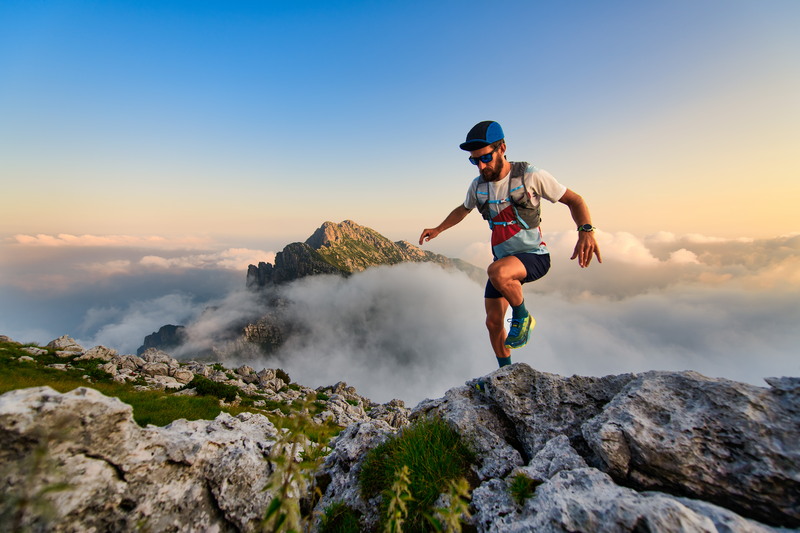
95% of researchers rate our articles as excellent or good
Learn more about the work of our research integrity team to safeguard the quality of each article we publish.
Find out more
REVIEW article
Front. Mater. , 02 December 2022
Sec. Structural Materials
Volume 9 - 2022 | https://doi.org/10.3389/fmats.2022.1091867
This article is part of the Research Topic Sustainable Fiber Reinforced Cementitious Composites for Construction and Building Materials View all 14 articles
A progressive advance in the construction sector is attained by employing ultra-high performance concrete (UHPC) technology. Rigorous efforts have been made in this research domain to have remarkable quality levels with 150 MPa or more strength and significant durability, which was impossible previously. Steel fiber incorporation in UHPC is vital in improving its mechanical characteristics. This review on the incorporation of steel fibers in UHPC evaluates, identifies, and synthesizes research outcomes for creating a summary of current evidence that can contribute to evidence-based practice. This study summarized a review of the literature on steel fibers’ effect on UHPC, intending to explore its essential aspects. The aim is to summarize the literature in this research domain and provide guidance for future research. Moreover, the basic requirements and materials, mixing and casting, mechanical properties, modern applications, advantages and disadvantages, and future perspectives associated with steel fibers reinforced UHPC in the construction sector are discussed. It is revealed from the conducted analysis that the most widely applied keyword is “steel fibers.” Due to the graphical illustration of the contributing studies, the current work may benefit academic scholars in sharing novel techniques and ideas and establishing collaborative efforts. Furthermore, the present work reveals that steel fibers have the potential to enhance the mechanical properties of UHPC; however, the large-scale production and applications of steel fiber-reinforced UHPC are controlled by parameters like fiber content and geometry.
Concrete is among the most frequently and widely utilized building construction materials globally. However, due to the natural properties of concrete, it bears a few shortcomings like less tensile resistance, more brittleness, lower strain capacity, and less resistance toward crack initiation and propagation (Huang et al., 2022). To cater such issues, the addition of fibers like synthetic fibers (Qin et al., 2019; Ahmed and Lim, 2021b; Rezaie et al., 2021; Meng et al., 2022), metallic/steel fibers (Zhang et al., 2020), natural fibers (Khan et al., 2018b; Farooqi and Ali, 2019; Ahmad W. et al., 2020; Farooqi and Ali, 2022), and mineral fibers (Khan et al., 2018a; Ahmed and Lim, 2021a; Akbar and Liew, 2021; Khan et al., 2021; Khan et al., 2022a), in concrete is usually made (Cao et al., 2020; Li et al., 2020; Ye et al., 2021) to improve its toughness (Khan et al.). The fiber incorporation into concrete started back in the early 1960s. The fiber-reinforced concrete (FRC) concept with a theory of fiber spacing was first proposed by Batson (Zollo, 1997). With the growing demand for durable and high-strength concrete, ultra-high performance concrete (UHPC), introduced in the 1990s, has excellent mechanical characteristics and a highly dense microstructure (Shi et al., 2015). The significant resistance against crack generation and further propagation are offered by adding fibers in concrete (Ahmad J. et al., 2020; Shi et al., 2022). Figure 1 depicts the different shapes of steel fibers considered dispersed reinforcement in UHPC by various researchers, as presented by Sidodikromo et al. (2019).
FIGURE 1. Steel fiber shapes considered for incorporation in UHPC (Sidodikromo et al., 2019).
UHPC is a cementitious material with higher strength and durability. It is a potentially practical solution to enhance the performance and sustainability of building elements and infrastructure components (Bahari et al., 2018; Bahari et al., 2021; Dabbaghi et al., 2021; Bahari et al., 2022). In the last 2 decades, UHPC has gained attention in several countries with its possible applications in bridges, building components, repair and rehabilitation, architectural features, cladding, and vertical elements like windmill and utility towers, offshore structures, the oil and gas industry, overlay materials, and hydraulic structures (Tayeh et al., 2013a; Voo et al., 2017; Zhang et al., 2021). In all these mentioned applications, bridge and road construction using UHPC is more frequent in practice. UHPC is utilized in various countries like the United States (US), China, Austria, Canada, the Czech Republic, Australia, Germany, France, Italy, Malaysia, Japan, New Zealand, the Netherlands, South Korea, and Switzerland (Voo et al., 2017; Aisheh et al., 2022; Aslam et al., 2022). The available design codes for typical concrete manufacturing are not meant for UHPC. Different countries, including Australia (Gowripalan and Gilbert, 2000), Germany (Brühwiler, 2016), Spain (López et al., 2017), Canada (Perry and Habel, 2017), Japan (JSCE, 2004), and Switzerland (Brühwiler, 2016), are developing UHPC design guidelines. The non-availability of design codes, insufficient information on raw materials and manufacturing methods, and higher overall costs seem to restrict the practical implementation of this exceptional material in addition to already developed projects (Vande Voort et al., 2008; Lei et al., 2012; Nematollahi et al., 2012; Voo et al., 2017). The public and private sectors are paying significant attention to extensive efforts to utilize this promising material (Alwesabi et al., 2020; Abadel et al., 2022; Alwesabi et al., 2022).
The current study’s review is conducted to explore the steel fibers’ effect on the UHPC key characteristics. The steel fiber characteristics that influence the UHPC matrix to fiber bonding mechanism include the orientation of fibers and their distribution, resistance to pullout, and the bonding zone microstructure are elaborated in addition to the impact of shapes, length, and hybridization of steel fibers on mechanical properties, failure mode, durability, and autogenous shrinkage of UHPC. As research on steel fibers reinforced UHPC enhances an urge to achieve high-strength concrete, researchers face limitations on the information that restricts novel research and collaborations. Therefore, it is critical to establish and execute a scheme that aids researchers in acquiring important and necessary information from highly authentic sources. The current study focuses on the review of bibliographic published data on steel fiber-reinforced UHPC. The present study’s findings would help young researchers exchange state-of-the-art ideas and procedures and establish joint ventures. In light of the conducted literature review, the current research discusses and emphasizes the steel fiber-reinforced UHPC basic requirements and materials, mixing and casting, mechanical properties, modern applications, advantages and disadvantages, and its future perspectives.
In this study, a detailed review methodology is carried out to retrieve data from the available relevant literature for keyword analysis. Numerous publications relevant to the steel fiber-reinforced UHPC domain are available, and difficulty is usually faced in the selection of a reliable search engine. Scopus and Web of Science are the two most reliable and dependent search engines (Zhang et al., 2022). The highly recommended search engine, that is, Scopus (Amin et al., 2022), is used in this research to retrieve the bibliographic data on steel fiber-reinforced UHPC. The needless documents are excluded by using several screening filters. An inclusive methodical flowchart representing all the performed steps is shown in Figure 2. It is interesting to see the progressive concentration of academic research on using steel fibers in UHPC. Furthermore, in pursuance of a review study regarding most related articles and critical review analysis, the primary elements of steel fiber-reinforced UHPC research are highlighted and illustrated in the succeeding sections. Keywords are vital in research as they distinguish and emphasize the primary theme of a particular research study (Song et al., 2021). The keyword minimum repetition criteria are set at 30. A total of 20 keywords are shortlisted this way, as provided in Table 1. Steel fibers, ultra-high performance concrete, and compressive strength are the three frequently used keywords in the steel fiber-reinforced UHPC research field. It is extracted from keyword analysis that steel fibers in UHPC have been studied to achieve enhanced compressive strength.
Figure 3 shows a map for occurrence frequency based on connections and density. Here again, the dimensions of the frame for a specific keyword (Figure 3A) depict the frequency of the keyword, and the frame position shows its co-occurrence in papers. Furthermore, the frame size is comparatively larger for leading keywords than others, as shown in the graph, indicating their importance for the exploration of research on steel fiber-reinforced UHPC. The representation of keyword co-occurrences in different publications is made by clustering. Multiple colors are allocated to every individual cluster to signify the keywords’ co-occurrences in published articles. The different color shades are used to illustrate four distinct groups (Figure 3A). Similarly, different unique colors represent keyword density concentrations (Figure 3B). The color shades are organized according to density, with red being employed for maximum density followed by yellow, green, and blue shades depicting subsequently lesser densities. Steel fibers, ultra-high performance concrete, UHPC, and other noteworthy keywords are shown in red or yellow shades, indicating their higher density of occurrences. This conclusion will aid young scientists in opting for keywords that can minimize the efforts required for exploring this specific research area-related publication.
Figure 4 shows the basic requirements of UHPC, as reported by Mishra and Singh (2019). Shi et al. (2015) reported the main factors for preparing UHPC: porosity reduction, enhanced fresh paste homogeneity, and improved microstructure. The parameters are closely linked with the raw materials and mix design for UHPC. The impact of additives, like silica fume (Yazıcı, 2007), rice husk ash (Van Tuan et al., 2011b), nano-particle (Rong et al., 2015; Wu et al., 2017a), limestone powder (Yu et al., 2015a), and fly ash (Chen et al., 2019; Li G. et al., 2022), in addition to raw materials, on UHPC has been extensively investigated in various studies. For UHPC mix design, several techniques are suggested, such as the compressive packing model (CPM) (De Larrard and Sedran, 2002), the linearly packing density model (LPDM) (Stovall et al., 1986), and the Aim and Goff model (Sohail et al., 2018). In recent years, the most famous UHPC mix design model is the Andreasen and Andersen model (AAM) (Yu et al., 2014b; Yu et al., 2015a; Dingqiang et al., 2021; Du et al., 2021). Figure 5 shows the dense particle packing mechanism in UHPC, as presented by Abu-Lebdeh et al. (2022).
FIGURE 5. Particle packing mechanism in the UHPC (Abu-Lebdeh et al., 2022).
