- 1Department of Materials Sciences and Engineering, The University of Tennessee, Knoxville, TN, United States
- 2Neutron Scattering Division, Oak Ridge National Laboratory, Oak Ridge, TN, United States
- 3Neutron Technology Division, Oak Ridge National Laboratory, Oak Ridge, TN, United States
- 4Center for Nanophase Materials Sciences, Oak Ridge National Laboratory, Oak Ridge, TN, United States
- 5Department of Physics and Astronomy, University of Tennessee, Knoxville, TN, United States
High-entropy alloys (HEAs) are materials which leverage the entropy of mixing to motivate the formation of single-phase solid solutions, even of immiscible elements. While these materials are well-recognized for their application to structural engineering, there is increasing interest in the use of HEAs for functional applications such as memory storage and energy devices. The current work investigates the HEA Al1.3CoCrCuFeNi, which has been previously shown to be single-phase at high temperatures, but undergoes phase separation at lower temperatures, transforming the structural and the functional properties. This phase separation is investigated at high temperatures with in-situ small angle neutron scattering (SANS) and scanning transmission electron microscopy (EDS). These techniques show that increasing the temperature up to 800°C, the microstructure of the HEA adiabatically disorders and abruptly homogenizes near 700°C, which is consistent with spinodal decomposition. Overall, the microstructural evolution proceeds mainly by the atomistic redistribution of the constituent elements within simple crystal lattices, producing coherent phase mixtures.
Introduction
High-entropy alloys (HEAs) have been the focus of research since their discovery in 2004 due to their potential in structural applications (Tong et al., 2005a) and more recently functional devices such as memory storage and energy technologies (Wang et al., 2021). These materials are comprised of five or more elements which randomly occupy a single lattice site in an otherwise ordered crystal lattice; the large entropy from the chemical disorder can stabilize alloy compositions even between immiscible elements. The AlxCoCrCuFeNi family of HEAs was among the first to be studied, and continues to provide challenges and opportunities for researchers seeking to better understand phase stability, phase separation, and microstructure development in advanced alloys (Yeh et al., 2004; Tong et al., 2005b; Zhang et al., 2014; Santodonato et al., 2015; Gao et al., 2016; Miracle and Senkov, 2017; Xu et al., 2018; Pan et al., 2021). HEAs were initially recognized for their tendency to form single-phase solid solutions (e.g., alloys) with excellent mechanical properties such as high yield strength and hardness, which can be systematically varied by changing the aluminum content (x-parameter) (Yeh et al., 2004; Tong et al., 2005b). Subsequent studies, particularly by Yeh et al. (2004) and Tong et al. (2005b), have revealed more details about this system, including phase separation between the Al-Ni and Cr-Fe for compositions with precentages Al ≥ 1. Commensurate with the phase separation is an enhancement of the hardness and ductility (Wang et al., 2009; Singh et al., 2011; Tang et al., 2015). The interface between these phases has been proposed to be coherent, a feature which strongly contributes to the improved structural performance in modern superalloys (Zhao et al., 2003; Prasher et al., 2019). In both the x = 1 and x = 1.3 compositions, phase separation of Al-Ni and Cr-Fe is reported at room temperature, while at high-temperatures the material is a single homogenized phase. The dissolution of the two phases has been proposed to occur by spinodal decomposition (Welk et al., 2013; Santodonato et al., 2015). The high-temperature transformation is determined by the Gibbs free energy, which couples the temperature to the entropy, affirming the role of the HEA paradigm in determining the ordering.
The high-temperature, entropically-driven transformation is the focus of the current work. Our previous work has investigated the HEA Al1.3CoCrCuFeNi using in-situ diffraction while heating through the transition, capturing changes in the crystal structure (Santodonato et al., 2015), but had little sensitivity to the microstructure or chemical ordering. Using differential thermal analysis and room-temperature microscopy, it has been proposed that the transformation occurs by spinodal decomposition (SD) at ≈600°C. During the SD, the microstructure is proposed to change abruptly, with discrete, well-defined phases merging at higher temperatures into a homogenized alloy. Due to the strong dependence of the macroscopic structural properties on the microstructure and compositional disorder (homogeneity), it is critical to develop a thorough understanding of the structure before, during and after the SD. The present study uses in-situ heating with small-angle neutron scattering (SANS) and scanning transmission electron microscopy (STEM) with energy dispersive x-ray spectroscopy (EDS) to investigate the temperature-dependent formation and distribution of phases, confirming the SD transition in Al1.3CoCrCuFeNi.
