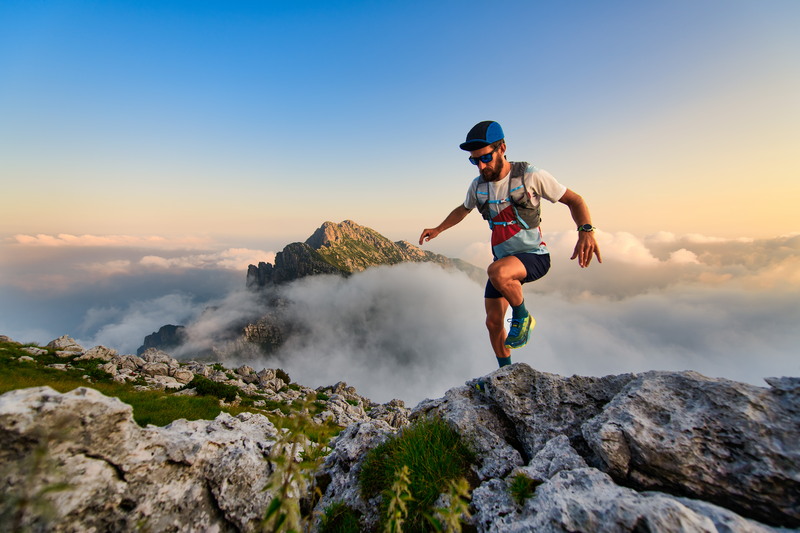
95% of researchers rate our articles as excellent or good
Learn more about the work of our research integrity team to safeguard the quality of each article we publish.
Find out more
REVIEW article
Front. Mater. , 01 March 2022
Sec. Mechanics of Materials
Volume 9 - 2022 | https://doi.org/10.3389/fmats.2022.837359
The metallic glasses are known as amorphous and metastable materials. These materials have superior mechanical properties over crystalline materials with the same chemistry. Continuous efforts were made to improve the properties of metallic glass. The severe plastic deformation (SPD) method is used to improve the ductility of the glass. SPD causes the deformation at the atomic level in the disordered structure of the glass. Many methods are reported, such as cryogenic cycling, high-pressure torsion, and equal channel angular pressing, which are used for the SPD. In recent works on nanostructured metallic glasses, it has been evidenced that some properties, for example, mechanical, thermal, and magnetic, have improved compared to the bulk metallic glass. This paper has reviewed the recent progress in the SPD of the bulk and nanostructured metallic glasses. Different methods for the SPD have been addressed here. The effect of SPD on the properties of metallic glass is deliberated in this paper. Moreover, the challenging tasks of deformation occurrence in the glass and its characterization were considered, trying to develop a sound understanding of SPD in bulk and nanostructured metallic glasses.
It has been more than six decades for metallic glass (MG) to become an active research topic for the materials science community (Cheng and Ma, 2011; Schroers, 2013). MG has unique properties compared to their counterpart crystalline materials of the same chemical compositions, such as high hardness, high strength, better corrosion resistance, and excellent soft magnetic property (Kruzic, 2016; Zhu et al., 2018). MG reveals an excellent combination of mechanical properties such as high strength and high toughness, making them suitable for several mechanical engineering applications (Wagner et al., 2011; Ma, 2015). There is substantial progress in the synthesis and processing of metallic glasses. Due to the rapid quenching from the melts at a high cooling rate, MG possesses a disordered atomic structure (amorphous) and is thermodynamically unstable. However, MG shows superior properties. Still, several challenges exist for MG, such as its bulk production and embrittlement at room temperature. Hence, it is essential to have a clear understanding of glass structure and its relation to the properties of MG. It is known that the MG does not have any ordered microstructure (featureless) and is homogeneous, which is supported by earlier studies (Ma, 2015). However, recently, with the availability of advanced characterization techniques and simulation tools, it has been found that there is chemical inhomogeneity at the atomic level in the MG. Moreover, in recent times, there have been reports on the synthesis of nanostructured MG termed as nanoglass using techniques such as inert gas condensation, sputtering, and electrolysis (Stoesser et al., 2014; Sniadecki et al., 2016; Guo et al., 2017; Mohri et al., 2018; Benel et al., 2019; Chen et al., 2019). These nanoglasses have demonstrated exciting properties that have not been seen in the bulk MG of the same chemical compositions. It is evidenced that the bulk MG’s atomic structure is different from the nanostructured MG, which affects the properties of these glassy materials.
Several processing methodologies are extensively used to improve the properties of the bulk and nanostructured MG. Severe plastic deformation (SPD) is a technique that deforms the atomic structure of the material and results in the modification in their chemistry and microstructure at the nanoscale (Ebrahimi, 2017; Ebrahimi and Shamsborhan, 2017; Djavanroodi et al., 2019). Several reports explored some exciting properties of the MG due to the deformation phenomena at the nanoscale (Valiev et al., 2000; Dmowski et al., 2010; Peng et al., 2011; Hufnagel et al., 2016). Liu et al. (2007) reported the superplasticity in ZrCuNiAl BMG at room temperature and proposed a solution to the brittleness of glasses. They have found that the superplasticity of bulk metallic glasses is due to the presence of hard regions surrounded by soft regions, which is evidenced by the microstructure analysis. This feature allows the glasses to experience a true strain of more than 160%. Greer et al. (2013) discussed shear banding, a pervasive plastic deformation mode in materials. They emphasized that shear bands play a decisive role and are considered a controlling factor in the metallic glasses, demonstrating the plasticity and failure at room temperature. In general, shear bands are treated as a fundamental materials science issue. Mature shear bands are developed by initiating shear transformation zones, propagating, and structural evolution. The enthalpy and free volume of metallic glasses can considerably rise by the rejuvenation process by the structural excitation. Feng et al. (2018) reported the rejuvenation in Zr46Cu46Al8 metallic glasses by molecular dynamics simulation using a pressure preloading model. They found that high-density deformation units in different regions are gradually formed by increasing strain in the rejuvenated Zr46Cu46Al8 metallic glass with pressure preloading. Moreover, the degree of the short-range order increases with the pressure preloading. In another study, Zhang et al. (2020) annealed the Ce69Al10Cu20Co1 metallic glass to its metastable equilibrium super-cooled liquid state below the calorimetric glass transition temperature. They performed the quenching of the super-cooled liquid state in the liquid nitrogen. The quenching process affects the growth of the structural units, free volume, internal stress, and atomic clusters in the metallic glass, and it shows the relaxation-to-rejuvenation transition.
