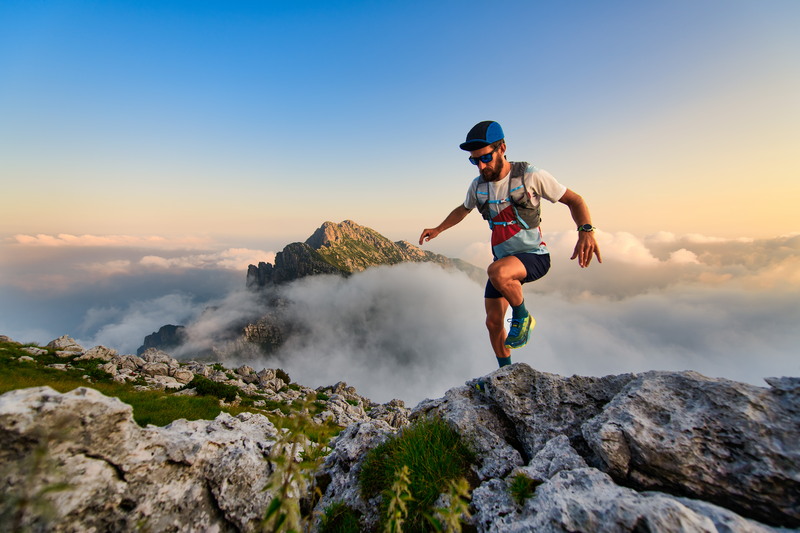
95% of researchers rate our articles as excellent or good
Learn more about the work of our research integrity team to safeguard the quality of each article we publish.
Find out more
MINI REVIEW article
Front. Mater. , 09 November 2022
Sec. Environmental Degradation of Materials
Volume 9 - 2022 | https://doi.org/10.3389/fmats.2022.1058394
This article is part of the Research Topic Nuclear Materials Degradation View all 6 articles
A large amount of nuclear waste produced in the process of nuclear energy utilization has always been a key problem to be solved urgently for nuclear safety. At present, “deep geological disposal” is a feasible method and is generally accepted by many countries. It is a “multi-barrier system” composed of an artificial barrier, including the solidified waste body, outer packaging material, buffer backfill material, and a natural barrier including the surrounding rock. During deep geological disposal, a near-field environment, where the corrosion of a container could happen, is formed with continuous groundwater infiltration and the release of much heat energy in the process of nuclear waste decay and fission. At the same time, the environment will become a long-term reduction place because of the gradual consumption of the initially retained oxygen. The hydrogen evolution reaction is dominant, so unpredictable hydrogen embrittlement of the container materials could happen due to hydrogen absorption and penetration. This study summarizes the possibility of hydrogen embrittlement of carbon steel, titanium, and their alloys from three aspects, namely, hydrogen solubility, diffusion coefficient, and hydrogen embrittlement, which provides a theoretical basis for predicting the container life in a large time scale.
Generally, it takes a long period about hundreds of thousands of years after the nuclear waste container is buried for deep geological disposal. With the increasing time, groundwater continues to infiltrate the nuclear waste container. After the buffer backfill material reaches saturation, the container will be completely exposed to groundwater, resulting in exposure to the environment where the corrosion of the container could happen. According to the evolution law of the oxygen content at the interface between the metal container and buffer backfill material, it can be found that oxygen will be continuously consumed with the progression of the corrosion reaction after the container is buried, which will promote the progression of the hydrogen evolution reaction (Huang et al., 2018). The reduction of hydrogen ions even under the condition of aerobic corrosion was well-studied, and they have shown that there will be reduction of hydrogen ions even under the condition of aerobic corrosion (Huang and Zhu, 2005; Tsuru et al., 2005). Therefore, hydrogen permeation into metal container materials is accompanied by the whole process of corrosion. There are several basic steps of the hydrogen evolution reaction (Dafft et al., 1979), and the reaction formulas are as follows:
The reaction formulae refer to 1) the adsorption of hydrogen, 2) the recombination with hydrogen to form hydrogen molecules, and 3) some adsorbed H atoms that may be absorbed into the lattice.
