- 1Department of Safety Engineering, Heilongjiang University of Science and Technology, Harbin, China
- 2National Professional Center Laboratory of Safety Basic Research for Hydrocarbon Gas Pipeline Transportation Network, Harbin, China
- 3Department of Architectural and Civil Engineering, Heilongjiang University of Science of Technology, Harbin, China
As a critical technical issue, gas extraction borehole sealing significantly restricts the effects of gas extraction. Polymer-modified cement-based composite (PMCC) sealing materials were developed to improve the sealing effect of gas extraction drilling. In this study, a self-built mechanical property and permeability test platform for grouting-based cemented coal bodies was used to test the viscosity, gelation time, and mechanical properties of PMCC sealing materials and the permeability of cemented coal bodies. Through the obtained relevant results, it was demonstrated that the material viscosity of PMCC sealing materials and the permeability and compressive strength of cemented bodies are under the influence of additive ratios. Moreover, the viscosity of sealing materials was found to be linearly related to the gelation time. In particular, the higher the viscosity, the shorter the gelation time. Additionally, on one hand, it was found that the viscosity of such sealing materials is positively correlated to the compressive strength of cemented coal bodies. On the other hand, it forms a negative correlation with their permeability. Based on relevant analysis outcomes, it was deemed that the sufficient hydration reaction and the interspace reticulate microstructure formed by the polymer of PMCC sealing materials allow the cemented coal body to achieve high compressive strength and low permeability.
Introduction
Gas extraction is one of the most important technical approaches with regard to safety in mining operations (Díaz Aguado and González Nicieza, 2007; Aguilera et al., 2014). However, in China, coal seam boreholes sometimes fail due to ineffective sealing. Consequently, problems such as the short hole sealing distance of gas extraction boreholes and poor sealing quality seriously limit boring during gas extraction (Lin et al., 1993; Lin and Cui, 1998; Yao, 2006; Zhang et al., 2013). In the process of borehole sealing, the performance of the used sealing materials has an important influence on the sealing effects of the fractures around boreholes (Zhiyong et al., 2012; Ge et al., 2015).
At present, in the coal mines in China, cement-based materials are primarily used to seal gas extraction boreholes. However, the defects of cement-based materials, such as high brittleness, cracking, and poor mobility, place an adverse influence on their sealing effects. In recent years, gas extraction borehole sealing materials have been extensively studied, and multiple new sealing materials have been proposed, including modified cement-based materials, nanopolymers, flexible gel materials and composite materials. Also, new gas extraction borehole sealing processes have been developed (Zhai et al., 2016; Hao et al., 2018; Ni et al., 2020; Dong et al., 2021a; Dong et al., 2021b; Fu et al., 2021).
By using aluminum powder as the main expansion driving force, Ni et al. (2020) combined the material composite mechanism, microcapsule technology, and expansion mechanism to develop efficient drilling sealing materials. Also, Fu et al. (2021) proposed a bag grouting sealing method and a material with dual expansion sources, high expansion ratio, and good stability, and the proposed method and material were found to be better than the traditional “two sealing and one grouting” method and modified cement. Hao et al. (2018) theoretically demonstrated the feasibility of silica sol (S.G325) as a sealing material for the boreholes used in the extraction of coal mine gases. The experimental results indicated that S.G325 has obvious advantages over other materials because of its greater compactness, stability, and performance after sealing. Zhai et al. (2016) developed a flexible gel (FG) that adapts to borehole deformation and has preferable sealing performance, and the sealing mechanism of the FG was proposed. Dong et al. (2021a) used SiO2, sodium silicate, and styrene–acrylic emulsion to optimize pore structures. The influence of each substance on the pore structure and the physical strength of the sealing materials were qualitatively and quantitatively analyzed. The results showed that the synergistic effects of styrene–acrylic emulsion and SiO2 on improving the cement performance are better than those of a single substance. They also proved the feasibility of applying polyvinyl alcohol/aluminum microcapsule expansion agents (Dong et al., 2021b), and the experimental results showed that microcapsule expansion materials have the advantages of high strength, low porosity, and good sealing.