Furthermore, in terms of materials for UHPC, its compressive strength is more highly influenced by the variation in cement than any other ingredient. Cement of higher quality is an important requirement for consistently manufacturing uniform UHPC (Ahmad et al., 2021). In addition to cement, silica fume also possesses pozzolanic characteristics, making it vital for manufacturing UHPC. It is extracted from ferrocenium alloy production (Wetzel and Middendorf, 2019). Silica fume results in an enhanced interfacial transition zone (ITZ) between aggregates and cement paste (Rossignolo, 2007). The optimum content of silica fume is dependent on the water–binder ratio (Máca et al., 2014), which is reported to be between 20% and 30% by mass of cement, by Chan and Chu (2004). To improve the rheology of UHPC, nano-particles such as nano-silica (nano-SiO2), nano-iron (nano-Fe2O3), nano-titanium oxide (nano-TiO2), and nano-CaCO3 are used to fill the spaces among paste agglomerates and physical contact sites (Qian, 2017). High-range polycarboxylate-based water-reducing agents are also considered for UHPC to have a lower water–binder ratio (Schröfl et al., 2012). The suitable range of these polycarboxylate-based superplasticizers is 2.0%–3.5% by weight of the binder. As far as aggregates are concerned for UHPC, the mineralogy, surface texture, and shape of aggregates influence the overall requirement for mixing water. The coarse aggregates larger than 4.75 mm are usually avoided for UHPC to sidestep the negative influence of their angularity on particle packing density and to achieve a stronger interfacial transition zone (Richard and Cheyrezy, 1995; Alkaysi et al., 2016; Li et al., 2018). In UHPC, the quartz sand should preferably be replaced with river sand (Soliman and Tagnit-Hamou, 2016). However, in river sand, the size range of particles is 0–4.75 mm, in which the maximum particle size is 5–8 times that of quartz sand, which may lead to reduced particle packing density. In this scenario, the finer masonry sand with a size of up to 2 mm extracted by grinding and crushing the coarse aggregates, was recommended by Meng et al. (2017) for improving the packing of particles. The higher particle angularity of river sand may reduce the UHPC’s workability (Yang et al., 2009). Hence, the packing particles should be optimized using the aforementioned fine aggregates. The percentage distribution of aggregates in conventional concrete and UHPC is shown in Figure 6, as presented by Sidodikromo et al. (2019).
FIGURE 6. Percentage contents of aggregates in normal strength concrete (NSC) and UHPC (Sidodikromo et al., 2019).
The fiber addition in UHPC is important for attaining improved mechanical characteristics (Li et al., 2021). The schematic composition of fiber-reinforced UHPC, as devised by the Korea Institute of Civil Engineering and Building Technology (KCI-M-12-003, 2012), is shown in Figure 7. Out of all fibers, the most widely utilized fibers in UHPC are steel fibers due to their exceptional mechanical characteristics. UHPC is exceptionally brittle due to its high homogeneity and strength, so this brittleness may be reduced by incorporating steel fibers (Wang et al., 2015). Abbas et al. (2015) reported improved compressive properties, such as tensile behavior and peak load, of UHPC with more steel fiber content. Wille, Naaman [47] concluded that UHPC’s 28-day compressive strength was enhanced up to 292 MPa upon incorporating steel fibers up to 8% volumetric content. Significant improvements in deflection under peak flexural loading and corresponding strength were observed in UHPC upon the incorporation of steel fibers (Niu et al., 2019). Incorporating steel fibers in UHPC with up to 3% volumetric content provides uniform fiber dispersion and acceptable workability. The UHPC flowability was improved by incorporating quartz and limestone as replacements, as investigated by Yu et al. (2014b). It was reported in the study that with the increasing content of steel fibers, the flowability decreased. Similarly, in a study by Wu et al. [38], a 21.4% reduction in UHPC flowability was reported upon adding straight steel fibers upon enhancing the volumetric fiber content from 1% to 3% having 0.02% content of the superplasticizer. It might be because more steel fiber content enhanced the contact surface between fibers and matrix, resulting in reduced workability and cohesive force (Yu et al., 2014b; Xu et al., 2019; Gul et al., 2021). Moreover, the flowability reduction is more significant when incorporating steel fibers with a higher aspect ratio (Cao et al., 2019).
FIGURE 7. Schematic composition (not to scale) of fiber-reinforced UHPC (taken from Park et al. (2015)).
In past research, it has been reported that the fiber shapes also considerably influence the UHPC flowability (Soliman and Nehdi, 2014; Abbas et al., 2015; Meng and Khayat, 2018). Table 2 illustrates the four unique steel fiber shapes usually incorporated in UHPC. The UHPC flowability can be further decreased by using deformed steel fibers instead of straight ones. Wu et al. (2016b) reported a 21.1% and 10.9% reduction in UHPC flowability with 3% volumetric content of corrugated and hooked-end steel fibers, respectively, compared with straight steel fibers. It might be due to 1) the friction between aggregates and hooked-end steel fibers being higher than other considered fiber shapes, 2) the added mechanical anchorage in the case of deformed steel fibers within the matrix-fiber bonding region, and 3) the comparatively easy bundling of deformed fibers compared to straight fibers (Wang et al., 2012; Yu et al., 2014b). There is a critical steel fiber content value, and the UHPC flowability may be considerably decreased. It might be agglomerating, and balls forming steel fibers exceed the fiber content from critical value (Khayat et al., 2019). The UHPC workability is usually improved by adding a vital superplasticizer, as reported by Shi et al. (2015) and Wang et al. (2017). However, the direct incorporation of water and superplasticizer led to the cement particles’ absorption by the superplasticizer, and subsequently, effective dispersion cannot be attained while mixing (Shi et al., 2015). Hence, in Schachinger et al. (2004), Graybeal (2006), Yu et al. (2014a), Zhao et al. (2014), Abbas et al. (2015), Yu et al. (2015a), Meng W. and Khayat K. (2017), and Huang et al. (2018), the stepwise process is proposed to add steel fibers that improve the superplasticizer dispersion in UHPC. The UHPC yield viscosity enhanced up to 53 Pa s upon increasing the viscosity-modified admixture content to 1% (Meng W. and Khayat K. H., 2017). In parallel, the workability of steel fibers reinforced UHPC is also dependent on mixing time. Generally, additional time and energy for mixing are vital for fiber uniform distribution in UHPC. Instead, the UHPC temperature is enhanced because of the extended time for mixing and air bubble formation, leading to strength reduction (Dils et al., 2012; ACI 239R-18, 2018). As per the literature, the UHPC mixing time is usually controlled between 10 and 20 min.
TABLE 2. Steel fiber types and geometry (Park et al., 2012; Wu et al., 2016a; 2017b; Yoo et al., 2017b; Wu et al., 2019b; Yoo et al., 2019).
In the past 60 years, there has been continuous improvement in FRCs. An advanced form of FRC is UHPC, which is composed of higher cement contents, superplasticizer (SP), fibers, silica fume, and other supplementary cementitious materials. The design of UHPC is a way to achieve dense packing of solid materials by limiting water content (w/c) below 0.2 (Meng et al., 2020). Such features result in UHPC’s higher compressive strength, even more than 150 MPa (C/CM-17, 2017; Qin et al., 2022), which is almost 3–16 times more than conventional concrete (Yoo and Banthia, 2016; Xu S. et al., 2021), and excellent energy absorption capability and ductility. As per standards, multiple criteria are there for describing UHPC, for example, the American Society for Testing and Materials (ASTM) C185 (C/CM-17, 2017), the American Concrete Institute (ACI) committee 239 (ACI 239R-18, 2018), the Japan Society of Civil Engineers (JSCE) (JSCE, 2004), and the U.S. Department of Transportation Federal Highway Administration (FHWA) (Graybeal, 2006). As per the main definitions, the suggested compressive strength and tensile ductility for UHPC are 150 MPa and 5 MPa, respectively. With such excellent mechanical characteristics, the UHPC structures have 1/2 to 2/3 times less weight than conventional concrete without compromising the loading requirements (Schmidt and Fehling, 2005).
UHPC is similar to conventional concrete; therefore, the traditional procedure of casting remains usable and relevant. The standard concrete mixer is used for mixing UHPC. Figure 8 shows the steps of UHPC mixing, as presented by Zheng et al. (2022), similar to conventional concrete. The superplasticizer and water are added after mixing powdered ingredients for almost 10 min, and the mixing process is repeated for another 5–10 min. The addition of steel fibers is performed as per the mix design on the satisfactory flowability of the mortar to have optimum workability. It should be noted that in the case of UHPC, more energy is consumed than conventional concrete, so the mixing process requires more time. Due to the additional energy input and lesser contents of water and coarse aggregates, additional care is used to avoid overheating during the mixing process. Cooling ingredients, utilizing a high-energy mixer, and replacing water partially or completely with ice may solve this overheating issue. Such UHPC can then be mixed in a conventional concrete mixer and in ready-mix trucks (Graybeal, 2011). Casting steel fibers incorporated in UHPC requires special attention regarding placement methods. In this case, the internal vibration is not recommended for UHPC; a slight external vibration can be applied to exclude the entrapped air.
FIGURE 8. Steel fiber-reinforced UHPC mixing process (Zheng et al., 2022).
The workability of concrete is basically an effort to manipulate a fresh concrete mix with maximum uniformity (homogeneity) (ASTM, 2018; Abetua and Kebedeb, 2021; Aisheh et al., 2022). This manipulation subjects to the placing, compaction, and concrete finishing (Li Z. et al., 2022). Concrete’s workability is affected by adding fibers to it to improve the concrete’s characteristics and performance (Cao et al., 2018a; Cao et al., 2018b). Usually, the viscosity of UHPC is more than conventional concrete (Sadrmomtazi et al., 2018). This is due to the dense packing of the finer ingredients in UHPC and the significantly lower water-to-binder ratio. Moreover, the UHPC’s durability and mechanical characteristics are primarily based on its fresh state (Askar et al., 2013; Tayeh et al., 2013b; Tayeh et al., 2013d; Soliman and Nehdi, 2014). During the manufacturing of steel fiber-reinforced UHPC, its flowability is influenced by the surface area, geometry, shape, and volumetric content (Wang et al., 2017). The steel fiber incorporation in the UHPC mix enhances the air content in the fresh mix and decreases the relative droop (Akeed et al., 2022a). Biswas et al. (2021) also reported a decrease in the flowability of fiber-reinforced UHPC with increasing fiber contents, as also illustrated in Figure 9. Furthermore, the enhancement in cohesive force among steel fibers and paste also reduces the flowability of respective UHPC (Yu et al., 2015b). Kwon et al. (2014) proposed an equation, that is, χf = Vf × lf/df, for computing the factor named fiber factor to estimate the flowability of fiber-reinforced UHPC, where the fiber factor is shown by χf; Vf is notated for fiber volume, and df and lf show the diameter and length of the fiber, respectively. It was revealed from the conducted study that with the increasing fiber factor, the fiber-reinforced UHPC slump tends to decrease. Similar types of results were also reported by Naaman and Wille (2010) and Marković (2006).
FIGURE 9. UHPC flowability having (A) 4%, (B) 5%, (C) 6%, and (D) 8% fiber contents (Biswas et al., 2021).
The flexural and compressive strengths are the two vital mechanical factors in UHPC mix design to evaluate ductility and strength. However, the nature of UHPC is brittle. To cater to this issue, the incorporation of uniformly dispersed steel fibers with higher ultimate elongation and tensile strength is reported with enhanced strength and ductility of UHPC. Such concrete is considered ultra-high performance steel fiber-reinforced concrete by Qu et al. (2018). The role of steel fibers in UHPC is to enhance the cohesive forces among matrix and fibers, alter the granular skeleton, and enhance the length of anchorage among fibers and the UHPC matrix (Grünewald, 2004; Zdeb, 2017). Moreover, as frequently reported in the literature, the steel fibers provide a bridging mechanism in case of cracking and resist the crack propagation (Lan et al., 2022), ultimately enhancing the steel fiber-reinforced UHPC strength and ductility (Yu et al., 2014b). It may also be noted that the steel fiber content in UHPC is also of significant importance as the incorporation of steel fibers in bulk quantities can lead to their interlocking and inter-wrapping with each other, influencing the workability of the respective composite, which ultimately results in strength reduction (Qu et al., 2018). So, this review on the utilization of steel fibers in UHPC may assist in adopting the appropriate composition and characteristics like length, diameter, and content, for improving the mechanical properties of respective composites.
