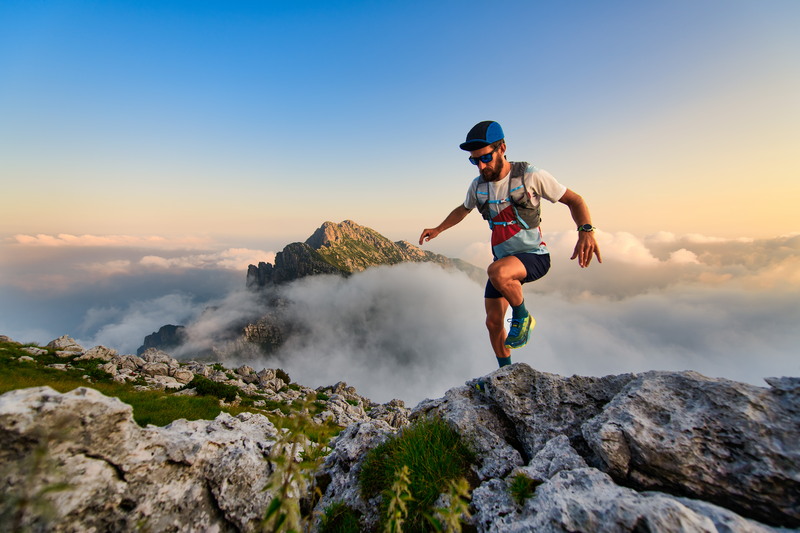
95% of researchers rate our articles as excellent or good
Learn more about the work of our research integrity team to safeguard the quality of each article we publish.
Find out more
ORIGINAL RESEARCH article
Front. Mater. , 28 January 2022
Sec. Polymeric and Composite Materials
Volume 8 - 2021 | https://doi.org/10.3389/fmats.2021.807004
This article is part of the Research Topic Advanced Green Thermosetting Composites: Design and Performances View all 6 articles
The use of natural fibre-reinforced plastics for higher-stressed applications is currently often limited by the high price of high-quality semi-finished products. Therefore, the present study deals with developing yarns from cost-effective hemp from a disordered separation process (total fibre line) for composite reinforcements. Composites were fabricated using a miniature pultrusion process with thermosetting matrices from the yarns. The results show that around 90% of the flexural strength and flexural modulus of identically produced flax composites could be achieved with maximum values of 282 MPa for the flexural strength and 23.4 GPa for the flexural modulus. The yarns were additionally used to manufacture quasi-unidirectional fabrics to produce composite laminates using different manufacturing processes. The highest values were obtained for a laminate with 39 vol% fibre content, produced with a resin injection process in an autoclave, achieving a tensile strength of 155 MPa, Young’s modulus of 19.4 GPa, a flexural strength of 174 MPa and bending modulus of 12.4 GPa. The characteristic values are sufficient to use the materials in applications with higher mechanical requirements.
Due to increasing environmental awareness and finite fossil resources, more and more materials based on renewable raw materials are being used in the composites sector (Liu et al., 2017a; Tanasă et al., 2020). The use of hemp fibres in various applications is mainly due to their biological origin, which is associated with carbon sequestration during growth (Ingrao et al., 2015). In general, natural fibres display benefits for the environment like biodegradability, renewability of raw material, and reduction in emission of greenhouse gasses (Thyavihalli Girijappa et al., 2019). Bast fibres like hemp display comparatively high strength and stiffness compared to many other vegetable fibres (Bourmaud et al., 2018; Müssig, 2010). There has been increasing attention on using bast fibres for higher loaded applications in recent years. In particular, flax fibres and flax fibre-reinforced plastics were examined in depth (Yan et al., 2014; Bourmaud et al., 2018; Ramesh, 2019; Baley et al., 2020). Compared to flax, hemp fibres are often more challenging to process. An overview of steps to be taken for using hemp in high-performance composites is given by Müssig et al. (2020a).
For use in technical applications, many factors can influence the properties of the hemp fibres and composites like the cultivation, harvesting, retting and processing (Liu et al., 2017b; Musio et al., 2018; Müssig et al., 2020a; Müssig et al., 2020b; Bourmaud et al., 2020; Hao et al., 2020; Réquilé et al., 2021). As with all natural fibres, a major disadvantage of hemp fibres is the fact that the properties can vary considerably due to the different cultivation and processing conditions (Müssig and Martens, 2003; Shahzad, 2012). To achieve a good reinforcing effect in a composite, hemp fibres usually require modifications to improve their characteristic values and interfacial bonding with polymer matrices and reduce their hydrophilic character (Mittal et al., 2016; Liu et al., 2017a). Tanasă et al. (2020) grouped these modification methods into three major categories: chemical, physical and biological. Chemical reagents like alkali (Islam et al., 2011; Dayo et al., 2018; Sepe et al., 2018), silane (Dayo et al., 2018; Sepe et al., 2018) or cyclohexane/ethanol (Dayo et al., 2018) may reduce the hydrophilic character of the fibres and thus improve compatibility with the hydrophobic matrix. They often expose more reactive groups on the fibre surface to improve the fibre/matrix adhesion. With physical methods, structure and surface properties can be changed without extensively changing the chemical composition of the fibres. With biological agents and processes like fungi (Li et al., 2009), enzymes (Fischer et al., 2006; Liu et al., 2016a; Liu et al., 2017c), bacteria (Tamburini et al., 2004) and lignin (Wood et al., 2011), the fibre surface properties can also be adapted (Tanasă et al., 2020). The improved interfacial adhesion between hydrophilic fibres and hydrophobic polymers reduced moisture uptake, which may lead to higher strength and stiffness (Réquilé et al., 2019), increased microbial degradation resistance, higher thermal stability and prolonged durability of composites can be achieved (Shahzad, 2012; Mittal et al., 2016; Liu et al., 2017a). In addition to fibre/matrix adhesion, other factors like fibre content (Sebe et al., 2000), fibre geometry and fibre size (Müssig and Amaducci, 2018) influence the mechanical and thermal behaviour, the tendency to absorb water and swell (Perrier et al., 2017) have been presented for hemp fibre-reinforced composites (HFC). Besides the fibre characteristics and processing methods, the properties of the composites can be significantly influenced by the reinforcement structure, as shown by several studies for flax fibre-reinforced composites (Goutianos et al., 2006; Liu and Hughes, 2008; Baets et al., 2014; Poilâne et al., 2014; Shah et al., 2014; Santamala et al., 2016; Scida et al., 2017) and HFC (Madsen et al., 2007; Santulli and Caruso, 2009; Abbas et al., 2020; Corbin et al., 2020a; Müssig et al., 2020a; Corbin et al., 2020b). Corbin et al. (2020a) pointed out that recent developments in the field of natural fibre-reinforced composites for higher stressed applications mainly focus on using unidirectional reinforcements. Usually, composites reinforced with yarns perform better than composites prepared from fleece or needle felt with random fibre orientation (Zhang and Miao, 2010). Due to the finite length of plant fibres and the high number of selectable process parameters, the production of yarns, rovings and fabrics is complex. Some studies focus on developing novel reinforcement structures (semi-finished products) in the hemp sector. For example, Boccarusso et al. (2018) developed grid-like fabrics. The results of the study show interesting mechanical properties, highlighting their possible use as a core for sandwich composite structures. Borrello et al. (2020) used a braiding technique to produce different structures and found a strong dependency of the topology of textile reinforcements by the braiding manufacturing parameters. Corbin et al. (2020b) developed a quasi-unidirectional woven hemp fabric designed to combine the advantages of easy handling, impregnability by the matrix and fibre alignment. Therefore, low twisted rovings with a high density in the main direction were used whereby the crimp was kept minimal.
Compared with glass fibres, the density of hemp fibres is clearly lower, which may also lead to a lower density of the composite. However, the processing procedure must also be taken into account. The maximum fibre volume fraction of hemp fibres to be achieved in a composite is often lower than that of glass due to the irregular shape and the associated irregular fibre packing. Therefore, the thickness of the components may be higher and the mass of HFC similar (Scarponi and Messano, 2015) or even higher than that of glass fibre-reinforced (GFC) composites (Maino et al., 2019). However, with lower and comparable fibre volume fractions, the HFCs have clear advantages in terms of lightweight construction potential compared to GFC, which also positively influences the results of life cycle analyses (LCA) (Müssig and Albrecht, 2018).
A major disadvantage of bast fibre-reinforced plastics, and HFCs in particular, is a relatively low toughness which is significantly lower compared with GFC (Shahzad, 2011; Patel et al., 2015), often limiting their use to applications that do not have to withstand high impact loads. For example, Shahzad (2012) gives a value of 4.8 kJ/m2 for hemp/UP and 80.4 kJ/m2 for glass/UP reinforced with a fibre volume fraction of 20%. The failure of hemp and GFC composites differs significantly (Bonnafous et al., 2011; Maino et al., 2019), and the fibre orientation, as well as the semi-finished product, have a significant influence on the toughness (Santulli and Caruso, 2009). At the same time, HFC display better (acoustic) damping characteristics than GFC (Buksnowitz et al., 2010).
Hybrid materials are now being used with increasing frequency for highly stressed composite materials to minimise the disadvantages of HFC and GFC. Above all, the toughness of HFC and the damping behaviour of GFC can be significantly improved by hybridisation. An overview of the hybridisation of GFC and bast/glass hybrid composites is given in the review articles by Singh et al. (2017) and Kumar et al. (2017). Thermosetting hemp/glass hybrid materials have also been investigated in some studies (Cicala et al., 2009; Scutaru et al., 2014; Somashekar et al., 2016; Sanjay et al., 2016; Sanjay and Yogesha, 2017; Patel et al., 2018; Bhoopathi et al., 2018; S. Sharavanan et al. et al., 2018; Murugu Nachippan et al., 2020; Boria et al., 2020; Murugan et al., 2021). Generally, hybridisation with glass fibres improves the properties of the composites, like mechanical characteristics and water absorption capacity, compared to pure HFC (Sanjay et al., 2016). However, it should be noted that the properties of the hybrid materials significantly depend on the layer arrangement (Murugu Nachippan et al., 2020; S. Sharavanan et al. et al., 2018). Hybrid composites exhibit damage patterns that are mostly dominated by the higher fibre volume fraction of glass fibres and their location in the outermost layers (Boria et al., 2020). For applications that have to withstand dynamic loads, the determination of the fatigue behaviour of composites is also of particular interest (Yuanjian and Isaac, 2007; de Vasconcellos et al., 2014a; de Vasconcellos et al., 2014b; Fotouh et al., 2014; Shahzad and Isaac, 2014; Barbière et al., 2018; Barbière et al., 2020). Compared to GFC, HFC shows lower fatigue sensitivity and lower stiffness degradation at the same normalised peak stress levels and better resistance to crack formation (Yuanjian and Isaac, 2007; Shahzad and Isaac, 2014). LCA has shown for hybrid materials, that the use of hemp can lead to considerable ecological advantages by the reduction of glass fibres and resin content compared to standard GFC. An environmental advantage was found during the production phase, and it is mainly attributed to the biological and sustainable origin of hemp (La Rosa et al., 2013).
