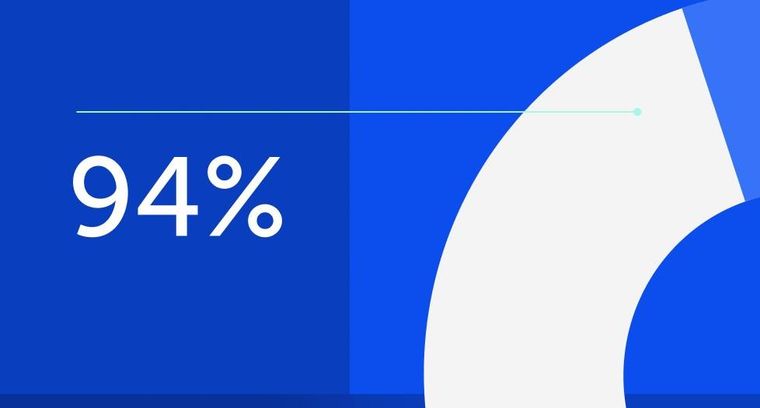
94% of researchers rate our articles as excellent or good
Learn more about the work of our research integrity team to safeguard the quality of each article we publish.
Find out more
REVIEW article
Front. Mater., 12 January 2022
Sec. Smart Materials
Volume 8 - 2021 | https://doi.org/10.3389/fmats.2021.795397
This article is part of the Research TopicHorizons in MaterialsView all 10 articles
Corrosion inhibitors loaded in coatings promote the protection performance of coatings, avoid the local corrosion of metal substrates, and endow the self-healing properties of the coatings. The stimuli-responsive release of corrosion inhibitors, which is generally achieved by loading corrosion inhibitors in containers, is key to the self-healing and long-term protection of the coatings. The loading and release methods of corrosion inhibitors are discussed in the article. First, two kinds of loading methods for corrosion inhibitors are reviewed, which are one-step synthetic methods and multistep synthetic methods. Then the released methods of corrosion inhibitors, which can be achieved by intrinsic properties and surface modification of containers, are summarized.
Organic coatings on metal surfaces physically isolate the metal substrate from the external corrosion environment, which is one of the most widely used measures in metal corrosion prevention (Abdolah et al., 2016; Zhang et al., 2016). However, traditional organic coatings are susceptible to defects and cracks during use, and it is easy to be infiltrated by corrosive media during service. If not repaired in time, the shielding effect of coatings will be significantly reduced, resulting in metal corrosion. Therefore, in order to prolong the service time of coatings and avoid the local corrosion of the metal substrate caused by coating defects, it is necessary to endow coatings with self-healing protection performance when coatings are damaged or corroded. Self-healing coating is an intelligent protective material, which can self-repair the damage generated in the process of use and has become a research hotspot in the coating field in recent years (Cui et al., 2021). Some articles (Abu-Thabit et al., 2016; Zhang et al., 2018), patents (Keeney et al., 2002; Cho et al., 2018), and books (Li and Meng, 2015; et al., Hosseini, 2016) on self-healing coatings have been published. According to the recent view (Zhang et al., 2018), self-healing coatings are classified into autonomous and non-autonomous healing coatings. The self-repair process can be realized by adding corrosion inhibitors to the coatings shown in Figure 1, which is efficient, economical, and convenient, and have become one of the most widely used corrosion protection methods in recent years (Liu et al., 2021).
FIGURE 1. Basic structure and functions of a coating system and major self-healing mechanisms (Zhang et al., 2018).
Adding corrosion inhibitors can obviously inhibit the corrosion electrochemical reaction on the metal surface. However, if corrosion inhibitors are directly added to the coating, they will react with the metal substrate or the material in the coating in advance, so as to prematurely lose the self-healing protection performance and cause adverse effects to coatings (Zhang et al., 2018). The strategy to overcome these drawbacks is encapsulating inhibitors using micro- or nanocontainers (Saji, 2019). Inspired by drug delivery in the medical field, researchers first proposed using nano-/microcapsules to load healing agents and then doped them into coatings. White et al. used capsules to load healing agents (White et al., 2001). When the coating is damaged by external force, the healing agent and catalyst released from ruptured capsules at the mechanical damage caused a cross-linking reaction to repair cracks, and the physical shielding performance of the coating is restored in time. However, in this way, the corrosion inhibitor is released by the mechanical damage of containers, which will result in uncontrollable one-time release of corrosion inhibitors. The self-healing protection performance of coatings will soon disappear and cannot realize long-term service of coatings. In addition, the diameters of microcapsules usually range from dozens of microns to hundreds of microns, and they are not suitable for thin coatings. Also, the weak mechanical properties of microcapsules and incompatibility between microcapsules and matrix destroy the performance of final composites.
The method to overcome this disadvantage is to encapsulate corrosion inhibitors into micro-/nanocontainers, such as mesoporous silica containers (Recloux et al., 2015; Ma et al., 2017; Xu et al., 2018; Wang, et al., 2019; Xiong et al., 2019a), silica nanocapsules (Exbrayat et al., 2019), zeolitic imidazolate framework-8 (ZIF-8) (Xiong et al., 2019b), zeolite (ZEO) (Lv et al., 2021), and layered double hydroxides (LDHs) (Tedim et al., 2016; Alibakhshi et al., 2016). Micro-/nanocontainers have more extensive structure and characteristics. While loading corrosion inhibitors efficiently, it can respond to the external changes in light, heat, pressure, pH, and potential during corrosion occurrence and realize the controllable release of corrosion inhibitors (Shchukin and Moehwald, 2013). Corrosion inhibitors can be released from micro-/nanocontainers only when these internal/external stimuli are triggered. This can prevent corrosion inhibitors from leaking out of coatings and increase the durability of coatings, thereby enhancing the self-healing ability of coatings and preventing corrosion.
Stimuli-responsive self-healing coatings can avoid corrosion inhibitor failure in advance (Zheludkevich et al., 2007) and one-time release leading to loss of self-healing protection performance (White et al., 2001), which is generally achieved by loading corrosion inhibitors in containers, and the critical issue is the loading and release of corrosion inhibitors. In recent works (Crespy et al., 2016; Zhang et al., 2018; Ye K et al., 2020), most of the self-healing coatings are classified according to the type of containers, but the comprehensive investigation of loading and release methods of corrosion inhibitors is rare. Therefore, in this paper, loading and release methods of corrosion inhibitor are reviewed in detail, the main loading and release methods of corrosion inhibitors in this review are shown in Figure 2. In the last section, a prospect with critical issues, aiming to provide insights for the further development of self-healing coatings was proposed.
