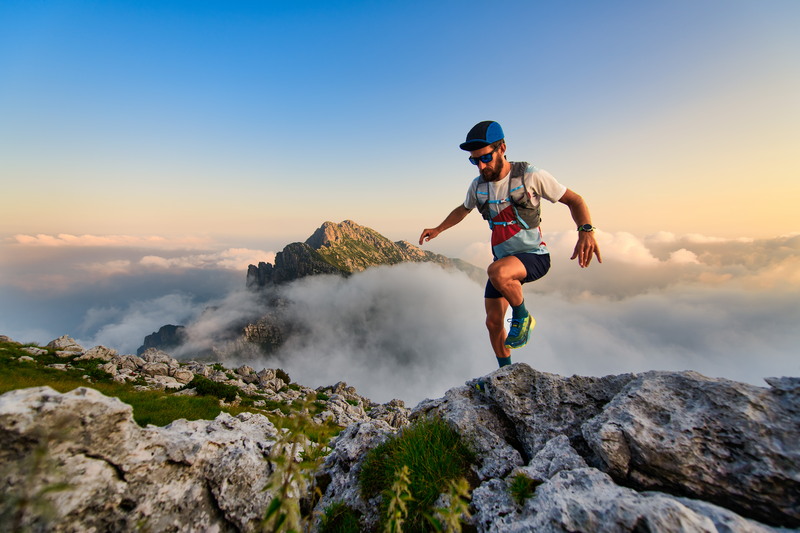
94% of researchers rate our articles as excellent or good
Learn more about the work of our research integrity team to safeguard the quality of each article we publish.
Find out more
MINI REVIEW article
Front. Mater. , 13 October 2022
Sec. Energy Materials
Volume 9 - 2022 | https://doi.org/10.3389/fmats.2022.1046883
This article is part of the Research Topic Micro-Nano Experimental Mechanics of Solid Films View all 5 articles
At the beginning of the 21st century, micro-nano processing technology has developed rapidly, and research on wearable electronic devices has exploded. In particular, flexible thermoelectric materials and thermoelectric generators (TEGs) that have stretchable or foldable properties have been widely studied. Textile-based thermoelectric materials are more suitable for use on the human body than are film or block types of devices, and they are accordingly favoured for wearable smart devices. The design idea of textile thermoelectric materials include the preparation of thermoelectric fibres, textiles, fabric-based films and some novel methods, like using three-dimensional modules to become two-dimensional fabrics by a weaving method, which not to rely something as a base for TE modules. Investigators are thus gaining opportunities to make comfortable and effective fabric TEGs using a wider variety of materials. This article briefly introduces the common methods used to produce textile TEGs. The opportunities and challenges of fabric TEGs are discussed at the end.
The history of thermoelectric materials spans three centuries (Beretta et al., 2019). Nowadays, with the rapid development of wearable devices, researchers have begun to explore more-flexible thermoelectric generators (TEGs) because rigid TEGs based on inorganic blocks have difficulty in meeting the needs of these applications. Flexible TEGs need to consider wearability, so the design of such a device concerns not only its hotspot performance but also the necessity to make trade-offs between mechanical performance and comfort. Flexible TEG designs include blocks, membranes and textiles. The thermoelectric material used in a block-type TEG is a traditional rigid material that is wrapped in a flexible substrate. Such TEGs produce higher power, which can reach the mW level. Membrane TEGs use thin-film thermoelectric materials attached to a flexible base plate. The advantage of a membrane TEG is that its structure has design flexibility. Both n-type and p-type thermoelectric films can be used in a variety of design methods to accommodate bending, folding, cross-tiling and so on. These methods are all attempts to make the hotspot module as three-dimensional as possible for the environment in which it is to be used, in order to obtain higher energy efficiency than is possible with a two-dimensional surface (Yamamoto and Takai, 2002; Snyder et al., 2003; Lee et al., 2016; Ito et al., 2017; Mather and Wilson, 2017; Wu and Hu, 2017; Nan et al., 2018; Jia et al., 2019). Textile TEGs use fabric as a substrate on which to integrate thermoelectric fabrics or thermoelectric films. The common methods for producing textile TEGs include wet textiles, drip or dip coating, screen printing and magnetron sputtering. In addition, a three-dimensional weaving method has recently been introduced in which a single thermoelectric module is made into a bundle-like collection and then wrapped. The bundle of modules is then woven into a fabric, and the core of the fibre is left exposed at the junction used for connecting the thermoelectric module. This three-dimensional weaving method does not need to rely on a substrate to produce a fabric-type TEG.