Manaia et al. (2019) pointed out that advanced research and progress led to increasing mechanical performance of HFC. Nonetheless, more research is needed to improve their properties and to expand their range of applications. In the same vein, Müssig et al. (2020a) stated that hemp will be found in high-performance composites in the short-to-medium term. However, there is a need for performance optimisation especially through the selection of crop variety, best practices in retting, and adequate fibre extraction methods to obtain more consistent fibre qualities suitable for the production of semi-finished products for high-performance composite applications (Müssig et al., 2020a). A study by Madsen et al. (2007) showed that hemp yarns produced in two different years did not show significant differences in linear density and fibre size distribution from a textile point of view. Nevertheless, the yarns resulted in different composite properties, which should be eliminated in future research.
One of the biggest problems with the industrial use of bast fibres for high-value applications is the high price of semi-finished products. Currently, long flax is used for highly stressed natural fibre-reinforced components, which is cost-intensive due to the complex and intense harvesting and processing technology. The semi-finished product costs can be almost at the level of carbon fibre semi-finished products (Deimann, 2020). In a previous study, we have already shown that comparable composite properties can be achieved with less expensive flax staple fibres from tow by producing an alternative staple fibre yarn (Graupner et al., 2021). It is well known that the twist of ring-spun yarns prevents the full utilisation of the fibre reinforcement potential in a composite (Zhang and Miao, 2010). The higher the yarn twist, the lower the mechanical composite properties (Goutianos et al., 2006; Baets et al., 2014; Scida et al., 2017). Therefore, the staple fibre yarn had an almost unidirectional fibre orientation. The yarn costs are significantly lower than the prices of low-twist yarns or rovings available on the market while achieving a comparable reinforcing effect. It was also possible to produce a demonstrator component (leaf spring / axle tie for a bogie of a narrow-gauge railway) from flax and a hybrid material from flax and glass. The hybrid material displayed significantly higher tensile, bending and impact properties than the pure flax fibre-reinforced plastic. At the same time, the flax layer is protected against moisture and environmental influences by the outer glass layers (Graupner et al., 2021). This process developed for flax was recently transferred to hemp. Like flax fibres, hemp fibres from the disordered fibre line (total fibre line with no preferred fibre orientation (Müssig et al., 2020a)) are of bio-based origin and thus offer considerable advantages in terms of environmental friendliness compared to synthetically produced fibres. Hemp may provide comparable mechanical properties to flax, but compared to the previously used flax tow, it is even cheaper at ∼1.0 €/kg compared to ∼1.4 €/kg for flax. If similarly good mechanical properties can be achieved in a composite, this aspect represents a considerable economic motivation for the industry to use hemp as a reinforcing fibre in its products.
The raw hemp is processed into slivers, yarns, fabrics, and composites in the study presented here. The reinforcing effect of the developed yarns is verified with the testing of unidirectional composites and compared with the results of the previously developed flax yarn. Laminates of hemp fabrics and hybrids of hemp and glass fabrics were produced with project partners from the industry by vacuum infusion, resin-transfer-moulding (RTM) and a resin injection process in an autoclave. The aim was to achieve 80% of the mechanical characteristic values obtained with the previously developed flax composites.
Hemp fibre bundles were used for the development of staple fibre yarns. Hemp was cultivated in France (Planéte Chanvre, Aulnoy, FR) with a sowing density of 45 kg per hectare to obtain thin stems and a high fibre yield (6–7 t straw, 25–30% fibre bundles) and was harvested, field retted and pressed at seed maturity. The variety used was USO 31, a co-utilisation variety used for needle felts and fleeces. The seeds can also be used, and thus a favourable market price is possible.
The developed flax staple fibre yarn presented in (Graupner et al., 2021) and a glass fibre roving (type EC16 200 TD22C with zero-twist and a fineness of 200 tex; Saint-Gobain Vetrotex, Aachen, DE) were used as reference samples for reasons of comparison.
Composites were produced from two different matrices: 1) an epoxy resin (type Epikote RIMR 135 with hardener Epikure RIMH 137, Momentive Specialty Chemicals B.V., Rotterdam, Netherlands; mixing ratio 100:30; density 1.15 g/cm³) and 2) a bio-based epoxy resin PTP-L® (Polymer material made of Triglycerides and Polycarbon acid anhydrides; density 1.1 g/cm³) produced by company Biocomposites And More (B.A.M., Ipsheim, DE).1
Raw hemp was further processed by SachsenLeinen (Markkleeberg, DE). The fibre bundles were stretched (Schlumberger GN 5, FR) with a processing speed of 30 m/min on a carding machine (Russian design, UDSSR) into card slivers. The tape-laying process was used with the aid of work cards and needle tape draw frames. An 11 ktex sliver was processed into a twisted yarn with a fineness of 525 tex and was provided by SachsenLeinen.
Two staple fibre yarns without twist were produced with 30 m/min from a 5 ktex sliver with a fineness of approx. 300 tex. Fibres in yarns are held together with a polyamide polyfil (78 dtex, 20 single endless fibres) that is spun helically around the fibre yarn (Santamala et al., 2016).
For the production of rotor yarns, a modified open-end (OE) rotor spinning process was used. The rotor spinning tester was assembled at ITA (Institut für Textiltechnik of RWTH Aachen University, DE) of various components. The basic construction of the spinning tester is a custom-made product from Schlafhorst (Mönchengladbach, DE). The construction is characterised above all by the rotor housing for the use of rotors with large diameters. Therefore, fibres with lengths of up to about 120 mm can be processed. As a result of excessive dust deposits in the rotor and the high fibre shortening, the process stability in rotor spinning is unacceptably low. To overcome this problem and to stabilise the rotor spinning process when processing hemp, further machine adaptation was necessary and had to be developed. A suction system to discharge fibre dust from the opening roller led to a significant improvement in the spinning stability. By reducing the deposition of fibre trash in the rotor of the OE rotor spinner, it was possible to produce OE rotor yarns from hemp successfully. Spinning was possible with the small rotor (diameter 100 mm) and the large rotor (diameter 200 mm). The machine settings had to be adapted to the rotor used. Spinning was carried out with an external false-twist unit to reduce the yarn twist. The false twist unit was mounted between the draw-off nozzle and the pair of draw-off rollers. The yarn was given a temporary twist (false twist) by using the device. The temporary twist increased the yarn strength and thus bridged the critical area of the spinning process between the rotor groove and the navel. The temporary yarn twist is no longer present in the spinning direction downstream of the false twist device; consequently, the yarn produced showed reduced twist (Lehmann et al., 2020). The yarn produced shows a fineness between 550 and 600 tex. The processing parameters are summarised as follows:
• Rotor yarn V1: 344 twists/m, 6,000 rpm rotor speed, 100 mm rotor diameter, 24 m/min delivering speed, use of false-twist unit.
• Rotor yarn V2: 408 twists/m, 7,000 rpm rotor speed, 100 mm rotor diameter, 17 m/min delivering speed, no use of false-twist unit.
• Rotor yarn V3: 312 twists/m, 5,000 rpm rotor speed, 200 mm rotor diameter, 19 m/min delivering speed, no use of false-twist unit.
• Rotor yarn V4: 262 twists/m, 5,000 rpm rotor speed, 200 mm rotor diameter, 19 m/min delivering speed, no use of false-twist unit.
The twist angles of the yarn provided by SachsenLeinen and the rotor yarns were determined on 6 yarn sections each. The yarn sections were scanned with an Epson Perfection V800 photo scanner (Suwa, Nagano, Japan) with 600 dpi in reflected light mode and measured at 10 points each with ImageJ version 1.52i (Wayne Rasband, National Institutes of Health, USA), resulting in 60 measured values per yarn type.
Fabrics (quasi-UD) were produced from the staple fibre yarns and the glass roving on an industrial scale by Wenzel & Hoos in the weft with a warp system of polyester (Nm 50/2; Polyester Staple Fiber (SD OB) with a density of 1.39 g/cm³; Chung-Shing Textile Co., LTD. Yang-Mei Chemical Fiber Factory, Taipei, TW). A rapier weaving machine type HTV S (Lindauer Dornier GmbH, Lindau, DE) was used with a width of 180 cm. The weaving machine is equipped with an electronic dobby, electronic warp drain and electronic take-up motion. A weaving speed of 200 1/min and a weft insertion rate of 236 m/min with a weft density of 12 threads per centimetre was used. To determine the warp thread content of the fabrics, 15 × 15 cm2 of each fabric was cut to size and was sorted into warp and weft threads. The composition and the mass per unit area of the fabrics in the dried state (drying for 18 h at 60°C in an oven, type UN 450, Memmert GmbH & Co. KG, Schwabach, DE) is listed as follows:
• Flax fabric (Aδ3): 287.5 g/m2, 83.9% flax weft threads, 16.1% polyester (PES) warp threads.
• Glass fabric (Rδ1): 296.6 g/m2, 83.6% flax weft threads, 16.4% polyester (PES) warp threads.
• Hemp fabric (Eδ1): 288.3 g/m2, 84.0% flax weft threads, 16.0% polyester (PES) warp threads.
Fibre bundles from all process stages were examined after conditioning in a standard climate according to DIN EN ISO 139 (Deutsches Institut für Normung, 2005) to investigate the influence of processing on fibre characteristics.
The fibre bundle length distributions of hemp from different processing steps were evaluated visually by manual length stacking. The fibre bundles were conditioned for at least 18 h at 20°C and 65% relative humidity in a climate chamber (type VCL 4003; Vötsch Industrietechnik GmbH, Reiskirchen-Lindenstruth, DE) and were weighed at 0.6 g with a scale (type Kern ABT 120-5 DM; d = 0.00001 g; Kern und Sohn GmbH, Balingen, DE). Individual fibre bundles were arranged end to end and fixed to copying film with double-sided adhesive tape. Prepared fibre bundles were scanned with an incident light scanner (Epson Perfection Photo V800, Epson, Meerbusch, DE) at 600 dpi with a black background.
The fineness, measured as object width, was examined with the Fibreshape measuring system (X-Shape Version 6.1.4, IST AG, Vilters, CH). The fibre bundles were prepared on an Epson Perfection Photo V800 flatbed scanner and scanned with a resolution of 2,400 dpi in transmitted light mode. For the raw hemp, 4,906 object sections were measured. The fibre bundles prepared from the sliver, the rotor yarn V1, rotor yarn V2, the staple fibre yarn V2 and the fabric, 30,141, 4,013, 4,317, 23,414, and 4,653 object sections were analysed, respectively. The flax fibre bundles from the staple fibre yarn were also measured (n = 42,182).
Single fibre bundles were analysed regarding their tensile characteristics with a Fafegraph M testing machine (Textechno, Mönchengladbach, Germany) working with a pneumatic clamping system (PVC clamps) and a 10 N load cell with a test speed of 10 mm/min at a gauge length of 20 mm. Per test series 80 single fibre bundles were investigated.
For composite production, four different production procedures were used: 1) pultrusion, 2) vacuum infusion, 3) resin injection in an autoclave (autoclave injection), and 4) resin transfer moulding (RTM). The pultrusion process was used to produce UD-reinforced test specimens to investigate the reinforcement potential of the staple fibre yarns, while autoclave injection, vacuum infusion and RTM were applied to investigate the industrial processing of the fabrics.
