Corrigendum: Experimental Study on Mechanical Performance of Recycled Fine Aggregate Concrete Reinforced With Discarded Carbon Fibers
- Department of Civil Engineering, Military College of Engineering, National University of Sciences and Technology, Islamabad, Pakistan
With the development of technology in every field, it is necessary to recommend an eco-friendly material to be utilized in the construction industry. Recently, using waste/recycled materials in the concrete as a substitute is a trend to bring sustainability to the construction industry, but the recycled/waste materials has poor mechanical properties, thus to enhance these poor properties, this research studies the mechanical performance of sustainable concrete incorporating waste materials as aggregates, the study is performed in the three stages. In the first stage, the natural sand was substituted with recycled sand in the percentage of 0, 35, 70, and 100%, and all the tests i.e. compressive strength, split tensile strength and flexural strength were performed on concrete which was cured in water for 28 days. As the 35% substitution of natural sand with recycled fine aggregate presented the optimum mechanical performance, it was selected for the third stage of the research. In the second and the third stages, the discarded carbon fibers were utilized in concrete with 2, 4, and 6% by weight. A total of 90 samples were prepared for this research, in which 30 samples were cubes, 30 samples were cylinders and 30 samples were beams, all the samples were tested at 28 days. Comparative analysis was performed to validate and verify the results of this paper with the relevant literature. The SEM test was also performed on a fractured concrete surface to study its microstructure. The outcome of tests revealed that the utilization of discarded carbon fibers in concrete enhances compressive, split tensile and flexural strength by 27.8, 17.8, and 35.9% and acts as a crack bridging and also restrain the propagation of the first cracks. Fibers also helped the concrete to improve its energy absorption capacity and ductility.
Introduction
In recent years, the development of more infrastructure projects results in more waste from demolition and construction (Mohseni et al., 2017), particularly waste concrete. A large quantity of construction and demolition waste has formed severe issues for the environment (Wang et al., 2021). Thus, researchers (Ahmad Bhat, 2021) propose to utilize these construction and demolition waste to recycled waste materials to reduce the developing issue of landfills (Marinković et al., 2010). Substituting crushed stone aggregates with recycled concrete aggregates to diminish the reliance on material from natural resources is another economic and environmental advantage that can be obtained by utilizing recycled materials in concrete. Developed countries are facing problems regarding the lack of natural materials for construction (Cabral et al., 2010). Hence, the practice and utilization of RCA are getting dominant in a lot of nations presently. For example, Germany (Pepe et al., 2016) is ahead of all countries by developing recycled aggregates which are nearly 70 million tons. Netherlands, Australia, United Kingdom, and France produced recycled aggregate which is nearly 20, 10, 49, and 17 million tons, respectively (Tam, 2009). The author in a study (Dosho, 2007) revealed that Japan is recycling roughly 96% of concrete waste. The development and utilization of fiber-reinforced polymer have significantly risen in the industries of aerospace, automobile, and construction (Broekel and Scharr, 2005). Unique properties of fiber-reinforced polymer-based (Baena et al., 2016) materials for example high impact resistance, high strength to weight ratio, low maintenance, easy to use, corrosion resistance, and high fatigue resistance make them common material among the industry of civil engineering globally (Ahmad et al., 2021; Zaid et al., 2021a).
Carbon fibers enhance the mechanical aspect of the reinforced concrete. Though, the utilization (Baena et al., 2016) of virgin carbon fiber reinforced polymer is restricted because of its very few specific products due to its high cost. Because of the chemical stability of carbon fiber reinforced polymer sheets, it is not biodegradable (Mastali et al., 2016).
Furthermore, there are two methods (Das et al., 2018) for the waste management of carbon fiber reinforced polymer, burning and left in the fields. But these are not the cleverest way that could be adopted because of the hundreds and thousands of tons of carbon fiber reinforced polymer being unexploited annually worldwide (Zaid et al., 2021b). When carbon fiber reinforced polymer is burned, about 40–60% of residual fiber reinforced polymer materials will still need to be landfilled which leads to land pollution (Yazdanbakhsh and Bank, 2014).
Moreover, even though few studies focused on utilizing recycled materials in plain and reinforced concrete (Thomas et al., 2013; Jiang et al., 2014; Koenders et al., 2014; Yazdanbakhsh and Bank, 2014; High et al., 2015; Baena et al., 2016; Grabois et al., 2016; Mastali and Dalvand, 2016), there is still a very limited quantity of researches that are performed on reinforced concrete with waste carbon fiber reinforced polymer (Mastali and Dalvand, 2016; Nguyen et al., 2016). It is important to examine all characteristics of utilizing discarded carbon fiber reinforced polymer materials in various types of concrete for example concrete made from recycled aggregates which is the key aim of the present research.
