- 1School of Mechatronics and Control Engineering, Shenzhen University, Shenzhen, China
- 2Department of Electrical Engineering, Yuan Ze University, Taoyuan, China
Bulk amorphous alloys have some good mechanical properties due to their special atomic arrangement and are now popular in the field of materials. Zr-based amorphous alloys have good mechanical properties, but they are different from lattice slip materials with high ductility. When these materials are compressed and deformed, it generates a concentrated elastic force in the shear zone that causes instantaneous amorphous fracture. The extremely poor plasticity of Zr-based amorphous materials highlight their shortcomings and make them difficult to use in engineering applications. In this paper, it is found that the plasticity of Zr-based amorphous alloys is enhanced to a certain extent by intermittent ultrasonic vibration-assisted compression (IUVC). The ultrasonic vibration stress of IUVC can increase the extra free volume of Zr-based amorphous alloys and increase their degree of “rejuvenation”, which is manifested as an increase in plasticity. To explore how IUVC affects the plasticity of Zr-based amorphous alloys, we design experiments to analyse the effects of different intermittent times, pre-pressures and ultrasonic amplitudes on the plasticity of amorphous alloys.
Introduction
Amorphous alloy materials are called metallic glasses (MGs) because their microstructure is similar to a glass structure. Its high strength, high wear resistance, corrosion resistance and a series of unique properties are derived from this structure (Christopher et al., 2007; Zhang et al., 2016). However, most amorphous alloys exhibit catastrophic defects as structural materials; that is, they lack macroscopic room temperature plastic deformation abilities. To date, various methods have been developed to improve the compressive plasticity and fracture toughness of amorphous alloys at room temperature. In 2000, Johnson’s group first made a breakthrough in amorphous plasticizing (Hays et al., 2000). They improved the ductility of amorphous alloys by introducing a crystalline second phase into the matrix. Ma et al. (2019) proposed the high rheological rate forming (HRRF) method, which improves the energy storage of metal alloys by transferring mechanical work to a metallic supercooled liquid, thereby improving the quasi-static and dynamic compressive plasticity of amorphous alloys. In addition, the compressive plasticity of amorphous alloys can be greatly improved by surface treatment (Zhang et al., 2006) because an internal stress can be formed on the surface after surface spraying, which limits the initiation and expansion of shear bands and thus improves the plasticity. In addition, ultrasonic technology has been used to cut and weld metals and plastics, and alloys can refine grains and improve segregation through ultrasonic vibration to improve their mechanical properties (Gao et al., 2008). Lou et al. (2020) used the ultrasonic vibration precompression (UVPC) method to quickly rejuvenate Zr-based bulk metallic glass (BMG) and to enhance the structural nonuniformity and plasticity of BMG. When energy is injected into metallic glass by ultrasonic vibration, amorphous alloys are rejuvenated because they obtain extra free volume and greater plasticity (Spaepen, 1977).
However, when using ultrasonic vibration compression on BMG, our research team discovered that although the plasticity of compressed amorphous material can improve, the material also very readily crystallizes, even completely. Ultrasonic vibration has an ultrasonic stress effect and an ultrasonic thermal effect that can drive the loosely packed atoms in amorphous alloys to high-energy regions, thereby driving the formation of other regions with free volume and rheological units to improve the forming ability (Chen et al., 2018). The thermal effect of ultrasonic vibration causes the temperature of the amorphous alloy to rise, thereby causing relaxation phenomena to hinder “rejuvenation” and easily form crystalline phases.
Ma et al. (2015) used ultrasonic vibration to stamp BMGs and found that this moulding method can complete thermoplastic moulding in a few seconds and to a large extent avoid time-dependent crystallization and oxidation processes, thereby avoiding traditional heat treatment and the risk of crystallization during the process. Li et al. (2014) conducted uniaxial tensile and compression experiments on Zr-based amorphous alloys under the action of a vibration field and found that as the vibration frequency increases, the free volume content of the amorphous alloy increases, and the flow unit volume is reduced, which leads to a decrease in flow viscosity and an increase in microforming ability. To prevent the relaxation of amorphous alloys, combined with information from previous studies, we decided to adjust the ultrasonic thermal effect by controlling the amplitude and intermittent time in intermittent ultrasonic vibration-assisted compression, thereby effectively improving the mechanical properties of an amorphous alloy. This provides a new way to improve the plasticity of BMGs at room temperature.