Unidirectional composites were produced by miniature pultrusion from yarns and epoxy resin in round and rectangular rods with a length of 50 cm. The process is described in detail in (Graupner et al., 2020). The round rods with a fibre volume fraction of approx. 40% had a diameter ranging between 5.5 and 5.8 mm. The rectangular samples were produced with a fibre volume fraction of around 30%, a width of 10 mm and a thickness of 4.5–4.7 mm. After hardening for at least 48 h, the samples were post-cured at 60°C for 18 h in an oven (type UN 450, Memmert GmbH & Co.KG, Schwabach, DE). Afterwards, the rods were demoulded and cut to the required length for impact and bending tests.
Composite laminates were produced by a vacuum injection method in an autoclave with the PTP-L matrix and a vacuum infusion process with epoxy resin from the quasi-UD fabrics as described in (Graupner et al., 2021). In addition, the fabrics were processed into laminates with the PTP-L matrix using a resin transfer moulding (RTM) process. For this purpose, the fabrics were placed in a heated, multi-part steel mould. The mould was closed, and the fabrics were dried in the mould. The matrix was then injected with the injection equipment. The mould was heated to curing temperature and held for a while. Afterwards, the mould was cooled down, opened, and the plate was removed.
Composite plates from vacuum infusion, autoclave injection and RTM resulted in a thickness of approx. 2 mm and were cut by water jet cutting to the appropriate dimensions for further tensile, bending, impact and interlaminar shear strength (ILSS) tests. Produced types of composites are listed below:
‐ Pultruded yarns and rovings:
• Twist yarn, 525 tex
• Rotor yarn V1, 588 tex
• Rotor yarn V2, 550 tex
• Rotor yarn V3, 604 tex
• Rotor yarn V4, 581 tex
• Staple fibre yarn V1, 294 tex
• Staple fibre yarn V2, 285 tex
• Flax yarn V9, 200 tex
‐ Processed fabrics:
• Fabric from staple fibre yarn V2, processed by vacuum infusion (4 layers), autoclave injection (4 layers) and RTM (4 layers)
• Flax fabric from flax yarn V9, processed by vacuum infusion (4 layers) and autoclave injection (5 layers)
• Glass fabric, processed by vacuum infusion (6 layers), autoclave injection (9 layers) and RTM (9 layers)
• Hybrid—glass and hemp fabric, processed by vacuum infusion, autoclave injection and RTM (1 layer glass, 3 layers hemp, 1 layer glass)
Before composite testing, test specimens were conditioned according to DIN EN ISO 291 (Deutsches Institut für Normung, 2006).
Bending tests on 7 pultruded round rods with a length of 120 mm were carried out at a span length of 96 mm according to DIN EN ISO 14125 (Deutsches Institut für Normung, 2003a) with a waisted load applicator (radius of waist: 6 mm) according to ISO 3597-2 (International Organization for Standardization, 2003) with a pre-load of 10 N and a testing speed of 5 mm/min. Tests were operated on a Zwick/Roell Z020 universal testing machine (Zwick GmbH and Co., Ulm, DE) equipped with a 20 kN load cell. 6 to 7 specimens of the pultruded rectangular specimens with a length of 100 mm were analysed according to DIN EN ISO 14125 (Deutsches Institut für Normung, 2003a) at a span length of 74 mm. The test speed was set to 1 mm/min to determine the bending modulus, then accelerated to 5 mm/min. The bending tests of the composite laminates were carried out for 8 specimens, each with the dimensions of 100 × 15 mm2 according to the DIN EN ISO 14125 standard (Deutsches Institut für Normung, 2003a) with the Zwick/Roell Z020 universal testing machine. A span length of 45 mm and a test speed of 1 mm/min were chosen. The flexural modulus of all bending tests was determined between 0.05 and 0.25% flexural strain via linear regression. The strain was calculated from the traverse path of the testing machine.
Impact characteristics were analysed with Charpy impact pendulum devices type 5102 and 5101 (Zwick GmbH, Ulm, DE) according to DIN EN ISO 179-1 (Deutsches Institut für Normung, 2010) operating with pendulum sizes of 0.5–4.0 J (type 5102) or 7–50 J (type 5102). Seven specimens of the pultruded rods were tested for each test series. The span distance was set to 40 mm for the round rods and 62.5 mm for the rectangular rods. 8 specimens per test series of composite laminates were tested at a span length of 40 mm.
The interlaminar shear strength (ILSS) of 8 test specimens with the dimensions of 20 × 10 mm2 of the composite laminates was determined according to the standard 14130 (Deutsches Institut für Normung, 2003b) using the Zwick/Roell Z020 testing machine at a test speed of 1 mm/min. The span length was set individually for each test series and resulted from 5 times the sample thickness.
Tensile tests of hemp and glass/hemp hybrid composite laminates of 8 specimens per test series with a width of 25 mm and a length of 250 mm were carried out according to DIN EN ISO 527-2 (Deutsches Institut für Normung, 1996) with the Zwick/Roell universal testing machine equipped with a 20 kN load cell and a test speed of 2 mm/min until breakage. The elongation was recorded with a video extensometer (VideoXtens, Zwick/Roell GmbH, Ulm, DE) between 0.05 and 0.25% strain after reaching a pre-load of 20 N. The Young’s moduli of the GFC composite laminates were also determined with the Zwick/Roell universal testing machine. As the load cell capacity was too low to measure the breaking force of the glass fibre composites, the samples were run to break on a Galdabini Quasar 250 universal testing machine (Galdabini (S.P.A.), Cardano Al Campo VA, IT, load cell 250 kN) until they broke.
The density of the specimens was determined gravimetrically and via the measured volume of the bending samples.
Figure 1A shows that the raw hemp consists of coarse fibre bundles with lengths partly higher than 25 cm. The production of the slivers resulted in significant refinement of the fibre bundles and a related shortening. The spinning process led to a further slight shortening, whereas further processing into fabric did not result in any further change of length. The fibre bundle lengths in the fabric were many times higher than the critical fibre length required for the reinforcement effect in a composite material. The critical fibre length of bast fibres in an epoxy resin is given between 0.2 mm (ramie) (Adusumalli et al., 2010) and 0.6 mm (jute) (Tripathy et al., 2000), whereby it should be noted that the fibre/fibre bundle fineness influences the critical fibre length.
FIGURE 1. (A) Staple length of hemp fibre bundles prepared from raw fibres, staple fibre yarn and fabric and (B) Staple length of hemp fibre bundles from different yarns compared to flax fibre bundles from a staple fibre yarn (last picture on the right); the scale is given in cm.
A visual comparison of the fibre bundle lengths from the different yarns is shown in Figure 1B. The fibre bundle lengths in the rotor yarns are significantly shorter compared with the twist and staple fibre yarns. Nevertheless, the length values are clearly higher than the critical fibre length required to reinforce a thermosetting composite. However, the rotor spinning process leads to a higher fibre bundle shortening than the production process for staple fibre yarns. The fibre bundle lengths from the twist yarn and the hemp staple fibre yarn are slightly higher than the lengths from the flax staple fibre yarn (Figure 1B, last picture on the right side). It follows that hemp could be processed with similar care as flax.
For comparison, the fineness was measured for hemp from the different process steps and the flax staple fibre yarn. The results are shown in Figure 2 as Box-Whisker plots. Due to the large and uneven number of samples, no statistical evaluation could be done. Hence, only the fibre width distributions with the median values are shown. Raw hemp shows the highest median value of 40.2 µm. Nevertheless, the median value does not differ clearly from the median width of the fibre bundles from sliver, yarns and fabric. This means, despite the appearance of the coarse fibre bundles in the fibre length stack (Figure 1B), a large number of very fine fibre bundles or single cells that are spliced off the bundle are present in the sample. It is visible that a larger number of very coarse bundles are contained in the sample compared to the fibres from the further process steps (see Figure 2). The fibre width distribution is shifted due to the sliver production compared to the raw fibres. Coarser fibre bundles are split and refined by the processing. Only a slight further refinement of the fibre bundles was observed due to the yarn production. The rotor yarns tend to have even less coarse bundles than the staple fibre yarns, which the different spinning processes can explain. The fibre bundles from the rotor yarns showed a significantly higher shortening, which can also be explained by improved fibre bundle separation. Compared to the fibre bundles from the flax staple fibre yarn with a median value of 24.0 µm, the fibre bundles in the hemp staple fibre yarn are significantly coarser with a median width of 36.3 µm.
FIGURE 2. Fibre width shown as Box-Whisker plots of fibre bundles prepared from raw hemp, the sliver, the rotor yarn, the staple fibre yarn, the fabric and the flax staple fibre yarn.
The tensile properties of the hemp fibre bundles extracted from the different process steps are shown as Box-Whisker plots in Figure 3. As not all results follow a normal distribution, a multiple Wilcoxon test with an error probability (α) of 5% was used for statistical analysis. From a statistical point of view, the tensile strength results (Figure 3A) show that the fibre bundles were not significantly damaged by the preparation into the sliver. The twist yarn and the rotor yarns have comparable tensile strength, although the fibre tensile strength of the rotor yarns tended to decrease slightly from rotor yarn V1 to V4. The fibre bundles prepared from the staple fibre yarns and the fabric have slightly higher strength than the fibre bundles from the rotor yarns, suggesting that the production of the staple fibre yarns is more gentle than processing the fibre bundles in the rotor spinning process. Compared to the flax staple fibre yarn, the strength of the fibre bundles from the hemp staple fibre yarns is slightly lower but not significantly different from a statistical point of view. A slightly different trend appears for Young´s modulus (Figure 3B). It can be seen that Young´s modulus of all hemp fibre bundles tested is significantly lower compared to flax. However, as described for the tensile strength, no significant damage to the fibre bundles due to the production of the sliver could be proven. Fibre bundles from the twist yarn, the staple fibre yarns and the woven fabric showed comparable tensile moduli. The fibre bundles from the rotor yarns showed a trend towards slightly lower Young´s moduli. The significantly lower Young´s modulus compared to the flax fibre bundles could be related to the size of the fibre bundles. Compared to flax, the prepared hemp fibre bundles were coarser. Due to the presence of a larger number of single cells in the bundle, the compliance within the fibre bundle could be greater, explaining a lower Young´s modulus. The literature often reports lower Young´s moduli of hemp fibre bundles compared to flax (Müssig et al., 2010).
FIGURE 3. Box-Whisker plots of the tensile strength (A) and Young´s modulus (B) of hemp fibre bundles prepared from different processing stages compared to flax with mean value as rhombus (results which do not follow a normal distribution are marked with *, significant differences are indicated with different letters).
The reinforcing effect of the yarns produced was verified on unidirectional pultruded round and rectangular rods. A fibre volume fraction of 40% was targeted for the round rods and 30% for the rectangular rods. Fibre volume fractions and porosity were calculated based on the mass and density of fibres, matrix and composites. Table 1 shows that the targeted volume fractions were met with a maximum deviation of 4.3% for the round rods and 2.2% for the rectangular rods. It becomes apparent that the porosity of the round rods is significantly lower than that of the rectangular rods. It is assumed that this effect is caused by the lower volume fraction of the rectangular rods, as pores can accumulate due to a looser fibre packing.
