- 1Department of Environment and Food, Chuzhou Vocational and Technical College, Chuzhou, China
- 2Department of Applied Mathematics, Hong Kong Polytechnic University, Kowloon, Hong Kong SAR, China
A surface acoustic wave (SAW) formaldehyde sensor based on a graphene/polymethyl methacrylate (PMMA) composite film with high sensitivity, and short response and recovery time was proposed in this study. Using a novel multi-source spray deposition method, graphene sheets were uniformly dispersed in a PMMA film to fabricate sensitive films with a three-dimensional framework structure for use in SAW devices. The formaldehyde-sensing ability was enhanced by optimizing the film thickness and operating temperature. The highest performance was achieved for a graphene/PPMA film thickness of 2.2 μm at a temperature of 120°C.
1 Introduction
Formaldehyde is a colorless, acrid pollutant that can cause several harmful effects upon exposure to even small doses, such as a burning sensation in the eyes and pharynx, queasiness, and labored respiration. The acute toxicity of formaldehyde stimulates the skin and mucous membrane; moreover, inhaling high concentrations of formaldehyde can cause symptoms of respiratory irritation, sneezing, coughing, and a burning sensation in the nose and pharynx (Ura et al., 1989; Zhang, 2018). Formaldehyde is also a carcinogen, which might lead to central nervous system disorders, immune system disorders, and respiratory diseases (Ashby and Lefevre, 1982). The main sources of formaldehyde pollution for most people seem to be at their homes, such as building materials and household products, but also include power stations, factories, and automotive emissions (Pickrell et al., 1983). Therefore, selective and precise detection using portable and low-cost gas sensors is crucial for real-time tracking of formaldehyde in home and workplace.
The highly selective and sensitive surface acoustic wave (SAW) gas-sensing technology has proven to be greatly beneficial for the detection of toxic gases (Groves, 2006). Various SAW sensors have been studied for formaldehyde detection, including those composed of metal oxides such as SnO2 (Li et al., 2017), ZnO (Chen et al., 2022), and NiO (Zheng et al., 2011); polymers such as polyaniline and polyethylenimine (PEI) (Antwi-Boampong and BelBruno, 2013); and composite materials such as PEI/TiO2 (Wang et al., 2012),Sn3O4/rGO (Yin et al., 2020), PEI/MWCNTs (He et al., 2014), and polymers and functionalized carbon nanotubes (Palla-Papavlu et al., 2021). Recently, the application of composite sensitive films has been extensively studied because of their potential to ameliorate the sensitivity by combining various compounds into one sensing layer while simultaneously retaining the individual characteristics of their components and increasing their surface functionality.
Graphene is a two-dimensional carbon allotrope with excellent electronical, chemical, mechanical, thermal, and optical properties. Graphene has been widely used as a sensing material, owing to its unique electrical properties such as high mobility, large specific surface area, and low electrical noise (Allen et al., 2009). Graphene has two main advantages regarding its application in electrochemical sensors and biosensors, that is, graphene does not contain metallic impurities, which interfere with the material electrochemistry. In addition, graphene can be easily connected by
In developing high-efficiency and low-cost sensor films, various deposition methods like ink-jet printing (Hossain et al., 2009), screen printing (Qi et al., 2008), 3D printing (Wang et al., 2019), and spraying (Mani and Rayappan, 2013) have been used for large-area coating. Among them, the spray technologies can prepare uniform large-area polymer films through a relatively simple process, which provides sufficient processing possibility for the engineering of the film structure. The preparation of the film by spraying involves a reconstruction process in which the solution particles are atomized and driven to the substrate by a carrier gas; therefore, the size of the solution droplets and the resulting domain can be well-controlled by controlling the atomization process (Chen et al., 2010). Furthermore, spraying can produce films over a wide range of concentrations and varying compositions, allowing for direct treatment and application of polymers with poor solubility (Green et al., 2008) and good treatment of organic and inorganic materials with different solubilities or dispersion in the liquid phase.