UHPC compressive strength is a vital characteristic that is usually determined with respect to conventional concrete (Russell H. G. et al., 2013). The steel fibers are incorporated in UHPC to have bridging behavior (Alsalman et al., 2017; Khan et al., 2019). Compared with conventional concrete, the steel fiber-reinforced UHPC’s compressive behavior is not considerably different. The main difference is in stiffness and compressive strength, which are significantly higher in UHPC. The ingredients influence the compressive strength of UHPC, mix design, fiber content, and curing (Russell H. G. et al., 2013). Researchers have reported different results for the compressive strength of steel fiber-reinforced UHPC. Bae et al. (2016) reported a slight effect (i.e., <10%) on the compressive strength of UHPC upon the incorporation of steel fibers. Arora et al. (2019) reported that the UHPC compressive strength is primarily based on aggregates’ packing density and the amount of hydration products. However, Ibrahim et al. (2017) reported considerable influence (i.e., >50% enhancement) in UHPC compressive strength upon the addition of steel fibers. This might be due to steel fibers capacity to delay fracture development and propagation (Ibrahim et al., 2017). The increasing content of fiber tends to have enhanced compressive strength (Wu et al., 2016b; Ibrahim et al., 2017). Compared with straight steel fibers, deformed steel fibers offer enhanced pullout strength, ultimately bridging the cracks more effectively (Meng and Khayat, 2018). However, this increased pullout strength does not considerably influence the UHPC compressive strength. Liu et al. (2016) reported a slight variation in UHPC compressive strength between macro and micro hooked-end steel fibers. Yoo et al. (2017a) reported that straight steel fibers have a comparatively lesser enhancement in UHPC compressive strength than macro-deformed steel fibers. The reported compressive strengths of UHPC are shown in Figure 10, as summarized from the literature (Wang et al., 2012; Yu et al., 2014a; Wu et al., 2016b; Shafieifar et al., 2017; Wu et al., 2019a; Hung et al., 2020; Mo et al., 2020; Teng et al., 2020).
The incorporation of steel fibers in UHPC offers the achievement of structural integrity through load transference across cracks (Gu et al., 2022) through the crack bridging phenomenon. Pakravan and Ozbakkaloglu (2019) reported the enhancement in UHPC flexural strength as a fiber content function. As reported in the literature, the UHPC flexural tensile strength is generally increased with increasing fiber content. Abbas et al. (2015) associated this enhancement in UHPC flexural strength with more closely spaced fibers in cases of higher content. In this scenario, each crack is spanned by more fibers, thus offering more area for bonding between fibers and matrix [54] and more resistance against crack propagation (Abbas et al., 2015; Yoo et al., 2017c). Park et al. (2017) reported three times more peak strength for the UHPC matrix, having 2% volumetric content of steel fibers than a matrix with 0.5% volumetric content. It is also reported in the literature that UHPC flexural strength did not improve continuously with increasing fiber content (Gesoglu et al., 2016; Meng and Khayat, 2018). Meng and Khayat (2018) reported the agglomeration of steel fibers in cases of higher contents (i.e., >3%), resulting in an adverse impact on flexural strength. However, Abbas et al. (2015) concluded with slightly decreased workability even in the case of higher fiber contents (i.e., up to 6%) and significant enhancement in peak load. The prolonged curing might offer a higher degree of hydration and more dense microstructure, resulting in improved bond strength among steel fibers and the surrounding matrix (Wu et al., 2016c). The incorporation of more content of coarse aggregates in UHPC may result in microstructure defects, thus weakening the fiber–matrix bond strength. Furthermore, fiber dispersion may also be impaired by using more coarse aggregates, resulting in lower flexural strength (Liu et al., 2016). Kim et al. (2011) reported 20%–40% enhanced flexural strength in UHPC with 1% deformed steel fibers than that of straight steel fibers. Numerous researchers have reported that the flexural strength of UHPC can be enhanced by more than 20% by incorporating longer steel fibers (Yoo et al., 2016; Yoo et al., 2017a; Wu et al., 2017b; Yoo et al., 2017c; Park et al., 2017; Pourbaba et al., 2018). The reported flexural strengths of UHPC are shown in Figure 11, as summarized from the literature (Yu et al., 2014b; Wu et al., 2016b; Shafieifar et al., 2017; Wu et al., 2019a; Mo et al., 2020; Teng et al., 2020).
An essential constituent in UHPC is discontinuous fiber reinforcement. The fiber incorporation in UHPC is vital for enhancing the ductility under compressive loading, as needed to attain structural safety. The addition of fibers can reduce the brittleness of concrete and enhance numerous material characteristics, like enhanced energy absorption capability and provision of significant tensile strength. Different fiber types can be made based on material, shape, and size. As far as steel fiber incorporation in UHPC is concerned, its reinforcing effect is evaluated through adhesion bonding among matrix and fibers. The bonding characteristics, determined via a pullout test (single), are associated with the UHPC manufacturing method, the shape of the steel fiber, the friction coefficient, fiber content, orientation, and distribution (Gong et al., 2022; Huang, 2022). The bridging effect in UHPC due to steel fibers can be enhanced by optimizing the content (≤3%), orientation (<45°), and distribution of steel fibers to evade the accumulation of fibers in a way to prevent stress from transferring from the matrix to the steel fibers (Gong et al., 2022). This bridging phenomenon due to addition of fibers is illustrated in Figure 12, as presented by He et al. (2021). The scanning electronic microscopic view of the interfacial transition zone (ITZ) of steel fiber-reinforced concrete UHPC is illustrated in Figure 13, as presented by You et al. (2017). These SEM images show a durable bond between the steel fiber and the surrounding concrete matrix, depicting its capability to decrease stress concentrations and prevent internal degradation, ultimately leading to enhanced mechanical properties. The complexity of the UHPC structural design may be due to the varied content, combination, geometry, orientation, and distribution of fibers. Steel fibers may also be the reason behind UHPC’s more carbon footprint and costs. Accordingly, enhancing the information regarding steel fibers’ effects on UHPC is a crucial step for devising generally accepted UHPC applications and standard design codes.
FIGURE 12. Effective bridging mechanism due to higher fiber contents in UHPC (taken from He et al. (2021)).
FIGURE 13. SEM images for steel fiber-reinforced UHPC (taken from You et al. (2017)).
In the last two decades, researchers/academics and engineers around the globe have performed wide-ranging research to industrialize the technology of UHPC as a potential sustainable construction material in the future (Voo and Poon, 2009). It is extracted from a detailed literature search that almost 200 bridges have incorporated UHPC into their elements (Voo et al., 2017). Some other applications of UHPC include structural strengthening, building, precast elements, and retrofitting (Vande Voort et al., 2008). The resources and efforts of both the private and public sectors are focused on exploiting UHPC for practical implementation as a sustainable construction material (Ng et al., 2012; Akeed et al., 2022a; Akeed et al., 2022b; Akeed et al., 2022c). The superior mechanical characteristics of UHPC offer the design/manufacturing of aesthetically good, light, and slim architectural elements. The European and Mediterranean Civilizations Museum in France is an example where UHPC was used substantially for the very first time in the world. UHPC was utilized in creating perimeter footbridge decks and brackets, roof lattices, and prestressing anchorage points’ protective covers. Various studies have been conducted for optimum designs of UHPC components, concluding in the construction of UHPC bridges around the globe. Some of the other possible applications of UHPC comprise security infrastructure or basic infrastructure elements. Furthermore, extensive research has also been conducted on UHPC mechanical properties subjected to penetration resistance, blast resistance (Wu et al., 2009), and high strain loading rate (Habel and Gauvreau, 2008; Millard et al., 2010). Moreover, UHPC has also been frequently used as a repair overlay for existing concrete structures because of its excellent properties that require less maintenance work (Hajar et al., 2013; Moreillon and Menétrey, 2013). UHPC overlay was reported to be first applied on a bridge in Switzerland over the La Morge River (Denarié, 2005). The UHPC utilization was also found in cover plates throughout the high-speed railroads in China (Gu et al., 2013) and in retrofitting containment walls for a nuclear reactor in France (Corvez and Masson, 2013). Further than bridges and buildings, the UHPC can also be utilized in wind turbine towers, nuclear power plants, and tunnels. Gamarra (2016) reported that UHPC could also be utilized in developing more effective tunnel systems by reducing the thickness of tunnel elements. Hence, it can be summarized that the improved UHPC composite incorporating steel fibers may be utilized in pavements, tunnel and canal linings, bridge decks, airport runways and aprons, hydraulic structures, pipes, and slope stabilization, as also illustrated in Figure 14.
Compared to conventional cementitious concrete, ultra-high performance concrete (UHPC) is one of the advanced cementitious composites that have significantly enhanced durability and mechanical characteristics (Russell H. et al., 2013). The interest in commercial applications and research on UHPC is growing daily. Despite UHPC’s acceptability in various countries, there are still limitations, such as a lack of information on its material categorization procedures, structural capability for extensive usage, and design codes for general acceptability. The points of attention toward its enhanced utilization are the designing of slender/lightweight structures (Yoo and Banthia, 2016; Zhang and Ali, 2021), low maintenance, decreased environmental footprint, and overall cost. Depending on the results of the detailed literature review, the following advantages and disadvantages of steel fiber-reinforced UHPC are summarized as follows.
Advantages of steel fiber-reinforced UHPC: The compressive strengths of UHPC are reported in the literature (Tayeh et al., 2013c; Tayeh et al., 2013d; Qaidi et al., 2022) from 150 to 810 MPa which is almost 3–16 times more than that the in case of conventional concrete. The energy absorption capability and ductility of UHPC are conventionally increased by 300 times upon incorporation of steel fibers. CO2, sulfates, and chlorides are almost non-permeable (Abetua and Kebedeb, 2021) to UHPC. Its improved durability comes with a prolonged service life that requires low maintenance. Industrial floors and bridge decks benefit from enhanced resistance against abrasion, whereas spots with harsh or poor climatic conditions benefit from enhanced resistance against corrosion (Tam et al., 2012). Un-hydrated cement’s substantial percentage in the finished product during the cracking mechanism offers self-healing capability. Due to their exceptionally higher compressive strengths, buildings having UHPC weigh only 1/3rd or ½ of their conventional concrete components under similar loading conditions. This weight reduction comes out with thinner construction, additional serviceable floor space in case of multi-storey buildings, and reduced overall cost. The steel reinforcement bar exclusion enhances architectural freedom and reduces labor costs. Moreover, it also offers designers and architects the forms and shapes of structural members without virtual limits (Tam et al., 2012; Tayeh et al., 2014).
Disadvantages of steel fiber-reinforced UHPC: The UHPC disadvantages comprise its higher contents of cement (i.e., 950–1,000 kg/m3) and silica fume (i.e., 100–250 kg/m3) which enhance its manufacturing costs and CO2 emissions, ultimately contributing toward ozone layer depletion and global warming (Aı̈tcin, 2000; Mostofinejad et al., 2016; Almeshal et al., 2022; Faraj et al., 2022). Moreover, the sensitivity in case of quantities for water-to-binder materials, superplasticizers-to-binder, material chemical characteristics, and fine particle distribution (requires high-speed mixers) are UHPC’s additional disadvantages. Furthermore, in the absence of fibers, the brittleness of UHPC would be significantly higher, as in the case of high-strength concrete possessing a higher elastic modulus (i.e., around 45–60 GPa), which is not desirable. These issues might be resolved effectively by incorporating metakaolin (Huang et al., 2017; Amin et al., 2020; Mansour and Tayeh, 2020) and rice husk ash, slag, fly ash, and zeolite, as partial substitution for cement (Sobuz et al., 2016). Also, the SCMs may also be utilized in UHPC to reduce the manufacturing cost to encourage the potential customer for more wide-ranging applications.
A literature review-based research is an appropriate practice to recognize the growing trend in literature volume concentrating on steel fiber-reinforced UHPC-relevant evaluation, which may aid young academics. The primary objective of this research is to conduct a detailed review of steel fiber-reinforced UHPC’s available literature for exploring the different aspects. The following conclusions are drawn:
• The evaluation of steel fiber-reinforced UHPC research shows that steel fibers, ultra-high performance concrete, and compressive strength are the three most widely adopted keywords. This assessment also shows that steel fibers in UHPC have primarily been investigated to achieve high-strength concrete.
• The reported cement quantity incorporated in different types of concrete was 16% for HPC, 33% for UHPC, and 20% for SCC. Accordingly, in the steel fiber-reinforced UHPC, a significant cement quantity (i.e., 800–1,300 kg/m3) was reported. The partial replacement of cement with readily available SCMs like slag and fly ash and the utilization of silica fume come out with certain benefits in terms of improved mechanical properties like higher compressive strength (i.e., up to 150–200 MPa), lower shrinkage, and reduced overall cost. The content of polycarboxylate-based superplasticizers has a significant influence on calcium silicate reactivity.