Given the above discussions, it is crucial to study the deformation of metallic glass. It is interesting to understand the size effect on the deformation mechanism in metallic glass. Herein, we reviewed the state of the art of SPD of the bulk and nanostructured metallic glasses. Different deformation techniques, their mechanism, and their effect on structure and properties are discussed in detail. It is believed that the SPD in metallic glasses is essential to make sophisticated designs and to realize how to attain the desired properties.
SPD is an innovative process technology used for bulk nanostructured materials production with interesting properties (Valiev et al., 2000; Valiev, 2003). Generally, SPDed materials have been subjected to high-pressure torsion (HPT) or equal channel angular pressing (ECAP) at room temperature, as shown in Figure 1. These techniques generate heat during the experiment and are usually done under hot deformation. However, there are some reports on cryogenic SPD at low temperatures (Yin et al., 2004; Kim et al., 2009; Zhang et al., 2013; Edalati et al., 2014). The effect of higher temperature on the SPD is also studied by providing external heat. In such a situation, time-dependent diffusion occurs through thermally activated mobility of atoms and vacancies (Setiawan et al., 2011). Rogachev et al. (2021) reported the effect of the temperature during the HPT deformation process and successive annealing at different temperatures on the phase and structural transformations of the Zr-2.5% Nb alloy. They examined the temperature effect on the microhardness of the alloy. It was found that, during the HPT process, the a-Zr to ω-Zr phase transformation happens. However, being subjected to annealing of the HPT-processed alloy samples leads to reverse ω-Zr to a-Zr phase transformation. Dong et al. (2022) studied the combined effect of SPD and annealing process on the 316LN stainless steel to achieve excellent mechanical properties. They reported that the ultra-fine grained 316LN steels were achieved after annealing at a higher temperature. It is interesting to see the σ phase creation at grain boundaries in the temperature range of 750–850°C. The SPD method has several advantages over the other methods in nanostructured material production, such as physical vapor deposition, ball milling, and chemical route synthesis. Furthermore, SPD can solve the problems of residual porosity, impurity during processing, and limited production of nanostructured materials. It is known that severe deformation down to the atomic level can significantly refine the microstructure, leading to interesting properties of the nanostructured materials. In general, the average grain size of the crystalline material plays a significant role in defining the mechanical and physical properties of the materials.
FIGURE 1. Schematic presentation of the (A) high-pressure torsion (HPT) and (B) equal channel angular pressing (ECAP).
Cepeda-Jimenez et al. reported the effect of HPT on the magnetic property of the pure hafnium (Hf) (Cepeda-Jiménez et al., 2017). They reported the room temperature ferromagnetism occurrence in pure hafnium by SPD using HPT. However, it is paramagnet in nature. This work demonstrates an elastic lattice distortion in pure Hf by HPT, resulting in grain refinement down to the nanocrystalline. This condition leads to a new monoclinic crystalline structure establishment and spontaneous magnetization at room temperature. The mechanical strength of polycrystalline materials is associated with the grain size, and the relationship is well defined by the Hall–Petch equation that quantifies the yield stress, σy, where σf is the friction stress, ky is the constant of yielding, and d is the grain size as follows (Valiev and Langdon, 2006):
In the above equation, the mechanical strength increases with the reduction in the grain size of the crystalline materials. Hence, refining the crystalline materials through SPD leads to the fabrication of exceptionally fine grain sizes that enhance the mechanical strength of the materials.
However, Gleiter et al. in 1989 discovered an interesting observation that the hardness of the Cu and Pd nanocrystalline metals of grain size of 5–10 nm decreases with the decrease in the grain size at room temperature (Chokshi et al., 1989). They have suggested the reason for such a result is the diffusional creep manifestation at the grain boundaries. Later on, several studies discovered similar effects for the nanocrystalline materials termed as the “inverse Hall–Petch effect.” Many systems of very small nanocrystalline grains (<100 nm) demonstrated the grain boundary sliding and dislocation emission from the grain boundaries. When a load is applied to nanocrystalline materials of very small grains, the stress is developed due to the grain boundary sliding and results in the lattice dislocations emission at the triple junctions. Therefore, in such a situation, nanocrystalline materials behave contrary to the Hall–Petch effect, valid for bigger grain size (Padmanabhan et al., 2014; Quek et al., 2016; Li and Ma, 2018).
In the case of SPD of metallic glass, the atomic structure and its behavior under stress should be carefully understood. It is known that, in glasses, atoms are disordered and experience a distorted environment, which gives rise to the atomic-level stress in the glass. It is defined that the average of the atomic-level stress is equivalent to the external stress that is typically zero. Primarily, the atomic-level stress was considered a tool to describe the local structure of the metallic glasses. However, progressively, it is important to look beyond the early expectations. It is realized that this is a controlling factor for many phenomena in the disordered glass system, such as structural relaxation, glass transition, and mechanical behavior. Egami (2011) pointed out that the stress at the atomic level is defined for each atom in the glass system. This stress depends on the nature of the atom (e.g., size and volume) and is related to the surrounding environment (i.e., interaction with other atoms) and the atomic cage (network) formed around the atom. The atomic-level stress in glasses was introduced to define the structural defects as the extreme stress values. In the glass, fluctuation of the densities is observed at the atomic level. The low-density regions are considered regions with a more free volume. However, high-density regions are anti-free-volume regions (Egami et al., 1980). Egami et al. (1980) illustrated the defects of free volume and anti-free volume as the n- and p-type defects, respectively. The unrelaxed structure has both n- and p-type defects. Hence, the structural relaxation happens through recombining the n- and p-type defects (Srolovitz et al., 1981). The total change in the volume owing to relaxation occurs by considering the contribution from both n- and p-type defects. It is found that the n- and p-type defects neutralize each other, and the total volume change due to relaxation is about 0.5% (Egami et al., 2013). However, a change in the atomic pair-density function (PDF) that emphasizes the local environment role of the atomic structure is more prominent (about 10%) (Egami, 1978; Srolovitz et al., 1981). Glasses are known for their universal feature of dynamic relaxation. The relaxation processes occurring in the time, frequency, and temperature domains regulate the functions, properties, and applications of glass materials. Hence, the above intrinsic behavior of glass is expected to be affected by the severe plastic deformation mechanism. The nature of the SPD will be dependent on the synthesis techniques and processing parameters of the glass.
