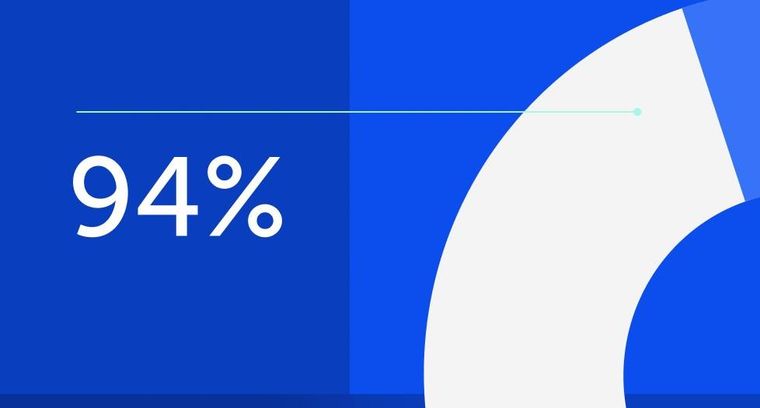
94% of researchers rate our articles as excellent or good
Learn more about the work of our research integrity team to safeguard the quality of each article we publish.
Find out more
ORIGINAL RESEARCH article
Front. Mater., 03 January 2022
Sec. Structural Materials
Volume 8 - 2021 | https://doi.org/10.3389/fmats.2021.792714
This article is part of the Research TopicFluxes and Steel QualityView all 5 articles
A thermodynamic model for seven CaO-MgO-BaO-CaF2-SiO2-Al2O3-TiO2 ladle slags based on the Ion and Molecule Coexistence theory (IMCT) is establishment and validated by the experiment results at 1873K. The calculated activity of SiO2, Al2O3 and TiO2 in the slag can be approved by the experiment results and the IMCT model used in this study is reasonable. Then the influence factors such as the mass ratio of CaO to SiO2 (C/S ratio) ranging from 1 to 10, the mass ratio of CaO to Al2O3 (C/A ratio) ranging from 1 to 2.5, TiO2 content (wt pct) ranging from 0 to 30, BaO content (wt pct) ranging from 0 to 30 are investigated based on the thermodynamic calculating results. The raise of C/S ratio, TiO2 content and BaO content in the slag can increase the molar Gibbs energy change (ΔG) of Ti reacted with SiO2 and Al2O3 or Al reacted with SiO2. The effect of C/A ratio on the molar Gibbs energy change (ΔG) of Ti reacted with SiO2 and Al2O3 or Al reacted with SiO2 was less. Finally, the slag with higher C/S ratio and TiO2 content and appropriate BaO content can weaken the reaction between Ti and SiO2 or Al2O3 in the slag.
TiC and TiN inclusion can be formed in the Ti bearing steel in the solidification process (Cavazos et al., 2011; Leban and Tisu, 2013), which can increase the strength of the final products, as the steel’s secondary phase (Huang et al., 2018). During the initial solidification period, the heterogeneous nucleation of delta ferrite could formed on the TiN inclusions and then the equiaxed fine-grained structure was generated (Fujimura et al., 2001). For this reason, the addition of titanium to the liquid steel in the ladle for improving properties has increased in recent years. Nevertheless the loss of Ti will persist in the ladle metallurgy process, mainly oxidized by the slag. Then the formed TiOx in the steel would reacted with Mg, Ca or Al2O3 in the steel and the complex inclusions such as MgAl2O4 spinal and MgO-TiOx spinal, surrounded by TiN and perovskite are formed. This would lead to the clogging of submerged nozzle and forming of surface defects on the steel products (Maddalena et al., 2000; Nunnington and Sutcliffe, 2001; Zheng et al., 2004). Thus, in order to obtain an optimal slag composition for the ladle refining of Al-killed and Ti bearing steel, it is important to investigate the reaction between slag and molten steel.