We aimed to introduce graphene into a polymer matrix to prepare novel nanocomposite SAW sensors for formaldehyde detection and to compare the sensitivity of the developed SAW sensors with that of sensors based on graphene and PMMA nanocomposite films. In this study, we report the development of graphene/PMMA nanocomposites fabricated by a novel multi-source spray deposition method that can form uniformly dispersed graphene nanofillers in the PMMA-based multi-component films, regardless of their different material properties. PMMA has excellent characteristics as a rigid and transparent plastic, such as having high impact strength, being light weight, showing high transparency, and exhibiting better processing performance. All these make PMMA widely used in sensors, battery electrolyte, polymer conductivity, nanotechnology, and other fields (Ali et al., 2015). Nanostructured sensors have a higher specific surface area-to-volume ratio than traditional microsensors, which can provide a larger detection area for nanostructured materials and increased gas adsorption, thereby improving the sensing ability. The sensitivity, responsivity, and selectivity to formaldehyde vapor, and reversibility of the graphene/PMMA nanocomposite sensors were studied and compared with other polymer sensors; the results confirmed that our sensors exhibited a significantly higher sensitivity to formaldehyde vapor.
2 Materials and methods
2.1 Graphene/polymethyl methacrylate composite sensitive film synthesis
2.1.1 Synthesis of multi-source spray-deposited graphene dispersions
To obtain spray-settling integral dispersions, the dried graphite oxide (GO) powder (60 mg) was added to deionized water (20 ml) and ultrasonicated for 12 h. After centrifugation of the solution, the coarse dispersion obtained, which contained highly dispersed coarse GO, was transferred to a vial. Polyethylene glycol 200 (0.2 ml) was added; then, the mixture was ultrasonicated for 30 min to obtain a very fine dispersion of GO. The GO was then reduced to graphene using the hydrazine hydrate in N, N-dimethylformamide (DMF); the color change from yellow-brown to black confirmed the conversion of GO to graphene platelets. The graphene platelets were filtered by suction and washed with water, and then dried under vacuum for 12 h at 60°C.
2.1.2 Synthesis of the polymethyl methacrylate solution
PMMA (35,000 g/mol) was obtained from Sigma-Aldrich (Germany). PMMA was dissolved in 1,2-dichloroethane to form solutions over a concentration range of 4–7 wt%.
2.1.3 Modified multi-source spray deposition
The processes of the modified multi-source spray deposition method are shown in Figure 1. The building of the film involves a reconstruction process, in which the solution particles are atomized and driven onto the substrate by a carrier gas; therefore, the droplet and the resulting domain size can be well-controlled by controlling the atomization process. By spraying, a wide range of film concentrations and composition can be obtained. In order to simplify the experimental conditions, we controlled the film thickness by setting the deposition time and nozzle size. Nitrogen at a pressure of 15 psi was used as the carrier gas, and the distance between the nozzle tip and the substrate was 12 cm. The spray nozzle used had a maximum spray rate of approximately 20 ml/min. After spray deposition, the resultant layers were cross-linked at 50°C for 2 h.
2.2 Characterization and testing instrumentation
The morphologies of the samples were characterized by field emission scanning electron microscopy (FESEM; Carl Zeiss Supra 55).
2.3 Apparatus measurement of gas-sensing properties of the materials
The sensor used was of a “delay-line” type with a center frequency of 69.4 MHz. Fifty pairs of interdigital transducers (IDTs) with a diameter of 2,500 μm and a period of 40 μm were fabricated on piezoelectric substrates. Gold IDTs with a thickness of 150 nm were deposited on 10-nm chromium IDTs using standard photolithographic techniques. The effective area of the quartz substrate was 8 mm2, and its geometric structure was a parallelogram so as to reduce the acoustic reflection on the edges of the substrate.
