- 1Research Institute of Leather and Footwear Industry of Wenzhou, Wenzhou, China
- 2Fujian Provincial Engineering Research Center of Rural Waste Recycling Technology, Department of Environmental Science and Engineering, Fuzhou University, Minhou, China
Plant straw fibers have been used widely in composite materials as reinforcement due to their advantages of low density, easy degradation, low cost, and abundance. However, the mechanical properties and water resistance of the as-prepared composites are limited due to the poor compatibility between plant straw fibers and polymer matrix. In this work, the rice straw fibers were pretreated with the silane coupling agent, lipase, and hydrothermal, and then blended with phenolic resin to prepare composites. The results showed that the pretreatment of the fibers can improve their compatibility with the resin matrix and improve the comprehensive mechanical properties and the thickness swelling of composites. When the mass ratio of fiber to resin is 1:1 and the hot-pressing condition is 160°C and 11 min, the static bending strength, elastic modulus, and thickness swelling of the phenolic resin/lipase-treatment rice straw fibers (PF/L-SF) composite reached 23.03 MPa and 2588.39 MPa, which increased by 32.9% and 30.5% compared with the unmodified fiber/phenolic resin composite (PF/SF).
1 Introduction
Since synthetic plastics were produced in the 1950s, they have been used widely in various areas of modern society due to their excellent properties (lightweight, low-cost, resistant to corrosion, flexibility, and easy processibility) (Chandra et al., 2016; Peplow, 2016; Liu et al., 2020). However, most synthetic plastics cannot be degraded in the natural environment due to their durable chemistry structure (Thompson et al., 2009; Cressey, 2016; Yu et al., 2022). Until now, there has produced over 6,300 million tonnes of plastic waste globally, and the primary treatment of plastic waste is landfilling, which has caused serious environmental problems (Geyer et al., 2017; Chinthapalli et al., 2019; Guan et al., 2021). In recent years, many works reported that more and more different types of degradable plastics were developed, such as polylactic acid (PLA), polycaprolactone (PCL), polyhydroxyalkanoates (PHAs), etc., (Cywar et al., 2022). Due to the high-cost and complicated synthesis process, these degradable plastics cannot replace common petroleum-based plastics (phenolic resin, polypropylene, polyethylene, epoxy resin, etc.,) (Cywar et al., 2022). Therefore, it is necessary to develop new strategies to reduce the amount of usage of undegradable plastics in low-cost and scalable-production methods.
Lignocellulosic biomass as the most abundant natural polymers on Earth is composed of three compounds (cellulose, hemicellulose, and lignin), produced through photosynthesis from solar energy, water, and carbon dioxide (Nanda et al., 2015). The annual world production of biomass is high to 200 billion tons, and they have been used as the starting materials to fabricate degradable material through “bottom-up” and “top-down” approaches (Zhang et al., 2022a; Zhang et al., 2022b). For example, lignocellulosic bioplastic was produced by dissolving wood powders and regeneration, which presented high tensile strength of 128 MPa, excellent water stability, and UV resistance (Xia et al., 2021). Nanocellulose is also produced from lignocellulosic biomass to prepare films, aerogels, hydrogels, fibers, etc., (De France et al., 2021). Although these materials exhibit excellent mechanical properties, they still cannot be produced on an industrial scale due to the complex fabrication process and high cost (Li et al., 2018). In addition, lignocellulosic biomass can also be used directly as reinforcement in the plastic matrix to prepare various composite materials, which can reduce the usage of plastics dramatically (Bledzki and Gassan, 1999; Sui et al., 2009). However, the interfacial compatibility between lignocellulosic biomass and synthetic plastics is poor due to the principle of dissolution in a similar material structure (Torres and Cubillas, 2005; Edeerozey et al., 2007). Therefore, developing facile methods to improve compatibility is vital for the scalable production of plant fiber/plastic composites.
In this work, we reported three different green and feasible approaches (silane modification, hydrothermal treatment, and enzyme treatment) to treat rice straw fibers. Then the PF/SF composites were fabricated by simple mixing and hot-pressing with high mechanical performance and water resistance. The obtained composites showed improved static bending strength (23.34 MPa), elastic modulus (2279.04 MPa), and thickness swelling (10.3%) compared to the composite without pretreatment. The interfacial compatibility between rice straw fibers and phenolic resin was investigated by Dynamic mechanical analysis (DMA). Therefore, this research work provided different strategies to improve the performance of plastic/plant fiber composites, which showed great potential for reducing the amount of usage of plastics in the future.
