- Université de Lyon INSA Lyon, CNRS UMR 5223, Ingénierie des Matériaux Polymères, Villeurbanne, France
The objectives of circularity are often focused on recycling, but combining use of alternative building blocks such as bio-sourced ones for virgin materials with ability for recycling seems to be a relevant challenge. Unfortunately, the volumes of rather new bio-based plastics, such as Poly (lactide) (PLA), seem be too low to allow the development of new recycling chains in the next years. Therefore, these bio-plastics are not likely to be recycled at large scale, reducing their interest when considering their whole life cycle. Nevertheless, continuing to produce petroleum-based plastics and searching for a way to recycle them seems not to be a self-sufficient solution. Indeed, in order to reconciliate recycling and bio-based plastics, a strategy is to focus on the production of conventional plastics, such as poly (ethylene terephthalate) (PET), from renewable resources while ensuring their recycling in existing chains. In this context, this review focuses on alternative building blocks sources to produce PET, for which recycling seems relevant and developed. Although still produced in small quantities, some alternative sources for building block production have been able to establish themselves in the industrial landscape. Nevertheless, there is still little industrialization and the synthons are often produced in small quantities. Most of the discoveries are still confined to laboratory studies with some pilot tests for part of them. It should be emphasized that, even if some synthons are already commercialized, research is active with the aim of improving yields, discovering cleaner catalysts, reducing energy consumption. The review describes alternative routes and sources for the production of PET, not only with technological but also socio-economical points of view with discussion on their potentials and limits. The different routes proposed display promising advantages to be improved by research studies. Nevertheless, producing bio-sourced polymers at a large-scale could lead to problems of access to resources. A more local economy involving smaller volumes of material and adapting to the resources of the territory could be an alternative. The review could help in orientating research contributing to a circular economy depending less on non renewable resources, considering technological and socio-economical points of view.
1 Introduction
The plastics are an integral part of our modern way of life. Their production and consumption increase every year, responding to the growth of the world demography and the development of emerging countries. Indeed, between 1950 and 2019, the plastic production was multiplied by 160, from 2.3 to 368 million tons (Plastics Europe 2020). Thus, since 1950 more than 9.2 billion tons of plastics have been produced, the half since the beginning of the 21st century (Heinrich Böll Foundation and Break Free From Plastic 2019).
According to Plastic Europe, in 2020 in Europe, the most consuming sectors are the packaging (40%), the building and construction (20%) and the automotive (9%), The polymer used for these applications are the most produced: polypropylene PP (20%), low density polyethylene LDPE (17%), high density polyethylene HDPE (13%), polyvinyl chloride PVC (10%) and poly (ethylene terephthalate) PET (8%).
Nowadays, raw materials necessary for the synthesis of these polymers are exclusively petroleum-based and represent between 4 and 6% of the global crude oil production per year. This value could reach 20% by 2050 if the demand continues to grow (Plastics Europe 2016). To fight against this oil dependence and reduce the environmental footprint, the bio-based plastics production seems to be a solution. According to European Bioplastics, their production represents less than 1% of plastic production but increases every year (2.42 million in 2021 and should rise to 7.59 million of tons in 2026) (European Bioplastics 2021). However, this increase follows that of plastic production, so it should not represent more than 2%. The conventional polymers represent only 17.6% of the bio-plastics. The main part (64.2%) of the plastic from renewable resources are resins which emerged over the past 2 decades, such as PLA or PBAT.
Regarding the life cycle of plastics, 40% of them are single-use plastics and 80% finish their lives in landfills or in the natural environments (National Geographic UK 2021). This represents a considerable amount of waste to manage, which increases every year. In 2015, PET primary plastic waste represented approximately 32 million tons (Geyer, Jambeck, and Law 2017). Watercourse, seas and oceans are polluted natural areas, with huge quantities of plastic wastes accumulated: estimated between 93,000 and 236,000 tons by the Henrich Böll Foundation. In Europe, the part of plastics sent to landfills decreases to the benefit of recycling and energy recovery, reflecting the sensitization on the importance of controlling the end of life of plastics. But Only 20% of the plastics are recycled or undergo energy recovery in Europe.
Despite the desire of developing a circular economy, ensuring both a renewable origin and managed end of life of plastic waste, one fact remains: the volumes of the new bio-based plastics, such as PLA, might be too low to allow the development of new recycling chains for them in the next years. Therefore, these bio-plastics are not likely to be recycled reducing the efficacity of their uses with a non-controlled life ending. By contrast, continuing to produce petroleum-based plastics and searching for a way to recycle them is not a self-sufficient solution.
In this context of reconciliating recycling and bio-based plastics, one of the solutions is to focus on the production of conventional plastics, such as PET, from renewable resources while ensuring their recycling in existing chains. Currently, the most recycled polymers in Europe are PET, PE, PP, PS and PVC.
When looking at the literature, four main technologies are adapted to produce bio-based polymers: the biorefinery based on the sugar and starch chemistry, the biotechnologies using bacteria, the pyrolysis and the gasification of biomass.
For about 15 years, the ethylene can be produced from bio-based ethanol. The first generation (1G) process uses corn and sugar cane, it is the most used process (Braskem PE). The second generation (2G) uses lignocellulosic resources (Axens process) (De Marignan and Poncelet 2020). And the third generation (3G) uses seaweeds (laboratory research) (de Farias Silva and Bertucco 2016). Biorefinery is not the only solution: gasification and pyrolysis have shown interesting results. The gasification is the conversion of organic compounds into gas. This gas can be a mix of carbon monoxide and dihydrogen, called syngas, produced by the conversion of biomass at high temperatures (800–900°C). Then, syngas is transformed into ethanol by fermentation (Daniell, Köpke, and Simpson 2012). At lowest temperatures and in the absence of oxygen, a biogas, mainly made of methane (50–70%) and carbon dioxide (20–50%), is produced. The methane can be used to synthesize other building blocks, such as olefins (methanol to olefins process, MTO) (Tian et al., 2015). For the pyrolysis, we can use biomass or plastic wastes made of PE or PP. Axens and Plastic Energy are developing a thermal anaerobic conversion process to transform mixed plastics wastes into an oil, which is purified by their solution Rewind Mix (Axens 2022). The naphtha obtained can then be injected into existing cracker infrastructures to produce olefins.
The PS is synthesized from styrene, itself synthesized from ethylbenzene. Ethylene and benzene are at the start of this chain. If ethylene can be bio-based, the benzene is a product of the petrochemical industry, as well as xylene and toluene. Stelle et al. noticed that styrene is present in many plants and foods, such as cinnamon (169–39,200 ng/g), beef (5,25–7,85 ng/g) or also coffee (1,57–7,14 ng/g) (Steele et al., 1994). These values are too low to be considered as an exploitable source of styrene but allow recent studies to show that styrene can be produced from cinnamic acid, one of the main constituents of the cinnamon oil (Fragnière et al., 2003). This molecule can also be synthesized from glucose (after several reactions), using yeast (Saccharomyces cerevisiae) and enzyme (Claypool et al., 2014). Nevertheless, due to the low yield, the production of styrene from the biomass is not conclusive now. By contrast, pyrolysis seems to be a valuable solution, using MgO catalyst at 400°C, with yield around 83% (Rasul, Shah, and Rahim 2008).
PET presents a double challenge since its synthesis requires two monomers: ethylene glycol (EG) and terephthalic acid (TA). The production of bio-sourced EG is already known and has been greatly facilitated by the production of bio-sourced ethylene from which it is synthesized. Thus, companies like Coca-Cola have already been able to commercialize partially bio-based products (the Plant Bottle in 2009) (Ren et al., 2015). TA seems more complex to be bio-based, and the challenge is high, as 80% of the carbon of PET come from TA. The other complex part is the high purity of TA needed. A TA with a purity <99% is considered as crude and purification steps are required to obtain a purity around 99,99% (Schwartz and Stark 1987). Although bio-based EG is still more commercialized for bio-sourced PET than TA, both show some dynamic in recent years. Recent studies have shown that the production of PET via alternative sources is possible in many ways. The diversity of these solutions opens the way to more research. It seems interesting to understand what these alternatives are and their feasibility.
This review focuses on alternative building blocks sources to produce PET, with consideration of not only technological but also socio-economical points of view. Figure 1 illustrates the different ways identified in this review. As EG is already known through bio-PE, only its production from other building blocks will be discussed. For TA, a larger number of solutions will be presented: from bio-based p-xylene or other molecules. We will discuss on the scientific and socio-economical aspects of each proposal (Figure 2).
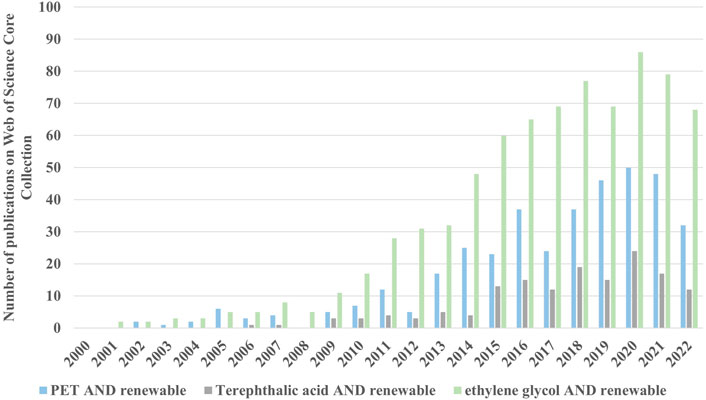
FIGURE 1. Number of publications, for the period (2000–2022) on Web of Science, 19 September 2022, for different combinations of key words dealing with renewable PET.Alternatives routes for bio-based PET.
2 Bio-based ethylene glycol
Ethylene glycol (EG) is conventionally synthesized from ethylene which is oxidized and then hydrolyzed. Thus, the main obstacle to the production of bio-based ethylene glycol is the production of bio-ethanol, which is mainly made from food products. This can be a major problem. Moreover, its price is also largely influenced by the one of bio-ethylene. It is for both reasons that alternative processes for direct conversion of biomass are under development.
The process of direct conversion of lignocellulose to ethylene glycol (DLEG) has been developed with tungsten-based catalysts. The process has been applied with different types of biomasses: miscanthus, corn stalks, poplar wood (Pang et al., 2016). This direct conversion of cellulose into EG allows to bypass the hydrolysis treatments of cellulose which are environmentally or costly problematic. The conversion of cellulose to ethylene glycol is done in water with a W2C/AC tungsten-based catalyst but faces a problem of separation of ethylene glycol and water as well as poor hydrothermal stability of the catalyst (Xu et al., 2017). The reaction is done in two steps. The first is the hydrolysis and then the hydrogenation of cellulose to form glucose.
The reaction begins with the hydrolysis of cellulose to form oligosaccharides and glucose catalyzed by H+ in water at the subcritical stage and by tungsten. It is this step that will limit the kinetics of the process. According to Figure 3, the formed sugars are then catalytically degraded into glycolaldehyde by a retro aldol reaction in the presence of tungsten. The glycolaldehyde is then hydrogenated to form ethylene glycol. Fructose leads to the formation of propylene glycol and glycerol.

FIGURE 3. Alternative (from cellulose) and conventional (from ethylene) routes to produce ethylene glycol.
The conversion reaction of pure cellulose to ethylene glycol has a very good yield but the selectivity for ethylene glycol is low. As an example, raw corn stalks show a conversion of 96.1% with a selectivity for ethylene glycol of only 18.3%. The problem stems from the lignin which, upon degradation, produces aromatic compounds that deactivate the catalyst. The presence of hemicellulose does not adversely affect the yield. On the contrary, the sugars can be degraded. The use of birch wood results in a 75.6% yield of ethylene glycol and a conversion of some of the lignin. The conversion of grass (miscanthus) allows a 35.5% yield at low concentration (1%) while a lignin removal pretreatment allows to reach a 39.1%, even at high concentration (10%). This possibility of using the raw materials at high concentrations is interesting for industrial applications (Zheng et al., 2014). Indeed, it allows to limit the water and energy consumption of the process. Pre-treatment of the biomass also seems necessary before treatment to improve the yield.