The research on the mechanical aspects of self-compacting concrete strengthened with 3 proportions of carbon fiber reinforced polymer pieces (0.30, 0.60, and 0.90% by fraction of volume) shows that raising the number of recycled fibers enhances the flexural and compressive strength and impact resistance of samples (Mastali et al., 2016). Similarly, the workability of concrete reinforced with discarded carbon fiber reinforced polymer decreases, whereas used fibers with high length and volume enhance the mechanical characteristics, impact and crack resistance of concrete samples (Mastali et al., 2016). Authors in a study (Nguyen et al., 2016) revealed that, utilizing different kinds or amounts of discarded CFs have few merits and demerits. Concrete samples with discarded CFs reinforced polymer improved the compressive strength by 6–14%; though, a decrease in strength was observed when reclaimed carbon fibers were used. Furthermore, flexural strength was normally increased by 18%.
Confidently, the current research was performed to examine the mechanical performance of concrete made from recycled aggregate, which is called recycled aggregate concrete strengthened with discarded carbon fibers in chopped form. The study was performed in three stages; fine aggregate from recycled concrete was substituted with the river sand in the first stage in three substitution rates: 35, 70, and 100%. After that optimal substitution rate was designated for the sample, mix design for the next stage, which was comprised of three varying percentages of waste carbon fibers by weight (2, 4, and 6%) in recycled and natural aggregate concrete. To summarize, in this lab research, 90 samples were prepared in which each ten mix proportions involved three cube samples for compressive strength, three beams to evaluate flexural strength, and three cylindrical samples to assess split tensile strength of concrete. To study the microstructure in detail, a scanning electron microscope (SEM) test was performed on concrete reinforced with fibers.
Materials and Methods
Materials
General-purpose type-I OPC (Ordinary Portland Cement) per ASTM C150 (ASTM, 2015) was used for the current research. The physical and chemical characteristics of cement are provided in Table 1. The complete mix proportion of concrete samples in three stages is provided in Table 2. The mix IDs of all samples are designed in such a way that number next to “RFA” denotes the rate of substitution of recycled fine aggregate, and the number next to “CF” represents the rate of carbon fibers that are included. In the first stage, the concrete was made by substitution of natural sand with recycled fine aggregate with varying proportions such as (0, 35, 75, and 100%). Due to the difference in absorption values of natural and recycled fine aggregate, corrected water values were included in a concrete mix. In the second stage of research, discarded carbon fibers were included in normal concrete by (2, 4, and 6%) weight. In the third stage, 2, 4, and 6% of discarded carbon fibers were added by volume fraction with 35% replacement of natural sand with recycled fine aggregate, which was recognized as an optimum ratio in the first stage. To make a concrete flowable minimum amount of superplasticizer was also included in the concrete mixes.
Particle size distribution for fine and coarse aggregates is presented in Figure 1A,B. The maximum size for coarse aggregate was 25 mm. Waste pieces of carbon fibers were obtained from the leftover sheets of other researchers, which were then chopped to 3.5 cm in length as presented in Figure 2. The characteristics of carbon fibers are displayed in Table 3.
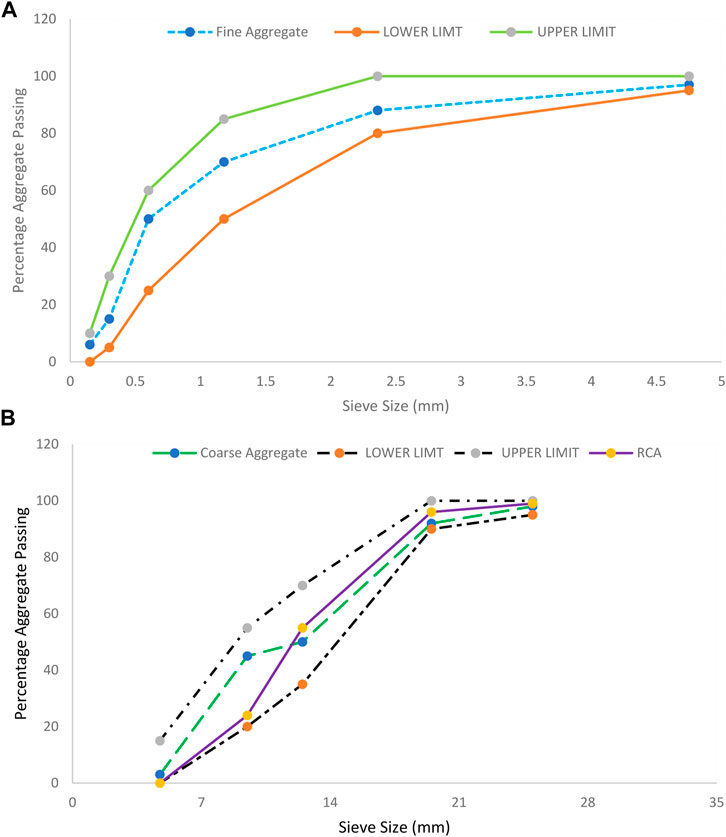
FIGURE 1. (A) Particle size distribution of fine aggregate, (B) Particle size distribution of fine aggregate.
