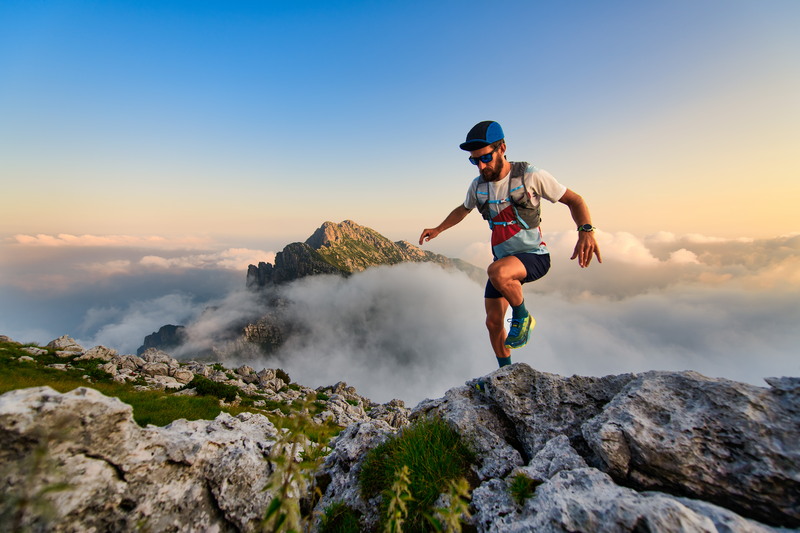
95% of researchers rate our articles as excellent or good
Learn more about the work of our research integrity team to safeguard the quality of each article we publish.
Find out more
ORIGINAL RESEARCH article
Front. Mater. , 11 May 2022
Sec. Mechanics of Materials
Volume 9 - 2022 | https://doi.org/10.3389/fmats.2022.891011
This article is part of the Research Topic High entropy alloy design concept enabled emerging novel materials with enhanced mechanical properties View all 7 articles
This study investigated the effect of potential change on the microstructure and corrosion properties of CoCrFeMnNi HEA coatings synthesized by the electrochemical deposition method. The films were precipitated in an electrolyte based on a DMF-CH3CN organic system comprising Co, Cr, Fe, Mn, and Ni cations. GIXRD pattern in all samples showed a single face-centered-cubic structure. SEM-EDS results show that the coating morphology and the elements value in alloy composition vary at different coating potentials. Coatings were uniform and crack-free surfaces. The results of the wettability test showed all coatings were super-hydrophilic. All the alloys exhibited similar passivation and negative hysteresis processes in the CPP test. However, the 5 V sample exhibited a lower Epit value than the 6 V, and none of the samples were sensitive to pitting corrosion. The CPP test result showed that the corrosion current density of the 5 V sample was 0.0525 μA/cm2, the minimum corrosion rate for the coated samples, and has improved the corrosion resistance of the substrate by about 44 times. The EIS test results showed the excellent performance of the coatings in enhancing the corrosion resistance compared to Cu substrate and similar alloy samples in a 3.5 wt% NaCl solution, as the protection efficiency was about 90%. These High entropy alloy coatings are suitable for engineering applications in which higher corrosion protection is needed.
The production of traditional alloys has been based on selecting one or two major elements. To improve their properties, the addition of different other alloying elements in small quantities, families of alloys were produced based on the critical element. With increasing the number and concentration of alloying elements, the alloying system composes more unstable phases and intermetallics (Tsai and Yeh, 2014), limiting the design concept of alloying systems (Ye et al., 2017). In recent years, a new concept of alloys called High Entropy Alloys (HEA) has been introduced as alloys with 5–13 main elements; each element must have a concentration of about 5–35 atomic percent in this group. HEAs can also contain alloying elements in amounts less than five atomic percent. In these alloys, because of the higher mixing entropy they have, the probability of forming intermetallic compounds is reduced compared to conventional ones. In contrast, the stability of the solid solution would be available. Nevertheless, Only a few HEAs can form a mono-phase solid solution structure (Tsai and Yeh, 2014; Ye et al., 2017; Murty et al., 2019). Also, “cocktail effects” have been differentiated the properties of HEAs from their constituent elements due to the components’ interaction (Meghwal et al., 2021). HEAs have shown the unique potential for applications in different environments due to their attractive properties.
The high mixing entropy in these alloys makes them have higher corrosion resistance, mechanical, thermal, and magnetic properties than conventional alloys. Significant and stable corrosion properties in HEAs are one of the major results of their chemical and structural composition homogeneity. Many authors have studied the corrosion resistance of HEAs over the last decade. Achieving optimal properties and investigating the corrosion behavior of cavities while producing with low-cost and available methods still needs further investigation. Studies have shown that different coating potentials affect the alloy composition and morphology; the content of each element may also affect the structure and morphology of the alloy and produce significant electrochemical properties. Because of the pivotal role of corrosion resistance and its improvement in stabilizing future engineering applications of HEA, the study of the interaction of corrosion properties, morphology, and alloy composition is considered in this article (Aliyu and Srivastava, 2022; Nascimento et al., 2022).
A significant focus of the HEA community has been to tune and exploit the above properties by various synthesis routes to manufacture alloys with desirable properties. However, most existing published studies have been done on bulk materials. Although using them as a coating material will enhance its application fields, distinguish damage tolerance, and reduce the cost (Meghwal et al., 2021).