• Steel fiber effectiveness in UHPC, which enhances the energy absorption capability, toughness, and tensile strength is evident from the literature. The hooked-end steel fibers are reported to be more effective than straight steel fibers. It might be due to (i) the friction between aggregates and hooked-end steel fibers being more than other considered fiber shapes, (ii) the added mechanical anchorage in the case of deformed steel fibers within the matrix–fiber bonding region, and (iii) the comparatively easier bundling of deformed fibers than straight fibers. The reinforcing effect of steel fibers is endorsed through adhesion bonding between the UHPC matrix and steel fibers. Steel fiber types such as micro or macro steel fibers, and straight and deformed (twisted, hooked-end, or corrugated), have been explored for UHPC.
• The basic concept for the design of steel fiber-reinforced UHPC is to achieve improved microstructure, reduced porosity, and enhanced toughness and homogeneity. The UHPC properties are considerably affected by the raw ingredients, method of preparation, and curing treatments.
• The overall outcomes for UHPC compressive strength depict that incorporating deformed steel fibers instead of straight fibers does not have a considerable impact. However, in the case of UHPC flexural strength, deformed fibers positively impact the lower contents of steel fibers. On the other hand, the higher content of straight steel fibers results in better performance.
• As revealed from the reported SEM analysis, the durable bond between the steel fiber and the surrounding concrete matrix can decrease stress concentrations and prevent internal degradation of the material, ultimately leading to enhanced mechanical properties of steel fiber-reinforced UHPC.
• Around the globe, accomplishments in steel fiber-reinforced UHPC can be seen. At the same time, UHPC is progressing slowly with limitations that restrict its applications. Higher initial costs, non-availability of design codes, complex manufacturing approaches, design challenges, and inadequate availability of resources obstructed its development at the commercial level and utilization in modern structures of buildings in developing countries.
• The applications and significant production of steel fiber-reinforced UHPC depend on parameters like fiber content, geometry, mix design, w/c ratio, and supplementary cementitious material contents Furthermore, there is limited knowledge on durability, steel fiber hybridization, life cycle assessment (LCA), bonding mechanisms, and life cycle cost analysis (LCCA) for steel fiber-reinforced UHPC. Hence, steel fiber-reinforced UHPC should be further explored in detail.
Based on the review conducted on steel fiber-reinforced UHPC, the following prospects for this research domain are proposed:
• For a better comprehensive understanding from the joint efforts of the research community, the future evaluation of all variables and testing mechanisms, in parallel, should be explored.
• It is also evident that researchers from different cultures would not agree to utilize a single standard among the already available guides. Therefore, considering the development of multiple standards for UHPC, the comparison studies among different proposed standards, by keeping all other parameters constant, will benefit scientific discussions by relating the novel research with existing ones (Larsen and Thorstensen, 2020).
• Furthermore, for the provision of a scientific basis for improving the performance, the UHPC load–slip modeling should also be explored comprehensively in terms of steel fiber effects regarding matrix age and compressive strength, fracture, damage of the matrix along the fiber and at the anchorage end, concrete macro-properties, slip-hardening, and incomplete straightening (Deng et al., 2022).
• In the literature, some recent studies show the feasibility of using steel fiber-reinforced UHPC in 3D printing (Van Tuan et al., 2011a; Arunothayan et al., 2020). Arunothayan et al. (2020) concluded that utilizing fiber-reinforced UHPC has enhanced shape retention ability compared to conventional concrete. Despite the available data on the 3D printing of UHPC, its manufacturing is still dependent on dedicated printing with specific configurations, such as the flow rate, nozzle type, and pumping specifications. It might not be feasible for various printing configurations and cementitious mixes (Arunothayan et al., 2020). As practitioners over the globe find it difficult to create 3D printing with UHPC, much effort is required to gain accessible information on utilizing steel fiber-reinforced UHPC for large-scale production of structural components using 3D printing technology.
• Additionally, a detailed, in-depth analysis of the bonding mechanism between steel fibers and the UHPC matrix should also be made to get a clear idea of UHPC’s mechanical characteristics for its structural applications.
• The durability evaluation in extreme ageing/environmental/climatic conditions is also required, with numerous coupling effects to have an insight into UHPC’s full utilization throughout the structure’s design life.
• Although the effect of deformed steel fibers in UHPC shows better bonding, as revealed from single pullout strength testing, the mechanical characteristics in the case of deformed fibers are less than those of straight fibers in some scenarios (Gong et al., 2022). Therefore, further investigation should also be conducted to validate the deformed steel fibers’ effectiveness.
• Cracks in UHPC usually resulted in debonding among steel and the surrounded UHPC matrix that may damage the inert coating on surface of steel and accelerate corrosion. So, to address this issue, the concept of self-healing cracks is important in UHPC to attain long-term durability. The cement hydration low degree may be attributed to self-healing of UHPC. Moreover, the fibers, other than steel, like carbon fibers, mineral fibers, and synthetic fibers, possess unique impacts on UHPC performance. Hence, incorporating such fibers to avoid corrosion in the case of steel and to improve UHPC performance as per their properties needs to be explored.
• Further research on the treatment of fibers, both chemically and physically, for enhancing the bonding mechanism between the fiber and matrix is highly recommended in the future.
• Although some studies have been carried out on using hybrid fibers in UHPC, analytical and experimental investigations to explore the effect of hybrid fibers on UHPC are still lacking. The synergistic mechanism of hybrid fibers is still not clear. Therefore, further research is required to optimize the combination of the hybrid fiber to enhance the UHPC’s mechanical characteristics, microstructure, and durability.
• The concept of hybridization of steel fibers in a way to incorporate a combination of steel fibers of varying lengths and shapes (Khan et al., 2022b) should also be further explored to resist the initiation and propagation of cracks in UHPC.
• Furthermore, various researchers like Wang et al. (2022) and Khan et al. (2022c) used various machine learning (ML) techniques under the concept of artificial intelligence (AI) to predict the mechanical properties (i.e., compressive and flexural strengths) of UHPC. However, there is still a gap in the employment of ML approaches for optimization of different variables, such as the fiber length, shape, content, mix design, w/c ratio, and supplementary cementitious material contents, considered in the design of steel fiber-reinforced UHPC to conserve natural resources and reduce the consumption of time, efforts, and cost, which is necessary to be covered (Xu Y. et al., 2021; Farooq et al., 2021; Wang et al., 2022).
• In the recent two decades, UHPC has been utilized in various countries for structural and non-structural applications. However, due to the higher cost of UHPC and the non-availability of its design codes, the application of UHPC in the construction industry is still limited. Therefore, future studies are required to reduce the UHPC cost for its wide-ranging practical implementation. Furthermore, the life cycle cost analysis (LCCA) of steel fiber-reinforced UHPC is also necessary before its applicability on large-scale production.
• Lastly, multiple studies were carried out to balance material mixes by adopting locally available raw and waste materials to reduce the quantity of cement, SP, and steel fibers [208]. With lesser environmental impacts, UHPC would be much more effective to implement by the construction industry. Hence, the knowledge of steel fiber-reinforced UHPC life cycle assessment (LCA) is also important to be explored before its practical applicability in the construction sector.
HA: visualization, funding acquisition, and writing—reviewing and editing. MA: conceptualization, validation, investigation, project administration, funding acquisition, and writing—reviewing and editing. WA: conceptualization, methodology, resources, supervision, software, validation, investigation, writing—original draft, and writing—reviewing and editing. KK: data curation, methodology, visualization, and writing—reviewing and editing. U-u-S: data curation, formal analysis, and writing—reviewing and editing. MA-H: investigation, formal analysis, and writing—reviewing and editing. AM: resources, validation, investigation, and writing—reviewing and editing.
This work was supported by the Deanship of Scientific Research, Vice Presidency for Graduate Studies and Scientific Research, King Faisal University, Saudi Arabia (Project No. GRANT2041), through its KFU Research Summer Initiative.
The authors acknowledge the Deanship of Scientific Research, Vice Presidency for Graduate Studies and Scientific Research, King Faisal University, Saudi Arabia (Project No. GRANT2041), through its KFU Research Summer Initiative. The authors extend their appreciation for the financial support that made this study possible.
The authors declare that the research was conducted in the absence of any commercial or financial relationships that could be construed as a potential conflict of interest.
All claims expressed in this article are solely those of the authors and do not necessarily represent those of their affiliated organizations, or those of the publisher, the editors, and the reviewers. Any product that may be evaluated in this article, or claim that may be made by its manufacturer, is not guaranteed or endorsed by the publisher.
Abadel, A., Abbas, H., Almusallam, T., Alshaikh, I. M. H., Khawaji, M., Alghamdi, H., et al. (2022). Experimental study of shear behavior of CFRP strengthened ultra-high-performance fiber-reinforced concrete deep beams. Case Stud. Constr. Mater. 16, e01103. doi:10.1016/j.cscm.2022.e01103
Abbas, S., Soliman, A. M., and Nehdi, M. L. (2015). Exploring mechanical and durability properties of ultra-high performance concrete incorporating various steel fiber lengths and dosages. Constr. Build. Mater. 75, 429–441. doi:10.1016/j.conbuildmat.2014.11.017
Abetua, A. G., and Kebedeb, A. B. (2021). Crushed concrete as adsorptive material for removal of phosphate ions from aqueous solutions. Water Conserv. Manag. 2 (5), 40–46.
Abu-Lebdeh, T. M., Damptey, R., Ungureanu, L. M., and Petrescu, F. I. T. (2022). A ternary model for particle packing optimization. J. Compos. Sci. 6 (4), 113. doi:10.3390/jcs6040113
ACI 239R-18 (2018). Ultra-high-performance concrete: An emerging technology report. American Concrete Institute. ACI 239R-18).