The loading methods of corrosion inhibitors are generally divided into two types: one-step method and multistep method. The one-step method refers to the completion of container preparation and corrosion inhibitor loading in one step, usually through oil-in-water, the template method, and in situ polymerization. The multistep method refers to the prior preparation of the container and then loading of the corrosion inhibitor (Hu et al., 2011), usually by vacuum adsorption, ion exchange, and layer-by-layer self-assembly. These common loading methods of corrosion inhibitors are shown in Figure 3.
Container preparation and corrosion inhibitor loading are completed in one step. This refers to the direct loading of corrosion inhibitors while preparing containers. In recent years, one-step synthesis of nanocontainers loaded with corrosion inhibitors has attracted attention due to its simple process and economy. The widely used method is oil-in-water microemulsion polymerization. Yi et al. based on the oil-in-water Pickering solution template stabilized by lignin nanoparticles, prepared multilayer composite microcapsules loaded with healing agents and controlled the particle size of microcapsules by changing the lignin content and oil-to-water volume ratio in the Pickering emulsion. When the microcapsules were doped into the epoxy coating, the immersion test showed that the self-healing epoxy coating loaded with microcapsules had good dispersion and a good anticorrosion effect (Yi et al., 2015). However, the particle size obtained by this preparation method is usually at micron level so that the doping may destroy the integrity of the coating and affect its performances. In addition, toxic organic solvents are inevitably used in the preparation of nanocontainers with a diameter less than 150 nm. In this context, it is necessary to study the one-step synthetic method of nanocontainers loaded with corrosion inhibitors for energy conservation and environmental protection.
In various micro-/nanocontainers, mesoporous silica nanoparticles (MSN) have many advantages, such as high stability, large specific surface area, adjustable pore size, and easy surface functionalization, so they are often used as corrosion inhibitors loaded containers in the field of metal corrosion protection. However, traditional methods of loading corrosion inhibitors on MSN include the synthesis of silica template composites, removal of the template by calcination or acid extraction, functionalization of silica nanoparticles, and loading of corrosion inhibitors, which are time-consuming and inefficient. Therefore, it is necessary to develop a simple and effective loading inhibitor method to improve industrial application value. Based on high solubility of organic inhibitors in the template micelle hydrophobic core, Xu et al. prepared the mesoporous silica nanocontainers loaded with corrosion inhibitors by a simple one-step synthetic method, as shown in Figure 4 (Xu et al., 2018). The MSN loaded with benzotriazole (BTA) and cetyltrimethyl ammonium bromide (CTAB) were prepared without additional steps, such as removing templates or loading corrosion inhibitors, which has H+ stimulus-response release characteristics. SVET results show that the coatings doped with these nanocontainers exhibit effective corrosion protection performance. The results show that the one-step synthesis method is simple and efficient, and the whole preparation process does not require organic solvents, compared with the traditional multistep preparation method and the one-step synthesis method with toxic organic solvents in the preparation process. It is energy-saving and environmentally friendly and can be applied to a variety of self-healing coatings.
FIGURE 4. Schematic illustration of MSN loaded with corrosion inhibitors synthesized by traditional multistep method and current one-step methods in this work (Xu et al., 2018).
In addition, in situ polymerization is also one of the common methods for one-step preparation of micro-/nanocontainers loaded with healing agents, which has the advantages of economy and easy operation. White et al. prepared the urea–formaldehyde resin microcapsules loaded with a polymer-based self-healing material dicyclopentadiene by in situ polymerization (White et al., 2001). However, the development of in situ polymerization is limited because the preparation time is usually as long as several hours.
Container preparation and corrosion inhibitor loading are completed by using the multistep synthetic method, which is the most common way to load corrosion inhibitors. After the preparation of micro-/nanocontainers, appropriate methods can be selected according to the properties of containers and corrosion inhibitors. The common corrosion inhibitor loading methods include the vacuum adsorption method, ion exchange method, and layer-by-layer self-assembly technology.
The vacuum adsorption method uses decompression (vacuum) to load corrosion inhibitors. Many corrosion inhibitors loaded into containers, such as mesoporous silica, use this method to load corrosion inhibitors.
MSN can be dispersed in the corrosion inhibitor solution and placed in a low-pressure environment to adsorb corrosion inhibitors. Borisova et al. adsorbed BTA as a corrosion inhibitor after the synthesis of MSN and incorporated into a sol-gel coating to protect aluminum alloy (Borisova et al., 2011). Mechanical stability, high specific surface area (1,000 m2 g−1), and large pore volume (1 ml g−1) of mesoporous silica make its load capacity reach 409 mg BTA/1g SiO2. SVET is used to simulate the corrosion process. It was found that the newly developed self-healing anticorrosive coating had better corrosion protection performance than control sol-gel coatings.
Some micro-/nanocontainers have ion exchange properties, and some corrosion inhibitors are loaded into containers by exchanging with the original ions in the containers. The large specific surface area and porosity of layered silicate materials make it possible to load corrosion inhibitors. Researchers have found that cations (such as Na+) contained in zeolites have cation exchange properties, which can be exchanged with some cation corrosion inhibitors to incorporate corrosion inhibitors into zeolites.
Rassouli et al. embedded Zn2+ into NaX zeolite for corrosion inhibition by ion exchange reaction and doped it into an epoxy coating (Rassouli et al., 2017). Electrochemical tests and surface analysis show that the coating containing NaX zeolite load with corrosion inhibitor Zn2+ has better corrosion protection performance than the control group. This is because in the process of corrosion reaction, the zeolite container releases Zn2+ by ion exchange with Na+ in the corrosive medium and forms zinc hydroxide precipitation in the active area, which leads to a decrease in corrosion rate and thus inhibits corrosion. Wang et al. (2016) obtained Ce-MCM-22 zeolite by loading Ce3+ corrosion inhibitors into it through the cation exchange reaction of MCM-22 zeolite and added it to the epoxy coating on Mg–Li alloy. Scratch test results show that the epoxy coating containing Ce-MCM-22 zeolite has a self-healing function because during the corrosion process of the Mg–Li alloy substrate, Ce3+ is released from MCM-22 zeolite based on the ion exchange of zeolite.