Different methods are used for severe plastic deformation depending on the nature and targeted properties of the materials. In general, two SPD techniques are most popular: HPT and ECAP.
As depicted in Figure 1A, the HPT is designed to apply shear at high pressure on the material to bring the deformation down to the atomic level. It is a top-down approach to produce the nanomaterials from the bulk. The bulk sample in the disk shape is placed between two anvils under a compressive applied pressure of several GPa at room temperature or an elevated temperature. At the same time, a torsional strain is applied through rotation of the lower anvil. The disk sample deforms through surface frictional forces due to shear, and deformation continues under a quasi-hydrostatic pressure. The shear strain (dα) can be calculated using the radius of the disk (r), change in the rotational angle (dθ), and the thickness of the disk (L) as follows:
The deformation of the sample subjected to the HPT is carried out under two conditions depending on the confinement of the materials flow under deformation (Zhilyaev and Langdon, 2008). These are termed constrained and unconstrained HPT. In the constrained HPT, the material flow is restricted within the sample. In this case, the sample size exactly matched with the crater size of the lower anvil so that the material cannot come out of the crater, and deformation takes place effectively inside the sample with a generation of some back pressure during the process. However, it is difficult to achieve the total flow restriction inside the crater in most cases. Some portion of the sample is outside of the crater, which flows unrestricted under torsion. In contrast, in the case of the unconstrained HPT, the sample was placed between the anvils. The sample flows freely during the deformation process, and there is negligible back pressure experienced. In general, the HPT technique is extensively used for crystalline materials. However, few studies were recently carried out on glassy materials (Wang et al., 2011; Singh et al., 2020a, 2020b).
ECAP has materialized as a well-known technique for producing ultrafine-grained nanostructured materials through a deformation mechanism, and the technique is based on the extrusion principle (Ebrahimi et al., 2015; Ebrahimi and Gode, 2017). The ECAP is carried out with the rod- and plate-shaped bulk samples that angularly extruded, as shown in Figure 1B. In this case, samples are enclosed in the angular cavity, and flow is restricted in all directions. However, it is allowed in one direction under externally applied pressure. A few factors affect the ECAP process: channel angle, curvature angle of the outer arc, pressing speed (≈1–20 mm s−1), pressing temperature, internal heating during ECAP, and back pressure imposed during ECAP (Valiev and Langdon, 2006). This method is promising for producing many metallic nanostructured materials with crystalline and glassy phases. The ECAP process helps improve mechanical strength, ductility, and fatigue behavior.
Rezaei et al. (2017) consolidated the Al65Cu20Ti15 metallic glass reinforced with Al composites using the ECAP process. They studied the effects of consolidation temperature ranging from room temperature to a lower temperature of the first crystallization of metallic glass during the ECAP process on the relative densities, structural evolutions, and mechanical properties. The precipitation of some intermetallic compounds such as Al5CuTi2, Al3Ti, and Al4Cu9 from the metallic glass was observed at 300°C of the consolidation temperature. Moreover, the matrix grains size of the composite was not affected by the consolidation temperature. The density was increased with the consolidation temperature to 250°C. The best combination of mechanical properties with the yield strength of 184 MPa and ductility of 48% was reported for the composite consolidated at 250°C through the ECAP process. Some more studies were carried out on the consolidation of Al-Cu-Ti metallic glass reinforced with the Al using the ECAP process (Rezaei et al., 2016, 2018). Tong et al. (2013) performed another study using the ECAP on (La0.5Ce0.5)65Co25Al10 and Zr52.5Cu17.9Ni14.6Al10Ti5 BMGs. They found the anisotropic strain in the processed samples using high-energy X-ray diffraction patterns analysis. Further analysis on the strain anisotropy in the ECAP processed samples was observed due to elastic strains. It was summarized that the elastic strain is carried on by residual stress initiating from the shear bands. In addition, the deformation during the ECAP process is characteristically inhomogeneous.
The characterization of the SPDed crystalline materials is relatively more straightforward than that of the glassy materials. The most prevalent techniques are electron microscopy, such as transmission electron microscopy (TEM) and field emission electron microscopy (FESEM). However, other approaches such as atom probe tomography (APT) are more reliable for crystalline and glassy materials in order to visualize the deformation during SPD. The most exciting visualized effect in the SPDed materials is the high-density grain boundaries found in the nanostructured crystalline materials. These grain boundaries are in the non-equilibrium state and thus of high importance. The deformations due to the SPD lead to the fabrication of grain boundary segregation. The other techniques used for the characterization of the SPD include X-ray diffraction, Mössbauer spectroscopy, differential scanning calorimetry, and impedance spectroscopy. These characterization techniques are helpful to study the defects in both the grain boundaries and the grain body of nanostructured materials. Different models for the nanostructured materials are proposed based on these results. However, it is challenging to study the deformation caused by the SPD in the case of glassy materials. It is known that the glassy materials do not have any ordered microstructure, and hence, it is difficult to find the defects in the glassy materials.
SPD has been used for the refinement of the microstructure of crystalline materials. Nevertheless, in recent times, it has been one of the exciting methods for processing glassy materials and observing some fascinating resultant properties tools for glassy materials. However, glassy materials are one of the disordered and metastable states of the matter. They do not have any defined microstructure, and each atom experience a unique environment. Hence, the structure–properties relationship is more complex than the crystalline materials.
