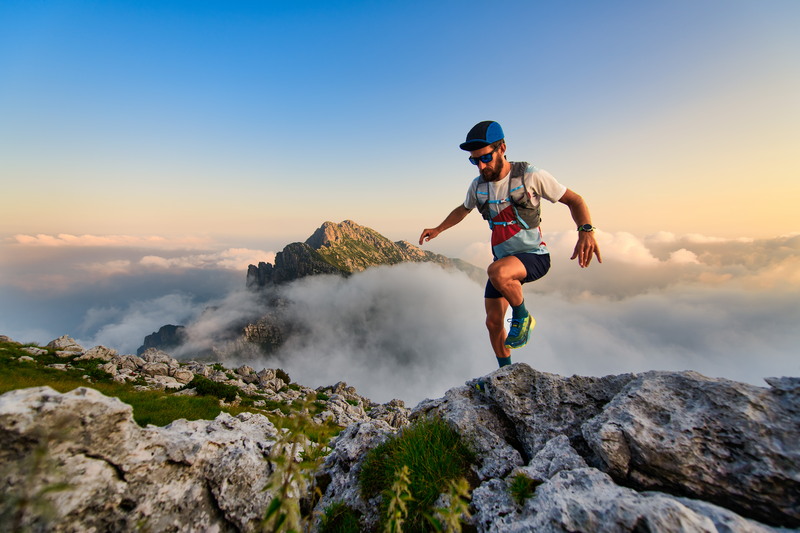
95% of researchers rate our articles as excellent or good
Learn more about the work of our research integrity team to safeguard the quality of each article we publish.
Find out more
REVIEW article
Front. Mater. , 14 March 2022
Sec. Carbon-Based Materials
Volume 9 - 2022 | https://doi.org/10.3389/fmats.2022.810575
This article is part of the Research Topic Horizons in Materials View all 10 articles
In the era of renewable technologies and clean processes, carbon science must adapt to this new model of a green society. Carbon materials are often obtained from petroleum precursors through polluting processes that do not meet the requirements of sustainable and green chemistry. Biomass is considered the only renewable source for the production of carbon materials, as the carbon in biomass comes from the consumption of carbon dioxide from the atmosphere, resulting in zero net carbon dioxide emissions. In addition to being a green source of carbon materials, biomass has many advantages such as being a readily available, large and cheap feedstock, as well as the ability to create unique carbon-derived structures with well-developed porosity and heteroatom doping. All these positive aspects position biomass-derived carbon materials as attractive alternatives in multiple applications, from energy storage to electrocatalysis, via adsorption and biosensors, among others. This review focuses on the application of phenolic resins to the production of electrodes for energy storage and the slow but inexorable movement from petroleum-derived phenolic compounds to biosourced molecules (i.e., lignins, tannins, etc.) as precursors for these carbon materials. Important perspectives and challenges for the design of these biosourced electrodes are discussed.
Most countries have signed the Paris Agreement on climate change, with the intention of avoiding a global temperature increase of 1.5°C above pre-industrial levels (Paris Agreement to the United Nations Framework Convention on Climate Change, 2015). According to the IPCC report (IPCC, 2021: Climate Change 2021), the risk of not being able to slow the rate of temperature increase would threaten human life and environmental health worldwide. This fact encourages society toward a governmental and social movement that involves net zero emissions in the coming years. This movement should also be accompanied by the growth of clean and renewable energy technologies. In this context, multiple green technologies have been presented as attractive alternatives to replace fossil fuel-based energy (Du and Li, 2019). Electrochemistry is at the forefront of this renewable movement since most of these technologies are based on electrochemical processes and reactions (Ganiyu and Martínez-Huitle, 2020). Fuel cells (Ganiyu and Martínez-Huitle, 2020; Sazali et al., 2020; Neatu et al., 2021), supercapacitors (Muzaffar et al., 2019; Pomerantseva et al., 2019; Poonam et al., 2019), batteries (Mauger et al., 2019; Xu et al., 2020; Liu et al., 2021) and electrolyzers (Abbasi et al., 2019; Brauns and Turek, 2020), among others, are electrochemical devices that are among the most innovative suppliers of energy and chemicals.
Carbon materials have been proposed as excellent low-cost electrodes for all these electrochemical devices due to their unique properties, such as high availability, large developed porosity, wide variety of pore size distributions, tunability of surface chemistry, high conductivity, excellent chemical and thermal stability, etc. (Quílez-Bermejo et al., 2020a; Castro-Gutierrez et al., 2020; Wu et al., 2020; Yin et al., 2020). Nevertheless, carbon materials chemistry, and carbon science in general, must adapt immediately to the rapid changes facing our society. Traditional methods of preparing carbon materials are often based on thermal processing of petrochemical precursors (Liu W.-J. et al., 2015; Titirici et al., 2015; Yahya et al., 2015; Ma et al., 2017; Lan et al., 2021). This is a huge problem because, despite their use in renewable technologies, most of the carbon electrodes in these devices are still produced from fossil fuels, which does not solve the problematic issue of polluting emissions. If the ultimate goal is to use technologies with fully environmentally friendly equipment, the renewable production of carbon materials is mandatory.
A branch of carbon science and technology involves the preparation of carbon materials from phenolic resins (Effendi et al., 2008; Celzard and Fierro, 2020; Szczesniak et al., 2020; Torres et al., 2021). Phenolic resins are synthetic polymeric compounds that are obtained from the condensation reaction of phenolic molecules with or without a crosslinking agent (Sarika et al., 2020). Such resins are excellent precursors for carbon materials since the selection of phenolic molecules and crosslinkers allows excellent control of the properties of the resulting carbon materials. Nevertheless, it is worth noting that phenolic precursors and crosslinkers are commonly obtained from petrochemical precursors that involve polluting processes (European Chemicals Agency, 2021a; European Chemicals Agency, 2021c; European Chemicals Agency, 2021d). Due to the high levels of pollution in recent years, new renewable alternatives have been proposed to replace petroleum precursors to produce carbon materials derived from phenolic molecules (Nieuwenhove et al., 2020; Sarika et al., 2020; Sternberg et al., 2021).
Biomass-derived carbon precursors are considered the only renewable carbon source since the carbon emissions released during thermal processing of biomass were previously consumed from the atmosphere during biomass growth (Forest Research 2021). This means that biomass absorbs anthropic carbon dioxide emissions while growing and releases them back into the atmosphere during carbon materials production. Therefore, the carbon cycle remains closed with zero net emissions while synthesizing a value-added product. This closed cycle can be very useful for preparing carbon materials derived from phenolic resins since the phenolic and crosslinking components can be found in nature as biomass feedstocks (Foyer et al., 2016; Nieuwenhove et al., 2020; Sarika et al., 2020; Sternberg et al., 2021). Biomass represents a large amount of natural reservoirs of carbon, including agricultural crops, plants, forest residues or materials, and industrial or domestic biowastes, among others. The nature, composition, structure and other features of these biosourced precursors have been widely detailed in extensive reviews (Jian et al., 2018; Li et al., 2019; Szczesniak et al., 2020).
In this review, we aim to summarize the most fundamental advances in the preparation of carbon electrodes from biosourced phenolic molecules in the quest for the non-dependence on fossil fuels. This review does not provide a detailed overview but shows the extensive possibilities of carbon materials derived from biosourced phenolic molecules as electrodes for energy storage and conversion applications.
Phenolic resins, of which the best known are phenol-formaldehyde resins, are primarily based on two main components: phenolic and aldehyde structural units. The phenolic units react with the crosslinkers in ortho- or para- position, leading to a condensed product, the phenolic resin, whose characteristics depend on phenol/aldehyde ratio, the phenol and aldehyde precursors and the synthesis conditions, in particular the pH (Grenier-Loustalot et al., 1994; Effendi et al., 2008). Regarding phenolic and aldehyde precursors, it is important to emphasize that phenol and formaldehyde are the most common raw materials for the preparation of phenolic resins.
The reaction mechanisms for the formation of phenol-formaldehyde resins have been extensively studied in the literature since their discovery in 1907, and multiple works can be found regarding the proposed mechanisms (Yeddanapalli and Francis, 1962; Grenier-Loustalot et al., 1994; Pilato, 2013). The first step of the mechanism is attributed to the formaldehyde substitution in ortho- or para- positions in the phenolic ring, leading to the possible formation of mono-, di-, and tri-functionalized phenol monomer, which is thought to be mainly related to the phenol/formaldehyde ratio during synthesis. Then, the second step of the mechanism involves polymeric reactions between the monomeric products through condensation processes. Such processes have been shown to be highly dependent on pH (Pizzi and Stephanou, 1994). Under alkaline conditions, the bonds between the monomers are based on methylene-type (-CH2-) bridging bonds, while in neutral or acid environments, ether-type (-CH2-O-CH2-) bridging bonds can also be found.
All the parameters that influence the synthesis are of paramount importance to adapt the properties of phenolic resins. The high process tunability (pH, temperature, precursor ratios, etc.) makes them of prime interest for a wide range of applications: aerospace industry, adhesives, coatings, and high-yield precursors for the preparation of carbon materials, among others (Celzard and Fierro, 2020). However, one of the main concerns about phenolic resins is their production from petrochemical feedstocks (European Chemicals Agency, 2021a; European Chemicals Agency, 2021c; European Chemicals Agency, 2021d). On the one hand, 95% of the world’s phenol production is based on the cumene process (Zakoshansky, 2007), which involves the partial oxidation of benzene and propylene to obtain phenol and acetone. Benzene and propylene are highly polluting petrochemical raw materials (European Chemicals Agency, 2021b; European Chemicals Agency. Propene). On the other hand, although crosslinker-free resins exist (Celzard and Fierro, 2020), the most common preparation of carbon materials from phenolic molecules involves the reaction between the phenolic groups and formaldehyde (Grenier-Loustalot et al., 1994; Zhang et al., 2015; Foyer et al., 2016). Unfortunately, formaldehyde is also considered a pollutant since it is obtained from hydrocarbons such as methanol (European Chemicals Agency, 2021a). The presence of formaldehyde in the air can have dangerous consequences for human health (European Chemicals Agency, 2021a).
Biosourced precursors of phenolic resins have been explored over the last decades in the search for fully green technologies. This section reviews the most common bio-based precursors of phenolic molecules (lignin and tannins), including structure, properties and role in bio-resins. Moreover, crosslinker-free resins and bio-based crosslinker components will also be studied in this section.
Lignin is an amorphous 3D phenolic polymer composed mainly of three structural units: p-hydroxyphenyl (H), guaiacyl (G) and syringyl (S) (Figure 1). Lignin is one of the largest components of plant matter, along with cellulose and hemicellulose. However, unlike the other two, lignin is the only component with aromatic properties and carbon contents above 60 wt%, making it desirable for the development of carbon materials (Fierro et al., 2005, 2006). Lignin is a highly heterogeneous polymer that plants naturally produce through the consumption of carbon dioxide followed by the formation of carbohydrates through the photosynthesis (Hu, 2002).
As commented above, phenol-formaldehyde resins do not necessarily involve the use of pure phenol as the phenolic component. Lignin can serve as a substitute for phenol molecules in these resins (Sellers et al., 2004; Hu et al., 2011; Nieuwenhove et al., 2020). The structural units of lignin are based on phenol-like moieties, which can interact with aldehydes in a form similar to phenol-formaldehyde resins (Figure 1). Assuming that lignin-aldehyde resins are formed through the same mechanism and that the para- positions of phenolic rings in lignin are occupied, the reaction can only take place through the ortho- position of H and G moieties of lignin via methylene or ether bridging bonds. At the same time, S-type groups would not be able to interact in such crosslinking reactions (Xu and Ferdosian, 2017; Wang Y.-Y. et al., 2020).
The main problem with lignin as a phenol-type component in phenolic resins is its considerable molecular weight and complex, stable structure, which results in low reactivity of the lignin feedstock. In order to increase the reaction rate, lignin is often purified and chemically modified by methylolation (Peng et al., 1993; Vázquez et al., 1997), phenolation (Jiang et al., 2018) and demethylation (Song et al., 2016; Wang et al., 2019) reactions. Without applying modifications to the non-reactive raw structure, the use of lignin as a phenolic component is severely hampered. After these chemical modifications, large amounts of phenol [up to 100% of lignin-based resins (Kalami et al., 2017)] were successfully substituted by lignin components in phenol-formaldehyde resins (Zhang et al., 2013; Kalami et al., 2017). Interestingly, lignin has also been shown to react with glyoxal (as a crosslinker) to form lignin-based phenolic resins without using phenol and formaldehyde in the formulation (Kumar et al., 2021).
Tannins are complex polyphenolic biomolecules found in plant materials, especially in dicotyledonous plants. After lignin, tannins are the second most abundant aromatic compound in biomass, with a high carbon content. However, tannin composition highly depends on the plant source. High tannin concentration has been reported in mimosa, quebracho, pine and chestnut. Nevertheless, despite the heterogeneous nature of tannins, these can be classified into three different groups according to their structural units; 1) hydrolysable tannins, 2) condensed tannins and 3) complex tannins (Gross, 1999; Kahnbabaee and Van-Ree, 2001).
Condensed tannins (also known as flavan-3,4-diol-derived tannins) are another important renewable substitute for phenol in phenolic resins. The monomers of condensed tannins is based on flavonoid units, which are formed by a heterocyclic ring linking two phenolic rings: the A ring and the B ring (Figure 2).
The use of tannin as a phenolic-type component has been widely demonstrated in the scientific literature through the formation of multiple tannin-formaldehyde resins (Amaral-Labat et al., 2013; Pizzi et al., 2013; Lagel et al., 2014; Li et al., 2016). Due to their phenolic moieties, these tannin-derived substances indeed undergo the same kind of reaction mechanisms with aldehydes. Such reactions are mainly based on the polymerization of flavonoid units with formaldehyde through -C-C- and -C-O-C bridging bonds (Figure 3) (Gross, 1999; Kahnbabaee and Van-Ree, 2001), similar to the original phenol-formaldehyde resins.