A schematic diagram of this experimental setup is shown in Figure 2. The sensor measurement was carried out in a sealed chamber under static conditions. The temperature in the chamber could be set to a specific value and monitored by using a thermometer. By setting the voltage and current of the heating stage, the surface temperature of the sensor acted as the working temperature. The corresponding liquid solution containing a certain amount of formaldehyde was injected into a small heating plate that was fixed in the mixing chamber. After formaldehyde gas was mixed with indoor air evenly, the indoor valve was opened so the gas could come into contact with the sensor. The concentration of formaldehyde can be obtained by controlling the number of droplets. After each measurement, nitrogen was pumped into the chamber to purge the sensor environment.
3 Results
3.1 Graphene/polymethyl methacrylate composite sensor and its response to formaldehyde
FESEM investigations confirmed the deposition of a continuous graphene/PMMA film on the surface of the sensor devices (Figure 3A). As can be seen from Figure 3A, the film smoothly and compactly covers the entire substrate. A high-magnification SEM image (Figure 3B) further confirms the uniform deposition of the graphene/PMMA film by the multi-source spray deposition method. The graphene sheets (gray-white bulk in the image) were uniformly dispersed in the PMMA film, and thus, the film formed a three-dimensional framework structure. The detailed side view of the as-prepared film in Figure 3C shows that the typical thickness is about 2.2 μm. The film thickness can be increased by prolonging the deposition time, while the surface morphology can be tuned by changing the spraying parameters and solution composition. However, increasing the amount of the sprayed solution and the carrier gas flow rate and decreasing the gap between the nozzle and the substrate changes the morphology of the film from a uniform dispersion to a dense structure.
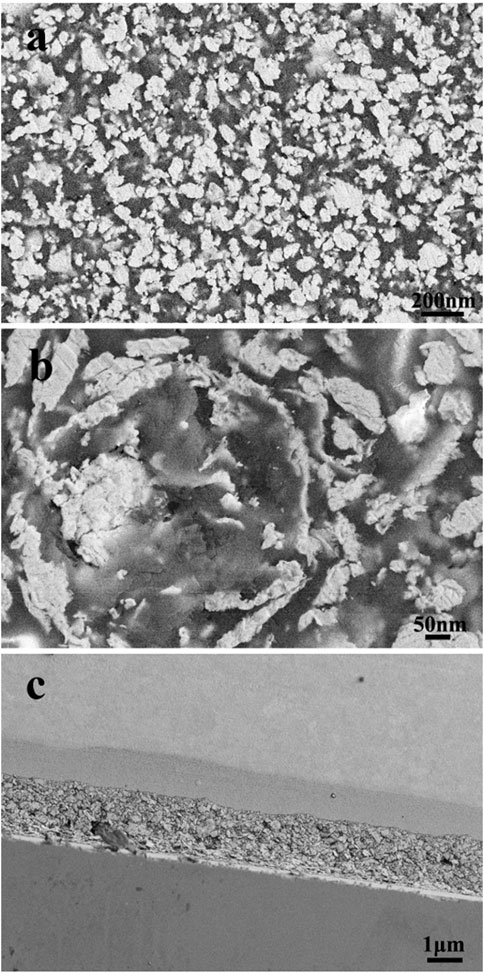
FIGURE 3. FESEM images of the surface morphology of graphene/PMMA sensitive films: (A) top view; (B) Magnified view; and (C) sideways view.
The response of sensors with different graphene/PMMA film thicknesses to 4.0 ppm formaldehyde at 120°C is shown in Figure 4. All the samples exhibited responses and could be recovered after formaldehyde was extracted. The response amplitude varied with the coating thickness. The results show that the sensor with 2.2-µm film thickness had the highest sensitivity and performance compared to the other sensors. When the graphene/PMMA film is extremely thin or thick, its sensitivity to formaldehyde drastically reduces. As mentioned previously, thickness of films is controlled by controlling the spraying time. Since the structure of all the films was the same in all factors other than thickness, it can be concluded that the difference in sensor response was mainly due to the difference in film thickness. The increase in film thickness affects the normal direction of the surface, interferes with the propagation of the wave, increases the insertion loss, and reduces the center frequency of the sensor sample. Therefore, sensitivity can be adjusted by adjusting the thickness of graphene/PMMA sensitive films.
