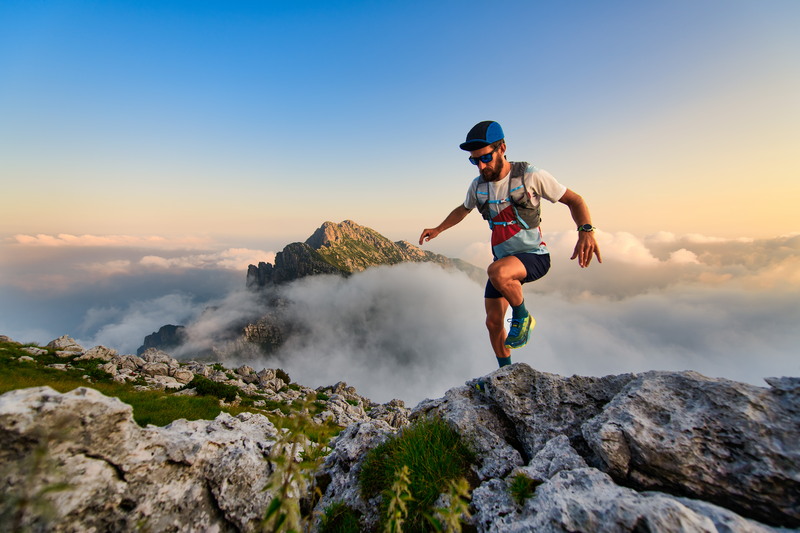
95% of researchers rate our articles as excellent or good
Learn more about the work of our research integrity team to safeguard the quality of each article we publish.
Find out more
ORIGINAL RESEARCH article
Front. Mater. , 08 April 2022
Sec. Polymeric and Composite Materials
Volume 9 - 2022 | https://doi.org/10.3389/fmats.2022.863731
This article is part of the Research Topic Advanced Technologies for Electrical Engineering View all 6 articles
Composite insulators are widely used in the external insulation of transmission lines due to their excellent pollution flashover resistance. However, the large amount of silicone rubber material is difficult to degrade naturally in decommissioned composite insulators resulting in great pressure on the environment. A method for recycling waste silicone rubber by microbial degradation was proposed. The insulator shed materials of composite insulators naturally retired under 10–15 years of operation are collected. Using dominant species to decompose silicone rubber, the decomposed product is obtained, and the chemical reaction process is deduced according to the three-dimensional structural characteristics of monomers. The biodegradation process does not require the participation of a strong acid and alkali, and the recovery method is safe and effective. At the same time, the nano-silicon dioxide is separated from the waste silicone rubber and modified by the surfactant. The particle size of nano-silica is reduced to ∼18 nm with an excellent dispersibility, indicating high economic value. It is demonstrated that microbial decomposition recycles polymeric materials with the ability to turn them into a valuable resource, which is a very-low-carbon green and environment-friendly method of recycling.
Composite insulators are widely used in the external insulation of power system transmission lines owing to their excellent pollution flashover resistance (Gou et al., 2021). The material of silicone rubber composite insulator shed sheath is high-temperature-vulcanized silicone rubber; high-temperature-vulcanized silicone rubber is an elastomer based on dimethylsiloxane, initiated by organic peroxide, mixed with reinforcing filler and vulcanizing agent and vulcanized under heat and pressure (Halim et al., 2022). The silicone rubber part of the insulator is directly exposed to the atmosphere; during operation, it is subject to the multi-factor interactive coupling effect of environmental factors such as temperature, pollution, humidity, irradiation, microorganisms, and electrical phenomena such as partial discharge and high field strength. Main chain depolymerization and side-chain oxidation occur after long-term use; macroscopically, there are different degrees of aging phenomena such as fading, cracking, chalking, hardening, and reduced hydrophobicity (Ullah et al., 2021).
Test research and operating experience show that, under normal design, manufacture, operation, and maintenance, the service life of composite insulator silicone rubber material is generally 15–20 years (Chen et al., 2021). Since the large-scale application of composite insulators in 1995, the composite insulators put into operation in the early stage have reached the service life and begun to retire in batches, and the number of retired composite insulators has increased year by year (Liu et al., 2019). In addition, up to now, more than 4 million insulators have been operating for more than 10 years and have entered the middle and late stages of their life (Cozzarini et al., 2020). Therefore, how to recycle the waste silicone rubber will become an inevitable problem.