In general, bulk metallic glasses are employed properly below the glass transition temperatures for several engineering applications. Liu et al. (2007) reported the superplasticity for the different ZrCuNiAl bulk metallic glass compositions at room temperature. It was concluded that superplasticity is due to the presence of hard regions surrounded by soft regions that increase the strain up to 160%. They performed several compression tests on the three different compositions of ZrCuNiAl BMG at room temperature. The compression test causes intense deformation of the BMG rods into flakes without fracturing (Figure 2). The high flowability of the BMGs under compression causes expansion of the flacks to larger sizes (i.e., diameter more than 5 mm), as shown in Figure 2. In addition, these BMGs in the shape of both rod and plates are bent into desired shapes at a maximum bending angle of 90o (Figure 2).
FIGURE 2. Demonstration of the deformation of the ZrCuNiAl BMG by the compression and bending experiments. (A) True stress-true strain curve of S1 (Zr61.88Cu18Ni10.12Al10), S2 (Zr64.13Cu15.75Ni10.12Al10), and S3 (Zr62Cu15.5Ni12.5Al10) is tested at room temperature. (B) Deformed (under compression) flakes’ images of S1, S2, and S3. (C) Demonstration of exceptional deformability of S2 through bending into different shapes. (D) S2 BMG deformed at various compressive strains. Adapted from Figure 2 of Liu et al. (2007).
Wang et al. (2012) used SPD of a quasi-constrained volume to introduce the strain hardening and decrease shear localization in BMGs that substantially enhance their ductility. The improved ductility is due to increased free volume and nanoscale heterogeneity induced by SPD revealed by the structural characterization.
The formation of the shear bands is another feature of SPD in metallic glass. The shear bands are designed due to strain localization as restricted volume shears of the material relative to the rest. These shear bands cause chemical inhomogeneity during the deformation. Chellali et al. (2020) investigated the chemical inhomogeneity in the shear bands of bulk metallic glass. They observed rapid enhancement in the diffusivities of Cu and Zr along with the shear band subjected to the deformation of Cu50Zr50 metallic glass at room temperature. The change in the atomic distribution was examined using atom probe tomography. It is assumed that such a significantly enhanced diffusion during the shear bands creation is due to the increase in the temperature and the plastic deformation during the shear band motion. Interestingly, the chemical homogeneity remains the same in the regions outside of the shear bands. Moreover, they have found that the diffusivity of Ni tracer is eight times faster along with the shear bands than the homogeneous glassy regions. Such enhanced diffusivity in the shear bands indicates more free volume than the homogeneous metallic glass. In another study, Bokeloh et al. (2011) used the radiotracer measurement technique and found that the atomic diffusivity increased by more than eight orders of magnitude in the shear bands of the Pd40Ni40P20 metallic glass compared to the undeformed glassy region. They could not achieve a mechanism behind such fast diffusion. However, they assumed that excess free volume in the shear bands is non-homogeneous, and it stores near the interfaces between the undeformed region and deformed shear bands of the metallic glass. Hence, the SPD and its mechanism in the metallic glass are still unclear and need more insights with advanced experimental tools and simulation models.
There has been immense interest in nanostructured metallic glass for its unique structure compared to conventional metallic glass. Gleiter’s research group (Gleiter, 2008, 2013, 2016; Gleiter et al., 2014) proposed distinctive features for the nanostructured metallic glass, known as “nanoglass.” These nanoglass structures include the core glassy region and glass-glass interfaces, similar to the grain and grain boundaries in the nanocrystalline materials. A schematic representation of the nanoglass is provided in Figure 3. The atomic arrangements in the glassy core are different from the glass-glass interfaces, which contain an excess free volume and a more relaxed structure. This type of nanoglass is produced by consolidating glassy nanoparticles under high pressure and creating two non-homogeneous regions (i.e., glass and interfaces). The glassy nanoparticles are produced by the inert gas condensation technique using helium gas as a quencher medium. However, other methods are also used to produce the nanostructured glassy materials, including electrolysis, sputtering, and molecular beam epitaxy (Ivanisenko et al., 2018; Mohri et al., 2018; Benel et al., 2019; Singh et al., 2020a; Chen et al., 2020).
FIGURE 3. Schematic presentation of the nanostructured metallic glass (nanoglass) features containing glassy core and glass-glass interface regions.
Our previous study studied the deformation of the Tb75Fe25 nanostructured metallic glass (nanoglass) using high-pressure torsion (Singh et al., 2020a). In this regard, the TbFe nanoglass pellet was produced using the inert gas condensation technique and subjected to the HPT to introduce the deformation. This deformed nanoglass revealed the appearance of shear bands. In the shear bands, Tb has shown the high diffusivity in the shear band that is eight to ten times higher than the undeformed region of the nanoglass. Hence, a chemical inhomogeneity was observed between the shear bands and the undeformed regions, as shown in Figure 4. Moreover, a higher thermal stability parameter was reported for the as-prepared nanoglass than the deformed nanoglass under HPT. Moreover, high magnetic coercivity was observed in the as-prepared and deformed TbFe nanoglass of about 4 T at 1.8 K (Singh et al., 2020b). The as-prepared and deformed (HPT) nanoglass of TbFe underwent heat treatment. The heat-treated deformed nanoglass revealed a high magnetization compared to the heat-treated samples of the as-prepared nanoglass. Sharma et al. (2021) reported the effect of free volume on the deformation behavior of CuZr nanoglass. This work compared the deformation behavior between the as-prepared and the structurally relaxed CuZr nanoglass. They found that the structurally relaxed nanoglass exhibited a higher hardness value than the as-prepared nanoglass. Moreover, the structurally relaxed nanoglass demonstrated the heterogeneous plastic deformation behavior under the micro-hardness test in contrast to the as-prepared nanoglass. This was also supported by the shear bands found at the periphery of the micro-indentation imprint for the structurally relaxed nanoglass.
FIGURE 4. Atom probe tomography image of the shear bands (A,B) found for the Tb75Fe25 nanoglass subjected to severe plastic deformation by HPT. The chemical composition profiles of Tb and Fe across the shear bands indicate the compositional fluctuation. (C) The image was adapted from Singh et al. (2020a).