Among these new materials, modified cement-based materials feature certain advantages, including stable performance, high compressive strength, high permeability resistance, and ease of use and they are mainly selected to seal the gas extraction boreholes in the coal mines of China. Nevertheless, the studies on modified cement-based sealing materials still stick around qualitative research, and there were only few investigations with regard to reinforcing and sealing the action mechanisms of such materials. In addition, some properties of new borehole sealing materials, such as their mobility, gelation time, expansibility, and strength, need to be further verified. Consequently, a lot of new sealing materials are not widely used in the field of coal mining. On this basis, in this study, a curtain grouting-based cemented sealing technique is proposed for gas extraction. The proposed method is expected to alter the mechanical properties around the coal bodies to be cemented, decrease the gas permeability of the coal bodies in cementation areas, and enhance the drilling stability of gas extraction boring by means of grouting-based coal body fracture sealing. This way, the research purpose of improving the efficiency of gas extraction can be achieved. Furthermore, a new polymer modified cement-based composite (PMCC) sealing material was developed using a high-molecular polymer as an additive, based on the optimizing effect of polymers on mechanical characteristics, permeability resistance, and damage resistance of cement-based materials (Emad et al., 2021; Zhang et al., 2021; Bahraq et al., 2022). The mechanical property and permeability test platform were then used to test target parameters such as viscosity, gelation time, unconfined compressive strength, and gas permeability of PMCC at various ratios. It provides further references for perfecting the proposed curtain grouting-based cemented sealing technique and applying PMCC.
Main Experimental Facilities
Experiment Platform Building
The established mechanical property and permeability test platform for grouting-based cemented coal bodies are composed of a test device for the sealing material properties, a grouting cementation test device, and an analytical test device for cemented coal bodies. The test device for the sealing material properties is equipped with a ZKS-100 gelation time meter and a consistometer, and the grouting cementation test device consists of a detachable cemented coal body mold that was designed independently and a manual grouting equipment, as shown in Figure 1 and Figure 2. To be specific, the artificial core molds are made from high-quality stainless steel, and their working pressure is no more than 40 MPa. Also, they can be divided into large-sized and small-sized molds. While the large-sized mold is utilized to make cylinders with a height of 100 mm and a diameter of 50 mm from coal samples, the small-sized mold is capable of producing cylinders with a height of 50 mm and a diameter of 25 mm. As its motion system, the press is supported by a high-quality straight sliding bearing. Considering that the press is independent of the running resistance, it can be flexibly operated, ensuring that all the samples are uniformly pressed. In terms of the booster system, it is a fast and stable jack that is easy to operate. At last, the analytical test device for cemented coal bodies includes an RMT-150 rock mechanical test system and a STY-2 gas permeameter. Respectively, the RMT-150 system is under digital control, has a high degree of automation, and can be used to test the mechanical properties of various materials, including rock. The maximum output of the vertical hydraulic cylinder is 1,000 kN, the piston stroke is 50 mm, the deformation rate is 0.0001–1 mm/s, the loading rate is 0.01–100 kN/s, and the displacement sensor accuracy is 1.5‰ F.S. The STY-2 gas permeameter is designed based on the Darcy law, and it was adopted to measure the gas capability to penetrate porous rocks at a certain pressure difference.
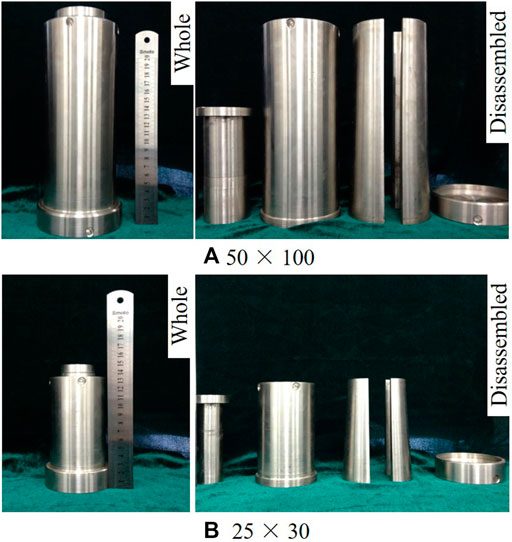
FIGURE 1. Detachable cemented coal body mold that was designed independently. (A) 50 × 100, (B) 25 ×30.