Since silicone rubber is relatively stable and extremely difficult to decompose under natural conditions, it is necessary to first process the silicone rubber if you want to recycle it. At present, the recovery methods of waste high-temperature-vulcanized silicone rubber mainly include the physical crushing method, chemical depolymerization method, and fixed-value pyrolysis method (Wang and Liu, 2001). The physical crushing method is to embrittle the block or granular waste rubber at ultra-low temperature or normal temperature and then perform mechanical crushing (Th et al., 2021). Ultra-low-temperature pulverization can produce a fine powder with a particle size of 75–355 μm, but the production cost and operating cost are correspondingly high; the normal temperature pulverization method is simple in process and low in energy consumption, but the particle size of the obtained powder is larger, between 150–830 μm.
Chemical depolymerization methods are divided into acid-catalyzed and base-catalyzed methods (Oku et al., 2002). The acid-catalyzed method can depolymerize polydimethylsiloxane with a high degree of polymerization into a slurry at room temperature. The commonly used catalyst in China is sulfuric acid because sulfuric acid can dissolve siloxane and break the -Si-O-Si- bond at the same time. When sulfuric acid is used as a silicone rubber cracking catalyst, the catalytic activity decreases with the decrease in sulfuric acid concentration, but the high-concentration sulfuric acid causes serious corrosion of equipment and a high replacement rate. At the same time, there is a large amount of acidic waste liquid in the acid catalytic cracking method, which will lead to secondary pollution problems and increase the cost of comprehensive utilization. Bases are catalysts for organosiloxane polymerization, rearrangement, and equilibration. The alkali catalytic cracking method has higher cracking efficiency and less equipment corrosion, but the catalyst consumption is large, and the production of 1 ton of crude dimethyl carbonate (DMC) needs consumption 700–750 kg of KOH (Okoshi et al., 2021).
The fixed-value pyrolysis method is to convert waste silicone rubber into a rubber compound that can be re-processed and vulcanized through a moderate depolymerization reaction or depolymerize it into a cyclic siloxane intermediate, and even a siloxane monomer (Guo et al., 2012). Siloxane has a repeating -Si-O- as the main chain of the molecular chain; since the bond energy of the Si-O bond is higher than that of the C-C bond, the silicone rubber has better high-temperature resistance than other general-purpose rubbers (Yang et al., 2018; Zhao et al., 2021). The pyrolysis method is complicated in process and high in energy consumption, and the effective recovery part only accounts for about one-third of the total pyrolysis treatment, which greatly increases the cracking cost. To sum up, it is necessary to study a method for the safe and green degradation of composite insulator waste.
When the transmission line passes through the densely vegetated temperature and humidity or hot and humid areas, it is usually easy to breed microorganisms such as algae and fungi on the surface of the silicone rubber, and the cells adhere to other cells or the silicone rubber matrix through their adhesion molecules; after the formation of micropopulation and mature biofilm colonies, extracellular organic matter constitutes a skeleton to form a biofilm (Wallstrm and Karlsson, 2004; Wang et al., 2012). The long-term coverage of microorganisms has a slow deterioration effect on the structure and function of the silicone rubber shed sheath (Flemming, 1998; Yang et al., 2017). Aging silicone rubber can be degraded by the erosive effect of microorganisms on the silicone rubber matrix.
In this article, the dominant species were selected, the products of microorganisms on the silicone rubber matrix were analyzed, the chemical reaction process was given according to its structural characteristics, the biological pyrolysis mechanism was explained based on the monomer removal angle, and the nano-dioxide with high economic value was prepared and recovered. Meanwhile, the products are verified to be environment friendly.
In this article, the composite insulator silicone rubber shed, naturally retired after 15 years of operation, was used as the raw material to degrade and prepare nano-silica materials. The typical appearance of some shed samples is shown in Figure 1. Cracks appeared on the surface of some sheds of waste composite insulators, and the sheds were seriously whitened, faded, and hardened. The color of the shed surface and the interior of some samples are very different, and the fading is obvious, which can be directly identified with the naked eye. It means that its aging is very serious and it is no longer suitable for continuing to run on the network. The Shore A of waste silicone rubber was 73.10, and its average hydrophobic angle was 88.73°.