It is interesting to compare the deformation mechanism between the bulk and nanostructured metallic glass. It is evidenced that the nanostructured metallic glass (nanoglass) has excess free volume at the glass-glass interfaces compared to the chemically homogeneous bulk metallic glass. Moreover, simulation studies experimentally proved and confirmed that, in the case of nanoglass, the segregation of the elements is pronounced. Danilov et al. (2016) pointed out that nanoglasses with unique, glassy microstructures display density variations that are not common in bulk metallic glasses with the same chemical composition. They perform some molecular dynamic simulations to study the nanoglass prepared by the physical vapor deposition (PVD) process, applying on the glassy nanoparticles and subsequently consolidating into a nanoglass. They found that these nanoglass structures prepared by PVD consist of two structural regions: nanometer-sized non-crystalline cores and interfacial regions between two non-crystalline cores. Interestingly, the interfacial regions’ atomic arrangement and internal energy differed from the conventional melt-quenched glass of the same composition. This diversity in properties is due to the boundary condition of the two regions of nanoglass. The presence of interface in the nanoglass resulted in different compositions revealing the segregation of elemental atoms, as shown in Figure 5. The other authors also reported the segregation of the elemental atoms at the interfaces in the nanoglass (Wang C. et al., 2016, Wang X. et al., 2016, 2019; Adjaoud and Albe, 2018; Ivanisenko et al., 2018).
FIGURE 5. (A) represents the radial profiles of the nanoglass as a function of potential energy. The inset of (A) shows the cross section of the nanoglass. The red atoms signify the core, and the blue atoms represent the shell. In (B), the nanoglass of the AB composition is prepared by vapor phase deposition where blue circles and green triangles are assigned to the concentration of A and B atoms, respectively. The image was adapted from the (Danilov et al., 2016).
Nandam et al. (2017) compared the deformation mechanism using a micro-indentation test for the nanoglass and melt-spun ribbon (bulk) of Cu50Zr50 metallic glass. They observed the homogeneous deformation in the case of the nanoglass. The melt-spun ribbon exhibited an inhomogeneous microstructure resulting from the shear bands. These two microstructures for the Cu50Zr50 metallic glass produced by two methods proposed that the nanoglass contains an additional structural feature as the interfacial regions. These interfacial regions have high free volume and act as nucleating sites to create numbers of shear transformation zones throughout the nanoglass and give rise to homogeneous deformation. However, such interfacial regions are absent in the melt-spun ribbons (bulk) of the metallic glass, and shear bands appear through mechanical deformation localized non-homogeneously. The melt-spun ribbon has shown pop-ins in the load versus displacement nanoindentation curve, whereas these pop-ins are absent in the nanoglass sample. This observation evidenced that the nanoglass has uniform deformation behavior under the load. In contrast, the melt-spun ribbon shows non-uniform deformation that appeared as pop-ins in the displacement curve. Hence, the atomic arrangements in the case of nanoglass and the bulk metallic glasses are diverse, resulting in different deformation mechanisms. The deformation mechanism in both the nanoglass and bulk metallic glass is an open topic of discussion. However, it is evidenced that nanoglass has a high volume of interfacial regions with extra free volume facilitating the deformation homogeneously. Moreover, in the previous discussions, it is also observed that the deformation in the nanoglass and the bulk metallic glass resulted in the shear bands demonstrating the high diffusivity along with the shear bands compared to the undeformed regions (Singh et al., 2020a; Chellali et al., 2020).
This study discussed the severe plastic deformation (SPD) processing of metallic glasses. In general, the SPD technique is more common and widely used for crystalline materials. However, SPD processing of metallic glass materials has recently attracted much attention. A fundamental understanding of the different techniques of the SPD, such as high-pressure torsion and equal channel angular pressing, was also presented. Shear bands are the most common feature of the SPD. In this study, different aspects of the SPD in the bulk metallic glass and the nanostructured metallic glass were systematically discussed. The deformation mechanisms are different in both cases because of their different microstructures. The bulk metallic glass has a uniform microstructure and chemical homogeneity. However, the nanostructured metallic glass, also termed nanoglass, demonstrated the two structural features of the glassy core and the glass-glass interface. The atomic arrangement and energy landscape for these two regions are different and provide a unique structural feature absent in the bulk metallic glass. However, in both cases, high diffusivity in the shear bands has been observed compared to the undeformed region. These deformed metallic glasses have demonstrated some interesting properties. More studies are needed to understand the deformation mechanism in the metallic glasses of different structures. It is believed that much research is required to thoroughly explain the role of relaxation and free volume in the above metallic glasses on the different properties.
SS conceptualized, wrote the first draft and edited the manuscript. ME, SA, LW, QW, and FD edited the manuscript.
The authors declare that the research was conducted in the absence of any commercial or financial relationships that could be construed as a potential conflict of interest.
All claims expressed in this article are solely those of the authors and do not necessarily represent those of their affiliated organizations or those of the publisher, the editors, and the reviewers. Any product that may be evaluated in this article, or claim that may be made by its manufacturer, is not guaranteed or endorsed by the publisher.
Adjaoud, O., and Albe, K. (2018). Microstructure Formation of Metallic Nanoglasses: Insights from Molecular Dynamics Simulations. Acta Materialia 145, 322–330. doi:10.1016/j.actamat.2017.12.014
Benel, C., Fischer, A., Zimina, A., Steininger, R., Kruk, R., Hahn, H., et al. (2019). Controlling the Structure and Magnetic Properties of Cluster-Assembled Metallic Glasses. Mater. Horiz. 6, 727–732. doi:10.1039/c8mh01013g
Bokeloh, J., Divinski, S. V., Reglitz, G., and Wilde, G. (2011). Tracer Measurements of Atomic Diffusion inside Shear Bands of a Bulk Metallic Glass. Phys. Rev. Lett. 107, 235503–235505. doi:10.1103/PhysRevLett.107.235503
Cepeda-Jiménez, C. M., Beltrán, J. I., Hernando, A., García, M. A., Ynduráin, F., Zhilyaev, A., et al. (2017). Tuning the Magnetic Properties of Pure Hafnium by High Pressure Torsion. Acta Mater. 123, 206–213.