Mixing Process
During the process of mixing, the first fine and coarse aggregates were mixed per ACI 211.1 (ACI 211.1, 1991). After that superplasticizer and cement were added, the mixture was blended for 10 min. To avoid balling phenomenon, the waste carbon fibers were added slowly to the mixture. Then slump test was conducted on all concrete specimens as per ASTM C 143 (ASTM C143/C143M-15a, 2015). All the concrete specimens with recycled aggregates, waste fibers, were prepared and cast following ASTM C31 (ASTM C31/C31M-17. A-C, 2017). The size of the cube mold was (100 mm × 100 mm x 100 mm), cylinder molds (200 mm × 100 mm), and the beam mold (100 mm × 100 mm x 500 mm). The samples were removed from the molds after 24 hours, and then they were kept in water at a temperature of 24°C for 28 days for its curing.
Test Method
Compressive Test
The compressive test was performed following ASTM C 39 (ASTM C39/C39M-17. A-C, 2017), thirty concrete cubes with a size of (100 × 100 × 100 mm3) were prepared for the compressive test at 28 days of curing. For every mix proportion, three concrete cubes were made. For the first stage the impact of the substitution of recycled aggregates, and as far as the second and the third stages, the influence of including fibers by (2, 4, and 6%) by volume fraction were examined. Control concrete compressive strength came out to be 53 MPa since recycled concrete with 35% of substitution didn’t display a significant reduction in compression capacity, it was specified as a primary mixture proportion utilized in the third stage of the study for including varying proportions of discarded carbon fibers.
Splitting Tensile Test
The splitting tensile test was performed following ASTM C 496 (ASTM C496/C496M-17. A-C, 2017), thirty concrete cylinders with a size of (100 × 200 mm) were prepared for the splitting tensile test at 28 days of curing. For every mixture proportion, three concrete cylinders were prepared, the average value of those three samples was taken as the final tensile capacity of concrete.
Flexural Test
To evaluate concrete bending behavior, a three-point bending test (see Figure 3A,B) was performed as per ASTM C 293 (293 AC, 2016). Thirty beams which had the dimension of (100 × 100 × 500 mm3) were prepared, the deflection at mid-span was recorded using (LVDT) displacement data logger. The load was applied on concrete beams at a rate of 0.6 mm/min.
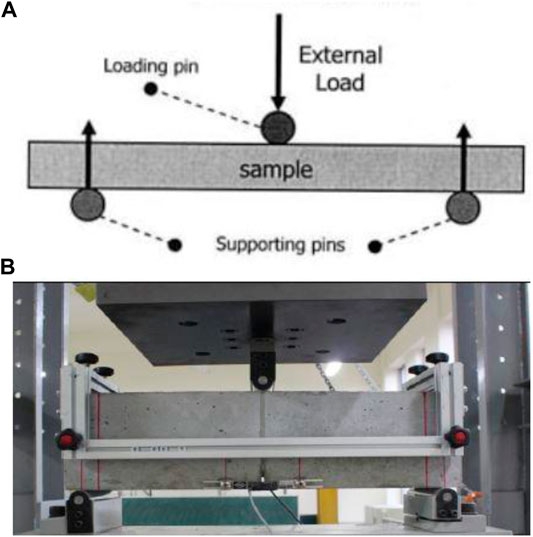
FIGURE 3. (A) Schematic diagram for flexural testing of samples. (B) Test setup for flexural strength of samples.
Experimental Results
Slump
A slump test was performed to assess the workability of concrete, its values are provided in Table 4 and Figure 4. From the slump test result, it was revealed that the inclusion of discarded carbon fibers reduces slump and hence reducing the concrete workability. These fibers could make a network structure in concrete that restrain concrete mix from flow and segregation. Moreover, because of the large surface area and high content of discarded carbon fibers, they could effortlessly absorb water from cement paste to wrap around, consequently enhancing recycled concrete aggregate viscosity. In the first stage, as the quantity of absorbed water for RAC raised, the slump also enhanced with it.