Pretreatment of waste silicone rubber sheds: the silicone rubber sheds of the waste composite insulators are peeled off as a whole, thinned, and cut to obtain silicone rubber particles. Then, the silicon rubber particles obtained by cutting are fully stirred with a sufficient amount of anhydrous ethanol to separate silicone oil and silicone grease, and the filtrate is filtered to remove the filtrate to obtain once-washed silicone rubber particles, which are repeatedly washed several times to obtain clean silicone rubber particles. The clean silicone rubber particles are dried in a blast drying oven at 60°C for 0.5–2 h to make them lose moisture completely.
When the transmission line passes through the humid areas with dense vegetation, it is usually easy to breed microorganisms such as algae and fungi on the surface of the silicone rubber (Figure 2). After genetic identification, the epiphytes on the surface of the silicone rubber are mainly Streptomyces and Xanthomonas. Dominant flora including Streptomyces and Xanthomonas were extracted and added to a mineral salt medium. The formula of the culture medium (Jansomboon et al., 2020) is entered in the following having 0.1 mL of the trace element (FeSO4·7H2O, 50 mg; ZnSO4·7H2O, 1 mg; MnCl2·4H2O, 0.3 mg; H3BO3, 3 mg; CoCl2·6H2O, 2 mg; CuCl2·2H2O, 0.1 mg; NiCl2·6H2O, 0.2 mg; and Na2MoO4·H2O, 0.3 mg) in 100 ml of media adjusted to pH 7.0, including (g/L) Na2HPO4·12H2O (9.0), KH2PO4 (1.5), NH4NO3 (1.0), MgSO4·7H2O (0.2), CaCl2·2H2O (0.02), and Fe(III)[NH4] citrate (0.0012).
The ternary mixtures from solvents including diethylamine, hexane, and methanol or in a binary mixture of hexane and methanol were prepared in a 250 ml flask. A small piece (approximately 5 mm × 3 mm × 4 mm in size) of the vulcanized silicone rubber shed containing filler was mixed with acetone into the solvent. At room temperature or under solvent reflux conditions, the mixture is fully contacted via a magnetic or mechanical stirrer to dissolve the silica in the silicone rubber into the solvent, the mixed solution is filtered, and the filtrate is transferred to a 250 ml beaker. If adjusting the pH value is necessary, a small amount of KOH is added, and then, the solution is heated and distilled to remove the solvent. The filtration residue was treated again with a mixture of diethylamine and hexane to obtain the packing.
After the reaction, a white powder, namely, silicon dioxide, was collected, and 0.5 g of the recovered filler was added to 10 ml of a mixture of methanol and H2O (v/v = 1:1) and placed in a planetary ball mill for wet grinding at room temperature for 24 h. Then, it is dried and put into a glass bottle with an aluminum cover to obtain nano-silica. The removal of this antimicrobial substance by organic solvent extraction would lead to increased growth of several microorganisms on this substrate in the next experiment.
The schematic diagram of the established biodegradation is shown in Figure 3. The bioreactor column (I.D. 5 cm × l80 cm) is made of borosilicate glass. The lower part of the bioreactor (up to 28 cm in height) was used as a suspended growth bio scrubber, and the upper part (up to 70 cm in height) was used as a conventional biofilter. The biofilter unit was filled with blocks of polyurethane foam and held at a height of over 34 cm by using a stainless steel frit (0.1 mm × 0.1 mm). Bacterial cultures are cultured by packaging media via an upper nutrient tank. Excess bacterial culture is collected at the bottom of the bioreactor through a bed of polyurethane foam forming a suspended growth bioscrubber. The OD value of liquid samples from the device is periodically monitored. When the OD value exceeds 0.9, 10% culture medium is added. The gas product produced in the bubbler is injected into the scrubber at a flow rate of 0.06–0.48 m3/h. The carbon dioxide concentration was measured by gas chromatography, and two sampling ports were appropriately set in each unit to extract samples. The biodegradation took 30 days.
