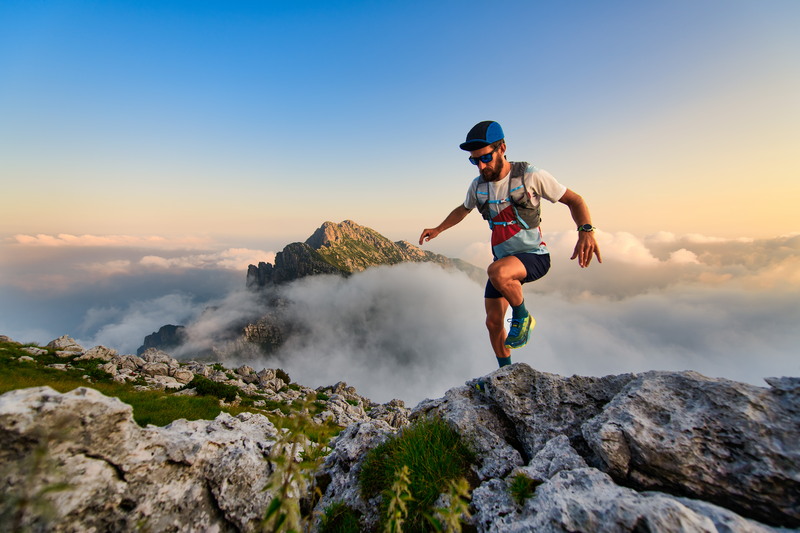
95% of researchers rate our articles as excellent or good
Learn more about the work of our research integrity team to safeguard the quality of each article we publish.
Find out more
ORIGINAL RESEARCH article
Front. Mater. , 03 November 2021
Sec. Structural Materials
Volume 8 - 2021 | https://doi.org/10.3389/fmats.2021.778833
This article is part of the Research Topic 2021 Retrospective: Structural Materials View all 13 articles
In this paper, the microstructure, electromagnetic shielding properties and mechanical properties of Mg-6Zn-3Sn-0.5Cu alloys are studied. As indicated from the results, the phases in the as-cast alloy comprise α-Mg, MgZnCu, Mg2Sn and Mg2Zn3 phases. After homogenization, Mg2Sn and Mg2Zn3 phases are decomposed, but the MgZnCu phase remains. During extrusion, complete dynamic recrystallization (DRX) occurs, and the spherical Mg2Sn phase precipitates dynamically. Due to considerable rod-like β′1 phases precipitate by complying with the [0001] Mg direction, the mechanical properties of aged alloys are remarkably enhanced. The peak-aged alloy achieves the tensile strength of 366 MPa, the yield strength of 358 MPa and the elongation of 7%. With the increase in the size of the β′1 phase, the mechanical properties of the over-aged alloy are reduced. Since the phases precipitate, the electrical conductivity of the alloy is enhanced, and the internal reflective interface increases, so the aged alloys exhibit improved electromagnetic shielding performance. The electromagnetic shielding efficiency of the peak-aged alloy exceeds 105 dB in the range of 30–1500 MHz, showing the best match between mechanical and electromagnetic shielding properties.
As modern electronic technology is advancing, people’s production life has been facilitated, while the issue of electromagnetic pollution has arisen. Electromagnetic waves are capable of affecting the life and health of living organisms and interfering with the normal operation of electronic equipment. Moreover, the risk of information leakage in national defense will be raised if electromagnetic waves are not effectively shielded (García et al., 2008; Shen et al., 2013; Shahzad et al., 2016; Kim et al., 2017). On the whole, the existing electromagnetic shielding materials complies with polymer composites and metal-based materials, whereas polymer materials exhibit poor mechanical properties, and metal-based materials face a problem of high density (Geetha et al., 2009). For this reason, the development of lightweight electromagnetic shielding materials with high mechanical properties has become one of the hotspots in materials research.
Magnesium alloys have been extensively employed in automotive, aerospace, defense and military industries for their low density, high specific strength over stiffness, good damping properties and easy recycling (Ali et al., 2015; You et al., 2017). At present, in addition to studying the microstructure and mechanical properties of magnesium alloys, the study of their functional properties has also become an emerging research hotspot (Yang et al., 2021). Electromagnetic shielding performance as an important functional property of magnesium alloys has also attracted the attention of researchers. Pandey et al. (2019) found that the addition of Ti can improve the electromagnetic shielding performance of pure magnesium. Wang et al. (2019) developed an Mg-Li alloy with high mechanical and electromagnetic shielding properties by rolling. Ye et al. (2021) prepared an Mg-Sn-Zn alloy with a tensile strength of 337 MPa and an electromagnetic shielding efficiency of 97–114 dB, which had a good comprehensive performance. Chen et al. (2012), Chen et al. (2013), and Chen et al. (2015a) revealed that aging treatment could improve the electromagnetic shielding properties of Mg-Zn alloys. By introducing suitable alloying elements to the alloy, combined with plastic deformation and aging treatment, magnesium alloys with high electromagnetic shielding properties and prominent mechanical properties can be prepared, which is critical to expanding the application of magnesium alloys.
