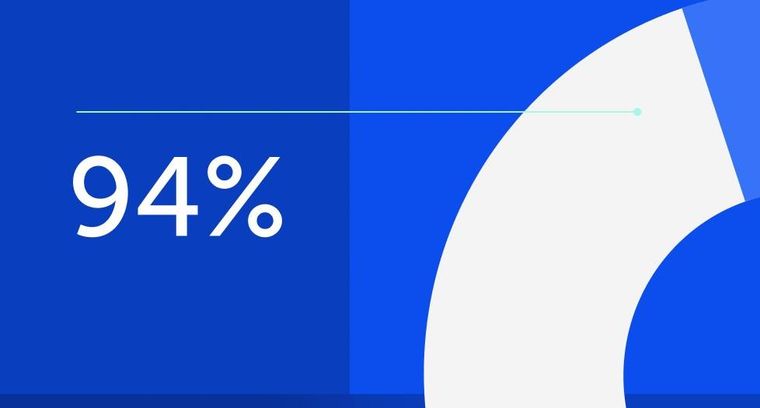
94% of researchers rate our articles as excellent or good
Learn more about the work of our research integrity team to safeguard the quality of each article we publish.
Find out more
MINI REVIEW article
Front. Mater., 12 November 2021
Sec. Structural Materials
Volume 8 - 2021 | https://doi.org/10.3389/fmats.2021.746022
This article is part of the Research TopicConcrete: New Functionalities and NanotechnologyView all 8 articles
Ultra-high performance concrete (UHPC) has the inherent potential to self-sensing capability due to its inclusion of steel fibers or other electrically conductive materials. Many studies have investigated the electrical and piezoresistive properties of UHPC. With the incorporation of micro steel fibers, carbon nanotubes, carbon nanofibrils, or nano graphite platelets, it opens up great potential to allow UHPC to effectively sense stress, strain, and crack damage. Therefore, the UHPC-based structures can achieve the functionality of structure health monitoring (SHM). This article reviews the recent advances in self-sensing capability of various UHPC-based materials with the focus on sensing capability and mechanisms. Future applications and challenges are also discussed.
Ultra-high performance concrete (UHPC) has gained increasing attention during the last two decades (Schmidt and Fehling, 2005; Batoz and Behloul, 2011; Gowda and Das, 2017; Xue et al., 2020). Up to now, the commercially available UHPC can easily reach 150 MPa or higher in compressive strength and 15 MPa in flexural strength. The superior mechanical properties and durability of UHPC enabled many applications in the field of bridge engineering, building engineering, and military engineering. In addition, many potential functions are enabled due to the unique compositions of UHPC, including electrical and piezoelectric properties such as self-sensing and structural health monitoring (SHM), joule heating (electrified to generate heat), and electromagnetic shielding. This allows designers to specifically tailor desired properties of UHPC structures or components to meet special requirements, as well as to improve safety, reliability, and serviceability of the infrastructures.
Self-sensing capability was first introduced to cementitious composites (Chen and Chung, 1993), by incorporating carbon fiber in concrete for the purpose of non-destructive flow detection. Since then, many concretes with in-situ self-sensing capability was developed and studied for their ability to monitor the stress, strain, cracking, damage, frequency, or deflection. In general, the self-sensing capability was introduced by the addition of electrically conductive functional fillers, such as metal fibers, conductive particles (copper aggregate, nickel or iron powder), and nano carbon materials (carbon nanotubes, carbon nanofibrils, carbon black, graphite platelets, and graphene). There are several literatures providing comprehensive reviews on the self-sensing concrete for SHM (Sun et al., 2010; Han et al., 2011; Han et al., 2015a; Han et al., 2015b; Han et al., 2015c; Dinesh et al., 2021)
UHPC has the inherit self-sensing capability due to its inclusion of metal fibers. In many other cases, electrically conductive nano carbon materials are often added to UHPC mixture to enhance mechanical properties, which also opens up great potential to allow UHPC to effectively sense stress, strain, and crack damage. For a typical UHPC, the compressive strength can reach up to 150–200 MPa, the fracture energy is up to 40,000 J/m2, and the ultimate tensile strain comparable to steel (can be on the order of 1%) which are all magnitude higher than ordinary cement-based composites (Dong et al., 2016). Therefore, UHPC is an ideal material to achieve functionality of SHM due to its high self-sending capability while providing superior strength and durability to the components or structures at the same time. This article reviews the recent advances in self-sensing capability of various UHPC-based composite materials. Future applications and challenges are also discussed.