Layer-by-layer self-assembly (LBL) technology, which emerged in the 1990s, is a simple, fast, and green multifunctional surface modification method. The most classical principle is the alternate deposition of polyelectrolyte self-assembly multilayers in polyelectrolyte solutions with opposite charges. Common polyelectrolyte multilayers include negatively charged polystyrene sulfonic acid (PSS) and positively charged polyetherimide (PEI). Due to the electrostatic interaction between layers, the polyelectrolyte layer is sensitive to external stimuli such as pH and light, and the active substance encapsulated between layers can be released slowly. Therefore, the controllable release of corrosion inhibitors can be realized when the corrosion environment changes. In this context, layer-by-layer self-assembly technology is often used in the coating field for corrosion inhibitor loading.
Falcón et al. studied the self-repairing and anti-corrosion effects of nanocontainers coated with dodecylamine on carbon steel (Falcón et al., 2014). Researchers used LBL technology to alternately deposit several polyelectrolyte layers (PEI and PSS) and corrosion inhibitor (dodecylamine) layers on the surface of SiO2 nanoparticles, and the final structure of the obtained nanocontainer is SiO2/PEI/PSS/dodecylamine/PSS/dodecylamine. The corrosion resistance of coatings at different pH (2.0, 6.2, and 9.0) is evaluated by electrochemical impedance spectroscopy (EIS) and scanning vibrating electrode technique (SVET). The results showed that when the coating contained 10 wt% nanocontainer loaded with dodecylamine, the corrosion inhibition effect was best at pH = 2. At the same time, the salt spray test of carbon steel samples coated with prefabricated scratches shows that the coating with nanocontainers has self-healing performance.
Chen et al. developed a SnO2 nanocontainer and deposited polypyrrole (PPy), molybdate corrosion inhibitors, and PDA layers using the LBL assembly technology, as shown in Figure 5 (Chen et al., 2020a). The prepared SnO2 nanocontainer was incorporated into the epoxy coating of stainless steel, which makes the electrochemical tests of the coating show the best anti-corrosion and self-healing properties. The PDA layer can control the on-demand release of the molybdate corrosion inhibitors and reforms the cracked polymer networks using the dopamine functional group and iron oxide to enhance the self-healing ability of the epoxy coatings.
FIGURE 5. Schematic illustration of SnO2-ppy-Inh-PDA (Chen et al., 2020a).
A large number of studies have shown that compared with the direct doping of healing agents in the coating, whether healing agents are encapsulated into microcapsules or hollow fibers, they can have a better effect. This is because the packaging of healing agents can avoid the adverse reaction with coatings. When coating microcracks form and begin to propagate, microcapsules or hollow fibers at the crack are then ruptured, and healing agents flow out to refill the crack area. This method has high packaging efficiency, strong core material protection ability, and fast response to environmental hazards. Figure 6 shows its mechanism.
Inspired by the use of capsule-coated drugs for directional delivery in the medical field, White et al. reported the first generation of self-healing systems based on polymer-based self-healing materials, dicyclopentadiene (DCPD), in 2001 (White et al., 2001), which received a strong response in the field of materials. Since then, microcapsule-based self-healing materials have attracted widespread attention and have begun to be applied in the field of coatings. They dispersed the microcapsules loaded with a liquid DCPD healing agent and powdered Grubbs catalyst in the epoxy substrate. When microcracks appeared in the substrate and began to propagate, the microcapsules at the crack propagation ruptured, resulting in the release of DCPD and Grubbs catalysts, and contacted at the defect, triggering ring-opening complex decomposition polymerization (ROMP), which led to the formation of cross-linked networks and the healing of damaged areas. The self-healing mechanism is shown in Figure 7 (White et al., 2001).
FIGURE 7. Schematic diagram of autonomic healing concept. (A) cracks appeared in the substrate; (B) release of the healing agent loaded in microcapsules ruptured by cracks; and (C) polymerization reaction between the healing agent and the catalyst (White et al., 2001).
In order to optimize the defect that the repair process cannot continue due to the depletion of healing agents in the microcapsule model, researchers inspired by the biological vascular system propose the method of encapsulating healing agents and catalysts with hollow fibers, which opens up a new way for the continuous transportation of healing agents and other active substances to the coating defects. Toohey et al. encapsulated DCPD into a three-dimensional capillary network system and embedded it into the coating (Toohey et al., 2007). When the coating is cracked by mechanical force, the fiber pipeline at the “wound” ruptures, the healing agent and the catalyst flow out, and the curing reaction occurs after contact with the coating damage, thus repairing microcracks. The structure is shown in Figure 8.
FIGURE 8. Structure diagram of self-healing materials with 3D microvascular networks. (A) Dermal capillary network with a cut in the epidermis layer and (B) self-healing structure consisting of a microvascular substrate and an epoxy coating embedded with a catalyst in a four-point bending configuration monitored with an acoustic emission sensor (Toohey et al., 2007).
Since then, based on the packaging technology of healing agents, researchers have continued to study the packaging of different types of healing agents, and explore healing agents that can cross-link and cure without additional catalyst or curing agent. For example, the hydrophobic structure is formed by the combination of methylsilyl ester and water in the corrosive environment. Isocyanates can react with water. Some healing agents that polymerize under the stimulation of visible light can also be loaded into microcapsules or hollow fibers, which was developed inspired by human vascular system, which simplifies the process.
A large number of studies have shown that adding a certain amount of nanocontainers to the coating can fill the original defects in the coating and enhance the physical shielding effect of the coating. At the same time, the corrosion inhibitor loaded in the nanocontainer will slowly release into the coating, enhancing the integrity of the coating and protecting the metal substrate. Figure 9 shows its mechanism.
Since the microcapsule size is usually between tens and hundreds of microns, it cannot be used for thin coating. And part of the cavity formed after the rupture of microcapsules will affect the coating stability. In addition to the natural release methods of corrosion inhibitors flowing out of microcapsules or hollow fibers caused by crack propagation, researchers can also realize the slow release of corrosion inhibitors by directly loading the corrosion inhibitor into nanocontainers and adding it into coatings.