Experimental
Samples were fabricated using standard arc melting techniques as described previously (Zhao et al., 2003; Ohmura et al., 2006; Lee et al., 2018; Lee et al., 2020a; Lee et al., 2020b). The samples for in-situ STEM heating experiments were prepared by first sectioning the as-cast ingots into ≈5 mm cube-shaped pieces. A Hitachi NB5000 Ga+ focused ion beam (FIB) operated at 40 kV Ga+ was then used to extract and thin (≈100 nm) specimens, followed by a low 5 kV surface cleaning procedure. An in-situ micromanipulator was subsequently employed to transfer the specimen onto a MEMS fabricated heating microchip device, (Protochips, Inc. Morrisville, NC), following the protocol outlined by Duchamp et al. (2014) FIB milling is an established technique for traditional TEM specimen preparation (Giannuzzi and Stevie, 1999) and it is well known that preparation using this method results in Ga+ implantation (Langford and Petford-Long, 2001). However, the final cleaning at 5 kV reduces the Ga defects in the final specimen (Langford et al., 2001). The in-situ STEM heating experiments were performed from room temperature to 800°C on a Hitachi HF-3300 STEM, operating at 300 kV, ramping the temperature at 5°C per minute then holding the temperature constant for 30 min before imaging. STEM-EDS elemental maps were acquired using a Bruker silicon drift EDS detector at 256 × 192 pixels, a pixel dwell time of 13 ms, with an overall acquisition time of 11 min. Small-angle neutron scattering studies were conducted at the High Flux Isotope Reactor (HFIR) on the General-Purpose SANS beamline (GP-SANS) (Wignall et al., 2012). This technique is sensitive to the microstructure of the material, specifically chemical phase separation and the resulting change in the nuclear scattering length density. The instrument was configured to use a neutron wavelength (λ) of 8 Å with the resolution Δλ/λ of 0.15. The sample-to-detector distance of 19.3 m was chosen to provide a q-range of 0.002 Å-1 to 0.04 Å-1 for observing microstructural features in the size range of 160–3,100 Å. A tube furnace exposed to atmosphere was used to control the sample temperature during the SANS measurements, up to 800°C, allowing in-situ measurement of the structure. The temperature was initially heated to 400°C with a ramp rate of 20°C/s and then ramped to higher temperatures by 50°C every 15 min. The SANS prepared samples were 10 mm diameter disks with a thicknesses of 1 mm.
Results and Discussion
The first step of the in-situ STEM-EDS study was to reproduce the previously reported room-temperature microstructure of the Al1.3CoCrCuFeNi alloy (Santodonato et al., 2018). The as-cast metal has a dendritic microstructure, with Cu-lean dendrites and Cu-rich inter-dendrites, spanning several hundred microns in scale (not shown). Within the dendrites, a periodic microstructure consisting of Cr-Fe rich plates in a matrix of Al-Ni of is observed and shown in Figure 1. The Cr-Fe has a body-centered-cubic (BCC) structure, with the plate growth direction normal to the <1 0 0 > vectors (Wang et al., 2009); the Al-Ni matrix has an ordered BCC (i.e., B2) structure. These two phases have nearly equal lattice parameters of ≈2.9 Å, allowing for a coherent interface, characterized previously by Welk et. al. (Welk et al., 2013) The Co (not shown) is included in both the Cr-Fe and the Al-Ni phases, with a signal appearing throughout the dendrites. The Cu is shown to form its own plates that are separate from both the Cr-Fe and the Al-Ni, which have a face-centered cubic (FCC) structure (Xu et al., 2018). Most of the Cu in the sample forms FCC phases in the inter-dendritic regions (Tong et al., 2005b; Santodonato et al., 2015; Xu et al., 2018). These FCC inter-dendritic zones are stable to temperatures near the melting point of pure Cu (1,085°C). In contrast, the oriented-plate microstructure of the dendrite region undergoes significant changes between room temperature and 800°C; which is the main focus of the present in-situ study.