Experimental Material Preparations
PMCC samples with diverse additive ratios were selected as the main material to test the viscosity and gelation time along with the permeability of cemented coal bodies and to perform unconfined compression strength experiments. According to different ratios, coal particles with sizes ranging from 4,000 to 8,000 μm were screened, mixed in a ratio of 1:1, and subsequently compressed into cemented coal bodies (Figure 3). Separately, cemented coal bodies with sizes of 50 × 100mm (Figure 3A) and 25 × 30 mm were used to perform mechanical property experiments and relevant permeability tests, respectively. Before the experiment, the samples were dried in a 105 °C drying box, and then placed in a dryer to wait for the samples to come to room temperature for testing.
Experimental Process
Water–Cement Ratio Optimization for Cement Grouting
The water–cement ratio refers to the mass ratio of water to cement in cement grouts (i.e., mw/mc), and it is an important influencing factor with regard to the effects of grouting. If the water–cement ratio is excessively high, a lot of fine cracks may be generated after the hardening of a cemented body. Consequently, the strength of the cemented body is lowered, but its permeability is increased. On the contrary, colloids fail to be sufficiently formed when the water–cement ratio is too low, causing the grout workability to decline and making it difficult to form compact cemented bodies. Moreover, if the unreacted cement undergoes a secondary hydration reaction after the cemented body is hardened, the hydration products may produce swelling stresses, leading to more cracks. Thus, optimization tests under mw/mc ratios of 0.3:1, 0.5:1, 0.7:1, and 0.9:1 were conducted to test the viscosity and gelation time of cement grouts. Additionally, the cement grouts of the respective water–cement ratios were mixed with coal particles to produce cemented coal bodies through pressing. Furthermore, the cemented coal bodies were subjected to compression tests. For relevant results, please refer to Table 1. It should be noted that the used cement (strength grade: 32.5) in these tests was purchased from Harbin Cement Co., Ltd., Yatai Group.
Based on the aforementioned experiments, it was proven that the grout viscosity is rather high when the water–cement ratio is 0.3; however, it showed a non-flowing character in this condition, failing to meet the relevant testing requirements. In accordance with the experimental data in Table 1, the curves were portrayed to reflect the influencing relations of the water–cement ratio on the viscosity and compressive strength, as presented in Figure 4. Clearly, the grout viscosity gradually decreased with the increase in the water–cement ratio and was also at a moderate level, thus meeting the test requirements. Also, based on the compressive strength curves, the compressive strength of the cemented coal bodies was 3.29, 6.02, and 4.37 Mpa when the water–cement ratio was set to 0.5, 0.7, and 0.9, respectively. With the increase in the water–cement ratio, the compressive strength of the cemented coal body inclined to first go up and then go down. This indicates that the peak compressive strength was formed within this range of the water–cement ratio. Through the binomial fitting of the testing results, it became clear that the peak value appeared when the water–cement ratio ranged between 0.6 and 0.85. Based on the mentioned analysis results, we determined the best three water–cement ratios for composite sealing materials: 0.65, 0.75, and 0.85.
Viscosity and Gelation Time Tests for PMCC
During borehole sealing, both the viscosity and gelation time of the used sealing materials are critical parameters. In detail, viscosity has a direct influence on the flowing properties and thus indirectly affects the grouting results. Also, studying the gelation time may help us obtain a more appropriate diffusion radius and more satisfactory sealing effects of the sealing material. Moreover, the gelation time is constituted by the initial and final setting times. The initial setting time refers to the time partially consumed by the sealing materials in losing their plasticity, and the final setting time refers to the time taken by the sealing materials to reach their inherent properties and completely lose their plasticity. The viscosity of PMCC was obtained based on the time taken by the PMCC grout to completely flow out of the consistometer. The gelation time was calculated using the penetrating resistance strength into PMCC. The water–cement ratio, polymer amount, and another two additives (A and B) were selected as influence factors and orthogonal experiments based on the four factors and three levels were designed. The viscosity and gelation time testing results of PMCC were demonstrated, as shown in Table 2.