Mg-Zn alloys can be strengthened by heat treatment, and their cost is significantly lowered compared with rare-earth magnesium alloys. However, the mechanical properties of Mg-Zn alloys are poor, and further alloying is required to enhance the properties of the alloys. For example, elements such as Sn, Ca, Mn, and Cu are added to the Mg-Zn alloys to improve their mechanical properties (Liu et al., 2020; Wang et al., 2021). As reported by Wei et al. (2013) and Qi et al. (2014), the addition of Sn elements to Mg-Zn alloys resulted in grain refinement and improvement of mechanical properties. Wang et al. (2018) reported that the Cu element could refine the second phase in Mg-Sn-Zn alloy and enhance the mechanical properties of the alloy.
As indicated from recent studies, Mg-Zn alloys also exhibit high electromagnetic shielding properties (Chen et al., 2012; Chen et al., 2013; Chen et al., 2015a). However, Research on structural-functional integration Mg-Zn alloys is still relatively rare Rare research has been reported on. Thus, to further expand the application of Mg-Zn alloy and enrich its basic theoretical data as structural-functional materials, we prepared Mg-6Zn-3Sn-0.5Cu alloy based on Mg-6Zn-3Sn alloy with the addition of a trace amount of Cu elements. The microstructure evolution of the alloy was studied, and the mechanical properties and electromagnetic shielding properties of the extruded, peak-aged and over-aged alloy were analyzed. such a study will provide novel ideas for preparing low-cost and high-performance magnesium alloys.
The raw materials applied for preparing the alloy included pure Mg (99.95%), pure Zn (99.95%), pure Sn (99.99%) and pure Cu (99.99%), which were melted in a medium frequency induction furnace. A mixture of argon and tetrafluoroethane (Ar: CH2FCF3 = 20:1) was introduced in the melting to protect the melt, the final size of the ingot reached Φ100 × 360 mm. The element content of the ingots was determined with Inductively Coupled Plasma-Atomic Emission Spectrometry (ICP-AES), and the results are listed in Table 1. The ingots were homogenized at 335°C−24h + 420°C−24h and then extruded at 370 °C at an extrusion speed of 0.6 mm/s as well as an extrusion ratio of 23:1. The final extruded bar with a diameter of 25 mm was obtained. The alloy was aged at 180°C under an aging period of 0–100 h.
The microstructure of the alloy was explored under an optical microscope (OM, Carl Zeiss Axiovet2000MAT), a field emission scanning electron microscope (FE-SEM, JEOL JSM-7600), an X-ray diffractometer (XRD, Smartlab), as well as a transmission electron microscope (TEM, Tecnai G2 F20). JEOL JSM-7900F equipped with an electron backscattered diffraction (EBSD) system was used to analyze the texture of the alloy. The etchant for the alloy is a mixture of ethanol (l0 ml) + picric acid (0.3 g) + glacial acetic acid (1 ml) + distilled water (1 ml). EBSD samples were electropolished in a 10% nitric acid alcohol solution. The average grain size of the alloy was determined by the linear intercept method. The tensile properties for the different state alloy were obtained by a SANS universal testing machine. Cylindrical samples of diameter 5 mm and gauge length 25 mm were used for tensile tests. Three tensile tests were performed, and the strength and elongation were taken as the mean value. A Brinell hardness tester (HBS 62.5) was employed to examine the hardness of the alloy during aging. The load during the test was 30 kg and the loading time was 25 s. Each sample was tested five times, and the average hardness value was taken. The electrical conductivity of the alloy was tested with a WD-Z eddy current conductivity tester, with the respective sample being tested five times, and the final result was taken as the mean value. The standard coaxial cable method was employed to measure the electromagnetic shielding properties of the different state alloys. The electromagnetic shielding test equipment involved an E6063A vector network analyzer and a DR-S04 micro-coaxial shield effectiveness tester. The samples were taken from the cross-section of the bar, with a diameter of 20 mm and a thickness of 0.9 mm. The electromagnetic wave frequency range of the test was 30–1500 MHz. Each sample was tested five times, and the final shielding effectiveness was taken as its average value.
The XRD patterns of the as-cast and as-homogenized alloys are illustrated in Figure 1. α-Mg, MgZnCu phase, Mg2Sn phase and Mg2Zn3 phase are found in the as-cast alloy. After the homogenization treatment, the diffraction peaks belonging to the Mg2Sn and Mg2Zn3 phases disappear, and only the diffraction peak of the MgZnCu phase existed except for the α-Mg, which demonstrates that the homogenization can make the Mg2Sn and Mg2Zn3 phases decompose, and the Zn and Sn atoms dissolve back into the matrix, while the MgZnCu phase is not decomposed.