Not only that, many different derivatives can be obtained through organic reactions between condensed tannins and other compounds. Tannins have proven to be able to react with amines to obtain polycondensed resins (Delgado-Sánchez et al., 2017). Some recent work shows that in alkaline or acidic solution, the reaction mechanism proceeds through 1) the reaction of the amine and the phenolic-type component and 2) the formation of ionic bonds between the protonated amino groups and the hydroxyl groups of the flavonoid structure of the tannin (Santiago-Medina et al., 2017). Biosourced tannin resins have also been obtained from the reaction between tannin and furfuryl alcohol with glyoxal, a crosslinker that is much less toxic and much less volatile than formaldehyde (Lacoste et al., 2013).
However, one of the most exciting tannin-based preparation is the one obtained by the self-condensation of these organic molecules (Pizzi et al., 1995; Pizzi, 2008; Basso et al., 2014). Unlike simple phenolic molecules, condensed tannins are also prone to self-condensation reactions through methylene or ether bridging bonds in alkaline and acids (Pizzi et al., 1995). The mechanism of self-condensation is well-known; tannins react through three different reactions that are: 1) degradation of tannins to lower molecular weight compounds, such as catechin, 2) condensation reaction by hydrolysis of aromatic rings, and 3) formation and reaction of free radicals in the presence of air. This feature makes tannins one of the few phenolic-type molecules capable of producing phenolic resins without the presence of additional crosslinkers, leading to tannin-only resins.
Lignin and tannins are the main substitutes for phenol in phenol-formaldehyde resins. In the case of aldehyde components, hydroxymethylfurfural (HMF) represents the main biosourced alternative to replace formaldehyde (Sarika et al., 2020). HMF is an aromatic aldehyde found in sugars, fruits, coffee, flavoring agents and other carbohydrate polymers. It is usually synthesized from cellulose and lignocellulose using ionic liquids and/or organic solvents (Stahlberg et al., 2011; Zakrzewska et al., 2011).
HMF has proven to be an effective substitute for formaldehyde in the manufacture of “green” phenolic resins, in which the production of polluting formaldehyde emissions is avoided (Zhang et al., 2016a). The use of HMF in fully “green” resins have already been demonstrated: phenol was replaced by lignin derivatives, while formaldehyde was substituted by HMF, resulting in a green phenolic resin with interesting properties in terms of thermal stability and mechanical strength (Zhang et al., 2016b). Nevertheless, HMF is not the only biosourced crosslinker. Other formaldehyde substitutes have proven to be helpful for the formation of phenolic resin with excellent properties. Among all the aldehyde-type alternatives, the role of furfural (Oliveira et al., 2008; Zhang et al., 2020), furfuryl alcohol (Cheng et al., 2018), glyoxal (Ramires et al., 2010) and vanillin (Foyer et al., 2016) should be highlighted. If readers are looking for more details on biosourced precursors to phenolic resins, we encourage them to read the following scientific literature (Sarika et al., 2020).
The high carbon content and low cost of biosourced phenolic molecules and the resultant phenolic resins make them an attractive alternative to petrochemical compounds for producing carbon materials. The variety of phenolic and crosslinking precursors (if used) and their extensive properties make them a potential material for the production of carbons with different chemical and structural properties, such as porosity, carbon and oxygen content, heteroatom doping, electrical conductivity or thermal stability. The following section briefly summarizes the most common methodologies for producing carbon materials from phenolic compounds and resins.
The most widely used method for the production of carbon materials is based on high-temperatures heat treatment of precursors in an oxygen-free atmosphere. These high temperatures promote condensation reactions of chains of phenolic molecules or resins (Meng et al., 2006; Muylaert et al., 2012). Prior to carbonization processes, a standard methodology for increasing the carbonization yield is a well-known curing process (Meng et al., 2006; Muylaert et al., 2012). The curing process uses heat treatments at moderate temperatures in an air atmosphere to promote crosslinking reactions of the phenolic structure. After the pre-treatment, high-temperature carbonization is applied (Meng et al., 2006; Muylaert et al., 2012). This procedure consists of the thermal degradation of carbon precursors by heating in an inert atmosphere at temperatures above 300°C, leading to the conversion of the phenolic matrix into highly disordered carbon (Ko et al., 2000). Such conversion involves multiple reactions at high temperature: crosslinking, dehydration, isomerization and condensation (Trick and Saliba, 1995). The mechanism of pyrolysis of phenolic resins is well established: 1) formation of additional crosslinks, 2) scission of these crosslinks, and 3) polycyclic aromatization (Jiang et al., 2012). As a result of phenolic resin decomposition, water vapor, hydrogen, methane and carbon monoxide emissions are produced during thermal processing (Trick and Saliba, 1995).
The properties of the carbon material depend on the heat-treatment temperature, heating rate, residence time, flow rate, and phenolic and crosslinking precursors. As with other biomass precursors, to achieve high carbonization yields, a rather slow heating rate is preferable. Otherwise, rapid carbonization leads to volatilization of most of the biomass and production of bio-oils, and thus to low carbonization yields (Szczesniak et al., 2020).
With respect to the previously mentioned biosourced phenolic resins, it is worth noting that tannin-derived carbon materials have been prepared extensively through the carbonization of self-condensed tannins and tannin-aldehyde resins (Celzard and Fierro, 2020). The properties of such carbons have been tailored through heating temperature, heating rate, etc., but the non-graphitizable structure remains present regardless of the carbonization parameters. Moreover, tannins alone have been shown to be a promising precursor for obtaining carbon materials with excellent properties in terms of porosity (SNLDFT = 770 m2 g−1), without requiring any additional crosslinking procedures, thereby avoiding any additional steps related to the formation of phenolic resins (Jagiello et al., 2019). In the case of lignin, the properties of lignin-derived carbon materials are also highly dependent on carbonization conditions. Lignin has been used as a phenolic substitute in resins for subsequent carbon materials (Simitzis and Sfyrakis, 1993; Guo et al., 2015; Zhang et al., 2018; Castro-Díaz et al., 2019). The heat-treatment temperature was found to be of paramount importance in the apparent surface area of carbon materials since the same lignin precursor shows 496 m2 g−1 at 500°C and 278 m2 g−1 at 900°C at a heating rate of 10°C·min−1 (Rodríguez-Mirasol et al., 1993a; 1993b). This effect of the temperature is related to the constriction of micropores when increasing the treatment temperature at such a high heating rate (Rodríguez-Mirasol et al., 1993a; 1993b). However, treatment at the same temperatures at a heating rate of 2.5°C·min−1 shows the opposite trend. The higher the treatment temperature, the higher the apparent surface area of the carbon materials (Xie et al., 2009), which also highlights the relevance of the heating rate.
Hydrothermal carbonization, also known as aqueous carbonization or wet pyrolysis, is an alternative method for producing carbon materials from phenolic resins under milder conditions. The most common hydrothermal carbonization is done under subcritical conditions, which involves thermal treatment of a carbon precursor at temperatures between 150 and 350°C in a pressure vessel in the presence of water (or other aqueous solvents). In this temperature and pressure range, ionization of water occurs, which promotes hydrolysis of organic compounds. Besides, this process can be further accelerated by the presence of acids in the solution. The reaction mechanisms of hydrothermal carbonization are still contradictory because they seem to depend strongly on the carbon precursor. Nevertheless, there is a general consensus that hydrothermal carbonization involves dehydration, decarboxylation, aromatization and condensation reactions, which govern the structural arrangement of the resultant carbon materials, also called hydrochars (Mohamed et al., 2017; Nizamuddin et al., 2017).
This methodology for producing carbon materials from phenolic resins is less standard than conventional carbonization. Nevertheless, there is a large number of publications reporting phenolic resins-derived carbon nanospheres (Xu and Guo, 2013), fibers (Fei et al., 2015), ordered mesoporous carbons (Yu and So, 2019), etc., obtained by hydrothermal method.
It is also worth mentioning that lignin and tannins are widely used to prepare carbon materials by hydrothermal carbonization without prior formation of phenolic resins, as these two kinds of organic molecules can produce carbon materials with excellent properties. Tannins are especially attractive for the preparation of carbon materials by hydrothermal methods because they are soluble in water. This facilitates condensation and dehydration reactions in hot pressurized water, leading to high hydrothermal yields near 60% (Braghiroli et al., 2014). Furthermore, this methodology is desirable for doping with heteroatoms since heteroatom precursors can also be introduced in the hydrothermal equipment. Following this approach, apparent surface areas of 500 m2 g−1 and nitrogen content above 8 at% were obtained in tannin-derived hydrothermal carbons (Braghiroli et al., 2015). In hydrothermal carbons derived from biomass under mild conditions, the most common nitrogen species are edge-type functionalities, such as imines and amines. However, more aggressive conditions are needed to obtain heterocyclic-type nitrogen groups, such as pyridines, pyrroles and graphitic nitrogen (Zhuang et al., 2018). The same principle of nitrogen doping can be used to complex transition metals and, therefore, to form metal-carbon hybrids.
On the other hand, lignin-based carbons have also been obtained by hydrothermal carbonization (Kang et al., 2013), with promising hydrothermal pyrolysis yields up to 66 wt% (Li et al., 2021). Carbon dots with photoluminescence emissions were obtained from hydrothermal carbonization of lignin in the presence of a small amount of hydrogen peroxide at 180°C. H2O2 act as an oxidizing agent that functionalizes the lignin-derived carbon domains during hydrothermal treatment (Chen et al., 2016). The functionalization involves the formation of oxygen groups and the creation of defects on the surface of the carbon dots. These can act as excitation energy traps, which may be responsible for the photoluminescence behavior (Chen et al., 2016).
Activation processes are not strictly speaking synthetic routes to produce carbon materials, but a promising pathway to modulate the microporosity and nanostructure of carbon materials derived from phenolic compounds. There are two types of activation processes: 1) chemical activation, and 2) physical activation (Marsh and Rodríguez-Reinoso, 2006).
Chemical activations involve the use of chemical activating agents, such as KOH, NaOH, and H3PO4 (Marsh and Rodríguez-Reinoso, 2006; Pérez-Mayoral et al., 2021; Pérez-Rodríguez et al., 2021). These activating agents are mixed with the carbon precursors, followed by thermal treatment at temperatures of 350–900°C. The mechanisms of chemical activation with KOH and NaOH have been widely studied. KOH (or NaOH) reacts with carbon materials at about 400°C to form K2CO3 (Lillo-Rodenas et al., 2003). At temperatures above 700°C, potassium (or sodium) carbonate decomposes into K2O (or Na2O) and CO2. At this high temperature, CO2 can also interact with the carbon matrix through oxidation of the carbon material to produce two CO molecules. In addition, K2O or K2CO3 can also be reduced by the carbon network to produce metallic K, leading to the removal of carbon atoms.
Besides alkaline agents, acidic solvents can also be used during the activation process. Although many acidic agents have been used (Legrouri et al., 2004; Sanchez et al., 2006; Liu et al., 2011; Gao et al., 2020), the most widely used acidic activation agent is H3PO4 (Molina-Sabio et al., 1996; Jagtoyen and Derbyshite, 1998; Puziy et al., 2003). H3PO4 operates by different mechanisms than NaOH and KOH. The carbon material and acid solution are mixed and subjected to heat treatment at temperatures between 350 and 700°C. The proposed mechanism of acid activation is as follows: evaporation of the acidic agent leads to depolymerization and dehydration reactions of the polymeric materials. Then, the volatile by-products of the reaction between H3PO4 and the carbon material decompose, releasing cavities and pores (Gao et al., 2020). Chemical activations with acidic agents of biosourced phenolic molecules have generated significant developments of microporosity in carbon materials, reaching surface areas of nearly 3,000 m2 g−1 (Fierro et al., 2008). Nevertheless, by regulating the acid concentration, many surface areas can also be obtained (Gao et al., 2020).
On the other hand, physical activation consists of a two-step process: 1) carbonization of the carbon precursor, and 2) high-temperature treatment (500–900°C) in the presence of oxidizing agents, such as air, water vapor or CO2 (Marsh and Rodríguez-Reinoso, 2006; Din et al., 2017; Heidarinejad et al., 2020; Pérez-Mayoral et al., 2021). These gases consume the carbon material creating microchannels in the carbonaceous structure. Carbons subjected to physical activation develop a large surface area due to the formation of micropores. Depending on the physical agent, the microporosity can be modulated. The use of CO2 results in narrower micropores, whereas the use of steam leads to a broader pore size distribution with a lower content of micropores (Pérez-Mayoral et al., 2021).
Among all activating agents, CO2 is by far the most common in physical activations, whose reaction mechanisms have been widely explained according to the following reaction:
This means that the carbon material reduces the CO2 molecule while the carbon material is oxidized, producing two carbon monoxide molecules and eliminating one carbon atom from the surface. Such physical activation has been widely applied to obtain carbon materials from biosourced phenolic molecules (Doney et al., 2009; Xue et al., 2011).
The main limitation of the above carbonization processes is the lack of control over the porosity of the resultant carbon materials. Carbonization in the presence of templates is a powerful strategy to produce carbon materials with accurate control of pore structure and size distribution. In order to prepare carbon materials with a well-defined pore structure, one attractive strategy, known as hard-templating, is to replicate a template material that already has a well-ordered structure (Muylaert et al., 2012; Wang H. et al., 2020; Xie et al., 2020; Díez et al., 2021). Thus, the carbon precursor is deposited chemically (Jun et al., 2009) or electrochemically (Quílez-Bermejo et al., 2020b) as the inverse template structure, filling the pores of the pristine template structure. For carbon materials derived from phenolic resins, the template cannot only be added during carbonization but also during the formation of the phenolic resins (Muylaert et al., 2012). Therefore, porosity control can be overcome early in resin production or during pyrolysis of carbon precursors. This approach has been widely applied to obtain ordered mesoporous carbons (OMCs) from biosourced phenolic compounds (Fierro et al., 2013; Salinas-Torres et al., 2016; Xi et al., 2020). The main limitation of this approach is the need for an additional step to remove the template from the composition of the material, which often involves the use of hazardous and toxic chemicals, such as hydrofluoric acid or high concentrations of sodium hydroxide.