2 Materials and methods
2.1 Materials
Rice straw was obtained from Jin He Agricultural Technology Co., Ltd. (Shanxi, China). Bis-(γ-triethoxysilylpropyl)-tetrasulfide and anhydrous ethanol were purchased from Aladdin Biochemical Technology Co., Ltd. (Shanghai, China). Lipase was obtained from Shandong Longkete Enzyme Preparation Co., Ltd. (Shandong, China). The phenolic resin was obtained Guangdong Yitong Plastic Chemical Raw Materials Co., Ltd. (Guangdong, China). All chemicals were used as received without further purification. All solutions were prepared with deionized water.
2.2 Preparation of rice straw fiber
1,000 g rice straw was washed with deionized water and dried completely in the oven at 105°C. Then rice straw was cut into small sections with a length of 1–2 cm and put into a centrifugal mill for crushing. The unmodified rice straw fibers (SF) were obtained after the crushed rice straw passed the 0.5 mm sieve.
2.3 Pretreatment of rice straw fibers
Silane-modified rice straw fibers: 9 g double-[γ-(triethoxysilicon) propyl] tetrasulfide was dissolved in 285 g ethanol/water solution with the mass ratio at 95:5 and stirred for 1 h at room temperature (25°C). Then 90 g rice straw fibers were added into the prepared mixed solution and stirred for another 1 h. After the reaction was finished, the rice straw fibers were washed with ethanol three times to remove the unreacted silane coupling agent. Finally, the silane-modified rice straw fibers (S-SF) were obtained by drying at 80°C ± 2°C for 24 h and stored in a sealed bag for further use.
Hydrothermal treatment of rice straw fibers: 90 g rice straw fibers and 300 ml deionized water were added into a three-necked flask and stirred at 90°C with a water bath for 1 h. Then the hydrothermally treated rice straw fibers (H-SF) were obtained by drying at 80°C for 24 h and stored in a sealed bag.
Lipase treatment of rice straw fibers: 9 g lipase was dissolved into 300 ml deionized water, and 90 g rice straw fibers were added into the solution with stirring for 4 h under a 40°C water bath. After the treatment, the obtained rice straw fibers were washed with ethanol three times to remove the unreacted lipase. Then the L-SF were obtained by drying at 80°C for 24 h and stored in a sealed bag for further use.
2.4 Preparation of rice straw fiber phenolic resin composite
30 g SF, S-SF, H-SF, and L-SF were mixed with phenolic resin with the weight ratio at 1:1 respectively. 1% curing agent of the weight ratio of phenolic resin was added to the mixture and stirred for 1 h. Then the uniformly mixed fibers and phenolic resin were added into the mold and cured by hot-pressing under different conditions with a pressure of 5 MPa.
2.5 Characterization
2.5.1 Fourier transform infrared spectroscopy (FT-IR)
At room temperature (25°C), SF, S-SF, H-SF, and L-SF were mixed with KBr with a weight ratio of 1:100 and ground and pressed to prepare the samples for analysis. The test of the FT-IR of different samples was carried out at the resolution of 4 cm−1, and the scanning range of 4,000–500 cm−1.
2.5.2 Mechanical performance
Three-point bending test of the rice straw fibers/phenolic resin composites was carried out according to GB/T228-2010 standard with an Instron 5565A universal testing machine. For all the samples, the direction of the loading was perpendicular to the layers, and each sample was tested at least 5 times with the loading rate at 1.0 mm min−1 and the support span at 12.5 mm.
2.5.3 Thickness swelling
Five specimens of 20 mm × 20 mm × 3 mm different types of rice straw fibers/phenolic resin composites were prepared according to the standard of ASTM D570 to test the thickness swelling. The thickness swelling was calculated according to the following equation:
In which d0 presents the thickness of specimens before immersing them in water. d1 presents the thickness of specimens after 7 days of immersion in distilled water.
2.5.4 DMA
The DMA of rice straw fibers/phenolic resin composites was performed using a dynamic mechanical analyzer (Q800 TA Instruments, USA). All of the specimens were cut into the same shape (50 × 8 × 2 mm3). The testing was carried out in three-point bending pattern mode at 1 Hz with the temperature in a range of 25°C–270°C in an air atmosphere.