Chellali, M. R., Nandam, S. H., and Hahn, H. (2020). Deformation-induced Chemical Inhomogeneity and Short-Circuit Diffusion in Shear Bands of a Bulk Metallic Glass. Phys. Rev. Lett. 125, 205501. doi:10.1103/physrevlett.125.205501
Chen, N., Wang, D., Guan, P. F., Bai, H. Y., Wang, W. H., Zhang, Z. J., et al. (2019). Direct Observation of Fast Surface Dynamics in Sub-10-nm Nanoglass Particles. Appl. Phys. Lett. 114, 043103. doi:10.1063/1.5052016
Chen, W. Y., Chen, H. W., Li, W. P., Huang, J. C., Yu, H. S., Duh, J. G., et al. (2020). Compositionally Modulated Microstructure in Nano-Layered Ni-P Metallic Glass Composite Coating Prepared by Electrodeposition. Surf. Coat. Technol. 389, 125636. doi:10.1016/j.surfcoat.2020.125636
Cheng, Y. Q., and Ma, E. (2011). Atomic-level Structure and Structure-Property Relationship in Metallic Glasses. Prog. Mater. Sci. 56, 379–473. doi:10.1016/j.pmatsci.2010.12.002
Chokshi, A. H., Rosen, A., Karch, J., and Gleiter, H. (1989). On the Validity of the Hall-Petch Relationship in Nanocrystalline Materials. Scripta Metallurgica 23, 1679–1683. doi:10.1016/0036-9748(89)90342-6
Danilov, D., Hahn, H., Gleiter, H., and Wenzel, W. (2016). Mechanisms of Nanoglass Ultrastability. ACS Nano 10, 3241–3247. doi:10.1021/acsnano.5b05897
Djavanroodi, F., Ebrahimi, M., and Nayfeh, J. F. (2019). Tribological and Mechanical Investigation of Multi-Directional Forged Nickel. Sci. Rep. 9, 241–248. doi:10.1038/s41598-018-36584-w
Dmowski, W., Yokoyama, Y., Chuang, A., Ren, Y., Umemoto, M., Tsuchiya, K., et al. (2010). Structural Rejuvenation in a Bulk Metallic Glass Induced by Severe Plastic Deformation. Acta Materialia 58, 429–438. doi:10.1016/j.actamat.2009.09.021
Dong, Y., Zhang, Z., Yang, Z., Zheng, R., and Chen, X. (2022). Effect of Annealing Temperature on the Microstructure and Mechanical Properties of High-Pressure Torsion-Produced 316LN Stainless Steel. Materials (Basel) 15, 181.
Ebrahimi, M., Djavanroodi, F., Tiji, S., Gholipour, H., and Gode, C. (2015). Experimental Investigation of the Equal Channel Forward Extrusion Process. Metals 5, 471–483. doi:10.3390/met5010471
Ebrahimi, M. (2017). Fatigue Behaviors of Materials Processed by Planar Twist Extrusion. Metall. Mat Trans. A. 48, 6126–6134. doi:10.1007/s11661-017-4375-4
Ebrahimi, M., and Gode, C. (2017). Severely Deformed Copper by Equal Channel Angular Pressing. Prog. Nat. Sci. Mater. Int. 27, 244–250. doi:10.1016/j.pnsc.2017.03.002
Ebrahimi, M., and Shamsborhan, M. (2017). Monotonic and Dynamic Mechanical Properties of PTCAE Aluminum. J. Alloys Compd. 705, 28–37. doi:10.1016/j.jallcom.2017.02.109
Edalati, K., Cubero-Sesin, J. M., Alhamidi, A., Mohamed, I. F., and Horita, Z. (2014). Influence of Severe Plastic Deformation at Cryogenic Temperature on Grain Refinement and Softening of Pure Metals: Investigation Using High-Pressure Torsion. Mater. Sci. Eng. A 613, 103–110. doi:10.1016/j.msea.2014.06.084
Egami, T. (2011). Atomic Level Stresses. Prog. Mater. Sci. 56, 637–653. doi:10.1016/j.pmatsci.2011.01.004
Egami, T., Iwashita, T., and Dmowski, W. (2013). Mechanical Properties of Metallic Glasses. Metals 3, 77–113. doi:10.3390/met3010077
Egami, T., Maeda, K., and Vitek, V. (1980). Structural Defects in Amorphous Solids A Computer Simulation Study. Philosophical Mag. A 41, 883–901. doi:10.1080/01418618008243894
Egami, T. (1978). Structural Relaxation in Amorphous Fe40Ni40P14 B6 Studied by Energy Dispersive X-ray Diffraction. J. Mater. Sci. 13, 2587–2599. doi:10.1007/bf02402745
Feng, S. D., Chan, K. C., Zhao, L., Pan, S. P., Qi, L., Wang, L. M., et al. (2018). Rejuvenation by Weakening the Medium Range Order in Zr46Cu46Al8 Metallic Glass with Pressure Preloading: A Molecular Dynamics Simulation Study. Mater. Des. 158, 248–255. doi:10.1016/j.matdes.2018.08.040
Gleiter, H. (2016). Nanoglasses: A New Kind of Noncrystalline Material and the Way to an Age of New Technologies? Small 12, 2225–2233. doi:10.1002/smll.201500899
Gleiter, H. (2013). Nanoglasses: A New Kind of Noncrystalline Materials. Beilstein J. Nanotechnol. 4, 517–533. doi:10.3762/bjnano.4.61
Gleiter, H. (2008). Our Thoughts Are Ours , Their Ends None of Our Own : Are There Ways to Synthesize Materials beyond the Limitations of Today? Acta Mater. 56, 5873–5891. doi:10.1016/j.actamat.2008.08.028
Gleiter, H., Schimmel, T., and Hahn, H. (2014). Nanostructured Solids - from Nano-Glasses to Quantum Transistors. Nano Today 9, 17–68. doi:10.1016/j.nantod.2014.02.008
Greer, A. L., Cheng, Y. Q., and Ma, E. (2013). Shear Bands in Metallic Glasses. Mater. Sci. Eng. R: Rep. 74, 71–132. doi:10.1016/j.mser.2013.04.001