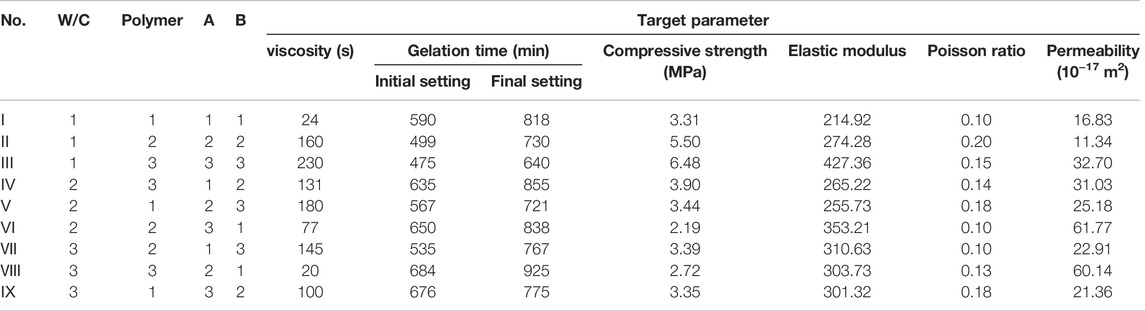
TABLE 2. Orthogonal experimental design and experimental results of target parameters of PMCC sealing materials and cemented coal bodies.
Gas Permeability Tests for the Cemented Coal Bodies Sealed With PMCC
The permeability of the cemented coal body was measured according to the flow of the gas penetrating through cemented coal bodies with given sizes under differential pressure (Yu and Page, 1991; Yu and Page, 1995; Rilem, 1999). In this process, the inlet pressure was set at 0.4 MPa and nitrogen was used as a medium. Considering that the gaseous medium falls into the category of compressible fluids and that gas volume changes may affect the corresponding flow velocity, the permeability computing equation should be modified based on Darcy law. That is, the designed formula was modified into the following equation by introducing another parameter of the mean volume flow rate:
In the aforementioned equation, K (unit: µm2) denotes a proportional constant for the tested coal body to be permeable, P0 (unit: MPa) denotes atmospheric pressure, Q0 (unit: ml/min) denotes the gas flow rate at normal pressure, μ (unit: μPa·s) denotes the viscosity of the gas medium, L (unit: m) denotes the length of the tested coal body, A (unit: m2) denotes the cross-section of the tested coal body, and P1 (unit: MPa) and P2 (unit: MPa) denote the inlet and outlet pressures of the coal rock retainer, respectively. Table 2 lists the permeability testing results of the cemented coal body.
Unconfined Compression Strength Test for the Cemented Coal Bodies Sealed With PMCC
To perform unconfined compression strength tests for the cemented coal bodies, a strain gauge was utilized to obtain relevant strain data by touching the coal body. The corresponding testing platform is given in Figure 5. During the experiment, the surface of the cemented coal bodies was wrapped with plastic film, and the strain gauge was tested close to the surface. Clearly, the total number of horizontal and vertical strain collection sheets was 8. For the purpose of acquiring comparatively complete relation curves of the stress and strain, displacement control was conducted to gradually increase the axial loads at a velocity of 0.010 mm/s. Additionally, mechanical property experiments were performed three times in each group, and the corresponding values were averaged. Their average values were used as the final testing results. This way, the experimental results could be ensured to be more accurate. In the testing process, the used software automatically noted down the stress–strain relations, including the axial and radial strains.
As reflected in the experimental results, the cemented coal body failure process conforms to the elastic-plastic deformation curves. The typical relation curves of stress and strain are given in Figure 6. As revealed in this figure, the curves on the left reflect the relations between the stress and radial strains. At the initial stage of applying the axial load, the radial strain kept decreasing for a period of time and then gradually increased until brittle failures occured. The curves on the right represent the stress and axial strain relations. At the initial stage of applying the axial load, the axial strain gradually increased along with the load increase and eventually reached the corresponding yield limit that led to fracturing. The failure process of the cemented coal body is presented in Figure 7. Before Point A, the cemented coal body showed no obvious changes, and the elastic deformation played a crucial role. In this case, the relation curves of stress and strain were approximately straight. After Point A, the microcracks inside the cemented coal body were extended and developed under the action of stress concentration, giving rise to partial plastic deformation. Under such circumstances, the strain increases were accelerated, and the stress–strain curve gradually deviated from the straight line and bends downward. In addition, the development of microcracks led to greater lateral deformations of the cemented coal body. It is worth mentioning that microcracks were stably developed at this stage. After the failure process reached Point B, some interior microcracks began to be interconnected, and an unstable crack development took place. Accordingly, a lateral deformation was built up. Under the long-term actions of stress, cracks were unceasingly developed, eventually leading to failure. At last, the failure process arrived at Point C. The interconnected cracks inside the cemented coal body formed a failure surface. In this case, the strain growth rate obviously increased, and the peak compressive strength was acquired at Point C (Sagar and Sivakumar, 2021).