3 Results and discussion
3.1 The influence of hot-pressing temperature
Hot-pressing temperature is an important factor to influence the curing process of phenolic resin, which affects the mechanical properties and thickness swelling of the rice straw/phenolic resin composites. As is shown in Figure 1, the region of temperature from 150°C to 170°C was selected to carry out the three-point bending test. The results presented that the static bending strength and elastic modulus at 150°C were 14.95 MPa and 1,606.53 MPa, and then static bending strength and elastic modulus increased to 15.25 MPa and 1783.61 MPa when the temperature increased to 160°C. The thickness swelling decreased from 15.3% to 10.2%. However, when the temperature increased from 160°C to 170°C, the static bending strength and elastic modulus decreased to 14.76 MPa and 1,695.68 MPa. At the same time, the thickness swelling increased from 10.2% to 12.8%. Therefore, the temperature of 160°C is the optimal hot-processing condition to fabricate the rice straw fiber/phenolic resin composites.
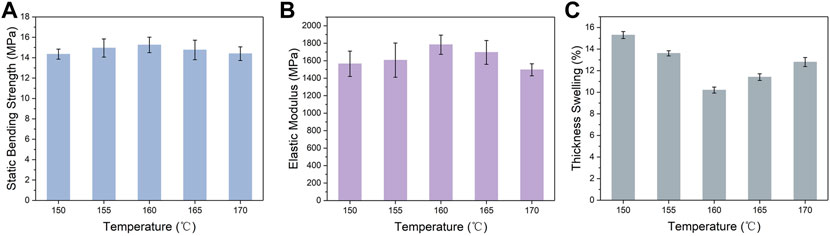
FIGURE 1. (A) Static bending strength of PF/SF. (B) Corresponding elastic modulus of PF/SF. (C) The thickness swelling of PF/SF. The fiber content is 50% and the hot-pressure time is 9 min.
3.2 The influence of hot-pressing time
Hot-pressing time is also an important factor for phenolic resin curing. The influence of hot-pressing time on the mechanical performance and thickness swelling of the rice straw/phenolic resin composites was also investigated in Figure 2. We can see that the static bending strength and elastic modulus were 14.68 MPa and 1,668.27 MPa with 7 min hot-pressing treatment. Then the static bending strength and elastic modulus increased to 17.32 MPa and 1981.98 MPa with the hot-pressing time increased to 11 min, and they became stable with a further extension of hot-pressing time. What’s more, the rice straw/phenolic resin composite showed the lowest thickness swelling at 11 min. Thus, 11 min was the optimal hot-pressing time for the preparation of the rice straw/phenolic resin composites.
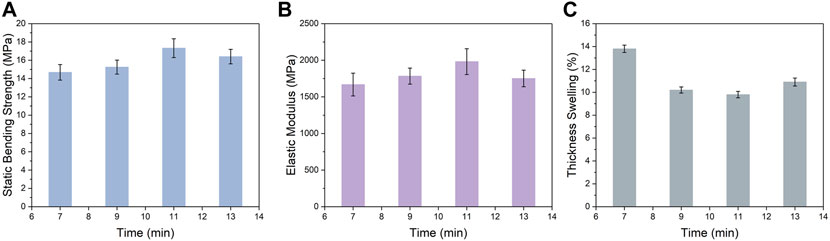
FIGURE 2. (A) Static bending strength of PF/SF. (B) Elastic modulus of PF/SF. (C) Corresponding thickness swelling of PF/SF. The fiber content is 50% and the hot-pressing temperature is 160°C.
3.3 The influence of the weight ratio of the rice straw/phenolic resin
The weight ratio of the rice straw fibers:phenolic resin has a significant influence on the mechanical properties and thickness swelling of the composites. As is shown in Figure 3, the static bending strength of the composites with the fiber content at 35% was 14.52 MPa. Then the static bending strength increased with increasing the fiber content and reach 17.33 MPa. However, when the fiber content increased to 55%, the static bending strength decreased to 15.56 MPa, mainly due to the aggregation of the fibers in the matrix of phenolic resin (Shah, 2013). The elastic modulus of the composites with the fiber content at 35% was 1724.93 MPa and increased to 1950.34 MPa with the fiber content increased to 55%. The thickness swelling of the composite increased from 7.2% to 12.5% with the fiber content increasing from 35% to 55%, indicating the water resistance decreased with decreasing the phenolic resin content.