Ahmad, J., Manan, A., Ali, A., Khan, M. W., Asim, M., and Zaid, O. (2020a). A study on mechanical and durability aspects of concrete modified with steel fibers (SFs). cea. 8, 814–823. doi:10.13189/cea.2020.080508
Ahmad, J., Zaid, O., Shahzaib, M., Abdullah, M. U., Ullah, A., and Ullah, R. (2021). Mechanical properties of sustainable concrete modified by adding marble slurry as cement substitution. AIMS Mat. Sci. 8, 343–358. doi:10.3934/matersci.2021022
Ahmad, W., Farooq, S. H., Usman, M., Khan, M., Ahmad, A., Aslam, F., et al. (2020b). Effect of coconut fiber length and content on properties of high strength concrete. Materials 13 (5), 1075. doi:10.3390/ma13051075
Ahmed, W., and Lim, C. W. (2021a). Coupling effect assessment of vacuum based pozzolana slurry encrusted recycled aggregate and basalt fiber on mechanical performance of fiber reinforced concrete. Constr. Build. Mater. 300, 124032. doi:10.1016/j.conbuildmat.2021.124032
Ahmed, W., and Lim, C. W. (2021b). Production of sustainable and structural fiber reinforced recycled aggregate concrete with improved fracture properties: A review. J. Clean. Prod. 279, 123832. doi:10.1016/j.jclepro.2020.123832
Aisheh, Y. I. A., Atrushi, D. S., Akeed, M. H., Qaidi, S., and Tayeh, B. A. (2022). Influence of steel fibers and microsilica on the mechanical properties of ultra-high-performance geopolymer concrete (UHP-GPC). Case Stud. Constr. Mater. 17, e01245. doi:10.1016/j.cscm.2022.e01245
Aı̈tcin, P.-C. (2000). Cements of yesterday and today: Concrete of tomorrow. Cem. Concr. Res. 30 (9), 1349–1359. doi:10.1016/S0008-8846(00)00365-3
Akbar, A., and Liew, K. (2021). Multicriteria performance evaluation of fiber-reinforced cement composites: An environmental perspective. Compos. Part B Eng. 218, 108937. doi:10.1016/j.compositesb.2021.108937
Akeed, M. H., Qaidi, S., Ahmed, H. U., Emad, W., Faraj, R. H., Mohammed, A. S., et al. (2022a). Ultra-high-performance fiber-reinforced concrete. Part III: Fresh and hardened properties. Case Stud. Constr. Mater. 17, e01265. doi:10.1016/j.cscm.2022.e01265
Akeed, M. H., Qaidi, S., Ahmed, H. U., Faraj, R. H., Mohammed, A. S., Emad, W., et al. (2022b). Ultra-high-performance fiber-reinforced concrete. Part IV: Durability properties, cost assessment, applications, and challenges. Case Stud. Constr. Mater. 17, e01271. doi:10.1016/j.cscm.2022.e01271
Akeed, M. H., Qaidi, S., Ahmed, H. U., Faraj, R. H., Mohammed, A. S., Emad, W., et al. (2022c). Ultra-high-performance fiber-reinforced concrete. Part II: Hydration and microstructure. Case Stud. Constr. Mater. 17, e01289. doi:10.1016/j.cscm.2022.e01289
Alkaysi, M., El-Tawil, S., Liu, Z., and Hansen, W. (2016). Effects of silica powder and cement type on durability of ultra high performance concrete (UHPC). Cem. Concr. Compos. 66, 47–56. doi:10.1016/j.cemconcomp.2015.11.005
Almeshal, I., Al-Tayeb, M. M., Qaidi, S. M. A., Abu Bakar, B. H., and Tayeh, B. A. (2022). Mechanical properties of eco-friendly cements-based glass powder in aggressive medium. Mater. Today Proc. 58, 1582–1587. doi:10.1016/j.matpr.2022.03.613
Alsalman, A., Dang, C. N., and Hale, W. M. (2017). Development of ultra-high performance concrete with locally available materials. Constr. Build. Mater. 133, 135–145. doi:10.1016/j.conbuildmat.2016.12.040
Alwesabi, E. A. H., Abu Bakar, B. H., Alshaikh, I. M. H., Abadel, A. A., Alghamdi, H., and Wasim, M. (2022). An experimental study of compressive toughness of Steel–Polypropylene hybrid Fibre-Reinforced concrete. Structures 37, 379–388. doi:10.1016/j.istruc.2022.01.025
Alwesabi, E. A. H., Bakar, B. H. A., Alshaikh, I. M. H., and Akil, H. M. (2020). Experimental investigation on mechanical properties of plain and rubberised concretes with steel–polypropylene hybrid fibre. Constr. Build. Mater. 233, 117194. doi:10.1016/j.conbuildmat.2019.117194
Amin, M. N., Ahmad, W., Khan, K., and Sayed, M. M. (2022). Mapping research knowledge on rice husk ash application in concrete: A scientometric review. Materials 15 (10), 3431. doi:10.3390/ma15103431
Amin, M., Tayeh, B. A., and Agwa, I. S. (2020). Effect of using mineral admixtures and ceramic wastes as coarse aggregates on properties of ultrahigh-performance concrete. J. Clean. Prod. 273, 123073. doi:10.1016/j.jclepro.2020.123073
Arora, A., Yao, Y., Mobasher, B., and Neithalath, N. (2019). Fundamental insights into the compressive and flexural response of binder-and aggregate-optimized ultra-high performance concrete (UHPC). Cem. Concr. Compos. 98, 1–13. doi:10.1016/j.cemconcomp.2019.01.015
Arunothayan, A. R., Nematollahi, B., Ranade, R., Bong, S. H., and Sanjayan, J. (2020). Development of 3D-printable ultra-high performance fiber-reinforced concrete for digital construction. Constr. Build. Mater. 257, 119546. doi:10.1016/j.conbuildmat.2020.119546
Askar, L. K., Tayeh, B. A., and Abu Bakar, B. H. (2013). Effect of different curing conditions on the mechanical properties of UHPFC. Iran. J. Energy & Environ. 4 (3). doi:10.5829/idosi.ijee.2013.04.03.18
Aslam, F., Zaid, O., Althoey, F., Alyami, S. H., Qaidi, S. M., de Prado Gil, J., et al. (2022). Evaluating the influence of fly ash and waste glass on the characteristics of coconut fibers reinforced concrete. New Jersey, NJ: Structural Concrete.
ASTM (2018). ASTM C125-standard terminology relating to concrete and concrete aggregates. Pennsylvania: ASTM International West Conshohocken.
Aubry, S., Bompas, P., Vaudeville, B., Corvez, D., Lagrange, T., Mazzacane, P., et al. (2013). “A UHPFRC cladding challenge: The fondation louis vuitton pour la création" iceberg,” in 2nd RILEM-fib-AFGC international Symposium on ultra-high performance fibre-reinforced concrete.
Bae, B.-I., Choi, H.-K., Lee, B.-S., and Bang, C.-H. (2016). Compressive behavior and mechanical characteristics and their application to stress-strain relationship of steel fiber-reinforced reactive powder concrete. Adv. Mater. Sci. Eng. 2016, 1–11. doi:10.1155/2016/6465218
Bahari, A., Sadeghi-Nik, A., Cerro-Prada, E., Sadeghi-Nik, A., Roodbari, M., and Zhuge, Y. (2021). One-step random-walk process of nano-particles in cement-based materials. J. Cent. South Univ. 28 (6), 1679–1691. doi:10.1007/s11771-021-4726-6
Bahari, A., Sadeghi-Nik, A., Roodbari, M., Sadeghi-Nik, A., and Mirshafiei, E. (2018). Experimental and theoretical studies of ordinary Portland cement composites contains nano LSCO perovskite with Fokker-Planck and chemical reaction equations. Constr. Build. Mater. 163, 247–255. doi:10.1016/j.conbuildmat.2017.12.073
Bahari, A., Sadeghi-Nik, A., Shaikh, F. U. A., Sadeghi-Nik, A., Cerro-Prada, E., Mirshafiei, E., et al. (2022). Experimental studies on rheological, mechanical, and microstructure properties of self-compacting concrete containing perovskite nanomaterial. Struct. Concr. 23 (1), 564–578. doi:10.1002/suco.202000548
Biswas, R. K., Bin Ahmed, F., Haque, M. E., Provasha, A. A., Hasan, Z., Hayat, F., et al. (2021). Effects of steel fiber percentage and aspect ratios on fresh and harden properties of ultra-high performance fiber reinforced concrete. Appl. Mech. 2 (3), 501–515. doi:10.3390/applmech2030028
Brühwiler, E. (2016). Recommendation: Ultra-high performance fibre reinforced cement-based composites (UHPFRC) construction material, dimensioning and application. Zurich: EPFL.
C/Cm-17, A. (2017). Standard practice for fabricating and testing specimens of ultra-high performance concrete. West Conshohocken, PA: ASTM International.
Cao, M., Li, L., and Khan, M. (2018a). Effect of hybrid fibers, calcium carbonate whisker and coarse sand on mechanical properties of cement-based composites. Mat. construcc. 68 (330), e156. doi:10.3989/mc.2018.01717
Cao, M., Xie, C., Li, L., and Khan, M. (2019). Effect of different PVA and steel fiber length and content on mechanical properties of CaCO<sub>3</sub> whisker reinforced cementitious composites. Mat. construcc. 69 (336), e200. doi:10.3989/mc.2019.12918
Cao, M., Xie, C., Li, L., and Khan, M. (2018b). The relationship between reinforcing index and flexural parameters of new hybrid fiber reinforced slab. Comput. Concr. Int. J. 22 (5), 481–492.
Cao, Y., Liu, G., Brouwers, H., and Yu, Q. (2020). Enhancing the low-velocity impact resistance of ultra-high performance concrete by an optimized layered-structure concept. Compos. Part B Eng. 200, 108221. doi:10.1016/j.compositesb.2020.108221
Chan, Y.-W., and Chu, S.-H. (2004). Effect of silica fume on steel fiber bond characteristics in reactive powder concrete. Cem. Concr. Res. 34 (7), 1167–1172. doi:10.1016/j.cemconres.2003.12.023
Chen, X., Wan, D.-w., Jin, L.-z., Qian, K., and Fu, F. (2019). Experimental studies and microstructure analysis for ultra high-performance reactive powder concrete. Constr. Build. Mater. 229, 116924. doi:10.1016/j.conbuildmat.2019.116924
Corvez, D., and Masson, B. (2013). “UHPFRC solutions for the retrofit of nuclear reactor containment walls,” in Proceedings UHPFRC, 147–156.
Dabbaghi, F., Sadeghi-Nik, A., Libre, N. A., and Nasrollahpour, S. (2021). Characterizing fiber reinforced concrete incorporating zeolite and metakaolin as natural pozzolans. Structures 34, 2617–2627. doi:10.1016/j.istruc.2021.09.025
De Larrard, F., and Sedran, T. (2002). Mixture-proportioning of high-performance concrete. Cem. Concr. Res. 32 (11), 1699–1704. doi:10.1016/s0008-8846(02)00861-x
Denarié, E. (2005). Samaris D22 - full scale application of UHPFRC for the rehabilitation of bridges – from the lab to the field. SAMARIS.
Deng, Y., Zhang, Z., Shi, C., Wu, Z., and Zhang, C. (2022). Steel fiber–matrix interfacial bond in ultra-high performance concrete: A review. Engineering.
Dils, J., De Schutter, G., and Boel, V. (2012). Influence of mixing procedure and mixer type on fresh and hardened properties of concrete: A review. Mat. Struct. 45 (11), 1673–1683. doi:10.1617/s11527-012-9864-8
Dingqiang, F., Yu, R., Kangning, L., Junhui, T., Zhonghe, S., Chunfeng, W., et al. (2021). Optimized design of steel fibres reinforced ultra-high performance concrete (UHPC) composites: Towards to dense structure and efficient fibre application. Constr. Build. Mater. 273, 121698. doi:10.1016/j.conbuildmat.2020.121698
Du, J., Meng, W., Khayat, K. H., Bao, Y., Guo, P., Lyu, Z., et al. (2021). New development of ultra-high-performance concrete (UHPC). Compos. Part B Eng. 224, 109220. doi:10.1016/j.compositesb.2021.109220
Faraj, R. H., Ahmed, H. U., Rafiq, S., Sor, N. H., Ibrahim, D. F., and Qaidi, S. M. A. (2022). Performance of self-compacting mortars modified with nano-particles: A systematic review and modeling. Clean. Mater. 4, 100086. doi:10.1016/j.clema.2022.100086
Farooq, F., Ahmed, W., Akbar, A., Aslam, F., and Alyousef, R. (2021). Predictive modeling for sustainable high-performance concrete from industrial wastes: A comparison and optimization of models using ensemble learners. J. Clean. Prod. 292, 126032. doi:10.1016/j.jclepro.2021.126032
Farooqi, M. U., and Ali, M. (2022). A study on natural fibre reinforced concrete from materials to structural applications. Arab. J. Sci. Eng. doi:10.1007/s13369-022-06977-1
Farooqi, M. U., and Ali, M. (2019). Effect of pre-treatment and content of wheat straw on energy absorption capability of concrete. Constr. Build. Mater. 224, 572–583. doi:10.1016/j.conbuildmat.2019.07.086
Gamarra, J. (2016). Potential application of ultra-high performance fiber-reinforced concrete with wet-mix shotcrete system in tunneling.
Gesoglu, M., Güneyisi, E., Muhyaddin, G. F., and Asaad, D. S. (2016). Strain hardening ultra-high performance fiber reinforced cementitious composites: Effect of fiber type and concentration. Compos. Part B Eng. 103, 74–83. doi:10.1016/j.compositesb.2016.08.004
Gong, J., Ma, Y., Fu, J., Hu, J., Ouyang, X., Zhang, Z., et al. (2022). Utilization of fibers in ultra-high performance concrete: A review. Engineering: Composites Part B, 109995.
Gowripalan, N., and Gilbert, R. (2000). Design guidelines for ductal prestressed concrete beams. Reference Artical. Sydney, NSW: The University of NSW.
Graybeal, B. A. (2006). Material property characterization of ultra-high performance concrete. United States: Federal Highway Administration. Office of Infrastructure.
Gu, C., Zhao, S., Sun, W., and Wang, Q. (2013). “Production of precast UHPFRC pavement cover plates in high-speed railway construction,” in Proceedings of international symposium on ultra-high performance fiber-reinforced concrete. Editors F. Toutlemonde, and J. Resplendino (Marseille, France, 463–470.