Chen et al. loaded molybdate corrosion inhibitors into TiO2 nanotubes, which can slowly release inhibitors into the natural environment (Chen et al., 2020b). Ye et al. loaded corrosion inhibitors of benzotriazole (BTA) into the porous graphene sheets and then embedded into epoxy coating to form composite coating. The spontaneous release of BTA from the graphene-based nanocontainer makes the coating obtain good corrosion resistance (Ye Y et al., 2020). Borisova et al. studied and evaluated using a simplified coating system. They adsorbed BTA under reduced pressure in MSN without additional modification. And then, they added it to the sol-gel coating and coated it on the surface of aluminum alloy (Borisova et al., 2011). The optical images of the bare aluminum alloy substrate, the substrate coated with sol-gel coating, the substrate coated with a sol-gel coating doped with BTA, and the substrate coated with a sol-gel coating doped with MSN loaded with BTA showed that MSN loaded with BTA in the coating has the best corrosion inhibition effect, while the long-term corrosion resistance of other control groups is low, and there are many defects and corrosion products. This is due to the uniform distribution of MSN in the coating, filling coating defects, and improving its physical barrier properties. At the same time, corrosion inhibitors are loaded into nanocontainers to prevent their early leakage and reaction with the coating substrate. In addition, MSN can release corrosion inhibitors in the coating, which can inhibit corrosion.
Khramov et al. loaded inhibitors of mercaptobenzimidazole (MBI) and mercaptobenzothiazole (MBT) in the hydrophobic cavity of β-cyclodextrin, as shown in Figure 10 (Khramov et al., 2004). The container loaded with corrosion inhibitors is added to the silane film and coated on the aluminum alloy surface. SVET test results show that the coating of β-cyclodextrin containers loaded with corrosion inhibitors has the best corrosion resistance performance compared with the coating without corrosion inhibitors and the coating directly doped with corrosion inhibitors, which could be explained that corrosion inhibitors could be continuously and slowly released from β-cyclodextrin and promote the repair of corrosion defects.
FIGURE 10. Chemical structures of studied organic corrosion inhibitors MBT and MBI, and schematic of the inclusion complexes formation with b-cyclodextrin (Khramov et al., 2004).
Problems such as premature failure of corrosion inhibitors can be avoided by loading healing agents with microcapsules or hollow fibers or loading corrosion inhibitors in nanocontainers and then adding coatings. The corrosion inhibition effect is enhanced compared with directly doping corrosion inhibitors in coatings. However, these release methods of corrosion inhibitors are natural releases, with low corrosion inhibition efficiency and short service life, which cannot meet the growing demand of industry. Therefore, the study on the controlled release methods of corrosion inhibitors has become a hot issue. The main stimuli-responsive release methods are described in detail in this article.
A large number of studies have shown that when nanocontainers loaded with corrosion inhibitors are doped in coatings, the self-performance or surface modification of nanocontainers can be used to perceive the changes in external conditions (such as light, heat, pressure, potential, pH, and other common variables) when corrosion occurs, and finally, the controllable release of corrosion inhibitors is realized. The controlled release of corrosion inhibitors can greatly improve the corrosion inhibition efficiency and prolong the service time of coatings, which plays an important role in the field of corrosion protection. Figure 11 shows the mechanism of the process.
FIGURE 11. Schematic diagram of the self-healing coating based on stimuli-responsive of corrosion inhibitors.
Some containers have ion exchange properties or are sensitive to some metal ions, such as LDH and MOF. The structure of layered double hydroxides (LDHs) (such as hydrotalcite) includes two parts, which are the layered main body with positive electric property and the interlayer ions with negative electric property and neutral electric property. The two parts are connected by hydrogen bonds, so interlayer ions can move freely so as to replace anions in the environment (Serdechnova et al., 2016).
Tedim et al. studied the preparation of LDHs, the load and release of corrosion inhibitors, and their application in corrosion protection (Tedim et al., 2012). They doped Zn–Al LDH intercalated with NO3− into organic polymer coatings as containers to absorb Cl− during corrosion, which can greatly reduce the penetration of corrosive Cl− in coatings. The spectrophotometric results show that the organic anion NO3−in Zn (2)-Al-NO3 LDH is released due to the presence of Cl−. The release of NO3−from LDHs intercalates, and the absorption of Cl− by LDHs reduces the concentration of Cl− in the solution, which is controlled by the ion exchange equilibrium. Compared with the unmodified coating, the modified coating significantly reduced the chloride permeability, which proves the protective effect of LDHs on the coating when corrosion occurs and has a good application prospect in the field of self-healing coatings. The mechanism of LDHs releasing anionic corrosion inhibitors and absorbing corrosive anions in the environment is shown in Figure 12 (Tedim et al., 2010).
FIGURE 12. Mechanism diagram of LDHs in corrosion protection (Tedim et al., 2010). (I) Anion (Cl−) in the solution triggers the release of the inhibitors (Inh−), and (II) LDHs play a double-role, providing inhibitors to protect the metallic substrates and entrapping aggressive species from the environment.
The cage-like pore structure of some layered silicates, such as montmorillonite, kaolinite, and zeolite, is formed by the periodic arrangement of tetrahedra such as SiO44−and AlO45-. The isomorphous replacement of Si4+ and Al3+ makes the main structure negatively charged, so the cation in the pore can be replaced with the cation in the environment.
Thai et al. proposed a new protective coating based on cerium ion corrosion inhibitors for AA2024 corrosion protection (Thai et al., 2020). Cerium cation is inserted into the nanoclay layer by cation exchange reaction to obtain cerium modified montmorillonite (CeMMT). EIS measurement and polarization curves showed that CeMMT had a good corrosion inhibition effect. The corrosion protection performance of AA2024 is improved after the CeMMT is added. Salt spray results of the pre-scratched specimen showed that CeMMT had self-healing performance. UV-Vis spectra showed that the excellent corrosion inhibition performance might be due to the release rate of Ce ions from CeMMT reached 60% in NaCl solution.
When LDHs and some layered silicate containers mentioned earlier have corrosive ions (such as Cl− or metal ions) in the external environment, the embedded corrosion inhibitor reacts with them by ion exchange, which not only absorbs Cl− or metal ions in the corrosive environment but also realizes the release of corrosion inhibitors. In addition, the two-dimensional structure of LDHs and chemical stability of layered silicate containers enhance the physical shielding effect of coatings as the carriers of corrosion inhibitors have been favored by industrial production.