Experimental Materials and Methods
Preparation of Test Materials
In the experiment, a Zr-based amorphous alloy with excellent properties—Zr41.2Ti13.8Cu12.5Ni10Be22.5 (Tg = 624 K)—was selected as the experimental material. All the elements are obtained from pure metals with a concentration higher than 99% and then formulated according to the element proportions in Table 1. The vacuum degree reaches 3 × 10–5 MPa or more in the vacuum arc melting furnace, and the master alloy is prepared by melting under the protection of argon gas. The master alloy is repeatedly melted approximately 5 times to ensure the uniform distribution of the elements, and a columnar amorphous alloy with a radius of φ2×70 mm is prepared by suction casting with a water-cooled copper mould.

TABLE 1. Mass fractions in the chemical composition of the Zr41.2Ti13.8Cu12.5Ni10Be22.5 master ingot alloy (wt%).
The test piece is cut into a 3.0 mm long rod shape. To prevent the sample from moving or flying out during the compression process due to the uneven upper and lower surfaces of the sample, it needs to be polished with fine sandpaper and placed in the fixture, and ultimately, a test piece perpendicular to the axis is obtained.
Design of Intermittent Ultrasonic Vibration-Assisted Compression Experiment
The intermittent ultrasound-assisted compression (IUVC) experiment platform is composed of an ultrasonic module, a temperature measurement module and a Zwick Z050 universal material testing machine (ZwickRoell, Berlin, Germany). The ultrasonic module used in this experiment consists of a bracket, an ultrasonic generator, a moving beam, an ultrasonic transducer, an ultrasonic horn and an ultrasonic punch, as shown in Figure 1. The ultrasonic generator converts electrical energy into 20 kHz mechanical vibration, amplifies it to the required amplitude through a horn, and finally transmits the ultrasonic vibration to the amorphous sample for high-frequency periodic impact.
The bracket is fixed on the moving beam of the universal testing machine, and the moving speed can be controlled by a computer. At the same time, the force and displacement sensors record experimental data in real time. An ultrasonic generator is used to achieve the ratio of ultrasonic work and intermittent time, and the holding pressure is set. When the punch presses down and contacts the sample, the pre-pressure is continuously increased to the set value, and then the ultrasonic timer is turned on to apply intermittent ultrasonic action on the amorphous sample. The temperature module is used to collect the temperature rise of the amorphous alloy under the action of intermittent ultrasonic waves. It mainly includes a K-type thermocouple (Herou wire and Cable Co. LTD., Shanghai, China) contacting the side surface of the sample and an acquisition card (NI-9211, National Instruments, Austin, United States) for the real-time recording of temperature fluctuations.
The ultrasonic working time is set to Tw, and the intermittent time is set to Ti. We plan five comparison groups (Table 2); that is, the ratios of ultrasonic working time to intermittent time Tw:Ti are 1:3, 1:2, 1:1, 2:1 and without ultrasonication. The 2:1 ratio is 2 s of ultrasonication, 1 s of intermittent treatment, and so on. Each group of parameters includes five repeat samples.
X-Ray Diffractometer
X-ray diffraction (XRD) is used to detect whether the amorphous material is crystalline and to detect the internal structure changes of each amorphous sample after IUVC treatment. The equipment model is a Bruker D8-AA25 (Bruker, Billerica, United States), the X-ray incident range is set from 20° to 80°, the step length is 0.02°, and the Cu-Ka ray wavelength is λ = 1.5418.
Scanning Electron Microscopy
In this experiment, scanning electron microscopy (SEM, Philips XL30, Philips, Amsterdam, Netherlands) was used to detect the evolution and fracture morphology of the shear band of the samples after IUVC treatment.
Compression Experiment
A universal tensile testing machine (Zwick Z050) is used to compress the Zr-based amorphous alloy at a strain rate of 3 × 10–4 s−1, and a cylindrical specimen with a size of approximately φ2×3 mm is cut from the mother bar and annealed at 560 K for 12 h to eliminate inner stress. The end face of the sample is carefully polished to ensure that the upper and lower surfaces are parallel to each other and perpendicular to the height of the sample.
Results and Analysis
Effect of Ultrasonic Intermittent Time on the Mechanical Properties
From the IUVC experimental results shown in Figure 2A, it can be roughly seen that when Tw:Ti is 1:1, the temperature rises sharply in 1–2 s, and the temperature drops slightly in 2–3 s. It increases under the ultrasonic action and decreases during the intermittent period. This is because the ultrasonic intermittent time is short, the heat has no time to release, and ultrasonication starts to work again, resulting in less released heat than absorbed heat, so the overall temperature rises in the next three ultrasonic working cycles. When Tw:Ti is 1:2, this perception is confirmed. Since the intermittent time is twice the ultrasonic working time, the heat absorption is not as great as that at the 1:1 ratio and is only slightly greater than the heat release. The temperature rises slightly after four cycles. The red dotted line is the temperature change of the amorphous alloy under continuous ultrasonic-assisted compression. The temperature of the IUVC is significantly lower than that of continuous ultrasonic-assisted compression.