During the service life of the container, it will suffer from the coupling action of heat-water stress. The low carbon steel and titanium alloy may also be damaged by strong crustal movements such as earthquake, even when they are generally considered to show the reduction of plasticity in the slow strain tensile test under hydrogen charging due to low sensitivity to stress corrosion and hydrogen embrittlement. There is a risk of hydrogen embrittlement because of the influence dominated by the hydrogen evolution reaction. Therefore, it is necessary to study hydrogen permeation, medium- and long-term hydrogen absorption, and hydrogen embrittlement behavior of the metal container, especially the safety evaluation of container materials by researching hydrogen absorption and hydrogen concentration distribution in a large time scale. The continuous consumption of oxygen showed that the hydrogen evolution reaction will dominate the cathodic reaction in corrosion. The research shows that oxygen will be exhausted in a year at the earliest (Yang et al., 2007). Some factors accelerate the consumption of oxygen, such as oxygen absorption corrosion, rock dissolution, and oxidation of methane in bentonite. After that, the hydrogen generated by the hydrogen evolution reaction will accumulate with the disposal year. For carbon steel, hydrogen diffuses fast so that a lot of hydrogen can escape. However, hydrogen will react with titanium, and hydrides are formed. The titanium hydrides show brittleness. Once the amount of hydrides accumulated through disposal time after oxygen exhausted reaches a certain degree, the titanium container may suffer from hydrogen embrittlement.
Shoesmith assessed the corrosion performance of high-level nuclear waste containers and summarized different models of the container’s materials, including the general corrosion model and the local corrosion model (Shoesmith, 2006). However, there is no research about the hydrogen embrittlement model of container materials. The article mainly summarized the possibility of hydrogen embrittlement of carbon steel, titanium, and their alloys from three aspects: hydrogen solubility, diffusion coefficient, and hydrogen permeation. This affords the basis for the hydrogen embrittlement model.
At present, it is well known that the solubility of hydrogen basically does not depend on the purity of iron and the existence of grain boundaries and dislocations in different microstructures. For pure iron, it is known that the body-centered cubic (bcc) and face-centered cubic (fcc) lattices provide different gap positions for hydrogen residence. The dense structure of fcc iron can provide a large single-gap space at the octahedral site, which is the most favorable position occupied by hydrogen and has a higher lattice solubility than bcc. The small position of a single gap in the bcc lattice leads to the low solubility of hydrogen, but the large number of gaps in the bcc lattice provide a path for the rapid diffusion of hydrogen through the lattice.
Hydrogen atoms are slightly larger than all gaps, so the lattice requires additional energy to hold the hydrogen atoms. Due to the endothermic characteristics of hydrogen dissolution in these two lattices, heat promotes the dissolution of hydrogen in bcc and fcc iron (Wei and Tsuzaki, 2012). Silva and Mclellan (1976) first measured that the solubility of hydrogen in iron at room temperature was less than 10–6 (hydrogen atom/iron atom). It fitted the formula of the relationship between solubility and temperature:
where θ = NH/NF and x = 104/T. NH/NFe represents the ratio of the number of hydrogen atoms dissolved in iron to the number of iron atoms per unit volume.
Kiuchi et al. (1986) found that the solubility of hydrogen in bcc iron does not follow the strict linear relationship with the reciprocal of temperature but shows a slight deviation in the low temperature range. Therefore, solubility cannot be accurately expressed in the form of Arrhenius equation based on their theory that the pre-exponential factor contains T4/7. They also pointed out that hydrogen occupying tetrahedral positions mostly occurs at low temperatures. However, it is more likely to occupy octahedral positions above about 100°C. Hirth (1980) suggested that the most reliable method is to express the solubility of hydrogen in the bcc lattice in the exponential form. The solubility of hydrogen is expressed in atomic fraction. The equation is as follows:
where P is the pressure of hydrogen, Hs (= 28.6 kJ mol−1) is the heat of dissolution, R is the gas constant, and T is the absolute temperature. When the pressure is too high (above about 20 MPa), P should be replaced by fugacity.
The results obtained from these studies are closely related to the experimental methods and conditions.
According to the source of hydrogen, hydrogen in titanium is divided into two kinds: internal hydrogen and external hydrogen (Cui and Peng, 2003).