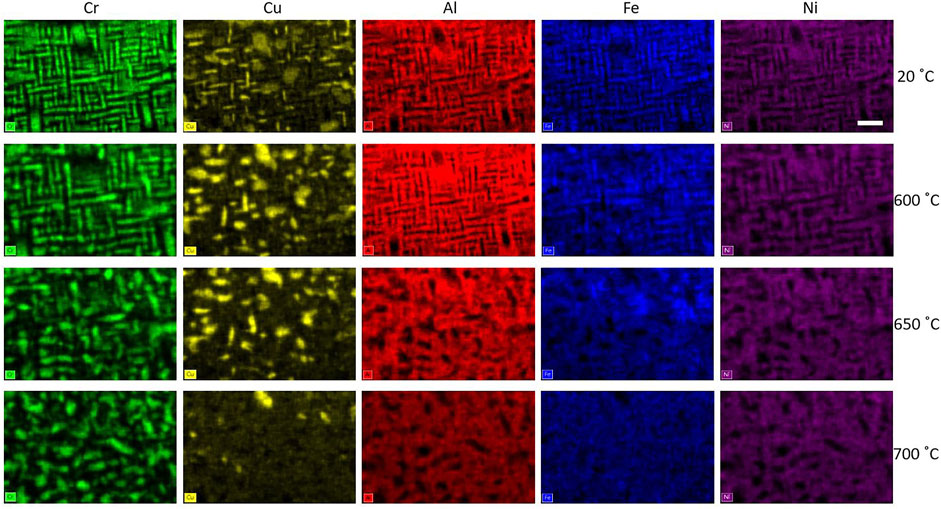
FIGURE 1. EDS elemental maps acquired during in-situ STEM heating experiments of Al1.3CoCrCuFeNi: (top to bottom) 20, 600, 650, and 700°C. Images show the compositional distributions for (left to right) Cr, Cu, Al, Fe, and Ni. Scale bar is 5,000 Å.
The STEM-EDS images in Figure 1 show that the microstructure of the sample gradually changes as the alloy is heated from room temperature to 600°C. STEM images showing the microstructure were published in a previous work (Santodonato et al., 2015). As the Cr images emphasize, at 600°C the plates become larger, with an increasingly diffuse boundary. Increasing the temperature to 650°C further degrades the plates, causing them to lose their well-defined structure and coherent orientation. At 650°C the Fe leaves the Cr, entering the Al-Ni phase, which now forms a matrix with voids for Cr and Cu.
Finally, heating to 700°C further homogenizes the sample, resulting in a disordered dispersion of Cr-rich and Cu-rich precipitates. The Co micrograph shows that at high temperatures the Co is intermixed predominantly with the AlFeNi matrix. High-temperature neutron diffraction spectra presented in Santodonato et al. (2015) shows little change to the underlying crystal structure between room temperature and 1,000°C. Comparing the STEM-EDS results shown here to the diffraction spectra indicates that the microstructural changes occur without significant changes to the underlying crystal structures, consistent with SD.
While the STEM images show the local microstructure in the FIB-defined flake sample, a broader perspective of the bulk microstructure is necessary to confirm these results. Small angle neutron scattering is used as a bulk-technique, which is sensitive to microstructural changes in the proposed length scales but is insensitive to the crystal structure. The platelets of the different phases each have a distinct calculated neutron scattering length density: Cr (3.28 × 10−6 Å−2), Cu (6.55 × 10−6 Å−2), and AlFeNiCo (6.02 × 10−6 Å−2). This difference enables the neutron to diffract from the plates, providing the measured signal. Furthermore, the Cu is largely segregated to the inter-dendrite boundary which is sufficiently large in scale (>1 μm) that it will not show up in the SANS data.
