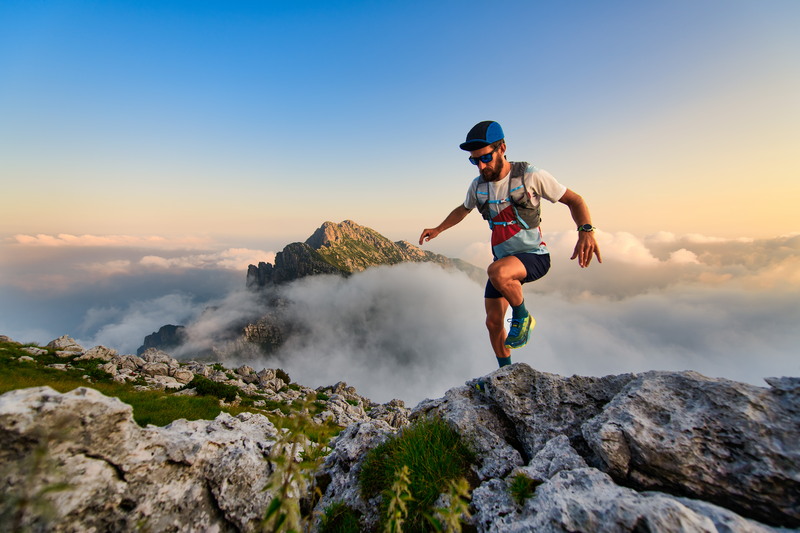
94% of researchers rate our articles as excellent or good
Learn more about the work of our research integrity team to safeguard the quality of each article we publish.
Find out more
ORIGINAL RESEARCH article
Front. Mater. , 29 November 2021
Sec. Structural Materials
Volume 8 - 2021 | https://doi.org/10.3389/fmats.2021.792682
This article is part of the Research Topic Non-BF Slag-based Green Cementitious Materials View all 20 articles
In this study, the influence of steel slag (SS) content on the strength of the cementitious materials was investigated. The quaternary active cementitious material (CaO-SiO2-Al2O3-SO3) was prepared using various proportions of steel slag (SS), granulated blast furnace slag (BFS), and desulfurized gypsum (DG). The mechanism of synergistic excitation hydration of the cementitious materials was examined using various techniques such as X-ray diffraction (XRD), scanning electron microscopy (SEM) and Fourier transform infrared spectrometry (FTIR). The strength of the mortar test block was initially increased and decreased later with the increase of the SS content. Mortar test block with 20% steel slag, 65% granulated blast furnace slag, and 15% desulfurized gypsum with 0.35 water-binder ratio showed the highest compressive strength of 57.3 MPa on 28 days. The free calcium oxide (f-CaO) in the SS reacted with water and produced calcium hydroxide (Ca(OH)2) which created an alkaline environment. Under the alkaline environment, the alkali-activated reaction occurred with BFS. In the early stage of hydration reaction, calcium silicate hydrate (C-S-H) gel and fibrous hydration product ettringite (AFt) crystals were formed, which provided early strength to the cementitious materials. As the hydration reaction progressed, the interlocked growth of C-S-H gel and AFt crystals continued and promoted the increase of the strength of the cementitious system.
Solid waste refers to the garbage and discarded material resulting from commercial, industrial, and community activities (Chen et al., 2010). Among all types of solid waste, seven (coal gangue, fly ash, tailings, industrial by-product gypsum, smelting slag, construction waste, and crop straw) can be considered as bulk solid waste owing to their high annual production which exceeds 100 million tons (National Development and Reform Commission of the People’s Republic of China, 2021). Bulk solid waste is a key area in the field of comprehensive utilization of resources due to its large quantity, wide range, adverse environmental impact, and broad utilization prospects (S Yüksel, 2018).