Internal hydrogen exists before titanium is used. It is procured mainly from the hydrogen absorbed by materials in smelting, thermal process, and other processes (Zhu, 1989; Cui and Peng, 2003). The internal hydrogen solubility in α-Ti at room temperature is between 20 and 150 ppm. External hydrogen refers to hydrogen that enters the material from the external environment during usage. There is a critical value for the external hydrogen content. If hydrogen absorption reaches this critical level, hydrides will be formed on the titanium surface. The brittleness and elastic properties of hydrides are different from the parent lattice. The standard Gibbs enthalpy of titanium–hydrogen compound formation is negative, that is, titanium–hydrogen compounds are easy to form through thermodynamic analysis. The atomic ratio of hydrogen to titanium (H/Ti) in titanium hydride (TiHx) is related to the diffusion flux of hydrogen atoms, so TiHx obtained under different experimental conditions is not the same. Yan et al. (2006) calculated that its average atomic ratio (H/Ti) is close to 1.6 and 1.8 (except for the minimum hydrogen charging current density of 0.5 mA cm−2). Millenbach and Givon (1982) measured the atomic ratio (H/Ti) between 1.62 and 1.78 at a higher current density (5 mA cm−2–20 mA cm−2) by X-ray diffraction. However, Phillips et al. (1972) calculated that H/Ti in hydride increased from 1.2 to 1.5 (in 0.05 mol L−1 H2SO4) at an applied hydrogen charging current density of 0.05 mA cm-2–3.0 mA cm−2. Zhang et al. (2019) carried out hydrogen charging in 0.05 mol L−1 H2SO4 solution and simulated Beishan groundwater solution, respectively, with an applied current density of 1 mA cm−2. The X-ray diffraction result showed that H/Ti was 1.5. According to the titanium–hydrogen phase diagram (Cui and Peng, 2003), as shown in Figure 1, it is easier to understand the structure of titanium hydride. The γ-hydride has fcc crystal cells relative to titanium atoms, and the hydrogen atoms are randomly distributed in the tetrahedral gap (CaF2 structure). For the high hydrogen concentration close to the limit component 2 of H/Ti, the hydride changes to a tetragonal structure at lower temperature. In the lower concentration region, the hydrogen intrinsic solubility in the α-phase is basically small at room temperature, so hydrides often appear in pure titanium (Numakura and Koiwa, 1984).
FIGURE 1. Titanium–hydrogen phase diagram (Cui and Peng, 2003).
Numakura and Koiwa (1984) showed that titanium hydride can form three different crystal structures and morphologies in the titanium alloy at a low temperature range of 40°C–60°C, depending on different values of X in TiHx: a hydride with a low hydrogen concentration (TiH0-1.5) (ordered face-centered tetragonal structure); a hydride with a medium hydrogen concentration (TiH1.5-1.9) (face-centered cubic structure); and a hydride with a high hydrogen concentration (TiH1.9-2.0) (face-centered tetragonal structure). Panin et al. (2003) believed that TiH2 has a face-centered cubic structure, and Ti is at the node. Titanium hydride is a gray powder, which is stable in air. This hydride can be completely dehydrogenated at about 1,000°C (Huang et al., 2006). According to the dissociation, heat of the hydride between TiH1.75 and TiH1.93 is obtained as follows:
Because the phase diagram of titanium hydrogen is relatively complex, there are still some new thermodynamic characteristics to be found (Aronsson et al., 2001).
Kiuchi et al. (1986) analyzed a large number of hydrogen diffusion data comprehensively measured by various methods, indicating that the most representative equation of the hydrogen diffusion coefficient is as follows:
The temperature range for Eq. 8 is −40°C to 80°C and that for Eq. 9 is 50°C–550°C.
Figure 2 summarizes the current diffusion coefficient of hydrogen in iron. The regions A and B correspond to Eqs 8, 9, respectively. However, the diffusion coefficients of regions C and D are much smaller than those calculated by Eqs 8, 9. In the normal lattice of bcc iron, the diffusion of hydrogen is so high that the measurement of hydrogen diffusivity is easily affected by the surface state and hydrogen traps at the defects in the lattice. The true hydrogen diffusion characteristics can only be measured when these external effects are eliminated. Therefore, the lattice defects and/or surface contamination result in regions C and D. At the same time, regions C and D reflect the diffusion coefficients obtained in the presence of surface state effects and hydrogen traps, respectively.
FIGURE 2. Hydrogen diffusivity in bcc iron (Kiuchi et al., 1986).
There are few data on the diffusion coefficient of hydrogen in titanium. Wasilewski and Kehl (1954) measured the hydrogen diffusion coefficient in α-titanium in the 1950s at the temperature range of 500°C–824°C as follows:
Papazoglou and Hepworth (1968) also researched the diffusion coefficient equation in the 1960s as follows:
Obviously, there is a linear relationship between LnD and 1/T, and the difference between the two groups of data may result from different experimental methods. Wasilewski and Kehl prepared the β-Ti surface layer on the α-Ti film based on hydrogen stabilization in the β-phase. The surface layer saturated with hydrogen is then used as the interior constant hydrogen source of the α-phase. Papazoglou and Hepworth introduced hydrogen directly from the gas phase to the α-phase at a sufficiently low pressure to prevent β-phase formation. Christ et al. (2000) also believed that the diffusion coefficient of hydrogen in the titanium alloy is independent of the hydrogen concentration in the sample and follows the Arrhenius equation. Hydrogen diffusion in the α-phase of the titanium alloy is slow, but in the stable β-phase, it is relatively fast. This difference is most significant at low temperature and decreases with the increasing temperature. Miyoshi et al. (1996) studied the diffusion of hydrogen in titanium, Ti88Al12, and Ti3Al and found that the pre-exponential factor and activation energy of the diffusion coefficient increased with the increasing aluminum content. Johnson and Nelson (1973) used a mass spectrometer to measure the hydrogen flow through the sample at a temperature of 400°C–800°C and a hydrogen pressure of 0.004–2.0 torr. Gaseous hydrogen and a hollow cylinder sample were used to make hydrogen penetrate from the inner surface of the sample and diffuse from the outer surface. The equation is as follows:
where P is the hydrogen pressure and the unit of osmotic activation energy is cal·mol−1.