Compressive Strength
The compressive strength of all 3 stages of samples is presented in Figure 5. The compressive strength of the control sample was 53 MPa at 28 days of curing and when 100% of natural sand was substituted with recycled fine aggregate, the compressive strength was reduced by 25%, see Figure 5. The compressive strength of waste carbon fiber concrete with recycled fine aggregate and only waste carbon fiber concrete was 62 and 69 MPa, respectively. Likewise, the compressive strength was improved as we increased the dosage of fibers in concrete, see figure. When 6% of waste carbon fibers were added, the compressive strength touched 69 MPa, which is 36% higher than the same mix without fibers.
To validate and verify our research data with the present literature, comparative analysis was performed and statistical model was made, from Table 5 we can see that the current research falls between the present literature for the compressive strength at 28 days, and from Figure 6 it can be observed that the value of R square is close to unity which shows consistency in the values, therefore validating and verifying the results for the present research.
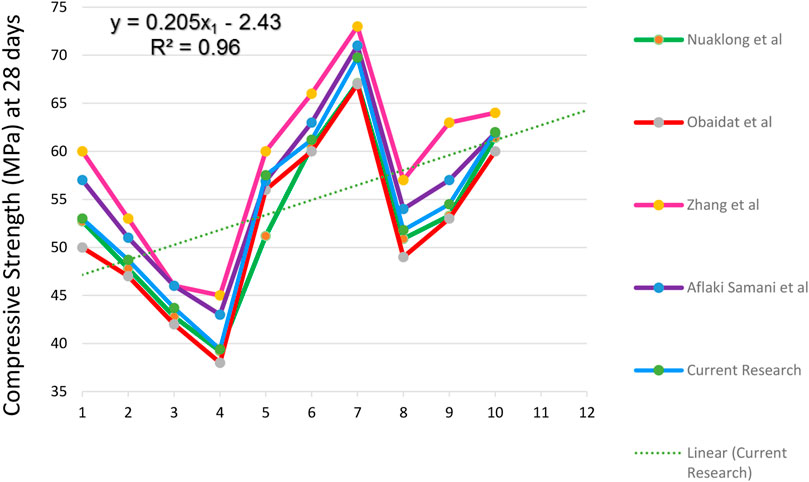
FIGURE 6. Comparative analysis of present literature and current research for compressive strength (MPa) at 28 days.
Splitting Tensile Strength
The splitting tensile strength of all three stages of samples is presented in a Figure 7. The splitting tensile strength of the control sample was 3.9 MPa and when 100% of natural fine aggregate was substituted with RFA, the splitting tensile strength came out to be 3.4 MPa. As shown in Figure 7, the highest splitting tensile strength that was obtained was 5.6 and 5.3 MPa for the RFA-0-CF-6 and RFA-35-CF-6 mix design, respectively. It is noticeable (Ferdosian and Camões, 2021) that with the addition of fibers the split tensile strength of the concrete improved significantly and prevents crack propagation. By adding more amount of waste carbon fibers to the concrete mix, the length and depth of the cracks will be reduced.
To validate and verify our research data with the present literature, comparative analysis was performed and statistical model was made, from Table 6 we can see that the current research falls between the present literature for the splitting tensile strength at 28 days, and from Figure 8 it can be observed that the value of R square is close to unity which shows consistency in the values, therefore validating and verifying the results for the present research.
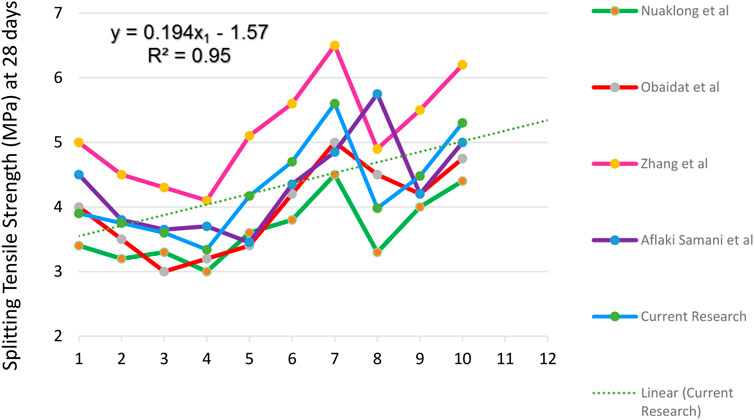
FIGURE 8. Comparative analysis of present literature and current research for splitting tensile strength (MPa) at 28 days.