Kim et al. (1993) found that the SiO2 in the slag could oxidize the Titanium in the liquid steel. Park et al. (2004) also found that Aluminum and Titanium could be simultaneously oxidized by the SiO2 in the 14%CaO-35%Al2O3-10%MgO-%4SiO2 slag and the soluble oxygen was supersaturated during the course, particularly with respect to Al. Then the re-oxidation mechanism of Al and Ti in the liquid steel by SiO2 was depicted in Figure 1. It can be seen from Figure 1, the oxidation process of Al or Ti mainly include two ways, on the one hand, the Al or Ti in the metal reacted with the SiO2 in the slag directly; on the other hand, the SiO2 in the slag decomposed of Si and O, then they transferred to the liquid steel and oxidized the Al and Ti in the liquid steel. Park et al. (2009) also investigate the thermodynamic behavior of TiOx in the refining slag (CaO-SiO2-MgO-Al2O3-TiOx
-CaF2) equilibrated with Fe-11%Cr melts. They found that the equilibrium between silicon and titanium in steel melts and their oxides in the slags are theoretically expected and experimentally proved well. They also calculated the relationship between Aluminum and Titanium in the steel melts and their oxides in the slag. The slope of the line is 0.5, which is lower than 1. Therefore, they summarized that the activity coefficient of TiOx in the slag would be affected in the composition range investigated in their study. They also found that with the increase of (%SiO2)/(%SiO2+%Al2O3) in the slag, the activity coefficient of TiO2 gradually decreased. The attraction between TiO2 and SiO2 is greater than that between TiO2 and Al2O3 in the present slag system due to the electronegativity difference between each cation involved. The activity of TiO2 in the slag system containing 10% MgO shows a negative deviation from an ideality, while that in the CaO-SiO2-Al2O3-MgOsatd-CaF2 system is really close to the ideal behavior up to about
Qian et al. (2014) found that when the TiO2 content in the slag reached to 8%, the oxidation of Ti in the Ti-stabilized stainless steel was minimum and the T. O (Total O in the steel) was constant with the time increase. They also found the influence of TiO2 adding to the slag on the oxidation rate change of Al has an opposite tendency compared with Ti. The activity change behavior of TiO2 in different TiO2 content slag, calculated by IMCT model, are in good agreement of the experiment results. Li and Cheng (2019) investigated the effect of the CaF2 contents in the CaO-SiO2- MgO-Al2O3-TiO2-CaF2 slag on the formation of inclusion in Ti-Stabilized 20Cr Stainless Steel. They found that with the increase of CaF2 content in the slag, the equilibrium content of Ti and Mg in the steel increased. When the CaF2 content in the slag changed from 0 to 9.57, the equilibrium content of Ti changed from 0.018 to 0.031% and the equilibrium content of Mg changed from 12ppm to 23ppm. Due to the increase of CaF2 content in the slag can decrease the
According to the previous researches (Qian et al., 2014; Jiang et al., 2016; Li and Cheng, 2019), The IMCT model has been applied in CaO-SiO2-MgO-Al2O3-TiO2-CaF2 slag system successfully for Ti-bearing stainless steel and 825 alloy refining process. However, the CaO-SiO2-MgO-Al2O3-TiO2-CaF2-BaO slag for low alloy high Ti-bearing steel refining, has never been explored. Due to the adding of BaO in the ladle slag has a excellently ability for desulphurization (Gao et al., 2012), Therefore this study is mainly focused on the investigation of the reactive between CaO-SiO2-MgO-Al2O3-TiO2-CaF2-BaO slag and 0.361% Ti bearing steel (0.0361%Al) by use the thermodynamic model (IMCT model), which is needed to be approved by the experiment results.
The composition of Al-killed and Ti-bearing steel used in this study was listed in Table 1. During the ladle metallurgy process, the reactions (1–3) between the liquid steel and slag would lead to the loss of Ti and Al in the steel (Qian et al., 2014; Li and Cheng, 2019). The slag composition assigned for this paper’s discussion section is shown in Table 2.
From Eqs. 1–12,
TABLE 3. Interaction parameters used in this paper (Hino, 2009).