In addition, the metal–organic framework (MOF) material is a new type of porous material with broad prospects. The zeolite imidazole ester framework material (ZIF) is a subclass of the MOF. The structure of ZIF-8 is a tetrahedral unit composed of a Zn2+ and four imidazole anions, and the large internal space can load corrosion inhibitors. The structure of ZIF-8 will decompose or collapse with the change of some external conditions. For example, ZIF-8 decomposes at pH 5.0–6.0 due to the coordination dissociation of Zn2+ and imidazole anions (Zhuang et al., 2014), and ZIF-8 is unstable with divalent and higher valence metal cations. If treated with an Al3+ solution, ZIF-8 will completely collapse (Zhang et al., 2011). The corrosion inhibitor loaded in ZIF-8 also released with its structure’s decomposition or collapse. In this context, the acidic environment and metal cations can stimulate ZIF-8 to achieve the response release of corrosion inhibitors. Yang et al. loaded with BTA into ZIF-8 by a one-step method and modified it with tannic acid, as shown in Figure 13 (Yang et al., 2021). The synthesized pH-responsive hydrophilic stimuli-responsive release system TA@ZIF-8@tannic acid (ZBT) based on ZIF-8 was used for epoxy resin coating. EIS and salt spray tests showed that ZBT could significantly inhibit the corrosion of carbon steel and endow the coating with effective self-healing performance. After 20 d of immersion, the impedance modulus of the ZBT/EP composite coating was about two orders of magnitude higher than that of the blank coating.
FIGURE 13. Schematic illustration of the procedure for the synthesis of ZBT nanomaterials (Yang et al., 2021).
Xiong et al. used ZIF-8 nanoparticles to load corrosion inhibitor salicylaldehyde (SA) and modified GO to obtain SGZ two-dimensional nanocomposites, as shown in Figure 14 (Xiong et al., 2019b). When corrosion occurred, under the stimulation of Al3+ in the environment, the structure of ZIF-8 collapsed, and SA was released and formed an adsorption layer on the surface of the metal substrate, which prevented the corrosion activity. EIS and immersion tests showed that SGZ effectively improved the protective performance of the PVB coating.
FIGURE 14. Synthetic procedure illustration of SZG (Xiong et al., 2019b).
The surface modification of nanocontainers enables some inorganic nanocontainers to combine with some polymer molecular chains with stimulus response characteristics (such as pH, temperature, and light), which can realize the response of containers to external stimuli. At the same time, the grafted molecular chains are expected to enhance the dispersion of inorganic nanocontainers in organic coatings and improve the stability of coatings. Fu et al. used ferrocenyl acid–cucurbituril binary system to modify hollow mesoporous SiO2 microspheres as pH-responsive valves and loaded caffeine molecules, which realized the controlled release under acidic and alkaline conditions (Fu et al., 2013). Adding nanocontainers loaded with corrosion inhibitors to smart nanocontainers implanted into the self-assembled nanophase particles (SNAP) films on the AA2024 surface, it was found that the composite coating had significant physical shielding and self-healing protection properties. Chen et al. reported a light-responsive self-healing coating loaded with BTA and light-responsive molecular switch azobenzene in MSN (Chen et al., 2015). Azobenzene molecules close under visible light but open under ultraviolet light, and corrosion inhibitor molecules released from containers. SVET results show that MSN modified by azobenzene molecular switch has excellent light sensitivity and self-healing properties, which can prolong the corrosion protection effect of aluminum alloy.
Wang et al. successfully synthesized hollow MSN modified by a functional polymer poly-(dimethylaminoethyl methacrylate) (PDMAEMA) to load corrosion inhibitors (Wang et al., 2021). Because of its CO2 response mechanism, it can react with CO2 corrosion in aqueous solution. In the presence of CO2 in aqueous solution, the polymer shell PDMAEMA on the surface of the MSN can change from a hydrophobic state to a hydrophilic state to improve the release rate of corrosion inhibitors. Xiong et al. prepared graphene oxide–mesoporous silica nanocomposites (GS) to load the corrosion inhibitor BTA, and nanogates of the GS container were constructed by aminosilane, as shown in Figure 15 (Xiong et al., 2019a). Aminosilane as a pH-driven “nanogate” inhibits premature leakage of corrosion inhibitors and endows fGS-BTA nanocomposites with stimuli-responsive release characteristics under alkaline conditions. At the same time, aminosilane functionalization significantly enhances its dispersion stability in organic coating. The EIS and scratch tests show that the sol-gel coating filled with fGS-BTA has enhanced barrier performance and self-healing protection performance.
FIGURE 15. Illustration of the synthetic processes for fGS-BTA nanosheets (Xiong et al., 2019b).
In addition to surface grafting of containers, nanocontainers can also be encapsulated with pH-sensitive polyelectrolyte layers or polymer shells (such as polyphenyl acrylate) by LBL technology. The polyelectrolyte layer is coated outside with microcapsules, and corrosion inhibitors are loaded. When pH changes, the electrostatic adsorption between polyelectrolyte layers changes, thus releasing corrosion inhibitors and realizing the stimulation response to pH. Shchukin et al. loaded corrosion inhibitor 2–mercaptobenzothiazole inside halloysite nanotubes, and polypropylene amine, as shown in Figure 16 (Shchukin et al., 2008). When corrosion occurs, the local pH value changes, resulting in the dissociation of polyelectrolyte layers outside nanocontainers and the release of inhibitors, which makes the corrosion area repaired.
FIGURE 16. Schematic illustration of the fabrication of 2-mercaptobenzothiazole-loaded halloysite/polyelectrolyte nanocontainers (Shchukin et al., 2008).
Leal et al. synthesized microcapsules loading flaxseed oil by in situ polymerization and used LBL technology to assemble BTA between polyelectrolyte layer polyetherimide (PEI) and polystyrene sulfonate (PSS) outside microcapsules (Leal et al., 2018). The structure is shown in Figure 17. The system has two stimuli-responsive mechanisms, which are mechanical stimulation (which controls the release of flaxseed oil) and pH-responsive stimulation (which controls the release of BTA). The EIS results show that the epoxy resin doped with 4.8 wt% dual stimuli-responsive microcapsules is more effective in corrosion protection than the control sample, which is related to the release of flaxseed oil by mechanical stimulation (induced defects) and the release of BTA by pH stimulation.