In general, for any cementitious composites or concretes that possess self-sensing capability, the sensing properties stem from the change of intrinsic conductive network (from conductive functional fillers or metal fibers). The most commonly measured sensing signals are volume resistance/resistivity. To quantify sensing effectiveness, fractional change in resistance/resistivity (FCR, %) is often used. For instance, stress sensitivity can be quantified as FCR/σ (%/MPa). Higher value usually indicates better sensitivity. A much more detailed review on measurement of sensing signals can be found in literature (Han et al., 2015a). It should be noted that a proper content of functional filler is critical to achieve effective self-sensing capabilities. Too much fillers do not guarantee better performance, because the initial conductive network formed are too stable to respond to the external loads. Therefore, to achieve effective and efficient self-sensing ability in smart UHPC, it is important to select proper functional fillers and their content.
First of all, it should be noted that a well dispersed mixture is critical to achieve a stable and repeatable sensing capability for self-sensing concrete. For metal fibers or particles as the electrically conductive fillers, the strategy is to adjust the fiber content to reach percolation. For self-sensing concrete containing nano carbon materials (NCMs), the dispersion of NCMs is a difficult challenge. A commonly accepted method is to disperse NCMs in polycarboxylate-based superplasticizer by ultrasonication (Han et al., 2011; Shah et al., 2011). However, the dispersion issue is greatly aggravated by the extremely low water to binder ratio of UHPC. Therefore, the effective dispersion of functional fillers should be a premise in achieving stable self-sensing capability in UHPC.
Although many studies on self-sensing and smart concrete have been reported, there have been few investigations focused on self-sensing capability of UHPC only until recently. Dong et al. (2016) reported the first effective self-sensing short-cut super-fine stainless-steel wire reinforced reactive powder concrete (RPC) under external loads. In their previous report, the RPC (with a steel fiber diameter of 8 and 20 μm) achieved 28-day compressive strength between 100 and 130 MPa and tensile strength between 9 and 14 MPa, as well as more than four times more fracture energy comparing to the plain RPC. In addition, the electrical behavior of wire reinforced RPC was studied under three loading conditions: 1) cyclic compressive loading, 2) monotonically loaded until failure in compression, and 3) monotonically loaded until failure in flexure. Then the relationships between stress/strain and FCR were established. The results showed that percolation was achieved when adding 0.5 vol% wire of 20 μm diameter or 1.5 vol% wire of 8 μm, reducing the electrical resistivity up to four orders of magnitude. To reveal the intrinsic conductive mechanism of wire reinforced RPC, the equivalent circuits were proposed and analyzed considering many factors, such as pore solution resistance, charge transfer resistance, inductance, surface capacitance of C-S-H gel, diffusion impedance, resistance of wires, and, interface capacitance of wire-matrix. The equivalent circuits analysis concluded that 1) the conductivity is dominated by cement matrix when wire content was far below percolation threshold, 2) as the wire content increased, the conductivity was determined by both connection of wire and surface capacitance of C-S-H gel, and, 3) when the conductive network was formed (percolation), the conductivity was dominated by wires. Both the experimental results and the equivalent circuits analysis demonstrated that wires of 20 μm diameter were more suitable to be used as the conductive filler for PRC due to better dispersion. In another study from the same research team, Qiu et al. (2021) investigated the mechanical, electrical, and self-sensing properties of UHPC with the incorporation of stainless steel fibers (SFs) and copper coated steel fibers (CCSFs) at the dosage of 0.6 and 1.2 vol%. The UHPC with 1.2 vol% CCSFs demonstrated superior mechanical performance, as well as sensing sensitivity, in cyclic compressive loading and monotonic load up to 125.7 MPa, which is comparable to the previous work using 1.5 vol% wire. Another interesting finding was the equivalent circuits analysis demonstrated that the curing age has greater influence than incorporation of fibers on electrical resistivity, meaning at later age (28 days) cement matrix and pore solution are more dominate than metal fibers in term of conductive mechanism of UHPC.