In addition,
According to the IMCT hypotheses proposed by literature (Zaitsev et al., 1990; Li and Zhang, 2000; Zhang, 2004; Zhang, 2007; Yang et al., 2009) and phase diagrams (Eisenhüttenleute, 1995; Shukla, 2012; Boulay et al., 2014), there are 4 simple cation-anion couples, 3 simple molecules and 51 complex molecules in this model at 1800–1935K, as shown in Table 4. The mole fraction of theses studied slag’s components is assigned as a1 =
TABLE 4. The kinds of structural units in this model, and their definition mole number and mass action concentration.
TABLE 5. The chemical reaction formulas of complex molecular in this model, and their Standard Molar Gibbs Free Energy Changes and Mass Action Concentrations of complex molecules expressed by Ki.
According to the definition of mass action concentration and mass conservation, Eq. 15–22 can be obtained, which could be solved with Matlab.
According to Eq. 8 and Eq. 12, the dependence of the activity ratio of steel on the activity ratio of slag at different experiment heats, which includes JY. Li’s (Li and Cheng, 2019), ZH. Jian’s (Jiang et al., 2016),J.Park’s (Park et al., 2008) and this author’s experiment data, are shown in Figure 2. The activity of SiO2, Al2O3 and TiO2 in the slag are calculated by the IMCT model according to the final slag composition and the activity of Si, Al and Ti in the steel calculated by Eq. 13 and Eq. 14 according to the final steel composition, at different experiment heats. The magenta lines in this Figure are derived From Eq. 8 and Eq. 12. And we can find that the activity of the slag calculated by IMCT Model are approved by the experiments.
FIGURE 2. The relationship between the activity ratio of steel and the activity ratio of slag in the experiment.
The data of blue sphere is calculated by using this author’s experiment results as shown in Table 6 and the experiment method is described in Table 7. The CaO-MgO-BaO-CaF2-SiO2-Al2 O3-TiO2 slags before reacting with steel were pre-melted in a carbon crucible and the composition was shown in Table 8, which are marked as No.1∼No.13. The steel sample A, described in Table 1, and the pre-melted CaO-MgO-BaO-CaF2-SiO2-Al2O3-TiO2 slags were equilibrated in MgO crucible by using resistance furnace under Ar atmosphere for 1 h.
The detailed process of slag/metal experiment can be described as follows. At first, 400 g steel were placed in a MgO crucible. Then, the slag/metal reaction chamber was filled by Ar gas and followed by resistance heating. After temperature reached 1873K, the initial steel sample was taken by quartz tube and then 32 g pre-melted slag was added. After the slag was melted at 1873K for 60 min, steel sample and slag sample were taken out. During the metal-slag reacting process, the steel sample were taken at 5, 20 and 40min after slag melting completely. The contents of silicon, soluble aluminum, titanium in steel samples were measured by the inductively coupled plasma optical emission spectrometry (ICP-OES) with ±5% relative standard deviation. The compositions of slag samples were measured by an X-ray fluorescence spectrometer. During the metal-slag reacting process, the composition change behavior of the silicon in the steel was shown in Figure 3. From Figure 3, the experiment equilibrium state has realized.
In addition, the activity of SiO2, Al2O3 and TiO2 in 2–5 dimensional slag from the literature (Gzieo and Jowsa, 1984; Nomura et al., 1991; Hino, 1994; Kishi et al., 1994; Ohta and Suito, 1994; Ohta and Suito, 1998a; Ohta and Suito, 1998b; Moeizane et al., 1999; Jung and Fruehan, 2001; Stolyarova et al., 2005; Sun et al., 2015; Safarin, 2019) are calculated by this paper’s IMCT model, and compared with their experiment results (Gzieo and Jowsa, 1984; Nomura et al., 1991; Hino, 1994; Kishi et al., 1994; Ohta and Suito, 1994; Ohta and Suito, 1998a; Ohta and Suito, 1998b; Moeizane et al., 1999; Jung and Fruehan, 2001; Stolyarova et al., 2005; Sun et al., 2015; Safarin, 2019) and Factsage-7.0 calculating values, as shown in Figure 4. In Figure 4A or Figure 4B, the activity of SiO2 or Al2O3 in the CaO-BaO-Al2O3-SiO2 slag system calculated by the IMCT model are in good agreement with the Factsage-7.0 calculating values. It also can be found that, the activity of low system slag calculated by IMCT model are in accordance to the experimental results. In summary, the IMCT model for CaO-MgO-BaO-CaF2-SiO2-Al2O3-TiO2 slag in this paper is reasonable.
