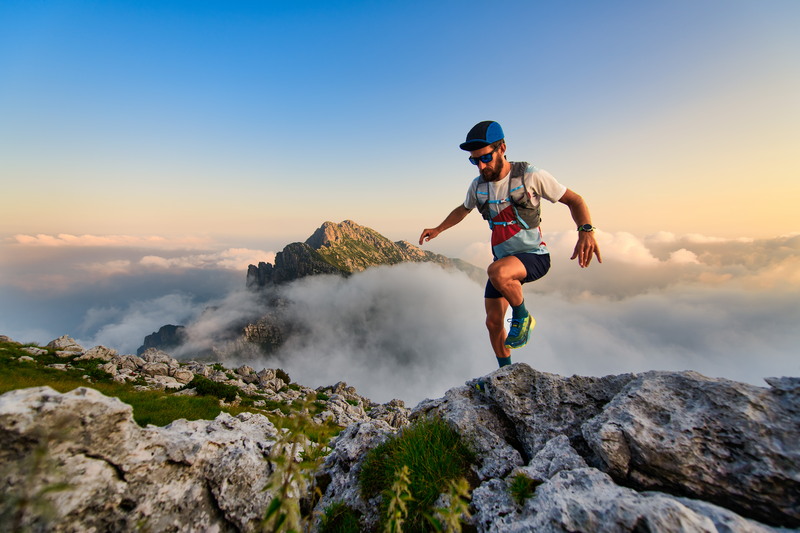
95% of researchers rate our articles as excellent or good
Learn more about the work of our research integrity team to safeguard the quality of each article we publish.
Find out more
MINI REVIEW article
Front. Mater. , 05 January 2023
Sec. Polymeric and Composite Materials
Volume 9 - 2022 | https://doi.org/10.3389/fmats.2022.1118943
This article is part of the Research Topic Additive Manufacturing for Polymers View all 10 articles
Vat polymerization, the earliest and most established 3D printing technology, offers abundant advantages of high-precision fabrication and rapid printing speed, among others. This technology is often applied to fabricated objects with complex and delicate structures, which are of specific interest in numerous fields. However, it suffers from poor mechanical properties of the resultant printed parts due to layer-by-layer manufacturing patterns and the absence of functionality, restricting the broader application of printed objects. Integrating nanomaterials with vat polymerization-based 3D printing endows the creation of products with enhanced properties and unprecedented functional adjunction with flexible designs. Giving a brief description of 3D printing technology, this review illustrates the principles and characteristics of vat polymerization technology. In this mini-review, we emphasize recent advances in nanocomposite fabricated using vat polymerization, predominantly focusing on creating nanocomposites with enhanced mechanical, thermal properties, and electrical conductivity. Finally, we summarize the article with the challenges being faced and future perspectives of nanocomposites fabricated from vat polymerization.
3D printing, often referred to as additive manufacturing, is a disruptive manufacturing technology in which replica physical objects with complicated internal structures are fabricated directly from interacted digital models in a layer-by-layer fashion. In recent times, 3D printing has been employed in various fields of research due to the enormous advantages of product-design freedom, simple customization, and the waste minimization of raw materials, including catalysis (Lawson et al., 2021), electronics (Espera et al., 2019), aerospace (Joshi and Sheikh, 2015), and tissue engineering (Distler and Boccaccini, 2020). According to the principle of pattern formation, 3D printing employs diverse technologies, including material extrusion, binder jetting, material jetting, directed energy deposition, sheet lamination, powder bed fusion, and vat photo polymerization (Lee et al., 2017). Each technology has its pros and cons in terms of practical applicability. Nevertheless, choosing a unique technology often considers the manufacturing material, printing speed, resolution, cost, and performance requirements of the final product (Clarissa et al., 2021).
The lack of reliable load-bearing ability and functionality in 3D-printed structural work pieces makes them insufficiently fabricated as functional end-use products. To address this concern, the possibility of tuning the performances by introducing nanomaterials into 3D printed constructs furnishes an attractive path for achieving high performance and multi-functional integration (Kankala et al., 2018; Valino et al., 2019). Due to the advancement of nanotechnology, incorporating nanofillers (in the range of 1–100 nm) produces different properties than their micro- and macro-sized counterparts (Roduner, 2006). Nanomaterials have a wide range of application prospects owing to their electrical, magnetic, thermal, optical, sensitive properties, and surface stability (Baig et al., 2021). These unique interactions give rise to the optimal control of polymer performance. Several efforts have been dedicated to developing nanocomposites based on 3D printing by incorporating ceramic, metallic, and/or organic fillers to improve thermal, electrical, mechanical, and other properties to overcome the limitations of traditional single-component materials (Campbell and Ivanova, 2013; Hassan et al., 2019; Wang et al., 2020) (Figure 1).