The second template method, known as soft-templating, involves cooperative assembly between an amphiphilic templating agent and the carbon precursor. This is the most common method for obtaining carbon materials of phenolic origin (Szczesniak et al., 2020). In general, in soft-templating, the templating agent consists of surfactants or copolymers and the carbon precursor is based on phenolic precursors. The mixture of the components and a solvent leads to a mesophase that is heated to produce well-ordered carbon materials. At the same time, the templating agent is removed by heat treatment (Muylaert et al., 2012; Nita et al., 2016; Choma et al., 2020). Compared to hard-templating, the main advantage of this methodology is the lack of need for corrosive compounds to remove the template from the final carbon material. After pyrolysis at temperatures above 400°C, the soft template is completely eliminated, releasing the porosity of the resultant carbons.
In soft-template methods for the formation of phenolic-derived carbons, some factors are of paramount importance, especially the effect of pH (Meng et al., 2006; Huang et al., 2009; Xie et al., 2011; Renda and Bertholdo, 2018). In a basic medium, phenolic moieties are deprotonated by the action of the OH− anions, which leads to the formation of phenolate anions. Then, these anions interact with the surfactant. The resultant polymer has large amounts of hydroxyl groups that strengthen the template-resin interaction through hydrogen bonding.
These hard- and soft-templating methodologies have been widely applied to bio-based phenolic resins. Furthermore, carbon materials by templating directly from biosourced phenolic molecules have proven to be an effective way to produce well-ordered carbon materials, especially from tannins (Figure 4) and triblock copolymers such as Pluronic® (Castro-Gutierrez et al., 2018, 2021a; Sanchez-Sanchez et al., 2018). These ordered carbon materials show outstanding properties not only for electrochemical applications (Celzard and Fierro, 2020), as discussed in the next section, but also for adsorption (Nelson et al., 2016; Canevesi et al., 2020; Zhao et al., 2020), hydrogen storage (Schaefer et al., 2016) or even molecular sieving of alkanes (Castro-Gutierrez et al., 2021b). Lignin-derived ordered carbon materials obtained by template methods have also shown excellent properties in catalysis (Gan et al., 2019; Wang X. et al., 2020) or adsorption (Xie et al., 2019).
FIGURE 4. Bright-field TEM micrographs of transverse and longitudinal views of well-ordered mesoporous carbon materials obtained by soft-templating of tannins [Reprinted with permission from (Castro-Gutierrez et al., 2018)].
Mechanosynthesis has emerged in recent years as a promising methodology to simplify all the above-mentioned synthetic protocols (Suryanarayana, 2001; James et al., 2012). Mechanochemical synthesis has the advantage of using mechanical forces to produce the reaction instead of using hazardous chemicals or high temperatures and pressures as in conventional procedures (Figure 5).
FIGURE 5. Schematic representation of the ball motion inside the ball-milling and illustration of deformation and reaction in mechanochemical processes (Xu et al., 2015).
Mechanosynthesis is based on milling processes in which the mechanical energy of motion is transferred to the precursor through abundant collisions (Margetic and Strukil, 2016). Depending on the mechanical forces, elastic or plastic deformation can be achieved (Figure 5) (Xu et al., 2015). If the mechanical forces are not strong enough, the kinetics transferred to the reagents only provides energy to reduce the size of the carbon particles. However, if the energy is high enough, the organic reactants can be chemically altered through the cleavage of chemical bonds (Figure 5) (James et al., 2012; Margetic and Strukil, 2016). This leads to the formation of new bonds between reactants and, consequently, the formation of new materials with significantly different chemical properties. Although it is a technique primarily used for the formation of metallic alloys, metal oxides and co-crystals, the use of mechanosynthesis for the preparation of carbon materials has been increasing significantly in recent years (Friscic, 2012; Margetic and Strukil, 2016; Zhang P. et al., 2017). This is particularly remarkable in the use of biosourced phenolic molecules and resins. In recent years, a few very relevant works can be found on this hot topic for lignin (Zhang J. et al., 2017; Liang et al., 2018; Liu et al., 2019) and tannins (Zhang P. et al., 2017; Castro-Gutierrez et al., 2018). Tannin, a templating agent (Pluronic® F127), and a small amount of water were ball-milled at room temperature. Interestingly, despite the absence of aldehyde, this synthetic methodology produces a structured mesophase through the self-condensation of tannin monomers due to the considerable energy provided by this novel technique without the need for hazardous solutions or compounds (Castro-Gutierrez et al., 2018). Moreover, this synthetic procedure has proven to be very versatile since multiple mesostructures can be found by modifying the amount of water, surfactant, and energy applied to the mechanochemical process. After heat treatment of the carbon mesophase, the well-ordered homogeneous pore size distribution was still observed (Castro-Gutierrez et al., 2018).
Nevertheless, mechanosynthesis is still in the early stages of carbon science. It holds promising prospects for the future of phenolic resins and carbon materials. However, more fundamental and applicative studies are still necessary to go further in its realization and understanding.
Carbon materials, whose most important characteristics are high availability, tunable porosity and chemical nature, easy of processing, inexpensive synthesis, and intrinsic heteroatom doping, can be found in almost every aspect and branch of materials science, such as membranes, water treatment, optics, aerospace industry, biosensors, energy storage and energy conversion (Ruoff, 2018). Considering all the properties already mentioned, carbon materials have proven to be an excellent way to improve performance in electrochemical applications, in the form of electrodes for electrochemical energy storage and conversion.
This review section will focus on the significant findings and advances in the different electrochemical applications of carbon materials obtained from “green” phenolic compounds. This will cover their use as electrodes in supercapacitors and rechargeable batteries for energy storage.
Supercapacitors (SCs), also known as electrochemical capacitors or ultracapacitors, have attracted significant attention in the energy storage field due to their superior rate capability, high power density, fast charge/discharge rates, and long-term durability (Sharma and Bhatti, 2010; Xing et al., 2014). These unique properties of SCs bridge the gap between batteries and traditional capacitors. SCs consist of two electrodes electrically isolated by an ion-permeable separator containing an electrolyte, where energy storage occurs by charge accumulation at the electrode-electrolyte interface. Among the various parameters influencing the performance of SCs, the porous structure of the active electrodes, i.e., the pore size and specific surface area, is of critical importance. Carbons with well-developed porosity obtained from fossil precursors (such as mesoporous carbons, carbon gels, nanostructured materials, etc.) have been widely explored as electrodes for SCs. Nowadays, the fabrication of cost-effective and high energy density electrodes using environmentally friendly resources remains a challenge facing material scientists worldwide.
Lignin and other natural phenolic compounds, especially tannin and tannin-related molecules (such as phloroglucinol), have been investigated in the reaction with an aldehyde for the production of porous carbons derived from phenolic resins with outstanding electrochemical performance when used as SC electrodes (Liu M. et al., 2015; Miao et al., 2017; Vinodh et al., 2020; Sima et al., 2021). In this regard, hierarchical structured pore materials, incorporating ultramicropores, supermicropores and mesopores in a carbon network, were successfully synthesized by solvothermal polymerization of phloroglucinol and terephthaldehyde in dioxane, followed by carbonization (Miao et al., 2017; Vinodh et al., 2020). In these reaction systems, dioxane acts as both a solvent and a template to produce mesoporous domains, whereas the polymeric phloroglucinol/terephthaldehyde units serve as self-template to generate micropores during pyrolysis. Interestingly, the authors (Miao et al., 2017) reported the production of porous carbons with a high specific surface area (up to 1,003 m2 g−1) by this strategy. The developed porosity, together with the micro-mesopore network, provides the resultant SC electrodes adequate specific capacitance (214 F g−1 at 1 A g−1) in 6M KOH aqueous electrolyte, high-rate capability (154 F g−1 at 50 A g−1), and long-term cycling stability (with a capacitance retention of 95.5% after 10,000 cycles) (Miao et al., 2017).
Further efforts in the eco-friendly synthesis of carbon electrodes for SCs from greener, non-toxic phenolic resins have been made by replacing formaldehyde with glyoxylic acid or glyoxal as crosslinkers (Moussa et al., 2018; Herou et al., 2019). For example, the synthesis of sustainable ordered mesoporous carbons (OMCs) by self-assembly of a phloroglucinol/lignin mixture (phenolic precursor) and glyoxal (crosslinker) in the presence of a soft template (Pluronic® F127) has been recently reported (Herou et al., 2019). The influence of phloroglucinol/lignin mass ratio on the electrochemical performance of the resultant OMC-based electrodes was investigated. The bio-based electrode derived from 50 wt% lignin + 50 wt% phloroglucinol showed optimal behavior with an enhanced volumetric capacitance (90 F cm−3), twice as high as the material prepared with phloroglucinol alone.
Self-condensation of tannins in the absence of crosslinkers has emerged over the past decade as an environmentally friendly approach to fabricate carbon materials with outstanding capacitive properties and high-rate capability (Castro-Gutierrez et al., 2019; 2021a). This particular route paves the way for the production of green, phenolic resin-derived carbon materials for energy storage applications with zero formaldehyde emissions. Several micro-mesoporous carbon materials obtained from the self-condensation of tannins by different synthetic routes have been explored as SC electrodes with promising results. Nano-cast OMCs based on tannin-related polyphenols (phloroglucinol, gallic acid, catechin or Mimosa tannin) have been investigated for electrochemical double-layer capacitors (Sanchez-Sanchez et al., 2017a). The synthesis route consists of a one-step impregnation of the hard template (SBA-15 silica) with the natural phenolic molecule in ethanol, which avoids the use of toxic solvents. The pyrolyzed carbon material achieved specific capacitances up to 277 F g−1 (at 0.5 mV s−1) in 1M H2SO4 aqueous electrolyte, which is in the range of OMCs with comparable textural parameters (Jurewicz et al., 2004; Tanaka et al., 2015) but obtained from petrochemical carbon precursors, and which require additional post-oxidation treatment to introduce oxygenated functionalities. These surface oxygen-containing groups increase the specific capacitance through: 1) pseudocapacitive contributions (quinone-hydroquinone redox reactions), and 2) improved carbon wettability and hence, increased electrochemical active area.
Although the nanocasting approach provides good control of the surface area and pore size of the resultant carbon electrodes, it requires the use of harsh acids (e.g., HF) to remove the hard silica template, which prevents the scaling-up of this methodology. A subsequent work showed successful soft-templating synthesis of OMCs by self-assembly of Mimosa tannin with Pluronic® F127 under mild conditions (30°C, pH 3) (Sanchez-Sanchez et al., 2018). An additional CO2 activation step led to highly porous carbons (specific surface area up to 1,152 m2 g−1) with a gravimetric capacitance of 286 F g−1 (at 0.5 mV s−1) and better capacitance retention compared to the non-activated electrode. Although this strategy free of phenol and formaldehyde avoids the acid leaching step (essential for hard-templating routes), long polymerization times (three days) are needed, making the methodology time-consuming and limiting its practical application for SC electrode production.
Recently, a versatile water-assisted mechanochemical tannin self-assembly method was reported for the rapid production of phenolic resins (1 h) using Pluronic® F127 as a surfactant. By controlling the mimosa tannin/water/F127 ratio, disordered and perfectly ordered mesoporous carbons (DMC and OMC, respectively) with similar physicochemical properties and differing only in the mesoporous structure were obtained, see Figure 6A (Castro-Gutierrez et al., 2018, 2019; 2021a). After physical activation with CO2, which resulted in a fourfold increase in surface area (from ca 500–2000 m2 g−1), the resultant mesoporous carbon electrodes exhibited superior capacitive properties with excellent rate capabilities at high current densities and long-term stability in both aqueous (1M H2SO4) and organic (TEABF4) electrolytes (Figure 6B). By scanning the hysteresis loops of nitrogen adsorption-desorption isotherms, the role of the connectivity of the micro-mesopore structure on the capacitive behavior has been studied (Castro-Gutierrez et al., 2021a). A 15% higher capacitance retention at 40 A g−1 in organic electrolyte was obtained with DMC compared to the ordered analog due to the more interconnected porosity of the former material, which allows for better diffusion of large ions. Conversely, the longer diffusion paths for small ions in 1M H2SO4 of the disordered mesoporous structure led to a 12% lower capacitance retention at 80 A g−1 than that obtained with OMC in the aqueous electrolyte.
FIGURE 6. (A) Schematic representations of the synthesis of ordered and disordered mesoporous carbons (OMC and DMC, respectively) by mechanochemical mesostructuration. TEM images and schematic porous structure of the resultant OMC and DMC materials. (B) Cell capacitance (Ccell) as a function of the applied current and Ragone-like plots in aqueous (1M H2SO4) and organic (TEABF4) electrolytes. Adapted with permission from (Castro-Gutierrez et al., 2021a).
As mentioned above, the interfacial capacitance of the materials can be further increased by the introduction of pseudocapacitance, which has been the subject of intensive research in the past decades. In addition to the surface oxygen functionalities, the introduction of other heteroatoms (nitrogen, phosphorous, boron, etc.) in the carbon lattice has been presented as a promising strategy to improve the capacitive performance of carbon electrodes derived from self-condensed-tannin. An innovative approach is the hydrothermal carbonization of aqueous tannin solutions, which benefits from tannin self-condensation under basic or acidic conditions. For example, a highly N- and O-doped carbon was prepared by hydrothermal carbonization (190°C) of pine tannins in ammonia, followed by pyrolysis of the resultant hydrochar at 900°C to develop the porous structure (Sanchez-Sanchez et al., 2017b). This easy, activation-free route to a carbon material with low ultramicroporosity and well-developed mesoporosity, as well as high N + O content (i.e., 24 μmol m−2), resulting in a specific capacitance of 252 F g−1 (0.5 mV s−1) in 1M H2SO4 and a high energy density (up to ∼1,500 mA g−1).