FIGURE 17. Structure diagram of dual-stimulus responsive microcapsules (Leal et al., 2018).
Stimuli-responsive self-healing coatings avoid the one-time release of corrosion inhibitors and the premature failure of self-healing performance, which is generally achieved by loading corrosion inhibitors in containers, and key is the loading and release of corrosion inhibitors.
The adverse reaction between corrosion inhibitors and coatings can also be avoided by loading corrosion inhibitors in micro-/nanocontainers. However, it is found that the micro-/nanocontainers loaded with corrosion inhibitors in coatings may affect the stability of the coating. Therefore, effective loading methods of corrosion inhibitors are important in surface engineering and corrosion protection. The preparation of containers and corrosion inhibitor loading can be completed by a one-step or step-by-step synthetic method. Among them, the loading methods of corrosion inhibitors in micro-/nanocontainers mainly include physical adsorption, ion exchange, and layer-by-layer self-assembly.
Compared with the natural release of corrosion inhibitors from micro-/nanocontainers, the stimuli-responsive release methods increase the inhibition efficiency and service time of coatings, which can be achieved by intrinsic properties or surface modification of containers. For the former, the stimuli-responsive release of corrosion inhibitors is achieved by an ion exchange reaction between corrosion ions and corrosion inhibitors loaded in the containers, or by the collapse of the container structures. For the latter, the stimuli-responsive release of corrosion inhibitors can be achieved by grafting nanocontainers to construct the “nanogate” or by using layer-by-layer self-assembly technology on modified containers.
Self-healing coatings based on the stimuli-responsive release of corrosion inhibitors have potentially broad applications in the future. Although significant progress in the area of self-healing coating has been obtained, many challenges still need to be addressed with a continuous improvement. For example, the efficient encapsulation of these healing agents is critical, since it prolongs the shelf life and endows the coatings with a long-term corrosion inhibition effect. In addition, the containers should be compatible with organic coatings, and their fabrication should be cost-effective for practical applications. Finally, next-generation self-healing coatings will be smarter and multifunctional, for example, the anticorrosion and corrosion sensing. We expect that all these efforts will make a progress in anticorrosion engineering.
YZ made the illustrations and the main analytic and writing work. CC collected the references. MY contributed to the idea and design of the study and participated in the revision of the manuscript with JL and SL. All authors contributed to the article and approved the submitted version.
This work was supported by the Beijing Natural Science Foundation (Grant No. 2172032).
The authors declare that the research was conducted in the absence of any commercial or financial relationships that could be construed as a potential conflict of interest.
All claims expressed in this article are solely those of the authors and do not necessarily represent those of their affiliated organizations, or those of the publisher, the editors, and the reviewers. Any product that may be evaluated in this article, or claim that may be made by its manufacturer, is not guaranteed or endorsed by the publisher.
Abdolah Zadeh, M., van der Zwaag, S., and Garcia, S. J. (2016). Adhesion and Long-Term Barrier Restoration of Intrinsic Self-Healing Hybrid Sol-Gel Coatings. ACS Appl. Mater. Inter. 8, 4126–4136. doi:10.1021/acsami.5b11867
Abu-Thabit, N. Y., and Hamdy, A. S. (2016). Stimuli-Responsive Polyelectrolyte Multilayers for Fabrication of Self-Healing Coatings - A Review. Surf. Coat. Technology. 303, 406–424. doi:10.1016/j.surfcoat.2015.11.020
Alibakhshi, E., Ghasemi, E., Mahdavian, M., and Ramezanzadeh, B. (2017). A Comparative Study on Corrosion Inhibitive Effect of Nitrate and Phosphate Intercalated Zn-Al- Layered Double Hydroxides (LDHs) Nanocontainers Incorporated into a Hybrid Silane Layer and Their Effect on Cathodic Delamination of Epoxy Topcoat. Corrosion Sci. 115, 159–174. doi:10.1016/j.corsci.2016.12.001
Borisova, D., Möhwald, H., and Shchukin, D. G. (2011). Mesoporous Silica Nanoparticles for Active Corrosion Protection. Acs. Nano. 5 (3), 1939–1946. doi:10.1021/nn102871v
Chen, T., Chen, R., Jin, Z., and Liu, J. (2015). Engineering Hollow Mesoporous Silica Nanocontainers with Molecular Switches for Continuous Self-Healing Anticorrosion Coating. J. Mater. Chem. A. 3 (18), 9510–9516. doi:10.1039/c5ta01188d
Chen, Z., Yang, W., Chen, Y., Yin, X., and Liu, Y. (2020a). Smart Coatings Embedded With Polydopamine-Decorated Layer-By-Layer Assembled SnO2 Nanocontainers for the Corrosion Protection of 304 Stainless Steels. J. Colloid Interf. Sci. 579, 741–753. doi:10.1016/j.jcis.2020.06.118
Chen, Z., Yang, W., Yin, X., Chen, Y., Liu, Y., and Xu, B. (2020b). Corrosion Protection of 304 Stainless Steel From a Smart Conducting Polypyrrole Coating Doped with pH-Sensitive Molybdate-Loaded TiO2 Nanocontainers. Prog. Org. Coat. 146, 105750. doi:10.1016/j.porgcoat.2020.105750
Cho, C., Kovalev, M., Sakai, N., and Kim, M. (2018). Anti-Fingerpringing Compositon With Self- Healing Property, Film, Laminate, and Device. U.S. Patent Application No. 15/889,607. Washington, D.C.: U.S. Patent and Trademark Office.