TABLE 1. Mean fibre volume fraction (standard deviation in brackets) and porosity of pultruded round and rectangular rods.
The pultruded samples were analysed by impact and bending tests. The results of the unnotched Charpy impact strength values are shown in Figure 4. The data of the samples from the twist yarns supplied by SachsenLeinen, the rotor yarns and the unidirectional staple fibre yarns from hemp are compared with the results of the composites produced from flax staple fibre yarns. The results of the round and rectangular rods show the same trend. Due to the lower fibre content, the values of the rectangular rods are slightly lower than those of the round rods. None of the hemp yarns could achieve the impact strength of the flax-reinforced sample. The twist yarn achieved 51 and 59% of the impact strength of flax in the round and rectangular samples, respectively. The rotor yarn achieved 43 and 46% of the impact strength of flax with the round and rectangular samples, respectively. The staple fibre yarn V2 showed the highest values with the hemp samples, achieving 56 and 63% of the impact strength of the round and rectangular flax samples.
FIGURE 4. Unnotched Charpy impact strength (mean value ± standard deviation) of pultruded round rods with a fibre volume fraction of 40% (A) and rectangular rods with a fibre volume fraction of 30% (B).
The fibre orientation plays an essential role in the mechanical characteristics of fibre-reinforced composites (Cordin et al., 2018). This statement does not contradict the results. The twist angles of the twisted hemp yarn and the rotor yarns were measured (compare Table 2) to evaluate the results. The twist yarn showed a significantly lower twist angle than the rotor yarns. This is assumed the main reason for the different impact values. Although the fibres are more clearly shortened by rotor spinning (see Figure 1B), they still have significantly higher lengths than the critical fibre length of hemp in an epoxy matrix, and the tensile strength of the fibre bundles does not differ significantly from the results of the staple fibre yarns (Figure 3A). The twist yarn shows comparable fibre lengths to the staple fibre yarns, which lead to the highest impact values in the hemp composites due to their almost unidirectional orientation. However, even the best hemp yarn displays significantly lower impact strength values compared with the flax composite.
TABLE 2. Mean twist angles (standard deviation in brackets) of hemp twist yarns and hemp rotor yarns.
The fracture behaviour of the hemp composites reinforced with different yarns and the flax-reinforced composite is shown in Figure 5. While the composites from the rotor yarn V2 only show complete fractures, the flax composites as well as the samples from the twist yarn and the staple fibre yarn, display only hinge fractures. Compared to the flax samples, the remaining sample thickness of the composites reinforced with hemp yarn where the test specimens are still attached is significantly thinner. The rotor yarns with higher impact strength show complete and hinge breaks. I.e. the toughness can also be partially assessed by the fracture appearance: the most brittle samples showed only complete fractures, the slightly less brittle ones a mixture of complete and hinge fractures and those with the twist yarn and the staple fibre yarn only hinge fractures, whereby the fracture halves can be easily pulled apart. In contrast, the flax samples hold together more strongly. The higher impact strength of flax fibre-reinforced composites compared to hemp fibre-reinforced composites is also described by other authors (Müller and Krobjilowski, 2004; Awais et al., 2020). It can be stated that the aim of achieving 80% of the impact strength of flax fibre-reinforced composites could not be achieved with the developed hemp yarns.
The bending properties were investigated on round and rectangular rods and are summarised in Figure 6. As described for the impact strength, similar trends are obtained for the different test specimen geometries. However, due to the lower fibre volume fraction of 30% compared to 40% of the round rods, the characteristic values of rectangular rods are lower (Figures 6A,C). However, compared to the impact strength, the reinforcement effect of the hemp yarns is considerably better. The flax-reinforced composite also provides the highest characteristic values with 290 MPa for the round rods and 210 MPa for the rectangular rods. However, the hemp staple fibre yarn V2 also provides good characteristic values, with 282 MPa for the round rods and 186 MPa for the rectangular rods, which corresponds to 97 and 89% of the bending strength of the flax samples, respectively. The twist yarn with a twist angle of 25° resulted in 84 and 83% of the flax round and rectangular rods, respectively. The rotor yarns V1 and V2 showed the lowest bending strength overall. As described for the impact strength, this effect may be attributed to the high twist angle of approx. 40°. It can be seen that a lower twist angle of the rotor yarns V3 and V4 leads to slightly higher characteristic values.
FIGURE 6. Flexural strength and flexural modulus (mean value ± standard deviation) of pultruded round rods with a fibre volume fraction of 40% (A,B) and rectangular rods with a fibre volume fraction of 30% (C,D).
The trend described for the flexural strength was also found for the flexural modulus (Figures 6B,D). Likewise, the flax fibre-reinforced composite shows the highest values with 23.5 GPa for the round rods and 14.4 GPa for the rectangular rods. However, the composites with the hemp staple fibre yarns come very close, reaching values of 23.4 GPa for the staple fibre yarn V2 and 12.9 GPa for the rectangular rods, which corresponds to 99.6 and 89.4% of the properties of the flax composite. The twist yarn achieved 71 and 76% of the bending modulus of the flax composite. The bending moduli of the composites reinforced with the rotor yarns were significantly lower, with a trend towards slightly higher characteristic values when using the yarns with the lower twist angle (rotor yarns V3 and V4).
In summary, the best reinforcement effect for the staple fibre yarn V2 with bending strengths of 282 and 186 MPa and bending moduli of 23.4 and 12.9 GPa was achieved for the round rods with 40% fibre volume content and the rectangular rods with 30% fibre volume content, respectively. The hemp staple fibre yarns exceeded the goal of achieving a reinforcement effect of at least 80% of the flax yarns in terms of bending properties. To classify the determined properties with published data of unidirectionally reinforced hemp fibre-reinforced epoxy composites, we refer to the work of Liu et al. (2016a) and Liu et al. (2016b), for example. The authors produced composites from bast fibre strips with a volume fraction of 50% in the compression moulding process and achieved a flexural strength of 65 MPa. Robillard et al. (2010) and Santulli and Caruso (2009) processed hemp fibre bundles in a hand lay-up process with a fibre volume fraction of 30 and 55%, respectively, and achieved a flexural strength of 77 and 170 MPa, and a flexural modulus of 3.8 and 17 GPa, respectively. A twist yarn was processed by Bledzki et al. (2004) in a winding process and resulted in bending strength of 148 MPa and a bending modulus of 5.9 GPa. The results show that the reinforcement effect covers a wide range depending on the fibres and process techniques used. A clear reinforcement effect was demonstrated for the staple fibre yarns produced here.
The same staple fibre yarns were used to produce fabrics on an industrial scale and processed into composite laminates in industrial companies.
The industry partners produced fabrics and composite laminates to test the processability of the hemp staple fibre yarns. Fabrics were processed by vacuum infusion with an epoxy resin and by autoclave injection and resin transfer moulding (RTM) with a bio-based epoxy (PTP-L). Table 3 shows the construction and the calculated fibre volume fractions of hemp weft and polyester warp threads of the different composites. For comparative purposes, the already published results of composites made from flax fabrics produced in the same manner (Graupner et al., 2021) are also listed here. For the combination of the properties of hemp and glass fibres, hybrid materials were also produced, and a glass fibre-reinforced laminate was used as a reference sample. The autoclave injection process leads to significantly higher fibre volume fractions than the vacuum infusion and RTM process. Furthermore, it is noticeable that the flax laminates produced in the vacuum infusion and autoclave injection processes show significantly higher fibre volume fractions than the hemp laminates. This can be explained by the lower uniformity of the hemp yarn, which makes the fibre packing less dense (Scarponi and Messano, 2015; Maino et al., 2019). The different fibre volume fractions must be considered when evaluating the mechanical properties (Sanjay et al., 2016).
TABLE 3. Construction and composition of composite laminates (hybrid materials are symmetrically constructed; designations in brackets with Greek letters indicate internal project labels).
The tensile properties of the different laminates produced are shown in Figure 7. Vacuum infusion was used to produce hemp, glass and flax laminates as well as hybrid materials with outer hemp and inner glass layers and vice versa. The autoclave injection process was applied to produce hemp, glass and flax laminates and a hybrid material with outer glass and inner hemp layers. The RTM process was used to manufacture glass and hemp laminates, and a hybrid material with outer glass and inner hemp layers. As expected, the glass laminates show the highest tensile strength and Young’s modulus values. The hemp laminates, which were produced using the vacuum infusion and the RTM process, show comparable characteristics with tensile strengths around 150 MPa and Young´s moduli between 16.1 and 16.7 GPa (Figures 7A,B,E,F). The strength and Young’s modulus values of the hemp laminates from the autoclave injection process are slightly higher (154 MPa and 19.4 GPa), presumably due to the higher fibre volume content (Figures 7C,D). The hemp laminate produced in the autoclave injection process achieved 72% of the strength and 90% of Young’s modulus of the flax laminate. The vacuum infusion process yields 78 and 99% of the strength and Young’s modulus of the flax laminate These results can be explained due to the slightly lower reinforcing effect of the hemp yarns compared to flax (Figure 6).
FIGURE 7. Tensile strength and Young´s modulus (mean value ± standard deviation) of composite laminates produced by vacuum infusion (A,B), autoclave injection (C,D) and RTM (E,F).
The reinforcement effect is additionally affected by the crimp of the fabrics. It was shown in a previous study that the flax yarns, processed in the same way as the hemp yarns, were not completely aligned, and some crimp was present in the fabric (Graupner et al., 2021). Due to the lower fineness of the hemp yarns (300 tex) compared to the flax yarns (200 tex), it is assumed that the crimp may be more pronounced, and the reinforcing effect of the hemp yarns in the fabric is slightly reduced. In addition, the lower mechanical fibre characteristics, and the lower interlaminar shear strength (ILSS), compared to flax and flax-reinforced composites, may affect the composite characteristics (Figure 8).
FIGURE 8. Interlaminar shear strength—ILSS (mean value ± standard deviation) of composite laminates produced by vacuum infusion (A), autoclave injection (B) and RTM (C).
Table 4 summarises comparative literature values. The characteristic values determined are in the upper range of the results presented in the literature for unidirectional or fabric-reinforced hemp composites. Corbin et al. (2020b) showed that even higher tensile characteristic values are procurable with a comparable fabric with a significantly higher fibre volume fraction of 60%.
The hybrid materials made of hemp and glass show a significant improvement in tensile strength and Young’s modulus compared to the pure hemp laminates. Hybrid materials with both, outer hemp or outer glass layers were produced using the vacuum infusion process (Figures 7A,B). In this case, the higher mechanical properties of the materials with the outer hemp layers can be explained by the volume proportion of the different types of fabrics. The composite with the outer hemp layers consists of two layers of hemp and three layers of glass, whereas the material with the outer glass layers consists of two layers of glass fabric and three layers of hemp fabric. Due to the higher volume fraction of glass fibres (compare Table 3), the material with the outer hemp layers shows higher strength and stiffness. It should be noted that the properties of the hybrid materials depend significantly on the layer arrangement (S. Sharavanan et al. et al., 2018; Murugu Nachippan et al., 2020). However, due to the different volumes of hemp and glass fibres, this influence is currently difficult to assess. Hybrid composites exhibit damage patterns dominated mainly by the higher fibre volume fraction of glass fibres and their location in the outermost layers (Boria et al., 2020). In addition to the positive influence on the mechanical properties of hemp laminates, hybridisation can produce a significant advantage over glass laminates, like improved damping characteristics (La Rosa et al., 2013).