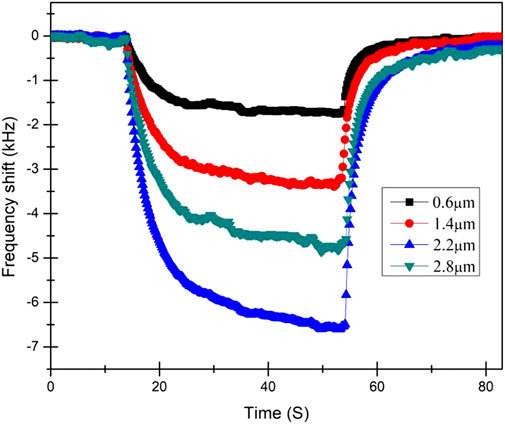
FIGURE 4. Sensor responses toward 4.0 ppm formaldehyde for samples with different film thickness at 120°C.
The effect of temperature on the formaldehyde vapor sensor was also investigated. The sensor responses of the same sample with the graphene/PMMA film thickness of 2.2 μm at temperatures ranging from 30°C to 180°C are depicted in Figure 5. The response performance underwent a sharp frequency shift when the temperature reaches 120°C, following which the response decreased with the increasing temperature.
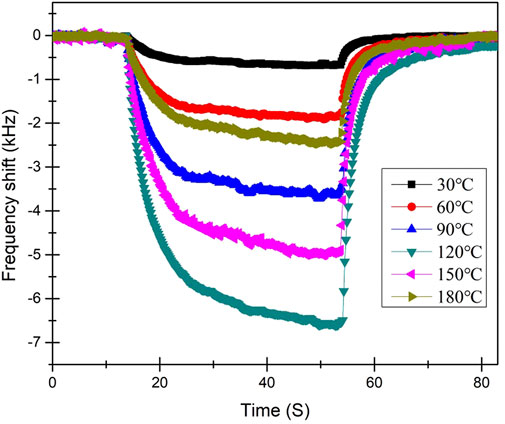
FIGURE 5. Sensor responses toward 4.0 ppm formaldehyde for the sample with film thickness of 2.2 μm at different temperatures.
Figure 6 shows the response of the graphene/PMMA film sensor sample with a thickness of 2.2 μm to formaldehyde gas of different concentrations at an operating temperature of 120°C. The sensor was exposed to varying concentrations of formaldehyde via the synthetic air that was introduced into the room for calibration, and the dynamic responses of the sensor were measured; the results showed good consistency at different times. The relationship between the frequency shift and gas concentration is linear. After purging formaldehyde with dry synthetic air, the working frequency of the SAW sensor increased and returned to baseline. In these experiments, the graphene/PMMA sensor samples exhibited immediate response upon both exposure to and recovery of formaldehyde, indicating the good response and recovery features of the sensor.
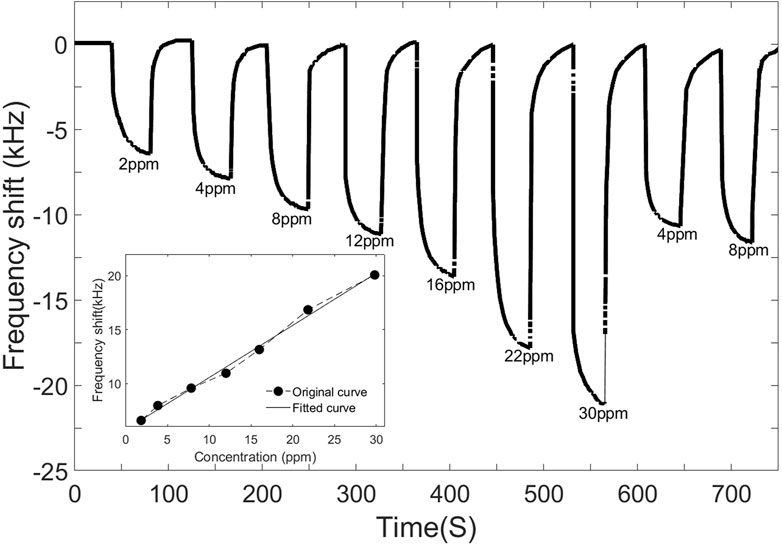
FIGURE 6. Dynamic response of graphene/PMMA sensors towards formaldehyde vapor at 120°C, inset is the measured frequency shift with different concentrations.