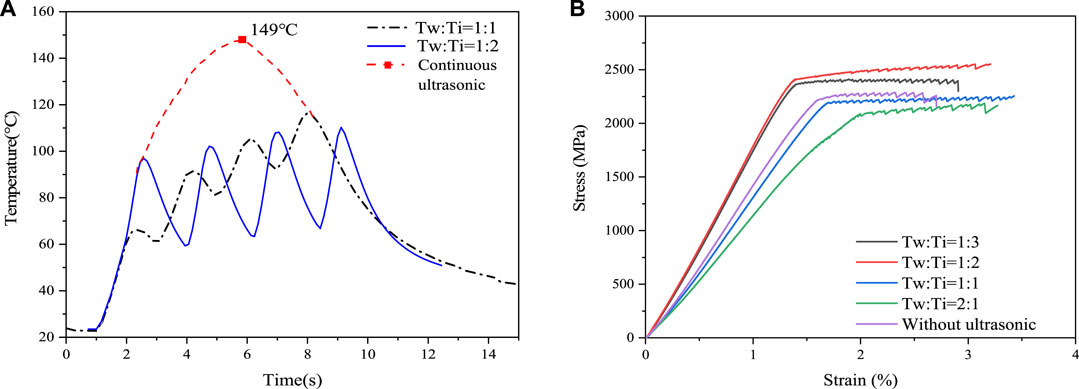
FIGURE 2. IUVC treatment temperature and mechanical curve under different intermittent times: (A) Sample temperature curve during the IUVC process, (B) stress-strain curve of the sample compression test after IUVC treatment.
Figure 2B shows the stress-strain mechanical curve of the amorphous alloy after IUVC treatment with preload Fs = 650 N, ultrasonic amplitude A = 26 μm, and different ultrasonic interval time ratios. The mechanical curve of the amorphous alloy at the yield stage has an obvious “sawtooth” shape, and when the limit value is reached, fracture failure occurs. It can be preliminarily concluded that the intermittent ultrasonic vibration-assisted compression time ratio Tw:Ti has almost no direct relationship with the plasticity and ultimate strength of the Zr matrix. The shorter the intermittent time is, the greater the temperature rise (Figure 2A), and the amount of heat absorbed by the amorphous material and the mechanical properties of the Zr-based amorphous material decrease slightly (Figure 2B). This may be because the glass transition temperature of Zr-based amorphous glass is approximately 340°C, and the temperature rise caused by the ultrasonic heating effect is much lower than this temperature, so its performance has little effect.
Effect of Pre-Pressure on the Mechanical Properties
To explore the effect of pre-pressure on the mechanical properties of amorphous alloys, the ultrasonic amplitude is set to 26 μm, the Tw:Ti is 1:1, and the pre-pressure is changed to conduct IUVC experiments.
From the stress-strain curve in Figure 3A, it can be seen that the as-cast sample has the worst plasticity, and brittle fracture occurs immediately after elastic deformation. The plasticity of the amorphous sample after IUVC treatment increases first and then decreases with increasing pre-pressure and reaches the maximum plasticity when the pre-pressure of Fs is 650 N, which is close to 3.8% compression plasticity. This is because Zr-based amorphous alloys are often brittle at room temperature. The pre-pressure drives the atoms to a higher potential energy during the deformation process under the action of external force, which can increase the free volume content of the amorphous alloy and lead to an increase in plasticity. However, when the pre-pressure reaches 650 N, the energy in the amorphous alloy is high enough to cause the amorphous alloy to begin to precipitate crystals, and as the pre-pressure increases, more crystals are precipitated (see Figure 7 in XRD Pattern Analysis below). At this time, due to the appearance of an ordered crystal lattice arrangement, the free volume content in the amorphous alloy decreases, and the plasticity decreases. In addition, when the yield stage is reached, the stress-strain curves of the Zr-based amorphous materials are all zigzags, indicating that a shear band appears inside the Zr-based amorphous material, and the shear band continues to expand, eventually leading to fracture. In short, pre-pressure can improve the plasticity of amorphous alloys to a certain extent.