The tensile properties of the hybrid materials from the vacuum infusion and RTM processes are of a similar order of magnitude. In contrast, the properties of the materials produced in the autoclave injection process were significantly higher due to the higher fibre volume content (Figure 7). Despite comparable properties of the samples from the vacuum infusion process and the RTM process, there are considerable differences in fracture behaviour (see Figure 9). The samples produced with the epoxy resin by the vacuum infusion process failed brittle near the cap strips (Figure 9A), while the samples produced with the autoclave injection and the RTM process in combination with the bio-based epoxy resin show significant delaminations between the glass and hemp layers (Figures 9B,C). Despite the different appearance, no significant differences in the interlaminar shear strength (ILSS), which was determined using short beam shear tests, could be detected (Figure 8). One possible explanation could be the fact that the shear failure in the short beam shear test takes place in the neutral plane where the hemp fibres are located and not between the hemp and glass fabrics. The same phenomenon was determined for the previously examined flax composites (Graupner et al., 2021). It is assumed that the different failures can be attributed to the different resin systems. Despite the clear delaminations, no negative influences on the tensile properties could be detected. The materials with comparable fibre volume fractions from the vacuum infusion and RTM processes produced comparable results.
FIGURE 9. Fracture behaviour of hybrid hemp/glass tensile test specimens (glass outer layers) produced by vacuum infusion (A), autoclave injection (B) and RTM (C).
The results of the bending properties are shown in Figure 10. The trends are similar to the tensile properties with the difference that the hybrid materials with the outer hemp or glass layers from the vacuum infusion process gave the opposite result (Figures 10A,B). This effect can be attributed to the different loading during a flexural test. While the cross-sectional area is homogeneously loaded during tensile testing, in the bending test, the upper side of the specimen is loaded in compression and the lower side in tension. As the tensile forces mainly act on the outer layer, and glass fibres can absorb higher tensile forces than hemp fibres, the bending characteristics of the composite with the outer glass layer are better despite the lower glass fibre content compared to the composite with the outer hemp layers. Otherwise, the bending properties also show that hybridisation can significantly improve the properties compared to the pure hemp composite. The reinforcement potential of flax is not fully achieved by hemp, even in terms of bending properties. The hemp laminates produced in the autoclave injection process exhibited 81% of the flexural strength and 78% of the flexural modulus of the flax laminate; the vacuum infusion process achieved 89 and 76% of the flexural strength and flexural modulus. However, a comparison of the bending properties of the hemp laminates with literature data in Table 4 shows that both the bending strength and the bending modulus are in the upper range of the specified characteristic values.
FIGURE 10. Flexural strength and flexural modulus (mean value ± standard deviation) of composite laminates produced by vacuum infusion (A,B), autoclave injection (C,D) and RTM (E,F).
The results of the unnotched Charpy impact strength of composite laminates are shown in Figure 11. The glass fibre-reinforced laminates show the highest characteristic values. It is known that glass fibre-reinforced plastics have a higher toughness compared with bast fibre-reinforced composites, especially hemp fibre-reinforced plastics (Yuanjian and Isaac, 2007; Patel et al., 2015), and the fracture behaviour is different (Bonnafous et al., 2011). The impact strength of the hemp laminates ranges between 10 kJ/m2 for the laminate produced with the RTM process and 24 kJ/m2 for the laminate manufactured with the autoclave injection process. These values are comparable to an epoxy laminate produced from 0/90° fibre webs resulting in Charpy impact strength of 20 kJ/m2 (Väisänen et al., 2018).
FIGURE 11. Unnotched Charpy impact strength (mean value ± standard deviation) of composite laminates produced by vacuum infusion (A), autoclave injection (B) and RTM (C).
Compared to the tensile and flexural properties, it is noticeable that the use of hybrid materials leads to an even more significant improvement in impact strength than the hemp laminate. The hybrid materials from the vacuum infusion process, which were produced with outer hemp or outer glass layers, show higher values for the material with the outer hemp layers. Since glass fibres are considerably tougher than hemp fibre bundles, the one additional glass layer in the material with the outer hemp layers results in better energy absorption under impact loading.
As visible in Figure 9, it was expected that delaminations could positively affect the impact strength due to energy absorption. However, this hypothesis can only be confirmed by tendency. The laminates from the vacuum infusion process and the RTM process have a comparable fibre volume fraction (Table 3) and similar tensile and flexural properties (Figures 7, 10). The impact strength of the samples from the vacuum infusion process (126 kJ/m2) was slightly lower than that of the samples from the RTM process (132 kJ/m2). The significant delaminations could explain the somewhat higher impact strength between the glass and hemp layers, which can absorb energy during fracture under impact loading.
As described for the round and rectangular rods, the hemp fibre bundles in the laminates also lead to low impact strength compared to the flax fibre-reinforced laminates. For the laminates produced in the autoclave injection process and vacuum infusion process, the impact strength corresponds only to 57 and 52% to the values of the flax fibre laminate.
The price is still a major barrier to the widespread use of natural fibres in higher-value applications. Prices for raw fibres from high-quality long flax are around 4.40 €/kg. The development of high-quality semi-finished products from flax tow significantly reduced costs, as 1 kg of the raw fibres is currently at 1.00 to 1.50 € (Graupner et al., 2021). By using hemp fibres, the raw material price can be further reduced to below 1.00 €. The lower raw material costs subsequently affect the costs of the resulting semi-finished product (yarn or fabric). The properties of the pultruded composites and the laminates made from the quasi-UD fabrics show that it would be possible to use them in areas subject to higher loads. Although the mechanical properties of flax fibre-reinforced composites could not be achieved, the hemp laminates achieved on average a reinforcing effect of more than 85% of the tensile and bending properties, in some cases even more. One deficit is the lower impact strength, which should be understood and improved in future work. The previous work showed that a leaf spring for the bogie of a narrow-gauge railway could be made from the fabrics produced from the novel flax staple fibre yarns (Graupner et al., 2021). The use of hemp fabrics is also considered but has not yet been implemented. By hybridising hemp and glass, deficits such as the low toughness of the hemp laminates can be reduced. In addition, water absorption is significantly reduced by the outer glass layers, making it conceivable for use in exterior areas subject to higher mechanical loads, such as leaf springs. Due to the good damping characteristics of the hemp fibres combined with the higher toughness, strength and stiffness of the glass fibres, there may be further fields of development.
The work followed the objective of developing cost-efficient, high-quality textile semi-finished products made of hemp for the composites sector. This goal has already been achieved for flax tow in a previous study and could be transferred to hemp from the disordered fibre line (total fibre line) to reduce further the raw material costs and the resulting semi-finished product costs. Similar to flax, the fibre properties slightly decreased due to the sliver production but were not significantly influenced by the following processing steps (yarn and fabric production).
The aim was to achieve at least 80% of the reinforcing potential of flax composites. It has been shown that the fibre bundles in the staple fibre yarns with almost unidirectional fibre orientation were considerably less shortened by the spinning process than the fibre bundles in the rotor yarns. Nevertheless, the rotor yarns contained fibre bundles with considerably higher lengths than the critical fibre length necessary to reinforce composites. However, in contrast to the staple fibre yarns, the rotor yarns exhibited a rather large twist. Therefore, the reinforcing effect of the staple fibre yarns was significantly better. With the staple fibre yarns, the set goal was achieved for the tensile and bending properties and was in some cases even considerably exceeded for the UD pultruded composites. The impact properties represent a deficit. The unnotched Charpy impact strength only ranged between 50 and 60% of the flax composites. The exact reason for the lower toughness of hemp compared to flax is investigated in our ongoing research.
The staple fibre yarns were used to manufacture quasi-UD fabrics, which were processed into composite laminates in industrial processes. The achieved characteristic values of the tensile and bending properties were relatively high. It is expected that these can be further increased if the fabric structure is improved. It was found that the yarns have an ondulation (crimp), which leads to a deviation of the fibre orientation from the longitudinal axis and thus reduces the reinforcement effect. It is expected that a further increase in the characteristic values can be achieved by minimising the crimp. Moreover, further processing of the raw hemp and the elimination of shives can help to improve the uniformity of the yarns and fabrics and thus achieve a higher packing density in the composite.
The development of hybrid materials from hemp and glass is a solution to improve the low toughness of hemp laminates. At the same time, tensile and bending properties are also improved, whereas the damping properties of glass laminates will probably increase. Further application possibilities, especially for vibration-loaded outdoor applications, should be investigated in future research work.
Overall, it could be shown that good semi-finished textile products can be produced with cost-efficient hemp from the disordered fibre line, which leads to good tensile and bending properties for use in components subject to higher loads.
The original contributions presented in the study can be provided upon request by the corresponding authors.
Conceptualization: NG and JM. Formal analysis: NG, K-HL, DW, EB, IW, MJ, and JM. Funding acquisition: NG, K-HL, H-WH, IW, and JM. Investigation: NG, K-HL, DW, H-WH, EB, HR, MJ, and JM. Methodology: NG, K-HL, DW, H-WH, EB, IW, HR, MJ, and JM. Project administration, NG, K-HL, EB, IW, MJ, and JM. Resources: TG and JM. Visualization: NG. Writing—original draft: NG and JM. Writing—review and editing, NG, K-HL, DW, H-WH, EB, and JM. All authors have read and agreed to the published version of the manuscript.
The research project, Innovative yarn structures and their competitiveness as part of the project fibre-reinforced composites for structural applications based on novel, low-twist bast fibre yarns (NF-CompPlus), was carried out in the framework of the industrial collective research programme. This study received funding from the Federal Ministry of Food and Agriculture (BMEL) based on a resolution of the German Bundestag (funding no. 22026215, 22014817 & 22015417). The funder was not involved in the study design, collection, analysis, interpretation of data, the writing of this article or the decision to submit it for publication. The costs for the open-access publication are covered by the State and University Library of Bremen (Bremen, Germany).
The company INVENT GmbH is represented by the authors IW and MJ. INVENT GmbH was involved in the project as a sub-project leader and received proportionate funding from the Federal Ministry of Food and Agriculture (BMEL). Author H-WH is employed by Wenzel & Hoos GmbH. Wenzel & Hoos GmbH was responsible for the production of the fabrics and received a proportionate grant in the form of a subcontract from the Federal Ministry of Food and Agriculture (BMEL). The companies Novacom Verstärkte Kunststoffe GmbH, SachsenLeinen GmbH and BAFA Neu GmbH received proportionate funding in the form of subcontracts from the Federal Ministry of Food and Agriculture (BMEL). Novacom Verstärkte Kunststoffe GmbH was responsible for the production of composite materials from the fabrics. SachsenLeinen GmbH and BAFA Neu GmbH were responsible for supplying the fibres. All the companies listed were only proportionally funded by the Federal Ministry of Food and Agriculture (BMEL). The companies provided the remaining funding in the form of machine and labour hours.
