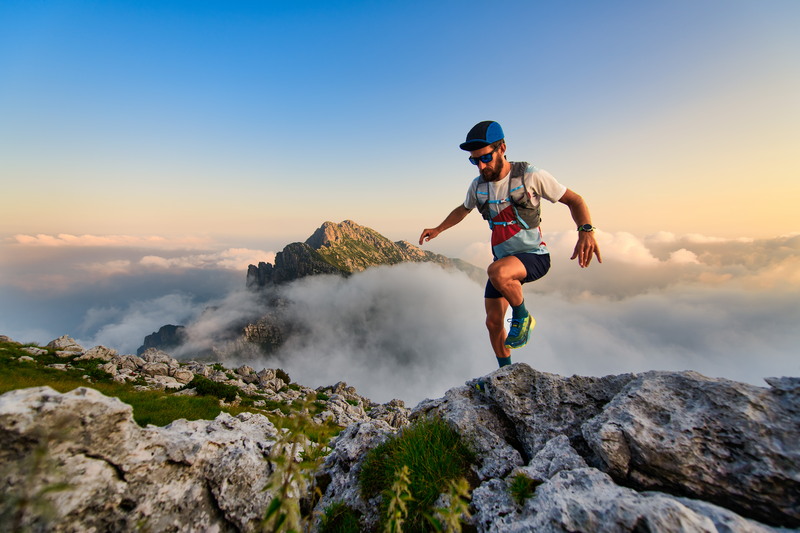
95% of researchers rate our articles as excellent or good
Learn more about the work of our research integrity team to safeguard the quality of each article we publish.
Find out more
REVIEW article
Front. Mater. , 10 January 2023
Sec. Polymeric and Composite Materials
Volume 9 - 2022 | https://doi.org/10.3389/fmats.2022.1089996
This article is part of the Research Topic ECCM Research Topic on Advanced Manufacturing of Composites View all 14 articles
Since the inception of carbon fiber reinforced polymer (CFRP) composites, different nanofillers have been investigated to strengthen their mechanical and physical properties. To date, the majority of research has focused on enhancing fiber/matrix interface characteristics and/or optimizing nanofiller dispersion within the matrix, both of which improve the performance of carbon fiber-epoxy composite structures. Nanofillers can be dispersed into the polymer matrix by different techniques or nanofillers are chemically bonded to fiber, polymer, or both via multiple reaction steps. However, a few studies were conducted showing the effects of different nanofillers on the performance of carbon fiber-epoxy composites. Here a critical study has been done to explore different carbon and cellulose-based nanofillers which are used to enhance the mechanical and physical properties of carbon fiber-epoxy composites. After giving a short history of carbon fiber production, the synthesis of carbon nanotubes (CNTs), graphene, cellulose-based nanofillers (cellulose nanocrystals and nanofibers), their dispersion in the polymer matrix, and chemical/physical bonding with the fiber or polymer have been extensively described here along with their processing techniques, characterizations, and applications in various fields.
Sir Joseph Wilson Swan has been coined as the father of the carbon fiber industry after he invented new incandescent light bulbs with carbonized paper as the newly used filament (Keyte et al., 2019). The American chemical inventor and businessman Thomas A. Edison commercialized the use of carbon filaments in his light bulbs. The use of carbon filaments allowed his bulbs to last for over 1200 h in his patent Electric-Lamp (U.S.P. Office, 1880). Minor discoveries in the use of carbon fiber were uncovered in the early 1900 s, but the next major milestone for carbon fiber was with Roger Bacon’s discovery of graphite whiskers, in the later 1950 s. These thin cylindrical-like layers of graphene laid the foundation of what we know today as carbon fibers, as Bacon discovered that when graphite was heated to arc temperatures, they form incredibly strong and flexible filaments (Bacon, 1960). In later years, Bacon also uncovered further discoveries with the microstructure of graphite (Bacon and Tang, 1964), further aiding to our current knowledge of carbon fibers. One of such discoveries Bacon and Wesley Schalamon patented was the use of creating carbon fiber by heating rayon and implementing a new method of stretching these fibers at temperatures as high as 2800°C, which resulted in greater young’s modulus (Schalamon et al., 1970). On the other side of the globe, researchers were uncovering the intricacies of carbon in tandem to Bacon. Polyacrylonitrile (PAN) acquired by Dr. Akio Shindo was researched in 1959 and it was discovered that it produced the greatest increase in mechanical properties. Shindo delved deeper in order to compare oxidized PAN fibers to non-oxidized PAN fibers which helped uncover that the oxidized fibers were better when simultaneously carbonizing a vast array of carbon fiber batches (Tanaka et al., 2018). After this discovery, William Watt and William Johnson, under the Royal Aircraft Establishment (RAE), spearheaded the commercial use of high-strength carbon fibers in 1963. It was discovered that heating the PAN fibers to 2500°C nearly tripled its stiffness and restricting the PAN fibers during oxidation allowed full production lines to be implemented by 1966 (Johnson and Figueiredo, 1990). These discoveries pushed PAN-based fibers into being the primary method of forming carbon fibers even currently forming 90% of all commercially used carbon fibers (Frank et al., 2017).
Rayon was first used to create high-strength carbon fibers back in the 1960 s, however, these produced low tensile strength and Young’s modulus relative to the other materials. Rayon is a cellulose-based carbon fiber, that is, known for having defects such as large void contents and interfilament bonding (Peng et al., 2003). However, a better method of creating usable carbon fiber was through another material called Pitch, which is derived from petroleum asphalt, coal tar or polyvinyl chloride. Pitch-based carbon fibers can be formed into either isotropic-pitch-based ormesophase-pitch-based carbon fibers (Inagaki and Inagaki, 2000). However, only mesophase pitches are commercially used to create carbon fiber. Pitch is typically used to create high-modulus fibers that many critical military operations need, while PAN allows for high-strength fibers. Currently, about 90% of the carbon fiber used is PAN-based. These three materials have led to a key shift in the use of carbon fiber as a material in popularity similar to aluminum, primarily due to material’s lightweight and strength properties. Despite its humble beginnings, the use of carbon fibers in structural applications has transformed this material into a multi-billion dollar industry (Mohee et al., 2016). Due to its increase in popularity, the PAN-based CF industry has been estimated to grow by 10% per year (Tanaka et al., 2018). Increasing its global market from $3.7 billion in 2020 to $8.9 billion in 2031 (Gogoi et al., 2022). This percentage increases within the construction industry, where estimates of its global usage increases by 12% (Roberts, 2009). However, due to the recent COVID-19 pandemic, the production of most composite businesses was halted with decreased production, increased costs and material and labor shortages.
Let’s discuss present day carbon fiber uses and how their versatility is displayed around the world. In recent years, (carbon) fiber-reinforced plastics usage within concrete has been investigated globally (Hollaway, 2003; Van Den Einde et al., 2003; Sadeghian et al., 2010; Mehdi and Resatoglu, 2022). In Asia, tests have been conducted on the effects of carbon fiber on their structures to replace steel (Ueda and Sato, 2002; Wu et al., 2014). The automotive industry also recognizes the application of composites, like carbon fiber, for introducing light weight structures (Alves et al., 2010; Koronis et al., 2013). As the price of CFRPs decreases yearly, composite usage is becoming more and more cost-effective. The main drawback of CFRPs is their ability to meet the needs of high-volume manufacturability or low downtime production. Still CFRPs are desired for their superior mechanical and structural properties relative to traditional materials (Ravishankar et al., 2019). In fact, when three Korean manufacturing companies joined together to create a CF battery pack module carrier, they experienced a 26% weight reduction, better recyclability, and cost reductions relative to a standard steel carrier (Koniuszewska and Kaczmar, 2016). Carbon fiber composites have also found their way into the sporting industry, once their price decreased to 100 Euro/kg (Perner et al., 2016). Super lightweight bicycle frames, tennis rackets and kayaks have been formed with carbon fiber prepreg. Even sensors and detection systems have been researched, with the aim of creating sensors that detect deformations within composite structures. The aviation and space industry are also looking at the key advantages that CFRPs have, especially Boeing and Airbus. In fact, 50 wt% of their newer airplanes, such as the Boeing 787 and Airbus 350, are composed of composites, which they have been using since the start of 1980 s 28, (Maria, 2013; Gerard, 2015). Aerospace manufacturers claimed that the use of these composite materials would help lower operating costs by 20% and lower greenhouse gas emissions by 25% (Marsh, 2007). Even other classes of airplanes, specifically privatized aircraft, have responded to this dramatic change from aluminum to composites. Airplanes can take advantage of carbon fiber’s high heat capacity and low density to create brake disks that are 40% lighter and lasts twice as long compared to traditional steel brakes (Windhorst and Blount, 1997). The defense and space industry has invested major stakes into CFRPs and their high strength to weight ratio. The British Aerospace Defense has spent the last 50 years developing and implementing carbon fiber composites within their war fighting planes, all to bluster their defenses and air superiority (Lewis, 1994). The Moscow based company AeroComposit is a company focused on researching and applying stronger components like carbon fiber within Russian aircraft for next-generation, single-aisle aircraft (Koniuszewska and Kaczmar, 2016). Due to stipulations put forth by the FAA, increasing thickness or radically changing aircraft internal features in favor of increased strength and mechanical properties incures costly impacts on composites, while maintaining a factor of safety. These issues are of key importance to the aerospace and defense industry (Mason et al., 2004).
One way carbon fiber can increase strength without increasing thickness is through its fiber orientation. Carbon fiber has four main orientations: uni-directional, bi-directional, quasi-isotropic and randomly oriented. When a load is placed onto a carbon fiber composite, the load must be distributed in the direction of the fibers, as opposed to the weak resin, else delamination occurs, and the component fails. A uni-directionally oriented composite has fibers along only one axis (vertically, horizontally, or diagonally), bi-directional has fibers aligned onto two axes, typically vertically and horizontally. Most applications have quasi-isotropic carbon fibers, due to its ability to apply loads in any direction which is done with different stackups. Most stackups use a variety of uni and bi-directional fibers assorted in different orientations.
A more recent approach to increasing the strength of these carbon composites has been the application of adding nanofillers between the epoxy matrix—nanoscopic materials that have the ability to increase the mechanical and electrical properties of composites. The word nanotechnology has been in use since the 1970s and was coined to distinguish the difference between microscale and nanoscale materials (Njuguna and Pielichowski, 2004a). Due to the large area of conventional fillers, it's only natural that buds and voids can occur randomly, which causes reductions in the laminate’s strength. Nanoparticles such as multi-walled carbon nanotubes (MWCNTs) and single-walled carbon nanotubes (SWCNTs) have gained much popularity and are being studied globally as an answer to composite reinforcement (Njuguna and Pielichowski, 2004b). CNTs are cylindrical hollow structures of pure graphite sheets. CNT structures are 100 times stronger than steel, while being six times less dense (Mittal et al., 2018). SWCNTs tend to have greater electrical properties than their multi-walled counterparts, which allows them to be used in electrical applications. Cellulose nanocrystals (CNC) are cellulose extracted from plant cell walls or other biological sources, with length and diameter within the nano scale (Xu et al., 2013). The properties of CNCs are greatly subject to change and can vary based on size, structure, and surface charge (Liu et al., 2011). These changes can occur due to their extraction method, but as a result of this versatility, CNCs and CNTs have been used in optical and chemical sensors (Consales et al., 2006; Cusano et al., 2006; Huang et al., 2015). Graphene is another nanomaterial that has been regarded as a wonder material, when referring to its electrical properties. Graphene is a monolayer of carbon atoms, which form a two-dimensional lattice, versus the one-dimensional graphite (Geim and Novoselov, 2007). Graphene and CNC have shown promising results as a superconductor with high power and energy density (Yang et al., 2019). It has also been studied within the nuclear industry for its uranium absorption (Liu and Mao, 2021). However, its high cost tends to make others shy from using this. To produce graphene with the greatest surface area and nearly defect-free an expensive bottom-up technique such as chemical vapor deposition, total organic synthesis or epitaxial growth is needed to synthesize graphene (Lee et al., 2019). Three innovative routes for low-cost graphene bulk manufacturing have been created, using graphite oxide, liquid-phase exfoliation and an electrochemical route (Zhong et al., 2015). This paper aims to review the current innovative uses of these nanomaterials as carbon composite reinforcements. These nano-reinforcements offer to strengthen the mechanical and physical properties of CFRPs composites. The paper also seeks an in-depth analysis of the material synthesis process and processing strategies utilizing polymer composites along with their applications.
In the advanced composites sector, continuous fiber-reinforced composites play a larger role than nanocomposites when it comes to mechanical qualities. The CFRP manufacturing process has multiple varying elements, of both chemical and physical inputs, which can affect things like surface quality due to coefficient of thermal expansion, wetting, etc. These defects can also contribute to various flaws in the composite laminate. Moreover, the failure modes found in composites are considerably more complex. It depends on the types of loads, physical qualities, and element microstructures. (Talreja, 1994). Typically, the failure mechanism of polymer composites is a fully random process, with damage dispersed throughout the composites (Dzenis, 1996). Before the final catastrophic breakdown, damage accumulates and combines to form macroscopic cracking. Moreover, the types of failure in composite materials differ significantly from those of metals. Here, the failure was governed by the propagation and expansion of a single crack until catastrophic failure occurred. As depicted in Figure 1, FRP composites typically experience multiple types of failure over their lifetime, including fiber/matrix debonding, interlaminar delamination, fiber breaking, and matrix cracking (Dzenis and Qian, 2001).