Through the third generation ethanol, algae (micro and macro) are considered as raw materials. It is the lipids and carbohydrates present in the algae that allow the production of ethanol. There are three ways: hydrolysis then fermentation, dark fermentation (growth in the absence of light) and photo-fermentation (from CO2, water and light) (de Farias Silva and Bertucco 2016). Because of their very rapid reproduction and growth, algae can help to overcome the problems of resource depletion (Ursachi and Gutt 2020). On the other hand, the costs related to the culture of algae and the technological processes are still too important to be profitable, yet (Oyler 2021).
3 Ethylene from CO2
One possible route to produce plastics is the valorization of industrial gases. Indeed, the electrolytic conversion of CO2 in the presence of water allows the formation of H2 and CO. Currently, research is mainly focused on the formation of ethanol from these molecules, via the following reactions (Daniell, Köpke, and Simpson 2012):
In the case where CO is used as the only source of carbon and energy, the conversion to ethanol is33% only. The rest of the carbon is lost as CO2. In the case of the second equation where CO and H2 are equimolar, the conversion is 67% (Devarapalli and Atiyeh 2015).
The processes used and studied are rarely detailed, but it seems that the technology is based on the use of organisms to reproduce the principles of assimilation by trees. Daniell et al. mention the use of anaerobic bacteria of the acetogen type to synthesize acetyl CoA from CO2. They refer to studies with C. autoethanogenum (0.32 g/L), C. ljungdahlii (48 g/L), C. ragsdalei (25.26 g/L), A. bacchi (1.27 g/L). Acetyl-CoA is mainly converted to acetate with production of ATP which is used for synthesis of methyl groups. When the cell enters a stationary phase, where the medium contains less nutrients and the pH decreases, acetyl CoA is reduced to acetaldehyde by aldehyde dehydrogenase (ALDH), which is then reduced to ethanol by alcohol dehydrogenase (ADH). Acetate can also be reduced to ethanol. In this case, acetate is reduced to acetaldehyde by aldehyde ferredoxin oxidoreductase (AOR) and then reduced to ethanol by ADH (Sun et al., 2019). A similar technology has been developed by Migros, which announced, in 2021, the manufacture of PET bottles produced from ethanol derived from the fermentation of CO2 by bacteria (Caliendo 2021). Moreover, the start-up Fairbrics describes itself as specialized in polymer-based textile fibers and has developed a technology based on the conversion of CO2 into polyester (Fairbrics 2020). It announces that its technology is based on mixtures of CO2, green hydrogen catalysts, enzymes in a solvent. The molecules obtained are then used to produce polyesters, including PET, which will be transformed into fibers. Still at the pilot stage, the company seems to be looking at creating partnerships with industrial companies to use their emissions as a source of CO2. A new pilot plant has been announced on early 2022, with the investment of AP Ventures, to produce 30 tons per year (AP Ventures 2022).
4 Bio-based terephthalic acid
The industrial production of terephthalic acid can be carried out by oxidation of p-xylene (Amoco process, Figure 4). Two cases are considered: the biosynthesis of p-xylene or the biosynthesis of molecules very close to TA and allowing the synthesis of PET. The first one is the most developed and is in pilot testing or early industrialization in 2022. The second goes from the stage of laboratory studies to the beginning of pilot tests.
P-xylene from the biomass pyrolysis
Sustainable technology company Anellotech and its joint development partners, IFPEN and Axens, have developed a technology for the direct conversion of biomass into aromatics (primarily Benzene, Toluene and Xylene) at Anellotech’s TCat-8® pilot plant, located in Texas. These aromatics will be processed to recover high purity bio-based p-xylene (Sudolsky et al., 2019).
The process used for the conversion of biomass to aromatics is called “Biomass to Aromatics™.” It uses catalytic pyrolysis of dried and ground biomass using zeolites as catalysts (Waal and de Jong 2013). The process can be subdivided into 3 steps:
- Preparation of the biomass source by drying and grinding. In the process, several forms of biomass can be used: wood, sugarcane, corn stover etc.
- Pre-treated biomass is catalytically pyrolyzed, near 600 °C. The rapid heating of the biomass mainly allows to produce gaseous material. Coke is also produced but can be recovered and used as fuel to power the pyrolysis process.
- The gas is transformed into aromatics, thanks to the use of acidic zeolite H-ZSM-5. To obtain the best conversion to aromatics, it is advised to have a high feed ratio catalyst/biomass.
Yields for the production of aromatics can be as high as 47% depending on the nature of the biomass used as feedstock: a high level of lignin will reduce the part of aromatics (25–30%) whereas the biomass with sugar (glucose or xylitol) allows to obtain the highest yields (30–47%). Figure 5 displays the aromatics obtained by the pyrolysis of biomass, with the Anellotech process (Huber et al., 2009). We observe that half of aromatics produced are benzene, toluene, xylene and ethylbenzene. The other part is mainly naphthalene. Actually, the process is not able to produce exclusively aromatics yet and research focuses on finding better catalysts. The best selectivity for producing xylene, which seems of interest to produce terephthalic acid, is around 17% with xylitol feed.
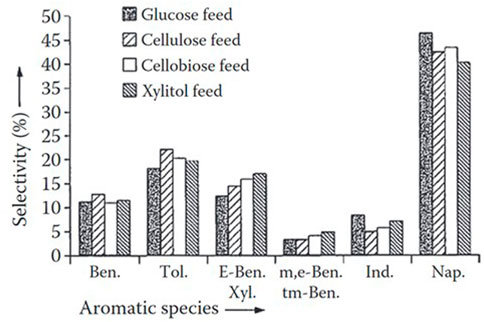
FIGURE 5. Aromatic chemical yields from pyrolysis of various biomass sources. Benzene (Ben), toluene (Tol), ethyl-benzene (E-ben), xylene (Xyl), methyl-éthyl or trimethyl-benzene (m,e-Ben, tm-Ben), indanes (Ind) and naphthalenes (Nap) (from Huber et al., 2009).
Isobutanol
Isobutanol is a four-carbon primary alcohol, which can be used to synthesize p-xylene, which will be used to synthesize terephthalic acid. For about 10 years, pilot industrial processes have been developed to produce isobutanol from polysaccharides. Two main routes have been exploited: fermentation (Gevo Inc.) and chemical catalysis (BioForming® by Virent). Both have been able to pass the pilot stage and have already been commercializing their production for several years. In both cases, the processes used can be adapted to produce other chemical compounds.
Fermentation
The technology developed by Gevo is based on two major advances: creation of a recombinant yeast capable of producing isobutanol from biomass by fermentation of sugars (numerous patents, including United States 2018/0179557 A1 (R. Feldman et al., 2018) and WO 2021/178805 A1 (Smith, Hanley, and Benoit 2021)) and invention of the GIFT® process (Gevo Integrated Fermentation Technology) allowing direct separation of the isobutanol produced from the biomass that is still fermenting (patent United States 8,017,375 B2 (Peters et al., 2011)). Both pathways are described in Figure 6. The first industrial experimentation took place at Gevo’s bio-ethanol production site in Silsbee (Texas, United States), based on these two patents. The project was made possible thanks to collaboration between the Japanese industrialist specialized in plastic films, Toray (which later bought p-xylene) and Coca-Cola, with a pooling of human resources in R&D.
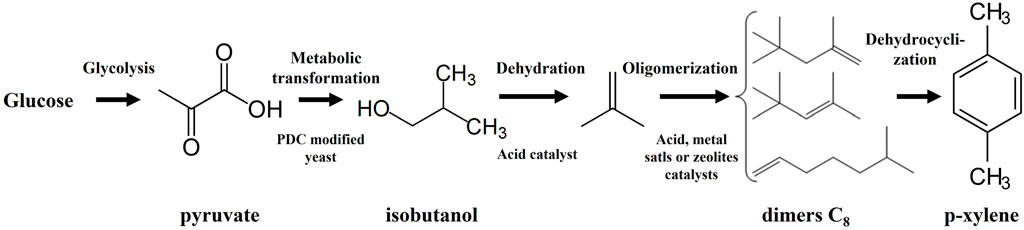
FIGURE 6. Routes of conversion of glucose to isobutanol then to p-xylene (adapted from Volanti et al., 2019).
Gevo has filed several patents on yeasts capable of obtaining isobutanol. In 2008, the yeast was a modification of pyruvate decarboxylase (PDC) derived from a glycolysis of the raw material. After this patent, the following patents tended to complement the previous one, through genetic modifications of the yeast, or proposed a new principle. The most recent patent using PDC dated February 2018 (R. Feldman et al., 2018) and complements a yeast entirely designed by Gevo and patented in 2008 (R. M. R. Feldman et al., 2011). It is created from a pyruvate decarboxylase gene of a polypeptide and the recombination of different microorganisms (Saccharomyces, Kluyveromyces, Zygosaccharomyces, Debaryomyces, Pichia or Schizosac charomyces) allowing the production of isobutanol from pyruvate. Saccharomyces is also used for the production of bio-ethanol, which shows the real interest of breeding these microorganisms. This yeast allows to obtain the Crabtree effect (production of alcohol by yeast from glucose). This pathway consists of the succession of metabolic transformation using the particularities of the following enzymes: an acetolactate synthase (ALS), a ketol-acid reductoisomerase (KARI), a dihydroxy-acid dehydratase (DHAD), a 2-keto acid decarboxylase (KIVD) and an alcohol dehydrogenase (ADH). The same patent states that the microorganism capable of producing isobutanol from a carbon source has a theoretical yield of glucose to isobutanol conversion of 0.41 g/g. The measured values were able to represent 10–50% of the theoretical yield (i.e. 0.04 g/g to 0.21 g/g). This process also produces ethanol at a conversion rate close to the theoretical one (0.99 g/g). More recently, Gevo published a new patent focusing on a microorganism with at least one nucleic acid molecule encoding a KARI or a ADH (Smith, Hanley, and Benoit 2021), a new yeast developed to limit inhibition by molecules, such as 2,3—dihydroxyisovalerate. The authors announced that the yield can now reach 97.5% of the theoretical value (i.e. 0,40 g/g). Experimentally, the best values presented in the patent are more around 0.363 g/g, or 88.5%.
After the development of its first yeast, Gevo focused on the process to achieve fermentation and recovery of isobutanol. Patent United States 2011/0087000 A1 addresses these two issues. Catalysts are not listed in the patent, and the entire process is summarized as:
- Processing biomass to form fermentable feedstock.
- Fermentation of the feedstock with one or more microorganisms. Obtaining of an aqueous phase of isobutanol.
- Separation of the aqueous phase from the fermented phase (the raw material).
- Dehydration of the aqueous phase to obtain different C4 alkenes.
- Oligomerization to form C8 alkenes;
- Dehydrocyclization to form xylenes.
In more details, the separation of isobutanol and water is made possible by the 8°C difference between the boiling points of the two liquids (108°C and 100°C respectively). The GIFT® process uses this property to evaporate both phases. The steam has a concentration of isobutanol about 20 times higher than the one in the fermenter. By condensing the steam, the concentration of isobutanol is well above its solubility limit in water (1.02 at 20°C), resulting in two pure phases. The two phases are separated by decantation and then purified. The water is distilled and returned to the fermenter, thus operating in a closed loop.
The purified isobutanol is then dehydrated, in the presence of an acid catalyst, to form a gas (or a liquid depending on the conditions) made of C4 alkenes: isobutene (at least 95%), 1-butene and/or 2-butene. The gas is recovered, condensed and purified. The catalyst used has to be water-tolerant because dehydration produces a large amount of water (about 24.3%) and allows the conversion of C4 alcohols into C4 alkenes, with a high selectivity favoring the formation of isobutene. The most relevant seems to be BASF AL-3996, with a conversion of 99.8%, divided into isobutene (96%), 1-butene (1%) and 2-butene (2.5%), with the choice of limiting the purification steps. In the reactor, the pressure can range from 0 to 13.8 × 105 Pa and the temperature from 100 to 400°C. For example, for isobutene the operation can be carried out between 300 and 400°C with an aluminum oxide catalyst in the vapor phase (United States patent 5,6256,109), or with a sulphonic acid catalyst in the liquid phase between 120 and 200°C (United States patent 4,602,119). This step is mostly done in a heterogeneous fixed bed catalytic reactor. The C4 alcohols (including isobutanol) not transformed at the end of the step can be reinjected at the beginning of the step.