FIGURE 4. The comparison of specie’s activity in slag between measured and calculated values. (A) The activity of SiO2; (B) The activity of Al2O3; (C) The activity of TiO2.
The dependence of C/S ratio in the slag (S1), listed in Table 2, on the ΔG of reactions 1–3 was shown in Figure 5. With the increase of C/S ratio in the slag, the ΔG of reactions 1–2 increased and the ΔG of reaction 3 decreased. In general, the C/S ratio in the slag was suggested to be higher 4 for Al-killed steel refining process. But Zhang et al. (Zhang, 2019) found that the C/S ratio of 6 was the most effective to improve the steel cleanliness. When the C/S ratio was higher 6, the ΔG of reaction 1 was higher than 0 kJ/mol and the ΔG of reactions 2–3 were about -25 kJ/mol, Therefore Ti in the steel will be oxidized by the SiO2 and Al2O3 in the slag. Therefore it is necessary to investigate other factors such as C/A ratio, TiO2 content and BaO content to suppress the re-oxidation of Ti by SiO2 and Al2O3.
The effect of C/A ratio in the slag (S2), listed in Table 2, on the ΔG of reaction 1–3 is shown in Figure 6. In this figure, the blue symbol-line represents the C/S ration in the slag is 6, the magenta symbol-line means the C/S ratio is 8, and the olive symbol-line means the C/S ratio is 10. From this figure we can found that, when the C/A ratio changed from 1 to 2.5, the ΔG of reaction 2 and 3 are also lower -20 kJ/mol. Yoon et al. (Yoon et al., 2002) reported that the most effective C/A ratio in the high basicity slag, in which the C/S ratio was higher than 4, was 1.7–1.8 to removing inclusions from bearing steel. Therefore, the mass ratio of CaO to Al2O3 in the slag (S3 and S4) was 1.7 in the following discussion.
Figure 7 shows the variation behavior of ΔG for reactions 1–3 with the increase of TiO2 content in the slag (S3), listed in Table2. In this figure, the C/S ratio in the slag, marked in different color symbols, was the same with Figure 6. From Figure 7, with the increase of TiO2 content in the slag, the ΔG of reaction 1 decreased, And the ΔG of reaction 2 and 3 increased. When the TiO2 content in the slag was greater than 20%, the ΔG of reaction 2 are also lower than -10 kJ/mol. Therefore, it is necessary to increase the C/S ratio in the slag. However, the activity of CaO in the slag would increase and the solid calcium titanates (Li et al., 2018) would appear. This will lead to decrease the desulfurizer ability of the slag. In the basic slag TiO2 exits as
Figure 8 shows the influence of BaO content in the slag (S4) on the ΔG of reactions 1–3. In this figure, the C/S ratio in the slag, marked in different color symbols, was the same with Figure 6. It is clear that, the ΔG of reaction 1 changed less and the ΔG of reactions 2 and 3 increased with the addition of BaO to the slag. It is clear that from Figure 8A, when the slag contained 15%TiO2, the C/S ratio was higher than 10 and the BaO content was 25–30%, the ΔG of reactions 1–3 are higher than 0 kJ/mol. When the TiO2 content in the slag was higher than 20%, with the increase of BaO content in the slag, the ΔG of reaction 1 was still lower than 0. Therefore, when the BaO content and TiO2 content in the slag were controlled as 20–30% and 15–25%, the C/S ratio should be controlled as higher than 10 according to the thermodynamic results. However, the desulfurizer and inclusion absorption ability of the slag should be considered. When the TiO2 content was higher than 30%, a large amount of solid calcium titanates (Li et al., 2018) will formed in the slag, the viscosity of the slag increase. This would lead to the desulfurizer and inclusion absorption ability descend. BaO is more powerful desulfurizer than CaO. Adding BaO to the flux not only desulfurizers by itself, but also enhances the desulphurization ability of CaO. In addition, BaO is more inclined to release the oxygen ion for less affinity to oxygen than CaO, which also favors desulfurization. However, the increase of BaO content in the flux may lead to the decrease of molar fraction of basic components because of its high molecular mass (153). Also, BaS is not stable and tends to decompose with the increase of BaS, which is disadvantageous to the desulfurization reaction (Gao et al., 2012).