FIGURE 1. Common modes of damage in a cross-layer composite include (1) fiber breakage, (2) matrix cracking, (3) matrix/fiber debonding, and (4) delamination.
Matrix cracking theoretically occurs when the polymer tensile stress exceeds the matrix’s ultimate tensile strength. Fiber rupture occurs when the normal stress exceeds the ultimate tensile strength of the fiber. Moreover, fiber/matrix debonding depends on interfacial bonding or strength parameters. Due to the fact that fiber reinforcement is a two-dimensional architecture, the out-of-plane mechanical properties (interlayer fracture toughness and shear strength) of typical laminated composites are significantly lower than the in-plane properties. Interlaminar fracture has thus been identified as the most catastrophic and severe failure mechanism in composite materials. Due to these limitations, considerable effort has been devoted to identifying the failure modes of FRP composites for applications that are superior and more plausible. In addition, recent advances in nanotechnology have provided a promising avenue for improving the chemical, thermal, electrical, and mechanical properties of CFRP composites. Mechanical parameters such as shear and flexural strength and interlaminar fracture toughness can be enhanced by incorporating nanomaterials into laminated composites. In practice, nanostructured materials can either replace the resins used to produce composites or integrate within the interlayers of resin sandwiching the composite plies. Nanoscale materials such as nanoclay, nanofilaments, and carbon nanotubes (CNTs) have been investigated for the reinforcement of composite materials (Dzenis and Qian, 2001; Wu, 2003; Wu, 2009). Among a variety of nanomaterials, electrospinning-produced continuous nanofilaments have garnered considerable interest over the past decade. ENFs offer distinct advantages over other nanostructured materials, such as carbon nanotubes and clay nanoparticles, including low-cost production, continuity, flexible material characteristics, and fiber diameter. In addition, an overview of nanofiber production through electrospinning and other techniques is presented in this article.
Standard one-dimensional nanostructure materials include organic and inorganic nanoparticles, nanorods, carbon nanotubes, polymer, and Carbon nanofibers. The division of these varying types of organic and inorganic nanofillers can be shown in Figure 2. Among the aforementioned nanomaterials, carbon nanotubes are the most studied for increasing the mechanical properties of engineering materials. Non-etheless, due to the many factors such as agglomeration and poor dispersion properties, increasing experimental data have projected growing uncertainties regarding the CNTs’ impact on the reinforcement of structural materials. In addition, the expensive cost of CNTs inhibits their widespread application in large structural components such as aviation or aerospace components. Clay nanoparticles are widely considered an evolution in terms of the reinforcing phase when it comes to innovative polymer nanocomposites. These nanoparticles can improve the stiffness, fracture toughness, and tensile strength of a wide variety of polymers (Subramaniyan and Sun, 2007). Since the first research in Toyota Inc., Japan, clay-reinforced polymer nanoparticles have found uses in numerous industries, including automobile components. However, an experimental study on fiber-reinforced polymer composites found that nanoparticles of clay have a limited effect on interlaminar fracture toughness because clay platelets are equivalent to strengthening fibers (Subramaniyan and Sun, 2008). Recent research has demonstrated that functionalized carbon nanotubes strengthen the interlaminar characteristics of FRP composites (Sager et al., 2011) and electrospun polymer nanofibers (Wu, 2009) can be utilized. There has been no prior study on the interfacial toughening/strengthening of woven fabrics/epoxy structures made using electrospun thermoset CNT/epoxy nanofibers. As a result, we are very interested in employing the low-cost continuous nanofibers electrospinning technology to improve the mechanical characteristics of FRP composites.
FIGURE 2. Different types of nanofillers (Ehsani et al., 2021).
Carbon is an incredibly versatile and resourceful chemical that can be used in most scientific situations and applications. Carbon can diverge into many different allotropes with varying properties and configurations (Zhang and Jiang, 2018). One allotropes that has been garnering much attention are carbon nanotubes (CNTs). In fact, many researchers have explored the potential of integrating CNTs into carbon fiber. A comprehensive table displaying many of their results can be shown in Table 1. It is well known that the base chemical structure of carbon consists of a one-dimensional (1D) layer of graphite, and when these layers are oriented in such a way that they “roll” onto each other, they form a cylindrical tube-like structure. When only one layer of graphite is rolled, it is called a single-walled carbon nanotube (SWCNT), and multiple layers of graphite form multi-walled carbon nanotubes (MWCNTs) (Ahmad, 1999). The diameters of these cylindrical tubes typically range within the nanometer range, more than a billionth of a meter, and several microns in length. Research has shown that these tubes can reach diameters as narrow as 4 Å, the lowest it can theoretically be, while remaining energetically stable (Qin et al., 2000), and these small diameters have elevated CNTs into a prominent role within the composite industry. However, relative to graphite powders and soot products, the manufacturing costs of these nanomaterials remain a hindrance for its usage within the manufacturing industry (Hammel et al., 2004). Despite this, the outstanding properties that CNTs offer, branches the gulf of price and usability. Kamae and Drzal (2012) showed the development of carbon nanotube coated carbon fibers and the evaluation of their adhesion. A carbon fiber bundle was dipped into the solution, then squeezed and dried, obtaining MWNT/polyelectrolyte coated CF, which was then evaluated. As a result, the use of repulsive forces between the polyelectrolyte-treated MWNTs achieved a good dispersion of the MWNTs in water. Using the charge differential between the MWNTs and CF resulted in a uniform coating of MWNTs to the CF, also resin sizing and the MWNT coating combined resulted in good adhesion to the epoxy matrix. Incorporating MWNTs at the CF/matrix interface resulted in improved mechanical properties, such as shear modulus and strength, increasing stress transfer, and subsequently IFSS. Also, using PEI as a cationic polymer caused high interfacial shear strength (IFSS), given the strong interaction between its amine groups and epoxy groups. The novelty of the experiment and research in this paper is to be able to coat CFs with CNTs by a process in which the CF is dipped into a water/CNT suspension.
TABLE 1. Summary of mechanical properties improvement of carbon fiber-epoxy composite by carbon nanotubes.
In another study of manufacturing and characterization of carbon fiber/epoxy composite prepregs containing carbon nanotubes, it was shown that Epoxy was added to the CNT/acetone solution, mixed by ultrasonication, and degassed in a vacuum oven to remove acetone completely (Siddiqui et al., 2011) as shown in Figure 3B. To further disperse the CNT, a shear speed mixer was used. To select the optimal matrix material and prepreg parameters, four types of resin blends were studied, 0 wt%, 0.5 wt%, 0.7 wt%, and 1.0 wt% CNT. The viscosity changes were measured, and the effects of shear mixing speed, type of epoxy, and CNT functionalization were evaluated. Also evaluated were the effects of CNT on curing during the prepreg process. The study concluded that increasing the CNT content in the epoxy resin increased its viscosity. Such viscosity was lowered by using high-speed shear mixing and functionalization of the CNT. It was also concluded that the adverse effects of the higher viscosity could be mitigated by increasing resin temperature, fiber tension, and the exit dies gap of the prepreg. Also, the catalytic activity of surfactant treated CNT only became prominent at a CNT content of 1.0 wt%. The novelty of this study was to analyze how resin type and CNT content would affect various parameters in the whole prepreg process. The preparation of continuous carbon nanotube networks in carbon fiber/epoxy composite was shown in another work (Dong et al., 2014) as shown in Figures 3C, D. The materials used were polyacrylonitrile-based carbon fiber, plain cloth woven in a 0°/90° satin-weave. A CNT paste was used, with a CNT, water, polyvinyl pyrrolidone dispersant, weight ratio of 5:95:1, and CNT diameter between 10 and 30 nm and length between 1 and 5 µm. A glycidyl epoxy resin was used with a methylnadic anhydride curing agent. The mix ratio of curing agent to epoxy was 135 to 100 g. The CNT paste was diluted using deionized water, with concentrations of 1 wt% to 2 wt%. The CF fabric, fixed by glass slides, was immersed into this solution under a vacuum, then dried by freeze-drying, followed by heat-treatment under an argon atmosphere. Liquid epoxy resin was introduced into three types of CF and cured. The process resulted in a significant increase in the electrical conductivity of the composite. It is also stated that an appropriate CNT network could increase the interlaminar shear strength of the composite. The study assesses that the process in question is expected to provide a new method to optimize the CNT dispersion rate in fiber fabrics and composites. The novelty of this study is the use of the freeze-drying method in the preparation of continuous CNT networks, and how feasible the process would be.
FIGURE 3. (A) Examples of anticipated property enhancements of CFRP due to CNT incorporation; (B) schematic of prepregger (Siddiqui et al., 2011), (C) Dispersion state of carbon nanotubes in fiber/epoxy composites: primarily in interface and matrix, demonstrating CNT morphology between fibers before (upper) and after (lower) epoxy was introduced into fabric (Dong et al., 2014). SEM images of unsized carbon fibers, displayed on top, and untangled vs aligned MWCNTs displayed on the bottom respectively (De Greef et al., 2011).
The effect of carbon nanotubes on the damage development in carbon fiber/epoxy composites was shown in another work (De Greef et al., 2011). The materials used in this study were a balanced carbon twin 2/2 fabric, with an areal density of 300 g/m2, woven from 6 K yarns of AS4C GP carbon fiber. A CNT modified resin was used, based on liquid Bisphenol-A epoxy resin, with a high concentration of NC 700 multi-walled carbon nanotubes. The CNTs have an average diameter of 9.5 nm. The no-CNT composites utilized Epikote 828LVEL epoxy and 1,2-diaminocyclohexane Dytek DCH-99 hardener. The experimental methodology utilized consisted of three steps. The first step consisted of tensile static tests and acoustic emissions registration. The second step focused on identifying characteristic thresholds of damage from the first step. The third step investigated the damage patterns by using X-ray and SEM. The results of the study showed no improvement of the young’s modulus in the fiber direction, but a slight improvement in strength (3.1%) and strain-to-failure (4.6%). An improvement in the three damage development thresholds (ɛmin, ɛ1, ɛ2) 30%, 42%, and 56% were observed, as well as a reduced number of medium energy events and an increase in low energy events in non-engineered fiber reinforced composites (nFRC). A reduced density of transverse cracks was also observed (15.7%–10%), but isolated debonded fibers were found. The novelty of this study was the use of acoustic emissions as a method to investigate the effects of CNTs on transverse cracking in nFRCs.
One study found that controlling the orientation and length of carbon nanotubes grown on carbon fibers increased the interfacial strength of carbon fiber/epoxy composites (Lv et al., 2011). The materials used were carbon fiber based on polyacrylonitrile with a high modulus and an average diameter of 7.5 m. Thermal treatment at 800°C in the presence of argon yields CFs without dimensions. A matrix of bisphenol-A epoxy resin was utilized. ICVD in a reactor corundum tube furnace was the method for the growth of MWCNTs on CFs. To align the MWCNTs on CFs, the surface of the CNTs was treated by immersing them in toluene containing 5% tetraethoxy silane and 5% silicon tetrachloride. The CFs were coated with a solid SiO2 layer after hydrolysis and pyrolysis. The chemical composition before and after the treatment was characterized using X-ray photoelectron spectroscopy. SEM and TEM were used to analyze the properties of the MWCNTs and surface-modified CFs. The surface characteristics of unsized CFs and MWCNT-CF hybrids were determined by nitrogen absorption, and the wettability of such hybrids with epoxy resin was measured in a drop-on-fiber system using the generalized drop length-height method. The tensile strength of each fiber was measured using a WDW-50/100 Microcomputer-Control Electronic universal Testing Machine to determine the effect of CNT growth on axial properties. In addition, single fiber fragmentation tests were conducted to evaluate the fiber/matrix interface. The MWCNT-CF hybrid increased the specific surface area by two orders of magnitude, according to the study’s findings. The contact angle test demonstrated excellent wettability. Depending on the orientation and length of the MWCNT arrays, the IFSS improvement between the MWCNT-CF and the epoxy resin varied. With MWCNT arrays measuring 47,2 m in length, the IFSS was enhanced by as much as 175 percent. The novelty of this study was the analysis of IFSS in MWCNT-CF hybrids based on the orientation and length of the CNTs, as well as the analysis of the hybrid’s physical properties.
The interfacial enhancement of carbon fiber/epoxy composites has been investigated utilizing a simple approach for depositing commercially functionalized carbon nanotubes on the fibers (Li et al., 2013) as shown in Figure 4A. The materials used for this study were two types of carbon fiber, T700SC yarns of 1200 filament count (7 µm diameter, circular cross-section), and T300B yarns of 3000 filament count (7 µm diameter, irregular circular, or elliptical cross-section). Both have a sizing content of 1 wt%. Two types of MWCNTs were used, MWCNTs functionalized with carboxylic acid (COOH-CNT) and functionalized with hydroxyl groups (OH-CNT), with lengths varying from 0.2 to 2 μm, and diameters between 20 and 40 µm. For the matrix, a diglycidylether of bisphenol A based epoxy resin (YD-128) was used, as well as a polyether amine-based hardener (EC301). The preparation process began with the CNTs being dispersed in de-ionized water, obtaining a concentration of 0.05 wt%. After, the CF bundles were immersed in a bath with the CNT suspension, then dried at two different temperatures. The CNTs in suspension had their structures examined by a TEM. Another suspension was prepared to contain a non-ionic surfactant polyoxyethylene octyl phenyl ether to increase CNT content. TEM and FTIR were used to observe the dimensions of functionalized CNTs and to confirm the functional groups on the surface respectively. With the CNT-depositing completed, the bundles were examined by an SEM, to evaluate the adherence of CNT onto the fiber surface. Surface roughness was determined by an AFM. To test the dynamic contact angle and determine wettability, the modified Wilhelmy plate method was used. FTIR was also used to confirm if the functionalized CNTs can react with the industrial sizing of CF. Single fiber-composite fragmentation was used to assess the influence of CNTs on the interfacial bonding by testing its IFSS. The results of the study show that the CNT deposition process improved the interfacial shear strength of the composite. It also showed that the increased interfacial bonding between the CNT-hybridized carbon fiber and epoxy matrix is due to the interfacial friction, chemical bonding, and resin toughening near the interphase. There were also improvements in the tensile strength and interlaminar shear strength of the composite.