The remaining authors declare that the research was conducted in the absence of any commercial or financial relationships that could be construed as a potential conflict of interest.
All claims expressed in this article are solely those of the authors and do not necessarily represent those of their affiliated organizations, or those of the publisher, the editors and the reviewers. Any product that may be evaluated in this article, or claim that may be made by its manufacturer, is not guaranteed or endorsed by the publisher.
Our special thanks go to our project partners, without whom we would not have been able to realise the project: Novacom Verstärkte Kunststoffe GmbH (Lisa Bruns, Luisa Berger & Albert Bruns), SachsenLeinen GmbH (Torsten Brückner & Kay Kölzig) & BAFA Neu GmbH (Bernd Frank). Moreover, we would like to thank our student co-workers Alexander Behrens, Steffen Deutsch, Charlotte Spelsberg, Julia Kubitz and Timo Acktun, who supported us with practical experiments during the project.
1† In memory and honour of Uwe Schönfeld, the PTP resin developer, who passed away much too early.
Abbas, Z., Shahid, S., Nawab, Y., Shaker, K., and Umair, M. (2020). Effect of Glass Microspheres and Fabric Weave Structure on Mechanical Performance of Hemp/green Epoxy Composites. Polym. Composites 41 (11), 4771–4787. doi:10.1002/pc.25751
Adusumalli, R.-B., Reifferscheid, M., Weber, H. K., Roeder, T., Sixta, H., and Gindl, W. (2010). Shear Strength of the Lyocell Fiber/polymer Matrix Interface Evaluated with the Microbond Technique. J. Compos. Mater. 46 (3), 359–367. doi:10.1177/0021998310382312
Awais, H., Nawab, Y., Anjang, A., Akil, H. M., and Abidin, M. S. Z. (2020). Mechanical Properties of Continuous Natural Fibres (Jute, Hemp, Flax) Reinforced Polypropylene Composites Modified with Hollow Glass Microspheres. Fibers Polym. 21 (9), 2076–2083. doi:10.1007/s12221-020-2260-z
Baets, J., Plastria, D., Ivens, J., and Verpoest, I. (2014). Determination of the Optimal Flax Fibre Preparation for Use in Unidirectional Flax-Epoxy Composites. J. Reinforced Plastics Composites 33 (5), 493–502. doi:10.1177/0731684413518620
Baley, C., Gomina, M., Breard, J., Bourmaud, A., and Davies, P. (2020). Variability of Mechanical Properties of Flax Fibres for Composite Reinforcement. A Review. Ind. Crops Prod. 145, 111984. doi:10.1016/j.indcrop.2019.111984
Bambach, M. R. (2020). Direct Comparison of the Structural Compression Characteristics of Natural and Synthetic Fiber-Epoxy Composites: Flax, Jute, Hemp, Glass and Carbon Fibers. Fibers 8 (10), 62. doi:10.3390/fib8100062
Barbière, R., Touchard, F., and Chocinski-Arnault, L. (2018). “Fatigue Behaviour in Different Moisture Conditions Ofa Woven Hemp Fibre Reinforced Epoxy Composite,” in ECCM18 – 18th European Conference on Composite Material, Athens, Greece (ESCM – European Society for Composite Materials and University of Patras). June.
Barbière, R., Touchard, F., Chocinski-Arnault, L., and Mellier, D. (2020). Influence of Moisture and Drying on Fatigue Damage Mechanisms in a Woven Hemp/Epoxy Composite: Acoustic Emission and Micro-ct Analysis. Int. J. Fatigue 136, 105593. doi:10.1016/j.ijfatigue.2020.105593
Bhoopathi, R., Ramesh, M., Naveen Kumar, M., Sanjay Balaji, P., and Sasikala, G. (2018). Studies on Mechanical Strengths of Hemp-Glass Fibre Reinforced Epoxy Composites. IOP Conf. Ser. Mater. Sci. Eng. 402, 012083. doi:10.1088/1757-899x/402/1/012083
Bledzki, A. K., Fink, H.-P., and Specht, K. (2004). Unidirectional Hemp and Flax EP- and PP-Composites: Influence of Defined Fiber Treatments. J. Appl. Polym. Sci. 93 (5), 2150–2156. doi:10.1002/app.20712
Boccarusso, L., Carrino, L., Durante, M., Formisano, A., Langella, A., and Memola Capece Minutolo, F. (2016). Hemp Fabric/Epoxy Composites Manufactured by Infusion Process: Improvement of Fire Properties Promoted by Ammonium Polyphosphate. Composites B: Eng. 89, 117–126. doi:10.1016/j.compositesb.2015.10.045
Boccarusso, L., Durante, M., and Langella, A. (2018). Lightweight Hemp/Bio-Epoxy Grid Structure Manufactured by a New Continuous Process. Composites Part B: Eng. 146, 165–175. doi:10.1016/j.compositesb.2018.04.009
Bonnafous, C., Touchard, F., and Chocinski-Arnault, L. (2011). Damage Mechanisms in Hemp-Fibre Woven Fabric Composite, and Comparison with Glass-Fibre Composite. Polym. Polym. Composites 19 (7), 543–552. doi:10.1177/096739111101900703
Boria, S., Santulli, C., Raponi, E., Sarasini, F., and Tirillò, J. (2020). Analytical Modeling and Experimental Validation of the Low-Velocity Impact Response of Hemp and Hemp/Glass Thermoset Composites. J. Compos. Mater. 54 (3), 409–421. doi:10.1177/0021998319862856
Borrello, M., Mele, M., Campana, G., and Secchi, M. (2020). Manufacturing and Characterization of Hemp‐reinforced Epoxy Composites. Polym. Composites 41 (6), 2316–2329. doi:10.1002/pc.25540
Bourmaud, A., Beaugrand, J., Shah, D. U., Placet, V., and Baley, C. (2018). Towards the Design of High-Performance Plant Fibre Composites. Prog. Mater. Sci. 97, 347–408. doi:10.1016/j.pmatsci.2018.05.005
Bourmaud, A., Shah, D. U., Beaugrand, J., and Dhakal, H. N. (2020). Property Changes in Plant Fibres during the Processing of Bio-Based Composites. Ind. Crops Prod. 154, 112705. doi:10.1016/j.indcrop.2020.112705
Branda, F., Malucelli, G., Durante, M., Piccolo, A., Mazzei, P., Costantini, A., et al. (2016). Silica Treatments: A Fire Retardant Strategy for Hemp Fabric/epoxy Composites. Polymers (Basel) 8 (8). doi:10.3390/polym8080313
Buksnowitz, C., Adusumalli, R., Pahler, A., Sixta, H., and Gindl, W. (2010). Acoustical Properties of Lyocell, Hemp, and Flax Composites. J. Reinforced Plastics Composites 29 (20), 3149–3154. doi:10.1177/0731684410367533
Cicala, G., Cristaldi, G., Recca, G., Ziegmann, G., El-Sabbagh, A., and Dickert, M. (2009). Properties and Performances of Various Hybrid Glass/Natural Fibre Composites for Curved Pipes. Mater. Des. 30 (7), 2538–2542. doi:10.1016/j.matdes.2008.09.044
Corbin, A.-C., Sala, B., Soulat, D., Ferreira, M., Labanieh, A.-R., and Placet, V. (2020). Development of Quasi-Unidirectional Fabrics with Hemp Fiber: A Competitive Reinforcement for Composite Materials. J. Compos. Mater. 0 (0), 0021998320954230. doi:10.1177/0021998320954230
Corbin, A.-C., Soulat, D., Ferreira, M., Labanieh, A.-R., Gabrion, X., Malécot, P., et al. (2020). Towards Hemp Fabrics for High-Performance Composites: Influence of Weave Pattern and Features. Composites Part B: Eng. 181, 107582. doi:10.1016/j.compositesb.2019.107582
Cordin, M., Bechtold, T., and Pham, T. (2018). Effect of Fibre Orientation on the Mechanical Properties of Polypropylene-Lyocell Composites. Cellulose 25 (12), 7197–7210. doi:10.1007/s10570-018-2079-6
Dayo, A. Q., Zegaoui, A., Nizamani, A. A., Kiran, S., Wang, J., Derradji, M., et al. (2018). The Influence of Different Chemical Treatments on the Hemp Fiber/Polybenzoxazine Based green Composites: Mechanical, thermal and Water Absorption Properties. Mater. Chem. Phys. 217, 270–277. doi:10.1016/j.matchemphys.2018.06.040
de Vasconcellos, D. S., Sarasini, F., Touchard, F., Chocinski-Arnault, L., Pucci, M., Santulli, C., et al. (2014). Influence of Low Velocity Impact on Fatigue Behaviour of Woven Hemp Fibre Reinforced Epoxy Composites. Composites Part B: Eng. 66, 46–57. doi:10.1016/j.compositesb.2014.04.025
de Vasconcellos, D. S., Touchard, F., and Chocinski-Arnault, L. (2014). Tension-tension Fatigue Behaviour of Woven Hemp Fibre Reinforced Epoxy Composite: A Multi-Instrumented Damage Analysis. Int. J. Fatigue 59, 159–169. doi:10.1016/j.ijfatigue.2013.08.029
Deimann, F. (2020). “Personal Communication with Mr,” in Friedrich Deimann about Prices for Biaxial Flax Fabrics from 2020-11-13.
Deutsches Institut für Normung (2003a). DIN EN 14130:1998–Verstärkte Kunststoffverbundwerkstoffe–Bestimmung der scheinbaren interlaminaren Scherfestigkeit nach dem Dreipunktverfahren mit kurzem Balken. (Determination of the Apparent Interlaminar Shear Strength According to the Three-Point Bending Method with Short Beam), German version.
Deutsches Institut für Normung (2005). “DIN EN ISO 139:2005 –Textilien - Normalklimate für die Probenvorbereitung und Prüfung (Textiles - Standard Atmospheres for Conditioning and Testing). German version.
Deutsches Institut für Normung (2003b). DIN EN ISO 14125:2003 – Faserverstärkte Kunststoffe - Bestimmung der Biegeeigenschaften. (Fibre-reinforced plastics - Determination of bending properties), German version.
Deutsches Institut für Normung (2010). DIN EN ISO 179-1 – Kunststoffe – Bestimmung Der Charpy-Schlageigenschaften – Teil 1. (Plastics - Determination of the Charpy Impact Properties), German version. Nicht instrumentierte schlagzähigkeitsprüfung.
Deutsches Institut für Normung (2006). “DIN EN ISO 291:2005 – Kunststoffe - Normalklimate für Konditionierung und Prüfung,” (Plastics–Standard Atmospheres for Conditioning and Testing). German version.
Deutsches Institut für Normung (1996). “DIN EN ISO 527-2 – Kunststoffe: Bestimmung der Zugeigenschaften; Teil 2 Prüfbedingungen für Form- und Extrusionsmassen,” (Plastics–Determination of Tensile Properties – Part 2: Test Conditions for Moulding and Extrusion Plastics). German version.