In the formula,
In order to explore the biodegradation law of waste silicone rubber and the formation mechanism of nano-silica, a gas chromatography-mass spectrometer (GC-MS, US, Agilent) was used to test the composition of gas-phase products with a detection accuracy of 0.01 × 10−6. Also, a thermogravimetric-mass spectrometer (TG-MS) was used to analyze the gas generation process and reasons. To analyze the physical and chemical properties of the solid product, X-ray photoelectron spectroscopy (XPS, ESCALAB 250Xi) and Fourier transform infrared spectroscopy (FTIR, Nicolet iS5) were used to study its elements and functional groups, respectively. At the same time, the particle size and particle size distribution were detected by using a laser particle size analyzer (LPSA, Mastersizer 2000), and the morphology was observed by using a scanning electron microscope (SEM, JEOL JSM-7800F, Japan).
The degradation test lasted 30 days. During the test, an analytical balance was used to monitor the quality change of the silicone rubber, the weight loss in the silicone rubber was detected, and different factors and levels of the orthogonal test were set. Three parallel samples were made for each experimental condition, and the average value was taken as the experimental result.
According to the experimental results in Table 1, when the temperature is the same, the primary and secondary relationship between the factors affecting the degradation experiment is the concentration of bacteria, followed by the ventilation. The optimal experimental condition obtained by the orthogonal experiment is B3C2; that is, the biomass concentration is 1500 CFU/ml and oxygen ventilation is 15 L/min while keeping the room temperature at 25°C, with pH adjusted to 7.0.
The degradation experiment of waste silicone rubber was carried out under optimized conditions, and the calculated cross-linking density of silicone rubber was only the total cross-linking density of silicone rubber, or the apparent cross-linking density. In silicone rubber systems, cross-linking points can be divided into two categories: one type is formed by the crosslinking on the molecular chain and the entanglement between the molecular chains, which is called chemical crosslinking; another type is formed by the relatively weak chemical bond between the filler and the siloxane polymer, such as the adsorption of the filler and the siloxane molecule, which is called physical crosslinking. Jansomboon et al. (2020) proposed that the silicone rubber filled with fillers was fully swollen in toluene dissolved with ammonia gas, and the ammonia gas could enter the silicone rubber to destroy the adsorption between the filler and the siloxane molecules, thereby destroying the physical crosslinks in the silicone rubber system. Under this condition, the measured cross-linking density of silicone rubber is only the chemical cross-linking density, which is lower than the apparent cross-linking density, and the difference between the physical cross-linking density and the chemical cross-linking density is the apparent cross-linking density of the silicone rubber. The cross-linking density reflects the number of cross-linking bonds in the rubber. Under optimized conditions, after 60 days of degradation, the cross-linking density of waste silicone rubber is as shown in Figure 4. After degradation, the cross-linking density decreased by 47.6%, indicating that mold destroyed part of the cross-linking bonds in the rubber, which was helpful for the further degradation of natural rubber.
According to the GC-MS monitoring results during the experiment, the dimethicone rings (D3–D8) are the main cracking products of silicone rubber. Because the structure of the lysis products is relatively similar, the chromatographic retention time is also relatively close. The specific product mass fraction and its share in the PDMS are shown in Table 2, and small-molecule siloxane rings (D3, D4, and D5) are numerous compared to the slightly larger molecular weights of D6, D7, and D8.
Small-molecule cyclosiloxane fragments captured by GC-MS are characterized with obvious characteristics. For example, the characteristic ions of D3 are m/z 133 and 191, the characteristic ions of D4 are m/z 249 and 265 (Figures 5A,B), the characteristic ions of D5 are m/z 267 and 201, the characteristic ions of D6 are m/z 341, and the characteristic ions of D7 are m/z 415, 327, and 281. D8 and D9 mass spectrograms such as m/z 73, 147, 221, 281, and 355 are more obvious, but when comparing D8 with D9, the proportion of m/z 355 fragments in the D8 mass spectrogram is higher, and m/z 429 in D9 is higher (Figures 5C,D); it may be that D8 is more easily decomposed into D5, and D9 is more easily decomposed into D6. Exploring its decomposition law, it can be found that the ring decomposition products all have D3, indicating that it is easy to decompose at a high temperature of D5–D9 due to the instability, while D3 is relatively stable, so it is decomposed into cyclosiloxane with a small molecule such as D3, which is consistent with the trend of product proportion change. Comparing chain siloxanes to cyclic ones, the abundance of fragment ions produced by chain siloxane decreases with the increase in molecular weight mainly due to the occurrence of breakage of the main chain. For example, the content of m/z 73, 147, 221, 281, 355, and 429 in tetramethylhexasiloxane (C14H42O5Si6) (Figure 5E) is higher, and the possible cracking mechanism is discussed as follows.