FIGURE 4. (A) Schematic of the CNT-depositing process on carbon fibers (Li et al., 2013), (B) Schematic of manufacturing sized carbon fiber (Yao et al., 2015) and (C) The molecular structure of the trifunctional epoxy resin TDE-85 and the amine curing agent DDM (active functional groups are represented by circles) with the CNT-COOH and the CNT-NH2 groups (Zhang et al., 2019a).
The novelty of the study is the use of evaluation methods such as investigating IFSS, focusing on the interfacial reinforcing mechanism, effects of CNT depositing on fiber surface morphology, wettability of epoxy on fiber, chemical bonding, and fracture pattern to improve the interfacial strength between CNT-deposited CF and epoxy matrix. Improving interfacial and mechanical properties of nanotube-sized carbon fiber/epoxy composites as studied (Zhang et al., 2019a) in Figure 4C. The study utilized materials that were unsized, commercial JH-T800 carbon fiber, with an average 5 µm diameter and sizing content of approximately 1 wt%. Multiwalled carboxyl-functionalized CNT (MWCNT-COOH) with 10–30 µm diameter and MWCNT-NH2 CNTs were used. For the matrix, a diglycidyl ester of aliphatic cyclo tri-functional epoxy, with 4,4′-diaminodiphenylmethane curing agent was used. The samples were prepared by dispersing both MWCNTs in the sizing agent at 0.5 wt%, then immersing the CFs in the solution for a set time, followed by drying it. Both single fiber and unidirectional composite samples were created (average volume fraction of CF of 60%). Dimensions and chemical composition of functionalized CNTs were observed by a TEM and XPS respectively. Fracture morphology and CF surface were analyzed via SEM, and surface roughness was determined by an AFM. To evaluate the IFSS of single fiber composites, single fiber fragmentation tests were performed under shear loading. For unidirectional composites, interlaminar shear strength (ILSS) and flexural properties were tested by a universal testing machine. A model was created to investigate the relationship between components, structures, properties of the system, and the effects of functionalized CNTs in the sizing agent. The MD simulations were conducted using Material Studio 6.0 Software. The interaction and interfacial bonding energy, mean-squared displacement, radial distribution function, and relative concentration were calculated using different equations. The results of this study showed that CNT-COOH-sized CFs had a significant performance improvement of 10%, 27%, and 59% in the IFSS, ILSS, and flexural strength respectively when compared to commercial CF. CNT-NH2-sized CF showed adverse effects on IFSS and ILSS and a smaller improvement in flexural strength when compared to CNT-COOH-sized CF. The interfacial bonding between fiber and matrix still needs to be clarified. The novelty of the study is the use of experiments and simulations to investigate and detail the mechanisms of different functionalized CNT-reinforced composites on the surface of CFs, and their effects on the molecular structure of the matrix and the properties of the composites.
Another study was conducted on interfacial and mechanical improvement of carbon fiber/epoxy composites by depositing multi-walled carbon nanotubes on fibers (Xiao et al., 2018). The materials used in the study were a monodirectional carbon fiber fabric, S-MWNT-1020, with a 0.5–2 µm length, 10–20 nm diameter, and a purity greater than 97%. E-44 epoxy resin (0.44 mol/100 g epoxy value), and a D-230 polyether amine curing agent were used. The MWCNTs were dispersed in de-ionized water by ultrasonication to obtain a CNT suspension of 0.1 wt% concentration. CF fabric was immersed in the suspension, for a set time, then dried at two different temperatures. The sample laminates were prepared by compression molding. After deposition, the CF fabric was torn apart and examined by a SEM to evaluate CNT/fiber adhesion. Tensile strength and modulus were measured by the electronic universal machine, as well as a three-point bending test. ILSS was also tested. The test specimens had their mechanical properties tested after being placed in sealed plastic bags with distilled water at a certain temperature for 24 h and dried. The heat resistance was measured by DSC, and the micromorphology of the fracture surface was examined by SEM. The results of the study showed an improvement in the interfacial interaction and interfacial bond strength between MWCNTs-T300 and EP, and a reduction in the contact angle (40.3°). The interfacial energy and adhesion work were increased by 49.5% and 4.7% respectively, compared to original T300 fiber. The mechanical properties of MWCNT-T300/EP laminated composite also improved. Flexural strength, tensile strength, and interlaminar shear strength increased by 15.1%, 17.6%, and 12.6% respectively. After CNT deposition, the (MWCNT-T300/EP) composite interfacial strength is improved. The novelty of the study was using an aqueous suspension deposition method to coat CF with MWCNTs to improve interfacial and mechanical properties, evaluating surface morphology, wettability, and interfacial properties, as well as testing mechanical properties.
Preparation and characterization of carbon nanotube-hybridized carbon fiber to reinforce epoxy composite has been explored (An et al., 2012). The materials used in the study were an unsized polyacrylonitrile-based carbon fiber, analytical grade reagents of ferrocene and acetone, E-51 epoxy resin consisting of diglycidyl ether of bishenol-A, and phthalic anhydride and benzyl dimethylamine as curing agents. The preparation of the CNT-hybridized CF happened in a single zone horizontal quartz tube furnace, using acetylene (carbon source), ferrocene and a H2/N2 carrier gas mix. CFs were placed at the center, and a pure nitrogen atmosphere was created. At 700°C, Ferrocene-acetone introduced, and an aerosol is formed, ferrocene is decomposed into catalyst, depositing onto CFs. At 750°C, C2H2 is introduced, and CNT growth starts. After a set time, carbon source stops being fed, and power is turned off to allow for cool down. Both a monofilament of CNT/CF hybrid composite and multifilament unidirectional CNT/CF hybrid composite were created. SEM and high-resolution transmission electron microscopy were used to characterize the morphology and microstructure of the CNT/CF hybrid. BET method and an absorption instrument were used to calculate the specific surface area of CF and CNT/CF hybrid. Single fiber tensile tests were conducted using a tensile testing machine, with an optical microscope being used to measure each specimen’s diameter. To calculate IFSS, single fiber pull-out tests were conducted using an interfacial micro-bond evaluation instrument. Using a universal testing machine, the tension fracture for the cured epoxy composites was performed, and the morphology and structure of the fractured section were evaluated by a SEM. The results of the study show that grafting of CNTs on the CF surface resulted in a near threefold increase in BET surface area. The CF’s tensile modulus remained similar while tensile strength had an approximately 10% decrease. Interfacial shear strength increased by 94%. The presence of CNTs resulted in different fracture morphology of the composite. There was an increase in fiber surface area, providing a stronger interfacial bonding between the fibers and matrix. The novelty of the study is the use of a newly developed aerosol-assisted chemical vapor deposition method to create CNT/CF hybrid composites by using several methodologies and instruments to evaluate the material.
Optimization was done for interfacial microstructure and mechanical properties of carbon fiber/epoxy composites via carbon nanotube sizing (Yao et al., 2015). The materials used in the study were short hydroxyl MWCNT of 95% purity, length of 0.5–2 μm, and -OH content of 1.76%, T700S carbon fibers, JC-02A modified epoxy, JH-0511 modified 2-ethyl-4-methylimidazole accelerant, and a tetrahydro phthalic anhydride curing agent. To remove the commercial sizing and help CNTs obtain a dispersion in the small inter-fiber-spaces of CF bundles, CFs were refluxed by acetone. The CNTs were dispersed in ethyl alcohol and sonicated for 2 h forming a suspension. The CF is then sized with a self-made device, passed through the sizing agent suspension, wound up on a roller and dried. The content of CNT on fiber surface was controlled by number of sizing treatment. Unidirectional CF composites with volume fraction of 45% were made. A SEM was used to detect CF surface topography and the fracture surface of composite specimens. A universal testing machine performed a short beam shear test and a flexural test to assess the influence of the sizing process on interfacial properties. Composite interfacial microstructures were investigated using EDS-equipped SEM and f-AFM. SEM for the distribution of carbon elements in the interference layer of composites and f-AFM for the distribution of modulus. The results of this study indicate that the sizing deposition method is a simple and continuous technique for producing CF/CNTs/epoxy composites on an industrial scale. In addition, a gradient transition interphase was discovered, allowing for the possibility of uniform stress transfer. In addition, it was discovered that a uniform CNT distribution on a CF surface caused the interface thickness of the composite’s gradient structure and mechanical properties to increase gradually as the sizing treatment time increased. Interlaminar shear strength and flexure strength increased by 13.45% and 20.31%, respectively, in a quintuple-sized CF with a wider gradient interphase. However, excessive sizing will result in diminished mechanical properties. This study investigates the novel aspects of incorporating CNTs via a multi-sizing process into the interfacial microstructure and its relationship to composite performance.
Graphene has often times been added to CF/epoxy composite materials to improve their mechanical and electrical properties (Hadden et al., 2015). This is possible due to it being a single-layered two-dimensional allotrope of carbon, which grants it greater properties than flax fibers like CNCs. Graphene, outside of its pristine form, has two main derivatives within the composites industry, graphene oxide (GO) and reduced graphene oxide (rGO). Other form of graphene that have been researched are graphene nanoribbons (GNR) and graphene oxide nanoribbons (GONR) (Chien et al., 2015). Graphene fibers have also been explored as a potential substitute for carbon fiber, due to their large lateral crystal size. This allows it to potentially have greater mechanical, electrical, and thermal performance (Xu and Gao, 2015; Xu et al., 2016).
The use of graphene as a nanofiller, specifically graphene oxide (GO) has caught the attention of many researchers throughout the world. Researchers like Aduk et al. investigated the effects of the mechanical properties of carbon fiber with incorporated GO (Adak et al., 2018). To create the GO, graphite flakes were dispersed in THF at concentrations of 0.05 wt%, 0.1 wt%, 0.2 wt%, and 0.4 wt%. The GO/carbon fiber composites were created using the VARTM process. Through testing, a maximum of 0.4 wt% GO was used, but the best results were found at 0.2 wt% GO. Tensile testing results show an increase of 33.8% in tensile strength, a 19.7% increase in Young’s modulus, and an 83.1% increase in toughness. While both the flexural strength and modulus testing showed increases of 35.7% and increases of 31.3% for flexural modulus. This is similar to the results found by Wang et al. where desized carbon fibers and GO were made using carbon fibers and natural graphite flakes to increase the overall strength of the carbon fibers (Wang et al., 2017a). D400, concentrated nitric acid, a coupling agent (HATU), and deionized water was also used to create the GO mixtures. To facilitate separation, the GO suspension was placed in a burette. The solution at the bottom was labeled GO-1. The remaining solution was separated, centrifuged, then divided into GO-2 and GO-3 subgroups. The preparation of these materials can be visually shown in Figure 5A. SEM, TEM, and AFM were utilized to determine the structure, roughness, and thickness of the GO sheets. XPS analysis revealed a greater concentration of oxygen functional groups. The FTIR analysis revealed that amino groups were incorporated into the carbon fibers and that GO was covalently bonded to them. Dynamic contact angle tests performed to determine wettability revealed an increase in the surface free energy. Tensile strength tests revealed an increase in tensile strength from 4.72 GPa to 5.02 GPa when compared to GO-2 sheets. IFSS testing revealed an improvement in compressive strength from 46.8 MPa for untreated carbon fibers to 82.2 MPa for GO-2 sheets. This group developed a method for grafting GO onto carbon fibers that was simpler and more environmentally friendly than previous methods. Their methodology made use of fewer resources and chemicals. Additionally, the separation of the GO solutions is time-consuming and results in lower quantities of each solution. In a study by Altin et al. (2020) an advanced Hummers technique was used to rectify this issue.
FIGURE 5. (A) Grafting of size-controlled graphene oxide sheets onto carbon fiber (Wang et al., 2017a), (B) The functionalized progress of carbon fiber (Zhang et al., 2016), (C) surface treatments on the interfacial adhesion of graphene oxide/carbon fiber/epoxy composites (Yuan et al., 2018) and (D) Preparation process of prGO, CF-PEI, CF-PEI-GO and CF-PEI-prGO (Wu et al., 2022).