Vat polymerization, the most mature and widely used 3D printing technology, offers the advantages of high resolution and printing efficiency. It can be subdivided into stereolithography appearance (SLA), digital light processing (DLP), liquid crystal display, continuous liquid interface production, two-photon 3D printing, and computed axial lithography (Sampson et al., 2021). Vat polymerization is based on photopolymerization, where a photosensitive liquid resin can be utilized as the raw material. As illustrated in Figure 2, three processes are commonly used: The design of a computer-aided model, the development of vat polymerization, and dispensing for practical applications. During the printing process, laser emitters or a projector projects a pattern of light onto a layer of liquid photosensitive resin that hardens in the desired shape. The platform engaged as the printed part moves in the layer-thickness, and the resin is replenished. This procedure is repeated until the successful construction of the final 3D object. The light source and imaging systems differ for different vat polymerization technologies to some extent, while the control and stepping systems remain similar. The photosensitive resin can be cured under light irradiation at a corresponding wavelength. While in places without irradiation, it can be maintained as a liquid. Hence, parts can be easily separated from the liquid resin. It is noteworthy to acknowledge the high precision of light irradiation and the rapid photocuring polymerization of vat polymerization for the quick printing of complex objects.
Photosensitive resin for vat polymerization is typically composed of initiator, oligomer, monomer (active diluent), and additives (Skliutas et al., 2018). The initiators in photosensitive resin are shifted to highly active intermediates under irradiation at specific wavelengths. These trigger cross-linking reactions between oligomers and monomers in the photosensitive resin, transforming it from the original liquid resin into a solid object. The typical raw materials and photocuring mechanisms are chosen depending on the laser wavelength and the printer projector. Acrylate resins, which undergo a free-radical polymerization mechanism, are the most popular photosensitive resin for vat polymerization technologies due to their high photopolymerization curing speed. However, acrylate resins exhibit large volume shrinkage after photopolymerization, resulting in a reduction in printing precision and the deformation of printed objects. To overcome the problem of volume shrinkage, epoxy resin has been incorporated into cationic photopolymerization (Crivello, 1999). However, the photopolymerization induction period for the cationic photosensitive resin remains longer and has a relatively slower curing rate. Hence, a hybrid photosensitive resin containing acrylate and epoxy resin is an optimal choice when considering volume shrinkage, curing speed, and cost when the light source matches. Although numerous studies have been devoted to obtaining multiple printed parts by adjusting and designing segments constructed by photosensitive resin polymer backbones (Peng et al., 2020; Zhou et al., 2020; Yiming et al., 2021), currently, vat polymerization products generally suffer from several disadvantages, such as fragility, ease of deformation, poor thermal resistance, and low biocompatibility. However, there is an urgent need for higher-performance products to meet high-end application demands.
The demand for lightweight, high-strength materials is increasing in various engineering sectors. Polymeric composites, including nanofillers, offer outstanding improvements at relatively lower loadings than micro-sized fillers, helping achieve high-level performance improvements across various advanced applications (Quaresimin et al., 2012). Recently, the mechanical properties of engineered structural components, including structural integrity and durability, produced by vat polymerization have been enhanced by incorporating second-phase nanofillers.
Nanoparticles are widely used to enhance the mechanical properties of vat polymerization polymers because of their low cost and the significant enhancements they deliver, of which, SiO2 nanoparticles are the most widely used. In an instance, (Weng et al., 2016) and colleagues demonstrated that the absorption and scattering of UV light by SiO2 nanoparticles were weaker than that of other 1D and 2D materials containing silicon elements (i.e., attapulgite and montmorillonite), which improved the tensile strength and elastic modulus of SiO2-containing nanocomposites. In another instance, Chiappone and coworkers (Chiappone et al., 2016) introduced the precursor tetraethoxysilane to a photosensitive resin and post-treated samples with acidic vapor to generate SiO2 nanoparticles in situ by the sol-gel reaction of the precursor in the polymer network after DLP printing. The generation of a SiO2 inorganic phase contributed to significant enhancement of the tensile and compressive strengths, modulus, and surface hardness of the fabricated samples due to the preferential growth of induced nanoparticles on the surface of the samples. Moreover, different surface treatments create diverse nanoparticle interfacial adhesion and dispersion stability, leading to altered mechanical properties of various nanocomposites (Song et al., 2018). Some other 1D nanomaterials, including nano-TiO2 (Duan et al., 2011), Cu nanopowder (Vidakis et al., 2022), and polyhedral oligomeric silsesquioxane (Li et al., 2019), have been used as reinforcing phases for photosensitive resins. In addition, the specific orientation of reinforcing fillers is believed to supply the creation of composites with design properties (Martin et al., 2015).
Carbon nanotubes (CNTs) are structurally stable, long, thin carbon columns with high aspect ratios. These CNTs often exhibit excellent polymer reinforcement due to their ability to cause the formation of higher-order interphase polymer layers and promote mechanical strength through interfacial stress transfer between nanotubes and polymers (Wong et al., 2003; Spitalsky et al., 2010). Creating CNT composites with photosensitive resins greatly improves the performance of the matrix. Sandoval et al., (2007) demonstrated that the ultimate tensile and fracture stress of SLA epoxy-based resins increased by 17% and 37%, respectively, with the introduction of .05% (w/v) multiwall CNTs (MWCNTs). Introducing MWCNTs would create strong interfacial bonding between the SLA epoxy matrix and buckled MWCNTs. However, the resultant mechanical properties of nanocomposites depended on the arrangement of CNTs in resins (Chavez et al., 2019). In addition, other 1D nanofillers, such as boehmite nanowires (Han et al., 2018), Al2O3 nanowires (Han et al., 2017), and cellulose nanocrystals (Kumar et al., 2012), have been incorporated into photosensitive resins for vat polymerization to enhance mechanical properties.