Gu, M., Mo, H., Qiu, J., Yuan, J., and Xia, Q. (2022). Behavior of floating stone columns reinforced with geogrid encasement in model tests. Front. Mat. 9, 980851. doi:10.3389/fmats.2022.980851
Gul, A., Alam, B., Iqbal, M. J., Ahmed, W., Shahzada, K., Javed, M. H., et al. (2021). Impact of length and percent dosage of recycled steel fibers on the mechanical properties of concrete. Civ. Eng. J. 7 (10), 1650–1666. doi:10.28991/cej-2021-03091750
Habel, K., and Gauvreau, P. (2008). Response of ultra-high performance fiber reinforced concrete (UHPFRC) to impact and static loading. Cem. Concr. Compos. 30 (10), 938–946. doi:10.1016/j.cemconcomp.2008.09.001
Hajar, Z., Novarin, M., Servant, C., Généreux, G., Przybyla, D., and Bitar, D. (2013). “"Innovative solution for strengthening orthotropic decks using UHPFRC: The Illzach bridge,” in Proceedings of international symposium on ultra-high performance fiber-reinforced concrete, 117–126.
He, J., Chen, W., Zhang, B., Yu, J., and Liu, H. (2021). The mechanical properties and damage evolution of UHPC reinforced with glass fibers and high-performance polypropylene fibers. Materials 14 (9), 2455. doi:10.3390/ma14092455
Huang, H., Gao, X., Li, L., and Wang, H. (2018). Improvement effect of steel fiber orientation control on mechanical performance of UHPC. Constr. Build. Mater. 188, 709–721. doi:10.1016/j.conbuildmat.2018.08.146
Huang, H., Yao, Y., Liang, C., and Ye, Y. (2022). Experimental study on cyclic performance of steel-hollow core partially encased composite spliced frame beam. Soil Dyn. Earthq. Eng. 163, 107499. doi:10.1016/j.soildyn.2022.107499
Huang, W., Kazemi-Kamyab, H., Sun, W., and Scrivener, K. (2017). Effect of replacement of silica fume with calcined clay on the hydration and microstructural development of eco-UHPFRC. Mater. Des. 121, 36–46. doi:10.1016/j.matdes.2017.02.052
Huang, Y. (2022). Three-dimensional numerical investigation of mixed-mode debonding of FRP-concrete interface using a cohesive zone model. Constr. Build. Mater. 350, 128818. doi:10.1016/j.conbuildmat.2022.128818
Hung, C.-C., Chen, Y.-T., and Yen, C.-H. (2020). Workability, fiber distribution, and mechanical properties of UHPC with hooked end steel macro-fibers. Constr. Build. Mater. 260, 119944. doi:10.1016/j.conbuildmat.2020.119944
Ibrahim, M. A., Farhat, M., Issa, M. A., and Hasse, J. A. (2017). Effect of material constituents on mechanical and fracture mechanics properties of ultra-high-performance concrete. ACI Mater. J. 114 (3). doi:10.14359/51689717
Jsce, F. (2004). Recommendations for design and construction of ultra-high strength fiber reinforced concrete structures (Draft). Japan: Japan Society of Civil Engineers Tokyo.
Kci-M-12-003, (2012). Design recommendations for ultra-high performance concrete K-UHPC. Seoul: Korea Concrete Institute Seoul.
Khan, M., Cao, M., and Ali, M. (2018a). Effect of basalt fibers on mechanical properties of calcium carbonate whisker-steel fiber reinforced concrete. Constr. Build. Mater. 192, 742–753. doi:10.1016/j.conbuildmat.2018.10.159
Khan, M., Cao, M., and Ali, M. (2018b). “Influence of CaCO3 whiskers, steel fibers and basalt fibers hybridization on flexural toughness of concrete,” in Proceedings of the fifth international conference on sustainable construction materials and technologies (London, UK), 14–17.
Khan, M., Cao, M., Chu, S., and Ali, M. (2022a). Properties of hybrid steel-basalt fiber reinforced concrete exposed to different surrounding conditions. Constr. Build. Mater. 322, 126340. doi:10.1016/j.conbuildmat.2022.126340
Khan, M., Cao, M., Xie, C., and Ali, M. (2022b). Effectiveness of hybrid steel-basalt fiber reinforced concrete under compression. Case Stud. Constr. Mater. 16, e00941. doi:10.1016/j.cscm.2022.e00941
Khan, M., Cao, M., Xie, C., and Ali, M. (2021). Efficiency of basalt fiber length and content on mechanical and microstructural properties of hybrid fiber concrete. Fatigue Fract. Eng. Mat. Struct. 44 (8), 2135–2152. doi:10.1111/ffe.13483
Khan, M., Lao, J., and Dai, J.-G. (2022c). Comparative study of advanced computational techniques for estimating the compressive strength of UHPC. J. Asian Concr. Fed. 8, 51–68. doi:10.18702/acf.2022.6.8.1.51
Khan, U. A., Jahanzaib, H. M., Khan, M., and Ali, M. (2019). “Improving the tensile energy absorption of high strength natural fiber reinforced concrete with fly-ash for bridge girders,” in Key engineering materials. Switzerland: Trans Tech Publ, 335–342.
Khayat, K. H., Meng, W., Vallurupalli, K., and Teng, L. (2019). Rheological properties of ultra-high-performance concrete—an overview. Cem. Concr. Res. 124, 105828. doi:10.1016/j.cemconres.2019.105828
Kim, D. J., Park, S. H., Ryu, G. S., and Koh, K. T. (2011). Comparative flexural behavior of hybrid ultra high performance fiber reinforced concrete with different macro fibers. Constr. Build. Mater. 25 (11), 4144–4155. doi:10.1016/j.conbuildmat.2011.04.051
Kwon, S., Nishiwaki, T., Kikuta, T., and Mihashi, H. (2014). Development of ultra-high-performance hybrid fiber-reinforced cement-based composites. ACI Mater. J. 111 (3), 309. doi:10.14359/51686890
Lan, Y., Zheng, B., Shi, T., Ma, C., Liu, Y., and Zhao, Z. (2022). Crack resistance properties of carbon nanotube-modified concrete. Mag. Concr. Res. 74, 1165–1175. doi:10.1680/jmacr.21.00227
Larsen, I. L., and Thorstensen, R. T. (2020). The influence of steel fibres on compressive and tensile strength of ultra high performance concrete: A review. Constr. Build. Mater. 256, 119459. doi:10.1016/j.conbuildmat.2020.119459
Lei, V.-Y., Nematollahi, B., Said, A. B. M., Gopal, B. A., and Yee, T. S. (2012). Application of ultra high performance fiber reinforced concrete †"the Malaysia perspective. Int. J. Sustain. Constr. Eng. Technol. 3 (1), 26–44.
Li, G., Zhou, C., Ahmad, W., Usanova, K. I., Karelina, M., Mohamed, A. M., et al. (2022a). Fly ash application as supplementary cementitious material: A review. Materials 15 (7), 2664. doi:10.3390/ma15072664
Li, P., Sluijsmans, M. J., Brouwers, H., and Yu, Q. (2020). Functionally graded ultra-high performance cementitious composite with enhanced impact properties. Compos. Part B Eng. 183, 107680. doi:10.1016/j.compositesb.2019.107680
Li, P., Yu, Q., and Brouwers, H. (2018). Effect of coarse basalt aggregates on the properties of Ultra-high Performance Concrete (UHPC). Constr. Build. Mater. 170, 649–659. doi:10.1016/j.conbuildmat.2018.03.109
Li, S., Jensen, O. M., Wang, Z., and Yu, Q. (2021). Influence of micromechanical property on the rate-dependent flexural strength of ultra-high performance concrete containing coarse aggregates (UHPC-CA). Compos. Part B Eng. 227, 109394. doi:10.1016/j.compositesb.2021.109394
Liu, J., Han, F., Cui, G., Zhang, Q., Lv, J., Zhang, L., et al. (2016). Combined effect of coarse aggregate and fiber on tensile behavior of ultra-high performance concrete. Constr. Build. Mater. 121, 310–318. doi:10.1016/j.conbuildmat.2016.05.039
López, J. A., Serna, P., and Navarro-Gregori, J. (2017). “Advances in the development of the first UHPFRC recommendations in Spain: Material classification, design and characterization,” in UHPFRC 2017 Designing and Building with UHPFRC: New large-Scale implementations, recent technical advances, experience and standards. Editors F. Toutlemonde, and J. T. Ch. Resplendino (France: RILEM Publications SAR), 565–574.
Máca, P., Sovják, R., and Konvalinka, P. (2014). Mix design of UHPFRC and its response to projectile impact. Int. J. Impact Eng. 63, 158–163. doi:10.1016/j.ijimpeng.2013.08.003
Mansour, W., and Tayeh, B. A. (2020). Shear behaviour of RC beams strengthened by various ultrahigh performance fibre-reinforced concrete systems. Adv. Civ. Eng. 2020, 1–18. doi:10.1155/2020/2139054
Marković, I. (2006). High-performance hybrid-fibre concrete: Development and utilisation. (Amsterdam, NH: IOS Press).
Mazzacane, P., Ricciotti, R., Lamoureux, G., and Corvez, D. (2013a). “Roofing of the stade jean bouin in UHPFRC,” in Proceedings of international Symposium on ultra-high performance fibre-reinforced concrete, 59–68.
Mazzacane, P., Ricciotti, R., Teply, F., Tollini, E., and Corvez, D. (2013b). “Mucem: The builder's perspective,” in Proceedings UHPFRC, 3–16.
Menétrey, P. (2013). “UHPFRC cladding for the Qatar national Museum,” in Proceedings of the international symposium on ultra-high performance fiber-reinforced concrete (Marseille, France, 1–3.
Meng, Q., Wu, C., Li, J., Liu, Z., Wu, P., Yang, Y., et al. (2020). Steel/basalt rebar reinforced Ultra-High Performance Concrete components against methane-air explosion loads. Compos. Part B Eng. 198, 108215. doi:10.1016/j.compositesb.2020.108215
Meng, W., and Khayat, K. (2017a). Effects of saturated lightweight sand content on key characteristics of ultra-high-performance concrete. Cem. Concr. Res. 101, 46–54. doi:10.1016/j.cemconres.2017.08.018
Meng, W., and Khayat, K. H. (2018). Effect of hybrid fibers on fresh properties, mechanical properties, and autogenous shrinkage of cost-effective UHPC. J. Mat. Civ. Eng. 30 (4), 04018030. doi:10.1061/(asce)mt.1943-5533.0002212
Meng, W., and Khayat, K. H. (2017b). Improving flexural performance of ultra-high-performance concrete by rheology control of suspending mortar. Compos. Part B Eng. 117, 26–34. doi:10.1016/j.compositesb.2017.02.019
Meng, W., Valipour, M., and Khayat, K. H. (2017). Optimization and performance of cost-effective ultra-high performance concrete. Mat. Struct. 50 (1), 29–16. doi:10.1617/s11527-016-0896-3
Meng, Z., Li, L., Farooqi, M. U., Feng, L., and Wang, L. (2022). Fiber factor for fresh and hardened properties of polyethylene fiber-reinforced geopolymer mortar. J. Build. Eng. 53, 104556. doi:10.1016/j.jobe.2022.104556
Millard, S. G., Molyneaux, T. C. K., Barnett, S. J., and Gao, X. (2010). Dynamic enhancement of blast-resistant ultra high performance fibre-reinforced concrete under flexural and shear loading. Int. J. Impact Eng. 37 (4), 405–413. doi:10.1016/j.ijimpeng.2009.09.004
Mishra, O., and Singh, S. (2019). An overview of microstructural and material properties of ultra-high-performance concrete. J. Sustain. Cement-Based Mater. 8 (2), 97–143. doi:10.1080/21650373.2018.1564398
Mo, Z., Wang, R., and Gao, X. (2020). Hydration and mechanical properties of UHPC matrix containing limestone and different levels of metakaolin. Constr. Build. Mater. 256, 119454. doi:10.1016/j.conbuildmat.2020.119454
Moreillon, L., and Menétrey, P. (2013). “Rehabilitation and strengthening of existing RC structures with UHPFRC: Various applications,” in RILEM-fib-AFGC int. Symposium on ultra-high performance fibre-reinforced concrete (France: RILEM Publication SARL), 136.