Figure 2 presents the SEM images of the as-cast and as-homogenized alloys. As indicated from the low magnification SEM image (Figure 2A), the as-cast alloy displays a typical petal-like dendritic structure, with the eutectic compounds primarily distributed on the grain boundaries. As suggested from the high magnification SEM image (Figure 2B), the eutectic compounds are mainly skeletal and massive in shape. The results of the EDS composition analysis of the eutectic compounds at different locations (marked as A, B, and C in Figure 2B) are listed in Table 2. Given the EDS and XRD results, the skeletal phase is the MgZnCu phase and the bulk phase refers to the Mg2Sn phase or Mg2Zn3 phase. Figure 2C shows that the dendritic morphology of the alloy disappears after homogenization, the segregation of elements at the grain boundaries is noticeably reduced and the eutectic compounds are largely decomposed, but some of the granular or lumpy phases remain at the grain boundaries. Given the XRD results, the residual second phase is the MgZnCu phase (Figure 2D), which is a thermally stable phase that fails to decompose during homogenization.
FIGURE 2. SEM images of as-cast and as-homogenized alloys: (A,B) as-cast alloy, (C,D) as-homogenized alloy.
Figure 3 presents the XRD pattern, OM and SEM images of the extruded alloy. XRD pattern reveals that the Mg2Sn phase appears in the extruded alloy besides the MgZnCu phase and the α-Mg, thereby indicating that the dynamic precipitation of the Mg2Sn phase occurs in the extrusion (Figure 3A). Figure 3B shows that complete dynamic recrystallization (DRX) takes place in the extrusion, and the dynamically recrystallized grains are equiaxed with an average size of approximately 39 μm. As indicated in Figure 3C, besides the broken MgZnCu phase, there are also numerous dispersed spot phases in the alloy. Combined with the XRD results, it can be concluded that the phase is the Mg2Sn phase.
FIGURE 3. X-ray diffraction pattern and microstructure images of the extruded alloy: (A) XRD pattern, (B) OM image, (C) SEM image (inset: high magnification SEM image of the precipitated phase).
For the extruded alloy, texture also affects its properties. The inverse pole figure of the extruded alloy (Figure 4A) reveals that it exhibits a basal fiber texture, in which the
FIGURE 4. Inverse pole figure, Schmid factor map, and Schmid factor distribution of the extruded alloy: (A) inverse pole figure (inset: ED inverse pole figure), (B) Schmid factor map, (C) Schmid factor distribution.
TEM images of the extruded alloy are presented in Figure 5. The larger phase can be identified as the MgZnCu phase (Figure 5A). Figure 5B indicates that the dynamically precipitated Mg2Sn phase is spherical, distributed near the grain boundaries, with sizes ranging from 200–500 nm. SEAD pattern of the phase reveals it has a face-centered cubic structure (FCC, a = 0.6763 nm) (Figure 5C). Moreover, a certain number of dislocations in the alloy are observed in the TEM bright-field image (Figure 5D).
FIGURE 5. TEM images of the extruded alloy: (A) MgZnCu phase (inset: SEAD pattern of MgZnCu phase), (B) distribution of Mg2Sn phase, (C) Mg2Sn phase (inset: SEAD pattern of Mg2Sn phase), (D) dislocations in the alloy.
The precipitation of the Mg2Sn phase is closely related to the deformation temperature and the stress state during the deformation process. The eutectic temperature of Mg-Sn is 567°C, and the solid solubility of Sn increases with the rise of the temperature (Ghosh et al., 2012). With the deformation temperature lower than the homogenization temperature, the Mg2Sn phase exerts a certain precipitation driving force. In addition, the compressive stress in the extrusion process also facilitates the precipitation of the Mg2Sn phase (Kabir et al., 2014). Accordingly, under the combined effect of temperature and stress, the Mg2Sn phase with a high eutectic temperature can precipitate from the matrix. The statically precipitated Mg2Sn phase has a range of forms, whereas the dynamically precipitated Mg2Sn phase during extrusion is subjected to stress, thereby leading to its spherical precipitation. In addition, it has been shown that Zn elements can reduce the activation energy of the Mg2Sn phase nucleation by reducing the interfacial energy at the Mg2Sn-Mg interface, thus promoting the precipitation of the Mg2Sn phase (Sasaki et al., 2011; Liu et al., 2016). Zn elements solid dissolved in the matrix during homogenization undoubtedly facilitate the precipitation of the Mg2Sn phase. The precipitated Mg2Sn, in turn, hinders the growth of recrystallized grains (Sasaki et al., 2008), thereby improving the mechanical properties of the alloy.