Fischer, H., Müssig, J., and Bluhm, C. (2006). Enzymatic Modification of Hemp Fibres for Sustainable Production of High Quality Materials: Influence of Processing Parameters. J. Nat. Fibers 3 (2/3), 39–53. doi:10.1300/j395v03n02_03
Fotouh, A., Wolodko, J. D., and Lipsett, M. G. (2014). Fatigue of Natural Fiber Thermoplastic Composites. Composites Part B: Eng. 62, 175–182. doi:10.1016/j.compositesb.2014.02.023
Goutianos, S., Peijs, T., Nystrom, B., and Skrifvars, M. (2006). Development of Flax Fibre Based Textile Reinforcements for Composite Applications. Appl. Compos. Mater. 13 (4), 199–215. doi:10.1007/s10443-006-9010-2
Graupner, N., Lehmann, K.-H., Weber, D. E., Hilgers, H. W., Bell, E. G., Walenta, I., et al. (2021). Novel Low-Twist Bast Fibre Yarns from Flax Tow for High-Performance Composite Applications. Materials 14 (1), 105.
Graupner, N., Sarasini, F., and Müssig, J. (2020). Ductile Viscose Fibres and Stiff basalt Fibres for Composite Applications - an Overview and the Potential of Hybridisation. Composites Part B: Eng. 194, 108041. doi:10.1016/j.compositesb.2020.108041
Hao, L. C., Abdan, K., Lee, S. H., and Liu, M. (2020). A Comprehensive Review on Bast Fibre Retting Process for Optimal Performance in Fibre-Reinforced Polymer Composites. Adv. Mater. Sci. Eng. 07, 1–27.
Ingrao, C., Lo Giudice, A., Bacenetti, J., Tricase, C., Dotelli, G., Fiala, M., et al. (2015). Energy and Environmental Assessment of Industrial Hemp for Building Applications: A Review. Renew. Sustain. Energ. Rev. 51, 29–42. doi:10.1016/j.rser.2015.06.002
International Organization for Standardization (2003). ISO 3597-1:2003: Textile-Glass-Reinforced Plastics – Determination of Mechanical Properties on Rods Made of Roving-Reinforced Resin – Part 2: Determination of Flexural Strength.
Islam, M. S., Pickering, K. L., and Foreman, N. J. (2011). Influence of Alkali Fiber Treatment and Fiber Processing on the Mechanical Properties of Hemp/Epoxy Composites. J. Appl. Polym. Sci. 119 (6), 3696–3707. doi:10.1002/app.31335
Kumar, S., Gangil, B., Prasad, L., and Kumar Patel, V. (2017). “A Review on Mechanical Behaviour of Bast-Glass Fibre Based Hybrid Polymer compositesICEMS-2016,” in Materials Today: Proceedings International Conference on Recent Trends in Engineering and Material Sciences, Jaipur, India, March 17-19, 2016, 49. Mater. Today Proc. 9576–9580. doi:10.1016/j.matpr.2017.06.227
La Rosa, A. D., Cozzo, G., Latteri, A., Recca, A., Björklund, A., Parrinello, E., et al. (2013). Life Cycle Assessment of a Novel Hybrid Glass-Hemp/Thermoset Composite. J. Clean. Prod. 44, 69–76. doi:10.1016/j.jclepro.2012.11.038
Lebrun, G., Couture, A., and Laperrière, L. (2013). Tensile and Impregnation Behavior of Unidirectional Hemp/Paper/Epoxy and Flax/Paper/Epoxy Composites. Compos. Structures 103, 151–160. doi:10.1016/j.compstruct.2013.04.028
Lehmann, K.-H., Janßen, A., Popzyk, M.-I., Schlesinger, Y., and Hansmann, T. J. (2020). Gries. Herstellung von Rotorgarnen mit niedriger Drehung. Melliand Textilberichte (4), 120–122. doi:10.1007/978-3-663-19754-6_3
Li, Y., Pickering, K. L., and Farrell, R. L. (2009). Determination of Interfacial Shear Strength of white Rot Fungi Treated Hemp Fibre Reinforced Polypropylene. Composites Sci. Tech. 69 (7-8), 1165–1171. doi:10.1016/j.compscitech.2009.02.018
Liu, M., Ale, M. T., Kołaczkowski, B., Fernando, D., Daniel, G., Meyer, A. S., et al. (2017). Comparison of Traditional Field Retting and Phlebia Radiata Cel 26 Retting of Hemp Fibres for Fibre-Reinforced Composites. AMB Expr. 7 (1), 58. doi:10.1186/s13568-017-0355-8
Liu, M., Baum, A., Odermatt, J., Berger, J., Yu, L., Zeuner, B., et al. (2017). Oxidation of Lignin in Hemp Fibres by Laccase: Effects on Mechanical Properties of Hemp Fibres and Unidirectional Fibre/Epoxy Composites. Composites A: Appl. Sci. Manufacturing 95, 377–387. doi:10.1016/j.compositesa.2017.01.026
Liu, M., Meyer, A. S., Fernando, D., Silva, D. A. S., Daniel, G., and Thygesen, A. (2016). Effect of Pectin and Hemicellulose Removal from Hemp Fibres on the Mechanical Properties of Unidirectional Hemp/Epoxy Composites. Composites Part A: Appl. Sci. Manufacturing 90, 724–735. doi:10.1016/j.compositesa.2016.08.037
Liu, M., Silva, D. A. S., Fernando, D., Meyer, A. S., Madsen, B., Daniel, G., et al. (2016). Controlled Retting of Hemp Fibres: Effect of Hydrothermal Pre-treatment and Enzymatic Retting on the Mechanical Properties of Unidirectional Hemp/Epoxy Composites. Composites Part A: Appl. Sci. Manufacturing 88, 253–262. doi:10.1016/j.compositesa.2016.06.003
Liu, M., Thygesen, A., Summerscales, J., and Meyer, A. S. (2017). Targeted Pre-treatment of Hemp Bast Fibres for Optimal Performance in Biocomposite Materials: A Review. Ind. Crops Prod. 108, 660–683. doi:10.1016/j.indcrop.2017.07.027
Liu, Q., and Hughes, M. (2008). The Fracture Behaviour and Toughness of Woven Flax Fibre Reinforced Epoxy Composites. Composites Part A: Appl. Sci. Manufacturing 39 (10), 1644–1652. doi:10.1016/j.compositesa.2008.07.008
Madsen, B., Hoffmeyer, P., Thomsen, A. B., and Lilholt, H. (2007). Hemp Yarn Reinforced Composites - I. Yarn Characteristics. Composites Part A: Appl. Sci. Manufacturing 38 (10), 2194–2203. doi:10.1016/j.compositesa.2007.06.001
Maino, A., Janszen, G., and Di Landro, L. (2019). Glass/Epoxy and Hemp/Bio Based Epoxy Composites: Manufacturing and Structural Performances. Polym. Composites 40 (S1), E723–E731. doi:10.1002/pc.24973
Manaia, J. P., Manaia, A. T., and Rodriges, L. (2019). Industrial Hemp Fibers: An Overview. Fibers 7 (12). doi:10.3390/fib7120106
Miritoiu, C. M., Stanescu, M. M., Burada, C. O., Bolcu, D., Padeanu, A., and Bolcu, A. (2019). “Comparisons between Some Composite Materials Reinforced with Hemp Fibers,” in Materials Today: Proceedings 35th Danubia Adria Symposium on Advances in Experimental Mechanics, 12, 499–507.
Mittal, V., Saini, R., and Sinha, S. (2016). Natural Fiber-Mediated Epoxy Composites - A Review. Composites Part B: Eng. 99, 425–435. doi:10.1016/j.compositesb.2016.06.051
Müller, D. H., and Krobjilowski, A. (2004). Improving the Impact Strength of Natural Fiber Reinforced Composites by Specifically Designed Material and Process Parameters. Int. Nonwovens J. (Inj) 13 (4), 31–38. doi:10.1177/1558925004os-1300405
Murugan, R., Muthukumar, V., Pradeepkumar, K., Muthukumaran, A., and Rajesh, V. (2021). “Influence of Fiber Orientation on Mechanical Properties and Free Vibration Characteristics of Glass/hemp Hybrid Composite Laminates,” in Trends in Mechanical and Biomedical Design. Editors E. Titilayo Akinlabi, P. Ramkumar, and M. Selvaraj (Singapore: Springer Singapore), 881–889. doi:10.1007/978-981-15-4488-0_74
Murugu Nachippan, N., Alphonse, M., K Bupesh Raja, V., Shasidhar, S., Varun Teja, G., and Harinath Reddy, R. (2020). Experimental Investigation of Hemp Fiber Hybrid Composite Material for Automotive Application. Mater. Today Proc. 44, 3666–3672. doi:10.1016/j.matpr.2020.10.798
Musio, S., Müssig, J., and Amaducci, S. (2018). Optimizing Hemp Fiber Production for High Performance Composite Applications. Front. Plant Sci. 9, 1702. doi:10.3389/fpls.2018.01702
Müssig, J., and Albrecht, K. (2018). Flax & Hemp Fiber Composites, a Market Reality - the Biobased Solutions for the Industry, Chapter Are Flax and Hemp Fiber Composites Sustainable? JEC Composites. Co-published CELC/JEC GROUP.
Müssig, J., and Amaducci, S. (2018). Scanner Based Image Analysis to Characterise the Influence of Agronomic Factors on Hemp (Cannabis Sativa L.) Fibre Width. Ind. Crops Prod. 113, 28–37. doi:10.1016/j.indcrop.2017.12.059
Müssig, J., Fischer, H., Graupner, N., and Drieling, A. (2010). “Testing Methods for Measuring Physical and Mechanical Fibre Properties (Plant and Animal Fibres), Chapter 13, Pages 269–311,” in Industrial Applications of Natural Fibre - Structure, Properties and Technical Applications. Editor J. Müssig. edition (Chichster, UK: John Wiley & Sons), 1.
Müssig, J., Amaducci, S., Bourmaud, A., Beaugrand, J., and Shah, D. U. (2020a). Transdisciplinary Top-Down Review of Hemp Fibre Composites: From an Advanced Product Design to Crop Variety Selection. Composites C: Open Access 2, 100010. doi:10.1016/j.jcomc.2020.100010
Müssig, J., Haag, K., Musio, S., Bjelková, M., Albrecht, K., Uhrlaub, B., et al. (2020b). Biobased 'Mid-Performance' Composites Using Losses from the Hackling Process of Long Hemp - A Feasibility Study as Part of the Development of a Biorefinery Concept -. Ind. Crops Prod. 145, 111938. doi:10.1016/j.indcrop.2019.111938
Müssig, J. (2010). Industrial Applications of Natural Fibres: Structure, Properties and Technical Applications. edition, 1. Chichster, UK: John Wiley & Sons.