Mostofinejad, D., Nikoo, M. R., and Hosseini, S. A. (2016). Determination of optimized mix design and curing conditions of reactive powder concrete (RPC). Constr. Build. Mater. 123, 754–767. doi:10.1016/j.conbuildmat.2016.07.082
Naaman, A., and Wille, K. (2010). Some correlation between high packing density, ultra-high performance, flow ability, and fiber reinforcement of a concrete matrix. BAC2010—2nd Iber. Congr. Self Compact.
Nematollahi, B., Saifulnaz, R. M., Jaafar, M. S., and Voo, Y. L. (2012). A review on ultra high performance'ductile'concrete (UHPdC) technology. Int. J. Civ. Struct. Eng. 2 (3), 994. doi:10.6088/ijcser.00202030026
Ng, T. S., Voo, Y. L., and Foster, S. J. (2012). “Sustainability with ultra-high performance and geopolymer concrete construction,” in Innovative materials and techniques in concrete construction. Editor M. N. Fardis (Springer Netherlands), 81–100.
Niu, Y., Huang, H., Zhang, J., Jin, W., Wei, J., and Yu, Q. (2019). Development of the strain field along the crack in ultra-high-performance fiber-reinforced concrete (UHPFRC) under bending by digital image correlation technique. Cem. Concr. Res. 125, 105821. doi:10.1016/j.cemconres.2019.105821
Pakravan, H. R., and Ozbakkaloglu, T. (2019). Synthetic fibers for cementitious composites: A critical and in-depth review of recent advances. Constr. Build. Mater. 207, 491–518. doi:10.1016/j.conbuildmat.2019.02.078
Park, J.-J., Yoo, D.-Y., Park, G.-J., and Kim, S.-W. (2017). Feasibility of reducing the fiber content in ultra-high-performance fiber-reinforced concrete under flexure. Materials 10 (2), 118. doi:10.3390/ma10020118
Park, J.-S., Kim, Y. J., Cho, J.-R., and Jeon, S.-J. (2015). Early-age strength of ultra-high performance concrete in various curing conditions. Materials 8 (8), 5537–5553. doi:10.3390/ma8085261
Park, S. H., Kim, D. J., Ryu, G. S., and Koh, K. T. (2012). Tensile behavior of ultra high performance hybrid fiber reinforced concrete. Cem. Concr. Compos. 34 (2), 172–184. doi:10.1016/j.cemconcomp.2011.09.009
Perry, V., and Habel, K. (2017). Standardization of ultra-high performance concrete the Canadian perspective. Paris: UHPFRC.
Pokorný, P., Kolísko, J., Čítek, D., and Kostelecká, M. (2020). Effect of elevated temperature on the bond strength of prestressing reinforcement in UHPC. Materials 13 (21), 4990. doi:10.3390/ma13214990
Pourbaba, M., Asefi, E., Sadaghian, H., and Mirmiran, A. (2018). Effect of age on the compressive strength of ultra-high-performance fiber-reinforced concrete. Constr. Build. Mater. 175, 402–410. doi:10.1016/j.conbuildmat.2018.04.203
Qaidi, S. M. A., Mohammed, A. S., Ahmed, H. U., Faraj, R. H., Emad, W., Tayeh, B. A., et al. (2022). Rubberized geopolymer composites: A comprehensive review. Ceram. Int. 48 (17), 24234–24259. doi:10.1016/j.ceramint.2022.06.123
Qian, Y. (2017). Characterization of structural rebuilding and shear migration in cementitious materials in consideration of thixotropy. Columbia University.
Qin, J., Dai, F., Ma, H., Dai, X., Li, Z., Jia, X., et al. (2022). Development and characterization of magnesium phosphate cement based ultra-high performance concrete. Compos. Part B Eng. 234, 109694. doi:10.1016/j.compositesb.2022.109694
Qin, Y., Zhang, X., Chai, J., Xu, Z., and Li, S. (2019). Experimental study of compressive behavior of polypropylene-fiber-reinforced and polypropylene-fiber-fabric-reinforced concrete. Constr. Build. Mater. 194, 216–225. doi:10.1016/j.conbuildmat.2018.11.042
Qu, D., Cai, X., and Chang, W. (2018). Evaluating the effects of steel fibers on mechanical properties of ultra-high performance concrete using artificial neural networks. Appl. Sci. 8 (7), 1120. doi:10.3390/app8071120
Rezaie, A. B., Liebscher, M., Ranjbarian, M., Simon, F., Zimmerer, C., Drechsler, A., et al. (2021). Enhancing the interfacial bonding between PE fibers and cementitious matrices through polydopamine surface modification. Compos. Part B Eng. 217, 108817. doi:10.1016/j.compositesb.2021.108817
Richard, P., and Cheyrezy, M. (1995). Composition of reactive powder concretes. Cem. Concr. Res. 25 (7), 1501–1511. doi:10.1016/0008-8846(95)00144-2
Rong, Z., Sun, W., Xiao, H., and Jiang, G. (2015). Effects of nano-SiO2 particles on the mechanical and microstructural properties of ultra-high performance cementitious composites. Cem. Concr. Compos. 56, 25–31. doi:10.1016/j.cemconcomp.2014.11.001
Rossignolo, J. A. (2007). Effect of silica fume and SBR latex on the pasteaggregate interfacial transition zone. Mat. Res. 10, 83–86. doi:10.1590/s1516-14392007000100018
Russell, H. G., Graybeal, B. A., and Russell, H. G. (2013b). Ultra-high performance concrete: A state-of-the-art report for the bridge community". United states. New Jersey, NJ: Federal Highway Administration. Office of Infrastructure.
Russell, H., Graybeal, B., and Russell, H. (2013a). Ultra-high performance concrete: A state-of-the-art report for the bridge community. Washington, DC: Federal Highway Administration. Rep. No". FHWA-HRT-13-060.
Sadrmomtazi, A., Tajasosi, S., and Tahmouresi, B. (2018). Effect of materials proportion on rheology and mechanical strength and microstructure of ultra-high performance concrete (UHPC). Constr. Build. Mater. 187, 1103–1112. doi:10.1016/j.conbuildmat.2018.08.070
Schachinger, I., Schubert, J., and Mazanec, O. (2004). “Effect of mixing and placement methods on fresh and hardened ultra high performance concrete (UHPC),” in International Symposium on ultra high performance concrete, 575–586.
Schmidt, M., and Fehling, E. (2005). Ultra-high-performance concrete: Research, development and application in europe. ACI Spec. Publ. 228 (1), 51–78.
Schröfl, C., Gruber, M., and Plank, J. (2012). Preferential adsorption of polycarboxylate superplasticizers on cement and silica fume in ultra-high performance concrete (UHPC). Cem. Concr. Res. 42 (11), 1401–1408. doi:10.1016/j.cemconres.2012.08.013
Shafieifar, M., Farzad, M., and Azizinamini, A. (2017). Experimental and numerical study on mechanical properties of ultra high performance concrete (UHPC). Constr. Build. Mater. 156, 402–411. doi:10.1016/j.conbuildmat.2017.08.170
Shi, C., Wu, Z., Xiao, J., Wang, D., Huang, Z., and Fang, Z. (2015). A review on ultra high performance concrete: Part I. Raw materials and mixture design. Constr. Build. Mater. 101, 741–751. doi:10.1016/j.conbuildmat.2015.10.088
Shi, T., Liu, Y., Zhao, X., Wang, J., Zhao, Z., Corr, D. J., et al. (2022). Study on mechanical properties of the interfacial transition zone in carbon nanofiber-reinforced cement mortar based on the PeakForce tapping mode of atomic force microscope. J. Build. Eng. 61, 105248. doi:10.1016/j.jobe.2022.105248
Sidodikromo, E. P., Chen, Z., and Habib, M. (2019). Review of the cement-based composite ultra-high-performance concrete (UHPC). Open Civ. Eng. J. 13 (1), 147–162. doi:10.2174/1874149501913010147
Sobuz, H. R., Visintin, P., Mohamed Ali, M. S., Singh, M., Griffith, M. C., and Sheikh, A. H. (2016). Manufacturing ultra-high performance concrete utilising conventional materials and production methods. Constr. Build. Mater. 111, 251–261. doi:10.1016/j.conbuildmat.2016.02.102
Sohail, M. G., Wang, B., Jain, A., Kahraman, R., Ozerkan, N. G., Gencturk, B., et al. (2018). Advancements in concrete mix designs: High-performance and ultrahigh-performance concretes from 1970 to 2016. J. Mat. Civ. Eng. 30 (3), 04017310. doi:10.1061/(asce)mt.1943-5533.0002144
Soliman, A., and Nehdi, M. (2014). Effects of shrinkage reducing admixture and wollastonite microfiber on early-age behavior of ultra-high performance concrete. Cem. Concr. Compos. 46, 81–89. doi:10.1016/j.cemconcomp.2013.11.008
Soliman, N., and Tagnit-Hamou, A. (2016). Development of ultra-high-performance concrete using glass powder–Towards ecofriendly concrete. Constr. Build. Mater. 125, 600–612. doi:10.1016/j.conbuildmat.2016.08.073
Song, H., Liu, J., He, K., and Ahmad, W. (2021). A comprehensive overview of jute fiber reinforced cementitious composites. Case Stud. Constr. Mater. 15, e00724. doi:10.1016/j.cscm.2021.e00724
Stovall, T., De Larrard, F., and Buil, M. (1986). Linear packing density model of grain mixtures. Powder Technol. 48 (1), 1–12. doi:10.1016/0032-5910(86)80058-4
Tam, C. M., Tam, V. W. Y., and Ng, K. M. (2012). Assessing drying shrinkage and water permeability of reactive powder concrete produced in Hong Kong. Constr. Build. Mater. 26 (1), 79–89. doi:10.1016/j.conbuildmat.2011.05.006
Tayeh, B. A., Abu Bakar, B. H., and Megat Johari, M. A. (2013a). Characterization of the interfacial bond between old concrete substrate and ultra high performance fiber concrete repair composite. Mat. Struct. 46 (5), 743–753. doi:10.1617/s11527-012-9931-1
Tayeh, B. A., Abu Bakar, B. H., Megat Johari, M. A., and Zeyad, A. M. (2014). Microstructural analysis of the adhesion mechanism between old concrete substrate and UHPFC. J. Adhesion Sci. Technol. 28 (18), 1846–1864. doi:10.1080/01694243.2014.925386
Tayeh, B. A., Bakar, B. A., Johari, M. M., and Ratnam, M. M. (2013b). The relationship between substrate roughness parameters and bond strength of ultra high-performance fiber concrete. J. Adhesion Sci. Technol. 27 (16), 1790–1810. doi:10.1080/01694243.2012.761543
Tayeh, B. A., Bakar, B. H. A., Johari, M. A. M., and Voo, Y. L. (2013c). Utilization of ultra-high performance fibre concrete (UHPFC) for rehabilitation – a review. Procedia Eng. 54, 525–538. doi:10.1016/j.proeng.2013.03.048
Tayeh, B. A., Bakar, B. H. A., Megat Johari, M. A., and Zeyad, A. (2013d). “Flexural strength behavior of composite UHPFC-existing concrete,” in Advanced materials research: Trans tech publ, 32–36.
Teng, L., Meng, W., and Khayat, K. H. (2020). Rheology control of ultra-high-performance concrete made with different fiber contents. Cem. Concr. Res. 138, 106222. doi:10.1016/j.cemconres.2020.106222
Van Tuan, N., Ye, G., van Breugel, K., and Copuroglu, O. (2011a). Hydration and microstructure of ultra high performance concrete incorporating rice husk ash. Cem. Concr. Res. 41 (11), 1104–1111. doi:10.1016/j.cemconres.2011.06.009
Van Tuan, N., Ye, G., Van Breugel, K., Fraaij, A. L., and Dai Bui, D. (2011b). The study of using rice husk ash to produce ultra high performance concrete. Constr. Build. Mater. 25 (4), 2030–2035. doi:10.1016/j.conbuildmat.2010.11.046
Vande Voort, T. L., Suleiman, M. T., and Sritharan, S. (2008). Design and performance verification of ultra-high performance concrete piles for deep foundations.