Result Analysis
Range and Variance Analysis of the Orthogonal Experimental Results
In orthogonal test analysis, R represents the range of factors. R reflects the maximum variation range of test results for target parameters when factors change.
The test data was analyzed using the variance method to better understand the degree of influence of factor level changes in the test process on the target parameters. First, we calculate the test mean
Then, we calculate the sum of the squares of deviations of all factors and errors in the experiment
We calculate the degree of freedom of each factor in the orthogonal experiment and the degree of freedom of the test error and divide the sum of the squares of deviation of factors and errors by their respective degrees of freedom to get the average sum of squares of deviation. The sum of the average deviations squared of the factors divided by the sum of the average deviations squared of the errors gives the variance ratio F.
The orthogonal experimental results were subjected to both range and variance analyses. The corresponding analytical results were demonstrated, as shown in Table 3. According to these results, the viscosity and gelation time completely had the same influencing rules. Among the four factors affecting the target parameters, factor B had the most significant influence on the viscosity and gelation time, followed by the water–cement ratio, factor A and the polymer amount. Moreover, the viscosity of PMCC was linearly correlated to the corresponding gelation time. The greater its viscosity, the shorter its gelation time, and vice versa. In line with the range analysis results of the compressive strength, the influence of the water–cement ratio on the uniaxial compressive strength of the cemented coal body was most significant. In this aspect, the amount of additive B took second place as far as its impacts on the uniaxial compressive strength are concerned. Furthermore, the sensitivity of the water–cement ratio to the compressive strength was similar to that of the amount of additive B. As for the polymer and the amount of additive B, their sensitivity values were rather low. Also, through the range analysis results of the permeability, it was proven that the amount of additive B had the most significant influence on the permeability of the cemented coal body, while the actions of the polymer amount and water–cement ratio ranked second and third, respectively. Additionally, the sensitivity of the amount of additive A to the target parameters was lowest.
Concerning the variance analysis viscosity results, the variances of factors W/C, polymer, A and B turned out to be 3.163, 1.000, 1.436, and 23.985, respectively. Among them, both B and W/C separately went beyond their critical values (Fα=0.10 for B and Fα=0.25 for W/C). This manifests that the water–cement ratio and additive B amount had obvious influences on the material viscosity. The variances of factors polymer and A were both below the critical values of Fα=0.25, indicating that neither polymer nor the additive A amount had significant influences and that none of them served as an important influencing factor on the experimental results. The gelation time analysis results are the same as those of the viscosity. In other words, factors W/C and B had a significant impact, while no significant influences of the polymer or A were found. Based on the compressive strength analysis results of the cemented coal body, factors W/C and B significantly affected the compressive strength. However, the polymer influence on the compressive strength was moderately significant. In terms of the mechanical properties of the cemented coal body, no significant influences of factor A were proven. With regard to the permeability analysis results, factor B significantly influenced the permeability of the cemented coal body but had no significant impacts on the target parameters.
Influencing Relation Analyses of the Target Parameters
To identify the influencing relations of the viscosity of the sealing material on the compressive strength/permeability of the cemented coal body, viscosity–compressive strength and viscosity–permeability curves were portrayed according to nine groups of different experimental systems to reflect their influencing relations (see Figure 8).