Although sufficient self-sensing capability was achieved in steel wire reinforced RPC development by Dong et al. (2016), the use of short-cut super-fine stainless-steel wire may have compromised considerably (approximately 50%) in term of flexural strength comparing to traditional steel fibers used in UHPC (Yoo et al., 2016). Inspired by the work by Dong et al. (2015), a research team (You et al., 2017; Lee et al., 2018; Yoo et al., 2018) investigated the electrical and self-sensing capacities of UHPC (containing steel fibers) with carbon nanotubes (CNTs). A high strength straight steel fiber with a diameter of 0.2 mm, a length of 13 mm, and a tensile strength of 2788 MPa, was used at 1 vol%, 2 vol%, and 3 vol%. A multi-walled CNTs were incorporated up to 0.5 vol%. Three loading conditions were studied including 1) monotonically loading until failure in compression, as seen in Figure 1A, 2) monotonically loading until failure in flexure, as seen Figure 1B, and 3) monotonically loading until failure in uniaxial tension, as seen in Figures 1C,E. The research team found that 1) UHPC containing steel fiber was capable to detect ultimate failure, but insufficient in term of piezoresistivity, 2) UHPC (containing no steel fiber) with CNTs exhibited high unintended signal noise in the FCR and high electrical resistance, likely due to poor conductive pathway formation by only CNTs in UHPC, and 3) the scanning electron images (SEM) demonstrated that the CNTs attached to the surface of steel fiber could explain the substantial reduction in electrical resistivity. The experimental results demonstrated a well-established relationship between pre-peak/post-cracking response of UHPC with CNTs and measured FCR, indicating that the UHPC containing steel fiber and CNTs can be used as a self-strain and cracking sensing material under tension and compression. Lee et al. (2018) went further and investigated the effect of different steel fiber types (different diameters, aspect ratio, tensile strength, straight and twisted shape, see Table 1). However, the results showed that the steel fiber types had more effect on mechanical properties but much less significant influence on electrical behaviors of UHPRFC.
FIGURE 1. Typical loading conditions and measurement of self-sensing capacity of UHPC. (A) compressive loading (You et al., 2017); (B) flexural loading (You et al., 2017); (C) direct tensile loading (Yoo et al., 2018); (D) typical electromechanical response under compression (Kim et al., 2021); (E) tensile stress- and strain-time behaviors of UPFRC with CNTs (Yoo et al., 2018); (F) typical cracking sensing (Jung et al., 2020).