In this study, the production of GO was accomplished using this enhanced Hummers technique, where spraying 5, 10, and 20 ml of GO onto three samples produced 0.5 wt% GO/CF, 1 wt% GO/CF, and 2 wt% GO/CF, respectively. The FTIR study demonstrated that graphite was successfully oxidized by Hummers’ technique and that oxygen functional groups were grafted. In mechanical tests, the 2 wt% group had the greatest gains in young’s modulus and tensile strength at 23.5% and 54.1%, respectively. Calculations using TGA revealed that the thermal stability of the samples reduced as the amount of GO increased. This modification process of spraying GO has shown to be efficient and cost-effective as this process was successful in coating carbon fibers with GO and improving mechanical properties. When researching GO, the use of diamines has been scarcely explored, but Ashori et al. (2015) researched ways to enhance the properties of carbon fiber and GO through functionalization with three diamines. In his investigation, GO was functionalized in three ways: first with ethylenediamine (EDA), then with 4,4′-diaminodiphenyl sulfone (DDS), and finally with p-phenylenediamine (PPD). The graphene oxide was made with, 1 g graphite powder, combined with 18 ml H2SO4, 9 ml HNO3, and 11 g KClO3. GO and functionalized GO/CF (FGO/CF) were added at concentrations of 0.1 wt%, 0.3 wt%, and 0.5 wt%. This combination was oxidized, washed, and then dried in a vacuum. The fibers were orientated at 0°, 90°, and 0° angles via hand lay-up. FTIR analysis revealed that GO contains oxygenated functional groups as well as functional groups containing EDA, DDS, and PPD. Tensile testing revealed increases in tensile strength with 0.3 wt% of each concentration showing the greatest rise, specifically PPD-FGO showing the highest increase of 22.5%, while flexural strength increased by the greatest amount, 76% when 0.5 wt% PPD-FGO was used. While GO has been used to improve the mechanical qualities of CF, the use of three differing diamines is a unique solution to increasing CF properties, but once again the long preparation time hinders its usage.
In another study, Yuan et al. (2018) reviewed the results of GO engaging in oxidative pretreatment and non-oxidative pretreatment before electrophoretic deposition (EPD) to enhance CF properties. As shown in Figure 5C, CF went through surface modifications of acid treatment oxidation, sizing treatment, APTES coupling agent treatment, and electrochemical oxidation. The EPD was completed using CF as the working electrode and a graphite plate as the counter electrode. Four samples were produced as GO/CF-Acid, GO/CF-Sizing, GO/CF-APTES, and GO/CF-ECO. Composite laminates were then combined with each sample and produced using VARTM method. SEM and AFM analysis showed overall increased surface roughness and added topography, but the APTES group showed a lower Ra value than untreated CF. Interfacial shear strength testing showed the highest increase of 50% by the GO/CF-ECO sample. The goal of Yuan et al. (2018) was to show the effects of surface pretreatments of CF when combined with EPD of GO, and overall, this process was successful.
Another successful and novel process was completed by Han et al., 2017 who for the first time, used GO combined with the organic solvent THF to boost the ILSS of CFRP. A modified version of the Hummer process was employed to create GO, which was then ultrasonically treated. The GO was then disseminated in the epoxy resin with the aid of. 0.05 wt%, 0.1 wt%, 0.2 wt%, and 0.4 wt% THF, after which, the cured resins were then painted on carbon fiber textiles. The FTIR and XPS analyses confirm that GO contains a wide range of functional oxygen groups. AFM image reveals a GO sheet thickness of 2–4 nm. When GO levels were low, TEM pictures revealed good dispersion of GO within the matrix, however substantial aggregation of GO layers was observed when GO content increased. After mechanical testing, the ILSS rose by 8.05% at 0.10 wt%, relative to epoxy samples without modifiers. Researching the use of GO and THF increased the ILSS of CFRP successfully while creating sheets that were thin and evenly spread when the weight percent was low, despite the novelty of this solution. Additional research aimed to do the same increase the mechanical properties of carbon fiber through GO (Pathak et al., 2016). Here, GO is added into the matrix using a wet transfer procedure to increase ILSS and bending strength by varying GO weights. The GO was produced using the Hummer’s technique, and then washed in 5% HCl. The cleansed solution was then dried in an oven to generate GO flakes. Seven concentrations of CO content were created ranging from 0.0% to 0.6 wt% GO and tested. The creation of said concentrations can be seen in Figure 6C. The greatest increases were observed at 0.3 wt%, after which, increases were affected at higher GO concentrations due to agglomeration. ILSS in samples containing 0.3wt% was found to have increased by 25%, with the flexural strength and modulus improved by 66 and 70 percent, respectively. Despite using conventional methods like the wet transfer method, increases in the mechanical characteristics of the material were achieved.
FIGURE 6. (A) Fabrication of CF/GNP/Epoxy nanocomposites (Kim et al., 2020), (B) r fabrication of graphene interleaved CF/E composites (Du et al., 2017), (C) introduction of GO into epoxy matrix to form GO reinforced epoxy-carbon fiber hybrid composites (Pathak et al., 2016) and (D) Fabrication process of GO/carbon fiber reinforced epoxy composites (Han et al., 2017).
The same can be said in another attempt to raise the IFSS of carbon fiber by Jiang et al. (2017) in which, GO was disseminated into sizing agents at concentrations of 0, 0.2, 0.5, 1, and 2 wt%. After preparing a sizing agent with a GO concentration of 2 wt%, the mixture was combined and placed onto the carbon fibers. The SEM images of the CF samples revealed that the amount of GO sheets increased as the GO level rose, but as the wt% reached 2%, agglomerates were observed. Single fiber pull-out experiments were conducted to determine the IFSS of each concentration, with the highest value found at 1% GO at 110.3 MPa, an 37.2% increase in strength. When determining impact resistance, this concentration also gave the highest increase at 79.16 kJ/m2, an increase of 45%. At 1 wt%, results were maximized, demonstrating the potential for enhancing IFSS by modifying GO sizing agents. Due to the great importance delamination can cause studies were also conducted to increase failure mode resistances (Du et al., 2017). GO was produced from graphite powder using a modified version of Hummer’s procedure. Figure 6B visualizes the creation of CF composites, where graphene powder was disseminated in acetone and epoxy was subsequently added. Single-edge notched bend (SENB) tests were used to quantify fracture toughness. The sample with the biggest gain, 74%, was the 1.0 wt% sample as mode one interlaminar fracture energy was enhanced by 145% with this percentage. The same could be said concerning the samples’ thermal characteristics, as samples containing 1.0 wt% exhibited a 30% drop in thermal expansion coefficient. In this investigation, the thermal reduction method of creating GO proved effective. The mechanical properties increased the most and the thermal coefficient decreased the most at a concentration of 1.0 wt%. It is also of utmost importance that the properties of carbon fiber with GO are known in most environments. Qu et al. (2020) at 77 K, studied the cryogenic flexural characteristics of CFRP by augmenting the material with different percentages of graphene oxide. Graphite granules were oxidized with acid to produce GO at concentrations ranging from 0 to 0.5 wt%. The graphite was disseminated in deionized water, subjected to sonification, dried, dispersed in acetone, and subjected to sonification once again, to finally be incorporated into epoxy matrices and carbon fiber. AFM images determined the thickness of GO nanosheets to be between 0.5 and 1 nm, with XRD examinations reaffirming that GO effectively formed layered sheets. FTIR revealed the functional groups responsible for GO’s effective dispersion in the matrix. Three-point bending tests were executed and 0.2% GO was the best-performing sample, with gains in flexural strength, flexural modulus, and ILSS of 6.4%, 9.6%, and 17.6%, respectively, at room temperature. At 77 K, these increases were 4.9%, 7.1%, and 8.7% respectively. While the biggest property enhancements were observed in samples at ambient temperature, the 77 K sample increases were significant and demonstrate evident application benefits in cryogenic environments. Despite determining the mechanical properties of carbon fiber at extreme temperatures, other methods shown in this paper have demonstrated greater increases in room temperature, and this study could benefit from employing these approaches.
Other forms of graphene have been explored and used as nanofillers as researchers looked at additional ways to stretch our knowledge of graphene’s effect on carbon fiber. Graphene nanoplatelets (GNP) are one of such forms. A study by Hawkins and Haque (2014) investigated the fracture resistance of carbon fiber-reinforced epoxy when reinforced with GNP. Before testing, G-Ep and C-G-Ep were manufactured using 0.1 wt% graphene, in which G-Ep was formed by mixing graphene nanopowder and acetone, followed by combining it with epoxy resin, heating it, and curing it. Other G-Ep samples with differing graphene concentrations were created without the use of acetone or high shear mixing, creating three samples: Carbon-epoxy (C-Ep), graphene-epoxy (G-Ep), and carbon-graphene-epoxy (C-G-Ep). Using SEM, the roughness of the fiber surfaces in G-Ep was found to be greater than in neat epoxy. This suggests increased fracture resistance. Three-point bending was used and verified that the fracture toughness of G-Ep rose by 128% relative to carbon fiber epoxy itself. As shown in this study, incorporating 0.1% graphene nanoplatelets significantly increased fracture toughness, which could be further improved. One improvement, suggested by the authors, was to improve the method of graphene dispersion to reduce graphene aggregation and enhance its mechanical characteristics. Another reason for GNP usage is its ability to be functionalized. Hence the usage of Poly (4-amiostyrene) (PAS) to non-covalently functionalize GNPs, was utilized by Kim et al. (2020) to boost fracture toughness and ILSS in CF composites. For the preparation of functionalized GNPs, PAS was dissolved in DMF, and GNPs were then added. These GNPs were subsequently dissolved in acetone and epoxy resin was applied for curing on CF. SEM imaging revealed that PAS-GNPs were uniformly dispersed inside the epoxy matrix, whereas GNPs without PAS exhibited aggregation. As a result, PAS-GNPs were able to further boost mechanical characteristics. This was verified when the ILSS of 4 wt% PAS-GNPs was raised by 252% and fracture toughness was increased by 142%. The use of functionalized GNPs and the application of PAS, permitted a more uniform dispersion in the matrix at high wt%. This resulted in a significant enhancement of mechanical characteristics.
In fact, Qin et al. (2015) allowed CFs to be coated with GNPs utilizing a continuous coating technique to evaluate 90° and 0° flexural strength as well as ILSS. SEM imaging revealed a homogeneous coating with additional roughness on the fibers. The flexural strength of GNP-coated CFs was 82% greater than that of uncoated CFs when tested at 90°. 0° testing revealed a 7% increase. Compared to uncoated CFs, the ILSS increased by 19%. GNPs have also been researched and their properties explored virtually (Hadden et al., 2015). The GNP molecules were modeled using molecular dynamics (MD) and micromechanical modeling. This studies the mechanical impact of adding graphene nanoplatelets (GNP) to carbon fiber and epoxy composites. The molecular structure of GNP layers was modeled, and their mass density was analyzed. To validate their findings, experimental tests were conducted. Neat epoxy used 100 g of EPON 862 with 26.4 g of EPIKURE, the curing agent. GNP/epoxy used an “appropriate amount” of GNP mixed with EPIKURE and was incorporated into carbon fiber via a winding process. This GNP/epoxy/carbon fiber composite was cut into sheets and then cured. Mechanical testing was then completed to determine the tensile strength, elastic modulus, and normalized modulus for this material. This analysis outlined the potential for computational multiscale modeling of GNP/epoxy composites to predict elastic properties. Overall, it can be concluded that the method developed is accurate and can provide insight into mechanical behaviors, despite some discrepancies between the model and experimental data.
Other alternatives to graphene oxide are porous graphene oxide (prGO), silanized graphene oxide (SGO), and reduced graphene oxide (RGO), with each showing similar increases in carbon fiber properties relative to GO, if not more. Chemical grafting and prGO were utilized by Wu et al. to increase the interfacial adhesion of CFRPs, in which the GO and prGO were grafted onto CFRP by means of a chemical process (Wu et al., 2022). After the prGO and GO solutions were prepared, SEM pictures were captured to investigate the new structure of the changed fibers. Due to the grafting of GO and prGO, the fibers exhibited ridges and enhanced roughness. XPS analysis revealed greater O/C ratios in prGO samples compared to GO samples, indicating that prGO includes more oxygen groups. According to contact angle studies, the surface energy of the modified fibers increased as the contact angles decreased. All these factors contributed to a 78.64% increase in the interfacial shear strength of fibers containing prGO, while GO demonstrated a gain of 48.54%. The innovation was the utilization of prGO to enhance the CFRP characteristics. As this modifier had never been done previously, the overall improvement was successful and substantial. SGO also displayed similar success, when it was formed in order to increase GO dispersion and adherence to epoxy (Chen et al., 2014). Here, graphene oxide was functionalized with silane coupling agents to form silanized graphene oxide (SGO). After soaking unmodified carbon fibers into modified epoxy mixtures, samples with carbon nanoparticle concentrations of 0.2 wt%, 0.5 wt%, and 1 wt% were obtained. AFM measurements revealed that GO and SGO have similar thicknesses, with SGO having a greater thickness on the fibers and the XPS study verified that the functionalization of GO to SGO was effective. The 0.5 wt% sample demonstrated greater gains in IFSS, ILSS, flexural strength, and flexural modulus during mechanical testing than the other sample groups, at increases of 60%, 19%, 15%, and 16%, respectively. Chen et al. were able to successfully functionalize GO with silane and increase carbon fibers’ mechanical characteristics, nevertheless, due to SGO’s lengthy curing time, this technique is not the most effective.
RGO offers potential as Jenkins et al. (2019) surveyed its enhancement of CFRP’s mechanical properties. Graphene oxide was manufactured using a modified and enhanced version of Hummer’s technique. A mixture of H2SO4 and H3PO4 was added to graphite powder and KMnO4, followed by 12 h of heated mixing. The cooled, rinsed, centrifuged, and then filtered mixture was then filtered into CFRP samples containing 0.1, 0.2, and 0.3 wt% RGO for testing, as shown in Figure 7B. The SEM images of RGO specimens revealed uneven, folding structures, which gave the composite stability, with TEM morphology confirming this. Flexural testing was conducted at -10°C, 23°C, and 40°C. The sample with the best performance was the 0.3 wt% set increasing the flexural strength by 62% and the flexural modulus by 44%. Overall, the objective of enhancing the CFRP’s shear and flexural characteristics, with RGO, was achieved between −10°C and 23°C. There were noticeable slight strength decreases at 40°C.