Graphene, a single layer of carbon atoms, consists of a backbone of sp2 hybrid bonds filled in a honeycomb lattice. 2p orbitals forming the π state bands delocalize over the carbon layer and result in the highly stiff characteristic graphene (Papageorgiou et al., 2017), which is often applied in photosensitive resins (Li et al., 2018). The combination of enhanced strength and flexibility in SLA manufacturing is realized by introducing graphene oxide (GO), which is related to increasing the crystallinity of nanocomposites (Lin et al., 2015). Nanocomposites prepared by the bottom-up vat polymerization exhibit significant anisotropic mechanical properties because graphene nanosheets tend to be arranged more parallel in resins during 3D printing (Markandan and Lai, 2020). The annealing process after the completion of printing also affects the mechanical properties of nanocomposites (Manapat et al., 2017). In addition, Ti3C2 MXene, a novel 2D ultrathin nanomaterial, is an excellent candidate for enhancing the tensile strength of photosensitive resins to obtain reliable elastomers (Li et al., 2022a). The dispersion effect of nanofillers in photosensitive resins contributes directly to the strengthening development of 3D printed objects. A uniformly dispersed nanofiller can effectively absorb and dissipate energy, improving the mechanical properties of nanocomposites in terms of fracturing. Agglomerated nanofillers induce the formation of micro flaws, deteriorating the mechanical properties. Therefore, there is an optimum loading level for incorporated nanofillers to increase the mechanical strength of nanocomposites from vat polymerization.
A growing task in the design and application of advanced devices is heat management. In this context, an expanding demand for high thermal conductivity materials that can dissipate waste heat from the operation processes of devices exists. The preparation of composites by introducing fillers, such as graphene, metal, and inorganic nanomaterials, is a promising strategy for improving the thermal conductivity of photosensitive resins (Lee et al., 2021; Pezzana et al., 2021). Carbon fibers, due to their remarkable thermal conductivity and high aspect ratio, are also widely used to enhance the thermal conductivity of polymers, which is beneficial for forming nanocomposite percolating networks (Hong et al., 2010). In a case, acidified vapor-grown carbon nanofiber (VGCF)-supplemented dual-cure photosensitive resins were prepared by the SLA technology (Li et al., 2022b). The addition of 2% w/w VGCFs increased the thermal conductivity of a composite by 79% compared to control through the transfer of thermal energy by VGCF phonons.
High filler loadings are typically necessary to achieve appropriately enhanced thermal conductivity in polymeric matrices. It has been reported that the 7.4 wt% loading of a polymer with graphene caused nozzle clogging in a fused filament fabrication printer (Wei et al., 2015). For vat polymerization, using liquid resin would avoid the problem of the repeated clogging of nozzles or spraying devices due to the introduced nanofillers. This would create a quantum leap in the thermal conductivity of printed products through the high loading of nanofillers. However, vat polymerization remains a significant challenge due to the processing requirements of photoactivity and viscosity. Yang et al., (2022) prepared a nanocomposite with a high loading (60 wt%) of micro silica, resulting in the improved thermal conductivity of .44 W m−1 K−1, with 196.91% compared with the pure matrix. Nanocomposites assembled with high thermal conductivity due to closely arranged phonon transportation pathways in resin matrices could be applied to fabrication injection and vacuum casting molding to extend the service life. In addition, the fabrication of ultralow thermal conductivity thermoelectric materials can be realized by mixing thermoelectric materials, including Bi0.5Sb1.5Te3 (He et al., 2015) and Ag2Se (Park et al., 2021) materials, with photosensitive resins.
Incorporating nanoparticles also offers the possibility of improving the thermal stability of vat-polymerized printed fabrications. However, it should be noted that the thermal stability of the composite is influenced by the organic modifier, filler content, and structural features of nanocomposites (Leszczyńska et al., 2007). The introduction of nanoparticles can also effectively enhance the thermal resistance of nanocomposites (Chiu and Wu, 2008). Zhang et al., (2015) and colleagues dispersed SiO2 nanoparticles, which modified the silane coupling agent, into a photosensitive resin by ultrasonic and a planetary ball mill treatment, followed by 3D printing. The glass-transition temperature of the nanocomposites increased from 67.28°C for the pure resin to 80.18°C for the nanocomposites with the addition of .7 wt% SiO2. Similarly, the addition of a 1D nanomaterial, microcrystalline cellulose, had a formative influence on the thermal properties of the photosensitive resin, which increased the degradation temperature of the nanocomposite, and the β-relaxation of the photosensitive resin tended to move toward higher temperatures (Han et al., 2017).