In the bioreactor cavity, polysiloxanes are first broken into chain-like siloxanes with smaller molecules. However, as the lysis reaction progresses, the lysed chain siloxane undergoes rearrangement degradation to form a more stable small cyclic dimethicone. The possible cleavage mechanism of chain siloxane decomposition into D3 and D4 is shown in Figure 6. Similarly, other ring bodies can be rearranged from chain siloxanes.
Compared with C-O-C, the Si-O-Si chemical bond has higher energy; therefore, the biochemical cracking of silicone rubber is generally more difficult. The capability of producing fragments is due to the fact that the atoms of their molecular chains contain pairs of solitary electrons, while the other atoms contain empty orbitals, and at high temperatures, two adjacent atoms coordinate with each other, prompting bond breaks to form cyclic compounds (Kumar and Wyman, 2008; Jiang et al., 2009). The possible cleavage mechanism of the main fragment ions of D4 and D3 is shown in Figures 7, 8.
By pretreatment and separation of waste silicone rubber according to Section 2.2, a fumed silica is obtained; despite it being fully ground since the silica tends to form a three-dimensional cluster structure, the resulting silica contains not only extracted nano-silica but also micron-level particles. Through the test of the particle size distribution of the silica obtained by the test, it was found that its particle size was normally distributed, containing three peaks, including 111.4, 134.3, and 217.8 nm.
The relatively average specific surface area is around 217.8 m2 g−1, and the specific distribution values are shown in Table 3. The dispersibility of silica particle size is not conducive to its effective recycling. Therefore, it is necessary to use surfactants to modify silica. First, silica particles above 200 nm are separated, 0.2 g of nano-silica, 0.3 g of sodium dodecyl sulfate (SDS), and 0.5 g of co-surfactant (monohydric or dihydric alcohol) are weighed, and 250 m is added; deionized water is added to the conical flask to 100 g, mixed well, and stirred at 80°C for 2 h; heating is stopped; nano-silica dispersion is obtained; and a certain amount is taken and allowed to stand in a transparent glass bottle to observe the stability of the nano-silica dispersion (whether there is precipitation at the bottom). In the process of modifying silica, the ambient temperature is 25°C and the relative humidity is 60%. The particle size of nano-silica was monitored, and the stability of silica colloidal suspension was represented by Zeta potential, as shown in Figure 9; we found that the particle size gradually decreased with time and finally stabilized and the absolute value of Zeta potential increases and stabilizes above 60, indicating that the solution is in a state of excellent stability.
As shown in Figures 10A,B, the nano-silica dispersions under different magnifications were observed by using a scanning electron microscope (SEM), and it was found that the particle diameter was about 18 nm, which was consistent with the results of the particle size analyzer.
FIGURE 10. The scanning electron microscope image of (A) nano-silica, (B) nano-silica and (C) microbial corroded silicone rubber, (D) microbial corroded silicone rubber.
Meanwhile, the micrographs of fungi corrosion on the surface of waste silicone rubber were also taken as shown in Figures 10C,D; spherical cells secrete extracellular polymers to form biofilms on the surface of silicone rubber, the corrosive protease contacts the surface of the silicone rubber, causing the silicone rubber to become rough and uneven in appearance, and the fungus penetrates deep into the silicone rubber and disintegrates the macromolecular structure of the PDMS, resulting in irreversible degradation.
In this article, the waste silicone rubber was biodegraded under an optimum reaction condition, and the nano-silica was separated. The main conclusions were as follows:
(1) The cracking product of silicone rubber is a series of dimethicone rings, and the main rings are D3, D4, and cyclopentasiloxane up to cyclic hexanesiloxane; the macrocylic is completely biodegraded, and only the cyclosiloxane monomers lysis products are left. The exhaust gas is eco-friendly under biodegradation, the process does not require the participation of strong acids and alkalis, and the recovery method is environmental.