FIGURE 7. (A) Fabrication process of CF/E composite laminate with MWCNTs/GO hybrid (Rodríguez-González et al., 2018), (B) graphene oxide to rGO and epoxy/rGO composite (Jenkins et al., 2019) and (C) procedure for the fabrication of CF/Ag/GO (Wang et al., 2017b).
Another RGO study explored creating hierarchical composites for greater mechanical and electrical effectiveness (Li et al., 2016). In this case, RGO with help of tetrahydrofuran (THF), was dispersed into an epoxy resin and deposited into the CF interface. A modified Hummer’s method was utilized to produce GO. This was then reduced, washed, and dried to form RGO resin, which was deposited into the CF. Through mechanical testing, 0.1 wt% was determined to be the highest-performing sample. ILSS improved by about 10% in RGO compared to non-modified CF. IFSS was increased by 21% in RGO. Reverifying that RGO does successfully improve the mechanical properties of carbon fiber. Finally, laser-induced graphene (LIG) was used to enhance the fracture toughness of CF (Nasser et al., 2021). By using a 40 W CO2 laser, LIG arrays with vertical alignment were generated on polyimide substrates, and the LIG was then transferred manually to CF prepreg. Short beam strength tests revealed a 300% increase in toughness. Additionally, mode I and mode II fracture toughness increased by 41% and 69%, respectively. Through the study, there was an increase in shear strength, fracture toughness, and both crack initiation and propagation resistance increased.
Crossbreeding of graphene with other nanomaterials were also explored to identify their effects on carbon fiber. Rodríguez-González et al. (2018) did so by using mode one and mode two interlaminar fracture toughness and interlaminar shear strength measurements to study the effects of MWCNTs and GO combinations. Using unidirectional carbon fiber/epoxy prepregs, three distinct samples of MWCNTs, graphene oxide, and MWCNTs/GO were sprayed onto carbon fiber at a concentration of 0.25 wt% relative to pristine carbon fiber, then cured for testing. A double cantilever beam test was used to determine the mode I interlaminar fracture toughness, and an end notched flexure testing was performed on pre-cracked and uncracked samples for mode II fracture toughness. Short beam shear tests were used to determine the interlaminar shear strength. SEM images were used to further assess the results following testing. Using double cantilever beam testing mode one toughness rose by 11.5%, 8.1%, and 16.7% for MWCNTs, GO, and MWCNTs/GO respectively. The same can be said with Mode two non-pre-cracked MWCNTs increasing by 14%, 8.1%, and 17.6% along with ILSS was increasing by 3.5%, 3.0%, and 4.7% respectively. In this article, although the total increase in ILSS was not as large as in other research, improvements were observed.
Similar to Gonzalez, Kwon et al. (2017) also used GO combined with carbon nanotubes (CNTs) to enhance the mechanical and electrical properties within CFRPs. In this case, GO sheets were produced from graphite flakes. 0.01 wt% of multi-walled CNTs were mixed into distilled water with 0.0003 wt% GO sheets. EPD was then utilized to allow the new GO/CNT hybrid to be deposited on the carbon fabric. After sample fabrication, weight percentages of 0.01, 0.37, 0.61, and 0.65 of GO/CNT were reported. Mechanical results from short bean strength showed a decrease from 62 MPa to 55 MPa due to excessive coating between carbon fibers. Crack pattern analysis showed that the applied load was transferred to the fibers instead of the epoxy. Electrical studies showed an increase of about 1400% in through-thickness electrical conductivity. Overall, the paper saw successful results in the main category they were striving for. The electrical properties were greatly enhanced with the obvious decrease in mechanical properties tested.
Another test that garnered improvements used silver nanoparticles (AgNPs), where through efficient electrodeposition and electrophoretic deposition, AgNPs and GO were deposited onto the surface of CF sheets to enhance the interfacial shear strength and tensile strength of the carbon fiber (Wang et al., 2017b). The process started by desizing CF in refluxed acetone. AgNPs were prepared for electrodeposition with CF as the cathode, stainless steel as the anode, and a mixture of AgNO3 and PVP as the electrolyte. This deposition was completed through electrophoretic deposition at times of 10, 30, 60, and 90 s. The samples CF/AG/GO-10, CF/AG/GO-30, CF/AG/GO-60, and CF/AG/GO-90 were named with respect to their deposition times. SEM and TEM images confirmed that AG NPs and GO were successfully deposited onto the CF sheets. After this confirmation, tensile testing showed an increase of 36.8% in CF/AG/GO-60 compared to untreated CF. Interfacial shear strength was increased by 86.1% in CF/AG/GO-60 compared to untreated CF. This article verified that the use of nanoparticles and GO together was able to successfully fill in surface cracks of CF, increase wettability, and overall reinforce the composite. Other metals, like iron oxide (Fe3O4) and their effects on the micro-crack behavior of CFs were also studied (He et al., 2018). To prepare these fillers, solid GO was obtained after filtration and freeze drying, with the Fe3O4/GO being magnetically separated and washed. The two mixes were created by adding either GO or Fe3O4/GO to epoxy in a 0.5:75 ratio and curing with D-230 in a 1:3 ratio. Through vacuum-assisted resin transfer molding, an epoxy laminate was strengthened with carbon fiber. In comparison to pure GO, Fe3O4/GO exhibited a significant reduction in the adsorption peaks of oxygen functional groups, via FTIR. XRD readings revealed the formation of a Fe3O4/GO particle during decomposition. SEM and TEM pictures revealed that the majority of GO coated with magnetite microspheres was reasonably uniform and that their distribution was uneven in shape and exhibited some aggregation. Tensile testing at room temperature and 77 K revealed an increase in tensile strength for GO and Fe3O4/GO composites. GO increased tensile strength by 6.9 percent at room temperature and Fe3O4/GO raised it by 14.1 percent. At 77K, GO increased tensile strength by 12.1% and Fe3O4/GO by 18.1%, and both Young’s modulus and the percentage of failure strain increased as well. Fe3O4/GO also boosted fracture toughness and impact strength at 77K by 75% and 21.1%, respectively, as well as reducing the coefficient of thermal expansion by 51.6%. This research provides unique results by testing at different temperatures and this procedure was proven successful despite a lengthy and complicated process.
Zhang et al. (2016) also ran a lengthy experiment as this group investigated the impact of adding polyhedral oligomeric silsesquioxane (POSS) to multi-scale carbon fiber via graphene oxide (GO). Both the carbon fiber and GO were functionalized and prepared for use. Later, SEM images of carbon fiber were produced before and after the addition of GO, followed by GO-POSS. This showed the clear structural changes between unfunctionalized and GO-functionalized carbon fibers. This was confirmed with an atomic force microscopy (AFM), which was used to examine the topography and roughness of the carbon fiber. Additionally, X-ray photoelectron spectroscopy, thermogravimetric analysis, and dynamic contact angle testing were performed to detect chemical and contact angle differences between GO and POSS in order to ensure successful grafting. Mechanical testing was then used to determine increases in shear strength, and a considerable increase of up to 53.05% in the ILSS was demonstrated. The study is innovative in that it makes use of both GO and POSS concurrently. However, with a total processing time of 112.83 h for functionalizing the carbon fiber and preparing GO and POSS, the fundamental limitation of this work is its time impracticality. Finally, Tareq et al. (2019) examined the effects of introducing montmorillonites nanoclay (MMT), GNPs, and a hybrid MMT and GNP to CFs. To disperse MMT, a 2% nanoclay was dried and then mixed with epoxy resin. GNP dispersion occurred from various ultrasonication and mixing with epoxy resin. These two processes came together to form the hybrid composite. After material preparation, 0.1 wt% GNP samples showed the best results of increasing flexural strength while 2% MMT increased flexural modulus the most with increases of 21% and 28% respectively. Overall interfacial bonding was improved in all modified sample types and was confirmed by SEM. Although both GNP and MMT samples performed highest in different areas, the hybrid of the two, however, decreased flexural modulus by 5%. Table 2 below displays a culmination of the results discussed in this section. Showing graphene oxide used for carbon fiber optimization but with differing methods and results.
TABLE 2. Summary of mechanical properties improvement of carbon fiber-epoxy composite by graphene/graphene oxide.
Many studies aimed at increasing the interlaminar or interfacial fracture toughness of carbon fiber composites, specifically CFRPs with various nanomaterials. However, the high manufacturing and operating costs of using some of these nanomaterials have led researchers to study other cost-effective methods of creating stronger and more optimized composites. This has led to the creation of hybrid nanofillers, a fusion of two or more nanofillers that take on the properties of their constituents. A near-infinite number of these hybrid forms and concentrations can be created to construct stronger and more affordable components. In this section, some of these hybrids will be explored.
A key property that carbon fiber manufacturers aim to increase is the fracture toughness of these composites, to prevent delamination and ultimately, failure. Gabr et al. aimed to create tougher polymer matrix composites with epoxy resin, varying amounts of the nanomaterials bacterial cellulose, BC, (0, 0.5, and 1 wt%) and Carboxyl-Terminated Liquid Butadiene—Acrylonitrile (0, 10 and 20 wt%) or CTBN as enhancers for these composites (Gabr et al., 2010a). Initially, a decrease in young’s modulus and tensile strength was found for all eight combinations, relative to pristine carbon fiber with only 1% BC/10%CTBN having higher tensile strength. Non-significant increases in flexural strength and modulus were discovered. However, the initial and propagation experienced a significant increase of 84% and 72% counteracting the decreases in other mechanical properties. Gabr et al. also studied the effects of 0%, 0.5wt%, 1wt%, and 2wt% of microfibrillated cellulose (MFCs) as the reinforcement of an epoxy polymer matrix and plain-woven carbon fiber. Using the JIS K7073 and K7086 standards 2wt% MFC experienced the greatest increase in mode one interlaminar fracture toughness, crack initiation force, and glass transition temperature with increases of 44%, 80%, and 12°C respectively.
Researchers at Doshisha University conducted a comparative study also using BC and MFCs against CNFs to research their effects on fatigue life (Shao et al., 2015). The weight fractions of both BC and MFC were separated into 0, 0.3, and 0.8 wt% of the epoxy matrix and once the carbon fiber was laminated and cut, both mechanical and fatigue tests were analyzed via ASTM D3039-08 and ASTM D3479 standards for two million cycles. The high cycle fatigue life increased greatly for 0.8 wt% MFC and BC, by nearly 10–30 times for 0.3 wt% MFC. The effects of the nanofillers with the carbon fiber and epoxy adhesion were also realized due to a 76.9% increase in the interfacial shear strength. There was also an increased delamination resistance as the energy release ratio increased by 1.6 times. These results exemplify the use of nanofillers to produce significant increases in carbon fiber fatigue life and are scarcely found throughout the composite industry.
These same researchers also researched hybridizing 0, 0.5, and 1 wt% MFCs and 0, 10 and 20 wt% CTBN (Gabr et al., 2010b). In this study, the hybrid nanofillers incurred slight decreases in the young’s modulus, flexural and tensile strength, relative to pristine carbon fiber in all but one concentration. However, the mode one fracture toughness increased by 96% and 127% in both initial and propagation fracture toughness. These papers show the novelty of using other cellulose microfibrils like MFC and BC to create increases in fracture toughness, with little to no effects, on a carbon fiber composite’s mechanical structure. Another alternative cellulose that was explored is nanocrystalline cellulose (NCC) silanized by 3-aminopropyltriethoxysilane (AMEO) (Zhang et al., 2019b). Continuous coating was a method proposed by Zhang et al. as an inexpensive way to increase the interfacial properties of carbon fibers, in which concentrations of 0, 0.1, 0.3, 0.5 wt% AMEO-NCC was dip-coated onto eight layers of carbon fiber, cured, and cut for testing. This is accurately displayed under Figure 8C. The greatest mechanical increases of these hybrid concentrations were incurred by 0.3wt%, where interfacial shear strength, flexural modulus, and flexural strength increased by 91%, 23.24%, and 18.21%. Although continuous coating has been highly utilized, it has not been adequately studied for NCCs, hence the novelty of this experiment.
FIGURE 8. (A) Preparation of aqueous suspension of CNC-pCNT using probe sonication (Shariatnia et al., 2020), (B) Preparation of Homogeneous CNC−CNT and CNC−GnP Suspensions by Probe Sonication Treatment, (2) Immersion Coating of CFs to Integrate CNC−CNT and CNC−GnP on CF Surface (Kaynan et al., 2022), (C) he schematic of manufacturing AMEO-NCC coated CF and composites (Zhang et al., 2019b).