In the first half of the 19th century, Ørsted coined the term ‘thermoelectric’, and he created the first thermoelectric pile, made of bismuth and antimony (Roget, 1832), with the help of the mathematician and physicist Jean Baptiste Joseph Fourier. In the middle and second half of the 19th century, the three basic thermoelectric effects were well explained (Thomson, 2017), and heat-source power-generation devices using metallic conductors were developed (Kennedy, 1903); they were the first TEGs. At that time, thermoelectric materials were not very efficient, and people have been struggling ever since to find classes of materials with good thermoelectric properties. In the middle of the 20th century, Ioffe proposed a theory of the thermoelectric effect in semiconductors, which greatly increased the range of potential thermoelectric materials (Beretta et al., 2019). He also introduced the dimensionless thermocouple figure of merit, ZT (Ioffe, 1957). After semiconductor materials began to be used to make TEGs, the ZT value increased from the 19th-century value ZT = 0.1 to ZT = 1.0. At that time, people began to recognise the potential benefits of thermoelectric materials and to pay attention to them. In the 1980s, researchers prepared a variety of wearable devices (Mann, 1997), including computers, cameras and sensors. Without exception, none of them looked aesthetically pleasing and comfortable, and some even looked bulky because they had to be plugged into huge power supplies. Today, however, the development of micro-nano processing technology has led to their viability in many fields, materials, electronics and biology—and microelectronics and micro-power sources have also been created. The ability to modify thermoelectric materials has also long been upgraded to the microscopic level (Chen et al., 2019; Chen et al., 2020; Chen et al., 2021). The exploration of wearable TEGs has never stopped, and people can see the prospects and hopes for future wearable smart devices in products such as Google Project Glass, Ralph Lauren’s smart jersey and OM Signal.
As noted above, the common methods for producing fabric-based thermoelectric material technologies include wet textiles, drip or dip coatings, screen printing and magnetron sputtering. ‘Wet textiles’ refer to the original step of spinning a stock solution doped with materials that have thermoelectric properties, such as carbon nanotubes (CNTs) and poly (3,4-ethylenedioxythiophene) (PEDOT) complex with poly (styrene sulfonate) (PEDOT:PSS). So, far as possible, they are dispersed evenly in a solution, and the mixture is sprayed from a hole into a pool for solidification, after which it can be washed and dried to produce n-type or p-type spinnable thermoelectric fibres. These fibres can be modified by using different doping and different stock solutions. However, the thermoelectric properties of the resulting fabrics are generally not as high as those of other types of thermoelectric materials. Because PEDOT:PSS is a polymer with a high electrical conductivity σ, which also has good tensile strength and flexibility (Xu et al., 2020) (Figures 1A,C), it is a very good sheet-conductive material, which is often used in flexible and stretchable devices (Kayser and Lipomi, 2019) (Figure 1B).
FIGURE 1. (A) Photos showing the bending of the composite fibre, based on PEDOT (The radius of curvature is about 1.4 mm) (Xu et al., 2020). (B) Applications of stretchable conductive PEDOT:PSS in energy, electronics and biology (Kayser and Lipomi, 2019). (C) Fibre and fabric display (Xu et al., 2020). (D) Drip-coated, silk-based thermoelectric generator (Lu et al., 2016).
At present, PEDOT:PSS can be made into fibres by wet weaving, which can achieve a conductivity σ = 4,039 ± 215 S cm−1, a Young’s modulus of 22 GPa, and a fracture stress of 550 MPa, which is also the highest value reported for PEDOT to date (Sarabia-Riquelme et al., 2020).