Müssig, J., and Martens, R. (2003). Quality Aspects in Hemp Fibre Production-Influence of Cultivation, Harvesting and Retting. J. Ind. Hemp 8 (1), 11–32. doi:10.1300/j237v08n01_03
Patel, H., Ren, G., Hogg, P. J., and Peijs, T. (2015). Hemp Fibre as Alternative to Glass Fibre in Sheet Moulding Compound. Part 2 Impact Properties. Plastics, Rubber and Composites 44 (7), 291–298. doi:10.1179/1743289815y.0000000030
Patel, K., Gohil, P. P., and Chaudhary, V. (2018). Investigations on Drilling of Hemp/Glass Hybrid Composites. Mater. Manufacturing Process. 33 (15), 1714–1725. doi:10.1080/10426914.2018.1453150
Perrier, A., de Vasconcellos, D. S., Touchard, F., Chocinski-Arnault, L., and Mellier, D. (2015). Full-field Measurement at the Weave Scale in Hemp/Epoxy Composite Using Digital Image Correlation. Polym. Polym. Composites 23 (9), 589–600. doi:10.1177/096739111502300901
Perrier, A., Touchard, F., Chocinski-Arnault, L., and Mellier, D. (2017). Quantitative Analysis by Micro-ct of Damage during Tensile Test in a Woven Hemp/Epoxy Composite after Water Ageing. Composites Part A: Appl. Sci. Manufacturing 102, 18–27. doi:10.1016/j.compositesa.2017.07.018
Poilâne, C., Cherif, Z. E., Richard, F., Vivet, A., Ben Doudou, B., and Chen, J. (2014). Polymer Reinforced by Flax Fibres as a Viscoelastoplastic Material. Compos. Structures 112 (0), 100–112. doi:10.1016/j.compstruct.2014.01.043
Ramesh, M. (2019). Flax (Linum Usitatissimum l.) Fibre Reinforced Polymer Composite Materials: A Review on Preparation, Properties and Prospects. Prog. Mater. Sci. 102, 109–166. doi:10.1016/j.pmatsci.2018.12.004
Réquilé, S., Le Duigou, A., Bourmaud, A., and Baley, C. (2019). Deeper Insights into the Moisture-Induced Hygroscopic and Mechanical Properties of Hemp Reinforced Biocomposites. Composites Part A: Appl. Sci. Manufacturing 123, 278–285. doi:10.1016/j.compositesa.2019.05.006
Réquilé, S., Mazian, B., Grégoire, M., Musio, S., Gautreau, M., Nuez, L., et al. (2021). Exploring the Dew Retting Feasibility of Hemp in Very Contrasting European Environments: Influence on the Tensile Mechanical Properties of Fibres and Composites. Ind. Crops Prod. 164, 113337. doi:10.1016/j.indcrop.2021.113337
Robillard, M., Lebrun, G., Veritá, Monte., and Ascona, (2010). “Processing and Mechanical Properties of Unidirectional Hemp-Paper/Epoxy Composites,” in The 10th International Conference on Flow Processes in Composite Materials (FPCM10), July 11-15, 2010 (CH).
Sanjay, M. R., Arpitha, G. R., Laxmana Naik, L., Gopalakrishna, K., and Yogesha, B. (2016). Experimental Investigation on Mechanical Properties of Hemp/E-Glass Fabric Reinforced Polyester Hybrid Composites. J. Mater. Eng. Structures 3 (3), 117–128.
Sanjay, M., and Yogesha, B. (2017). “Studies on Natural/glass Fiber Reinforced Polymer Hybrid Composites: An Evolution,” in Materials Today: Proceedings5th International Conference of Materials Processing and Characterization (ICMPC), 2739–2747. Part A2016. doi:10.1016/j.matpr.2017.02.151Mater. Today Proc.42
Santamala, H., Livingston, R., Sixta, H., Hummel, M., Skrifvars, M., and Saarela, O. (2016). Advantages of Regenerated Cellulose Fibres as Compared to Flax Fibres in the Processability and Mechanical Performance of Thermoset Composites. Composites Part A: Appl. Sci. Manufacturing 84, 377–385. doi:10.1016/j.compositesa.2016.02.011
Santulli, C., and Caruso, A. P. (2009). Effect of Fibre Architecture on the Falling Weight Impact Properties of Hemp/Epoxy Composites. J. Biobased Mat Bioenergy 3, 291–297. doi:10.1166/jbmb.2009.1037
Scarponi, C., and Messano, M. (2015). Comparative Evaluation between E-Glass and Hemp Fiber Composites Application in Rotorcraft Interiors. Composites Part B: Eng. 69, 542–549. doi:10.1016/j.compositesb.2014.09.010
Scida, D., Bourmaud, A., and Baley, C. (2017). Influence of the Scattering of Flax Fibres Properties on Flax/Epoxy Woven Ply Stiffness. Mater. Des. 122, 136–145. doi:10.1016/j.matdes.2017.02.094
Scutaru, M. L., Baba, M., and Baritz, M. I. (2014). Irradiation Influence on a New Hybrid Hemp Bio-Composite. J. Optoelectronics Adv. Mater. 16 (7-8), 887–891.
Sebe, G., Cetin, N. S., Hill, C. A. S., and Hughes, M. (2000). RTM Hemp Fibre-Reinforced Polyester Composites. Appl. Compos. Mater. 7 (5-6), 341–349.
Sepe, R., Bollino, F., Boccarusso, L., and Caputo, F. (2018). Influence of Chemical Treatments on Mechanical Properties of Hemp Fiber Reinforced Composites. Composites Part B: Eng. 133, 210–217. doi:10.1016/j.compositesb.2017.09.030
Shah, D. U., Schubel, P. J., Clifford, M. J., and Licence, P. (2014). Mechanical Property Characterization of Aligned Plant Yarn Reinforced Thermoset Matrix Composites Manufactured via Vacuum Infusion. Polymer-Plastics Tech. Eng. 53 (3), 239–253. doi:10.1080/03602559.2013.843710
Shahzad, A. (2011). Comparison of Tensile Properties and Impact Damage Tolerance of Hemp and Glass Fiber Composites. J. Reinforced Plastics Composites 30 (22), 1877–1893. doi:10.1177/0731684411431123
Shahzad, A. (2012). Hemp Fiber and its Composites - a Review. J. Compos. Mater. 46 (8), 973–986. doi:10.1177/0021998311413623
Shahzad, A., and Isaac, D. H. (2014). Fatigue Properties of Hemp and Glass Fiber Composites. Polym. Compos. 35 (10), 1926–1934. doi:10.1002/pc.22851
Singh, J., Kumar, M., Kumar, S., and Mohapatra, S. K. (2017). Properties of Glass-Fiber Hybrid Composites: A Review. Polymer-Plastics Tech. Eng. 56 (5), 455–469. doi:10.1080/03602559.2016.1233271
Somashekar, S. M., Manjunath, V., Gowtham, M. J., and Balasubramaniam, N. S. (2016). Investigation on Mechanical Properties of Hemp-E Glass Fiber Reinforced Polymer Composites. Int. J. Mech. Eng. Tech. 7 (3), 182–192.
S. Sharavanan et al., S., Vijaya Ramnath, S. S. e. a., Elanchezhian, C., and Rajesh, S. (2018). Experimental Investigation of Tensile and Impact Behaviour of Hemp Flax Hybrid Composite. Ijmperd 8 (3), 549–556. doi:10.24247/ijmperdjun201859
Tamburini, E., Leon, A. G., Perito, B., Di Candilo, M., and Mastromei, G. (2004). Exploitation of Bacterial Pectinolytic Strains for Improvement of Hemp Water Retting - Pectinolytic Bacteria in Water Retting. Euphytica 140 (1-2), 47–54. doi:10.1007/s10681-004-4754-y
Tanasă, F., Zănoagă, M., Teacă, C.-A., Nechifor, M., and Shahzad, A. (2020). Modified Hemp Fibers Intended for Fiber-Reinforced Polymer Composites Used in Structural Applications - a Review. I. Methods of Modification. Polym. Composites 41 (1), 5–31.
Thyavihalli Girijappa, Y. G., Mavinkere Rangappa, S., Parameswaranpillai, J., and Siengchin, S. (2019). Natural Fibers as Sustainable and Renewable Resource for Development of Eco-Friendly Composites: A Comprehensive Review. Front. Mater. 6, 226. doi:10.3389/fmats.2019.00226
Tripathy, S. S., Di Landro, L., Fontanelli, D., Marchetti, A., and Levita, G. (2000). Mechanical Properties of Jute Fibers and Interface Strength with an Epoxy Resin. J. Appl. Polym. Sci. 75, 1585–1596. doi:10.1002/(sici)1097-4628(20000328)75:13<1585:aid-app4>3.0.co;2-q
Väisänen, T., Batello, P., Lappalainen, R., and Tomppo, L. (2018). Modification of Hemp Fibers (Cannabis Sativa L.) for Composite Applications. Ind. Crops Prod. 111, 422–429. doi:10.1016/j.indcrop.2017.10.049
Wood, B. M., Coles, S. R., Maggs, S., Meredith, J., and Kirwan, K. (2011). Use of Lignin as a Compatibiliser in Hemp/Epoxy Composites. Composites Sci. Tech. 71 (16), 1804–1810. doi:10.1016/j.compscitech.2011.06.005
Yan, L., Chouw, N., and Jayaraman, K. (2014). Flax Fibre and its Composites - A Review. Composites Part B: Eng. 56 (0), 296–317. doi:10.1016/j.compositesb.2013.08.014
Yuanjian, T., and Isaac, D. H. (2007). Impact and Fatigue Behaviour of Hemp Fibre Composites. Composites Sci. Tech. 67 (15), 3300–3307. doi:10.1016/j.compscitech.2007.03.039
Keywords: Staple fibre yarn, rotor yarn, quasi-unidirectional fabric, hemp, mechanical properties, hybrid hemp/glass composites
Citation: Graupner N, Weber DE, Bell EG, Lehmann K-H, Hilgers H-W, Randerath H, Gries T, Walenta I, Joulian M and Müssig J (2022) Hemp From Disordered Lines for New Staple Fibre Yarns and High-Performance Composite Applications. Front. Mater. 8:807004. doi: 10.3389/fmats.2021.807004
Received: 01 November 2021; Accepted: 22 December 2021;
Published: 28 January 2022.
Edited by:
Nicholas Fantuzzi, University of Bologna, ItalyReviewed by:
Sanjay Mavinkere Rangappa, King Mongkut’s University of Technology North Bangkok, ThailandCopyright © 2022 Graupner, Weber, Bell, Lehmann, Hilgers, Randerath, Gries, Walenta, Joulian and Müssig. This is an open-access article distributed under the terms of the Creative Commons Attribution License (CC BY). The use, distribution or reproduction in other forums is permitted, provided the original author(s) and the copyright owner(s) are credited and that the original publication in this journal is cited, in accordance with accepted academic practice. No use, distribution or reproduction is permitted which does not comply with these terms.
*Correspondence: Nina Graupner, bmluYS5ncmF1cG5lckBocy1icmVtZW4uZGU=; Jörg Müssig, am11ZXNzaWdAYmlvbmlrLmhzLWJyZW1lbi5kZQ==
Disclaimer: All claims expressed in this article are solely those of the authors and do not necessarily represent those of their affiliated organizations, or those of the publisher, the editors and the reviewers. Any product that may be evaluated in this article or claim that may be made by its manufacturer is not guaranteed or endorsed by the publisher.
Research integrity at Frontiers
Learn more about the work of our research integrity team to safeguard the quality of each article we publish.