The crucial role of N and O co-doping in carbon materials has been demonstrated to have a positive impact for other electrochemical applications by acting as active sites towards the oxygen reduction reaction in fuel cells or metal-air batteries (Quílez-Bermejo et al., 2017, Quílez-Bermejo et al., 2019; Quílez-Bermejo et al., 2020c). Other works have also revealed the superior capacitive properties of dual heteroatom-doped carbon materials from aminated tannin or tannin-melamine resins using a microwave-assisted carbonization method (Nasini et al., 2014; Bairi et al., 2015). Following this strategy, these authors synthesized phosphorus- and nitrogen- co-doped mesoporous carbons from tannin crosslinked by melamine (N precursor) in the presence of phosphoric acid (as the P source) (Fu et al., 2016). The resultant carbon materials achieved specific capacitances up to 271 F g−1 in acidic (1M H2SO4) and 236 F g−1 in alkaline (6M KOH) aqueous electrolytes, which can be explained by: 1) the developed surface area (up to 855 m2 g−1), which plays a key role in the electric double layer capacitive behavior; and 2) the modification of the carbon with nitrogen moieties (specially pyridinic-N and quaternary-N), which is responsible for the pseudocapacitance.
In addition to the carbonization of renewable phenolic resins, the direct thermal treatment of lignin and tannin has also been evaluated for the production of advanced carbon electrodes for electrochemical capacitors. A recent work (Pérez-Rodríguez et al., 2021) used biochars obtained as a byproduct of bio-oil production from the fast pyrolysis of pine bark tannin as green and abundant precursors for the fabrication of SC electrodes (Figure 7A). After activation of the tannin-derived biochars with KOH at 650°C at different activation ratios (ARs), the resultant microporous activated carbons exhibited highly developed surface areas (up to 2,200 m2 g−1) and high oxygen content (10–15 wt%). These values explain their excellent capacitive behavior, with a maximum electrode capacitance of 232 F g−1 (at 0.5 A g−1, 1M H2SO4) and a capacitance retention of 70% at 10 A g−1 for the most activated carbons, i.e., those obtained at ARs of 2.8 and 3.6 g of KOH per gram of biochar (TBC-K2.8 and TBC-K3.6, respectively). This improved condition for energy storage is also evident in the Ragone-like plots (Figure 7B): TBC-K2.8 and TBC-K3.6 presented the highest specific energies with maxima of 5.4 and 6.7 Wh kg−1 at 110 W kg−1 under standard commercial mass loadings (∼10 mg cm−2). From the power-energy curves, the performance of a commercial device was extrapolated by estimating the carbon mass to be 30% of the SC stack (Gogotsi and Simon, 2011; Sevilla et al., 2019). The materials obtained from the upgrading of pine tannin biochars provided similar behavior to that of commercial reference SCs, showing their practical use for energy storage. The tannin-derived activated carbons also exhibited long-term stability, retaining 94% (at 5 A g−1) of the initial stored charge after 10,000 cycles. Further details of the use of lignin- and tannin-derived carbon materials as advanced electrodes for SCs can be found in the following references (Espinoza-Acosta et al., 2018; Castro-Gutierrez et al., 2020). All these results are comparable or even better than those obtained with other biomass precursors not based on phenolic molecules, such as the 228 F g−1 achieved in an alkaline electrolyte by using coconut shell as carbon precursor (Mi et al., 2012). This highlights the paramount importance of lignin and tannin as carbon precursors for the preparation of supercapacitor electrodes.
FIGURE 7. (A) Schematic representations of the upgrading of biochars obtained as a byproduct of bio-oil production from pine bark tannin as precursors for the fabrication of SC electrodes. (B) Ragone plots of symmetrical SCs based on tannin biochars (TBCs) activated with different ratios (from 0 to 0.6 g KOH per gram of biochar) (full symbols) and Ragone-like curves of the packaged device extrapolated by dividing the specific energy values by a factor of 3 (empty symbols). Commercial electrochemical capacitor technologies have been included in the green zone. Reprinted with permission from (Pérez-Rodríguez et al., 2021).
Despite all the above advantages of SCs, the low energy density compared to batteries and fuel cells limits their practical application as autonomous devices. The next section reviews significant progress in the development of carbon electrodes derived from phenolic compounds for rechargeable batteries.
Rechargeable batteries (secondary batteries) are older electrochemical energy storage devices than SCs on the market. In particular, batteries are used in a wide range of mid- and short-term storage technologies, such as electric vehicles, portable devices and grid storage. Similar to an SC, a battery also consists of two electrodes and an electrolyte-soaked separator, but the main energy storage mechanism is based on chemical reactions (redox reactions) and not on charge separation as in electrochemical capacitors. Among the different types of batteries, lithium-ion batteries (LIBs) outperform other systems due to their high energy density (180 Wh kg−1), cycle stability, and design flexibility (Tarascon and Armand, 2001). However, the uneven distribution and scarcity of lithium resources limit the large-scale application of LIBs. Similar technologies, such as sodium-ion batteries (NIBs), have emerged in the recent years as affordable alternatives due to the greater availability and lower cost of sodium comparted to lithium (Hwang et al., 2017).
In commercial LIBs, the negative electrode is typically graphite, where lithium ions are de-intercalated during battery discharge (spontaneous reaction, oxidation semi-reaction at the graphite electrode) and intercalated during the charging process (current is applied, reduction semi-reaction at the graphite electrode) for thousands of cycles (Figure 8). While graphite electrodes offer a suitable lithium intercalation capacity (with a theoretical value of 372 mAh g−1), the instability of Na-graphite intercalation compounds (NaC6 or NaC8) limits their use in NIBs (Stevens and Dahn, 2001; Yoon et al., 2016).
FIGURE 8. Schematic representations of a lithium-ion battery (in discharge mode of operation) (reprinted with permission from (Xu et al., 2004).
Motivated by graphite’s inability to store sodium ions and the energy transition to a sustainable economy, many groups have focused their research on developing of green, cheap and efficient carbon electrodes for next-generation rechargeable metal-ion batteries. Hard (i.e., non-graphitizable) carbons have attracted special attention as negative electrodes due to their high ability to store more lithium ions than graphite and their suitability for NIBs (Soltani et al., 2021; Xie et al., 2021). Hard carbons are usually obtained from the pyrolysis of biomass waste, sugars, or phenolic resins. Phenolic resins have recently been shown to be more suitable precursors than commercial cellulose or lignin to produce hard carbons for practical use in NIBs due to their high carbon yield and reversible sodium ion insertion capacity (249 mAh g−1) (Irisarri et al., 2018). In this study, however, commercial phenolic resins based on toxic and petrochemical precursors were used. The abundance, low cost, sustainability and non-toxicity of biomass make eco-friendly phenolic resin-derived hard carbons a promising option for metal-ion batteries.
Although the development of hard carbons from green (or partially green) phenolic resins for high-performance metal-ion batteries is an emerging field, a few examples can already be found in the literature involving different biosourced phenolic molecules (tannin, phloroglucinol, lignin, etc.) and crosslinkers (formaldehyde, furfuryl alcohol, glyoxylic acid, glyoxal) (Beda et al., 2018; Sun et al., 2020). Interestingly, a recent work synthesized hard carbons materials from phloroglucinol crosslinked with glyoxylic acid for NIB negative electrodes (Beda et al., 2018). In this environmentally friendly route, glyoxylic acid, containing aldehyde and carboxylic acid functionalities, acts as both a crosslinker and acidic catalyst, which leads to the formation of a phenolic resin with shorter curing times (Ghimbeu et al., 2015). Pyrolysis of the phenolic resin at high temperature (1,100–1700°C) led to the production of hard carbons with low surface area, disordered structure and moderate carbon yields (25–35%). The materials provided a sodium intercalation capacity of 270 mA h g−1 at a specific current density of 37.2 mA g−1 and good stability for 40 cycles, showing the potential of these green hard carbons for rechargeable metal-ion batteries.
It is also worth mentioning here a very recent work in which a hard carbon powder derived from tannin was tested as an anode material for NIB (Tonnoir et al., 2021). This powder was obtained by milling glassy carbon foam, itself obtained from self-generated foaming of a resin based on tannin and furfuryl alcohol and pyrolyzed at temperatures between 900 and 1,600°C. The hard carbon obtained at the highest temperature showed a high reversible capacity of 306 mAh g−1 at C/20 and a high initial Coulombic efficiency of 87%. To the best of our knowledge, these electrochemical performances are among the best reported in the literature for hard carbon derived from biomass.
Other attempts to increase defects (or active sites) and electrical conductivity of hard carbons derived from biophenolics-based polymer networks, and hence, to improve the sodium or lithium storage capabilities, have been made by heteroatom doping (such as nitrogen or sulfur) of carbon structures (Zhang et al., 2018; Huang et al., 2020). Recently, N-doped hard carbons derived from resole and urea have been explored for Na-ion storage (Sun et al., 2020). Porous carbons were obtained by a co-assembly strategy using phloroglucinol/glyoxal as the carbon precursor and urea as the nitrogen source, whereas Pluronic® F123 was used as a soft template. The resultant N-doped carbon electrode exhibited higher ability for sodium intercalation with a stable capacity of 229 mAh g−1 (at 100 mA g−1) for 200 cycles, which is almost twice that of the non-doped electrode (123 mAh g−1). The better performance of N-doped carbon materials has been also been proven for LIBs using hard carbons obtained by carbonizing formaldehyde- crosslinked lignin/melamine resins at 1,000°C (Yang et al., 2018). Nickel nitrate was used as a catalyst to induce graphitization, and thus, to enhance the electrical conductivity of the resultant hard carbon. When assembled into lithium-ion batteries, the electrode containing nitrogen moieties delivered a higher reversible lithium insertion capacity (340 mAh g−1 at 0.1 A g−1) than the N-free electrode (260 mAh g−1). In addition, the N-doped electrode presented a capacity retention of 69% when the current density increased from 0.1 to 1 A g−1, which is higher than for the non-doped electrode (42%) or the N-doped electrode synthesized in the absence of nickel nitrate (55%). This study also reveals the long-term stability of the N-doped electrode for 300 cycles at 0.5 A g−1. This work shows the potential of both introducing nitrogen-containing species and creating graphitic carbon structures to improve the electrochemical performance for LIBs of hard carbons obtained from phenolic bioresources.
The direct use of lignin (in the absence of any crosslinker) for the production of porous carbon-based electrodes has also been explored for metal-ion batteries and other related storage technologies, for example, as positive electrodes in Li-O2 batteries or primary batteries. This research field has been the subject of recent reviews and we encourage readers to find more details in the following references (Espinoza-Acosta et al., 2018; Mehta et al., 2020; Baloch and Labidi, 2021).
On the other hand, porous carbons obtained by polymerization of biophenolic molecules (tannin, phloroglucinol, lignin) in the presence of an aldehyde or by crosslinker-free methodologies and subsequent carbonization have been explored for the oxygen reduction reaction (ORR), leading to promising results (Nasini et al., 2013; Bairi et al., 2015; Parthiban et al., 2019). These works pave the way for the production of metal-free carbon electrodes with outstanding catalytic properties when used as cathodes in fuel cells but also as positive electrodes in metal-air batteries. However, further efforts are required for the design of green and highly active phenolic resin-derived carbon electrocatalysts for ORR with Pt-like performance (state-of-the-art electrodes) and with bi-functional activity for both oxygen reduction and oxygen evolution reactions, which plays a key role in the development of metal-air batteries and regenerative fuel cells.
Biosourced phenolic resins represent one of the most promising alternatives to petrochemical feedstocks for the production of carbon materials. The properties of phenolic resins and the resultant carbon materials are highly dependent on the precursor ratios, their nature, synthesis protocols, etc., making phenolic resins a critical and complex branch of materials science. In the quest for green production of carbon materials from phenolic resins, lignin and tannin have proven to be the most realistic substitutes for traditional fossil fuel-based precursors because of their abundance in nature and high carbon content.
Throughout this review, the most essential information has been collected and detailed, from the type of biomass precursors to the methods of obtaining these carbon materials from phenolic resins. Biomass precursors, and especially tannin and lignin, possess tunable characteristics that can further enhance the properties of these carbon electrodes through defects, heteroatom or metal doping. Phenolic-derived carbon materials have received much attention in recent years due to their excellent energy storage properties in supercapacitors and rechargeable batteries, reaching or surpassing the state-of-the-art electrodes. The high surface area and tunability of the surface chemistry by simple functionalization processes make them ideal for combining large surface area electrodes with pseudocapacitive reactions on the surface of the carbon electrodes, which can increase the energy storage in these electrochemical devices.
A deeper understanding on carbon materials derived from phenolic compounds is needed, with a focus on synthetic methods and functionalization processes. Special mention must be made here for mechanosynthesis, which has proven to be a new synthetic route to overcome the limitations of conventional fabrication protocols, but further research is still needed as it is in the early stages of carbon materials preparation.
Supercapacitors and rechargeable batteries are just two devices in which phenolic-derived carbon materials play a crucial role, but these properties are scalable to multiple electrochemical and non-electrochemical devices. The outstanding and tunable properties of these carbons make them an attractive alternative for adsorption, gas storage, fuel cells, electrochemical biosensors, or as electrodes for electrochemical water splitting.
JQ-B compiled, organized the data and wrote the first draft. SP-R contributed to wrote the first draft. AC reviewed the manuscript. VF conceived and reviewed the manuscript. All authors read and approved the submitted version.
This study was partly supported by ANR-15-IDEX-04-LUE and TALiSMAN project (2019- 000214), funded by European Regional Development Fund (ERDF). SPR acknowledges MCIN/AEI/10.13039/501100011033 for her Juan de la Cierva Incorporación research contract (IJC 2019-041874-I).
The authors declare that the research was conducted in the absence of any commercial or financial relationships that could be construed as a potential conflict of interest.
All claims expressed in this article are solely those of the authors and do not necessarily represent those of their affiliated organizations, or those of the publisher, the editors and the reviewers. Any product that may be evaluated in this article, or claim that may be made by its manufacturer, is not guaranteed or endorsed by the publisher.