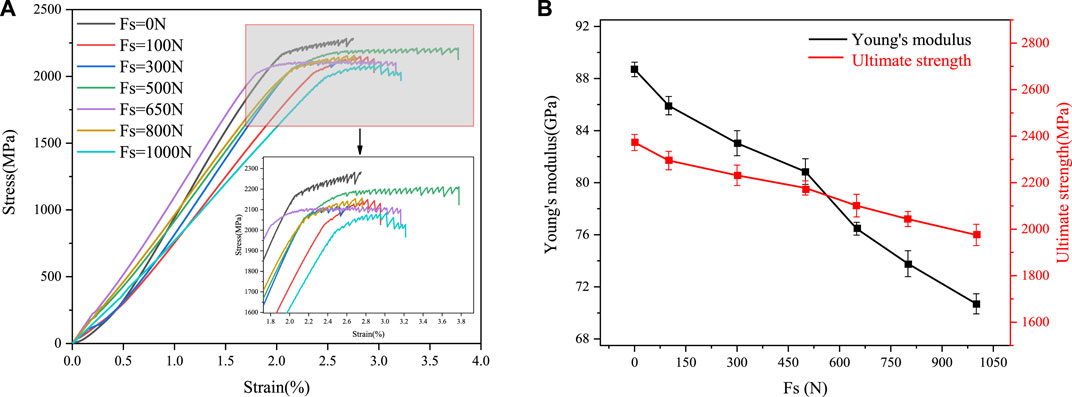
FIGURE 3. Mechanical performance parameters after IUVC treatment with different prepressures: (A) Compressive stress-strain curve of samples after IUVC treatment, (B) Young’s modulus and ultimate strength of the sample after IUVC treatment.
From Figure 3B, it can be seen that the Young’s modulus and ultimate strength of Zr-based amorphous alloys both decrease with increasing pre-pressure. This is because an increase in the pre-pressure increases the temperature and reduces the viscosity of the amorphous alloys, thereby reducing the ultimate strength of the fracture (Wang et al., 2017).
Effect of Amplitude on the Mechanical Properties
To explore the effects of different ultrasonic amplitudes and intermittent ultrasound on the properties of Zr-based amorphous alloys, the ratio of the IUVC working time to intermittent time is set to Tw:Ti = 1:1, and the pre-pressure is 650 N. It can be seen from the test results in Figure 4 that the temperature of the Zr-based amorphous alloy increases with increasing ultrasonic amplitude. The dotted line represents the temperature curve of continuous ultrasonic compression (CUVC). When the ultrasonic amplitude is 26 μm, the highest temperature is 159°C, and when the amplitude is 39 μm, the highest temperature is 264°C, both of which are lower than the crystallization transition temperature of Zr41.2Ti13.8Cu1.5Ni10Be22.5, Tx = 352°C. The solid line is the temperature change curve of intermittent ultrasonic compression. The temperature rise of continuous ultrasonic compression is approximately 50°C higher than that of the IUVC regardless of the amplitude. The atom diffusion distance can be estimated (Faupel et al., 2005) and is so small that any annealing effect caused by temperature rise can be ignored. It can be preliminarily concluded that the transformation and plasticity increase of the amorphous structure by ultrasound is not caused by temperature.
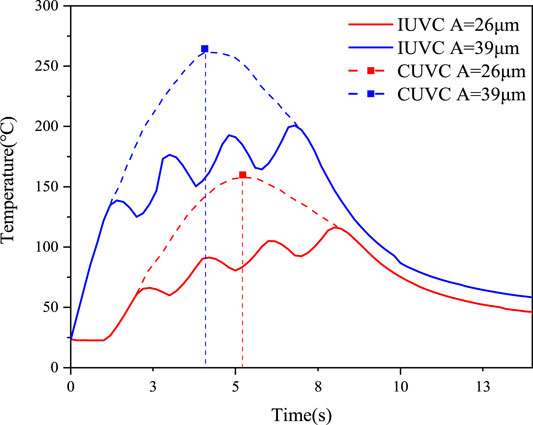
FIGURE 4. Zr41.2Ti13.8Cu12.5Ni10Be22.5 temperature curves under ultrasonic amplitudes of 26 and 39 microns.