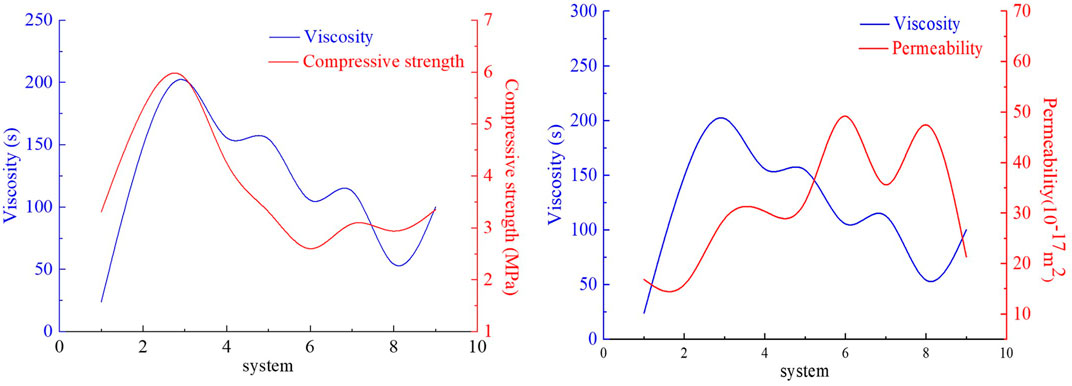
FIGURE 8. Influence curves of viscosity–compressive strength and viscosity–permeability under orthogonal experiment system.
As shown by the viscosity–compressive strength curves, the viscosity of PMCC had a variation tendency identical to that of the compressive strength of the cemented coal body when the experimental system changed. This reveals that viscosity is positively correlated to compressive strength. In other words, the higher the viscosity, the greater the compressive strength. According to the viscosity–permeability curves, it can be seen that the variation tendency of permeability is contrary to that of viscosity. That is, a higher viscosity of the sealing material corresponds to a lower permeability of the cemented coal body. Therefore, the relations between the compressive strength of the cemented coal body and its permeability could be clarified. That is, the greater the compressive strength, the lower the permeability.
Mix Ratio Optimization for PMCC
In accordance with the experimental results in Table 2, the cemented coal body adopting a mix ratio of System 3 had the greatest compressive strength, largest elastic modulus and an unsatisfactory permeability. In addition, the sealing materials in this system presented the highest viscosity and also featured the earliest initial setting time and poor groutability. With respect to the mix ratio selected for System 2, it made the compressive strength of the cemented coal body slightly lower than that in the case of System 3. Additionally, the permeability of the cemented coal body subjected to System 2 was lowest among the nine experimental groups. In terms of the sealing materials in System 2, their viscosity was moderate, which contributed to their grouting into the coal body. From the perspective of PMCC mix ratio optimization, System 2 had a comparatively appropriate sealing material mix ratio, thus applying obvious mechanical reinforcement effects and sealing actions on the grouting-based cemented coal bodies.
The viscosity of sealing material and the permeability and mechanical properties of cemented coal bodies are all under the obvious influence of the additive mix ratio. Through analysis, it was deemed that the hydration reaction degree of PMCC and polymer properties determined both the strength and permeability of cemented coal bodies to some extent. In the hardening process of the sealing material that contacted the coal body, a hydration reaction took place between the cement clinker and water, producing hydrates. Then, the hydrates were mutually overlapped and bound by virtue of multiple attractions, forming a cemented body structure and further producing more strength. Moreover, sufficient hydration reactions corresponded to a closer overlapping and binding of hydrates as well as to more stable structures and greater strength. As a result, the number of porous cracks within the corresponding cemented body declined and the permeability of the cemented body was thus lowered. Simultaneously, the polymer has good bonding properties and can form an interspace reticulate microstructure, which can fill the pores of hydration products, improve the density of hydration products, and produce flexible reinforcement. As a result, the strength of the cemented coal body was further improved and the permeability was reduced.
Conclusion
Both the water–cement ratio and additive B amount in PMCC significantly influence the viscosity and gelation time of sealing materials. The viscosity of sealing materials forms a linear relation with their gelation time. That is, the higher the grout viscosity, the shorter the gelation time.
Both the water–cement ratio and additive B amount in PMCC have a significant influence on the mechanical properties of cemented coal bodies. In addition, the amount of additive B also significantly affects the permeability of cemented coal bodies.
The viscosity of PMCC is positively correlated with the compressive strength of cemented coal bodies but forms a negative correlation with its permeability. Through comprehensive considerations based on the viscosity, gelation time, permeability, and compressive strength of cemented coal bodies, it was found that the sealing material mix ratio of System 2 is most proper, as it had obvious mechanical reinforcement effects and sealing actions on the proposed grouting-based cemented coal body.
The viscosity of sealing material and the permeability and mechanical properties of cemented coal bodies are all under the obvious influence of the additive mix ratio. Through analysis, it was concluded that such a phenomenon is closely related to the hydration reaction degree and the polymer properties of sealing materials. The sufficient hydration reaction and the interspace reticulate microstructure formed by the polymer allow the cemented coal body to achieve high compressive strength and low permeability.