Another novel cellulose that has scarcely been utilized with carbon fiber is carboxymethyl cellulose (CMC). Qiu et al. (2021) studied the possibility of avoiding stress concentrations by introducing polar functional groups with 0, 0.025, 0.05, 0.075, and 1 g of CMC. The methodology of creating CMC-modified CFRPs can be visually shown within Figure 9C. After testing their modified carbon fiber samples, tests unveiled that the contact angle of modified samples decreased as CMC increased, proving greater wettability as CMC increases. The ILSS of modified CFs were tested using ASTM D2344 and increased with all amounts of CMC, most noticeably with an increase of 18% with CF/0.075 g CMC. Cellulose Nanocrystals (CNC) in combination with thermoplastic polysulfone (PSF) were used by Cai et al. (2019). To toughen the epoxy resin with the aim of creating stronger carbon fiber composites. A 16-layered carbon fiber composite was prepared using the hand-layup method with different CNC, PSF, and epoxy concentrations. CNC/Epoxy bulk composites were divided into 0.1%, 0.3%, 0.5%, 0.75% and 1%CNC/EP, with supplementary bulk composites comprised of: 10%PSF/EP, 20%PSF/EP, 10%PSF/0.5%CNC/EP and 20%PSF/0.5%CNC/EP. After each concentration was applied onto the composite, it was then evacuated for 30 min, cured for 16 h at 120°C under a 250 kPa load, and cut for the following ASTM tests: ASTM D3039, D7264, D5045, D5528, and D7905. These tests verified that 0.5%CNC/EP garnered the greatest increase in strength relative to other CNC/Epoxy bulk composites, increasing the tensile strength and modulus by 13% and 18%, as well as the critical stress intensity factor (KIc) by 33%. Although these increases in strength are apparent, when it comes to the increases in fracture toughness, the PSF/EP and PSF/CNC/EP composites display much larger increases. These bulk composites increased the mode I and II fracture properties of critical strain energy release rate (GIc) and KIc upwards of 126% and 109% respectively. However, the flexural and tensile strengths of these composites decrease significantly, limiting their use. Despite this, the use of PSF for increasing mode I and II fracture toughness, through electrospinning has been rarely explored. More researchers also modified carbon fiber with CNC through functionalizing cellulose nanocrystals with 3-aminopropyltriethoxysilane (APTES) (Reale Batista and Drzal, 2018).
FIGURE 9. (A) preparation process of multiscale cellulose interlayer (Zhang et al., 2021), (B) Illustration of the preparation of modified CFRPs and reaction mechanism (Qiu et al., 2020), (C) Illustration of the preparation of modified CFs, the preparation structure of CFRPs, illustration of the experimental process of modified CFRPs. (Qiu et al., 2021).
The APTES-CNC solution concentrations were set at 0.6%, 1%, and 2 wt% for two varying sizing methods. The first was immersing 12 k CF tow into the solution for 20 s, then slowly raising CFs. The second sequence places the CFs in the solution at a sequence of 5 min with stir/3 min without stir for about 32 min. Respectively, these sequences produce 12 k tow-sized and individually sized carbon fibers. After ILSS testing was conducted 1.0 wt% APTES-CNC gave the largest growth at 77% and 81% increase for 12 k tow-sized CF and individually sized CF, respectively. Work done by Qiu et al. (2020) explored increasing the interfacial performance of carbon fiber through a sizing process with Carboxymethyl cellulose (CMC) and graphene oxide (GO) as the sizing agents. This research aimed to avoid mechanical damage but to also complete this task in an environmentally friendly manner. Graphene oxide sheets were synthesized, and four test beakers were created containing, 100% CF, 0.003 g of GO, 0.05 g CMC and 0.003 g GO with 0.05 g CMC which were named CF, GO/CF, CMC/CF and CF/GO/CMC respectively. FTIR spectrometry, SEM imaging and Raman spectrometry were conducted and verified that hydrogen bonds were formed in this process, which increases the composites’ energy absorption. This was verified through an interlaminar shear strength of the GO/CF, CMC/CF and CF/GO/CMC increased by 13.2%, 28%, and 50% respectively. With the rising concern of a product’s environmental impact, increasing CFs in an environmentally friendly way like this article attempts to has been rarely explored.
Another way to test and optimize carbon fiber composites, in an environmentally friendly way is to do so virtually. Ahmad and Bajpai (2018) conducted an experiment electronically simulating the structural applications of jute fiber woven mats by using simulation software such as Simulia Abaqus and Siemens PLM NX. Varying types of composite sheets were created and simulated, such as unidirectional jute fiber, Bi-directional woven jute mat and random oriented short jute fibers; all with jute amounts ranging from 0% to 100% jute. The tensile tests were conducted experimentally, under ASM D3039 standards, and through a simulation, in which the modeled data was slightly higher than the experimental findings. Additional parameters were chosen and studied, including ply orientation, varying jute fiber reinforcement and differing weft fiber angles. The methodology as to how the virtual carbon fibers were composed was extensive but very little is known about the physical CFs that were tested. Shariatnia et al. explored the use of producing hybrid composites without chemical functionalization or inserting surfactants into the manufacturing process, which can lead to a more cost-effective composite. Kaynan et al. (2022) also tried a new approach to create stronger CFRPs by using hybrid nanomaterials.
Kaynan aimed to insert CNT and graphene nanoplates (GnPs) via dip coating with CNCs to stabilize these nanomaterials within CFRPs. These nanomaterials were categorized via the mass ratio CNC to CNT/GnP and separated as CNC-CNT 4:1, 6:1, 8:1, 10:1, and 12:1 with CNC-GnP 1:1, 2:1, 4:1, and 6:1, all to be measure and tested (Kaynan et al., 2022). The combinations of CNC, CNC-CNT, and CNC-GnP accounted for 0.2 wt% of the epoxy matrix, in which the coating and immersion of unidirectional CF fabrics were applied for 20 min and cured at 120°C for 24 h. These CF fabrics were stacked in an [02,902,02]s sequence using a VaRTM process and separated by nanomaterial for testing. The results showed that 10:1 CNC-CNT and 4:1 CNC-GnP had the greatest interfacial shear strength increases of 200% and 145% respectively, with morphology images showing that polar oxygen groups increase the adhesion of interfacial properties. It was also determined that flexural and tensile strengths increased as well. Although the process to create these results are not unique, as many have integrated nanomaterials onto CFRPs via dip coating, the results garnered are impactful, relevant, and offer minor disadvantages. Another plant fiber that has attained greater attention is chopped flax fibers (FFs). This is due to their microstructure enhancing the toughness of composites, which is what researchers at Tongji university aimed to do (Shariatnia et al., 2020). In their research, these researchers combined pristine carbon nanotubes (pCNT) and assisting FFs, such as CNC, on functionalized CNT (fCNTs) to aid in pCNT dispersion onto a CFRP polymer. Two coating processes were used for this project: Immersion (I-coating) and Simultaneous Immersion (IS-coating), for an eight-layered CF composite. After the layers have been oriented, they undergo a VaRTM process, then encased and vacuumed to permit resin infusion afterward, where the vent was operational for 24 h To promote curing. After said curing, the sample was cut via a water jet for various testing and analysis. Implanting CNC-pCNT onto CF produced increases in flexural strength, flexural modulus and interlaminar shear strength by 33%, 15% and 35% respectively. The use of processing-manufacturing methods for creating CFRPs is not typical for structural applications but can be an appropriate method to do so, as this project produces noticeable results in mechanical and thermal properties, despite its novelty.
Wang et al. (2017c) utilized chemical vapor deposition in an experiment determining the effects of hybridizing polyimide-graft-bisphenol A diglyceryl acrylate (PI-BDA) and SWCNT concentrations to increase the ILSS of the carbon fiber matrix. The carbon fiber tows were prepared in two different ways, desize via Soxhlet extraction and the CVD method and separated into four concentrations of 0.2%, 0.5%, 1.0%, and 2.0% SWNT/PI-BDA. These concentrations were characterized under FESEM imaging, Raman spectrum analysis and atomic force microscopy (AFM). It was hypothesized the coatings allow for an increase within the carbon fiber and matrix contact area. After testing, the ILSS analysis showed significant increases in strength for all concentrations, with 0.5 wt% increasing the ILSS by 103%, relative to control CF/Epoxy composites. Zhang et al. (2021) also considered the use of plant fibers comprising of FFs and CNFs for interlaminar toughening. CNF/FF-film was created when flax fibers were dissolved into water with a CNF suspension and waterborne epoxy added. These were then separated into three interlayers: neat FF mat, CNF-network film and CNF-film for testing. The Mode II Interlaminar fracture toughness was analyzed using ASTM D7905 standards and it was discovered that the fracture toughness of each interlayer, barring CNF-networks without WE, increased relative to the control. The greatest increases were in CFRPs that contained WE and were found to be 38.7%, 69.4%, and 112% increases in mode II toughness.
Lastly, Umeki et al. (2016) expands on previous research to create a macro-thin composite which was made from plain woven fabrics and an extremely thin CNFs as combinations of regular N (120 µm) and spread (40 µm) carbon fiber tow. Umeki classified thick prepreg as a combination of 16 layers of regular CF tow and both epoxy resin with thin prepreg consisting of 48 layers of spread CF tow with both epoxy resin, creating four classes of testable laminates. These laminates were then subject to mechanical and fatigue life testing, in which minor increases in tensile strength and modulus were achieved, relative to the unmodified epoxy/regular tow. The modified epoxy/spread tow reached the greatest fatigue life, even exceeding the number of cycles to failure. A condensed culmination of all of these results can be shown below in Table 3.
TABLE 3. Summary of mechanical properties improvement of carbon fiber-epoxy composite by organic nanofillers (CNC/CNF).
The use of nanofillers within carbon fiber has been studied and proven to be successful when incorporated into epoxy and carbon fiber laminates. This paper has explored four main nanomaterials that have been gaining popularity, with the aim of providing up-to-date information on the novel studies researchers have been conducting. This paper identified the current uses of pure graphene, CNT, CNC and CNF. Incorporating the cellulose based nanoreinforcements offered the greatest potential in increasing mechanical properties and was shown to increase interfacial interaction and roughness. The incorporation of graphene as nanoreinforcement was able to do so as well, irrespective of testing temperature, as well as increase CF electrical properties such as through-thickness conductivity. Hybrid combinations varying nanomaterials were shown to increase ILSS and IFSS. However, most reports showed that hybridization showed little, none or even negative effects on other parameters. Overall, the covalent interactions of the nanofillers with carbon fiber and its matrix led to the enhancement of its mechanical and even thermal and electrical properties. All while adding little to the weight and thickness of carbon fiber. Due to the unique composition of these nanomaterials, it has been shown that the mechanical properties of carbon fiber tend to increase with minimal weight percentages. Despite this, one challenge that was observed was the preparation time. In many processes to increase the strength of carbon fiber, long and complicated material preparation were recorded, which hinders the practicality of these methods. Hence, if timing is important, a compromise will have to be reached. To conclude, this comprehensive study on the preparation, testing and applications of these nanofillers demonstrate the immaturity of our knowledge, as unique processes are uncovered continuously. More research is required within this field to realize the full potential of these nanomaterials.
PB and OO: Conceptualization, methodology, investigation, resources, and writing; GP and EC: Literature review, proofreading the manuscript; HD and MA: Supervision and project administration, funding acquisition.
The authors declare a potential financial conflict of interest. Multiscale Integrated Technology Solutions LLC (MITS), which has been awarded the National Science Foundation (NSF) Small Business Technology Transfer (STTR) (#2036490) grant to conduct research and development (R&D) work on enhancing the strength of carbon fiber reinforced polymer composites, has potential commercial interest in the research presented in this paper.
All claims expressed in this article are solely those of the authors and do not necessarily represent those of their affiliated organizations, or those of the publisher, the editors and the reviewers. Any product that may be evaluated in this article, or claim that may be made by its manufacturer, is not guaranteed or endorsed by the publisher.
Adak, N. C., Chhetri, S., Kim, N. H., Murmu, N. C., Samanta, P., and Kuila, T. (2018). Static and dynamic mechanical properties of graphene oxide-incorporated woven carbon fiber/epoxy composite. J. Mat. Eng. Perform. 27 (3), 1138–1147. doi:10.1007/s11665-018-3201-5
Ahmad, F., and Bajpai, P. K. (2018). Evaluation of stiffness in a cellulose fiber reinforced epoxy laminates for structural applications: Experimental and finite element analysis. Def. Technol. 14 (4), 278–286. doi:10.1016/j.dt.2018.05.006
Ahmad, S. (1999). Carbon nanostructures fullerenes and carbon nanotubes. IETE Tech. Rev. 16 (3-4), 297–310. doi:10.1080/02564602.1999.11416845
Altin, Y., Yilmaz, H., Unsal, O. F., and Bedeloglu, A. C. (2020). Graphene oxide modified carbon fiber reinforced epoxy composites. J. Polym. Eng. 40 (5), 415–420. doi:10.1515/polyeng-2019-0247
Alves, C., Ferrao, P., Silva, A., Reis, L., Freitas, M., Rodrigues, L., et al. (2010). Ecodesign of automotive components making use of natural jute fiber composites. J. Clean. Prod. 18 (4), 313–327. doi:10.1016/j.jclepro.2009.10.022
An, F., Lu, C., Li, Y., Guo, J., Lu, X., Lu, H., et al. (2012). Preparation and characterization of carbon nanotube-hybridized carbon fiber to reinforce epoxy composite. Mater. Des. 33, 197–202. doi:10.1016/j.matdes.2011.07.027
Ashori, A., Rahmani, H., and Bahrami, R. (2015). Preparation and characterization of functionalized graphene oxide/carbon fiber/epoxy nanocomposites. Polym. Test. 48, 82–88. doi:10.1016/j.polymertesting.2015.09.010
Bacon, R. (1960). Growth, structure, and properties of graphite whiskers. J. Appl. Phys. 31 (2), 283–290. doi:10.1063/1.1735559
Bacon, R., and Tang, M. M. (1964). Carbonization of cellulose fibers—II. Physical property study. Carbon 2 (3), 221–225. doi:10.1016/0008-6223(64)90036-3
Cai, S., Li, Y., Liu, H. Y., and Mai, Y. W. (2019). Effect of electrospun polysulfone/cellulose nanocrystals interleaves on the interlaminar fracture toughness of carbon fiber/epoxy composites. Compos. Sci. Technol. 181, 107673. doi:10.1016/j.compscitech.2019.05.030
Chen, L., Jin, H., Xu, Z., Shan, M., Tian, X., Yang, C., et al. (2014). A design of gradient interphase reinforced by silanized graphene oxide and its effect on carbon fiber/epoxy interface. Mater. Chem. Phys. 145 (1), 186–196. doi:10.1016/j.matchemphys.2014.02.001
Chien, A.-T., Liu, H. C., Newcomb, B. A., Xiang, C., Tour, J. M., and Kumar, S. (2015). Polyacrylonitrile fibers containing graphene oxide nanoribbons. ACS Appl. Mat. Interfaces 7 (9), 5281–5288. doi:10.1021/am508594p
Consales, M., Cutolo, A., Cusano, A., Penza, M., Aversa, P., Giordano, M., et al. (2006). “Optical fiber sensors coated with carbon nanotubes, Tin dioxide and nanoporous polymers for cryogenic detection of hydrogen,” in Sensors (Jersey, United States: IEEE).