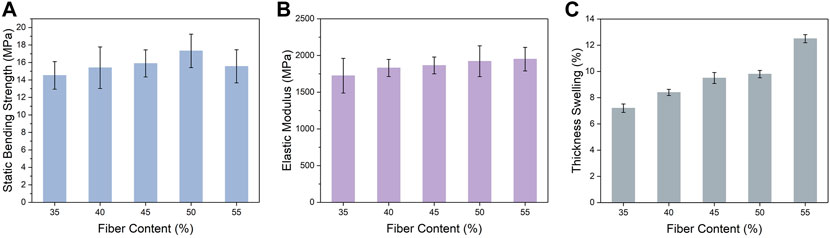
FIGURE 3. (A) Static bending strength of PF/SF. (B) Elastic modulus of PF/SF. (C) Thickness swelling of PF/SF. The hot-pressing temperature is 160°C and the hot-pressing time is 11 min.
3.4 FT-IR analysis of rice straw fibers
Rice straw fiber (SF) is mainly composed of three main natural polymers (cellulose, hemicellulose, and lignin). In order to study the influence of hydrothermal treatment, silane coupling agent modification, and enzyme treatment on the chemical structure of the SF surface, the samples were characterized by FT-IR. As shown in Figure 4, the FT-IR spectra of raw rice straw fiber show characteristic bands within the selected region, including a band at 3,450 cm−1 attributed to the stretching vibration absorption peak of the -OH group (Tan et al., 2022), a peak at 2970 cm−1for -CH2- stretching vibrations (Mo et al., 2019), the peaks at 1,600 cm−1 and 1,486 cm−1 corresponding to the skeleton vibration absorption of the aromatic ring of lignin (Cheng et al., 2016), and a peak at 1,055 cm−1 belonging to the characteristic absorption peak of the hemicellulose ether bond (Liang and Wang, 2017).
Compared with SF, the absorption peaks at 3,450 cm−1 and the absorption peak at 2970 cm−1 of lipase-treated fiber (L-SF) increased, indicating that the lipophilic substances on the surface of the SF were removed (Jiang et al., 2009). Therefore, the functional groups in cellulose, hemicellulose, and lignin could be fully exposed, which is beneficial to the formation of good interfacial bonding with the resin adhesive. For the S-SF, the enhancement of the -CH2-stretching vibration absorption peak at 2940 cm−1 and the characteristic absorption peak of the -O-Si- group at 1,019 cm−1 (Herrera-Franco and Valadez-Gonzalez, 2005), which proved the silane coupling agent was successfully introduced onto the SF. In the H-SF, the absorption peak intensities at 1,055 cm−1 and 1,019 cm−1 became weaker, presenting that the hydrothermal reaction result in the reduction of the hemicellulose and lignin, which may be beneficial to improve the interfacial adhesion between the rice straw fibers and the polymer matrix.
3.5 The influence of pretreatment
The interface compatibility between natural polymers and synthetic polymers is usually poor, which results in a relatively low mechanical strength. In order to improve the mechanical performance of the composite, many efforts have been reported to treat the surface of natural polymers with various approaches. In this work, three different approaches (silane modification, hydrothermal treatment and enzyme treatment) were used to treat the SF, and the static bending strength and elastic modulus of the rice straw/phenolic resin composites were also tested in Figure 5. For the PF/SF, the static bending strength and elastic modulus were 17.32 MPa and 1981.98 MPa. After hydrothermal treatment, the static bending strength and elastic modulus of the PF/H-SF were 18.94 MPa and 2096.85 MPa. The silane modification and enzyme treatment can also increase the mechanical performance of the PF/S-SF and PF/L-SF, and the static bending strength and elastic modulus were 20.44 MPa and 2362.33 MPa, and 23.03 MPa and 2588.39 MPa. What’s more, the thickness swelling of PF/H-SF (9.2%), PF/S-SF (8.6%), and PF/L-SF (7.9%) reduced significantly compared to the PF/SF (9.8%). It can be seen from the above results that the mechanical properties and thickness swelling of the rice straw/phenolic resin composites can be improved by the three different treatments of the SF. This is because the pretreatment can benefit their dispersion in the phenolic resin matrix by improving the interface compatibility.