Figure 7 depicts the simultaneous interpretation of the response curves of sensors when coated with different sensing films (pure PMMA, pure graphene, and the graphene/PMMA composite). Compared with sensors based on pure graphene and PMMA films, the graphene/PMMA multilayer film sensor exhibited excellent performance. The frequency shift exhibited by graphene/PMMA was approximately 6.9 kHz, while that of pure graphene and PMMA sensors was 2.0 and 0.5 kHz, respectively. Furthermore, the results show that the sensitivity of the acoustic electric effect to the gas film interaction is far greater than that of the mass loading effect, indicating that the acoustic electric effect is the dominant effect of graphene/PMMA-laminated film sensors.
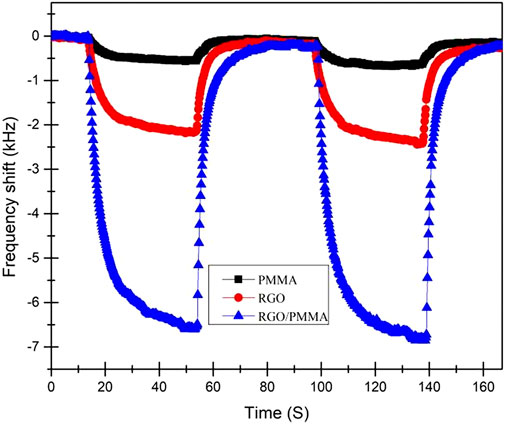
FIGURE 7. Sensitive responses of SAW sensors using pure PMMA, pure graphene and graphene/PMMA composite exposed to 4.0 ppm formaldehyde.
Good selectivity is generally considered an important function of high-performance gas sensors. Figure 8 shows the response of the graphene/PMMA sensor to four gases, ethanol, NO, NH3, and acetone, where PMMA is insoluble in NO, NH3, and ethanol and soluble in (acetone). The gas sensitivity measurement was carried out at 120°C. The frequency shifts of 5 ppm formaldehyde, 100 ppm ethanol, 100 ppm NO, 100 ppm NH3, and 100 ppm acetone were 7.9, 1.1, 0.4, 0.2, and 1.4, respectively. The results show that the graphene/PMMA sensor had a significant response to formaldehyde and a comparatively weak response to the other gases, revealing that the developed sensor has a high selectivity to formaldehyde.
3.2 Sensing mechanism of the chemiresistor
Two response mechanisms are proposed in terms of graphene/PMMA chemical resistance to formaldehyde. First, due to the tunneling effect of quantum mechanics, a conductive path is formed in the graphene/polymer composite; the distance between the conductive elements allows for electron hopping (Goh et al., 2003; Valentini et al., 2003; Wang et al., 2017). Due to the absorption of the organic vapor, the polymer matrix expands and increases in size, therefore leading to an increase in the distance between graphene sheets and, consequently, a further increase in the contact resistance. The degree of distension and the resulting electrical response depends on the solubility of the polymer in steam. Second, the electronic properties of the conductive elements in the composite film undergo changes, owing to the charge transfer caused by the adsorption of organic molecules (Fan et al., 2002; Someya et al., 2003).