3D printing has been used as an alternative approach for manufacturing conductive composites due to the advantages of reduced cost and eco-friendly features, which are of unique interest in various functional applications, such as electrodes (Ahn et al., 2009; Rymansaib et al., 2016), wearable devices (Hao et al., 2021), and sensors (Leigh et al., 2017). This method balances a low-cost, fast, and versatile production process with the excellent performance of the resultant products.
Metal fillers with good conductivity have been used for conductive materials in vat polymerization. Fantino and coworkers (Fantino et al., 2016) introduced silver nitrate to a photosensitive resin. The silver nitrate was reduced to silver nanoparticles via a UV post-curing process after DLP printing to prepare conductive nanocomposites. The direct loading of the filler affected the electrical conductivity of the composites: Increased amounts of silver nitrate increased the silver nanoparticle content in the matrix, thereby promoting the formation of charge movement paths between the nanoparticles, which led to a decline in the electrical resistance of the nanocomposites. However, due to its prohibitive cost and ease of oxidation, the application of metal has been limited.
In comparison, carbon fillers exhibit considerable stability and high conductivity, which makes them easier to obtain and more widely used (Gonzalez et al., 2017; Zhang et al., 2017). Therefore, CNTs are widely used due to their excellent electrical properties arising from the freedom of the movement of unpaired electrons in orbitals perpendicular to the π-π plane within the plane. Mu et al., (2017) and colleagues combined commercial photosensitive resin with MWCNTs to obtain conductive composite structures using a DLP printer. To optimize printability and conductivity, .3 wt% of MWCNTs was added, increasing the nanocomposite conductivity to .027 S m−1. Guo and coworkers (Guo et al., 2020) prepared a DLP-printed conductive nanocomposite with 2 wt% carboxyl CNTs that exhibited an electrical conductivity of .13 S m−1. These shreds of evidence indicated that the composites with high conductivity, high gauge strain sensors, and superior cycling stability could provide stable signal information for human motion monitoring.
The use of graphene is also an effective strategy for increasing the electrical conductivity of photosensitive resins. Since GO has better compatibility with photosensitive resins, GO can be used directly as a filler. It is reduced to graphene during post-processing after printing, and different post-processing processes affect the electrical conductivity of the samples (Chiappone et al., 2017). Nanocomposites post-cured by UV light exhibit a non-linear electrical correspondence due to uneven internal curing, while homogeneous thermally post-cured models show a linear electrical response. In addition, the combination of 1D and 2D nanofillers provides effective conductive pathways in nanocomposites and has been used to produce conductive structures (Han and Cho, 2018).
Although numerous designs of vat polymerization-based 3D printed nanocomposites have been prepared, there is still a gap in meeting the demands of industrial applications, and many impediments, from molding craft to product performance, remain unsolved. First, the viscosity of photosensitive resin tends to increase with increased nanofiller content. Meanwhile, the polymer self-diffusion coefficient is reduced (Mu et al., 2009), challenging the leveling properties of photosensitive resin and thus affecting the surface quality of printed products (Gurr et al., 2008). Second, the random scattering of UV light in a photosensitive resin observed in vat polymerization has been attributed to either the aggregation of nanoparticles or the incorporation of overlarge nanofillers (Cho et al., 2005), resulting in reduced UV penetration depth and lateral resolution. Nevertheless, it should be noted that slower speeds and/or higher laser power are required to remedy the degeneration of curing depth and group conversions (Cheah et al., 1999). Third, it is difficult to disperse nanofillers uniformly with high surface energy in photosensitive resins, and weak interfacial interaction usually leads to poor performance of the fabricated parts. At the same time, the density of nanofillers and photosensitive resins usually differs, resulting in a tendency to settle in the resin without forming a stable dispersion. Therefore, the chemical compatibility of nanofillers with photosensitive resins must be considered to improve the stability of the resins, which contain nanofillers, and enhance the performance of printed parts.
Overcoming the current bottleneck in the vat polymerization-based 3D printing of nanocomposites requires a further reduction in the production costs of nanofillers and the improved compatibility of nanofillers and resin matrices. These aspects will undoubtedly result in the excellent performance and competitiveness of fabricated products towards the further development of the main directions. Various new vat-polymerized nanocomposites with outstanding performance, including magnetic, catalytic, and dielectric properties and so on, should be developed to meet new frontiers and evolving technology requirements. The evaluation criteria of vat-polymerized nanomaterials are necessary to establish and improve, favoring the development of new composites and selecting suitable materials for various applications.
YL investigated and processed the data, pointed out the framework of the paper, made a summary and analysis, supported the project and completed the writing of the article. WW and FW participated in proofreading and part of the writing. At the same time, RKK reviewed the paper.
This work was supported by the National Natural Science Foundation of China (32071323), the Natural Science Foundation of Fujian Province (2021J05054), the Fundamental Research Funds for the Central University (ZQN-1004), and the Scientific Research Funds of Huaqiao University (20BS302).