Crespy, D., Landfester, K., Fickert, J., and Rohwerder, M. (2016). Self-Healing for Anticorrosion Based on Encapsulated Healing Agents. Adv. Polym. Sci. 273, 219–245. doi:10.1007/12_2015_342
Cui, M., Njoku, D. I., Li, B., Yang, L., Wang, Z., Hou, B., et al. (2021). Corrosion Protection of Aluminium Alloy 2024 Through an Epoxy Coating Embedded With Smart Microcapsules: The Responses of Smart Microcapsules to Corrosive Entities. Corrosion Commun. 1, 1–9. doi:10.1016/j.corcom.2021.06.001
Exbrayat, L., Salaluk, S., Uebel, M., Jenjob, R., Rameau, B., Koynov, K., et al. (2019). Nanosensors for Monitoring Early Stages of Metallic Corrosion. ACS Appl. Nano Mater. 2 (2), 812–818. doi:10.1021/acsanm.8b02045
Falcón, J. M., Batista, F. F., and Aoki, I. V. (2014). Encapsulation of Dodecylamine Corrosion Inhibitor on Silica Nanoparticles. Electrochim. Acta. 124, 109–118. doi:10.1016/j.electacta.2013.06.114
Fu, J., Chen, T., Wang, M., Yang, N., Li, S., Wang, Y., et al. (2013). Acid and Alkaline Dual Stimuli-Responsive Mechanized Hollow Mesoporous Silica Nanoparticles as Smart Nanocontainers for Intelligent Anticorrosion Coatings. Acs Nano. 7 (12), 11397–11408. doi:10.1021/nn4053233
Hosseini, M. (2016). Industrial Applications for Intelligent Polymers and Coatings. Switzerland: Springer International Publishing.
Hu, J., Wang, J., Zhang, J., and Cao, C. (2011). Corrosion of a Metal Surface Loading Methods and Uses. CN, CN102268709 B. China: Intellectual Property Publishing House.
Keeney, C., Clements, M., Hawkins, J., Yollick, S., and Fader, J. (2002). Encapsulated Anti-Corrosion Coating. Washington: U.S. Patent No 6,090,051. US6420052 B1.
Khramov, A. N., Voevodin, N. N., Balbyshev, V. N., and Donley, M. S. (2004). Hybrid Organo-Ceramic Corrosion Protection Coatings With Encapsulated Organic Corrosion Inhibitors. Thin Solid Films. 447-448, 549–557. doi:10.1016/j.tsf.2003.07.016
Leal, D. A., Riegel-Vidotti, I. C., Ferreira, M. G. S., and Marino, C. E. B. (2018). Smart Coating Based on Double Stimuli-Responsive Microcapsules Containing Linseed Oil and Benzotriazole for Active Corrosion protection. Corrosion Sci. 130, 56–63. doi:10.1016/j.corsci.2017.10.009
Li, G., and Meng, H. (2015). Recent Advances in Smart Self-Healing Polymers and Composites. United Kingdom: Woodhead Publishing.
Liu, T., Ma, L., Wang, X., Wang, J., Qian, H., Zhang, D., et al. (2021). Self-Healing Corrosion Protective Coatings Based on Micro/Nanocarriers: a Review. Corrosion. Commun. 1, 18–25. doi:10.1016/j.corcom.2021.05.004
Lv, J., Yue, Q.-X., Ding, R., Han, Q., Liu, X., Liu, J.-L., et al. (2021). Construction of Zeolite-Loaded Fluorescent Supramolecular On-Off Probes for Corrosion Detection Based on a Cation Exchange Mechanism. Nanomaterials. 11 (1), 169. doi:10.3390/nano11010169
Ma, X., Xu, L., Wang, W., Lin, Z., and Li, X. (2017). Synthesis and Characterisation of Composite Nanoparticles of Mesoporous Silica Loaded With Inhibitor for Corrosion Protection of Cu-Zn alloy. Corrosion Sci. 120, 139–147. doi:10.1016/j.corsci.2017.02.004
Rassouli, L., Naderi, R., and Mahdavain, M. (2017). The Role of Micro/Nano Zeolites Doped with Zinc Cations in the Active protection of Epoxy Ester Coating. Appl. Surf. Sci. 423, 571–583. doi:10.1016/j.apsusc.2017.06.245
Recloux, I., Mouanga, M., Druart, M.-E., Paint, Y., and Olivier, M.-G. (2015). Silica Mesoporous Thin Films as Containers for Benzotriazole for Corrosion protection of 2024 Aluminium Alloys. Appl. Surf. Sci. 346, 124–133. doi:10.1016/j.apsusc.2015.03.191
Saji, V. S. (2019). Supramolecular Concepts and Approaches in Corrosion and Biofouling Prevention. Corros. Revc. 37 (3), 187–230. doi:10.1515/corrrev-2018-0105
Serdechnova, M., Salak, A. N., Barbosa, F. S., Vieira, D. E. L., Tedim, J., Zheludkevich, M. L., et al. (2016). Interlayer Intercalation and Arrangement of 2-Mercaptobenzothiazolate and 1,2,3-Benzotriazolate Anions in Layered Double Hydroxides: In Situ X-ray Diffraction Study. J. Solid State Chem. 233, 158–165. doi:10.1016/j.jssc.2015.10.023
Shchukin, D. G., Lamaka, S. V., Yasakau, K. A., Zheludkevich, M. L., Ferreira, M. G. S., and Möhwald, H. (2008). Active Anticorrosion Coatings With Halloysite Nanocontainers. J. Phys. Chem. C. 112 (4), 958–964. doi:10.1021/jp076188r
Shchukin, D., and Möhwald, H. (2013). A Coat of Many Functions. Science. 341 (6153), 1458–1459. doi:10.1126/science.1242895
Tedim, J., Bastos, A. C., Kallip, S., Zheludkevich, M. L., and Ferreira, M. G. S. (2016). Corrosion Protection of AA2024-T3 by LDH Conversion Films. Analysis of SVET Results. Electrochimica Acta. 210, 215–224. doi:10.1016/j.electacta.2016.05.134
Tedim, J., Kuznetsova, A., Salak, A. N., Montemor, F., Snihirova, D., Pilz, M., et al. (2012). Zn-Al Layered Double Hydroxides as Chloride Nanotraps in Active Protective Coatings. Corrosion Sci. 55, 1–4. doi:10.1016/j.corsci.2011.10.003
Tedim, J., Poznyak, S. K., Kuznetsova, A., Raps, D., Hack, T., Zheludkevich, M. L., et al. (2010). Enhancement of Active Corrosion Protection via Combination of Inhibitor-Loaded Nanocontainers. ACS Appl. Mater. Inter. 2 (5), 1528–1535. doi:10.1021/am100174t
Thai, T. T., Trinh, A. T., and Olivier, M. G. (2020). Hybrid Sol-Gel Coatings Doped with Cerium Nanocontainers for Active Corrosion Protection of AA2024. Prog. Org. Coat. 138, 105428. doi:10.1016/j.porgcoat.2019.105428