As shown in Figure 8, the graphene/PMMA film has a high sensitivity to formaldehyde. In spite of acetone being an ideal solvent for PMMA, the response of the composite membrane to other solvents, including acetone, is significantly less compared with that to formaldehyde. In addition, solvents that are insoluble or insoluble in PMMA, such as ethanol, would cause a recognizable response as well, which indicates that the main mechanism of the reaction to the formaldehyde vapor cannot be attributed to volume expansion. Thus, it can be concluded that the interaction between the composite surface and formaldehyde was responsible for the observed response. As mentioned previously (Jeremy et al., 2008), formaldehyde seems to adsorb to the graphene sheet through interactions with polar functional groups (such as hydroxyl groups), the existence of which in the graphene structure is a long established fact. This could affect the conductivity of graphene materials, owing to the occurrence of the charge exchange between the p-type semiconductor graphene (Lu et al., 2009) and the adsorbed formaldehyde molecules. Graphene nanoflakes dispersed uniformly in the three-dimensional framework structure of the polymer matrix provide a high aspect ratio and a high surface-area-to-volume ratio for the nanocomposites; due to this interaction, the number of holes in the semiconductor would be reduced, and the electric resistance of the device would thus increase.
4 Discussion
In this study, we reported a novel multi-source spray deposition method to fabricate graphene/PMMA composite sensitive films. The graphene sheets were uniformly dispersed in the PMMA film; the film formed a continuous three-dimensional framework structure. The SAW formaldehyde gas sensor with the developed composite material as the sensing layer was studied and compared with the SAW gas sensors based on graphene and PMMA layers. The thickness of the graphene/PMMA film and the operating temperature significantly affected the response of the sensor to formaldehyde. The graphene/PMMA film with a thickness of 2.2 μm was used to prepare the sensor, and its sensitivity was the highest at 120°C. Because of the high sensitivity, recovery, and selectivity of the test sample, the novel composite film has a broad application prospect as the basic device for the wireless passive sensing and detection of specific environmental gases.
Data availability statement
The original contributions presented in the study are included in the article/Supplementary Material; further inquiries can be directed to the corresponding author.
Author contributions
Conceptualization, BW and LZ; methodology, BW; software, BW and XW; formal analysis, BW; investigation, BW and XW; resources, BW; data curation, BW; writing—original draft preparation, BW, LZ, and XW; writing—review and editing, LZ; visualization, BW; supervision, LZ; and project administration, LZ. All authors have read and agreed to the published version of the manuscript.
Funding
This work is funded by the University-level discipline (major) of Chuzhou Polytechnic College (ZD2019011).
Conflict of interest
The authors declare that the research was conducted in the absence of any commercial or financial relationships that could be construed as a potential conflict of interest.
Publisher’s note
All claims expressed in this article are solely those of the authors and do not necessarily represent those of their affiliated organizations, or those of the publisher, the editors, and the reviewers. Any product that may be evaluated in this article, or claim that may be made by its manufacturer, is not guaranteed or endorsed by the publisher.
References
Ali, U., Karim, K. Bt. A., and Buang, N. (2015). A review of the properties and applications of poly (methyl methacrylate) (PMMA). Polym. Rev. 55 (4), 678–705. doi:10.1080/15583724.2015.1031377
Allen, M., Tung, V., and Kaner, R. B. (2009). Honeycomb carbon: A review of graphene. Chem. Rev. 1101, 132–145. doi:10.1021/cr900070d
Antwi-Boampong, S., and BelBruno, J. (2013). Detection of formaldehyde vapor using conductive polymer films. Sensors Actuators B Chem. 182, 300–306. doi:10.1016/j.snb.2013.03.008
Ashby, J., and Lefevre, P. (1982). Formaldehyde generators: Relationship between stability, lipophilicity and carcinogenic potency. Carcinogenesis 3 (11), 1273–1276. doi:10.1093/carcin/3.11.1273
Chen, D., Chen, R., and Yuan, Y. (2022). Investigation on formaldehyde SAW sensor with ZnO film prepared through radio frequency magnetron sputtering. Russ. J. Phys. Chem. 96 (1), S197–S202. doi:10.1134/S0036024422140047
Chen, L., Hong, Z., Kwan, W., Lu, C., Lai, Y., Lei, B., et al. (2010). Multi-source/component spray coating for polymer solar cells. ACS Nano 4 (8), 4744–4752. doi:10.1021/nn901758p
Fan, Y., Burghard, M., and Kern, K. (2002). Chemical defect decoration of carbon nanotubes. Adv. Mater. 14 (2), 130–133. doi:10.1002/1521-4095(20020116)14:2<130:AID-ADMA130>3.0
Goh, H., Goh, S., Xu, G., Pramoda, K., and Zhang, W. (2003). Dynamic mechanical behavior of in situ functionalized multi-walled carbon nanotube/phenoxy resin composite. Chem. Phys. Lett. 373 (3-4), 277–283. doi:10.1016/S0009-2614(03)00621-3
Green, R., Morfa, A., Ferguson, A., Kopidakis, N., Rumbles, G., and Shaheen, S. (2008). Performance of bulk heterojunction photovoltaic devices prepared by airbrush spray deposition. Appl. Phys. Lett. 92 (3), 33301. doi:10.1063/1.2836267
Groves, W. (2006). Sensors in the measurement of toxic gases in the air.” in Encycl. Anal. Chem. Appl. Theory Instrum.