(Xu et al., 2020) have used PEDOT:PSS/Te to prepare TE fibres, which they have then woven into TE fabrics. They added Te nanowires, Polyethylene glycol (PEG Molecular Weight ∼400), PEDOT:PSS pellets and other substances to make the original solution, which they then dispersed uniformly through a syringe into the isopropyl alcohol coagulation bath. After spinning, the resulting fibres were dried and repeatedly coated with silver paste to obtain the required thermoelectric composite fibres, as shown in Figures 1A,C.
Drip or dip coating is a method for depositing a thermoelectric film on a fabric base, and it has good applicability. First, a solution containing a thermoelectric material is prepared, and it is then dripped onto a substrate, infiltrates the fabric substrate and is finally dried. This deposition process can be performed repeatedly. This preparation method is simple, but the binding strength between the film and substrate is not high, and the film thickness is difficult to control (Lu et al., 2016) produced a silk fabric TEG from a paste of the raw materials Te, Bi and CNTs, which they repeatedly deposited on a substrate of Bombyx mori cocoons to make a textile-based TEG (Figure 1D).
Screen printing is also a common method for preparing thermoelectric fabrics. Kim et al. (2014) synthesised n-type Bi2Te3 and p-type Sb2Te3 and printed them onto a glass fabric using a screen-printing technique. They placed the resulting Bi2Te3 and Sb2Te3 films in ambient N2 at 530°C for 10 min and at 500°C for 30 min, respectively. Under mechanical pressure, the films crystallised and densified. Finally, the investigators embedded copper foil into polydimethylsiloxane (PDMS) to form the top and bottom plates, stacked them together and immersed them in the PDMS to fill the voids (Figure 2A).
FIGURE 2. (A) Glass fabric, results of screen printing, filling with PDMS (Kim et al., 2014). (B) Showing of segmented thermoelectric-fabric product, using magnetron sputtering (Lee et al., 2016). (C) The architecture of the fabric (Sun et al., 2020).
Magnetron sputtering is another common film-preparation method, the coating repeatability is high, the substrate requirements are low and the resulting film is compact and highly binding (Lee et al., 2016) devised a method using magnetron-sputtering technology with high-purity Bi2Te3 and Sb2Te3 targets for producing thermoelectric fabrics. After spinning the substrate and depositing TE membranes on polyacrylonitrile (PAN) nanofiber plates with a density of about 0.15 mg cm−2. They deposited Bi2Te3 and Sb2Te3 to prepare separate n-type and p-type yarns, which they twisted and wound to make segmented thermoelectric fabrics (Figure 2B).
Each of the above four methods has its limitations. The thermoelectric properties of the fabrics from ‘wet textiles’ method are generally not as high as those of other types of thermoelectric materials. For drip or dip coating method, the binding strength between the film and substrate is not high, and the film thickness is difficult to control. Screen printing requires high temperature and mechanical pressure to make the films crystallised and densified. Magnetron sputtering have to synthesize n-type and p-type yarns separately then make segmented thermoelectric fabrics.
Recently, (Sun et al., 2020) introduced the novel method of weaving a thermoelectric module into a fabric. They designed a three-dimensional thermoelectric module using the interlock-weaving method to form a two-dimensional structure. They obtained an output voltage from this structure that is 24 times greater than that obtainable from a two-dimensional architecture. Based on basic thermal theories (Priya and Inman, 2009; Nan et al., 2018) (Figure 2C), the collection of human heat and the dissipation of cold-end heat are essential for a high-efficiency TEG. This Sun et al. device not only can make good use of the temperature gradient—like a three-dimensional thermoelectric module—but also fits the human body like a fabric. Therefore, unlike a TEG, which requires a substrate to support its thermoelectric module, the mechanical properties, stability and power from this device are not affected by the substrate. It has a high output power—a power density of 70 mW m−2 at 44 K—and has excellent stretchability. It has a biaxial stretchable property rather than being stretchable only uniaxially. The output voltage fluctuates by only 4% during elbow movement, so it is almost unaffected by the movement and has fairly good practicality.