(2) The cracking process of waste silicone rubber is the process of finding energy minimization; polysiloxane first breaks into a chain siloxane with smaller molecules and then carries out terminal group back-biting reaction, and the cracked chain siloxane is rearranged and degraded to form a more stable small cyclic dimethicone.
(3) Directly precipitated silica has an agglomeration phenomenon and can be modified by the surfactant sodium lauryl sulfate; modified fumed silica has low particle size about 18 nm and excellent dispersion, which can be directly applied.
The original contributions presented in the study are included in the article/Supplementary Material, further inquiries can be directed to the corresponding author.
SY was responsible for the design and carrying out the experiments, sorting out experimental data, and drafting articles, YL was mainly responsible for the formulation of topics and overall scheme design, and DZ contributed to the writing and typesetting of articles.
This work was supported by the Fundamental Research Funds for the Central Universities (2021MS067).
The authors declare that the research was conducted in the absence of any commercial or financial relationships that could be construed as a potential conflict of interest.
All claims expressed in this article are solely those of the authors and do not necessarily represent those of their affiliated organizations, or those of the publisher, the editors and the reviewers. Any product that may be evaluated in this article, or claim that may be made by its manufacturer, is not guaranteed or endorsed by the publisher.
Chen, L., Guo, F., Yang, T., Hu, T., Bennett, P., Yang, Q., et al. (2021). Aging Characteristics and Self-Healing Properties of Laser-Textured Superhydrophobic Silicone Rubber for Composite Insulators. Polym. Degrad. Stab. 192, 1–10. doi:10.1016/j.polymdegradstab.2021.109693
Cozzarini, L., Marsich, L., Ferluga, A., and Schmid, C. (2020). Life Cycle Analysis of a Novel thermal Insulator Obtained from Recycled Glass Waste. Dev. Built Environ. 3, 100014. doi:10.1016/j.dibe.2020.100014
Flemming, H.-C. (1998). Relevance of Biofilms for the Biodeterioration of Surfaces of Polymeric Materials*. Polym. Degrad. Stab. 59, 309–315. doi:10.1016/s0141-3910(97)00189-4
Guo, L., Tan, J., and Gong, J. (2012). Chemical Aging of the Silicone Rubber in a Simulated and Three Accelerated Proton Exchange Membrane Fuel Cell Environments. J. Power Sourc. 217, 175–183. doi:10.1016/j.jpowsour.2012.05.105
Gou, B., Xie, C., Xu, H., Du, Y., Wang, R., Li, L., et al. (2021). Cracking Mechanism and Degradation Performances of HTV Silicone Rubber with Interfacial Defects under Acid and thermal Stress. Eng. Fail. Anal. 127, 105468. doi:10.1016/j.engfailanal.2021.105468
Halim, Z. A. A., Ahmad, N., Yajid, M. A. M., and Hamdan, H. (2022). Thermal Insulation Performance of Silicone Rubber/silica Aerogel Composite. Mater. Chem. Phys. 276, 1–11. doi:10.1016/j.matchemphys.2021.125359
Jansomboon, W., Prapainainar, P., Loykulnant, S., Kongkachuichay, P., Dittanet, P., Kumnorkaew, P., et al. (2020). Raman Spectroscopic Study of Reinforcement Mechanisms of Electron Beam Radiation Crosslinking of Natural Rubber Composites Filled with Graphene and Silica/graphene Mixture Prepared by Latex Mixing. Composites C: Open Access 3, 100049. doi:10.1016/j.jcomc.2020.100049
Jiang, K. Z., Ni, Y., Wu, J. R., Qiu, H. Y., Lai, G. Q., Jing, Z. Z., et al. (2009). Analysis of Condensed and Addition Type of Silicon Rubbers by Online Pyrolysis Gas Chromatography-Mass Spectrometry. Chin. J. Anal. Chem. 107, 102940. doi:10.1159/000210413
Kumar, R., and Wyman, C. E. (2008). The Impact of Dilute Sulfuric Acid on the Selectivity of Xylooligomer Depolymerization to Monomers. Carbohydr. Res. 343 (2), 290–300. doi:10.1016/j.carres.2007.10.022