In this work, the thermodynamic interaction between ladle slag and 0.361%Ti bearing steel has been analyzed using IMCT model and the following conclusion are obtained.
1) According to the comparing results between thermodynamic calculation and experimental values, the IMCT model established in this paper is reasonable.
2) With the increase of C/S ratio in the slag, the ΔG of reaction for Al and Ti reacted with SiO2 increased, and Ti reacted with Al2O3 decreased; the effect of C/A ratio in the slag on the change of ΔG for Al or Ti reacted with slag is less; with the addition of TiO2 to the slag, the ΔG for Ti reacted with SiO2 and Al2O3 increase, and Al reacted with SiO2 decrease; with the increase of BaO in the slag, the ΔG change for reaction 1 is less, and the ΔG for reaction 2 and 3 increase.
3) When the BaO content and TiO2 content in the slag were controlled as 20–30% and 15–25%, the C/S ratio should be controlled as higher than 10 according to the thermodynamic results. However, the desulphurization and inclusion absorption ability of the slag should be considered.
The original contributions presented in the study are included in the article/supplementary material, further inquiries can be directed to the corresponding author.
M-GZ was the first author and has made significant contribution to the manuscript. X-FW and G-JC have contributed towards the conception and review of the manuscript. S-PH provided correspondence and guidance on the manuscript.
The authors gratefully express their appreciation to National Natural Science Foundation of China (No.52074054) and the fourth batch of major science and technology projects in panxi experimental base (low cost manufacturing technique of titanium alloyed high-strength and hightoughness steel and its application).
The authors declare that the research was conducted in the absence of any commercial or financial relationships that could be construed as a potential conflict of interest.
All claims expressed in this article are solely those of the authors and do not necessarily represent those of their affiliated organizations, or those of the publisher, the editors and the reviewers. Any product that may be evaluated in this article, or claim that may be made by its manufacturer, is not guaranteed or endorsed by the publisher.
Bale, C. W., Bélisle, E., Chartrand, P., Decterov, S. A., Eriksson, G., Hack, K., et al. (2009). FactSage Thermochemical Software and Databases - Recent Developments. Calphad 33 (2), 295–311. doi:10.1016/j.calphad.2008.09.009
Bomberger, H. B., and Froes, F. H. (1984). The Melting of Titanium. Jom 36, 39–47. doi:10.1007/bf03339212
Boulay, E., Nakano, J., Turner, S., Idrissi, H., Schryvers, D., and Godet, S. (2014). Critical Assessments and Thermodynamic Modeling of BaO-SiO2 and SiO2-TiO2 Systems and Their Extensions into Liquid Immiscibility in the BaO-SiO2-TiO2 System. Calphad 47, 68–82. doi:10.1016/j.calphad.2014.06.004
Carmack, W. J., Smolik, G. R., and Mccarthy, K. A. (1996). Electroslag Remelt Processing of Irradiated Vanadium Alloys. J. Nucl. Mater. 233-237, 416–420. doi:10.1016/s0022-3115(96)00228-0
Cavazos, J. L., Gomez, I., and Guerrero-Mata, M. P. (2011). Stabilisation of Ferritic Stainless Steels with Zr and Ti Additions. Mater. Sci. Technol. 27, 530–536. doi:10.1179/026708309x12506933873747
Cheng, J. X. (2010). Steelmaking Commonly Used Chart Data Manual. BeiJing: Metallurgical Industry Press.