The SANS measurements were performed with in-situ heating from room temperature to 800°C using the Al1.3CoCrCuFeNi sample, presented in Figure 2A. The SANS scattering patterns are plotted as a radial average of the intensity as a function of the scattering vector, Q. All of the SANS patterns show a smoothly changing, Porod-like decay. The size distribution of the microstructural phases was determined by analyzing the SANS patterns using the IRENA package (Ilavsky and Jemian, 2009). This package uses the cross-sectional scattering formula of
Where,
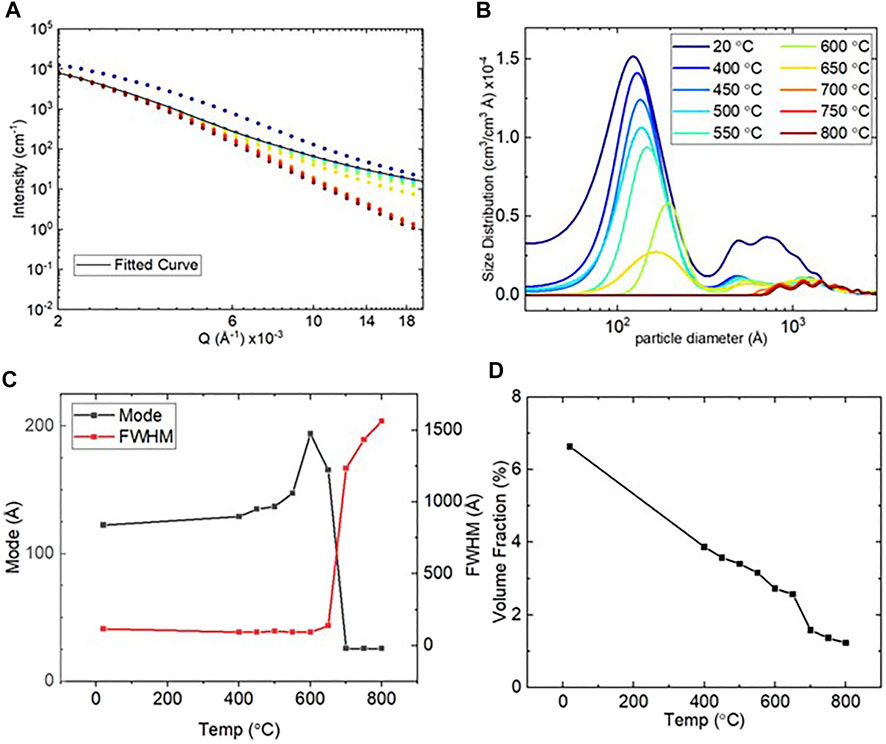
FIGURE 2. (A) The 1D (SANS) for Al1.3CoCrCuFeNi and the size distribution analysis. (B) Size distribution from the IRENA size distribution tool. (C) Trends in the data of the size distribution of mode and full-width at half maximum (FWHM). (D) Volume fraction as percentage.
As the temperature increased to the SD range, at 650°C the distribution of the scattering center sizes increases significantly in width and decreases in their average size. This trend is consistent with a reduction in the periodicity of the plate structure and the merging of the Al, Fe and Ni features seen in the STEM-EDS images in Figure 1. Finally, heating above 650°C, the size distribution is largely flat, indicating the loss of long-range regularity of the plate-like structures.
To summarize the combined SANS and STEM-EDS results, an expected magnetic transition is observed by SANS between 20 and 400°C due to the loss of the magnetic domain structure present at lower temperatures. Subtle changes in the microstructure occur with increasing temperatures between 400 and 600°C; these gradual changes correspond primarily to structures in the 120–200 Å range. The STEM-EDS images corroborate the growth of the nanoscale plate-like microstructure of the sample. At 650°C the STEM-EDS results show that the plates begin to lose their regularity and structure, then at 700°C the sample transforms from an ordered, quasi-oriented structure to a disordered microstructure. The sequence of gradual elemental redistribution, followed by an abrupt microstructural change, strongly suggests that a spinodal transformation occurs in Al1.3CoCrCuFeNi, and likely in other similar alloys, as suggested in the early HEA literature (Wang et al., 2021).
Conclusion
The microstructure evolution of the high-entropy alloy Al1.3CoCrCuFeNi is shown to occur by the precipitation/dissolution of ordered Fe-Cr and Al-Ni nanoplatelet phases. These chemically distinct phases have similar lattice structures and parameters, allowing for a coherent interface between them, but making it difficult to distinguish them by diffraction. The current in-situ measurements (SANS and STEM-EDS) are uniquely sensitive to the chemical phase separation and were used to directly probe this phase transition. Using this sensitivity, the present work provides a direct look at the spinodal decomposition previously proposed. In addition to the SD between the Al-Ni and Fe-Cr phases, Cu-rich and Cr-rich secondary phases are observed to persist throughout the matrix at high temperatures. Throughout the transformation and homogenization process, the sample maintains a similar lattice structure and nearly constant size (Santodonato et al., 2015), implying the transformation is predominantly chemical ordering, with minimal structural contributions.