Flexural Strength
The values for the bending point test of all three stages of samples are presented in Figure 9. When more quantity of natural fine aggregate was swapped with RFA, the flexural strength of concrete specimens was reduced, with 35, 70, and 100% substitution of natural fine aggregate was replaced with RFA, the flexural strength reduced by 4.1, 8.3, and 14.9%, respectively. Though, with increasing the percentage of fibers in concrete, the flexural strength raised to 7.1 MPa for mix design of RFA-0-CF-6. Figure 10 shows the load-displacement curve for the second and the third stages of concrete beams made of waste carbon concrete and waste carbon concrete with recycled sand. From Figure 10, it could be noticed that inclusion of discarded carbon fibers enhances the capacity of energy absorption and the ductility of samples. This was also (Kazmi et al., 2018) proved because of the sample’s elastic fractures. Control concrete samples and concrete samples with only recycled fine aggregate made for the split tensile and flexural test were all fractured in a brittle fashion, but when the waste carbon fibers were added to the concrete, they made the concrete more ductile and the fibers also helped by restraining the cracks propagation in concrete.
To validate and verify our research data with the present literature, comparative analysis was performed and statistical model was made, from Table 7 we can see that the current research falls between the present literature for the flexural strength at 28 days, and from Figure 11 it can be observed that the value of R square is close to unity which shows consistency in the values, therefore validating and verifying the results for the present research.
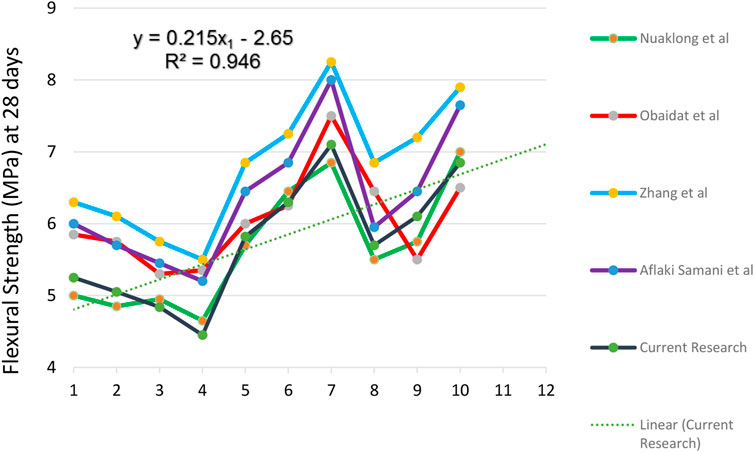
FIGURE 11. Comparative analysis of present literature and current research for flexural strength (MPa) at 28 days.
Bond Performance
From the concrete SEM images, it may be observed that the discarded carbon fibers are uniformly dispersed in the concrete matrix when the sample broke, the bond amid the mortar and the fibers made the fibers to be stretched and scratched. The micro openings that are formed when the concrete failed are presented in Figure 12, which show (Baena et al., 2016) the parting of the carbon fiber from the sample and indicates that the fibers’ mechanical strength is not utilized completely. Though, the existence of carbon fibers in samples enhances the split tensile, compression, and flexural capacity. When the concrete sample with waste carbon fibers was broken during the test see Figure 13, the role of crack bridging of carbon fibers was easily visible to the naked eye.
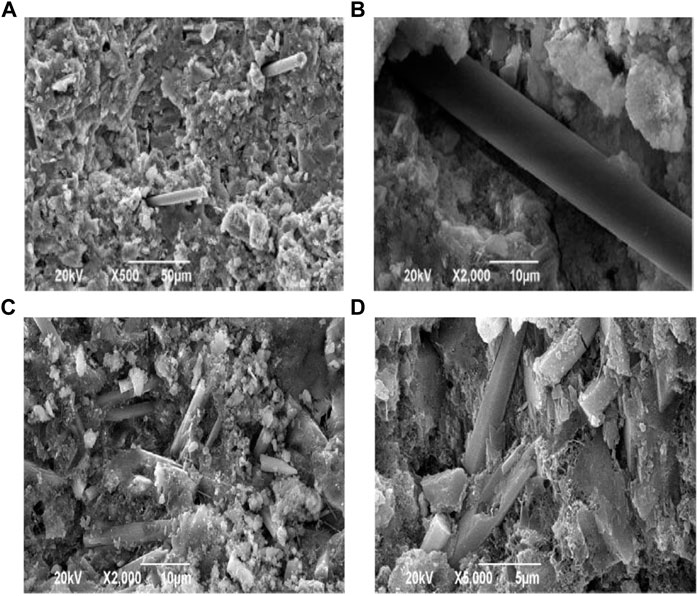
FIGURE 12. (A) Even dispersion of waste carbon fibers in cement mortar, (B) Scratches on deboned carbon fibers from the concrete, (C) marks on waste carbon fibers, (D) remaining marks of deboned carbon fibers.