In this article, preliminary studies were performed on the performance of PMCC and on the compressive strength and permeability of its cemented coal bodies. However, extensive research still needs to be performed to ensure that the proposed curtain grouting-based cemented sealing technique can be industrially applied in gas extraction boring.
Data Availability Statement
The raw data supporting the conclusions of this article will be made available by the authors, without undue reservation.
Author Contributions
QZ, YY, and QW contributed to the conception and design of the study. BZ and YY organized the database. YY performed the statistical analysis. YY wrote the first draft of the manuscript. BZ, YY, XG, and QW wrote sections of the manuscript. All authors contributed to manuscript revision and read and approved the submitted version.
Funding
The work reported in this article was funded by the National Natural Science Foundation of China under NSFC Contract Nos. 51774123, 51704103, and 51974112 and Heilongjiang Province Natural Science Foundation of China (E2016058).
Conflict of Interest
The authors declare that the research was conducted in the absence of any commercial or financial relationships that could be construed as a potential conflict of interest.
Publisher’s Note
All claims expressed in this article are solely those of the authors and do not necessarily represent those of their affiliated organizations, or those of the publisher, the editors, and the reviewers. Any product that may be evaluated in this article, or claim that may be made by its manufacturer, is not guaranteed or endorsed by the publisher.
Acknowledgments
Special thanks are due to the National Professional Center Lab of Safety Basic Research for Hydrocarbon Gas Pipeline Transportation Network, Heilongjiang University of Science and Technology in China.
References
Aguilera, R. F., Ripple, R. D., and Aguilera, R. (2014). Link between Endowments, Economics and Environment in Conventional and Unconventional Gas Reservoirs. Fuel 126 (15), 224–238. doi:10.1016/j.fuel.2014.02.063
Bahraq, A. A., Al-Osta, M. A., Al-Amoudi, O. S. B., Saleh, T. A., and Obot, I. B. (2022). Atomistic Simulation of Polymer-Cement Interactions: Progress and Research Challenges. Constr. Build. Mater. 327, 126881. doi:10.1016/j.conbuildmat.2022.126881
Díaz Aguado, M. B., and González Nicieza, C. (2007). Control and Prevention of Gas Outbursts in Coal Mines, Riosa-Olloniego Coalfield, Spain. Int. J. Coal Geol. 69 (4), 253–266. doi:10.1016/j.coal.2006.05.004
Dong, K., Ni, G. H., Nie, B., Xu, Y., Wang, G., Sun, L., et al. (2021). Effect of Polyvinyl Alcohol/aluminum Microcapsule Expansion Agent on Porosity and Strength of Cement-Based Drilling Sealing Material. Energy 224, 119966. doi:10.1016/j.energy.2021.119966
Dong, K., Ni, G. H., Xu, Y. H., Xun, M., Hui, W., Li, S., et al. (2021). Effect of Optimized Pore Structure on Sealing Performance of Drilling Sealing Materials in Coal Mine. Constr. Build. Mater. 274, 121765. doi:10.1016/j.conbuildmat.2020.121765
Emad, W., Salih, A., Kurda, R., and Hassan, A. M. T. (2021). Multivariable Models to Forecast the Mechanical Properties of Polymerized Cement Paste. J. Mater. Res. Technol. 14, 2677–2699. doi:10.1016/j.jmrt.2021.07.137
Fu, J., Li, X., and Wang, Z. (2021). A Novel Sealing Material and a Bag-Grouting Sealing Method for Underground CBM Drainage in China. Constr. Build. Mater. 299 (4), 124016. doi:10.1016/j.conbuildmat.2021.124016
Ge, Z. L., Mei, X. D., Lu, Y. Y., Tang, J., and Xia, B. (2015). Optimization and Application of Sealing Material and Sealing Length for Hydraulic Fracturing Borehole in Underground Coal Mines. Arabian J. Geosciences 8, 3477–3490. doi:10.1007/s12517-014-1488-6
Hao, C., Cheng, Y., Dong, J., Liu, H., Jiang, Z., and Tu, Q. (2018). Effect of Silica Sol on the Sealing Mechanism of a Coalbed Methane Reservoir: New Insights into Enhancing the Methane Concentration and Utilization Rate. J. Nat. Gas Sci. Eng. 56, 51–61. doi:10.1016/j.jngse.2018.05.032
Lin, B. Q., and Cui, H. (1998). Mine Gas Prevention and Control Theory and Technology. Xuzhou: China University of Mining and Technology Press.