The generation of smelting slag has been substantially increased over the last few decades in China due to the rapid development in iron and steel industries (Li, 2020). The smelting slag accumulated on soil occupies a large area of land and easily form fine dust when exposed to air, thereby seriously impact on the local environment. Consequently, increasing attention has been paid to proper disposal and resource utilization of smelting slag generated from the iron and steel industries. A large-scale application of smelting slag in the construction industry is one such example of resource utilization. For a long time, solid waste such as fly ash, granulated blast furnace, silica fume, etc., is used to make cementitious material which is an important substance added alongside cement in concrete production (Jagadisha et al., 2020). The application of cementitious materials reduces the amount of cement required to be added in concrete production. Cement production consumes a large amount of energy and emits a high amount of CO2. Therefore, these environmental impacts can be reduced when the amount of cement used in concrete production is reduced (Ansai et al., 2009).
Cementitious material is a substance that can change a slurry to a solid stone-like body through a series of physical and chemical reactions and can cement other solid materials into a whole with mechanical strength. They are used to increase the performance of concrete. Active Si-Al components can be used effectively to prepare high-quality cementitious materials from smelting slag. As a consequence, the utilization of steel slag has been enhanced and the production of CO2 has been greatly reduced when making cement (Wang et al., 2019).
For example, using the similarity of mineral composition between blast furnace slag, converter slag, and cement clinker, homogeneously mixed them under a hot melting state can produce the same components of cement clinker (Gudim et al., 2009; Zhu, 2002). However, in this process, it is difficult to control the production parameters and the heat consumption is too large. Zhao et al. (2007), prepared mortar test blocks having 28 days strength of 49 MPa using blast furnace slag and fly ash with the desulfurized gypsum as the activator. The performance of these mortar test blocks was improved using the “partial ultra-fine grinding process.” However, the ultra-fine grinding is an expensive process consequently, the actual production cost was very high. According to Jiang et al. (2019), high-strength composite cementitious materials can be prepared using optimum mixture ratio of steel slag: fly ash 1:2 with 1.4 water glass modules at an early curing temperature (80°C).
The above studies highlighted the importance of low energy consumption when preparing cementitious materials using smelting slag. Therefore, subsequent research was more focused on the reaction mechanism of making cementitious materials from smelting slag to reduce energy consumption. Yan and Wang. (2009) found that the steel slag-based cementitious materials can significantly shorten the induction period thereby can accelerate the hydration reaction rate under high-temperature curing. The steel-based cementitious materials had low dissolved Si-Al matter in the early stage of hydration reaction compared to the later stage suggesting a rapid reaction rate at the later stage (Cui et al., 2017). Calcium silicate hydrate (C-S-H) gel and AFt were the main hydration products obtained from steel-based cementitious materials.
Therefore, further research is needed to improve the early strength of steel slag-based cementitious materials. The chemical activation and hydration mechanism of cementitious materials have been studied with different dosages of activators such CaO or Na2SO4. However, these activators are unable to influence the hydration product types (Cui et al., 2018). During the hydration, the generation of Ca(OH)2 through the reaction of tricalcium silicate in the steel slag could promote the breaking of Si-O-Al and O-Si-O bonds (Xu et al., 2019). Although the crystallinity of Ca(OH)2 and the strength of the cementitious material were weak, the second exothermic peak of steel slag AFter the alkali activation was strong (Sun, 2019). Water glass was used to activate the steel slag in place of traditional cement clinker (Sun, 2019).
Compared with an ordinary mortar, the strength of the mortar prepared with steel slag powder was increased by 72%, and the chloride ion permeability was decreased by 52% at high temperatures indicating better mechanical properties and durability (Jihad Miah et al., 2021). In recent years, research has used advanced methods to study the reaction mechanism of smelting slag cementitious materials. However, only a few of them have been applied in engineering practice. Therefore, it is important to solve the possible utilization of large quantities of smelting slag to prepare cementitious materials at a low cost. In this study, steel slag, granulated blast furnace slag, and desulfurized gypsum were used to prepare solid waste based cementitious materials. The strength and the hydration mechanism were studied to lay a theoretical foundation for the utilization of solid waste in the iron and steel industry.
The steel slag, granulated blast furnace slag, and desulfurized gypsum used in the experiment were obtained from Tangshan, Hebei Province, China. The chemical composition of the three raw materials is shown in Table 1, and XRD scans of the raw materials are shown in Figure 1.