Bustard et al. (1980) studied the effect of hydrogen on the diffusion mechanism in the γ-phase of titanium hydride at the temperature range of 400°C–600°C. According to the measurement result of spin lattice relaxation time T1, it can be determined that the average sojourn time among the atomic jump is τd. These two factors are related to the jump length L and the tracer correlation factor fT:
It is found that the ratio of the pre-exponential factor is 9.7/6.1 = 1.59, which is in good agreement with the vacancy concentration ratio of 1.55. Stalinski and CooganGutowsky (1961) pointed out that there was a direct proportional relationship between the pre-exponential factor and vacancy concentration (2-x) in the γ-phase of TiHx.
The aforementioned hydrogen diffusion coefficients in titanium and its alloys are obtained at high temperatures (at least 400°C), while there are few studies at low temperature. The hydrogen diffusion coefficients at low temperature are basically extrapolated from the diffusion coefficient equation obtained at high temperature. Some studies showed that the hydrogen diffusion coefficient at low temperature obtained by this method is not reliable (Malyshev et al., 1982). Wipf et al. (1999) showed that hydrogen diffusion in titanium has tunnel diffusion at low temperatures. The diffusion behavior of hydrogen in titanium and its alloys at low temperature is very complex. In order to obtain a more accurate hydrogen diffusion coefficient, further research is needed.
The hydrogen evolution reaction usually occurs in the corrosion process in the acidic or poorly ventilated environment, excessive polarization caused by cathodic protection, and pitting corrosion of steel (Neretnieks, 1985a). Therefore, hydrogen absorption is likely to occur in this deep geological environment. The main sources include hydrogen introduced during the production and anaerobic corrosion of iron in a steel container during disposal. It is generally believed that hydrogen produced by anaerobic corrosion of iron is the largest source (Neretnieks, 1985a; Ortiz et al., 2002), and the reaction formulas are as follows:
OH− produced in reaction Eq. 15 may be involved in carbonate or hydroxide deposition, such as reaction Eq. 16. Reardon (1995) believes that Fe (OH)2 is metastable in the anaerobic groundwater environment and is converted to magnetite (Fe3O4) according to Shikorr reaction thermodynamics, as shown in reaction Eq. 17. The reactions in Eqs. 15, 16, 17 are combined to obtain the total reaction, as shown in Eq. 18. Neretnieks (1985b) predicted when the H2 partial pressure is increased to more than 40 MPa, the gas production stopped from a thermodynamic point of view. Similar to the dissolution and precipitation of common mineral phases in geochemical simulation, Lasaga et al. (1994) adopted the transition-state rate method to express the kinetic rate for Fe dissolution and magnetite precipitation:
Here, r represents the kinetic rate (the positive value indicates dissolution, and the negative value indicates precipitation), k represents the rate constant (moles per unit mineral surface area and unit time), A is the total reaction surface area of the steel container, K is the equilibrium constant of the mineral–water reaction, and Q is the reaction quotient.
The release of chemical components from waste, bentonite buffer, and clay may affect iron corrosion and gas generation. For example, the solid treatment of nuclear waste (glass solidified body) can reduce its probability of entering the biosphere, and the Si released from the waste glass can be adsorbed on the surface of Fe magnetite and other corrosion products (Philippini et al., 2006). However, Lapuerta et al. (2007) believed that the current corrosion model only considers the oxidation of Fe in water, but this effect (hydrolysis) may also occur under reducing conditions. H2 produced by the radiation decomposition of water is not considered.