Fujimura, H., Tsuge, S., Komizo, Y., and Nishizawa, T. (2001). Effect of Oxide Composition on Solidification Structure of Ti Added Ferritic Stainless Steel. Tetsu-to-Hagane 87, 707–712. doi:10.2355/tetsutohagane1955.87.11_707
Gao, Y., Liu, Q., and Bian, L. (2012). Effect of Composition on Desulfurization Capacity in the CaO-SiO2-Al2O3-MgO-CaF2-BaO System. Metall. Materi Trans. B 43, 229–232. doi:10.1007/s11663-011-9607-1
Gzieo, A., and Jowsa, J. (1984). Activity of SiO2 in Slag CaO-SiO2-Al2O3-CaF2. Archiwum Hutnictwa 29, 319–331.
Huang, L., Deng, X., Jia, Y., Li, C., and Wang, Z. (2018). Effects of Using (Ti,Mo)C Particles to Reduce the Three-Body Abrasive Wear of a Low alloy Steel. Wear 410-411, 119–126. doi:10.1016/j.wear.2018.06.008
Jiang, Z.-H., Hou, D., Dong, Y.-W., Cao, Y.-L., Cao, H.-B., and Gong, W. (2016). Effect of Slag on Titanium, Silicon, and Aluminum Contents in Superalloy during Electroslag Remelting. Metall. Materi Trans. B 47, 1465–1474. doi:10.1007/s11663-015-0530-8
Jiang, Z. H. (2000). The Physical Chemistry and Transmission during Electroslag Remelting. Shenyang: Northeastern University Press.
Jung, S.-M., and Fruehan, R. J. (2001). Thermodynamics of Titanium Oxide in Ladle Slags. ISIJ Int. 41, 1447–1453. doi:10.2355/isijinternational.41.1447
Kim, D. S., Park, J. J., Song, H. S., Shin, Y. K., Choi, B. H., and Yim, S. S. “Iron and Steel Society. Steelmaking Division,” in Proceedings of the 76th Steelmaking Conference, Warrendale, PA, 1993, 291–297.
Kishi, M., Ioue, R., and Suito, H. (1994). Thermodynamics of Oxygen and Nitrogen in Liquid Fe-20mass%Cr alloy Equilibrated with Titania-Based Slags. ISIJ 34, 859–867.
Leban, M. B., and Tisu, R. (2013). The Effect of TiN Inclusions and Deformation-Induced Martensite on the Corrosion Properties of AISI 321 Stainless Steel. Eng. Fail. Anal. 33, 430–438. doi:10.1016/j.engfailanal.2013.06.021
Li, J., and Cheng, G. (2019). Effect of CaO-MgO-SiO2-Al2O3-TiO2 Slags with Different CaF2 Contents on Inclusions in Ti-Stabilized 20Cr Stainless Steel. ISIJ Int. 59, 2013–2023. doi:10.2355/isijinternational.isijint-2019-277
Li, J., Ruan, G., Li, J., Pan, J., and Chen, X. (2018). Evolution Mechanism of Inclusions in Al-Killed, Ti-Bearing 11Cr Stainless Steel with Ca Treatment. ISIJ Int. 58, 1042–1051. doi:10.2355/isijinternational.isijint-2017-565
Li, J. X., and Zhang, J. (2000). Calculation Model on Viscosity of CaO-MgO-MnO-FeO-CaF2-Al2O3-SiO2 Slags. J. Univ. Sci. Technol Beijing 22, 438–441. doi:10.13374/j.issn1001-053x.2000.05.012
Li, Z. B. (2010). Electroslag Metallurgy Theory and Practice. Beijing: Metallurgical Industry Press.