Electrochemical deposition techniques are unique approaches to fabricating HEA coating with the following advantages: creating thin and uniform films on conductive and non-conductive substrates, production of nanostructured materials, good adhesion to the substrate, low process temperature, no need for special equipment, and environment-friendly process (Landolt, 2002; Gamburg and Zangari, 2011; Brenner, 2013).
Due to their attractive surface protection ability, the HEA-based coatings have been electrodeposited on different substrates, such as Cu, St. Q235, and St. 304. The research results on the corrosion behavior of high entropy alloys CoCrFeMnNi have shown significant improvements in resistance properties to various corrosive environments (Soare et al., 2015; Zhang et al., 2016; Shang et al., 2017; Popescu et al., 2021; Yoosefan et al., 2021). Using the electrodeposition process to produce HEA coatings is a simple, inexpensive, and affordable choice for synthesizing compact and crack-free coatings with good corrosion resistance behavior. Development of deposition bath chemistry and operational parameters are needed. In this study, CoCrFeMnNi high entropy alloy coatings were deposited on a Cu substrate by the electrochemical deposition method in chloride baths using DMF-CH3CN solvent. The purpose is to investigate the relationship between coating morphology, phase structure, corrosion properties in 3.5 wt% NaCl solution, and the effect of changes in the coating potential on those.
In this study, the copper (99.98% purity) disks with 10 mm diameter and 0.4 mm thickness were used as substrates. The substrate surfaces were mechanically polished with abrasive emery papers of 120–2,400 granulations. After that, the samples were cleaned ultrasonically in C2H5OH for 15 min. In the following, electro-polishing of each sample was performed at −50 mA/cm2 for 6 min in a solution containing H3PO4 (70%), double distilled water (30%), and +1% PEG. At last, the coatings were rinsed with double distilled water and immediately placed in the electrodeposition bath.
The electrodeposition and electrochemical studies were conducted at 298 K via a DC Power Supply generator model HEP35 Extra. The plating bath (in a 100 ml beaker) based on a DMF–CH3CN (with a 4:1 volume fraction) organic system, containing 0.01 mol/L FeCl2, 0.013 mol/L CrCl3, 0.0103 mol/L MnCl2, 0.001 mol/L NiCl2, 0.01 mol/L CoCl2, and LiClO4 as supporting electrolyte [similar to the solution composition in the previous study (Yoosefan et al., 2020)]. The Cu substrate (cathode) and the platinum electrode (anode) were placed vertically in the beaker, in front of each other at a 1 cm distance.
To choose the deposition potential of elements, cyclic voltammograms (C-V) of Cu electrodes in the exact solutions and ion concentration were performed at a 100 mV/s sweep rate. From the C-V graph (Supplementary Figure S1), There are four reduction peaks (decreases) at 1) −0.8 V, 2) −1.37 V, and 3) −2.59 V, which correspond to the reduction of 1) Cr (III), 2) Fe (II) and Ni (II) and 3) Co (II), and Mn (II) respectively. Three potentials of 4, 5, and 6 V were selected to synthesize the HEA coatings because of the uniformity and adhesion.
Coating time for all the samples was considered 1 hr., and three potentials of 4, 5, and 6 V were selected as process variables. Soon after the deposition, the surface of the coating was washed twice with double distilled water to remove residual chlorides from the plating bath. The electrodeposition potential for each sample is used as the coating code.
Surface morphology and chemical composition of the high entropy alloy thin films were evaluated via a Philips-XL30 scanning electron microscope (SEM) equipped with a SeronAIS2300C energy dispersive X-ray spectrometer (EDS). The crystal structure of the samples was characterized via grazing incidence X-ray diffractometry (GIXRD) and an Asenware AW-DX300 X-ray diffractometer (Cu anode, 40 kV, 30 mA, Step Time: 1 s, Step size: 0.05). The obtained data were processed via the X’Pert High Score Plus software. The Nelson–Riley function (Yeh et al., 2004; Nelson and Riley, 1945) was used to calculate the lattice parameters and the lattice strain. The crystallite size was computed using the width of the (111) peak at their half-height through Scherrer’s equation (Otte, 1961; Holzwarth and Gibson, 2011).
To investigate the formation of the simple structure of face-centered cubic (FCC) or body-centered cubic (BCC) as a solid solution in deposited alloys, according to Eq. 1, the mixing entropy for each coating is calculated and reported in Supplementary Table S1.
Equation 1:
Where R (= 8.314 J/Kmol) is the molar gas constant, and Ci is the molar content of component i.
A goniometer equipped with a CCD camera and an optical system was used to measure the contact angle between the thin film surface and water drop. This method placed 0.004 ml of a water drop (distilled water with conductivity less than 1 μs) on the coating surface (3 times for each sample). The images were recorded digitally through a CCD camera. Eventually, the mean contact angles were measured using the ImageJ software.