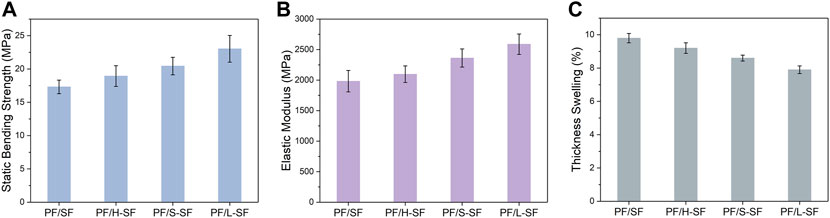
FIGURE 5. (A) Static bending strength of PF/SF, PF/H-SF, PF/S-SF, and PF/L-SF. (B) Elastic modulus of PF/SF, PF/H-SF, PF/S-SF, and PF/L-SF. (C) Thickness swelling of PF/SF, PF/H-SF, PF/S-SF, and PF/L-SF. The fiber content is 1:1, the hot-pressing condition is 160°C and 11 min.
3.6 DMA
DMA is an effective tool to investigate the interactions between the polymer matrix and fiber at different temperatures (Gupta and Singh, 2018). The storage modulus of PF/SF, PF/H-SF, PF/S-SF, and PF/L-SF was investigated in Figure 6. As is shown, the storage modulus of PF/SF, PF/H-SF, PF/S-SF, and PF/L-SF at room temperature (25°C) were 903.5 MPa, 1,583 MPa, 1,325 MPa, and 1,630 MPa, indicating the treatment of the SF can improve the interface compatibility between the fibers and the polymer matrix. Therefore, the treated fibers present better inhibition for the mobility of the phenolic resin molecule chain and resulted in the increased storage modulus. The storage modulus of PF/SF, PF/H-SF, PF/S-SF, and PF/L-SF decreased with increasing temperature. When the temperature is over 225°C, the storage modulus of the composites decreased dramatically because the composite start to degrade (Stevulova et al., 2016).
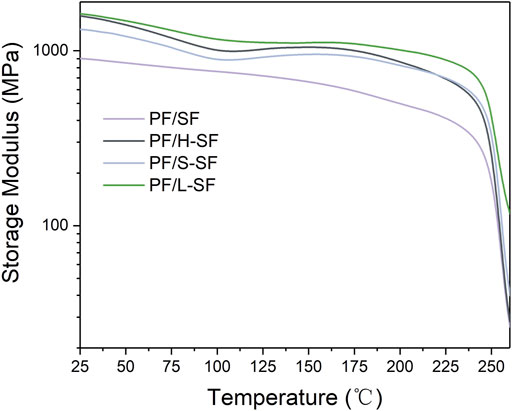
FIGURE 6. Storage modulus of PF/SF, PF/H-SF, PF/S-SF, and PF/L-SF at different temperatures with the fiber content at 50%.
4 Conclusion
In this work, the rice straw fibers were treated with the silane coupling agent, lipase, and hydrothermal successfully. The obtained fibers of SF, H-SF, S-SF, and L-SF were used to fabricate phenolic resin/straw fibers composites (PF/H-SF, PF/S-SF, and PF/L-SF), which presented improved static bending strength, elastic modulus, and thickness swelling compared to PF/SF. The static bending strength, elastic modulus, and thickness swelling of PF/L-SF were 23.03 MPa, 2588.39 MPa and 7.9%, which improved 33%, 30%, and 19% compared to that of PF/SF. The DMA results indicated that the pretreatment of the SF can improve the interface compatibility of the fibers and polymer matrix, and PF/L-SF showed the highest storage modulus with 1,630 MPa at room temperature (25°C). Therefore, this work provides green and high-efficiency routes for producing plant fiber/polymer composites with excellent performance on a large scale.
Data availability statement
The raw data supporting the conclusion of this article will be made available by the authors, without undue reservation.
Author contributions
SZ and XY contributed to the conception of the study; SZ and XC performed the experiment; SZ and RH contributed significantly to analysis and manuscript preparation; SZ performed the data analyses and wrote the manuscript; YL helped perform the analysis with constructive discussions.
Funding
This research was financially supported by the National Natural Science Foundation of China (No. 22008035) and the Natural Fujian Science Foundation National (No. 2020J05131).