FIGURE 1. XRD scans of raw materials, Peaks of the different mineral phases are numbered 1- Dicalcium silicate (C2S) 2- Tricalcium silicate (C3S) 3-Dicalcium ferrite (C2F) 4-FeO/MgO(RO phase) 5-f-CaO 6- Gehlenite (C2AS) 7-CaSO4.2H2O.
The major mineral phases in steel slag are dicalcium silicate (C2S), tricalcium silicate (C3S), FeO/MgO(RO phase), and free calcium oxide (f-CaO). According to Mason’s theory (Mason, 1994), the basicity coefficient of the steel slag was calculated using Eq. 1. Here, the basicity coefficient value indicates high alkalinity in steel slag with excess f-CaO that can provide an alkaline environment for the cementitious system.
The diffuse peak at 25°–35° in the XRD pattern (Figure 1) of the granulated blast furnace slag confirms the occurrence of glassy substances and a small amount of gehlenite (peak 6, Figure 1). The quality coefficient of granulated blast furnace slag was determined using Eq. 2 (Saafan et al., 2020).
The main component of desulfurized gypsum is dihydrate gypsum (peak 7, Figure 1). The alkalinity coefficient of desulfurized gypsum was determined from Eq. 3 (Hou et al., 2006).
The alkalinity coefficient of desulfurized gypsum indicates that it is easier to simulate the activity and to improve the strength of the cementitious system.
Steel slag contains high iron content which makes it difficult to grind. These excess iron in the slag must be removed to maximize the activity of raw materials under low energy consumption. Therefore, the circular iron removal method called “magnetic separation grinding” was used to remove the iron minerals in steel slag. AFter grinding, the density of steel slag and granulated blast furnace were 3.27 g/cm3 and 2.86 g/cm3 and the specific surface areas were 440 m2/kg and 480 m2/kg, respectively.
The approximate proportions of three raw materials for the pilot study were determined based on the previous research. According to the pilot study, the proportion of steel slag should be less than 40% and that of desulfurization gypsum should be between 13 and 17%. Beyond these limits the workability of the mortar test block is poor and the strength would grow slowly. The water-binder ratio was determined as 0.35 by following the water consumption experiment of standard consistency. A test scheme with different proportions of SS, BFS, and DG was designed to further study the effect of steel slag content on the strength of the mortar test block (Table 2).
A homogenised mixture of raw materials was obtained by mixing them according to the above ratios in a mixer, and the mortar test blocks were shaped following the standard method called “Method of testing cements-Determination of strength (ISO Method)” (ISO, 1999). The mortar test blocks were then cured in a standard curing room and the strength and the workability were determined at a specified age.
Based on the strength of the mortar the ideal proportion of the raw materials was selected to prepare the paste test block. The selected best raw materials proportion mixture was ground to powder and dried at the specified age to carry out microscopic tests. The micromorphology of the cementitious system was analyzed by the SEM. The mineralogical phases of the cementitious system were determined using the XRD. The molecular structure of the gelling system was analyzed by FTIR at the spectral scanning range of 400–4,000 cm −1 (Li et al., 2011).
The strength of the cementitious material AFter hardening is an important indicator of its performance (Han et al., 2020).
Figure 2 shows the variation of the mortar test block strength with steel slag content. The ideal ratio to prepare cementitious material was in Group D with a steel slag content of 20% (Figure 2; Table 2). At steel slag content of 20%, the highest flexural (9.64 MPa) and compressive (57.26 MPa) strengths were observed in the test block aged for 28 days (Figure 2). A slight increase in both flexural and compressive strengths occurred at steel stag content from 5 to 20%. However, a significant decrease in both types of strengths occurred when steel slag content was greater than 20% (Figure 2).
FIGURE 2. Influence of different steel slag content on test blocks strength (A) flexural strength (B) compressive strength.
The strength can be changed when the Ca-Si-Al-S system in the raw materials stimulates each other and when a hydration reaction occurs. The strength of the cementing system can be promoted as AFt and C-S-H gel are continuously formed during the hydration. The increase in the steel slag content results in a decrease in the granulated blast furnace slag content together with the content of the active ingredients in the system. However, the increase in f-CaO content led to an increase in the basicity of the system. The hydration product AFt is prone to swell, which can ultimately lead to a decrease in the strength of the mortar test block (Ni et al., 2019).