Hydrogen-induced cracking will occur when the combined action of the hydrogen content, stress, and strain reaches a certain degree, including hydrogen-induced cracking (HIC) without an external force and hydrogen-induced cracking (SOHIC) under an external force. The basic concept of the hydrogen pressure mechanism is that hydrogen atoms recombine molecular hydrogen at the internal voids or cracks. These voids may be cavities formed at the interface during production. In the presence of stress, they expand the micro-pores that the strain concentration has at the base metal, particles or the Fe3C/ferrite phase boundary, and the hydrogen trapped at the interface. If there is a significant hydrostatic stress component around the interface, the hydrogen concentration may be further enhanced. If enough hydrogen escapes into the gap, the pressure reaching the gap may be large enough to produce cracks (Turnbull, 2009). In the absence of significant stress, these HIC cracks connect the crack tips through shear fracture in the 45°C direction, thus forming a stepped appearance, which is called step-by-step cracking. However, if there is residual stress or external stress, the effect of stress not only promotes the local accumulation of hydrogen but also changes the connection mode between cracks. In this case, the connected cracks tend to form laminations (nearly stepped shape) because the position of the maximum shear stress moves from the tip of the crack to the middle (Iino, 1978; Dewsnap and Jones, 1986; Pargeter, 2007). The HIC growth rate depends on the rate of hydrogen diffusing to voids/cracks. This depends on the hydrogen capture characteristics of steel, including the density and volume of voids/cracks, which will change over time. At present, there is still no reliable model to quantitatively predict the crack growth rate, but the in-depth insight on the microstructure can qualitatively predict which microstructure characteristics are easy to cause cracks (Turnbull, 2009).
The sources of hydrogen in the titanium container mainly contain hydrogen introduced during production and hydrogen precipitated by electrochemical corrosion during disposal (Wei et al., 2013). There are two effects of hydrogen on the mechanical properties for titanium alloys (Shen and Feng, 2000). These are the influences caused by the existence of inherently dissolved hydrogen and the change of the phase composition and microstructure caused by the hydrogen entry, that is, the formation of hydride.
Generally, the essence of hydrogen embrittlement for titanium is caused by titanium hydride, which is related to the shape and distribution of the hydride. Its structure also affects the hydrogen embrittlement of different titanium alloys. For example, the β-Ti alloy is more sensitive to hydrogen embrittlement than the α-Ti alloy (the former is a body-centered cubic structure, and the latter is a closely packed hexagonal structure) (Shen and Feng, 2000). Schutz (1987) believed that there are three main factors affecting hydrogen embrittlement of the titanium alloy: 1) there is a mechanism of continuous generation of new atomic hydrogen on the titanium surface (such as corrosion); 2) the reaction temperature is higher than 80°C, and the diffusion hydrogen rate of α-Ti is more significant; and 3) the pH value is lower than 3 or higher than 12, or the applied potential is more negative than −0.70v (vs. SCE). The HIC of titanium and its alloys can be avoided by eliminating one or more of the three factors (Hua et al., 2005).
Studies have shown that there is a critical hydrogen concentration, HC. Once the critical hydrogen concentration is exceeded, the fracture toughness of TA2 and TA12 will be significantly affected (Clarke et al., 1995; Clarke et al., 1997).
Sorensen (1990) drew the conclusion that only when the hydrogen content in TA12 is greater than 500 μg g−1, loss of ductility will occur. Also, the premise is that other factors are basically the same, such as the appearance of the β-phase. The critical concentration, HC, depends on the strength of the material. Materials with lower strength are more resistant to hydrogen (Clarke et al., 1997). According to the current research results, the critical hydrogen content (HC) of TA2 is between 500 μg g-1 and 800 μg g−1; the critical hydrogen content (HC) of TA12 is between 400 μg g-1 and 600 μg g−1; and the critical hydrogen content (HC) of TA16 is between 1,000 μg g-1 and 2000 μg g−1 (Clarke et al., 1994; Clarke et al., 1995; Ikeda and Quinn, 1998).
However, there are still some problems to solve for hydrogen embrittlement of container materials in deep geological disposal. First, the source of hydrogen needs to be solved before hydrogen embrittlement is studied. It is still not clear. In addition to general corrosion, there may be radiation decomposition of groundwater and microbial effects. Second, the prediction of the hydrogen content is based on the corrosion rate of container materials in a large time scale. Therefore, it is very important to estimate the corrosion rate. Meanwhile, whether local corrosion will affect HE sensitivity of container materials still remains unclear. Last, the problem about hydrogen embrittlement of the metal container in a deep geological environment is mainly the difficulty to predict the hydrogen content accumulated after long-term disposal in the deep geological environment, and it is uncertain whether there is a risk of hydrogen embrittlement before reaching the expected service life. Therefore, it is necessary to carry out more in-depth research on this basis.
Because of the continuous consumption of oxygen, the cathodic reaction of corrosion changes from oxygen absorption to hydrogen evolution, and the nuclear waste metal container has the possibility of hydrogen embrittlement in deep geological disposal for a long time. However, the mechanism of hydrogen embrittlement in different metal containers is different. Due to the rapid diffusion rate of hydrogen in carbon steel, carbon steel will show hydrogen embrittlement sensitivity only when it exists in carbon steel for a long time. For titanium and its alloys, hydrogen will react on its surface to form titanium hydride. Once the hydrogen concentration reaches a certain level, it shows hydrogen embrittlement sensitivity, although titanium hydrides will hinder the diffusion of hydrogen.