The current work, together with the previous studies (Yeh et al., 2004; Tong et al., 2005b; Santodonato et al., 2015; Zhang et al., 2016; Butler and Weaver, 2017; Xu et al., 2018), confirms that Al1.3CoCrCuFeNi has a unique structure, consisting of a solid-solution matrix with a large fraction of secondary phases at room temperature, and up to 650°C. The secondary phases arise from both spinodal decomposition and the independent precipitation Cu-rich phases, occurring in stages at different temperatures. These phase separation processes may be used to selectively tune heat treatment for beneficial properties if properly understood and controlled. The coexistence of different formation mechanisms and the coherency of some of the resulting phases provides opportunities to explore property optimization through microstructure control. It has been noted that many important engineering alloys, such as Ni-based superalloys, owe their strength to the presence of coherent precipitates, hence similar features developed in high-entropy alloys may bring extraordinary benefits (Santodonato et al., 2015). It is in this context that the AlxCoCrCuFeNi family of alloys should undergo further scientific and technical study, providing great opportunities for advanced alloy development.
Data Availability Statement
The raw data supporting the conclusion of this article will be made available by the authors, without undue reservation.
Author Contributions
CJ, LD-S, and DG reduced and analyzed the SANS and microscopy data. LS and PL, initiated the research concept and organized the experiments. CJ, LD-S, LS, and DG contributed to the manuscript. LS and RU conducted the in-situ microscopy experiments. LD-S, LS, and KL performed the SANS experiment and helped interpret the data. CK and CL fabricated the sample.
Funding
PL very much appreciates the supports from 1) the National Science Foundation (DMR-1611180 and 1809640) with program directors, J. Yang, G. Shiflet, and D. Farkas and 2) the US Army Research Office (W911NF-13–1-0438 and W911NF-19–2-0049) with program managers, M. P. Bakas, S. N. Mathaudhu, and D. M. Stepp.
Conflict of Interest
The authors declare that the research was conducted in the absence of any commercial or financial relationships that could be construed as a potential conflict of interest.
Publisher’s Note
All claims expressed in this article are solely those of the authors and do not necessarily represent those of their affiliated organizations, or those of the publisher, the editors and the reviewers. Any product that may be evaluated in this article, or claim that may be made by its manufacturer, is not guaranteed or endorsed by the publisher.
Acknowledgments
A portion of this research used resources at the High Flux Isotope Reactor, a DOE Office of Science User Facility operated by the Oak Ridge National Laboratory. The in-situ STEM experiments were conducted at the Center for Nanophase Materials Sciences, which is a DOE Office of Science User Facility. This manuscript has been authored by UT-Battelle, LLC under Contract No. DE-AC05-00OR22725 with the U.S. Department of Energy. The United States Government retains and the publisher, by accepting the article for publication, acknowledges that the United States Government retains a non-exclusive, paid-up, irrevocable, world-wide license to publish or reproduce the published form of this manuscript, or allow others to do so, for United States Government purposes. The Department of Energy will provide public access to these results of federally sponsored research in accordance with the DOE Public Access Plan (http://energy.gov/downloads/doe-public-access-plan).
References
Butler, T. M., and Weaver, M. L. (2017). Investigation of the Phase Stabilities in AlNiCoCrFe High Entropy Alloys. J. Alloys Comp. 691, 119–129. doi:10.1016/j.jallcom.2016.08.121
Duchamp, M., Xu, Q., and Dunin-Borkowski, R. E. (2014). Convenient Preparation of High-Quality Specimens for Annealing Experiments in the Transmission Electron Microscope. Microsc. Microanal 20 (6), 1638–1645. doi:10.1017/S1431927614013476
Gao, M. C., Yeh, J.-W., Liaw, P. K., and Zhang, Y. (2016). High-Entropy Alloys. 1 edn, 1 536. Cham, Switzerland: Springer International.