Then, the C4 alkenes undergo oligomerization to form C8 alkenes (at least 90%): with at least 50% of 2,4,4-trimethylpentene, 2,5-dimethylhexane and/or 2,5-dimethylhexadiene. The advantage compared to the oligomerization made in petrochemistry, is that the compounds produced are mainly diisobutylenes instead of isooctanes and isododecane. Therefore, it is not necessary to carry out isolation and purification steps before dehydrocyclization. The catalysts used are acids (sulfonic, polyfluoroalkylated or heteropolyacid), metal salts or zeolites with a high selectivity to produce the three compounds mentioned above. For batch reactions, acidic catalysts are favored and introduced from 0.01 to 50% with respect to the mass of reactants. This step is generally carried out between 100 and 200°C under a pressure between 0 and 1.107 Pa. The remaining C4 alkenes can be reused for the next oligomerization reaction.
Afterwards, the C8 alkenes undergo dehydrocyclization, in the presence of a catalyst, to form various compounds (liquid and gaseous) including xylenes (with a minimum of 75% of p-xylene). To maximize the production of p-xylene, the C8 must be predominantly 2,4,4-trimethylpentenes, 2,5-dimethylhexanes and/or 2,5-dimethylhexadienes. The reaction is carried out at (or close to) atmospheric pressure and at temperatures between 400 and 600°C. To optimize this step, the selectivity of p-xylene has to be increased. This can be done by keeping the remaining C4 from the previous step or by adding some diluents (hydrogen, argon, methane or nitrogen). If the dehydrocyclization is done in the presence of oxygen, the hydrogen released forms water. The catalysts used are metallic (platinum, nickel, palladium.). As for oligomerization, C4 and/or C8 alkenes may remain at the end of this step and, if recovered, can be reinjected into the step associated with their transformation.
For these three main stages and in view of the information provided, the patent recommends carrying out this stage under the different conditions presented in Table 1 below. All steps with the same number are part of the same reaction chain.
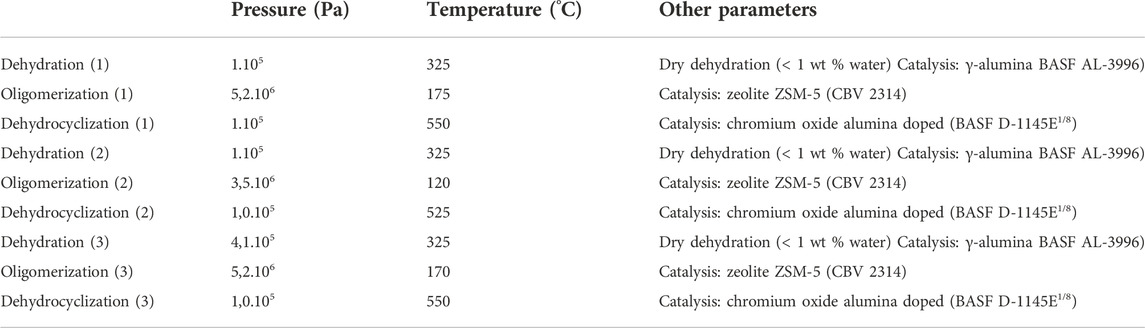
TABLE 1. Examples of pressure conditions, temperatures and other parameters for the GIFT® process steps (adapted from Peters et al., 2011).
Finally, the p-xylene is recovered and condensed. It can then be converted into p-xylene without a purification step (its purity being >99.5%). The patent proposes as a solution (following the dehydrocyclization) to place the p-xylene (0.03 mol) obtained in a reactor with acetic acid (1 mol), bromoacetic acid (0.01 mol) and cobalt (II) acetate tetrahydrate (0.025 mol). Heating the whole at 150°C under a pressure of 3.4 × 105 to 4.1 × 105 Pa, for 4 h allows the formation of TA. However, the latter must be purified to remove the remaining acids.
In terms of yields, a typical case is presented in Figure 7. The data are taken from patent United States 2011/0087000 A1. After fermentation and purification steps, it is considered that 100 kg of isobutanol are recovered. Of these 100 kg, 75.7% are converted to C4 alkenes after dehydration (the remaining 24.3% being water which is recovered for re-injection in further steps). The subsequent oligomerization yields 90% C8 alkene and 10% C12 alkene. Only the C8 are used for the next dehydrocyclization step. After this last step, 40.7% of the products are gases (hydrogen, gasoline gas form and iso butylene) and 59.3% are liquids (heavy and light aromatics, isooctane and xylene). The part we are interested in is the para form of xylene, which represents about 75–95% of the ortho-meta-para xylene mixture. Finally, the conversion rate of isobutanol to p-xylene is 18.7% on average.
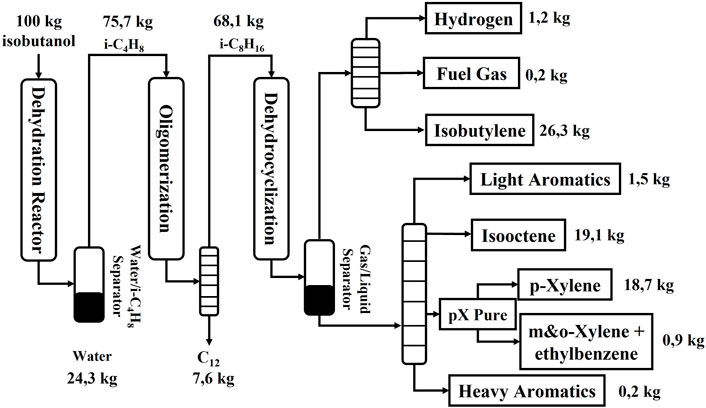
FIGURE 7. Process for the industrial conversion of 100 kg of isobutanol into p-xylene (from Peters et al., 2011).
Following initial successful trials, Gevo decided to industrially implement this process in Luverne (Minnesota, United States) in 2014 (Ryan 2019). Isobutanol and bio-based p-xylene are currently produced in Luverne since 2014. At the same site, bio-ethanol is also produced, which allows the pooling of resources and facilities (including water treatment). The Silsbee site is now used as a biorefinery to produce biofuels for aviation and naval applications. This use of isobutanol is, and is likely to continue to be, in increasing demand. Indeed, since isobutanol is not very soluble in water but very soluble in octane, it is an appropriate answer for an isobutanol-gasoline mixture for ship engines. As a result, biobutanol was recognized by the National Marine Manufacturers Association (NMMA) as a marine fuel in 2015 (Green Car Congress 2015), received ASTM certification in 2016 for aviation (Willis 2015b), and has had a Renewable Identification Number (RIN) D6 since 2017 (Rodewald and Severson 2017). The production of isobutanol as a biofuel is therefore in competition with the plastics industry as long as the quantities produced are small and limited. As an example, in 2016, Lufthansa has shown interest in biofuel produced from Gevo isobutanol and wished to enter into a 5-year agreement to purchase between 30 and 150 million liters. The agreement was not concluded because the Luverne site had to be adapted to convert isobutanol into biofuel, which was not done at that time. However, a similar agreement was signed between HCS Group and Gevo to produce 60,000 tons of aviation biofuel by the end of 2024 (Zirm 2021). We can also note the sale of this same fuel to NASA in 2015 (Willis 2015a). Isobutanol currently seems to be mostly used for biofuels than for the production of alternative building blocks sources.
Chemical catalysis
The technology developed by Virent is called BioForming® (see Figure 8 (Green Car Congress 2011)) and makes it possible to obtain several molecules of interest from biomass. P-xylene (PX) is one of them, via the production of benzene, toluene and xylene (BTX), produced in Madison (Wisconsin, United States) and sold under the name BioForm PX®. The process was in the laboratory study stage from 2001, and gained on rise with a collaboration with Shell in 2008 for the production of biofuels. Another turning point came in 2011 following a collaboration between Virent and Coca-Cola. Indeed, the beverage giant wanted to market its products in 100% bio-based PET bottles, under the name PlantBottle goals (commercialized in 2009 and then partially bio-based, up to 30%) (Coca-Cola Company 2021). To achieve this, carbohydrate-containing biomass is converted into C4+ hydrocarbon mixtures. Two main steps are required to achieve this: aqueous phase reforming and catalytic condensation. The BioForming® process is protected by several patents, commonly gathered under the name “Synthesis of liquid fuels and chemicals from oxygenated hydrocarbons” (United States 8017818 B2 (Cortright and Blommel 2011b), United States 7977517 B2 (Cortright and Blommel 2011a) or United States 2011/0257448 A1 (Cortright and Blommel 2011c)).
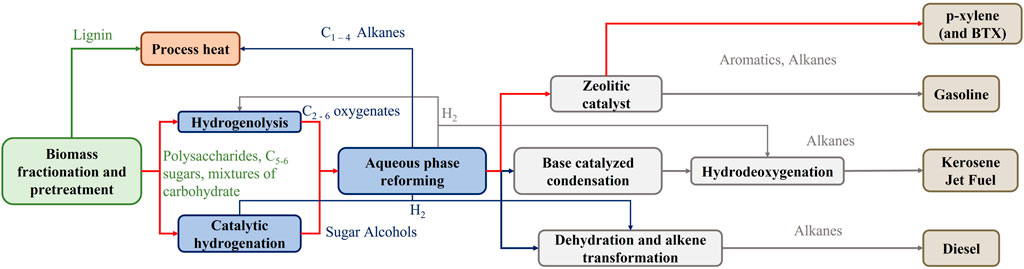
FIGURE 8. Schematic illustration of the BioForming® process, with the route to p-xylene in red (adapted from Green Car Congress, 2011).
The first step was developed by Virent in 2001, following the work of R. Cortright (co-founder and chief technical officer) and J. Dumesic, at the University of Wisconsin (Komula 2011). It consists of the following steps (all the following explanations are taken from the United States 7977517 B2 patent): 1) hydrogenolysis and/or catalytic hydrogenation of an aqueous mixture of carbohydrate sources to produce sugar alcohols and oxygenated molecules of low molar mass, 2) deoxygenation of the mixture to convert it to hydrocarbons and low oxygenated compounds. Temperatures vary depending on the step, and the pressure is always chosen so that both water and compounds are in liquid or gaseous form. The raw material must initially be water soluble. The hydrogenolysis is carried out at temperatures between 100 and 300°C and at a pressure of 10–2,400 psig, the parameters varying according to the raw materials and the desired compounds. The catalysts used are metallic (Cu, Re, Ru, Pt, Ni...). An example cited in the patent is a metallic sponge A7063 developed by Activated Metals and Chemicals Inc., which should allow to react glucose with hydrogen, to linearize the cyclic molecules. The hydrogen used can come from the biomass or be introduced independently. The deoxygenation is done at temperatures between 177 and 302°C, and pressures between 10 and 90 bar. The catalysts used have to catalyze a reaction between a hydrogen and an oxygenated compound to remove one or more oxygen atoms. Thus, alcohols, ketones, aldehydes etc. can be obtained. Metallic catalysts are generally used, such as rhenium or NiSn based catalysts. The input mixture must contain at least 1% by weight of oxygenated hydrocarbons. The ratio of oxygenated compounds to hydrogen must be higher than 1.
The second and last step is a catalytic condensation to convert hydrocarbons and low oxygenated compounds into other compounds. The resulting mixture is called BioForm®. It is carried out at temperatures ranging from 80 to 500°C, under pressures from 0 to 1,200 psig. One of the possible condensations is done in an acidic medium, with a zeolitic catalyst type ZSM-5. It is the latter that is used to produce aromatics (including BTX). It uses acid catalysts including zeolite ZSM-5.