The corrosion behavior of the thin films was evaluated in 100 ml of a solution containing 3.5 wt% NaCl, open-air, at 25°C temperature. A three-electrode cell with a saturated calomel electrode (SCE) as the reference, a platinum sheet as the counter, and the studied coating as the working electrode were used. A Princeton Applied Research model PARSTAT 2273A was used to investigate corrosion behaviors. In each turn of the electrochemical analysis, the open-circuit potential (OCP), electrochemical impedance spectroscopy (EIS), linear polarization resistance (LPR), and cyclic potentiodynamic polarization (CPP) tests were recorded sequentially. At first, each sample was immersed in the prepared solution for 15 min to reach a static condition, while the OCP was recorded. The LPR tests were carried out between ±20 mV vs. OCP with a scan rate of 0.16 mV/s. The EIS tests were performed at a frequency range of 100 kHz to 25 mHz sine signals with an amplitude of 5 mV. For the potentiodynamic polarization tests, the electrode’s potential was made at a 1 mV/s scan rate in the potential range of -0.4–0.5 V vs. SCE. The potentiodynamic polarization and impedance data were modeled using Corr-View version 3.1c and Z-View version 3.1, respectively.
The icorr was calculated via extrapolation of the potentiodynamic polarization curves using the Tafel method by the Stern–Geary Eq. 2 (Stern and Geary, 1957; Gerengi et al., 2013):
Equation 2:
The Rp values were calculated using Eq. 3.
Equation 3:
Where B is calculated via the Tafel slopes Eq. 4.
Equation 4:
The ba and bc are the anodic and cathodic Tafel slopes, respectively. B is the proportionality constant (ba = bc = 120 mV/dec) and is 0.026 V for a particular system (Akid and Mills, 2001).
The CoCrFeMnNi high entropy alloy coatings composition evaluated by EDS is presented in Supplementary Table S1. The presence of all five elements in the coating composition prove that the alloy coating has been successfully synthesized. Supplementary Figure S3A shows the changes in the chemical composition of the coating with increasing in the applied potential. It can be seen that, for all the elements except Mn, the element’s content did not follow a specific trend by changing the potential. It is observed that the amount of deposited Mn has increased with increasing potential. In a study by Loukil et al., it was observed that the deposited Mn content in the coating had been raised by the coating potential (Loukil and Feki, 2017). In studies conducted by Lee, Soare, and Yao, it was also observed that by changing the applied potential between 1 and 3 V, the chemical composition of Co, Cr, Fe and Ni did not follow a significant change (Yao et al., 2008; Soare et al., 2015; Li et al., 2017).
The results of studies have shown that changes in applied potential differences lead to changes in the morphology, phase composition, and thickness of thin film (Kozlovskiy and Zdorovets, 2019; Omarova and Kadyrzhanov, 2019). As can be seen from the data presented in this study, increasing the difference in applied potentials (4–6 V) leads to changes in the film’s element concentration and morphology (section 3.1.3), especially in the 5 V sample. This change occurs due to overvoltage during the synthesis process, but no significant relationship was observed between these changes. Besides the effect of applied potential differences, changes in chemical composition can also affect the morphology of the final coating.
The change in the elements amount in the chemical composition of coatings, especially in Fe and Co, is because of differences in the reduction potential of the elements. This change in the 5 V sample is out of linear mode for all elements (except Mn). Kadyrzhanov (Kadyrzhanov et al., 2020) showed that Co recovery from the electrolyte solution occurs slowly at low potential differences, while Zn reduces much faster. However, increasing the potential difference because of the dominance of Co reduction potential over Zn reduction potential leads to an increase in Co content.
Whiles the amount of Mn, Cr, and Ni did not change significantly in the potential change from 4 to 6 V, the Co reduction occurred faster than other elements, but with increasing potential up to 6 V (increasing potential difference), Co reduction decreased. The reduction of Fe at the potential of 5 V was the lowest value compared to the potentials of 4 and 6 V.
Due to the low thickness of the coatings, peaks of the Cu (substrate metal) are observed in the EDS results (Supplementary Figure S3B). According to the Cu content in the EDS analysis results, it can be concluded that the thickness of the applied coatings increases in the potential of 4 V (8.32 at.% Cu), 6 V (3.64 at.% Cu), and 5 V (1.89 at.% Cu) for 1 hr., respectively.
The GIXRD patterns of the coatings on the Cu substrates were examined within a range of 2θ = 10°–80° and are presented in Supplementary Figure S4. No diffraction peaks can be found for the coatings, except those relating to the simple FCC solid solution structure. After identifying the phase present in samples by X’Pert High Score Plus software, the lattice constant (a) and lattice strain (ε) were calculated via Bragg’s law.
It can be seen that the 6 V sample has the highest peak intensity and the 4 and 5 V samples have almost equal peak intensity. The increase in peak intensity in these samples could be attributed to the increase in order and arrangement of grains and change in coating conditions. According to the reported values of the elements in different coating conditions (Supplementary Table S1), it is observed that the 6 V sample with the highest peak intensity among the other samples had lower amounts of Cr and Mn (larger atomic radius) and had more elevated amounts of Ni and Co (smaller atomic radius); Therefore, it can be concluded that the sample crystal lattice is more compact than the rest. Also, for lightweight elements, the peak intensity is reduced; as can be seen, in the sample with higher peak intensities, heavier element amounts (Ni and Co) were higher, and lighter element levels (Cr and Mn) were less. The results of Rini’s research also showed that the intensity of the diffraction pattern is affected by the cation’s ionic radius. However, the change in the peaks intensity is not uniformly related to the ion radius due to the factors affecting the X-ray scattering in the crystals (Rini, 2019).
The crystallite size of the alloys was calculated through Scherrer’s equation and is reported in Supplementary Table S1. The absence of complex, ordered, and intermetallic phases can be attributed to the lower free energy (∆G) relating to the effect of the mixing high entropy (∆S). According to the literature (Tsai and Yeh, 2014), the high entropy of mixing can reduce the free energy remarkably and make a random solid solution more stable than the ordered phases.