Abbasi, R., Setzler, B. P., Lin, S., Wang, J., Zhao, Y., Xu, H., et al. (2019). A Roadmap to Low‐Cost Hydrogen with Hydroxide Exchange Membrane Electrolyzers. Adv. Mater. 31, 1805876. doi:10.1002/adma.201805876
Amaral-Labat, G., Szczurek, A., Fierro, V., Pizzi, A., and Celzard, A. (2013). Systematic Studies of Tannin-Formaldehyde Aerogels: Preparation and Properties. Sci. Tech. Adv. Mater. 14, 015001. doi:10.1088/1468-6996/14/1/015001
Bairi, V. G., Nasini, U. B., Kumar Ramasahayam, S., Bourdo, S. E., and Viswanathan, T. (2015). Electrocatalytic and Supercapacitor Performance of Phosphorous and Nitrogen Co-doped Porous Carbons Synthesized from Aminated Tannins. Electrochimica Acta 182, 987–994. doi:10.1016/j.electacta.2015.10.011
Baloch, M., and Labidi, J. (2021). Lignin Biopolymer: the Material of Choice for Advanced Lithium-Based Batteries. RSC Adv. 11, 23644–23653. doi:10.1039/d1ra02611a
Basso, M. C., Giovando, S., Pizzi, A., Lagel, M. C., and Celzard, A. (2014). Alkaline Tannin Rigid Foams. J. Renew. Mater. 2, 3. doi:10.7569/jrm.2013.634137
Beda, A., Taberna, P.-L., Simon, P., and Matei Ghimbeu, C. (2018). Hard Carbons Derived from green Phenolic Resins for Na-Ion Batteries. Carbon 139, 248–257. doi:10.1016/j.carbon.2018.06.036
Braghiroli, F. L., Fierro, V., Izquierdo, M. T., Parmentier, J., Pizzi, A., and Celzard, A. (2014). Kinetics of the Hydrothermal Treatment of Tannin for Producing Carbonaceous Microspheres. Bioresour. Tech. 151, 271–277. doi:10.1016/j.biortech.2013.10.045
Braghiroli, F. L., Fierro, V., Izquierdo, M. T., Parmentier, J., Pizzi, A., Delmotte, L., et al. (2015). High Surface - Highly N-Doped Carbons from Hydrothermally Treated Tannin. Ind. Crops Prod. 66, 282–290. doi:10.1016/j.indcrop.2014.11.022
Brauns, J., and Turek, T. (2020). Alkaline Water Electrolysis Powered by Renewable Energy: A Review. Processes 8, 248. doi:10.3390/pr8020248
Canevesi, R. L. S., Sanchez-Sanchez, A., Gadonneix, P., Celzard, A., and Fierro, V. (2020). Hierarchical Tannin-Derived Carbons as Efficient Tetracycline Adsorbents. Appl. Surf. Sci. 533, 147428. doi:10.1016/j.apsusc.2020.147428
Castro-Díaz, M., Vega, M. F., Díaz-Faes, E., Barriocanal, C., and Snape, C. (2019). Evaluation of Demineralized Lignin and Lignin-Phenolic Resin Blends to Produce Biocoke Suitable for Blast Furnace Operation. Fuel 258, 116125. doi:10.1016/j.fuel.2019.116125
Castro-Gutiérrez, J., Celzard, A., and Fierro, V. (2020). Energy Storage in Supercapacitors: Focus on Tannin-Derived Carbon Electrodes. Front. Mater. 7, 217. doi:10.3389/fmats.2020.00217
Castro-Gutiérrez, J., De Oliveira Jardim, E., Canevesi, R. L. S., Silvestre-Albero, J., Kriesten, M., Thommes, M., et al. (2021b). Molecular Sieving of Linear and Branched C6 Alkanes by Tannin-Derived Carbons. Carbon 174, 413–422. doi:10.1016/j.carbon.2020.12.061
Castro-Gutiérrez, J., Díez, N., Sevilla, M., Izquierdo, M. T., Celzard, A., and Fierro, V. (2021a). Model Carbon Materials Derived from Tannin to Assess the Importance of Pore Connectivity in Supercapacitors. Renew. Sust. Energ. Rev. 151, 111600. doi:10.1016/j.rser.2021.111600
Castro-Gutiérrez, J., Díez, N., Sevilla, M., Izquierdo, M. T., Ghanbaja, J., Celzard, A., et al. (2019). High-Rate Capability of Supercapacitors Based on Tannin-Derived Ordered Mesoporous Carbons. ACS Sust. Chem. Eng. 7, 17627–17635. doi:10.1021/acssuschemeng.9b03407
Castro-Gutiérrez, J., Sanchez-Sanchez, A., Ghanbaja, J., Díez, N., Sevilla, M., Celzard, A., et al. (2018). Synthesis of Perfectly Ordered Mesoporous Carbons by Water-Assisted Mechanochemical Self-Assembly of Tannin. Green. Chem. 20, 5123–5132. doi:10.1039/c8gc02295j
Celzard, A., and Fierro, V. (2020). "Green", Innovative, Versatile and Efficient Carbon Materials from Polyphenolic Plant Extracts. Carbon 167, 792–815. doi:10.1016/j.carbon.2020.05.053
Chen, W., Hu, C., Yang, Y., Cui, J., and Liu, Y. (2016). Rapid Synthesis of Carbon Dots by Hydrothermal Treatment of Lignin. Materials 9, 184. doi:10.3390/ma9030184
Cheng, Y., Sui, G., Liu, H., Wang, X., Yang, X., and Wang, Z. (2018). Preparation of Highly Phenol Substituted Bio-Oil-Phenol-Formaldehyde Adhesives with Enhanced Bonding Performance Using Furfural as Crosslinking Agent. J. Appl. Polym. Sci. 136, 46995. doi:10.1002/app.46995
Choma, J., Zubrowska, A., Górka, J., and Jaroniec, M. (2020). Adsorption Properties of Phenolic Resin-Based Mesoporous Carbons Obtained by Using Mixed Templates of Pluronic F127 and Brij 58 or Brij 78 Polymers. Adsorption 16, 377. doi:10.1007/s10450-010-9230-5
Delgado-Sánchez, C., Fierro, V., Li, S., Pasc, A., Pizzi, A., and Celzard, A. (2017). Stability Analysis of Tannin-Based Foams Using Multiple Light-Scattering Measurements. Eur. Polym. J. 87, 318–330. doi:10.1016/j.eurpolymj.2016.12.036
Díez, N., Sevilla, M., and Fuertes, A. B. (2021). Synthesis Strategies of Templated Porous Carbons beyond the Silica Nanocasting Technique. Carbon 178, 451–476. doi:10.1016/j.carbon.2021.03.029
Din, M. I., Ashraf, S., and Intisar, A. (2017). Comparative Study of Different Activation Treatments for the Preparation of Activated Carbon: a Mini-Review. Sci. Prog. 100, 299–312. doi:10.3184/003685017x14967570531606
Doney, S. C., Fabry, V. J., Feely, R. A., and Kleypas, J. A. (2009). Ocean Acidification: The Other CO2 Problem. Annu. Rev. Mar. Sci. 1, 169–192. doi:10.1146/annurev.marine.010908.163834
Du, K., and Li, J. (2019). Towards a green World: How Do green Technology Innovations Affect Total-Factor Carbon Productivity. Energy Policy 131, 240–250. doi:10.1016/j.enpol.2019.04.033
Effendi, A., Gerhauser, H., and Bridgwater, A. V. (2008). Production of Renewable Phenolic Resins by Thermochemical Conversion of Biomass: A Review. Renew. Sust. Energ. Rev. 12, 2092–2116. doi:10.1016/j.rser.2007.04.008
Espinoza-Acosta, J. L., Torres-Chávez, P. I., Olmedo-Martínez, J. L., Vega-Rios, A., Flores-Gallardo, S., and Zaragoza-Contreras, E. A. (2018). Lignin in Storage and Renewable Energy Applications: A Review. J. Energ. Chem. 27, 1422–1438. doi:10.1016/j.jechem.2018.02.015
European Chemicals Agency (2021a). Substance Infocard - Benzene. https://echa.europa.eu/nl/substance-information/-/substanceinfo/100.000.685 (accessed Aug 28, 2021).
European Chemicals Agency (2021b). Substance Infocard - Propene. https://echa.europa.eu/nl/substance-information/-/substanceinfo/100.003.693 (accessed Aug 28, 2021).
European Chemicals Agency (2021c). Substance Infocard − Formaldehyde. https://echa.europa.eu/nl/substance-information/-/substanceinfo/100.000.002 (accessed Aug 28, 2021).
European Chemicals Agency (2021d). Substance Infocard − Phenol. https://echa.europa.eu/nl/substance-information/-/substanceinfo/100.003.303 (accessed Aug 28, 2021).
Fei, J., Luo, W., Huang, J., Ouyang, H., Wang, H., and Cao, L. (2015). Effect of Hydrothermal Modified Carbon Fiber through Diels-Alder Reaction and its Reinforced Phenolic Composites. RSC Adv. 5, 64450–64455. doi:10.1039/c5ra09798c
Fierro, C. M., Górka, J., Zazo, J. A., Rodríguez, J. J., Ludwinowicz, J., and Jaroniec, M. (2013). Colloidal Templating Synthesis and Adsorption Characteristics of Microporous-Mesoporous Carbons from Kraft Lignin. Carbon 62, 233–239. doi:10.1016/j.carbon.2013.06.012
Fierro, V., Torné-Fernández, V., and Celzard, A. (2006). Kraft Lignin as a Precursor for Microporous Activated Carbons Prepared by Impregnation with Ortho-Phosphoric Acid: Synthesis and Textural Characterisation. Microporous Mesoporous Mater. 92, 243–250. doi:10.1016/j.micromeso.2006.01.013
Fierro, V., Torné-Fernández, V., Montané, D., and Celzard, A. (2008). Adsorption of Phenol onto Activated Carbons Having Different Textural and Surface Properties. Microporous Mesoporous Mater. 111, 276–284. doi:10.1016/j.micromeso.2007.08.002
Fierro, V., Torné-Fernández, V., Montané, D., and Celzard, A. (2005). Study of the Decomposition of Kraft Lignin Impregnated with Orthophosphoric Acid. Thermochim. Acta 433, 142–148. doi:10.1016/j.tca.2005.02.026
Forest Research (2021). https://www.forestresearch.gov.uk/tools-and-resources/fthr/biomass-energy-resources/general-biomass-information/what-is-biomass/(accessed Aug 28, 2021).
Foyer, G., Chanfi, B.-H., Boutevin, B., Caillol, S., and David, G. (2016). New Method for the Synthesis of Formaldehyde-free Phenolic Resins from Lignin-Based Aldehyde Precursors. Eur. Polym. J. 74, 296–309. doi:10.1016/j.eurpolymj.2015.11.036
Friscic, T. (2012). Supramolecular Concepts and New Techniques in Mechanochemistry: Cocrystals, Cages, Rotaxanes, Open Metal–Organic Frameworks. Chem. Soc. Rev. 41, 3493–3510.
Fu, Y. a., Huang, Y., Xiang, Z., Liu, G., and Cao, D. (2016). Phosphorous-Nitrogen‐Codoped Carbon Materials Derived from Metal-Organic Frameworks as Efficient Electrocatalysts for Oxygen Reduction Reactions. Eur. J. Inorg. Chem. 2016, 2100–2105. doi:10.1002/ejic.201500822
Gan, L., Lyu, L., Shen, T., and Wang, S. (2019). Sulfonated Lignin-Derived Ordered Mesoporous Carbon with Highly Selective and Recyclable Catalysis for the Conversion of Fructose into 5-hydroxymethylfurfural. Appl. Catal. A: Gen. 574, 132–143. doi:10.1016/j.apcata.2019.02.008
Ganiyu, S. O., and Martínez-Huitle, C. A. (2020). The Use of Renewable Energies Driving Electrochemical Technologies for Environmental Applications. Curr. Opin. Electrochemistry 22, 211–220. doi:10.1016/j.coelec.2020.07.007
Gao, Y., Yue, Q., Gao, B., and Li, A. (2020). Insight into Activated Carbon from Different Kinds of Chemical Activating Agents: A Review. Sci. Total Environ. 746, 141094. doi:10.1016/j.scitotenv.2020.141094
Ghimbeu, C. M., Vidal, L., Delmotte, L., Meins, J. M. Le., and Vix-Guterl, C. (2015). Catalyst-free Soft-Template Synthesis of Ordered Mesoporous Carbon Tailored Using Phloroglucinol/Glyoxylic Acid Environmentally Friendly Precursors. Green. Chem. 16, 3079. doi:10.1039/C4GC00269E
Gogotsi, Y., and Simon, P. (2011). True Performance Metrics in Electrochemical Energy Storage. Science 334, 917–918. doi:10.1126/science.1213003
Grenier-Loustalot, M.-F., Larroque, S., Grenier, P., Leca, J.-P., and Bedel, D. (1994). Phenolic Resins: 1. Mechanisms and Kinetics of Phenol and of the First Polycondensates towards Formaldehyde in Solution. Polymer 35, 3046–3054. doi:10.1016/0032-3861(94)90418-9
Gross, G. (1999). “Biosynthesis of Hydrolysable Tannins,” in Comprehensive Natural Product Chemistry: Carbohydrates and Their Derivatives Including Tannins, Cellulose and Related Lignings.