During the curing period, hydration reaction occurs in the cementitious system. This process leads to a change in the mineralogy and the micromorphology of the mortar which in turn affects the strength of the mortar (Chen et al., 2019; Ni et al., 2019).
The SEM images of pastes at different ages are shown in Figure 3.
FIGURE 3. SEM images of pastes at different ages (A) Day 3 (B) Day 7 (C) Day 28. (A) Low power diagram and high power diagram at 3 days of hydration. (B) Low power diagram and high power diagram at 7 days of hydration. (C) Low power diagram and high power diagram at 28 days of hydration.
The SEM images of the cementitious system paste test cubes AFter 3, 7, and 28 days of hydration are shown in Figures 3A–C, respectively. A large number of needle-like AFt crystals were in the cementitious system AFter 3 days of hydration (Li et al., 2013). These AFt crystals, interspersed in irregularly shaped C-S-H gel, formed a spatial framework that provided an early strength to the cementitious system (Figure 3A). However, this framework was not dense hence, had low intensity at the early stage. By 7 days, the AFt crystals had grown stronger and the growth continued to a stable crystal form. The C-S-H gel was wrapped more tightly and the structure porosity had been reduced. As a result, the strength of the test cubes continued to increase during the hydration (Figure 3B) (Cui and Ni, 2016). By 28 days of hydration, the structure became more compact as the unreacted fine particles in the raw material were interweaved and wrapped by the AFt crystals and the C-S-H gel in the cementitious system (Figure 3C) (Cui and Ren, 2016) This lead to increase the strength of the test cubes further and was consistent with the strength test results.
The XRD scans of the pastes at different ages are shown in Figure 4.
FIGURE 4. XRD scan of pastes at different ages. Peaks of the different mineral phases are numbered, 1-AFt 2-Gypsum 3-RO 4-Ca(OH)2 5-C2S.
The main mineral phases of the cementitious system under standard curing conditions were AFt, Ca(OH)2, gypsum, RO phase, and C2S (Figure 4). The RO phase derived from the steel slag showed no evident activation and did not participate in the reaction. At the early hydration period, AFt and Ca(OH)2 were formed (Figure 4). The diffuse peak near the diffraction angle of 30°, indicates the formation of C-S-H gel with lower crystallinity (Figure 4). The gradual decrease in diffraction peaks of gypsum and C2S with prolonged hydration indicates the disappearance of the two minerals. This could be due to their participation in the hydration reaction and subsequent formation of AFt and Ca(OH)2 (Figure 4). ThereAFter, the Ca(OH)2 was reacted with the active salic minerals in the system, causing a pozzolanic reaction and eventually forming C-S-H gel (Chang et al., 2021). XRD results confirmed that the acicular substance in the corresponding SEM was AFt, and the amorphous substance is C-S-H gel.
FTIR analysis was carried out on the paste test cube at different ages to identify and understand the molecular structure of the mineral phases. The corresponding FTIR spectra are shown in Figure 5.
The absorption bands at 3548∼3407 cm−1 and 1620 cm−1 indicate the asymmetric stretching band of H2O and the flexural vibration peak of OH−, respectively, in the hydration product. With aging, the absorption peaks were increased and broadened indicating a continuous increase of OH in the system. As the hydration reaction continued, more hydration products were gradually added. The asymmetric stretching band of CO32- at 1486 cm−1 suggests the occurrence of carbonation reaction in the air. The asymmetric stretching bands of Si-O at 1118, 1004, and 475 cm−1, and the characteristic peak of C-S-H gel near 1004 cm−1 indicates the reaction of the f-CaO in the steel slag with water at the initial stage of hydration. During this hydration reaction, Ca(OH)2 was produced which provided an alkaline environment to the system.