Giannuzzi, L. A., and Stevie, F. A. (1999). A Review of Focused Ion Beam Milling Techniques for TEM Specimen Preparation. Micron 30 (3), 197–204. doi:10.1016/s0968-4328(99)00005-0
Huang, S., Li, W., Li, X., Schönecker, S., Bergqvist, L., Holmström, E., et al. (2016). Mechanism of Magnetic Transition in FeCrCoNi-Based High Entropy Alloys. Mater. Des. 103, 71–74. doi:10.1016/j.matdes.2016.04.053
Ilavsky, J., and Jemian, P. R. (2009). Irena: Tool Suite for Modeling and Analysis of Small-Angle Scattering. J. Appl. Cryst. 42, 347–353. doi:10.1107/s0021889809002222
Langford, R. M., Huang, Y. Z., Lozano-Perez, S., Titchmarsh, J. M., and Petford-Long, A. K. (2001). Preparation of Site Specific Transmission Electron Microscopy Plan-View Specimens Using a Focused Ion Beam System. J. Vac. Sci. Technol. B 19 (3), 755–758. doi:10.1116/1.1371317
Langford, R. M., and Petford-Long, A. K. (2001). Preparation of Transmission Electron Microscopy Cross-Section Specimens Using Focused Ion Beam Milling. J. Vacuum Sci. Techn. A: Vacuum, Surf. Films 19 (5), 2186–2193. doi:10.1116/1.1378072
Lee, C., Chou, Y., Kim, G., Gao, M. C., An, K., Brechtl, J., et al. (2020a). Lattice‐Distortion‐Enhanced Yield Strength in a Refractory High‐Entropy Alloy. Adv. Mater. 32 (49), 2004029. doi:10.1002/adma.202004029
Lee, C., Kim, G., Chou, Y., Musicó, B. L., Gao, M. C., An, K., et al. (2020b). Temperature Dependence of Elastic and Plastic Deformation Behavior of a Refractory High-Entropy alloy. Sci. Adv. 6 (37), eaaz4748. doi:10.1126/sciadv.aaz4748
Lee, C., Song, G., Gao, M. C., Feng, R., Chen, P., Brechtl, J., et al. (2018). Lattice Distortion in a strong and Ductile Refractory High-Entropy alloy. Acta Materialia 160, 158–172. doi:10.1016/j.actamat.2018.08.053
Miracle, D. B., and Senkov, O. N. (2017). A Critical Review of High Entropy Alloys and Related Concepts. Acta Materialia 122, 448–511. doi:10.1016/j.actamat.2016.08.081
Ohmura, T., Tsuzaki, K., Sawada, K., and Kimura, K. (2006). Inhomogeneous Nano-Mechanical Properties in the Multi-phase Microstructure of Long-Term Aged Type 316 Stainless Steel. J. Mater. Res. 21 (5), 1229–1236. doi:10.1557/jmr.2006.0143
Pan, Q., Zhang, L., Feng, R., Lu, Q., An, K., Chuang, A. C., et al. (2021). Gradient Cell-Structured High-Entropy alloy with Exceptional Strength and Ductility. Science 374 (6570), 984–989. doi:10.1126/science.abj8114
Prasher, M., Sen, D., Bahadur, J., Tewari, R., and Krishnan, M. (2019). Correlative SANS and TEM Investigation on Precipitation Kinetics of H-phase in Ni50.3Ti29.7Hf20 High Temperature Shape Memory alloy. J. Alloys Comp. 779, 630–642. doi:10.1016/j.jallcom.2018.11.303
Santodonato, L. J., Liaw, P. K., Unocic, R. R., Bei, H., and Morris, J. R. (2018). Predictive Multiphase Evolution in Al-Containing High-Entropy Alloys. Nat. Commun. 9, 4520. doi:10.1038/s41467-018-06757-2
Santodonato, L. J., Zhang, Y., Feygenson, M., Parish, C. M., Gao, M. C., Weber, R. J. K., et al. (2015). Deviation from High-Entropy Configurations in the Atomic Distributions of a Multi-Principal-Element alloy. Nat. Commun. 6, 5964. doi:10.1038/ncomms6964
Singh, S., Wanderka, N., Murty, B. S., Glatzel, U., and Banhart, J. (2011). Decomposition in Multi-Component AlCoCrCuFeNi High-Entropy alloy. Acta Materialia 59, 182–190. doi:10.1016/j.actamat.2010.09.023
Tang, Z., Senkov, O. N., Parish, C. M., Zhang, C., Zhang, F., Santodonato, L. J., et al. (2015). Tensile Ductility of an AlCoCrFeNi Multi-phase High-Entropy alloy through Hot Isostatic Pressing (HIP) and Homogenization. Mater. Sci. Eng. A 647, 229–240. doi:10.1016/j.msea.2015.08.078