Supplementary Figure S5 represents surface morphologies of the CoCrFeMnNi high entropy alloy coatings produced after 1 hr. electrochemical deposition in different potentials of 4, 5, and 6 V.
As shown in Supplementary Figure S5A, the coated samples at a potential of 4 V have a surface without cracks and any specific morphology, the crystallite size of which has been calculated according to the results of GIXRD analysis at about 121 nm. Some hydrogen blisters are observed on the surface of the coating, which can be due to the low overvoltage at this potential and the production of H2 after the decomposition of chromium hydrides (CrHx) (Adelkhani and Arshadi, 2009). According to the results of EDS analysis, it is observed that the coating created in this potential has a minimum amount of Mn compared to other samples. Because of the large atomic radius of the Mn, which leads to internal stresses in the coating and cracking; therefore, justified the absence of cracks in this coating compared to other samples. In addition, in the BSE image of the sample surface, it can be seen that even at low thickness, the coating completely covers the substrate surface.
Supplementary Figure S5B shows the morphology of the coated samples at the potential of 5 V. As can be seen; the coating has an uneven surface. There are blisters on the coating surface, and in some places, the effects of blister bursting are also observed. The surface comprises several cracks, which in some parts of the cracks are branched with greater width and depth. According to the results of the GIXRD analysis, the crystallite size was calculated to be about 143 nm. According to EDS results, this coating contains the maximum amount of Co and Cr and the minimum amount of Fe and Ni compared to other samples; therefore, cracks on the coating surface can be attributed to low amounts of Ni and high quantities of Co.
As shown in Supplementary Figure S5C, the coating created at a potential of 6 V is a crack-free coating in which the effects of small hydrogen bubbles are observed. According to the results of GIXRD analysis, the crystallite size of the sample was calculated to be about 119 nm. The results of EDS analysis showed that, in this coating, there is a minimum amount of Cr and Co and a maximum amount of Mn and Ni; According to the amounts of Co and Ni can be justified without cracking the coating.
For the morphological study, besides the amount of each element, it is necessary to consider the effect of the element’s presence along with each other. According to the literature, in the 6 V sample, the maximum amount of Ni (prevents crack formation) and the minimum amount of Co (crack formation factor) prevail over the higher amount of manganese than the 4 V sample (crack formation factor). Whereas in the 4 V sample, besides the amount of Ni and Co elements close to the 6 V composition, the minimum amount of manganese was also influential in forming a crack-free morphology.
In the present study, it is observed that the coating structure in the two samples coated using 4 and 6 V potentials is smooth and has a spherical and prominent morphology on the surface. In the samples coated using 5 V potential, the surface is uneven and has deep cracks and multiple porosities. In a study by Chung et al., it was observed that with increasing the potential, due to increasing the applied current density and sedimentation rate, a more uneven surface is created (Chung and Chang, 2009; Tsai and Chung, 2014).
Loukil et al. researched ZnMn electrodeposited coatings, and it was observed that increasing the current density from 60 to 140 mA/cm2 increased the crystallite size (Loukil and Feki, 2017). In the present study, according to Supplementary Table S1, it is observed that with increasing the coating potential from 4 to 6 V, the crystallite size has increased. However, at the potential of 5 V, the largest crystallite size has been reported, which can be considered due to the highest amount of Cr (low atomic mobility due to large atomic radius) and the lowest amount of Ni (high atomic mobility due to small atomic radius).
The work of corrosion resistance is related to the wettability of coatings. For this purpose, the contact angle of water droplets with the surface was used as a criterion for checking the wettability of the coating.
As shown in Supplementary Figure S6, in all three coatings, the water droplet completely spreads over the surface. In constant potential coated samples, it is observed that in 4 and 6 V samples where the coating surface was smooth and fully compacted, the wetting angle is less than 5 V sample; where the coating surface is uneven, and it has porosity and cracks. 4 and 6 V samples with a smaller contact angle and having a rough surface compared to others, have a surface close to super-hydrophilic models.
Published articles have shown that the chemical composition of coatings affects the contact angle. Mani et al.’s research showed that higher contact angles in coatings were attributed to low electronegativity elements such as Cr compared to the high electronegative element (Mani et al., 2022). In the 5 V sample, the most cobalt content (the higher electronegativity) can be considered an influential factor in the coating’s wettability. However, due to elements with close electronegativity in this alloy, the effect of electronegativity on wettability does not follow a specific trend.
To investigate the corrosion-resistant behavior of coatings, Linear Polarization, Electrochemical Impedance Spectroscopy, and Cyclic Potentiodynamic Polarization were performed on the coatings. The 4 V sample did not stabilize even after 40 min due to the high resistance of the coating; therefore, no corrosion test was performed on it.
The OCP diagram is shown in Supplementary Figure S7A. The OCP goes through a minimum before a positive increase to -0.3 V within the first 500–900 s. Afterward, the potential stabilizes at this value for the immersion period. In contrast, the 5 V sample positively changed the whole experiment.
Supplementary Figure S7B shows LP curves of coatings. The intersection point and slope were obtained from the LP resistance graphs, which determine Ecorr and Rp values, respectively. The icorr can be calculated using Eq. 3 to determine charge transfer control reaction kinetics in slight corrosion potential deflection (Popova and Christov, 2006; Gerengi et al., 2013). The Rp, icorr, and Ecorr values calculated from LP measurement results are also listed in Supplementary Table S2. The value of B was calculated as 19.37 for the 5 V sample and 41.58 for the 6 V sample.