Figure 6 presents the changes in hardness and electrical conductivity of the extruded alloy during aging at 180°C. The hardness of the alloy increases rapidly first and then decreases with time, reaching a peak at 6 h. Compared with the extruded alloy, the hardness of the peak-aged alloy increases significantly, which demonstrates a strong aging strengthening effect. At the early stage of aging, the second phase gradually precipitates, and the phase density increases. The denser the phase is distributed, the stronger its resistance to dislocation motion (Kim and Park, 2016). Therefore, the hardness of the alloy continues to increase until reaches its peak. With the extension of time, the size of the precipitated phase increases, leading to a decrease in dislocation hindrance efficiency and a drop in hardness. In addition, the electrical conductivity of the alloy rises continuously over time. This is because the scattering effect of the second phase on the electrons is significantly weaker than that of the solid solution atoms (Pan et al., 2013). As the second phase continues to precipitate, the content of solute solution atoms in the matrix is reduced, the lattice distortion of the matrix declines, the chance of being scattered during electron transport is lowered, and the conductivity of the alloy increases continuously.
FIGURE 6. Curves of hardness and electrical conductivity of the extruded alloy during aging at 180°C.
Figure 7 gives TEM images of the peak-aged alloy. Considerable rod-shaped phases precipitate in the alloy, complying with the long axis of
FIGURE 7. TEM images of peak-aged alloy (180°C–6 h): (A) Bright-field TEM image of peak-aged alloy, taken along the
Figure 8 illustrates the TEM images of the over-aged alloy. Both the β′1 and β′2 phases grow significantly with the prolonging of the aging time, and the β′1 phase is converted into a slender rod shape (Figure 8A). Moreover, the β′2 phase is observed to be disk-shaped from the
FIGURE 8. TEM images of over-aged alloy (180°C–100 h): (A) Bright-field TEM image of over-aged alloy, taken along the
The room temperature tensile mechanical properties of the extruded, peak-aged and over-aged alloys are illustrated in Figure 9. The tensile strength, yield strength and elongation of the extruded alloy reach 319 MPa, 298 MPa and 13%, respectively. The tensile and yield strengths of the peak-aged alloy substantially increase compared with the extruded alloy, with the tensile strength increasing by 47 MPa and the yield strength by 60 MPa, whereas the elongation is reduced to only 7%. In comparison with the peak-aged alloy, the mechanical properties of the over-aged alloy are reduced, to be specific, the tensile strength is reduced to 337 MPa, the yield strength declines to 308 MPa, and the elongation is approximately 6%.
Many factors are affecting the mechanical properties of the alloy. For the extruded alloy, complete dynamic recrystallization takes place, forming recrystallized grain structure, which can be the basis for high mechanical properties. Secondly, considerable Zn atoms are solid dissolved in the extruded alloy. The solid dissolved Zn atoms interact with dislocation, hindering dislocation movement and improving the mechanical properties of the alloy. In addition, the size of the Mg2Sn phase precipitated during extrusion ranges from 200 to 500 nm, thereby exerting a small effect on dislocation, whereas it can hinder the sliding of grain boundaries and thus improve the mechanical properties of the alloy. Lastly, the extruded alloy develops a strong fiber texture with the basal plane (0001)//ED. When the alloy is deformed under the tensile stress in the ED, the Schmid factor (SF) along the basal plane equaled to 0, and the basal slip is difficult to activate, thereby improving the yield strength of the alloy (Chen et al., 2005; Wu et al., 2020; Li et al., 2021). In general, the high mechanical properties of the extruded alloy are attributed to the combined strengthening mechanisms (e.g., grain refinement, solid solution strengthening, precipitation strengthening, as well as texture strengthening). For the peak-aged alloys, the fine and dense short rod-like β′1 phase precipitates along with the
To analyze the fracture mode of the extruded, peak-aged and over-aged alloys, SEM images of fracture surfaces for these alloys are illustrated in Figure 10. There are a certain amount of dimples in the fracture surface of the extruded alloy; moreover, part of the cleavage planes and tearing ridges are founded, so a ductile-brittle mixed fracture mode is presented (Figure 10A). The number of dimples in the peak-aged alloy (Figure 10C) decreases significantly compared with that of extruded alloy, and the cleavage plane rises, which demonstrates that the plasticity of the alloy decreases, as reflected in a decrease in the elongation. The smooth cleavage plane in the over-aged alloy (Figure 10E) further increases, and dimples are hardly visible, which demonstrates that the fracture mechanism of the over-aged alloy is characterized by the brittle fracture mode. In addition, as indicated from the high-magnification BEI images of fracture surfaces for the extruded, peak-aged and over-aged alloys (Figures 10B,D,F), some MgZnCu phases are distributed at the bottom of dimples, and the MgZnCu phases are partially broken. In addition, precipitated Mg2Sn phase during extrusion is also observed, mainly distributed near the dimple. The MgZnCu phase is brittle (Cheng et al., 2014), its presence accounts for the fracture failure of the alloy. When the alloy is subjected to external forces, stress concentration will occur near the MgZnCu phase, and MgZnCu particles can be the nucleation sites of microcracks formed by a void nucleation and coalescence mechanism (Zhu et al., 2011), eventually leading to the fracture failure of the alloy.