In the alkaline environment, the Si-O-Al bond breaks and oxygen-silicon tetrahedron depolymerizes with the aluminum-oxygen tetrahedron. This follows another reaction with SO42- in the desulfurized gypsum and the Ca2+ in the system to produce AFt. The AFt formation through the hydration reaction was facilitated by a small amount of C2S in steel slag and the pozzolanic effect by the C-S-H gel. The C-S-H gel and the AFt were interconnected and the gaps were filled by the steel slag powder which acted as a microaggregate thereby resulting in an early strength (Zhang, 2016; Xiao et al., 2018). As the reaction continued, with the progress of the hydration reaction, the characteristic peak of the C-S-H gel shifted slightly to a high wavenumber. This shift indicates an increase in the degree of polymerization of the C-S-H gel thereby promoting the strength of the cementitious system.
In this study, the effect of steel slag content on the strength of the CaO-SiO2-Al2O3-SO3 quaternary active cementitious system was investigated using metallurgical slag as the primary raw material. The strength was initially increased and decreased thereAFter with the increase of the steel slag content. The steel slag content of 20% was the ideal percentage which showed the highest compressive strength of 57 MPa on the 28th day. The synergistic excitation of steel slag, granulated blast furnace slag, and desulfurized gypsum promoted the staggering growth of hydration products, AFt, and C-S-H gel. These hydration products formed a network structure, making the system more compact and ensuring further development of strength. Steel slag has low hydration activity and poor stability. Therefore, in depth research is required to further excite the activity of steel slag in the cementitious material, to increase the steel slag consumption, and to improve the efficiency of solid waste resource utilization.
The raw data supporting the conclusion of this article will be made available by the authors, without undue reservation.
All authors listed have made a substantial, direct, and intellectual contribution to the work and approved it for publication.
This work was supported by the Key R and D Plan of Hebei Province (20373801D). Key R and D Plan of Hebei Province (18273807D); Hebei graduate innovation funding project 2021(CXZZBS2021099) and Tangshan Basic Innovation team for clean utilization of industrial solid waste (19130207C).
The authors declare that the research was conducted in the absence of any commercial or financial relationships that could be construed as a potential conflict of interest.
All claims expressed in this article are solely those of the authors and do not necessarily represent those of their affiliated organizations, or those of the publisher, the editors and the reviewers. Any product that may be evaluated in this article, or claim that may be made by its manufacturer, is not guaranteed or endorsed by the publisher.
Ansai, T., Nishikawa, M., Ikeo, Y., and Sakai, E. (2009). Hydration Reaction Analysis of Cement Having High Blast-Furnace Slag. Cement ence Concrete Tech. 63 (1), 22–27. doi:10.14250/cement.63.22
Chang, J., Zhang, X., Gu, Y. Y., and Zhang, Y. Y. (2021). Effects of Pozzolanic Reaction on Carbonation Degree and Strength of Steel Slag Compacts Containing Zeolite. Construction Building Mater. 277 (277), 122334. doi:10.1016/J.CONBUILDMAT.2021.122334