Figure 5A shows the stress-strain curves of the IUVC-treated amorphous alloy samples with different ultrasonic amplitudes. With increasing ultrasonic amplitude, the elastic modulus of the IUVC-treated sample is basically the same as that of the as-cast sample. However, their ultimate strength declines slightly. The plasticity increases with increasing ultrasonic amplitude within a certain range, especially when the ultrasonic amplitude reaches 26 μm, and the plasticity is the best, reaching 3.8%. In addition, Figures 5B,C compare the fracture morphologies of the as-cast sample and the sample after IUVC treatment. The surface of the as-cast sample is relatively smooth. There are many shear bands on the surface of the IUVC-treated sample, indicating that the as-cast sample exhibits a typical brittle fracture, while the IUVC-treated sample produces shear bands during the compression process, which is an important factor that causes the plasticity of the IUVC-treated sample to increase.
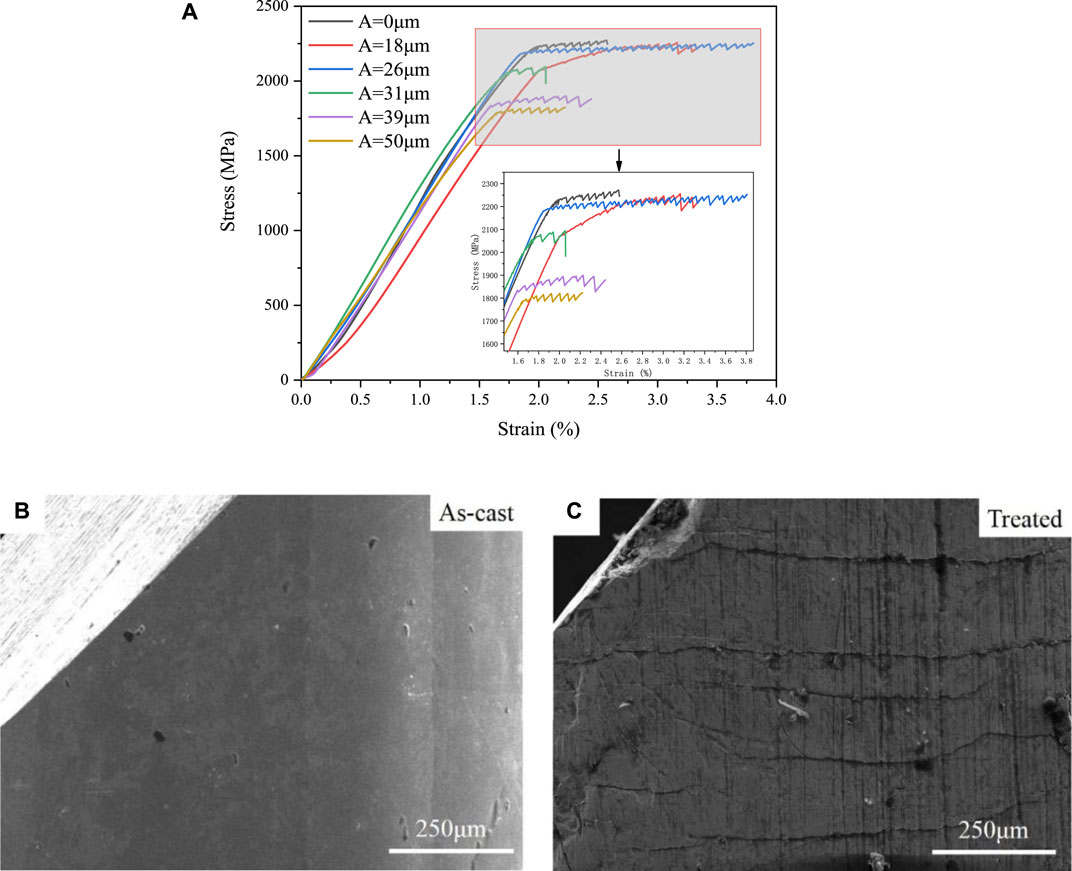
FIGURE 5. Mechanical curves and fracture scanning electron micrographs of IUVC amorphous alloy samples with different ultrasonic amplitudes: (A) compression stress-strain curve of IUVC amorphous samples, (B) outer surface of the compression fracture of the as-cast amorphous sample, (C) outer surface of the compression fracture of the IUVC amorphous sample.
XRD Pattern Analysis
Crystallinity can be used to reflect the integrity of the internal grains of a material. A surface with high crystallinity is arranged regularly, and the diffraction peaks are sharp, complete and symmetrical in the XRD pattern. Based on the above characteristics, the crystallinity of amorphous alloys can be calculated from their X-ray diffraction pattern as:
where WA and WC are the mass percentages of crystalline and amorphous material, IC and IA are the cumulative diffraction intensities of crystalline and amorphous materials, K =
Figure 6 shows the XRD patterns of Zr-based amorphous alloys with different ultrasound intervals. It can be seen that not only the as-cast samples but also all the samples processed by IUVC show broad peaks, indicating that they still remain amorphous. Therefore, changing the ultrasonic interval has no significant effect on the microstructure of the amorphous alloy.