FIGURE 10. SEM images of fracture surfaces for different state alloy: (A,B) extruded alloy, (C,D) peak-aged alloy, (E,F) over-aged alloy.
Figure 11 presents the frequency dependence of EMI shielding performance of the extruded, peak-aged and over-aged alloys. In the frequency range of 30–1500 MHz, the electromagnetic shielding effectiveness of the alloys gradually decreases with the increase in the electromagnetic wave frequency. The shielding efficiency of the extruded alloy exceeds 95 dB throughout the whole range, while the peak-aged alloy exhibits a significantly higher shielding efficiency than the extruded alloy, higher than 105 dB throughout the range. Moreover, the over-aged alloy exhibits a lower shielding performance compared with the peak-aged alloy, with a shielding efficiency between 97 and 112 dB, which can still be better than that of the extruded alloy. The peak-aged alloy exhibits the optimal electromagnetic shielding performance. Table 3 gives a comparison of tensile strengths and SE results of the studied alloy with other alloys in the literature. Obviously, the alloys obtained in this paper have excellent comprehensive performance.
TABLE 3. Comparison of tensile strengths and SE results between the studied alloys and alloys in the literature.
According to the transmission line theory, the attenuation of electromagnetic waves by a shield is achieved by three mechanisms, i.e., reflection attenuation, absorption attenuation and multiple reflection attenuation. The electromagnetic shielding efficiency can be calculated by the following equations (Schulz et al., 1988; Tong, 2009).
where A denotes the absorption attenuation; R represents the reflection attenuation; M expresses the multiple reflection attenuation;
FIGURE 12. Schematic diagram of the electromagnetic shielding mechanism: (A) reflection attenuation, absorption attenuation and multiple reflection attenuation, (B) multiple reflection attenuation of different second phases for electromagnetic waves.
The electrical conductivity for the extruded, peak-aged and over-aged alloy are 11.7 Ms/m, 12.4 Ms/m, 13.5 Ms/m, respectively. Notably, the conductivity of the alloy increases after aging treatment, whereas the electromagnetic shielding performance exhibited by the alloy fails to increase monotonically with the increase in conductivity. Thus, electrical conductivity can not be a single factor affecting the electromagnetic shielding performance of the alloy, and the transmission line theory has certain limitations. The effect of the fine structure of the alloy on its electromagnetic shielding performance should be further considered. In general, the conductivity of the precipitated phase is significantly lower than that of the matrix, and there is a serious impedance mismatch at the interface between the precipitated phase and the matrix. Thus, electromagnetic waves will be reflected when reaching the phase interface. Accordingly, the precipitation of Mg2Sn, β′1 and β′2 phases will remarkably increase the phase interface in the alloy, and the multiple reflections of electromagnetic waves will be noticeably enhanced as they advance in the alloy, thereby improving the electromagnetic shielding performance of the alloy (Chen et al., 2015a; Wang et al., 2020). The diagram of the multiple reflections of electromagnetic waves for different second phases is presented in Figure 12B. As obviously indicated from the figure, the precipitation of the dense β′1 phase in the peak-aged alloy results in a significant increase in the proportion of phase interface area in the alloy, thereby endowing the alloy with excellent electromagnetic shielding properties. After the aging period is extended to 100h, the electromagnetic shielding performance of the over-aged alloy decreases compared with the peak-aged alloy, which demonstrates that the size of the precipitated phase also impacts the electromagnetic shielding performance of the alloy. As illustrated in Figure 12B, the size of the β′1 phase increases significantly in the over-aged alloy. The phase interface in the over-aged alloy is significantly reduced compared with the peak-aged alloy, and the multiple reflection attenuation of the precipitated phase on the electromagnetic waves is correspondingly weakened (Chen et al., 2013), so the electromagnetic shielding performance of the over-aged alloy decreased. The factors influencing the electromagnetic shielding performance of the alloy are complex, whereas it can be generally conducive to obtaining the alloy exhibiting high electromagnetic shielding properties through appropriate alloy composition design combined with deformation and heat treatment means to endow the alloy with higher electrical conductivity and more reflective interfaces.
The microstructure, mechanical properties and electromagnetic shielding properties exhibited by Mg-6Zn-3Sn-0.5Cu alloy are explored, and possible shielding mechanisms and strengthening mechanisms are analyzed. The conclusions are drawn below:
1) The phases in the as-cast alloy are comprised of α-Mg, MgZnCu, Mg2Sn, and Mg2Zn3 phases. During homogenization, only the MgZnCu phase remains. Complete dynamic recrystallization (DRX) takes place in the extrusion, and the spherical Mg2Sn phase precipitates dynamically. Considerable β′1 phase along [0001]Mg precipitates in the peak-aged alloy. The size of the β′1 phase increases as the aging time is prolonged.