The original contributions presented in the study are included in the article/supplementary material. Further inquiries can be directed to the corresponding authors.
QZ has written the draft. YJ provided guidance. Other authors completed the revised manuscript.
This work was financially supported by the Natural Science Foundation of Shandong Province under Grant <No. ZR2022QE131>.
The authors declare that the research was conducted in the absence of any commercial or financial relationships that could be construed as a potential conflict of interest.
All claims expressed in this article are solely those of the authors and do not necessarily represent those of their affiliated organizations, or those of the publisher, the editors, and the reviewers. Any product that may be evaluated in this article, or claim that may be made by its manufacturer, is not guaranteed or endorsed by the publisher.
Aronsson, B.‐O., Hjörvarsson, B., Frauchiger, L., Taborelli, M., Vallotton, P. H., and Descouts, P. (2001). Hydrogen desorption from sand-blasted and acid-etched titanium surfaces after glow-discharge treatment. J. Biomed. Mat. Res. 54 (1), 20–29. doi:10.1002/1097-4636(200101)54:1<20::aid-jbm3>3.0.co;2-z
Bustard, L. D., Cotts, R. M., and Seymour, E. F. W. (1980). Determination of the hydrogen diffusion mechanism inγ-titanium hydride using nuclear magnetic resonance. Phys. Rev. B 22 (1), 12–20. doi:10.1103/physrevb.22.12
Christ, H. J., Decker, M., and Zeitler, S. (2000). Hydrogen diffusion coefficients in the titanium alloys IMI 834, Ti 10-2-3, Ti 21 S, and alloy C. Metall. Mat. Trans. A 31 (6), 1507–1517. doi:10.1007/s11661-000-0161-8
Clarke, C. F., Hardie, D., and Ikeda, B. M. (1995). Hydrogen induced cracking of Grade-2 titanium[R]. Chalk River, Canada: Atomic Energy of Canada Ltd.
Clarke, C. F., Hardie, D., and Ikeda, B. M. (1997). Hydrogen-induced cracking of commercial purity titanium. Corros. Sci. 39 (9), 1545–1559. doi:10.1016/s0010-938x(97)00055-3
Clarke, C. F., Hardie, D., and Ikeda, B. M. (1994). The effect of hydrogen content on the fracture of pre-cracked titanium specimens. Corros. Sci. 36 (3), 487–509. doi:10.1016/0010-938x(94)90039-6
Cui, C. J., and Peng, Q. (2003). Study on hydrogen permeation process in titanium and Ti alloys[J]. Rare Metal Mater. Eng. 32 (12), 1011–1015.
Dafft, E. G., Bohnenkamp, K., and Engell, H. J. (1979). Investigations of the hydrogen evolution kinetics and hydrogen absorption by iron electrodes during cathodic polarization. Corros. Sci. 19 (7), 591–612. doi:10.1016/s0010-938x(79)80130-4
Dewsnap, R. F., and Jones, C. L. (1986). A review of information on hydrogen induced cracking and sulphide stress corrosion cracking in linepipe steels[J]. United States: National Academies of Sciences, Engineering, and Medicine.
Hirth, J. P. (1980). Effects of hydrogen on the properties of iron and steel. Metall. Trans. A 11 (6), 861–890. doi:10.1007/bf02654700
Hua, F., Pasupathi, P., Shoesmith, D., and Gordon, G. (2005). A Review of corrosion of titanium grade 7 and other titanium alloys in nuclear waste repository environments. J. Corros. Houst. Tx- 61 (10), 987–1003. doi:10.5006/1.3280899
Huang, G., Cao, X. H., and Long, X. G. (2006). Physical and chemical properties of titanium-hydrogen system[J]. Mater. Rev. 20 (10), 128–131. doi:10.3321/j.issn:1005-023X.2006.10.032
Huang, Y. L., Zheng, M., Zhang, Q. C., Lu, D. Z., Wang, X. T., Hans-Jrg, K., et al. (2018). Forecast on long term chemical environment evolution on surface of nuclear waste container[J]. Equip. Environ. Eng. 15 (10), 6. doi:10.7643/issn.1672-9242.2018.10.017
Huang, Y. L., and Zhu, Y. Y. (2005). Hydrogen ion reduction in the process of iron rusting. Corros. Sci. 47 (6), 1545–1554. doi:10.1016/j.corsci.2004.07.044
Iino, M. (1978). The extension of hydrogen blister-crack array in linepipe steels. Metall. Trans. A 9 (11), 1581–1590. doi:10.1007/bf02661940
Ikeda, B. M., and Quinn, M. J. (1998). Hydrogen assisted cracking of grade-16 titanium: A preliminary examination of behaviour at room temperature[J] Ontario Hydro.