Lu, X. G., and Jin, Z. P. (2001). Thermodynamic Assessment of the BaO-TiO2 Quasibinary System. Calphad 24, 319–338. doi:10.1016/S0364-5916(01)00008-6
Maddalena, R., Rastogi, R., El-Dasher, B., and Cramb, A. W. “Nozzle Deposits in Titanium Treated Stainless Steel,” in 58th Electric Furnace Conf. and 17th Process Technology Conf. Proc.,Iron and Steel Society, London, 2000, 811–832.
Moeizane, Y., Ozturk, B., and Fruehan, R. J. (1999). Thermodynamics of TiOx in Blast Furnace-type Slags. Metallurgical Mater. Trans. B 30, 29–43.
Nomura, K., Ozturk, B., and Fruehan, R. J. (1991). Removal of Nitrogen from Steel Using Novel Fluxes. Mtb 22, 783–790. doi:10.1007/bf02651155
Nunnington, R. C., and Sutcliffe, N. “The Steelmaking and Casting of Ti Stabilized Stainless Steels,” in Proceedings of the 59th Electric Furnace Conf. and 19th Process Technology Conference, Warrendale, PA, 2001, 361–394.
Ohta, H., and Suito, H. (1994). Activities in CaO-MgO-Al2O3 Slags and Deoxidation Equilibria of Al, Mg and Ca. ISIJ.Int 36, 983–990.
Ohta, H., and Suito, H. (1998). Activities of SiO2 and Al2O3 and Activity Coefficients of FetO and MnO in CaO-SiO2-Al2O3-MgO Slags. Metall. Materi Trans. B 29, 119–129. doi:10.1007/s11663-998-0014-1
Ohta, H., and Suito, H. (1998). Deoxidation Equilibria of Calcium and Magnesium in Liquid Iron. Metallurgical Mater. Trans. B 28, 1131–1139.
Park, D.-C., Jung, I.-H., Rhee, P. C. H., and Lee, H.-G. (2004). Reoxidation of Al-Ti Containing Steels by CaO-Al2O3-MgO-SiO2 Slag. ISIJ Int. 44, 1669–1678. doi:10.2355/isijinternational.44.1669
Park, J.-H., Lee, S.-B., Kim, D. S., and Pak, J.-J. (2009). Thermodynamics of Titanium Oxide in CaO-SiO2-Al2O3-MgOsatd-CaF2 Slag Equilibrated with Fe-11mass %Cr Melt. ISIJ Int. 49, 337–342. doi:10.2355/isijinternational.49.337
Park, J. H., Lee, S.-B., and Gaye, H. R. (2008). Thermodynamics of the Formation of MgO-Al2O3-TiO X Inclusions in Ti-Stabilized 11Cr Ferritic Stainless Steel. Metall. Materi Trans. B 39, 853–861. doi:10.1007/s11663-008-9172-4
Qian, G.-Y., Jiang, F., Cheng, G.-G., and Wang, C.-S. (2014). Effect of TiO2addition to LF Refining Slag on the Ti, Al, and Cleanliness of Ti-Stabilized Stainless Steel. Metall. Res. Technol. 111, 229–237. doi:10.1051/metal/2014029
Safarin, J. (2019). Thermochemical Aspects of boron and Phosphours Distribution between Silicon and CaO-BaO-SiO2 Slags. SILICON 11, 437–451. doi:10.1007/s12633-018-9919-8
Sahu, M., Mukherjee, S., Keskar, M., Krishnan, K., Dash, S., and Tomar, B. S. (2018). Investigations of Thermophysico-Chemical Properties of Ba 2 TiSi 2 O 8 (S) and Sr 2 TiSi 2 O 8 (S). Thermochim. Acta 663, 215–226. doi:10.1016/j.tca.2018.02.003
Shukla, A. (2012). Development of a Critically Evaluated Thermodynamic Databse for the Systems Containing Alkaline-Earth Oxides. Montreal, Canada: École Polytechnique de Montréal.
Sommerville, I. D., and Bell, H. B. (1982). The Behaviour of Titania in Metallurgical Slags. Can. Metallurgical Q. 21, 145–155. doi:10.1179/cmq.1982.21.2.145
Stolyarova, V. L., Opatin, S. I. L., and Plotnikov, E. N. (2005). Thermodynamic Properties and Vaporisation Processes of Ternary Glass Forming Silicate Systems: CaO-Al2O3-SiO2, CaO-TiO2-SiO2 and BaO-TiO2-SiO2. Phys. Chem. glasses 46, 119–127.