The patent does not specify any yield, but other external studies mention a biomass/aromatic compound yield between 25 and 30% (Waal and de Jong 2013), the precise parameters being kept secret. On the other hand, in a description of its product, Virent indicates a purity of p-xylene of 99.86% (Virent Inc. 2019). BioForm PX® won the 2013 Independent Commodity Intelligence Services (ICIS) award for “Best Innovation for Sustainability”. On this occasion, the group announced its collaboration with Renmatix in the production of bio-based p-xylene. Renmatix will supply Virent with the raw material (cellulosic sugar) (Badran et al., 2017). Similarly, the food company Cargill is interested in entering into an agreement with Virent to provide corn dextrose as feedstock (Cargill 2020). Coca-Cola continued to work with Virent and reinvested in the company in 2014, to allow for expanded production capabilities, focusing on the “separation and purification” part of the process. This new agreement showed its benefits in June 2015, at the World Expo in Milan, where the first 100% bio-based PET bottle was presented. In 2015, the Madison site produced 10 tons of p-xylene. This low quantity is explained by the non-industrialization of the process, which was still in the laboratory/pilot phase transition. This production served as a demonstrator for potential collaborators. The demonstration was promising, since in 2016, a collaboration between Virent and Tesoro (refining specialist, new Andeavor) started to increase the production capacity and to allow the commercialization of the different products resulting from the BioForm® process. In the same year, Virent was bought by Tesoro to become one of its subsidiaries (Norris 2016). Finally, Tesoro was acquired in April 2018 by Marathon Petroleum (one of the largest refiners in the United States). With the buyout by an oil industry company, Tesoro’s products are expected to be predominantly for 2G biofuel manufacturing. This is suggested on their website, presenting a project with Virent in the “renewable fuels” tab (Marathon Petroleum 2022). However, in March 2019, an agreement between Virent, Johnson Matthey, and BP was reached to improve the production capabilities and commercialization of 2G fuel, and of p-xylene (BP 2019). The company communicates very little about its sales and production capabilities. An official document from 2011 mentioned facilities for an industrial launch of 30,000 to 225,000 tonnes per year of BioForm PX® (Komula 2011).
p-cymene and terpenes
The p-cymene (PCY) can be used to synthesize terephthalic acid. It is an aromatic compound naturally present in plants such as cumin or thyme. It is part of the terpene family (molecule of formula (C5H8)n, comprising two isoprenes). The use of terpenes and terpenoids (or mixture of both) for the synthesis of PCY, and then its conversion into TA was the subject of patents filed by SABIC Innovative Plastics in 2008 (Berti et al., 2010b; Berti et al. 2010; Berti et al. 2010a). Terpenes include many molecules: limonene, carotene, α and β-pinene, delta-3-carene... These patents and the various studies stated thereafter, however, focus on the production of PCY from limonene. Berti et al., the authors of the patents, also published the results of their experiments in the scientific journal “Green Chemistry” (Colonna et al., 2011). The reactions and their yield are presented in Figure 4. The final yield, limonene to terephthalic acid is estimated to be 84%.
SABIC patents report 75%–95% yield for the conversion of terpenes to PCY. And this yield rises to 99% in the case of limonene. Thus, they recommend its use as a precursor of PCY. The other motivation to use limonene lies in its origin as it is the main component of citrus fruits, after water (80%). Up to 90% can be found in citrus peel oils (Ladaniya 2008). Miller et al. announced more than 60 million tons of orange produced annually, of which 22 million tons will form waste (peel) (Miller 2015).
The extraction of limonene from peels uses conventional essential oil extraction processes (steam distillation, cold pressure and solvent extraction). However, these techniques are time consuming (up to 12 h), energy intensive and use a lot of solvents (Attard et al., 2014). Studies were interested in the optimization of the extraction processes of limonene. We can retain that Attard et al. were interested in demonstrating the interest of microwaves compared to conventional techniques. To do this, orange peels were placed in a tube containing hexane, and stirred at temperatures of 70, 90 and 110°C. The choice of hexane is only due to its low boiling point, 69°C, against 178°C for limonene. The study even recommends the use of greener solvents such as supercritical CO2. The experiment was carried out with and without microwaves (at 200 W). The extraction is only done over 30 min, because beyond that, compounds formed by the decomposition of the bark start to form. The temperatures were chosen to avoid the decomposition of pectin and cellulose between 160 and 180°C. The authors showed that the temperature has a great impact on the profitability of the process, as an increase of 20°C allows to almost double the yield (they made the hypothesis of the excitation of water molecules). They also noticed that microwaves allow to obtain the same yields as without, for half the time. Finally, while the maximum experimental yield was around 4.7% under standard conditions, this one increases to 11.1% at 110°C. In view of the evolution of the yield as a function of time, the study extrapolates the data to conclude that the maximum yield under microwaves is 14.1% by mass, at 110°C.
For the conversion of limonene to PCY, the SABIC patents refer to the conversion of terpenes to PCY by dehydrogenation in the presence of catalysts, such as ethylene diamine (C2H8N2) and an iron (III) chloride (FeCl3). The catalysts used are metals, amines or a combination of both. The mixture that enabled the synthesis in the laboratory was composed, for the first oxidation, of a mixture of ethylene diamine (525 mmol, 31.6 g), FeCl3 (0.964 mmol, 0.160 g) and Na (145 mmol, 3.34 g), the whole heated to 50°C under nitrogen atmosphere. The mixture darkens upon dissolution of the sodium. At this point, the temperature is raised to 100°C, and limonene can be added (742 mmol, 101 g) dropwise. The whole mixture is left to stand for 8h, still at 100 °C. Then, the mixture was cooled to room temperature before being diluted with water (300 ml). The limonene was converted to PCY up to 99%.
Patents filed by SABIC report the conversion of PCY to TA by oxidation, done in the absence of chromium oxide. This oxidation is more precisely broken down into two successive oxidations: one with a mineral acid, and the second with a metallic catalyst with oxidizing power. The laboratory study is done with a solution of p-cymene (742 mmol, 100 g) and water (400 ml). For the first oxidation, 65% HNO3 nitric acid (2.97 mol, 288 g) is added. The whole is mixed for 24 h. Afterwards, it is purified from its solvent before being mixed with sodium hydroxide NaOH (1.484 mol, 83 g) and 1 L of water. The second oxidation is done by taking the mixture from the first oxidation, and adding potassium permanganate KMnO4 (1.484 mol, 253 g) for 16 h. Then, the whole is filtered and washed with water, then sulfuric acid H2SO4 (98%) is added to bring down the pH of the solution to 1 (to precipitate the mixture). A terephthalic acid white solid is then formed, cleaned with water and dichloromethane before being dried at 80°C. The yield after the two oxidations is of 85%.
According to a study published in 2015, the process developed by SABIC is not yet sufficiently cost-effective due to the use of KMnO4, which seems still too expensive (Miller 2015). Future research should then turn to the use of a new catalyst. One of the routes is the use of metallic catalysts based on manganese (Mn) and iron (Fe) (Neaţu et al., 2016), and always under oxygenated conditions. This choice is explained by the industrial use of Mn2+ ions for the oxidation of p-xylene to TA, and by the improvement of redox properties in the presence of Fe3+ ions. The optimal parameters are established at 140°C, under 20 bar and for 24 h for a mixture of 3 mmol of p-cymene and 25 mg of catalyst. However, although the conversion of p-cymene to other compounds is 100%, the selectivity of TA is only 51%. This is due to the large number of intermediate molecules to this conversion (the selectivity of p-toluic acid, noted TOA, is 40%). Volanti et al. identified two possible routes to oxidize PCY to TA (Volanti et al., 2019). The first takes place when the oxidation occurs on the isopropyl group (C3H7), to form a tertiary cymene hydroperoxide (TCHP). Then, several routes are possible, with intermediate molecules such as: p-cymenol (COL), p,α-dimethylstyrene (DMS), p-methylacetophenone (MAP), p-tolualdehyde (TALD) and p-toluic acid (TOA). The second pathway occurs when the oxidation is done on the methyl group (CH4), to form PCHP. Cuminaldehyde (CA) and p-isopropyl benzoic acid (IBA) then intervene. Mn-Fe based catalysts are less selective than KMnO4.
Furane derivatives
Furan derivatives look interesting to produce p-xylene. This concerns mainly: 5-(hydroxymethyl)furfural (HMF), dimethylfuran (DMF) and furfural. Their structures allow the formation of p-xylene, with as main operation the Diels-Alder cycloaddition to remove the oxygen atom from the aromatic ring. Currently, DMF is used for the production of p-xylene, in reaction with ethylene via the Diels-Alder process. DMF is synthesized from HMF, which can be bio-sourced. In fact, HMF can be synthesized from lignocellulose from biomass, and more particularly from fructose (Román-Leshkov et al., 2007). It is produced from glucose, which can come from starch (Volanti et al., 2019). The three steps of this pathway: saccharification of starch to glucose, isomerization of glucose to fructose, and dehydration of fructose to HMF. The studies carried out during the last 15 years focus on the last step and the catalysts to be used. They are still at the laboratory scale (Román-Leshkov et al., 2007; Nikolla et al., 2011). Then, to convert HMF to DMF and obtain p-xylene, the different steps are presented in Figure 4: dehydration of fructose in HMF, hydrodeoxygenation of HMF to DMF, Diels-Alder cycloaddition of DMF and ethylene to form an oxygenated compound, and Dehydration of the oxygenated compound into p-xylene (Collias et al., 2014).
In 2007, Román-Leshkov et al. proposed a process using a biphasic reactor, with water and a partially miscible organic solvent with low boiling temperature (tetrahydrofuran THF or butanol). The solvent served as a phase for the extraction of HMF. An acid catalyst (HCl), used for the dehydration of fructose and the inorganic salt (here NaCl), is also used to improve the recovery of HMF (selectivity increased from 66% to 89%) and to ensure that there are two phases, regardless of the ratio Vorganic/Vaqueous. The authors recommend a mass percentage of fructose of about 30% and a Vorganic/Vaqueous ratio = 3.2 so that the phase to be extracted is already saturated in water and salt. The reactor is then heated to 80°C for 2 min, then 180 °C for 2.5–3 min before being cooled to −20°C. Phase separation and purification steps must be performed. The conversion rate is close to 75%. Nikolla et al. propose a process using a Sn-Beta zeolite catalyst and an acid (HCl, for a pH of 1) in a two-phase system (water/organic solvent). The results of the different experiments are reported in Table 2, which demonstrates the interest of using a two-phase system to increase the conversion of the raw material into HMF. This is due to the fact that the transformed HMF can be directly extracted from the aqueous phase and thus avoid its degradation. The authors also indicate that Sn-Beta is used for the isomerization of glucose to fructose while HCl is used for the dehydration of fructose into HMF (and conversion of starch to glucose). They also show the increase in selectivity of the reaction to produce HMF by addition of inorganic salts (NaCl, MgCl2, KBr and KCl). NaCl is reported to increase the most the selectivity.
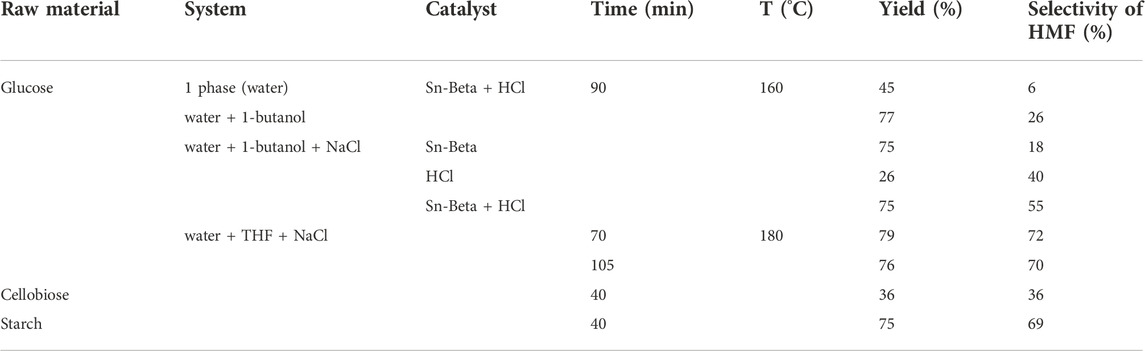
TABLE 2. Result of the conversion of glucose, cellobiose and starch into HMF (adapted from Nikolla et al., 2011).
Ava Biochem, a subsidiary of AVALON Industries, has industrialized HMF bio-production at a site in Muttenz, Switzerland, since 2014. Based on a 2011 patent (Vyskocil and Kruse 2013), the company was producing 20 tons of bio-based HMF per year in 2014 (Kläusli 2014). For other patents, the Chinese group China Petrochemical Corporation filed patents between 2013 and 2015 on the production of HMF from organic solvent and inorganic salts (Yangfeng et al., 2015; Ming et al., 2016). IFPEN also filed patents in 2015 on the use of acid catalysts from the sulfonic acid family (Souleymanou, Jacquin, and Delcroix 2017) or organic catalysts from the sulfonamide family (Souleymanou and Delcroix 2017). The reactions are carried out at temperatures between 30 and 300°C, and under pressures of 0.1–10 MPa.