Conclusion
The current experimental research examines the mechanical performance of concrete with recycled aggregate, concrete with discarded carbon fibers, and concrete with both recycled aggregate and discarded carbon fibers. The following conclusions were obtained from the study.
• The experimental study revealed that recycled concrete aggregate has a detrimental effect on concrete mechanical performance. Results exhibit that when 100% sand was substituted with recycled fine aggregate in concrete with no fibers, the split tensile and flexural strength was reduced by 14.2 and 14.9%, respectively. It is important to note that the detrimental effect of recycled fine aggregate on concrete compressive strength is more as compared to concrete split tensile and flexural strength.
• In the second stage, by adding waste carbon fibers, concrete achieved with more strength as compared to control concrete. Including 6% of discarded carbon fibers to concrete enhanced the compressive, split tensile and flexural strength by 31.2, 20.1, and 34.8%, respectively.
• In the third stage, the inclusion of 6% of discarded carbon fibers to concrete with 35% of recycled aggregate as a substitute for natural aggregate, improves the concrete compressive, split tensile and flexural strength by 27.8, 17.8, and 35.9%.
• The existence of fibers in concrete leads to a postponement in the arrival of the initial crack and averts the sample from being failed in a brittle fashion. From load-displacement figures, it can be also observed that the energy absorption capacity of control concrete and concrete with recycled materials is enhanced by utilizing discarded carbon fibers. The concrete mix design of RFA-0-CF-6 and RFA-35-CF-6 had the highest energy absorption capacity as compared to the other samples.
• From the scanning electron microscope (SEM) images of fiber concrete, it was observed that the fibers were dispersed uniformly in the concrete matrix.
• The detrimental impacts of substituting natural aggregates with recycled concrete aggregates can be remunerated by utilizing discarded carbon fibers which will improve the mechanical performance of recycled aggregate concrete.
• Utilizing recycled fine aggregates and waste carbon fibers in concrete will make the concrete economical since the materials used are recycled so their cost will reduce the overall concrete cost and it will also make the environment and the construction industry much more sustainable, and this green concrete will be a very suitable for structural application, which will pave the way for the sustainable construction of RC structures.
Data Availability Statement
The raw data supporting the conclusion of this article will be made available by the authors, without undue reservation.
Author Contributions
All authors listed have made a substantial, direct, and intellectual contribution to the work and approved it for publication.
Conflict of Interest
The authors declare that the research was conducted in the absence of any commercial or financial relationships that could be construed as a potential conflict of interest.
Publisher’s Note
All claims expressed in this article are solely those of the authors and do not necessarily represent those of their affiliated organizations, or those of the publisher, the editors and the reviewers. Any product that may be evaluated in this article, or claim that may be made by its manufacturer, is not guaranteed or endorsed by the publisher.
References
293 AC, 2016293 AC (2016). Standard Test Method for Flexural Strength of concrete (Using Simple Beam with Centerpoint Loading). West Conshohocken: ASTM International.
ACI 211.1 (1991). Standard Practice for Selecting Proportions for Normal, Heavyweight, and Mass Concrete (ACI 211.1-91). Quebec city: American Concrete Institute.
Aflaki Samani, M., and Jabbari Lak, S. (2019). Experimental Investigation on the Mechanical Properties of Recycled Aggregate Concrete Reinforced by Waste Carbon Fibers. Int. J. Environ. Sci. Technol. 16, 4519–4530. doi:10.1007/s13762-018-1855-z
Ahmad Bhat, J. (2021). Effect of Strength of Parent concrete on the Mechanical Properties of Recycled Aggregate concrete. Mater. Today Proc. 42, 1462–1469. doi:10.1016/j.matpr.2021.01.310
Ahmad, J., Zaid, O., Aslam, F., Shahzaib, M., Ullah, R., Alabduljabbar, H., et al. (2021). A Study on the Mechanical Characteristics of Glass and Nylon Fiber Reinforced Peach Shell Lightweight Concrete. Materials 14, 4488. doi:10.3390/ma14164488
ASTM (2015). C150 (ASTM) C150 (Standard Specification for Portland Cement). Quebec city: American Concrete Institute.