Guo, Z., Liu, Z., Ye, L., Ge, K., and Zhao, T. (2015). The Production of Lignin-Phenol-Formaldehyde Resin Derived Carbon Fibers Stabilized by BN Preceramic Polymer. Mater. Lett. 142, 49–51. doi:10.1016/j.matlet.2014.11.068
Heidarinejad, Z., Dehghani, M. H., Heidari, M., Javedan, G., Ali, I., and Sillanpää, M. (2020). Methods for Preparation and Activation of Activated Carbon: a Review. Environ. Chem. Lett. 18, 393–415. doi:10.1007/s10311-019-00955-0
Herou, S., Ribadeneyra, M. C., Madhu, R., Araullo-Peters, V., Jensen, A., Schlee, P., et al. (2019). Ordered Mesoporous Carbons from Lignin: a New Class of Biobased Electrodes for Supercapacitors. Green. Chem. 21, 550–559. doi:10.1039/c8gc03497d
Hu, L., Pan, H., Zhou, Y., and Zhang, M. (2011). Methods to Improve Lignin's Reactivity as a Phenol Substitute and as Replacement for Other Phenolic Compounds: A Brief Review. BioRes 6, 3515–3525. doi:10.15376/biores.6.3.3515-3525
Huang, Q., Hu, J., Wen, S., Zhang, X., Liu, G., Chang, S., et al. (2020). Sulfur-Doped and Bio-Resin-Derived Hard Carbon@rGO Composites as Sustainable Anodes for Lithium-Ion Batteries. Front. Chem. 8, 241. doi:10.3389/fchem.2020.00241
Huang, Y., Yang, J., Cai, H., Zhai, Y., Feng, D., Deng, Y., et al. (2009). A Curing Agent Method to Synthesize Ordered Mesoporous Carbons from Linear Novolac Phenolic Resin Polymers. J. Mater. Chem. 19, 6536–6541. doi:10.1039/b908183f
Hwang, J.-Y., Myung, S.-T., and Sun, Y.-K. (2017). Sodium-ion Batteries: Present and Future. Chem. Soc. Rev. 46, 3529–3614. doi:10.1039/c6cs00776g
Irisarri, E., Amini, N., Tennison, S., Ghimbeu, C. M., Gorka, J., Vix-Guterl, C., et al. (2018). Optimization of Large Scale Produced Hard Carbon Performance in Na-Ion Batteries: Effect of Precursor, Temperature and Processing Conditions. J. Electrochem. Soc. 165, A4058–A4066. doi:10.1149/2.1171816jes
Jagiello, J., Kenvin, J., Celzard, A., and Fierro, V. (2019). Enhanced Resolution of Ultra Micropore Size Determination of Biochars and Activated Carbons by Dual Gas Analysis Using N2 and CO2 with 2D-NLDFT Adsorption Models. Carbon 144, 206–215. doi:10.1016/j.carbon.2018.12.028
Jagtoyen, M., and Derbyshire, F. (1998). Activated Carbons from Yellow poplar and white Oak by H3PO4 Activation. Carbon 36, 1085–1097. doi:10.1016/s0008-6223(98)00082-7
James, S. L., Adams, C. J., Bolm, C., Braga, D., Collier, P., Friščić, T., et al. (2012). Mechanochemistry: Opportunities for New and Cleaner Synthesis. Chem. Soc. Rev. 41, 413–447. doi:10.1039/c1cs15171a
Jiang, H., Wang, J., Wu, S., Yuan, Z., Hu, Z., Wu, R., et al. (2012). The Pyrolysis Mechanism of Phenol Formaldehyde Resin. Polym. Degrad. Stab. 97, 1527–1533. doi:10.1016/j.polymdegradstab.2012.04.016
Jiang, L., Sheng, L., and Fan, Z. (2018). Biomass-derived Carbon Materials with Structural Diversities and Their Applications in Energy Storage. Sci. China Mater. 61, 133–158. doi:10.1007/s40843-017-9169-4
Jiang, X., Liu, J., Du, X., Hu, Z., Chang, H.-m., and Jameel, H. (2018). Phenolation to Improve Lignin Reactivity toward Thermosets Application. ACS Sust. Chem. Eng. 6, 5504–5512. doi:10.1021/acssuschemeng.8b00369
Jun, Y.-S., Hong, W. H., Antonietti, M., and Thomas, A. (2009). Mesoporous, 2D Hexagonal Carbon Nitride and Titanium Nitride/Carbon Composites. Adv. Mater. 21, 4270–4274. doi:10.1002/adma.200803500
Jurewicz, K., Vix-Guterl, C., Frackowiak, E., Saadallah, S., Reda, M., Parmentier, J., et al. (2004). Capacitance Properties of Ordered Porous Carbon Materials Prepared by a Templating Procedure. J. Phys. Chem. Sol. 65, 287–293. doi:10.1016/j.jpcs.2003.10.024
Kahnbabaee, K., and Van-Ree, T. (2001). Tannins: Classification and Definition. Nat. Prod. Rep. 18, 641. doi:10.1039/B101061L
Kalami, S., Arefmanesh, M., Master, E., and Nejad, M. (2017). Replacing 100% of Phenol in Phenolic Adhesive Formulations with Lignin. Appl. Polym. Sci. 134, 45124
Kang, S., Li, X., Fan, J., and Chang, J. (2013). Hydrothermal Conversion of Lignin: A Review. Renew. Sustain. Energ. Rev. 27, 13. doi:10.1016/j.rser.2013.07.013
Ko, T.-H., Kuo, W.-S., and Chang, Y.-H. (2000). Raman Study of the Microstructure Changes of Phenolic Resin during Pyrolysis. Polym. Compos. 21, 745–750. doi:10.1002/pc.10229
Kumar, B., Agumba, D. O., Pham, D. H., Latif, M., DineshKim, H. C., Kim, H. C., et al. (2021). Recent Research Progress on Lignin-Derived Resins for Natural Fiber Composite Applications. Polymers 13, 1162. doi:10.3390/polym13071162
Lacoste, C., Basso, M. C., Pizzi, A., Laborie, M.-P., Garcia, D., and Celzard, A. (2013). Bioresourced pine Tannin/furanic Foams with Glyoxal and Glutaraldehyde. Ind. Crops Prod. 45, 401–405. doi:10.1016/j.indcrop.2012.12.032
Lagel, M. C., Pizzi, A., Giovando, S., and Celzard, A. (2014). Development and Characterisation of Phenolic Foams with Phenol-Formaldehyde-Chestnut Tannins Resin. J. Renew. Mater. 2, 220–229. doi:10.7569/jrm.2014.634113
Lan, G., Yang, J., Ye, R. P., Boyjoo, Y., Liang, J., Liu, X., et al. (2021). Sustainable Carbon Materials toward Emerging Applications. Small Methods 5, 2001250. doi:10.1002/smtd.202001250
Legrouri, K., Khouya, E., Ezzine, M., Hannache, H., Denoyel, R., Pallier, R., et al. (2004). Production of Activated Carbon from a New Precursor Molasses by Activation with Sulphuric Acid. J. Hazard. Mater. 118, 259–263. doi:10.1016/j.jhazmat.2004.11.004
Li, H., Shi, F., An, Q., Zhai, S., Wang, K., and Tong, Y. (2021). Three-dimensional Hierarchical Porous Carbon Derived from Lignin for Supercapacitors: Insight into the Hydrothermal Carbonization and Activation. Int. J. Biol. Macromolecules 166, 923–933. doi:10.1016/j.ijbiomac.2020.10.249
Li, J., Li, C., Wang, W., Zhang, W., and Li, J. (2016). Reactivity of Larch and Valonia Tannins in Synthesis of Tannin-Formaldehyde Resins. BioResources 11, 2256–2268. doi:10.15376/biores.11.1.2256-2268
Li, T., Ma, R., Lin, J., Hu, Y., Zhang, P., Sun, S., et al. (2019). The Synthesis and Performance Analysis of Various Biomass‐based Carbon Materials for Electric Double‐layer Capacitors: A Review. Int. J. Energ. Res. 44, 2426–2454. doi:10.1002/er.5061
Liang, J., Zhang, J., Du, G., Feng, S., Xi, X., and Lei, H. (2018). Lignin-based Grinding Wheels with Aluminum Oxide: Synthesis and Characterization. BioResources 13, 1388–1400. doi:10.15376/biores.13.1.1388-1400
Lillo-Ródenas, M. A., Cazorla-Amorós, D., and Linares-Solano, A. (2003). Understanding Chemical Reactions between Carbons and NaOH and KOH. Carbon 41, 267–275. doi:10.1016/s0008-6223(02)00279-8
Liu, L., Deng, Q.-F., Liu, Y.-P., Ren, T.-Z., and Yuan, Z.-Y. (2011). HNO3-activated Mesoporous Carbon Catalyst for Direct Dehydrogenation of Propane to Propylene. Catal. Commun. 16, 81–85. doi:10.1016/j.catcom.2011.09.005
Liu, L., Solin, N., and Inganäs, O. (2019). Scalable Lignin/graphite Electrodes Formed by Mechanochemistry. RSC Adv. 9, 39758–39767. doi:10.1039/c9ra07507k
Liu, M., Qian, J., Zhao, Y., Zhu, D., Gan, L., and Chen, L. (2015a). Core-shell Ultramicroporous@microporous Carbon Nanospheres as Advanced Supercapacitor Electrodes. J. Mater. Chem. A. 3, 11517–11526. doi:10.1039/c5ta02224j
Liu, W.-J., Jiang, H., and Yu, H.-Q. (2015b). Development of Biochar-Based Functional Materials: Toward a Sustainable Platform Carbon Material. Chem. Rev. 115, 12251–12285. doi:10.1021/acs.chemrev.5b00195
Liu, X., Li, Y., Xu, X., Zhou, L., and Mai, L. (2021). Rechargeable Metal (Li, Na, Mg, Al)-Sulfur Batteries: Materials and Advances. J. Energ. Chem. 61. doi:10.1016/j.jechem.2021.02.028
López de Letona Sánchez, M., Macías-García, A., Díaz-Díez, M. A., Cuerda-Correa, E. M., Gañán-Gómez, J., and Nadal-Gisbert, A. (2006). Preparation of Activated Carbons Previously Treated with Hydrogen Peroxide: Study of Their Porous Texture. Appl. Surf. Sci. 252, 5984–5987. doi:10.1016/j.apsusc.2005.11.022
Ma, Q., Yu, Y., Sindoro, M., Fane, A. G., Wang, R., and Zhang, H. (2017). Carbon-Based Functional Materials Derived from Waste for Water Remediation and Energy Storage. Adv. Mater. 29, 1605361. doi:10.1002/adma.201605361
Margetic, D., and Strukil, V. (2016). Mechanochemical Organic Synthesis. Elsevier. 978-0-12-802184-2.
Mauger, A., Julien, C. M., Paolella, A., Armand, M., and Zaghib, K. (2019). Building Better Batteries in the Solid State: A Review. Materials 12, 3892. doi:10.3390/ma12233892
Mayoral, E. P., Matos, I., Bernardo, M., Durán-Valle, C., and Fonseca, I. (2021). Functional Porous Carbons: Synthetic Strategies and Catalytic Application in fine Chemical Synthesis. Emerging Carbon Mater. Catal. 601, 299–352. doi:10.1016/b978-0-12-817561-3.00009-3
Mehta, S., Jha, S., and Liang, H. (2020). Lignocellulose Materials for Supercapacitor and Battery Electrodes: A Review. Renew. Sust. Energ. Rev. 134, 110345. doi:10.1016/j.rser.2020.110345
Meng, Y., Gu, D., Zhang, F., Shi, Y., Cheng, L., Feng, D., et al. (2006). A Family of Highly Ordered Mesoporous Polymer Resin and Carbon Structures from Organic−Organic Self-Assembly. Chem. Mater. 18, 4447–4464. doi:10.1021/cm060921u
Mi, J., Wang, X.-R., Fan, R.-J., Qu, W.-H., and Li, W.-C. (2012). Coconut-Shell-Based Porous Carbons with a Tunable Micro/Mesopore Ratio for High-Performance Supercapacitors. Energy Fuels 26, 5321–5329. doi:10.1021/ef3009234
Miao, L., Zhu, D., Zhao, Y., Liu, M., Duan, H., Xiong, W., et al. (2017). Design of Carbon Materials with Ultramicro-, Supermicro- and Mesopores Using Solvent- and Self-Template Strategy for Supercapacitors. Microporous Mesoporous Mater. 253, 1–9. doi:10.1016/j.micromeso.2017.06.032
Mohamed, G., El-Shafey, O., and Fathy, N. A. (2017). Preparation of Carbonaceous Hydrochar Adsorbents from Cellulose and Lignin Derived from rice Straw. Egypt. J. Chem. 60, 793–804. doi:10.21608/ejchem.2017.1311.1080
Molina-Sabio, M., Rodríguez-Reinoso, F., Caturla, F., and Sellés, M. J. (1996). Development of Porosity in Combined Phosphoric Acid-Carbon Dioxide Activation. Carbon 34, 457–462. doi:10.1016/0008-6223(95)00209-x
Moussa, G., Hajjar-Garreau, S., Taberna, P.-L., Simon, P., and Matei Ghimbeu, C. (2018). Eco-Friendly Synthesis of Nitrogen-Doped Mesoporous Carbon for Supercapacitor Application. C. J. Carbon. Res. 4, 20. doi:10.3390/c4020020
Muylaert, I., Verberckmoes, A., De Decker, J., and Van Der Voort, P. (2012). Ordered Mesoporous Phenolic Resins: Highly Versatile and Ultra Stable Support Materials. Adv. Colloid Interf. Sci. 175, 39–51. doi:10.1016/j.cis.2012.03.007
Muzaffar, A., Ahamed, M. B., Deshmukh, K., and Thirumalai, J. (2019). A Review on Recent Advances in Hybrid Supercapacitors: Design, Fabrication and Applications. Renew. Sust. Energ. Rev. 101, 123–145. doi:10.1016/j.rser.2018.10.026
Nasini, U. B., Bairi, V. G., Ramasahayam, S. K., Bourdo, S. E., Viswanathan, T., and Shaikh, A. U. (2014). Phosphorous and Nitrogen Dual Heteroatom Doped Mesoporous Carbon Synthesized via Microwave Method for Supercapacitor Application. J. Power Sourc. 250, 257–265. doi:10.1016/j.jpowsour.2013.11.014
Nasini, U. B., Gopal Bairi, V., Kumar Ramasahayam, S., Bourdo, S. E., Viswanathan, T., and Shaikh, A. U. (2013). Oxygen Reduction Reaction Studies of Phosphorus and Nitrogen Co-doped Mesoporous Carbon Synthesized via Microwave Technique. ChemElectroChem 1, 573–579. doi:10.1002/celc.201300047
Neatu, S., Neatu, F., Chirica, J. M., Borbath, I., Talas, E., Tompos, A., et al. (2021). Recent Progress in Electrocatalysts and Electrodes for Portable Fuel Cells. J. Mater. Chem. A. 9, 17065. doi:10.1039/D1TA03644K
Nelson, K. M., Mahurin, S. M., Mayes, R. T., Williamson, B., Teague, C. M., Binder, A. J., et al. (2016). Preparation and CO2 Adsorption Properties of Soft-Templated Mesoporous Carbons Derived from Chestnut Tannin Precursors. Microporous Mesoporous Mater. 222, 94–103. doi:10.1016/j.micromeso.2015.09.050
Nita, C., Bensafia, M., Vaulot, C., Delmotte, L., and Matei Ghimbeu, C. (2016). Insights on the Synthesis Mechanism of green Phenolic Resin Derived Porous Carbons via a Salt-Soft Templating Approach. Carbon 109, 227–238. doi:10.1016/j.carbon.2016.08.011
Nizamuddin, S., Baloch, H. A., Griffin, G. J., Mubarak, N. M., Bhutto, A. W., Abro, R., et al. (2017). An Overview of Effect of Process Parameters on Hydrothermal Carbonization of Biomass. Renew. Sust. Energ. Rev. 73, 1289–1299. doi:10.1016/j.rser.2016.12.122
Oliveira, F. B., Gardrat, C., Enjalbal, C., Frollini, E., and Castellan, A. (2008). Phenol-furfural Resins to Elaborate Composites Reinforced with Sisal Fibers-Molecular Analysis of Resin and Properties of Composites. J. Appl. Polym. Sci. 109, 2291–2303. doi:10.1002/app.28312
Paris Agreement to the United Nations Framework Convention on Climate Change (2015). New York, NY: T.I.A.S. No, 16–1104.