The authors declare that the research was conducted in the absence of any commercial or financial relationships that could be construed as a potential conflict of interest.
All claims expressed in this article are solely those of the authors and do not necessarily represent those of their affiliated organizations, or those of the publisher, the editors and the reviewers. Any product that may be evaluated in this article, or claim that may be made by its manufacturer, is not guaranteed or endorsed by the publisher.
Ahn, B. Y., Duoss, E. B., Motala, M. J., Guo, X., Park, S. I., Xiong, Y., et al. (2009). Omnidirectional printing of flexible, stretchable, and spanning silver microelectrodes. Science 323, 1590–1593. doi:10.1126/science.1168375
Baig, N., Kammakakam, I., Falath, W., and Nanomaterials, (2021). Nanomaterials: A review of synthesis methods, properties, recent progress, and challenges. Mat. Adv. 2, 1821–1871. doi:10.1039/d0ma00807a
Campbell, T. A., and Ivanova, O. S. (2013). 3D printing of multifunctional nanocomposites. Nano Today 8, 119–120. doi:10.1016/j.nantod.2012.12.002
Chavez, L. A., Regis, J. E., Delfin, L. C., Rosales, C. A. G., Kim, H., Love, N., et al. (2019). Electrical and mechanical tuning of 3D printed photopolymer–MWCNT nanocomposites through in situ dispersion. J. Mat. Sci. 136, 47600. doi:10.1002/app.47600
Cheah, C. M., Fuh, J. Y. H., Nee, A. Y. C., and Lu, L. (1999). Mechanical characteristics of fiber-filled photo-polymer used in stereolithography. Rapid Prototyp. J. 5, 112–119. doi:10.1108/13552549910278937
Chiappone, A., Fantino, E., Roppolo, I., Lorusso, M., Manfredi, D., Fino, P., et al. (2016). 3D printed PEG-based hybrid nanocomposites obtained by sol-gel technique. ACS Appl. Mat. Interfaces 8, 5627–5633. doi:10.1021/acsami.5b12578
Chiappone, A., Roppolo, I., Naretto, E., Fantino, E., Calignano, F., Sangermano, M., et al. (2017). Study of graphene oxide-based 3D printable composites: Effect of the in situ reduction. Compos. Pt. B-Eng. 124, 9–15. doi:10.1016/j.compositesb.2017.05.049
Chiu, S. H., and Wu, D. C. (2008). Preparation and physical properties of photopolymer/SiO2 nanocomposite for rapid prototyping system. J. Appl. Polym. Sci. 107, 3529–3534. doi:10.1002/app.27535
Cho, J. D., Ju, H. T., and Hong, J. W. (2005). Photocuring kinetics of UV-initiated free-radical photopolymerizations with and without silica nanoparticles. J. Polym. Sci. Pol. Chem. 43, 658–670. doi:10.1002/pola.20529
Clarissa, W. H. Y., Chia, C. H., Zakaria, S., and Ycy, Evyan (2021). Recent advancement in 3-D printing: Nanocomposites with added functionality. Prog. Addit. Manuf. 7, 325–350. doi:10.1007/s40964-021-00232-z
Crivello, J. V. (1999). UV and electron beam-induced cationic polymerization. Nucl. Instrum. Methods Phys. Res. Sect. B Beam Interact. Mater. Atoms 151, 8–21. doi:10.1016/s0168-583x(99)00109-3
Distler, T., and Boccaccini, A. R. (2020). 3D printing of electrically conductive hydrogels for tissue engineering and biosensors–A review. Acta Biomater. 101, 1–13. doi:10.1016/j.actbio.2019.08.044
Duan, Y., Zhou, Y., Tang, Y., and Li, D. (2011). Nano-TiO2-Modified photosensitive resin for RP. Rapid Prototyp. J. 17, 247–252. doi:10.1108/13552541111138360
Espera, A. H., Dizon, J. R. C., Chen, Q., and Advincula, R. C. (2019). 3D-Printing and advanced manufacturing for electronics. Prog. Addit. Manuf. 4, 245–267. doi:10.1007/s40964-019-00077-7
Fantino, E., Chiappone, A., Roppolo, I., Manfredi, D., Bongiovanni, R., Pirri, C. F., et al. (2016). 3D printing of conductive complex structures with in situ generation of silver nanoparticles. Adv. Mat. 28, 3712–3717. doi:10.1002/adma.201505109
Gonzalez, G., Chiappone, A., Roppolo, I., Fantino, E., Bertana, V., Perrucci, F., et al. (2017). Development of 3D printable formulations containing CNT with enhanced electrical properties. Polymer 109, 246–253. doi:10.1016/j.polymer.2016.12.051
Guo, B., Ji, X., Chen, X., Li, G., Lu, Y., and Bai, J. (2020). A highly stretchable and intrinsically self-healing strain sensor produced by 3D printing. Virtual Phys. Prototyp. 15, 520–531. doi:10.1080/17452759.2020.1823570