Toohey, K. S., Sottos, N. R., Lewis, J. A., Moore, J. S., and White, S. R. (2007). Self-Healing Materials With Microvascular Networks. Nat. Mater. 6 (8), 581–585. doi:10.1038/nmat1934
Wang, J., Tang, J., Zhang, H., Wang, Y., Wang, H., and Lin, B. (2021). A CO2-Responsive Anti-Corrosion Ethyl Cellulose Coating Based on the pH-Response Mechanism. Corros Sci. 180, 109194. doi:10.1016/j.corsci.2020.109194
Wang, W., Wang, H., Zhao, J., Wang, X., Xiong, C., Song, L., et al. (2019). Self-Healing Performance and Corrosion Resistance of Graphene Oxide-Mesoporous Silicon Layer-Nanosphere Structure Coating Under Marine Alternating Hydrostatic Pressure. Chem. Eng. J. 361, 792–804. doi:10.1016/j.cej.2018.12.124
Wang, Y., Zhu, Y., Li, C., Song, D., Zhang, T., Zheng, X., et al. (2016). Smart Epoxy Coating Containing Ce-MCM-22 Zeolites for Corrosion Protection of Mg-Li Alloy. Appl. Surf. Sci. 369, 384–389. doi:10.1016/j.apsusc.2016.02.102
White, S. R., Sottos, N. R., Geubelle, P. H., Moore, J. S., Kessler, M. R., Sriram, S. R., et al. (2001). Autonomic Healing of Polymer Composites. Nature. 409, 794–797. doi:10.1038/35057232
Xiong, L., Liu, J., Li, Y., Li, S., and Yu, M. (2019a). Enhancing Corrosion protection Properties of Sol-Gel Coating by pH-Responsive Amino-Silane Functionalized Graphene Oxide-Mesoporous Silica Nanosheets. Prog. Org. Coat. 135, 228–239. doi:10.1016/j.porgcoat.2019.06.007
Xiong, L., Liu, J., Yu, M., and Li, S. (2019b). Improving the Corrosion protection Properties of Pvb Coating by Using Salicylaldehyde@zif-8/graphene Oxide Two-Dimensional Nanocomposites. Corrosion Sci. 146, 70–79. doi:10.1016/j.corsci.2018.10.016
Xu, J.-B., Cao, Y.-Q., Fang, L., and Hu, J.-M. (2018). A One-Step Preparation of Inhibitor-Loaded Silica Nanocontainers for Self-Healing Coatings. Corrosion Sci. 140, 349–362. doi:10.1016/j.corsci.2018.05.030
Yang, C., Xu, W. J., Meng, X., Shi, X. L., Shao, L. H., Zeng, X. L., et al. (2021). A pH-Responsive Hydrophilic Controlled Release System Based on Zif-8 for Self-Healing Anticorrosion Application. Che. Eng. J. 415, 128985. doi:10.1016/j.cej.2021.128985
Ye, K., Bi, Z., Cui, G., Zhang, B., and Li, Z. (2020). External Self-Healing Coatings in Anticorrosion Applications: A Review. Corrosion 76 (3), 279–298. doi:10.5006/3430
Ye, Y., Chen, H., Zou, Y., Ye, Y., and Zhao, H. (2020). Corrosion Protective Mechanism of Smart Graphene-Based Self-Healing Coating on Carbon Steel. Corrosion Sci. 174, 108825. doi:10.1016/j.corsci.2020.108825
Yi, H., Yang, Y., Gu, X., Huang, J., and Wang, C. (2015). Multilayer Composite Microcapsules Synthesized by Pickering Emulsion Templates and Their Application in Self-Healing Coating.J. Mater. Chem. A. 3 (26), 13749–13757. doi:10.1039/c5ta02288f
Zhang, D., Qian, H., Wang, L., and Li, X. (2016). Comparison of Barrier Properties for a Superhydrophobic Epoxy Coating Under Different Simulated Corrosion Environments. Corrosion Sci. 103, 230–241. doi:10.1016/j.corsci.2015.11.023
Zhang, F., Ju, P., Pan, M., Zhang, D., Huang, Y., Li, G., et al. (2018). Self-Healing Mechanisms in Smart Protective Coatings: a Review. Corrosion Sci. 144, 74–88. doi:10.1016/j.corsci.2018.08.005
Zhang, L., and Hu, Y. H. (2011). Strong Effects of Higher-Valent Cations on the Structure of the Zeolitic Zn(2-Methylimidazole)2 Framework (ZIF-8). J. Phys. Chem. C. 115 (16), 7967–7971. doi:10.1021/jp200699n
Zheludkevich, M. L., Shchukin, D. G., Yasakau, K. A., Möhwald, H., and Ferreira, M. G. S. (2007). Anticorrosion Coatings With Self-Healing Effect Based on Nanocontainers Impregnated with Corrosion Inhibitor. Chem. Mater. 19 (3), 402–411. doi:10.1021/cm062066k
Keywords: self-healing coatings, corrosion inhibitors, containers, loading methods, stimuli-responsive release
Citation: Zhang Y, Yu M, Chen C, Li S and Liu J (2022) Self-Healing Coatings Based on Stimuli-Responsive Release of Corrosion Inhibitors: A Review. Front. Mater. 8:795397. doi: 10.3389/fmats.2021.795397
Received: 15 October 2021; Accepted: 15 December 2021;
Published: 12 January 2022.
Edited by:
Jinglei Yang, Hong Kong University of Science and Technology, Hong Kong SAR, ChinaReviewed by:
Viswanathan S. Saji, King Fahd University of Petroleum and Minerals (KFUPM), Saudi ArabiaCopyright © 2022 Zhang, Yu, Chen, Li and Liu. This is an open-access article distributed under the terms of the Creative Commons Attribution License (CC BY). The use, distribution or reproduction in other forums is permitted, provided the original author(s) and the copyright owner(s) are credited and that the original publication in this journal is cited, in accordance with accepted academic practice. No use, distribution or reproduction is permitted which does not comply with these terms.
*Correspondence: Mei Yu, eXVtZWlAYnVhYS5lZHUuY24=
Disclaimer: All claims expressed in this article are solely those of the authors and do not necessarily represent those of their affiliated organizations, or those of the publisher, the editors and the reviewers. Any product that may be evaluated in this article or claim that may be made by its manufacturer is not guaranteed or endorsed by the publisher.
Research integrity at Frontiers
Learn more about the work of our research integrity team to safeguard the quality of each article we publish.