For the conversion of HMF to DMF, done by hydrodeoxygenation, Román-Leshkov et al. used a copper, ruthenium and carbon (Cu-Re/C) catalyst. They mention a CuCrO4 copper chromate catalyst to perform this conversion (61% yield under optimized conditions). However, it is not currently applied in these conditions, because it is deactivated by the chloride ions present in the salts used, making the yield drop to 6%. Despite the possibility of deactivation of copper catalysts by Chloride, the developed Cu-Re/C catalyst is presented to be stable in chlorinated medium. HMF is dissolved in an organic solvent (1-butanol), with a 1:19 ratio. The air is removed from the reactor, and the pressure is increased to 20 bar by adding hydrogen. The whole is heated to 220°C for 10 h, under stirring at 400 rpm. Finally, the reactor is cooled to room temperature. The yield is 71%. Another study, conducted by Tao et al. from 2018, reports the use of formic acid as a hydrogen source, and a mixed gold, palladium, and tetragonal phase zirconia (AuPd/t-ZrO2) catalyst (Tao et al., 2018). For a 1.5 h reaction under 140°C, the HMF conversion was 99% with DMF selectivity of 97%.
The conversion of DMF and ethylene to p-xylene is a dehydration following the Diels-Alder mechanism (reaction between a diene and an alkene to form a cyclohexane derivative). The process was developed and patented by Toray Industries in 2008 (Takanishi and Sone 2009). Acid zeolite catalysts are conventionally used, such as H-Beta, which achieves a conversion of more than 99% at 250°C and 62 bar, with a selectivity for p-xylene of 90% (Miller 2015). Catalysts based on triflate (CF3SO3H, abbreviated to OTf) are also used, as with copper (Cu(OTf)2) or scandium (Sc(OTf)3). The conversions are however a little lower, between 75 and 94%. Tao et al., performed the conversion using the same catalyst as for the conversion of HMF to DMF (AuPd/t-ZrO2). Optimization of the process results in optimal conditions: 18 h reaction at 275°C, 1 mmol DMF, 5 ml n-heptane and 300 mg catalyst, which corresponds to conversion greater than 99%, with 90% selectivity. With these two transformations, the yield of the PX route from HMF was 85%. Finally, a 2014 study reports a 93% yield using a PtAl2O3 metal catalyst under 400°C (Collias et al., 2014). Research into more interesting and environmentally friendly catalysts is ongoing.
Others
Other ways are possible, although less solicited, for the production of TA (without necessarily going through p-xylene). Some of them are at the laboratory stage and others should be industrialized soon. They have not been further detailed because they are still minor and the building blocks produced do not yet offer sufficiently interesting or controlled conversion routes to p-xylene or TA. Table 3 below gives an overview of the different solutions proposed (Collias et al., 2014; Miller 2015). It should be noted that muconic acid seems to be more solicited than the other building blocks (an example is given in Figure 4), and that building blocks from glucose are predominant.
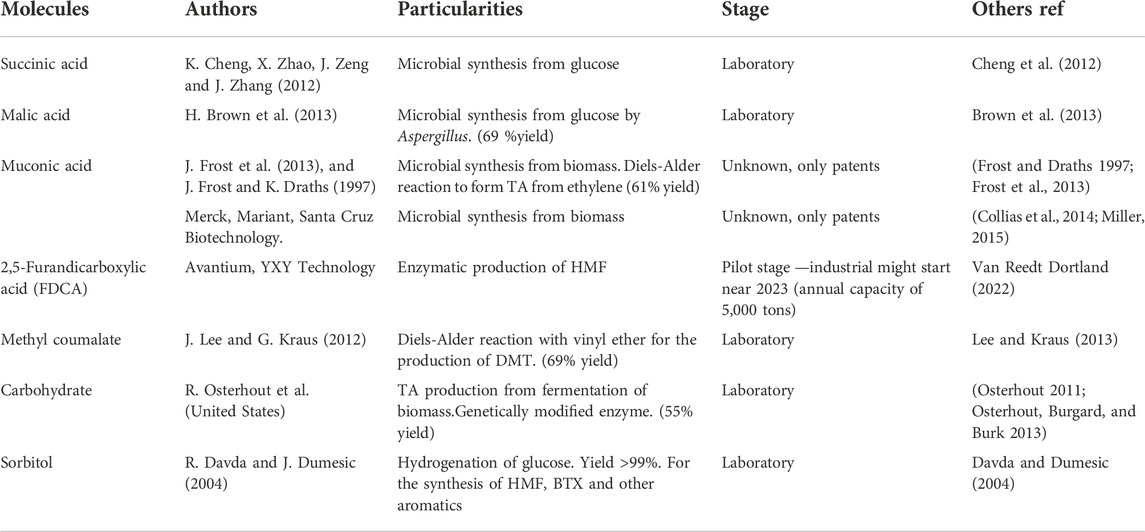
TABLE 3. Synthesis of the different molecules used for the synthesis of TA and example of research (adapted from Collias et al., 2014 and Miller, 2015).
5 Discussion and comprehensive point of view
Research into alternatives to oil for producing polymers has been very active for more than 30 years. The depletion of non renewable resources as well as the increasing deterioration of the environmental situation tends to accelerate this movement. This review highlights several synthons and processes for the production of PET from renewable resources. Although still produced in small quantities, some of them have been able to establish themselves in the industrial landscape, under the action of magnates. There is still little industrialization and the synthons are produced in small quantities, except ethanol. The other part is still confined to laboratory studies with the beginning of pilot tests for some. It should be emphasized that, even if some synthons are already commercialized, the research does not remain less active with the aim of improving yields, discovering cleaner catalysts, reducing energy consumption. This last part aims at discussing on different aspects to consider (petroleum-based quantity, raw material, economy of scale etc.) in order to understand the limits of each alternative building blocks sources discussed previously.
Taking stock of the level of maturity gives an initial idea of the research that still needs to be carried out to move towards the industrialization of a process. However, this is not the only criterion to consider for determining which pathway deserves the most attention and investment. Life cycle assessments (LCA) are a very good way to take into account environmental as well as social and economic factors. Unfortunately, these technologies are often too young to make LCA. This discussion aims at making a balance on the ways of synthesis and production of each studied synthon, to discuss the availability of the bio-sourced raw materials and to consider the associated issues. Thus, it will be possible to foresee the tracks likely to be followed.
To estimate the ability of the different solutions discussed to meet the current demand, it is necessary to evaluate the petroleum and bio-sourced production capacities. The values presented in Table 4 below are estimations based on different articles and statistical platforms such as Statista or PlaneteScope, with values before COVID-19 crisis (2020) and must be taken with hindsight. The petroleum shares may be slightly lower, as they are based on total production, without always knowing if a biobased part is included. Bio-based parts are not always known with accuracy because industrial processes are not well always developed and not all companies communicate on their production capacity. The annotation NL means “not listed” and appears for values that we could not fully determine. In addition, the bio-based synthons produced are not necessarily used to produce other bio-based synthons or resins but are sometimes produced only in pilot tests or are intended for other applications (such as biofuels). As a reminder, PET production was estimated to be higher than 30 million tons in 2017, of which about 250 kt was bio-based. For all the synthons, we notice that the important volumes produced are still very far from being bio-sourced. This observation is understandable as the industrialization of these synthons is incipient. There is no doubt that if cost effectiveness is demonstrated, a transition could take place. Indeed, the sites of transformation of a synthon into another would not have, or little, to undergo transformation, because only the origin of the raw material would be changed. A unit transforming p-xylene into terephthalic acid would probably not see significant difference between petroleum-based and bio-based p-xylene.
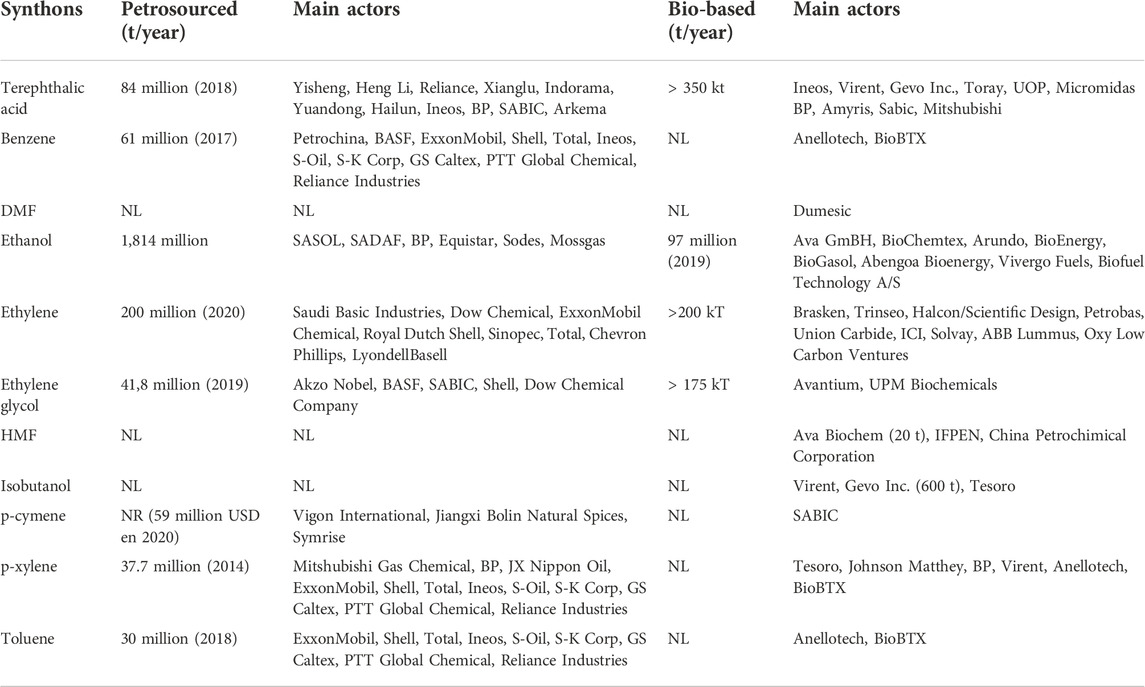
TABLE 4. Production capacity and main actors for the synthesis of the studied synthons (NL means “not listed”).
Table 5 below shows the current status of the bio-sourced origin of raw materials such as starch, glucose and cellulose. For each of these molecules, the world production in terms of tons and hectares, the main producing countries and the sectors competing with the production of bio-plastics have been listed. The values shown are for all global production, regardless of the purpose of the product. For example, 370 million tons of potatoes produced in 2019 does not mean that 370 million tons of starch were produced from potatoes in 2019, but that the starch to be used as a molecule of interest may come from potatoes whose global production was 370 million tons in 2019. The values must be taken with hindsight, as annual production can vary from 1 year to another, depending on diseases, natural disasters, etc.
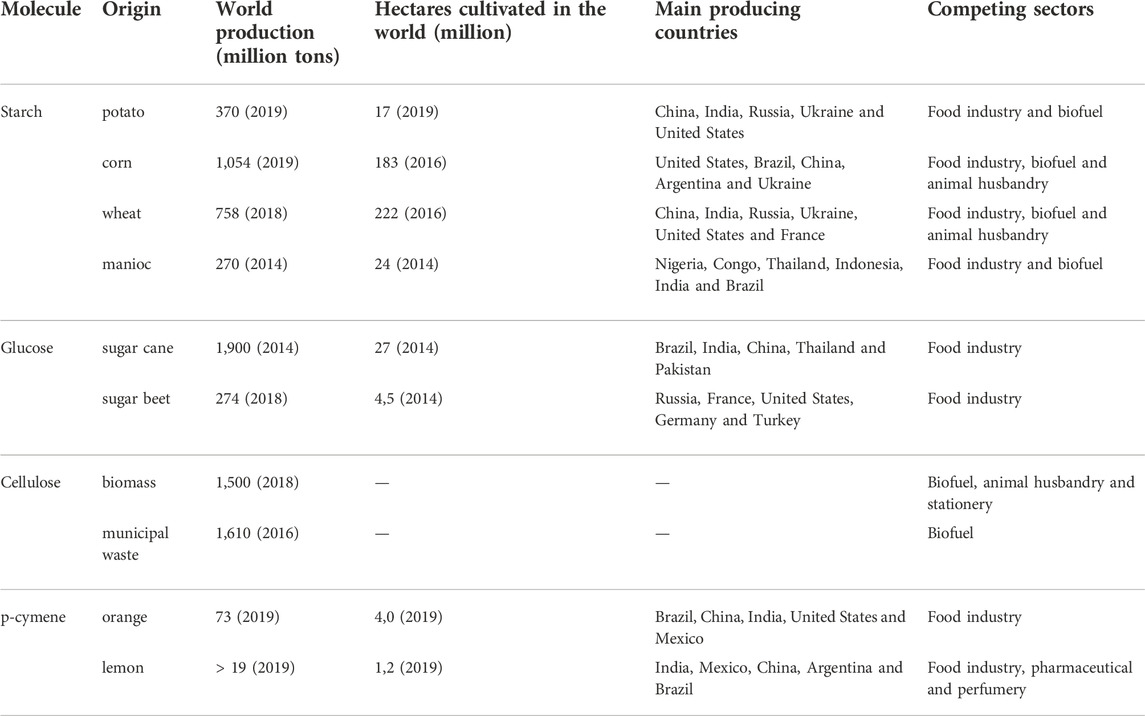
TABLE 5. Origin, production capacity, in volume and surface area, main producers and competing sectors for the production of molecules used as raw materials.