Gurr, M., Hofmann, D., Ehm, M., Thomann, Y., Kübler, R., and Mülhaupt, R. (2008). Acrylic nanocomposite resins for use in stereolithography and structural light modulation based rapid prototyping and rapid manufacturing technologies. Adv. Funct. Mat. 18, 2390–2397. doi:10.1002/adfm.200800344
Han, H., and Cho, S. (2018). Fabrication of conducting polyacrylate resin solution with polyaniline nanofiber and graphene for conductive 3D printing application. Polymers 10, 1003. doi:10.3390/polym10091003
Han, Y., Wang, F. K., Wang, H., Jiao, X., and Chen, D. (2018). High-strength boehmite-acrylate composites for 3D printing: Reinforced filler-matrix interactions. Compos. Sci. Technol. 154, 104–109. doi:10.1016/j.compscitech.2017.10.026
Han, Y., Yeo, C. C. J., Chen, D., Wang, F., Chong, Y., Li, X., et al. (2017). Nanowire enhanced dimensional accuracy in acrylate resin-based 3D printing. New J. Chem. 41, 8407–8412. doi:10.1039/c7nj02145c
Hao, S., Li, T., Yang, X., Song, H., and Ultrastretchable, (2021). Ultrastretchable, adhesive, fast self-healable, and three-dimensional printable photoluminescent ionic skin based on hybrid network ionogels. ACS Appl. Mat. Interfaces 14, 2029–2037. doi:10.1021/acsami.1c21325
Hassan, M., Dave, K., Chandrawati, R., Dehghani, F., and Gomes, V. G. (2019). 3D printing of biopolymer nanocomposites for tissue engineering: Nanomaterials, processing and structure-function relation. Eur. Polym. 12, 1109340.
He, M., Zhao, Y., Wang, B., Xi, Q., Zhou, J., and Liang, Z. (2015). 3D printing fabrication of amorphous thermoelectric materials with ultralow thermal conductivity. Small 11, 5889–5894. doi:10.1002/smll.201502153
Hong, J., Park, D. W., and Shim, S. E. (2010). A review on thermal conductivity of polymer composites using carbon-based fillers: Carbon nanotubes and carbon fibers. Carbon Lett. 11, 347–356. doi:10.5714/cl.2010.11.4.347
Joshi, S. C., and Sheikh, A. A. (2015). 3D printing in aerospace and its long-term sustainability. Virtual Phys. Prototyp. 10, 175–185. doi:10.1080/17452759.2015.1111519
Kankala, R. K., Zhu, K., Sun, X. N., Liu, C. G., Wang, S. B., and andChen, A. Z. (2018). Cardiac tissue engineering on the nanoscale. ACS Biomater. Sci. Eng. 4, 800–818. doi:10.1021/acsbiomaterials.7b00913
Kumar, S., Hofmann, M., Steinmann, B., Foster, E. J., and Weder, C. (2012). Reinforcement of stereolithographic resins for rapid prototyping with cellulose nanocrystals. ACS Appl. Mat. Interfaces 4, 5399–5407. doi:10.1021/am301321v
Lawson, S., Li, X., Thakkar, H., Rownaghi, A. A., and Rezaei, F. (2021). Recent advances in 3D printing of structured materials for adsorption and catalysis applications. Chem. Rev. 121, 6246–6291. doi:10.1021/acs.chemrev.1c00060
Lee, J. Y., An, J., and Chua, C. K. (2017). Fundamentals and applications of 3D printing for novel materials. Appl. Mat. Today 7, 120–133. doi:10.1016/j.apmt.2017.02.004
Lee, S., Kim, Y., Park, D., and Kim, J. (2021). The thermal properties of a UV curable acrylate composite prepared by digital light processing 3D printing. Compos. Commun. 26, 100796. doi:10.1016/j.coco.2021.100796
Leigh, S. J., Bradley, R. J., Purssell, C. P., Billson, D. R., and Hutchins, D. A. (2017). A simple, low-cost conductive composite material for 3D printing of electronic sensors. PLoS One 7, e49365. doi:10.1371/journal.pone.0049365
Leszczyńska, A., Njuguna, J. A. K., Pielichowski, K., and Banerjee, J. R. (2007). Polymer/montmorillonite nanocomposites with improved thermal properties: Part I. Factors influencing thermal stability and mechanisms of thermal stability improvement. Thermochim. Acta. 453, 75–96. doi:10.1016/j.tca.2006.11.002
Li, J., Wang, L., Dai, L., Zhong, L., Liu, B., Ren, J., et al. (2018). Synthesis and characterization of reinforced acrylate photosensitive resin by 2-hydroxyethyl methacrylate-functionalized graphene nanosheets for 3D printing. J. Mat. Sci. 53, 1874–1886. doi:10.1007/s10853-017-1432-8
Li, Y., Kankala, R. K., Weng, Z., and Wu, L. (2022). Dual-cure vapor-grown carbon nanofiber-supplemented 3D-printed resin: Implications for improved stiffness and thermal resistance. ACS Appl. Nano Mat. 5, 9544–9553. doi:10.1021/acsanm.2c01774