By comparing the Rp estimated from the LP diagrams with the Rcoat from the EIS results (section 3.2.2), the Rp values are much higher than the Rcoat values; however, the Rp of the 6 V sample is higher than the 5 V sample.
The comparison of this study’s results with similar alloy samples showed that despite the high corrosion potential of the coatings in this study, they have relatively good corrosion resistance; the results of several studies are presented in Supplementary Table S4.
The impedance of the coatings was evaluated after OCP monitoring. The Nyquist plots of the coatings are shown in Supplementary Figure S7C. Considering the single semi-circle shape of the Nyquist curve, the electrical equivalent circuit (EC) model employed to fit the experimental data of the substrate and the coated samples are Rs(RpCdl) and Rs(Ccoat(Rcoat(RpCdl))), respectively. The substrate EC model consists of an uncompensated solution resistance (Rs) in series with the oxide layer capacitance (Cdl) in parallel with a polarization resistance (Rp) accounting for the non-ideal double-layer capacitance. The coatings EC model is comprising the capacitance of the coating (Ccoat), a charge transfer resistance of the coatings (Rcoat), a Cdl, and Rp. Data obtained via the best fitting procedure (using ZView software) are listed in Supplementary Table S3.
The data are presented in Supplementary Figure S8 to clarify the electrochemical impedance parameters changes.
The result of the electrochemical impedance test and the values of the Φ and |Z| parameters are presented in Supplementary Table S3 (from Bode and Bode-phase plots in 0.025 Hz frequency). According to the data, the coating polarization resistance increases compared to the Cu substrate.
It can be seen that the 6 V sample has higher corrosion resistance than the 5 V sample despite its larger CP. The 5 V sample had a higher RP than the 6 V sample with less Cdl. The |Z| values show a higher resistance of the 5 V sample than the 6 V.
The comparison of this study’s results with similar alloy samples showed that despite the high capacity of the coatings in this study, they have relatively good corrosion resistance; the results of several studies are presented in Supplementary Table S4. The capacitance of the double-layer in these HEA coatings is less than similar samples, leading to good polarization resistance in these samples. Another noteworthy point is that, contrary to expectations, these coatings have good corrosion resistance despite being super-hydrophilic.
The PP curves of the coatings and the Cu substrate are plotted in Supplementary Figure S9A. The kinetic parameters were calculated using the Tafel extrapolation fit method. The curves showed considerably more corrosion-resistant behavior in the coatings than in the substrate. All PP curves of samples showed an aptitude for being a “spontaneously passive” layer (Qiu et al., 2015).
The PP test parameters (corrosion current (icorr), corrosion potential (Ecorr), cathodic (bc), and anodic (ba) slopes) and the corrosion protection efficiency are computed and listed in Supplementary Table S5. The corrosion protection efficiency gained from electrochemical polarization measurements through
The Ecorr and icorr of coatings are significantly less than Cu substrate. According to the polarization curves, it can be seen that the coated sample with a potential of 6 V has a higher corrosion current density than the sample with 5 V, and the potential of these samples has also tended towards more positive values. So the 5 V sample has the best corrosion protection performance. As can be seen, the slope of the anodic curve of the 6 V sample (168.406 mv/dec) is higher than the 5 V sample, which shows the more appropriate anodic behavior of these coatings.
Also, as the potential increases (above Ecorr), the PP diagrams show a narrow window of passivity. These HEA coatings offer good pitting corrosion-resistance behavior, with the passive layer having a high resistance to Cl− ion attack. The attack of Cl− ions on the passive film and the replacement of the O element has led to cavities in the passive films and, as a result, causes corrosion (Poornima et al., 2010; Ye et al., 2017).
According to the PP curves, the corrosion density in the 5 V sample had the most significant decrease compared to the substrate; Corrosion potential has also been transferred to more positive values, which show an increase in the corrosion resistance of the 5 V sample. The corrosion protection efficiency of the 5 V sample is 97.71%.
A comparison between the results of the PP test of these samples with other HEA coatings is presented in Supplementary Table S6. The icorr of sample 5 V is lower than other samples, showing better corrosion resistance. The Ecorr of all samples is more positive than the samples of this study. Therefore, according to the results, sample 5 V was selected as the optimal condition in the coating process for corrosion resistance applications.
Supplementary Figure S9B shows the cyclic potentiodynamic polarization curves to investigate the pitting corrosion behavior. The first cycle (forward) is shown by a black arrow, and the second cycle (backward) is shown with a red arrow. The CPP curve shows a negative hysteresis loop, which means the resistance of the alloy (in all samples) to pitting corrosion. This behavior can be attributed to the uniform composition of the entire coating and its chemical stability. The re-passivation potential (Erp) increases as the coating potential increases.
When Epit > Erp > Ecorr, the coating is resistant to pitting corrosion (Almarshad and Jamal, 2004). According to the second peak of the diagrams, the 5 and 6 V samples are not sensitive to pitting corrosion and have high corrosion resistance.
By comparison of icorr estimated from the LP and CPP diagrams, it can be seen that the values of icorr obtained from the LP diagrams for the 6 V sample correspond to the results of the CPP diagram. Still, the icorr of 5 V sample, from LP, it is higher than the values estimated from the CPP results. However, the icorr value of the 5 V sample is less than that of the 6 V sample, so it has higher corrosion resistance.