2) The mechanical properties of the peak-aged alloy are improved compared to the extruded alloy due to the strengthening effect of the β′1 phase, with a tensile strength of 366 MPa and elongation of 7%. The mechanical properties of the over-aged alloy decrease as the strengthening effect of β′1 is weakened. The fracture mode of the extruded and peak-aged alloys can be a ductile-brittle mixed fracture, and the over-aged alloy is a brittle fracture mode.
3) The electromagnetic shielding performance of the aged alloy is improved in comparison with the extruded alloy. The growth of precipitates results in a decrease in the electromagnetic shielding property of the over-aged alloy. The peak-aged alloy exhibits the optimal electromagnetic shielding performance, with the shielding effectiveness exceeds 105 dB in the 30–1,500 MHz frequency.
The raw data supporting the conclusion of this article will be made available by the authors, without undue reservation.
YHL and MM contributed conception and design of the study. YHL organized the database and analytic results and wrote the draft of the manuscript. All authors participated in the preparation of the material. YHL and MM did the writing-review and editing.
This study was financially supported by The Project of Achievement Transformation of Jiangsu Province (BA2017044).
Authors YHL, MM, XL, YJL, GS, JY, and KZ were employed by the company GRINM Co., Ltd. Authors YHL, MM, XL, YJL, GS, JY, and KZ were employed by the company GRIMAT Engineering Institute Co., Ltd. Authors YHL, MM, XL, YJL, GS, JY, and KZ were employed by the company General Research Institute for Nonferrous Metals.
All claims expressed in this article are solely those of the authors and do not necessarily represent those of their affiliated organizations, or those of the publisher, the editors and the reviewers. Any product that may be evaluated in this article, or claim that may be made by its manufacturer, is not guaranteed or endorsed by the publisher.
Ali, Y., Qiu, D., Jiang, B., Pan, F., and Zhang, M.-X. (2015). Current Research Progress in Grain Refinement of Cast Magnesium Alloys: A Review Article. J. Alloys Comp. 619, 639–651. doi:10.1016/j.jallcom.2014.09.061
Alizadeh, R., Wang, J., and Llorca, J. (2021). Precipitate Strengthening of Pyramidal Slip in Mg-Zn Alloys. Mater. Sci. Eng. A 804, 140697. doi:10.1016/j.msea.2020.140697
Chen, X., Liu, J., and Pan, F. (2013). Enhanced Electromagnetic Interference Shielding in ZK60 Magnesium alloy by Aging Precipitation. J. Phys. Chem. Sol. 74, 872–878. doi:10.1016/j.jpcs.2013.02.003
Chen, X., Liu, J., Zhang, Z., and Pan, F. (2012). Effect of Heat Treatment on Electromagnetic Shielding Effectiveness of ZK60 Magnesium alloy. Mater. Des. 42, 327–333. doi:10.1016/j.matdes.2012.05.061
Chen, X., Liu, L., Liu, J., and Pan, F. (2015). Microstructure, Electromagnetic Shielding Effectiveness and Mechanical Properties of Mg-Zn-Y-Zr Alloys. Mater. Des. (1980-2015) 65, 360–369. doi:10.1016/j.matdes.2014.09.034
Chen, X., Liu, L., Pan, F., Mao, J., Xu, X., and Yan, T. (2015). Microstructure, Electromagnetic Shielding Effectiveness and Mechanical Properties of Mg-Zn-Cu-Zr Alloys. Mater. Sci. Eng. B 197, 67–74., doi:10.1016/j.mseb.2015.03.012
Chen, Z. H., Xia, W. J., Cheng, Y. Q., and Fu, D. F. (2005). Texture and Anisotropy in Magnesium Alloys. Chin. J. Nonferrous Met. 15, 1–11. doi:10.3321/j.issn:1004-0609.2005.01.001
Cheng, L., Shuai, Z., Yu, Z., Da-Wei, Z., Chao-Zheng, H., and Zhi-Wen, L. (2014). Insights into Structural and Thermodynamic Properties of the Intermetallic Compound in Ternary Mg-Zn-Cu alloy under High Pressure and High Temperature. J. Alloys Comp. 597, 119–123. doi:10.1016/j.jallcom.2014.01.210
García, A. M., Sisternas, A., and Hoyos, S. P. (2008). Occupational Exposure to Extremely Low Frequency Electric and Magnetic fields and Alzheimer Disease: a Meta-Analysis. Int. J. Epidemiol. 37, 329–340. doi:10.1093/ije/dym295
Geetha, S., Satheesh Kumar, K. K., Rao, C. R. K., Vijayan, M., and Trivedi, D. C. (2009). EMI Shielding: Methods and Materials-A Review. J. Appl. Polym. Sci. 112, 2073–2086. doi:10.1002/app.29812