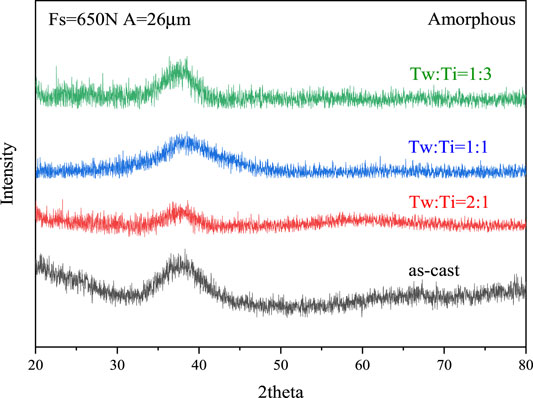
FIGURE 6. XRD analysis results of Zr-based amorphous alloy after Fs = 650 N A = 26 µm IUVC treatment.
Figure 7 shows the XRD patterns of Zr-based amorphous alloys under different pre-pressures. When the pre-pressure is 300 N, the IUVC-treated sample still maintains an amorphous structure. However, when the pre-pressure is increased to 650 N, the Be13Zr crystal phase begins to precipitate. With increasing ultrasonic pre-pressure, the crystallinity increases, and the crystal phases of CuZr2 and BeNi are found to precipitate, indicating that the orderly range of the atomic arrangement inside the IUVC-treated samples is expanded. Observing the crystallization peak of the IUVC-treated samples, we find that the greater the pre-pressure is, the sharper the crystallization peak, indicating that increasing the pre-pressure promotes the crystallization and grain growth of the amorphous alloy. In addition, the crystallization of amorphous alloys is a metastable phase, and a metastable phase changes with changes in stress conditions.
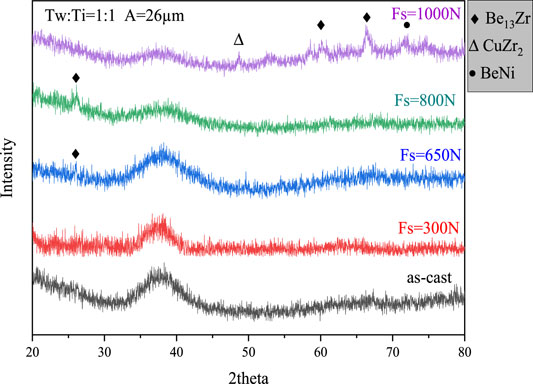
FIGURE 7. XRD analysis results of Zr-based amorphous alloy after Ti:Tc = 1:1 and A = 26 µm IUVC treatment.
Figure 8 shows the XRD patterns of Zr-based amorphous alloys under different ultrasonic amplitudes. With increasing amplitude, the precipitated crystalline phases of the IUVC-treated samples increase. Zr2Cu, Be13Zr and BeNi crystal phases appear (Sun et al., 1996). This shows that an increase in the amplitude promotes the precipitation of crystals in the Zr-based amorphous alloy, thereby changing the internal structure of the amorphous alloy.
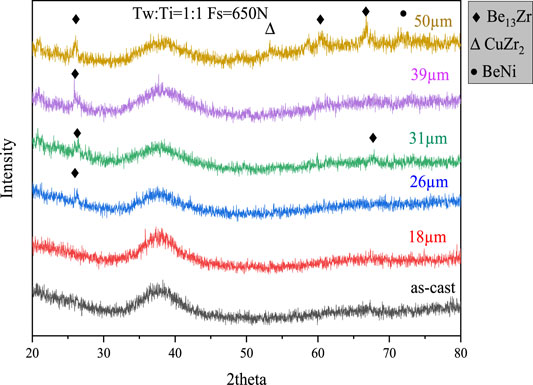
FIGURE 8. XRD analysis results of Zr-based amorphous alloy at Fs = 650 with Ti:Tc = 1:1 IUVC treatment.