Conflict of interest
The authors declare that the research was conducted in the absence of any commercial or financial relationships that could be construed as a potential conflict of interest.
Publisher’s note
All claims expressed in this article are solely those of the authors and do not necessarily represent those of their affiliated organizations, or those of the publisher, the editors and the reviewers. Any product that may be evaluated in this article, or claim that may be made by its manufacturer, is not guaranteed or endorsed by the publisher.
References
Bledzki, A., and Gassan, J. (1999). Composites reinforced with cellulose based fibres. Prog. Polym. Sci. 24, 221–274. doi:10.1016/S0079-6700(98)00018-5
Chandra, M., Kohn, C., Pawlitz, J., and Powell, G. (2016). Real cost of styrofoam. Missouri: St. Louis University.
Cheng, S., Huang, A., Wang, S., and Zhang, Q. (2016). Effect of different heat treatment temperatures on the chemical composition and structure of Chinese fir wood. BioResources 11, 4006–4016. doi:10.15376/biores.11.2.4006-4016
Chinthapalli, R., Skoczinski, P., Carus, M., Baltus, W., de Guzman, D., Käb, H., et al. (2019). Biobased building blocks and polymers—Global capacities, production and trends. Ind. Biotechnol. New. Rochelle. N. Y). 15, 237–241. doi:10.1089/ind.2019.29179.rch
Cressey, D. (2016). Bottles, bags, ropes and toothbrushes: The struggle to track ocean plastics. Nature 536, 263–265. doi:10.1038/536263a
Cywar, R. M., Rorrer, N. A., Hoyt, C. B., Beckham, G. T., and Chen, E. Y.-X. (2022). Bio-based polymers with performance-advantaged properties. Nat. Rev. Mat. 7, 83–103. doi:10.1038/s41578-021-00363-3
De France, K., Zeng, Z., Wu, T., and Nyström, G. (2021). Functional materials from nanocellulose: Utilizing structure–property relationships in bottom‐up fabrication. Adv. Mat. 33, 2000657. doi:10.1002/adma.202000657
Edeerozey, A. M., Akil, H. M., Azhar, A., and Ariffin, M. Z. (2007). Chemical modification of kenaf fibers. Mat. Lett. 61, 2023–2025. doi:10.1016/j.matlet.2006.08.006
Geyer, R., Jambeck, J. R., and Law, K. L. (2017). Production, use, and fate of all plastics ever made. Sci. Adv. 3, e1700782. doi:10.1126/sciadv.1700782
Guan, Q. F., Yang, H. B., Zhao, Y. X., Han, Z. M., Ling, Z. C., Yang, K. P., et al. (2021). Microplastics release from victuals packaging materials during daily usage. EcoMat 3, e12107. doi:10.1002/eom2.12107
Gupta, M., and Singh, R. (2018). Flexural and dynamic mechanical analysis (DMA) of polylactic acid (PLA) coated sisal fibre reinforced polyester composite. Mater. Today Proc. 5, 6109–6114. doi:10.1016/j.matpr.2017.12.216
Herrera-Franco, P., and Valadez-Gonzalez, A. (2005). A study of the mechanical properties of short natural-fiber reinforced composites. Compos. Part B Eng. 36, 597–608. doi:10.1016/j.compositesb.2005.04.001
Jiang, H., Zhang, Y., and Wang, X. (2009). Effect of lipases on the surface properties of wheat straw. Ind. Crops Prod. 30, 304–310. doi:10.1016/j.indcrop.2009.05.009
Li, T., Song, J., Zhao, X., Yang, Z., Pastel, G., Xu, S., et al. (2018). Anisotropic, lightweight, strong, and super thermally insulating nanowood with naturally aligned nanocellulose. Sci. Adv. 4, eaar3724. doi:10.1126/sciadv.aar3724
Liang, T., and Wang, L. (2017). Thermal treatment of poplar hemicelluloses at 180 to 220 C under nitrogen atmosphere. BioResources 12, 1128–1135. doi:10.15376/biores.12.1.1128-1135
Liu, C., Luan, P., Li, Q., Cheng, Z., Sun, X., Cao, D., et al. (2020). Biodegradable, hygienic, and compostable tableware from hybrid sugarcane and bamboo fibers as plastic alternative. Matter 3, 2066–2079. doi:10.1016/j.matt.2020.10.004