Parthiban, V., Bhuvaneshwari, B., Karthikeyan, J., Murugan, P., and Sahu, A. K. (2019). Fluorine-enriched Mesoporous Carbon as Efficient Oxygen Reduction Catalyst: Understanding the Defects in Porous Matrix and Fuel Cell Applications. Nanoscale Adv. 1, 4926–4937. doi:10.1039/c9na00572b
Peng, W., Riedl, B., and Barry, A. O. (1993). Study on the Kinetics of Lignin Methylolation. J. Appl. Polym. Sci. 48, 1757–1763. doi:10.1002/app.1993.070481009
Pérez-Rodríguez, S., Pinto, O., Izquierdo, M. T., Segura, C., Poon, P. S., Celzard, A., et al. (2021). Upgrading of pine Tannin Biochars as Electrochemical Capacitor Electrodes. J. Colloid Inter. Sci. 601, 836–876. doi:10.1016/j.jcis.2021.05.162
Pilato, L. (2013). Phenolic Resins: 100Years and Still Going strong. Reactive Funct. Polym. 73, 270–277. doi:10.1016/j.reactfunctpolym.2012.07.008
Pizzi, A., Meikleham, N., Dombo, B., and Roll, W. (1995). Autocondensation-based, Zero-Emission, Tannin Adhesives for Particleboard. Holz als Roh-und Werkstoff 53, 201–204. doi:10.1007/bf02716424
Pizzi, A., Pasch, H., Celzard, A., and Szczurek, A. (2013). Oligomers Distribution at the Gel point of Tannin-Formaldehyde Thermosetting Adhesives for wood Panels. J. Adhes. Sci. Tech. 27, 2094–2102. doi:10.1080/01694243.2012.697669
Pizzi, A. (2008). Polyflavonoid Tannins Self-Condensation Adhesives for Wood Particleboard. J. Adhes. 85, 57–68.
Pizzi, A., and Stephanou, A. (1994). Phenol-Formaldehyde Wood Adhesives under Very Alkaline Conditions. Part I: Behaviour and Proposed Mechanism. Holzforschung 48, 35–40. doi:10.1515/hfsg.1994.48.1.35
Pomerantseva, E., Bonaccorso, F., Feng, X., Cui, Y., and Gogotsi, Y. (2019). Energy Storage: The Future Enabled by Nanomaterials. Science 366, 6468. doi:10.1126/science.aan8285
Poonam, , Sharma, K., Arora, A., and Tripathi, S. K. (2019). Review of Supercapacitors: Materials and Devices. J. Energ. Storage 21, 801–825. doi:10.1016/j.est.2019.01.010
Puziy, A. M., Poddubnaya, O. I., Martínez-Alonso, A., Suárez-Garcı́a, F., and Tascón, J. M. D. (2003). Synthetic Carbons Activated with Phosphoric Acid III. Carbons Prepared in Air. Carbon 41, 1181–1191. doi:10.1016/s0008-6223(03)00031-9
Quílez-Bermejo, J., González-Gaitán, C., Morallón, E., and Cazorla-Amorós, D. (2017). Effect of Carbonization Conditions of Polyaniline on its Catalytic Activity towards ORR. Some Insights about the Nature of the Active Sites. Carbon 119, 62–71. doi:10.1016/j.carbon.2017.04.015
Quílez-Bermejo, J., Melle-Franco, M., San-Fabián, E., Morallón, E., and Cazorla-Amorós, D. (2019). Towards Understanding the Active Sites for the ORR in N-Doped Carbon Materials through fine-tuning of Nitrogen Functionalities: an Experimental and Computational Approach. J. Mater. Chem. A. 7, 24239–24250. doi:10.1039/c9ta07932g
Quílez-Bermejo, J., Morallón, E., and Cazorla-Amorós, D. (2020a). Metal-free Heteroatom-Doped Carbon-Based Catalysts for ORR: A Critical Assessment about the Role of Heteroatoms. Carbon 165, 434–454. doi:10.1016/j.carbon.2020.04.068
Quílez-Bermejo, J., Morallón, E., and Cazorla-Amorós, D. (2020b). Polyaniline-Derived N-Doped Ordered Mesoporous Carbon Thin Films: Efficient Catalysts towards Oxygen Reduction Reaction. Polymers 12, 2382. doi:10.3390/polym12102382
Quílez-Bermejo, J., Strutyński, K., Melle-Franco, M., Morallón, E., and Cazorla-Amorós, D. (2020c). On the Origin of the Effect of pH in Oxygen Reduction Reaction for Nondoped and Edge-type Quaternary N-Doped Metal-free Carbon-Based Catalysts. ACS Appl. Mater. Inter. 12, 54815–54823. doi:10.1021/acsami.0c17249
Ramires, E. C., Megiatto, J. D., Gardrat, C., Castellan, A., and Frollini, E. (2010). Biobased Composites from Glyoxal-Phenolic Resins and Sisal Fibers. Bioresour. Tech. 101, 1998–2006. doi:10.1016/j.biortech.2009.10.005
Renda, C. G., and Bertholdo, R. (2018). Study of Phenolic Resin and Their Tendency for Carbon Graphitization. J. Polym. Res. 25, 241. doi:10.1007/s10965-018-1635-y
Rodríguez-Mirasol, J., Cordero, T., and Rodríguez, J. J. (1993a). Activated Carbons from Carbon Dioxide Partial Gasification of eucalyptus Kraft Lignin. Energy Fuels 7, 133–138. doi:10.1021/ef00037a021
Rodríguez-Mirasol, J., Cordero, T., and Rodríguez, J. J. (1993b). Preparation and Characterization of Activated Carbons from eucalyptus Kraft Lignin. Carbon 31, 87–95. doi:10.1016/0008-6223(93)90160-c
Ruoff, R. S. (2018). A Perspective on Objectives for Carbon Science. Carbon 132, 802. doi:10.1016/j.carbon.2018.02.057
Salinas-Torres, D., Ruiz-Rosas, R., Valero-Romero, M. J., Rodríguez- Mirasol, J., Cordero, T., Morallón, E., et al. (2016). Asymmetric Capacitors Using Lignin-Based Hierarchical Porous Carbons. J. Power Sourc. 326, 641–651. doi:10.1016/j.jpowsour.2016.03.096
Sanchez-Sanchez, A., Izquierdo, M. T., Ghanbaja, J., Medjahdi, G., Mathieu, S., Celzard, A., et al. (2017a). Excellent Electrochemical Performances of Nanocast Ordered Mesoporous Carbons Based on Tannin-Related Polyphenols as Supercapacitor Electrodes. J. Power Sourc. 344, 15–24. doi:10.1016/j.jpowsour.2017.01.099
Sanchez-Sanchez, A., Izquierdo, M. T., Mathieu, S., González-Álvarez, J., Celzard, A., and Fierro, V. (2017b). Outstanding Electrochemical Performance of Highly N- and O-Doped Carbons Derived from pine Tannin. Green. Chem. 19, 2653–2665. doi:10.1039/c7gc00491e
Sanchez-Sanchez, A., Izquierdo, M. T., Medjahdi, G., Ghanbaja, J., Celzard, A., and Fierro, V. (2018). Ordered Mesoporous Carbons Obtained by Soft-Templating of Tannin in Mild Conditions. Microporous Mesoporous Mater. 270, 129–139. doi:10.1016/j.micromeso.2018.05.017
Santiago-Medina, F.-J., Pizzi, A., Basso, M., Delmotte, L., and Celzard, A. (2017). Polycondensation Resins by Flavonoid Tannins Reaction with Amines. Polymers 9, 37. doi:10.3390/polym9020037
Sarika, P. R., Nancarrow, P., Khansaheb, A., and Ibrahim, T. (2020). Bio-Based Alternatives to Phenol and Formaldehyde for the Production of Resins. Polymers 12, 2237. doi:10.3390/polym12102237
Sazali, N., Wan Salleh, W. N., Jamaludin, A. S., and Mhd Razali, M. N. (2020). New Perspectives on Fuel Cell Technology: A Brief Review. Membranes 10, 99. doi:10.3390/membranes10050099
Schaefer, S., Fierro, V., Izquierdo, M. T., and Celzard, A. (2016). Assessment of Hydrogen Storage in Activated Carbons Produced from Hydrothermally Treated Organic Materials. Int. J. Hydrogen Energ. 41, 12146–12156. doi:10.1016/j.ijhydene.2016.05.086
Sellers, T., McGinnis, G. D., Ruffin, T. M., and Janiga, E. R. (2004). Lignin-modified Phenol-Formaldehyde Resin Development for Fiberboard. For. Prod. J. 54, 45–51.
Sevilla, M., Diez, N., Ferrero, G. A., and Fuertes, A. B. (2019). Sustainable Supercapacitor Electrodes Produced by the Activation of Biomass with Sodium Thiosulfate. Energ. Storage Mater. 18, 356–365. doi:10.1016/j.ensm.2019.01.023
Sharma, P., and Bhatti, T. S. (2010). A Review on Electrochemical Double-Layer Capacitors. Energ. Convers. Manage. 51, 2901–2912. doi:10.1016/j.enconman.2010.06.031
Sima, G., Gan, L., Chang, L., Cui, Y., and Kankala, R. K. (2021). Efficient Fabrication of Ordered Mesoporous Carbon Derived from Lignin via Deep Eutectic Solvent Pretreatment for Supercapacitors. Microporous Mesoporous Mater. 323, 111192. doi:10.1016/j.micromeso.2021.111192
Simitzis, J., and Sfyrakis, J. (1993). Pyrolysis of Lignin Biomass-Novolac Resin for the Production of Polymeric Carbon Adsorbents. J. Anal. Appl. Pyrolysis 26, 37–52. doi:10.1016/0165-2370(93)85017-s
Soltani, N., Bahrami, A., Giebeler, L., Gemming, T., and Mikhailova, D. (2021). Progress and Challenges in Using Sustainable Carbon Anodes in Rechargeable Metal-Ion Batteries. Prog. Energ. Combustion Sci. 87, 100929. doi:10.1016/j.pecs.2021.100929
Song, Y., Wang, Z., Yan, N., Zhang, R., and Li, J. (2016). Demethylation of Wheat Straw Alkali Lignin for Application in Phenol Formaldehyde Adhesives. Polymers 8, 209. doi:10.3390/polym8060209
Ståhlberg, T., Fu, W., Woodley, J. M., and Riisager, A. (2011). Synthesis of 5-(Hydroxymethyl)furfural in Ionic Liquids: Paving the Way to Renewable Chemicals. ChemSusChem 4, 451–458. doi:10.1002/cssc.201000374
Sternberg, J., Sequerth, O., and Pilla, S. (2021). Green Chemistry Design in Polymers Derived from Lignin: Review and Perspective. Prog. Polym. Sci. 113, 101344. doi:10.1016/j.progpolymsci.2020.101344
Stevens, D. A., and Dahn, J. R. (2001). The Mechanisms of Lithium and Sodium Insertion in Carbon Materials. J. Electrochem. Soc. 148, A803. doi:10.1149/1.1379565
Sun, S., Zhang, C., Yao, J., Wang, H., Zhao, X., and Shen, X. (2020). Resol and Urea Derived N-Doped Porous Carbon for Na-Ion Storage. Mater. Chem. Phys. 254, 123535. doi:10.1016/j.matchemphys.2020.123535
Suryanarayana, C. (2001). Mechanical Alloying and Milling. Prog. Mater. Sci. 46, 1–184. doi:10.1016/s0079-6425(99)00010-9
Szczesniak, B., Phuriragpitikhon, J., Choma, J., and Jaroniec, M. (2020). Recent Advances in the Development and Applications of Biomass-Derived Carbons with Uniform Porosity. J. Mater. Chem. A. 8, 18464–18491.