Combined with the above experiments, it is known that the ratio of ultrasonic working time to intermittent time has no direct relationship to crystal crystallization, so the single factor variable Tw:Ti is controlled for the experiment. Except for the sample without ultrasonic amplitude and pre-pressure, the other samples are processed under the ratio of ultrasonic working time to intermittent time Tw:Ti = 1:1. Through background removal, smoothing and integral analysis in the software JADE, the crystallinity of IUVC amorphous alloy samples under different pre-pressure and ultrasonic amplitudes is determined, as shown in Figure 9. In the figure, the black solid line represents the crystallinity of each sample under different ultrasonic amplitudes, and the red crossed line represents the crystallinity of each sample under different pre-pressures. When the pre-pressure and amplitude are low, an amorphous phase appears.
Preliminary analysis can be obtained: the precipitated crystals can prevent the nucleation of shear bands and reduce the generation of multiple shear bands due to changes in elastic modulus, thereby improving the plasticity of BMG (Dong et al., 2006). The volume fraction of crystals is also closely related to plasticity. Since crystals are formed in situ and are combined well with the amorphous matrix, effective force transfer occurs between the two phases, with different elastic moduli between the crystals and the amorphous matrix. Therefore, the difference in elastic properties near the amorphous matrix and the crystal more easily introduces stress concentration, and a shear band is more likely to nucleate at the junction (Ohkubo et al., 2007). The initial size of the crystals is small, and the initial shear band is formed, so the deformation is more uniformly distributed instead of localizing in the single shear band BMG, achieving an improvement in plasticity. However, the volume fraction of crystals exceeds the permeation limit, causing the crystals and microstructures to communicate with each other, and the size of the crystals increases sharply, which limits the expansion of the shear band. Such amorphous samples are more prone to fracture and experience a gradual decrease in plasticity.
Conclusion
This paper studies the effect of intermittent ultrasonic vibration-assisted compression treatment on the mechanical properties of Zr41.2Ti13.8Cu12.5Ni10Be22.5 bulk amorphous alloys at room temperature. After summarizing these experimental data, we draw the following:
1) Intermittent ultrasonic vibration-assisted compression can effectively improve the plasticity of Zr41.2Ti13.8Cu12.5Ni10Be22.5. The ultrasonic amplitude and pre-pressure are the main factors that increase the plasticity of Zr-based amorphous alloys. Both the amplitude and the pre-pressure can increase the free volume content and enthalpy of the Zr-based amorphous alloy, thereby increasing the plasticity of the Zr-based amorphous alloy. When the pre-pressure is 650 N and the ultrasonic amplitude is 26 μm, the plasticity is the best, reaching 3.8%.
2) The pre-pressure and ultrasonic amplitude of intermittent ultrasonic vibration-assisted compression promote the precipitation of Zr-based crystals. At the same time, as the pre-pressure and amplitude increase, the crystallinity increases, and the crystals hinder the expansion of the shear band and reduce the plasticity.
3) The ultrasonic intermittent time has no effect on the plasticity and crystallization of Zr-based amorphous alloys.
Data Availability Statement
The original contributions presented in the study are included in the article/Supplementary Material, further inquiries can be directed to the corresponding author.
Author Contributions
Conceptualization, YL and XS; methodology, XS; validation, LY; investigation, XS and LY; data curation, LY; writing—review and editing, YL and LY; supervision, YL. All authors have read and agreed to published version of the manuscript.
Funding
This work was supported financially by the Shenzhen Basic Research General Project (No. JCYJ20190808152409578).
Conflict of Interest
The authors declare that the research was conducted in the absence of any commercial or financial relationships that could be construed as a potential conflict of interest.
Publisher’s Note
All claims expressed in this article are solely those of the authors and do not necessarily represent those of their affiliated organizations, or those of the publisher, the editors and the reviewers. Any product that may be evaluated in this article, or claim that may be made by its manufacturer, is not guaranteed or endorsed by the publisher.
References
Chen, P., Liao, W. B., Liu, L. H., Luo, F., Wu, X. Y., Li, P. J., et al. (2018). Ultrafast Consolidation of Bulk Nanocrystalline Titanium alloy through Ultrasonic Vibration. Sci. Rep. 8 (1), 801. doi:10.1038/s41598-018-19190-8
Christopher, A. S., Todd, C. H., and Ramamurty, U. (2007). Mechanical Behavior of Amorphous Alloys[J]. Acta Materialia 55 (12), 4067–4109.
Dong, W., Zhang, H., and Jing, C. (2006). Enhanced Plasticity in a Zr-Based Bulk Metallic Glass Containing Nanocrystalline Precipitates[J]. J. Alloys Comp. 425 (1-2), L1–L4. doi:10.1016/j.jallcom.2006.01.021
Faupel, F., Frank, W., and Macht, M. P. (2005). Diffusion in Metallic Glasses and Supercooled Melts[J]. MRS Online Proceeding Libr. Archive 644 (1), 237–280.