Guo, C., Fang, Y., Wu, B., Lan, S., Peng, G., Wang, X.-l., et al. (2017). Ni-P Nanoglass Prepared by Multi-phase Pulsed Electrodeposition. Mater. Res. Lett. 5, 293–299. doi:10.1080/21663831.2016.1264495
Hufnagel, T. C., Schuh, C. A., and Falk, M. L. (2016). Deformation of Metallic Glasses: Recent Developments in Theory, Simulations, and Experiments. Acta Materialia 109, 375–393. doi:10.1016/j.actamat.2016.01.049
Ivanisenko, Y., Kübel, C., Nandam, S. H., Wang, C., Mu, X., Adjaoud, O., et al. (2018). Structure and Properties of Nanoglasses. Adv. Eng. Mater. 20, 1–16. doi:10.1002/adem.201800404
Kim, W. J., Jeong, H. G., and Jeong, H. T. (2009). Achieving High Strength and High Ductility in Magnesium Alloys Using Severe Plastic Deformation Combined with Low-Temperature Aging. Scripta Materialia 61, 1040–1043. doi:10.1016/j.scriptamat.2009.08.020
Kruzic, J. J. (2016). Bulk Metallic Glasses as Structural Materials: A Review. Adv. Eng. Mater. 18, 1308–1331. doi:10.1002/adem.201600066
Li, Q.-J., and Ma, E. (2018). When 'smaller Is Stronger' No Longer Holds. Mater. Res. Lett. 6, 283–292. doi:10.1080/21663831.2018.1446192
Liu, Y. H., Wang, G., Wang, R. J., Zhao, D. Q., Pan, M. X., and Wang, W. H. (2007). Super Plastic Bulk Metallic Glasses at Room Temperature. Science 315, 1385–1388. doi:10.1126/science.1136726
Mohri, M., Wang, D., Ivanisenko, J., Gleiter, H., and Hahn, H. (2018). Thermal Stability of the Ti-Zr-Cu-Pd Nano-Glassy Thin Films. J. Alloys Compd. 735, 2197–2204. doi:10.1016/j.jallcom.2017.11.387
Nandam, S. H., Ivanisenko, Y., Schwaiger, R., Śniadecki, Z., Mu, X., Wang, D., et al. (2017). Cu-Zr Nanoglasses: Atomic Structure, thermal Stability and Indentation Properties. Acta Materialia 136, 181–189. doi:10.1016/j.actamat.2017.07.001
Padmanabhan, K. A., Sripathi, S., Hahn, H., and Gleiter, H. (2014). Inverse Hall-Petch Effect in Quasi- and Nanocrystalline Materials. Mater. Lett. 133, 151–154. doi:10.1016/j.matlet.2014.06.153
Peng, H. L., Li, M. Z., and Wang, W. H. (2011). Structural Signature of Plastic Deformation in Metallic Glasses. Phys. Rev. Lett. 106, 135503. doi:10.1103/physrevlett.106.135503
Quek, S. S., Chooi, Z. H., Wu, Z., Zhang, Y. W., and Srolovitz, D. J. (2016). The Inverse Hall-Petch Relation in Nanocrystalline Metals: A Discrete Dislocation Dynamics Analysis. J. Mech. Phys. Sol. 88, 252–266. doi:10.1016/j.jmps.2015.12.012
Rezaei, M. R., Razavi, S. H., and Shabestari, S. G. (2016). Development of a Novel Al-Cu-Ti Metallic Glass Reinforced Al Matrix Composite Consolidated through Equal Channel Angular Pressing (ECAP). J. Alloys Compd. 673, 17–27. doi:10.1016/j.jallcom.2016.02.234
Rezaei, M. R., Shabestari, S. G., and Razavi, S. H. (2018). Effect of ECAP Consolidation Process on the Interfacial Characteristics of Al-Cu-Ti Metallic Glass Reinforced Aluminum Matrix Composite. Compos. Inter. 25, 669–679. doi:10.1080/09276440.2018.1439619
Rezaei, M. R., Shabestari, S. G., and Razavi, S. H. (2017). Effect of ECAP Consolidation Temperature on the Microstructure and Mechanical Properties of Al-Cu-Ti Metallic Glass Reinforced Aluminum Matrix Composite. J. Mater. Sci. Technol. 33, 1031–1038. doi:10.1016/j.jmst.2016.10.013
Rogachev, S. O., Sundeev, R. V., and Nikulin, S. A. (2021). Effect of Severe Plastic Deformation by High-Pressure Torsion at Different Temperatures and Subsequent Annealing on Structural and Phase Transformations in Zr-2.5% Nb alloy. J. Alloys Compd. 865, 158874.
Setiawan, A., Terada, D., and Tsuji, N. (2011). High-temperature Severe Plastic Deformation of Ferritic Steel by Torsion. Mater. Sci. Forum 667–669, 403–408.
Sharma, A., Nandam, S. H., Hahn, H., and Prasad, K. E. (2021). Effect of Structural Relaxation on the Indentation Size Effect and Deformation Behavior of Cu-Zr-Based Nanoglasses. Front. Mater. 8, 676764. doi:10.3389/fmats.2021.676764
Singh, S. P., Chellali, M. R., Velasco, L., Ivanisenko, Y., Boltynjuk, E., Gleiter, H., et al. (2020a). Deformation-induced Atomic Rearrangements and Crystallization in the Shear Bands of a Tb75Fe25 Nanoglass. J. Alloys Compd. 821, 153486. doi:10.1016/j.jallcom.2019.153486
Singh, S. P., Witte, R., Clemens, O., Sarkar, A., Velasco, L., Kruk, R., et al. (2020b). Magnetic Tb75Fe25 Nanoglass for Cryogenic Permanent Magnet Undulator. ACS Appl. Nano Mater. 3, 7281–7290. doi:10.1021/acsanm.0c01674
Sniadecki, Z., Wang, D., Ivanisenko, Y., Chakravadhanula, V. S. K., Kübel, C., Hahn, H., et al. (2016). Nanoscale Morphology of Ni50Ti45Cu5 Nanoglass. Mater. Charact. 113, 26–33.