Another research team (Le et al., 2020; Le et al., 2021a; Le et al., 2021b; Kim et al., 2021) investigated the self-sensing ability of UHPC (containing steel fibers) with conductive aggregates under compression. The ideal was to utilize the tunneling conduction formed by conductive functional fillers (conductive aggregates in this case) to enhance the contact conduction (direct contact of neighboring functional fillers or steel fibers). Tunneling conduction, also sometimes referred as quantum tunneling conduction, happens when the distance between particles/fibers are less than approximately 10 nm. Le et al. (2020) used ball shaped slag steel aggregates (SSAs) with different sizes (0.39, 2, and 5 mm) to replace silica sands in UHPC (containing 2 vol% steel fibers with diameter of 0.2 mm and length of 6 mm). It should be noted that the SSAs used in this study was reported to contain low free-CaO (0.1–0.3 wt%), which could be potentially volumetrically stable in the long-term performance. However, the authors suggested that the effect of corrosion on long-term piezoelectric response should be further investigated. The results showed that the higher electrical conductivity was related to the higher content of SSAs and steel fibers, due to enhanced tunneling effect and contacting conduction within the composites. In addition, the incorporation of SSAs altered the piezoresistive response under compression comparing to the typical response, and finer SSAs demonstrated higher FCR likely due to a more uniform distribution. Le et al. (2021a) further investigated the effect of different functional fillers (including fine SSA, nickel aggregate, copper aggregate, and multi-wall CNT) on self-stress sensing ability of UHPC under compression. The results showed that all fillers can significantly reduce the electrical resistivity of the composites, but the fine SSA was the most economical choice with the highest FCR. Based on previously developed piezoresistive responses models with the consideration of electrical tunneling resistance and electrical contacting resistance, a theoretical calculation of optimum functional fillers content and fiber content was proposed. There results provided insights into the potential application of self-sensing abilities for monitoring the loss of prestressing stress in prestressed UHPC. In later studies, the research team also investigated the effect of loading rate (Kim et al., 2021), temperature, humidities, and age (Le et al., 2021b) on electrical properties of S-UHPC. The results showed that the stress-sensitive coefficient was decreased by 42.8 and 72.7% when increase the loading rate from 1 mm/min (representing static loading) to 4 mm/min and 8 mm/min (mimicking seismic loading), respectively. In terms of environmental temperature, the effect can be accounted for (approximately 2.27% change in electrical resistivity per °C). In addition, there is little effect of relative humidity change from 20 to 80%, and little changed after 21 days of age.
It is quite interesting to mention that a few attempts were made to migrate self-sensing capability of UHPC from laboratory to filed applications. Different from previous mentioned studies, Jung et al. (2020) added CNTs to UHPC to take advantage of the significantly decreased electrical resistivity of UHPC/CNT composites so as to achieve effective electrical curing at low voltage. A multi-wall CNT was added to the UHPC mixture at 1.2 wt% of total binder content, which was close to the calculated percolation threshold. The mechanical preparties tests and SEM results showed that the incorporation of CNTs improved the compressive strength mainly through bridging effect, pore filling effect, and C-S-H hardening effect. More importantly, the electrical resistivity of UHPC/CNT composites was reduced about 100 times comparing to the plain UHPC, which allowed a much more effective and energy efficient electrical curing even at a low voltage between 19 and 23 v. The temperature inside UHPC under low voltage only reached about 38°C during the first 48 h electrical curing period. The presence of CNT significantly increased the curing efficiency, and the UHPC/CNT composites stayed over 90°C during the 48 h curing period and completed the curing process. This enabled the effective electrical curing for filed casting of UHPC. In addition, the FCR measured can be used as an indicator of failure under compression or first cracking under flexure (Figure 1F), which might enable the potential cracking sensing application of UHPC/CNT composites.
Wang et al., deliberately poured fresh UHPC through L-shaped funnel to form UHPC specimen with aligned steel fibers. The UHPC contained up to 1.2% stainless steel fiber. The ultrasonic velocity test and image analysis proved that the L-shape funnel method can effectively distribute and align steel fibers, resulting in better conductivity, compressive strength, flexural strength and toughness.
Kim et al. (2021) designed and fabricated a S-UHPC block (smart concrete block, also known as SCB) integrated with multiple channel wireless sensing system (WSS) to monitor the stress loss and damage of prestressed tendons. The S-UHPC contained fine steel slag aggregates and short steel fiber as the conductive fillers. The design of SCB is based on actual post-tensioned components on bridges to provide excellent mechanical properties, efficient self-sensing capacity, and convenient data acquisition and transfer. The SCB was tested in the laboratory and a finite element analysis was carried out to simulate the stress distribution under different loading conditions. The results showed that the change in electrical resistivity was capable to monitor the loss of pre-stressing stress and detect local damage under eccentric external compression (Figure 1D). Multiple WSSs greatly improved the feasibility of SCB application in real structures.