ASTM C143/C143M-15a (2015). Standard Test Method for Slump of Hydraulic-Cement Concrete. Quebec city: ASTM International.
ASTM C31/C31M-17. A-C (2017). Standard Practice for Making and Curing concrete Test Specimens in the Field. West Conshohocken: ASTM International.
ASTM C39/C39M-17. A-C (2017). Standard Test Method for Compressive Strength of Cylindrical concrete Specimens. West Conshohocken: ASTM International.
ASTM C496/C496M-17. A-C (2017). Standard Test Method for Splitting Tensile Strength of Cylindrical concrete Specimens. West Conshohocken: ASTM International.
Baena, M., Torres, L., Turon, A., Llorens, M., and Barris, C. (2016). Bond Behaviour between Recycled Aggregate concrete and Glass Fibre Reinforced Polymer Bars. Construction Building Mater. 106, 449–460. doi:10.1016/j.conbuildmat.2015.12.145
Broekel, J., and Scharr, G. (2005). The Specialities of Fibre-Reinforced Plastics in Terms of Product Lifecycle Management. J. Mater. Process. Technol. 162-163, 725–729. doi:10.1016/j.jmatprotec.2005.02.226
Cabral, A. E. B., Schalch, V., Molin, D. C. C. D., and Ribeiro, J. L. D. (2010). Mechanical Properties Modeling of Recycled Aggregate Concrete. Construction Building Mater. 24, 421–430. doi:10.1016/j.conbuildmat.2009.10.011
Das, C. S., Dey, T., Dandapat, R., Mukharjee, B. B., and Kumar, J. (2018). Performance Evaluation of Polypropylene Fibre Reinforced Recycled Aggregate Concrete. Construction Building Mater. 189, 649–659. doi:10.1016/j.conbuildmat.2018.09.036
Dosho, Y. (2007). Development of a Sustainable Concrete Waste Recycling System. J. Adv. Concr Technol. 5, 27–42. doi:10.3151/jact.5.27
Ferdosian, I., and Camões, A. (2021). Mechanical Performance and Post-Cracking Behavior of Self-Compacting Steel-Fiber Reinforced Eco-Efficient Ultra-high Performance concrete. Cement and Concrete Composites 121, 104050. doi:10.1016/j.cemconcomp.2021.104050
Grabois, T. M., Cordeiro, G. C., and Toledo Filho, R. D. (2016). Fresh and Hardened-State Properties of Self-Compacting Lightweight Concrete Reinforced with Steel Fibers. Construction Building Mater. 104, 284–292. doi:10.1016/j.conbuildmat.2015.12.060
High, C., Seliem, H. M., El-Safty, A., and Rizkalla, S. H. (2015). Use of basalt Fibers for concrete Structures. Construction Building Mater. 96, 37–46. doi:10.1016/j.conbuildmat.2015.07.138
Jiang, C., Fan, K., Wu, F., and Chen, D. (2014). Experimental Study on the Mechanical Properties and Microstructure of Chopped Basalt Fibre Reinforced Concrete. Mater. Des. 58, 187–193. doi:10.1016/j.matdes.2014.01.056
Kazmi, S. M. S., Munir, M. J., Wu, Y.-F., and Patnaikuni, I. (2018). Effect of Macro-Synthetic Fibers on the Fracture Energy and Mechanical Behavior of Recycled Aggregate concrete. Construction Building Mater. 189, 857–868. doi:10.1016/j.conbuildmat.2018.08.161
Koenders, E. A. B., Pepe, M., and Martinelli, E. (2014). Compressive Strength and Hydration Processes of concrete with Recycled Aggregates. Cement Concrete Res. 56, 203–212. doi:10.1016/j.cemconres.2013.11.012
Marinković, S., Radonjanin, V., Malešev, M., and Ignjatović, I. (2010). Comparative Environmental Assessment of Natural and Recycled Aggregate Concrete. Waste Manag. 30, 2255–2264. doi:10.1016/j.wasman.2010.04.012
Mastali, M., and Dalvand, A. (2016). The Impact Resistance and Mechanical Properties of Self-Compacting concrete Reinforced with Recycled CFRP Pieces. Composites B: Eng. 92, 360–376. doi:10.1016/j.compositesb.2016.01.046
Mastali, M., Dalvand, A., and Sattarifard, A. R. (2016). The Impact Resistance and Mechanical Properties of Reinforced Self-Compacting Concrete with Recycled Glass Fibre Reinforced Polymers. J. Clean. Prod. 124, 312–324. doi:10.1016/j.jclepro.2016.02.148