Tanaka, S., Fujimoto, H., Denayer, J. F. M., Miyamoto, M., Oumi, Y., and Miyake, Y. (2015). Surface Modification of Soft-Templated Ordered Mesoporous Carbon for Electrochemical Supercapacitors. Microporous Mesoporous Mater. 217, 141–149. doi:10.1016/j.micromeso.2015.06.017
Tarascon, J.-M., and Armand, M. (2001). Issues and Challenges Facing Rechargeable Lithium Batteries. Nature 414, 359–367. doi:10.1038/35104644
Titirici, M.-M., White, R. J., Brun, N., Budarin, V. L., Su, D. S., del Monte, F., et al. (2015). Sustainable Carbon Materials. Chem. Soc. Rev. 44, 250–290. doi:10.1039/c4cs00232f
Tonnoir, H., Huo, D., Canevesi, R. L. S., Fierro, V., Celzard, A., and Janot, R. (2021). Tannin-Based Hard-Carbons as High-Performance Anode Materials for Sodium-Ion Batteries. Mater. Today Chem. 23, 100614. doi:10.1016/j.mtchem.2021.100614
Torres, D., Pérez-Rodríguez, S., Cesari, L., Castel, C., Favre, E., Fierro, V., et al. (2021). Review on the Preparation of Carbon Membranes Derived from Phenolic Resins for Gas Separation: From Petrochemical Precursors to Bioresources. Carbon 183, 12–33. doi:10.1016/j.carbon.2021.06.087
T. Q. Hu (Editor) (2002). Chemical Modification, Properties, and Usage of Lignin (Boston, MA: Springer). 978-1-4613-5173-3.
Trick, K. A., and Saliba, T. E. (1995). Mechanisms of the Pyrolysis of Phenolic Resin in a Carbon/phenolic Composite. Carbon 33, 1509–1515. doi:10.1016/0008-6223(95)00092-r
Van Nieuwenhove, I., Renders, T., Lauwaert, J., De Roo, T., De Clercq, J., and Verberckmoes, A. (2020). Biobased Resins Using Lignin and Glyoxal. ACS Sust. Chem. Eng. 8, 18789–18809. doi:10.1021/acssuschemeng.0c07227
Vázquez, G., González, J., Freire, S., and Antorrena, G. (1997). Effect of Chemical Modification of Lignin on the Gluebond Performance of Lignin-Phenolic Resins. Bioresour. Tech. 60, 191–198. doi:10.1016/s0960-8524(97)00030-8
Vinodh, R., Muralee Gopi, C. V. V., Yang, Z., Deviprasath, C., Atchudan, R., Raman, V., et al. (2020). Novel Electrode Material Derived from Porous Polymeric Organic Framework of Phloroglucinol and Terephthaldehyde for Symmetric Supercapacitors. J. Energ. Storage 28, 101283. doi:10.1016/j.est.2020.101283
Wang, H., Eberhardt, T. L., Wang, C., Gao, S., and Pan, H. (2019). Demethylation of Alkali Lignin with Halogen Acids and its Application to Phenolic Resins. Polymers 11, 1771. doi:10.3390/polym11111771
Wang, H., Shao, Y., Mei, S., Lu, Y., Zhang, M., Sun, J.-k., et al. (2020a). Polymer-Derived Heteroatom-Doped Porous Carbon Materials. Chem. Rev. 120, 9363–9419. doi:10.1021/acs.chemrev.0c00080
Wang, X., Qiu, M., Smith, R. L., Yang, J., Shen, F., and Qi, X. (2020b). Ferromagnetic Lignin-Derived Ordered Mesoporous Carbon for Catalytic Hydrogenation of Furfural to Furfuryl Alcohol. ACS Sust. Chem. Eng. 8, 18157–18166. doi:10.1021/acssuschemeng.0c06533
Wang, Y.-Y., Meng, X., Pu, Y., and J. Ragauskas, A. (2020c). Recent Advances in the Application of Functionalized Lignin in Value-Added Polymeric Materials. Polymers 12, 2277. doi:10.3390/polym12102277
Wu, M., Liao, J., Yu, L., Lv, R., Li, P., Sun, W., et al. (2020). 2020 Roadmap on Carbon Materials for Energy Storage and Conversion. Chem. Asian J. 15, 995–1013. doi:10.1002/asia.201901802
Xi, J., Li, H., Xi, J., Tan, S., Zheng, J., and Tan, Z. (2020). Preparation of High Porosity Biochar Materials by Template Method: a Review. Environ. Sci. Pollut. Res. 27, 20675–20684. doi:10.1007/s11356-020-08593-8
Xie, A., Dai, J., Chen, Y., Liu, N., Ge, W., Ma, P., et al. (2019). NaCl-template Assisted Preparation of Porous Carbon Nanosheets Started from Lignin for Efficient Removal of Tetracycline. Adv. Powder Tech. 30, 170–179. doi:10.1016/j.apt.2018.10.020
Xie, L., Jin, Z., Dai, Z., Chang, Y., Jiang, X., and Wang, H. (2020). Porous Carbons Synthesized by Templating Approach from Fluid Precursors and Their Applications in Environment and Energy Storage: A Review. Carbon 170, 100–118. doi:10.1016/j.carbon.2020.07.034
Xie, L., Tang, C., Bi, Z., Song, M., Fan, Y., Yan, C., et al. (2021). Hard Carbon Anodes for Next‐Generation Li‐Ion Batteries: Review and Perspective. Adv. Energ. Mater. 11, 2101650. doi:10.1002/aenm.202101650
Xie, M., Dong, H., Zhang, D., Guo, X., and Ding, W. (2011). Simple Synthesis of Highly Ordered Mesoporous Carbon by Self-Assembly of Phenol-Formaldehyde and Block Copolymers under Designed Aqueous Basic/acidic Conditions. Carbon 49, 2459–2464. doi:10.1016/j.carbon.2011.02.014
Xie, X., Goodell, B., Zhang, D., Nagle, D. C., Qian, Y., Peterson, M. L., et al. (2009). Characterization of Carbons Derived from Cellulose and Lignin and Their Oxidative Behavior. Bioresour. Tech. 100, 1797–1802. doi:10.1016/j.biortech.2008.09.057
Xing, T., Zheng, Y., Li, L. H., Cowie, B. C. C., Gunzelmann, D., Qiao, S. Z., et al. (2014). Observation of Active Sites for Oxygen Reduction Reaction on Nitrogen-Doped Multilayer Graphene. ACS Nano 8, 6856–6862. doi:10.1021/nn501506p
Xu, K. (2004). Nonaqueous Liquid Electrolytes for Lithium-Based Rechargeable Batteries. Chem. Rev. 104, 4303–4418. doi:10.1021/cr030203g
Xu, C., De, S., Balu, A. M., Ojeda, M., and Luque, R. (2015). Mechanochemical Synthesis of Advanced Nanomaterials for Catalytic Applications. Chem. Commun. 51, 6698–6713. doi:10.1039/c4cc09876e
Xu, C., and Ferdosian, F. (2017). Conversion of Lignin into Bio-Based Chemicals and Materials. Springer.
Xu, C., Zhang, Y., Zhang, N., Liu, X., Yi, J., Liu, X., et al. (2020). 2020 Roadmap on Zinc Metal Batteries. Chem. Asian J. 15, 3696–3708. doi:10.1002/asia.202000946
Xu, Z., and Guo, Q. (2013). A Simple Method to Prepare Monodisperse and Size-Tunable Carbon Nanospheres from Phenolic Resin. Carbon 52, 464–467. doi:10.1016/j.carbon.2012.09.057
Xue, R., Yan, J., Liu, X., Tian, Y., and Yi, B. (2011). Effect of Activation on the Carbon Fibers from Phenol-Formaldehyde Resins for Electrochemical Supercapacitors. J. Appl. Electrochem. 41, 1357–1366. doi:10.1007/s10800-011-0357-1
Yahya, M. A., Al-Qodah, Z., and Ngah, C. W. Z. (2015). Agricultural Bio-Waste Materials as Potential Sustainable Precursors Used for Activated Carbon Production: A Review. Renew. Sust. Energ. Rev. 46, 218–235. doi:10.1016/j.rser.2015.02.051
Yang, Z., Guo, H., Li, F., Li, X., Wang, Z., Cui, L., et al. (2018). Cooperation of Nitrogen-Doping and Catalysis to Improve the Li-Ion Storage Performance of Lignin-Based Hard Carbon. J. Energ. Chem. 27, 1390–1396. doi:10.1016/j.jechem.2018.01.013
Yeddanapalli, L. M., and Joseph Francis, D. (1962). Kinetics and Mechanism of the Alkali Catalysed Condensation of O- and P-Methylol Phenols by Themselves and with Phenol. Makromol. Chem. 55, 74–86. doi:10.1002/macp.1962.020550106
Yin, J., Zhang, W., Alhebshi, N. A., Salah, N., and Alshareef, H. N. (2020). Synthesis Strategies of Porous Carbon for Supercapacitor Applications. Small Methods 4, 1900853. doi:10.1002/smtd.201900853
Yoon, G., Kim, H., Park, I., and Kang, K. (2016). Conditions for Reversible Na Intercalation in Graphite: Theoretical Studies on the Interplay Among Guest Ions, Solvent, and Graphite Host. Adv. Energ. Mater. 7, 1601519. doi:10.1002/aenm.201601519
Yu, J., and So, J. (2019). Synthesis and Characterization of Nitrogen-Containing Hydrothermal Carbon with Ordered Mesostructure. Chem. Phys. Lett. 716, 237–246. doi:10.1016/j.cplett.2018.12.014
Zakoshansky, V. M. (2007). The Cumene Process for Phenol-Acetone Production. Pet. Chem. 47, 273–284. doi:10.1134/s096554410704007x
Zakrzewska, M. E., Bogel-Łukasik, E., and Bogel-Łukasik, R. (2011). Ionic Liquid-Mediated Formation of 5-Hydroxymethylfurfural-A Promising Biomass-Derived Building Block. Chem. Rev. 111, 397–417. doi:10.1021/cr100171a
Zhang, H., Zhang, W., Ming, H., Pang, J., Zhang, H., Cao, G., et al. (2018). Design Advanced Carbon Materials from Lignin-Based Interpenetrating Polymer Networks for High Performance Sodium-Ion Batteries. Chem. Eng. J. 341, 280–288. doi:10.1016/j.cej.2018.02.016
Zhang, J., Liang, J., Du, G., Zhou, X., Wang, H., and Wang, H. (2017a). Performance of Cutting and Grinding Wheel Based on Lignin-Phenolic Resin Matrix and Aluminum Oxide. BioRes 12, 9118–9129. doi:10.15376/biores.12.4.9118-9129
Zhang, P., Wang, L., Yang, S., Schott, J. A., Liu, X., Mahurin, S. M., et al. (2017b). Solid-state Synthesis of Ordered Mesoporous Carbon Catalysts via a Mechanochemical Assembly through Coordination Cross-Linking. Nat. Commun. 8, 15020. doi:10.1038/ncomms15020
Zhang, W., Ma, Y., Wang, C., Li, S., Zhang, M., and Chu, F. (2013). Preparation and Properties of Lignin-Phenol-Formaldehyde Resins Based on Different Biorefinery Residues of Agricultural Biomass. Ind. Crops Prod. 43, 326–333. doi:10.1016/j.indcrop.2012.07.037
Zhang, Y., Li, N., Chen, Z., Ding, C., ZHeng, Q., Xu, J., et al. (2020). Synthesis of High-Water-Resistance Lignin-Phenol Resin Adhesive with Furfural as a Crosslinking Agent. Polymers 12, 2805. doi:10.3390/polym12122805
Zhang, Y., Nanda, M., Tymchyshyn, M., Yuan, Z., and Xu, C. (2016a). Mechanical, thermal, and Curing Characteristics of Renewable Phenol-Hydroxymethylfurfural Resin for Application in Bio-Composites. J. Mater. Sci. 51, 732–738. doi:10.1007/s10853-015-9392-3
Zhang, Y., Yuan, Z., Mahmood, N., Huang, S., and Xu, C. (2016b). Sustainable Bio-Phenol-Hydroxymethylfurfural Resins Using Phenolated De-polymerized Hydrolysis Lignin and Their Application in Bio-Composites. Ind. Crops Prod. 79, 84–90. doi:10.1016/j.indcrop.2015.10.048
Zhang, Y., Yuan, Z., and Xu, C. C. (2015). Engineering Biomass into Formaldehyde-free Phenolic Resin for Composite Materials. Aiche J. 61, 1275–1283. doi:10.1002/aic.14716
Zhao, J., Shan, W., Zhang, P., and Dai, S. (2020). Solvent-free and Mechanochemical Synthesis of N-Doped Mesoporous Carbon from Tannin and Related Gas Sorption Property. Chem. Eng. J. 381, 122579. doi:10.1016/j.cej.2019.122579
Keywords: biosourced, phenolic molecules, electrodes, carbon, energy storage
Citation: Quílez-Bermejo J, Pérez-Rodríguez S, Celzard A and Fierro V (2022) Progress in the Use of Biosourced Phenolic Molecules for Electrode Manufacturing. Front. Mater. 9:810575. doi: 10.3389/fmats.2022.810575
Received: 22 November 2021; Accepted: 31 January 2022;
Published: 14 March 2022.
Edited by:
Liming Dai, Case Western Reserve University, United StatesReviewed by:
Jun Maruyama, Osaka Research Institute of Industrial Science and Technology, JapanCopyright © 2022 Quílez-Bermejo, Pérez-Rodríguez, Celzard and Fierro. This is an open-access article distributed under the terms of the Creative Commons Attribution License (CC BY). The use, distribution or reproduction in other forums is permitted, provided the original author(s) and the copyright owner(s) are credited and that the original publication in this journal is cited, in accordance with accepted academic practice. No use, distribution or reproduction is permitted which does not comply with these terms.
*Correspondence: Vanessa Fierro, dmFuZXNzYS5maWVycm9AdW5pdi1sb3JyYWluZS5mcg==; Javier Quílez-Bermejo, amF2aWVyLnF1aWxlei1iZXJtZWpvQHVuaXYtbG9ycmFpbmUuZnI=
Disclaimer: All claims expressed in this article are solely those of the authors and do not necessarily represent those of their affiliated organizations, or those of the publisher, the editors and the reviewers. Any product that may be evaluated in this article or claim that may be made by its manufacturer is not guaranteed or endorsed by the publisher.
Research integrity at Frontiers
Learn more about the work of our research integrity team to safeguard the quality of each article we publish.