Gao, D. M., Li, Z. J., Han, Q. Y., and Zhai, Q. J. (2008). Effect of Ultrasonic Power on Microstructure and Mechanical Properties of AZ91 Alloy[J]. Mater. Sci. Eng. A 502 (1), 2–5.
Hays, C. C., Kim, C. P., and Johnson, W. L. (2000). Microstructure Controlled Shear Band Pattern Formation and Enhanced Plasticity of Bulk Metallic Glasses Containingin situFormed Ductile Phase Dendrite Dispersions. Phys. Rev. Lett. 84 (13), 2901–2904. doi:10.1103/physrevlett.84.2901
Li, N., Xu, X., Zheng, Z., and Liu, L. (2014). Enhanced Formability of a Zr-Based Bulk Metallic Glass in a Supercooled Liquid State by Vibrational Loading. Acta Materialia 65, 400–411. doi:10.1016/j.actamat.2013.11.009
Lou, Y., Liu, X., Yang, X., Ge, Y., Zhao, D., Wang, H., et al. (2020). Fast Rejuvenation in Bulk Metallic Glass Induced by Ultrasonic Vibration Precompression. Intermetallics 118 (18), 106687. doi:10.1016/j.intermet.2019.106687
Ma, J., Liang, X., Wu, X., Liu, Z., and Gong, F. (2015). Sub-second Thermoplastic Forming of Bulk Metallic Glasses by Ultrasonic Beating. Sci. Rep. 5, 17844. doi:10.1038/srep17844
Ma, Y.-B., Wang, B.-Z., Zhang, Q.-D., Jiang, Y., Hou, D.-W., Cui, X., et al. (2019). Change Dynamic Behaviors by Heightening its Stored Energy of Monolithic Bulk Metallic Glass. Mater. Des. 181, 107971. doi:10.1016/j.matdes.2019.107971
Ohkubo, T., Nagahama, D., Mukai, T., and Hono, K. (2007). Stress-strain Behaviors of Ti-Based Bulk Metallic Glass and Their Nanostructures. J. Mater. Res. 22 (5), 1406–1413. doi:10.1557/jmr.2007.0180
Spaepen, F. (1977). A Microscopic Mechanism for Steady State Inhomogeneous Flow in Metallic Glasses. Acta Metallurgica 25 (4), 407–415. doi:10.1016/0001-6160(77)90232-2
Sun, X., Schneider, S., Geyer, U., Johnson, W. L., and Nicolet, M.-A. (1996). Oxidation and Crystallization of an Amorphous Zr60Al15Ni25 alloy. J. Mater. Res. 11 (11), 2738–2743. doi:10.1557/jmr.1996.0347
Wang, D. P., Yang, Y., and Niu, X. R. (2017). Resonance Ultrasonic Actuation and Local Structural Rejuvenation in Metallic Glasses[J]. Phys. Rev. B Condensed Matter Materals Phys. 95 (23), 235407.1–235407.5. doi:10.1103/physrevb.95.235407
Zhang, J., Estévez, D., Zhao, Y., Huo, L., Chang, C., Wang, X., et al. (2016). Flexural Strength and Weibull Analysis of Bulk Metallic Glasses[J]. J. Mater. Sci. Tech. 32 (02), 129–133. doi:10.1016/j.jmst.2015.12.016
Keywords: bulk amorphous alloy, intermittent ultrasonic vibration, pre-pressure, free volume, plasticity
Citation: Lingyun Y, Shenpeng X and Yan L (2021) Effect of Intermittent Ultrasonic Vibration-Assisted Compression on the Mechanical Properties of Zr-Based Amorphous Alloys. Front. Mater. 8:801991. doi: 10.3389/fmats.2021.801991
Received: 26 October 2021; Accepted: 24 November 2021;
Published: 17 December 2021.
Edited by:
Huai-Jun Lin, Jinan University, ChinaReviewed by:
Jichao Qiao, Northwestern Polytechnical University, ChinaMeng Zhang, Jinan University, China
Copyright © 2021 Lingyun, Shenpeng and Yan. This is an open-access article distributed under the terms of the Creative Commons Attribution License (CC BY). The use, distribution or reproduction in other forums is permitted, provided the original author(s) and the copyright owner(s) are credited and that the original publication in this journal is cited, in accordance with accepted academic practice. No use, distribution or reproduction is permitted which does not comply with these terms.
*Correspondence: Lou Yan, bG91eWFuQHN6dS5lZHUuY24=