Ghosh, P., Mezbahul-islam, M., and Medraj, M. (2012). Critical Assessment and Thermodynamic Modeling of Mg-Zn, Mg-Sn, Sn-Zn and Mg-Sn-Zn Systems. Calphad 36, 28–43. doi:10.1016/j.calphad.2011.10.007
Kabir, A. S. H., Sanjari, M., Su, J., Jung, I.-H., and Yue, S. (2014). Effect of Strain-Induced Precipitation on Dynamic Recrystallization in Mg-Al-Sn Alloys. Mater. Sci. Eng. A 616, 252–259. doi:10.1016/j.msea.2014.08.032
Kim, J. T., Park, C. W., and Kim, B.-J. (2017). A Study on Synergetic EMI Shielding Behaviors of Ni-Co alloy-coated Carbon Fibers-Reinforced Composites. Synth. Met. 223, 212–217. doi:10.1016/j.synthmet.2016.11.027
Kim, S.-H., and Park, S. H. (2016). Influence of Ce Addition and Homogenization Temperature on Microstructural Evolution and Mechanical Properties of Extruded Mg-Sn-Al-Zn alloy. Mater. Sci. Eng. A 676, 232–240. doi:10.1016/j.msea.2016.08.093
Li, R. G., Li, H. R., Pan, H. C., Xie, D. S., Zhang, J. H., Fang, D. Q., et al. (2021). Achieving Exceptionally High Strength in Binary Mg-13Gd alloy by strong Texture and Substantial Precipitates. Scripta Materialia 193, 142–146. doi:10.1016/j.scriptamat.2020.10.052
Liu, C., Chen, H., and Nie, J.-F. (2016). Interphase Boundary Segregation of Zn in Mg-Sn-Zn Alloys. Scripta Materialia 123, 5–8. doi:10.1016/j.scriptamat.2016.05.035
Liu, C., Chen, X., Chen, J., Atrens, A., and Pan, F. (2020). The Effects of Ca and Mn on the Microstructure, Texture and Mechanical Properties of Mg-4 Zn alloy. J. Magnesium Alloys 9, 1084–1097. doi:10.1016/j.jma.2020.03.012
Pan, H., Pan, F., Peng, J., Gou, J., Tang, A., Wu, L., et al. (2013). High-conductivity Binary Mg-Zn Sheet Processed by Cold Rolling and Subsequent Aging. J. Alloys Comp. 578, 493–500. doi:10.1016/j.jallcom.2013.06.082
Pandey, R., Tekumalla, S., and Gupta, M. (2019). Enhanced (X-Band) Microwave Shielding Properties of Pure Magnesium by Addition of Diamagnetic Titanium Micro-particulates. J. Alloys Comp. 770, 473–482. doi:10.1016/j.jallcom.2018.08.147
Qi, F., Zhang, D., Zhang, X., and Xu, X. X. (2014). Effect of Sn Addition on the Microstructure and Mechanical Properties of Mg-6Zn-1Mn (wt.%) alloy. J. Alloys Compd. 585, 656–666. doi:10.1016/j.jallcom.2013.09.156
Rashkova, B., Prantl, W., Görgl, R., Keckes, J., Cohen, S., Bamberger, M., et al. (2008). Precipitation Processes in a Mg-Zn-Sn alloy Studied by TEM and SAXS. Mater. Sci. Eng. A 494, 158–165. doi:10.1016/j.msea.2008.04.005
Ren, Y., Liu, B., Xie, H., Li, H., Jiang, M., and Qin, G. (2021). Characterization of Precipitates in Aged Mg-4 wt%Zn alloy. Mater. Today Commun. 26, 102017. doi:10.1016/j.mtcomm.2021.102017
Rosalie, J. M., and Pauw, B. R. (2014). Form-free Size Distributions from Complementary Stereological TEM/SAXS on Precipitates in a Mg-Zn alloy. Acta Materialia 66, 150–162. doi:10.1016/j.actamat.2013.11.029
Sasaki, T. T., Oh-ishi, K., Ohkubo, T., and Hono, K. (2011). Effect of Double Aging and Microalloying on the Age Hardening Behavior of a Mg-Sn-Zn alloy. Mater. Sci. Eng. A 530, 1–8. doi:10.1016/j.msea.2010.05.010
Sasaki, T. T., Yamamoto, K., Honma, T., Kamado, S., and Hono, K. (2008). A High-Strength Mg-Sn-Zn-Al alloy Extruded at Low Temperature. Scripta Materialia 59, 1111–1114. doi:10.1016/j.scriptamat.2008.07.042
Schulz, R. B., Plantz, V. C., and Brush, D. R. (1988). Shielding Theory and Practice. IEEE Trans. Electromagn. Compat. 30, 187–201. doi:10.1109/15.3297
Shahzad, F., Alhabeb, M., Hatter, C. B., Anasori, B., Man Hong, S., Koo, C. M., et al. (2016). Electromagnetic Interference Shielding with 2D Transition Metal Carbides (MXenes). Science 353, 1137–1140. doi:10.1126/science.aag2421
Shen, B., Zhai, W., Tao, M., Ling, J., and Zheng, W. (2013). Lightweight, Multifunctional polyetherimide/graphene@Fe3O4 Composite Foams for Shielding of Electromagnetic Pollution. ACS Appl. Mater. Inter. 5, 11383–11391. doi:10.1021/am4036527
Tong, X. C. (2009). Advanced Materials and Design for Electromagnetic Interference Shielding. CRC Press, Taylor & Francis Group.