Starch is one of the most used raw materials because its saccharification allows to obtain glucose. It is a plant-based polysaccharide found mainly in cereals (corn, wheat, etc.) and tubers (potato, manioc, etc.). It represents an important part of the dry matter: 30–70% for cereal seeds and 60–90% in tubers (Wertz et al., 2016). Being a source of energy for living organisms, it is used in the agri-food sector (livestock and food industry). It is also found in the pharmaceutical, cosmetic and more recently chemical industries. Indeed, as it has been demonstrated in this report, its fermentation allows the synthesis of many molecules of interest. The problem of starch availability arises when several sectors compete. Globally, Planetscope makes an approximate production of corn of 863 million tons in 2012, of wheat of 758 million tons in 2018, of cassava of 250 million tons in 2009.
The United States produce 40% of the world’s corn and consume a very large part of it (80%). This corn is used for animal consumption, for food as well as for the production of bio-ethanol. This use has grown so rapidly that it accounts alone for 40% of United States corn production (Vaughan 2020). The total crop area is 166 million hectares, and 22% (37 million hectares) is dedicated to corn (U.S. Department of the Interior 2021). Thus, 15 million hectares (8.8% of crops) are used for ethanol production (Buckner 2018). The crops are mainly located in the Midwest, where bio-ethanol production plants are located. This bio-ethanol is used to make biofuels that contribute to 10% of United States fuel production. The industry wants to increase this percentage to 15–20% in the long term. This would mean using 17.6% of the crop to grow corn for bio-ethanol. This means using almost 1/5 of the agricultural capacity for a grain that will not be used to feed people or animals at a time when the food consumption and cattle breeding are intensifying. Since the 1990s, about 95 percent of corn production has been used for livestock and consumption. By further reducing the proportion of corn for food, supply will decrease while demand will continue to increase suggesting the price of corn will increase. As the United States is the largest exporter of corn (49% of world exports, or 45 million tons), the price of corn is largely based on its production. This effect has already been felt as the price per bushel has risen from $1-2 in the early 2000s to $4-7 during the 2010s (Macrotrends 2021). Farms using corn as feed are passing on this increase to the final products: egg, milk or meat (Bullis 2011). The overconsumption of fuel and feed impacts the economics of bio-ethanol. For bio-ethanol to be stable or profitable, the share of corn used for food would have to decrease, which seems difficult to envisage.
From an environmental point of view, bio-ethanol is also subject to discussion. If we focus on its use as biofuel, the CO2 released during its combustion is theoretically absorbed by the corn plantations necessary for its future production. This is done over a fairly short period of time, which means that this resource, unlike oil, can be considered as renewable. It is this aspect that, in a circular economy context, drives its production. However, CO2 is not the only factor to be taken into account when assessing the ecological interest. This is what Professor David Pimentel tried to show by studying, in 2005, the impact of the different stages of bio-ethanol production [266]. He based his study on the data available at the time in terms of energy, and considered the production of corn (seed, watering, labor, machinery, insecticides, etc.) and its transformation into bio-ethanol (seed, water, electricity, etc.). He established that the production of 1 L of bio-ethanol requires 6,600 kcal. However, he had established that this same liter of bioethanol contained only 5,130 kcal, a difference of 22.3%. It is then a negative energy process. Howeved, other studies, conducted before or after Pimentel’s one, conclude that it is a positive energy process. For example, a 2018 study, as seen in the bio-ethanol section, reports a 40% gain (Paz Cedeno et al., 2018). These differences are explained by the number of inputs for the calculations and the energy values used. They also highlight the uncertainty about the real ecological impact of bio-ethanol produced from corn. As this case is fuel related, gain calculation should be established for the specific case of polymer production and use.
Corn is undoubtedly a very interesting source of starch for the production of bio-plastics, but its cultivation and transformation should lead more people to suffer from hunger in the world (FAO et al., 2022).
Glucose is also one of the most requested raw materials, if not the most. Indeed, starch and lignocellulose are both used to obtain glucose. The sources that are naturally rich in glucose are therefore very interesting. This concerns mainly sugar cane (14%) and sugar beet (15–18%) where it is produced by photosynthesis. At the global level, these crops represent respectively 1,900 million tons in 2014, and 274 million tons in 2018. The main sugarcane producing countries are Brazil (40%), India (19%), China (7.0%) and Thailand (5.5%). The main sugar beet producing countries are Russia (15%), France (14%), United States (11%) and Germany (9.5%). Both plants are used for the production of glucose. The latter, and more widely sucrose (glucose + fructose), is used almost exclusively in the food industry to produce sugar. However, it is increasingly used for the production of first generation biofuels. The same problems as for starch and maize arise: should current production be used for food or for chemistry? The case of sugarcane will be treated with the case of Brazil, the first world producer, whose agricultural policy underlines the environmental problems linked to sugarcane.
Brazil produced 736 million tons of sugarcane, spread over 27 million hectares, in 2014. Part of this is used to produce ethanol, making the country the second largest producer in the world (27%). The crops are mainly located in the south of the country, in the states of Sao Paulo, Parana, Goias and Minas Gerais. With agribusiness accounting for 23.5% of GDP in 2017, sugar cane is an essential pillar of the country. In 2017, most of the sugarcane produced was not for sugar (45%) but for ethanol (55%) (Gaudoin 2018). Of this ethanol, only 6% was for export. Thus, the price of sugar will depend on Brazil’s ethanol production. It has been estimated that a 1% fluctuation in ethanol production leads to a fluctuation of 1.4% in sugar exports, which also impacts the price of sugar. Like corn starch, the production of sugarcane for ethanol will increase the price of sugar for the agribusiness, with implications for the price of processed products.
On the ecological aspect, the balance is questioning. This time, it is not about the ratio of energy produced to energy consumed but about a problem that particularly affects Brazil: deforestation, as represented in Figure 9. With the numerous government subsidies, sugarcane production in Brazil has increased fivefold in less than 25 years. For such a growth to be possible, there is a need for a significant increase in agricultural land. In Brazil, the “world’s farm”, the creation of new agricultural land, however, has resulted in massive deforestation. Like the massive deforestation of the Amazon rainforest for cattle, soy or palm oil, the deforestation of the Atlantic forest (west coast of Brazil) is for sugar cane. This forest now represents only 10 million hectares, compared to 1,290 million hectares at the beginning of the 20th century (i.e. more than 7.3%). Urbanism is also responsible, but the current deforestation still concerns agriculture (Haddad et al., 2015). This deforestation for the benefit of agriculture threatens biodiversity, leads to water and air pollution as well as the expropriation of indigenous peoples.
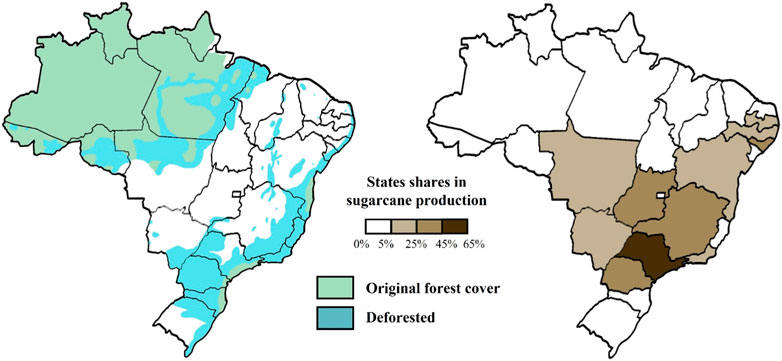
FIGURE 9. Extent of the Amazon Forest from the 16th century to the present day and distribution of sugar crop production in Brazil in 2018 (adapted from Gaudoin, 2018 and Haddad et al., 2015).
Lignocellulosic biomass has a high availability with about 1.5 billion tons produced per year (Deshavath, Veeranki, and Goud 2019). A large part of these lignocellulosic materials comes from agricultural residues which are, for a part, used as animal feed but mostly burned. This practice is a source of greenhouse gases. In 2016, the European Union produced 1.7 million tons of CO2 equivalent. The sources of lignocellulosic biomass can come from agricultural residues (stems or leaves) or from forestry. Some herbaceous plants can be grown with a much higher yield than corn or sugarcane. The use of second generation biomass can have a limited impact from a socio-economic point of view if it is the agricultural surplus that is used. Otherwise, the problems of land use change and arable land use are still present.
Citrus fruits can be used for limonene extraction and TA synthesis. Their global production is much lower than sugar or starch, with about 100 million tons in 2019. This limits the amount that could be used for plastic production. For example, in 2015, it was stated that 37% of the volume of oranges produced ended up as waste, mainly consisting of peels (Miller 2015). The extraction of limonene from these peels has a yield between 4.7 and 11.1% with current techniques. The yield for the synthesis of terephthalic acid from p-cymene, itself produced from limonene, is 84%. Finally, and in the best case, the yield of bark to terephthalic acid is 9.3%. Thus, by collecting current citrus production, we would have 37 million tons of peel that would produce 3.4 million tons of terephthalic acid. The current production of terephthalic acid is over 84 million tons. Therefore, citrus could, at best, contribute 4% of the terephthalic acid production. To reach 100% TA, 903 million tons of peel would have to be produced, or 2,440 million tons of citrus, corresponding to about 146 million hectares. This is more than 20 times the current area. Citrus may still be interesting as a complementary production to other alternatives. However, it would be necessary to locate the processing sites as close as possible to the food industry or to limit transportation costs. It seems more reasonable to use all these small sources of raw material only when they are derived from waste.
Authors point of view and conclusion
The Table 6 lists the advantages, disadvantages and economies of scale considered for the routes studied. We observe than one of the recurring problems remains the possible competition with biofuels or agri-food industries. As this industry is also very dependent on oil, it is looking for bio-sourced alternatives. Two major cases have been illustrated in this report and show that, at present, the synthons concerned are intended more for fuels, such as bio-ethanol and isobutanol, than for plastics through the production of bio-ethylene. From an environmental point of view, the two uses are roughly equivalent. A life cycle study (McKechnie et al., 2015), carried out with bio-ethanol made from corn, estimates that the use of one ton of CO2 to produce ethylene avoids the release of 2.3 kg of CO2 equivalent, whereas if ethanol is used as a fuel, the release of 2.5 kg of CO2 equivalent is avoided. Currently, bio-ethanol is mainly used to produce biofuels whereas isobutanol, is produced on a much smaller scale but raises the same problem.
From all these observations, it is not easy to determine which pathway is the most relevant for the production of bio-based PET. We can see that the problem of plastic production is not only related to oil, but also to the global overconsumption. This overconsumption obviously concerns plastics, but also foodstuffs. As these industries are linked and in competition, one will inevitably have an impact on the other. It is essential to have the broadest possible vision to respond to the current situations: should we work on access to raw materials, the maturity of the technology, yields, catalysts, etc.? In general, catalysts and yields will constantly be the focus of studies, even for technologies that are already industrialized. The main problem is the access to raw material, and more specifically competition with other industries (food, animal husbandry or fuel). Life cycle assessments are essential to consider and evaluate the maximum impact and to see if the transition from petroleum-based to bio-based does not just move the barriers. These analyses should not only estimate the release of CO2 but also the impacts of all resources and products used: water, pesticides, raw materials, energy etc.