Table 1 gives a summary of the reviewed studies including the functional fillers used, loading conditions, and major findings. Figure 1 demonstrated the typical loading conditions and sensing measurements of self-sensing UHPC units. Although there are only a handful of studies on self-sensing capabilities of UPHC, all studies showed promising results. With many different tried functional fillers, the current knowledge suggests that the combination of steel fiber and CNTs seems to be the most efficient in terms of sensing capability due to an ideal conductive network formation, and it could be further enhanced with the addition of fine metal aggregates due to tunneling effect.
Although concrete with self-sensing capability has been around for almost three decades, and there are already reports of self-sensing UHPC applications (Jung et al., 2020; Le et al., 2021a; Kim et al., 2021), the further development and applications still face several critical challenges:
• Preperation of self-sensing UHPC. As discussed in this review, self-sensing properties of cementitious composites stem from functional fillers, including metal fibers, CNTs, and metal aggregates. Adding these materials into the UHPC mixture which already has extremely low water to binder ratio requires careful selection of dispersion agents, mixing methods, and consolidation methods to ensure a uniform distribution of the functional fillers. To be able to cast large-scale structure components, a simple, reliable, and environmentally friendly solution is still being sought out.
• Long-term environmental effect on electrical properties. As self-sensing UHPC contains metal fiber of metal aggregate, corrosion might affect the self-sensing capability. The stability of long-term electrical properties needs further investigation. In addition, in-situ self-sensing UHPC could potentially affected by the surrounding environment including temperature and relative humidity change, and their long-term effect is unknown.
• Self-sensing mechanisms. There are a few self-sensing mechanisms proposed for smart concrete. However, its applicability to UHPC is not completely understood. More research effort is required to reveal the self-sensing mechanisms of UHPC in order to provide insights for designing UHPC with self-sensing capabilities.
• Application in large-scale structure components. Although structures made of UHPC are quite frequently seen nowadays, there is few reports on actual UHPC structure components which has functional self-sensing abilities. This technology is still in great need to be transformed from laboratory to engineering applications.
It has been almost three decades since the self-sensing capability was first introduced to cementitious composites, however, only until recently there are limited number of studies on UHPC with self-sensing capabilities. There capabilities include in-situ monitoring of stress, strain, and, cracking detection under compression, tension, and flexure, mainly through measuring changes in electrical resistivity, introduced by adding conductive functional fillers such as steel fiber, CNT, metal aggregates. This article provides a summary and critical reviews of studies focused on self-sensing capabilities of UHPC composites. Future challenges of this technology are also discussed in the hope of safer, durable, sustainable, and smart infrastructures with extended service life.
All authors contributed to the article and approved the submitted manuscript.
This work was supported by Engineering Research Center of Prevention and Control of Geological Disasters in Northern Fujian, Fujian Province University (WYERC 2020-1), Science Foundation Projects of Fujian Province (2019J01824), and National Natural Science Foundation of China (51808121). The authors also would like to thank the funding provided by Fujian Provincial Educational Research Grant for Young Faculty, Fujian Provincial Department of Education (JT180157).
The authors declare that the research was conducted in the absence of any commercial or financial relationships that could be construed as a potential conflict of interest.
All claims expressed in this article are solely those of the authors and do not necessarily represent those of their affiliated organizations, or those of the publisher, the editors and the reviewers. Any product that may be evaluated in this article, or claim that may be made by its manufacturer, is not guaranteed or endorsed by the publisher.
Batoz, J. F., and Behloul, M. (2011). “UHPFRC Development on the Last Two Decades: an Overview,” in Designing and Building with UHPFRC: State of the Art and Development (London, UK and Hoboken, NJ: ISTE Ltd and John Wiley & Sons, Inc), 43–62.