Tong, C.-J., Chen, M.-R., Yeh, J.-W., Lin, S.-J., Chen, S.-K., Shun, T.-T., et al. (2005a). Mechanical Performance of the Al X CoCrCuFeNi High-Entropy alloy System with Multiprincipal Elements. Metall. Mat Trans. A. 36 (5), 1263–1271. doi:10.1007/s11661-005-0218-9
Tong, C.-J., Chen, Y.-L., Yeh, J.-W., Lin, S.-J., Chen, S.-K., Shun, T.-T., et al. (2005b). Microstructure Characterization of Al X CoCrCuFeNi High-Entropy alloy System with Multiprincipal Elements. Metall. Mat Trans. A. 36, 881–893. doi:10.1007/s11661-005-0283-0
Wang, X., Guo, W., and Fu, Y. (2021). High-entropy Alloys: Emerging Materials for Advanced Functional Applications. J. Mater. Chem. A. 9 (2), 663–701. doi:10.1039/d0ta09601f
Wang, Y. P., Li, B. S., and Fu, H. Z. (2009). Solid Solution or Intermetallics in a High-Entropy Alloy. Adv. Eng. Mater. 11 (8), 641–644. doi:10.1002/adem.200900057
Welk, B. A., Williams, R. E. A., Viswanathan, G. B., Gibson, M. A., Liaw, P. K., and Fraser, H. L. (2013). Nature of the Interfaces between the Constituent Phases in the High Entropy alloy CoCrCuFeNiAl. Ultramicroscopy 134, 193–199. doi:10.1016/j.ultramic.2013.06.006
Wignall, G. D., Littrell, K. C., Heller, W. T., Melnichenko, Y. B., Bailey, K. M., Lynn, G. W., et al. (2012). The 40 M General Purpose Small-Angle Neutron Scattering Instrument at Oak Ridge National Laboratory. J. Appl. Cryst. 45, 990–998. doi:10.1107/S0021889812027057
Xu, X. D., Liu, P., Tang, Z., Hirata, A., Song, S. X., Nieh, T. G., et al. (2018). Transmission Electron Microscopy Characterization of Dislocation Structure in a Face-Centered Cubic High-Entropy alloy Al0.1CoCrFeNi. Acta Materialia 144, 107–115. doi:10.1016/j.actamat.2017.10.050
Yeh, J.-W., Chen, S.-K., Lin, S.-J., Gan, J.-Y., Chin, T.-S., Shun, T.-T., et al. (2004). Nanostructured High-Entropy Alloys with Multiple Principal Elements: Novel alloy Design Concepts and Outcomes. Adv. Eng. Mater. 6, 299–303. doi:10.1002/adem.200300567
Zhang, C., Zhang, F., Diao, H., Gao, M. C., Tang, Z., Poplawsky, J. D., et al. (2016). Understanding Phase Stability of Al-Co-Cr-Fe-Ni High Entropy Alloys. Mater. Des. 109, 425–433. doi:10.1016/j.matdes.2016.07.073
Zhang, Y., Zuo, T. T., Tang, Z., Gao, M. C., Dahmen, K. A., Liaw, P. K., et al. (2014). Microstructures and Properties of High-Entropy Alloys. Prog. Mater. Sci. 61, 1–93. doi:10.1016/j.pmatsci.2013.10.001
Keywords: high-entropy alloy (HEA), in situ, spinodal decomposition, microstructure, SANS (small-angle neutron scattering)
Citation: Jorgensen CS, Santodonato LJ, Littrell KC, Kuo CH, Lee C, Unocic RR, Liaw PK, Gilbert DA and DeBeer-Schmitt LM (2022) In-Situ Study of Microstructure Evolution of Spinodal Decomposition in an Al-Rich High-Entropy Alloy. Front. Mater. 9:827333. doi: 10.3389/fmats.2022.827333
Received: 01 December 2021; Accepted: 01 March 2022;
Published: 25 March 2022.
Edited by:
Dongchan Jang, Korea Advanced Institute of Science and Technology, South KoreaReviewed by:
Venkata Sai Kiran Chakravadhanula, Skyroot Aerospace Private Limited, IndiaSongqin Xia, North China Electric Power University, China
Copyright © 2022 Jorgensen, Santodonato, Littrell, Kuo, Lee, Unocic, Liaw, Gilbert and DeBeer-Schmitt. This is an open-access article distributed under the terms of the Creative Commons Attribution License (CC BY). The use, distribution or reproduction in other forums is permitted, provided the original author(s) and the copyright owner(s) are credited and that the original publication in this journal is cited, in accordance with accepted academic practice. No use, distribution or reproduction is permitted which does not comply with these terms.
*Correspondence: Lisa M. DeBeer-Schmitt, ZGViZWVyc2NobWxtQG9ybmwuZ292