Wang, C., Luo, T., Liu, Y., Huang, Q., and Yang, Y. (2021). Residual Stress and Precipitation of Mg-5Zn-3.5Sn-1Mn-0.5Ca-0.5Cu alloy with Different Quenching Rates. J. Magnesium Alloys 9, 604–612. doi:10.1016/j.jma.2020.02.021
Wang, J., Wu, R., Feng, J., Zhang, J., Hou, L., and Zhang, M. (2019). Influence of Rolling Strain on Electromagnetic Shielding Property and Mechanical Properties of Dual-phase Mg-9Li alloy. Mater. Characterization 157, 109924. doi:10.1016/j.matchar.2019.109924
Wang, J., Xu, L., Wu, R., Feng, J., Zhang, J., Hou, L., et al. (2020). Enhanced Electromagnetic Interference Shielding in a Duplex-phase Mg-9Li-3Al-1Zn Alloy Processed by Accumulative Roll Bonding. Acta Metall. Sin. (Engl. Lett. 33, 490–499. doi:10.1007/s40195-020-01017-z
Wang, Y., Peng, J., and Zhong, L. (2018). On the Microstructure and Mechanical Property of As-Extruded Mg-Sn-Zn alloy with Cu Addition. J. Alloys Comp. 744, 234–242. doi:10.1016/j.jallcom.2018.02.013
Wei, S., Zhu, T., Hodgson, M., and Gao, W. (2013). Effects of Sn Addition on the Microstructure and Mechanical Properties of As-Cast, Rolled and Annealed Mg-4Zn Alloys. Mater. Sci. Eng. A 585, 139–148. doi:10.1016/j.msea.2013.07.051
Wu, J., Jin, L., Dong, J., Wang, F., and Dong, S. (2020). The Texture and its Optimization in Magnesium alloy. J. Mater. Sci. Tech. 42, 175–189. doi:10.1016/j.jmst.2019.10.010
Yang, Y., Xiong, X., Chen, J., Peng, X., Chen, D., and Pan, F. (2021). Research Advances in Magnesium and Magnesium Alloys Worldwide in 2020. J. Magnesium Alloys 9, 705–747. doi:10.1016/j.jma.2021.04.001
Ye, J., Chen, X., Luo, Z., Li, J., Yuan, Y., Tan, J., et al. (2021). Improving Strength and Electromagnetic Shielding Effectiveness of Mg-Sn-Zn-Ca-Ce Alloy by Sn Addition. Adv. Eng. Mater. 23, 2100166. doi:10.1002/adem.202100166
You, S., Huang, Y., Kainer, K. U., and Hort, N. (2017). Recent Research and Developments on Wrought Magnesium Alloys. J. Magnesium Alloys 5, 239–253. doi:10.1016/j.jma.2017.09.001
Keywords: Mg-Zn-Sn-Cu alloy, extrusion, aging treatment, mechanical properties, electromagnetic shielding properties
Citation: Liu YH, Ma ML, Li XG, Li YJ, Shi GL, Yuan JW and Zhang K (2021) Research on Microstructure, Mechanical Properties and Electromagnetic Shielding Properties of Mg-6Zn-3Sn-0.5Cu Alloy. Front. Mater. 8:778833. doi: 10.3389/fmats.2021.778833
Received: 17 September 2021; Accepted: 20 October 2021;
Published: 03 November 2021.
Edited by:
Lai-Chang Zhang, Edith Cowan University, AustraliaReviewed by:
Xiaodong Peng, Chongqing University, ChinaCopyright © 2021 Liu, Ma, Li, Li, Shi, Yuan and Zhang. This is an open-access article distributed under the terms of the Creative Commons Attribution License (CC BY). The use, distribution or reproduction in other forums is permitted, provided the original author(s) and the copyright owner(s) are credited and that the original publication in this journal is cited, in accordance with accepted academic practice. No use, distribution or reproduction is permitted which does not comply with these terms.
*Correspondence: Ming Long Ma, bWFtaW5nbG9uZ0BncmlubS5jb20=; Kui Zhang, emhrdWlAZ3Jpbm0uY29t
Disclaimer: All claims expressed in this article are solely those of the authors and do not necessarily represent those of their affiliated organizations, or those of the publisher, the editors and the reviewers. Any product that may be evaluated in this article or claim that may be made by its manufacturer is not guaranteed or endorsed by the publisher.
Research integrity at Frontiers
Learn more about the work of our research integrity team to safeguard the quality of each article we publish.