For a more detailed study, the 5 and 6 V samples were compared with several similar HEA samples (Supplementary Table S6); the results showed that pitting corrosion occurred in other samples, and the samples were sensitive to pitting.
The corrosion resistance of multi-component alloys depends mainly on microstructural homogeneity and uniform distribution of alloying elements through the grain boundary and crystalline phases. The stability of passive film plays a significant role. The unique point is the suitably combines of alloying elements such as Co and Cr, effectively increasing the corrosion resistance. The studies on HEAs have shown that the Ni content has no linear effect on corrosion resistance. In the 5 V sample, with fewer Ni (support passivation element), the corrosion rate compared to the 6 V sample showed more corrosion resistance. Besides forming Cr2O3 as the main passivation element, Cr increases the surface chemical stability and the protective effect of Fe2O3, NiO, and CoO in corrosion protection. In the 5 V sample, the Cr amount had a more positive effect on protecting the alloy against corrosion than in the 6 V sample. The effect of Co content (as the support passivation element) on the stability of its passive layer and the stability of the Cr2O3 layer has been studied. Mn acts as a destructive agent in reducing the protection of Cr and Ni oxides (causing sensitivity to pitting corrosion) and increasing the probability of passive layer dissolution. The 5 V sample with less Mn content in the alloy composition showed higher corrosion resistance than the 6 V sample. Along with other elements, less Fe has increased the corrosion resistance in the 5 V sample compared to the 6 V sample (Shi et al., 2017; Nascimento et al., 2022). Besides the chemical composition, the uniform distribution of the elements (Supplementary Figure S3B) and the homogeneous microstructure of the alloy (Supplementary Figures 6–8) have led to significant corrosion resistance properties.
This study synthesized high-entropy CoCrFeMnNi alloy coatings by electrochemical deposition at 4, 5, and 6 V constant potentials. The SEM images showed that the created coating covered the substrate surface well, and a uniform surface was made. The morphology of the coating has been affected by different coating conditions. The results of the potentiodynamic polarization test showed that the corrosion rate of the 5 V sample is the lowest one. All coatings significantly improved the corrosion resistance of the substrate; in the best case, the 5 V sample improved the corrosion resistance of the Cu substrate by over 40 times and was selected as the optimal condition. Also, according to the corrosion curves, none of the samples were sensitive to pitting corrosion. The electrochemical impedance spectroscopy test showed an excellent performance of coatings to improve corrosion resistance compared to similar alloys, with a protection efficiency of over 80%. The results showed that the corrosion resistance of coatings depends on the microstructural and chemical homogeneity caused by the elements distribution of the coatings.
The original contributions presented in the study are included in the article/Supplementary Material, further inquiries can be directed to the corresponding author.
All authors listed have made a substantial, direct, and intellectual contribution to the work and approved it for publication.
The authors declare that the research was conducted in the absence of any commercial or financial relationships that could be construed as a potential conflict of interest.
All claims expressed in this article are solely those of the authors and do not necessarily represent those of their affiliated organizations, or those of the publisher, the editors and the reviewers. Any product that may be evaluated in this article, or claim that may be made by its manufacturer, is not guaranteed or endorsed by the publisher.
Thanks to Eng. Mahnoush Tajmir Riyahi, Lab technician of electronics engineering department for her help and guidance throughout the work.
The Supplementary Material for this article can be found online at: https://www.frontiersin.org/articles/10.3389/fmats.2022.891011/full#supplementary-material
Adelkhani, H., and Arshadi, M. R. (2009). Properties of Fe–Ni–Cr Alloy Coatings by Using Direct and Pulse Current Electrodeposition. J. Alloys Compd. 476 (No. 1–2), 234–237. doi:10.1016/j.jallcom.2008.09.108
Akid, R., and Mills, D. J. (2001). A Comparison between Conventional Macroscopic and Novel Microscopic Scanning Electrochemical Methods to Evaluate Galvanic Corrosion. Corros. Sci. 43 (No. 7), 1203–1216. doi:10.1016/s0010-938x(00)00091-3
Aliyu, A., and Srivastava, C. (2022). Phase Constitution, Surface Chemistry and Corrosion Behavior of Electrodeposited MnFeCoNiCu High Entropy Alloy-Graphene Oxide Composite Coatings. Surf. Coatings Technol. 429, 127943. doi:10.1016/j.surfcoat.2021.127943
Almarshad, A. I., and Jamal, D. (2004). Electrochemical Investigations of Pitting Corrosion Behaviour of Type UNS S31603 Stainless Steel in Thiosulfate-Chloride Environment. J. Appl. Electrochem. 34 (1), 67–70. doi:10.1023/b:jach.0000005579.84264.73
Brenner, A. (2013). Electrodeposition of Alloys: Principles and Practice. New York: Springer. doi:10.1007/978-1-4419-9669-5
Chung, C.-K., and Chang, W. T. (2009). Effect of Pulse Frequency and Current Density on Anomalous Composition and Nanomechanical Property of Electrodeposited Ni–Co Films. Thin Solid Films 517 (No. 17), 4800–4804. doi:10.1016/j.tsf.2009.03.087
Gamburg, Y. D., and Zangari, G. (2011). Theory and Practice of Metal Electrodeposition. New York: Academic Press.