For ethylene glycol, it is the production of ethylene that should be prioritized via second generation bio-ethanol, because it can be based on green waste that would have no other use. For terephthalic acid, p-xylene seems the priority synthon of interest. Its production from isobutanol seems a way to be favored on the technological aspect. Indeed, the Gevo and Virent processes are already industrialized, even if the production capacities are still low (less than 350 kt produced per year). It is therefore necessary to continue to optimize these processes, especially in order to improve the yields which are quite low. However, isobutanol is mainly used to produce biofuels for aviation and marine applications. Its price will therefore be linked to its availability. The major problem remains the availability of raw materials. In the case of Gevo, corn is used to form glucose. Since the yield of production of glucose from isobutanol is 41%, and isobutanol to p-xylene is 18.7%, less than 500 million tons of glucose would have been necessary to synthesize the 37.7 million tons of p-xylene produced in 2014. Even in the ideal case, considering that corn is made of 100% starch which allows to obtain 100% glucose, it would be necessary to use half of the world production of corn based on the 2019 production. Obviously, this does not seem feasible as production capacity will be limited by competition with the food and livestock industries. As with ethylene, efforts should focus on access to raw materials, by finding sources of starch/glucose that do not conflict with other industries. In the idea of having a raw material other than food, HMF and furans are a good alternative. Currently, the fructose used is derived from biomass and yields are higher than for isobutanol (HMF in p-xylene has a yield of 85%). However, its production is very limited and still at the pilot stage. Therefore, for HMF it is also necessary to focus on the technological aspects. First of all, to correctly size the installations, improve the processes but also to consider the possibilities of rehabilitation of plants which normally produce terephthalic acid from p-xylene. These changes in installations can possibly present a non-negligible cost and may be a brake to the development of this technology.
The different solutions proposed display advantages that can become very interesting if research contributes to their improvement. On the other hand, when considering the problem of the competition with food, fuels, availability of raw material, it seems that there is not one ideal solution but several ones. In particular, as producing bio-sourced polymers at a large-scale could lead to problems of access to resources, a local economy involving small volumes of materials adapted to the resources of the territory could be an alternative.
Author contributions
Conceptualization, BS VM, and RB; Methodology, BS VM, and RB; Formal Analysis, BS VM, and RB; Investigation, BS VM, and RB; Data Curation, BS VM, and RB; Validation, BS VM, and RB; Visualization, BS VM, and RB; Writing Original Draft Preparation, BS VM, and RB; Writing Review and Editing, BS VM, and RB Resources, BS, VM, and RB; Project Administration, BS, VM, and RB All authors have read and agreed to the published version of the manuscript.
Funding
CITEO (https://www.citeo.com/) has funded part of the present study. Valuable discussions with CITEO staff members have enabled to clarify what society expects from research to contribute to a circular economy depending less on non renewable resources.
Acknowledgments
The authors wish to acknowledge Orianne Broussard and Vincent Colard, Mael Gueneguan, Yann-Ulrich Feuzing-Tango for valuable discussions and CITEO for financial support.
Conflict of interest
The authors declare that the research was conducted in the absence of any commercial or financial relationships that could be construed as a potential conflict of interest.
Publisher’s note
All claims expressed in this article are solely those of the authors and do not necessarily represent those of their affiliated organizations, or those of the publisher, the editors and the reviewers. Any product that may be evaluated in this article, or claim that may be made by its manufacturer, is not guaranteed or endorsed by the publisher.
Abbreviations
1G/2G/3G, first, second and third generation ethanol; BTX, butene, toluene, xylene; DMF, dimethylfuran; EG, ethylene glycol; HDPE, high density polyethylene; HMF, 5-(hydroxymethyl)furfural; LCA, life cycle assessments; LDPE, low density polyethylene; NL, non listed; PBAT, polybutylene adipate terephthalate; PCY, p-cymene; PET, poly(ethylene terephthalate); PLA, polylactic acid, polylactide; PP, polypropylene; PS, polystyrene; PVC, polyvinyl chloride; PX, p-xylene; TA, terephthalic acid; ZSM-5, Zeolite Socony Mobil-5 (aluminosillicate zeolite).
References
Attard, Thomas M., Watterson, Baillie, Vitaliy, L., Budarin, James H. Clark, and Hunt, Andrew J. (2014). Microwave assisted extraction as an important technology for valorising orange waste. New J. Chem. 38 (6), 2278–2283. doi:10.1039/C4NJ00043A
Green Car Congress, (2015). National marine manufacturers association endorses use of isobutanol in marine fuel market.” green car congress. June 18, 2015).
Cortright, Randy D., and Blommel, Paul G. (2011). Synthesis of liquid fuels and chemicals from oxygenated hydrocarbons. Available at: https://patents.google.com/patent/US8017818/en?oq=US8017818.
Cortright, Randy D., and Blommel, Paul G. (2011c). Synthesis of liquid fuels and chemicals from oxygenated hydrocarbons. Available at: https://patents.google.com/patent/US20110257448A1/en?oq=US2011%2f0257448.
Axens (2022). Plastic recycling | Axens.” Axens powering integrated solutions. Available at: https://www.axens.net/markets/plastic-recycling.
Badran, Adnan, Murad, Sohail, Elias, Baydoun, and Daghir, Nuhad (2017). Water, energy & food sustainability in the Middle East: The sustainability triangle. 1st ed. Heidelberg, Germany: Springer.
Berti, Corrado, Binassi, Enrico, Colonna, Martino, Fiorini, Maurizio, Kannan, Ganesh, Karanam, Sreepadaraj, et al. (2010a). Bio-based terephthalate polyesters. Available at: https://patents.google.com/patent/US20100168372/en?oq=2010%2f0168372.
Berti, Corrado, Binassi, Enrico, Colonna, Martino, Fiorini, Maurizio, Kannan, Ganesh, Karanam, Sreepadaraj, et al. (2010). Bio-based terephthalate polyesters. Available at: https://patents.google.com/patent/US20100168371/en?oq=2010%2f0168371.
Bioplastics, European (2021). European Bioplastics (blog). Available at: https://www.european-bioplastics.org/market/.
B.P. (2019). partners with virent and Johnson Matthey on virent’s bioforming process for production of bio-paraxylene. Focus Catal. 2019 (10), 6. doi:10.1016/j.focat.2019.09.030
Brown, Stephen H., Bashkirova, Lena, Berka, Randy, Chandler, Tyler, Doty, Tammy, McCall, Keith, et al. (2013). Metabolic engineering of Aspergillus oryzae NRRL 3488 for increased production of L-malic acid. Appl. Microbiol. Biotechnol. 97 (20), 8903–8912. doi:10.1007/s00253-013-5132-2
Buckner, Chris. 2018. “U.S. Fuel ethanol production capacity continues to increase.” Eia, U.S. Energy Inf. Adm. August 1, 2018.
Caliendo, Heather (2021). Switzerland retail company producing PET bottles made from recycled carbon. Switzerland: Plastics Technology.
Cargill. 2020. “Cargill and virent collaborate to study virent’s BioForming® technology to produce biobased fuels and chemicals | Cargill.” Cargill, Help. World Thrive. September 30, 2020.
Cheng, Ke-Ke, Zhao, Xue-Bing, Zeng, Jing, and Zhang, Jian-An (2012). Biotechnological production of succinic acid: Current state and perspectives. Biofuel. Bioprod. Biorefin. 6 (3), 302–318. doi:10.1002/bbb.1327
Claypool, Joshua T., Raman, D. Raj, Laura, R. Jarboe, and Nielsen, David R. (2014). Technoeconomic evaluation of bio-based styrene production by engineered Escherichia coli. J. Ind. Microbiol. Biotechnol. 41 (8), 1211–1216. doi:10.1007/s10295-014-1469-5
Coca-Cola Company. 2021. “Bottles made from 100% plant plastic.” The Coca-Cola Company. October 21, 2021.
Collias, Dimitris I., Harris, Angela M., Nagpal, Vidhu, Cottrell, Ian W., and Schultheis, Mikell W. (2014). Biobased terephthalic acid technologies: A literature review. Ind. Biotechnol. 10 (2), 91–105. doi:10.1089/ind.2014.0002
Colonna, Martino, Berti, Corrado, Fiorini, Maurizio, Binassi, Enrico, Mazzacurati, Marzia, Vannini, Micaela, et al. (2011). Synthesis and radiocarbon evidence of terephthalate polyesters completely prepared from renewable resources. Green Chem. 13 (9), 2543. doi:10.1039/c1gc15400a
Cortright, Randy D., and Blommel, Paul G. (2011a). Synthesis of liquid fuels and chemicals from oxygenated hydrocarbons. Available at: https://patents.google.com/patent/US7977517B2/en?oq=US7977517.
Daniell, James, Köpke, Michael, and Simpson, Séan Dennis (2012). Commercial biomass syngas fermentation. Energies 5 (12), 5372–5417. doi:10.3390/en5125372
Davda, Rupali R., and Dumesic, James A. (2004). Renewable hydrogen by aqueous-phase reforming of glucose. Chem. Commun. 1, 36–37. doi:10.1039/B310152E
Anne-Laure, De Marignan, and Amélie, Poncelet (2020). 2nd generation biofuels: An industrial first for French FuturolTM technology. IFPEN.
Deshavath, Narendra Naik, Veeranki, Venkata Dasu, and Goud, Vaibhav V. (2019). Lignocellulosic feedstocks for the production of bioethanol: Availability, structure, and composition. Sustain. Bioenergy, 1. doi:10.1016/B978-0-12-817654-2.00001-0
Devarapalli, Mamatha, and Atiyeh, Hasan K. (2015). A review of conversion processes for bioethanol production with a focus on syngas fermentation. Biofuel Res. J. 2 (3), 268–280. doi:10.18331/BRJ2015.2.3.5
Fairbrics (2020). Technology – Fairbrics.” Fairbrics (blog). Available at: https://fairbrics.co/technology/.
Fao, I. F. A. D., Unicef, W. F. P., and Who, (2022). Repurposing food and agricultural policies to make healthy diets more affordable. Rome: FAO.
Carlos Eduardo, De Farias Silva, and Alberto, Bertucco (2016). Bioethanol from microalgae and cyanobacteria: A review and technological outlook. Process Biochem. 51 (11), 1833–1842. doi:10.1016/j.procbio.2016.02.016
Feldman, Reid, Gunawardena, Uvini, Urano, Jun, Meinhold, Peter, Aristidou, Aristos, Dundon, Catherine Asleson, et al. (2018). Yeast organism producing isobutanol at a high yield. Available at: https://patents.google.com/patent/US20180179557A1/en?q=Yeast+organism+producing+isobutanol+high+yield&assignee=gevo&sort=new.
Feldman, Reid M. Renny, Gunawardena, Uvini, Urano, Jun, Meinhold, Peter, Aristidou, Aristos A., and Asleson, Catherine (2011). Yeast organism producing isobutanol at a high yield. Available at: https://patents.google.com/patent/US8017375B2/en.
Fragnière, Céline, Aebischer, Jean-Nicolas, Vincent, Dudler, and Fritz, Sager (2003). A Short Study on the Formation of Styrene in Cinnamon.
Frost, John W., and Draths, Karen M. (1997). Bacterial cell tranformants for production of cis, cis-muconic acid and catechol. Available at: https://patents.google.com/patent/US5616496A/en?oq=5%2c616%2c496.
Frost, John W., Miermont, Adeline, Schweitzer, Dirk, Vu, Bui, and Wicks, Douglas A. (2013). Terephthalic and trimellitic based acids and carboxylate derivatives thereof. Available at: https://patents.google.com/patent/US8367858/en?oq=8%2c367%2c858+B2.
Gaudoin, Christopher. 2018. “La politique sucrière Au brésil : La régulation par l’éthanol.” agriculture strategies. November 6, 2018.
Geyer, Roland, Jambeck, Jenna R., and Law, Kara Lavender (2017). Production, use, and fate of all plastics ever made. Sci. Adv. 3 (7), e1700782. doi:10.1126/sciadv.1700782
GreenCongress, Car (2011). Virent produces biogasoline reformate from cellulosics, with molecular composition similar to petroleum reformate stream.” green car congress. June 3, 2011.