Sun, Y., Liu, Z. N., and Tao, D. P. (2015). Prediction of TiO2 Activity in Al2O3-CaO-MgO-SiO2-TiO2 Slag System by Molecular Interaction Volume Model. J. Kunming Univ. Sci. Technology(Natural Sci. Edition) 40, 1–9. doi:10.16112/j.cnki.53-1223/n.2015.05.001
Yang, X.-M., Jiao, J.-S., Ding, R.-C., Shi, C.-B., and Guo, H.-J. (2009). A Thermodynamic Model for Calculating Sulphur Distribution Ratio between CaO-SiO2-MgO-Al2O3 Ironmaking Slags and Carbon Saturated Hot Metal Based on the Ion and Molecule Coexistence Theory. ISIJ Int. 49, 1828–1837. doi:10.2355/isijinternational.49.1828
Ye, D. L. (2002). Handbook of Practical Inorganic Thermodynamics. BeiJing: Metallurgical Industry Press.
Yoon, B.-H., Heo, K.-H., Kim, J.-S., and Sohn, H.-S. (2002). Improvement of Steel Cleanliness by Controlling Slag Composition. Ironmaking & Steelmaking 29, 214–217. doi:10.1179/030192302225004160
Zaitsev, A. I., Korolyov, N. V., Mogutnov, B. M., and Vyatkin, Y. F. “Thermodynamic and Crystallization Model of Slag for Ladle Treatment of Steel,” in Proceedings of the 6th International Iron Steel Congress, 1990 (Nagoya, 185–193.
Zhang, J. (2004). Application of Annexation Principle to the Study of Thermodynamic Properties of Ternary Molten Salts CaCl2-MgCl2-NaCl. Rare Met. 23, 209–213.
Zhang, J. (2007). Thermodynamic Calculations of Metallurgical Melts and Solutions. BeiJing: Metallurgical Industry Press.
Zhang, L. F. (2019). Non-metallic Inclusions in Steel: Fundamentals. BeiJing: Metallurgical Industry Press.
Zheng, H., Chen, W., and Hu, Y. “Iron and Steel Technology Conference,” in Proceedings Iron & Steel Technology Conference. (AISTech 2004), Warrendale, PA, September 2004 (AISI), 397.
C/S ratio the mass ratio of CaO-SiO2
C/Al ratio the mass ratio of CaO-Al2O3
Keywords: thermodynamic model, Ti-bearing steel, slag, IMCT, ladel
Citation: Zhao M-G, Wang X-F, Chen G-J and He S-P (2022) The Establishment of Thermodynamic Model for Ti Bearing Steel-Slag Reaction and Discuss. Front. Mater. 8:792714. doi: 10.3389/fmats.2021.792714
Received: 11 October 2021; Accepted: 15 November 2021;
Published: 03 January 2022.
Edited by:
Antonio Caggiano, Darmstadt University of Technology, GermanyCopyright © 2022 Zhao, Wang, Chen and He. This is an open-access article distributed under the terms of the Creative Commons Attribution License (CC BY). The use, distribution or reproduction in other forums is permitted, provided the original author(s) and the copyright owner(s) are credited and that the original publication in this journal is cited, in accordance with accepted academic practice. No use, distribution or reproduction is permitted which does not comply with these terms.
*Correspondence: Sheng-Ping He, aGVzaHBAY3F1LmVkdS5jbg==
Disclaimer: All claims expressed in this article are solely those of the authors and do not necessarily represent those of their affiliated organizations, or those of the publisher, the editors and the reviewers. Any product that may be evaluated in this article or claim that may be made by its manufacturer is not guaranteed or endorsed by the publisher.
Research integrity at Frontiers
Learn more about the work of our research integrity team to safeguard the quality of each article we publish.