Li, Y., Peng, S., Kankala, R. K., Wu, L., Chen, A. Z., and Wang, S. B. (2022). 3D printing of mechanically robust MXene-encapsulated polyurethane elastomer. Compos. Pt. A-Appl. Sci. Manuf. 163, 107182. doi:10.1016/j.compositesa.2022.107182
Li, Y., Zhong, J., Wu, L., Weng, Z., Zheng, L., Peng, S., et al. (2019). High performance POSS filled nanocomposites prepared via UV-curing based on 3D stereolithography printing. Compos. Pt. A-Appl. Sci. Manuf. 117, 276–286. doi:10.1016/j.compositesa.2018.11.024
Lin, D., Jin, S., Zhang, F., Wang, C., Wang, Y., Zhou, C., et al. (2015). 3D stereolithography printing of graphene oxide reinforced complex architectures. Nanotechnology 26, 434003. doi:10.1088/0957-4484/26/43/434003
Manapat, J. Z., Mangadlao, J. D., Tiu, B. D. B., Tritchler, G. C., and Advincula, R. C. (2017). High-strength stereolithographic 3D printed nanocomposites: Graphene oxide metastability. ACS Appl. Mat. Interfaces 9, 10085–10093. doi:10.1021/acsami.6b16174
Markandan, K., and Lai, C. Q. (2020). Enhanced mechanical properties of 3D printed graphene-polymer composite lattices at very low graphene concentrations. Compos. Pt. A-Appl. Sci. Manuf. 129, 105726. doi:10.1016/j.compositesa.2019.105726
Martin, J. J., Fiore, B. E., and Erb, R. M. (2015). Designing bioinspired composite reinforcement architectures via 3D magnetic printing. Nat. Commun. 6, 8641. doi:10.1038/ncomms9641
Mu, M. F., Clarke, N., Composto, R. J., and Winey, K. I. (2009). Polymer diffusion exhibits a minimum with increasing single-walled carbon nanotube concentration. Macromolecules 42, 7091–7097. doi:10.1021/ma901122s
Mu, Q., Wang, L., Dunn, C. K., Kuang, X., Duan, F., Zhang, Z., et al. (2017). Digital light processing 3D printing of conductive complex structures. Addit. Manuf. 18, 74–83. doi:10.1016/j.addma.2017.08.011
Papageorgiou, D. G., Kinloch, I. A., and andYoung, R. J. (2017). Mechanical properties of graphene and graphene-based nanocomposites. Prog. Mat. Sci. 90, 75–127. doi:10.1016/j.pmatsci.2017.07.004
Park, D., Lee, S., and Kim, J. (2021). Enhanced thermoelectric performance of UV-curable silver (I) selenide-based composite for energy harvesting. Sci. Rep. 11, 16683–16688. doi:10.1038/s41598-021-96267-x
Peng, S., Li, Y., Wu, L., Zhong, J., Weng, Z., Zheng, L., et al. (2020). 3D printing mechanically robust and transparent polyurethane elastomers for stretchable electronic sensors. ACS Appl. Mat. Interfaces 12, 6479–6488. doi:10.1021/acsami.9b20631
Pezzana, L., Riccucci, G., Spriano, S., Battegazzore, D., Sangermano, M., and Chiappone, A. (2021). 3D printing of pdms-like polymer nanocomposites with enhanced thermal conductivity: Boron nitride based photocuring system. Nanomaterials 11, 373. doi:10.3390/nano11020373
Quaresimin, M., Salviato, M., and Zappalorto, M. (2012). Strategies for the assessment of nanocomposite mechanical properties. Compos. Pt. B-Eng. 43, 2290–2297. doi:10.1016/j.compositesb.2011.12.012
Roduner, E. (2006). Size matters: Why nanomaterials are different. Chem. Soc. Rev. 35, 583–592. doi:10.1039/b502142c
Rymansaib, Z., Iravani, P., Emslie, E., Medvidović-Kosanović, M., Sak-Bosnar, M., Verdejo, R., et al. (2016). All-polystyrene 3D-printed electrochemical device with embedded carbon nanofiber-graphite-polystyrene composite conductor. Electroanalysis 28, 1517–1523. doi:10.1002/elan.201600017
Sampson, K. L., Deore, B., Go, A., Nayak, M. A., Orth, A., Gallerneault, M., et al. (2021). Multimaterial vat polymerization additive manufacturing. ACS Appl. Polym. Mat. 3, 4304–4324. doi:10.1021/acsapm.1c00262
Sandoval, J. H., Soto, K. F., Murr, L. E., and Wicker, R. B. (2007). Nanotailoring photocrosslinkable epoxy resins with multi-walled carbon nanotubes for stereolithography layered manufacturing. J. Mat. Sci. 42, 156–165. doi:10.1007/s10853-006-1035-2
Skliutas, E., Kasetaite, S., Jonušauskas, L., Ostrauskaite, J., and Malinauskas, M. (2018). Photosensitive naturally derived resins toward optical 3-D printing. Opt. Eng. 57, 1. doi:10.1117/1.oe.57.4.041412
Song, S. Y., Park, M. S., Lee, J. W., and Yun, J. S. (2018). A study on the rheological and mechanical properties of photo-curable ceramic/polymer composites with different silane coupling agents for SLA 3D printing technology. Nanomaterials 8, 93. doi:10.3390/nano8020093