He, Y., Jiang, Y., Tai, H., and Xie, G. (2014).The investigation of Quartz Crystal Microbalance (QCM) formaldehyde sensors based on PEI-MWCNTs composites, Adv. Mater. Res., 1030, 217–222. doi:10.4028/www.scientific.net/AMR.1030-1032.217
Hossain, S., Luckham, R., Smith, A., Lebert, J., Davies, L., Pelton, R., et al. (2009). Development of a bioactive paper sensor for detection of neurotoxins using piezoelectric inkjet printing of sol− gel-derived bioinks. Anal. Chem. 81 (13), 5474–5483. doi:10.1021/ac900660p
Jeremy, T., Robinson, F., Perkins, K., Snow, E., Wei, Z., and Sheehan, P. (2008). Reduced graphene oxide molecular sensors. Nano Lett. 8, 3137–3140. doi:10.1021/nl8013007
Justino, C., Gomes, A., Freitas, A., Duarte, A., and Rocha-Santos, T. (2017). Graphene based sensors and biosensors. TrAC Trends Anal. Chem. 91, 53–66. doi:10.1016/j.trac.2017.04.003
Kim, H., and Macosko, C. (2008). Morphology and properties of polyester/exfoliated graphite nanocomposites. Macromolecules 41 (9), 3317–3327. doi:10.1021/ma702385h
Kim, I., Choi, S., and Cho, H. (2015). Graphene-based composite materials for chemical sensor application. Electrospinning High Perform. Sensors, 65–101. doi:10.1007/978-3-319-14406-1_3
Li, Y., Chen, N., Deng, D., Xing, X., Xiao, X., and Wang, Y. (2017). Formaldehyde detection: SnO2 microspheres for formaldehyde gas sensor with high sensitivity, fast response/recovery and good selectivity. Sensors Actuators B Chem. 238, 264–273. doi:10.1016/j.snb.2016.07.051
Lu, G., Ocola, L., and Chen, J. (2009). Reduced graphene oxide for room-temperature gas sensors. Nanotechnology 20 (44), 445502. doi:10.1088/0957-4484/20/44/445502
Mani, G., and Rayappan, J. (2013). A highly selective room temperature ammonia sensor using spray deposited zinc oxide thin film. Sensors actuators B Chem. 183, 459–466. doi:10.1016/j.snb.2013.03.132
Palla-Papavlu, A., Voicu, S., and Dinescu, M. (2021). Sensitive materials and coating technologies for surface acoustic wave sensors. Chemosensors 9 (5), 105. doi:10.3390/chemosensors9050105
Pickrell, J., Mokler, B., Griffis, L., Hobbs, C., and Bathija, A. (1983). Formaldehyde release rate coefficients from selected consumer products. Environ. Sci. Technol. 17 (12), 753–757. doi:10.1021/es00118a012
Qi, Q., Zhang, T., Yu, Q., Wang, R., Zeng, Y., Liu, L., et al. (2008). Properties of humidity sensing ZnO nanorods-base sensor fabricated by screen-printing. Sensors Actuators B Chem. 133 (2), 638–643. doi:10.1016/j.snb.2008.03.035
Someya, T., Small, J., Kim, P., Nuckolls, C., and Yardley, J. (2003). Alcohol vapor sensors based on single-walled carbon nanotube field effect transistors. Nano Lett. 3 (7), 877–881. doi:10.1021/nl034061h
Ura, H., Nowak, P., Litwin, S., Watts, P., Bonfil, R., and Klein-Szanto, A. (1989). Effects of formaldehyde on normal xenotransplanted human tracheobronchial epithelium. Am. J. Pathol. 134 (1), 99