Johnson, D. L., and Nelson, H. G. (1973). Determination of hydrogen pęrmeation parameters in alpha titanium using the mass spectrometer. Metall. Trans. 4 (2), 569–573. doi:10.1007/bf02648711
Kiuchi, K., and Mclellan, R. B. (1986). “Overview No. 27 – the solubility and diffusivity of hydrogen in well-annealed and deformed iron [J],” in Perspectives in hydrogen in metals. Editors M. F. Ashby, and J. P. Hirth (Amsterdam, Netherlands: Elsevier), 29–52.
Lapuerta, S., Millard-Pinard, N., Moncoffre, N., Bererd, N., Jaffrezic, H., Brunel, G., et al. (2007). Origin of the hydrogen involved in iron corrosion under irradiation [J]. Surf. Coatings Technol. 201 (19–20), 8197–8201. doi:10.1016/j.surfcoat.2006.01.094
Lasaga, A. C., Soler, J. M., Ganor, J., Burch, T. E., and Nagy, K. L. (1994). Chemical weathering rate laws and global geochemical cycles. Geochimica Cosmochimica Acta 58 (10), 2361–2386. doi:10.1016/0016-7037(94)90016-7
Malyshev, L. G., Lebedev, S. A., Ryabov, R. A., Gel'd, P. V., and Kuznetsov, S. A. (1982). Hydrogen diffusion in titanium at room temperature. Soviet Phys. J. 25 (3), 232–235. doi:10.1007/bf00891692
Millenbach, P., and Givon, M. (1982). The electrochemical formation of titanium hydride. J. Less Common Metals 87 (2), 179–184. doi:10.1016/0022-5088(82)90086-8
Miyoshi, T., Naito, S., Yamamoto, M., Doi, M., and Kimura, M. (1996). Diffusion of hydrogen in titanium, Ti88Al12 and Ti3Al. Faraday Trans. 92 (3), 483–486. doi:10.1039/ft9969200483
Neretnieks, I. (1985). Some aspects on the use of iron canisters for HLW. MRS Proc. 50, 411. doi:10.1557/proc-50-411
Neretnieks, I. (1985). Some aspects of the use of iron canisters in deep lying repositories for nuclear waste[R]. Switzerland: NAGRAWettingen. NAGRA Technical Report NTB 85-35.
Numakura, H., and Koiwa, M. (1984). Hydride precipitation in titanium. Acta Metall. 32 (10), 1799–1807. doi:10.1016/0001-6160(84)90236-0
Ortiz, L., Volckaert, G., and Mallants, D. (2002). Gas generation and migration in Boom Clay, a potential host rock formation for nuclear waste storage. Eng. Geol. 64 (2), 287–296. doi:10.1016/s0013-7952(01)00107-7
Panin, A., Kazachenok, M., Pochivalov, Y., Chernov, I., and Klimenov, V. A. Hydrogen treatment of titanium specimens in various structural states[C], Proceedings of the 7th Korea-Russia International Symposium on Science and Technology, Proceedings KORUS 2003, 28 June 2003 - 06 July 2003, Ulsan, Korea (South), (IEEE Cat. No. 03EX737) IEEE, 2003, 1: 97–101.
Papazoglou, T. P., and Hepworth, M. T. (1968). The diffusion of hydrogen in titanium[J]. Trans. Met. Soc. AIME 242, 4.
Pargeter, R. J. (2007). Susceptibility to SOHIC for linepipe and pressure vessel steels-Review of current knowledge. Houston, Texas, United States: NACE International. [C]//CORROSION 2007.
Philippini, V., Naveau, A., Catalette, H., and Leclercq, S. (2006). Sorption of silicon on magnetite and other corrosion products of iron. J. Nucl. Mater. 348 (1), 60–69. doi:10.1016/j.jnucmat.2005.09.002
Phillips, I. I., Poole, P., and Shreir, L. L. (1972). Hydride formation during cathodicpolarization of Ti—I. Effect of current density on kinetics of growth and composition of hydride. Corros. Sci. 12 (11), 855–866. doi:10.1016/s0010-938x(72)80014-3
Reardon, E. J. (1995). Anaerobic corrosion of granular iron: Measurement and interpretation of hydrogen evolution rates. Environ. Sci. Technol. 29 (12), 2936–2945. doi:10.1021/es00012a008
Schutz, R. Corrosion of titanium and titanium aloys[J]. Asmi Handbook Committee Metals Handbook, 1987.