Cusano, A., Pisco, M., Consales, M., Cutolo, A., Giordano, M., Penza, M., et al. (2006). Novel optochemical sensors based on hollow fibers and single walled carbon nanotubes. IEEE Photonics Technol. Lett. 18 (22), 2431–2433. doi:10.1109/lpt.2006.885618
De Greef, N., Gorbatikh, L., Godara, A., Mezzo, L., Lomov, S. V., and Verpoest, I. (2011). The effect of carbon nanotubes on the damage development in carbon fiber/epoxy composites. Carbon 49, 4650–4664. doi:10.1016/j.carbon.2011.06.047
Dong, L., Hou, F., Li, Y., Wang, L., Gao, H., and Tang, Y. (2014). Preparation of continuous carbon nanotube networks in carbon fiber/epoxy composite. Compos. Part A Appl. Sci. Manuf. 56, 248–255. doi:10.1016/j.compositesa.2013.10.016
Du, X., Zhou, H., Sun, W., Liu, H. Y., Zhou, G., Zhou, H., et al. (2017). Graphene/epoxy interleaves for delamination toughening and monitoring of crack damage in carbon fibre/epoxy composite laminates. Compos. Sci. Technol. 140, 123–133. doi:10.1016/j.compscitech.2016.12.028
Dzenis, Y. A., and Qian, J. (2001). Analysis of microdamage evolution histories in composites. Int. J. solids Struct. 38 (10-13), 1831–1854. doi:10.1016/s0020-7683(00)00138-4
Dzenis, Y. A. (1996). Stochastic damage evolution modeling in laminates. J. Thermoplast. Compos. Mater. 9 (1), 21–34. doi:10.1177/089270579600900103
Ehsani, M., Rahimi, P., and Joseph, Y. (2021). Structure–function relationships of nanocarbon/polymer composites for chemiresistive sensing: A review. Sensors 21 (9), 3291. doi:10.3390/s21093291
Frank, E., Ingildeev, D., and Buchmeiser, M. R. (2017). “2 - high-performance PAN-based carbon fibers and their performance requirements,” in Structure and properties of high-performance fibers. Editor G. Bhat (Oxford: Woodhead Publishing), 7–30.
Gabr, M. H., Elrahman, M. A., Okubo, K., and Fujii, T. (2010). Interfacial adhesion improvement of plain woven carbon fiber reinforced epoxy filled with micro-fibrillated cellulose by addition liquid rubber. J. Mat. Sci. 45 (14), 3841–3850. doi:10.1007/s10853-010-4439-y
Gabr, M. H., Elrahman, M. A., Okubo, K., and Fujii, T. (2010a). A study on mechanical properties of bacterial cellulose/epoxy reinforced by plain woven carbon fiber modified with liquid rubber. Compos. Part A Appl. Sci. Manuf. 41 (9), 1263–1271.
Geim, A. K., and Novoselov, K. S. (2007). The rise of graphene. Nat. Mat. 6 (3), 183–191. doi:10.1038/nmat1849
Gerard, H. G. (2015). “Boeing and the 787 dreamliner,” in Decisions: An engineering and management perspective (Jersey, United States: IEEE), 187–218.
Gogoi, R., Maurya, A. K., and Manik, G. (2022). A review on recent development in carbon fiber reinforced polyolefin composites. Compos. Part C. Open Access 8, 100279. doi:10.1016/j.jcomc.2022.100279
Hadden, C. M., Klimek-McDonald, D., Pineda, E., King, J., Reichanadter, A., Miskioglu, I., et al. (2015). Mechanical properties of graphene nanoplatelet/carbon fiber/epoxy hybrid composites: Multiscale modeling and experiments. Carbon 95, 100–112. doi:10.1016/j.carbon.2015.08.026
Hammel, E., Tang, X., Trampert, M., Schmitt, T., Mauthner, K., Eder, A., et al. (2004). Carbon nanofibers for composite applications. Carbon 42 (5), 1153–1158. doi:10.1016/j.carbon.2003.12.043
Han, X., Zhao, Y., Sun, J. m., Li, Y., Zhang, J. d., and Hao, Y. (2017). Effect of graphene oxide addition on the interlaminar shear property of carbon fiber-reinforced epoxy composites. Carbon N. Y. 32 (1), 489–555. doi:10.1016/j.carbon.2017.02.077
Hawkins, D. A., and Haque, A. (2014). Fracture toughness of carbon-graphene/epoxy hybrid nanocomposites. Procedia Eng. 90, 176–181. doi:10.1016/j.proeng.2014.11.833
He, Y., Chen, Q., Yang, S., Lu, C., Feng, M., Jiang, Y., et al. (2018). Micro-crack behavior of carbon fiber reinforced Fe3O4/graphene oxide modified epoxy composites for cryogenic application. Compos. Part A Appl. Sci. Manuf. 108, 12–22. doi:10.1016/j.compositesa.2018.02.014
Hollaway, L. C. (2003). The evolution of and the way forward for advanced polymer composites in the civil infrastructure. Constr. Build. Mater. 17 (6), 365–378. doi:10.1016/s0950-0618(03)00038-2
Huang, J. Y., Tan, Y. C., and Chow, K. K. (2015). “Carbon-nanotube-deposited multi-mode fiber cavity for refractive index sensing applications,” in 2015 10th International Conference on Information, Communications and Signal Processing (ICICS), Singapore, 02-04 December 2015.
Inagaki, M. (2000). “Chapter 4 - carbon fibers,” in New carbons - control of structure and functions. Editor M. Inagaki (Oxford: Elsevier Science), 82–123.
Jenkins, P., Siddique, S., Khan, S., Usman, A., Starost, K., MacPherson, A., et al. (2019). Influence of reduced graphene oxide on epoxy/carbon fiber-reinforced hybrid composite: Flexural and shear properties under varying temperature conditions. Adv. Eng. Mat. 21 (6), 1800614. doi:10.1002/adem.201800614
Jiang, D., Liu, L., Wu, G., Zhang, Q., Long, J., Wu, Z., et al. (2017). Mechanical properties of carbon fiber composites modified with graphene oxide in the interphase. Polym. Compos. 38 (11), 2425–2432. doi:10.1002/pc.23828
Johnson, D. J. (1990). “Structure and properties of carbon fibres,” in Carbon fibers filaments and composites. Editor J. L. Figueiredo (Dordrecht: Springer Netherlands), 119–146.
Kamae, T., and Drzal, L. T. (2012). Carbon fiber/epoxy composite property enhancement through incorporation of carbon nanotubes at the fiber–matrix interphase – Part I: The development of carbon nanotube coated carbon fibers and the evaluation of their adhesion. Compos. Part A Appl. Sci. Manuf. 43 (9), 1569–1577. doi:10.1016/j.compositesa.2012.02.016
Kaynan, O., Pérez, L. M., and Asadi, A. (2022). Cellulose nanocrystal-enabled Tailoring of the interface in carbon nanotube- and graphene nanoplatelet-carbon fiber polymer composites: Implications for structural applications. ACS Appl. Nano Mat. 5 (1), 1284–1295. doi:10.1021/acsanm.1c03860
Keyte, J., Pancholi, K., and Njuguna, J. (2019). Recent developments in graphene oxide/epoxy carbon fiber-reinforced composites. Front. Mat. 6. doi:10.3389/fmats.2019.00224
Kim, J., Cha, J., Chung, B., Ryu, S., and Hong, S. H. (2020). Fabrication and mechanical properties of carbon fiber/epoxy nanocomposites containing high loadings of noncovalently functionalized graphene nanoplatelets. Compos. Sci. Technol. 192, 108101. doi:10.1016/j.compscitech.2020.108101
Koniuszewska, A. G., and Kaczmar, J. W. (2016). Application of polymer based composite materials in Transportation. Prog. Rubber, Plastics Recycl. Technol. 32 (1), 1–24. doi:10.1177/147776061603200101
Koronis, G., Silva, A., and Fontul, M. (2013). Green composites: A review of adequate materials for automotive applications. Compos. Part B Eng. 44 (1), 120–127. doi:10.1016/j.compositesb.2012.07.004
Kwon, Y. J., Kim, Y., Jeon, H., Cho, S., Lee, W., and Lee, J. U. (2017). Graphene/carbon nanotube hybrid as a multi-functional interfacial reinforcement for carbon fiber-reinforced composites. Compos. Part B Eng. 122, 23–30. doi:10.1016/j.compositesb.2017.04.005
Lee, X. J., Hiew, B. Y. Z., Lai, K. C., Lee, L. Y., Gan, S., Thangalazhy-Gopakumar, S., et al. (2019). Review on graphene and its derivatives: Synthesis methods and potential industrial implementation. J. Taiwan Inst. Chem. Eng. 98, 163–180. doi:10.1016/j.jtice.2018.10.028
Lewis, S. J. (1994). The use of carbon fibre composites on military aircraft. Compos. Manuf. 5 (2), 95–103. doi:10.1016/0956-7143(94)90060-4
Li, M., Gu, Y., Liu, Y., Li, Y., and Zhang, Z. (2013). Interfacial improvement of carbon fiber/epoxy composites using a simple process for depositing commercially functionalized carbon nanotubes on the fibers. Carbon 52, 109–121. doi:10.1016/j.carbon.2012.09.011
Li, Y., Zhao, Y., Sun, J., Hao, Y., Zhang, J., and Han, X. (2016). Mechanical and electromagnetic interference shielding properties of carbon fiber/graphene nanosheets/epoxy composite. Polym. Compos. 37 (8), 2494–2502. doi:10.1002/pc.23436
Liu, D., Chen, X., Yue, Y., Chen, M., and Wu, Q. (2011). Structure and rheology of nanocrystalline cellulose. Carbohydr. Polym. 84 (1), 316–322. doi:10.1016/j.carbpol.2010.11.039
Liu, H., and Mao, Y. (2021). Graphene oxide-based nanomaterials for uranium adsorptive uptake. ES Mat. Manuf. 13, 3–22. doi:10.30919/esmm5f453
Lv, P., Feng, Y. y., Zhang, P., Chen, H. m., Zhao, N., and Feng, W. (2011). Increasing the interfacial strength in carbon fiber/epoxy composites by controlling the orientation and length of carbon nanotubes grown on the fibers. Carbon 49 (14), 4665–4673. doi:10.1016/j.carbon.2011.06.064
Maria, M. (2013). Advanced composite materials of the future in aerospace industry. INCAS Bull. 5, 139–150. doi:10.13111/2066-8201.2013.5.3.14
Marsh, G. (2007). Airbus takes on Boeing with reinforced plastic A350 XWB. Reinf. Plast. 51 (11), 26–29. doi:10.1016/s0034-3617(07)70383-1
Mason, R. B., Gintert, L. A., Singleton, M. F., and Skelton, D. (2004). Composites for military equipment. Adv. Mater. Process. 162, 37.