Spitalsky, Z., Tasis, D., Papagelis, K., and Galiotis, C. (2010). Carbon nanotube–polymer composites: Chemistry, processing, mechanical and electrical properties. Prog. Polym. Sci. 35, 357–401. doi:10.1016/j.progpolymsci.2009.09.003
Valino, A. D., Dizon, J. R. C., JrAH, Espera, Chen, Q., Messman, J., and Advincula, R. C. (2019). Advances in 3D printing of thermoplastic polymer composites and nanocomposites. Prog. Polym. Sci. 98, 101162. doi:10.1016/j.progpolymsci.2019.101162
Vidakis, N., Petousis, M., Velidakis, E., Mountakis, N., Tsikritzis, D., Gkagkanatsiou, A., et al. (2022). Investigation of the biocidal performance of multi-functional resin/copper nanocomposites with superior mechanical response in SLA 3D printing. Biomimetics 7, 8. doi:10.3390/biomimetics7010008
Wang, J., Mubarak, S., Dhamodharan, D., Divakaran, N., Wu, L., and andZhang, X. (2020). Fabrication of thermoplastic functionally gradient composite parts with anisotropic thermal conductive properties based on multicomponent fused deposition modeling 3D printing. Compos. Commun. 19, 142–146. doi:10.1016/j.coco.2020.03.012
Wei, X., Li, D., Jiang, W., Gu, Z., Wang, X., Zhang, Z., et al. (2015). 3D printable graphene composite. Sci. Rep. 5, 11181–11187. doi:10.1038/srep11181
Weng, Z., Zhou, Y., Lin, W., Senthil, T., and Wu, L. (2016). Structure-property relationship of nano enhanced stereolithography resin for desktop SLA 3D printer. Compos Pt A-Appl Sci. Manuf. 88, 234–242. doi:10.1016/j.compositesa.2016.05.035
Wong, M., Paramsothy, M., Xu, X. J., Ren, Y., Li, S., and Liao, K. (2003). Physical interactions at carbon nanotube-polymer interface. Polymer 44, 7757–7764. doi:10.1016/j.polymer.2003.10.011
Yang, Z., Peng, S., Wang, Z., Miao, J. T., Zheng, L., Wu, L., et al. (2022). UV-curable, low-viscosity resin with a high silica filler content for preparing ultrastiff, 3D-printed molds. ACS Appl. Polym. Mat. 4, 2636–2647. doi:10.1021/acsapm.1c01920
Yiming, B., Han, Y., Han, Z., Zhang, X., Li, Y., Lian, W., et al. (2021). A mechanically robust and versatile liquid-free ionic conductive elastomer. Adv. Mat. 33, 2006111. doi:10.1002/adma.202006111
Zhang, C., Cui, Y., Li, J., and Jiang, D. (2015). Nano-SiO2-Reinforced ultraviolet-curing materials for three-dimensional printing. J. Appl. Polym. Sci. 132, 42307. doi:10.1002/app.42307
Zhang, J., Yang, B., Fu, F., You, F., Dong, X., and Dai, M. (2017). Resistivity and its anisotropy characterization of 3D-printed acrylonitrile butadiene styrene copolymer (ABS)/Carbon black (CB) composites. Appl. Sci. 7, 20. doi:10.3390/app7010020
Keywords: vat polymerization, 3D printing, nanocomposites, mechanical properties, thermal properties, conductivity
Citation: Li Y, Wang W, Wu F and Kankala RK (2023) Vat polymerization-based 3D printing of nanocomposites: A mini review. Front. Mater. 9:1118943. doi: 10.3389/fmats.2022.1118943
Received: 08 December 2022; Accepted: 20 December 2022;
Published: 05 January 2023.
Edited by:
Jianlei Wang, Chinese Academy of Sciences (CAS), ChinaReviewed by:
Yao Yuan, Xiamen University of Technology, ChinaCopyright © 2023 Li, Wang, Wu and Kankala. This is an open-access article distributed under the terms of the Creative Commons Attribution License (CC BY). The use, distribution or reproduction in other forums is permitted, provided the original author(s) and the copyright owner(s) are credited and that the original publication in this journal is cited, in accordance with accepted academic practice. No use, distribution or reproduction is permitted which does not comply with these terms.
*Correspondence: Yuewei Li, eXdsaUBocXUuZWR1LmNu
Disclaimer: All claims expressed in this article are solely those of the authors and do not necessarily represent those of their affiliated organizations, or those of the publisher, the editors and the reviewers. Any product that may be evaluated in this article or claim that may be made by its manufacturer is not guaranteed or endorsed by the publisher.
Research integrity at Frontiers
Learn more about the work of our research integrity team to safeguard the quality of each article we publish.