Fabric-based TEGs are produced using a variety of methods, all of which are designed to solve the problem of flexibility and refinement of the thermoelectric materials. For fabric-based thermoelectric materials and TEGs, oxidation, mechanical life and losses are always issues to be overcome. Discovering new structural and functional materials and proposing novel and more efficient structural designs are clearly useful directions to explore in order to improve the practicality of textile TEGs. In addition, the successful development of flexible inorganic thermoelectric materials in 2019 has provided a new direction for the development of flexible thermoelectric materials (Liang et al., 2019). More preparation processes and design methods for TEGs thus remain to be explored.
All authors listed have made a substantial, direct, and intellectual contribution to the work, and approved it for publication.
National Natural Science Foundation of China (51702091, 51801057), Natural Science Foundation of Hubei Province (2020CFB245), and Research Start-up Fund of Hubei University of Education (19RC02, 19RC03).
The authors thank the College Outstanding Young Scientific and Technological Innovation Team of Hubei province (T201922).
The reviewer CH is currently organizing a Research Topic with the author XC.
The remaining authors declare that the research was conducted in the absence of any commercial or financial relationships that could be construed as a potential conflict of interest.
All claims expressed in this article are solely those of the authors and do not necessarily represent those of their affiliated organizations, or those of the publisher, the editors and the reviewers. Any product that may be evaluated in this article, or claim that may be made by its manufacturer, is not guaranteed or endorsed by the publisher.
Beretta, D., Neophytou, N., Hodges, J. M., Kanatzidis, M. G., Narducci, D., Martin- Gonzalez, M., et al. (2019). Thermoelectrics: From history, a window to the future. Mater. Sci. Eng. R Rep. 138, 100501–101255. doi:10.1016/j.mser.2018.09.001
Chen, X. Q., Fan, S. J., Han, C., Wu, T., Wang, L. J., Jiang, W., et al. (2021). Multiscale architectures boosting thermoelectric performance of copper sulfide compound. Rare Met. 40 (8), 2017–2025. doi:10.1007/s12598-020-01698-6
Chen, X. Q., Yang, J. P., Katkus, T., Wu, T., Tao, J. H., Li, J., et al. (2020). Exploring thermoelectric property improvement for binary copper chalcogenides. Front. Mat. 7, 589568. doi:10.3389/fmats.2020.589568
Chen, X. Q., Zhang, H., Zhao, Y. Y., Liu, W.-D., Dai, W., Wu, T., et al. (2019). Carbon-encapsulated copper sulfide leading to enhanced thermoelectric properties. ACS Appl. Mat. Interfaces 11 (25), 22457–22463. doi:10.1021/acsami.9b06212
Ioffe, A. F. (1957). Semiconductor thermoelements and thermoelectric cooling, infosearch. London, United Kingdom: Infosearch Limited London.
Ito, M., Koizumi, T., Kojima, H., Saito, T., and Nakamura, M. (2017). From materials to device design of a thermoelectric fabric for wearable energy harvesters. J. Mat. Chem. A Mat. 5 (24), 12068–12072. doi:10.1039/c7ta00304h
Jia, Y., Shen, L., Liu, J., Zhou, W., Du, Y., Xu, J., et al. (2019). An efficient PEDOT-coated textile for wearable thermoelectric generators and strain sensors. J. Mat. Chem. C Mat. 7 (12), 3496–3502. doi:10.1039/c8tc05906c
Kayser, L. V., and Lipomi, D. J. (2019). Stretchable conductive polymers and composites based on PEDOT and PEDOT: PSS. Adv. Mat. 31 (10), 1806133. doi:10.1002/adma.201806133
Kennedy, R. (1903). Electrical Installations of electric light, power, traction and industrial electrical machinery. Caxton, London: Jack.