Haddad, Nick M., Brudvig, Lars A., Clobert, Jean, Davies, Kendi F. Andrew Gonzalez, Holt, Robert D., Lovejoy, Thomas E., et al. (2015). Habitat fragmentation and its lasting impact on earth’s ecosystems. Sci. Adv. 1 (2), e1500052. doi:10.1126/sciadv.1500052
Heinrich Böll Foundation, and Break Free From Plastic, (2019). Plastic atlas 2019: Facts and figures about the world of synthetic polymers. 2nd ed. Berlin: Heinrich Böll foundation.
Huber, George W., Cheng, Yu-Ting, Carlson, Torren, Vispute, Tushar, Jungho, Jae, and Tompsett, Geoff (2009). Catalytic pyrolysis of solid biomass and related biofuels, aromatic, and olefin compounds. United States US20090227823A1.
Kläusli, Thomas (2014). AVA Biochem: Commercialising renewable platform chemical 5-HMF.” green Processing and synthesis 3. doi:10.1515/gps-2014-0029
Ladaniya, Milind S. (2008). “6 - fruit biochemistry,” in Citrus fruit. 125–90. Editor Milind S. Ladaniya (San Diego: Academic Press). doi:10.1016/B978-012374130-1.50008-5
Lee, Jennifer J., and Kraus, George A. (2013). Divergent diels–alder methodology from methyl coumalate toward functionalized aromatics. Tetrahedron Lett. 54 (19), 2366–2368. doi:10.1016/j.tetlet.2013.02.083
Ma, Ming, Han, Xiao, Jiang, Ming, Zou, Bing, and SuJiang, Xia (2015). Inorganic salt catalytic synthesis method for 5-hydroxy methyl furfural. Available at: https://patents.google.com/patent/CN105330623A/en?oq=CN105330623+.
Marathon Petroleum (2022). Renewable fuels.” Marathon petroleum. Available at: https://www.marathonpetroleum.com/Operations/Renewable-Fuels/.
McKechnie, Jon, Pourbafrani, Mohammad, Saville, Bradley A., and MacLean, Heather L. (2015). Environmental and financial implications of ethanol as a bioethylene feedstock versus as a transportation fuel. Environ. Res. Lett. 10 (12), 124018. doi:10.1088/1748-9326/10/12/124018
Miller, Kelly (2015). Process for preparation of terephthalic acid. Chimie, Michigan, USA: Michigan State University.
National Geographic Uk, (2021). 10 shocking facts about plastic.” national geographic. March 24, 2021.
Neaţu, Florentina, Culică, Geanina, Florea, Mihaela, Parvulescu, Vasile I., and Cavani, Fabrizio (2016). Synthesis of terephthalic acid by P-cymene oxidation using oxygen: Toward a more sustainable production of bio-polyethylene terephthalate. ChemSusChem 9 (21), 3102–3112. doi:10.1002/cssc.201600718
Nikolla, Eranda, Román-Leshkov, Yuriy, Moliner, Manuel, and MarkDavis, E. (2011). ‘One-Pot’ synthesis of 5-(Hydroxymethyl)Furfural from carbohydrates using tin-beta zeolite. ACS Catal. 1 (4), 408–410. doi:10.1021/cs2000544
Norris, Shelly (2016). Tesoro to Acquire Virent in Support of Commercializing Renewable Fuels and Chemicals. Virent, Inc. Sept. 6.
Osterhout, Robin E., Burgard, Anthony P., and Burk, Mark J. (2013). Microorganisms and processes for producing terephthalic acid and its salts. World Intellectual Property Organization WO2013109865A2.
Osterhout, Robin E. (2011). Microorganisms and methods for the biosynthesis of p-toluate and terephthalate. U. S. US20110207185A1, filed January 25.
Oyler, James R. (2021). Two-stage process for producing oil from microalgaeSalt Lake City, UT: United States US20210071213A1.
Pang, Jifeng, Zheng, Mingyuan, Sun, Ruiyan, Wang, Aiqin, Wang, Xiaodong, and Zhang, Tao (2016). Synthesis of ethylene glycol and terephthalic acid from biomass for producing PET. Green Chem. 18 (2), 342–359. doi:10.1039/C5GC01771H
Paz, Cedeno, Roberto, Fernando, Chavez, Eddyn, Oliveira, L. E., Gelli, Valéria, Monti, Rubens, et al. (2018). Bioethanol and Beyond: Advances in Production Process and Future Directions, 203–30. New York: Nova Science Publishers.Perspectives for the production of bioethanol from macroalgae biomass
Peters, Matthew W., Taylor, Joshua D., Jenni, Madeline, Manzer, Leo E., and Henton, David E. (2011). Integrated process to selectively convert renewable isobutanol to p-xylene. Available at: https://patentimages.storage.googleapis.com/34/3c/ba/eccd552d8e73b6/US20110087000A1.pdf.
Rasul, Md. Mustaun, Shah, Jasmin, and Rahim, Abdur (2008). Recovery of styrene monomer from waste polystyrene using catalytic degradation. Am. Laboratory 40 (2 February), 12–14.
Ren, Haiyu, Qiao, Fangqing, Shi, Yu, Knutzen, Michael W., Wang, Zhou, Du, Huanzheng, et al. (2015). PlantBottleTM packaging program is continuing its journey to pursue bio-mono-ethylene glycol using agricultural waste. J. Renew. Sustain. Energy 7 (4), 041510. doi:10.1063/1.4929336
Rodewald, David, and Severson, Shawn (2017). EPA approves pathway for isobutanol as an advanced biofuel. Gevo Inc. - News. January 17, 2017.
Román-LeshkovLiu, Yuriy, Christopher J. BarrettZhen Y., Dumesic, James A., Liu, Z. Y., and Dumesic, J. A. (2007). Production of dimethylfuran for liquid fuels from biomass-derived carbohydrates. Nature 447 (7147), 982–985. doi:10.1038/nature05923
Ryan, Dr. Chris (2019). An overview of gevo’s biobased isobutanol production process. Englewood, CO): Gevo Inc.
Schwartz, Michael M., and Stark., Leonard E. (1987). Direct continuous flow integration of production and purification of high purity iso- or terephthalic acid. Available at: https://patents.google.com/patent/US4675438A/en.
Smith, Christopher, Hanley, Timothy, and Benoit, Jeanne (2021). Novel nkr variants for increased production of isobutanol. Geneva, Switzerland: World Intellectual Property Organization WO2021178805A1.
Souleymanou, Myriam, and Delcroix, Damien (2017). Procede de production de 5-hydroxymethylfurfural en presence de catalyseurs organiques de la famille des sulfonamides. Rueil-Malmaison (France): World Intellectual Property Organization WO2017016925A1.
Souleymanou, Myriam, Jacquin, Marc, and Delcroix, Damien (2017). Procede de production de 5-hydroxymethylfurfural en presence de catalyseurs de la famille des acides sulfoniques homogenes en presence d’au moins un solvant polaire aprotique. Rueil-Malmaison (France): World Intellectual Property Organization WO2017076626A1.
Steele, David H., Thornburg, Michael J. John S. Stanley, Miller, Roland R. Richard Brooke, Cushman, Janette R., George, Cruzan, Cushman, J. R., et al. (1994). Determination of styrene in selected foods. J. Agric. Food Chem. 42 (8), 1661–1665. doi:10.1021/jf00044a015
Sudolsky, David, Mendes-Jorge, Barbara, De Marignan, Anne-Laure, and Garriga, Corinne (2019). 100% renewable plastic bottle significantly closer to reality after successful production of bio-based paraxylene from non-food biomass bio-based benzene is next. Anellotech, IFPEN Axens 23.
Sun, Xiao, Atiyeh, Hasan K., Huhnke, Raymond L., and Tanner, Ralph S. (2019). Syngas fermentation process development for production of biofuels and chemicals: A review. Bioresour. Technol. Rep. 7 2 (September), 100279. doi:10.1016/j.biteb.2019.100279
Takanishi, K., and Sone, S. (2009). Procédé de production du paraxylène. Available at: https://patents.google.codslum/patent/WO2009110402A1/fr?oq=2009%2f110402.
Tao, Lei, Yan, Tian-Hao, Li, Wenqin, Zhao, Yi, Zhang, Qi, Liu, Yong-Mei, et al. (2018). Toward an integrated conversion of 5-hydroxymethylfurfural and ethylene for the production of renewable p-xylene. Chem 4 (9), 2212–2227. doi:10.1016/j.chempr.2018.07.007
Tian, Peng, Wei, Yingxu, Ye, Mao, and Liu, Zhongmin (2015). Methanol to olefins (MTO): From fundamentals to commercialization. ACS Catal. 5 (3), 1922–1938. doi:10.1021/acscatal.5b00007
Ursachi, Vasile-Florin, and Gutt, Gheorghe (2020). Feedstocks used for production of 2nd and 3rd generation bioethanol - review. Food Environ. Saf. J. 19 (2), 156–169.
U.S. Department of the Interior, (2021). Map of croplands in the United States. Available at: https://www.usgs.gov/media/images/map-croplands-united-states.
Van Reedt Dortland, Caroline (2022). Avantium reaches financial close for its FDCA flagship. Avantium: Plant - Press Release.
Vaughan, Carson (2020). Ethanol market is disturbing to American farmers. And now there’s covid-19. Success. Farming, March 30, 2020.
Ventures, A. P. (2022). Fairbrics raises over EUR6.5m to develop carbon-neutral fabrics for the fashion industry. AP Ventur. Adv. Pioneer 2022.
Volanti, M., Cespi, D., Passarini, F., Neri, E., Cavani, F., Mizsey, P., et al. (2019). Terephthalic acid from renewable sources: Early-stage sustainability Analysis of a bio-PET precursor. Green Chem. 21 (4), 885–896. doi:10.1039/C8GC03666G
Vyskocil, Jan, and Kruse, Andrea (2013). Verfahren zur Extraktion von Furfuralen aus Biomasse. Available at: https://patents.google.com/patent/DE102011053034A1/de?oq=DE102011053034.
Waal, Jan C., and de Jong, Ed (2013). Producing fuels and fine chemicals from biomass using nanomaterials. CRC Press.
Wang, Yangfeng, Bo, Dechen, Zang, Long, Zhang, Shengzhong, and Gao, Jingshan (2015). Method for producing 5-hydroxymethyl furfural. Available at: https://patents.google.com/patent/CN104557805A/en?oq=CN104557805.
Jean-Luc, Wertz, Céline, Heneffe, Aurore, Richel, and Patrick, Gerin (2016). ValBiom. Polymères biobasés : Amidon, PLA, PHA, PE et PET
Xu, Gang, Wang, Aiqin, Pang, Jifeng, Zhao, Xiaochen, Xu, Jinming, Lei, Nian, et al. (2017). Chemocatalytic conversion of cellulosic biomass to methyl glycolate, ethylene glycol, and ethanol. ChemSusChem 10 (7), 1390–1394. doi:10.1002/cssc.201601714
Zheng, Mingyuan, Pang, Jifeng, Wang, Aiqin, and Zhang, Tao (2014). One-pot catalytic conversion of cellulose to ethylene glycol and other chemicals: From fundamental discovery to potential commercialization. Chin. J. Catal. 35 (5), 602–613. doi:10.1016/S1872-2067(14)60013-9
Keywords: PET, bio-based, alternative building blocks, biorefinery, terephtalic acid, socio-economic
Citation: Sandei B, Massardier V and Brunel R (2022) Alternative building blocks sources for poly (ethylene terephthalate): A short review with socio-economical points of view. Front. Mater. 9:1005770. doi: 10.3389/fmats.2022.1005770
Received: 28 July 2022; Accepted: 03 November 2022;
Published: 21 November 2022.
Edited by:
Pratheep K Annamalai, The University of Queensland, AustraliaReviewed by:
Peter Halley, The University of Queensland, AustraliaAntonio Buonerba, University of Salerno, Italy
Copyright © 2022 Sandei, Massardier and Brunel. This is an open-access article distributed under the terms of the Creative Commons Attribution License (CC BY). The use, distribution or reproduction in other forums is permitted, provided the original author(s) and the copyright owner(s) are credited and that the original publication in this journal is cited, in accordance with accepted academic practice. No use, distribution or reproduction is permitted which does not comply with these terms.
*Correspondence: Valérie Massardier, dmFsZXJpZS5tYXNzYXJkaWVyLW5hZ2VvdHRlQGluc2EtbHlvbi5mcg==