Liu, T., Zhang, J., Wu, J., Liu, J., Li, C., Ning, T., et al. (2019). The Utilization of Electrical Insulators Waste and Red Mud for Fabrication of Partially Vitrified Ceramic Materials with High Porosity and High Strength. J. Clean. Prod. 223, 790–800. doi:10.1016/j.jclepro.2019.03.162
Okoshi, M., Iwasaki, K., and Yoshida, T. (2021). Fabrication of Silicone Microcap on Periodic Microswelling Structure of Silicone Rubber by 193-nm ArF Excimer Laser. ACS Mater. Lett. 309, 131335. doi:10.1016/j.matlet.2021.131335
Oku, A., Huang, W., and Ikeda, Y. (2002). Monomer Recycling for Vulcanized Silicone Rubbers in the Form of Cyclosiloxane Monomers. Role of Acid Buffers. Polymer 43, 7289–7293. doi:10.1016/s0032-3861(02)00714-0
Th, A., Ak, A., Tf, A., Hh, B., and Yo, B. (2021). Depth Profiling of Surface Degradation of Silicone Rubber Composite Insulators by Remote Laser-Induced Breakdown Spectroscopy. Spectrochim Acta Part. B Spectrosc. 180, 106206. doi:10.1016/j.sab.2021.106206
Ullah, I., Akbar, M., and Khan, H. A. (2021). Degradation Analysis of RTV-SiR Based Composites under Both Polarities DC Voltage for Insulators Coating. Mater. Today Commun. 29, 1–13. doi:10.1016/j.mtcomm.2021.102890
Wallstrm, S., and Karlsson, S. (2004). Biofilms on Silicone Rubber Insulators; Microbial Composition and Diagnostics of Removal by Use of ESEM/EDS. Polym. Degrad. Stab. 85, 841–846. doi:10.1016/j.polymdegradstab.2004.02.014
Wang, J., Gubanski, S., Blennow, J., Atarijabarzadeh, S., Stromberg, E., and Karlsson, S. (2012). Influence of Biofilm Contamination on Electrical Performance of Silicone Rubber Based Composite Materials. IEEE Trans. Dielect. Electr. Insul. 19, 1690–1699. doi:10.1109/tdei.2012.6311517
Wang, X., and Liu, Q. (2001). Research on Pyrolysis of Waste Rubber Recycling. Therm. Sci. Eng. Prog. 10, 36–42.
Yang, S., Jia, Z., Ouyang, X., Bai, H., and Liu, R. (2017). Hydrophobicity Characteristics of Algae-Fouled HVDC Insulators in Subtropical Climates. Electric Power Systems Research. Electr. Power Syst. Res. 163, 626–637. doi:10.1016/j.epsr.2017.11.009
Yang, S., Jia, Z., Ouyang, X., and Wang, S. (2018). Inhibition of Algae Growth on HVDC Polymeric Insulators Using Antibiotic-Loaded Silica Aerogel Nanocomposites. Polym. Degrad. Stab. 155, 262–270. doi:10.1016/j.polymdegradstab.2018.07.024
Keywords: biodegradation, polymers, monomer recycling, nano-silica, waste silicone rubber composite insulator
Citation: Yang S, Liu Y and Zhou D (2022) Monomer Recovery and Nano-Silica Separation From Biodegraded Waste Silicone Rubber Shed of Composite Insulator. Front. Mater. 9:863731. doi: 10.3389/fmats.2022.863731
Received: 27 January 2022; Accepted: 14 February 2022;
Published: 08 April 2022.
Edited by:
Jun-Wei Zha, University of Science and Technology Beijing, ChinaCopyright © 2022 Yang, Liu and Zhou. This is an open-access article distributed under the terms of the Creative Commons Attribution License (CC BY). The use, distribution or reproduction in other forums is permitted, provided the original author(s) and the copyright owner(s) are credited and that the original publication in this journal is cited, in accordance with accepted academic practice. No use, distribution or reproduction is permitted which does not comply with these terms.
*Correspondence: Shifang Yang, eWFuZ3NmQG5jZXB1LmVkdS5jbg==
Disclaimer: All claims expressed in this article are solely those of the authors and do not necessarily represent those of their affiliated organizations, or those of the publisher, the editors and the reviewers. Any product that may be evaluated in this article or claim that may be made by its manufacturer is not guaranteed or endorsed by the publisher.
Research integrity at Frontiers
Learn more about the work of our research integrity team to safeguard the quality of each article we publish.