Gerengi, H., Slepski, P., and Bereket, G. (2013). Dynamic Electrochemical Impedance Spectroscopy and Polarization Studies to Evaluate the Inhibition Effect of Benzotriazole on Copper‐Manganese‐Aluminium Alloy in Artificial Seawater. Mater. Corros. 64 (No. 11), 1024–1031. doi:10.1002/maco.201206565
Holzwarth, U., and Gibson, N. (2011). The Scherrer Equation versus the 'Debye-Scherrer Equation'. Nat. Nanotechnol. 6 (No. 9), 534. doi:10.1038/nnano.2011.145
Kadyrzhanov, K. K., Zikirina, A., Egizbek, K., Kozlovskiy, A. L., Petrov, A. V., and Zdorovets, M. V. (2020). Phase Transformations in CoZnO/CoZn Nanostructures Depending on the Difference in Applied Potentials. Surf. Coatings Technol. 386, 125495. doi:10.1016/j.surfcoat.2020.125495
Kozlovskiy, A. L., and Zdorovets, M. V. (2019). Synthesis, Structural, Strength and Corrosion Properties of Thin Films of the Type CuX (X= Bi, Mg, Ni). J. Mater. Sci. Mater. Electron. 30 (No. 12), 11819–11832. doi:10.1007/s10854-019-01556-x
Landolt, D. (2002). Electrodeposition Science and Technology in the Last Quarter of the Twentieth Century. J. Electrochem. Soc. 149 (No. 3), 2–3. doi:10.1149/1.1469028
Li, W.-J., Khan, U., Irfan, M., Javed, K., Liu, P., Ban, S. L., et al. (2017). Fabrication and Magnetic Investigations of Highly Uniform CoNiGa Alloy Nanowires. J. Magnetism Magnetic Mater. 432, 124–128. doi:10.1016/j.jmmm.2017.01.074
Loukil, N., and Feki, M. (2017). Zn–Mn Alloy Coatings From Acidic Chloride Bath: Effect Of Deposition Conditions on the Zn–Mn Electrodeposition-Morphological And Structural Characterization. Appl. Surf. Sci. 410, 574–584. doi:10.1016/j.apsusc.2017.02.075
Mani, S. P., Agilan, P., Kalaiarasan, M., Ravichandran, K., Rajendran, N., and Meng, Y. (2022). Effect of Multilayer CrN/CrAlN Coating on the Corrosion and Contact Resistance Behavior of 316L SS Bipolar Plate for High Temperature Proton Exchange Membrane Fuel Cell. J. Mater. Sci. Technol. 97, 134–146. doi:10.1016/j.jmst.2021.04.043
Meghwal, A., Anupam, A., Luzin, V., Schulz, C., Hall, C., Murty, B. S., et al. (2021). Multiscale Mechanical Performance and Corrosion Behaviour of Plasma Sprayed AlCoCrFeNi High-Entropy Alloy Coatings. J. Alloys Compd. 854, 157140. doi:10.1016/j.jallcom.2020.157140
Murty, B. S., Yeh, J. W., and Ranganathan, S. (2019). High-Entropy Alloys. Second Edition. Elsevier.
Nascimento, C. B., Donatus, U., Ríos, C. T., Oliveira, M. C. L., and Antunes, R. A. (2022). A Review on Corrosion of High Entropy Alloys: Exploring the Interplay between Corrosion Properties, Alloy Composition, Passive Film Stability and Materials Selection. Mater. Res. 25, 2022. doi:10.1590/1980-5373-MR-2021-0442
Nelson, J. B., and Riley, D. P. (1945). An Experimental Investigation of Extrapolation Methods in the Derivation of Accurate Unit-Cell Dimensions of Crystals. Proc. Phys. Soc. 57 (3), 160. doi:10.1088/0959-5309/57/3/302
Omarova, A., and Kadyrzhanov, K. K. (2019). “Study of the Effect of Potential Difference on the Phase Composition of Nanostructured Films Based on CdSe”. Interaction of Radiation with Solids, Proceedings of the 13th International Conference. Editorial board: V.V. Uglov [i dr.]. Minsk: Belarusian State University.