Chen, X., Geng, Y., and Fujita, T. (2010). An Overview of Municipal Solid Waste Management in china. Waste Manage. 30 (4), 716–724. doi:10.1016/j.wasman.2009.10.011
Chen, X., Wan, D.-W., Jin, L.-Z., Qian, K., and Fu, F. (2019). Experimental Studies and Microstructure Analysis for Ultra High-Performance Reactive Powder concrete. Construction Building Mater. 229 (Dec.30), 116924–1116924. doi:10.1016/j.conbuildmat.2019.116924
Cui, X., and Ni, W. (2016). Hydration Behavior of Cementitious Materials with All Solid Waste Based of Steel Slag and Blast Furnace Slag. Revista de la Facultad de Ingeniería 31 (7), 172–181. doi:10.21311/002.31.7.17
Cui, X., Ni, W., and Ren, C. (2016). Early Hydration Kinetics of Cementitious Materials Containing Different Steel Slag Powder Contents. Ijht 34 (4), 590–596. doi:10.18280/ijht.340406
Cui, X., Ni, W., and Di, Y. (2018). Chemical Activation of Cementitious Materials with All Solid Waste Based of Steel Slag and Blast Furnace Slag. Bull. Chin. Ceram. Soc. 37 (4), 1411–1417. doi:10.16552/j.cnki.issn1001-1625.2018.04.047
Cui, X., Ni, W., and Ren, C. (2017). Hydration Reaction Mechanism of Steel Slag Slag Based Solid Waste Cementitious Material. Chin. J. Mater. Res. 31 (09), 687–694. doi:10.11901/1005.3093.2016.741
Gudim, Y. A., Golubev, A. A., Ovchinnikov, S. G., and Zinurov, I. Y. (2009). Waste-free Processing of Steel-Smelting Slag. Steel Transl. 39 (7), 612–614. doi:10.3103/s0967091209070237
Han, X., Feng, J., Shao, Y., and Hong, R. (2020). Influence of a Steel Slag Powder-Ground Fly Ash Composite Supplementary Cementitious Material on the Chloride and Sulphate Resistance of Mass concrete. Powder Tech. 370, 176–183. doi:10.1016/j.powtec.2020.05.015
Hou, X., Xu, D., Cao, H., Han, T., and Shang, B. (2006). Effects of Ground Blast-Furnace-Slag with Highly Hydraulic Activity on the Cement Properties. J. Xi'an Univ. architecture Tech. (NATURAL SCIENCE EDITION) 01, 9–17. doi:10.3969/j.issn.1006-7930.2006.01.003
ISO (1999). Method of testing cements—Determination of strength. China National Standardization Administration Committee. GB/T 17671-2020. Available at: https://kns.cnki.net/kcms/detail/detail.aspx?FileName=SCSF00023001&DbName=SCSF.
Jagadisha, K., Rao, B., Nayak, G., and Shenoy, B. A. (2020). A Review on Properties of Sustainable Concrete Using Iron and Steel Slag Aggregate as Replacement for Natural Aggregate. doi:10.1007/978-981-15-8293-6_7
Jiang, Y., Jia, L. J., Wen, M. Y., and Niu, Y. H. (2019). Preparation of Alkali-Activated Fly Ash/steel Slag Cementitious Materials. Bull. Chin. Ceram. Soc. (07), 2152–2156+2161. doi:10.16552/j.cnki.issn1001-1625.2019.07.027
Jihad Miah, M., Kawsar Ali, M., Lo Monte, F., Chandra Paul, S., John Babafemi, A., and Šavija, B. (2021). The Effect of Furnace Steel Slag Powder on the Performance of Cementitious Mortar at Ambient Temperature and AFter Exposure to Elevated Temperatures. Structures 33 (2), 2811–2823. doi:10.1016/j.istruc.2021.06.047
Li, C., Zhang, Z. F., Liu, S. Y., and Cheng, L. (2013). Ettringite Formation in Lime and Cement-Stabilized clay. Chin. J. Geotechnical Eng. 35 (zk2), 662–665.
Li, X. (2020). Development Road of China's Modern Iron and Steel Industry. China: Metallurgical Industry Press. doi:10.1007/978-981-15-2074-7_1
Li, L., Xie, Y., Feng, Z., and Zhu, C. H. (2011). Hydration Mechanism of Cement and its Research Methods. Concrete (06), 76–80.
National Development and Reform Commission of the people's Republic of China. (2021). Available at: https://www.163.com/dy/article/G60SC6FI05148IM8.html.