Chen, P.-W., and Chung, D. D. L. (1993). Carbon Fiber Reinforced concrete for Smart Structures Capable of Non-destructive Flaw Detection. Smart Mater. Struct. 2 (1), 22–30. doi:10.1088/0964-1726/2/1/004
Dinesh, A., Sudharsan, S. T., and Haribala, S. (2021). Self-sensing Cement-Based Sensor with Carbon Nanotube: Fabrication and Properties - A Review. Mater. Today Proc. 46, 5801–5807. doi:10.1016/j.matpr.2021.02.722
Dong, S., Han, B., Ou, J., Li, Z., Han, L., and Yu, X. (2016). Electrically Conductive Behaviors and Mechanisms of Short-Cut Super-fine Stainless Wire Reinforced Reactive Powder Concrete. Cement and Concrete Composites 72, 48–65. doi:10.1016/j.cemconcomp.2016.05.022
Gowda, H., and Das, B. B. (2017). Ultra High Performance Concrete-Sustainable Solution for the Next Generation Infrastructure, International Conference on Sustainable Infrastructure. Reston, VA: American Society of Civil Engineers, 397–405.
Han, B., Ding, S., and Yu, X. (2015a). Intrinsic Self-Sensing concrete and Structures: A Review. Measurement 59, 110–128. doi:10.1016/j.measurement.2014.09.048
Han, B., Sun, S., Ding, S., Zhang, L., Yu, X., and Ou, J. (2015b). Review of Nanocarbon-Engineered Multifunctional Cementitious Composites. Composites A: Appl. Sci. Manufacturing 70, 69–81. doi:10.1016/j.compositesa.2014.12.002
Han, B., Wang, Y., Dong, S., Zhang, L., Ding, S., Yu, X., et al. (2015c). Smart Concretes and Structures: A Review. J. Intell. Mater. Syst. Struct. 26 (11), 1303–1345. doi:10.1177/1045389X15586452
Han, B., Yu, X., and Ou, J. (2011). “Multifunctional and Smart Carbon Nanotube Reinforced Cement-Based Materials,” in Nanotechnology in Civil Infrastructure (New York, NY: Springer), 1–47. doi:10.1007/978-3-642-16657-0_1
Jung, M., Park, J., Hong, S., and Moon, J. (2020). Electrically Cured Ultra-high Performance concrete (UHPC) Embedded with Carbon Nanotubes for Field Casting and Crack Sensing. Mater. Des. 196, 1–12. doi:10.1016/j.matdes.2020.109127
Kim, T. U., Le, H. V., Park, J. W., Eock, S. K., Jang, Y., and Kim, D. J. (2021). Development of a Smart concrete Block with an Eccentric Load Sensing Capacity. Constr Build Mater. 306, 1–13. doi:10.1016/j.conbuildmat.2021.124881
Le, H. V., Kim, M. K., Kim, D. J., and Park, J. (2021b). Electrical Properties of Smart Ultra-high Performance Concrete Under Various Temperatures, Humidities, and Age of concrete. Cem Concr Compos. 118, 1–14. doi:10.1016/j.cemconcomp.2021.103979
Le, H. V., Kim, M. K., Kim, S. U., Chung, S. Y., and Kim, D. J. (2021a). Enhancing Self-Stress Sensing Ability of Smart Ultra-high Performance Concretes Under Compression by Using Nano Functional Fillers. J. Build Eng. 44, 1–14. doi:10.1016/j.jobe.2021.102717
Le, H. V., Lee, D. H., and Kim, D. J. (2020). Effects of Steel Slag Aggregate Size and Content on Piezoresistive Responses of Smart Ultra-high-performance Fiber-Reinforced Concretes. Sens Actuators A 305, 1–14. doi:10.1016/j.sna.2020.111925
Lee, S. H., Kim, S., and Yoo, D.-Y. (2018). Hybrid Effects of Steel Fiber and Carbon Nanotube on Self-Sensing Capability of Ultra-high-performance Concrete. Construction Building Mater. 185, 530–544. doi:10.1016/j.conbuildmat.2018.07.071
Lee, S. Y., Kim, M. K., and Kim, D. J. (2021). Effect of Loading Rate on Self-Stress Sensing Capacity of the Smart UHPC. J. Korea Academia-Industrial cooperation Soc. 22 (5), 81–88. doi:10.3390/s21155251
Qiu, L., Dong, S., Yu, X., and Han, B. (2021). Self-sensing Ultra-high Performance Concrete for In-Situ Monitoring. Sens Actuators A 331, 1–11. doi:10.1016/j.sna.2021.113049
Schmidt, M., and Fehling, E. (2005). Ultra-high-performance concrete: Research, Development and Application in Europe. ACI Symp. Publ. 228, 51–78. https://www.concrete.org/publications/internationalconcreteabstractsportal.aspx?m=details&i=14460.