Otte, H. M. (1961). Lattice Parameter Determinations with an X‐Ray Spectrogoniometer by the Debye‐Scherrer Method and the Effect of Specimen Condition. J. Appl. Phys. 32 (8), 1536–1546. doi:10.1063/1.1728392
Poornima, T., Jagannatha, N., and Shetty, A. N. (2010). Studies on Corrosion of Annealed and Aged 18 Ni 250 Grade Maraging Steel in Sulphuric Acid Medium. Port. Electrochim. Acta 28 (3), 173–188. doi:10.4152/pea.201003173
Popescu, A.-M. J., Branzoi, F., Constantin, I., Anastasescu, M., Burada, M., Mitrică, D., et al. (2021). Electrodeposition, Characterization, and Corrosion Behavior of CoCrFeMnNi High-Entropy Alloy Thin Films. Coatings 11 (No. 11), 1367. doi:10.3390/coatings11111367
Popova, A., and Christov, M. (2006). Evaluation of Impedance Measurements on Mild Steel Corrosion in Acid Media in the Presence of Heterocyclic Compounds. Corros. Sci. 48 (No. 10), 3208–3221. doi:10.1016/j.corsci.2005.11.001
Qiu, Y., Gibson, M. A., Fraser, H. L., and Birbilis, N. (2015). Corrosion Characteristics of High Entropy Alloys. Mater. Sci. Technol. 31 (No. 10), 1235–1243. doi:10.1179/1743284715y.0000000026
Rini, A. S. (2019). Diffraction Pattern Simulation of Crystal Structure towards the Ionic Radius Changes via Vesta Program. J. Technomaterial Phys. 1 (No. 2), 132–139. doi:10.32734/jotp.v1i2.1288
Shang, C., Axinte, E., Ge, W., Zhang, Z., and Wang, Y. (2017). High-entropy Alloy Coatings with Excellent Mechanical, Corrosion Resistance and Magnetic Properties Prepared by Mechanical Alloying and Hot Pressing Sintering. Surfaces Interfaces 9, 36–43. doi:10.1016/j.surfin.2017.06.012
Shi, Y., Yang, B., and Liaw, P. K. (2017). Corrosion-resistant High-Entropy Alloys: a Review. Metals 743 (No. 2). doi:10.3390/met7020043
Soare, V., Burada, M., Constantin, I., Mitrică, D., Bădiliţă, V., Caragea, A., et al. (2015). Electrochemical Deposition and Microstructural Characterization of AlCrFeMnNi and AlCrCuFeMnNi High Entropy Alloy Thin Films. Appl. Surf. Sci. 358, 533–539. doi:10.1016/j.apsusc.2015.07.142
Stern, M., and Geary, A. L. (1957). Electrochemical Polarization: I. A Theoretical Analysis of the Shape of Polarization Curves. J. Electrochem. Soc. 104 (No. 1), 56. doi:10.1149/1.2428473
Tsai, M.-H., and Yeh, J.-W. (2014). High-Entropy Alloys: A Critical Review. Mater. Res. Lett. 2 (No. 3), 107–123. doi:10.1080/21663831.2014.912690
Tsai, W.-T., and Chung, S.-T. (2014). Electrodeposition of High Phosphorus Ni-P Alloys in Emulsified Supercritical CO2 Baths. J. Supercrit. Fluids 95, 292–297. doi:10.1016/j.supflu.2014.09.025
Yao, C.-Z., Zhang, P., Liu, M., Li, G.-R., Ye, J.-Q., Liu, P., et al. (2008). Electrochemical Preparation and Magnetic Study of Bi–fe–co–ni–mn High Entropy Alloy. Electrochimica Acta 53 (No. 28), 8359–8365. doi:10.1016/j.electacta.2008.06.036
Ye, Q., Feng, K., Li, Z., Lu, F., Li, R., Huang, J., et al. (2017). Microstructure and Corrosion Properties of CrMnFeCoNi High Entropy Alloy Coating. Appl. Surf. Sci. 396, 1420–1426. doi:10.1016/j.apsusc.2016.11.176
Yeh, J., Chen, S., Lin, S., Gan, J., Chin, T., Shun, T., et al. (2004). Nanostructured High-Entropy Alloys with Multiple Principal Elements: Novel Alloy Design Concepts and Outcomes. Adv. Eng. Mater. 6 (No. 5), 299–303. doi:10.1002/adem.200300567
Yoosefan, F., Ashrafi, A., and Monir vaghefi, S. M. (2021). Characterization of Co–cr–fe–mn–ni High-Entropy Alloy Thin Films Synthesized by Pulse Electrodeposition: Part 2: Effect of Pulse Electrodeposition Parameters on the Wettability and Corrosion Resistance. Metals Mater. Int. 27 (No. 1), 106–117. doi:10.1007/s12540-019-00584-w
Yoosefan, F., Ashrafi, A., Monir vaghefi, S. M., and Constantin, I. (2020). Synthesis of CoCrFeMnNi High Entropy Alloy Thin Films by Pulse Electrodeposition: Part 1: Effect of Pulse Electrodeposition Parameters. Metals Mater. Int. 26 (No. 8), 1262–1269. doi:10.1007/s12540-019-00404-1
Keywords: high-entropy alloy coating, electrochemical deposition, organic system, corrosion resistance, hydrophilic
Citation: Yoosefan F, Ashrafi A and Monir Vaghefi SM (2022) Microstructure and Corrosion Properties of Electrodeposited CoCrFeMnNi High Entropy Alloy Coatings. Front. Mater. 9:891011. doi: 10.3389/fmats.2022.891011
Received: 07 March 2022; Accepted: 08 April 2022;
Published: 11 May 2022.
Edited by:
Praveen Sathiyamoorthi, Indian Institute of Technology (BHU), IndiaCopyright © 2022 Yoosefan, Ashrafi and Monir Vaghefi. This is an open-access article distributed under the terms of the Creative Commons Attribution License (CC BY). The use, distribution or reproduction in other forums is permitted, provided the original author(s) and the copyright owner(s) are credited and that the original publication in this journal is cited, in accordance with accepted academic practice. No use, distribution or reproduction is permitted which does not comply with these terms.
*Correspondence: Ali Ashrafi, QXNocmFmaUBpdXQuYWMuaXI=
Disclaimer: All claims expressed in this article are solely those of the authors and do not necessarily represent those of their affiliated organizations, or those of the publisher, the editors and the reviewers. Any product that may be evaluated in this article or claim that may be made by its manufacturer is not guaranteed or endorsed by the publisher.
Research integrity at Frontiers
Learn more about the work of our research integrity team to safeguard the quality of each article we publish.