Mo, L., Pang, H., Tan, Y., Zhang, S., and Li, J. (2019). 3D multi-wall perforated nanocellulose-based polyethylenimine aerogels for ultrahigh efficient and reversible removal of Cu (II) ions from water. Chem. Eng. J. 378, 122157. doi:10.1016/j.cej.2019.122157
Nanda, S., Azargohar, R., Dalai, A. K., and Kozinski, J. A. (2015). An assessment on the sustainability of lignocellulosic biomass for biorefining. Renew. Sustain. Energy Rev. 50, 925–941. doi:10.1016/j.rser.2015.05.058
Peplow, M. (2016). The plastics revolution: How chemists are pushing polymers to new limits. Nature 536, 266–268. doi:10.1038/536266a
Shah, D. U. (2013). Developing plant fibre composites for structural applications by optimising composite parameters: A critical review. J. Mat. Sci. 48, 6083–6107. doi:10.1007/s10853-013-7458-7
Stevulova, N., Hospodárova, V., and Estokova, A. (2016). Study of thermal analysis of selected cellulose fibres. Geosci. Eng. 62, 18–21. doi:10.1515/gse-2016-0020
Sui, G., Fuqua, M., Ulven, C., and Zhong, W. (2009). A plant fiber reinforced polymer composite prepared by a twin-screw extruder. Bioresour. Technol. 100, 1246–1251. doi:10.1016/j.biortech.2008.03.065
Tan, L., Zhang, W., Zhu, X., Ru, Y., Yi, W., Pang, B., et al. (2022). Porous fibrous bacterial cellulose/La(OH)3 membrane for superior phosphate removal from water. Carbohydr. Polym. 298, 120135. doi:10.1016/j.carbpol.2022.120135
Thompson, R. C., Moore, C. J., Vom Saal, F. S., and Swan, S. H. (2009). Plastics, the environment and human health: Current consensus and future trends. Phil. Trans. R. Soc. B 364, 2153–2166. doi:10.1098/rstb.2009.0053
Torres, F., and Cubillas, M. (2005). Study of the interfacial properties of natural fibre reinforced polyethylene. Polym. Test. 24, 694–698. doi:10.1016/j.polymertesting.2005.05.004
Xia, Q., Chen, C., Yao, Y., Li, J., He, S., Zhou, Y., et al. (2021). A strong, biodegradable and recyclable lignocellulosic bioplastic. Nat. Sustain. 4, 627–635. doi:10.1038/s41893-021-00702-w
Yu, Y., Guo, Z., Zhao, Y., Kong, K., Pan, H., Xu, X., et al. (2022). A flexible and degradable hybrid mineral as a plastic substitute. Adv. Mat. 34, 2107523. doi:10.1002/adma.202107523
Zhang, W., Han, X., You, J., Zhang, X., Pei, D., Willför, S., et al. (2022a). Rapid and manual-shaking exfoliation of amidoximated cellulose nanofibrils for a large-capacity filtration capture of uranium. J. Mat. Chem. A 10, 7920–7927. doi:10.1039/D1TA10357A
Keywords: straw fiber, phenolic resin, composite, strength, thickness swelling
Citation: Zhou S, Chen X, Huang R, Lin Y and Ye X (2022) Interfacial treatment-induced high-strength plant fiber/phenolic resin composite. Front. Mater. 9:1072249. doi: 10.3389/fmats.2022.1072249
Received: 17 October 2022; Accepted: 24 October 2022;
Published: 03 November 2022.
Edited by:
Bo Pang, Stockholm University, SwedenReviewed by:
Xiankai Li, Qingdao University, ChinaWeihua Zhang, Sichuan University, China
Haishun Du, University of Wisconsin-Madison, United States
Copyright © 2022 Zhou, Chen, Huang, Lin and Ye. This is an open-access article distributed under the terms of the Creative Commons Attribution License (CC BY). The use, distribution or reproduction in other forums is permitted, provided the original author(s) and the copyright owner(s) are credited and that the original publication in this journal is cited, in accordance with accepted academic practice. No use, distribution or reproduction is permitted which does not comply with these terms.
*Correspondence: Xiaoxia Ye, eWV4aWFveGlhQGZ6dS5lZHUuY24=