Mohseni, E., Saadati, R., Kordbacheh, N., Parpinchi, Z. S., and Tang, W. (2017). Engineering and Microstructural Assessment of Fibre-Reinforced Self-Compacting concrete Containing Recycled Coarse Aggregate. J. Clean. Prod. 168, 605–613. doi:10.1016/j.jclepro.2017.09.070
Nguyen, H., Carvelli, V., Fujii, T., and Okubo, K. (2016). Cement Mortar Reinforced with Reclaimed Carbon Fibres, CFRP Waste or Prepreg Carbon Waste. Construction Building Mater. 126, 321–331. doi:10.1016/j.conbuildmat.2016.09.044
Nuaklong, P., Wongsa, A., Boonserm, K., Ngohpok, C., Jongvivatsakul, P., Sata, V., et al. (2021). Enhancement of Mechanical Properties of Fly Ash Geopolymer Containing fine Recycled concrete Aggregate with Micro Carbon Fiber. J. Building Eng. 41, 102403. doi:10.1016/j.jobe.2021.102403
Obaidat, Y. T., Barham, W. S., and Abdelrahman, B. N. (2020). Effect of Elevated Temperature on the Bond Behavior between Near Surface Mounted-Carbon Fiber Reinforced Polymers Strips and Recycled Aggregate concrete. Construction Building Mater. 251, 118970. doi:10.1016/j.conbuildmat.2020.118970
Pepe, M., Toledo Filho, R. D., Koenders, E. A. B., and Martinelli, E. (2016). A Novel Mix Design Methodology for Recycled Aggregate Concrete. Construction Building Mater. 122, 362–372. doi:10.1016/j.conbuildmat.2016.06.061
Tam, V. W. Y. (2009). Comparing the Implementation of concrete Recycling in the Australian and Japanese Construction Industries. J. Clean. Prod. 17, 688–702. doi:10.1016/j.jclepro.2008.11.015
Thomas, C., Cimentada, A., Polanco, J. A., Setién, J., Méndez, D., and Rico, J. (2013). Influence of Recycled Aggregates Containing sulphur on Properties of Recycled Aggregate Mortar and concrete. Composites Part B: Eng. 45, 474–485. doi:10.1016/j.compositesb.2012.05.019
Wang, B., Yan, L., Fu, Q., and Kasal, B. (2021). A Comprehensive Review on Recycled Aggregate and Recycled Aggregate Concrete. Resour. Conservation Recycling 171, 105565. doi:10.1016/j.resconrec.2021.105565
Yazdanbakhsh, A., and Bank, L. (2014). A Critical Review of Research on Reuse of Mechanically Recycled FRP Production and End-Of-Life Waste for Construction. Polymers 6, 1810–1826. doi:10.3390/polym6061810
Zaid, O., Ahmad, J., Siddique, M. S., and Aslam, F. (2021). Effect of Incorporation of Rice Husk Ash Instead of Cement on the Performance of Steel Fibers Reinforced Concrete. Front. Mater. 8, 665625. doi:10.3389/fmats.2021.665625
Zaid, O., Ahmad, J., Siddique, M. S., Aslam, F., Alabduljabbar, H., and Khedher, K. M. (2021). A Step towards Sustainable Glass Fiber Reinforced Concrete Utilizing Silica Fume and Waste Coconut Shell Aggregate. Sci. Rep. 11, 12822–12914. doi:10.1038/s41598-021-92228-6
Keywords: recycled aggregate, concrete strength, discarded carbon fibers, concrete, based materials, concrete and cement
Citation: Zaid O and Zamir Hashmi SR (2021) Experimental Study on Mechanical Performance of Recycled Fine Aggregate Concrete Reinforced With Discarded Carbon Fibers. Front. Mater. 8:771423. doi: 10.3389/fmats.2021.771423
Received: 06 September 2021; Accepted: 18 October 2021;
Published: 24 November 2021.
Edited by:
Roberto Realfonzo, University of Salerno, ItalyReviewed by:
Francesco Micelli, University of Salento, ItalyEnzo Martinelli, University of Salerno, Italy
Copyright © 2021 Zaid and Zamir Hashmi. This is an open-access article distributed under the terms of the Creative Commons Attribution License (CC BY). The use, distribution or reproduction in other forums is permitted, provided the original author(s) and the copyright owner(s) are credited and that the original publication in this journal is cited, in accordance with accepted academic practice. No use, distribution or reproduction is permitted which does not comply with these terms.
*Correspondence: Osama Zaid, b3NhbWF6YWlkbWFyd2F0QGdtYWlsLmNvbQ==