Mehdi, H., and Resatoglu, R. (2022). Confinement of concrete columns using CFRP and expanded grout. J. Struct. Integr. Maintenance 7 (2), 128–135. doi:10.1080/24705314.2021.2018841
Mittal, G., Rhee, K. Y., Miskovic-Stankovic, V., and Hui, D. (2018). Reinforcements in multi-scale polymer composites: Processing, properties, and applications. Compos. Part B Eng. 138, 122–139. doi:10.1016/j.compositesb.2017.11.028
Mohee, F. M., Al-Mayah, A., and Plumtree, A. (2016). Anchors for CFRP plates: State-of-the-art review and future potential. Compos. Part B Eng. 90, 432–442. doi:10.1016/j.compositesb.2016.01.011
Nasser, J., Zhang, L., and Sodano, H. (2021). Laser induced graphene interlaminar reinforcement for tough carbon fiber/epoxy composites. Compos. Sci. Technol. 201, 108493. doi:10.1016/j.compscitech.2020.108493
Njuguna, J., and Pielichowski, K. (2004). Polymer nanocomposites for aerospace applications: Characterization. Adv. Eng. Mat. 6 (4), 204–210. doi:10.1002/adem.200305110
Njuguna, J., and Pielichowski, K. (2004). Polymer nanocomposites for aerospace applications: Fabrication. Adv. Eng. Mat. 6 (4), 193–203. doi:10.1002/adem.200305111
Pathak, A. K., Borah, M., Gupta, A., Yokozeki, T., and Dhakate, S. R. (2016). Improved mechanical properties of carbon fiber/graphene oxide-epoxy hybrid composites. Compos. Sci. Technol. 135, 28–38. doi:10.1016/j.compscitech.2016.09.007
Peng, S., Shao, H., and Hu, X. (2003). Lyocell fibers as the precursor of carbon fibers. J. Appl. Polym. Sci. 90 (7), 1941–1947. doi:10.1002/app.12879
Perner, M., Algermissen, S., Keimer, R., and Monner, H. (2016). Avoiding defects in manufacturing processes: A review for automated CFRP production. Robotics Computer-Integrated Manuf. 38, 82–92. doi:10.1016/j.rcim.2015.10.008
Qin, L.-C., Zhao, X., Hirahara, K., Miyamoto, Y., Ando, Y., and Iijima, S. (2000). The smallest carbon nanotube. Nature 408 (6808), 50. doi:10.1038/35040699
Qin, W., Vautard, F., Drzal, L. T., and Yu, J. (2015). Mechanical and electrical properties of carbon fiber composites with incorporation of graphene nanoplatelets at the fiber–matrix interphase. Compos. Part B Eng. 69, 335–341. doi:10.1016/j.compositesb.2014.10.014
Qiu, B., Li, M., Zhang, X., Chen, Y., Zhou, S., Liang, M., et al. (2021). Carboxymethyl cellulose sizing repairs carbon fiber surface defects in epoxy composites. Mater. Chem. Phys. 258, 123677. doi:10.1016/j.matchemphys.2020.123677
Qiu, B., Sun, T., Li, M., Chen, Y., Zhou, S., Liang, M., et al. (2020). High micromechanical interlocking graphene oxide/carboxymethyl cellulose composite architectures for enhancing the interface adhesion between carbon fiber and epoxy. Compos. Part A Appl. Sci. Manuf. 139, 106092. doi:10.1016/j.compositesa.2020.106092
Qu, C.-B., Huang, Y., Li, F., Xiao, H. M., Liu, Y., Feng, Q. P., et al. (2020). Enhanced cryogenic mechanical properties of carbon fiber reinforced epoxy composites by introducing graphene oxide. Compos. Commun. 22, 100480. doi:10.1016/j.coco.2020.100480
Ravishankar, B., Nayak, S. K., and Kader, M. A. (2019). Hybrid composites for automotive applications – a review. J. Reinf. Plastics Compos. 38 (18), 835–845. doi:10.1177/0731684419849708
Reale Batista, M. D., and Drzal, L. T. (2018). Carbon fiber/epoxy matrix composite interphases modified with cellulose nanocrystals. Compos. Sci. Technol. 164, 274–281. doi:10.1016/j.compscitech.2018.05.010
Rodríguez-González, J. A., Rubio-Gonzalez, C., Jimenez-Mora, M., Ramos-Galicia, L., and Velasco-Santos, C. (2018). Influence of the hybrid combination of multiwalled carbon nanotubes and graphene oxide on interlaminar mechanical properties of carbon fiber/epoxy laminates. Appl. Compos. Mat. (Dordr). 25 (5), 1115–1131. doi:10.1007/s10443-017-9656-y
Sadeghian, P., Rahai, A. R., and Ehsani, M. R. (2010). Effect of fiber orientation on compressive behavior of CFRP-confined concrete columns. J. Reinf. Plastics Compos. 29 (9), 1335–1346. doi:10.1177/0731684409102985
Sager, R. J., Klein, P. J., Davis, D. C., Lagoudas, D. C., Warren, G. L., and Sue, H. J. (2011). Interlaminar fracture toughness of woven fabric composite laminates with carbon nanotube/epoxy interleaf films. J. Appl. Polym. Sci. 121 (4), 2394–2405. doi:10.1002/app.33479
Schalamon, W., and Bacon, R. (1970). in Process for producing carbon fibers having a high YOUNG'S modulus of elast city. Editor U. S. Patent (United States: Union Carbide Corporation), 4.
Shao, Y., Yashiro, T., Okubo, K., and Fujii, T. (2015). Effect of cellulose nano fiber (CNF) on fatigue performance of carbon fiber fabric composites. Compos. Part A Appl. Sci. Manuf. 76, 244–254. doi:10.1016/j.compositesa.2015.05.033
Shariatnia, S., Kumar, A. V., Kaynan, O., and Asadi, A. (2020). Hybrid cellulose nanocrystal-bonded carbon nanotubes/carbon fiber polymer composites for structural applications. ACS Appl. Nano Mat. 3 (6), 5421–5436. doi:10.1021/acsanm.0c00785
Siddiqui, N. A., Khan, S. U., Ma, P. C., Li, C. Y., and Kim, J. K. (2011). Manufacturing and characterization of carbon fibre/epoxy composite prepregs containing carbon nanotubes. Compos. Part A Appl. Sci. Manuf. 42 (10), 1412–1420. doi:10.1016/j.compositesa.2011.06.005
Subramaniyan, A. K., and Sun, C. (2008). Interlaminar fracture behavior of nanoclay reinforced glass fiber composites. J. Compos. Mater. 42 (20), 2111–2122. doi:10.1177/0021998308094550
Subramaniyan, A. K., and Sun, C. (2007). Toughening polymeric composites using nanoclay: Crack tip scale effects on fracture toughness. Compos. Part A Appl. Sci. Manuf. 38 (1), 34–43. doi:10.1016/j.compositesa.2006.01.021
Talreja, R. (1994). Damage mechanics of composite materials. Amsterdam, Netherlands: Elsevier Science.
Tanaka, F., and Okabe, T. (2018). “1.4 historical review of processing, microstructures, and mechanical properties of PAN-based carbon fibers,” in Comprehensive composite materials II. Editors P. W. R. Beaumont, and C. H. Zweben (Oxford: Elsevier), 66–85.
Tareq, M. S., Zainuddin, S., Woodside, E., and Syed, F. (2019). Investigation of the flexural and thermomechanical properties of nanoclay/graphene reinforced carbon fiber epoxy composites. J. Mat. Res. 34 (21), 3678–3687. doi:10.1557/jmr.2019.302
Ueda, T., and Sato, Y. (2002). New approach for usage of continuous fiber as non-metallic reinforcement of concrete. Struct. Eng. Int. 12 (2), 111–116. doi:10.2749/101686602777965478
Umeki, R., Tanaka, A., Okubo, K., Fujii, T., Kawabe, K., Kondo, K., et al. (2016). A new unidirectional carbon fiber prepreg using physically modified epoxy matrix with cellulose nano fibers and spread tows. Compos. Part A Appl. Sci. Manuf. 90, 400–409. doi:10.1016/j.compositesa.2016.06.011
Van Den Einde, L., Zhao, L., and Seible, F. (2003). Use of FRP composites in civil structural applications. Constr. Build. Mater. 17 (6), 389–403. doi:10.1016/s0950-0618(03)00040-0
Wang, C., Li, J., Yu, J., Sun, S., Li, X., Xie, F., et al. (2017). Grafting of size-controlled graphene oxide sheets onto carbon fiber for reinforcement of carbon fiber/epoxy composite interfacial strength. Compos. Part A Appl. Sci. Manuf. 101, 511–520. doi:10.1016/j.compositesa.2017.07.015
Wang, C., Zhao, M., Li, J., Yu, J., Sun, S., Ge, S., et al. (2017). Silver nanoparticles/graphene oxide decorated carbon fiber synergistic reinforcement in epoxy-based composites. Polymer 131, 263–271. doi:10.1016/j.polymer.2017.10.049
Wang, Y., Raman Pillai, S. K., Che, J., and Chan-Park, M. B. (2017). High interlaminar shear strength enhancement of carbon fiber/epoxy composite through fiber- and matrix-anchored carbon nanotube networks. ACS Appl. Mat. Interfaces 9 (10), 8960–8966. doi:10.1021/acsami.6b13197
Windhorst, T., and Blount, G. (1997). Carbon-carbon composites: A summary of recent developments and applications. Mater. Des. 18 (1), 11–15. doi:10.1016/s0261-3069(97)00024-1
Wu, Q., Yang, X., He, J., Ye, Z., Liu, Q., Bai, H., et al. (2022). Improved interfacial adhesion of epoxy composites by grafting porous graphene oxide on carbon fiber. Appl. Surf. Sci. 573, 151605. doi:10.1016/j.apsusc.2021.151605
Wu, X.-F. (2003). Fracture of advanced polymer composites with nanofiber reinforced interfaces. Lincoln, United States: University of Nebraska - Lincoln.
Wu, X. (2009). Fracture of advanced composites with nanofiber reinforced interfaces: Fabrication, characterization and modeling. Werdohl, Germany: VDM Publishing.
Wu, Z., Wang, X., Zhao, X., and Noori, M. (2014) State-of-the-art review of FRP composites for major construction with high performance and longevity 1(3): p. 201–231. doi:10.1504/ijsmss.2014.062757
Xiao, C., Tan, Y., Wang, X., Gao, L., Wang, L., and Qi, Z. (2018). Study on interfacial and mechanical improvement of carbon fiber/epoxy composites by depositing multi-walled carbon nanotubes on fibers. Chem. Phys. Lett. 703, 8–16. doi:10.1016/j.cplett.2018.05.012
Xu, X., Liu, F., Jiang, L., Zhu, J. Y., Haagenson, D., and Wiesenborn, D. P. (2013). Cellulose nanocrystals vs. Cellulose nanofibrils: A comparative study on their microstructures and effects as polymer reinforcing agents. ACS Appl. Mat. Interfaces 5 (8), 2999–3009. doi:10.1021/am302624t
Xu, Z., and Gao, C. (2015). Graphene fiber: A new trend in carbon fibers. Mater. Today 18 (9), 480–492. doi:10.1016/j.mattod.2015.06.009
Xu, Z., Liu, Y., Zhao, X., Peng, L., Sun, H., Xu, Y., et al. (2016). Ultrastiff and strong graphene fibers via full-scale synergetic defect engineering. Adv. Mat. 28 (30), 6449–6456. doi:10.1002/adma.201506426
Yang, Z., Tian, J., Yin, Z., Cui, C., Qian, W., and Wei, F. (2019). Carbon nanotube- and graphene-based nanomaterials and applications in high-voltage supercapacitor: A review. Carbon 141, 467–480. doi:10.1016/j.carbon.2018.10.010
Yao, H., Sui, X., Zhao, Z., Xu, Z., Chen, L., Deng, H., et al. (2015). Optimization of interfacial microstructure and mechanical properties of carbon fiber/epoxy composites via carbon nanotube sizing. Appl. Surf. Sci. 347, 583–590. doi:10.1016/j.apsusc.2015.04.146
Yuan, X., Zhu, B., Cai, X., Qiao, K., Zhao, S., and Yu, J. (2018). Influence of different surface treatments on the interfacial adhesion of graphene oxide/carbon fiber/epoxy composites. Appl. Surf. Sci. 458, 996–1005. doi:10.1016/j.apsusc.2018.06.161
Zhang, M., Li, M., Liu, L., Fu, J., Jin, L., Shang, L., et al. (2019). Directly coating silanized nanocrystalline cellulose on carbon fiber for enhancing the interfacial adhesion of carbon fiber/epoxy resin composites. Polym. Compos. 40 (S1), E744–E752. doi:10.1002/pc.24983
Zhang, R.-S., and Jiang, J.-W. (2018). The art of designing carbon allotropes. Front. Phys. (Beijing). 14 (1), 13401. doi:10.1007/s11467-018-0836-5
Zhang, R. L., Gao, B., Du, W., Zhang, J., Cui, H., Liu, L., et al. (2016). Enhanced mechanical properties of multiscale carbon fiber/epoxy composites by fiber surface treatment with graphene oxide/polyhedral oligomeric silsesquioxane. Compos. Part A Appl. Sci. Manuf. 84, 455–463. doi:10.1016/j.compositesa.2016.02.021
Zhang, W., Deng, X., Sui, G., and Yang, X. (2019). Improving interfacial and mechanical properties of carbon nanotube-sized carbon fiber/epoxy composites. Carbon 145, 629–639. doi:10.1016/j.carbon.2019.01.063
Zhang, Z., Fu, K., and Li, Y. (2021). Improved interlaminar fracture toughness of carbon fiber/epoxy composites with a multiscale cellulose fiber interlayer. Compos. Commun. 27, 100898. doi:10.1016/j.coco.2021.100898
Keywords: polymer, matrix, CRFP, nanofillers, composite materials, epoxy composite
Citation: Biswas PK, Omole O, Peterson G, Cumbo E, Agarwal M and Dalir H (2023) Carbon and cellulose based nanofillers reinforcement to strengthen carbon fiber-epoxy composites: Processing, characterizations, and applications. Front. Mater. 9:1089996. doi: 10.3389/fmats.2022.1089996
Received: 04 November 2022; Accepted: 28 November 2022;
Published: 10 January 2023.
Edited by:
Christophe Binetruy, Ecole Centrale de Nantes, FranceReviewed by:
Marco Monti, Proplast Consortium for the Promotion of the Plastic Culture, ItalyCopyright © 2023 Biswas, Omole, Peterson, Cumbo, Agarwal and Dalir. This is an open-access article distributed under the terms of the Creative Commons Attribution License (CC BY). The use, distribution or reproduction in other forums is permitted, provided the original author(s) and the copyright owner(s) are credited and that the original publication in this journal is cited, in accordance with accepted academic practice. No use, distribution or reproduction is permitted which does not comply with these terms.
*Correspondence: Mangilal Agarwal, YWdhcndhbEBpdXB1aS5lZHU=; Hamid Dalir, aGRhbGlyQGl1LmVkdQ==
Disclaimer: All claims expressed in this article are solely those of the authors and do not necessarily represent those of their affiliated organizations, or those of the publisher, the editors and the reviewers. Any product that may be evaluated in this article or claim that may be made by its manufacturer is not guaranteed or endorsed by the publisher.
Research integrity at Frontiers
Learn more about the work of our research integrity team to safeguard the quality of each article we publish.