Kim, S. J., We, J. H., and Cho, B. J. (2014). A wearable thermoelectric generator fabricated on a glass fabric. Energy Environ. Sci. 7 (6), 1959–1965. doi:10.1039/C4EE00242C
Lee, J. A., Aliev, A. E., Bykova, J. S., de Andrade, M. J., Kim, D., Sim, H. J., et al. (2016). Woven yarn thermoelectric textiles. Adv. Mater. 28 (25), 5038–5044. doi:10.1002/adma.201600709
Liang, J., Wang, T., Qiu, P., Yang, S., Ming, C., Chen, H., et al. (2019). Flexible thermoelectrics: From silver chalcogenides to full-inorganic devices. Energy Environ. Sci. 12 (10), 2983–2990. doi:10.1039/c9ee01777a
Lu, Z., Zhang, H., Mao, C., and Li, C. M. (2016). Silk fabric-based wearable thermoelectric generator for energy harvesting from the human body. Appl. energy 164, 57–63. doi:10.1016/j.apenergy.2015.11.038
Mann, S. (1997). Smart clothing: The wearable computer and wearcam. Personal. Technol. 1, 21–27. doi:10.1007/bf01317885
Mather, R. R., and Wilson, J. I. (2017). Fabrication of photovoltaic textiles. Coatings 7 (5), 63. doi:10.3390/coatings7050063
Nan, K., Kang, S. D., Li, K., Yu, K. J., Zhu, F., Wang, J., et al. (2018). Compliant and stretchable thermoelectric coils for energy harvesting in miniature flexible devices. Sci. Adv. 4 (11), eaau5849. doi:10.1126/sciadv.aau5849
Roget, P. M. (1832). Treatises on electricity, galvanism, magnetism, and electro-magnetism. London: Baldwin and Cradock.
Sarabia-Riquelme, R., Andrews, R., Anthony, J. E., and Weisenberger, M. C. (2020). Highly conductive wet-spun PEDOT: PSS fibers for applications in electronic textiles. J. Mat. Chem. C Mat. 8 (33), 11618–11630. doi:10.1039/d0tc02558e
Snyder, G. J., Lim, J. R., Huang, C.-K., and Fleurial, J.-P. (2003). Thermoelectric microdevice fabricated by a MEMS-like electrochemical process. Nat. Mat. 2 (8), 528–531. doi:10.1038/nmat943
Sun, T., Zhou, B., Zheng, Q., Wang, L., Jiang, W., and Snyder, G. J. (2020). Stretchable fabric generates electric power from woven thermoelectric fibers. Nat. Commun. 11 (1), 572. doi:10.1038/s41467-020-14399-6
Wu, Q., and Hu, J. (2017). A novel design for a wearable thermoelectric generator based on 3D fabric structure. Smart Mat. Struct. 26 (4), 045037. doi:10.1088/1361-665x/aa5694
Xu, H., Guo, Y., Wu, B., Hou, C., Zhang, Q., Li, Y., et al. (2020). Highly integrable thermoelectric fiber. ACS Appl. Mat. Interfaces 12 (29), 33297–33304. doi:10.1021/acsami.0c09446
Keywords: wearable device, flexible thermoelectric material, thermoelectric generators, fabric, fiber
Citation: Li Y, Zeng J, Zhao Y, Wang C, Zhang C, Cheng T, Tao J, Li J, Wang C, Zhang L and Chen X (2022) Fabric-based flexible thermoelectric generators: Design methods and prospects. Front. Mater. 9:1046883. doi: 10.3389/fmats.2022.1046883
Received: 17 September 2022; Accepted: 03 October 2022;
Published: 13 October 2022.
Edited by:
Jiantie Xu, South China University of Technology, ChinaReviewed by:
Chao Han, University of Technology Sydney, AustraliaCopyright © 2022 Li, Zeng, Zhao, Wang, Zhang, Cheng, Tao, Li, Wang, Zhang and Chen. This is an open-access article distributed under the terms of the Creative Commons Attribution License (CC BY). The use, distribution or reproduction in other forums is permitted, provided the original author(s) and the copyright owner(s) are credited and that the original publication in this journal is cited, in accordance with accepted academic practice. No use, distribution or reproduction is permitted which does not comply with these terms.
*Correspondence: Xinqi Chen, Y2hlbnhpbnFpQGh1ZS5lZHUuY24=
Disclaimer: All claims expressed in this article are solely those of the authors and do not necessarily represent those of their affiliated organizations, or those of the publisher, the editors and the reviewers. Any product that may be evaluated in this article or claim that may be made by its manufacturer is not guaranteed or endorsed by the publisher.
Research integrity at Frontiers
Learn more about the work of our research integrity team to safeguard the quality of each article we publish.