Shah, S. P., Konsta-Gdoutos, M. S., and Metaxa, Z. S. (2011). “Advanced Cement Based Nanocomposites,” in Recent Adv Mech. Springer. Editors A. N. Kounadis, and E. E. Gdoutos, 313–327. doi:10.1007/978-94-007-0557-9_16
Sun, M., Staszewski, W. J., and Swamy, R. N. (2010). Smart Sensing Technologies for Structural Health Monitoring of Civil Engineering Structures. Adv. Civil Eng. 2010, 1–13. doi:10.1155/2010/724962
Wang, H., Shi, F., Shen, J., and Zhang, A. (2021). Research on the Self-Sensing and Mechanical Properties of Aligned Stainless Steel Fiber0reinfroced Reactive Powder concrete. Cem Concr Compos. 119, 1–18. doi:10.1016/j.cemconcomp.2021.104001
Xue, J., Briseghella, B., Huang, F., Nuti, C., Tabatabai, H., and Chen, B. (2020). Review of Ultra-high Performance Concrete and its Application in Bridge Engineering. Constr Build Mater. 260, 13–20. doi:10.1016/j.conbuildmat.2020.119844
Yoo, D.-Y., Banthia, N., Kang, S.-T., and Yoon, Y.-S. (2016). Size Effect in Ultra-high-performance Concrete Beams. Eng. Fracture Mech. 157, 86–106. doi:10.1016/j.engfracmech.2016.02.009
Yoo, D.-Y., Kim, S., and Lee, S. H. (2018). Self-sensing Capability of Ultra-high-performance Concrete Containing Steel Fibers and Carbon Nanotubes Under Tension. Sensors Actuators A: Phys. 276, 125–136. doi:10.1016/j.sna.2018.04.009
Keywords: UHPC, functional filler, self-sensing, electrical resistivity, piezoelectric property
Citation: Lian J, Hu C, Fu T and Wang Y (2021) Review of Self-sensing Capability of Ultra-high Performance Concrete. Front. Mater. 8:746022. doi: 10.3389/fmats.2021.746022
Received: 23 July 2021; Accepted: 12 October 2021;
Published: 12 November 2021.
Edited by:
Konstantin Sobolev, University of Wisconsin–Milwaukee, United StatesReviewed by:
Zhiyong Liu, Southeast University, ChinaCopyright © 2021 Lian, Hu, Fu and Wang. This is an open-access article distributed under the terms of the Creative Commons Attribution License (CC BY). The use, distribution or reproduction in other forums is permitted, provided the original author(s) and the copyright owner(s) are credited and that the original publication in this journal is cited, in accordance with accepted academic practice. No use, distribution or reproduction is permitted which does not comply with these terms.
*Correspondence: Tengfei Fu, ZnV0ZW5nZmVpQGZhZnUuZWR1LmNu; Yulin Wang, eWx3YW5naG1AMTYzLmNvbQ==
Disclaimer: All claims expressed in this article are solely those of the authors and do not necessarily represent those of their affiliated organizations, or those of the publisher, the editors and the reviewers. Any product that may be evaluated in this article or claim that may be made by its manufacturer is not guaranteed or endorsed by the publisher.
Research integrity at Frontiers
Learn more about the work of our research integrity team to safeguard the quality of each article we publish.