Voo, Y., Foster, S., and Pek, L. (2017). “Ultra-high performance concrete—Technology for present and future,” in Proceedings of the high tech concrete: Where technology and engineering meet (Maastricht, Netherlands, 12–14.
Voo, Y., and Poon, W. (2009). “Ultra High performance ductile concrete (UHPdC) for Bridge engineering,” in Proceedings of the international Conference and Exhibition on bridge engineering.
Wang, C., Yang, C., Liu, F., Wan, C., and Pu, X. (2012). Preparation of ultra-high performance concrete with common technology and materials. Cem. Concr. Compos. 34 (4), 538–544. doi:10.1016/j.cemconcomp.2011.11.005
Wang, D., Shi, C., Wu, Z., Xiao, J., Huang, Z., and Fang, Z. (2015). A review on ultra high performance concrete: Part II. Hydration, microstructure and properties. Constr. Build. Mater. 96, 368–377. doi:10.1016/j.conbuildmat.2015.08.095
Wang, Q., Hussain, A., Farooqi, M. U., and Deifalla, A. F. (2022). Artificial intelligence-based estimation of ultra-high-strength concrete's flexural property. Case Stud. Constr. Mater. 17, e01243. doi:10.1016/j.cscm.2022.e01243
Wang, R., Gao, X., Huang, H., and Han, G. (2017). Influence of rheological properties of cement mortar on steel fiber distribution in UHPC. Constr. Build. Mater. 144, 65–73. doi:10.1016/j.conbuildmat.2017.03.173
Wetzel, A., and Middendorf, B. (2019). Influence of silica fume on properties of fresh and hardened ultra-high performance concrete based on alkali-activated slag. Cem. Concr. Compos. 100, 53–59. doi:10.1016/j.cemconcomp.2019.03.023
Wu, C., Oehlers, D. J., Rebentrost, M., Leach, J., and Whittaker, A. S. (2009). Blast testing of ultra-high performance fibre and FRP-retrofitted concrete slabs. Eng. Struct. 31 (9), 2060–2069. doi:10.1016/j.engstruct.2009.03.020
Wu, Z., Khayat, K. H., and Shi, C. (2019a). Changes in rheology and mechanical properties of ultra-high performance concrete with silica fume content. Cem. Concr. Res. 123, 105786. doi:10.1016/j.cemconres.2019.105786
Wu, Z., Khayat, K. H., and Shi, C. (2017a). Effect of nano-SiO2 particles and curing time on development of fiber-matrix bond properties and microstructure of ultra-high strength concrete. Cem. Concr. Res. 95, 247–256. doi:10.1016/j.cemconres.2017.02.031
Wu, Z., Shi, C., He, W., and Wang, D. (2017b). Static and dynamic compressive properties of ultra-high performance concrete (UHPC) with hybrid steel fiber reinforcements. Cem. Concr. Compos. 79, 148–157. doi:10.1016/j.cemconcomp.2017.02.010
Wu, Z., Shi, C., He, W., and Wang, D. (2016a). Uniaxial compression behavior of ultra-high performance concrete with hybrid steel fiber. J. Mat. Civ. Eng. 28 (12), 06016017. doi:10.1061/(asce)mt.1943-5533.0001684
Wu, Z., Shi, C., He, W., and Wu, L. (2016b). Effects of steel fiber content and shape on mechanical properties of ultra high performance concrete. Constr. Build. Mater. 103, 8–14. doi:10.1016/j.conbuildmat.2015.11.028
Wu, Z., Shi, C., and Khayat, K. H. (2019b). Investigation of mechanical properties and shrinkage of ultra-high performance concrete: Influence of steel fiber content and shape. Compos. Part B Eng. 174, 107021. doi:10.1016/j.compositesb.2019.107021
Wu, Z., Shi, C., and Khayat, K. (2016c). Influence of silica fume content on microstructure development and bond to steel fiber in ultra-high strength cement-based materials (UHSC). Cem. Concr. Compos. 71, 97–109. doi:10.1016/j.cemconcomp.2016.05.005
Xu, L., Wu, F., Chi, Y., Cheng, P., Zeng, Y., and Chen, Q. (2019). Effects of coarse aggregate and steel fibre contents on mechanical properties of high performance concrete. Constr. Build. Mater. 206, 97–110. doi:10.1016/j.conbuildmat.2019.01.190
Xu, S., Zhou, F., Li, Q., and Wu, P. (2021a). A novel dynamic cavity expansion model to predict the resistance of reactive powder concrete (RPC) against projectile impact. Compos. Part B Eng. 223, 109107. doi:10.1016/j.compositesb.2021.109107
Xu, Y., Ahmad, W., Ahmad, A., Ostrowski, K. A., Dudek, M., Aslam, F., et al. (2021b). Computation of high-performance concrete compressive strength using standalone and ensembled machine learning techniques. Materials 14 (22), 7034. doi:10.3390/ma14227034
Yang, S., Millard, S., Soutsos, M., Barnett, S., and Le, T. T. (2009). Influence of aggregate and curing regime on the mechanical properties of ultra-high performance fibre reinforced concrete (UHPFRC). Constr. Build. Mater. 23 (6), 2291–2298. doi:10.1016/j.conbuildmat.2008.11.012
Yazıcı, H. (2007). The effect of curing conditions on compressive strength of ultra high strength concrete with high volume mineral admixtures. Build. Environ. 42 (5), 2083–2089. doi:10.1016/j.buildenv.2006.03.013
Ye, J., Cui, C., Yu, J., Yu, K., and Xiao, J. (2021). Fresh and anisotropic-mechanical properties of 3D printable ultra-high ductile concrete with crumb rubber. Compos. Part B Eng. 211, 108639. doi:10.1016/j.compositesb.2021.108639
Yoo, D.-Y., and Banthia, N. (2016). Mechanical properties of ultra-high-performance fiber-reinforced concrete: A review. Cem. Concr. Compos. 73, 267–280. doi:10.1016/j.cemconcomp.2016.08.001
Yoo, D.-Y., Kang, S.-T., and Yoon, Y.-S. (2016). Enhancing the flexural performance of ultra-high-performance concrete using long steel fibers. Compos. Struct. 147, 220–230. doi:10.1016/j.compstruct.2016.03.032
Yoo, D.-Y., Kim, J.-J., and Chun, B. (2019). Dynamic pullout behavior of half-hooked and twisted steel fibers in ultra-high-performance concrete containing expansive agents. Compos. Part B Eng. 167, 517–532. doi:10.1016/j.compositesb.2019.03.022
Yoo, D.-Y., Kim, M. J., Kim, S.-W., and Park, J.-J. (2017a). Development of cost effective ultra-high-performance fiber-reinforced concrete using single and hybrid steel fibers. Constr. Build. Mater. 150, 383–394. doi:10.1016/j.conbuildmat.2017.06.018
Yoo, D.-Y., Kim, S.-W., and Park, J.-J. (2017b). Comparative flexural behavior of ultra-high-performance concrete reinforced with hybrid straight steel fibers. Constr. Build. Mater. 132, 219–229. doi:10.1016/j.conbuildmat.2016.11.104
Yoo, D.-Y., Kim, S., Park, G.-J., Park, J.-J., and Kim, S.-W. (2017c). Effects of fiber shape, aspect ratio, and volume fraction on flexural behavior of ultra-high-performance fiber-reinforced cement composites. Compos. Struct. 174, 375–388. doi:10.1016/j.compstruct.2017.04.069
You, I., Yoo, D.-Y., Kim, S., Kim, M.-J., and Zi, G. (2017). Electrical and self-sensing properties of ultra-high-performance fiber-reinforced concrete with carbon nanotubes. Sensors 17 (11), 2481. doi:10.3390/s17112481
Yu, R., Spiesz, P., and Brouwers, H. (2015a). Development of an eco-friendly Ultra-High Performance Concrete (UHPC) with efficient cement and mineral admixtures uses. Cem. Concr. Compos. 55, 383–394. doi:10.1016/j.cemconcomp.2014.09.024
Yu, R., Spiesz, P., and Brouwers, H. (2015b). Development of ultra-high performance fibre reinforced concrete (UHPFRC): Towards an efficient utilization of binders and fibres. Constr. Build. Mater. 79, 273–282. doi:10.1016/j.conbuildmat.2015.01.050
Yu, R., Spiesz, P., and Brouwers, H. (2014a). Effect of nano-silica on the hydration and microstructure development of Ultra-High Performance Concrete (UHPC) with a low binder amount. Constr. Build. Mater. 65, 140–150. doi:10.1016/j.conbuildmat.2014.04.063
Yu, R., Spiesz, P., and Brouwers, H. (2014b). Mix design and properties assessment of ultra-high performance fibre reinforced concrete (UHPFRC). Cem. Concr. Res. 56, 29–39. doi:10.1016/j.cemconres.2013.11.002
Zdeb, T. (2017). An analysis of the steam curing and autoclaving process parameters for reactive powder concretes. Constr. Build. Mater. 131, 758–766. doi:10.1016/j.conbuildmat.2016.11.026
Zhang, B., Ahmad, W., Ahmad, A., Aslam, F., and Joyklad, P. (2022). A scientometric analysis approach to analyze the present research on recycled aggregate concrete. J. Build. Eng. 46, 103679. doi:10.1016/j.jobe.2021.103679
Zhang, C., and Ali, A. (2021). The advancement of seismic isolation and energy dissipation mechanisms based on friction. Soil Dyn. Earthq. Eng. 146, 106746. doi:10.1016/j.soildyn.2021.106746
Zhang, Y., Li, X., Zhu, Y., and Shao, X. (2020). Experimental study on flexural behavior of damaged reinforced concrete (RC) beam strengthened by toughness-improved ultra-high performance concrete (UHPC) layer. Compos. Part B Eng. 186, 107834. doi:10.1016/j.compositesb.2020.107834
Zhang, Z., Yang, F., Zhang, H., Zhang, T., Wang, H., Xu, Y., et al. (2021). Influence of CeO2 addition on forming quality and microstructure of TiC -reinforced CrTi4-based laser cladding composite coating. Mater. Charact. 171, 110732. doi:10.1016/j.matchar.2020.110732
Zhao, S., Fan, J., and Sun, W. (2014). Utilization of iron ore tailings as fine aggregate in ultra-high performance concrete. Constr. Build. Mater. 50, 540–548. doi:10.1016/j.conbuildmat.2013.10.019
Zheng, Y., Zhou, Y., Nie, F., Luo, H., and Huang, X. (2022). Effect of a novel vibration mixing on the fiber distribution and mechanical properties of ultra-high performance concrete. Sustainability 14 (13), 7920. doi:10.3390/su14137920
Keywords: steel fiber, mechanical properties, concrete, fiber, fiber-reinforced composite
Citation: Alkadhim HA, Amin MN, Ahmad W, Khan K, Umbreen-us-Sahar , Al-Hashem MN and Mohamed A (2022) An overview of progressive advancement in ultra-high performance concrete with steel fibers. Front. Mater. 9:1091867. doi: 10.3389/fmats.2022.1091867
Received: 07 November 2022; Accepted: 16 November 2022;
Published: 02 December 2022.
Edited by:
Li Li, Northwest A & F University, ChinaReviewed by:
Junfeng Guan, North China University of Water Conservancy and Electric Power, ChinaCopyright © 2022 Alkadhim, Amin, Ahmad, Khan, Umbreen-us-Sahar, Al-Hashem and Mohamed. This is an open-access article distributed under the terms of the Creative Commons Attribution License (CC BY). The use, distribution or reproduction in other forums is permitted, provided the original author(s) and the copyright owner(s) are credited and that the original publication in this journal is cited, in accordance with accepted academic practice. No use, distribution or reproduction is permitted which does not comply with these terms.
*Correspondence: Muhammad Nasir Amin, bWdhZGlyQGtmdS5lZHUuc2E=
Disclaimer: All claims expressed in this article are solely those of the authors and do not necessarily represent those of their affiliated organizations, or those of the publisher, the editors and the reviewers. Any product that may be evaluated in this article or claim that may be made by its manufacturer is not guaranteed or endorsed by the publisher.
Research integrity at Frontiers
Learn more about the work of our research integrity team to safeguard the quality of each article we publish.