Shen, B. L., and Feng, K. Q. (2000). Research Progress on hydrogen embrittlement of titanium alloys[J]. Total Corros. Control 14 (3), 22–25.
Shoesmith, W. D. (2006). Assessing the corrosion performance of high-level nuclear waste containers. J. Corros. Houst. Tx- 62 (8), 703–722. doi:10.5006/1.3278296
Silva, J. R. G. D., and Mclellan, R. B. (1976). The solubility of hydrogen in super-pure-iron single crystals. J. Less Common Metals 50 (1), 1–5. doi:10.1016/0022-5088(76)90247-2
Sorensen, N. R. (1990). Laboratory studies of the corrosion and mechanical properties of titanium grade-12 under WIPP repository conditions[R] Canada: AECL.
Stalinski, B., and CooganGutowsky, C. K. H. S. (1961). Proton magnetic resonance studies of structure, diffusion, and resonance shifts in titanium hydride. J. Chem. Phys. 344, 1191–1206. doi:10.1063/1.1731720
Tsuru, T., Huang, Y. L., Ali, M. R., and Nishikata, A. (2005). Hydrogen entry into steel during atmospheric corrosion process. Corros. Sci. 47 (10), 2431–2440. doi:10.1016/j.corsci.2004.10.006
Turnbull, A. (2009). A review of the possible effects of hydrogen on lifetime of carbon steel nuclear waste canisters[M]. Wettingen, Switzerland: National Cooperative for the Disposal of Radioactive Waste.
Wasilewski, R. J., and Kehl, G. L. (1954). Diffusion of hydrogen in titanium[J]. J. Jpn. Inst. Light Metals 50 (6), 267–277.
Wei, F. G., and Tsuzaki, K. (2012). “Hydrogen trapping phenomena in martensitic steels[M],” in Gaseous hydrogen embrittlement of materials in energy technologies (Fukuoka, Japan: kyushu university), 493–525.
Wei, X., Dong, J. H., and Ke, W. (2013). Research Progress on Corrosion of titanium disposal container in geological disposal environment of high radioactive nuclear waste[J]. Corros. Sci. Prot. Technol. 25 (2), 160–164.
Wipf, H., Kappesser, B., and Werner, R. (1999). Hydrogen diffusion in titanium and zirconium hydrides. J. Alloys Compd. 310 (1), 190–195. doi:10.1016/s0925-8388(00)00945-2
Yan, L., Ramamurthy, S., Noël, J. J., and Shoesmith, D. (2006). Hydrogen absorption into alpha titanium in acidic solutions. Electrochimica Acta 52 (3), 1169–1181. doi:10.1016/j.electacta.2006.07.017
Yang, C. B., Bonilla, M., Samper, J., and Molinero, J. (2007). Modelling geochemical and microbial consumption of dissolved oxygen after backfilling a high level radiactive waste repository. J. Contam. Hydrology 93 (1-4), 130–148. doi:10.1016/j.jconhyd.2007.01.008
Zhang, Q. C., Huang, Y. L., Sand, W., and Wang, X. (2019). Effects of deep geological environments for nuclear waste disposal on the hydrogen entry into titanium. Int. J. Hydrogen Energy 44 (23), 12200–12214. doi:10.1016/j.ijhydene.2019.03.154
Keywords: metal corrosion, hydrogen permeation, hydrogen embrittlement, nuclear waste, deep geological disposal
Citation: Zhang Q, Jiang Y, Zhang B, Duan J, Zhao X and Chen J (2022) Research progress on the hydrogen permeation behavior of the nuclear waste container–A mini review. Front. Mater. 9:1058394. doi: 10.3389/fmats.2022.1058394
Received: 30 September 2022; Accepted: 13 October 2022;
Published: 09 November 2022.
Edited by:
Hongliang Ming, Institute of Metal Research, CAS, ChinaCopyright © 2022 Zhang, Jiang, Zhang, Duan, Zhao and Chen. This is an open-access article distributed under the terms of the Creative Commons Attribution License (CC BY). The use, distribution or reproduction in other forums is permitted, provided the original author(s) and the copyright owner(s) are credited and that the original publication in this journal is cited, in accordance with accepted academic practice. No use, distribution or reproduction is permitted which does not comply with these terms.
*Correspondence: Yishan Jiang, anlzMTMwQDEyNi5jb20=
Disclaimer: All claims expressed in this article are solely those of the authors and do not necessarily represent those of their affiliated organizations, or those of the publisher, the editors and the reviewers. Any product that may be evaluated in this article or claim that may be made by its manufacturer is not guaranteed or endorsed by the publisher.
Research integrity at Frontiers
Learn more about the work of our research integrity team to safeguard the quality of each article we publish.