Valentini, L., Biagiotti, J., Kenny, J., and Santucci, S. (2003). Morphological characterization of single-walled carbon nanotubes-PP composites. Compos. Sci. Technol. 63 (8), 1149–1153. doi:10.1016/S0266-3538(03)00036-8
Viespe, C., and Grigoriu, C. (2010). Surface acoustic wave sensors with carbon nanotubes and SiO2/Si nanoparticles based nanocomposites for VOC detection. Sensors Actuators B Chem. 147 (1), 43–47. doi:10.1016/j.snb.2010.02.064
Wang, P., Chong, H., Zhang, J., and Lu, H. (2017). Constructing 3D graphene networks in polymer composites for significantly improved electrical and mechanical properties. ACS Appl. Mat. Interfaces 9 (26), 22006–22017. doi:10.1021/acsami.7b07328
Wang, X., Cui, F., Lin, J., Ding, B., Yu, J., and Al-Deyab, S. S. (2012). Functionalized nanoporous TiO2 fibers on quartz crystal microbalance platform for formaldehyde sensor. Sensors Actuators B Chem. 171, 658–665. doi:10.1016/j.snb.2012.05.050
Wang, Y., Wang, Y., Liu, W., Chen, D., Wu, C., and Xie, J. (2019). An aerosol sensor for PM1 concentration detection based on 3D printed virtual impactor and SAW sensor. Sensors Actuators A Phys. 288, 67–74. doi:10.1016/j.sna.2019.01.013
Yin, F., Li, Y., Yue, W., Gao, S., Zhang, C., and Chen, Z. (2020). Sn3O4/Rgo heterostructure as a material for formaldehyde gas sensor with a wide detecting range and low operating temperature. Sensors Actuators B Chem. 312, 127954. doi:10.1016/j.snb.2020.127954
Zhang, L. (2018). Formaldehyde: Exposure, toxicity and health effects, R. Soc. Chem. 37, 1–1. doi:10.1007/S10337-018-3576-3
Keywords: formaldehyde, sensor, graphene, polymethyl methacrylate, polymer, surface acoustic wave sensors
Citation: Wang B, Zhou L and Wang X (2023) Surface acoustic wave sensor for formaldehyde gas detection using the multi-source spray-deposited graphene/PMMA composite film. Front. Mater. 9:1025903. doi: 10.3389/fmats.2022.1025903
Received: 23 August 2022; Accepted: 03 October 2022;
Published: 04 January 2023.
Edited by:
Vineet Kumar, Yeungnam University, South KoreaReviewed by:
Agus Arsad, University of Technology Malaysia, MalaysiaZaihua Duan, University of Electronic Science and Technology of China, China
Copyright © 2023 Wang, Zhou and Wang. This is an open-access article distributed under the terms of the Creative Commons Attribution License (CC BY). The use, distribution or reproduction in other forums is permitted, provided the original author(s) and the copyright owner(s) are credited and that the original publication in this journal is cited, in accordance with accepted academic practice. No use, distribution or reproduction is permitted which does not comply with these terms.
*Correspondence: Beibei Wang, d2FuZ3hpYW9xaWFuMTI1QDEyNi5jb20=