Lin, B. Q., Zhou, S. N., and Zhang, R. G. (1993). Investigation of Permeable Mechanisms of Sealing Medium in Sealing Section of Borehole. J. Liaoning Tech. Univ. 4 (2), 25–30.
Ni, G., Dong, K., Li, S., Qian, S., Dongmei, H., Ning, W., et al. (2020). Development and Performance Testing of the New Sealing Material for Gas Drainage Drilling in Coal Mine. Powder Technol. 363, 152–160. doi:10.1016/j.powtec.2019.12.031
Rilem, T. C. (1999). Permeability of Concrete as a Criterion of its Durability. Mater. Struct. 32, 174.
Sagar, B., and Sivakumar, M. V. N. (2021). Compressive Properties and Analytical Modelling for Stress-Strain Curves of Polyvinyl Alcohol Fiber Reinforced Concrete. Constr. Build. Mater. 291 (10), 123192. doi:10.1016/j.conbuildmat.2021.123192
Yao, S. W. (2006). Improving Method and Increasing Effect of Gas Drainage. J. China Coal Soc. 31 (6), 721–716. doi:10.3321/j.issn:0253-9993.2006.06.006
Yu, S. W., and Page, C. L. (1991). Diffusion in Cementitious Materials: 1. Comparative Study of Chloride and Oxygen Diffusion in Hydrated Cement Pastes. Cem. Concr. Res. 21 (4), 581–588. doi:10.1016/0008-8846(91)90109-u
Yu, S. W., and Page, C. L. (1995). Diffusion in Cementitious Materials:Ⅱ. Further Investigations of Chloride and Oxygen Diffusion in Well-Cured OPC and OPC/30%PFA Pastes. Cem. Concr. Res. 25 (4), 819.
Zhai, C., Xiang, X., Zou, Q., Yu, X., and Xu, Y. (2016). Influence Factors Analysis of a Flexible Gel Sealing Material for Coal-Bed Methane Drainage Boreholes. Environ. Earth Sci. 75 (5), 385. doi:10.1007/s12665-016-5286-1
Zhang, C., Lin, B. Q., Zhou, Y., Zhai, C., Wu, J., and Hao, Z. Y. (2013). Strong-weak-strong Borehole Pressurized Sealing Technology for Horizontal Gas Drainage Borehole in Mining Seam. J. Min. Saf. Eng. 30 (6), 935–939.
Zhang, X., Du, M., Fang, H., Shi, M., Zhang, C., and Wang, F. (2021). Polymer-modified Cement Mortars: Their Enhanced Properties, Applications, Prospects, and Challenges. Constr. Build. Mater. 299, 124290. doi:10.1016/j.conbuildmat.2021.124290
Keywords: polymer, composite sealing material, cemented coal body, mechanical properties, permeability
Citation: Zhang B, Yu Y, Gao X, Wu Q, Zhang Q and Liu C (2022) Experimental Study on the Optimization of Polymer-Modified Cement-Based Composite Sealing Materials and Mechanical Properties and Permeability of Cemented Coal Bodies. Front. Mater. 9:774887. doi: 10.3389/fmats.2022.774887
Received: 30 September 2021; Accepted: 19 April 2022;
Published: 20 May 2022.
Edited by:
Asa Barber, London South Bank University, United KingdomReviewed by:
Zhu Baijie, Institute of Engineering Mechanics, ChinaHao Wang, Shenzhen Polytechnic, China
Copyright © 2022 Zhang, Yu, Gao, Wu, Zhang and Liu. This is an open-access article distributed under the terms of the Creative Commons Attribution License (CC BY). The use, distribution or reproduction in other forums is permitted, provided the original author(s) and the copyright owner(s) are credited and that the original publication in this journal is cited, in accordance with accepted academic practice. No use, distribution or reproduction is permitted which does not comply with these terms.
*Correspondence: Yue Yu, eXV5dWVAaWVtLmFjLmNu