Ni, W., Li, Y., Xu, C., Xu, D., Jiang, Y., and Gao, G. (2019). Hydration Mechanism of Slag Electric Furnace Reduction Slag All Solid Waste Cementitious Material. J. Cent. South Univ. (NATURAL SCIENCE EDITION) 50 (10), 2342–2351. doi:10.11817/j.issn.1672-7207.2019.10.002
Saafan, M. A., ZeinabEtman, A., and Lakany, D. (2020). Microstructure and Durability of Ground Granulated Blast Furnace Slag Cement Mortars. Iranian J. Sci. Technology-Transactions Civil Eng. 45 (6). doi:10.1007/s40996-020-00533-3
Sun, J. (2019). Properties of Alkali Activated Steel Slag Cementitious Material and concrete. Beijing: China University of mining and Technology. doi:10.27624/d.cnki.gzkbu.2019.000009
Wang, A., Zheng, Y., Zhang, Z., Liu, K., Rui, M. A., and Sun., D. (2019). Research Progress of Geopolymer Cementitious Material Modification for Improving Durability of concrete. Mater. Rep. 33 (15), 2552–2560. doi:10.11896/cldb.19040211
Xiao, J., Li, H., Zhu, H., and Dang, Y. (2018). Analysis of Hydration Products of Slag Silicate Composite Cementitious Materials by Infrared and Nuclear Magnetic Spectroscopy. J. Mater. Sci. Eng. 36 (04), 132–137. doi:10.14136/j.cnki.issn1673-2812.2018.04.025
Xu, C., Ni, W., Li, K., Zhang, S., Li, Y., and Xu, D. (2019). Hydration Mechanism and Orthogonal Optimisation of Mix Proportion for Steel Slag-Slag-Based Clinker-free Prefabricated concrete. Construction Building Mater. 228, 117036. doi:10.1016/j.conbuildmat.2019.117036
Yan, P., and Wang, Q. (2009). Effect of High Temperature Curing on Early Hydration Properties of Steel Slag Composite Cementitious Materials. J. Tsinghua Univ. Nat. Sci. Edition 4, 790–793. doi:10.3321/j.issn:1000-0054.2009.06.003
Yüksel, S. (2018). A Review of Steel Slag Usage in Construction Industry for Sustainable Development. Environ. Dev. Sustainability 19 (2), 1–16. doi:10.1007/s10668-016-9759-x
Zhang, G. (2016). Formation and Evolution Mechanism of C-S-H Microstructure of Slag Cement Composite Slurry under the Action of Aggressive Ions. Doctoral dissertation. Wuhan University of Technology. Available at: https://kns.cnki.net/KCMS/detail/detail.aspx?dbname=CDFDLAST2019&filename=1019809008.nh.
Zhao, F.-Q., Ni, W., Wang, H.-J., and Liu, H.-J. (2007). Activated Fly Ash/slag Blended Cement. Resour. Conservation Recycling 52 (2), 303–313. doi:10.1016/j.resconrec.2007.04.002
Zhu, G. (2002). “Current Situation and Trend of Comprehensive Utilization of Solid Wastes of Iron and Steel Industry in PRC,” in CISA International Steel Congress 2002 and High-Ranking Conference on Innovation and Sustainable Development, Beijing, June 26, 2002 Research Institute for Processing and Utilization of Metallurgical Solid Waste, Central Research Institute of Building &Construction, MCC Group.
Keywords: steel slag, granulated blast furnace slag, full solid waste cementitious materials, AFT, C-S-H gel
Citation: Niu F, An Y, Zhang J, Chen W and He S (2021) Synergistic Excitation Mechanism of CaO-SiO2-Al2O3-SO3 Quaternary Active Cementitious System. Front. Mater. 8:792682. doi: 10.3389/fmats.2021.792682
Received: 11 October 2021; Accepted: 08 November 2021;
Published: 29 November 2021.
Edited by:
Lijie Guo, Beijing General Research Institute of Mining and Metallurgy, ChinaReviewed by:
Ruidong Wu, University of Science and Technology Beijing, ChinaCopyright © 2021 Niu, An, Zhang, Chen and He. This is an open-access article distributed under the terms of the Creative Commons Attribution License (CC BY). The use, distribution or reproduction in other forums is permitted, provided the original author(s) and the copyright owner(s) are credited and that the original publication in this journal is cited, in accordance with accepted academic practice. No use, distribution or reproduction is permitted which does not comply with these terms.
*Correspondence: Yukun An, YW55dWt1bkBuY3N0LmVkdS5jbg==; Jinxia Zhang, WmhhbmdqaW54aWExNjNAMTYzLmNvbQ==
Disclaimer: All claims expressed in this article are solely those of the authors and do not necessarily represent those of their affiliated organizations, or those of the publisher, the editors and the reviewers. Any product that may be evaluated in this article or claim that may be made by its manufacturer is not guaranteed or endorsed by the publisher.
Research integrity at Frontiers
Learn more about the work of our research integrity team to safeguard the quality of each article we publish.