Srolovitz, D., Egami, T., and Vitek, V. (1981). Radial Distribution Function and Structural Relaxation in Amorphous Solids. Phys. Rev. B 24, 6936–6944. doi:10.1103/physrevb.24.6936
Stoesser, A., Ghafari, M., Kilmametov, A., Gleiter, H., Sakurai, Y., Itou, M., et al. (2014). Influence of Interface on Structure and Magnetic Properties of Fe50B50 Nanoglass. J. Appl. Phys. 116, 134305. doi:10.1063/1.4897153
Tong, Y., Dmowski, W., Witczak, Z., Chuang, C.-P., and Egami, T. (2013). Residual Elastic Strain Induced by Equal Channel Angular Pressing on Bulk Metallic Glasses. Acta Materialia 61, 1204–1209. doi:10.1016/j.actamat.2012.10.030
Valiev, R. Z., Islamgaliev, R. K., and Alexandrov, I. V. (2000). Bulk Nanostructured Materials from Severe Plastic Deformation. Prog. Mater. Sci. 45, 103–189. doi:10.1016/s0079-6425(99)00007-9
Valiev, R. Z., and Langdon, T. G. (2006). Principles of Equal-Channel Angular Pressing as a Processing Tool for Grain Refinement. Prog. Mater. Sci. 51, 881–981. doi:10.1016/j.pmatsci.2006.02.003
Valiev, R. Z. (2003). Paradoxes of Severe Plastic Deformation. Adv. Eng. Mater. 5, 296–300. doi:10.1002/adem.200310089
Wagner, H., Bedorf, D., Küchemann, S., Schwabe, M., Zhang, B., Arnold, W., et al. (2011). Local Elastic Properties of a Metallic Glass. Nat. Mater 10, 439–442. doi:10.1038/nmat3024
Wang, C., Mu, X., Chellali, M. R., Kilmametov, A., Ivanisenko, Y., Gleiter, H., et al. (2019). Tuning the Curie Temperature of Fe90Sc10 Nanoglasses by Varying the Volume Fraction and the Composition of the Interfaces. Scripta Materialia 159, 109–112. doi:10.1016/j.scriptamat.2018.09.025
Wang, C., Wang, D., Mu, X., Goel, S., Feng, T., Ivanisenko, Y., et al. (2016a). Surface Segregation of Primary Glassy Nanoparticles of Fe90Sc10 Nanoglass. Mater. Lett. 181, 248–252. doi:10.1016/j.matlet.2016.05.189
Wang, X. D., Cao, Q. P., Jiang, J. Z., Franz, H., Schroers, J., Valiev, R. Z., et al. (2011). Atomic-level Structural Modifications Induced by Severe Plastic Shear Deformation in Bulk Metallic Glasses. Scripta Materialia 64, 81–84. doi:10.1016/j.scriptamat.2010.09.015
Wang, X., Jiang, F., Hahn, H., Li, J., Gleiter, H., Sun, J., et al. (2016b). Sample Size Effects on Strength and Deformation Mechanism of Sc75Fe25 Nanoglass and Metallic Glass. Scripta Materialia 116, 95–99. doi:10.1016/j.scriptamat.2016.01.036
Wang, Y. B., Qu, D. D., Wang, X. H., Cao, Y., Liao, X. Z., Kawasaki, M., et al. (2012). Introducing a Strain-Hardening Capability to Improve the Ductility of Bulk Metallic Glasses via Severe Plastic Deformation. Acta Materialia 60, 253–260. doi:10.1016/j.actamat.2011.09.026
Yin, J., Lu, J., Ma, H., and Zhang, P. (2004). Nanostructural Formation of fine Grained Aluminum alloy by Severe Plastic Deformation at Cryogenic Temperature. J. Mater. Sci. 39, 2851–2854. doi:10.1023/b:jmsc.0000021463.83899.b3
Zhang, W., Xiang, Q. C., Ma, C. Y., Ren, Y. L., and Qiu, K. Q. (2020). Relaxation-to-rejuvenation Transition of a Ce-Based Metallic Glass by Quenching/cryogenic Treatment Performed at Sub-tg. J. Alloys Compd. 825, 1–6. doi:10.1016/j.jallcom.2020.153997
Zhang, Y., Jiang, S., Hu, L., and Liang, Y. (2013). Deformation Mechanism of NiTi Shape Memory alloy Subjected to Severe Plastic Deformation at Low Temperature. Mater. Sci. Eng. A 559, 607–614. doi:10.1016/j.msea.2012.08.149
Zhilyaev, A., and Langdon, T. (2008). Using High-Pressure Torsion for Metal Processing: Fundamentals and Applications. Prog. Mater. Sci. 53, 893–979. doi:10.1016/j.pmatsci.2008.03.002
Keywords: severe plastic deformation, metallic glass, nanostructure, high-pressure torsion, shear band
Citation: Singh SP, Ebrahimi M, Attarilar S, Wang L, Wang Q and Djavanroodi F (2022) Assessment of Severe Plastic Deformation Processes in Bulk and Nanostructured Metallic Glass. Front. Mater. 9:837359. doi: 10.3389/fmats.2022.837359
Received: 16 December 2021; Accepted: 25 January 2022;
Published: 01 March 2022.
Edited by:
Stefano Mariani, Politecnico di Milano, ItalyReviewed by:
Jili Wu, Jiangsu University, ChinaCopyright © 2022 Singh, Ebrahimi, Attarilar, Wang, Wang and Djavanroodi. This is an open-access article distributed under the terms of the Creative Commons Attribution License (CC BY). The use, distribution or reproduction in other forums is permitted, provided the original author(s) and the copyright owner(s) are credited and that the original publication in this journal is cited, in accordance with accepted academic practice. No use, distribution or reproduction is permitted which does not comply with these terms.
*Correspondence: Shiv Prakash Singh, c3BzaW5naDY3QGdtYWlsLmNvbQ==; Mahmoud Ebrahimi, ZWJyYWhpbWlAbWFyYWdoZWguYWMuaXI=
Disclaimer: All claims expressed in this article are solely those of the authors and do not necessarily represent those of their affiliated organizations, or those of the publisher, the editors and the reviewers. Any product that may be evaluated in this article or claim that may be made by its manufacturer is not guaranteed or endorsed by the publisher.
Research integrity at Frontiers
Learn more about the work of our research integrity team to safeguard the quality of each article we publish.